第四章凸凹模型面成形磨削工艺
浅析吊扇叶片成形模具中凹、凸模成形面的车削加工方法
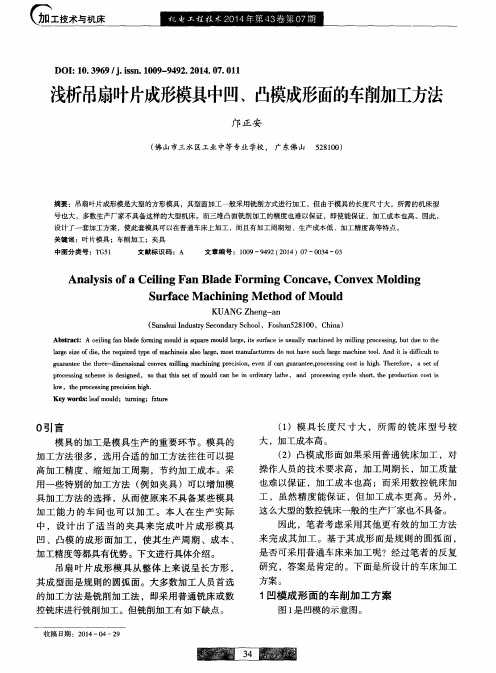
An a l y s i s o f a Ce i l i n g F a n Bl a d e F o r mi n g Co n c a v e , Co n v e x Mo l d i n g S u r f a c e Ma c h i n i n g Me t h o d o f Mo u l d
摘要:吊扇 叶片成形模是 大型的方形模具 , 其 型面加 工一般 采用 铣削方式进行加工 ,但由于模具的长度尺寸大 ,所需的机床型
号也大 ,多数生 产厂家不具 备这样的大型机 床。而三维凸面铣削加工 的精度也难 以保证 ,即使能保证 ,加工 成本也 高。因此 ,
设计了一套加工方案 ,使此套模 具可以在普通 车床上加工 ,而且有加工周期短 、生产成本低 、加工精度高等特点 。 关键词 :叶片模具 ;车削加工 ;夹具
KUANG Z h e n g — a n
( S a n s h u i I n d u s t r y S e c o n d a r y S c h o o l ,F o s h a n 5 2 8 1 0 0 ,C h i n a )
Abs t r a c t :A c e i l i n g f a n b l a d e f o r mi n g mo u l d i s s q u a r e mo u l d l rg a e ,i t s S u r f a c e i s u s u a l l y ma c h i n e d b y mi l l i ng p r o c e s s i n g , b u t d u e t o t h e l a r g e s i z e o f d i e , t h e r e q u i r e d t y pe o f ma c h i n e i s a l s o l a r g e ,mo s t ma n u f a c t u r e r s d o n o t h a v e s u c h l rg a e ma c h i n e t o o 1 . An d i t i s d i f f i c u l t t o g u ra a n t e e t he t h r e e — di me n s i o n l a c o n v e x mi l l i n g ma c h i n i n g p r e c i s i o n ,e v e n i f c a n g u a r a n t e e , p r o c e s s i n g c o s t i s h i g h .T h e r e f o r e, a s e t o f pr o c e s s i n g s c h e me i s d e s i g n e d, S O t ha t t h i s s e t o f mo u l d c a n b e i n o r d i n a r y l a t h e, a n d p r o c e s s i n g c y c l e s ho r t ,t h e p r o d u c t i o n c o s t i s l o w, t h e p r o c e s s i n g p r e c i s i o n h i s h . Ke y wo r d s : l e a f mo u l d: t u ni r n g;f x t u r e
凸凹模的铣削加工

其中: G02:表示顺时针圆弧插补。 G03:表示逆时针圆弧插补。 X Y Z :表示圆弧的终点坐标值,其值可以是绝 对坐标,也可以是增量坐标。在增量方式下,其值为圆弧终 点坐标相对于圆弧起点的增量值。 R :表示圆弧半径。 I J K :表示圆弧的圆心相对于其起点并分别在
三、刀具半径补偿
1.刀位点 在数控编程过程中,为了编程人员编程方便,通常将
数控刀具假想成一个点,该点称为刀位点或刀尖点。因此, 刀位点既是用于表示刀具特征的点,也是对刀和加工的基 准点。
数控刀具的刀位点
2.刀具补偿功能的概念
数控铣床的刀具补偿功能分成刀具半径补偿功能和刀具
长度补偿功能两种。
(1)刀具半径补偿定义
……
刀补进行 刀补取消
(4)刀具半径补偿注意事项 1)半径补偿模式的建立与取消程序段只能在G00或 G01移动指令模式下才有效。在半径补偿建立与取消程 序段最好不使用G02、G03指令。 2)为保证刀补建立与刀补取消时刀具与工件的安全 ,通常采用G01运动方式来建立或取消刀补。如果采用 G00运动方式来建立或取消刀补,则要采取先建立刀补 再下刀和先退刀再取消刀补的编程加工方法。 3)为了便于计算坐标,采用切线切入方式或法线切 入方式来建立或取消刀补。
(3)刀具半径补偿过程
刀具半径补偿过程
(3)刀具半径补偿过程
程序如下:
O0010; …… N10 G41 G01 X100.0 Y100.0 D01; 刀补建立
N20 Y200.0 F100;
N30 X200.0; N40 Y100.0 ; N50 X100.0 ; N60 G40 G00 X0 Y0;
磨削理论.pdf
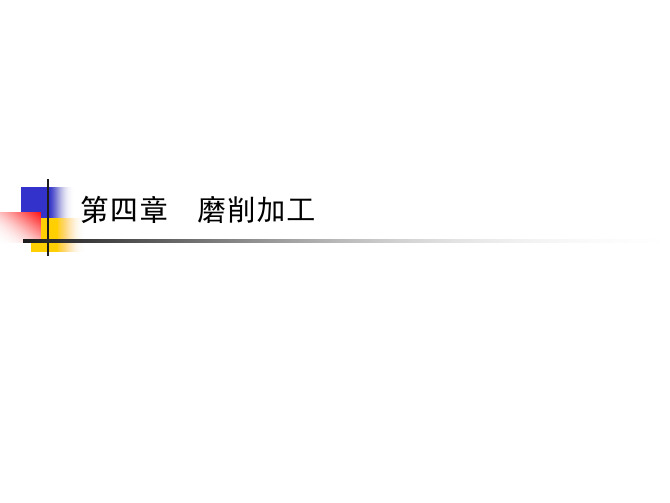
磨削过程
磨削时,如图所示,其切削厚度由零开始逐渐增大。由于磨粒具有
很大负前角和较大尖端圆角半径。因而磨粒开始切入工件时,只能在工
件表面上进行滑擦,这时切削表面产生弹性变形。当磨粒继续切入工
件,磨粒作用在工件上的法向力Fn增大到一定值时,工件表面产生塑性
变形,使磨粒前方受挤压的金属向力后从砂轮上脱落的难易程度。也就是说,磨粒 容易脱落的,称砂轮硬度为软;反之,为硬。因而磨具的硬度是粘 结剂对磨粒的粘结强度,与磨粒材料的硬度无关。
