切削油配方和性能对比
水溶性切削油的质量及性能指标分析

深圳多维贸易有限公司-水溶性切削油又分为乳化油、合成切削液、全合成切削液、半合成切削液、多功能切削液等这之类的细分。
那么乳化油就是由切削油和乳化剂等何种添加剂组合而成,需要加水使用,兑水比例一般为1:15--1:30,该乳油具有优良的润滑性和良好的排泄冷却效果,适用于黑色金属的磨,车,钻,锯等工序切削加工。
Apt MW 302乳化切削油密度是0.85,黏度可达到68。
切削油分为油型和水型两种,适用于铸铁,合金钢,碳钢,不锈钢,高镍钢,耐热钢,模具钢等金属制品的切削加工,高速切削及重负荷切削加工。
包括车,铣,镗,高速攻丝,钻孔,铰牙,拉削,滚齿等多种切削加工。
因此切削油必须兼具冷却,润滑,清洗和防锈四个作用。
MW-301是一种优良的水溶性乳化切削油,亦称太古油或枧油,兑水后乳化液呈乳白色的防锈乳化油。
防锈乳化油有极佳的润滑性和防锈性,防锈期长,可用于薄片的冲压,拉伸。
具有良好的清洗、冷却、润滑、防锈性能和加工末硝沉降分离功能,渗透、扩散性强,能有效提高工件加工质量,延长刀具使用寿命,降低加工成本。
产品使用安全,对人体无刺激、无伤害,对工件、机床无腐蚀。
可长期循环使用,无异味,有效使用时间长,高温不变质、不发臭。
产品使用:1、乳化切削油换液前彻底清洗水箱管道等与乳化液接触部位。
2、乳化切削油使用浓度3—10%水溶液,凡对润滑或光洁度要求高的加工过程,取上限浓度或更高浓度,使用过程中定期补加原液和水。
3、乳化切削油室内存放,密封保存,严禁混入水和杂质。
以下附上表格各种参数:种类表面张力稳化稳定度水/硬水不挥发成分PH 氯总硫泡沫试验耐腐蚀性W1-1号- 浅黄色油层2.5以下90以上8.5-10.5 - 5以下1以下没有变色(钢片)W2-1号- 浅黄色油层2.5以下90以上8.5-10.5 1-15 5以下1以下没有变色(钢片)W3-1号- 浅黄色油层2.5以下90以上8.0-10.5 1-15 5以下1以下没有变色铝及铜片W1-1号 4.0×10¯²以下- - 30以上8.5-10.5 - 5以下1以下未变色(钢片)W2-2号 4.0×10¯²以下- - 30以上8.5-10.5 1-15 5以下1以下未变色(钢片)W3-3号 4.0×10¯²以下- - 30以上8.0-10.5 - 1以下未变色铝及铜片注:W1是稀释20 倍,W2是稀释 3 0 倍。
切削油配方

切削油配方1. 引言切削油是在金属切削加工过程中起到润滑和冷却作用的重要润滑剂。
合理的切削油配方可以提高切削过程的效率和表面质量,延长切削工具的使用寿命,并减少切削过程中产生的废弃物。
本文将介绍切削油的组成成分,常见的切削油配方以及它们的应用。
2. 切削油的组成成分切削油主要由基础油和添加剂两部分组成。
2.1 基础油切削油的基础油是实现润滑和冷却效果的基础。
常见的切削油基础油有矿物油和合成油两种。
•矿物油:具有较高的稳定性和承载能力,适用于一般的切削过程。
•合成油:具有优异的抗氧化性能和高温稳定性,适用于高速、高温、重负荷的切削过程。
2.2 添加剂为了增强切削油的性能,常常需要添加一些化学添加剂。
•抗乳化剂:防止切削油与水发生乳化,保持切削液的稳定性。
•极压添加剂:提高润滑膜的承载能力,减少摩擦和磨损。
•抗氧化剂:延长切削油的使用寿命,防止氧化变质。
•防锈剂:保护金属切削表面,防止产生氧化层。
3. 常见的切削油配方根据不同切削过程的要求,切削油配方可以有所差异,下面介绍几种常见的切削油配方。
3.1 通用切削油配方•基础油:矿物油或合成油•抗乳化剂:2-5%•极压添加剂:5-8%•抗氧化剂:1-3%•防锈剂:1-3%•辅助添加剂:适量3.2 钢铁材料切削油配方•基础油:矿物油•抗乳化剂:2-5%•极压添加剂:10-15%•抗氧化剂:1-3%•防锈剂:1-3%•辅助添加剂:适量3.3 铝合金材料切削油配方•基础油:合成油•抗乳化剂:2-5%•极压添加剂:5-8%•抗氧化剂:1-3%•防锈剂:1-3%•辅助添加剂:适量4. 切削油的应用根据不同切削过程的需求,切削油的应用也会有所不同。
•一般切削过程:通用切削油配方可满足大多数金属切削的需求。
•高速切削:选择优质的合成油基础油和高性能的添加剂,以提高润滑和冷却效果。
•重载切削:采用添加剂中含有高极压性能的切削油,以提高润滑效果和减少磨损。
•高温切削:使用具有较高稳定性和抗氧化性能的合成油基础油。
切削加工用油概论

油性切削油的重要特性如下:1.黏度黏度是油品維持本身稠度的能力,在油性切削油中扮演重要角色。
低黏度油較稀薄,有較好的滲透力及濕潤力,如果選擇適當的添加劑,可使油更快速的到達切削區。
並且因為稀薄,其冷卻、清洗能力均較佳。
高黏度油較稠密,分子較大,有較佳的潤滑性及較大的金屬表面隔離能力,但是流動性及冷卻性不如低黏度油。
2.潤滑金屬在切削時,隨著工件材料的不同和切削速度的不同,會產生不同的熱量和壓力,潤滑作用主要是牽涉到刀具面在滑動區間的潤滑(如圖表47、48所示)潤滑過程包含三種基本機械理論:a.液動潤滑(物理上分離)液動潤滑是潤滑油介於刀具面和工作面之間作物理分離,並無化學反應發生。
黏度較高或較稠的油具有較大的分子,因此有較佳的分離效果。
在刀具滑動區間有較大負荷及壓力時,礦物油的黏度會升高,因此改進了它的潤滑性,這種特性稱為「彈性液動潤滑」。
