三切削刃BTA深孔钻钻削过程研究
BTA深孔钻结构及加工原理要点

BTA深孔钻的结构特点及加工原理要点bta深孔钻是内排屑深孔钻的一种典型结构,它是在单刃内排屑深孔钻的基础上改进而成,其切削刃呈双面错齿状,切屑从双面切下,并经双面排屑孔进入钻杆排出孔外。
bta深孔钻切削力分布均匀,分屑、断屑性能好,钻削平稳可靠,钻削出的深孔直线性好。
1、BTA深孔钻的结构特点BTA深孔钻具有以下结构特点:(1)刀体上分布有外刃刀片、中刃刀片、内刃刀片、导向块和双面排屑孔,并通过刀体上的浅牙多头矩形螺纹与空心钻杆联接。
(2)钻芯部分由内刀刃代替了麻花钻的横刃,从而克服了麻花钻横刃较长、轴向阻力较大的缺点;由于钻芯相对于钻孔轴心线偏移了一段距离,加工时钻芯处刀刃低于中心处刀刃,因此会形成一个导向芯柱,使钻头具有较好的导向性,钻孔时不易偏斜,该导向芯柱增长到一定长度后会自行折断并随切屑一起排出。
(3)主刀刃采用非对称的分段、交错排列形式,可保证分屑可靠,并避免用整体硬质合金刀片磨削卷屑槽、分屑槽时易产生裂纹的情况。
(4)刀片材料可采用几种不同牌号的硬质合金,以适应各部分结构对耐磨性和强度的不同要求,如钻芯部分切削速度低、切削力大,在切屑挤压作用下易发生崩刃,可选用韧性较好的硬质合金刀片;钻头外缘部分则可选用耐磨性较好的硬质合金刀片。
2、BTA深孔钻的加工原理BTA深孔钻在普通车床上的工作情况:被加工工件由车床大拖板上的v形铁定位并用螺栓压板夹紧。
钻孔加工时,钻杆由主轴内的专用夹头夹紧并在主轴带动下旋转,工件则由大拖板带动作进给运动。
机床工作台上安装了进液器,并通过o形密封圈与工件左端面密封连接。
加压切削液由进液器的进液口注入,经过钻杆外径与孔壁间的缝隙流入切削区,对进行冷却,切屑随同切削液一起由钻杆内孔通过专用夹头的出液口从排液箱排出。
切削液可采用浓度5%的乳化液;切削用量可选用:v=60~90m/min,s=0.035~0.23mm/r。
由于钻杆细长,容易变形,因此在机床导轨上安装了活动中心支承,可对钻杆的任意位置进行支承。
BTA深孔钻削智能纠偏技术研究

0 3 0 0 5 1 ; 2 . 西安工业大学 , 陕西 西安 7 1 0 0 3 2 )
摘
要: 基 于 目前 深 孔钻 削过源自程轴 线偏 斜技 术难 题 , 针对 B T A ( B o r i n g a n d T r e p a n n i n g A s s o c i a t i o n ) 深 孔钻 削过 程 出现 走偏
U n i v e r s i t y , S h a n x i X i ’ a n 7 1 0 0 3 2 , C h i n a )
Ab s t r a c t : A c c o r d i n g t o t h e c u r r e n t t e c h n i c a l p r o b l e m s o fa x i s d e v i a t i o n d u r i n g d e e p - h o l e d r i l l i n g p r o c e s s i n g , i n o r d e r t o s o l v e t h e p h e n o m e n o n f o d e v i ti a o n i n B T A ( B o r i n g a n d T r e p a n n i n g A s s o c i a t i o n ) d e e p - h o l e d r i l l i n g , a m e t h o d f o i n l a y s m i n i tu a r e c h e c k v a l v e i n d r i l l s h a n k s i u s e d , t h r o u g h t h e c h a n g e f o c u t t i n g lu f i d l f o w p r e s s u r e , c h e c k v a l v e s i o p e n e d a n d c l o s e d i n t e l l i g e n t y, l w h i c h s i o n l y a p p l i c a b l e t o t h e p r o c e s s i n g m e t h o d fw o o r k p i e c e r o t ti a o n nd a t o o l e d . D u r i n g t o o l i n g p r o c e s s i n g ,
三切削刃BTA深孔钴钴削过程研究

而 o t
三切 削 刃 B TA 深 孔 钴 钴 削 过程 研 究
关世玺, 国勇 范
( 北 大 学 机 电工 程 学院 , 中 山西 太原 0 0 5 ) 3 0 1
摘 要 : 通过 试验 对 3个切 削刃 B A 深 孔钻 削过程进 行 了研 究 , T 主要 分 析 了在 特 定 的深 孔奈 件 下切
1 试 验 设 备和 步 骤
整个试 验 系统主要 由深孔 钻床 和数据测 试 装置
组成。
2 切 屑 的 变 形
2 1 3条切 屑 刃上 的切屑 变形 . 根据 金 属 切削 原 理 , 切屑 变 形可 以用 下 列公 式
得到:
y CS O
1 1 试 验 设 备 .
1 )冷却 系统 。冷却液 流动速 度 q 0 / i, :1 0 L r n a 冷却液 压力 P 2 8 MP , 却 液 为 机 油 和 煤 油 的 一 . a冷
道 截面是 钻头 的喉部 , 际可用 的排屑 空间很 有 限 , 实 较 易造 成在钻 削过 程 中 产生 啃钻 、 向振 动 和 受 力 轴
涂层 刀片推 荐寿命 值 的 8 作 为 刀具 的 寿命 标 准 , O, 9 6
这个数 值也 适用 于通 用 的 B A 类 型 的钻 头 的工作 T 寿命 。 1 2 试验 步骤 . 1 )安装好 工件及 刀具 系统 ;
式 中: P为工件 材料 的密度 。
BTA内排屑深孔钻断屑机理及槽型设计