组织结构
砂轮的组织结构是指砂轮中磨料、粘结剂、气孔三者所占的比例。 如图4-1所示。当磨粒所占比例较高而气孔较少时,称砂轮组织结 构紧密,见图4-2(a); 当磨粒所占比例较低而气孔较多时,则称 砂轮组织结构疏松,见图4-2(c); 图4-2(b) 所示,为砂轮组织结构 属中等的情况。砂轮中的气孔可以容纳切屑,且容易携带冷却液 和空气进入磨削区,对降低磨削温度有利。
沟槽,而沟槽的两侧微微隆起,见图。当磨料继续切入工件,其切削厚
度增大到一定数值后,磨粒前方的金属在磨粒的挤压作用下,发生滑移
而成为切屑。
磨削过程
磨削中,砂轮表层的每个磨粒就像铣刀盘上的一个刀刃,各个磨粒形状、 分布和高低各不相同,使其切削过程也有差异。砂轮表层中的一些突出 和比较锋利的磨粒,切入工件较深,将经过滑擦、耕犁和切削三个阶 段,形成非常微细切屑。由于磨削温度很高,磨屑飞出时氧化形成火花。 比较钝的、突出高度较小的磨粒,切不下切屑,只是起刻划作用,在工 件表面挤压出微细的沟槽。更钝的、隐藏在其它磨粒下面的磨粒只稍微 滑接着工件表面起抛光作用。可见磨削过程是包含切削、刻划和抛光作 用的综合复杂过程。
运动外,在加工中砂轮还得沿径向做切入运动,其大小用工作台(或工件)
模具制造技术第5次课
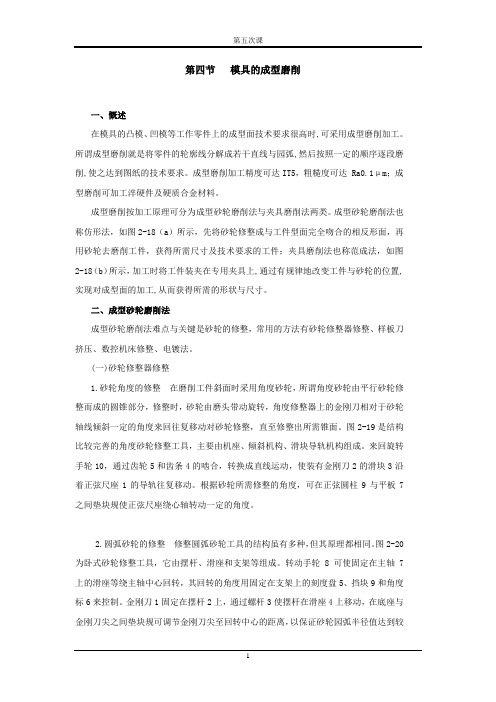
第四节模具的成型磨削一、慨述在模具的凸模、凹模等工作零件上的成型面技术要求很高时,可采用成型磨削加工。
所谓成型磨削就是将零件的轮廓线分解成若干直线与园弧,然后按照一定的顺序逐段磨削,使之达到图纸的技术要求。
成型磨削加工精度可达IT5,粗糙度可达 Ra0.1μm;成型磨削可加工淬硬件及硬质合金材料。
成型磨削按加工原理可分为成型砂轮磨削法与夹具磨削法两类。
成型砂轮磨削法也称仿形法,如图2-18(a)所示,先将砂轮修整成与工件型面完全吻合的相反形面,再用砂轮去磨削工件,获得所需尺寸及技术要求的工件;夹具磨削法也称范成法,如图2-18(b)所示,加工时将工件装夹在专用夹具上,通过有规律地改变工件与砂轮的位置,实现对成型面的加工,从而获得所需的形状与尺寸。
二、成型砂轮磨削法成型砂轮磨削法难点与关键是砂轮的修整,常用的方法有砂轮修整器修整、样板刀挤压、数控机床修整、电镀法。
(一)砂轮修整器修整1.砂轮角度的修整在磨削工件斜面时采用角度砂轮,所谓角度砂轮由平行砂轮修整而成的圆锥部分,修整时,砂轮由磨头带动旋转,角度修整器上的金刚刀相对于砂轮轴线倾斜一定的角度来回往复移动对砂轮修整,直至修整出所需锥面。
图2-19是结构比较完善的角度砂轮修整工具,主要由机座、倾斜机构、滑块导轨机构组成。
来回旋转手轮10,通过齿轮5和齿条4的啮合,转换成直线运动,使装有金刚刀2的滑块3沿着正弦尺座1的导轨往复移动。
根据砂轮所需修整的角度,可在正弦圆柱9与平板7之间垫块规使正弦尺座绕心轴转动一定的角度。
2.圆弧砂轮的修整修整圆弧砂轮工具的结构虽有多种,但其原理都相同。
图2-20为卧式砂轮修整工具,它由摆杆、滑座和支架等组成。
转动手轮8可使固定在主轴7上的滑座等绕主轴中心回转,其回转的角度用固定在支架上的刻度盘5、挡块9和角度标6来控制。
金刚刀1固定在摆杆2上,通过螺杆3使摆杆在滑座4上移动,在底座与金刚刀尖之间垫块规可调节金刚刀尖至回转中心的距离,以保证砂轮园弧半径值达到较高的精度,如图2-21所示。
凸凹体锉配工艺
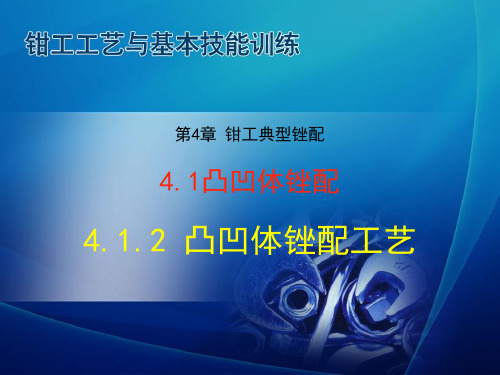
4.1凸凹体锉配
4.1.2 凸凹体锉配工艺
一、加工工艺流程。 1、检查来料毛坯尺寸,按图样要求锉削好外轮廓基准面,达到尺寸 60±0.05mm,40±0.05mm及垂直度、平行度等要求。 2、按图样要求分别划出凸凹体的加工线,用游标尺复查避免看错尺寸或画 错。并钻4-Φ3mm工艺孔。 3、加工凸形体:加工步骤按图所示。
2 1 3 4
(1)、按划线锯去工件一角,粗锉达到加工线(约为0.2mm加工余量)。 精锉①面,用千分尺测量A和C的实际尺寸,使A-C=20 0 -0.05mm。 (2)、精锉②面,用千分尺测尺寸B,B=总宽的实际尺寸除以2加上1000.025mm,使尺寸达到控制要求。 (3)、①②面精加工合格后再锯另一角。粗锉③、④面,保留0.2mm左右 加工余量,精加工③面方法同面①。 (4)、精加工④面,使其尺寸控制在20 0 -0.05mm以内。凸块加工完后 则作为基准件以后不再加工。
4、加工凹体:加工步骤按图所示。 (1)、将凹体部分锯、錾除多余部分,粗加工至加工线,保留0.2mm 的加工余量。 (2)、精锉⑤面用总长的实际尺寸减去20 0 -0.05mm,再分别精锉⑥ 、⑦面。控制凸体20 0 -0.05mm,用凸块与凹块试配,修整实际配合精度 要求。
7 5 5
6Hale Waihona Puke 二、考核评分标准
头盔外壳成形模凸、凹模的加工工艺方法
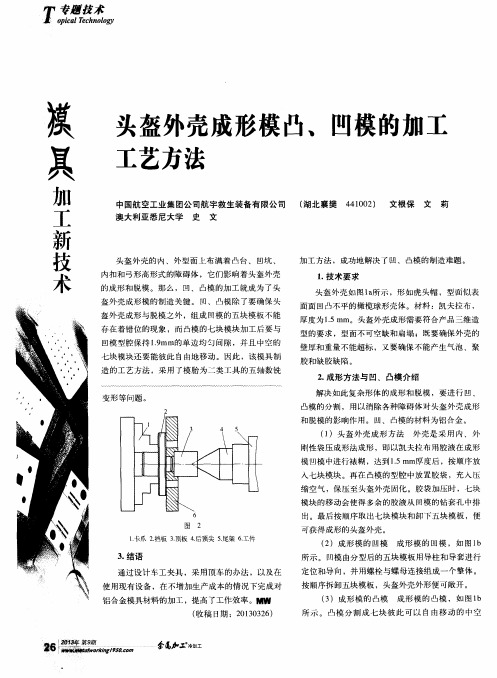
头盔外壳成形模凸 凹模的加工 工艺方法
中国航 空工业集 团公司航 宇救生装 备有限公 司 ( 湖北 襄樊 澳大利亚 悉尼大学 史 文 4 4 1 0 0 2 ) 文根保 文 莉
头 盔 外 壳 的 内 、外型 面 上 布 满 着 凸台 、凹坑 、 内扣 和 弓形 高 形 式 的障 碍 体 ,它 们影 响着 头 盔 外壳 的 成 形和 脱模 。那 么 ,凹 、 凸模 的加 工 就 成 为 了头 盔 外 壳 成 形模 的 制 造 关 键 。 凹 、 凸模 除 了要 确 保 头
图
2
1 . 卡爪 2 . 挡板 3 . 顶板 4 . 后顶尖 5 . 尾架 6 . 工件
3 . 结语 通过设计车工夹具 ,采用顶车的办法 ,以及在 使用现有设备 ,在不增加生产成本的情况下完成对
