压力管道检验案例.
压力容器压力管道事故案例
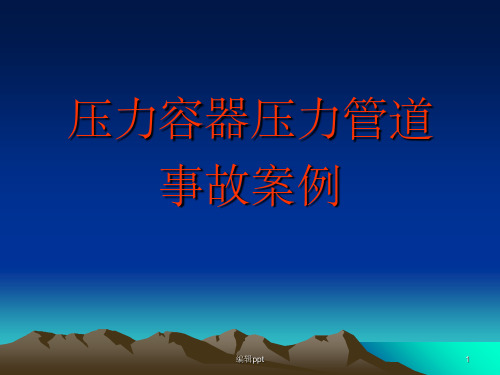
(一)特种设备事故造成10人以上30人以下死亡,或者50人以上 100人以下重伤,或者5000万元以上1亿元以下直接经济损失的;
(二)600兆瓦以上锅炉因安全故障中断运行240小时以上的; (三)压力容器、压力管道有毒介质泄漏,造成5万人以上15万 人以下转移的; (四)客运索道、大型游乐设施高空滞留100人以上并且时间在 24小时以上48小时以下的。
压力容器压力管道 事故案例
编辑ppt
1
压力容器、管道事故概述
• 2005年共发生特种设备严重以上事故274起, 其中特大事故1起,重大事故18起,严重事故 255起,共死亡301人,受伤293人,直接经济 损失6964.69万元。
• 在274起事故中,发生锅炉、气瓶、压力容器、 压力管道(下称承压类设备)事故133起,死亡 94人,受伤211人,直接经济损失4065.64万元 (其中“土锅炉”事故18起,死亡7人,受伤34 人,直接经济损失144.41万元。
一般事故: (一)特种设备事故造成3人以下死亡,或者10人以下重伤,或者1万元以
上1000万元以下直接经济损失的; (二)压力容器、压力管道有毒介质泄漏,造成500人以上1万人以下转移
的; (三)电梯轿厢滞留人员2小时以上的; (四)起重机械主要受力结构件折断或者起升机构坠落的; (五)客运索道高空滞留人员3.5小时以上12小时以下的; (六)大型游乐设施高空滞留人员1小时以上12小时以下的。 除前款规定外,国务院特种设备安全监督管理部门可以对一般事故的其他情
2004年4月22日上午,位于浙江宁波小港的浙
江善高化学有限公司双氧水车间发生爆炸火灾事
故,整个车间被毁。距离爆炸现场几百米的民居
窗玻璃全被震破。由于事故地点以北几十米还存
压力管道运行中的检查和监测范文(二篇)
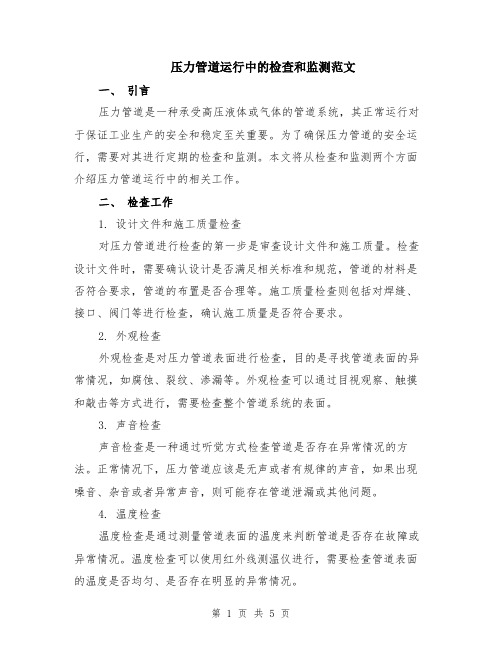
压力管道运行中的检查和监测范文一、引言压力管道是一种承受高压液体或气体的管道系统,其正常运行对于保证工业生产的安全和稳定至关重要。
为了确保压力管道的安全运行,需要对其进行定期的检查和监测。
本文将从检查和监测两个方面介绍压力管道运行中的相关工作。
二、检查工作1. 设计文件和施工质量检查对压力管道进行检查的第一步是审查设计文件和施工质量。
检查设计文件时,需要确认设计是否满足相关标准和规范,管道的材料是否符合要求,管道的布置是否合理等。
施工质量检查则包括对焊缝、接口、阀门等进行检查,确认施工质量是否符合要求。
2. 外观检查外观检查是对压力管道表面进行检查,目的是寻找管道表面的异常情况,如腐蚀、裂纹、渗漏等。
外观检查可以通过目视观察、触摸和敲击等方式进行,需要检查整个管道系统的表面。
3. 声音检查声音检查是一种通过听觉方式检查管道是否存在异常情况的方法。
正常情况下,压力管道应该是无声或者有规律的声音,如果出现噪音、杂音或者异常声音,则可能存在管道泄漏或其他问题。
4. 温度检查温度检查是通过测量管道表面的温度来判断管道是否存在故障或异常情况。
温度检查可以使用红外线测温仪进行,需要检查管道表面的温度是否均匀、是否存在明显的异常情况。
5. 压力检查压力检查是通过测量管道内的压力来判断管道是否正常工作。
压力检查可以使用压力表或者压力传感器进行,需要检查管道内的压力是否在设计范围内,是否存在压力过高或者压力波动的情况。
三、监测工作1. 泄漏监测泄漏是压力管道运行中最常见的问题之一,因此需要进行泄漏监测。
泄漏监测可以通过压力传感器、气体探测器等设备进行,需要定期检查泄漏监测设备的工作状况,确保其灵敏度和准确度。
2. 腐蚀监测腐蚀是压力管道长期运行中不可避免的问题,因此需要进行腐蚀监测。
