01 QC七大手法-特性要因图(鱼骨图)
品质管理:QC七大手法.

QC七大手法品管七手法,也叫品管七工具,是目前全世界都应用比较广的品质管理工具,它具有简单、实用的特性。
它们分别是:查检表、层别法、鱼骨图、柏拉图、散布图、管制图、直方图。
QC七大手法,是一种管理用的工具,学习它就需要掌握它们的主要精神和思考模式。
它们之间的应用关系如下:查检表:用来在现场收集数据,尽量让现场作业简单而有效,它是其它六手法的起点。
层别法:用来对收集来的数据进行分类,以利于统计分析,找出细部问题,通常需要查检表设定相并没有栏位,也是其它手法的一个基础。
鱼骨图:用来对一个现象或结果进行原因深入细致的分析,通常用来找原因及因素,最好同层别法结合起来使用。
柏拉图:用来对多种问题或原因进行分析,找出最大问题或原因,以利用工具积极地提升,实现花较少成本做好更多的事情。
散布图:用来对收集来两个或两个以上的问题或特性的数据,找出之间可能的相关性.管制图:用来了解品质在过程中的变化状态和预测品质下一步可能之状况,有助于提前发现问题,是实现第一次就把事情做好的基本步骤之一.如图所示:第一种手法-—查检表(Check Sheet)一、定义查检表就是一种为了便于收集数据,使用简单记号填记并予统计整理,并作进一步分析或作为核对、检查之用的一种表格或图表.二、查检表的种类1、记录用(或改善用)查检表主要功用在于根据收集的数据以调查不良项目、不良主因、工程分布、缺点位置等状况,并作为原始记录的凭证。
2、点检用查检表主要功用是为要确认作业实施、机械整备的实施状况,或为预防发生不良或事故、确保安全时使用。
三、查检表作法1、查检表设计的步骤A、明确目的—-将来要能提出改善对策及数据,因之必需把握现状解析,与使用目的相配合。
B、决定查检项目——从特性要因图圈选的4~6项决定。
C、决定检查的方式——全检或抽检。
D、决定查检细则-—查检基准、查检数量、查检时间与期间、查检对象之决定,并决定收集者、记录符号.E、设计表格实施查检。
QC七大手法培训资料(一)课件

柏拉图(五)
• 改善效果之确认
(元)
改善前
(%)
25000
支 20000
100
75 累
出 15000
計
金 10000
50 比
額 5000
25 率
0
0
伙零水教交其
食用電育際他
費 錢 瓦費 費
斯
費
(元)
改善後
(%)
25000
支 20000
效果
100 累
出 15000
計
金 10000
50 比
額 5000
按产品别分
1000
898
81.92%
88.33%
94.59%
97.68%
100.00% 100.00% 80.00%
69.40%
60.00%
500
162
0
不良数 不良率 累计不良率
隔音垫 898
69.40% 69.40%
顶蓬 162 12.52% 81.92%
40.00%
83
后搁板 83
6.41% 88.33%
加油隊伍長
車輛集中
等候停車隊伍長
婚喪隊伍多 油管不夠多 特定節日出門
收費速度過慢
節日遊行多
上下班時間 尖峰時段
用餐時間
車輛停靠不當
出門時間不對
為何 每天 都會 塞車 至少 一至 兩小 時?
. 24
特性要因图(七)
举例
机器
(大原因) 量
年久失修
具 偏
(小原因)
人 培訓不足
(中原因)
差
量具不穩
某
情緒不穩定
QC七大手法-特性要因图的制作方法

流程优化
03
在流程优化工作中,特性要因图可用于分析流程中存在的问题,
确定改进方向和优化措施。
02 特性要因图的制作步骤
确定分析对象
明确问题
首先需要明确要分析的问题或特性, 确定分析对象,并对其进行定义和描 述。
确定关键特性
根据分析对象,确定关键特性,即需 要重点关注和改善的特性。
确定影响因子
收集数据
通过箭头表示因果关系。箭头指向表示 响因子之间的因果关系、绘制特性要因
影响的方向,箭头指向结果,表示影响
图等。
因子对质量特性的影响。
分析影响因子的重要性
分析影响因子的重要性是特性要因图的重要应用之一。通过分析特性要因图,可 以确定影响质量特性的各个因素的重要程度,以便优先处理对质量特性影响较大 的因素。
案例一:产品不良率的分析
总结词
通过特性要因图分析产品不良率,找出主要影响因素。
详细描述
首先收集产品不良率的相关数据,然后使用特性要因图将这些数据绘制出来,通过观察图形,找出影 响产品不良率的主要因素,如原材料质量、生产工艺、员工操作等,进而制定相应的改善措施。
案例二:生产效率的提升
总结词
利用特性要因图分析生产流程,优化生 产效率。
层次分明
合理安排各因素之间的层级关系,确保布局层次 分明,易于理解。
