铸造生产过程控制程序
铸造工艺工作程序
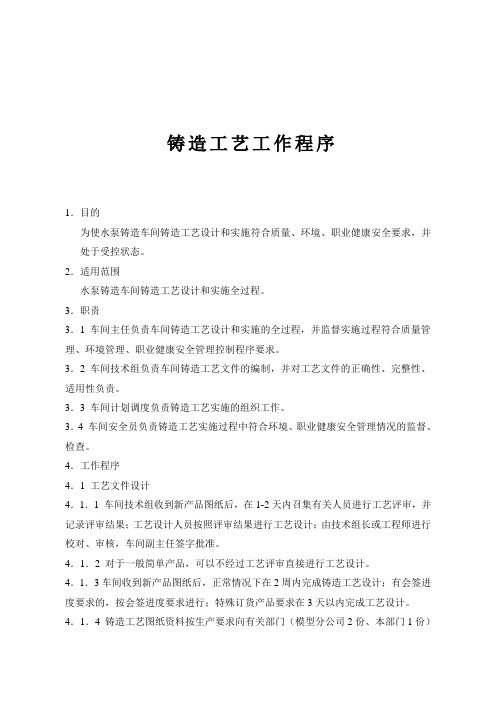
铸造工艺工作程序1.目的为使水泵铸造车间铸造工艺设计和实施符合质量、环境、职业健康安全要求,并处于受控状态。
2.适用范围水泵铸造车间铸造工艺设计和实施全过程。
3.职责3.1 车间主任负责车间铸造工艺设计和实施的全过程,并监督实施过程符合质量管理、环境管理、职业健康安全管理控制程序要求。
3.2 车间技术组负责车间铸造工艺文件的编制,并对工艺文件的正确性、完整性、适用性负责。
3.3 车间计划调度负责铸造工艺实施的组织工作。
3.4 车间安全员负责铸造工艺实施过程中符合环境、职业健康安全管理情况的监督、检查。
4.工作程序4.1 工艺文件设计4.1.1 车间技术组收到新产品图纸后,在1-2天内召集有关人员进行工艺评审,并记录评审结果;工艺设计人员按照评审结果进行工艺设计;由技术组长或工程师进行校对、审核,车间副主任签字批准。
4.1.2 对于一般简单产品,可以不经过工艺评审直接进行工艺设计。
4.1.3车间收到新产品图纸后,正常情况下在2周内完成铸造工艺设计;有会签进度要求的,按会签进度要求进行;特殊订货产品要求在3天以内完成工艺设计。
4.1.4 铸造工艺图纸资料按生产要求向有关部门(模型分公司2份、本部门1份)提供。
铸造工艺对下道工序有要求的以书面形式向下道工序反馈。
4.1.5 铸造文件设计要严格按照公司有关技术标准规定执行。
4.2 工艺文件管理4.2.1 车间资料员负责图纸、技术文件的收发、归档、管理和更改。
4.2.2 车间资料员签收图纸资料后,加盖本车间专用标识章,并填写《收图登记》,分类存放。
4.2.3 车间技术组收到改图通知后,按要求更改,保证零件图、工艺图、工装图的有效性。
对于涉及到铸造工艺整改、模型修改的,应通知工艺设计人员、生产班组进行相应处理。
4.2.4 铸造工艺改图由工艺设计人员对归档腊底的改动,保证底图工艺的一致性。
4.2.5 车间的图纸资料一律不外借。
外部门人员借用需经主管主任批准,并填写《借阅登记》,当日归还;特殊情况当日不能归还的,需经车间主任签字批准后,限期归还。
铸造生产流程中的主要步骤
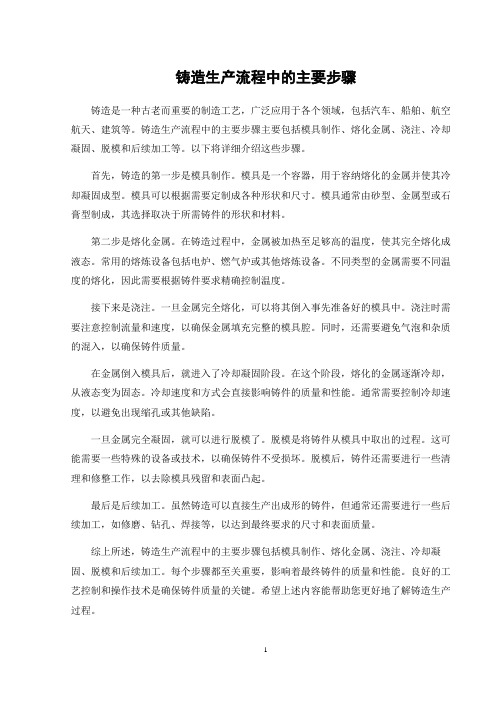
铸造生产流程中的主要步骤铸造是一种古老而重要的制造工艺,广泛应用于各个领域,包括汽车、船舶、航空航天、建筑等。
铸造生产流程中的主要步骤主要包括模具制作、熔化金属、浇注、冷却凝固、脱模和后续加工等。
以下将详细介绍这些步骤。
首先,铸造的第一步是模具制作。
模具是一个容器,用于容纳熔化的金属并使其冷却凝固成型。
模具可以根据需要定制成各种形状和尺寸。
模具通常由砂型、金属型或石膏型制成,其选择取决于所需铸件的形状和材料。
第二步是熔化金属。
在铸造过程中,金属被加热至足够高的温度,使其完全熔化成液态。
常用的熔炼设备包括电炉、燃气炉或其他熔炼设备。
不同类型的金属需要不同温度的熔化,因此需要根据铸件要求精确控制温度。
接下来是浇注。
一旦金属完全熔化,可以将其倒入事先准备好的模具中。
浇注时需要注意控制流量和速度,以确保金属填充完整的模具腔。
同时,还需要避免气泡和杂质的混入,以确保铸件质量。
