塑料瓶的注塑吹塑成型介绍
塑料桶吹塑工艺简述

塑料桶吹塑工艺简述•塑料桶中空吹塑根本上能够分为两大类:挤出—吹塑和注射—吹塑。
两者的主要不同点在于型坯的制备,然后的吹塑过程根本相同。
在这两种成型办法的根底上开展起来的有:挤出—拉伸—吹塑(简称挤—拉—吹),注射—拉伸—吹塑(简称注—拉—吹)以及多层映塑等。
注射-吹塑(简称注-吹)塑料瓶是采用注射成型法先将塑料制成有底型坯,再把型坯趁热移到吹塑模中吹塑成型的中空制品。
注-吹中空容器没有飞边,尺寸稳定性好,瓶口与螺纹质量优良,型坯厚度可预先调理,制品光泽度好,俭省原料。
但注-吹成型不合适消费大型和外形复杂的容器,又由于要运用注射和吹塑两副模具,所以设备投资较大。
注-吹中空容器以外形筒单的小型瓶体为主,它能够用聚氯乙烯、聚乙烯、聚丙烯和聚苯乙烯、聚酯、聚酰胺等多种树脂来消费。
主要用于医药、食品、化装品等的包装用于中空吹塑的塑料种类有聚乙烯、聚氯乙烯、聚丙烯、聚苯乙烯、线形聚酯、聚碳酸酯、聚酰胺、醋酸纤维素和聚缩醛树脂等。
其中高密度聚乙烯的耗费量占首位。
它普遍应用于食品、化工和处置液体的包装。
高分子量聚乙烯适用于制造大型燃料醝罐和桶等。
聚氯乙烯由于有较好的透明度和气密性,所以在化装品和洗濯剂的包装方面得到普遍应用。
随着无毒聚氯乙烯树脂和助剂的开发,以及拉伸吹塑技术的开展,聚氯乙烯容器在食品包装方面的用量疾速增加,并且曾经开端用于啤酒和其它含有二氧化碳气体饮料的包装。
线形聚酯资料是近几年进入中空吹塑范畴的新型资料。
由于其制品具有光泽的外观、优秀的透明性、较高的力学强度和容器内物品保管性较好,废弃物燃烧处置时不污染环境等方面的优点,所以在包装瓶方面开展很快,特别在耐压塑料食品容器方面的运用最为普遍。
聚丙烯因其树脂的改性和加工技术的进步,运用量也逐年增加。
主要原料及典型配方(l )聚乙烯普通选用熔体指数为l ~6 的聚乙烯树脂。
(2 )聚丙烯普通选网熔体指数为2 一4 的聚丙烯树脂。
(3 )聚苯乙烯普通选用通用型或抗冲型的注射级聚苯乙烯树脂。
药用塑料瓶的吹塑成型工艺
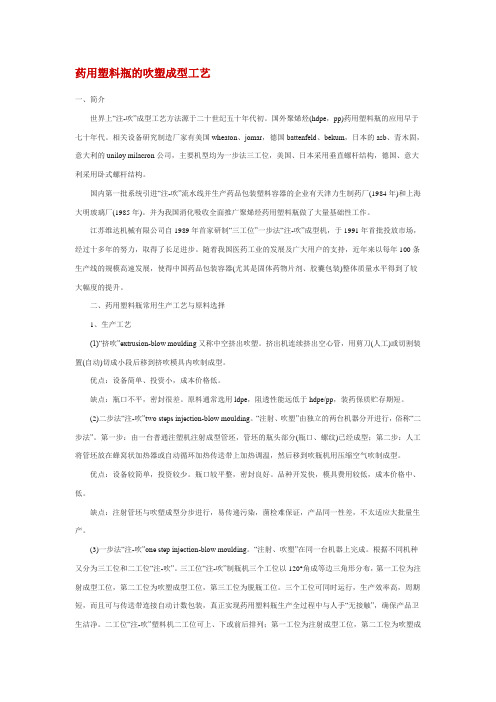
药用塑料瓶的吹塑成型工艺一、简介世界上“注-吹”成型工艺方法源于二十世纪五十年代初。
国外聚烯烃(hdpe,pp)药用塑料瓶的应用早于七十年代。
相关设备研究制造厂家有美国wheaton、jomar,德国battenfeld、bekum,日本的asb、青木固,意大利的uniloy milacron公司,主要机型均为一步法三工位,美国、日本采用垂直螺杆结构,德国、意大利采用卧式螺杆结构。
国内第一批系统引进“注-吹”流水线并生产药品包装塑料容器的企业有天津力生制药厂(1984年)和上海大明玻璃厂(1985年)。
并为我国消化吸收全面推广聚烯烃药用塑料瓶做了大量基础性工作。
江苏维达机械有限公司自1989年首家研制“三工位”一步法“注-吹”成型机,于1991年首批投放市场,经过十多年的努力,取得了长足进步。
随着我国医药工业的发展及广大用户的支持,近年来以每年100条生产线的规模高速发展,使得中国药品包装容器(尤其是固体药物片剂、胶囊包装)整体质量水平得到了较大幅度的提升。
二、药用塑料瓶常用生产工艺与原料选择1、生产工艺(1)“挤吹”extrusion-blow moulding又称中空挤出吹塑。
挤出机连续挤出空心管,用剪刀(人工)或切割装置(自动)切成小段后移到挤吹模具内吹制成型。
优点:设备简单、投资小,成本价格低。
缺点:瓶口不平,密封很差。
原料通常选用ldpe,阻透性能远低于hdpe/pp,装药保质贮存期短。
(2)二步法“注-吹”two steps injection-blow moulding。
“注射、吹塑”由独立的两台机器分开进行,俗称“二步法”。
第一步:由一台普通注塑机注射成型管坯,管坯的瓶头部分(瓶口、螺纹)已经成型;第二步:人工将管坯放在蜂窝状加热器或自动循环加热传送带上加热调温,然后移到吹瓶机用压缩空气吹制成型。
优点:设备较简单,投资较少。
瓶口较平整,密封良好。
品种开发快,模具费用较低,成本价格中、低。
药用塑料瓶的吹塑工艺及外面检测
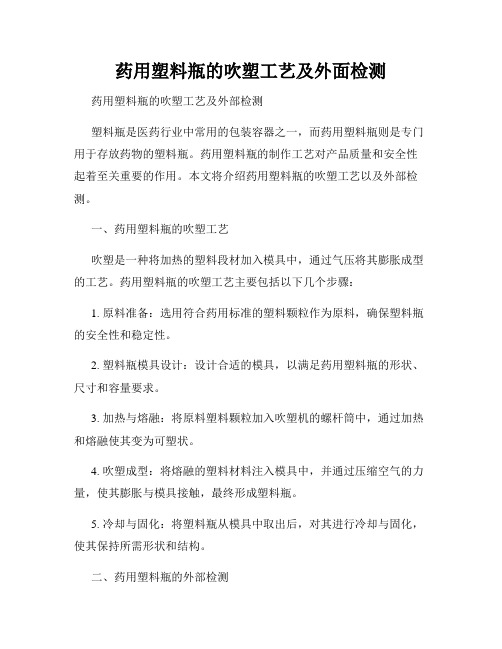
药用塑料瓶的吹塑工艺及外面检测药用塑料瓶的吹塑工艺及外部检测塑料瓶是医药行业中常用的包装容器之一,而药用塑料瓶则是专门用于存放药物的塑料瓶。
药用塑料瓶的制作工艺对产品质量和安全性起着至关重要的作用。
本文将介绍药用塑料瓶的吹塑工艺以及外部检测。
一、药用塑料瓶的吹塑工艺吹塑是一种将加热的塑料段材加入模具中,通过气压将其膨胀成型的工艺。
药用塑料瓶的吹塑工艺主要包括以下几个步骤:1. 原料准备:选用符合药用标准的塑料颗粒作为原料,确保塑料瓶的安全性和稳定性。