统一标准
在制作过程中,遵循统一的标准和规范,确保不 同特性要因图之间的可比性和一致性。
改进影响因子的分类方法
明确分类标准
制定明确的分类标准,确保影响因子能够准确归类,避免交叉和 重叠。
动态调整
根据实际情况对分类进行调整,以满足不同特性和问题的分析需 求。
分析影响因子的重要性的方法包括计算影响因子对质量特性的影响程度、分析影 响因子的发生频率和影响程度等。这些方法可以帮助分析人员了解影响质量特性 的主要因素,并制定相应的改进措施。
QC七大手法

品质管理手法培训内容QC方法是品质管理的重要方法,有新旧七大手法之分.我们比较熟悉旧的七大QC手法,即层别法、散布图法、鱼骨图(特性要因图)法、查检表法、直方图法、管制图法、柏拉图法。
而新的七大手法, 即KJ分析法、PDPC分析法、矢线分析法、矩阵数据分析法、关系图法、矩阵图法、系统图法应用就比较陌生。
其实新旧七大手法都是建立在品质管理应用的基础上,通过实际的应用能帮助我们了解解决品质问题的实际方法,进而达到全面解决品质问题的目的。
解决问题的步骤:1、发现问题;2、了解现状;3、原因分析;4、临时措施/长期措施;5、效果确认;6、标准化;7、制度化;8、处理客户投诉。
QC原则:三现七大手法三不“三现”为现场保留、现物、现实数据(情况)“三不”为不接受不良、不制造不良、不留出不良。
一、质量管理的基本概念与原理1、质量质量指产品或服务,满足规定或潜有需要的特征和特性的总和。
它既包括有形产品也包括无形产品;既包括产品内在的特性、也包括产品外在的特性。
即包括了产品的适用性和符合性的全部内涵。
2、工业产品质量工业产品质量指工业产品适合一定的用途,满足人们需要所具备的特性和特性的总和,也即是产品的适用性。
它包括产品的内在特性,如产品的结构、物理性能、化学成分、可靠性、精度、纯度等;也包括产品的外在特性,如形状、外观、色泽、音响、气味、包装等;还有经济特性如成本、价格、使用维修费等,以及其他方面的特性如交货期、污染公害等。
工业产品的不同特性,区别了各种产品的不同用途,满足了人们的不同需要。
可把各种产品的不同特性概括为:适用性、可靠性、安全性、寿命、经济性等。
3、工作质量工作质量指对产品质量有关的工作对于产品质量保证程度。
工作质量涉及到企业所有部门和人员,也就是说企业中每个科室、车间、班组,每个工作岗位都直接或间接地影响着产品质量,其中领导者的素质最为重要,起着决定性的作用,当然广大职工素质的普遍提高,是提高工作质量的基础。
QC七大手法详细讲解
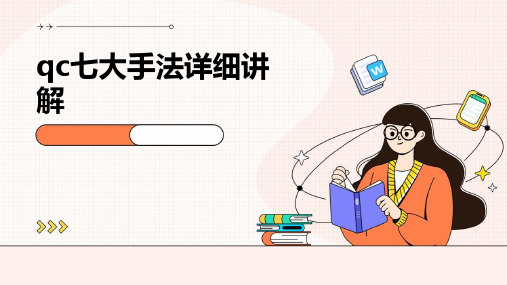
目录
CONTENTS
• 特性要因图法 • 柏拉图法 • 层别法 • 查检表法 • 散布图法 • 控制图法 • 直方图法
01 特性要因图法
定义与特点
01
定义
特性要因图法,也称为鱼骨图 ,是一种用于表示因果关系的 图形工具,通过将问题的结果 (特性)与可能的原因(要因 )关联起来,帮助分析者系统 地研究和分析问题。
使用步骤
1. 确定变量
明确需要分析的两个变量,例如尺寸和不良 率。
2. 收集数据
收集相关数据,确保数据的准确性和完整性。
3. 绘制散布图
将数据绘制在散布图上,通常使用笛卡尔坐标系 。
4. 分析关系
观察散布图上的点分布,分析两个变量之间的关系 。
5. 判断关联性
根据散布图中点的分布情况,判断两个变量是否 具有关联性。
绘制控制图
根据收集到的数据,绘制控制图,包 括中心线、上控制限和下控制限。
监控与分析
在控制图上标记数据点,观察数据点 的分布情况,分析生产过程的稳定性。
异常处理
当发现异常数据点时,及时采取措施 进行调整和改进,确保生产过程的稳 定性和产品质量。
实例分析Βιβλιοθήκη 实例某生产线上生产一种电子元件,通过控 制图法监控其电阻值。
6. 监控与评估
对改进措施的实施效果进行监控 和评估,确保问题得到有效解决
。
5. 制定改进措施
针对关键因素制定相应的改进措 施,并实施。
4. 确定关键因素
根据柏拉图的分析结果,确定对 质量影响最大的关键因素。
实例分析
在某生产线上,产品不合格率较高,通过柏拉图法分析发现,主要原因是 原材料质量不稳定和生产设备老化。
QC七大手法及SPC制程统计方法