在金属倒入模具后,就进入了冷却凝固阶段。
在这个阶段,熔化的金属逐渐冷却,从液态变为固态。
冷却速度和方式会直接影响铸件的质量和性能。
通常需要控制冷却速度,以避免出现缩孔或其他缺陷。
一旦金属完全凝固,就可以进行脱模了。
脱模是将铸件从模具中取出的过程。
这可能需要一些特殊的设备或技术,以确保铸件不受损坏。
脱模后,铸件还需要进行一些清理和修整工作,以去除模具残留和表面凸起。
最后是后续加工。
虽然铸造可以直接生产出成形的铸件,但通常还需要进行一些后续加工,如修磨、钻孔、焊接等,以达到最终要求的尺寸和表面质量。
综上所述,铸造生产流程中的主要步骤包括模具制作、熔化金属、浇注、冷却凝固、脱模和后续加工。
每个步骤都至关重要,影响着最终铸件的质量和性能。
良好的工艺控制和操作技术是确保铸件质量的关键。
希望上述内容能帮助您更好地了解铸造生产过程。
1。
机械制造业工艺流程

机械制造业工艺流程机械制造业是制造业的一个重要分支,主要涉及到机械、设备、工具等产品的生产制造。
在机械制造业中,工艺流程是非常重要的一个环节,它关系到产品的质量、生产效率以及成本控制。
下面将详细介绍机械制造业的工艺流程。
一、铸造工艺流程铸造是制造机械零部件的重要工艺之一,它的主要流程包括:模具制造、熔炼、浇注、冷却、砂型拆除、修整和检查等环节。
其中,模具制造是铸造工艺的第一步,它是根据零件图纸进行模型制作,以便后续的砂型制作。
在铸造工艺中,熔炼是至关重要的一个环节,它需要对原材料进行加热熔化,生成熔融金属液体。
然后,将熔融金属液体倒入巨大的砂型中,等待冷却凝固。
在冷却过程中,铸造零件的形状和尺寸会发生变化,因此需要进行修整。
最后,对铸造零件进行检查,以确保其质量达到标准。
二、机加工工艺流程机加工是一种通过机床进行精密加工的工艺,它主要包括:设计、准备、夹紧、加工、测量和检验等环节。
在机加工工艺中,首先需要根据零件图纸进行程序设计,确定机床的加工轨迹和刀具的选择。
在机床加工过程中,加工工件需要夹紧在机床上,以便进行精密加工。
然后,通过机床上的刀具进行切削加工,形成零件的轮廓和尺寸。
在加工过程中,需要进行测量和检验,以确保零件的质量符合要求。
三、焊接工艺流程焊接是一种将金属材料通过熔化的方法进行连接的工艺,它主要包括:准备、对接、焊接、冷却、打磨和检验等环节。
在焊接工艺中,首先需要对要连接的金属材料进行处理,以保证焊接的牢固度和质量。
在焊接过程中,需要将金属材料加热至熔点,使其熔化,并加入焊接材料,使其融合在一起。
焊接完成后,需要进行冷却和打磨,以确保焊接部位平整光滑。
最后,对焊接部位进行检验,以确认其质量符合要求。
四、表面处理工艺流程表面处理是一种通过对机械零部件表面进行化学、物理或电化学处理,以改变其表面性质和外观的工艺。
它主要包括:清洗、除锈、喷涂、电镀和抛光等环节。
在表面处理工艺中,首先需要将机械零部件进行清洗,以去除表面的污垢和油脂。
IATF16949生产过程控制程序(含附属表单)

XX 汽车部件股份有限公司生产过程控制程序文件编号:XX2.0806—20202020年01月10日发布2020年01月11日实施1 目的本程序规定了生产和服务提供过程中的人、机、料、法、环各因素的控制方法,确保生产和服务过程在受控状态下进行,以保证产品质量和服务质量的提供满足要求。
