挤出过程和挤出理论
第四章挤出成型

1
2
主要内容
4.1 4.2 4.3 4.4 4.5 4.6 概述 单螺杆挤出理论 螺杆挤出机的结构及选用方法 挤出成型过程 几种制品的挤出成型 挤出成型的发展
3
4.1
概述
1. 挤出成型(Extrusion Molding)是指用机械运动施加 力迫使高分子材料流体通过成型装置(机头、口 模) ,定型为具有恒定截面的连续型材的一种成型 方法。
31
螺杆的作用
输送物料 螺杆转动时,物料在旋转的同时受到轴向压 力,向机头方向流动以挤出成型。 传热、塑化物料 与料筒配合,使物料接触传热面并不断更新, 在料筒外加热与螺杆摩擦作用下软化、熔融为粘 流态。 混合与均化物料 与料筒和机头相配合产生强大的剪切作用,使 物料混合均匀、塑化完全。
32
螺杆沿长度方向一般分为三段,各段的作用和 结构是不同的:
52
主要内容
4.2.1 4.2.2 4.2.3 4.2.4 挤出理论的准备知识 加料段的固体输送理论 压缩段的熔融理论 均化段的熔体输送理论
53
4.2.1 挤出理论的准备知识
4.2.1.1 物料通过挤压系统的运动及物态变化
1.挤压系统的主要作用:连续、稳定输送物料;将固 体物料塑化成熔融物料;使物料的温度和组成一致。 加料段—进行高分子物料的固体输送 压缩段—压缩物料,并使物料熔融 均化段—对熔融物料进行搅拌和混合,定量定压挤出。 2.物料经历三种力学状态 n 玻璃态、高弹态、粘流态。
43
几种常见机头
44
45
46
47
48
5、传动系统 包括带动螺杆转动的电机和机械传动部件。 6、附属设备 塑料的输送、预热、干燥等预处理装置。 挤出后制品的定型、冷却装置。 牵引装置。 卷绕或切割装置。 控制设备等。
挤出成型工艺—挤出成型原理(塑料成型加工课件)
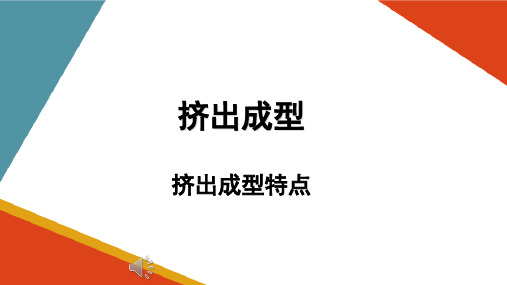
二、挤出成型过程
既有混合过 程,也有成 型过程
树脂原料 加热黏流 塑料熔体
助剂
混合过程
加压 挤出连续体
一定规格的 制品
切割 成型连续体
冷却定型
成型过程
以 管 材 挤 出 原料 成型为例
挤出连续体
熔体
定型连续体
制品
三、挤出成型特点
1. 可以连续化生产,生产效率高。 2. 设备自动化程度高,劳动强度低。 3. 生产操作简单,工艺控制容易。 4. 原料适应性强,适用大多数热塑性树脂和少数热固性 树脂。 5. 可生产的产品广泛,同一台挤出机,只要更换不同的 辅机,就可以生产不同的制品。
挤出成型
挤出成型特点
一、挤出成概述
挤出成型又叫挤出模塑,是利用加热使塑料熔融塑化成 为流动状态,然后在机械力(螺杆或柱塞的挤压)的作用下, 使熔融塑料通过一定形状的口模制成具有恒定截面连续的制 品,适用于绝大部分热塑性树脂和部分热固性树脂。
除了用于挤出造粒、染色、树脂掺和等共混改性,还可用于塑 料薄膜、网材、带包覆层的产品、截面一定、长度连续的管材、板 材、片材、棒材、打包带、单丝和异型材等塑料制品的生产。
料表面接近或达到黏流温度,表面发黏。
要求:输送能力要稍高于熔融段和均化段。
2. 压缩段 (熔融段)
位置:螺杆中部一段。 作用:输送物料,使物料受到热和剪切作用熔 融塑化,并进一步压实和排出气体。 特点:物料逐渐由玻璃态转变为粘流态,在熔 融段末端物料为粘流态。 要求:螺杆结构逐渐紧密,使物料进一步压实。
(3)横流(环流) 由垂直于螺棱方向的分速
度引起的使物料在螺槽内产生翻 转运动。对生产能力没有影响, 但能促进物料的混合和热交换。
(4)漏流 由机筒与螺棱间隙处形成的
第三章(1)固体输送理论

第三章挤出理论研究对象——塑料在单螺杆挤出机中的挤出过程研究目的——进行定性和定量分析,→揭示、掌握和促进此过程→达到优质、高效、低能耗研究始于19世纪20年代,取得突破性成果是在50、60年代,为70年代各种新型螺杆以及挤出机的新结构的发展打下了理论基础,使挤出产量和质量得到很大提高。
挤出过程——复杂的过程涉及——流变学、传热学、摩擦学、高分子结构学等理论模型——以一些基本假设和简化为前提有一定的局限性和片面性现在仍在不断修正、发展和完善中。