铝合金模具材料 的加工 ,提高 了工作效率 。MW ( 收稿 日 期 :2 0 1 3 0 3 2 6 )
参磊
籼工
T
凸台 “ 障
o
地 从 凹模 中 放 入 与 取 出 , 它 们 分 型 面 之 间应 制 成 3 。 的脱 模 斜 度 。 同 时 ,可 防止 胶 液 进 入 分 型 面 的
间隙 之 中 。
3 . 成形模 凹 凸模 的加 工工艺
如何制订 成形模 凹、 凸模的加工 工艺 ,便成
所示。凹模 由分型后的五块 模板用导柱和导套进行
定位和导 向,并用螺栓与螺母连接组成一个整体 。 按顺序拆卸五块模板 ,头盔外壳外形便可敞开 。
( 3 )成形模 的凸模 成形 模的 凸模 ,如 图1 b
所 示 。凸模 分割成 七块彼 此可以 自由移 动的 中空
r
i 9 5 o ; c o m
凹凸模数控铣削加工工艺及程序设计定稿

2013届本科生毕业论文学号:0成绩:凹凸模数控铣削加工工艺及程序设计系部:机电工程专业:机械设计制造及其自动化学生姓名:姚良玉指导教师:谢雪如二〇一三年四月毕业论文诚信声明本人郑重声明:所呈交的毕业论文《凹凸模数控铣削加工工艺及程序设计》是本人在指导老师的指导下,独立研究、写作的成果。
论文中所引用是他人的无论以何种方式发布的文字、研究成果,均在论文中以明确方式标明。
本声明的法律结果由本人独自承担。
毕业论文作者签名:姚良玉 2013年4月20日摘要数控机床的出现以及带来的巨大利益,引起世界各国科技界和工业界的普遍重视。
发展数控机床是当前我国机械制造业技术改造的必由之路,是未来工厂自动化的基础。
数控机床的大量使用,需要大批熟练掌握现代数控技术的人员。
数控技术的应用不但给传统制造业带来了革命性的变化,使制造业成为工业化的象征,而且随着数控技术的不断发展和应用领域的扩大,它对国计民生的一些重要行业的发展起着越来越重要的作用。
随着科技的发展,数控技术也在不断的发展更新,现在数控技术也称计算机数控技术,加工软件的更新快,CAD/CAM的应用是一项实践性很强的技术。
如像UG , PRO/E , Cimitron , MasterCAM ,CAXA制造工程师等。
数控技术是技术性极强的工作,尤其在模具领域应用最为广泛,所以这要求从业人员具有很高的机械加工工艺知识,数控编程知识和数控操作技能。
本文主要通过铣削加工薄壁配合件的数控工艺分析与加工,综合所学的专业基础知识,全面考虑可能影响在铣削、钻削、铰削加工中的因素,设计其加工工艺和编辑程序,完成配合要求。
【关键词】铣削钻削铰削 CAD/CAM 薄壁板类配合件零件加工The advent of NC machine tool which bring huge benefits, technology and industry around the world.Seriously,the development of numerical control machine tool is the necessary way of current in our country mechanical manufacturing industry technical innovation, is the factory in the future;The basis of automation, Use of CNC machine tools, need a large number of skilled personnel of modern numerical control technology. The application of numerical control technology not only brings revolutionary change to traditional manufacturing industry, manufacturing industry has become a symbol of industrialization, and with the continuous development of numerical control technology and application field expands, it to the national economy and people's livelihood some important industry plays a more and more important role in the development.Along with the development of science and technology, numerical control technology is also in constantly development update, now the numerical control also called computeriged numerical control technology, processing software updates fastly, the application of CAD/CAM is a practical technology. Cimitron such as UG, PRO/E, MasterCAM, CAXA manufacturing engineers, etc.Numerical control technology is a highly technical work, especially in the field of mould is most widely used, so this requires the employees have high mechanical processing knowledge, knowledge of CNC programming and CNC operation skills. This paper mainly through the milling machining with a CNC technology analysis and processing, comprehensive basic knowledge of my major in, comprehensive consider may affect in the milling, drilling, cutting and processing factors, design the process and editing program, complete with requirements.