2 范围适用于公司所有产品的生产和服务提供的过程处于受控状态。
3 术语和定义3.1特殊过程:指产品质量不能通过后续的监视或测量加以验证的过程;产品质量进行破坏性试验或采取复杂、昂贵的方法才能测量或只能进行间接监视的过程;不合格的质量特性要在产品使用后才能暴露的过程。
如:铸造铁水熔炼、铝合金熔炼,轴淬火处理等。
3.2 关键过程:对形成产品质量起决定作用的过程,一般包括形成关键、重要特性的过程。
如:精镗壳体轴承孔,泵轴探伤,加工进/排气管大面平面度等。
3.3 生产停工:制造过程空闲的情况,时间跨度可从几个小时到几个月不等。
3.4作业准备验证:指一种推荐的方法。
为应用统计过程控制而生产足够的产品以组成分组数。
对零件进行测量,并将结果绘制成控制图表。
如果这些测量结果落在控制极限区域的中间1/3范围内(如X-R控制图、彩虹图等),则作业准备可获批准。
如果测量结果落在其余控制区域的2/3范围内,应对第二分组零件进行测量并绘制控制图表;如结果仍落在其余控制区域的上述2/3的范围内,则作业准备应作调整并重复过程;如这些测量结果落在中间1/3控制区域内,则生产作业准备获得批准。
3.5制造:制作或加工的过程。
包括生产原材料、生产件或服务件、装配或热处理、焊接、涂装、电镀或其他表面处理服务。
3.6现场:发生增值的制造过程的场所。
3.7外部场所:支持现场并且为非生产过程发生的场所。
3.8支持功能:对同一组织的一个(或多个)制造现场提供支持的(在现场或外部场所进行的)非生产活动。
4 职责4.1制造部是生产和服务提供控制的归口管理部门。
a)负责编制具体的生产作业计划及组织实施;b)负责组织相关部门对生产和服务所有过程的确认;c)负责策划生产和服务提供的条件,包括:保持生产环境的管理;保持安全文明生产;提供适宜的设备,做好设备保养、预防性和预见性的维护等管理;负责实施生产线的布局,配置合适的流转器具和工位器具,组织流转器具和工位器具制造。
砂型铸造流程
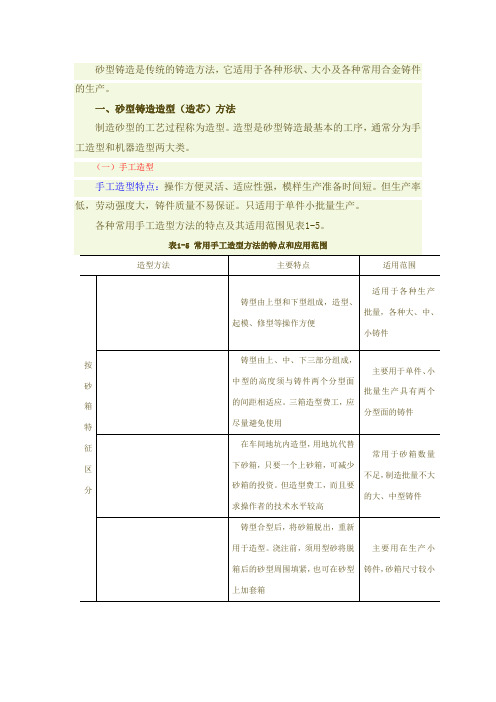
最小铸出孔的参考数值见表1-7。对于零件图上不要求加工的孔、槽以及弯曲孔
等,一般均应铸出。
表1-7 铸件毛坯的最小铸出孔(mm)
生产批量
大量生产 成批生产 单件、小批量生产
最小铸出孔的直径 d
灰铸铁件
铸钢件
12~15
—
15~30
30~50
30~50
50
2. 起模斜度 为了使模样(或型芯)易于从砂型(或芯盒)中取出,凡垂
注意:为了提高型芯的刚度和强度,需在型芯中放入芯骨;为了提高型芯的 透气性,需在型芯的内部制作通气孔;为了提高型芯的强度和透气性,一般型芯 需烘干使用。
二、砂型铸造工艺设计 目的:为了获得健全的合格铸件,减小铸型制造的工作量,降低铸件成本, 在砂型铸造的生产准备过程中,必须合理地制订出铸造工艺方案,并绘制出铸造 工艺图。 铸造工艺图:在零件图中用各种工艺符号表示出铸造工艺方案的图形,其中 包括:铸件的浇注位置;铸型分型面;型芯的数量、形状、固定方法及下芯次序; 加工余量;起模斜度;收缩率;浇注系统;冒口;冷铁的尺寸和布置等。铸造工 艺图是指导模样(芯盒)设计、生产准备、铸型制造和铸件检验的基本工艺文件。 依据铸造工艺图,结合所选造型方法,便可绘制出模样图及合箱图。图1-19为支 座的铸造工艺图、模样图及合箱图。