腐蚀监测可以通过电化学方法、超声波方法等进行,需要检测管道表面的腐蚀程度,并及时采取措施进行修复或更换。
3. 振动监测振动是压力管道运行中常见的问题之一,极端情况下会导致管道疲劳破裂,因此需要进行振动监测。
压力容器培训之压力管道失效分析及事故案例

培训效果评估和改进方向
培训效果评估:通过问卷调查、考试等方式评估培训效果 改进方向:根据评估结果,调整培训内容和方式,提高培训效果 加强实践操作:增加实际操作环节,提高学员实际操作能力 引入新技术和新方法:关注行业新技术和新方法,及时更新培训内容
持续推进安全培训和教育宣传工作
定期组织员工进行 安全培训,提高安 全意识
压力管道检验标准:《压力 管道检验规范》、《压力管 道检验质量控制规范》等
监管部门职责和要求
监管部门:国家质量监督检验 检疫总局
职责:负责压力管道的安全监 管工作
要求:制定压力管道安全技术 规范,监督企业执行情况
处罚措施:对违反规定的企业 进行处罚,确保压力管道安全 运行
企业主体责任落实情况
企业主体责任:企业对压力管 道安全的责任
定期检查压力管道的支 撑和固定情况
定期检查压力管道的安 全阀和泄压阀情况
定期检查压力管道的消 防和应急设备情况
定期检查压力管道的完 整性和密封性
定期检查压力管道的振 动和噪音情况
定期检查压力管道的保 温和隔热情况
定期检查压力管道的报 警和监控系统情况
定期检查压力管道的仪 表和阀门情况
相关法规标准概述
信息公开:公开压 力管道安全监管信 息,接受社会监督
培训对象和内容设计
培训对象:压力管道操作人员、管理人员、维护人员等 培训内容:压力管道基础知识、操作规程、维护保养、安全防护等 培训方式:理论教学、实践操作、案例分析、模拟演练等 培训效果评估:通过考试、实际操作、反馈等方式进行评估
教育宣传形式和渠道选择
加强员工培训, 提高操作技能和 应急处理能力
制定应急预案, 确保在紧急情况 下能够迅速响应 和处理
压力管道现场安装监督检验案例

压力管道现场安装监督检验案例本案例涉及一台新建的石油化工厂,在建设过程中需要安装一段长度为500米的石油输送管道,该管道将用于输送原油。
根据设计要求,管道材质为碳钢,额定工作压力为10MPa。
1.监督检验准备阶段:在安装之前,监督检验工作开始准备。
监督检验人员首先要熟悉设计和施工图纸,了解管道的布置和安装方法。
然后,与工程施工方组织会议,明确监督检验的相关要求和工作流程。
2.施工现场检查:监督检验人员到达施工现场后,首先对施工现场进行检查和评估。
他们要确认地基基础是否满足要求,并检查是否有足够的施工空间和设备。
同时,还需要检查压力管道的接口和组件,确保其符合规范和标准。
3.材料检验:在现场材料检验中,监督检验人员要对管道材料进行严格把关。
他们要检查管道材质是否符合设计要求,并对其进行化学成分和力学性能测试。
另外,还要查验管道配件的合格证书,以确保其质量可靠。
4.施工过程监督:在管道的安装过程中,监督检验人员要对施工现场进行实时监控和记录。
他们会检查焊接和涂层工艺,并对焊口和涂层进行质量评估。
另外,他们还会观察施工工人是否佩戴相关安全设备,确保安全规范得到遵守。
5.现场试验和功能验证:安装结束后,监督检验人员将进行现场试验和功能验证。
他们会进行水压试验,检查管道是否能承受额定工作压力。
同时,也会验证管道的功效,确保其能够稳定输送原油。
6.监督报告和验收:监督检验工作完成后,监督检验人员将撰写监督报告,并提交给工程施工方。
该报告需要详细记录检验过程、发现的问题以及建议的整改措施。
施工方根据监督报告进行相应的整改,并邀请监督检验人员进行验收。
通过上述的监督检验过程,可以及时发现和解决施工中存在的问题,确保压力管道的安装质量和安全性。
这种监督检验工作的重要性不言而喻,在各个行业都是必不可少的一环。