BTA内排屑深孔钻断屑机理及槽型设计
汽轮机低压加热器管板是核电设备的重要组成部分,加热器管板上的深孔加工难度较高。
BTA(Boring and Trepanning Association)内排屑深孔钻因生产效率高、加工质量好被广泛的应用于低压加热器管板的深孔加工,但由于被加工材料的韧性高,断屑和排屑较难,针对上述问题,本文提出了一种以车代钻的试验方法,主要从深孔钻钻削模型、各个切削刃不同角度下对切削力和断屑的影响规律等方面展开研究。
首先,针对BTA深孔钻封闭的使用环境,建立以车代钻的试验模型:不改变外刃、中间刃和中心刃的尺寸和角度,并保证各刃相对于深孔钻的位置不变,通过在工件端面进行切削加工,来模拟各个切削刃的加工过程。
其次,以钻削力为研究对象:通过对深孔钻外刃、中间刃和中心刃分别设计角度正交实验,分析了各切削刃的不同角度对切削力的影响规律,利用极差分析以切削力为研究对象,得到了各个切削刃的最佳角度组合。
再次,以断屑效果为研究对象:切屑的卷曲半径是切屑弯曲的重要指标,分析了各个切削刃的切屑形态,通过极差分析分析了各切削刃的不同刃倾角、后角和偏角对切屑的卷曲半径影响规律,发现各角度的变化对中心刃切屑的卷曲半径影响有限。
最后,针对深孔钻中心刃断屑难的问题,利用有限元仿真,建立了中心刃钻削模型,分析了不同槽宽(2n参数下的切削力、切削热和切屑的形态,得到了中心刃最佳的(2n参数对断屑的影响规律。
在BTA深孔加工中导向块作用的研究综述

译文学院:专业:学号:姓名:指导教师:江苏科技大学年月日在BTA深孔加工中导向块作用的研究综述R.Richardson , R.Bhatti英国格林威治大学工程学院摘要综述是由关于导向块在BTA深孔机加工过程中的作用的文献所组成的。
工艺和表现及导垫的抛光作用之间的联系是被检查的。
先前已被描述为完成工序的抛光操作实际上是在一个极其滥用的过程。
据表明,在抛光过程中导向块与切割面的接触面积最好只有其投影面积的1.2%。
此外,没有润滑膜能够在该导向垫的前存在。
关键字:导向块,力系统,,打磨,表面完整性,流体力学,磨损1.介绍BTA加工被证明是加工高长径之比,平行度,直线度,圆度和表面纹理孔的最经济的方法之一[1-3]。
高压冷却剂被送到孔的内径和管状钻柄外表面之间的外部。
切屑和流体回流是直接通过钻头的内部和通过定向管状钻柄的外部。
极高的流速是所产生的切割面,而不像枪钻,切屑在工具和孔之间被困住的可能性是可以避免的[4]。
该方法主要利用单刃刀具。
一个BTA钻头提供了提供了一个不对称的切割边缘(或边缘)通过设在切割边缘之后大约90和180的导向块来平衡。
由刀具已经进入工件后的孔壁提供引导。
BTA过程最初是由Beisner开发并1943年在德国获得专利,这个过程主要作为副产品来自德国二战技术[5]。
有两种类型的工具,一些最初由西德的海勒公司制造,另一些由瑞典的山特维克制造。
BTAH工具通常具有一个单件的硬质合金的切削刃。
山特维克在BTAH头已产生变化称为单管系统(STS)。
BTA(STS)山特维克头(之前被称为BTAS)有三个硬质合金定位技巧以至于得到重叠的部分。
这些技巧被定位以至于切削力被平衡,从而减小导向块上的压力。
2.BTA工具海勒设计的一个典型的钻削钻头如图1所示。
这说明了形成切削刃的三硬质合金片和被铜焊到钢钻体的两个导向块。
切削刃被分成三个部分,即外,中间和内缘。
内边缘是颠倒的,以至一个边缘而不是一个点是在中心旋转。
BTA深孔钻削智能纠偏技术研究

BTA深孔钻削智能纠偏技术研究李楠;吴伏家【摘要】基于目前深孔钻削过程轴线偏斜技术难题,针对BTA(Boring and Trepanning Association)深孔钻削过程出现走偏现象[1-2],采用钻柄位置镶嵌微型单向阀方法,通过切削液流道的油压变化智能开闭单向阀只适用于工件旋转、刀具进给的加工方式.在刀具加工过程中,刀具出现走偏时,指定位置的微型单向阀自动打开,运用油液的冲击力,使刀具自动纠偏.当刀具纠正后,微型单向阀会自动关闭,不用停机检测,可达到在线纠偏的效果,大大提高加工效率运用FLUENT流体动力学软件对切削液油压系统进行数值模拟,为BTA深孔钻削智能纠偏提供理论依据.%According to the current technical problems of axis deviation during deep-hole drilling processing,in order to solve the phenomenon of deviation in BTA (Boring and Trepanning Association)deep-hole drilling,a method of inlays miniature check valve in drill shank is used,through the change of cutting fluid flow pressure,check valve is opened and closed intelligently,which is only applicable to the processing method of workpiece rotation and tool feed. During tooling processing, when the tool appears to be going deviation,the miniature check valve at the designed spot is opened,using the oil impact to make tool intelligently corrected.When the tool is corrected,miniature check valve will be automatically shut down,not needing to be stop or to be tested,which can achieve the effect of online rectification,greatly improving the processing efficiency.By using FLUENT fluid dynamics software to carry on number simulation for cutting fluid oil pressure system,the theoretical basis hasbeen provided for the intelligent correction technique of BTA deep-hole drilling.【期刊名称】《机械设计与制造》【年(卷),期】2013(000)001【总页数】3页(P143-145)【关键词】BTA;FLUENT;微型单向阀;智能纠偏【作者】李楠;吴伏家【作者单位】中北大学机电工程学院,山西太原030051;西安工业大学,陕西西安710032【正文语种】中文【中图分类】TH16;TG713;TG5231 引言深孔钻削轴线纠偏是现今深孔加工领域面临的一个技术难题,国外刀具权威某公司、德国某公司都对此进行过深入研究[3]。
BTA深孔钻切削过程实验研究