20世纪40年代,享有品质管理之父美誉的美国电气工程师Joseph Juran 引入了Pareto理论。正是Juran决 定将这一80/20比值称为“柏拉法则”(The Pareto Principle),将柏拉法则运用于业务度量有助于从“有 用多数”(useful many,即其它80%)中分离出“重要少数”(vital few,具有最重要影响的20%)。柏拉 图通过标示频率阐明柏拉法则——频率出现越高的内容对结果影响越大。柏拉图是品质管理七大基础手段之 一。图中横轴显示自变量,因变量由条形高度表示。表示累积相对频率的点对点图可附加至该条形图上。由 于统计变量值按相对频率顺序排列,图表可清晰显示哪些因素具有最大影响力,以及关注哪些方面可能会产 生最大利益。
噪音高
无专人保养
训练不足 设备老化
技术不高
人员流动率高 人员疲劳
作业条件不全 某作业流程不当
法
交期不稳 文件不足
料
品质欠佳 售后服务不好
不良 率高
二.QC(Quality Control)七大手法之查检 表
6
1.定义
一种为了便于收集数据,而使用简单记号填写并予以统计整理,以便于作进一步分析或作为核对,检查之 用而设计的表格或图表。
•中心偏左的直方图
下限
•中心偏右的直方图
中心值
上限
直方图偏向规格的下限, 并伸展至规格下限左侧。 表示已产生部分超出规格 下限要求的不良品。
10
QC 七大手法

二:柏拉图
制作步骤 步骤一:决定不良的分类项目 步骤二:收集数据 步骤三:整理数据(计算累计比率) 步骤四:生成图表(双轴折线图加直条图)
二:柏拉图
制作步骤 步骤一:决定不良的分类项目
以JS-09340 为例
气泡大 不良 电镀 不良
功能 不良 不 良 项 目 PCB板 板 歪斜 有胶
二:柏拉图
真因
至现场对现物收集数据后,所验证出来的真正原因。 现场对现物收集数据后, 验证出 的真正原ห้องสมุดไป่ตู้。 物收集数据后
一:特效要因图(鱼骨图)
步骤三:制作特性要因图并补充遗漏原因
3.6 圈选真因
在所列的原因中认为影响最大的画上红圈,再从画上红圈的原因当中指出认为影响更 大者再画上红圈,一直检讨下去。最后圈选出重要原因。
制作步骤
演绎法(一般到特殊) 归纳法(特殊到一般)
由每位成员先写原因,再将大家的原因集合起来,删去重复的原因后,再加以分类。 优点:想出之原因会比较完整,不会被局限在某一范围內。 缺点:需花费较长时间。
归纳法(小骨集约法)
(1) 发掘主题之不良原因 (2) 依原因內容分类 (3) 制作特性要因图并补充遗漏原因 (4) 筛选重要原因
原材料 结构本身造成
一:特效要因图(鱼骨图)
注意事项
通过脑力激荡的方法,表达出全员的意见,发挥团队合作的力量。 发扬刨根问底的精神,依“5W2H”的方法,直到把细节问题暴露出来为止。 所有大、中、小要因间须有因果关系。 应按特性绘制多张鱼骨图,原因分析越细越好,特别是圈出的重要原因。 鱼头方向要正确,原因型向右,对策型向左。 记录必要的事项于鱼骨图旁,如产品型号、制程名称、参与人员、当班干部等。
制作步骤 步骤二:按照不良分类项目收集数据
品质管制(QC)七大手法-特性要因分析图、

重点把握
柏 拉 图
100%
1.决定改善目标(80/20) 能够以前几项为改善 的要点,可忽略最后 2.明了改善的效果 几项,卲常说的“前 3.掌握重点分析 三项”原则
简易有效
查 检 表
1.日常管理用 2.收集数据用 3.改善管理用
帮助每个人在最短时 间内完成必要之数据 收集
21
QC 旧 7 大手法简介
13
CATCHER
QCC小组活动流程:
1 选择课题 2 现状调查 3 设定目标 P 4 分析原因 5 确定主因 6 制定对策 D C 7 实施对策 8 检查效果 目标达到 A 目标未达到
QCC小组活劢流程的管理技术主要有三个方面 1、遵循PDCA循环 2、以事实为依据,用资料说话 3、应用统计方法 Goal
层 别 法 比较作用 1.应用层别区分法,找出 借用其他图形,本身 数据差异的因素而对症 无固定图形 下药. 2.以4M之每1M进行层别 1.了觋两种因数戒数据之 间的关系。 2.发现原因不结果的关系 应用范围较受限制 相关易懂 散 布 图 赺势明朗
管 制 图
1.掌握制程现况的品质 2.发现异常及时采取行动
文件编号: 209030001A 生效日期:2010年1月18日 修改日期:
品质管制(QC)七大手法
--- 特性要因分析图、柏拉图
1
请关闭手机戒调成震动
请把心帶来 请充分讨论不分享 请带空杯来,装点水回去
2
课程安排表
课 程 讲 师 考试
√ √ √ √
实作
√ √ √ √
助教1 助教2
汤智根 吴海燕 杨春会 邰雪妮 张志华 王德闯 曹刚 戴石为
表 面 处 理 部
組 立 部
QC七大手法
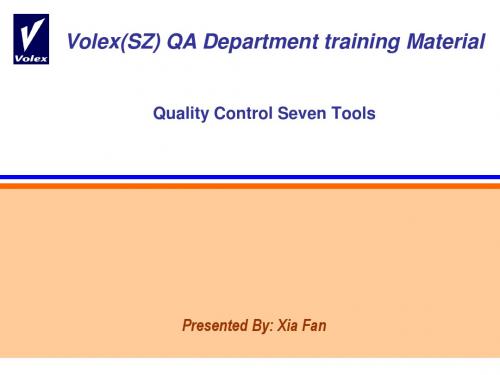