只有通过严格的监督检验,才能有效保障工程的质量和安全,为人们的生命财产提供有效的保护。
压力管道完整性评价原理及案例介绍
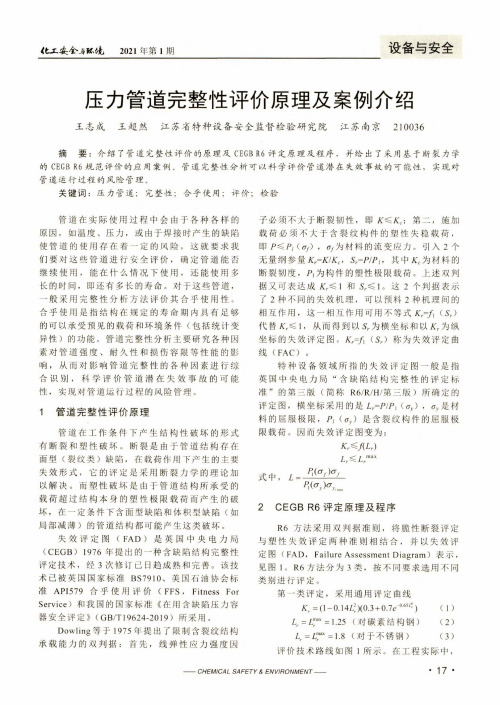
<匕1•妾舍为讯庇2021年第1期设备与安全压力管道完整性评价原理及案例介绍王志成王超然江苏省特种设备安全监督检验研究院江苏南京210036摘要:介绍了管道完整性评价的原理及CEGB R6评定原理及程序,并给出了采用基于断裂力学的CEGB R6规范评价的应用案例。
管道完整性分析可以科学评价管道潜在失效事故的可能性,实现对管道运行过程的风险管理。
关键词:压力管道;完整性;合乎使用;评价;检验管道在实际使用过程中会由于各种各样的原因,如温度、压力,或由于焊接时产生的缺陷使管道的使用存在着一定的风险,这就要求我们要对这些管道进行安全评价,确定管道能否继续使用,能在什么情况下使用,还能使用多长的时间,即还有多长的寿命。
对于这些管道,一般采用完整性分析方法评价其合乎使用性。
合乎使用是指结构在规定的寿命期内具有足够的可以承受预见的载荷和环境条件(包括统计变异性)的功能。
管道完整性分析主要研究各种因素对管道强度、耐久性和损伤容限等性能的影响,从而对影响管道完整性的各种因素进行综合识别,科学评价管道潜在失效事故的可能性,实现对管道运行过程的风险管理。
1管道完整性评价原理管道在工作条件下产生结构性破坏的形式有断裂和塑性破坏。
断裂是由于管道结构存在面型(裂纹类)缺陷,在载荷作用下产生的主要失效形式,它的评定是采用断裂力学的理论加以解决。
而塑性破坏是由于管道结构所承受的载荷超过结构本身的塑性极限载荷而产生的破坏,在一定条件下含面型缺陷和体积型缺陷(如局部减薄)的管道结构都可能产生这类破坏。
失效评定图(FAD)是英国中央电力局(CEGB)1976年提出的一种含缺陷结构完整性评定技术,经3次修订已日趋成熟和完善。
该技术己被英国国家标准BS7910.美国石油协会标准API579合乎使用评价(FFS,Fitness For Service)和我国的国家标准《在用含缺陷压力容器安全评定》(GB/T19624-2019)所采用。
电厂压力管道检验
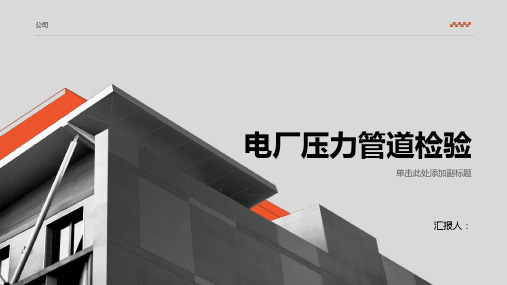
定期对异常情况进行总结,提出改进措施, 提高检验工作质量
检验设备和人员资质要求
人员资质:检验人员需要具 备相应的资质证书,如压力 管道检验员证书等
检验流程:需要按照规定的 检验流程进行,确保检验结
果的准确性
检验设备:需要具备压力管 道检验的专业设备,如压力 表、温度计等
检验记录:需要详细记录检 验过程中的各项数据,以便
管道防腐: 检查管道 防腐涂层 是否完整, 无破损、 脱落等现 象
管道支撑: 检查管道 支撑是否 牢固,无 松动、变 形等现象
管道试压: 进行管道 试压,确 保管道在 规定压力 下无泄漏、 管 理
管道运行检验
压力管道的运行状态检 查
问题及整改建议等
存档管理:检验报告和检验 数据应妥善存档,便于查询
和管理
异常情况处理和报告制度
发现异常情况,立即停止检验工作,并报 告上级领导
及时向上级领导报告异常情况及解决方案, 并等待批准
详细记录异常情况,包括时间、地点、原 因等
异常情况处理完毕后,重新进行检验工作, 并记录处理结果
对异常情况进行分析,找出原因并制定解 决方案
01
提高电厂压力管道检验质量的措施
加强检验人员的培训和管理
定期进行专业培训,提高检验人员的技术水平和业务能力 建立完善的管理制度,明确检验人员的职责和权限 加强检验人员的职业道德教育,提高其责任心和敬业精神 定期进行考核和评估,确保检验人员的工作质量和效率
完善检验设备和器材管理
定期检查和维护检验设备,确保 其性能稳定可靠
外观检验
检查管道表面是否有裂纹、 腐蚀、变形等缺陷