但是在滑動區間內,刀具與工作件在加工時所產生的壓力過高時仍會將油擠出,因此以具有物理上分離特性的純礦物油作為潤滑油使用,並非十分有效的方法。
單靠礦物油潤滑只能從事一般金屬之輕負荷加工,如果要用於硬性金屬(不銹鋼、合金鋼等)加工,則需另外加添加劑。
b.邊際潤滑在邊際潤滑中,將極性物質加入礦物油中,會在工件面和刀具面形成有化學鍵結的有機薄膜。
這種薄膜會黏附在金屬表面,因此耐磨性比單純以油分子隔離工件及刀具的效果更好。
脂類物質早已用為礦物油添加劑,用來製成可產生合適有機薄膜的潤滑油,脂類對改進切削有極顯著的效果,這有助於刀具壽命的延長。
常用的脂類添加劑有油酸脂、硬脂酸脂、菜籽油和它們的衍生物,目前亦有為數眾多的合成脂類被使用。
天然脂類、脂酸類和它們的衍生物能與金屬表面形成單一分子薄膜,這種碳氫鍵薄膜會形成金屬外表皮(如圖表49所示),這種膜是由金屬與脂類反應所產生,稱為「肥皂金屬」。
脂類添加劑會產生有機膜,它可以避免金屬的直接接觸,直到溫度升高至薄膜的熔點之前都有保護效果。
切削油的调配方法
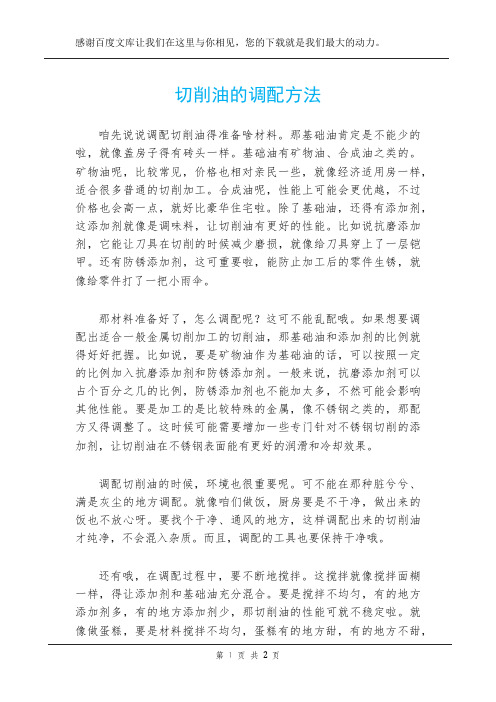
切削油的调配方法咱先说说调配切削油得准备啥材料。
那基础油肯定是不能少的啦,就像盖房子得有砖头一样。
基础油有矿物油、合成油之类的。
矿物油呢,比较常见,价格也相对亲民一些,就像经济适用房一样,适合很多普通的切削加工。
合成油呢,性能上可能会更优越,不过价格也会高一点,就好比豪华住宅啦。
除了基础油,还得有添加剂,这添加剂就像是调味料,让切削油有更好的性能。
比如说抗磨添加剂,它能让刀具在切削的时候减少磨损,就像给刀具穿上了一层铠甲。
还有防锈添加剂,这可重要啦,能防止加工后的零件生锈,就像给零件打了一把小雨伞。
那材料准备好了,怎么调配呢?这可不能乱配哦。
如果想要调配出适合一般金属切削加工的切削油,那基础油和添加剂的比例就得好好把握。
比如说,要是矿物油作为基础油的话,可以按照一定的比例加入抗磨添加剂和防锈添加剂。
一般来说,抗磨添加剂可以占个百分之几的比例,防锈添加剂也不能加太多,不然可能会影响其他性能。
要是加工的是比较特殊的金属,像不锈钢之类的,那配方又得调整了。
这时候可能需要增加一些专门针对不锈钢切削的添加剂,让切削油在不锈钢表面能有更好的润滑和冷却效果。
调配切削油的时候,环境也很重要呢。
可不能在那种脏兮兮、满是灰尘的地方调配。
就像咱们做饭,厨房要是不干净,做出来的饭也不放心呀。
要找个干净、通风的地方,这样调配出来的切削油才纯净,不会混入杂质。
而且,调配的工具也要保持干净哦。
还有哦,在调配过程中,要不断地搅拌。
这搅拌就像搅拌面糊一样,得让添加剂和基础油充分混合。
要是搅拌不均匀,有的地方添加剂多,有的地方添加剂少,那切削油的性能可就不稳定啦。
就像做蛋糕,要是材料搅拌不均匀,蛋糕有的地方甜,有的地方不甜,那可不好吃啦。
调配切削油虽然看起来有点复杂,但只要掌握了这些小诀窍,就能调配出适合自己需求的切削油啦。
而且呀,在调配的过程中,自己动手也挺有成就感的呢。
每次调配出一款好用的切削油,就像自己创造了一个小宝贝一样,能在切削加工中发挥大作用呢。
几种切削液配方及性能特点介绍

几种切削液配方及性能特点介绍切削液是一种用于金属切削、磨加工过程中,用来冷却、润滑刀具和加工件的工业用液体,切削液由多种超强功能助剂经科学复合配合而成,同时具备良好的冷却、润滑、防锈、除油、清洗、防腐、易稀释等性能。
适用于玻璃、树脂玻璃、光学玻璃、平板玻璃、相机镜片、眼镜镜片、蓝宝石玻璃、磁铁、石英光学制品、高档大理石、极品花岗岩、陶瓷晶片、电视机录像机显像管玻璃的切削、切割、磨削。
一、几种切削液配方介绍(1)透明水溶性切削液配方 1(%)乙二醇65.8%、十水硼砂3.0%、偏硅酸钠1.0%、磷酸钠0.2%、水余量。
本液用于结构钢的车削、研磨和钻孔,使用时用水稀释3倍。
(2)乳化切削油配方 1(%)1、石油磺酸钠13%、聚氧乙烯烷基酚醚(OP-10)6.5%、氯化石蜡10~30%、环烷酸铅5%、三乙醇胺油酸皂2.5%、高速机械油(5号)余量。
本油用于金属加工的挤压、车、钻等多道工序,使用浓度为本乳化油的5%~30%。
2、妥尔油酸钠盐4.5%~5.5%、石油酸钠盐4.5%~5.5%、C1-4合成脂肪酸2.5%~4%、聚乙二醇1.5%、工业机械油余量。
3、防锈极压乳化油配方:氯化石蜡10%、硫化油酸9%、石油磺酸钡20%、油酸2%、三乙醇胺5%、机械油(10号)余量。
本油主要用于重载切削加工,可代替植物油及硫化切削油。
以20%的浓度使用。
防锈性能良好。
(3)其它切削液配方硫化切削油:硫化棉子油500、棉子油1350、硫磺70、机械油(10号)2200配方组份1:石油磺酸钡10%、石油磺酸钠4%、司盘80 2%、三乙醇胺6.5%、氢氧化钠0.5% 、油酸11.5%、梓油10%、乙醇2%、20#机油51.5%、水2%;将氢氧化钠0.5%溶解于水,其它组份溶解于20#机油,搅拌均匀,加入氢氧化钠溶液再搅拌均匀即可;使用时配成2%~3%的乳化液,主要用于金属切削加工,作为冷却润滑剂使用。
配方组份2:(质量分数%)石油磺酸钠34.9%、三乙醇胺8.7%、油酸16.6%、10号机油34.9%、乙醇4.9%;此配方按2%稀释成为乳化液使用,铸铁可以防锈12天,用于精磨零件,可以作为高效防锈液使用。