Volex(SZ) QA Department training MaterialQuality Control Seven ToolsPresented By: Xia Fan2th April. 2001Suzhou Quality1Quality Control Seven Tools品质管理需要用科学的管理方法和统计技术,对影响品质的各方面因素进行系统的考虑;对相关数据进行收集、处理、分析;找出形成原因和解决方法;实施改进。
Quality Control Seven Tools品质管理活动中所运用的统计手法一般称为“QC七大手法”:1、检查表(又称点检表)——收集、整理资料;根据事实、数据说话。
2、柏拉图(又称排列图)——确定主导因素;并非对所有原因采取处置,而是先就其中影响较大的2~3项采取措施。
3、因果图(又称特性要因图、鱼骨图)——寻找引发结果的原因;整理原因与结果之关系,以探讨潜伏伏性的问题。
Quality Control Seven Tools4、分层法(又称层别法)——从不同角度层面发现问题;所有数据不可仅止于平均,须根据数据的层次,考虑适当分层。
5、散布图(又称散点图)——展示变量之间的线性关系;6、直方图(数次表)——展示过程的分布情况;凡事物不能完全单用平均值来考虑,应该了解事物均有变异存在,须从平均值与变异性来考虑-。
7、控制图(又称管控图)——识别波动的来源;凡事物不能完全单用平均值来考虑,应该了解事物均有变异存在,须从平均值与变异性来考虑-Quality Control Seven Tools具体步骤是:1、问题的把握点(柏拉图、直方图),2、对问题的现状分析(控制图、检查表、散布图、层别法),3、改善对策实施(利用各种统计方法及固定的技术),4、实施结果的确认(推移图、柏拉图),5、标准化。
Quality Control Seven Tools1.什么是检查表:检查表是一种为了便于收集数据而设计的表格。
QC 七大手法之特性要因图

(1)
方法 作業者
公差錯誤 作業條件 未註明 作業順序顛倒 自行更改條件 不熟練 遺漏作業
尺寸超限
振動不穩 硬度不符規定 控制回路故障 控制回路故障
精度不夠
為 什 麼 製 程 不 良 多
潤滑不足
材料 日期 : 2001 、 5 、30
機械
製作目的 : 為什麼製程不良多
製作者 : 陳文鵬、何石磊
(2) 人員
7、重點應放在解決問題上,並依結困提出對策,其方法可 依 5W2H原則執行。
(1)WHY(為何必要)?
(2)WHAT(目的何在)?
(3)WHERE(在何處做)? (4)WHEN(何時去做)? (5)WHO(由誰來做)? (6)HOW(方法如何)?
(7)HOW MUCH (費用多少)?
8、以事實為依據。 9、依據特性別分別製作不同的特性要因圖。
பைடு நூலகம்
特性
4、依據大要因,再分出中要因 : 細分出中要因之骨線(同樣 為60度插線)應較大骨線細,中要因之選定約3~5為宜,繪製 時應將有因果關係之要因歸於同一骨線內。
特性
5、要更詳細列出小要因 : 運用中要因之方式,可將更詳細 的小要因討論出來。
特性
6、圈出最重要的原因 : 造成一個結果的原因有很多可以透 過搜集數據或自由討論的方式,比較其對特性的影響程度, 以“ ”或“口”圈出來,作為進一步檢討或對策之用。
目錄
1、前言
2、特性要因分析圖之分類
3、如何繪製特性要因圖
4、繪製時注意事項
5、特性要因圖之應用
6、範例 7、實例演練 附、主要不良項目的魚骨圖範例
一.前言
所謂特性要因圖就是當一個問題特性(結果)受到一些要 因(原因)的影響時,吾人將這些要因予以整理,成為有相互 關係且有系統的圖形。簡言之就是將造成某項結果(特性)的 諸多原因(要因),以有系統的方式(圖表)來表達結果與原因 之間的關係,[某項結果的形成,必定有其原因;設法使用圖 解法找出這些原因來]這概念是由日本品管大石川馨博士首 先提出的,特牲要因圖又因是石川馨博士於1952年所發明, 又稱[石川圖]。主要目的在闡明因果關係,亦稱[因果圖], 因其形狀與魚骨相似,故又常被稱呼為[魚骨圖]。
QC七大手法
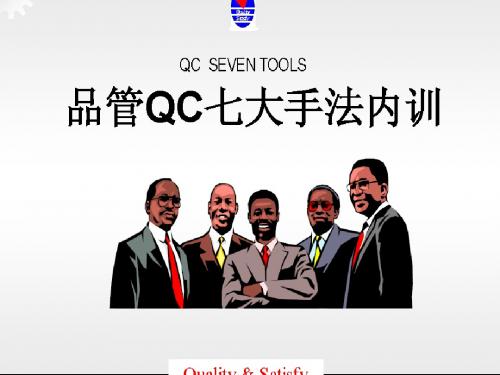
2、准備紙張,绘制特性要因圖的骨架,將特性寫在右端。
3、將可能影響特性的要因分類,填入要因大骨,大骨通
常以5M1E 法進行分類。
4、針對某一個大骨的要因作集体思考(腦力激蕩法)追究為 什么填入要因的中骨,然后從中骨再分成小骨,细骨,同 樣 以箭頭表示,最未端必頇是可以采取行動的要因。
特性要因圖的绘制法
如何看以上直方图?