检查管道连接处是否有松 动、漏气等现象
检查管道表面是否有油漆 脱落、锈蚀等现象
压力管道定期检验PPT
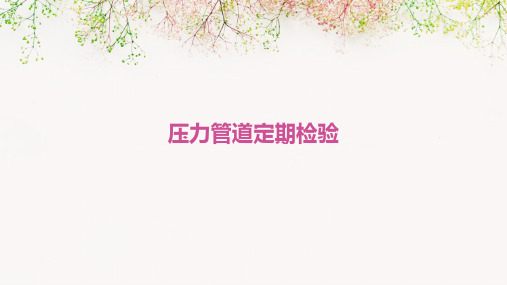
磁粉检测
利用磁粉在漏磁场中的吸附作用,对管道表面和近表面的缺 陷进行检测。
超声检测
利用超声波在材料中的传播特性,对管道内部和表面的缺陷 进行检测。
强度试验与气密性试验
强度试验
通过加压或真空试验,检测管道的强 度和密封性能是否符合要求。
气密性试验
通过充气或抽真空的方式,检测管道 的气密性能是否良好。
管道因流体的不稳定流动 而发生振动,可能导致连 接部位松动或疲劳断裂。
管道因腐蚀导致壁厚减薄 或穿孔,影响其强度和密 封性能。
压力管道的腐蚀与防护
01
电化学腐蚀
由于管道材料与电解质溶液接触,形成原电池而引起的腐蚀。为防止电
化学腐蚀,可采用耐腐蚀材料、涂层保护、阴极保护等措施。
02
化学腐蚀
管道材料与介质直接接触而发生的化学反应。可通过选用耐腐蚀材料、
收集资料
收集管道的设计图纸、施工记 录、验收报告、维修保养记录 等相关资料,以便了解管道的 历史和现状。
现场勘查
对管道的现场进行初步勘查, 了解管道的走向、布局、支撑 、防护等情况,为后续检验工 作提供基础数据。
现场检验
外观检查
对管道的外观进行目视检查,查 看管道是否有变形、裂纹、腐蚀、
磨损等损伤,以及支撑和防护措 施是否完好。
04
压力管道的缺陷与失效模式
压力管道的常见缺陷
01
裂纹
由于制造、安装或使用过程中产生的应力集中,可能 导致管道出现裂纹。
02
腐蚀
由于管道材料与介质之间的化学或电化学反应,导致 管道壁厚减薄或产生腐蚀坑。
03
变形
由于温度、压力或机械力的作用,管道可能发生弯曲 、鼓包或扭曲等变形。
压力容器压力管道事故案例

事故分类
特别重大事故:
(一)特种设备事故造成30人以上死亡,或者100人以上重伤( 包括急性工业中毒,下同),或者1亿元以上直接经济损失的;
(二)600兆瓦以上锅炉爆炸的; (三)压力容器、压力管道有毒介质泄漏,造成15万人以上转移 的; (四)客运索道、大型游乐设施高空滞留100人以上并且时间在 48小时以上的。
事故分类
较大事故: (一)特种设备事故造成3人以上10人以下死亡,或者10人以上50人以下重
伤,或者1000万元以上5000万元以下直接经济损失的; (二)锅炉、压力容器、压力管道爆炸的; (三)压力容器、压力管道有毒介质泄漏,造成1万人以上5万人以下转移的
; (四)起重机械整体倾覆的; (五)客运索道、大型游乐设施高空滞留人员12小时以上的;
直接原因
该设备因腐蚀穿孔导致盐水泄漏,造成三氯化氮形成和富 集;三氯化氮富集达到爆炸浓度和启动事故氯处理装置造 成振动,引起三氯化氮爆炸。
间接原因
⑴、压力容器日常管理差; ⑵、安全隐患整改不力,责 任制不落实; ⑶、对三氯化氮爆炸的机理研究不成熟; ⑷、相关安全技术规定不完善。
案例8:安徽铜陵市金港钢铁有限 公司制氧车间压力管道爆燃事故
⑸ 未按检验报告要求将安全阀及时送检而是自行修理 ;
⑹ 今年六月该厂曾发生因关闭出汽阀造成锅炉破裂的 事故,工厂请厂外无证人员非法修理锅炉,且未从中 吸取教训,致使极为类似的事故再次发生,酿成惨剧 。
▪ 2005年4月14日10时40分左右,安徽铜陵市金港 钢铁有限公司制氧车间调压站发生一起压力管道 爆燃重大事故,造成3人死亡,4人重伤。
▪ 直接原因 ▪ 现场更换承载1.2Mpa压力阀门时,脱脂不净,
2017.10(王军)专题五、工业管道的定期检验及案例分析
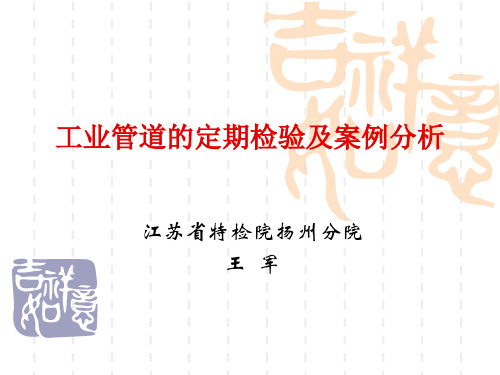
3
1.典型缺陷展示
4
1.典型缺陷展示
5
1.典型缺陷展示
6
1.典型缺陷展示
7
1.典型缺陷展示
8
