第六章金属塑性成形的工艺理论基础.pptx
金属塑性成形工艺基础培训讲座PPT课件( 38页)

•
4、心中没有过分的贪求,自然苦就少。口里不说多余的话,自然祸就少。腹内的食物能减少,自然病就少。思绪中没有过分欲,自然忧就少。大悲是无泪的,同样大悟
无言。缘来尽量要惜,缘尽就放。人生本来就空,对人家笑笑,对自己笑笑,笑着看天下,看日出日落,花谢花开,岂不自在,哪里来的尘埃!
•
5、心情就像衣服,脏了就拿去洗洗,晒晒,阳光自然就会蔓延开来。阳光那么好,何必自寻烦恼,过好每一个当下,一万个美丽的未来抵不过一个温暖的现在。
32
变形速度的影响
一方面由于变形速度的增大, 回复和再结晶不能及时克服加工硬 化现象,金属则表现出塑性下降、 变形抗力增大,可锻性变坏。
另一方面,金属在变形过程中, 消耗于塑性变形的能量有一部分转 化为热能,使金属温度升高(称为 热效应现象)。变形速度越大,热 效应现象越明显,使金属的塑性提
高、变形抗力下降(图中a点以后),
• 再结晶:当温度进一步提高, 金属原子获得更多热能,则 开始以某些碎晶或杂质为核 心结晶成新的晶粒,加工硬 化全部消除,这一过程为 “再结晶”。
30.05.2019
28
(4) 冷变形及热变形
冷变形
变形温度低于回复温度时,金属在变 形过程中只有加工硬化而无回复与再结晶现 象,变形后的金属只具有加工硬化组织,这 种变形称为冷变形。
可锻性变好。
30.05.2019
33
应力状态的影响
挤压时为三向受压状态。 拉拔时为两向受压一向受拉的状态。 压应力的数量愈多,则其塑性愈好,变形抗力
增大;拉应力的数量愈多,则其塑性愈差。
30.05.2019
34
思考题
1.纤维组织是怎样形成的?它对金属的 力学性能有何影响?
2.试分析用棒料切削加工成形和用棒料 冷镦成形制造六角螺栓的力学性能有何 不同?
金属塑性成形课件

2023-11-06•金属塑性成形概述•金属塑性成形工艺•金属塑性成形设备•金属塑性成形技术的发展趋势•金属塑性成形过程中的缺陷与质量控制目•金属塑性成形实例分析录01金属塑性成形概述金属塑性成形是一种使金属材料发生塑性变形,以获得所需形状、尺寸和性能的加工方法。
金属塑性成形广泛应用于机械制造、航空航天、汽车、电子等领域,是一种重要的材料加工技术。
金属塑性成形的定义金属塑性成形可以制造出复杂形状的零件,并且能够获得较高的精度和表面质量。
与切削加工相比,金属塑性成形具有更高的材料利用率和更低的能耗。
金属塑性成形过程中材料的变形是均匀的,因此可以避免应力集中和裂纹等缺陷。
金属塑性成形的特点03金属塑性成形的基本原理包括应力状态、屈服准则、塑性流动规律等。
金属塑性成形的基本原理01金属塑性成形的原理是基于金属的塑性变形规律,即在外力作用下,金属材料会发生形状和尺寸的变化。
02在金属塑性成形过程中,材料的变形受到应力状态、变形温度、变形速度等因素的影响。
02金属塑性成形工艺自由锻工艺自由锻是利用冲击力或静压力使金属坯料变形,并施加外力将其锻造成所需形状和尺寸的锻造方法。
定义特点流程应用自由锻具有较大的灵活性,可以生产形状各异的锻件,但生产效率较低,适用于单件或小批量生产。
自由锻的流程包括坯料准备、加热、变形和锻后冷却。
自由锻主要用于大型锻件和难变形材料的加工,如轴、轮毂、法兰等。
模锻工艺模锻是利用模具使金属坯料变形,并施加外力将其锻造成所需形状和尺寸的锻造方法。
定义模锻具有较高的生产效率,且能获得较为精确的形状和尺寸,但模具制造成本较高。
特点模锻的流程包括坯料准备、加热、放入模具、变形、锻后冷却和修整。
流程模锻广泛应用于中小型锻件的生产,如齿轮、轴套、法兰等。
应用板料冲压工艺板料冲压是利用冲压机将金属板料变形,并施加外力将其冲制成所需形状和尺寸的加工方法。
定义板料冲压具有较高的生产效率,且能获得较为精确的形状和尺寸,但模具对材料的厚度和硬度有一定要求。