1. 直方图偏移了规格中心,超出了规格下界。
2. 不成正态分布。是孤岛型,可能夹杂了其他分布 的少量数据。比如工序异常,或开始测量仪器不稳 定。
3. 当出现偏移的情况时,一般先检查其测量法,数
据来源是否同一条件下的,分组情况,以及测量人
员是否有同等。排除这些情况后再作判断。
4. 完整的直方图应增加:制作者,日期,简短评价,
Hale Waihona Puke 東區与西區別…..等。10、以制品層別:新舊品別、標准品或特殊品別、制造別…..等。 11、其他:以良品与不良品別、包裝別、運搬方法別….等。
层别法的製作步骤
(2)利用检查表收集数据 检查表根据需要自行设计。要清晰明简单。
(3)利用数据绘成推移图进行比较了解数 据相对于层别的趋势。
查檢表
為了便于收集數据,使用簡單易于了解的標准
品管七大手法应用说明
查检表:用来在现场收集数据,尽量让现场作业 简单而有效,它是其它六大手法的起点,它是 质量管理平台的基础。 柏拉图:用来对多种问题或原因进行分析,找出 最大问题或原因,它的出发点是抓主要矛盾, 因此具有花较少成本解决最大问题的功效。 鱼骨图:用来对一个现象或结果进行原因深入细 致的分析,通常用来找原因及因素,一般同层别法 结合起来使用。
某厂生产铸铁件,2月 的废品吨数为73.4吨,
QC七大手法1

2
25.38 25.44 25.22 25.30 25.28 25.29 25.27 25.30 25.31 25.56
3
25.58 25.60 25.52 25.54 25.54 25.53 25.47 25.42 25.48 25.50
不良品查检表:
时间 项目 披锋 缩水 气泡 流纹 顶白 毛边 ….. 8:00 0 3 0 0 0 01 …. 9:00 0 2 3 1 4 2 …. 10:00 2 0 3 4 0 2 …… 11:00 4 1 3 4 2 2 …… 12:00 3 0 2 2 3 3 … 13:00 1 0 0 0 1 5 …. 14:00 0 4 5 0 0 0 … 15:00 0 2 1 4 6 1 .. 16:00 …. ….. ….. ….. ….. … . 17:00 ….. … …. …. ….. … .
40
不 良 数
35
30
累 计 不 良 率
不良数 累计不良率
10
0
工程:N69鼠标不良率分析 批量:1000 总不良数:160 时间:04/15/02 分析者:王芳 绘图者:王芳
TO P印 刷 时 插 KE Y 包 装 流 水 线 放 BT 装 M 滚 轮 点 TO P印 油 刷 前 装 装 DI SU SK PP OR 贴 T FO OT
产品生产查检表:
NO 工序 场地 指导性文件 人员 材料 工具 照明 工作服 工作证 检查内容/项目 5S有没有执行,工作台是否布置妥当 SOP和SIP有没有挂在相应的位置 所有工作人员是否到位 各零配件的数量和料号是否已核对 清楚 相关人员的工夹具是否已准备齐全 所有要使用的照明和用电设施已就 续. 是否穿戴整洁 有没有正确配戴 “∨” “×” 备注
qc七大手法,有图有案例从零开始
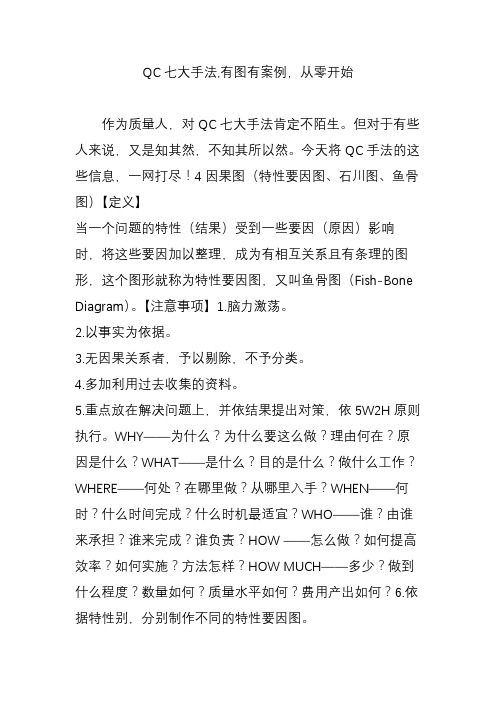
QC七大手法,有图有案例,从零开始作为质量人,对QC七大手法肯定不陌生。
但对于有些人来说,又是知其然,不知其所以然。
今天将QC手法的这些信息,一网打尽!4因果图(特性要因图、石川图、鱼骨图)【定义】当一个问题的特性(结果)受到一些要因(原因)影响时,将这些要因加以整理,成为有相互关系且有条理的图形,这个图形就称为特性要因图,又叫鱼骨图(Fish-Bone Diagram)。
【注意事项】1.脑力激荡。
2.以事实为依据。
3.无因果关系者,予以剔除,不予分类。
4.多加利用过去收集的资料。
5.重点放在解决问题上,并依结果提出对策,依5W2H原则执行。
WHY——为什么?为什么要这么做?理由何在?原因是什么?WHAT——是什么?目的是什么?做什么工作?WHERE——何处?在哪里做?从哪里入手?WHEN——何时?什么时间完成?什么时机最适宜?WHO——谁?由谁来承担?谁来完成?谁负责?HOW ——怎么做?如何提高效率?如何实施?方法怎样?HOW MUCH——多少?做到什么程度?数量如何?质量水平如何?费用产出如何?6.依据特性别,分别制作不同的特性要因图。
7. a.大要因通常代表是一个具体方向。
b.中要因通常代表的是一个概念、想法。
c.小要因通常代表的是具体事件。
8.至少要有4根大骨、3根中骨及2根小骨,且这些要因都不能重复。