第一节固体输送理论D a r n e l l -M o l 的固体输送理论(1956)以固体摩擦静力平衡为基础——M o l 固体输送理论一、固体输送方程的建立1. 基本假设⑴塑料充满螺槽,密实形成固体塞,特性为连续弹性体⑵P =f (z )⑶与机筒、螺槽表面紧密接触f =c o n s t. 但f b 、f s 可不同最有代表性、应用较为广泛⑷ρs =c o n s t.,重力忽略不计⑸螺杆与机筒之间的间隙忽略不计⑹螺槽截面为矩形,且深度不变思考题4. 提高固体输送率的有效结构措施是什么?为什么?3. 固体输送段消耗的总功率包含哪几项? 1. M o l 固体输送理论是如何建立的?2. 固体输送段物料向前输送的推动力是什么?第十三章:干燥通过本章的学习,应熟练掌握表示湿空气性质的参数,正确应用空气的H–I 图确定空气的状态点及其性质参数;熟练应用物料衡算及热量衡算解决干燥过程中的计算问题;了解干燥过程的平衡关系和速率特征及干燥时间的计算;了解干燥器的类型及强化干燥操作的基本方法。
二、本章思考题1、工业上常用的去湿方法有哪几种?态参数?11、当湿空气的总压变化时,湿空气H–I图上的各线将如何变化? 在t、H 相同的条件下,提高压力对干燥操作是否有利? 为什么?12、作为干燥介质的湿空气为什么要先经预热后再送入干燥器?13、采用一定湿度的热空气干燥湿物料,被除去的水分是结合水还是非结合水?为什么?14、干燥过程分哪几种阶段?它们有什么特征?15、什么叫临界含水量和平衡含水量?16、干燥时间包括几个部分?怎样计算?17、干燥哪一类物料用部分废气循环?废气的作用是什么?18、影响干燥操作的主要因素是什么?调节、控制时应注意哪些问题?三、例题例题13-1:已知湿空气的总压为101.3kN/m2 ,相对湿度为50%,干球温度为20o C。
挤出成型—挤出理论(高分子成型课件)

四、挤出机的挤出理论
3 熔体输送理论 流动流动状态:
①正流Qd:沿正轴向口模/机头方向流动。由旋转螺杆挤压造成。 ②逆流Qp:沿正方向相反,由机头压力引起。 ③横流Qt:环流。不影响总流量。但对熔体的混合、塑化、热交换起重要 作用。 ④漏流Qc 物料在螺杆与机筒之间间隙向加料口方向回流,可降低挤出量 。一般情况下漏流Qc很小,但磨损严重时,漏流Qc增加急剧增加。
p在挤出过程中,由于螺杆 和料筒机构、机头、过滤 网以及过滤板的阻力,使 塑料内部存在压力。
p压力可以提高挤出熔体的混合均匀性和稳定性,提高产品致密 度, 是塑料变为均匀熔体并得到致密塑件的重要条件之一。 p螺杆转速的变化,加热、冷却系统的不稳定都对产生压力波动 产生影响,对制品质量产生不利影响。 p为保证制品质量,应尽可能减少压力的波动。
六、挤出工艺的影响因素
3 挤出速率
p挤出速率因素影响较多(机头阻力、螺杆与料筒结构、螺杆转速、 加热冷却系统和塑料特性等)但主要与螺杆转速有关,提高转速,可 提高挤出产量,但塑化质量不高,因而挤出速率要大小合适。 p挤出速率在生产过程中也存在波动现象,挤出速率的波动影响制品 几何形状和尺寸。生产中应保证挤出速率的稳定。
LDPE 15~20 3~4 90~100 100~140 140~160 140~160
PP
22~25 2.5~4 140~160 165~185 180~200 160~185
PC
16~25 2.5~3 200~240 240~250 230~255 200~22100
六、挤出工艺的影响因素
2 压力
tan tanb
四、挤出机的挤出理论
挤出理论

第二节 单螺杆挤出成型基本原理
在此状态,可采用注射成型、挤出成型、压延成 型、吹塑成型、压制成型等加工方法,绝大多数 的塑料制品都是在黏流态流动成型的
结晶型塑料的高弹态并不明显,没有明确的黏流 温度,而是当温度高于熔融温度Tm时,则开始融 化,完全熔化时则进入黏流态 : Tm (或Tf )~T d 高分子材料的成型加工温度范 围越宽,成型加工越容易
36
第二节 单螺杆挤出成型基本原理
37
第二节 单螺杆挤出成型基本原理
5、熔体输送理论 研究的意义
亦称流体动力学理论,是研究在单螺杆计量 段如何保证物料的彻底塑化,并使之能定压、定 量和定温地从机头挤出,以获得稳定的产量和高 质量的挤出制品
53
第二节 单螺杆挤出成型基本原理
