后钢板弹簧吊耳设计说明书
后钢板弹簧吊耳单工序加工φ37夹具设计说明书

后钢板弹簧吊耳工艺规程及夹具设计学生姓名 xxx学号 xxxxxx所属学院 xxxxxxxxxxx专业机械设计制造及其自动化班级机械设计16-2指导教师 xxxxx目录机械制造工艺学课程设计设计任务书序言 1一、零件的分析 2(一)零件的作用 2(二)零件的工艺分析 2二、工艺规程设计 4(一)确定毛坯的制造形式 4(二)基面的选择 4(三)制订工艺路线 4(四)机械加工余量、工序尺寸及毛坯尺寸的确定 5(五)确定切削用量及基本工时 5三、专用夹具设计 8(一)设计主旨 8(二)夹具设计 8总结 11致谢 12参考文献 13xxxxx机械电气化工程学院机械制造工艺学课程设计设计任务书设计题目:后钢板弹簧吊耳机械加工工艺规程及夹具设计(生产纲领中批或大批)设计内容:1、产品零件图 1张2、产品毛坯图 1张3、机加工工艺过程卡 1套4、机加工工序卡 1套5、夹具设计装配图 1份6、夹具设计零件图 1-10张7、课程设计说明书 1份班级 xxxxxx设计者 xxxx指导教师 xxxx2015年11月20日摘要此说明书是对后钢板弹簧吊耳零件的加工工艺规程及加工孔的专用夹具设计。
后钢板弹簧吊耳零件的主要加工表面是平面及孔。
由加工工艺原则可知,保证平面的加工精度要比保证孔的加工精度容易。
所以本设计遵循先面后孔的原则。
并将孔与平面的加工明确划分成粗加工和精加工阶段以保证加工精度。
基准选择是用后钢板弹簧吊耳圆端面作为粗基准,用后钢板弹簧吊耳圆端面与两个工艺孔作为精基准。
主要加工工序安排是先以后钢板弹簧吊耳外圆端面互为基准加工出端面,再以端面定位加工出工艺孔。
在后续工序中除个别工序外均用端面和工艺孔定位加工其他孔与平面。
整个加工过程均选用组合机床。
关键词后钢板弹簧吊耳,加工工艺,专用夹具序言夹具设计是在完成了机械制造工艺学,公差测量等等专业课之后,进行的一次理论联系实际的综合运用,使我对专业知识、技能有了进一步的提高,为以后从事专业技术的工作打下基础。
后钢板弹簧吊耳工艺过程卡+工序卡+说明书

铣端面钻孔机械制造工艺学课程设计说明书设计题目设计“后钢板弹簧吊耳”零件的机械加工工艺规程及工艺装备(年产量为10000件)设计者:指导老师:2011年3月8日机械制造工艺学课程设计任务书题目:设计“后钢板弹簧吊耳”零件的机械加工工艺规程及工艺装备(年产量为件)内容:1、零件图 1张2、毛坯图 1张3、机械加工工艺过程综合卡 1张4、机械结构装配图 1张5、结构设计零件图 1张6、课程设计说明书 1份班级:学生: 指导老师:目录设计任务书序言————————————————— 4一.零件的分析二.工艺规程设计(一)确定毛坯的制造形式———————————— 4(二)基面的选择———————————————— 5(三)制订工艺路线——————————————— 5(四)机械加工余量、工序尺寸及毛坯尺寸的确定—— 7(五)确定切削用量及基本工时—————————— 8三.夹具设计(一)问题的提出———————————————— 13(二)卡具设计————————————————— 13四.参考文献—————————————————14序言机械制造工艺学课程设计是我们学完了大学的全部基础课、技术基础课以及大部分专业课之后进行的。
这是我们在进行毕业设计之前对所学各课程的一次深入的综合性的总复习,也是一次理论联系实际的训练,因此,它在我们四年的大学生活中占有重要的地位。
就我个人而言,我希望能通过这次的课程设计对自己未来将从事的工作进行一次适应性训练,从中锻炼自己分析问题、解决问题的能力,为今后参加祖国的四化建设打下一个良好的基础。
由于能力所限,设计尚有许多不足之处,恳请各位老师给与指教。
一、零件分析(一)、零件的作用:题目给出的零件是CA10B解放牌汽车后钢板弹簧吊耳。
后钢板弹簧吊耳的主要作用是载重后,使钢板能够得到延伸,伸展,能有正常的缓冲作用。
因此汽车后钢板弹簧吊耳零件的加工质量会影响汽车的工作精度、使用性能和寿命。
{生产工艺技术}后钢板弹簧吊耳工艺设计说明书附工艺卡

{生产工艺技术}后钢板弹簧吊耳工艺设计说明书附工艺卡一、产品简介后钢板弹簧吊耳是一种用于吊装物体的金属零件,常用于汽车、机械等行业的装配过程中。
它由钢板经过冲压成形,具有轻巧、坚固和可靠的特点。
二、工艺流程1.材料准备:选择优质的高强度钢板作为原材料。
根据产品图纸和要求,将钢板切割成合适的尺寸和形状。
2.表面处理:对钢板进行酸洗处理,去除表面的氧化物和杂质,以提高表面质量和粘附力。
3.工装设计:根据产品图纸和要求,设计制作冲压模具和模具夹具,确保工艺的精度和效率。
4.冲压成形:将经过表面处理的钢板放入冲床中,通过冲压模具施加压力,使钢板按照产品图纸的形状和尺寸进行成形。
5.冲孔:根据产品要求,在钢板上进行冲孔处理,以便后续组装和连接。
6.清洗:将冲压成形的钢板进行清洗,去除冲床过程中产生的切屑和残留物,保证产品的整洁和质量。
7.表面处理:对清洗后的钢板进行防锈处理,以提高产品的抗腐蚀性能和表面光洁度。
8.检验:对成品进行严格的质量检验,包括外观质量、尺寸精度和冲孔位置等方面,确保产品符合技术要求。
三、工艺卡工艺卡是对整个工艺流程的详细记录和规范,包括每个工序的操作步骤、质量控制要点和注意事项等。
下面是后钢板弹簧吊耳的一份工艺卡示例:工序:冲压成形设备:冲床操作员:XXX日期:XXXX年XX月XX日产品:后钢板弹簧吊耳1.将经过表面处理的钢板放置在冲床上,调整模具的位置和夹具的固定度。
2.打开冲床电源,调整冲床的压力和行程,以适应钢板的厚度和冲孔要求。
3.进行冲压成形,注意观察冲床的运行情况和成形效果,及时调整和纠正。
4.冲床完成后,取出成品,并进行必要的清洗和防锈处理。
5.进行产品的质量检验,包括外观质量、尺寸精度和冲孔位置等方面。
6.合格产品进行包装,不合格产品返工或报废。
四、总结后钢板弹簧吊耳的生产工艺按照以上流程进行,能够保证产品的质量和性能。
工艺卡的使用和记录对于工艺的规范和改进具有重要意义,要经常总结经验教训,不断改进和优化工艺流程,提高产品的质量和生产效率。
吊耳的设计说明书1

1.1.零件的工艺分析
由零件图可知,其材料为:35号钢,优质碳素结构钢有良好的塑性和适当的强度,工艺性能较好,焊接性能尚可,大多在正火状态和调质状态下用。
由后钢板弹簧吊耳零件图知可将其分为两组加工表面。