【举例】【用途说明】1.掌握问题点。
2.掌握重要要因。
3.确认改善效果。
【改善效果之确认】【效果确认的柏拉图制作要决】必须两个柏拉图并排,分为改善前与改善后。
收集数据的期间和对象必须一致。
季节性的变化应列入考虑。
对于改善项目以外的要因也要加以注意。
【范例:记录用查检表】8层别法【定义】对观察到的现象或所收集到的数据,按照它们共同的特征加以分类、统计的一种分析方法。
是容易观察,有效掌握事实的最有效、最简单的方法。
【用途说明】1.发现问题,界定问题。
2.发掘问题的要因。
3.验证要因产生的影响。
QC七大手法

0.00
其它 102
45.06 62.33
85.14 90.76
91.81 100.00
2017/12/12
15
分析:从图中可看出面饼偏重是面饼品质 状态的主要不良因素,应对其进行分析, 查找偏重形成的原因,可以运用QC手法中 的其他方法进行数据的收集和处理。 经分析对策、进行改进后,于4月份在基 数相同的情况下又进行了柏拉图分析,与 3月份对比如下:面饼偏重的情况减少了 115次。
面饼偏轻 243 64.16
品评不良 187 76.71
块型不良 112 84.23
色泽不良 89 90.20
油炸不良 20 91.54
其它 126 100.00
100.00 80.00 60.00 40.00 20.00 0.00
100.00 80.00 60.00 40.00 20.00
面饼偏 面饼偏 花型不 品评不 块型不 色泽不 油炸不 重 303 24.34 轻 258 良 215 良 164 75.50 良 120 良 70 良 13
为什 么油 炸棕 榈油 品质 不良
环境
方法
2017/12/12
22
特性要因图的制作方法
步骤五、标注制作目的、日期及制作者
物料
原油AV、POV较高 热交换器故障
机器
油炸锅漏水
人员
不知操作标准 责任心不强 油锅不是不锈钢
面团含水高
贮藏温度高
油温标准太高
车间温湿度太高 生产时加淋水
小克面生产太多
为什 么油 炸棕 榈油 品质 不良
不良数 412 301 47.85 243 64.16 187 76.71 112 84.23 89 90.20 20 91.54
QC 七大手法 鱼骨图

1.特性要因圖(CAUSE AND EFFECT DIAGRAM) -異常狀況或不良結果發生時的最有效之要因分析-1-1何謂特性要因圖(1)掌握結果(特性)與原因(要因)之間的關係(2)是改善現場問題之最方便有效的方法(3)形狀很像魚骨,亦稱魚骨圖(4)由石川馨博士研究提出,亦稱石川圖1-2特性要因圖的畫法步驟一、(1)決定品質特性1.品質:不良率,單位缺點數,不良數,……2.成本:損耗量,單位成本,……3.效率:收率,……4.交期:日(月)產量,……5.安全:災害件數,……6.士氣:出勤率,提案改善件數。
(2)自左向右劃一粗線,并將品質特性寫在箭頭的右邊如下圖品質特性步驟二:列出大要因(1)大要因以圈起來。
(2)大要因可依4M(人、械、材料、方法)或制程別來分類,如圖:步驟三:各要因分別再記入中小要因(1)各大要因依連問五次為什麼及合邏輯之原則,分別展開中、小要因。
(2)必須展開至能采取措施之小要因。
步驟四:圈選重要要因(1)根據過去以往之經驗來圈選重要要因。
(2)相關人員共同決定。
(3)圈選4-6項為原則1-3繪制特性要因圖之注意事項(1)集合全員之知識與經驗(a)集合有關人員、現場的主管、技術人員、前後製程人員等。
(b)以自由、無拘束的方式來發言進行。
(c)依照腦力激蕩法(Brain Storming)之原則。
*.禁止批評,歡迎自由聯想,構想越多越好,歡迎搭便車。
(2) 應用5W1H法,把重點放在解決問題上。
依5W1H的方法,重點先放在“為什麼會發生這種問題”。
(a)為何必要(Why)(b)在何處做(Where)(c)何人做(Who)(d)目的為何(What)(e)何時做起(When)(f)如何做(How)(3) 要因要依其重要度不同,加紅圈,紅圈越多表示越重要。
1-4特性要因圖之用途1.用途依目的分為:(a)改善解析用:以改善品質、提高效率、降低成本為目標,進行現狀解析改善時用。
(b)管理用:發生抱怨,不良品或異常時,為找尋原因,采取措施時用。
QC7大手法

车床
冲床
。。。。。。
机器 机床 设备 工夹刀具
磨床 铣床
工具 夹具 刀具 。。。。。。 。。。。。。
资料:
①操作人员: 按个人分,按现场分,按班次分,按经验分;
②机床设备: 按机器分,按工夹刀具分; ③材料: 按供应单位分,按品种分,按进厂批分;