假设:
进入计量段的物料己全部熔融塑化 熔体为等温牛顿流体,其黏度和密度不变 熔体流动是稳定的层流 熔体是不可压缩的 视螺槽为矩形,螺槽的曲率忽略 沿整个螺槽的速度分布不变。
带动物料转动而不移动。 流动的基本条件:Fbz>Fs
Q=V· va Q —单位时间内固体物料的流动体积; v a— 物料前进 速度;V—单位螺槽容积。
V
D 4
2
( D 2h) 2
Va 1 N
D h1 h2 1 cot 1 cot
DN va l N ctg ctg
控制螺杆与机筒的温度
金属与聚合物的摩檫系数是温度的函数,而且有一
个极大值
4、熔融理论——延迟熔融理论模型
概述 聚合物材料在固体输送段内随着固体塞温度的升 高,其与机筒内壁接触的表面首先达到熔点Tm或黏流温 度(Tf),产出聚合物熔体,随着固体床继续向前推进,熔 体开始聚集在固体床表面形成一层薄薄的熔膜,由于膜 较薄,螺棱的推进面还不足以将其刮下形成熔体池
挤出理论知识
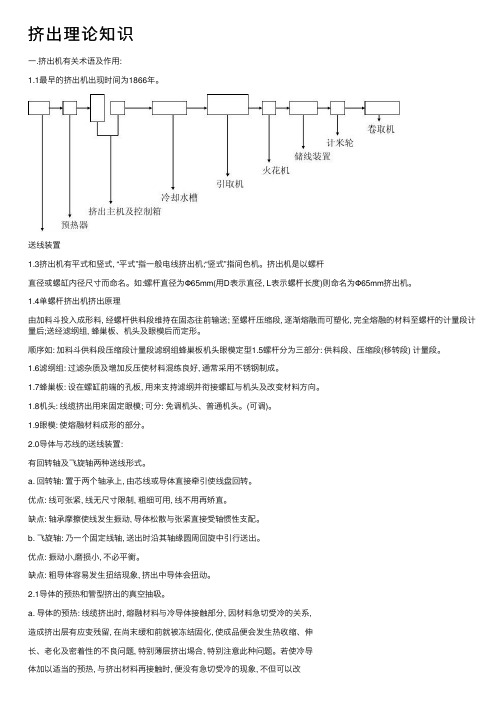
挤出理论知识⼀.挤出机有关术语及作⽤:1.1最早的挤出机出现时间为1866年。
送线装置1.3挤出机有平式和竖式, “平式”指⼀般电线挤出机;“竖式”指间⾊机。
挤出机是以螺杆直径或螺缸内径尺⼨⽽命名。
如:螺杆直径为Φ65mm(⽤D表⽰直径, L表⽰螺杆长度)则命名为Φ65mm挤出机。
1.4单螺杆挤出机挤出原理由加料⽃投⼊成形料, 经螺杆供料段维持在固态往前输送; ⾄螺杆压缩段, 逐渐熔融⽽可塑化, 完全熔融的材料⾄螺杆的计量段计量后;送经滤纲组, 蜂巢板、机头及眼模后⽽定形。
顺序如: 加料⽃供料段压缩段计量段滤纲组蜂巢板机头眼模定型1.5螺杆分为三部分: 供料段、压缩段(移转段) 计量段。
1.6滤纲组: 过滤杂质及增加反压使材料混练良好, 通常采⽤不锈钢制成。
1.7蜂巢板: 设在螺缸前端的孔板, ⽤来⽀持滤纲并衔接螺缸与机头及改变材料⽅向。
1.8机头: 线缆挤出⽤来固定眼模; 可分: 免调机头、普通机头。
(可调)。
1.9眼模: 使熔融材料成形的部分。
2.0导体与芯线的送线装置:有回转轴及飞旋轴两种送线形式。
a. 回转轴: 置于两个轴承上, 由芯线或导体直接牵引使线盘回转。
优点: 线可张紧, 线⽆尺⼨限制, 粗细可⽤, 线不⽤再矫直。
缺点: 轴承摩擦使线发⽣振动, 导体松散与张紧直接受轴惯性⽀配。
b. 飞旋轴: 乃⼀个固定线轴, 送出时沿其轴缘圆周回旋中引⾏送出。
优点: 振动⼩,磨损⼩, 不必平衡。
缺点: 粗导体容易发⽣扭结现象, 挤出中导体会扭动。
2.1导体的预热和管型挤出的真空抽吸。
a. 导体的预热: 线缆挤出时, 熔融材料与冷导体接触部分, 因材料急切受冷的关系,造成挤出层有应变残留, 在尚末缓和前就被冻结固化, 使成品便会发⽣热收缩、伸长、⽼化及密着性的不良问题, 特别薄层挤出埸合, 特别注意此种问题。
若使冷导体加以适当的预热, 与挤出材料再接触时, 便没有急切受冷的现象, 不但可以改善挤出质量, 对导体的⼲燥净化有较好的效果。
材料成型设备课后习题答案解析

材料成型设备一、填空题40分,共20小题,集中在二三四五章1、曲柄压力机的组成:工作机构、传动系统、操作机构、能源部分、支撑部分、辅助系统。
P102、曲柄压力机的辅助分类方式:P11按滑块数量分类:单动压力机、双动压力机-按压力机连杆数量分类:单点压力机、双点压力机和四点压力机(“点”数是指压力机工作机构中连杆的数目)3、曲柄压力机型号表示P124、曲柄滑块机构按曲柄形式,曲柄滑块机构主要有几种:曲轴式、偏心齿轮式P175、装模高度调节方式:调节连杆长度、调节滑块高度、调节工作台6、过载保护装置:压塌块式过载保护装置和液压式过载保护装置-两种P197、离合器可分为刚性离合器和摩擦式离合器-,制动器多为摩擦式、有盘式和带式-8、刚性离合器按结合零件可分为转键式,滑销式,滚柱式和牙嵌式9、飞轮的储存和释放能量的方式是转速的加快和减缓-10、曲柄压力机的主要技术参数:通常曲柄压力机设备越小,滑块行程次数越大。
装模高度是指滑块在下死点时滑块下表面到工作台点半上表面的距离。
最大装模高度是指当装模高度调节装置将滑块调节至最上位置时的装模高度值。