它们相互间有一定的位置要求。
现分析如下:
(1)以∅30mm两外圆端面为主要加工表面的加工面。
这一组加工表面包括:∅30mm两外圆端面的铣削,加工∅37mm的孔,其中∅30mm两外圆端面表面粗糙度要求为Ra6.3,∅37mm的孔表面粗糙度要求为Ra1.6
(2)以∅30mm孔为主要加工表面的加工面。
这一组加工表面包括:2个以∅30mm的孔,2个∅10.5mm的孔、2个∅30mm孔的内外两侧面的铣削,宽度为4mm 的开口槽的铣削、表面粗糙度要求为Ra50,2个∅30mm在同一中心线上数值为∅0.01的同轴度要求。
其中2个∅30mm的孔表面粗糙度要求为Ra1.6μm,2个∅10.5mm的孔表面粗糙度要求12.5Ramm,2个∅10.5mm孔的内侧面表面粗糙度要求为12.5Ramm,2个∅30孔的外侧面表面粗糙度要求为50Ramm,宽度为4mm的开口槽的表面粗糙度要求为50Ramm。
2.弹簧吊耳零件的技术要求。
后钢板弹簧吊耳工艺设计与夹具设计说明文书

课程设计说明书题目:批量生产“后钢板弹簧吊耳”机加工工艺规程及专用夹具设计学院:机电工程学院专业班级:学生:学号:指导教师:绪论机械的加工工艺及夹具设计是在完成了大三的全部课程之后,进行的一次理论联系实际的综合运用,使我对专业知识、技能有了进一步的提高,为以后从事专业技术的工作打下基础。
机械加工工艺是实现产品设计,保证产品质量、节约能源、降低成本的重要手段,是企业进行生产准备,计划调度、加工操作、生产安全、技术检测和健全劳动组织的重要依据,也是企业上品种、上质量、上水平,加速产品更新,提高经济效益的技术保证。
夹具又是制造系统的重要组成部分,不论是传统制造,还是现代制造系统,夹具都是十分重要的。
因此,好的夹具设计可以提高产品劳动生产率,保证和提高加工精度,降低生产成本等,还可以扩大机床的使用围,从而使产品在保证精度的前提下提高效率、降低成本。
所以对机械的加工工艺及夹具设计具有十分重要的意义。
通过这次课程设计,可对以前学过的课程进行一次综合的深入的总复习,把学习到的理论知识和实际结合起来,从而提高自己分析问题,解决问题的能力。
目录1 课程设计任务书 (1)1.1设计题目 (1)1.2设计任务 (1)1.3设计要求 (1)2 后钢板弹簧吊耳加工工艺规程设计 (2)2.1零件分析及毛坯设计 (2)2.1.1零件功用 (2)2.1.2零件的结构和技术要求分析 (3)2.2工艺过程设计所应采取的相应措施 (4)2.3后钢板弹簧吊耳加工定位基准的选择 (5)2.3.1 确定毛坯的制造形式 (5)2.3.2粗基准的选择 (5)2.3.3精基准的选择 (6)2.3.4零件表面加工方法的确定,吊耳各表面加工方案 (6)2.4 工艺路线的制定 (6)2.4.1 工艺方案一 (7)表2.1 工艺方案一表 (7)2.4.2 工艺方案二 (7)表2.2 工艺方案二表 (8)2.4.3 工艺方案的比较与分析 (8)2.5机床设备及工艺装备的选用 (9)2.5.1机床设备的选用 (9)2.5.2工艺装备的选用 (9)2.6机械加工余量、工序尺寸及毛坯尺寸的确定 (9)φ孔 (11)2.7 工序6 加工10.5mm2.7.1切削用量的确定 (11)2.7.2加工余量,工序尺寸及公差的确定 (14)2.8本章小结 (14)φ工艺孔夹具设计 (16)3 加工10.5mmφ工艺孔夹具设计 (16)3.1加工10.5mm3.2定位方案的分析和定位基准的选择 (16)3.3定位元件的设计 (17)3.4定位误差分析 (18)3.5切削力的计算与夹紧力分析 (19)3.6钻套、衬套、钻模板及夹具体设计 (19)3.7夹具精度分析 (22)3.8夹具设计及操作的简要说明 (23)3.9本章小结 (23)心得 (23)1 课程设计任务书1.1设计题目①设计某个零件的制造工艺和某道工序的专用夹具。
后钢板弹簧吊耳工艺设计说明书(附工艺卡)

【课程设计说明书】[附工艺卡片]班号:0351001学生姓名:***指导老师:杨志兵贺鸣目录一、零件的工艺分析及生产类型的确定1.零件的作用 (2)2.零件的工艺分析 (2)3.零件的生产类型 (2)二、选择毛坯、确定毛坯尺寸1.选择毛坯 (3)2.确定机械加工余量、毛坯尺寸和公差 (3)3.确定机械加工余量 (3)4.确定毛坯尺寸和尺寸公差 (4)三、选择加工方法、制定工艺路线1. 定位基准的选择 (4)2. 零件表面加工方法的选择 (4)3. 制定工艺路线 (5)四、工序设计1.机床设备的选用 (7)2.工艺装备的选用 (7)五、确定切削用量及基本时间工序1:“粗铣φ37孔的两φ60端面至78” (7)工序2:“粗铣两φ30孔内侧端面距离至75” (8)工序3:“精铣两φ30孔内侧端面距离至〖77〗_0^(+0.07)” (9)工序4:“粗铣两φ30孔外侧端面与内侧端面距离至22” (11)工序5:“半精铣φ37孔的两φ60端面至〖76〗_(-0.6)^(-0.2)” (12)工序6:“钻φ20孔 (13)工序7:“扩钻φ35孔” (14)工序8:“扩φ35孔至φ36.75” (15)工序9:“铰φ36.75孔至φ〖37〗_0^(+0.05)” (16)工序10:“钻φ15孔” (17)工序11:“钻φ28孔” (18)工序12:“扩φ28孔至φ29.93” (19)工序13:“铰φ29.93孔至φ〖30〗_0^(+0.05)” (20)工序14:“钻φ10.5孔” (21)工序15:“粗铣4mm开口槽” (22)附录工序卡课程设计题目:“板簧吊耳”零件工艺设计一、零件的工艺分析及生产类型的确定1.零件的作用后钢板弹簧吊耳的主要作用是在汽车载重之后,使得钢板能够自由延伸、伸展,起到正常的缓冲作用,故弹簧吊耳的加工质量会影响汽车的使用性能和寿命。
吊耳的作用包括减震功能、阻尼缓冲功能以及导向功能。
后钢板弹簧吊耳实用工艺及夹具设计说明书
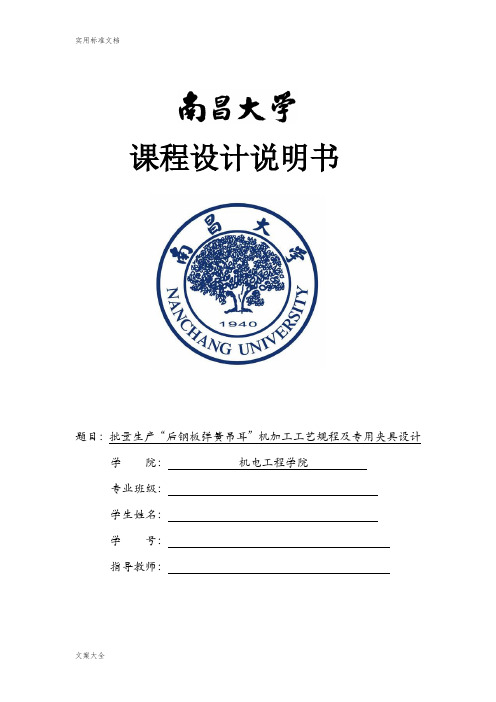
课程设计说明书题目:批量生产“后钢板弹簧吊耳”机加工工艺规程及专用夹具设计学院:机电工程学院专业班级:学生姓名:学号:指导教师:绪论机械的加工工艺及夹具设计是在完成了大三的全部课程之后,进行的一次理论联系实际的综合运用,使我对专业知识、技能有了进一步的提高,为以后从事专业技术的工作打下基础。
机械加工工艺是实现产品设计,保证产品质量、节约能源、降低成本的重要手段,是企业进行生产准备,计划调度、加工操作、生产安全、技术检测和健全劳动组织的重要依据,也是企业上品种、上质量、上水平,加速产品更新,提高经济效益的技术保证。
