DCS系统的设计
dcs控制系统课程设计

dcs控制系统课程设计一、课程目标知识目标:1. 理解DCS控制系统的基本原理和结构,掌握其主要组成部分及功能。
2. 学会分析DCS控制系统的优缺点,并能够与其它控制系统进行对比。
3. 掌握DCS控制系统的编程与组态方法,能够进行简单的系统设计。
技能目标:1. 培养学生运用所学知识解决实际问题的能力,能够针对特定工艺过程设计合适的DCS控制系统。
2. 提高学生的团队协作能力,通过小组讨论和项目实践,培养学生的沟通与协作技巧。
3. 培养学生独立思考和创新能力,能够对现有DCS控制系统进行改进和优化。
情感态度价值观目标:1. 培养学生对自动化控制技术的兴趣,激发其探索精神和求知欲望。
2. 引导学生关注我国自动化产业发展,增强民族自豪感,树立正确的价值观。
3. 培养学生的责任感和使命感,使其认识到自动化技术在国家经济建设中的重要作用。
本课程针对高年级学生,结合学科特点,注重理论与实践相结合。
课程目标旨在使学生掌握DCS控制系统的基本知识和技能,同时培养其情感态度价值观,为后续学习和工作打下坚实基础。
通过分解课程目标为具体学习成果,为教学设计和评估提供明确方向。
二、教学内容1. DCS控制系统概述:介绍DCS的定义、发展历程、应用领域,使学生了解DCS控制系统的背景和重要性。
教材章节:第一章 绪论2. DCS系统组成与原理:讲解DCS系统的硬件、软件结构,以及控制算法和通信网络。
教材章节:第二章 DCS系统组成与原理3. DCS编程与组态:学习DCS编程语言,掌握组态软件的使用,进行简单控制策略的设计与实现。
教材章节:第三章 DCS编程与组态4. DCS系统设计与应用:分析实际工艺过程,设计DCS控制系统,进行系统调试与优化。
教材章节:第四章 DCS系统设计与应用5. DCS控制系统案例分析:通过剖析典型工程案例,使学生了解DCS在工程实际中的应用。
教材章节:第五章 DCS控制系统案例分析6. DCS控制系统发展趋势与展望:探讨DCS技术的发展趋势,激发学生对未来自动化技术的探索欲望。
DCS系统控制组态仿真软件的设计和实现

DCS系统控制组态仿真软件的设计和实现DCS系统(分布式控制系统)是一种基于计算机网络的现代工业自动化控制系统,它通过连接和集成各种智能设备和传感器,实现对工业过程的实时监测、控制和优化。
DCS系统控制组态仿真软件是一种用于设计和验证DCS系统控制策略的工具。
本文将重点介绍DCS系统控制组态仿真软件的设计和实现。
一、DCS系统控制组态仿真软件的设计目标1.提供友好的图形用户界面,方便用户进行系统配置和仿真实验的操作;2.具备强大的模型和仿真引擎,能够对复杂的DCS系统进行准确的仿真;3.支持多种控制算法和策略的设计与验证;4.具备数据采集和分析功能,方便用户对仿真结果进行分析和优化;5.支持多用户和多项目的管理,方便团队合作和项目追溯。
二、DCS系统控制组态仿真软件的实现方法实现DCS系统控制组态仿真软件可以采用以下方法:1.采用面向对象的软件设计方法,将DCS系统中的各个设备和控制模块抽象为对象,并建立对象之间的关系和交互;2.使用图形编程技术,设计可视化界面,提供丰富的组态元素库,支持用户灵活地配置和布置控制系统;3.建立仿真引擎,采用适当的数学模型和算法,对DCS系统进行准确的仿真计算;4.提供开放的接口和数据格式,支持与其他软件的集成和数据交换;5.实现网络通信功能,支持多用户之间的远程协作和共享。
三、DCS系统控制组态仿真软件的关键技术在设计和实现DCS系统控制组态仿真软件时,需要运用以下关键技术:1.图形编程技术:包括界面设计、图形绘制、交互操作等;2.数据模型技术:包括数据结构设计、对象关系映射等;3.控制算法技术:包括PID控制、模糊控制、优化算法等;4.仿真计算技术:包括数学模型建立、仿真引擎实现等;5.网络通信技术:包括客户端/服务器架构、远程访问、数据传输等。
四、DCS系统控制组态仿真软件的应用场景1.工业过程优化:通过仿真和优化控制策略,改进和优化工业过程的性能;2.设备选型和配置:通过仿真和验证不同设备和配置的性能,选择最佳的设备和配置方案;3.故障诊断和维护:通过仿真和故障分析,帮助用户找到故障原因并进行及时维修;4.操作培训和安全培训:通过模拟实际工作场景,提供操作培训和安全培训的环境。
DCS单回路控制系统设计

DCS单回路控制系统设计DCS(分布式控制系统)是一种用于实时控制和监控工业过程的自动化系统。
它是由多个分布在整个工厂的分散控制设备组成的。
每个设备都有自己的控制功能,并可以相互通信以实现全面的过程控制。
DCS可以实现对各种设备、仪器、传感器和执行器的集中控制和监控,从而提高生产效率和产品质量。
在设计DCS单回路控制系统时,需要考虑以下几个方面:1.控制目标和需求:首先需要确定系统的控制目标,例如温度、压力、流量等。
然后根据目标确定系统所需的设备、仪器和传感器。
2.信号传输和处理:DCS系统中控制信号的传输和处理非常重要。
可以使用模拟信号或数字信号,模拟信号通常用于测量和控制,数字信号用于数据传输和处理。
3.控制策略:根据控制目标,选择合适的控制策略。
常用的控制策略包括比例-积分-微分(PID)控制、模糊控制、模型预测控制等。
根据实际情况,可以选择单回路控制或多回路控制。
4.控制设备和软件:选择合适的控制设备和软件。
常用的控制设备包括PLC(可编程逻辑控制器)、DCS控制器等。
控制软件通常包括实时数据库、报警管理、历史数据记录和故障诊断等功能。
5.安全性和可靠性:在设计DCS单回路控制系统时,必须考虑安全性和可靠性。
例如,选择适当的传感器和执行器,确保系统安全可靠运行。
此外,应设置适当的报警和故障诊断系统,及时发现和解决潜在问题。
6.通信和网络:DCS系统中的设备通常通过网络进行通信。
因此,设计时需要选择适当的通信协议和网络架构,以确保数据的传输和处理效率。
7.人机界面:为了方便操作和监控,DCS系统需要良好的人机界面。
设计时应考虑用户的需求和操作习惯,以实现直观、简单、易用的界面。
总结来说,DCS单回路控制系统设计应考虑控制目标和需求、信号传输和处理、控制策略、控制设备和软件、安全性和可靠性、通信和网络,以及人机界面等方面。
通过合理的设计,可以实现对工业过程的高效控制和监控,提高生产效率和产品质量。
dcs控制方案