金属塑性成形PPT课件

(Mg、Zn、Cd、α-Ti)
3.2塑性成 形机理
滑移
3 金属塑性 成形
滑移带 500倍
26
3.2塑性成 形机理 滑移
3 金属塑性 成形
27
3.2塑性成 形机理 滑
移
3 金属塑性 成形
28
3.2塑性成 形机理 滑移
3 金属塑性 成形
辊锻,楔横轧, 辗环,辊弯
7
3.1塑性成 形概述
塑性成形类型
3 金属塑性 成形
8
3.1塑性成 形概述
3 金属塑性 成形
体积成形
体积成形主要是指那些利用锻压设备和工、模具 ,对金属坯料(块料)进行体积重新分配的塑性 变形,得到所需形状、尺寸及性能的制件。
主要包括锻造(Forging)和挤压(Extrusion )两大类。
日 常 用 品
3
汽 车 覆 盖 件
飞
冲压成形产品示例—— 高科技产品
机 蒙 皮
4
5
6
3.1塑性成 形概述
3 金属塑性 成形
锻压3塑(性Met成al 形for分gin类g and stamping)
1.体积成形 (Bulk Metal Forming):
1.1 锻造 (Forging)
1.1.1自由锻造 1.1.2模锻
用伸长率δ、断面收缩率ψ表示:
δ= (L1-L0)/ L0 ×100% ψ=( S0-S1)/S0×100%
22
3.2塑性成
3 金属塑性
形机理
成形
2.金属塑性变形的实质
金 体—属——原—子显微组织——晶 典型晶格结构:
《塑性成形工艺基础》课件

模具的构成
模具由上模、下模和导向部件等组成,用于实现金属材料的塑性成形。
模具的工艺要求
模具设计需要考虑材料选择、温度控制、表面处理等多个方面的要求。
模具设计的方法
模具设计需要考虑产品形状、材料流动和成型工艺等因素,采用综合方法进行设计。
塑性成形加工工艺
塑性成形加工的流程 塑性成形加工的工艺参数与选择 塑性成形加工的质量控制
应用范围
塑性成形工艺广泛应用于汽车、航空航天、家电等领域,是现代工业的重要组成部分。
塑性变形的基本原理
1 金属的结构和性质
金属材料由多个晶格组 成,塑性变形是晶格滑 移和晶格形变的结果。
2 冷变形与热变形
冷变形在室温下进行, 热变形在高温下进行, 两者具有不同的变形特 点。
3 塑性变形的分类
塑性变形可分为压力加 工、拉伸加工、弯曲加 工和精密成型等多种类 型。
《塑性成形工艺基础》 PPT课件
本课程将介绍塑性成形工艺的基本原理、过程和模具设计,以及该工艺的发 展趋势。让我们一起探索这个令人着迷的领域!
背景介绍
塑性成形工艺的定义
塑性成形是通过施加压力,使金属材料在保持连续性的情况下发生塑性变形的一种制造工艺。
发展历程
塑性成形工艺自古已有,经历了手工操作、机械压力成形到现代数控技术的发展。
塑性成形的基本过程
1
拉伸加工
2
通过拉伸使金属材料变薄或变长,常
见的工艺有拉延、拉具的精细控制实现复杂零件的 成形,如注塑、挤压等。
压力加工
通过施加压力使金属在模具中变形, 包括冲压、锻造等工艺。
弯曲加工
通过施加力使金属材料弯曲或折弯, 常见的工艺有折弯、卷弯等。
塑性成形模具设计
第六章金属塑性成形工艺理论基础

目的:掌握金属塑性成形的基本原 理及影响塑性变形的因素。
要求掌握塑性成形的基本工艺、基 本变形理论;
熟悉回复与再结晶、冷变形与热变 形、纤维组织、最小阻力定律、体积 不变假设、锻造比、锻造性等概念;
了解影响塑性变形的因素。 重点:冷变形、热变形、纤维 组织利用原则、锻造性的概念。 难点:金属的回复与再结晶。
金属塑性成形(也称压力加工): 在外力作用下,金属产生了塑性变 形,以此获得具有一定形状、尺寸 和机械性能的原材料、毛坯或零件。
外力:冲击力——锤类设备 压 力——轧机、压力机
§6-1 金属塑性成形的基本工艺 1.轧制—-钢板、型材、无缝管材。
2.挤压
应用:低碳钢、非铁金属及其合金。
3.拉拔