夹具又是制造系统的重要组成部分,不论是传统制造,还是现代制造系统,夹具都是十分重要的。
因此,好的夹具设计可以提高产品劳动生产率,保证和提高加工精度,降低生产成本等,还可以扩大机床的使用范围,从而使产品在保证精度的前提下提高效率、降低成本。
所以对机械的加工工艺及夹具设计具有十分重要的意义。
通过这次课程设计,可对以前学过的课程进行一次综合的深入的总复习,把学习到的理论知识和实际结合起来,从而提高自己分析问题,解决问题的能力。
目录1 课程设计任务书 (1)1.1设计题目 (1)1.2设计任务 (1)1.3设计要求 (1)2 后钢板弹簧吊耳加工工艺规程设计 (2)2.1零件分析及毛坯设计 (2)2.1.1零件功用 (2)2.1.2零件的结构和技术要求分析 (3)2.2工艺过程设计所应采取的相应措施 (4)2.3后钢板弹簧吊耳加工定位基准的选择 (4)2.3.1 确定毛坯的制造形式 (4)2.3.2粗基准的选择 (5)2.3.3精基准的选择 (5)2.3.4零件表面加工方法的确定,吊耳各表面加工方案 (6)2.4 工艺路线的制定 (6)2.4.1 工艺方案一 (6)表 2.1 工艺方案一表 (7)2.4.2 工艺方案二 (7)表 2.2 工艺方案二表 (7)2.4.3 工艺方案的比较与分析 (7)2.5机床设备及工艺装备的选用 (8)2.5.1机床设备的选用 (8)2.5.2工艺装备的选用 (8)2.6机械加工余量、工序尺寸及毛坯尺寸的确定 (9)φ孔 (11)2.7 工序6 加工10.5mm2.7.1切削用量的确定 (11)2.7.2加工余量,工序尺寸及公差的确定 (13)2.8本章小结 (14)φ工艺孔夹具设计 (15)3 加工10.5mmφ工艺孔夹具设计 (15)3.1加工10.5mm3.2定位方案的分析和定位基准的选择 (15)3.3定位元件的设计 (16)3.4定位误差分析 (17)3.5切削力的计算与夹紧力分析 (18)3.6钻套、衬套、钻模板及夹具体设计 (18)3.7夹具精度分析 (20)3.8夹具设计及操作的简要说明 (21)3.9本章小结 (21)心得 (22)1 课程设计任务书1.1设计题目①设计某个零件的制造工艺和某道工序的专用夹具。
弹簧吊耳课程设计说明书

目录机械制造工艺学课程设计任务书 (Ⅰ)序言 (2)1 零件分析 (2)1.1 零件的作用 (2)1.2 零件的工艺分析 (2)2 铸造工艺方案设计 (3)2.1确定毛坯的成形方法 (3)2.2确定铸造工艺方案 (3)2.3确定工艺参数 (4)3 机械加工工艺规程设计 (4)3.1基面的选择 (4)3.2确定机械加工余量及工序尺寸 (7)3.3确定切削用量及基本工时 (10)4 夹具 (25)5 总结 (30)参考文献 (31)序 言机械制造工艺学课程设计是在我们学完了机械制造技术基础和机械制造工艺学等课程之后进行的。
这是我们对所学各课程的一次深入的综合性的总复习,也是我们在走进社会工作岗位前的一次理论联系实际的训练。
因此,它在我们的大学课程学习中占有重要的地位。
就我个人而言,我希望能通过这次课程设计对自己未来将从事的工作进行一次适应性训练,从中锻炼自己分析问题,解决问题的能力。
此次课程设计,需要我们熟练掌握基础课程知识以及充分了解专业学科知识,如运用软件绘制零件图、毛坯图,零件加工工艺路线的定制等。
同时通过设计让我们学会查询各种专业相关资料,有助于扩展我们的知识面。
总的来说,就是要让所学理论知识在实际设计过程中得到最充分地利用,并不断提高自己解决问题的能力。
本设计的内容是制订弹簧吊耳加工工艺规程。
通过分析弹簧吊耳从毛坯到成品的机械加工工艺过程,总结其结构特点、主要加工表面,并制定相应的机械加工工艺规程。
针对弹簧吊耳零件的主要技术要求,选择适当的夹具进行装夹。
本着力求与生产实际相结合的指导思想,本次课程设计达到了综合运用基本理论知识,解决实际生产问题的目的。
由于个人能力所限、实践经验少、资料缺乏,设计尚有许多不足之处,恳请老师给予指教1.对零件进行工艺分析:1.1 零件的作用弹簧吊耳的主要作用是载重后,使钢板能够得到延伸,伸展,能有正常的缓冲作用。
因此汽车后钢板弹簧吊耳零件的加工质量会影响汽车的工作精度、使用性能和寿命。
后钢板弹簧吊耳课程设计说明书

机械制造工艺学课程设计任务书题目:设计“后钢板弹簧吊耳”零件的机制加工工艺规程及工艺装备(大批量生产)内容:1. 毛坯图 1张2. 机械加工工艺过程卡片 1张3. 机械加工工序卡片4-5张4. 机床夹具装配总图1张5. 夹具主要零件图(包括夹具体) 2张6. 课程设计说明书1张院系:_____机电学院___________专业:姓名:__________________学号:______ ____指导老师:____ ______________2013年9月17日目 录目 录 .............................................................................................................................................. 2 1 绪 论 .......................................................................................................................................... 2 2 后钢板弹簧吊耳加工工艺规程设计 ......................................................................................... 3 2.1零件的分析 . (3)2.1.1零件的作用..................................................................................................................... 3 2.1.2零件的工艺分析 ............................................................................................................. 