1.典型缺陷展示
9
1.典型缺陷展示
10
1.典型缺陷展示
11
1.典型缺陷展示
12
1.典型缺陷展示
13
1.典型缺陷展示
14
1.典型缺陷展示
1.2腐蚀 金属的腐蚀按照机理可分为化学腐蚀与电化学腐蚀两 类。
工业管道的定期检验及案例分析
江苏省特检院扬州分院 王 军
1.典型缺陷展示
1.1裂纹 金属原子的结合遭到破坏而形成的新界面所产生的缝 隙,是一种危害性很大的面状缺陷。制作过程裂纹、使 用过程裂纹。 在用工业管道检验时还要结合管道材质、制造时的技 术条件、使用工况(温度、压力、介质等等)等分析可能出 现的裂纹(开裂),而且这种在一定工况下可能产生的裂纹 (开裂)也应是我们的检验重点所在。
64
2.工业管道定期检验过程中典型缺陷
2.6机械损伤 《承压设备损伤模式识别》GB 50379-2014关于机械损 伤的定义如下:“机械损伤是指材料在机械载荷或热载荷作 用下,发生的承载能力下降”。 2.6.1实例图片如下:
65
2.工业管道定期检验过程中典型缺陷
2.6.2原因分析: 经了解得知,该条管道上支管上是安全阀,因超压导致 安全阀经常起跳,导致在应力较为集中的角焊缝处出现 了裂纹。 2.6.3有效检验方法: 对角焊缝进行磁粉检测(或渗透检测)。 2.6.4缺陷处理思路: 打磨消除裂纹后再用磁粉检测方法进行检测,对于这种 材质焊后应及时进行局部消除应力退火处理。
55
压力管道弯头超标局部减薄安全状况等级评定
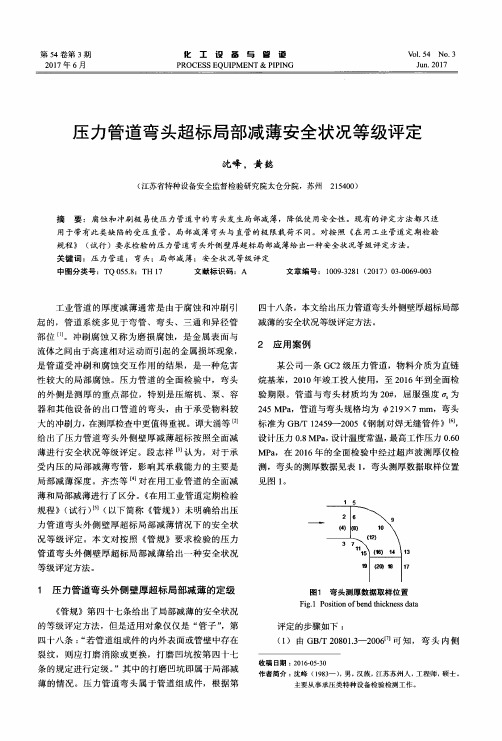
Hale Waihona Puke 化工设备与管道PROCESS EQUIPMENT&PIPING
Vr01.54
No.3
Jun.2017
压力管道弯头超标局部减薄安全状况等级评定
沈峰,黄懿
(江苏省特种设备安全监督检验研究院太仓分院,苏州
2 l 5400)
摘
要:腐蚀和冲刷极易使压力管道中的弯头发生局部减薄,降低使用安全性。现有的评定方法都只适
I砌,正常冲刷腐
蚀深度为7.0~6.2 mm。调取使用单位在线检验对该 弯头外弧处测厚数据,在该压力管道刚投入使用时该 弯头外弧处厚度为6.8 mm。弯头的减薄深度是相对 附近正常冲刷腐蚀壁厚来测量的,缺陷附近弯头外弧 处(位置9)局部减薄深度最大,其局部减薄深度为
6.8—0.8—4.8=1.2
mm,即6年时间局部减薄深度扩展1.2
用于带有此类缺陷的受压直管。局部减薄弯头与直管的极限载荷不同。对按照《在用工业管道定期检验 规程》(试行)要求检验的压力管道弯头外侧壁厚超标局部减薄给出一种安全状况等级评定方法。 关键词:压力管道;弯头:局部减薄;安全状况等级评定
中图分类号:TQ
055.8;TH 17
文献标识码:A
文章编号:1009—328l(2017)03—0069-003
'3
17
压力管道弯头外侧壁厚超标局部减薄的定级
《管规》第四十七条给出了局部减薄的安全状况
图1
Fig.1
弯头测厚数据取样位置
Position of bend thickness data
的等级评定方法,但是适用对象仅仅是“管子”,第 四十八条:“若管道组成件的内外表面或管壁中存在 裂纹,则应打磨消除或更换,打磨凹坑按第四十七 条的规定进行定级。”其中的打磨凹坑即属于局部减 薄的情况。压力管道弯头属于管道组成件,根据第
特种设备(锅炉、压力容器、起重机械、电梯、叉车、压力管道)事故案例分析

宁波市大自然新型墙材有限公司
蒸压釜爆炸事故
直接原因
筒体由于气体反推力的作用,拉脱固定
支座,向后移动,致墙倒人亡。
无 证 上
操 作 不
主要原因 1、操作工在操作时对齿面是否完全啮合 的情况,未经有效确认即开始升压,导
岗 当 致啮合齿局部受力过大,被压溃滑脱,
太 酿 引起事故,属于典型的操作不当。
特种设备 事故案例
共同努力, 建设平安企业!