! 切削实验方案
!7 % 机床的改装与冷却润滑系统的配置
实验系统如图 % 所示,主要由改装结构的普通机床和深孔 加工所需的冷却润滑系统组成。 &$’(%)* 普通车床能够满足切削切率实验件孔径加工的 要求,并且该机床的加工范围最大工件长度为 ! 米,也能满足 实验要求。 由于 "#$ 深孔钻头要求切削液具有高的压力和 / 或 0 大的 流量,切削液的传输装置应能将切削液沿钻杆和钻头的外部送 达切削刃,再由那里通过钻头和钻杆的内部带着切屑排出。固 冷却润滑系统主要由受油器、 油箱、 积屑箱、 油泵、 电机和相应
参考文献
0 G/ P?>*Q@>’?:R?>@S =/ H/ =/ H’->*S J/ G/ G>*R>@/ K* T*U:’#)$>#)&* E&@ #?: G#&%?>’#)% =&Q:T)*$ &E #?: V:’DT#>*# 9&@%: GA’#:- )* IJK B::W X&T: =>%?)*)*$/ T*#/ Y/ V:’/ 0Z2! 17 , " . 6!8 3 687/ 1 [/ V>&S =/ G/ G?D*-D$>-/ \:>@ G#DQ):’ )* I&@)*$ J@:W>**)*$ K’’&%)>#)&* B@)TT)*$/ \:>@/ 0Z22/ 01" 77 3 "7/ 机械设计与制 7 刘俊来等 / 小直径单刃外排屑深孔加工系统的研制, 造 / 0ZZ"/ " 72 3 7Z/ 管光晋译 / 深孔加工 / 国防工业出版社, " 斯温哈特编, 0Z8"/ 萧诗纲 / 切削用量手册 / 机械工业出版社, 0Z2"/ ! 艾兴, 6 陈日曜编 / 金属切削原理 / 机械工业出版社, 0Z2!/ 8 =/ P/ G?>]/ =:#>T PD##)*$ [@)*%)WT:’/ PT>@:*Q&* [@:’’S H^E&@Q/ 0Z2"/
三级钻孔加工法,孔深与径比超过100也能做

三级钻孔加工法,孔深与径比超过100也能做正常钻削技术所生产的孔,其孔深极少超过5倍直径,而在深孔钻削中,此比例可高达150﹕1,并且任何孔深大于5倍直径都应称为深孔。
深孔加工常见加工方式BTA系统中,钻头与钻杆为中空圆柱体,提高了刀具刚性和快速拆装问题。
其工作原理如视频所示,切削液经加压从入口进入授油器后通过钻杆与孔壁形成的密封环状空间,流向切削部分进行冷却润滑,并将切屑压入钻头上的出屑口,经钻杆内腔从出口排出。
BTA 系统主要适用于直径φ>12mm 的深孔加工。
▲BTA系统原理枪钻的钻柄是空的,由内外部供应的切削液流经钻头内输送管,并强行流经切削头内的孔。
钻柄外侧有一个沿着长度方向的V形槽,切削液携带切屑通过此V 形槽,并经过钻头外侧,最终切屑从孔中排出。
枪钻可应用于普通加工中心,但是需要高压力的切削液。
▲枪钻系统示意图深孔加工任务实例某壳体零件(见图)有两个直径4mm、1个直径5mm且深度都超过700mm 的深孔。
普通设备无法加工,必需使用专用的深孔加工设备——数控深孔钻床。
数控深孔钻机床是专门用于深孔加工的数控设备,加工的孔径小、深度大,孔径与孔深比达到1﹕100,一般的数控设备无法完成。
▲深孔零件数控深孔钻工作原理是采用不对称切削加工,不需用传统的中心钻来完成定位要求。
▲数控深孔钻深孔加工方案改进过程经过反复试验,1个深孔加工动作宜采用“三级加工法”:定位钻削、导向钻削及正常钻削,称为“三级钻孔技术”。
三级钻孔需要根据不同的钻孔深度采用不同的切削速度目前机床自带的数控钻孔指令只能完成1个钻孔深度和1个切削速度,如何使用常用的钻孔指令来实现三级钻孔可分两种方法:①手动干预:根据不同的钻孔深度,人为的手动来进行调节切削速度。
②重复进给:对同一个孔分别进行编制3个钻孔程序,指令不同的钻孔深度和切削速度,进行重复操作。
深孔加工改进方法对于上述两种方法的弊端,开发一个三级阶梯钻削指令方案。
BTA深孔钻的结构优化及切削仿真分析

BTA深孔钻的结构优化及切削仿真分析作者:吴雪峰马路苑忠亮杨树财来源:《哈尔滨理工大学学报》2018年第04期摘要:BTA 深孔钻是一种典型的深孔加工内排屑钻头,刀具结构与刀具角度是影响加工质量与加工效率的重要因素。
深孔加工过程中封闭,通过实验的方法优化刀具结构与角度难度较大。
采用有限元的方法,用ANSYS软件建立了BTA深孔钻静力及模态三维分析模型,得到了BTA深孔钻变形特点及六阶振型图,为BTA深孔钻钻头结构优化提供参考;采用AdvantEdge软件建立了BTA深孔钻各刀齿钻削过程模型,研究了切屑形成过程及刀具角度对切削力、扭矩的影响规律,进而为刀具角度优化提供理论参考。
关键词:BTA深孔钻;有限元仿真;模态分析;钻削仿真;结构优化DOI:10.15938/j.jhust.2018.04.004中图分类号: TG501.1文献标志码: A文章编号: 1007-2683(2018)04-0018-07Abstract:BAT deephole drill is a typical innerchip removal drill. Structures and angles of tools are the main factors that influence the machining quality and machining efficiency. Because the processing of deephole drilling is not visible, it is very difficult to optimize structure and angles of tool through the experiment method. In this paper, finite element method is used as follows: static analysis and modal analysis of BAT deephole drill are built by ANSYS, and then the deformation and sixset vibration mode diagram of BAT deephole drill are carried out as a reference for structural optimization of BAT deephole drilling; Drilling process model of each tool tooth is built by AdvantEdge, and the effect of chip formation process and tool angles on cutting force and torque are studied as reference for tool angle optimization.Keywords:BAT deephole drilling; finite element simulation; modal analysis; drilling simulation ; structural optimization深孔加工在机械行业中有着举足轻重的地位,当钻头孔深与孔径之比大于 10时,称之为深孔加工[1]。
BTA