2. 塑料瓶模具设计:设计合适的模具,以满足药用塑料瓶的形状、尺寸和容量要求。
3. 加热与熔融:将原料塑料颗粒加入吹塑机的螺杆筒中,通过加热和熔融使其变为可塑状。
4. 吹塑成型:将熔融的塑料材料注入模具中,并通过压缩空气的力量,使其膨胀与模具接触,最终形成塑料瓶。
5. 冷却与固化:将塑料瓶从模具中取出后,对其进行冷却与固化,使其保持所需形状和结构。
二、药用塑料瓶的外部检测为了确保药用塑料瓶的质量和安全性,外部检测是必不可少的环节。
药用塑料瓶的外部检测可以分为以下几个方面:1. 外观检查:对药用塑料瓶的外观进行检查,包括无明显瑕疵、无气泡、无划痕等。
2. 容量测定:使用专用设备对塑料瓶的容量进行测量,确保其符合设计要求。
3. 尺寸检测:使用测量工具对药用塑料瓶的尺寸进行检测,比如直径、高度、壁厚等。
4. 材料检验:对药用塑料瓶的材料进行检验,确保塑料材料符合药用标准,并不含有有害物质。
5. 密封性能测试:对药用塑料瓶的密封性能进行测试,确保不会发生泄漏或者污染。
除了以上的外部检测,还可以根据需要进行其他相关的检验,以确保药用塑料瓶的质量符合要求。
总结:药用塑料瓶的制作工艺中,吹塑工艺对于产品质量和安全性具有重要影响。
通过合理的原料准备、熔融加热、吹塑成型和冷却固化等步骤,可以制作出高质量的药用塑料瓶。
同时,外部检测是确保药用塑料瓶质量的重要环节,包括外观检查、容量测定、尺寸检测、材料检验和密封性能测试等。
注射拉伸吹塑成型工艺
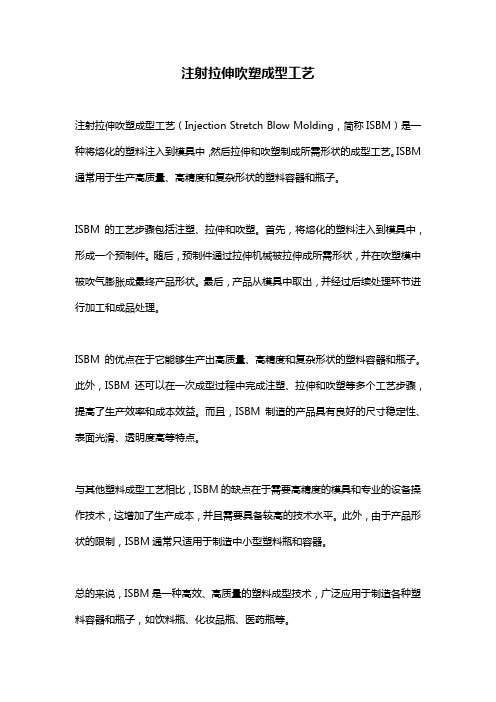
注射拉伸吹塑成型工艺
注射拉伸吹塑成型工艺(Injection Stretch Blow Molding,简称ISBM)是一种将熔化的塑料注入到模具中,然后拉伸和吹塑制成所需形状的成型工艺。
ISBM 通常用于生产高质量、高精度和复杂形状的塑料容器和瓶子。
ISBM的工艺步骤包括注塑、拉伸和吹塑。
首先,将熔化的塑料注入到模具中,形成一个预制件。
随后,预制件通过拉伸机械被拉伸成所需形状,并在吹塑模中被吹气膨胀成最终产品形状。
最后,产品从模具中取出,并经过后续处理环节进行加工和成品处理。
ISBM的优点在于它能够生产出高质量、高精度和复杂形状的塑料容器和瓶子。
此外,ISBM还可以在一次成型过程中完成注塑、拉伸和吹塑等多个工艺步骤,提高了生产效率和成本效益。
而且,ISBM制造的产品具有良好的尺寸稳定性、表面光滑、透明度高等特点。
与其他塑料成型工艺相比,ISBM的缺点在于需要高精度的模具和专业的设备操作技术,这增加了生产成本,并且需要具备较高的技术水平。
此外,由于产品形状的限制,ISBM通常只适用于制造中小型塑料瓶和容器。
总的来说,ISBM是一种高效、高质量的塑料成型技术,广泛应用于制造各种塑料容器和瓶子,如饮料瓶、化妆品瓶、医药瓶等。
塑料加工技术注塑挤出和吹塑
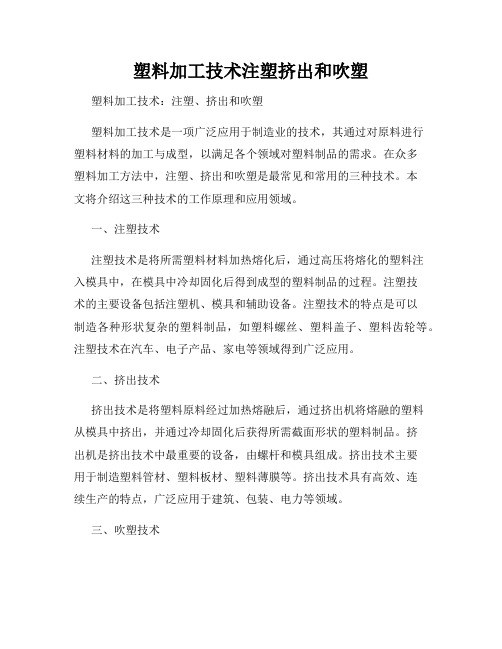
塑料加工技术注塑挤出和吹塑塑料加工技术:注塑、挤出和吹塑塑料加工技术是一项广泛应用于制造业的技术,其通过对原料进行塑料材料的加工与成型,以满足各个领域对塑料制品的需求。
在众多塑料加工方法中,注塑、挤出和吹塑是最常见和常用的三种技术。
本文将介绍这三种技术的工作原理和应用领域。
一、注塑技术注塑技术是将所需塑料材料加热熔化后,通过高压将熔化的塑料注入模具中,在模具中冷却固化后得到成型的塑料制品的过程。
注塑技术的主要设备包括注塑机、模具和辅助设备。
注塑技术的特点是可以制造各种形状复杂的塑料制品,如塑料螺丝、塑料盖子、塑料齿轮等。
注塑技术在汽车、电子产品、家电等领域得到广泛应用。
二、挤出技术挤出技术是将塑料原料经过加热熔融后,通过挤出机将熔融的塑料从模具中挤出,并通过冷却固化后获得所需截面形状的塑料制品。
挤出机是挤出技术中最重要的设备,由螺杆和模具组成。
挤出技术主要用于制造塑料管材、塑料板材、塑料薄膜等。
挤出技术具有高效、连续生产的特点,广泛应用于建筑、包装、电力等领域。
三、吹塑技术吹塑技术是将热塑性塑料预制成中空管状的“坯料”,再将其放入吹塑机的模具内,通过吹气或真空力使其沿模具内表面膨胀,从而获得所需的中空形状的塑料制品。
吹塑技术的主要设备是吹塑机和模具。
吹塑技术通常用于制造塑料瓶、塑料容器、塑料玩具等。
吹塑技术具有成本低、生产效率高、产品质量好的特点,被广泛应用于食品包装、日用品制造等领域。
总结起来,注塑、挤出和吹塑是塑料加工技术中最常见的三种方法。
它们各自具有独特的工作原理和应用领域,为满足不同行业对塑料制品的需求提供了可靠的解决方案。
随着技术不断进步和创新,塑料加工技术将在未来的发展中迎来更加广阔的应用前景。