4 2.1.3弹簧吊耳零件的技术要求 ............................................................................................. 5 2.2确定毛坯,绘制毛坯图 ........................................................................................................ 5 2.2.1 确定毛坯的制造形式 ........................................................................................................ 5 2.2.2 确定毛坯的尺寸公差和机械加工余量 ........................................................................ 5 2.2.4吊耳毛坯尺寸公差及机械加工余量 ............................................................................. 6 2.3拟定弹簧吊耳工艺路线 ........................................................................................................ 7 2.3.1 零件的加工定位基准 .................................................................................................... 7 2.3.2零件表面加工方法的确定,吊耳各表面加工方案 ..................................................... 8 2.3.3工序顺序的安排 ............................................................................................................. 8 2.3.4 工艺方案的比较与分析 ................................................................................................ 9 2.3.5确定吊耳工艺路线 ....................................................................................................... 10 2.4机床设备及工艺装备的选用 .............................................................................................. 11 2.4.1机床设备的选用 ........................................................................................................... 11 2.4.2工艺装备的选用 ........................................................................................................... 11 2.5加工余量,工序尺寸和公差的确定 .................................................................................. 11 2.5.1工序1—加工mm 60 孔两外圆端面至设计尺寸的加工余量,工序尺寸和公差的确定 ....................................................................................................................................... 11 2.5.2吊耳各加工表面的机械加工余量 ............................................................................... 14 2.6确定切削用量及基本工时(机动时间) .. (15)1 绪 论机械的加工工艺及夹具设计是在完成了大三的全部课程之后,进行的一次理论联系实际的综合运用,使我对专业知识、技能有了进一步的提高,为以后从事专业技术的工作打下基础。
后钢板弹簧吊耳锻造工艺设计

工艺设计说明书一、分析研究产品的零件图零件名称:后钢板弹簧吊耳材料:35钢质量:2.6kg产量:10000件技术要求:1、铸造拔模斜度不大于7°2、硬度HBS149-1873、涂漆二、锻造工艺性分析1. 加工目的、环境及锻后现象分析( 1 )分析零件锻造的目的是侧重于成形、减少加工余量,还是侧重于提高锻件的力学性能。
( 2 )分析工厂的现有设备、技术力量和加工能力。
( 3 )分析锻后零件性能可能变化的趋势。
2. 零件结构形状对锻造适应性的分析该零件的结构较为复杂,使用自由锻造方法是很难实现的,且由于该零件的材料为炭钢,塑性很好,采用模锻加工后即可以满足零件的锻造要求。
三、绘制锻件图锻件图是根据零件图绘制的。
模锻件图是在零件图的基础上考虑了加工余量、锻造公差、工艺余块等参数后绘制而成的。
四、参数选择参数选择主要依据该零件的机加工表面粗糙度要求,以及加工表面的几何尺寸大小,利用专门的查询工具查找相应的参数,综合对锻造工艺和方式的分析。
对于粗糙度要求为12.5的表面选取加工余量为2mm。
五、确定坯料质量和锻件尺寸1 、确定坯料质量坯料质量包括锻件本身的质量、加热时氧化烧损、切头时的损失及冲孔时的芯料损失等。