dcs控制方案一、概述DCS(分布式控制系统)是一种基于计算机网络和现场总线技术的自动化控制系统。
它可以集成各类控制设备、执行器和传感器,并通过高效的数据通信实现对生产过程的监控和控制。
本文将详细介绍DCS控制方案的设计与实施。
二、系统组成1. 硬件方案DCS控制方案的硬件组成主要包括控制器、输入/输出模块、执行器和传感器等。
控制器具备高性能的数据处理能力,负责控制算法的执行和监控系统的运行。
输入/输出模块则负责与外部设备进行数据交互,传输控制信号和采集过程数据。
执行器和传感器承担着实际动作和信号采集的任务,将系统状态信息反馈给控制器。
2. 软件方案DCS控制方案的软件方案是整个系统的核心。
它包括了实时嵌入式操作系统、控制算法、监视系统以及人机界面等。
实时嵌入式操作系统保证了系统的高可用性和稳定性,控制算法则实现了对生产过程的精确控制。
监视系统通过对采集到的数据进行分析和处理,提供运行状态的监控报告和故障诊断。
人机界面提供了直观友好的操作界面,方便操作人员进行实时监控和调整参数。
三、DCS控制方案设计1. 系统需求分析在设计DCS控制方案之前,需要对待控制的生产过程进行全面的需求分析。
包括对工艺流程、设备性能要求、安全性要求和监控需求等进行详细的了解。
通过充分了解系统需求,才能制定出符合实际情况的控制方案。
2. 系统结构设计根据分析得出的系统需求,进行系统结构设计。
将整个生产过程划分为若干个子系统,根据不同的功能和控制需求进行模块化设计。
同时考虑实时性、可靠性和安全性等因素,确定控制器和传感器的布置位置,以及各个子系统之间的数据通信方式。
3. 控制算法设计根据生产过程的特点和控制需求,设计合理的控制算法。
可以采用传统的PID控制算法,也可以结合先进的模糊控制、神经网络控制或模型预测控制等。
控制算法需要综合考虑系统的稳定性、鲁棒性和响应速度,以实现对生产过程的精确控制。
四、DCS控制方案实施1. 系统集成根据设计方案,进行硬件设备的安装和网络连接。
分布式控制系统(dcs)设计与应用实例

分布式控制系统(dcs)设计与应用实例1. 引言1.1 概述分布式控制系统(DCS)是一种应用于工业自动化领域的控制系统,其设计和应用对工业生产的高效性和可靠性起着重要的作用。
随着技术的不断发展和进步,DCS已经广泛应用于各个领域,如工厂生产线、建筑智能化控制和能源管理系统等。
1.2 文章结构本文将首先对分布式控制系统进行概述,包括其定义与特点以及架构。
然后探讨DCS设计的原则与方法,重点介绍系统模块划分、数据通信机制设计以及容错与安全性设计等方面。
接下来将通过实际案例,详细展示DCS在工业生产自动化、建筑智能化控制和能源管理系统方面的应用实例。
最后,在结论与展望部分对主要观点和发现进行总结,并展望分布式控制系统未来的发展趋势和挑战。
1.3 目的本文旨在深入介绍分布式控制系统的设计原则与方法,并通过实例展示其在不同领域中的广泛应用。
通过阅读本文,读者可以了解到DCS的基本概念、特点和架构,并了解到如何设计一个高效、可靠的分布式控制系统。
同时,对于工业生产自动化、建筑智能化控制和能源管理系统等领域感兴趣的读者,可以通过实例了解到DCS在这些领域中的应用及其所带来的好处和挑战。
最后,本文还将展望分布式控制系统未来的发展趋势,为相关研究者和从业人员提供参考思路。
2. 分布式控制系统概述2.1 定义与特点分布式控制系统(DCS)是一种将控制功能集中在中央处理器上,并通过网络将其连接到各个分散的现场设备的自动化系统。
它通过分布在整个工厂或建筑物内的现场设备,收集和传输数据以实现实时监测和远程操作。
DCS具有以下特点:- 灵活性:DCS可以根据需要进行可扩展和定制,适应不同规模和复杂度的应用。
- 实时性:DCS能够快速响应并传递准确的数据,以确保实时监测和控制。
- 通信能力:DCS利用网络技术实现设备之间的高效通信,使得信息可以即时传递。
- 可靠性:DCS采用冗余设计,确保系统出现故障时仍能正常工作,并提供数据备份和恢复机制。
DCS设计说明范文