由图2 分析并计算可知,钻削系统在x 、y 方向上的
钻 削合 力F x 、 分别 为 :
=
一
半 + ( 鲁 毗s i n + c o s O R ) 一 ( 2 )
式 中 ,F c 为轴 向进 给 力 ,M。 为钻 削 力转 矩 , e 为中 间 齿位 置角 ,e 为 中心 齿 内刃后 角 ,e 8 为 中心齿 外 刃后 角 ,e 为 中间齿 后 角 ,e 。 为外 齿后 角 ,a 、b 、C 、d 为各 钻齿 的 宽度 ,且 口 - I - b +C +d=R 。 设 挤光 力矩 为MB ,摩 擦 系数 为 。考 虑BT A深孔 钻
摘
要 :介绍 了深孔 钻削力学特性分析的意义 , 建 立了深孔 钻削的力学模 型 ,然后对B T A 深孔钻削系统 中的轴向进给力和转矩进行了计算,最后用实例分析了中间齿位角的确定方法 ,齿后角及中 间 齿位 角对钻削力的影响 ,并选 定了其合 适范围。
文章编号 :1 0 0 9 -0 1 3 4 ( 2 0 1 5 ) 0 7 ( 下) -0 0 4 1 - 0 3
s i n1 3 - gc o s 1 3 F x ( 。 — — — 面 面 ) + F y ( c o s (  ̄ + — g s i ~ n 1 3 )
唯’
SHEN Xi n g . q u a n 1 ' ,W ANG Hu i - r o n g。 ,L I Y o n g . c h u n ,W ANG We I 。
( 1 冲 北大学 机械与动力工程学 院,太原 0 3 0 0 5 1 ;2 . 山西省深孔加工 工程技术研究 中心 ,太原 0 3 0 0 5 1 )
M :
f ∑X = 0 一 。 一 1 C O S a - . u F c l s i n o t - F G 2 c o s l f 一 # F a 2 s i n l f = 0 { ∑y = 0 一 成0 + l s i n a 一 C O S O t + 2 s i n / ? 一 # F G 2  ̄ o s p = O ( 3 )
BTA深孔钻的制造及改进

1.BTA深 孔钻 的 制造
客 户 提 供 一 深 孔 钻 样 品 , 要 求 按 样 品 来 制 造 所 需 的 深 孔 钻 。该 深 孔 钻 用 于 加 工 摩 托 车 减 振 筒 内 孔 , 因 其 内 部 装 有 活 塞 杆 作 往 复 运 动 ,因 此 要 求 孔 的 精 度高 ,表 面粗 糙 度 值尺 <0.1 u m,即 需要 镜 面 加 工 。减振 简 材 料 为低 压 铸造 铝 合 金 ,内孔 单边 加 工 余 量 约 1.5ram,从 该深 孔钻 的 实 际 使 用情 况 来看 ,是 集 扩 孔 、铰 孔 与 挤 压 为一 体 的 复合 刀具 。
制 造 后 的 深 孔 钻 经 用 户 使 用 后 反映 效 果 不错 , 可 加 工 200个 孔 左 右 ,达 到 了样 品 刀具 水 平 。但 用 户 说 , 曾使 用 过 某 进 13品 牌 的 深 孔 钻 ,加 工 孔 数 可 达
矩 形螺 纹
4
图 I 矩 形螺 纹 来自图 2 56
由 于 切 屑 不 会 划 伤 工 件 孔 壁 , 加 之 环 形 间 隙 中 的 高 压 切 削 液 能 起 到 阻 尼 钻 杆 振 动 的 作 用 ,因 此 , BTA加 工 方法 具 有加 工表 面 粗糙 度 低 、精度 高 ,钻孔 效 率 高 及 7]具 系 统性 能 好 等优 点 。 图2是 用 户提 供 的 与深 孔 钻 相 配的 钻 杆 图 。
(2)挤 压 圆柱 刃O36mm表 面 要进 行镜 面 加 工 , 要求 表 面粗 糙 度R =0.J m。具 体 加 工时 应 在精 磨 后
留余 量0.005~0.0lmm,然 后 用 超 细微 粉 金 刚 石 砂 轮 进 行 表面 抛 光 ,HI],t达 到镜 面效 果 。 同时 ,在 磨 削过 程 中 要保 证 挤 压 圆柱 刃与 内孔 的 同轴 度 ≤0.0lmm。
BTA钻头受力分析

BTA钻头受力分析作者:师毓华来源:《科学与财富》2018年第30期摘要:BTA深孔钻削是金属切削中一种较为复杂的加工方式。
本文对首先对钻削过程中钻削力的来源进行了阐述,进而对BTA钻头的在加工过程中的受力进行了简化,从而获得了BTA深孔钻头的受力分析,为后续BTA钻头的设计与优化提供一定的参考。
关键词:BTA钻头;钻削力;深孔加工0.引言:BTA深孔钻削是深孔加工中常用的一种加工方法,由于其加工效率高产品质量好,目前广泛的应用于各种加工领域当中。
由于BTA深孔钻削属于内排屑自导向加工模式,所以钻头的受力对钻头在加工过程中的稳定性与自导性有着十分重要的影响。
1.钻削力的来源钻削过程是由刀具通过旋转加轴向进给,在待加工工件上加工出所需要的深孔,由于材料具有一定的韧性和硬度,材料在被加工过程中发生一系列的弹塑性变形,对钻头产生阻力,在切屑与工件分离的过程中切屑沿着前刀面流出,和前刀面接触并产生摩擦阻力。
随着刀具向前移动,工件已加工表面会有一定弹性恢复,继而与后刀面进行接触,然后产生摩擦力。
由此,钻削力的来源主要由以下三个方面组成[1]:(1)钻削过程中,被加工材料发生弹性变形所产生的阻力。
(2)钻削过程中,被加工材料发生塑性变形所产生的阻力。
(3)钻削过程中,切屑流出时对刀具前刀面产生的摩擦力和刀具向前移动时工件过渡表面和已加工表面对刀具后刀面挤压所产生摩擦力。
2.错齿BTA钻头钻削力分析BTA深孔钻削的过程中,除了刀具切削刃与工件接触以外,还有导向块与工件接触,致使加工过程中刀具的的受力分为三个部分,分别为切削刃所受的切削力、导向块所受的正压力和导向块与工件之间的摩擦力,这样一来使得刀具的受力相当复杂。
在一般的切削加工中,例如在车削加工中,只存在着工件、刀具、床身之间的正常力系,所以只需将车刀装在三向测力仪上,就可以测量出车刀所受的三向力。
而在深孔钻削的过程中,由于存在着导向块与工件之间的正压力和摩擦力,使工件与刀具切削刃和导向块之间构成封闭力系,所以就不能直接测量出切削刃所受的三向分力,只能测出刀具所受的轴向力与扭矩。
西安理工大学硕士学位论文BTA深孔钻削刀具系统特性研究姓名李