PET瓶吹塑生产工艺流程
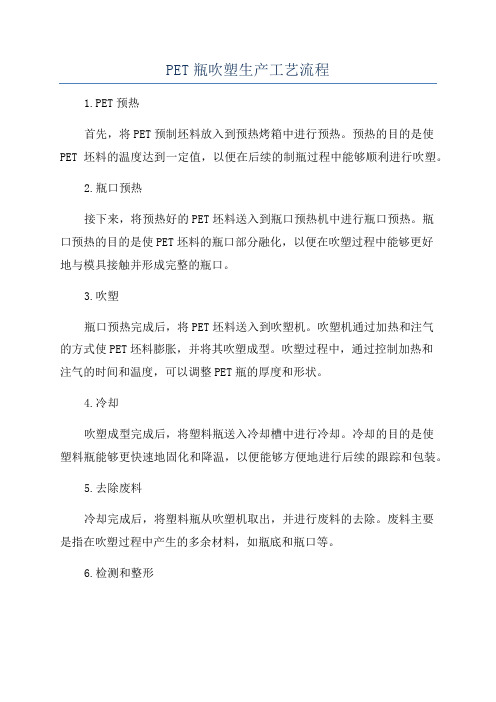
PET瓶吹塑生产工艺流程
1.PET预热
首先,将PET预制坯料放入到预热烤箱中进行预热。
预热的目的是使PET坯料的温度达到一定值,以便在后续的制瓶过程中能够顺利进行吹塑。
2.瓶口预热
接下来,将预热好的PET坯料送入到瓶口预热机中进行瓶口预热。
瓶
口预热的目的是使PET坯料的瓶口部分融化,以便在吹塑过程中能够更好
地与模具接触并形成完整的瓶口。
3.吹塑
瓶口预热完成后,将PET坯料送入到吹塑机。
吹塑机通过加热和注气
的方式使PET坯料膨胀,并将其吹塑成型。
吹塑过程中,通过控制加热和
注气的时间和温度,可以调整PET瓶的厚度和形状。
4.冷却
吹塑成型完成后,将塑料瓶送入冷却槽中进行冷却。
冷却的目的是使
塑料瓶能够更快速地固化和降温,以便能够方便地进行后续的跟踪和包装。
5.去除废料
冷却完成后,将塑料瓶从吹塑机取出,并进行废料的去除。
废料主要
是指在吹塑过程中产生的多余材料,如瓶底和瓶口等。
6.检测和整形
经过废料去除后,对塑料瓶进行检测和整形。
检测的目的是检查塑料
瓶的质量和外观是否合格,整形则是通过去除瓶口和底部的多余材料,使
塑料瓶形状更加完美。
7.包装
这就是PET瓶吹塑生产工艺流程的一个详细介绍。
通过以上的步骤,PET瓶生产过程可以实现自动化和批量化生产,提高生产效率和产品质量。
塑料成型工艺

塑料成型工艺1. 引言塑料成型工艺是一种将塑料原料经过加热、软化、塑性成型、冷却固化等过程,制成所需形状的工艺过程。
塑料成型工艺被广泛应用于各个领域,如塑料制品、电子产品、汽车零部件等行业。
本文将介绍几种常见的塑料成型工艺,包括注塑成型、挤出成型、吹塑成型以及压力成型。
2. 注塑成型注塑成型是一种常用的塑料成型工艺,它通过将塑料原料加热至熔化状态后,注入到模具中,经过冷却固化后获得所需形状的制品。
注塑成型具有制作复杂零件、生产效率高、成本低等优点。
常见的注塑成型设备包括注塑机、模具和辅助设备等。
在注塑成型过程中,需要控制好注塑机的温度、压力、注射速度等参数,以确保产品的质量。
3. 挤出成型挤出成型是将塑料原料加热至熔化状态后,通过挤出机将熔化的塑料挤出流动成型。
挤出成型可以制造出长条状、管状、片状等不同形状的产品。
挤出成型广泛应用于制造塑料薄膜、塑料管道、塑料板材等。
在挤出成型过程中,需要控制好挤出机的温度、挤压压力、挤出速度等参数,以确保产品的质量。
4. 吹塑成型吹塑成型是一种常见的制造塑料容器的工艺。
吹塑成型过程中,首先将塑料原料加热至熔化状态,然后将熔化的塑料放入吹塑机的模具中,通过气压将塑料吹气膨胀成型。
吹塑成型常用于制造各种塑料瓶、塑料容器等。
在吹塑成型过程中,需要控制好吹塑机的温度、气压、冷却时间等参数,以确保产品的质量。
5. 压力成型压力成型是一种通过施加压力将塑料原料在模具中成型的工艺。
压力成型常用于制造大型塑料制品,如汽车零部件、家电外壳等。
常见的压力成型工艺有压铸、热压和压延等。
在压力成型过程中,需要控制好压力、时间、温度等参数,以确保产品的质量。
6. 总结塑料成型工艺是一种常见的制造工艺,通过加热、软化、形状成型和冷却固化等步骤,将塑料原料制成所需形状的制品。
本文介绍了几种常见的塑料成型工艺,包括注塑成型、挤出成型、吹塑成型和压力成型。
每种成型工艺都有其适用的领域和优点,需要根据具体情况选择合适的工艺。
PET瓶吹塑工艺分析
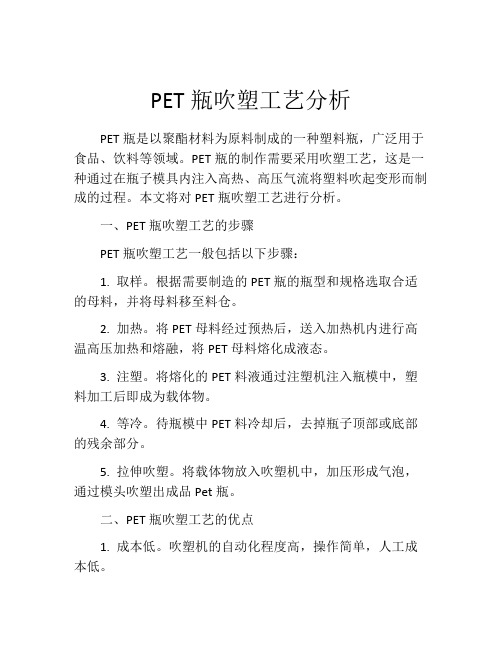
PET瓶吹塑工艺分析PET瓶是以聚酯材料为原料制成的一种塑料瓶,广泛用于食品、饮料等领域。
PET瓶的制作需要采用吹塑工艺,这是一种通过在瓶子模具内注入高热、高压气流将塑料吹起变形而制成的过程。
本文将对PET瓶吹塑工艺进行分析。
一、PET瓶吹塑工艺的步骤PET瓶吹塑工艺一般包括以下步骤:1. 取样。
根据需要制造的PET瓶的瓶型和规格选取合适的母料,并将母料移至料仓。
2. 加热。
将PET母料经过预热后,送入加热机内进行高温高压加热和熔融,将PET母料熔化成液态。
3. 注塑。
将熔化的PET料液通过注塑机注入瓶模中,塑料加工后即成为载体物。
4. 等冷。
待瓶模中PET料冷却后,去掉瓶子顶部或底部的残余部分。
5. 拉伸吹塑。
将载体物放入吹塑机中,加压形成气泡,通过模头吹塑出成品Pet瓶。
二、PET瓶吹塑工艺的优点1. 成本低。
吹塑机的自动化程度高,操作简单,人工成本低。
2. 生产效率高。
吹塑机的生产效率高,可24小时连续工作,产量大。
3. PET材料的塑性好。
PET瓶材料有较好的塑性和深拉伸性,可以制成各种形状的PET瓶,可广泛用于各个领域。
4. 生产成本低。