要求横向力学性能时: Y锻=2~2.5。 要求纵向力学性能时:Y锻适当增加。 由Y锻可得坯料的尺寸:
如:拔长时,S坯料=Y拔×S锻件
式中,S锻件为锻件的最大截面积;
L钢坯
V坯料 F钢坯
§6-4 影响塑性变形的因素
金属的可锻性:衡量材料在经受 压力加工时获得优质零件难易程 度的一个工艺性能。 可锻性好适合于压力加工成形; 可锻性差不宜于选用压力加工。
§6-3 塑性变形理论及假设
一、最小阻力定律
定义:受外力作用,金属发生
塑性变形时,如果金属颗粒在几 个方向上都可移动,那么金属颗 粒就沿着阻力最小的方向移动。
利用此定律,调整某个方向流 动阻力,改变金属在某些方向的 流动量→成形合理。
最小阻 力定律示 意图。
在镦粗中, 此定律也称 最小周边法 则。
但温度过高→过热、过烧、脱碳 和严重氧化等缺陷→锻件报废。
应严格控制锻造温度——始锻温 度和终锻温度间的温度范围(以 合金状态图为依据)。
《金属塑性成形方法》课件
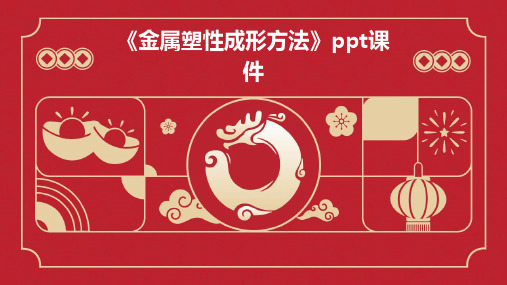
目录
CONTENTS
• 金属塑性成形方法简介 • 金属塑性成形的基本原理 • 金属塑性成形的主要方法 • 金属塑性成形的质量控制 • 金属塑性成形技术的发展趋势
01 金属塑性成形方法简介
CHAPTER
金属塑性成形的基本概念
金属塑性成形是一种通过施加外 力使金属材料发生塑性变形,从 而获得所需形状和性能的加工方
大型金属件和复杂形状的金属件制造,如轴、齿轮、连杆等。
模型锻造
要点一
总结词
通过将金属坯料放置在模具中,在高温和高压下使其发生 塑性变形,从而获得所需形状和尺寸的金属件。
要点二
详细描述
模型锻造是一种常见的金属塑性成形方法,通过将金属坯 料放置在模具中,在高温和高压下使其发生塑性变形,从 而获得所需形状和尺寸的金属件。模型锻造过程中,金属 坯料在高温和高压下发生变形,内部晶粒结构发生变化, 从而提高了金属的力学性能。模型锻造适用于中小型金属 件制造,如齿轮、轴承、气瓶等。
过程稳定可控。
在线检测
采用先进的在线检测技术,对成形 过程中的产品进行实时检测,及时 发现并处理问题。
成品检测
对成形后的产品进行全面的检测, 包括尺寸、外观、性能等,确保产 品质量符合要求。
05 金属塑性成形技术的发展趋势
CHAPTER
高性能金属材料的开发与应用
高强度钢
通过合金化、热处理等手段提高 钢材的强度和韧性,用于制造轻
流动法则与加工硬化
流动法则是描述金属在塑性成形过程中应力的分布规律。加工硬化是指 在塑性成形过程中,随着变形的进行,材料的强度和硬度逐渐提高的现 象。
金属塑性变形的工艺基础
塑性成形的基本方法
金属塑性变形理论.pptx

• 实现最佳的加工条件
研究创造最佳的工艺条件和使工艺内容定量化以及把能实现这种条件的新技术用于新加工机械设计和老 设备的挖潜改造上,并进行最优控制。
2024/10/8
43
第454页/共64页
课下练习
1、什么是金属的塑性?什么是塑性加工?塑性加工有何特点? 2、试述塑性加工的一般分类。
2024/10/8
• 做好课堂笔记,本课程中将有部分补充内容, 要求大家记笔记。
• 要求上课前预习,本课程内容较难,且内容 多,信息量较大,要求大家自觉预习。
• 遵守课堂纪律,本课程不允许迟到早退。
3
第54页/共64页
本课程主要内容
• 金属微观变形机理与宏观性能 • 金属变形过程的力学分析 • 变形体力学的求解方法
将计算机技术、信息技术、先进控制技术应用 于传统加工技术
➢ 提高生产效率
高速、全自动、无人化
➢ 扩大产品范围 ➢ 形状、尺寸的精确控制
2024/10/8
46
第487页/共64页
2024/10/8
铝合金镜面板
超小型精密挤压型材
47
第498页/共64页
发展先进成形加工技术
➢ 目的 ➢ 高附加值材料、难加工材料的加工 ➢ 实现组织性能的精确控制
44