切削液基础知识

切削液基础知识切削液是一种用在金属切、削、磨加工过程中,用来冷却和润滑刀具和加工件的工业用液体切削液是金属切削加工的重要配套材料。
18世纪中后期以来,切削液在各种金属加工领域中得到了广泛的应用。
20世纪初,人们从原油中提炼出大量润滑油,发明了各种润滑油添加剂,真正拉开了现代切削液技术的历史序幕。
一、切削液的组成及性能特点切削液的品种繁多,作用各异,分为油基切削液和水基切削液两大类。
油基切削液也叫切削油,它主要用于低速重切削加工和难加工材料的切削加工。
水基切削液分为3大类乳化切削液、微乳化切削液和合成切削液。
二、切削液的作用使用切削液的主要目的是为减少切削能耗,及时带走切削区内产生的热量以降低切削温度、减少刀具与工件间的摩擦和磨损、提高刀具使用寿命,保证工件加工精度和表面质量,提高加工效率,达到最佳经济效果。
切削液在加工过程中的这些效果主要来源于其润滑作用、冷却作用、清洗作用和防锈作用。
此外,因为切削液是油脂化学制品,直接与操作人员、工件和机床相接触,对其安全性和腐蚀性也必须有一定的要求。
三、切削液的发展趋势众所周知,切削液具有润滑、冷却、清洗及防锈等作用,对提高切削加工质量和效率、减少刀具磨损等均有显著效果。
近十多年来,我国的切削液技术发展很快,切削液新品种不断出现,性能也不断改进和完善,特别是20世纪70年代末生产的水基合成切削液和近几年发展起来的半合成切削液(微乳化切削液)在生产中的推广和应用,为机械加工向节能、减少环境污染、降低工业生产成本方向发展开辟了新路径。
四、切削液的选用切削液都是按照油基切削液和水基切削液来选用的。
总体上看,在加工质量和刀具寿命方面,油基切削液比水基切削液要优越,尽管随被加工材料、加工方法、加工条件的不同其优劣程度会有所差异。
所以,水基切削液应该用于存在着比加工质量和刀具寿命更优先的场合。
五、其他切削液1)膏状及固体润滑剂在攻螺纹时,常在刀具或工件上涂上一些膏状或固体润滑剂。
切削油配方

切削油配方超精用切削油1、油酸1~22、5号高速机油、灯用机油(1:1)98~99车钻1、石油磺酸钡2~52、机油95~98乳化液1、2、3、 4切削油4% 磺化切削油2.5~3.5% 聚乙醇4.4% 69-1 2-3%无水碳酸钠0.3% 无水碳酸钠0.25~0.35% 三乙醇胺8.9% 三乙醇胺0.1~0.2%亚钠0.3% 亚纳0.25~0.35% 亚纳31.1% 水余量水余量水余量水余量水余量5、 6 7691 3% 乳一1 2-3% 防锈乳化油2~6%碳酸钠0.3% 三乙醇胺0.7% 水余量亚纳0.3% 水余量水余量乳化油配制氯化石蜡20 先将油溶性缓蚀剂溶于油中,若难溶(如石油磺酸钡)二烷基硫代硫酸锌 1 加温搅拌五号高速机油79环烷酸铅 6 用皂类作乳化剂时氯化石蜡10 皂化反应条件(T、t)是关键7号机油10 油酸于三乙醇胺要在60-70C°不断搅拌半小时皂化石油磺酸钡0.5 才较完全20号机油余量氧化石油脂钡皂4 乳化油配乳化液时最好将水软化(加入碳酸钠0.2-0.3%)烷基硫代磷酸锌 4 尤其是油酸钠皂或钾皂、松香钠皂时石油磺酸钙 4 PH值=8-9 低用Na2Co3 高用油酸石油磺酸钡 4高速机油余量亚硒酸结晶体H2SeO3 7.5硫酸铜CuSo4.5H2O 8.5 +加热溶解硝酸1.42比重10水74乳化液=乳化油+水乳化油=矿物油+植物油+乳化剂+防锈剂+稳定剂+防霉剂+抗泡剂+助溶剂油性添加剂:动植物油脂肪酸及其皂脂肪醇及多元醇脂类、酮类及胺类化合物挤压添加剂;硫化油氯化石蜡、氯化脂肪酸或脂类防锈添加剂;水性:亚钠、磷酸三钠、磷酸氢二钠、水玻璃、苯甲酸钠、三乙醇胺、单乙、苯乙、苯骈三氮唑油性:石油磺酸钡、石油磺酸钠、石油磺酸钙、环烷酸锌、羊毛脂及其皂F防霉剂:苯酚、五氯酚抗泡剂:二甲基硅油助溶剂:乙醇、正丁醇乳化剂:阳离子:石油磺酸钡、油酸钠皂、松香酸钠皂、磺化蓖麻油、油酸三乙醇胺非离子:乙醇、正丁醇69-1 防锈乳化油乳-1石油磺酸钠10 环烷酸锌11.5磺化油10 石油磺酸钡11.5三乙醇胺10 磺化油12.7油酸 2.4 三乙醇胺油酸皂10:7 3.5-5KaOH 0.6 10号机油余量水 3 2-3%水玻璃5号机油余量乳化油石油磺酸钠34.9 三乙醇胺8.7 油酸16.6 乙醇 4.9 10号机油34.9。
切削液成分表

普通型水溶性玻璃切削液成分配比组份名称①投料量(g/L)甘油2%~3%二乙二醇丁醚4%~5%三乙醇胺5%~6%65014%~5%NP-103~5%乌洛托品1%~2%亚硝酸钠4%~5%水余量组份名称②投料量(g/L)矿物油4%~10%妥尔油1~3%二乙二醇4%~5%三乙醇胺5%~6%二乙醇胺1~4%AEO-93%~5%NP-103~5%乙二胺四乙醇1%~2%有机硅消泡剂1~2%亚硝酸钠4%~5%水余量1、切削液按油品化学组成分为非水溶性(油基)液和水溶性(水基)液两大类。
水基的切削液可分为乳化液、半合成切削液和合成切削液。
乳化液的成分:矿物油50-80%,脂肪酸0-30%,乳化剂15-25%,防锈剂0-5%,防腐剂<2%,消泡剂<1%半合成:矿物油0-30%,脂肪酸5-30%,极压剂0-20%,表面活性剂0-5%,防锈剂0-10%全合成:表面活性剂0-5%,胺基醇10-40%,防锈剂0-40%2、油基切削液和水基切削液的区别油基切削液的润滑性能较好,冷却效果较差。