与装模高度并行的标准还有封闭高度。
封闭高度是指滑块处于下死点时,滑块下表面与压力机工作台上表面的距离,封闭高度与装模高度不同的是少一块工作台垫板厚度P4211、一般拉深压力机有两个滑块(称双动拉深压力机),外滑块用于压边,内滑块用于拉伸成型P5312、液压机的工作介质有两种,采用乳化液的一般叫水压机,采用油的一般叫油压机,油压机中使用做多的是机械油(标准称全损耗系统用油)P8513、液压机本体结构一般由机架部件,液压缸部件,运动部件及其导向装置所组成。
P8714、液压机立柱的预紧方式主要有加热预紧、液压预紧和超压预紧P9115、液压缸结构可以分为柱塞式,活塞式和差动柱塞式三种形式。
P9416、液压元件是组成液压系统的基本要素,由动力元件,执行元件,控制元件及辅助元件四部分组成。
第二节 挤出理论

1)螺杆特性线: 挤出机均化段的流率方程如下:
Q
n
f
P
由上式可知:α、β、γ、L3是与螺杆几何参数相关的 常数,η.ηf也是常数。因此上述方程实际上成了Q与 △P的线性方程。
其直线的斜率为:
f
如下图,我们称AB为螺杆的特性线。它是一组相互 平行的直线族,随螺杆n转速的改变而改变。
d. 漏流: 由机筒与螺棱间隙δ处形成的倒流。方向沿螺杆轴 线方向,并由机头向后。流量用QL表示。对提高挤 出机流量起反作用。
实际上螺槽中熔体 的总的流动是这几 种流动的总和。 挤出机的生产能力 即:
Q=Qd-Qp-QL
3.均化段功率消耗于三部分: 螺槽中剪切物料所消耗的功率;
保持螺槽中压力所消耗的功率;
是由物料受机筒的摩擦拖曳引起的,最大处速度为
V1, 起到挤出物料的作用,流量用Qd表示。
b、倒流(压力流)
由机头、口型等阻力 元件产生的压力引起
Vb Vb
机筒表面
的回流。方向与正流
y
方向相反,流量为QP
正流
xz 螺杆表面
倒流
c.横流(环流):
由垂直于螺棱方向的分速度V2引起(如图), 使物料 在螺槽内产生翻转运动。方向与V2方向相同,对生 产能力没有影响,但能促进物料的混合、搅拌和热 交换,流量Qc=0
这就是说,人们还没有完全认识挤出过程。关于挤 出过程的理论正在发展中。
目前常用的关于挤出过程的理论,是在常规全螺纹 螺杆中建立起来的。
根据实验,物料自料斗加入到由机头挤出,要通过 几个职能区:固体输送区、熔融区和熔体输送区。
固体输送区,通常限定在自加料斗开始算起的几个 螺距中,在该区,物料向前输送并被压实,但仍以 固体状存在。
第三章(挤出机)
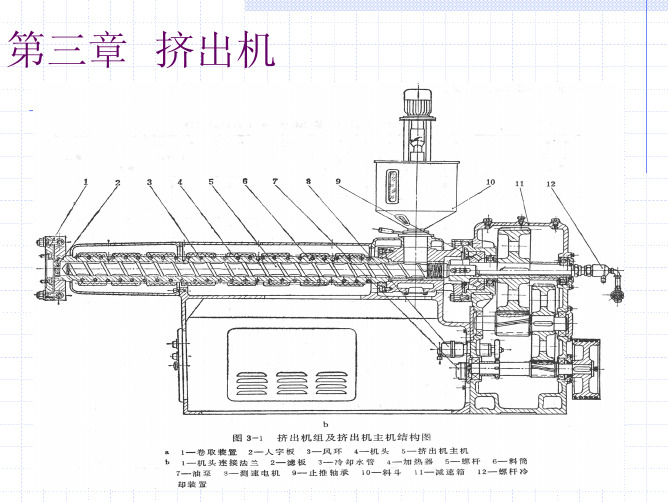
第一节 概述
一、挤出成型的过程 塑料原料
加热相变 挤出主机
塑料熔体
加压
挤出模具(机头) 切割 切割装置
初始形状的连续
定型 冷却(定型)装置
最终形状的连续体
一定规格的制品
二、挤出成型的特点
1、由于挤出过程具有连续性,故可生产任意长度的制品, 并且效率高、易实现生产过程的自动化。 2、应用范围广,能加工绝大多数的热塑性塑料和一些热固 性塑料。 制品成型:管材、板材、棒材、异型材、薄膜、丝、带 等; 原料准备工序:混合、塑化、脱水、着色、造粒、压延 喂料等; 半成品的加工:电缆料、色母料等。 3、由于挤出机结构简单,操作方便,成本低,故投资少, 收效快。
四、新型过滤器:长效,快换,不停机,多功能
五、静态混合器
在螺筒内加装分流、汇合混炼元件,让物料在流动的过 程中实现混 炼、均化的作用, 而不需要螺杆的 转动和螺棱的搅动。 ①Kenics静态混合器 ②Ross静态混合器 ③Sulzer静态混合器
第七节 加料装置
一、料斗的形式 圆形锥底、方形锥底、自热干燥料斗 二、上料方式 人工、鼓风、弹簧、真空(可以除去原料 中的空气和湿气) 三、强制加料结构 1、防止架桥 2、定量施压加料,有搅拌、螺旋、活塞等方式 四、加料装置的基本要求 1、有自动上料装置和计量器; 2、带有预热干燥或抽真空装置; 3、进料均匀; 4、如需混用两种或以上物料,需搅拌装置。
(一)固体输送理论
如计算固体输送流率,必把料筒转动线速度V= пDn, 该段的物料运动假设为理想化的物理模型。
流率Q = Vp1 F