第465页/共64页
补充材料
材料加工技术的主要发展方向
(1)高效化、高精度化 (2)发展先进成形加工技术 (3)材料设计、制备与成形加工一体化 (4)开发新型成形加工技术,发展新材料 (5)计算机模拟与过程仿真技术 (6)智能制备与加工技术
2024/10/8
45
第476页/共64页
传统技术的高效化与高精度化 ➢ 高新技术改造传统技术
6章 金属的塑性成型工艺理论基础

由于镦粗时,金属流动的距离越短,摩擦阻力越小。 端面上任何一点到边缘的距离最近处是垂直距离,所以这 个金属质点必然沿着垂直边缘的方向流动,因此方形截面 中心部分金属大多流向垂直于方形的四边,而对角线方向 很少有金属流向那里,随着变形程度的增加,断面的周边 将趋向于椭圆,而椭圆将进一步变为圆。此后,各质点将 沿着半径方向 流动,因为相 同面积的任何 形状,圆形的 周长最短,因 变形小时 而最小阻力定 律在镦粗中也 变形大时 称为最小周边 法则。
第二节 金属的塑性变形
一、金属塑性变形后的组织和性能
1.晶粒沿变形方向 拉长;2.晶格与晶 粒发生扭曲;3.晶 粒间产生碎晶 回复温度:T回= (0.25¬ 0.3)T熔 消除晶格扭曲和 部分加工硬化 再结晶温度
T再=0.4T熔
二、金属塑性变形的类型
由于金属在不同温度下变形后的组织和性能不同,通 常以再结晶温度为界,金属的塑性变形分为冷变形和热变 形两种。
2. 变形速度的影响
3. 应力状态的影响
二、热变形
变形温度在再结晶温度(T再=0.4T熔)以上时,变形
产生的加工硬化被随即发生的再结晶所抵消,变形后金属
具有再结晶的等轴晶粒组织,而无任何加工硬化痕迹,这
种变形称为热变形。 锻造和热挤热轧都属于热变形。
三、
纤维组织的利用原则
金属压力加工最原始的坯料是钢锭,其内部组织有许 多微小缺陷,通过压力加工能消除缺陷,经过塑性变形及 再结晶,从而改变了粗大的铸态组织,获得细小的再结晶 组织,力学性能有很大提高。
第三节 塑性变形理论及假设
一、最小阻力定律
金属塑性成形的实质是金属的塑性流动。塑性成型时影响金属 流动的因素十分复杂,要定量描述线性流动规律非常困难,但可以 应用最小阻力定律定性地描述金属质点的流动方向。金属受外力作 用发生塑性变形时,如果金属质点在几个方向上都可移动,那么金 属质点就沿着阻力最小的方向移动,这就叫最小阻力定律。这实际 上是力学的普遍原理。根据这一原理可以通过调整某个方向的流动 阻力,来改变金属在某些方向的流动量,使得成型更为合理。 运用最小阻力定律可以解释为什么用平头锤镦粗时,金属坯料 的截面形状随着坯料的变形都逐渐接近于圆形。
材料成型基础之常用金属塑性成形方法模版(PPT153张)
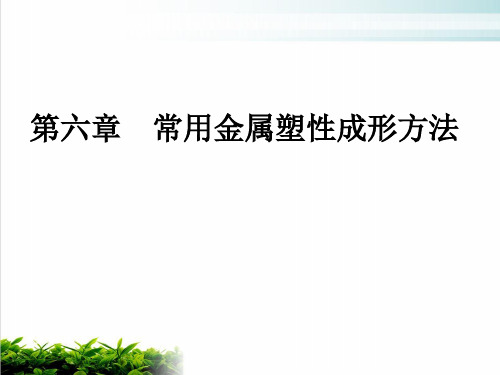
可采用镦粗、冲孔、拔长、整修
弯曲类锻件
可采用拔长、弯曲
自由锻造
曲拐轴类锻件
可采用拔长、分段、错移、整修
其他复杂锻件
可采用拔长、分段、镦粗、冲孔、整修
自由锻造
辅助工序:压肩、倒棱、压钳口等。
精整工序:整形、清出表面氧化皮等。
自由锻造
②锻造温度范围及加热冷却范围 常用金属材料的锻造温度范围
自由锻造
⑷自由锻典型过程举例
—轴类、盘类、环类、筒类、弯曲类等 ①轴类件自由锻工序
自由锻造
锻件名称:齿轮轴 坯料质量:2.8kg 坯料规格:ф90x59mm 锻件材料:40Cr 锻造设备:150kg空气锤
火次
温度(℃)
锻件图: 操作说明
简图
镦粗
拔长、打圆
1
1200~800
压肩
拔长、打圆
自由锻造
自由锻造
③当锻件的横截面有急剧变化或形状较复杂时,可将 其设计成几个简单件构成的组合件,用焊接或机械连 接方法连成整体件。
自由锻造
复杂件结构 成形性差的结构 成形性好的结构
胎模锻造
概念:在自由锻造设备上使用不固定在设备上的各种模具 称为胎模的单膛模具,将已加热的坯料用自由锻方法预锻 成接近锻件形状,然后用胎模终锻成形的锻造方法。