安全生产、人人有责
为了您和家人的幸福, 请照章使用特种设备!
1.部分单位的特种设备未进行注册。
• 《特种设备安全法》第三十三条规定:特 种设备使用单位应当在特种设备投入使用 前或者投入使用后三十日内,向负责特种 设备监督管理的部门办理使用登记,取得 使用登记证书。登记标志应当置于该特种 设备的显著位置。
此后不久此后不久工人工人吴某吴某发现发现圆形水箱圆形水箱中水温达中水温达8080左右左右正常工作温度为正常工作温度为5050左右左右担心过高的水温进入转轱后会把皮料烫坏担心过高的水温进入转轱后会把皮料烫坏于是于是将分汽缸上的通往将分汽缸上的通往圆形水箱圆形水箱的出汽阀关闭的出汽阀关闭而此时通往而此时通往方形水方形水箱箱的出汽阀已处于基本关闭状态的出汽阀已处于基本关闭状态锅炉内压力因无法有效释放锅炉内压力因无法有效释放而急剧上升而急剧上升约半小时后锅炉发生超压爆炸约半小时后锅炉发生超压爆炸
• 场(厂)内专用机动车辆是违章作业或操 作不当,全部是叉车事故;
• 客运索道和大型游乐设施是设备隐患和非 法使用。
2017年特种设备事故统计分析
• 与2016年相比,事故起数减少1起,下降 0.44%;死亡人数减少3人,下降1.03%; 受伤人数减少80人,下降22.60%。全国万 台设备死亡人数为0.46,与2016年相比下 降11.03%,较好地实现了国务院安委会下 达的万台设备死亡人数不超过0.51的控制 目标。从总体上看,全国特种设备安全形 势总体平稳。
压力管道检验计算案例

压力管道检验计算案例54、某公司管道规格为Φ89×6.5mm,材料20#,最大工作压力为1.8MPa,工作温度:常温,工作介质:放空气体。
管道等级为GC2,实际使用时间为11年,本次为首次全面检验,测厚时发现管道存在局部减薄,实测最小壁厚为5.4mm,减薄区域环向长度实测最大值为50mm。
该管道本次检验时未发现其他缺陷,材料未出现性能劣化;该管道结构符合设计规范且不承受疲劳载荷。
问该管道如何定级?第四十七条管子的局部减薄,安全状况等级的确定方法如下:(一)若局部减薄在制造或验收规范所允许的范围内,则不影响定级。
(二)局部减薄超过制造或验收规范所允许的范围时,如果同时满足以下条件,则按照表3或表4定级;否则安全状况等级定为4级。
1.管道结构符合设计规范或管道的应力分析结果满足有关规范;2.在实际工况下,材料韧性良好,并且未出现材料性能劣化及劣化趋向;3.局部减薄及其附近无其它表面缺陷或埋藏缺陷;4.局部减薄处剩余壁厚大于2mm;5.管道不承受疲劳载荷。
表3 GC2或GC3管道所允许的局部减薄深度的最大值(mm)注:D为缺陷附近管道外径实测最大值,mm,以下同;t为缺陷附近壁厚的实测最小值减去至下一检验周期的腐蚀量的2倍,mm,以下同;B为缺陷环向长度实测最大值,mm;P为管道最大工作压力,MPa,以下同;P L0管道极限内压,P L0=(2/√3)σs In[(D/2)/(D/2-t)],以下同;σs为管道材料的屈服强度,MPa,以下同;C为至下一检验周期局部减薄深度扩展量的估计值,mm,以下同。
表4 GC1级管道所允许的局部减薄深度的最大值(mm)答:根据《在用工业管道定期检验规程》第四十七条,该管道存在局部减薄, 已知:P=1.8MPa ,B=50mm ,D=89mm ,MPa 245s =σ(1)18.0)8950/(3.14D)/(=⨯=πB <0.25,(B 为缺陷环向长度实测最大值,50mm ) (2).2932)2/(2/ln 32P L0 =-=t D D s σ(3)计算C 、t 值减薄量为Δ=6.5-5.4=1.1mm (原始厚度-实测最小壁厚)年腐蚀速率为:1.1mm/11年=0.1mm/年如按运行3年计算,则:C=0.1mm /年×3年=0.3mmt=5.4-2C=5.4-2*0.3=4.8mm(4)计算允许的局部减薄深度的最大值GC2管道定2级所允许的局部减薄深度的最大值为:0.33t-C=0.33*4.8-0.3=1.28mm因减薄量为Δ=1.1mm <1.28mm (小于该管道定2级运行3年所允许的局部减薄深度最大值1.28mm )。