DCS设计说明范文DCS(集散式控制系统)是一种用于工业自动化控制的技术,将分布的控制设备与上位机连接起来,实现集中控制和监测。
DCS设计涉及多个方面,包括硬件设备、软件系统、网络通讯等。
一、硬件设备设计:在DCS设计中,硬件设备的选择和布置对整个系统的稳定性和可靠性有重要影响。
首先要考虑的是控制器的选择,在实际工程中可以选择具有高性能和可靠性的PLC(可编程逻辑控制器)作为控制器。
另外,还需要选择适配的输入输出模块、传感器和执行器等设备,以满足不同的控制任务。
设备的布置要合理,保证设备之间的连接方便可靠,同时要考虑到空间和电力的需求,做好布线和供电方案。
二、软件系统设计:软件系统是DCS设计中非常重要的一部分,它负责整个系统的控制和监测。
在软件系统设计中,应该考虑以下几个方面:1.根据实际需求设计合理的控制策略,包括逻辑控制、调节控制、报警控制等。
根据过程的特点和要求,选择合适的控制算法和参数,确保系统的稳定性和可靠性。
2.设计友好的人机界面,使操作人员能够方便地配置和监控整个系统,包括界面布局、操作逻辑、报警信息等。
同时也要考虑到系统的安全性和权限管理,确保只有授权人员可以进行操作。
3.数据采集和处理,包括实时数据的采集和存储,以及数据的处理和分析。
通过采集和分析数据,可以及时发现问题和优化系统性能。
4.设计完善的故障诊断和排除功能,在出现故障时,能够快速定位问题并采取相应的措施进行修复。
5.考虑系统的可扩展性和可维护性,在系统需要升级或扩展时,能够方便地进行改造和维护。
三、网络通信设计:DCS系统中,各个控制设备之间通过网络进行通信,传输控制命令和采集的数据。
因此,网络通信的设计也是DCS设计的重要内容。
以下是一些需要考虑的设计要点:1.网络拓扑结构的选择,根据实际情况选择合适的网络结构,如总线型、环形、星形等,确保网络的可靠性和稳定性。
2. 网络协议的选择,合理选择通信协议,如Modbus、OPC等,以满足实际需求。
DCS的工程设计方案

DCS的工程设计方案DCS(distributed control system)是一种分布式控制系统,广泛应用于工业生产和制造过程中的自动化控制及监控系统。
它通过联网的方式,将传感器、执行机构、控制器和监控设备连接起来,实现对生产过程进行全面的监测和控制。
在这篇文章中,将介绍一个DCS的工程设计方案。
1.系统架构设计首先,为了确保系统的运行和可靠性,我们需要设计一个合理的系统架构。
该架构应包括主控制器、子控制器和I/O模块。
主控制器负责整个系统的控制和监控,而子控制器用于管理和监控不同的子系统。
I/O模块则与传感器和执行机构连接,将其信号传输到控制器和监控设备。
2.传感器和执行机构的选择在选择传感器和执行机构时,需要考虑到其适用性和可靠性。
传感器应能够准确地收集和传输生产系统中的各种参数,例如温度、压力和流量等。
执行机构则需要能够根据控制器的指令,精确地执行相应的动作。
3.人机界面设计为了更好地实现对生产过程的监控和控制,需要设计一个易于操作和理解的人机界面。
该界面应包括图形化的显示和直观的控制按钮,使操作人员能够快速而准确地了解系统状态,并对其进行调整和控制。
4.通信网络设计DCS系统是一个分布式的网络控制系统,因此需要设计一个稳定和高效的通信网络。
该网络应支持数据的快速传输和实时反馈,以确保系统的高可靠性和精确性。
5.系统备份与故障恢复为了避免单点故障对整个系统的影响,需要设计系统备份和故障恢复机制。
例如,可以设置双机热备份,以防止主控制器的故障导致系统的中断。
此外,还可以建立故障诊断和自动修复机制,提高系统的稳定性和可靠性。
6.安全性设计在DCS系统中,安全是一个重要的考虑因素。
系统应具备必要的安全措施,以防止未经授权的访问和潜在的安全威胁。
例如,可以采用密码保护、权限控制、防火墙等安全措施,确保系统的安全运行。
总之,一个有效的DCS工程设计方案应考虑到系统的架构设计、传感器和执行机构的选择、人机界面的设计、通信网络的设计、系统备份与故障恢复以及安全性的设计等方面。
基于DCS的流体测控系统设计与实现

基于DCS(分布式控制系统)的流体测控系统设计与实现可以用于监测、控制和管理流体处理过程。
下面是一个基本的流体测控系统设计和实现的示例:1. 系统架构设计:-确定系统的整体架构,包括传感器、执行器、控制器和人机界面等组件的布局和连接方式。
-考虑系统的可扩展性和容错性,以满足未来的需求和故障恢复。
2. 传感器选择与布置:-选择适当的传感器,如压力传感器、温度传感器、流量传感器等,用于监测流体处理过程中的关键参数。
-合理布置传感器,确保能够准确地获取所需的流体参数数据。
3. 执行器选择与安装:-根据流体处理过程的要求,选择适当的执行器,如阀门、泵等,用于控制流体的流动。
-安装执行器,并与控制器进行连接,以实现对流体处理过程的精确控制。
4. 控制策略设计:-根据流体处理过程的特点和要求,设计合适的控制策略,如PID控制、模型预测控制等。
-考虑不同参数之间的相互关系,设置合理的控制算法和参数。
5. 控制器配置与编程:-配置DCS系统中的控制器,按照设计的控制策略进行参数设置和调整。
-根据需要,编程控制器,实现流体处理过程的自动化控制和优化。
6. 人机界面设计与实现:-设计直观友好的人机界面,用于监视和操作流体测控系统。
-实现人机界面,包括图形化显示流体参数、报警信息、控制操作等功能。
7. 数据采集与存储:-设置数据采集周期,定时采集传感器数据,并存储到数据库或历史数据存档中。
-可以利用采集的数据进行分析、趋势预测、故障诊断等后续处理。
8. 系统测试与调试:-在实际硬件上搭建流体测控系统,进行系统测试和调试。
-验证系统的性能和稳定性,确保系统在各种工况下正常运行。
以上是一个基于DCS的流体测控系统设计与实现的示例。
在实际设计中,可能还需要考虑安全性、可靠性、网络通信等方面的因素,以满足特定的应用需求。
设计和实现流体测控系统需要充分理解流体处理过程和控制原理,同时结合DCS技术和工程实践,进行综合考虑和优化。
DCS系统设计中的关键要素与考虑因素