【Keywords】stranded milling drilling cutting CAD/CAMThin plate assemblies parts processing第1章零件加工工艺的分析 (1)1.1 零件的技术要求分析 (1)1.2 零件的结构工艺分析 (1)1.3 编程尺寸的确定 (4)1.4 毛坯的选择 (5)1.5 工艺过程设计 (5)1.5.1 定位基准确定 (6)1.5.2 零件加工方案确定 (6)1.5.3 零件加工走到路线确定 (6)1.6 选择机床、工艺装备等 (8)1.6.1 数控机床及系统选择 (8)1.6.2 夹具及装夹方案确定 (8)1.6.3 刀具选择方案 (9)1.6.4 量具选择方案 (11)1.7 确定切削用量 (11)第2章凹凸模数控加工 (13)2.1 数控工艺文件 (13)2.1.1 凹模的加工工艺文件 (13)2.1.2 凸模的加工工艺文件 (17)2.2 数控加工程序设计 (21)小结 (25)参考文献 (26)致谢 (27)第1章零件加工工艺的分析1.1零件的技术要求分析零件的尺寸公差在0.05—0.1mm之间,且凸模薄壁厚度为8mm,区域面积较大,表面粗糙度也比较高,达到了Ra1.6um,相对难加工,加工时容易产生变形,处理不好可能会导致其壁厚公差及表面粗糙度难以达到要求。
第四章凸凹模型面成形磨削工艺
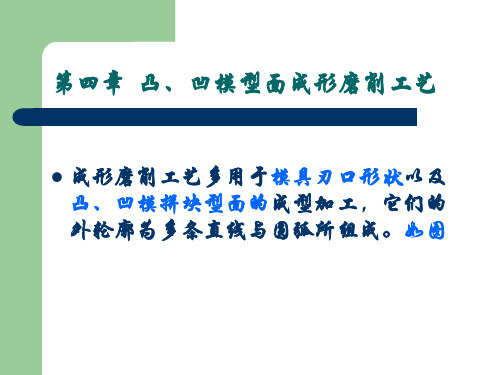
2)多回转中心定位磨削
多回转中心定位磨削会降低磨削精度
4、成形磨削工艺计算:
成形磨削之前需根据凸模与凹模拼块设计图进 行磨削工艺设计和工艺计算,并作出磨削工艺 图。 成形磨削工艺设计和工艺计算的主要内容有: 1)根据磨削规则,分析工件形状与尺寸精度 要求进行合理的分段,并确定各段的磨削顺序。
当工件尺寸大,需分段磨削 时,工件的定位方法与顺序 为:见图7-25,先使工件上 的拼合面b,对准放大图上 的拼合线b';此后,移动工作 台,使 工件外形基准面a,对 准放大图上a‘中心线;再用 尺寸为A的量块垫入机床 纵向滑板,以控制机床纵向 的移动距离。
数控成型磨削与坐标磨削工艺
一、数控成型磨削工艺与机床
坐标磨削精度与质量: 1)最大磨削速度:Vmax=100000r/min; 2)定位精度:在30mm长度内为0.8um;在全行程内为 2.3um。 3)NC连续轨迹磨削的形状精度:在全行程内为7.5um。 4)表面粗糙度为:一般磨削加工时达Ra(0.8~o.4)um;精 细加工时达:Ra0.2um。 所以,坐标磨削主要应用精密冲裁模的凸模、凹模与卸料 板型孔的精密加工。
3、万能夹具成形磨削工艺方法示例:
(1)回转中心定位磨削工艺: 1)万能回转夹具的X、Y滑座上,根据工 件形状及其尺寸要求,安装精密平口虎 钳或正弦磁力夹具,工件定位安装在夹具 中。然后,根据工艺尺寸计算图将工件 的O点调整到夹具的回转中心,转动不同 角度,进行相应平面的磨削。
安装于万能夹具Y导轨滑座上的平口虎钳、磁 力夹具,以及直接安装于滑座上的联接方式。
光学曲线磨削工艺
光学曲线磨床的组成:
凹凸模数控铣削加工工艺及程序设计

凹凸模数控铣削加工工艺及程序设计Chapter 1: AbstractThe emergence of CNC machine tools and the huge XXX CNC machine tools is the only way to transform China'XXX widespread use of CNC machine tools requires a large number of personnel skilled in modern CNC technology。
The n of CNC technology has not only XXX industries。
XXX n。
but also plays an increasingly important role in the development of some important industries for XXX its n areas.Chapter 2: Analysis of Parts Processing Technology2.1 Analysis of Technical Requirements for PartsThe technical requirements for parts include nal accuracy。
XXX roughness。
XXX.2.2 Analysis of Structural Process for PartsThe structural process of parts refers to the process of determining the processing sequence and processing methods based on the XXX.2.3 n of Programming nsThe programming ns are determined based on the technical requirements for parts and the structural process of parts.2.4 XXX BlanksXXX such as material。