(1) 计算锻件质量根据锻件的形状和基本尺寸,可计算出锻件的质量:m 锻= pV=3.35kg式中 m 锻—锻件质量; p —锻件材料的密度( kg/dm3 ); V —锻件的体积( dm3);(2)确定飞边槽的形式和尺寸选定飞边槽的尺寸为(选Ⅰ型飞边槽):h飞=1mm , h1=4mm , b=8mm , b1=25mm , R=2mm , S飞=120 mm2。
飞边体积 V飞=710×0.7×120=59640 mm3M切=0.059640*7.85=0.47kg(3) 计算坯料质量坯料的质量包括锻件本身的质量、加热时氧化烧损、切头时的损失及冲孔时的芯料损失等。
m坯= m锻+ m烧+ m切+ m芯=3.35+0.0777+0.47+0=3.9kg式中 m坯—坯料质量( kg );m锻—锻件质量( kg );—氧化烧损的质量( kg );—表示对拔长工件的切头损失( kg );—冲孔时冲掉的芯料损失( kg );一般按下面经验公式估算:圆形截面= 1.81矩形截面= 2.36 B2H式中—切头质量( kg );D —切头部分直径( dm );B —切头部分宽度( dm );H —切头部分高度( dm )。
郭枫后钢板弹簧吊耳设计说明书
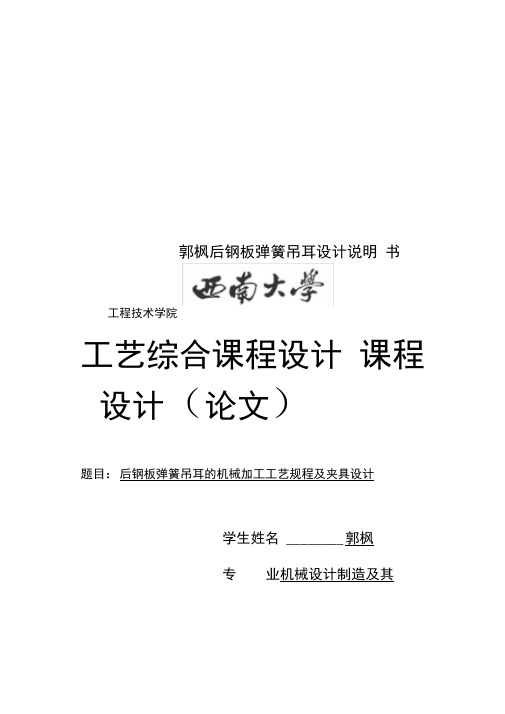
郭枫后钢板弹簧吊耳设计说明书工程技术学院工艺综合课程设计课程设计(论文)题目:后钢板弹簧吊耳的机械加工工艺规程及夹具设计学生姓名 ________ 郭枫专业机械设计制造及其自动化学号222012322220120班级2012级机制3班指导教师 _______ 何辉波成绩 _________________ 工程技术学院2015 年7 月机械制造工艺学课程设计任务书题目:“后钢板弹簧吊耳”零件的机制加工工艺规程及夹具设计内容:1、零件图 1 张2、毛坯图 1 张3、工艺过程卡 1 张4、工序卡 3 张4、夹具总装图 1 张5、夹具体零件图 3 张6、装配图 1 张7、课程设计说明书 1 份原始资料:零件图样,零件年产量5000 件/年。
2016 年06 月目录1引言 .....................................................................32课程设计的目的 ...........................................................3错误! 未定义书签。
3零件的工艺分析 ...........................................................43.1 零件结构及工艺性分析 (4)3.2 零件的的技术要求分析 (6)3.3 工艺过程设计所应采取的相应措施 (6)4毛坯的选择...............................................................7 5零件机械加工工艺路线 .....................................................75.1 定位基准的选择 (7)5.1.1 粗基准的选择 (7)5.1.2 精基准的选择 (8)5.2 工艺路线的制定 (8)5.2.1 加工方法的选择和加工阶段的划分 (8)5.2.2 工艺路线的拟定 (8)5.2.2.1 工艺方案一 (9)5.2.2.2 工艺方案5.2.2.3 工艺方案的比较与分析 (9)5.3加工余量及工序尺寸的拟定 .............................................105.3.1 毛坯尺寸的确定105.3.2 确定机械加工余量和工序尺寸 (12)5.4 切削用量的确定 .....................................................135.4.1 工序10切削用量的确定 (13)5.4.2 工序20切削用量的确定 (14)5.4.3 工序60切削用量的确定 (15)5.5 时间定额的确定 (15)5.5.1 工序10时间定额的确定 (15)5.5.2 工序20时间定额的确定 (16)5.5.3 工序60时间定额的确定 (18)6加工3O 0.045mm工艺孔夹具设计 (19)6.1加工工艺孔30 O.045mm夹具设计方案的确定 (19)6.2 选择定位方式及定位元件 (20)6.3 导向装置的确定 (20)6.4 切削力的计算与夹紧力分析 (20)6.5 夹紧机构的确定 (21)6.6 定位误差分析 (21)7小结 .....................................................................228参考文献................................................................23 9致谢.....................................................................23后钢板弹簧吊耳的机械加工工艺规程及夹具设计郭枫西南大学工程技术学院,重庆400716 1 引言机械的加工工艺及夹具设计是在我们完成机械原理和机械设计课程设计之后的又一次重要课程设计,本次课程设计安排在我们完成全部专业课程学习之后,旨在检验我们对所学专业知识的综合运用能力以及理论联系实际的能力。
后钢板弹簧吊耳说明书
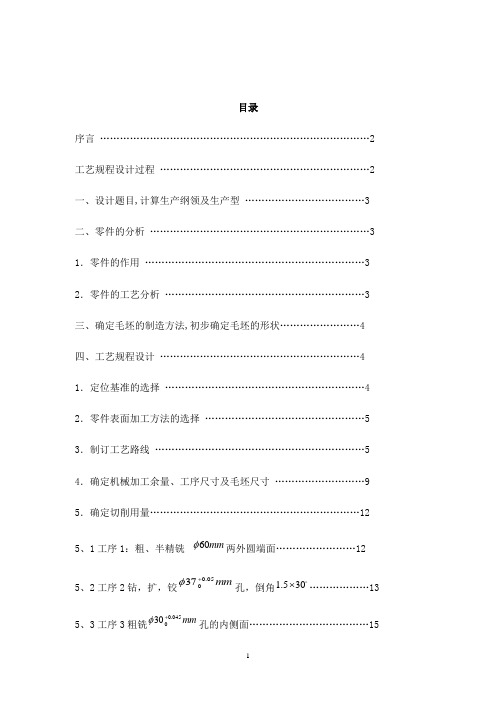
目录序言 .................................................................................2 工艺规程设计过程 ...............................................................2 一、设计题目,计算生产纲领及生产型 ....................................3 二、零件的分析 ..................................................................3 1.零件的作用 ..................................................................3 2.