水基切削液与油基切削液相比润滑性能相对较差,冷却效果较好。
慢速切削要求切削液的润滑性要强,一般来说,切削速度低于30m/min时使用切削油。
含有极压添加剂的切削油,不论对任何材料的切削加工,当切削速度不超过60m/min时都是有效的。
在高速切削时,由于发热量大,油基切削液的传热效果差,会使切削区的温度过高,导致切削油产生烟雾、起火等现象,并且由于工件温度过高产生热变形,影响工件加工精度,故多用水基切削液。
乳化液把油的润滑性和防锈性与水的极好冷却性结合起来,同时具备较好的润滑冷却性,因而对于大量热生成的高速低压力的金属切削加工很有效。
与油基切削液相比,乳化液的优点在于较大的散热性,清洗性,用水稀释使用而带来的经济性以及有利于操作者的卫生和安全而使他们乐于使用。
实际上除特别难加工的材料外,乳化液几乎可以用于所有的轻、中等负荷的切削加工及大部分重负荷加工,乳化液还可用于除螺纹磨削、槽沟麻削等复杂磨削外的所有磨削加工,乳化液的缺点是空易使细菌、霉菌繁殖,使乳化液中的有效成分产生化学分解而发臭、变质,所以一般都应加入毒性小的有机杀菌剂。
切削油配方-油性切削油的质量及性能
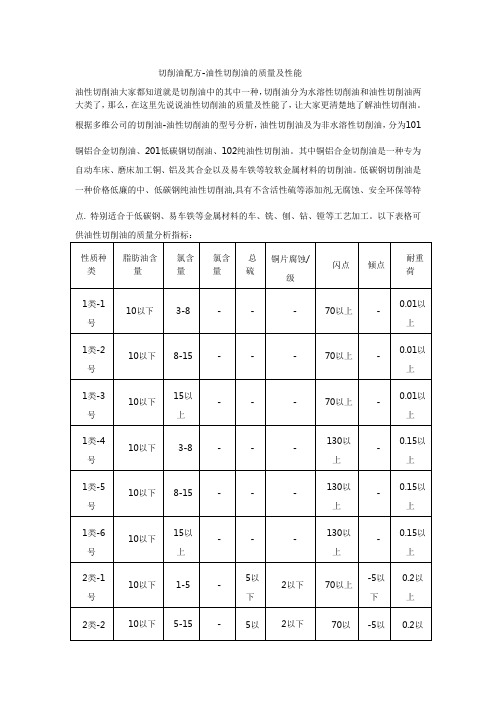
切削油配方-油性切削油的质量及性能油性切削油大家都知道就是切削油中的其中一种,切削油分为水溶性切削油和油性切削油两大类了,那么,在这里先说说油性切削油的质量及性能了,让大家更清楚地了解油性切削油。
根据多维公司的切削油-油性切削油的型号分析,油性切削油及为非水溶性切削油,分为101铜铝合金切削油、201低碳钢切削油、102纯油性切削油。
其中铜铝合金切削油是一种专为自动车床、磨床加工铜、铝及其合金以及易车铁等较软金属材料的切削油。
低碳钢切削油是一种价格低廉的中、低碳钢纯油性切削油,具有不含活性硫等添加剂,无腐蚀、安全环保等特点. 特别适合于低碳钢、易车铁等金属材料的车、铣、刨、钻、镗等工艺加工。
以下表格可供油性切削油的质量分析指标:性质种类脂肪油含量氯含量氯含量总硫铜片腐蚀/级闪点倾点耐重荷1类-1号10以下3-8---70以上-0.01以上1类-2号10以下8-15---70以上-0.01以上1类-3号10以下15以上---70以上-0.01以上1类-4号10以下3-8---130以上-0.15以上1类-5号10以下8-15---130以上-0.15以上1类-6号10以下15以上---130以上-0.15以上2类-1号10以下1-5-5以下2以下70以上-5以下0.2以上2类-210以下5-15-5以2以下70以-5以0.2以号下上下上2类-3号10-503-101-55以下2以下130以上-5以下0.2以上2类-4号10-503-105-155以下2以下130以上-5以下0.2以上2类-5号10-501-51-55以下2以下130以上-5以下0.2以上2类-6号10-505-155-155以下2以下130以上-5以下0.2以上2类-11号10以下1-51-55以下3以上70以上-5以下0.25以上2类-12号10以下5-155-155以下3以上70以上-5以下0.25以上2类-13号10-501-51-55以下3以上130以上-5以下0.25以上2类-14号10以下5-155-155以下3以上130以上-5以下0.25以上2类-15号10以下1-51-55以下3以上130以上-5以下0.25以上。
半合成切削液与全合成切削液的使用性能对比
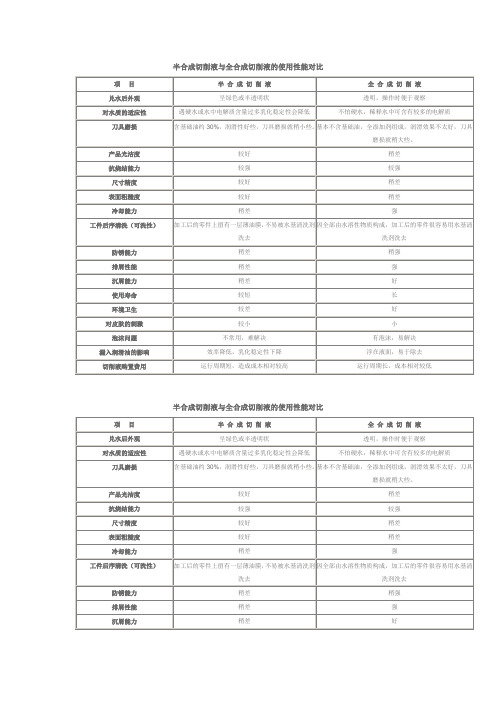
较好
稍差
抗烧结能力
较强
较强
尺寸精度
较好
稍差
表面粗糙度
较好
稍差
冷却能力
稍差
强
工件后序清洗(可洗性)
加工后的零件上留有一层薄油膜,不易被水基清洗剂洗去
因全部由水溶性物质构成,加工后的零件很容易用水基清洗剂洗去
防锈能力
稍差
稍强
排屑性能
稍差
强
沉屑能力
稍差
好
使用寿命
较短
长
环境卫生
较差
好
对皮肤的刺激
较小
因全部由水溶性物质构成,加工后的零件很容易用水基清洗剂洗去
防锈能力
稍差
稍强
排屑性能
稍差
强
沉屑能力
稍差
好
使用寿命
较短
长
环境卫生
较差
好
对皮肤的刺激
较小
小
泡沫问题
不常用,难解决
有泡沫,易解决
漏入润滑油的影响
效率降低,乳化稳定性下降
浮在液面,易于除去
切削液购置费用
运行周期短,造成成本相对较高
运行周期长,成本相对较低
不怕硬水,稀释水中可含有较多的电解质
刀具磨损
含基础油约30%,润滑性好些,刀具磨损就稍小些。
基本不含基础油,全添加剂组成,润滑效果不太好,刀具磨损就稍大些。
产品光洁度
较好
稍差
抗烧结能力
较强
较强
尺寸精度
较好
稍差
表面粗糙度
较好
稍差
冷却能力
稍差
强
工件后序清洗(可洗性)
加工后的零件上留有一层薄油膜,不易被水基清洗剂洗去
乳化切削油主要成分

乳化切削油配方主要成分乳化切削油配方主要成分包含主要成分:石油磺酸钠、聚氧乙烯烷基酚醚、氯化石蜡、环烷酸铅、三乙醇胺油酸皂、高速机械油、妥尔油酸钠盐、石油酸钠盐、合成脂肪酸、聚乙二醇、工业机械油。
石油磺酸钠又称烷基磺酸钠、T702防锈剂、石油磺酸钠T702;分子式:R-SO3Na(R=C14~C18烷基);结构式为:RSO3Na、其中R为平均14~18个碳原子的直链脂肪族烷基;溶解性:溶于水而成半透明液体,对酸碱和硬水都比较稳定氯化石蜡氯化石蜡是石蜡烃的氯化衍生物,具有低挥发性、阻燃、电绝缘性良好、价廉等优点,可用作阻燃剂和聚氯乙烯辅助增塑剂。