西安理工大学硕士学位论文BTA深孔钻削刀具系统特性研究姓名李西安理工大学硕士学位论文BTA深孔钻削刀具系统特性研究姓名:李春蕊申请学位级别:硕士专业:机械制造及其自动化指导教师:李言20080601摘要论文题目: 深孔钻削刀具系统特性研究学科专业:机械制造及其自动化研究生: 李春蕊签名:指导教师: 李言教授签名:瓣覃摘要本文分析了钻削的工作原理和钻削过程的特点,根据深孔加工中断屑和排屑障碍的问题,分别从内排屑深孔钻的分屑、断屑和导向条等方面进行了详细的讨论。
为保证顺利排屑,对切屑液的流动性也进行了分析和选择。
对合理配置导向块的位置和形状,进行了详细的分析和设计。
对深孔加工刀杆的屈曲行为进行了分析,通过静力平衡法得到无重刀杆受已加工表面约束在压扭组合作用下的屈曲微分方程,证明了均匀螺旋线确实为无重刀杆受已加工表面约束在压扭组合作用下的刀杆屈曲方程的精确解。
通过能量变分原理得到了欧拉方程及相应的自然边界条件,所得欧拉方程使我断直接能量法等所得近似结果的精度成为可能。
分析了影响深孔加工精度的主要因素,对孔中心线偏斜问题的机理进行了探讨,建立了刀杆的力学模型,通过理论分析得出了深孔偏斜的偏斜量。
通过深孔加工专用机床的实验,对比可以发现孔偏斜量的实际测量值和计算值比较一致,说明理论分析是正确的。
对支承不重合对孔偏斜的影响也进行了理论分析和实验验证,并提出了相应的一系列措施。
采用有限元分析软件进行了刀杆的模态分析,建立了有限元模型,划分了有限元的网格,分析刀杆加工过程的非线性。
把有限元仿真结果和实验结果做了对比和分析,得出液体和刀杆和孔壁的非线性接触对于刀杆的偏斜具有重要影响。
关键词:深孔钻,刀具系统,孔中心偏斜,钻削精度,压扭组合本项目受陕西省自然科学基金项目《振动深孔钻削精度及其控制方法研究》项目编号:资助。
,翻泐帕一.上华,.、聃, .., . ,,,. ,..?, ., ., ? , .,.,, 鲥 , . , ,.: ? , ,, ;西安理工大学硕士学位论文 : ,独创、性,:声明秉承祖国优良道德传统和学校的严谨学风郑重申明:本人所呈交的学位论文是我个~』~●,人在导师指导下进行的研究工作及取得的成果。
基于深度学习的TC32钛合金BTA深孔钻削容屑系数和切屑形态研究

基于深度学习的TC32钛合金BTA深孔钻削容屑系数和切屑
形态研究
冯亚洲;陶觅辰;刘战锋;孔浩
【期刊名称】《制造技术与机床》
【年(卷),期】2024()4
【摘要】在钛合金深孔钻削过程中,由于其难加工性经常会存在刀具磨损严重、排屑困难和内孔表面质量差等问题。
为了获得具有良好内孔表面质量和切屑形态的钛合金深孔类零件,以新型钛合金TC32为研究对象,在不同工艺参数下基于深度学习和BP神经网络进行了TC32钛合金的容屑系数预测和加工试验验证。
研究结果表明:预测模型的决定系数R 2为0.921,拟合程度和精度较高,预测性能良好;当进给量为0.08 mm/r、主轴转速为435 r/min时容屑系数为5.6,切屑形态以C形屑和短带状屑为主,排屑顺畅且加工过程稳定。
【总页数】6页(P57-62)
【作者】冯亚洲;陶觅辰;刘战锋;孔浩
【作者单位】西安石油大学机械工程学院;陕西深孔智越科技有限公司
【正文语种】中文
【中图分类】TG52
【相关文献】
1.BTA深孔钻削切屑变形与刀齿切削力分布规律仿真
2.错齿BTA深孔钻削切屑变形及刀屑接触长度分布规律研究
3.错齿BTA深孔钻削切屑变形断裂影响因素研究
4.基于BTA深孔钻钻削EA4T钢的切屑形成机制研究
5.TC11钛合金深孔钻削试验研究与切屑形态分析
因版权原因,仅展示原文概要,查看原文内容请购买。
基于ABAQUS错齿BTA深孔钻削过程的模拟仿真