零件的工艺分析 ............................................................3 三、确定毛坯的制造方法,初步确定毛坯的形状........................4 四、工艺规程设计 ............................................................4 1.定位基准的选择 ............................................................4 2.零件表面加工方法的选择 ................................................5 3.制订工艺路线 ...............................................................5 4.确定机械加工余量、工序尺寸及毛坯尺寸 ...........................9 5.确定切削用量...............................................................12 5、1工序1:粗、半精铣60mm φ两外圆端面 (12)5、2工序2钻,扩,铰mm05.0037+φ孔,倒角1.530⨯ (13)5、3工序3粗铣mm045.0030+φ孔的内侧面 (15)5、4工序4粗铣mm045.0030+φ孔的外侧面 (17)5、5工序5:钻,扩,铰mm30045.00+φ孔 (18)5、6工序6:钻,扩10.5mm φ孔................................................19 5、7工序7:粗铣宽度为4mm 的开口槽.......................................20 四、结论 ..............................................................................21 五、参考资料 (21)序 言一、设计目的:现代机械制造工艺设计是宽口径机械类专业学生在学完了《机械制造技术基础》等技术基础和专业课理论之后进行的一个实践教学环节。
广州大学厚钢板弹簧吊耳说明书
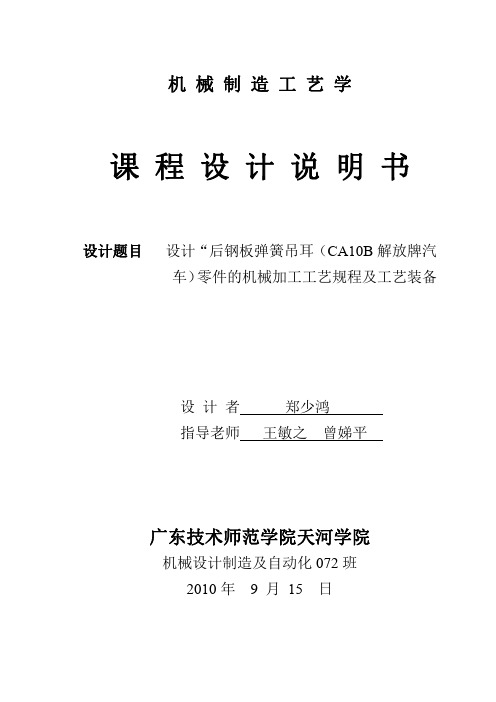
机械制造工艺学课程设计说明书设计题目设计“后钢板弹簧吊耳(CA10B解放牌汽车)零件的机械加工工艺规程及工艺装备设计者郑少鸿指导老师王敏之曾娣平广东技术师范学院天河学院机械设计制造及自动化072班2010年9月15日目录目录 (1)搞要 (3)1绪论 (4)2后钢板弹簧吊耳加工工艺规程设计 (6)2.1零件的分析 (6)2.1.1零件的作用 (6)1.1.2零件的工艺分析 (6)2.2工艺过程设计所应采取的相应措施 (7)2.3后钢板弹簧吊耳加工定位基准的选择 (7)2.3.1确定毛坯的制造形式 (7)2.3.2粗基准的选择 (7)2.3.3精基准的选择 (8)2.4工艺路线的制定 (8)2.4.1工艺方案一 (8)2.4.2工艺方案二 (8)2.4.3工艺方案的比较与分析 (9)2.5机械加工余量、工序尺寸及毛坯尺寸的确定 (9)2.6确定切削用量及基本工时(机动时间) (10)2.7时间定额计算及生产安排 (19)2.8本章小结 (21)3粗铣后钢板弹簧吊耳内侧端面夹具设计 (22)3.1粗铣后钢板弹簧吊耳内侧端面夹具设计 (22)3.2定位方案的分析和定位基准的选择 (22)3.3定位误差分析 (22)3.4铣削力与夹紧力计算 (23)3.5定向键与对刀装置设计 (24)3.6夹紧装置及夹具体设计 (26)3.7夹具设计及操作的简要说明 (27)3.8本章小结 (27)工艺孔夹具设计 (28)4加工30mm4.1加工30mm φ工艺孔夹具设计 (28)4.2定位方案的分析和定位基准的选择 (28)4.3定位误差分析 (28)4.4切削力的计算与夹紧力分析 (29)4.5钻套、衬套、钻模板及夹具体设计 (29)4.6夹具精度分析 (31)4.7夹具设计及操作的简要说明 (31)4.8本章小结................................................................................................................................325加工10.5mm φ工艺孔夹具设计. (33)5.1加工mm 5.10φ工艺孔夹具设计 (33)5.2定位方案的分析和定位基准的选择 (33)5.3定位元件的设计 (33)5.4定位误差分析 (35)5.5切削力的计算与夹紧力分析 (35)5.6钻套、衬套、钻模板及夹具体设计 (36)5.7夹具精度分析 (37)5.8夹具设计及操作的简要说明 (38)5.9本章小结 (38)结论 (39)参考文献................................................................................................................40致谢.. (40)摘要本次设计是对后钢板弹簧吊耳零件的加工工艺规程及一些工序的专用夹具设计。
后钢板弹簧吊耳工艺设计说明书

【课程设计说明书】[附工艺卡片]班号:0351001学生姓名:黄思翰指导老师:杨志兵贺鸣目录一、零件的工艺分析及生产类型的确定1.零件的作用 (2)2.零件的工艺分析 (2)3.零件的生产类型 (2)二、选择毛坯、确定毛坯尺寸1. 选择毛坯 (3)2. 确定机械加工余量、毛坯尺寸和公差 (3)3. 确定机械加工余量 (3)4. 确定毛坯尺寸和尺寸公差 (4)三、选择加工方法、制定工艺路线1. 定位基准的选择 (4)2. 零件表面加工方法的选择 (4)3. 制定工艺路线 (5)四、工序设计1.机床设备的选用 (7)2.工艺装备的选用 (7)五、确定切削用量及基本时间工序1:“粗铣φ37孔的两φ60端面至78” (7)工序2:“粗铣两φ30孔内侧端面距离至75” (8)工序3:“精铣两φ30孔内侧端面距离至〖77〗_0^(+0.07)” (9)工序4:“粗铣两φ30孔外侧端面与内侧端面距离至22” (11)工序5:“半精铣φ37孔的两φ60端面至〖76〗_(-0.6)^(-0.2)” (12)工序6:“钻φ20孔 (13)工序7:“扩钻φ35孔” (14)工序8:“扩φ35孔至φ36.75” (15)工序9:“铰φ36.75孔至φ〖37〗_0^(+0.05)” (16)工序10:“钻φ15孔” (17)工序11:“钻φ28孔” (18)工序12:“扩φ28孔至φ29.93” (19)工序13:“铰φ29.93孔至φ〖30〗_0^(+0.05)” (20)工序14:“钻φ10.5孔” (21)工序15:“粗铣4mm开口槽” (22)附录工序卡1课程设计题目:“板簧吊耳”零件工艺设计一、零件的工艺分析及生产类型的确定1.零件的作用后钢板弹簧吊耳的主要作用是在汽车载重之后,使得钢板能够自由延伸、伸展,起到正常的缓冲作用,故弹簧吊耳的加工质量会影响汽车的使用性能和寿命。