= πD b n(tgφtgθ ) /( tgφ + tgθ ) F = ∫ (2πR − Pe / sin α )dR
挤出问题探讨
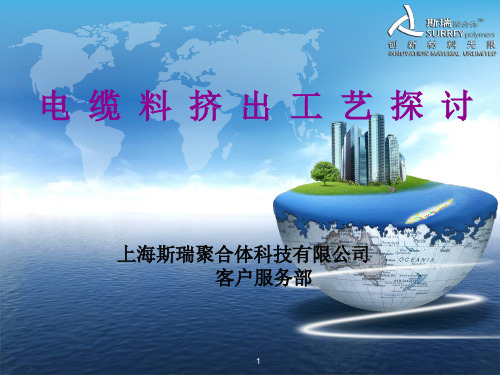
16
应当指出的是
塑料操作温度的比较,只有对同一设备才有意义。设备不 同,机筒壁厚薄不一样,测温点的深浅不一样,而且测温 仅是测机筒和机头的温度,与物料的实际温度也不一样。 因此,应根据观察挤出过程中塑料的塑化质量,并调节温 控,一般材料说明书给出温度的仅供参考。
17
2挤出机各段温控的作用
加料段采用低温:因为加料段要产生足够的推力、 机械搅拌并混合。如温度过高,使塑料过早熔融, 容易引起“打滑”,造成挤出压力波动,还容易因 过早熔融导致混合不充分,塑化不均匀。另外,还 容易使加料口料粒结块堵塞,使加料流终止,所以 这一段温度一般采用低温。
四、其它 结束语
2
前
言
说到电缆料的挤出,线缆行业的人们都不陌生,
大家天天都在接触,积累了丰富的经验和挤出理论。 因此,我们今天在这里抱着学习的态度,就挤出 工艺方面的一点浅显认识与大家共同探讨。
3
一、关于挤出原理
4
1 塑料挤出过程的三个阶段
塑料挤出最主要的依据是塑料所具有的可塑态。 塑料在挤出机中完成可塑过程成型是一个复杂的物 理过 程,包括了混合、破碎、熔融、塑化、排气、 压实并最 后成型定型,这一过程是连续实现的。 在实际应用中,这一连 续过程可以人为的分为三个不同 阶段,即: 塑化阶段、成形阶段、定形阶段。 塑化阶段、成形阶段、定形阶段。
5
塑化阶段 是在挤出机机筒里完成的。经过螺杆的旋转作用,塑 料由颗粒状的固体变为可塑性的粘流体。 塑料在塑化阶段取得由机筒外部的电加热和螺杆旋转 时产生的摩擦热两部分的热量。 起初的热量由机筒外部的电加热作用取得。正常开车 后,热量的取得则是由螺杆对物料的旋转、压缩、剪切、 搅拌等作用与机筒内壁的摩擦和物料分子间的内摩擦产生 的。 这两部分热量的共同作用使塑料粒子在机筒内塑化熔 融成粘流体。
公共基础知识挤出工艺基础知识概述
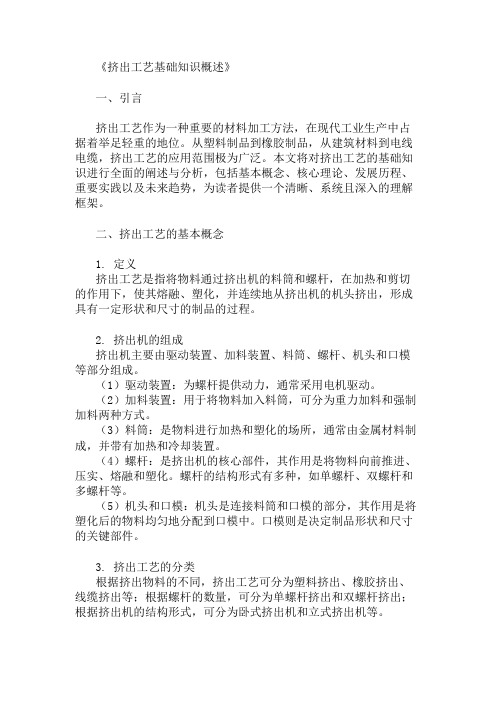
《挤出工艺基础知识概述》一、引言挤出工艺作为一种重要的材料加工方法,在现代工业生产中占据着举足轻重的地位。
从塑料制品到橡胶制品,从建筑材料到电线电缆,挤出工艺的应用范围极为广泛。
本文将对挤出工艺的基础知识进行全面的阐述与分析,包括基本概念、核心理论、发展历程、重要实践以及未来趋势,为读者提供一个清晰、系统且深入的理解框架。
二、挤出工艺的基本概念1. 定义挤出工艺是指将物料通过挤出机的料筒和螺杆,在加热和剪切的作用下,使其熔融、塑化,并连续地从挤出机的机头挤出,形成具有一定形状和尺寸的制品的过程。
2. 挤出机的组成挤出机主要由驱动装置、加料装置、料筒、螺杆、机头和口模等部分组成。
(1)驱动装置:为螺杆提供动力,通常采用电机驱动。
(2)加料装置:用于将物料加入料筒,可分为重力加料和强制加料两种方式。
(3)料筒:是物料进行加热和塑化的场所,通常由金属材料制成,并带有加热和冷却装置。
(4)螺杆:是挤出机的核心部件,其作用是将物料向前推进、压实、熔融和塑化。
螺杆的结构形式有多种,如单螺杆、双螺杆和多螺杆等。
(5)机头和口模:机头是连接料筒和口模的部分,其作用是将塑化后的物料均匀地分配到口模中。
口模则是决定制品形状和尺寸的关键部件。
3. 挤出工艺的分类根据挤出物料的不同,挤出工艺可分为塑料挤出、橡胶挤出、线缆挤出等;根据螺杆的数量,可分为单螺杆挤出和双螺杆挤出;根据挤出机的结构形式,可分为卧式挤出机和立式挤出机等。
三、挤出工艺的核心理论1. 物料的流动与变形在挤出过程中,物料在螺杆的推动下,经历了固体输送、熔融和均化三个阶段。
在固体输送阶段,物料主要依靠螺杆的旋转和摩擦力向前推进;在熔融阶段,物料在加热和剪切的作用下逐渐熔融;在均化阶段,物料被进一步混合和塑化,以保证挤出制品的质量均匀。
2. 螺杆的设计原理螺杆的设计是挤出工艺的关键,其主要参数包括螺杆直径、长径比、螺距、螺槽深度等。
螺杆的设计应根据物料的性质、挤出工艺的要求以及挤出机的性能等因素进行综合考虑,以实现物料的高效输送、熔融和塑化。
塑料在挤出机中的运动过程简介