式中 ——模样或芯盒工作面的尺寸,单位为 mm; ——铸件的尺寸,单位为 mm。
通常,灰铸铁的铸造收缩率为0.7%~1.0%,铸造碳钢为1.3%~2.0%,铸造锡青 铜为1.2%~1.4%。
4. 型芯头 型芯头可分为垂直芯头和水平芯头两大类,如图1-30所示。
图1-30 型芯头的构造 a)垂直芯头 b)水平芯头 (四)铸造工艺设计的一般程序
铸造工艺设计:在生产铸件之前,编制出控制该铸件生产工艺的技术文件。 铸造工艺设计主要是画铸造工艺图、铸件毛坯图、铸型装配图和编写工艺卡片等, 它们是生产的指导性文件,也是生产准备、管理和铸件验收的依据。因此,铸造 工艺设计的好坏,对铸件的质量、生产率及成本起着决定性的作用。
铝棒铸造安全指引及工艺操作规程

铝合金圆铸锭(铝棒)等水平密排热顶式铸造设备操作规程一、等水平密排热顶铸造安全指引1、操作人员注意事项2、铸造设备注意事项3、铸造用水4、铸造环境,深井与地面情况要求5、铸造工具要求6、铸造过滤要求7、天车及吊棒工具二、等水平密排热顶铸造工艺规程1、铸造工艺规程2、铸造操作要求3、铝棒质量控制及问题解决要点4、铸造机的保养方法及注意事项5、针对石墨环更换步骤及维护细节把握6、铸造工艺参数,合理运用数据参考分析等水平密排热顶铸造安全指引一.操作人员注意事项1、所有操作人员必须经过铸造安全及技能培训并签订安全协议。
2、所有操作人员必须体检视力、听力达标,无身体疾病。
3、所有操作人员必须穿戴好以下安全用品才能上岗:高温鞋、高温手套、牛仔布工作服,避免烫伤。
夜间操作人员必须穿戴反光服,以免受到其他伤害。
4、铸造之前点检确认铸造准备工作是否到位,铸造过程中,必须最少有3人在场看管并对应站在指定位置。
二.铸造设备注意事项1、流槽、分流盘、套管及引锭头、使用工具必须干燥。
2、每次铸造前必须铸造盘进行试水,通入铸造机正常铸造水量,检查水帘的成形情况及溢水孔有否漏水,溢水孔如有漏水,及时处理好再次确认后才能铸造。
3、铸造前引锭座必须上升至正常起动位置并调好水平,提前检查引锭头是否有卡死及脱落现象。
4、铸造开水泵前,必须将减压排水阀打开,直至铝液全部充满套管后才能关闭,以免“反水”造成爆炸。
5、若铸造机长时间不用或由于天气潮湿造成引锭头生锈,利用黄油做好防锈措施,则再次铸造前检查全部引锭头活动。
6、铸造机钢丝绳出现起毛或断股必须更换,以免铸造时断裂事故。
7、铸造机牵引钢丝绳轴承定期检查,损坏及时更换,每年对所有轴承进行统一更换一次。
8、流槽、分流盘、套管出现破损及时修补,情节严重的及时更换,以免造成渗铝水情况发生。
9、整个铸造系统定期维护保养,结晶器定期拆开清理水眼,确保冷却水水帘均匀成形。
三.铸造用水1、铸造用水必须有独立水泵,经过小于1毫米过滤,水的PH值约为7。
铸造生产规章制度范文模板
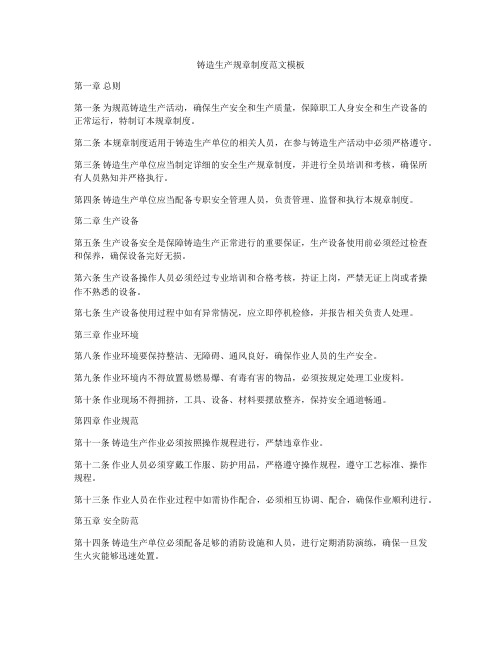
铸造生产规章制度范文模板第一章总则第一条为规范铸造生产活动,确保生产安全和生产质量,保障职工人身安全和生产设备的正常运行,特制订本规章制度。
第二条本规章制度适用于铸造生产单位的相关人员,在参与铸造生产活动中必须严格遵守。