吊耳的作用包括减震功能、阻尼缓冲功能以及导向功能。
后钢板弹簧吊耳说明书

目录绪论 (1)1 后钢板弹簧吊耳的工艺分析 (2)1.1 后钢板弹簧吊耳的用途 (2)1.2后钢板弹簧吊耳的技术要求 (2)1.3审查后钢板弹簧吊耳的工艺性 (3)1.4 确定后钢板弹簧吊耳 (3)2 确定毛坯、绘制毛坯简图 (4)2.1 选择毛坯 (4)2.2 确定毛坯的尺寸公差和机械加工余量 (4)2.3绘制后钢板弹簧吊耳锻造毛坯简图 (5)3 拟定后钢板弹簧吊耳工艺路线 (7)3.1 定位基准的选择 (7)3.2 表面加工方法的确定 (6)3.3 工艺路线的制定 (8)4 机床设备及工艺装备的选用 (10)4.1 机床设备的选用 (10)4.2 工艺设备的选用 (10)5 加工余量、工序尺寸和公差的确定 (11)6 切削用量、时间定额的计算 (12)6.1切削用量的计算 (12)6.2 时间定额的计算 (13)结论 (16)致谢 (17)参考文献 (18)绪论本次设计是对后钢板弹簧吊耳零件的加工工艺规程及一些工序的专用夹具设计。
后钢板弹簧吊零件的主要加工表面是平面及孔。
由加工工艺原则可知,保证平面的加工精度要比保证孔的加工精度容易。
所以本设计遵循先面后孔的原则。
并将孔与平面的加工明确划分成粗加工和精加工阶段以保证加工精度。
基准选择以后钢板弹簧吊耳大外圆端面作为粗基准,以后钢板弹簧吊耳大外圆端面与两个工艺孔作为精基准。
主要加工工序安排是先以后钢板弹簧吊耳大外圆端面互为基准加工出端面,再以端面定位加工出工艺孔。
在后续工序中除个别工序外均用端面和工艺孔定位加工其他孔与平面。
整个加工过程均选用组合机床。
关键词:后钢板弹簧吊耳;加工工艺;专用夹具;1 后钢板弹簧吊耳的工艺分析1.1 后钢板弹簧吊耳的用途题目给出的零件是CA10B 解放牌汽车后钢板弹簧吊耳。
后钢板弹簧吊耳的主要作用是载重后,使钢板能够得到延伸,伸展,能有正常的缓冲作用。
因此汽车后钢板弹簧吊耳零件的加工质量会影响汽车的工作精度、使用性能和寿命。
- 1、下载文档前请自行甄别文档内容的完整性,平台不提供额外的编辑、内容补充、找答案等附加服务。
- 2、"仅部分预览"的文档,不可在线预览部分如存在完整性等问题,可反馈申请退款(可完整预览的文档不适用该条件!)。
- 3、如文档侵犯您的权益,请联系客服反馈,我们会尽快为您处理(人工客服工作时间:9:00-18:30)。
1.零件的分析1.1零件的作用题目给出的零件是CA10B 解放牌汽车后钢板弹簧吊耳。
后钢板弹簧吊耳的主要作用是载重后,使钢板能够得到延伸,伸展,能有正常的缓冲作用。
因此汽车后钢板弹簧吊耳零件的加工质量会影响汽车的工作精度、使用性能和寿命。
汽车后钢板弹簧吊耳主要作用是减震功能、阻尼缓冲部分功能、导向功能。
1.2零件的工艺分析后钢板弹簧吊耳共有三组加工表面,现分述如下:1)以Ø3705.00+mm 孔为中心的加工表面这一组加工表面包括:一个Ø3705.00+mm 的孔,尺寸为762.06.0--mm 的与Ø3705.00+mm 孔相垂直的平面,其中主要加工表面为Ø3705.00+mm 的孔;2)以Ø30045.00+mm 孔为中的加工表面这一组加工表面包括:两个Ø30045.00+mm 的孔,以及尺寸为77074.00+与两个Ø30045.00+mm 孔相垂直的内平面,以及两个孔的外表面;3)以Ø10.5mm 孔为中心的加工表面 这一组加工表面包括:两个Ø10.5mm 的孔 4) 以Ø3705.00+mm 的孔和两个Ø30045.00+mm 的孔为基准,铣4mm 的槽由上面分析可知,加工时应先加工一组表面,再以这组加工后表面为基准加工另外一组。
2 后钢板弹簧吊耳加工工艺规程设计2.1零件的分析2.1.1零件的作用题目给出的零件是CA10B 解放牌汽车后钢板弹簧吊耳。
后钢板弹簧吊耳的主要作用是载重后,使钢板能够得到延伸,伸展,能有正常的缓冲作用。
因此汽车后钢板弹簧吊耳零件的加工质量会影响汽车的工作精度、使用性能和寿命。
汽车后钢板弹簧吊耳主要作用是减震功能、阻尼缓冲部分功能、导向功能。
`图2.1 后钢板弹簧吊耳零件图2.1.2确定毛坯的制造形式零件材料为Q235。
由于生量已达到大批生产的水平,而且零件的轮廓尺寸不大,故可以采用锻造成型,这对提高生产效率,保证加工质量也是有利的。
2.2基面的选择基准面选择是工艺规程设计中的重要工作之一。
基面选择的正确与合理,可以使加工质量得到保证,生产效率得以提高。
否则,加工工艺过程中会问题百出,更有甚者,还会造成零件大批报废,使生产无法正常进行。
2.2.1粗基准的选择。
以Ø30mm孔一侧端面为粗基准,以消除z,x,y三个自由度,然后加一个辅助支承。
粗基准选择应当满足以下要求:(1)粗基准的选择应以加工表面为粗基准。
目的是为了保证加工面与不加工面的相互位置关系精度。
如果工件上表面上有好几个不需加工的表面,则应选择其中与加工表面的相互位置精度要求较高的表面作为粗基准。
以求壁厚均匀、外形对称、少装夹等。
(2)选择加工余量要求均匀的重要表面作为粗基准。
例如:机床床身导轨面是其余量要求均匀的重要表面。
因而在加工时选择导轨面作为粗基准,加工床身的底面,再以底面作为精基准加工导轨面。
这样就能保证均匀地去掉较少的余量,使表层保留而细致的组织,以增加耐磨性。
(3)应选择加工余量最小的表面作为粗基准。
这样可以保证该面有足够的加工余量。
(4)应尽可能选择平整、光洁、面积足够大的表面作为粗基准,以保证定位准确夹紧可靠。
有浇口、冒口、飞边、毛刺的表面不宜选作粗基准,必要时需经初加工。
(5)粗基准应避免重复使用,因为粗基准的表面大多数是粗糙不规则的。
多次使用难以保证表面间的位置精度。
为了满足上述要求,基准选择以后钢板弹簧吊耳大外圆端面作为粗基准,先以后钢板弹簧吊耳大外圆端面互为基准加工出端面,再以端面定位加工出工艺孔。