自由锻造
锻后锻件的冷却:
锻件仍有较高的温度,冷却时由于 表面冷却快,内部冷的慢,锻件表里收 缩不一,可能使一些塑性较低的或大型 复杂锻件产生变形或开裂等缺陷。
自由锻造
锻件冷却方式常有下列3种:
1)直接在空气中冷却(空冷),此种多用于碳含 量小于0.5%的碳钢和碳含量小于0.3%的低合金钢 中小型锻件。 2)在炉灰或干砂中缓冷 对用于中碳钢、高碳钢和 大多数低合金钢中的中型锻件。 3)随炉缓冷 锻后随即将锻件放入500到700摄氏度 的炉中随炉缓冷,用于中碳钢和低合金钢的大型锻 件以及高合金钢的重要锻件。
金属塑性成形课件

要点二
高强度材料加工
挤压和拉拔适用于高强度材料的加工,如高强度钢、钛合金等,可以获得高精度、高质量的制品。
模具成本高
挤压和拉拔使用的模具制造较为复杂,成本较高,同时生产效率较低。
要点三
连续变形加工
锻造和轧制是两种连续变形加工的方法,锻造是通过冲击、静压等手段将金属坯料变形,而轧制则是将金属坯料放入轧辊中,通过旋转轧辊使金属变形并获得所需形状和尺寸的制品。
确定合理的变形程度,以充分利用材料的塑性潜力,同时避免材料开裂和变形过大。
合理控制应变速率,以实现材料的均匀变形和避免局部过快变形。
03
工艺参数的选择和控制
02
01
成形过程的模拟和仿真
模拟软件选用
选择适合的数值模拟软件,如有限元法或有限差分法等,对成形过程进行仿真和分析。
模拟精度控制
根据实际需要,提高模拟精度,以更准确地预测成形过程中的各种问题和缺陷。
成形方案优化
通过模拟和仿真,优化成形方案,提高生产效率和产品质量。
01
03
02
根据产品的特点和成形工艺的要求,选择适合的检测方法,如力学性能测试、金相分析、X射线检测等。
产品质量的检测和分析
检测方法选择
对检测结果进行误差分析,找出影响检测结果的主要因素,提出相应的控制措施。
误差分析和控制
根据产品质量检测结果,对产品结构进行优化,提高产品质量和使用性能。
产品结构优化
设备升级改造
针对成形过程中的设备和工艺装备进行升级改造,提高设备的自动化程度和生产效率。
工艺流程优化
通过对成形过程的各阶段进行全面分析,找出瓶颈和不足之处,提出相应的优化措施。
节能减排措施
采取节能减排措施,降低成形过程中的能源消耗和环境污染,实现绿色生产。
金属的塑性加工教学PPT
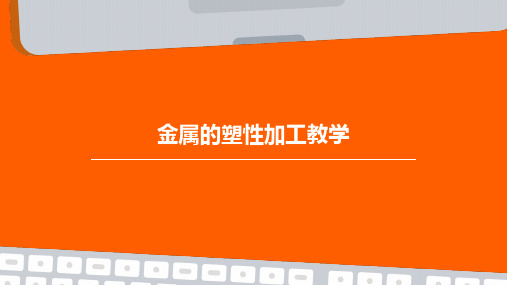
在无模具或少模具情况下,对坯料施加外力,使其产生塑性变形,获得所需形状和性能的锻件。
自由锻
在模具腔内对坯料施加压力,使其产生塑性变形,获得所需形状和性能的锻件。
模锻
通过旋转轧辊对金属坯料施加压力,使其产生塑性变形,获得所需形状和性能的轧制产品。
轧制
通过挤压模具对金属坯料施加压力,使其产生塑性变形,获得所需形状和性能的挤压产品。
高强度材料
精密成形技术如激光成形和等离子喷涂等,在金属塑性加工中得到广泛应用,提高了加工精度和表面质量。
精密成形技术
数值模拟技术用于预测金属塑性加工过程中的变形行为、流动规律和工艺参数优化,有助于提高产品质量和降低成本。
数值模拟与优化
新材料与新技术的发展
随着智能化和自动化技术的不断发展,金属塑性加工将更加高效、精确和可控,实现自动化生产线和智能制造。
采取措施确保金属各部位受热均匀,以减小变形不均匀和开裂的风险。
加热均匀性
加热与温度控制
塑性变形过程
模具设计
根据产品形状和尺寸要求设计合理的模具结构。
变形方式选择
根据金属特性和产品需求选择合适的塑性变形方式,如轧制、锻造、挤压等。
变形程度控制
在保证产品质量的前提下,合理控制变形程度,以提高生产效率和降低能耗。
总结词
拉拔技术主要用于生产各种细线、丝材等制品,如钢丝、铁丝等。在拉拔过程中,金属坯料通过模具孔逐渐被拉长和变细,同时发生塑性变形。
详细描述