凹凸模具加工工艺流程

凹凸模具加工工艺流程一、凹凸模具加工工艺简介凹凸模具加工工艺是一种常用的金属加工工艺,用于生产制造各种凹凸形状的模具。
凹凸模具广泛应用于汽车、航空航天、电子、家电等行业,是工业生产中不可或缺的重要工具。
二、凹凸模具加工工艺流程凹凸模具加工工艺流程主要包括模具设计、模具制造、模具试验和模具修正等几个步骤。
1. 模具设计模具设计是凹凸模具加工的第一步,它决定了模具的形状、尺寸和结构。
在模具设计过程中,需要根据产品的要求和使用环境,确定模具的材料、硬度和表面处理等参数。
同时,还需要考虑到模具的可制造性和经济性,以便在后续的加工过程中能够顺利进行。
2. 模具制造模具制造是凹凸模具加工的核心步骤,它包括模具加工工艺的选择、模具零件的加工和装配等过程。
在模具制造过程中,需要使用各种机床和工具进行材料的切削、成形和组装等操作。
这些操作需要高度的技术和经验,并要求制造出的模具具有高精度、高稳定性和长寿命等特点。
3. 模具试验模具试验是凹凸模具加工的重要环节,它主要用于验证模具的性能和可靠性。
在模具试验过程中,需要根据产品的要求进行模具的调试和优化,以确保模具能够满足生产的需求。
同时,还需要进行模具的寿命测试和性能测试,以评估模具的使用寿命和生产效果。
4. 模具修正模具修正是凹凸模具加工的最后一步,它主要用于修正模具在使用过程中出现的问题。
在模具修正过程中,需要根据实际生产情况进行调整和改进,以提高模具的使用寿命和生产效率。
同时,还需要进行模具的维护和保养,以延长模具的使用寿命。
三、凹凸模具加工工艺的优势凹凸模具加工工艺具有以下几个优势:1. 精度高:凹凸模具加工可以实现高精度的模具制造,能够满足复杂产品的加工要求。
2. 稳定性好:凹凸模具加工制造的模具具有高稳定性和长寿命的特点,能够满足大批量生产的需求。
3. 生产效率高:凹凸模具加工可以实现自动化生产,提高生产效率和产品质量。
4. 经济性好:凹凸模具加工的成本相对较低,能够满足企业的经济需求。
凸凹磨具的加工工艺流程
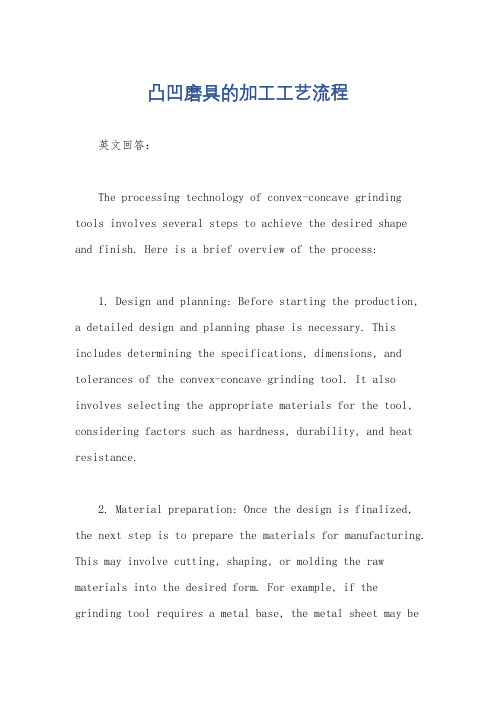
凸凹磨具的加工工艺流程英文回答:The processing technology of convex-concave grinding tools involves several steps to achieve the desired shape and finish. Here is a brief overview of the process:1. Design and planning: Before starting the production,a detailed design and planning phase is necessary. This includes determining the specifications, dimensions, and tolerances of the convex-concave grinding tool. It also involves selecting the appropriate materials for the tool, considering factors such as hardness, durability, and heat resistance.2. Material preparation: Once the design is finalized, the next step is to prepare the materials for manufacturing. This may involve cutting, shaping, or molding the raw materials into the desired form. For example, if thegrinding tool requires a metal base, the metal sheet may becut and bent into the required shape.3. Machining: Machining is a crucial step in the production of convex-concave grinding tools. It involves using various machining techniques such as milling, turning, drilling, and grinding to shape the tool. For example, milling machines may be used to remove excess material and create the desired contours, while grinding machines can be used to achieve the required surface finish.4. Heat treatment: Heat treatment is often employed to enhance the hardness and durability of the grinding tool. This process involves heating the tool to a specific temperature and then cooling it rapidly or slowly, depending on the desired properties. Heat