PET材料具有较低的成本,制作PET瓶的成本相对较低,因此价格较低,利润高。
三、PET瓶吹塑工艺的缺点1. 需要较高的技能技术。
PET瓶吹塑工艺需要技术工人具有良好的操作技能和专业知识,要求较高。
2. 技术和设备要求较高。
PET瓶吹塑工艺需要专业的技术和模具设备,多数的生产厂家都设置了专门的生产线,设备投入较大。
3. 塑料自然老化。
由于PET瓶中的塑料是有机材料,会随着老化逐渐失去弹性和韧性,长期使用存在安全隐患。
四、PET瓶吹塑工艺的应用范围PET瓶吹塑工艺可广泛用于食品、饮料、化妆品、药品、家居日化等领域。
具有重量轻、隔氧、保鲜、卫生、方便等优点。
在饮料市场上,PET瓶已经成为主流的包装形式。
因为它们是轻型,易于携带,便于装填,且具有更长的保管期限。
吸塑吸塑加工之吹塑、注塑、吸塑的区别

吸塑吸塑加工之吹塑、注塑、吸塑的区别在日常生活和工业生产中,我们经常听到吹塑、注塑、吸塑这些加工方式。
这些加工方式都属于热加工和塑料成型技术,它们各自有自己的优点和适用范围。
本文主要介绍吹塑、注塑和吸塑三种加工方式的区别。
吹塑吹塑是一种常用于制造塑料容器和瓶子的加工方式。
在吹塑过程中,先准备好预制的管状物,然后在管状物的一端加热软化,接着通过风压将塑料吹成成型的容器。
吹塑适用于制造中小型的塑料容器,如瓶子、桶等。
吹塑的优点在于成本低、生产率高、生产效率高、物料容易处理等。
而缺点是成型尺寸、形状有限,无法制造较复杂的产品。
注塑注塑是一种将加热的塑料材料注入模具,再冷却硬化成为成型产品的加工方法。
注塑过程中,首先将加热的塑料注入到模具中,然后经过短暂的冷却和硬化,即可以获得成型的产品。
注塑适用于生产各种尺寸、形状各异的产品,如手机外壳、汽车零部件、电器外壳等。
注塑的优点在于适用性广泛,可以制造非常复杂的产品,精度高,制品质量好,但缺点在于生产周期长,成本较高。
吸塑吸塑是通过真空把片状塑料材料贴附在塑料模具上,并使其与模具表面紧密贴合,待塑料材料冷却硬化后与模具一起成型的加工方法。
吸塑适用于生产各种中小型的塑料产品,如玩具、名片盒等。
吸塑的优点在于成本较低,手工操作容易,生产效率较高,并且可以生产中小型的塑料制品。
但缺点是成型尺寸、形状受限,无法制造较复杂的产品。
三种加工方法的比较下表列出了三种加工方法在成型效率、成本和适用范围等方面的比较。
吹塑注塑吸塑成型效率高低中等成本低高中等适用范围小型容器复杂零部件中小型产品结论以上是三种热加工技术的区别和优缺点,选择何种加工方式取决于所需要生产的产品,成本,生产周期和适用范围等因素。
注塑适用于生产各种尺寸、形状各异的产品。
吹塑适用于生产中小型的塑料容器,如瓶子、桶等。
吸塑适用于生产中小型的塑料制品,如玩具、名片盒等。
综上所述,吹塑、注塑和吸塑的加工方法都有各自的优劣,生产企业应根据实际需求和预算选择相应的加工方法,以获得最佳效益。
PET塑料瓶之吹瓶工艺简介
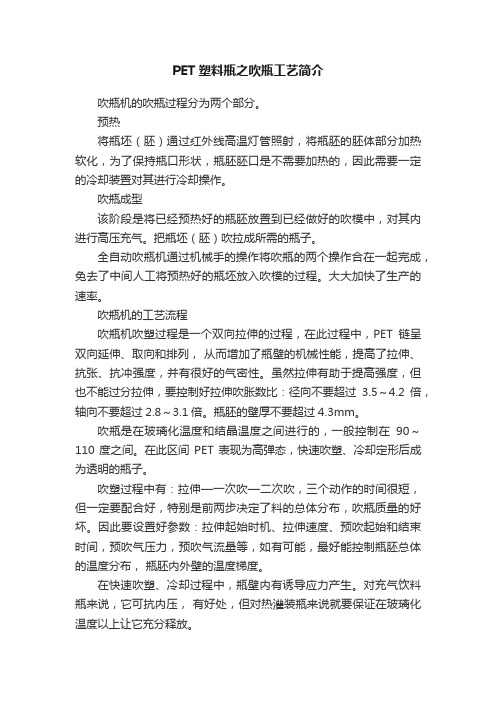
PET塑料瓶之吹瓶工艺简介吹瓶机的吹瓶过程分为两个部分。
预热将瓶坯(胚)通过红外线高温灯管照射,将瓶胚的胚体部分加热软化,为了保持瓶口形状,瓶胚胚口是不需要加热的,因此需要一定的冷却装置对其进行冷却操作。
吹瓶成型该阶段是将已经预热好的瓶胚放置到已经做好的吹模中,对其内进行高压充气。
把瓶坯(胚)吹拉成所需的瓶子。
全自动吹瓶机通过机械手的操作将吹瓶的两个操作合在一起完成,免去了中间人工将预热好的瓶坯放入吹模的过程。
大大加快了生产的速率。
吹瓶机的工艺流程吹瓶机吹塑过程是一个双向拉伸的过程,在此过程中,PET链呈双向延伸、取向和排列,从而增加了瓶壁的机械性能,提高了拉伸、抗张、抗冲强度,并有很好的气密性。
虽然拉伸有助于提高强度,但也不能过分拉伸,要控制好拉伸吹胀数比:径向不要超过3.5~4.2倍,轴向不要超过2.8~3.1倍。
瓶胚的壁厚不要超过4.3mm。
吹瓶是在玻璃化温度和结晶温度之间进行的,一般控制在90~110度之间。
在此区间PET 表现为高弹态,快速吹塑、冷却定形后成为透明的瓶子。
吹塑过程中有:拉伸—一次吹—二次吹,三个动作的时间很短,但一定要配合好,特别是前两步决定了料的总体分布,吹瓶质量的好坏。
因此要设置好参数:拉伸起始时机、拉伸速度、预吹起始和结束时间,预吹气压力,预吹气流量等,如有可能,最好能控制瓶胚总体的温度分布,瓶胚内外壁的温度梯度。
在快速吹塑、冷却过程中,瓶壁内有诱导应力产生。
对充气饮料瓶来说,它可抗内压,有好处,但对热灌装瓶来说就要保证在玻璃化温度以上让它充分释放。
下面是吹瓶工艺流程图:PET吹塑瓶可分为两类,一类是有压力瓶,如充装碳酸含气饮料的瓶;另一类为无压力瓶,如充装水、茶、食用油等的瓶。