塑料在挤出机中的运动过程简介( 发表于2006-6-18 13:37:15 )[该贴已经被绿色甲克虫于2006-6-18 13:37:15奖励+1威望][该贴已经获得+1朵鲜花]挤塑机的工作原理是:利用特定形状的螺杆,在加热的机筒中旋转,将由料斗中送来的塑料向前挤压,使塑料均匀地塑化(即熔融),通过机头和不同形状的模具,使塑料挤压成连续性的所需要各种形状的塑料层,挤包在线芯和电缆上。
一,塑料挤出过程电线电缆的塑料绝缘和护套是采用连续挤压方式进行的,挤出设备一般是单螺杆挤塑机。
塑料在挤出前,要事先检查塑料是否潮湿或有无其它杂物,然后把塑料预热后加入料斗内。
在挤出过程中,装人料斗中的塑料借助重力或加料螺旋进人机筒中,在旋转螺杆的推力作用下不断向前推进,从预热段开始逐渐地向均化段运动;同时,塑料受到螺杆的搅拌和挤压作用,并且在机筒的外热及塑料与设备之间的剪切摩擦热的作用下转变为粘流态,在螺槽中形成连续均匀的料流。
在工艺规定的温度作用下,塑料从固体状态转变为熔融状态的可塑物体,再经由螺杆的推动或搅拌,将完全塑化好的塑料推入机头,到达机头的料流,经模芯和模套间的环形间隙,从模套口挤出,挤包干线芯或缆芯周围,形成连续密实的绝缘层或护套层,然后经冷却和固化,制成电线电缆产品。
二,挤出过程的三个阶段塑料挤出主要依据的是塑料所具有的可塑态。
塑料在挤出机中完成可塑成型过程是一个复杂的物理过程:包括了混合、破碎、熔融、塑化、排气、压实并最后成型定型,这一过程是连续实现的。
然而习惯上,人们往往按塑料的不同反应将挤塑过程,人为的分成各个不同阶段;①塑化阶段(塑料的混合、熔融和均化);②成型阶段(塑料的挤压成型);③定型阶段(塑料层的冷却和固化)。
1,塑化阶段。
也称为压缩阶段。
它是在挤塑机机筒内完成的,经过螺杆的旋转作用,使塑料由颗粒状固体变为可塑性的粘流体。
塑料在塑化阶段获得热量的来源有两个方面:一是机筒外部的电加热;二是螺杆旋转时产生的摩擦热。
挤塑机的工作原理

利用特定形状的螺杆,在加热的机筒中旋转,将由料斗中送来的塑料向前挤压,使塑料均匀地塑化(即熔融),通过机头和不同形状的模具,使塑料挤压成连续性的所需要各种形状的塑料层,挤包在线芯和电缆上。
一,塑料挤出过程电线电缆的塑料绝缘和护套是采用连续挤压方式进行的,挤出设备普通是单螺杆挤塑机。
塑料在挤出前,要事先检查塑料是否潮湿或者有无其它杂物,然后把塑料预热后加入料斗内。
在挤出过程中,装人料斗中的塑料借助重力或者加料螺旋进人机筒中,在旋转螺杆的推力作用下不断向前推进,从预热段开始逐渐地向均化段运动;同时,塑料受到螺杆的搅拌和挤压作用,并且在机筒的外热及塑料与设备之间的剪切磨擦热的作用下转变为粘流态,在螺槽中形成连续均匀的料流。
在工艺规定的温度作用下,塑料从固体状态转变为熔融状态的可塑物体,再经由螺杆的推动或者搅拌,将彻底塑化好的塑料推入机头,到达机头的料流,经模芯和模套间的环形间隙,从模套口挤出,挤包干线芯或者缆芯周围,形成连续密实的绝缘层或者护套层,然后经冷却和固化,制成电线电缆产品。
二,挤出过程的三个阶段塑料挤出主要依据的是塑料所具有的可塑态。
塑料在挤出机中完成可塑成型过程是一个复杂的物理过程:包括了混合、破碎、熔融、塑化、排气、压实并最后成型定型,这一过程是连续实现的。
然而习惯上,人们往往按塑料的不同反应将挤塑过程,人为的分成各个不同阶段;①塑化阶段 (塑料的混合、熔融和均化) ;②成型阶段(塑料的挤压成型);③定型阶段(塑料层的冷却和固化)。
1,塑化阶段。
也称为压缩阶段。
它是在挤塑机机筒内完成的,经过螺杆的旋转作用,使塑料由颗粒状固体变为可塑性的粘流体。
塑料在塑化阶段获得热量的来源有两个方面:一是机筒外部的电加热;二是螺杆旋转时产生的磨擦热。
起初的热量是由机筒外部的电加热产生的;当正常开车后,热量的取得则是由螺杆旋转物料在压缩,剪切、搅拌过程中与机筒内壁的磨擦和物料份子问的内磨擦而产生的。
2,成型阶段。
第七章-挤出成型

粘流(熔融)体的变形。
动态变化:
在螺杆和料筒间沿螺槽向前流动。
挤出过程中有:
T、P、η 的变化; 化学结构和物理结构的变化。
一、挤出过程和螺杆各段的职能