压力管道事故案例分析
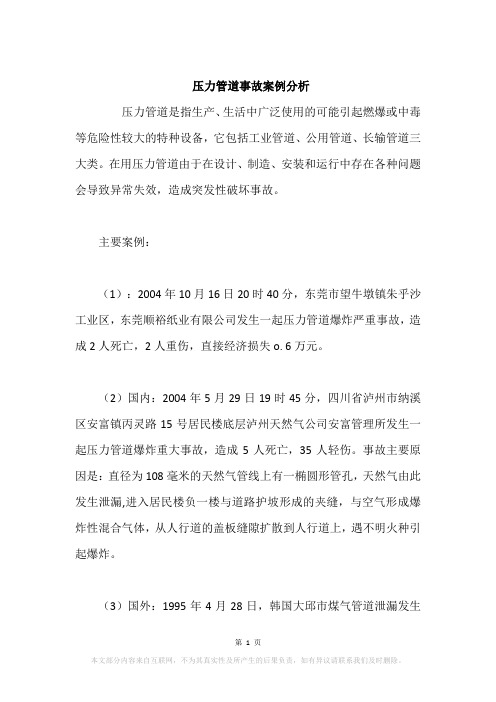
压力管道事故案例分析
压力管道是指生产、生活中广泛使用的可能引起燃爆或中毒等危险性较大的特种设备,它包括工业管道、公用管道、长输管道三大类。
在用压力管道由于在设计、制造、安装和运行中存在各种问题会导致异常失效,造成突发性破坏事故。
主要案例:
(1):2004年10月16日20时40分,东莞市望牛墩镇朱乎沙工业区,东莞顺裕纸业有限公司发生一起压力管道爆炸严重事故,造成2人死亡,2人重伤,直接经济损失o. 6万元。
(2)国内:2004年5月29日19时45分,四川省泸州市纳溪区安富镇丙灵路15号居民楼底层泸州天然气公司安富管理所发生一起压力管道爆炸重大事故,造成5人死亡,35人轻伤。
事故主要原因是:直径为108毫米的天然气管线上有一椭圆形管孔,天然气由此发生泄漏,进入居民楼负一楼与道路护坡形成的夹缝,与空气形成爆炸性混合气体,从人行道的盖板缝隙扩散到人行道上,遇不明火种引起爆炸。
(3)国外:1995年4月28日,韩国大邱市煤气管道泄漏发生
第 1 页
本文部分内容来自互联网,不为其真实性及所产生的后果负责,如有异议请联系我们及时删除。
事故案例分析-压力管道

2015年11月16日
2015年度第十六期
事故案例分析
压力管道事故案例分析
一、什么是压力管道
利用一定的压力,用于输送气体或者液体的管状设备,其范围规定为最高工作 压力大于或者等于0.1MPa(表压)的气体、液化气体、蒸汽介质或者可燃、易爆、有 毒、有腐蚀性、最高工作温度高于或者等于标准沸点的液体介质,且公称直径大于 25mm的管道。《特种设备安全监察条例》(国务院令第549号)
事故案例分析-压力管道事故案例分析
(4)抓住使用系统的安全监察和管理
使用单位应严格按照《规定》要求,落实压力管道安全专(兼)职人员和机构,落实安 全管理制度包括巡线检查制度和各项操作规程,落实定期检验和检修计划,操作人员经培训 考核持证上岗,压力管道逐步注册登记。对易产生腐蚀的管道,应正确选材、设计以及良好 的防护涂层,特殊情况下选用耐腐蚀非金属材料,埋地管线同时采用阴极保护。
事故案例分析-压力管道事故案例分析
2、制造原因 制造原因主要是管道组成件制造缺陷引发事故。其中阀门、管件(三通、弯头)、法兰、 垫片等是事故的源头,管子厚薄不均,管材存在裂纹、夹渣、气孔等严重缺陷,密封性能差, 引起泄漏爆炸。浙江省建德市某公司,因管道阀门爆裂,死亡4人;19 98年3月5日西安某公 司因球罐排污密封面泄漏,在抢修过程中爆炸,造成12人死亡(其中7名是消防人员)。1999 年3月8日,某市氮肥厂合成车间冷交换器进口管道在正常工作压力下泄漏,该厂维修人员在 高压力下带压检修继而造成管道脱落,管内高压氢氮气迅速喷出,发生空间爆炸,造成4人死 亡,1人重伤,合成、压缩、铜洗工段厂房、设备严重损坏,直接经济损失达300余万元,事 故主要原因是违章检修及管件、密封件质量差。
事故案例分析-压力管道事故案例分析
压力管道检验案例分析

压力管道检验案例分析摘要:由于我国的经济迅速发展,很多行业都采用了不同的管材,而压力管道的应用更是越来越广,其总体的质量和安全性能直接关系到整个行业的发展,同时也关系到工人的生命安全。
为此,本文根据相关案例,对压力管道检验中出现的问题就能写分析,并提出相应的解决措施。
关键词:压力管道;检验案例;分析一、压力管道特征与意义压力管道是化工、冶金等领域中常用的一种运输介质的特种设备。
为了保证管道的运输安全和提高输送的品质,作为压力管道的检查人员应该根据管道在输送中发生的各种变化进行细致的研究,找出存在的问题,从而有针对性地采取相应的方法来进行正确的处理。
本文通过对压力管道检验案例进行分析,同时进行了相应的改进,以期为相关检验工作提供借鉴。