treatment can improve the wear resistance and toughness of the tool, ensuring it can withstand the demanding grinding applications.5. Surface finishing: After the machining and heat treatment processes, the convex-concave grinding tool may undergo surface finishing to achieve the desired smoothnessand precision. This can be done through processes such as polishing, lapping, or electroplating. For example, polishing can help remove any surface imperfections and create a mirror-like finish on the tool.6. Quality control: Throughout the manufacturing process, quality control measures should be implemented to ensure the final product meets the required specifications. This may involve conducting inspections, measurements, and tests at various stages of production. For example, dimensional checks, hardness tests, and surface roughness measurements can be performed to verify the quality of the grinding tool.中文回答:凸凹磨具的加工工艺流程涉及多个步骤,以实现所需的形状和表面光洁度。
凸凹模的车削加工

(3)刀具半径补偿过程
刀具半径补偿过程
(3)刀具半径补偿过程
程序如下:
O0010; …… N10 G41 G01 X100.0 Y100.0 D01; 刀补建立
N20 Y200.0 F100;
N30 X200.0; N40 Y100.0 ; N50 X100.0 ; N60 G40 G00 X0 Y0;
1.快速点定位(G00)
书写格式:G00 X/U Z/W 1)X/U Z/W 为目标点坐标; 2)G00指令一般作为空行程; 3)G00可以单坐标运动,也可以两坐标运动,两坐标运动时 刀具先1:1两坐标联动,然后单坐标运动; 4)G00指令后不需给定进给速度,进给速度由参数设定。 5)G00的实际速度受机床面板上的倍率开关控制。
2.直线插补(G01)
书写格式:
G01 X/U Z/W
,C/R F ;
1)X/U Z/W
为目标点坐标;
2)G01指令一般作为加工行程;
3)G01可以单坐标运动,也可以两坐标联动。
4)F__为进给速度,可以是每分进给,亦可以是每转进给。
①用F指令刀具每分钟的进给量。在车床上常用G98指定。
②用F指令主轴每转的进给量,在车床上通常以G99方指 定。
3
任务引入 冲孔凸模零件,毛坯为φ20的棒料,材料:T10A;热处 理:HRC58~HRC62。
冲孔凸模
任务实施
一、数控车削常用夹具
数控车削常用夹具为卡盘,有三爪自定心卡盘、 四爪 单动卡盘、八爪单动卡盘(图中仅装了四个爪)。
三爪自定心卡盘
四爪单动卡盘
八爪单动卡盘
二、数控车削外轮廓常用刀具
采用模压断屑槽刀片的刀杆
3)通常要求M02/M30单独占一行。 4)FANUC系统中用M99表示子程序结束后返回主程序 。对于子程序结束指令M99,不一定要单独书写一行, 如上面程序中最后两行写成“G91 G28 Z0 M99;”也 是允许的。 5)SIEMENS系统中则通常用M17、M02或字符“RET”作 为子程序的结束标记。
第4章成形磨削夹具
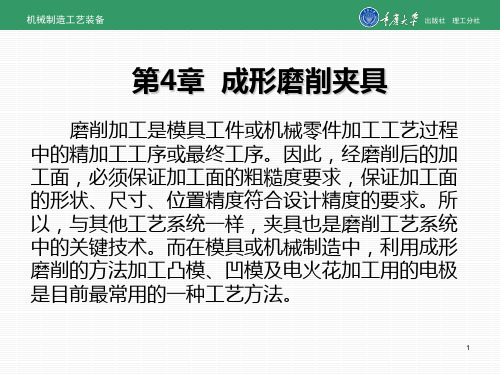
机械制造工艺装备
出版社 理工分社
图4.16 测量调整器
27
机械制造工艺装备
出版社 理工分社
图4.17 工序尺寸图
28
机械制造工艺装备
出版社 理工分社
图4.18 磨削工艺及夹具使用方法
29
机械制造工艺装备
出版社 理工分社
图4.18 磨削工艺及夹具使用方法
30
机械制造工艺装备
出版社 理工分社
25
机械制造工艺装备
出版社 理工分社
使用测量调整器、量块、百分表进行比较测量 的方法通常是:首先在测量平台上垫放适量高度P 的基础量块,然后调整测量平台的位置。通过百 分表对工件基准面和基础量块上表面的测量,使 两者的高度相等。当工件被测表面高于其基准面 时,在测量平台基础量块的上面再垫入量块组, 使百分表在量块组上表面与工件被测表面的读数 相同。这样,量块组的高度S就等于工件被测表面 至基准面的距离,量块的总高度为H=P+S。
15
机械制造工艺装备
出版社 理工分社
图4.10 磁性吸盘和平行导磁体
16
机械制造工艺装备
出版社 理工分社
图4.11 磁性吸盘和端面导磁体
17
机械制造工艺装备
出版社 理工分社
图4.12 导磁体装夹工件方法举例
18
机械制造工艺装备
出版社 理工分社
(2)精密平口钳 精密平口钳的结构如图4.13所示,主要由螺杆、 螺母、钳体、活动钳口与测量柱组成。钳体与活 动钳口,需淬火,并进行精密磨削、研磨。使钳 体 2侧面对底面及钳口的垂直度90°±1′。测量柱 在磨削斜面时,作比较测量用。精密平口钳装夹 工件的尺寸范围为60mm和80mm两种规格。 精密平口钳是装在磁力工作台上,并校正其钳 口平行或垂直于机床 x,y运动方向后使用。其作 用与用途有:
第四章凸面型宝石加工工艺
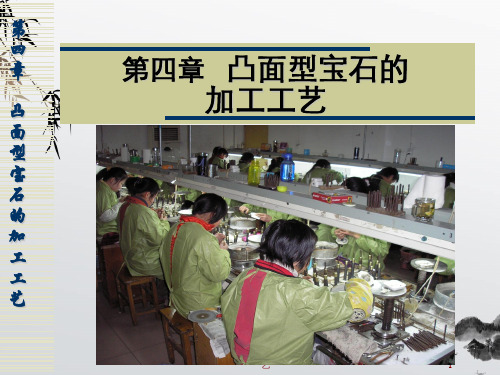
艺 粘接后,要等其自然冷却后再加工。
第四章凸面型宝石加工工艺
第
四 章
五、造型
凸
面 型 宝
将宝石坯料的顶部打磨成弧面,并要求基 本达到所设计的凸面形状。
石 成形步骤如下图所示:
的
加
工
工
艺
第四章凸面型宝石加工工艺
第 四 章
凸 面 型 宝 石 的 加 工 工 艺
第四章凸面型宝石加工工艺
第 四 章
凸
面 型
凸面型宝石的成形步骤
宝 操作方法:手握粘杆在砂轮机上打磨宝石
石 ,边打磨边转动,从边部逐层向中央打磨
的 加
成弧形。
工
工
艺
第四章凸面型宝石加工工艺
第 四 章
凸 面 型 宝 石 的 加 工 工 艺
第四章凸面型宝石加工工艺
第 四 章
凸 面 注意事项: 型 要根据宝石材料的性质不同选用合适的砂轮的 宝 粒度和转速; 石 要循序渐进,在任何方向上都不能一次过度打 的 磨,以免造成因某一部位磨削过多而影响整体 加 造型; 工 要为后续工序(细磨)保留少许加工余量,约 工 0.5mm; 艺 要充分保持水冷。
凸面型宝石设计的总原则是:保持和发挥宝石本身的优 点,去除或掩饰宝石的瑕疵,尽可能表现宝石美的品质
艺
,提高宝石的价值。
第四章凸面型宝石加工工艺
第
四 章
主要考虑如下因素
凸
面
型
宝 重量
石 的
特殊光学效应
加 颜色
工 工
瑕疵处理
艺
第四章凸面型宝石加工工艺
第
四 章
一、重量
凸 面 尽可能保有宝石成品的最大重量仍是体现凸面 型 型宝石价值的一个重要因素,高档宝石尤其如 宝 此。所以,在凸面型宝石的设计中要尽可能做 石 到料尽其用。方法是: 的 对于小块的宝石原料,宜依据原料的形状来考 加 虑设计加工成何种款式; 工 对于大块的宝石原料,要先考虑如何合理的分 工 割,然后对个体进行设计; 艺 在不影响宝石外观美感的前提下,可适当加厚
- 1、下载文档前请自行甄别文档内容的完整性,平台不提供额外的编辑、内容补充、找答案等附加服务。
- 2、"仅部分预览"的文档,不可在线预览部分如存在完整性等问题,可反馈申请退款(可完整预览的文档不适用该条件!)。
- 3、如文档侵犯您的权益,请联系客服反馈,我们会尽快为您处理(人工客服工作时间:9:00-18:30)。
工件的装夹方式:
夹具如图所示 组成部分:正弦分度头、尾座、底座
工件定位、安装在夹具中的方式有: 心轴装夹、双顶尖装夹
利用正弦头右侧的分度头,可控制工件 的回转角度,要求一般精度时可直接在分度盘 上读取,要求精度高时,可在垫板与正弦圆柱 间垫量块调节。 加工时,被磨表面的尺寸是采用比较测 量法测定的,测定依据是夹具中性线,用比较 测量器、量块、百分表找到比较测量面,当被 加工面与比较测量面等高时(即百分表读数一 致时),加工也就完成了。
采用CNC连续轨迹坐标磨削,可采同一 CNC磨削程序加工代码,以不同磨削用量、顺 次磨削凸模、凹模和卸料板型孔,以保证间隙。 另外,坐标磨床,还可以用来进行精密测量 和划线作业。
(2)坐标磨削原理
坐标磨床的磨削运动,见图7-30。其中:
1)磨头上的砂轮自转磨削运动,由高频电动机或压缩空 气驱动形成气动磨头。 2)磨头,则由电动机通过变速机构直接驱动主轴转动, 形成绕主轴转动的公转,与磨头自转合成行星运动,以 磨圆孔。 3)磨头还需具有上、下磨削运动。由液压或气压-液压 驱动主轴套筒,使磨头作上、下往复运动。 所以,坐标磨床除可进行内、外型孔、型面磨削以外, 还可以磨削孔内的键槽、清角等。
2)工件加工(型)面若在10mm×10mm以内,则可沿投影 于屏幕上的工件型面(也放大50倍)与放大50倍的描图样, 对照并移动砂轮架纵、横滑板磨去余量(见图7-24上虚线 处 )。 若型面> 10mm×10mm,则可逐段磨削成形,如图7-24 所示:先按图上1―2段曲线磨出工件上的1-2段型面;调整 工作台带动工件向左移动1010mm,并按图上2’-3段曲线 磨出工件上的2-3段型面;最后,向左、向上分别使工件移 动10mm,按图上3’-4段曲线磨出工件上的3-4段型面。
二、成形砂轮磨削法(仿形法):
成形砂轮磨削法(仿形法)的难点与关键点 是砂轮的修整。 常用的方法: 砂轮修整器修整(前图) 样板刀挤压 数控机床修整 电镀法
图3-19 修整砂轮角度的夹具 1—正弦尺座 2—金刚刀 3—滑块 4—齿条 5—齿轮 6—主轴 7—平板 8—侧板 9—正弦圆柱 10— 手轮 11—螺母 12—支座 13—底座
(如图)
样板刀挤压: 利用成形车刀挤压慢速旋转的砂轮将砂轮 修整成所需形状与尺寸。 此法的关键是利用电火花线切割机先加工 出成形车刀,然后再用车刀对慢速旋转的砂轮 挤压,修整出所需砂轮。
数控机床修整: 将砂轮安装在数控机床主轴上,金刚刀固定在刀 架(车床)或工作台(铣床)上,利用数控指令使金 刚刀相对于砂轮进给修整出成形砂轮。 电镀法: 此法与金刚石锉刀的制造方法相同,先加工钢的 轮坯,再用电镀法在轮坯表面镀一层金刚砂。 这种方法比较简单,但所得砂轮的耐用度比较低, 精度也不高。
具体工艺措施如下: 绘制放大图样时,比例和尺寸尽可能精细;线条 宜很细,一般需在精密绘图机上进行,线条细度为 0.05~0.08mm,手工绘制时,则为0.1~0.2mm。 同时,绘制放大图的材料要求随空气温度影响小, 变形小,图形精度高;牢固、易于保存。常用材料 与性能见表7―16。
磨削方法:
1、轨迹法:光曲磨床主要采用砂轮沿工件加工(型)面 连续展成磨削成形。其工艺过程为: 1)将工件的型面,放大50倍,采用精密绘图机绘制在 “描图样”上,并夹在屏幕4上;M9017A光曲磨床的 投影屏幕尺寸为500mm× 500mm,因此,其上只能 看到小于10mm×10mm的工件加工(型)面的轮廓。 若工件尺寸超过此尺寸范围,则可对型面进行分段,如 每段均放大50倍,并重叠绘制在同一幅描图上,见图724。并夹在屏幕上。