茶饮料瓶是掺混了聚萘二甲酸乙二酯(PEN)的改性PET瓶或PET与热塑性聚芳酯的复合瓶,在分类上属热瓶,可耐热85℃以上;水瓶则属冷瓶,对耐热性无要求。
在成型工艺上热瓶与冷瓶相似。
设备目前,PET全自动吹瓶机的生产厂家国外进口主要有法国的SIDEL 公司、德国的KRONES公司,国产的有福建全冠公司等。
洗涤水壶的吹塑和注塑工艺的特性
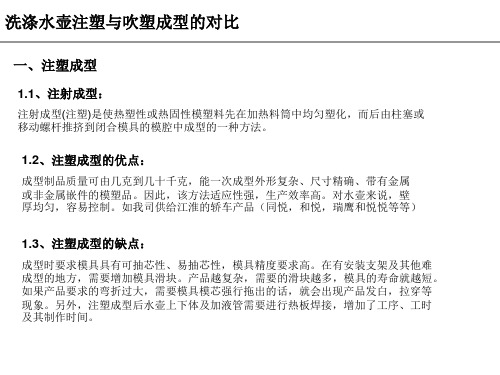
图1
图2
1 2
的对比
3.3、从产品内部模具抽芯来分析:
3.3.1、从模具分型分析
模具要施行注塑,必须要把水壶一 分为二,然后再通过热板焊接为一 体。如果以(图4)红色线进行分模, 在出现焊接面过大,焊接不牢固。 如果以(图5)进行分模,则水壶下 体白线处无法进行脱模
洗涤水壶注塑与吹塑成型的对比
三、注塑和吹塑成型工艺举例说明(以江淮轻卡N721窄体为例)
3.1、从整体上来看
(如图1),N721窄体水壶,外形比较复杂,尖角和面 比较多,外形为一个极不规则的造型。因而只能采用吹 塑工艺制作。
3.2、从外形制作分析:
3.2.1、图2中卡槽,弧形, 内部空间较大,开口较小, 另外还有粉色部分的放脱口, 注定无法脱模,只能强行脱 模。 3.2.2、图3中可以看出,水 壶的安装支架及其他卡槽过 多,如注塑需增加大量的滑 块及模具分型困难,无法实 现。
洗涤水壶注塑与吹塑成型的对比
一、注塑成型
1.1、注射成型:
注射成型(注塑)是使热塑性或热固性模塑料先在加热料筒中均匀塑化,而后由柱塞或 移动螺杆推挤到闭合模具的模腔中成型的一种方法。
1.2、注塑成型的优点:
成型制品质量可由几克到几十千克,能一次成型外形复杂、尺寸精确、带有金属 或非金属嵌件的模塑品。因此,该方法适应性强,生产效率高。对水壶来说,壁 厚均匀,容易控制。如我司供给江淮的轿车产品(同悦,和悦,瑞鹰和悦悦等等)
1.3、注塑成型的缺点:
成型时要求模具具有可抽芯性、易抽芯性,模具精度要求高。在有安装支架及其他难 成型的地方,需要增加模具滑块。产品越复杂,需要的滑块越多,模具的寿命就越短。 如果产品要求的弯折过大,需要模具模芯强行拖出的话,就会出现产品发白,拉穿等 现象。另外,注塑成型后水壶上下体及加液管需要进行热板焊接,增加了工序、工时 及其制作时间。
注塑吹塑工艺流程
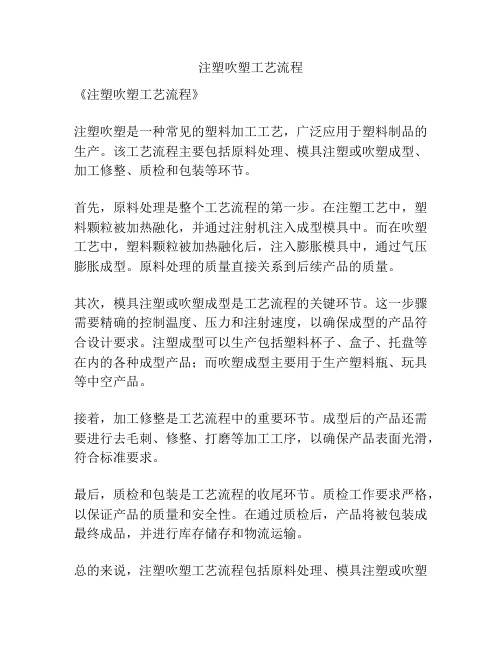
注塑吹塑工艺流程
《注塑吹塑工艺流程》
注塑吹塑是一种常见的塑料加工工艺,广泛应用于塑料制品的生产。
该工艺流程主要包括原料处理、模具注塑或吹塑成型、加工修整、质检和包装等环节。
首先,原料处理是整个工艺流程的第一步。
在注塑工艺中,塑料颗粒被加热融化,并通过注射机注入成型模具中。
而在吹塑工艺中,塑料颗粒被加热融化后,注入膨胀模具中,通过气压膨胀成型。
原料处理的质量直接关系到后续产品的质量。
其次,模具注塑或吹塑成型是工艺流程的关键环节。
这一步骤需要精确的控制温度、压力和注射速度,以确保成型的产品符合设计要求。
注塑成型可以生产包括塑料杯子、盒子、托盘等在内的各种成型产品;而吹塑成型主要用于生产塑料瓶、玩具等中空产品。
接着,加工修整是工艺流程中的重要环节。
成型后的产品还需要进行去毛刺、修整、打磨等加工工序,以确保产品表面光滑,符合标准要求。
最后,质检和包装是工艺流程的收尾环节。
质检工作要求严格,以保证产品的质量和安全性。
在通过质检后,产品将被包装成最终成品,并进行库存储存和物流运输。
总的来说,注塑吹塑工艺流程包括原料处理、模具注塑或吹塑
成型、加工修整、质检和包装等多个环节。
每个环节都需要严格的控制和管理,以确保最终产品的质量和安全。
PE塑料及其成型工艺整理讲解

PE塑料及其成型工艺整理讲解介绍本文档旨在对PE塑料及其成型工艺进行整理讲解,帮助读者了解PE塑料的特性以及常见的成型工艺。
PE塑料特性- PE塑料是聚乙烯(Polyethylene)的简称,是一种常见的塑料材料。
- PE塑料具有良好的韧性、耐磨性、耐寒性和化学稳定性。
- PE塑料具有较高的强度和刚度,并且易于加工。
PE塑料成型工艺1. 注塑成型(Injection Molding)- 注塑成型是一种常见的PE塑料成型工艺。
- 注塑成型利用注塑机将PE塑料加热熔化后,通过模具的注射动作,将熔融的塑料注入模具中,然后冷却成型。
- 注塑成型广泛应用于制造塑料制品,如塑料、塑料零件等。
2. 吹塑成型(Blow Molding)- 吹塑成型也是一种常见的PE塑料成型工艺。
- 吹塑成型是将PE塑料加热熔化后,通过吹塑机将熔融的塑料送入膨胀好的模具中,通过气压将塑料吹塑成型。
- 吹塑成型广泛应用于制造塑料瓶、塑料桶等中空。