第三条铸造生产单位应当制定详细的安全生产规章制度,并进行全员培训和考核,确保所有人员熟知并严格执行。
第四条铸造生产单位应当配备专职安全管理人员,负责管理、监督和执行本规章制度。
第二章生产设备第五条生产设备安全是保障铸造生产正常进行的重要保证,生产设备使用前必须经过检查和保养,确保设备完好无损。
第六条生产设备操作人员必须经过专业培训和合格考核,持证上岗,严禁无证上岗或者操作不熟悉的设备。
第七条生产设备使用过程中如有异常情况,应立即停机检修,并报告相关负责人处理。
第三章作业环境第八条作业环境要保持整洁、无障碍、通风良好,确保作业人员的生产安全。
第九条作业环境内不得放置易燃易爆、有毒有害的物品,必须按规定处理工业废料。
第十条作业现场不得拥挤,工具、设备、材料要摆放整齐,保持安全通道畅通。
第四章作业规范第十一条铸造生产作业必须按照操作规程进行,严禁违章作业。
第十二条作业人员必须穿戴工作服、防护用品,严格遵守操作规程,遵守工艺标准、操作规程。
第十三条作业人员在作业过程中如需协作配合,必须相互协调、配合,确保作业顺利进行。
第五章安全防范第十四条铸造生产单位必须配备足够的消防设施和人员,进行定期消防演练,确保一旦发生火灾能够迅速处置。
第十五条铸造生产单位必须配备足够的急救设备和急救人员,进行定期急救培训,确保在紧急情况下能够及时救治伤者。
第十六条铸造生产单位必须加强安全宣传教育,定期组织安全演讲和安全培训,提高全员的安全意识和自我保护能力。
第六章质量管理第十七条铸造生产单位必须遵守国家标准和行业规范,严格控制生产工艺,确保产品质量符合标准要求。
第十八条铸造生产单位必须严格按照工艺要求进行操作,不得随意更改工艺参数,严格控制产品的合格率。
铸造过程确认程序

文件制修订记录1.0目的规定了特殊过程的确认与控制要求及其工作程序。
对特殊工序的确认做出安排,确保能证实过程实现所策划结果的能力。
2.0范围本程序适用于铸造特殊工序的确认,确保特殊过程的质量控制。
3.0职责3.1 生产技术部负责特殊过程的确认及其控制。
3.2 检验部门参与特殊过程的确认及其控制工作,并对加工产品或零件(毛坯)检查验收的质量负责。
3.3 设备部门负责对特殊过程所用的设备进行最初鉴定和定期检定。
3.4 计量部门负责对特殊过程所用的仪器、仪表、量具等进行定期校验。
3.5 各生产单位负责做好特殊过程的确认及其控制的具体工作并按要求填写操作记录。
4.0程序4.1 特殊过程确认控制流程图4.2 特殊过程确认的程序特殊过程经确认后,采用该过程加工的产品方可投入生产,需确认的具体项目、内容和要求按以下程序进行:4.2.1 按特殊过程的工艺类别,生产单位选取有代表性的典型零件或试样(涉及特殊过程关、重特性的关键件、重要件均应选取),申请对工艺过程进行特殊过程确认,经生产技术部认可后,工艺员填写“特殊过程确认表”。
需要时,生产技术部可下达特殊过程确认项目的技术通知。
生产单位技术负责人组织工艺室、检验室及其过程操作人员、设备管理人员共同参加对过程的确认。
4.2.2 按照工艺文件确定的设备、工艺参数、步骤及检验项目,逐项进行验证。
操作人员对零件加工的过程要详细、如实进行记录, 检验人员应对检验项目逐项进行检验。