图2钻削仿真几何模型
材料本构模型
在有限元仿真模型中,工件材料本构模型是材料失效
判定的依据。
材料的本构模型有Johnson-Cook
图1BTA钻头刀齿切削力仿真方案
BTA钻削仿真模型建立
建立BTA深孔钻削几何模型
前刀面和切屑的摩擦属于内摩擦,在金属的切削仿真中,
深孔钻钻削过程的模拟仿真,
产生的切屑较小,
图4钻削仿真模拟的过程中所产生的钻削力波形图所规定的正方向方向相反。
从图中取出钻削力比较平稳的部分求出平均值得:Fx=2.3195N,Fy=15.1956N,Fz=418.9404N。
由此可以看出,刀齿所受的轴向力最大,径向力最小,主切削力最不稳定。
图3Φ20错齿BTA深孔钻模拟仿真
图4Φ20错齿BTA钻钻削力波形图。
BTA深孔振动钻削断屑分析设计
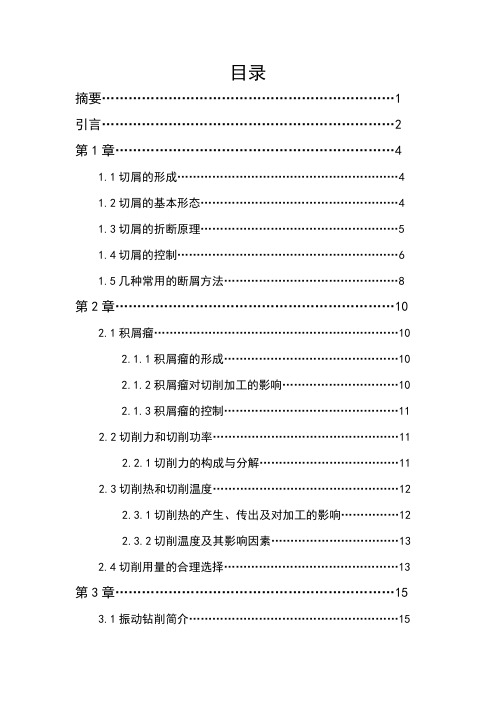
目录摘要 (1)引言 (2)第1章 (4)1.1切屑的形成 (4)1.2切屑的基本形态 (4)1.3切屑的折断原理 (5)1.4切屑的控制 (6)1.5几种常用的断屑方法 (8)第2章 (10)2.1积屑瘤 (10)2.1.1积屑瘤的形成 (10)2.1.2积屑瘤对切削加工的影响 (10)2.1.3积屑瘤的控制 (11)2.2切削力和切削功率 (11)2.2.1切削力的构成与分解 (11)2.3切削热和切削温度 (12)2.3.1切削热的产生、传出及对加工的影响 (12)2.3.2切削温度及其影响因素 (13)2.4切削用量的合理选择 (13)第3章 (15)3.1振动钻削简介 (15)3.2振动钻削原理 (15)3.3振动钻削的断屑机理 (16)3.4实验数据分析 (19)3.4.1断屑实验分析 (19)3.4.2断屑实验数据 (19)3.4.3断屑原因分析 (20)3.5加工精度分析 (21)3.5.1加工精度数据 (21)3.5.2原因分析 (21)总结 (23)致谢 (24)参考文献 (25)BTA深孔振动钻削断屑分析摘要在金属切削加工中,深孔加工一直是个难题。
加工精度难以满足产品要求。
深孔加工的关键就是解决断屑、排屑问题。
切屑顺利排出是BTA深孔加工的至要环节,是直接影响正常生产的关键问题,而断屑问题的解决是良好排屑的前提条件。
而振动钻削是目前最有效的断屑方法,只要振动参数匹配得当,不论加工何种材料,切屑大小可以通过改变切削用量和振动参数来控制。
本文结合生产实际对振动钻削断屑进行了理论分析;针对深孔加工存在的问题,通过切削实验,探讨了切屑形态变化与切削参数之间的关系,总结出断屑的最佳切削条件。
关键词: BTA; 断屑; 振动钻削;AbstractIn the metal cutting process, deep processing is a difficult problem. Precision is difficult to meet the product requirements. The key is to solve the deep.hole machining chip breaking, chip removal problems. The smooth discharge of chips is the BTA deep hole machining to be part of that is directly affecting the normal production of the key issues, and chip.breaking solution to the problem is a prerequisite for a good chip. The vibration drilling is the most effective method of breaking chips, as long as the proper vibration parametersmatch, no matter what kind of materials processing, chip size can change the cutting parameters and vibration control. In this paper, the actual production of the vibration drilling cuttings Xiaoduan a theoretical analysis; problems for deep holes, through the cutting experiment, morphological changes of the chip and the relationship between the cutting parameters, summed up the crumbs off the best cutting conditions.key words:BTA Chip breaking Vibration Drilling前言目前,国内外采用振动钻削来加工小直径深孔,但都存在着两类问题:一是振动钻削系统中,多数振动装置的振幅是不可调节的,或调幅十分困难和麻烦;二是小直径深孔钻头的设计与制造,大部分是采用外排屑枪钻,很少采用内排屑深孔钻。
BTA深孔钻头的受力分析及参数计算

BTA深孔钻头的受力分析及参数计算发表时间:2017-02-23T17:17:49.743Z 来源:《北方建筑》2016年12月第34期作者:范永刚1 刘媛媛2 杨西亚3 [导读] 传统BTA钻头主要是由钻体、钻柄、中心切削刃、中间切削刃、边切削刃、导向条、减震块等组成。
齐重数控装备股份有限公司黑龙江齐齐哈尔 161005 摘要:BTA深孔钻广泛应用在航天、航海、兵器工业、核容器制造等领域,特殊的排屑方式以及恶劣的工况使其钻头顶部各切削刃在高温作用下,极易脆化断裂,将划伤已加工工件的表面。
影响已加工深孔的表面粗糙度。
故对其进行受力分析并进行参数计算十分必要。
关键词:BTA深孔钻;受力分析;参数计算传统BTA钻头主要是由钻体、钻柄、中心切削刃、中间切削刃、边切削刃、导向条、减震块等组成[1]。
传统BTA多刃内排屑钻头在切削工件时,中心、中间、边切削刃先后和工件发生接触[2]。
中心切削刃先接触工件受力最大,最易遭受破坏[3]。
将导致中间、边切削刃承受的轴向切削力将会骤增,几何级加速切削刃耗损,导致钻刃整体失效[4]。
故需对钻头顶面各切削刃进行力学研究[5]。
一、BTA钻头静力分析BTA钻头的静力分析,如图1-1所示:三、结论通过上述受力分析及公式,将计算得到的三个方向力代入前式,即可得到刀具每个齿的分力,摩擦力矩、切削力转矩、导向条正压力、摩擦系数等参数。
参考文献:[1] 王峻. 现代深孔加工技术[M]. 哈尔滨:哈尔滨工业大学出版社,2005:135-137.[2] 胡凤兰,刘军安,魏华. BTA 深孔钻削力学特性及钻杆稳定性研究[J]. 现代制造工程,2011(7):73-76.[3] 陈振亚. 深孔加工孔轴心偏斜及系统优化设计研究[D]. 太原: 中北大学,2013:3-5.[4] 张晓. 深孔加工BTA 刀具的结构设计与参数化建模[D]. 太原: 中北大学,2014:24-28.[5] 熊艳伦,汤佳骏,刘炜. 深孔加工技术研究综述[J].现代农业装备,2016(3):24-34.。
BTA深孔钻杆的涡动研究