④加工方法: 按不同的加工、装配、测量、检验等方法分, 按工作条件分; ⑤时间: 按上、下午分,按年、月、日分,按季节分; ⑥环境: 按气象情况分,按室内环境分,按电场、磁场影响分;
●统计分析表
●调查表
●检查表
案例一:缺陷项目调查表
缺 陷 项目 表面发花 砂 眼 成型不良 缺 陷 频 数 小计
加工不良 变 形 其 它 合 计
32 23 9 48 7 9 127
分析:事先已对不良项目有明确的划分,通过列表,让
现场操作员在工作进行之中,进行划记号(每一划代 表1PC不良品)来简单记录所发现的不良品数量。
适应范围:可按其性质、来源、 影响等进行分类的情 况下均适应 。
原则:
A。分层要结合生产实际情况进行, 目的不同,分层的方法和粗细 程度不同。
B。分层要合理,要按相同的层次 进行组合分层,以便使问题暴 露的更清楚。
进行步骤:
1) 明确主题 之方面 2)确定相关项目的 内容与隶属关系;
。。。。。。
序 1 日期 08/01 检验数 1000 不良数 4 不良率% 0.40
2
3 4 5
08/02
08/03 08/04 08/05
950
1050 1212 850
3
5 3 1
0.32
0.47 0.25 0.12
6
QC七大手法之鱼骨图

World Class Company
关键功能 主要人物
核心资源
6
流程与关鉴质量特性案例
P
流程
O
C
产出
顾客
制纸浆厂
X1
关鉴质量特性 • •
关鉴制程特性 • •
纸 浆
造纸厂
纸
X2
关鉴质量特性
•纸厂对所需纸浆
所需要和期望的
回馈 特性
外部顾客
链回馈 Ys
关鉴质量特性 •顾客对所用纸 所需要和期望的 特性
World Class Company 10
特性要因图之思考原则
1. 脑力激荡法:BS (Brain Storming)
2. 4M1E法
3. 5W1H
4. 系统图法
5. 创造性思考法
a.特性列举法 b.希望点列举法 c.缺点列举法
6. 自由讨论/井边会议方式,速战速决方式,澡堂集会
World Class Company 11
现况分析
(3)以特性要因为主,利用现场、现物、现实的三现原则整理出有关图形。
2.从要因中追求主要因(真要因):
(1)办清影响度高的要因。 (2)可能实验的,透过实验来验证真因的影响度。
工程解析 或
(3)不可能实验的,由此后的活动结果确认。 (4)仔细调查并验证因果关系,找出主因。
要因解析
从以上两点可以找出影响问题约主要因,然后全体圈员才针对 这些重要的主要因,去观察、分析、思考,以求解决方案。
World Class Company 9
特性要因图的用途
(三)制定操作标准用
当特性要因图如果分析很彻底,则表示对于制 程的变异有充分把握,则在制定或修改操作 标准时,可充分就其原因或对策确实设定标 准。
- 1、下载文档前请自行甄别文档内容的完整性,平台不提供额外的编辑、内容补充、找答案等附加服务。
- 2、"仅部分预览"的文档,不可在线预览部分如存在完整性等问题,可反馈申请退款(可完整预览的文档不适用该条件!)。
- 3、如文档侵犯您的权益,请联系客服反馈,我们会尽快为您处理(人工客服工作时间:9:00-18:30)。
硬 座椅 亮度不足
灯光 黑板反光
言 率 低
其他
环境
8
为何要用特性要因图
有效防止落入思考障碍,是解决问题之好工具
▪ 自我限制 ▪ 「想原因」与「作判断」同时进行 ▪ 「思考」与「记忆」互相干扰
目的:找出影 响结果的要因
▪ 「想原因」与「想对策」混杂
▪ 未系统化而无法专注
9
为何要用特性要因图
▪ 联想力互动以激发想象 ▪ 深入掌握问题的因果,并彻底的分析原因 ▪ 用来分析影响产品质量各种原因的一种有效的方法
文件编号: 209030007A 生效日期:2010年1月18日 修改日期:
品质管制(QC)七大手法系列课程一
查检表
研习公约
请关闭手机或调成震动 请把心带来 请充分讨论与分享 请带空杯来,装点水回去
课程规则:
项目 理论授课
时间 (min)
分值 比例
说明
60
/ 据教材进行理论授课,讲解知识要点
试卷
特性要因图
团长 时间长 离题
主持不差
聊天
争吵 枯燥
气氛不够
圈员
怕失败 消极 心理障碍
未诱导发言
有人泼冷水
临时通知
情绪不好
口吃
会前准备不佳 主题不通知 工具不准备
愿意低 工作劳累 认开会没效果
表达力差
为 何
知识不足
圈
窄
员 发
不知如何开会 未教育训练
怕影响生产
太吵
噪音
主管不关心
应付上级 不参加
温度
对圈长不满 太热
我要变成 齐天大圣!