4.2.3 工艺员、操作人员、检验人员按实际验证过程填写“特殊过程确认表”,提供过程记录,逐级签字,对该过程能够达到目的及结果的能力给出结论性意见,最终经总冶金师批准,即完成该项过程的确认。
4.3 铸造过程确认的主要工艺参数和检验项目a)主要工艺参数:炉料成分、预热温度、熔炼时间、模具温度、熔剂用量、出炉温度及浇铸温度等;b)主要检验项目:表面质量、铸造尺寸、化学成分、机械性能、针孔等级、荧光检查或磁粉探伤、X射线检查等。
- 1、下载文档前请自行甄别文档内容的完整性,平台不提供额外的编辑、内容补充、找答案等附加服务。
- 2、"仅部分预览"的文档,不可在线预览部分如存在完整性等问题,可反馈申请退款(可完整预览的文档不适用该条件!)。
- 3、如文档侵犯您的权益,请联系客服反馈,我们会尽快为您处理(人工客服工作时间:9:00-18:30)。
4.2.10设备的控制 4.2.10.1车间主任负责车间设备的使用管理制度的制定修改和完善,并 保证其正确性和适用性。设备员和设备使用人员每日做点检、巡检,认 真填写检查和报修记录并按要求做好设备的一保和二保工作。 4.2.11废液、废气、噪声、固体废弃物的控制 4.2.11.1车间安全员按照《废液、废气、噪声、固体废弃物控制程序》 对车间生产过程中产生的废液、废气、噪声、固体废弃物进行控制和妥 善处置。 4.2.12废液、废气、噪声、固体废弃物的控制 4.2.12.1车间主任按照《职业健康安全/环境运行控制程序》对车间生 产过程中职业健康安全及环境进行控制。 5.文件 文件控制程序 记录控制程序 不合格品控制程序 铸造工艺工作程序 铸件清理标准 职业健康安全/环境运行控制程序 废液、废气、噪声、固体废弃物控制程序 6.记录 收图登记 改图通知签收与更改记录 借阅登记 型砂检验报告单 开炉记录 熔炼记录 浇注记录表
成分单为铸件验收依据。 4.2.6.5炉前控制人员每包取样浇注试块、试棒,指导炉后操作,控制 铝水质量。每天浇注试样,进行机械性能试验和化学成分分析;铸造检 查人员依据<<机械性能试验报告单>>验收铸件;化学成分单为熔炼提供 配料依据。 4.2.6.6浇注前浇注工要按工艺要求测温,温度合适后方可开始浇注, 温度低于下限时停止浇注。浇注结束后,由炉长或冶炼人员填写《熔炼 浇注记录表》,并由炉长确认,并对浇注完后的压箱铸件做好产品名 称、材料、浇注时间等标识。 4.2.6.7对于车间重点铸件熔炼技术员及班长负责与工艺技术员协商共 同确定熔炼浇注工艺。如:浇注速度,浇注温度并确定在铸造工艺文件 中,熔炼技术员和班长应监督检查熔炼浇注的质量,对出现的质量问题 要认真分析,提出解决办法,并做出相应的质量记录。 4.2.6.8按照车间计划调度员的生产指令组织生产,执行熔炼工作标准 及工艺守则。 4.2.6.9按照公司发材质标准配料、熔炼,班长要保证每炉次,每包次 化学成分合格。 4.2.6.10操作过程或操作结束后,班长或熔炼人员认真填写熔炼记录, 浇注记录,并记录汇总车间留存。 4.2.7打箱、落砂工序的控制 4.2.7.1按《铸件清理工艺规程》之3.1~3.7关于铸件打箱、落砂的规 定进行操作,每日检查落砂设备,输送设备是否正常,做好日常保养。 4.2.7.2铸件按压箱时间打箱落砂,一般不允许提前开箱,并严格按工 艺执行调度指令。 4.2.7.3打箱落砂后的铸件按材质不同分别堆放,严禁混杂,回收料作 好标识。 