成形磨削加工精度可达IT5,粗 糙度Ra0.1μm;成形磨削可加工 淬硬件及硬质合金材料
成形磨削按加工原理可分为: 成形砂轮磨削法(仿形法) 夹具磨削法(范成法) 成形砂轮磨削法(仿形法): 将砂轮修整成与工件型面完全吻合的相反型 面,再用砂轮去磨削工件。
夹具磨削法(范成法): 加工时将工件装夹在专用夹具上,通过有 规律地改变工件与砂轮的位置,实现对成型面 的加工,从而获得所需的形状与尺寸。
三、夹具磨削法:
此法的核心是依据成形面的复杂程度选用 不同的夹具,使工件相对于高速旋转的砂轮移 动,从而加工出所需形面。 加工平面或斜面可用正弦精密平口虎钳和 正弦精密磁力台。 加工具有一个回转中心的工件可用正弦分 中夹具。 加工具有多个回转中心的工件可用万能夹 具。
(1)正弦精密平口钳和正弦精密磁力台 两种夹具的结构如 图3-22所示,都可用于加工平面或斜面,都具有正弦尺机 构,在底座与正弦圆柱间垫块规可使夹具体倾斜,以带动 工件倾斜指定的角度,最大倾斜角度为45°。 (2)正弦分中夹具 正弦分中夹具主要用于加工具有一个回 转中心的工件,如图3-24所示。 (3)万能夹具 万能夹具可加工具有多个回转中心的工件, 如图3-27所示。
3)为使磨削出的工件型面之间能光顺、平滑、 精确地连接,常采用按几何元素来进行分割,使 合理地进行分段磨削,见表7-13。
(2)切入法 即采用成形砂进行切入式磨削,成形砂轮的型 面须与工件加工(型)面完全吻合、精确一致。 因此在光曲磨床上采用切入法时亦需使用金刚 石和相关夹具精密修整砂轮成形。
第四章 凸、凹模型面成形磨削工艺
成形磨削工艺多用于模具刃口形状以及 凸、凹模拼块型面的成型加工,它们的 外轮廓为多条直线与圆弧所组成。如图
一、成形磨削概述
进行磨削时,需将外形轮廓分为若干直 线或圆弧段,然后,按一定顺序逐段磨 削成形,以达到图样的尺寸、形状及其 精度要求,这样的加工方式称为成形磨 削。
砂轮修整器修整: (1)砂轮角度的修整:在磨削工件的斜面时,采用角 度砂轮,角度砂轮是由平砂轮修整而成的圆锥部分, 修整时,砂轮由磨头带动传动,角度修整器上的金刚 刀相对砂轮轴线倾斜一定的角度来回往复移动对砂轮 修整,直至修成所需的锥面。(采用修整砂轮角度的夹具) (2)圆弧砂轮的修整 修整圆弧砂轮工具的结构虽有多种,但其原理都相同。
3)两凸圆弧面相连接时,当先磨削半径较大 的凸圆弧面;两凹圆弧面相连接时,当先磨削 半径较小的凹圆弧面。 4)应先磨削形状简单、操作方便的面。
五 成形磨削实例
1、单向正弦电磁夹具磨削实例
2、正弦分度磨削
采用正弦分中夹具装夹工件进行成形磨 削的方式。 适用于磨削具有一个回转中心的凸圆弧 面、多角体、分度槽等工件,工件一般 不带凸台。
图3-22 正弦精密平口钳和正弦精密磁力台 a)正弦精密平口钳1—底座 2、4—钳口 3—工件 5—夹紧螺栓6—正弦圆柱 7—块规组 b) 正弦精密磁力台1—磁性平台 2—正弦圆柱3—块规组 4—底座 a)正弦精密平口钳 1—底座 2、4—钳口 3—工件 5—夹紧螺栓 6—正弦圆柱 7—块规组 b)正弦精密磁力台 1—磁性平台 2—正弦圆柱 3—块规组 4—底座
二、坐标磨削工艺与机床
1、坐标磨基本原理与应用: (1)坐标磨削应用: 常用坐标磨床为立式、单柱坐标磨床。坐标磨床 的进给系统常采用机械传动由直流电机或直流伺服系 统驱动。因此,可进行连续轨迹磨削;需要时,还可 以作X、Y、Z坐标点位数控。 所以,坐标磨的控制常采用:手动和数控(NC)程 序控制两种方式。
图3-27
四、成形磨削的顺序
模具凸模、凹模拼块一般由多圆弧面和 多角度平面相互平滑、光顺的连接成封 闭的柱状、型孔等,即构成凸模、凹模 的刃口。(后图) 成型磨削时,根据工件形状与技术要求, 采用分段磨削,并在实际加工中,有时 会仿形法、范成法混合使用。
根据长期的实践与分析,在进行凸凹模拼 块成形磨削时应遵循下列规则: 1)先确定、磨削水平与垂直方向的基准 面;再顺次磨削与基准面相平行的加工 面,以及精度高或较大的加工面。 2)当平面与凹圆弧面相连接时,需先磨 削凹圆弧面,再顺次磨削平面;当平面 与凸圆弧面相连接时,需先磨削平面, 再顺次磨削凸圆弧面。
(2)工件装夹、定位可靠、精确 其定位方法和顺序为: 1)将放大图的十字中心线,对准机床光屏上的中心标记; 即表明十字中心线已与机床工作台的纵、横运动方向 平行。 2)将装夹工件的专用夹具的测量边、精确对准放大 图样的十字中心线或分割线。 3)当工件尺寸小于10mm×10mm时,可直接用工件 外形精确对准放大图基准线进行定位。
当工件尺寸大,需分段磨削 时,工件的定位方法与顺序 为:见图7-25,先使工件上 的拼合面b,对准放大图上 的拼合线b';此后,移动工作 台,使 工件外形基准面a,对 准放大图上a‘中心线;再用 尺寸为A的量块垫入机床 纵向滑板,以控制机床纵向 的移动距离。
数控成型磨削与坐标磨削工艺
一、数控成型磨削工艺与机床
2)多回转中心定位磨削
多回转中心定位磨削会降低磨削精度
4、成形磨削工艺计算:
成形磨削之前需根据凸模与凹模拼块设计图进 行磨削工艺设计和工艺计算,并作出磨削工艺 图。 成形磨削工艺设计和工艺计算的主要内容有: 1)根据磨削规则,分析工件形状与尺寸精度 要求进行合理的分段,并确定各段的磨削顺序。
坐标磨削精度与质量: 1)最大磨削速度:Vmax=100000r/min; 2)定位精度:在30mm长度内为0.8um;在全行程内为 2.3um。 3)NC连续轨迹磨削的形状精度:在全行程内为7.5um。 4)表面粗糙度为:一般磨削加工时达Ra(0.8~o.4)um;精 细加工时达:Ra0.2um。 所以,坐标磨削主要应用精密冲裁模的凸模、凹模与卸料 板型孔的精密加工。