DCS系统设计中的关键要素与考虑因素在DCS(分布式控制系统)系统设计中,有一些关键要素与考虑因素需要被重视。
这些因素直接影响着系统的性能、可靠性和可扩展性。
本文将探讨DCS系统设计中的关键要素与考虑因素,旨在为系统设计者提供一些指导和建议。
1. 系统可靠性:DCS系统通常用于监控和控制关键过程中的工业设备。
因此,系统的可靠性至关重要。
在设计中,需要考虑以下因素:-冗余性设计:采用多个冗余组件,如控制器、通信模块和电源,以确保一旦一个组件发生故障,系统仍能正常运行。
-系统自诊断:集成自动检测和故障诊断功能,能够及时发现问题并采取相应的措施。
-备份和恢复机制:确保在系统故障或停电时能够快速地备份和恢复数据。
2. 系统性能:DCS系统需要处理大量的实时数据和控制指令。
为了确保系统具有良好的性能,需要考虑以下因素:-处理器性能:选择高性能的处理器和适当的处理器架构,以满足系统的计算需求。
-网络带宽:选择高带宽的通信网络,以支持实时数据传输和远程操作。
-数据存储和处理:采用高速的存储设备和数据库系统,以实现快速的数据存取和分析功能。
3. 系统安全:DCS系统通常连接到不同的工业设备和网络,因此系统的安全性至关重要。
以下是一些需要考虑的安全因素:-身份验证和访问控制:采用安全的用户身份验证机制,并限制用户的访问权限,以防止未经授权的访问。
-数据加密:对通过网络传输的数据进行加密,以确保数据的机密性和完整性。
-防止网络攻击:采用防火墙和入侵检测系统,以保护系统免受网络攻击和恶意软件的侵害。
4. 系统扩展性:DCS系统通常需要根据工艺流程和设备的变化进行扩展。
以下是一些需要考虑的扩展性因素:-模块化设计:将系统划分为多个模块,使得添加、删除或替换某个模块时对整个系统的影响最小化。
-接口标准化:使用行业标准的接口和通信协议,以便与其他设备和系统进行集成。
-容量规划:考虑系统的容量需求,预留足够的资源和性能,以容纳未来的扩展。
DCS系统仿真方案的设计
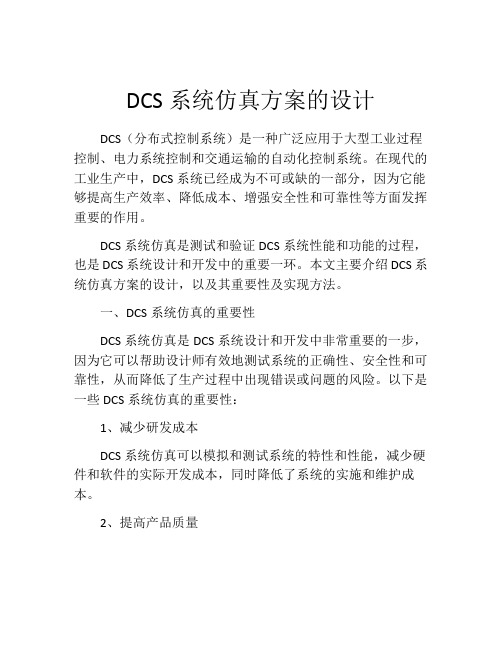
DCS系统仿真方案的设计DCS(分布式控制系统)是一种广泛应用于大型工业过程控制、电力系统控制和交通运输的自动化控制系统。
在现代的工业生产中,DCS系统已经成为不可或缺的一部分,因为它能够提高生产效率、降低成本、增强安全性和可靠性等方面发挥重要的作用。
DCS系统仿真是测试和验证DCS系统性能和功能的过程,也是DCS系统设计和开发中的重要一环。
本文主要介绍DCS系统仿真方案的设计,以及其重要性及实现方法。
一、DCS系统仿真的重要性DCS系统仿真是DCS系统设计和开发中非常重要的一步,因为它可以帮助设计师有效地测试系统的正确性、安全性和可靠性,从而降低了生产过程中出现错误或问题的风险。
以下是一些DCS系统仿真的重要性:1、减少研发成本DCS系统仿真可以模拟和测试系统的特性和性能,减少硬件和软件的实际开发成本,同时降低了系统的实施和维护成本。
2、提高产品质量DCS系统仿真可以帮助设计师在产品发行之前发现并解决潜在的缺陷和问题,从而提高产品质量,减少后期的维护和修复成本。
3、提高生产效率DCS系统仿真可以模拟和预测生产过程中可能出现的问题,从而提供解决方案以优化生产流程,提高生产效率和生产质量。
4、降低风险DCS系统仿真可以帮助设计师评估系统的安全性和可靠性,并减少生产中意外事件的风险。
二、DCS系统仿真方案的设计针对不同的DCS系统设计和功能,其仿真方案需要根据实际情况进行设计和优化。
以下是一些常见的DCS系统仿真方案设计步骤:1、确定仿真目标和需求在开始设计DCS系统仿真方案之前,需要先明确仿真的目标和需求,包括系统性能、执行效率和故障处理等方面。
2、设定仿真的范围和参数在确定仿真目标和需要之后,需要设定仿真的范围和参数。
这包括针对不同操作的参数设置、模拟环境的建立、仿真时间的确定等。
3、建立仿真模型在确定范围和参数之后,需要建立仿真模型,模拟系统的组件和行为。
在建模过程中,需要考虑每个组件的特性、性能和相互作用。
dcs控制方案
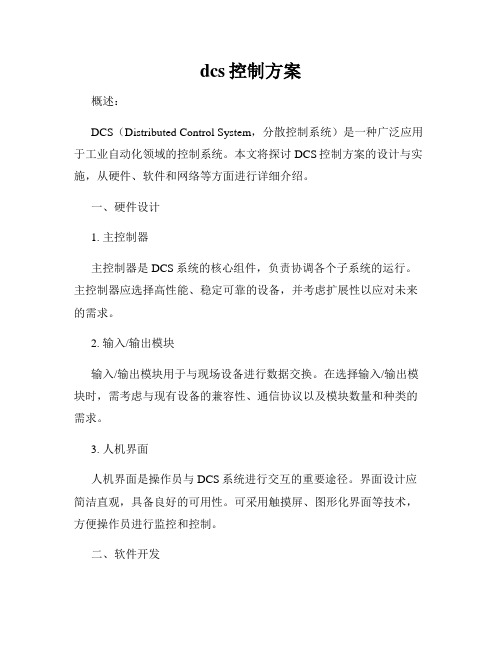
dcs控制方案概述:DCS(Distributed Control System,分散控制系统)是一种广泛应用于工业自动化领域的控制系统。
本文将探讨DCS控制方案的设计与实施,从硬件、软件和网络等方面进行详细介绍。
一、硬件设计1. 主控制器主控制器是DCS系统的核心组件,负责协调各个子系统的运行。
主控制器应选择高性能、稳定可靠的设备,并考虑扩展性以应对未来的需求。
2. 输入/输出模块输入/输出模块用于与现场设备进行数据交换。
在选择输入/输出模块时,需考虑与现有设备的兼容性、通信协议以及模块数量和种类的需求。
3. 人机界面人机界面是操作员与DCS系统进行交互的重要途径。
界面设计应简洁直观,具备良好的可用性。
可采用触摸屏、图形化界面等技术,方便操作员进行监控和控制。
二、软件开发1. 系统配置在DCS的软件开发中,首先需要进行系统配置。
配置工作包括设备信息录入、通信参数设置、遥控遥测点位定义等。
合理的系统配置有助于提高系统的稳定性和可靠性。
2. 控制逻辑编程控制逻辑编程是DCS控制方案的核心部分。
编程时应根据实际需求进行逻辑的设计和实现,确保系统具备可靠的自动控制能力。
同时,编程过程中要注重代码的可读性和可维护性。
3. 报警与事件处理DCS系统应具备报警和事件处理功能,及时向操作员提供异常情况的提示和处理建议。
在软件开发过程中,需要设定相关的报警和事件触发条件,并制定相应的处理策略。
三、网络建设1. 网络拓扑结构DCS系统的网络结构应具备可靠性和可扩展性。
通常采用冗余网络拓扑结构,以确保系统在部分网络故障情况下能够正常运行,并能够方便地扩展新设备。
2. 网络安全DCS系统的网络安全至关重要。
应采取一系列措施,如建立防火墙、加密通信、访问控制等,保障系统的安全性和稳定性。
3. 数据通信DCS系统中各设备之间的数据通信是系统正常运行的基础。
需要选择适用的通信协议和传输方式,确保数据的准确性和及时性。
四、方案实施与调试1. 设备安装与连线按照设计方案进行设备的安装和连线工作。
dcs系统智慧工厂设计方案