4.2.8铸件清理工序的控制 4.2.8.1严格执行《铸件清理工艺规程》,每日检查清砂设备,做好日 常保养。 4.2.8.2清理完的铸件经检查员检查合格后根据要求分别送下工序或涂 漆。 4.2.9搬运和入库工序的控制 4.2.9.1准备组负责生产所需各种原材料的运送。铸铁件清理检查合格 按要求刷漆入毛坯库;铸钢件毛坯清理合格后转至机加工车间热处理, 处理合格后转回车间抛丸清理入毛坯库;在搬运和入库过程中要认真清 点数目,并填写转序票或入库票;搬运及运输过程中严禁磕碰划伤。
试结果记录备案。 4.2过程控制 4.2.1图纸资料的控制 4.2.1.1车间技术组负责图纸、技术文件的收发、归档、管理和更改。 4.2.1.2车间技术组签收图纸、资料后,加盖本车间专用标记章,填写 《收图登记》,分类放置。 4.2.1.3车间技术组收到改图通知后,按要求更改,保证零件图、工艺 图、工装图的有效性,做出更改标识并通知到相关技术人员。车间技术 组对车间图纸、资料的正确性、完整性负责,保证在生产过程中使用的 图纸资料为有效版本。 4.2.1.4归口本部门管理的定型产品工改进、工装设计及新增零件的 工艺、工装设计、履行审核、批准手续。 4.2.1.5车间的图纸、资料一律不外借,外部门人员借用需经主管主任 批准,并填写《借阅登记》,当日归还,特殊情况当日不能归还的,需 经车间主任签字批准限期归还。 4.2.2工艺设计控制 4.2.2.1车间技术组负责铸件铸造工艺的编制,并对其正确性、适用性负 责,主管技术人员校对、审核、标准化后,主管主任签字批准,并正确 执行冶炼工艺。 4.2.2.2根据生产要求,图纸资料要向相关部门(模型分公司、生产技 术部和本部门)提供相应的图纸资料。 4.2.2.3工艺设计要严格按照公司的有关标准规定执行。 4.2.3原材料控制 4.2.3.1车间所有领用的原材料必须符合《铸造用金属原材料》、《铸 造用辅助原材料》、《造型用原材料》的要求,不合格品不能领用,并 及时向有关部门反馈。 4.2.3.2运料人员按领料单、配料单领取各种原材料送至各班组或指定 的位置存放,要有标识。 4.2.3.3对每批原材料,由质量管理部人员按公司规定取样送中心化验 室和理化室化验分析,以文字报告的形式将原辅材料的质量信息反馈到 质管部、生产技术部、铸造车间。车间做到不领、不用不合格品。 4.2.4配砂工序控制 4.2.4.1每班生产前,要检查配砂设备是否正常,根据当日生产调度的 安排配足当日或次日的造型用砂。 4.2.4.2型砂配制过程中,操作者要严格遵守《型砂制备工艺规程》, 不得随意改变配方。
4.2.4.3生产所需特种砂由技术员下达专用配方后方可生产。 4.2.4.4型砂试验员每天取样检测,湿型砂每机检测,树脂砂、再生砂 抽测,按砂种不同做型砂性能检测,填写《型砂检验报告单》,一般情 况下,湿型砂检测湿透、湿压、水分,合脂砂检测湿压,树脂砂检测抗 拉,再生砂检测微粉、砂温、灼减量。 4.2.4.5技术组负责分析型砂在造型过程中或铸件浇注后所出现问题的 原因,与造型主管技术员商讨后,提出改进后的配砂工艺及配方,并记 录在《型砂检验报告单》的“试验记录”一栏中并签字。 