摘
要: 对B T A深孔钻杆在加工过程中的涡动问题进行研 究。分析 了在切 削液作 用下 B T A钻杆与 内孔接触与非接触时
的钻杆 受力情况, 得到钻杆在 涡动面上的运动平衡方程 , 推导 出钻杆发 生涡动的理论 涡动点和钻杆脱 离内孔 的理论阀值 点。总结出钻杆因不平衡量作用时产生的偏 心距 小于理论 涡动点时 , 钻杆不会产生涡动, 即使存在最终也会 因切 削液流 体力作 用而消失; 同时涡动角频率的绝对值小于理论 阀值时 , 钻杆会 脱离孔壁 , 而涡动角频 率达到阀值后 , 钻杆运动就可
机 械 设 计 与 制 造
1 48
Ma c h i n e r y De s i g n
&
Ma n u f a c t u r e
第1 2期 2 0 1 3年 1 2月
B T A 深孔钻 杆 的 涡动研 究
江 敏 . 一 , 苗 鸿宾 t , 赵文 强 1 , 2 ( 1 . 中北大学 机械工程与 自动化学 院, 山西 太原 0 3 0 0 5 1 ; 2 . 山西省深孔加工工程技术研究中心, 山西 太原 0 3 0 0 5 1 )
T h e Re s e a r c h o f Wh i r l i n g o f t h e B o r i n g a n d Tr e p a n n i n g A s s o c i a t i o n( B T A) D r i l l
J I ANG Mi n ,MI AO Ho n g - b i n ,Z HAO We n - q i a n g , ( 1 . C o l l e g e o f Me c h a n i c a l E n g i n e e r i n g a n d A u t o m a t i o n , N o a h U n i v e r s i t y o f C h i n a , S h a n x i T a i y u a n 0 3 0 0 5 1 , C h i n a ;
深孔高效钻削法一BTA法