广泛用于生产电缆料、地板料、软管、人造革、橡胶等制品。
以及应用于涂料、润滑油等的添加剂。
环烷酸铅制备方法由环烷酸钠与乙酸铅复分解置换而得。
先将环烷酸加水升温至90-100℃,再缓缓加入30%的氢氧化钠溶液进行皂化,至溶液透明,得环烷酸钠,用再乙酸铅复分解置换得粗品,经水洗涤,加热脱水得成品环烷酸铅。
三乙醇胺油酸皂油酸皂对动植物油\矿物油\机油\石腊\润滑油等具有良好的清洗能力,并具有很好的防锈能力。
金属切削液中可作清洗部分,同时具有良好的润滑性能,黑色金属的防腐性能,并有很好的冷却和防锈功能,用于钢、铁、铝、合金钢、低合金钢、钟表元件等金属加工半成品清洗剂,有防锈作用。
在一般工业作为乳化剂,对矿物油,植物油,蜡垢有较好的乳化性能。
高速机械油高速机械油又称高速锭子油。
轻质机械油的一种。
粘度较低的润滑油。
由石油馏分经硫酸精制或溶剂精制并加入抗氧剂而得。
要求润滑性能好,对机械零件磨损小;稳定性好,长期使用不易变质;颜色浅,不污染纱布。
主要用于转速高、负荷轻的纺织机械摩擦部分,如细纺机、捻线机、粗纺机、针织机的止推轴承,也适用于其他高转速低负荷的机械及一些自动控制仪表的润滑。
主要质量指标是粘度、闪点、凝固点等。
合成脂肪酸合成脂肪酸是以石油产品经化学合成方法制得的脂肪酸。
【切削油配方】切削油的配方是什么

【切削油配方】切削油的配方是什么内容来源网络,由“深圳机械展(11万㎡,1100多家展商,超10万观众)”收集整理!更多cnc加工中心、车铣磨钻床、线切割、数控刀具工具、工业机器人、非标自动化、数字化无人工厂、精密测量、数控系统、3D打印、激光切割、钣金冲压折弯、精密零件加工等展示,就在深圳机械展切削油的配方是什么1、水基切削油常见配方矿物油:8%~20%+妥尔油:1~8%+PEG600:4%~5%+油酸三乙醇胺:5%~6%+氯化石蜡:1~3%+脂肪醇聚氧乙烯醚:3%~5%+NP-10:3~5%+乙二胺四乙醇:1%~2%+有机硅消泡剂:1~2%+酒石酸钠:1~2%+石油磺酸钠:4%~5%+水:余量2、油基切削油常见配方硫化脂肪酸酯(YD-3015):5%+硫化猪油YD-1810B:2%+氯化石蜡(T301):2%+环氧大豆油:1%+150SN基础油:余量切削油有哪些功能1、冷却表现在降低刀尖温度、抑制被切削材料和刀具的热膨胀,以提高操作性能和加工精度。
水的热导率和比热容均比油大,粘度也比油小,故乳化液的冷却性能远比油好。
2、润滑减少前刀面与屑、后刀面与加工表面的摩擦,防止发生粘着、积瘤、鳞刺或冷焊,以减少功率消耗和刀具磨损,并得到较好的表面光洁度。
3、防锈为防止大气中的水和氧气对新加工表面的锈蚀,在切削油中要加入防锈剂,提高切削油的防锈性能,以满足工件在加工过程中短期防护之需。
4、清洗利用液流冲去细小的切屑和粉末,防止粘结,以保证刀具和工件连续加工。
在磨加工中,清洗性差的切削油会导致堵塞砂轮,使磨削区温度升高和烧坏工件。
使用低粘度油和加入表面活性剂能提高切削的清洗性。
切削油的分类1、油型又分矿物油切削油(或复合油)、极压切削油、活性切削油三种。
所用的矿物油有煤油、柴油、轻质润滑油馏分。
矿物油中加入一定比例的动、植物油(5%~10%)便是复合油,适用于轻负荷的切削加工。
极压切削油中加有硫、磷、氯极压添加剂,以满足黑色金属,齿轮等深度金属加工的要求。
机加工切削液成分

机加工切削液成分机加工切削液是机床切削加工过程中必需的一种液体,它可以降低切削温度、增加切削润滑性以及清洗减量颗粒等作用。
切削液的性能直接关系到加工效率和加工质量,因此其成分和性能的研究十分重要。
一、切削液成分1.基础油:切削液中不同类型的基础油有着不同的物理性能,是切削液中最常用的添加剂之一。
常见的有矿物油(石油)、合成油(乙烯、丙烯等化学反应得到的油)、酯类油(脂肪酸、酸酯等)、聚醚油(PEO、POE等)、硅油、芳香烃等。
2.添加剂:切削液中的添加剂对其性能发挥至关重要,这些添加剂大多是化学合成物质。
常见的添加剂有抗菌剂、泡沫抑制剂、极压剂、摩擦剂、酸碱中和剂、防锈剂、抗氧化剂、抗腐蚀剂和清洗剂等。
3.水:水是切削液中的主要成分之一,水的密度相对较低,易于清洗,但也容易污染。
注意到加工液中水分的合适比例,过量的水分会导致切削液性能下降、铁件生锈和时间短的油泡现象。
4.颗粒:包括放射粒子、金属铵盐、氧化铝等,往往被加入到切削液中以增加其摩擦力、增加切削润滑性以及清洗加工件。
5.其他:此外,还有少量的酸、碱等物质被加入到切削液中以控制其润滑性能和清洁性能。
二、切削液性能1.切削液的润滑性能:润滑性是切削液的重要性能之一。
润滑性能好的机加工切削液可以有效地降低机床切削法向力和径向力,减少铣削加工过程中的断屑。
润滑性能好的切削液还能减小切削区的热量,降低工件的表面温度,确保切削过程中工件不产生过多的热变形。
2.切削液的清洗性能:清洗性能是切削液的另一个重要性能。
清洗性能好的切削液可以有效地去除加工过程中产生的铁屑和油泥、切屑等杂质,防止这些杂质在机床上磨损和堆积,影响机床和加工件的精度和寿命。
3.切削液的散热性能:散热性能是切削液的一个基本性能,它是指切削液在切削区域内的散热能力。
切削过程中,切削液的散热性能好可以降低切削区的温度,防止工件热变形。