在实际工作中,由于压力管道(如图1)与常规管道存在着很大的差异,因此,必须保障压力管道能够经受很大的内外压,从而能够很好地适应实际工作的要求。
在管道连接时,采用大量螺栓、阀门和其他构件将各种管道进行高效的连接,以适应各种危险介质的输送要求。
原因是压力管道输送的介质大多是易燃、爆炸等危险品,因此,对压力管道质量和性能要求也很高,要确保压力管道的各个环节都是合理、安全的,从而确保了管道在各种工作条件下的工作性能和安全性。
目前,压力管道的使用范围更广,不仅在化学领域,在其他行业中均有所涉及。
但是近几年来管道材料存在不合格、安装不当、检验程序不规范等问题,使得近几年来,压力管道的质量问题越来越突出,给企业造成了巨大的经济损失,因此,加强现阶段对压力管道的检验十分重要,通过加大管理力度,促使相关的政府部门积极进行标准规范的修订和完善,保障工作人员在检验过程中严格遵循检验标准规范和制度,以便工作人员在检验过程中严格遵循检验标准规范和制度,以此来确保压力管道安全稳定运行,避免引发安全事故[1]。
图1:压力管道二、压力管道定期检验的内容与方法(一)材料质量与管道壁厚检验工作对压力管道进行检验检测过程中,对管材的检查和标识进行了细致的检查。
压力管道检验计算案例
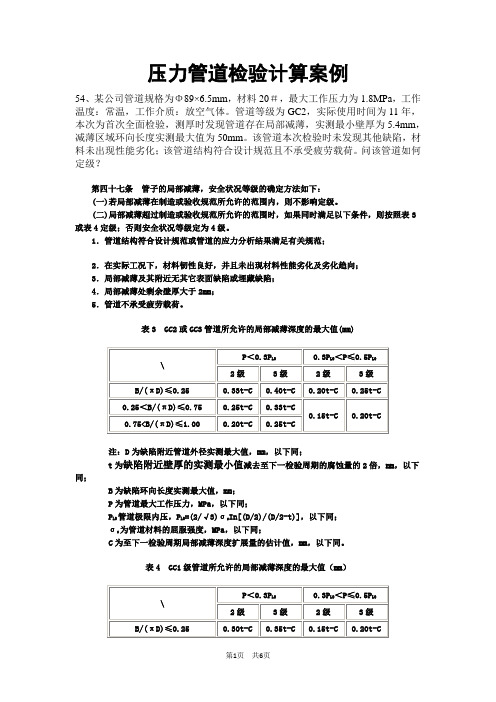
压力管道检验计算案例54、某公司管道规格为Φ89×6.5mm,材料20#,最大工作压力为1.8MPa,工作温度:常温,工作介质:放空气体。
管道等级为GC2,实际使用时间为11年,本次为首次全面检验,测厚时发现管道存在局部减薄,实测最小壁厚为5.4mm,减薄区域环向长度实测最大值为50mm。
该管道本次检验时未发现其他缺陷,材料未出现性能劣化;该管道结构符合设计规范且不承受疲劳载荷。
问该管道如何定级?第四十七条管子的局部减薄,安全状况等级的确定方法如下:(一)若局部减薄在制造或验收规范所允许的范围内,则不影响定级。
(二)局部减薄超过制造或验收规范所允许的范围时,如果同时满足以下条件,则按照表3或表4定级;否则安全状况等级定为4级。
1.管道结构符合设计规范或管道的应力分析结果满足有关规范;2.在实际工况下,材料韧性良好,并且未出现材料性能劣化及劣化趋向;3.局部减薄及其附近无其它表面缺陷或埋藏缺陷;4.局部减薄处剩余壁厚大于2mm;5.管道不承受疲劳载荷。
表3 GC2或GC3管道所允许的局部减薄深度的最大值(mm)注:D为缺陷附近管道外径实测最大值,mm,以下同;t为缺陷附近壁厚的实测最小值减去至下一检验周期的腐蚀量的2倍,mm,以下同;B为缺陷环向长度实测最大值,mm;P为管道最大工作压力,MPa,以下同;P L0管道极限内压,P L0=(2/√3)σs In[(D/2)/(D/2-t)],以下同;σs为管道材料的屈服强度,MPa,以下同;C为至下一检验周期局部减薄深度扩展量的估计值,mm,以下同。
表4 GC1级管道所允许的局部减薄深度的最大值(mm)答:根据《在用工业管道定期检验规程》第四十七条,该管道存在局部减薄, 已知:P=1.8MPa ,B=50mm ,D=89mm ,MPa 245s =σ(1)18.0)8950/(3.14D)/(=⨯=πB <0.25,(B 为缺陷环向长度实测最大值,50mm ) (2).2932)2/(2/ln 32P L0 =-=t D D s σ(3)计算C 、t 值减薄量为Δ=6.5-5.4=1.1mm (原始厚度-实测最小壁厚)年腐蚀速率为:1.1mm/11年=0.1mm/年如按运行3年计算,则:C=0.1mm /年×3年=0.3mmt=5.4-2C=5.4-2*0.3=4.8mm(4)计算允许的局部减薄深度的最大值GC2管道定2级所允许的局部减薄深度的最大值为:0.33t-C=0.33*4.8-0.3=1.28mm因减薄量为Δ=1.1mm <1.28mm (小于该管道定2级运行3年所允许的局部减薄深度最大值1.28mm )。