dcs系统智慧工厂设计方案智慧工厂是指通过集成各种物联网设备、传感器、机器学习算法等技术手段,实现生产过程的自动化、智能化和高效化。
在智慧工厂设计方案中,DCS(分散控制系统)起着至关重要的作用。
下面是一个基于DCS系统的智慧工厂设计方案。
设计目标:1. 自动化控制:实现生产全过程的自动化控制,提高生产效率和产品质量。
2. 数据分析与优化:通过收集和分析生产数据,实时监控生产过程,并提供即时的优化建议。
3. 透明化管理:实现生产过程的透明化管理,提高管理效能,降低生产成本。
1. DCS系统架构基于DCS系统实现智慧工厂的设计方案应包含以下几个主要模块:a) 实时控制模块:用于控制生产设备的运行状态和参数,实现自动化生产。
b) 监测与采集模块:通过传感器、监控设备等实时采集生产过程中的各种数据,包括温度、压力、湿度等。
c) 数据存储和处理模块:将采集到的数据存储到数据库中,并利用机器学习算法对数据进行分析和处理。
d) 可视化界面模块:通过可视化的操作界面展示生产过程中的各项指标,方便操作人员了解生产状态和调整参数。
2. DCS系统功能a) 实时数据监测与分析:DCS系统可以实时监测生产过程中的各项数据,并对其进行分析和处理。
例如,通过监测温度、湿度等参数,及时发现异常情况并进行报警处理。
b) 自动化控制:DCS系统可以根据设定的参数,实现生产过程的自动化控制。
例如,根据产品的不同要求自动调整温度、压力等工艺参数。
c) 故障诊断与维护:DCS系统可以通过对设备运行数据的分析,实现故障的诊断和维护。
例如,通过分析设备的振动频率、温度等参数,判断设备是否存在故障,并提供相应的维修建议。
d) 优化分析与决策支持:DCS系统可以通过对生产数据的分析,提供相应的优化建议和决策支持。
例如,通过分析历史数据,优化生产计划,提高生产效率和产品质量。
e) 数据共享与协同:DCS系统可以实现生产数据的共享和协同,实现供应链管理的全面优化。
DCS的工程设计方案