根据拉拔时金属坯料温度的不同,拉拔可分为热拉拔和冷拉拔两种。
总结词
热拉拔是将金属坯料加热至高温后进行拉拔,具有加工效率高、材料利用率高等优点,但产品精度相对较低。冷拉拔则是在常温下进行拉拔,产品精度高、表面质量好,但加工难度较大。
第六章金属塑性成形工艺理论基础

3)冲压件尺寸精度高,质量稳定,互换性好, 一般不需机械加工即可作零件使用。 4)冲压生产操作简单,生产率高,便于实现机 械化和自动化。
5)可以冲压形状复杂的零件,废料少。
6)冲压模具结构复杂,精度要求高,制造费用 高,只适用于大批量生产。
坯料在锻造过程中,除与上下抵铁或其它辅 助工具接触的部分表面外,都是自由表面,变形 不受限制,锻件的形状和尺寸靠锻工的技术来保 证,所用设备与工具通用性强。
自由锻主要用于单件、小批生产,也是生产 大型锻件的唯一方法。
1) 自由锻设备
空气锤 它由电动机直接驱动,打击速度快,锤击能量小,适
用于小型锻件;65~750Kg
挤压成形是使坯料在外力作用下,使模具内的金属坯 料产生定向塑性变形,并通过模具上的孔型,而获得 具有一定形状和尺寸的零件的加工方法。
图6-3 挤压
挤压的优点:
1)可提高成形零件的尺寸精度,并减小表面粗糙 度。 2)具有较高的生产率,并可提高材料的利用率。 3)提高零件的力学性能。 4)挤压可生产形状复杂的管材、型材及零件。
3)精整工序:修整锻件的最后尺寸和形状,消除表面的不 平和歪扭,使锻件达到图纸要求的工序。如修整鼓形、平 整端面、校直弯曲。
3)自由锻的特点
优点:
1)自由锻使用工具简单,不需要造价昂贵的模具;
2)可锻造各种重量的锻件,对大型锻件,它是唯一方法
3)由于自由锻的每次锻击坯料只产生局部变形,变形金属 的流动阻力也小,故同重量的锻件,自由锻比模锻所需的 设备吨位小。
实例:
当采用棒料直接经切削加工制造螺钉时,螺钉头部与 杆部的纤维被切断,不能连贯起来,受力时产生的切应力 顺着纤维方向,故螺钉的承载能力较弱(如图示 )。
精选第六章金属塑性成形的工艺理论基础
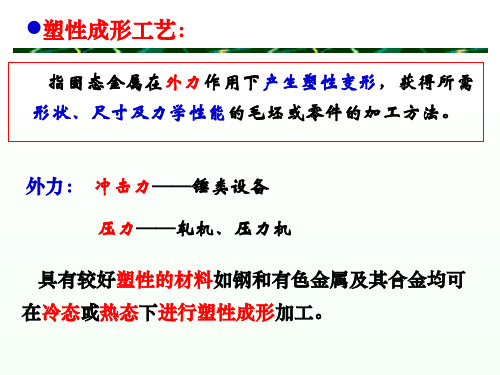
6. 板料冲压
板料冲压是利用装在冲床上的冲模对金属板料加 压,使之产生变形或分离,从而获得零件或毛坯的 加工方法。
板料冲压又称薄板冲压或冷冲压。
冲压工艺广泛应用于: 汽车、飞机、农业机械、 仪表电器、轻工和日用 品等工业部门。
① 使纤维分布与零件的轮廓相符合而不被切断; ②使零件所受的最大拉应力与纤维方向一致,最大切
应力与纤维方向垂直。
实例:
① 当采用棒料直接经切削加工制造螺钉时,螺钉头部与杆部 的纤维被切断,不能连贯起来,受力时产生的切应力顺着 纤维方向,故螺钉的承载能力较弱(如图示a)。
② 当采用同样棒料
经局部镦粗方法制造 螺钉时(如图示b),纤 维不被切断且连贯性 好,纤维方向也较为 有利,故螺钉质量较 好。
拉拔时为两向受压一向受拉的状态:拉应力使金属原子间距增
大,尤其当金属的内部存在气孔、微裂纹等缺陷时,在拉应力作用下,缺 陷处易产生应力集中,使裂纹扩展,甚至达到破坏报废的程度。
图6-13 挤压时金属应力状态
图6-14 拉拔时金属应力状态
压应力的数量愈多,则其塑性愈好,变形抗力增大; 拉应力的数量愈多,则其塑性愈差,变形抗力比挤压
的变形抗力小。 故必须综合考虑塑性和变形抗力。
对塑性较低的金属,应尽量在三向压应力下变形,以免产生裂纹。 对塑性较好的金属,变形时出现拉应力是有利的,可以减少变形能
单件、小批生产,也是生产大型锻件的唯一方法。
5. 模锻
模锻是将加热好的坯料放在锻模模膛内,在锻压力 的作用下迫使坯料变形而获得 锻件的一种加工方法。
坯料变形时,金属的流动 受到模膛的限制和引导,从而 获得与模膛形状一致的锻件。
塑性成形工艺基础ppt课件

组织;
ψ
σb
δ
A
A+F
A+L
E
A+Fe3CII