深孔高效钻削法一BTA法
宋晓刚
【期刊名称】《机械工人:冷加工》
【年(卷),期】2003(000)004
【摘要】BTA加工法,也就是内排屑高效率钻削法。
它是在枪炮钻基础上发展起来的,采用圆形空心钻杆和高压密封装置,将大量高压切削液压入钻杆和工件孔壁之间的环形间隙中,流入切削区。
【总页数】2页(P22-23)
【作者】宋晓刚
【作者单位】哈尔滨汽轮机有限责任公司150046
【正文语种】中文
【中图分类】TK266
【相关文献】
1.高速深孔BTA钻削系统的高效排屑设计与研究 [J], 蒿风花;沈兴全;王慧荣;朱红霞
2.基于BTA深孔钻钻削EA4T钢的切屑形成机制研究 [J], 曲乃恒;沈兴全;冯斌
3.错齿BTA深孔振动钻削刀具系统径向减振特性研究 [J], 郑亮奎; 郑建明; 李旭波; 肖世英; 刘驰
4.大长径比小深孔高速钻削BTA刀具的参数优化 [J], 刘军强;思代艳;吴伏家;康盼;周浩
5.BTA深孔钻的微织构制备与钻削试验研究 [J], 于洋;常耀恒;董智伟
因版权原因,仅展示原文概要,查看原文内容请购买。
- 1、下载文档前请自行甄别文档内容的完整性,平台不提供额外的编辑、内容补充、找答案等附加服务。
- 2、"仅部分预览"的文档,不可在线预览部分如存在完整性等问题,可反馈申请退款(可完整预览的文档不适用该条件!)。
- 3、如文档侵犯您的权益,请联系客服反馈,我们会尽快为您处理(人工客服工作时间:9:00-18:30)。
变形,C为与3个切削刃前角有关的常数。
该式表明,在BTA深孔加工过程中,轴向力与 3个切削刃所导致的切屑变形是线性关系。
4 磨损
在深孑L钻削试验中,BTA钻的磨损数据可以通
过测量获得。由
錾 试验数据可以得
出BTA钻的寿命
曲线,如图2所 示,这条曲线与泰 勒曲线相似,即随
哦o.3
鼯
0
着切削速度的增 加,低磨损区域减
1)安装好工件及刀具系统; 2)启动机床主轴及冷却液系统; 3)启动测量装置系统,调试好各信号线路; 4)设定好切削参数进行加工,同时采集信号; 5)对采集到的信号数据进行分析、处理。
2切屑的变形
2.1 3条切屑刃上的切屑变形
根据金属切削原理,切屑变形可以用下列公式
得到:
/
y一五面C丽OS‘2
(1)
3切削力与切屑变形
钻头上的切削力主要由3条切削刃上的切削
力、冷却液体压力、ຫໍສະໝຸດ 向块和已加工孔表面的摩擦力组成。该试验的钻孔直径为025 mm,只对轴向切 削力E进行了测量,并考虑到试验条件取同样的
切削深度,轴向力E是通过力传感器测量得到的。
通过对测量数据分析可以得出,当钻削速度口增加
的时候,轴向切削力只将会下降;当进给量,增加 时,轴向切削力E会上升。
F,=A∑y+B
(4)
式中;A和B是与加工条件有关的常数;∑7是3条
切削刃产生的切屑总变形。 外刃、中间刃、内刃的轴向力与切屑变形的函数
关系可以分别表示为:
Fo,=kl’,t o,(1.4%+Co)
(5)
F。=kP,to厂(1.4y埘+Co)
(6)
F打=kF,t o,(1.4竹+Ci)
(7)
式中:k为与加工条件有关的常数,E为最大剪切变 形量,t。为切削深度,扎为3个切削刃分别产生的
的切屑变形最大,3个切削刃(内刃、中间刃、外刃)的切削力和切屑变形的总体变化趋势是相同的。
关键词:BTA深孔钻头;切屑变形;切削力;刀具磨损
中图分类号:TG 713.1
文献标志码:A
在通常的机械加工过程中,一般都具有较大的 排屑空间,能够保证切屑正常排出。但是在钻削过 程中,尤其是对内排屑深孔钻削,由于其最小排屑通 道截面是钻头的喉部,实际可用的排屑空间很有限, 较易造成在钻削过程中产生啃钻、轴向振动和受力 分布不均等现象。在BTA深孔加工过程中,高效 率、恒稳定的排屑过程是保证正常钻削的必备条件。 通过研究钻头和工件间的相互作用力,来确定各种 不同加工条件下的切屑变形、切削力和切削刃磨损 情况是非常关键的。但是,用纯理论的方法难以得 到准确的数值,借助于试验的方法获得较为合理的、 对实际加工工艺有借鉴的数值是一个有效的办法。
mV,工作温度为一40~110。C。
3)信号放大器。精度为2%,响应频率为3
‘
kHz,拟定输出量<5 mV。
4)钻头刀片材料采用YG类硬质合金刀片。
5)工件材料为不锈钢0Crl8Ni9,钻孔直径为
西25 mm,长径比80:l。 图1是BTA钻中
头的典型结构,其头
部油孔设计成偏离钻
头中心线。为了得到 窄而短的小c形切屑
根据试验数据,BTA深孔钻的轴向力经验公式 估算为E=38 994fo·96V-0·148(N)。
同时研究发现,该公式给出的进给与对应的轴
向力变化不是线性的,这是由于加工过程中钻头导 向条和工件已加工表面之间存在摩擦。
从试验数据还可以看出,深孔钻的轴向力和3
个切削刃产生的切屑总变形可用式(4)表示。
[参考文献]
[1]王俊.现代深孔加工技术[M].哈尔滨:哈尔滨工业大 学出版社,1981. [2]王世清.深孔加工技术[M].西安:西安工业大学出版 社,2003. [31马新,周长城.数据采集与处理技术[M].西安:西安交 通大学出版社,1999.
作者简介:关世玺(1967一),男,工学硕士,副教授,研究方向 为先进制造技术。
图2 BTA钻头磨损曲线图
小;当钻削温度达到刀具材料熔化点时,刀具磨损的
速度迅速增大。
5 结语
通过对BTA深孔钻削试验数据的分析研究, 表明在深孑L加工过程中内刃所产生的切屑变形量最 大,而切屑的变形量随着进给速度的增大而增加,随 着前角和切削速度的增大而减小。另外,通过试验 数据对钻削时的轴向力经验公式进行了改进,并得 到了BTA钻头内刃磨损曲线(与泰勒曲线相近)。 这些研究结果,对在线控制BTA深孔钻削的切屑 形态和掌握BTA钻头磨损规律提供了依据。
最大,中间刃切削产生的切屑变形量次之,外刃切削
时切屑的变形量最小。
《新技术新工艺》·数字技术与机械加工工艺装备 2008年 第12期
·79·
万方数据
其原因是3条切削刃上的前角不同,内刃的前 角口一般是一25。~一30。,而另外2条切削刃的前 角口的范围是O。~2。。根据切屑变形原理,内刃切 削时的切屑变形要比另外2条切削刃的大,这和加 工轨迹所显示的结果一致。
收稿日期:2008年7月25日
责任编辑周守清
·80·
《新技术新工艺》·数字技术与机械加工工艺装备 2008年 第12期
万方数据
三切削刃BTA深孔钻钻削过程研究
作者: 作者单位: 刊名:
英文刊名: 年,卷(期):
关世玺, 范国勇, GUAN Shixi, FAN Guoyong 中北大学,机电工程学院,山西,太原,030051
图1 BTA钻头结构图
形态,切削刃被分为3个部分,即内刃、中间刃和外 刃。切削刃的设置取决于孔径的大小和工件的材料 属性,以保证切屑容易排出。刀具的寿命测试是根 据自导向钻头在满足正常生产要求进行的,即按照 涂层刀片推荐寿命值的80%作为刀具的寿命标准, 这个数值也适用于通用的BTA类型的钻头的工作 寿命。 1.2试验步骤
三切削刃BTA深孔钻钻削过程研究
关世玺,范国勇
(中北大学机电工程学院,山西太原030051)
摘 要:通过试验对3个切削刃BTA深孔钻削过程进行了研究,主要分析了在特定的深孔条件下切
屑变形和钻削力的情况。通过对测试系统所得到的试验数据进行评估和证实,阐述了BTA深孔钻轴向
力的组成和切屑变形、刀具磨损以及钻削力之间的关系。研究结果表明,钻头的内刃在切削过程中产生
此外,3个切削刃的切削线速度不同,外刃的切 削线速度最大,中间刃次之,内刃最小,这同样会造 成内刃切削时切屑的变形量比其他2条切削刃产生 的切屑变形量要大。 2.2切削参数对切屑变形的影响
切屑变形受深孔钻削加工条件的影响,可以从 分析切削刃前角、切削速度和进给量得出其规律:当 切削速度增加时,切屑的变形将减小;当进给量增加 时,切屑的变形将增大;当切削刃前角增大时,切屑 的变形将减小。
cot。一垒丛上二呈坐
(2)
。
COsa
式中:7为切屑变形程度,口为切削刃前角,妒为切削
剪切角,t。是切削厚度。t:则可以通过测量切屑的长
度l和重量w得出,即
£,:里
(3)
pwl
式中:p为工件材料的密度。
利用上面的3个公式就可以由加工过程得到切
屑的变形程度。 从试验可以得知,3条不同的切削刃上所产生
的切屑变形量是不同的,内刃切削时切屑的变形量
1试验设备和步骤
整个试验系统主要由深孔钻床和数据测试装置 组成。
1.1试验设备
1)冷却系统。冷却液流动速度q=100 L/min,
冷却液压力P=2.8 MPa,冷却液为机油和煤油的
混合液(机油65%,煤油35%)。 2)传感器。采用WYGl通用型压力传感器,其
测量范围为0~200 MPa,输出信号:满程≤士5
新技术新工艺 NEW TECHNOLOGY & NEW PROCESS 2008(12)
参考文献(3条) 1.马新;周长城 数据采集与处理技术 1999 2.王世清 深孔加工技术 2003 3.王俊 现代深孔加工技术 1981
本文链接:/Periodical_xjsxgy200812027.aspx