DCS的工程设计方案1. 引言DCS是指分散式控制系统(Distributed Control System),是通过在工业生产过程中集中监控和控制各个子系统的一种自动化控制系统。
本文将介绍DCS的工程设计方案,包括硬件设备选型、系统架构设计、通信网络设计和软件编程等方面。
2. 硬件设备选型在DCS的工程设计中,硬件设备的选型至关重要。
首先,需要选择适合特定工业场景的控制器。
常见的DCS控制器包括可编程逻辑控制器(PLC)和分散式控制器(DCS)。
根据具体的需求,可以选择适合的控制器品牌和型号。
此外,还需要选择合适的输入输出模块,用于与各个子系统进行数据交互。
一般来说,需要考虑模拟输入输出、数字输入输出和通信接口模块等。
最后,为了保证系统的可靠性和稳定性,还需要选择合适的供电设备和机柜。
供电设备需要具备稳定的电源输出和过载保护功能,机柜需要具备良好的散热性能和防尘、防水功能。
3. 系统架构设计DCS的系统架构设计需要考虑到各个子系统的互联和协同工作。
通常,可以采用三层结构设计,包括野外层、中控层和管理层。
在野外层,主要涉及到与现场设备的连接和数据采集。
可以通过现场总线(如Profibus、Modbus等)连接各个设备,采集实时数据,并将其传输到中控层。
中控层是整个DCS的核心,主要负责数据处理和控制指令的下发。
通过选择适合的DCS控制器和输入输出模块,可以实现对子系统的实时监控和控制。
管理层是DCS的上位系统,主要用于数据存储和监控。
可以通过连接数据库和安装监控软件实现对整个DCS系统的远程监控和数据分析。
4. 通信网络设计通信网络是确保DCS各个子系统能够顺利工作的重要保障。
在设计通信网络时,需要考虑以下几个方面:•网络拓扑结构:可以采用星型、总线型、环型等不同的拓扑结构,根据具体场景选择合适的结构。
•网络协议:根据设备的通信协议选择合适的网络协议,如TCP/IP、Ethernet等。
•网络安全性:在设计网络时,需要考虑网络的安全性,采取相应的安全措施,如防火墙、VPN等。
DCS系统设计汇报2

LT403
Add:8
8CHAI FM148A
Add:9
8CHAO FM161D
Add:6
8CHAI FM148A
Add:11
16CHDI 6CH
Relay output
LT203
Add:5
8CHAI FM148A
Add:12
16CH
Relay output
FM138_ACC
计算机控制系统综合实践
--------DCS设计
系统软件结构
具体步骤
1 确定控制方案和配置系统的硬件与软件;
2 设定各I/O模块与控制器的类型与地址。 3 采用功能块图、梯形图、结构化文本,指令列表或 顺序功能图等多种方式进行工程控制组态;
4 完成用户流程图、趋势图、报表以及监控网页的组 态; 5 程序下装,连接并调试各监控界面; 6 上机运行,加信号,整定调试,试运行,运行。
DCS控制系统结构图
计算机 以太网
FM801 FM910 FM910
计算机
计算机
计算机
IP范围: 128.0.0.20~40
IP: 128.0.0.10
0 1 2 3 4 5 6 7 0 1 2 3 4 5 6 7 1 2 3 4 5 6 7 0 1 2 3 4 5 6 7 1 2 3 4 5 6 7 1 2 3 4 5 6 7
FM171
Add:4
8CHAI FM148A
Add:13
16CH
Relay output 32
16CH
Relay output
Add:7
8CHAI
Conmaker组态
主程序
子程序(1)液位-液位PID串级
dcs控制系统方案

DCS控制系统方案1. 引言DCS(分散式控制系统)是一种用于工业自动化的控制系统,它将工厂的控制设备、传感器和执行器连接在一起,通过分布式控制器和监视器来实现对工厂过程的控制和监控。
本文将介绍一个DCS控制系统方案,包括系统架构、硬件设备、软件平台和功能模块等内容。
2. 系统架构DCS控制系统采用分布式架构,由多个子系统组成。
每个子系统包含一个分布式控制器和若干I/O模块,用于实现对特定过程的控制和监测。
所有子系统通过网络连接在一起,与中央控制室的监视器进行通信。
下图展示了DCS控制系统的架构。
+-------------------+| || 中央控制室 || |+-------------------+|+-------------------+| || 子系统1 || |+-------------------+...+-------------------+| || 子系统n || |+-------------------+3. 硬件设备3.1 分布式控制器每个子系统都配备一个分布式控制器,它负责对本地过程进行控制和监测。
分布式控制器通常采用工业级计算机,具有高可靠性和实时性能。
它与本地的I/O模块进行通信,并通过网络与其他子系统和中央控制室连接。
3.2 I/O模块每个子系统都连接了若干I/O模块,用于采集传感器数据和控制执行器。
I/O 模块负责将模拟量和数字量信号转换成数字信号,供分布式控制器进行处理。
常见的I/O模块包括模拟输入模块、模拟输出模块、数字输入模块和数字输出模块。
3.3 其他设备除了分布式控制器和I/O模块,DCS控制系统还包括其他设备,例如传感器、执行器和通信设备等。
这些设备与分布式控制器和I/O模块一起工作,用于实现对工厂过程的控制和监测。
4. 软件平台DCS控制系统的软件平台是实现系统功能的关键。
软件平台通常由以下几个部分组成:4.1 系统监视器系统监视器是中央控制室的核心组件,负责接收和显示来自各个子系统的数据和状态信息。
dcs工程项目方案设计

dcs工程项目方案设计一、项目概况本项目是一座新建的数字化控制系统(DCS)工程项目,旨在实现对工厂生产线的自动化控制和监控。
该项目将覆盖工厂的工艺生产线,并通过DCS系统对生产过程进行监控、调控和管理,以提高生产效率、降低成本、提高产品质量,并达到智能化生产的目标。
项目位置:工厂生产车间项目范围:涵盖生产车间的工艺设备控制和监测项目预算:预计投资5000万元项目周期:预计工期12个月二、项目目标1. 实现工厂生产设备的自动化控制和监测,提高生产效率和质量。
2. 构建集中化的生产监控平台,实现对生产过程的实时监测和远程控制。
3. 实现生产数据的采集和分析,为生产过程的优化提供支持。
三、系统架构设计1. DCS系统硬件设计DCS系统将采用先进的控制器和I/O模块,以及可靠的通信网络设备,确保系统的稳定性和可靠性。
控制器:选用知名的PLC品牌,以保证系统的稳定性和可靠性。
I/O模块:选择适配工厂设备的数字量、模拟量输入输出模块。
通信网络设备:选择高速、可靠的以太网设备,以及现场总线设备,确保设备间的通讯畅通。
2. DCS系统软件设计DCS系统将采用先进的集成控制软件,实现对工艺设备的自动化控制以及生产过程的监测和管理。
控制软件:选择功能强大的DCS软件,支持多种工艺控制策略,满足不同工艺要求。
监控软件:配置实时监控界面,支持多种图形化展示方式,便于操作和管理人员查看生产情况。
数据采集与分析软件:配置数据采集和分析软件,从生产过程中采集数据,并进行分析,为生产过程的优化提供支持。
四、系统集成方案本项目将采用分散型DCS系统,将生产线上的各种设备通过现场总线与控制器连接,实现对设备的控制和监测。
同时,将配置集中化的监控系统,通过网络连接各个生产线,实现远程监控和管理。
1. 设备控制集成根据生产线的实际情况,对各种设备进行功能分解,并设计相应的控制策略,实现设备的智能化控制。
同时,配置相应的I/O模块,将设备的输入输出信号连接到控制器,实现对设备的远程控制。
DCS设计说明范文