同时,也能延长机床等零部件的使用寿命,增加机床的效率和使用寿命。
切削液的优化配方与加工性能研究

切削液的优化配方与加工性能研究引言:切削液作为一种重要的切削工具,在金属加工过程中起到冷却、润滑和清洗等功能,对于保障加工质量和提高工作效率具有至关重要的作用。
因此,优化切削液的配方和研究其加工性能具有重要的意义。
本文就切削液的优化配方与加工性能进行了深入研究,并总结了相关研究成果。
一、切削液优化配方研究1.1 添加剂的优化选择切削液中的添加剂对切削液性能的改善至关重要。
根据不同的加工需要,选择合适的添加剂进行配方优化是提高切削液性能的关键。
例如,选择具有优良润滑性能的添加剂可以减小摩擦系数,提高切削液的润滑性能。
此外,添加抗菌剂和防锈剂可以有效延长切削液的使用寿命。
1.2 浓度控制的优化切削液的浓度对加工效果和成本都有着重要影响。
过高的切削液浓度会导致加工表面粗糙度过高,而过低则会影响切削液的全面使用效果。
因此,在研究中,对切削液浓度进行优化是必不可少的。
通过调整切削液的添加量和工作液的质量来控制切削液的浓度,以达到最佳的加工效果。
1.3 pH值的调控切削液pH值的调控直接影响切削液中溶解程度、防锈性能和生物稳定性等。
一般来说,较小的pH值对铁基金属加工有利,而在镁、铝等物质的切削加工过程中,较高的pH值更具优势。
因此,通过调整切削液的酸碱度,可以提高切削液的加工性能。
1.4 稳定性的改善切削液的稳定性对于保证长时间稳定运行和延长使用寿命非常重要。
切削液在长时间使用过程中容易受到污染和氧化,从而降低了其性能。
因此,研究人员通过添加稳定剂,并优化切削液的工作环境,如温度、湿度和氧气浓度等,来提高切削液的稳定性。
二、切削液的加工性能研究2.1 冷却性能的研究切削液的冷却性能是其最重要的功能之一。
研究人员通过测量不同切削液配方在冷却性能方面的数据,如冷却时间、冷却速率等,评估切削液的冷却效果。
研究结果表明,合理优化切削液的配方可以显著提高切削液的冷却性能,进而提高加工质量。
2.2 润滑性能的研究切削液的润滑性能直接影响切削刃具与工件之间的摩擦情况。
一种全合成切削液配方

一种全合成切削液配方
1 全合成切削液的特性
全合成切削液是一种合成性润滑油,它使用合成基础油(经过改
性油或环烷烃)生产而成。
因为它含有广泛的防腐剂和辅助成分,比
如抗磨损添加剂和氧化阻止剂,因此其具有良好的润滑性、防腐影响、耐热性、抗锈性等优点。
2 构成全合成切削液的配方
全合成切削液由以下几种不同油类构成:
(1)基础油:合成矿物油、石脑油或环烷烃都可以作为基础油,
以保证润滑质量。
(2)添加剂:包括抗磨剂、氧化阻止剂、抗腐蚀剂以及抗氧化剂等,可以帮助润滑油保持其良好的润滑性和耐热性。
(3)溶剂:用来降低润滑剂的粘度,使其便于处理。
3 全合成切削液的使用
全合成切削液可以用于车床、铣床、钻床等的切削加工,它可以
避免机器因热量变化而晃动、卡夹等现象,并且还可以有效降低振动
等机械噪声,减少工件弯曲等问题,提高机器效率。
切削油
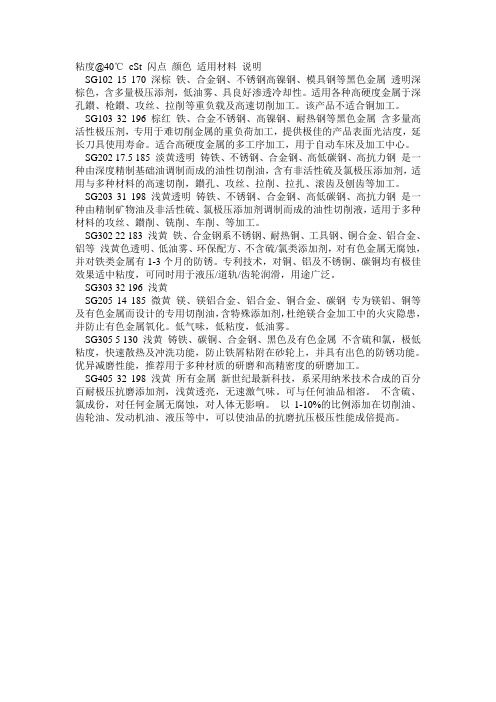
粘度@40℃cSt 闪点颜色适用材料说明SG102 15 170 深棕铁、合金钢、不锈钢高镍钢、模具钢等黑色金属透明深棕色,含多量极压添剂,低油雾、具良好渗透冷却性。
适用各种高硬度金属于深孔鑚、枪鑚、攻丝、拉削等重负载及高速切削加工。
该产品不适合铜加工。
SG103 32 196 棕红铁、合金不锈钢、高镍钢、耐热钢等黑色金属含多量高活性极压剂,专用于难切削金属的重负荷加工,提供极佳的产品表面光洁度,延长刀具使用寿命。
适合高硬度金属的多工序加工,用于自动车床及加工中心。
SG202 17.5 185 淡黄透明铸铁、不锈钢、合金钢、高低碳钢、高抗力钢是一种由深度精制基础油调制而成的油性切削油,含有非活性硫及氯极压添加剂,适用与多种材料的高速切削,鑚孔、攻丝、拉削、拉扎、滚齿及刨齿等加工。
SG203 31 198 浅黄透明铸铁、不锈钢、合金钢、高低碳钢、高抗力钢是一种由精制矿物油及非活性硫、氯极压添加剂调制而成的油性切削液,适用于多种材料的攻丝、鑚削、铣削、车削、等加工。
SG302 22 183 浅黄铁、合金钢系不锈钢、耐热铜、工具钢、铜合金、铝合金、铝等浅黄色透明、低油雾、环保配方、不含硫/氯类添加剂,对有色金属无腐蚀,并对铁类金属有1-3个月的防锈。
专利技术,对铜、铝及不锈铜、碳铜均有极佳效果适中粘度,可同时用于液压/道轨/齿轮润滑,用途广泛。
SG303 32 196 浅黄SG205 14 185 微黄镁、镁铝合金、铝合金、铜合金、碳钢专为镁铝、铜等及有色金属而设计的专用切削油,含特殊添加剂,杜绝镁合金加工中的火灾隐患,并防止有色金属氧化。
低气味,低粘度,低油雾。
SG305 5 130 浅黄铸铁、碳铜、合金钢、黑色及有色金属不含硫和氯,极低粘度,快速散热及冲洗功能,防止铁屑粘附在砂轮上,并具有出色的防锈功能。
优异减磨性能,推荐用于多种材质的研磨和高精密度的研磨加工。
SG405 32 198 浅黄所有金属新世纪最新科技,系采用纳米技术合成的百分百耐极压抗磨添加剂,浅黄透亮,无速激气味。
切削液切削油极压剂6015(含配方)

成都市鑫裕祥贸易有限公司
Chengdu XinYuXiang Trading Co., Ltd.