由于塑料在挤出过程中,在螺杆的全程中其形变特 点和流动情况是不同的。把塑料在挤出机内的流动沿螺 杆往机头方向分为三段来讨论。
加料段:固体输送区,物料形变很小; 压缩段:熔融区,物料压缩形变大,熔融流动次要; 均化段:熔体输送区,熔融流动是主要的。
正流与P无关,逆流和漏流与P成正比。
P
Q ,但有利于塑化。
2、螺杆转速n与流率Q的关系
AK
Q=
·n
B+K
对于一定的机器,挤出量与螺杆转速成正比。
3、螺杆几何尺寸与生产能力的关系
主要是螺杆直径、螺槽深度和均化段长度。
(1)螺槽深度H
正流与H成正比,逆 流与H3成正比。
三、挤出成型基本过程
1、塑化 在挤出机内将固体塑料加热并依靠塑料之间的内摩
擦热使其成为粘流态物料。 2、成型
在挤出机螺杆的旋转推挤作用下,通过具有一定形状 的口模,使粘流态物料成为连续的型材。
3、定型 用适当的方法,使挤出的连续型材冷却定型为制品。
四、挤出成型设备
螺杆式挤出机 连续成型,用处最多。 柱塞式挤出机 间歇成型,一般不用。
图7-9
二、挤出理论
1、固体输送理论
加料段的主要作用是固体输送。 塑料:未溶化、疏松的固体,表面发粘结块,形状不大。
物料沿螺槽 的向前运动
旋转运动-物料与螺杆的摩擦作用力 轴向水平运动-螺杆旋转时的轴向分力
物料
螺杆表面的摩擦力大 料筒表面的切向摩擦力小
旋转运动
第二节挤出过程和挤出理论

• 塑料由料斗进入料筒后,随着螺杆的旋转而被逐
渐推向机头方向。
• 1、加料段---输送并开始压实物料 • 螺槽为松散的固体粒子(或粉末)所充满,胶料
开始被压实。
• 2、压缩段 • 1)由于阻力,物料被压实 • 由于螺槽逐渐变浅,以及滤网、分流板和机头的
阻力,在塑料中形成了很高的压力,把物料压得 很密实。
筒上的沟槽深度变化、螺距的改变)
b.分流板、滤网Biblioteka 口模产生的阻力, c.压力的建立是挤出成型制品的重要条件
压力的建立也是物料得以经历物理状态变 化、得到均匀密实的熔体、并最后得到 成型制品的重要条件之一。
2)影响压力的因素
如果将沿料筒轴线 方向(包括口模) 测得的各点的物料 压力值作为纵座标, 以料筒轴线为横座 标做一曲线,即可 得到所谓压力轮廓 线,如右图所示。
L/Ds-一螺杆的长径比 L —— 螺杆的长度(螺杆的有效工 作长度)
P 一--螺纹头数i·
B ——螺纹槽的轴向宽度
Bb——机筒内表面处螺纹槽的轴向 宽度
Bs——螺杆螺纹槽根处的轴向宽度
B(r)——螺杆螺纹槽在任意半径处
的轴向宽度 W(r)---- 垂 直 于 螺棱的任意半 径处的螺槽宽度 Wb——机筒内表面处垂直于螺棱的 螺槽宽度 Ws——螺杆根径处垂直于螺棱的螺 槽宽度
(二)参变量
描写这一过程的参量有温度、压力、流率(或挤出 量、产量)和能量(或功率)。有时也用物料的 粘度,因其不易直接测得,而且它与温度有关, 故一般不用它来讨论挤出过程。
1、温度
温度是挤出过程得以进行的重要条件 之一。如前所述,物料从加入料斗到 最后成型为制品是经历了一个复杂的 温度过程的。
率波动、温度波动、压力波动。这些波 动也是评价挤出质量、挤压系统好坏的 标准之一。
- 1、下载文档前请自行甄别文档内容的完整性,平台不提供额外的编辑、内容补充、找答案等附加服务。
- 2、"仅部分预览"的文档,不可在线预览部分如存在完整性等问题,可反馈申请退款(可完整预览的文档不适用该条件!)。
- 3、如文档侵犯您的权益,请联系客服反馈,我们会尽快为您处理(人工客服工作时间:9:00-18:30)。
漏流也是由机头、口模、过滤网等对塑料反压引起的反 向流动,这种流动不是在螺槽中,而是在料筒与螺杆的 间隙中,这种流动的结果也使挤出量减少。塑料熔体的 真实流动是以螺旋形的轨迹出现的,其形状与一根嵌在 螺槽中的钢丝弹簧相仿。
公式
结论
由于漏流量与料筒螺杆间的间隙δ的三次方成正 比,新挤出机的间隙δ是很小的,随着螺杆料筒 的磨损,δ增大,则挤出量严重下降。
公式
结论
当流率G不变时,螺杆转速得增加将引起熔化速 率增加。
料筒温度的升高,先使熔化速率增加,但因为料 筒温度的提高会使熔体膜粘度下降,从而使剪切 热减少,因此存在着对应于最大融化速率的最佳 料筒温度。
进料温度的升高,可提高融化速率,从而缩短熔 化区的长度;但进料温度升高,对固体输送不利。