DCS设计说明范文一、项目背景随着信息化时代的到来,自动化控制系统在工业生产中的应用越来越广泛。
随之而来的是,要求自动控制系统具备更高的可靠性、稳定性和灵活性。
为了满足企业对自动化控制系统的需求,我们设计了一套基于DCS (分散控制系统)的自动化控制系统。
该系统旨在提高生产效率、降低生产成本、提升产品质量。
二、系统架构本系统采用分层模块化设计,主要包括监控层、控制层和执行层。
监控层负责实时监视生产过程,控制层负责处理监控层反馈的数据,执行层负责执行具体的控制操作。
其中,监控层包括监控界面和数据库,控制层包括控制器和算法,执行层包括执行器和传感器。
监控层:监控界面采用人机界面设计,实时显示生产过程的各项参数和数据,帮助操作员快速了解生产状况。
数据库负责数据的存储和备份,在系统故障时提供数据恢复功能。
控制层:控制器根据监控界面反馈的数据,通过算法计算出相应的控制指令,传送给执行层。
算法采用PID算法和模糊控制算法相结合,以保证系统在各种情况下的稳定性和精准性。
执行层:执行器根据控制层发送的指令,执行具体的操作,如启动、停止、调整参数等。
传感器用于实时监测生产过程中的各项参数,反馈给控制层。
三、系统功能1.实时监控:监控层实时显示各项生产参数和数据,帮助操作员及时掌握生产状况。
2.远程控制:系统支持远程控制功能,操作员可通过互联网远程操控系统,提高操作灵活性。
3.报警处理:系统支持报警功能,当项参数超出设定范围时,系统会自动发出警报,并提供相应的处理建议。
4.数据存储与分析:系统能够将生产过程中的数据存储在数据库中,并提供数据分析功能,帮助企业管理层做出有效的决策。
5.自动调节:系统自带PID算法和模糊控制算法,能够根据实时监测的数据,自动调节参数,提高生产效率和产品质量。
四、系统优势1.稳定性高:系统采用分层模块化设计,各模块之间相互独立,故障不会影响整个系统的运行。
2.灵活性强:系统支持远程控制,操作员可以随时随地监控和操控生产过程。
cvdp中的dcs设计概念表的意思