在后续工序中除个别工序外均用端面和工艺孔定位加工其他孔与平面。
2.2.2精基准的选择。
根据基准重合和互为基准原则,选用设计基准作为精基准,当设计基准与工序基准不重合时,应该进行尺寸换算。
2.3制订工艺路线制订工艺路线的出发点,应当是使零件的几何形状,尺寸精度及位置精度等技术要求得到合理的保证。
在生产纲领为中批生产的条件下,可以考虑采用万能性机床配以专用夹具来提高生产效率。
除此以外,还应当考虑经济效率,以便使生产成本尽量下降。
2.3.1工艺方案一:工序一粗铣Ø37mm孔端面。
工序二精铣Ø37mm孔端面。
工序三扩,粗铰,精铰Ø37mm孔并加工倒角1.5×45。
工序四粗铣Ø30mm孔端面。
工序五扩,粗铰Ø 30mm孔并加工倒角1×45°工序六粗铣尺寸为77mm的孔端面。
工序七精铣尺寸为77mm的孔端面。
工序八钻2-Ø 10.5mm孔。
工序九 铣宽为4mm 的槽 工序十 去毛刺 工序十一 检查。
2.3.2 工艺方案二:工序一 粗铣Ø37mm 孔端面。
工序二 粗镗Ø37mm 孔,倒角1.5×45°。
工序三 粗铣Ø30mm 孔外端面。
工序四 粗铣Ø30mm 孔内端面。
工序五 扩,粗铰Ø 30mm 孔并加工倒角1×45°。
工序六 粗镗Ø37mm 孔。
工序七 半精铣Ø37mm 孔端面。
工序八 半精铣Ø37mm 孔端面。
工序九 钻2-Ø10.5mm 孔。
工序十 铣宽为4mm 的槽 工序十一 去毛刺。
工序十二 检查.2.4. 工艺方案的比较与分析上述两个工艺方案的特点在于:方案一是先加工60mm φ两外圆端面,然后再以此为基面加工Ø3705.00+mm 孔,再加工10.5mm φ孔,0.043030mm φ孔,最后加工0.043030mm φ+孔的内外侧面以及宽度为4mm 的开口槽铣,则与方案二相反,先加工0.04330mm φ+孔的内外侧面,再以此为基面加工10.5mm φ孔,0.043030mm φ孔,宽度为4mm 的开口槽,最后加工60mm φ两外圆端面,Ø3705.00+mm 孔,经比较可见,先加工60mm φ两外圆端面,以后位置度较易保证,并且定位及装夹都较方便,但方案一中先加工10.5mm φ孔,0.043030mm φ孔,再加工0.043030mm φ+孔的内外侧面,不符合先面后孔的加工原则,加工余量更大,所用加工时间更多,这样加工路线就不合理,同理,宽度为4mm 的开口槽应放在最后一个工序加工。
所以合理具体加工艺如下:工序一粗铣Ø37mm孔端面。
工序二粗镗Ø37mm孔。
工序三粗铣Ø30mm孔外端面。
工序四粗铣Ø30mm孔内端面。
工序五扩Ø29.8mm孔工序六铰Ø30mm孔、倒角1×45°。
工序七精镗Ø37mm孔、倒角1.5×45°。
工序八精铣Ø37mm孔端面。
工序九精铣Ø30mm孔端面。
工序十钻2-Ø10.5mm孔。
工序十一铣4mm槽。
工序十二去毛刺。
工序十三检查。
2.5机械加工余量、工序尺寸及毛坯尺寸的确定“后钢板弹簧吊耳”零件材料为Q235,硬度HBS为149~187,生产类型为大批量生产,采用铸造毛坯。
根据上述原始资料及加工工艺,分别确定各加工表面的机械加工余量,工序尺寸及毛坯尺寸如下:1.Ø37mm孔毛坯为空心,参照《机械加工工艺手册》,确定工序尺寸为 Z=2.6mm。
由锻件复杂系数为S1,锻件材质系数取M1, 毛坯尺寸为Ø34.4。
根据《机械加工工艺手册》加工余量分别为:粗镗:Ø36mm 2Z=1.6mm精镗:Ø37mm 2Z=1.0mm2.Ø30mm孔毛坯为空心,参照《机械加工工艺手册》,确定工序尺寸为 Z=2.0mm。
由锻件复杂系数为S1,锻件材质系数取M1, 毛坯尺寸为Ø28根据《机械加工工艺手册》加工余量分别为:扩孔:Ø29.8mm 2Z=1.8mm铰孔:Ø30mm 2Z=0.2mm3. Ø37mm 孔、Ø30mm 孔端面的加工余量。
参照《机械加工工艺手册》,取加工精度F2 ,由锻件复杂系数为S3, 两孔外侧单边加工余量为Z=2mm 。
锻件材质系数取M1, 复杂系数为S3, 确定锻件偏差为2.16.0+- mm 和1.15.0+-mm 。
根据《机械加工工艺手册》加工余量分别为:Ø37mm 孔端面:粗铣 2Z=3.0mm 精铣 2Z=1.0mm Ø30mm 孔端面:粗铣 2Z=4.0mm 4. Ø10.5mm 孔毛坯为实心,不出孔 ,为自由工差。
根据《机械加工工艺手册》加工余量分别为: 钻孔:Ø10.5mm 2Z=10.5mm由于本设计规定的零件为中批生产,可采用调整法加工,因此在计算最大、最小加工余量时,可按调整法加工方式予以确定。
毛坯名义尺寸:122+2×2=126mm 毛坯最大尺寸:126+2×1.3=128.6mm 毛坯最小尺寸:126-2×0.7=124.6mm 铣后最大尺寸:122+0=122mm 铣后最小尺寸:122-0.17=121.83mm将以上计算的工序间尺寸及公差整理成下表: (mm )2.5.1工序一:粗铣Ø37mm 孔端面。
本设计采用查表法确定切削用量。
1. 加工条件工件材料:35钢,锻造。
加工要求:铣Ø37mm 端面,Ra6.3μm 。
机床:X51立式铣床。
刀具:YT15硬质合金面铣刀,齿数Z=5,w d =100mm 。
2. 计算切削用量根据《切削手册》 20.0=z f mm/z切削速度:根据相关手册 取118=v m/min 8.37510011810001000=⨯⨯==ππdw v n s (r/min ) 现采用X51立式铣床,根据机床说明书,取n w =375 r/min 。
故实际切削速度 5.11710003751001000=⨯⨯==ππww n d v (m/min )当n w =375 r/min 时,工作台每分钟进给量m f 应为 37537552.0=⨯⨯==w z m zn f f (mm/min ) 查机床说明书,取 375=m f mm/min 切削工时 27.037510021==++=m m f l l l t (min ) m t 为加工一侧端面的时间,总工时 528.0264.02=⨯=t (min )2.5.2工序二.粗镗Ø37mm 孔。
根据《机械加工工艺手册》查得镗Ø37mm 孔的进给量ƒ=0.3——1.0mm ,按机床 规格取f =0.6mm ,切削速度,根据相关手册及机床说明书,取v=30mm/s ,加工孔径0d =Ø36mm。