地址:成都市太升北路56号江信大厦707室
电话(Tel):+86-28-83219136 传真(Fax):+86-28-83219136
E-mail:xyxtrading@ Web:
产品型号:6015
介绍:6015是新一代浅色、低味硫化极压添加剂。
是由高纯合成酯生产而得。
在工作面上具有低粘度、高硫化活性,但在循环温度下能最小化活性。
铜片腐蚀1级。
应用:6015粘度低,与精炼基础油有很好的相溶性。
适用于钢材加工油和乳化油。
常见用途如下:
1、极压型乳化油,通常添加量为10%到15%。
2、钢材极压切削油和金属加工油,通常添加量7%。
产品优点和性能:
6015是一种高性能、浅色、低味、低粘度的添加剂,与大多数矿物油有很好的相容性。
6015可以用来生产高质量切削液和乳化油,它具有以下优点:
1、低味
2、可以用于黑色金属和黄色金属
3、可用于很多加工场合
6015的低粘度使得它非常适用于乳化油和高硬度物料切削油,可以减小高切削率下的刀面磨损,延长刀具寿命,提高工件加工质量。
乳化型切削液与合成切削液性能检测使用比较-最新文档
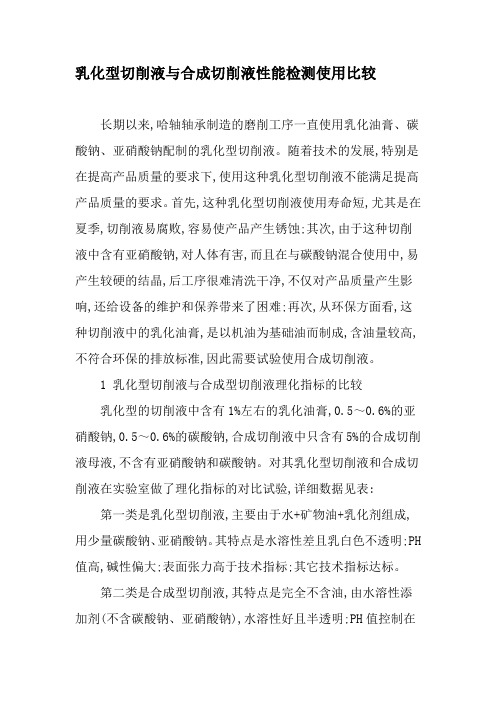
乳化型切削液与合成切削液性能检测使用比较长期以来,哈轴轴承制造的磨削工序一直使用乳化油膏、碳酸钠、亚硝酸钠配制的乳化型切削液。
随着技术的发展,特别是在提高产品质量的要求下,使用这种乳化型切削液不能满足提高产品质量的要求。
首先,这种乳化型切削液使用寿命短,尤其是在夏季,切削液易腐败,容易使产品产生锈蚀;其次,由于这种切削液中含有亚硝酸钠,对人体有害,而且在与碳酸钠混合使用中,易产生较硬的结晶,后工序很难清洗干净,不仅对产品质量产生影响,还给设备的维护和保养带来了困难;再次,从环保方面看,这种切削液中的乳化油膏,是以机油为基础油而制成,含油量较高,不符合环保的排放标准,因此需要试验使用合成切削液。
1 乳化型切削液与合成型切削液理化指标的比较乳化型的切削液中含有1%左右的乳化油膏,0.5~0.6%的亚硝酸钠,0.5~0.6%的碳酸钠,合成切削液中只含有5%的合成切削液母液,不含有亚硝酸钠和碳酸钠。
对其乳化型切削液和合成切削液在实验室做了理化指标的对比试验,详细数据见表: 第一类是乳化型切削液,主要由于水+矿物油+乳化剂组成,用少量碳酸钠、亚硝酸钠。
其特点是水溶性差且乳白色不透明;PH 值高,碱性偏大;表面张力高于技术指标;其它技术指标达标。
第二类是合成型切削液,其特点是完全不含油,由水溶性添加剂(不含碳酸钠、亚硝酸钠),水溶性好且半透明;PH值控制在8;最大无卡咬负荷高于技术指标;其它技术指标达标。
根据国家标准规定检验,合成切削液理化检验数据都达到国家标准。
2 生产使用比较2.1 使用中合成切削液无烧伤、不腐蚀,冷却性、水溶性及冷却液的使用寿命等方面都优于乳化型切削液。
合成切削液无油无碳酸钠、亚硝酸钠切削液粗糙度较乳化型有明显提高(能提高1小级)。
由于它不含碳酸钠、亚硝酸钠,无毒,对人体无害,深受工人的欢迎。
而使用乳化型切削液时个别操作者出现过皮肤过敏现象。
2.2 效果提高。
乳化型切削液粘稠度高,残留物容易粘在砂轮及金属表面。
铝合金切削液配方

切削液配方1、透明水溶性切削液配方1(%)透明水溶性切削液乙二醇 65.8;四硼酸钠 3.0;偏硅酸钠 1.0;磷酸钠 0.2;水余量。
本液用于结构钢的车削、研磨和钻孔,使用时用水稀释3倍。
……共三种配方。
2、乳化切削油配方1(%)石油磺酸钠 13;聚氧乙烯烷基酚醚(OP-10) 6.5;氯化石蜡 10~30;环烷酸铅 5;三乙醇胺油酸皂 2.5;高速机械油(5号)余量。
本油用于金属加工的挤压、车、钻等到工序,使用浓度为本乳化油的5%~30%.。
配方2(%)妥尔油酸钠盐 4.5~5.5;石油酸钠盐 4.5~5.5;C1-4合成脂肪酸 2.5~4;聚乙二醇 1.5;工业机械油余量。
……共五种配方。
3、防锈极压乳化油配方1(%)氯化石蜡 10;硫化油酸 9;石油磺酸钡 20;油酸 2;三乙醇胺 5;机械油(10号)余量。
本油主要用于重载切削加工,可代替植物油及硫化切削油。
以20%的浓度使用。
防锈性能良好。
……共两种配方。
4、其他切削液配方1(份)硫化切削油硫化棉子油 500;棉子油 1350;硫磺 70;机械油(10号) 2200.。
配方2……共有四种配方。
切削液的配方研究:水基切削液具有优良的冷却和清洗性能,但润滑和防锈性能差,因而应用范围受到限制。
以松香、顺酐和多元胺等原料合成了非离子表面活性剂H,同是以油酸和三乙醇胺为原料合成油酸三乙醇胺酯,经实用证明:以非离子表面活性剂H和油酸三乙醇胺酯等复合配制而成的水基切削液,具有优良的润滑性、防锈性、冷却性和清洗性。
是水基切削液的重大突破。
现代机械加工向高速、强力、精密方向发展,超硬、超强度等难加工材料的发展也使切削加工的难度日益增加。
这两方面的原因导致切削加工过程中的摩擦力、摩擦热大幅度提高,这就要求金属加工液具有更好的润滑、冷却、清洗、防锈性能,以便获得理想的加工表面。