3. 挤塑成型(Extrusion Molding)- 挤塑成型也是一种常见的PE塑料成型工艺。
- 挤塑成型利用挤塑机将PE塑料加热熔化后,通过模具的挤出动作,将熔融的塑料挤压出来,并冷却成型。
- 挤塑成型广泛应用于制造塑料管、塑料板材等长条状产品。
- 压力成型是一种将PE塑料加热熔化后,置于模具中,在一定的压力和温度下进行成型的工艺。
- 压力成型适用于制造PE塑料零件、PE塑料薄片等产品。
总结本文对PE塑料及其成型工艺进行了整理讲解。
PE塑料具有良好的特性,常见的成型工艺包括注塑成型、吹塑成型、挤塑成型和压力成型。
了解这些成型工艺对于进行塑料制品的设计和生产具有重要意义。
参考资料:[请填写参考资料,不要引用无法确认的内容]以上是关于PE塑料及其成型工艺的整理讲解。
如有疑问,请随时提问。
简述塑料成型的主要方法

简述塑料成型的主要方法塑料成型是将塑料原料转化为制件的过程,通过各种成型方法使塑料原料成为具有所需形状、尺寸和性能的制件。
以下是塑料成型的主要方法:1.注射成型:注射成型是一种常用的塑料成型方法,通过将塑料原料加热至熔融状态,然后注入模具中,冷却后脱模得到所需形状的制件。
注射成型适用于各种热塑性塑料和部分热固性塑料。
2.挤出成型:挤出成型是通过加压方式将塑料原料从模具口挤出,然后在冷却或定型过程中得到所需形状的制件。
挤出成型主要用于生产连续的管材、片材、型材等。
3.压延成型:压延成型是将塑料原料在加热状态下通过一系列轧辊的碾压、拉伸,使其成为薄膜或片材的工艺过程。
压延成型适用于热塑性塑料,如聚乙烯、聚氯乙烯等。
4.吹塑成型:吹塑成型是将塑料原料加热至熔融状态,然后通过模具口吹入空气使其膨胀并贴合模具型腔表面,冷却后得到所需形状的制件。
吹塑成型适用于生产各种中空制件,如瓶子、罐子等。
5.热成型:热成型是将塑料原料加热至软化状态,然后将其覆盖在模具上,通过冷却和定型得到所需形状的制件。
热成型适用于生产大型或复杂的制件,如汽车零部件、家具面板等。
6.旋转成型:旋转成型是通过旋转模具使塑料原料在离心力作用下充满模具型腔,冷却后得到所需形状的制件。
旋转成型主要用于生产圆筒形或旋转体形的制件,如油桶、瓶盖等。
7.激光成型:激光成型是一种高精度、高效率的塑料成型方法,通过激光束照射在塑料原料表面,使其熔融并按照预设形状固化,从而得到制件。
激光成型适用于生产小型、高精度制件,如电子元件、医疗器械等。
8.热压成型:热压成型是将塑料原料加热至软化状态,然后将其覆盖在模具上,再通过加压方式使其贴合模具型腔表面,冷却后得到所需形状的制件。
热压成型适用于生产薄片状或板材制件,如包装材料、建筑材料等。
9.真空成型:真空成型是将塑料原料加热至软化状态,然后在真空作用下使其贴合模具型腔表面,冷却后得到所需形状的制件。
真空成型适用于生产薄片状或管材制件,如食品包装材料、管道等。
药用塑料瓶的生产技术和成型工艺
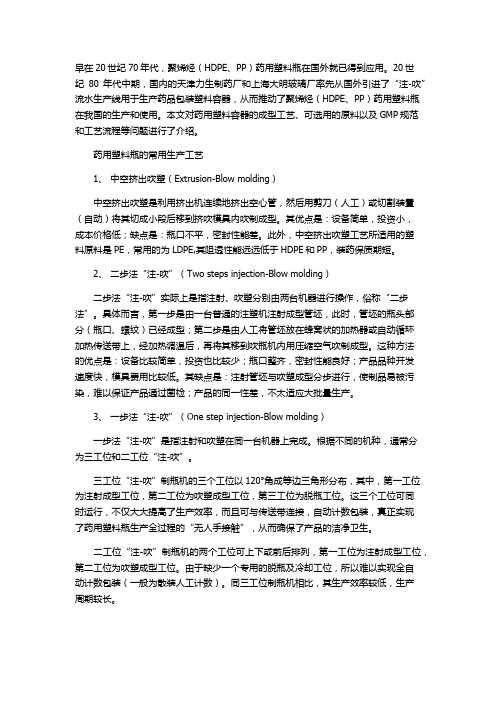
早在20世纪70年代,聚烯烃(HDPE、PP)药用塑料瓶在国外就已得到应用。
20世纪80年代中期,国内的天津力生制药厂和上海大明玻璃厂率先从国外引进了“注-吹”流水生产线用于生产药品包装塑料容器,从而推动了聚烯烃(HDPE、PP)药用塑料瓶在我国的生产和使用。
本文对药用塑料容器的成型工艺、可选用的原料以及GMP规范和工艺流程等问题进行了介绍。
药用塑料瓶的常用生产工艺1、中空挤出吹塑(Extrusion-Blow molding)中空挤出吹塑是利用挤出机连续地挤出空心管,然后用剪刀(人工)或切割装置(自动)将其切成小段后移到挤吹模具内吹制成型。
其优点是:设备简单,投资小,成本价格低;缺点是:瓶口不平,密封性能差。
此外,中空挤出吹塑工艺所适用的塑料原料是PE,常用的为LDPE,其阻透性能远远低于HDPE和PP,装药保质期短。
2、二步法“注-吹”(Two steps injection-Blow molding)二步法“注-吹”实际上是指注射、吹塑分别由两台机器进行操作,俗称“二步法”。
具体而言,第一步是由一台普通的注塑机注射成型管坯,此时,管坯的瓶头部分(瓶口、螺纹)已经成型;第二步是由人工将管坯放在蜂窝状的加热器或自动循环加热传送带上,经加热调温后,再将其移到吹瓶机内用压缩空气吹制成型。
这种方法的优点是:设备比较简单,投资也比较少;瓶口整齐,密封性能良好;产品品种开发速度快,模具费用比较低。
其缺点是:注射管坯与吹塑成型分步进行,使制品易被污染,难以保证产品通过菌检;产品的同一性差,不太适应大批量生产。
3、一步法“注-吹”(One step injection-Blow molding)一步法“注-吹”是指注射和吹塑在同一台机器上完成。
根据不同的机种,通常分为三工位和二工位“注-吹”。