400
温度 °C
P+F
P+Fe3CII
26
锻造温度范围
始锻温度和终锻温度间的温度范围
始锻温度过高,容易产生氧化、脱碳、过热、
过烧等缺陷
(自由锻造录像)
过热:晶粒过分粗大
过烧:晶界氧化或熔化
27
碳钢的锻造温度范围:
破碎并分散碳化物和非金属夹杂物的分布;
锻合内部孔隙和缩松
强度和抗疲劳性能得以提高,特别是塑性、韧性提 高较大。
17
变形程度的表示方法
• 锻造比:拔长时,S前/S后; 镦粗时:H前/H后
• 相对弯曲半径 • 拉深系数 • 翻边系数
18
(2)纤维组织的影响
在塑性变形过程中,晶粒和晶间杂质都沿着变
形最大方向伸长;再结晶后,晶ຫໍສະໝຸດ 恢复成等轴晶,而12% 30%
ZG45与轧制45的性能比较
580 610
320 360
ZG45 轧制45
性能
12 16
1
2
3
11
塑性成形工艺特点
(2)材料利用率高;
仅依靠形状变化和体积转移来实现。
(3)生产效率高;
生产自动化、机械化
(4)尺寸精度高。
少、无切削加工,向近净成形发展
12
塑性成形工艺不足
产品的形状(特别是内腔)不能太复杂。
1.塑性成形工艺方法及分类
塑性成形
一次塑性加工
二次塑性加工
轧制 挤压 拉拔 自由锻造 模型锻造 冲压
3
二次塑性加工
- 1、下载文档前请自行甄别文档内容的完整性,平台不提供额外的编辑、内容补充、找答案等附加服务。
- 2、"仅部分预览"的文档,不可在线预览部分如存在完整性等问题,可反馈申请退款(可完整预览的文档不适用该条件!)。
- 3、如文档侵犯您的权益,请联系客服反馈,我们会尽快为您处理(人工客服工作时间:9:00-18:30)。
第六章 金属塑性成形的工艺理论基础
第一节 金属塑性成形的基本工艺 第二节 金属的塑性变形 第三节 塑性变形理论及其假设 第四节 影响塑性变形的因素
第一节 金属塑性成形的基本工艺
自由锻
锻压的基本方 式
模锻 板料冲压 轧制
拉拔
挤压
1.轧制成形
轧制也叫压延,是金属坯料通过一对旋转轧辊之间的间隙而 使坯料受挤压产生横截面减少、长度增加的塑性变形过程。
1、冷变形
➢ 变形温度低于再结晶温度时,金属在变形过程中只有加工硬 化而无回复与再结晶现象,变形后的金属只具有加工硬化组 织,这种变形称为冷变形。
特点:产品表面品质好、尺寸精度高、力学性能好,一般不
需再切削加工。
生产中常用它来提高产品的性能。
2、热变形
➢ 变形温度高于再结晶温度时,变形产生的加工硬化被随即发 生的再结晶所抵消,变形后金属具有细而均匀的再结晶等轴 晶粒组织,而无任何加工硬化痕迹,这种变形称为热变形。
再结晶时的温度称为再结晶温度T再 = (0.35~0.4)T熔(K)
再结晶退火:为了消除加工生产中加工硬化给金属继续进行塑性 变形带来的困难,生产中以再结晶以上的温度加热已加工硬化的 金属,使其发生再结晶而再次获得良好的塑性的操作工艺。
二、金属塑性变形的类型
金属在不同温度下变形对其组织和性能的影响不同,因 此金属的塑性变形分为冷变形和热变形两种。
6)冲压模具结构复杂,精度要求高,制造费用高,只适用于 大批量生产。
第二节 金属的塑性变形
一、金属塑性变形后的组织和性能
金属受外力作用后,先产生弹性变形,当外力超出其屈服 强度后,开始产生塑性变形; 塑性变形过程中随着弹性变形的存在; 当外力去除后,弹性变形将恢复,该现象称为“恢复”。
金属在常温下经塑性变形后,其内部组织变化如下:
模锻广泛应用于: 国防工业和机械制造业,按质量计算模锻件在飞 机上占85%,坦克占70%,汽车占80%,机车占 60%。
6. 板料冲压
板料冲压是利用装在冲床上的冲模对金属板料加 压,使之产生变形或分离,从而获得零件或毛坯的 加工方法。
板料冲压又称薄板冲压或冷冲压。
冲压工艺广泛应用于: 汽车、飞机、农业机械、 仪表电器、轻工和日用 品等工业部门。
图6-8