5
脑力激荡的四大原则
• 禁止批评 • 欢迎自由联想 • 构想越多越好(创意) • 欢迎搭便车
天马行空、童言无忌、天真无邪。 没有范围与其它限制(除了不能批评)。 也许就能从1000的点子中找到重要的点子。
6
特性要因图(Causes & Effects Chart)
● 明确结果(特性)与原因(要因)间的关系 ● 系统化表示 ● 使人一目了然 ● 因状似鱼骨,又称鱼骨图(Fish-Bone Diagram )。 ● 为石川馨教授提出之方法,也称石川图
30
40% 对课堂知识进行回顾
抽签
10
抽签决定需要实作上台发表的圈组
实 作
60%
现场实作
20
将理论实际操作,加深印象,达到学以致用
1. 课堂需准备空白纸实作画图用。 2. 实作部分可视状况带计算机、Note book…等。
特性要因图 (鱼骨图)
脑力激荡 ( Brain Storming )
1938 年奥斯朋博士提出一种会议方法,这种 会议对某一主题尽量让大家在不批评的气氛下,提 出构想,同时利用灵感相互诱导,简而言之,此乃 充分发挥全员脑力,集思广义的技巧。
13
如何划特性要图
材料
机器
人员
步骤3
60° 60°
评价 特性
其他
环境
方法
14
如何划特性要图
步骤4.各大骨依序记入中骨、小骨 ❖反覆“为何?为何?为何?”追至较具体之小要因 ❖应用脑力激荡术(Brain Storming)
15
如何划特性要图
材料
机器
人员
小要因
60° 60°
步骤4
中要因 评价 特性
其他
环境
方法
16
如何划特性要图
步骤5.挑出影响目前问题较大的要因为主要因(红笔圈选) ❖全员参与圈选 ❖4-6项为宜 ❖整理并记录必要事项
17
材料 其他
机器 环境
人员
小要因
60° 60°
中要因
评价 特性
方法
步骤5
18
特性要因图的分析(次料)
19
特性要因图的分析(设备)
20
绘制特性要因图应Байду номын сангаас意事项
❖ 管理用:发生很多抱怨、不良品或异常时,为寻采 原因找取措施时用
❖ 检讨作业标准 ❖ 教育训练及经验之交流
❖ 自左向右画一粗线,并将评价特性写在箭头右边,如下图。
品质特性或现象
如何划特性要图
步骤2.记上背骨
步骤2
❖由左向右画一粗的箭号并于右侧写评价特性后委以
口号
评价 特性
步骤1
如何划特性要图
步骤3.记上大骨(大要因) ❖大骨个数以4-8较适当,通常以4M1E(人员、设备、材 料、方法、环)来分类,并可依工程(流程)别来分类 ❖大要因以口圈起来,并加上箭号到背骨、大骨与背骨相 交一般取60°较洽当 ❖为避免要因遗漏,可加其他项
10
特性要因图的画法
步骤一:明确问题的评价特性 (现象)
❖ 评价特性 :制品尺寸、不良率、成本、……
项目(例) 品质 产量 成本 安全 士气
评价特性 不良率、错误率、抱怨次数.. 产量达成率、作业效率、交期延迟率.. 制造费用、材料成本、损耗率.. 意外件数、公伤工时、工安自我检查不合格率.. 出勤率、提案件数、QCC参与率 ..
• 集合全员之知识与经验让有关人员如前后制程 人员、技术人员等能真心诚意参与说真话者
• 思考重点放在”为什么”而不是”如何解决” • 小要因若是无法采取对策,须再深入 • 若怕要因遗漏,可于隔天再进行一次(应用潜意
识活动)
21
特性要因图的应用
❖ 改善解析用:以改善现场之品质不良现象、成本或 效率时进行现状解析