三工位“注-吹”制瓶机的三个工位以120°角成等边三角形分布,其中,第一工位为注射成型工位,第二工位为吹塑成型工位,第三工位为脱瓶工位。
塑料包装瓶的成型过程

塑料包装瓶的成型过程塑料瓶主要是挤吹(洗发水瓶那种)和注吹(可乐瓶那种)。
挤出吹塑与注射吹塑成型塑料瓶的两种工艺方法的区别在于:注射成型中,用来成型塑料瓶体的模具要包括阳模与阴模。
由注射机在高压下把塑料熔体注入模具型腔内,打开模腔时,阳模必须从阴模内移开,以顶出瓶体。
而在挤出吹塑中,要采用挤出机头来成型型坯。
吹塑模具主要由两半阴模构成,一般不需阳模,用注入的压缩空气吹胀型坯。
注吹与挤吹相比挤出吹塑的特点为:(1)吹塑机械(尤其是吹塑模具)的造价较低,例如成型相同的产品时,吹塑机械的造价约为注塑机械的三分之一或二分之一,产品的生产成本也较低。
(2)吹塑上,型坯是在较低压力下通过挤出机头成型并在低压(多数为0.2-1.0Mpa)下吹胀的,因而产品的残余应力较小,耐拉伸、冲击、弯曲与环境等各种应变的性能较高,具有较好的使用性能。
而在注射吹塑成型中,塑料熔体要在高压(15-140Mpa)下通过模具流道与浇口,这会导致不匀称的应力分布。
(3)吹塑级塑料(例如PE)的分子量比注塑级塑料的高得多。
这样吹塑产品具有较高的冲击韧性与很高的耐环境应力开裂性能,这对生产大容量的塑料瓶是十分有利的。
(4)由于吹塑模具仅由阴模构成,故通过简单地调节机头模口间隙或挤出条件即可改变瓶体的壁厚,这对预先无法准确计算所需壁厚的产品是很有利的。
而对注射成型,需要改变产品壁厚的费用要高得多。
(5)吹塑可成型壁厚很薄的产品,这样的产品无法由注射方法来成型。
(6)吹塑可成型形状复杂、不规则且为整体式的产品。
采用注射吹塑成型时,要先生产出两件或多件后,通过搭扣配方,溶剂粘合或超声波焊接等组合在一起。
注射吹塑成型的特点为:(1)塑料熔体被注入型坯模具,它在型腔内周向受到一定的取向效应。
此外型坯吹胀时的温度比挤出吹塑的低些,吹胀产生的取向效应能较多地保留下来,这些有助于提高塑料瓶的强度等性能。
(2)塑料瓶尺寸(尤其是颈部螺纹尺寸)精度高,较易于按要求保证瓶体壁厚的均匀性,瓶体规格均一。
塑料瓶的注塑吹塑成型介绍(五篇)
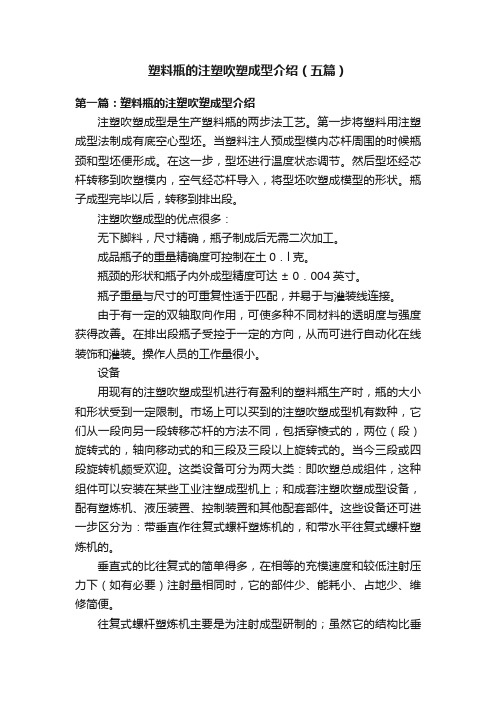
塑料瓶的注塑吹塑成型介绍(五篇)第一篇:塑料瓶的注塑吹塑成型介绍注塑吹塑成型是生产塑料瓶的两步法工艺。
第一步将塑料用注塑成型法制成有底空心型坯。
当塑料注人预成型模内芯杆周围的时候瓶颈和型坯便形成。
在这一步,型坯进行温度状态调节。
然后型坯经芯杆转移到吹塑模内,空气经芯杆导入,将型坯吹塑成模型的形状。
瓶子成型完毕以后,转移到排出段。
注塑吹塑成型的优点很多:无下脚料,尺寸精确,瓶子制成后无需二次加工。
成品瓶子的重量精确度可控制在土0.l克。
瓶颈的形状和瓶子内外成型精度可达± 0.004英寸。
瓶子重量与尺寸的可重复性适于匹配,并易于与灌装线连接。
由于有一定的双轴取向作用,可使多种不同材料的透明度与强度获得改善。
在排出段瓶子受控于一定的方向,从而可进行自动化在线装饰和灌装。
操作人员的工作量很小。
设备用现有的注塑吹塑成型机进行有盈利的塑料瓶生产时,瓶的大小和形状受到一定限制。
市场上可以买到的注塑吹塑成型机有数种,它们从一段向另一段转移芯杆的方法不同,包括穿棱式的,两位(段)旋转式的,轴向移动式的和三段及三段以上旋转式的。
当今三段或四段旋转机颇受欢迎。
这类设备可分为两大类:即吹塑总成组件,这种组件可以安装在某些工业注塑成型机上;和成套注塑吹塑成型设备,配有塑炼机、液压装置、控制装置和其他配套部件。
这些设备还可进一步区分为:带垂直作往复式螺杆塑炼机的,和带水平往复式螺杆塑炼机的。
垂直式的比往复式的简单得多,在相等的充模速度和较低注射压力下(如有必要)注射量相同时,它的部件少、能耗小、占地少、维修简便。
往复式螺杆塑炼机主要是为注射成型研制的;虽然它的结构比垂直式的复杂,但操作的可靠性较好。
当前的成型机械,包括大型的标准生产装置,可在较高的生产速度下生产出较大的瓶子来;注射装置的完善使聚氯乙烯和含丙烯睛的树脂更易于加工;增加工段(位)的开发工作正在继续进行。
通常,医药工业和化妆品工业是16央司和更小的注塑吹塑成型塑料瓶的市场。
塑料瓶包装工艺流程
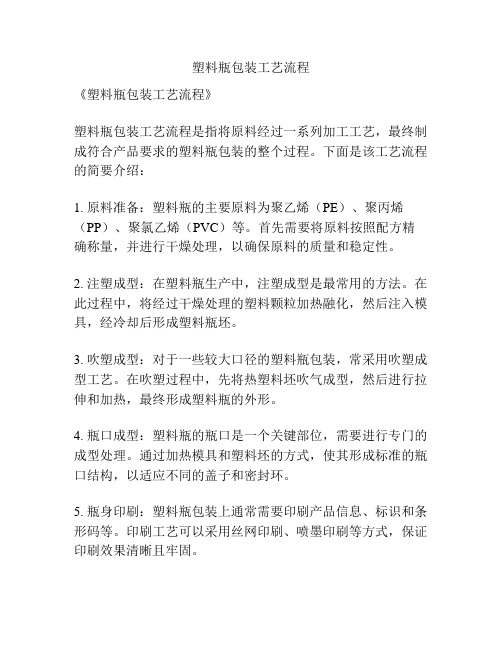
塑料瓶包装工艺流程
《塑料瓶包装工艺流程》
塑料瓶包装工艺流程是指将原料经过一系列加工工艺,最终制成符合产品要求的塑料瓶包装的整个过程。
下面是该工艺流程的简要介绍:
1. 原料准备:塑料瓶的主要原料为聚乙烯(PE)、聚丙烯(PP)、聚氯乙烯(PVC)等。