挤出过程-----压缩
在挤出过程中,塑料被压缩是绝对必要的。 首先塑料是一种热的不良导体,颗粒间如果有空
隙,将直接影响其传热,从而影响熔融速率; 其次也只有在沿螺杆长度方向上逐渐增加压力下,
才会将颗粒间的气体从料斗中排出,否则制品将 因为其内部产生气泡而成为次品或废品,最后较 高的系统压力,也保证了制品比较密实。
如果熔料从机头挤出过早,势必造成挤出物各处温度不 均匀,使制品产生色差、形变,或制品开裂的现象。
为了保证均匀混合,螺杆的熔体输送段应有足够的长度。
挤出过程-----排气
粉粒料颗粒之间夹杂着的空气。只要螺杆转速不太高, 一般来说,这部分气体在逐渐增高的压力下从料斗排出。
气体是物料从空气中吸附的水分,在加热时变成水蒸汽。 在塑料颗粒内部的一些物质,如低分子挥发物、低熔点
随着熔融的进行,当熔膜的厚度大于δ时,运动 着螺棱把熔膜刮下来,在螺棱的推进面前形成熔 池。在熔融的过程中,熔池愈来愈宽,剩下的固 体宽度越来越窄,直至最后完全消失。
挤出过程-----混合
物料体系中各组分均匀地分散混合,这些组分是指树脂 及各种添物料温度低,而固体和熔体之间的分界 面的温度正好是塑料的熔点。
公式
结论
降低Fs,在实际生产中,一方面是提高螺杆表 面的光洁度;另一方面,在成型过程中冷却螺杆 的加料段,这是塑料加工厂完全能够做到的。
增大Fb,塑料机械厂在制造挤出机时,经常在 料筒内开设纵向沟槽。
可采用最佳螺旋升角,而实际中并不这样做。
挤出理论----熔融
冷却实验
实验时,将本色母料和着色塑料(3%)的混合 物进行挤出。当达到稳态时,立即停止挤出并迅 速冷却螺杆和料筒,使机内塑料凝固,然后将凝 固的物料与螺杆一起从料斗中推出,物料从螺杆 上剥下,切断所得到的螺旋状带并观察物料的熔 化情况。
挤出过程-----压缩压力来源
在结构上螺杆的螺槽深度逐渐变浅,物料逐渐被 压缩;
在螺杆头部安装有分流板、过滤网及机头等阻力 元件;
实验证明,即使没有上述两因素,沿螺杆全长上 仍然会建立一定的压力。这是由物料对金属的摩 擦引起的。
挤出过程-----熔融
在压力升高的同时,固体塑料与加热着的料筒不 断地接触与摩擦,靠近机筒壁的塑料料温不断地 提高,到达熔点后,在机筒的内壁上形成一层薄 薄的熔膜δ1。
熔体输送
正流 (也称为拖曳流动)是指塑料沿着螺槽向机头方向的 流动,是由在螺槽中的塑料和螺杆与塑料和料筒的摩擦 作用而产生的;塑料的挤出量就是靠这种流动。
横流(也称为环流)是塑料在螺槽内不断地改变方向,作 环形流动;这种流动对塑料的混合、热交换和塑化都起了 积极的作用,但对挤出量不产生影响。
逆流 (也称为倒流或压力流动)它是由机头、口模、过滤 网等对塑料反压引起的反向流动;这种流动的结果减少了 挤出量。
挤出过程和挤出理论
高聚物的状态
玻璃态 高弹态 粘流态
挤出过程-----加料
塑料加入料斗后,依靠自重或在强制加料器的作 用下,进入螺杆螺槽的空间,在螺棱的推动下往 前挤出。在加料段螺槽内为松散的固体粒子或粉 末所充满,物料开始被压实。
挤出过程-----输送
从理论上讲,当塑料进入螺槽后,螺杆每转一转, 所有的塑料将往前输送一个导程。输送量事实上 取决于塑料对机筒的摩擦系数fb和塑料对螺杆的 摩擦系数fs。fb愈大或fs愈小,往前输送的固体 塑料量将越多。光滑机筒的输送效率为0.3~0.4。 加料段料筒开小沟槽时,其输送效率为0.5左右。 当机筒开大而深的沟槽时,输送效率可达到 0.6~0.8。
增塑剂等。在挤出过程中不断气化,只有当塑料熔融后 才能从熔体内部溢出。 因远离料斗,不得不使用排气式挤出机。
挤出理论----固体输送理论
当塑料进入挤出机的螺槽和料筒内壁,塑料立即就被压 实形成固体塞 (也称为固体床),并以恒定的速度移动。 固体塞的移动是受螺杆、料筒表面之间各摩擦力的控制 的。如果塑料与螺杆之间摩擦力Fs小于塑料与料筒之间 的摩擦力 Fb即Fs<Fb,则塑料沿螺棱方向前进,以其分 量沿轴向前进;如果Fs>=Fb,则塑料就随着螺杆转动, 不能沿轴向方向前进,也就是说挤出机不出料。塑料成 型加工的先驱们以固体摩擦力的静平衡为基础,得出了 固体输送速率 (Q)的计算式。