1)组织变化的特征:
①晶粒沿变形最大方向伸长; ②晶格与晶粒均发生畸变,产 生内应力; ③晶粒间产生碎晶。
2)性能变化的特征:
加工硬化: 随着变形程度的增加,其强度和硬度不断提高, 塑性和韧性不断下降。
有利:强化金属材料 不利:进一步的塑性变形带来困难
加工硬化是一种不稳定的现象,具有自发回复到稳定 状态的倾向,在室温下不易实现。
回复:当温度升高,原子获得热能其热运动加剧,使原子排列 回复到正常状态,从而消除晶格扭曲,并部分消除加工硬化。
回复时的温度称为回复温度T回 = (0.25~0.3)T熔(K)
再结晶:当温度继续升高到T熔的0.4倍,金属原子获得更多的 热能,开始以碎晶或杂质为核心结晶成为细小而均匀的再结晶 新晶粒,从而消除全部加工硬化。
它是生产型材、板材和管材的主要方法。生产效率高、 产品质量好、成本低、节约金属。
图6-1 轧制
2. 挤压成形
挤压成形是使坯料在外力作用下,使模具内的金属坯料产 生定向塑性变形,并通过模具上的孔型,而获得具有一定 形状和尺寸的零件的加工方法。
图6-3 挤压
3. 拉拔成形
拉拔是使金属坯料通过一定形状的模孔,使其横截面 减小、长度增加的加工方法,如图6-5所示。产品形状尺寸 精确、表面质量好、机械强度高,常用于拔制金属丝、细管 材和异型材等。
➢ 特点: ①可以用较小的功产生较大变形,可加工出形状复杂、尺寸
较大的塑件;
②再结晶组织力学性能较高。 ③金属表面易形成氧化皮,产品尺寸精度和表面品质较差,
劳动条件较差,生产率较低。
➢ 金属压力加工生产多采用热变形来进行。
三、纤维组织的利用原则
金属压力加工生产采用的最初坯料是铸锭,其内部组织 很不均匀,晶粒较粗大,并存在气孔、缩松、非金属夹杂物 等缺陷。
板料冲压的特点:
1)在常温下加工,金属板料必须具有足够的塑性和较低的变 形抗力。
2)金属板料经冷变形强化,获得一定的几何形状后,结构轻 巧,强度和刚度较高。
3)冲压件尺寸精度高,质量稳定,互换性好,一般不需机械 加工即可作零件使用。
4)冲压生产操作简单,生产率高,便于实现机械化和自动化。
5)可以冲压形状复杂的零件,废料少。
➢ 铸锭加热后经过压力加工,由于金 属经过塑性变形及再结晶:
第二篇 金属的塑性成形工艺
塑性成形工艺:
指固态金属在外力作用下产生塑性变形,获得所需 形状、尺寸及力学性能的毛坯或零件的加工方法。
外力: 冲击力——锤类设备 压力——轧机、压力机
具有较好塑性的材料如钢和有色金属及其合金均可 在冷态或热态下进行塑性成形加工。
第六章 金属塑性成形的工艺理论基础 第七章 锻压成形工艺 第八章 板料的冲压成型工艺 第九章 金属的其他成形工艺
2)锻件内部的锻造流线比较完整,从而提高了零件 的力学性能和使用寿命。
3)锻件表面光洁,尺寸精度高,节约材料和切削加 工工时;
4)生产率较高; 5)操作简单,易于实现机械化; 6)生产批量越大成本越低。
模锻的缺点:
1)模锻是整体成形,摩擦阻力大,故模锻所需设 备吨位大,设备费用高;
2)锻模加工பைடு நூலகம்艺复杂,制造周期长,费用高。故 只适用于中小型锻件的成批或大批生产。
图6-5 拉拔
4. 自由锻
自由锻指将金属坯料放在锻造设备的上下砥铁之间,施 加冲击力或压力,使之产生自由变形而获得所需形状的成形方 法。
坯料在锻造过程中,除与上下砥铁 或其它辅助工具接触的部分表面外, 都是自由表面,变形不受限制,锻件 的形状和尺寸靠锻工的技术来保证, 所用设备与工具通用性强。
自由锻主要用于:
单件、小批生产,也是生产大型锻件的唯一方法。
5. 模锻
模锻是将加热好的坯料放在锻模模膛内,在锻压力 的作用下迫使坯料变形而获得 锻件的一种加工方法。
坯料变形时,金属的流动 受到模膛的限制和引导,从而 获得与模膛形状一致的锻件。
与自由锻相比,模锻的优点是:
1)由于有模膛引导金属的流动,锻件的形状可以比 较复杂;