矿物润滑油的润滑、防锈性能优越,但冷却、清洗性能差;乳化液和水基切削液的冷却、清洗性能优良,但润滑、防锈性能差。
- 1、下载文档前请自行甄别文档内容的完整性,平台不提供额外的编辑、内容补充、找答案等附加服务。
- 2、"仅部分预览"的文档,不可在线预览部分如存在完整性等问题,可反馈申请退款(可完整预览的文档不适用该条件!)。
- 3、如文档侵犯您的权益,请联系客服反馈,我们会尽快为您处理(人工客服工作时间:9:00-18:30)。
切削油配方和性能对比
自2007年,中国精密机床的生产量就已经达到世界第一位,同时大量引进国外先进加工备,使得现在金属加工水平无论在质量还是数量方面都达到了前所未有的水平。
设备、技术不断提高,新材料不断应用,如果切削油不提高、不发展,势必会落后于金属加工工艺的发展,必然会导致产生许多新的问题,以不锈钢切削工艺为例:
一.目前市场中低端普遍采用的油品配方主要添加剂为:
T405A或黑琉+T301(氯化石蜡)+**40(硫化烯烃)+菜籽油
优点:各种原材料便于采购,除去硫化烯烃成本略高,其他几种添加剂价格都较低;
缺点:1.油品极压性低,造成刀具磨损快,工件光洁度达不到要求;
2.腐蚀性高,造成设备、工件发黄生锈,对环境、员工也极为不利;
3.设备容易起“黄袍”
二.市场高端油品配方的主要添加剂为:
硫化猪油(浅色)+T301(氯化石蜡)+**40(硫化烯烃)
优点:去除了不饱和酸的植物脂肪,避免“黄袍”现象的出现。
缺点:1. 腐蚀性高,造成设备、工件发黄生锈,对环境、操作人员也极为不利
2. 油品极压性仍然得不到提高,造成刀具磨损快,工件光洁度低
各种添加剂的作用如下:
1:黑色硫化猪油或菜籽油+硫化棉籽油:在切削加工起始阶段靠植物脂肪的油膜起到一定的抗磨作用。
2:氯化石蜡301:工作温度区间为50℃——350℃,所以,在切削加工的中期阶段,氯化石蜡占主导地位。
当切削工艺压力、温度上升到一定高度后,棉籽油的抗磨性失去效果,氯化石蜡极压性开始生成。
3:硫化烯烃**40: 活性硫含量高、铜腐蚀性高,烯烃在油中是游离状态的,极性低、吸附性差、几乎没有抗磨性,硫化添加剂极压性的高低取决于三方面:极性高低、硫的结合方式及硫含量高低;如果单纯凭借硫含量高低就判定极压性的高与低,就太片面了。
硫化烯烃在切削油中最主要的作用是预防切削瘤的形成,防止产生烧结现象。
切削加工中最容易出现问题的阶段就是在两款添加剂相互衔接、过渡的时候,在加工后期,由于硫化烯烃**40的极压性没有及时跟上,所以造成工件光洁度低、刀具磨损快,严重时还会产生烧结现象。
上述切削油配方的不足及改善对策:
1:切削加工初期需要的脂肪抗磨性棉籽油不能满足,天然不饱和脂肪酸的使用,会加快油品酸败的程度、也是黄袍产生的根本原因
---建议:更换抗磨性、抗氧性很好的硫化脂肪添加剂。
2:氯化石蜡在起极压作用的同时并释放大量的活性氯,会严重刺激皮肤、腐蚀设备。
---建议:T301不更换,添加氯俘获剂—环氧大豆油,在保证氯化石蜡极压作用的同时,抑制其腐蚀性
3:硫化烯烃**40在加工中、后期的极压性没有跟上,导致烧结产生。
---建议:将硫化烯烃**40更换为极压性高、硫释放快的硫化脂肪酸酯
我们通过分析四球机600N—7845N这十个图的数据得到以下线性图:
针对以上优缺点、结合各种添加剂的工作特性,根据大量的一线经验及四球数据,亿达石化推荐配方主剂为:
硫化脂肪酸酯(YD-3015)+硫化猪油(YD-1810C、YD-1811)+氯化石蜡(T301)+环氧大豆油+精制猪油
说明:1.在不增加成本的情况下,达到了良好的加工效果;
2.腐蚀性低,对设备、工件、环境、人员无损害。
以下数据是市场中主流不锈钢切削油的配方和亿达石化常用不锈钢切削油的配方对比:
A:黑硫 8%+T301 20%+植物油 5%+进口硫化烯烃(**40)2%+T106A 0.5%+150SN 余量
膜的过程阶段,由于旧的物理润滑油膜随压力、温度的增高而失去效应,新的化学极压油膜正处于形成过程中,由于极压剂里的化学物质正在发生剧烈反应,导致润滑不稳定,摩擦力才会出现不正常的波动,这是整个润滑过程中润滑效果最薄弱的阶段,此阶段的磨斑大小及形态,直接决定了加工效果和效率,所以金属加工中出现的问题绝大多数会发生在这个新旧油膜更替的阶段,这个阶段是无法避免的,但波动的剧烈程度是可以通过选用极压抗磨添加剂改善的,波动越平稳,时间越短暂,它的使用效果就越好。
通过以上四球数据可以看出,选用同样基础油、同样的实验方法,在不增加成本的情况下,配方B的极压抗磨性远优于配方A,加工效率必然要高,且通过对主剂添加量的调整,仍然有很大的提升空间;配方A即使再增加主剂的添加量,也没有太大的提升空间,所以,硫化添加剂在选用之前,应该运用“线性理论”进行必要的四球测试。
亿达渤润建议不锈钢切削加工油配方,反映到图中应该是这样的:
硫化猪油 + 氯化石蜡 + 硫化脂肪酸酯
此配方体系在国内各大油品调和厂及终端用户处均得到良好的回馈;鉴于金属加工工艺的特殊要求和成本控制,可以对主剂进行适当的增减;尚有很大的提升空间。
---沧州市亿达渤润石化有限公司。