cvdp中的dcs设计概念表的意思DCS设计概念表是指DCS(数字测控系统)中用于记录和说明系统
设计概念的表格。
DCS是一种应用于工业自动化的控制系统,它将中央控制器和分布式控制器相结合,用于监测和控制生产过程中的各种参
数和设备。
在DCS系统的设计过程中,为了明确系统的功能、性能和需求,
设计概念表用于详细描述系统设计的各个方面。
它通常包含以下信息:
1.功能描述:概括性地描述系统的主要功能和特点,例如过程监测、数据采集、报警处理等。
2.架构描述:说明系统的整体架构和模块组成,包括中央控制器、分布式控制器、I/O模块、通信网络等。
3.控制策略:描述系统所采用的控制策略和算法,例如PID控制、模型预测控制等。
4.通信协议:说明系统采用的通信协议,以确保各设备之间的数
据交换和通信的可靠性。
5.数据采集:描述系统对被控对象和传感器数据的采集方式和频率。
6.报警处理:说明系统对异常情况的报警处理方式和级别。
设计概念表的编制有助于确保设计人员对系统的功能和性能有清晰的认识,并提供给其他相关人员参考。
此外,设计概念表还可以作为系统设计报告和项目文档的一部分,方便后续的工程实施和运维工作。
- 1、下载文档前请自行甄别文档内容的完整性,平台不提供额外的编辑、内容补充、找答案等附加服务。
- 2、"仅部分预览"的文档,不可在线预览部分如存在完整性等问题,可反馈申请退款(可完整预览的文档不适用该条件!)。
- 3、如文档侵犯您的权益,请联系客服反馈,我们会尽快为您处理(人工客服工作时间:9:00-18:30)。
2
啤酒酿造生产主流程图
大米
该系统主要对糖化车间的三锅两槽 及其外围大米处理、称重、粉碎设备, 麦芽处理、称重、粉碎设备( 其中麦芽 粉碎设备从德国Steinecher公司引进, 称重采用电子定量散装秤) , 供水系统( 20℃水箱、78℃水箱、80℃水箱、 96℃水箱) ,冰水系统( 4℃水箱及相应 制冷设备) , CIP 洗涤罐( 预清洗罐、碱 液清洗罐、后清洗罐) 等实行控制, 采 用两级监控方案。
2
啤酒酿造糖化车间主流程图
2
糖化车间DCS控制系统结构图 控制系统结构图 糖化车间
系统有5台下位机, 采用英国欧陆公司 的T921( 单CPU) 。5台下位机通过LIN 网卡连接起来,通讯速率为1Mbps, 彼 此间可方便地交换数据。在PC 机上编 好的下位机程序通过S9565卡下载到 下位机, 通过S9565卡在上位机上可监 控下位机程序的运行, 也可实时在线修 改下位机数据。
系统有4台上位机, 采用的操作系统 为中文Window s NT 4.0, 4台上位机 通过Acton 网卡用NetBEUI 协议相 连, 运行的组态软件为T 3500( 针对 欧陆下位机的FIX 专用版软件) 。在 这4台机器中, 其中1台运行T 3500开 发版, 1台运T3500的运行版, 1台运 行T3500的客户版, 1台计算机做打 印服务器, 处理其它事务。
安全联锁控制: ESD是一种专门的仪表保护系统,具有很 高的可靠性和灵活性,当生产装置出现紧急 情况时,保护系统能在允许的时间内做出响 应,及时地发出保护联锁信号,对现场设备 进行安全保护。 在正常情况下,ESD系统是处于静态的, 不需要人为干预。作为安全保护系统,凌驾 于生产过程控制之上,实时在线监测装置的 安全性。只有当生产装置出现紧急情况时, 不需要经过DCS系统,而直接由ESD发出保 护联锁信号,对现场设备进行安全保护,避 免危险扩散造成巨大损失。
模拟量输入 70路 路 模拟量输出 16路 路 开关量输入 270路 路 开关量输出 250路 路
仪表方案: 4台控制柜(控制室)+3台气动柜(现场) +12台动力柜(动力室)
电源设计
电源: 4台西门子电源( 2台220V AC 输入, 20A 24V DC 输出, 2台380V AC 输入, 40A 24V DC 输出) 电源冗余: 控制室内还有一台3kVA、2h 在线式UPS, 对两台主控计算机、主控制柜、信号处理柜 供电, 在停电情况下, 保证温度、压力、料位 等信号的显示。
DCS系统在纯生啤酒生产工艺中的应用 系统在纯生啤酒生产工艺中的应用 ------欧陆 欧陆Network6000DCS
班级:测控801 班级:测控801 组别: 组别:第六组 时间: 时间:2011.6.2
主讲、答疑: 主讲、答疑:屈向利 搜集资料: 搜集资料:王豪、孔鹏飞 PPT制作:李慷 制作: 制作
contents
1 系统简介 工艺流程
2
3
控制原理及具体应用 系统应用的特点
4
1
产品信息
欧陆Network6000DCS 组成部分:
• • • • • 欧陆 T940X T940X策略引擎 2500过程接口单元 T3500监控站 T103控制站(欧陆老系统) T2550自治控制系统
1
系统特点
- 控制更加分散 -外来产品直接集成 -强有力的连续及顺控能力 -全功能的连续和顺序控制 -冗余CPU用于连续控制可无扰动 切换 • -可带电插拔CPU和I/O模件 • • • • •
• -高可用性的过程控制 • -分散控制单元每台最大I/O容量128 点 • -单元管理概念符合SP88批量控制模 型 • -ALIN控制网络提供对等及工作站通 讯 • -直接T640控制器集成 • -符合CE规范
2
啤酒生产工艺
1.工艺简介: 在啤酒厂糖化车间中, 生产啤酒的主要原料 麦芽、大米、酒花等, 通过一系列的机械加 工及工艺流程处理, 最终变成发酵车间生产 所需要的原麦汁。 2.主要设备: 三锅( 糊化锅、糖化锅、煮沸锅) 二槽( 过滤槽、旋涡沉淀槽) 体系结构
3
系统功能块及功能
三锅控制: (1)糊化锅的控制。将大米粉从大米粉仓输送入糊化 锅, 按给定的料水比通过糊化混水器输入定量定温的水, 按设定的糊化曲线, 通过蒸汽调节阀与开关阀控制糊化 锅温度, 完成糊化工作。 (2)糖化锅的控制。麦芽浆与糊化锅糊化好的料在糖 化锅混合并醪合, 按设定好的糖化曲线, 通过蒸汽调节 阀与开关阀控制糖化锅温度, 完成糖化工作, 要注意的 是糖化锅对温度控制的精度要求较高。 (3)煮沸锅的控制。贮存在麦汁贮罐里的麦汁, 通过 麦汁预热器( 96℃水→80℃或78℃水) , 进入煮沸锅。 煮沸锅在工作状态下有压力,其安全联锁控制非常重要。 在保证蒸发强度的前提下, 通过二次蒸汽回收将80℃ 水变成96℃水, 提高热能的利用率, 相应的控制还有加 糖控制, 加洒花控制, 取样控制等。
4
欧陆Network6000DCS系统 欧陆 系统
4
系统的控制特点及安全机制
强有力的连续及顺序控制能力 安全联锁控制。糖化车间的大部 份设备互有关联, 误操作会带来设 备损坏及人身伤亡的重大事故, 例 煮沸锅的锅顶排空大阀, 与煮沸锅 的出料泵、煮沸锅压力、煮沸锅 CIP 状态要有安全联锁控制, 防止 煮沸锅内出现真空或压力过高造 成煮沸锅的损坏, 可以说, 安全联 锁控制, 是糖化车间控制系统最重 要的工作之一。
上位机与下位机通过欧陆公司的LIN 网相连, 其中的两台上位机( 开发版与 运行版) 中安装有欧陆公司的LIN 网卡 S9565 运行T 3500客户版程序的上位计算机 通过多屏卡挂接了4台21寸大屏幕显 示器, 完整地显示了整个糖化车间的工 艺流程, 代替传统意义的模拟屏, 供操 作人员参考。
系统的规模:
3
系统功能块及功能
两槽控制: (1)过滤槽的控制。这部份控制比较复杂,从糖化
锅出来的料进入过滤槽, 经过自然沉淀,在过滤槽中形 成糟层, 通过调节变频调速器的转速及浊度计上的信 号控制决定麦汁是进入麦汁贮罐、弱麦汁罐或是回 流入过滤槽, 同时通过流量计控制洗糟水量。这部份 相应的控制还有出糟门、麦糟输送装置、麦糟筒仓 、耕刀升降的保护及挂脱钩、耕刀与排糟刀的旋转 等。 (2)旋涡沉淀槽控制。煮沸锅内的麦汁, 进入旋涡 沉淀槽后, 经过数小时的沉淀, 通过麦汁冷却器( 4℃ 水→78℃或80℃水) 并充氧后, 进入发酵车间。
Thank you!