4.2.5造型工序控制 4.2.5.1生产前由铸造技术员根据生产计划编制重要铸件的铸造作业指 导书,保证其正确性、适用性。 4.2.5.2生产前检查模型是否完整无损、符合使用要求,并校验模型的 关键部位尺寸,生产班组长与准备组联系准备砂箱、冷铁、芯铁等所需 物品。 4.2.5.3每日生产前要检查造型、制芯设备是否正常,做好日常保养。 4.2.5.4生产过程中严格遵守造型工艺守则。 4.2.5.5严格执行铸件首件予投制度,首件合格方可投入生产,避免造 成成批废品。铸造过程如遇生产周期太短 ,没有时间进行首件试制的 特殊情况时,如车间认为铸造工艺可靠时,可以直接投产。如车间认为 铸造工艺需评审时,可由车间召集有关部门评审后作出决定。 4.2.5.6每日填写浇注标牌,铸件上要有零件号、材质号、生产日期号 及班组序号。 4.2.5.7由专门的造型工序巡检人员进行工序检查,并填写《型芯巡检 记录》。 4.2.6熔炼、浇注工序的控制 4.2.6.1各熔炼浇注班组每日按车间调度员的生产指令,熔炼相应牌号 的铸件,操作过程认真执行《熔炼工艺规程》、。 4.2.6.2操作工开炉前认真检查炉上料设备、电炉设备及电器部分、水 泵等,做好开炉前的准备工作,发现问题应及时通知维修中心修理,不 得带病运行。 4.2.6.3炉料管理员根据当日产品材质及浇注吨位,按公司发材质标准 计算各种炉料所需数量,由运料工将炉料运至炉后,并挂上炉料种类标 牌。 4.2.6.4熔炼过程中由班长或熔炼人员填写《熔炼记录》,铸件每炉取 光谱分析化学成分试片,待化学成分合格后方可出炉,浇注铸件,并由 班长确认。电炉续料后按新炉号计,相应填写记录,并重新取样。化学
铸造生产过程控制程序
1.目的 为使产品铸件的整个生产过程的质量、环境、职业健康安全处于受控状 态。 2.适用范围 铸造车间所生产的本公司铸件的生产全过程。 3.职责 3.1车间主任负责各工序的生产管理,组织贯彻实施质量管理、环境管 理、职业健康安全管理各控制程序,对铸件生产中的质量、环境、职业 健康安全负责。 3.2车间计划调度员根据公司生产技术部下达的生产指令安排组织生产 活动。 3.3车间技术组负责编制工艺文件,并对工艺文件的正确性、完整性、 适用性负责。 3.4车间安全员负责车间生产的环境管理和职业健康安全管理的日常工 作。 3.5各班组长对本班组的产品质量、生产作业计划及进度、环境管理、 职业健康安全管理的完成情况负责。 4.工作程序 4.1过程准备 4.1.1车间计划调度员按照生产技术部下发的项目计划编制各班组的生 产计划,及时下发到各班组,完成调度指令兑现率,准备好各种工装器 具及原材料。 4.1.2车间生产所需各种工装器具及原材料放在有明显标识的指定区 域,由车间统一管理。 4.1.3车间技术组由专人负责管理图纸和技术资料,进行分类、标识、 定址存放,建立文件资料目录及管理规定。 4.1.4技术组的技术人员根据当月车间生产计划准备技术资料、图纸, 并保证这些资料正确、清晰、完整、有效。 4.1.5原料、辅料和工艺装备上场前有关人员应检验其是否符合规定要 求,检验结果应记录并明确标识。 4.1.6车间设备员要做好设备的日常管理和检查,其结果应记录备案。 4.1.7操作者上岗前应经过培训,培训合格后持证上岗,特殊过程(熔 炼、浇注、造型、焊接、热处理、机动车司机)必须经过专门培训,考