首先需要将原料按照配方精确称量,并进行干燥处理,以确保原料的质量和稳定性。
2. 注塑成型:在塑料瓶生产中,注塑成型是最常用的方法。
在此过程中,将经过干燥处理的塑料颗粒加热融化,然后注入模具,经冷却后形成塑料瓶坯。
3. 吹塑成型:对于一些较大口径的塑料瓶包装,常采用吹塑成型工艺。
在吹塑过程中,先将热塑料坯吹气成型,然后进行拉伸和加热,最终形成塑料瓶的外形。
4. 瓶口成型:塑料瓶的瓶口是一个关键部位,需要进行专门的成型处理。
通过加热模具和塑料坯的方式,使其形成标准的瓶口结构,以适应不同的盖子和密封环。
5. 瓶身印刷:塑料瓶包装上通常需要印刷产品信息、标识和条形码等。
印刷工艺可以采用丝网印刷、喷墨印刷等方式,保证印刷效果清晰且牢固。
6. 包装检验:在生产结束后,需要对塑料瓶进行外观质量、尺寸和重量等多项指标的检验,确保产品的质量符合标准要求。
综上所述,塑料瓶包装工艺流程涉及到原料准备、注塑成型、吹塑成型、瓶口成型、瓶身印刷和包装检验等多个环节。
通过这些工艺步骤,最终可以生产出质量可靠、外观精美的塑料瓶包装产品。
注拉吹成型工艺(一)

注拉吹成型工艺(一)什么是注拉吹成型工艺?注拉吹成型工艺(Injection Blow Molding)是一种将预制的塑料制品加热并吹制成型的工艺。
它结合了注塑成型和吹塑成型两种工艺的优点,在制造细长颈部或薄壁塑料瓶时非常有效。
注拉吹成型的流程注拉吹成型工艺一般分为三个步骤:注塑、吹塑和取出。
具体流程如下:1.注塑:将预制的塑料颗粒或粉末通过注射器喷入模具中,使其充满整个模具腔。
注塑时要注意温度、压力和速度的控制,以确保塑料可以充分填充模具并达到理想的形态和尺寸。
2.吹塑:在注塑完成后,模具会自动向下移动,将塑料模块从注射器上分离开来。
然后模具在旋转时会将空气吹入模具腔中,使得塑料被吹成型,形成瓶子的外形和颈部。
3.取出:在瓶子形成后,模具再次向下移动,将模具与吹出的瓶子分离。
瓶子从顶部弹出并通过传送带送出,准备进行下一步的处理。
注拉吹成型的应用注拉吹成型工艺广泛应用于生产各种塑料瓶和容器,如矿泉水瓶、洗发水瓶、油桶等等。
由于其高效、精度高、生产成本低、环保等优点,注拉吹成型工艺正逐渐取代其他传统的成型工艺。
结语总的来说,注拉吹成型工艺在现代塑料产品制造中扮演了重要的角色。
它的高效和精度已经被广泛地认可,并在生产过程中得到了广泛的应用。
随着技术的进步和需求的不断增加,注拉吹成型工艺在未来将会有更为广泛的应用。
注拉吹成型工艺的优点注拉吹成型工艺有以下优点:1.高效:注拉吹成型工艺可以快速、精确地制造大批量的塑料产品,生产效率远高于手工制作和其他传统的成型工艺。
2.精度高:注拉吹成型工艺通过计算机控制,可以精确地控制模具的温度、压力和速度,从而实现产品大小、形状和密度的高度一致。
3.制造成本低:注拉吹成型工艺使用的是塑料颗粒或粉末,相较于传统聚合物使用,成本更低并且可大规模生产。
4.环保:注拉吹成型工艺只使用塑料颗粒或粉末,不使用化学物质及其他危险物质,同时可回收再利用,减少浪费和对环境的影响。
注拉吹成型工艺的发展趋势及展望注拉吹成型在塑料制品行业中占据着重要的地位,随着市场需求和技术的创新,注拉吹成型工艺正在不断发展和完善。
吹塑成型原理

吹塑成型原理
吹塑成型是一种常用的塑料加工方法,主要用于制作中空容器和管道等产品。
其原理是通过将高温熔化的塑料挤出到模具中,然后利用气压或真空将塑料挤压成模具的形状。
具体来说,吹塑成型通常分为两个步骤:挤出和吹气。
在挤出过程中,将加热至熔融状态的塑料注入到挤出机的螺杆中。
螺杆加热和旋转,将塑料推送到模具中的挤出头部。
挤出头部附近有一个空气进气孔,通过调节气压来控制空气进入的速度和压力。
在挤出头部出口处,有一个圆形成型腔。
当塑料从挤出头部挤出时,空气通过进气孔进入模具,将热塑性塑料按照模具的形状吹膨胀。
形成薄壁中空形状的塑料制品。
在吹塑成型过程中,气压、温度和模具的形状等参数都会影响最终产品的质量。
通过控制这些参数,可以生产出各种不同形状和尺寸的塑料制品。
总的来说,吹塑成型是一种通过挤出塑料并利用气压将其形成成型的方法。
它在制造塑料容器和管道等产品时具有广泛的应用。
- 1、下载文档前请自行甄别文档内容的完整性,平台不提供额外的编辑、内容补充、找答案等附加服务。
- 2、"仅部分预览"的文档,不可在线预览部分如存在完整性等问题,可反馈申请退款(可完整预览的文档不适用该条件!)。
- 3、如文档侵犯您的权益,请联系客服反馈,我们会尽快为您处理(人工客服工作时间:9:00-18:30)。
注塑吹塑成型是生产塑料瓶的两步法工艺。
第一步将塑料用注塑成型法制成有底空心型坯。
当塑料注人预成型模内芯杆周围的时候瓶颈和型坯便形成。
在这一步,型坯进行温度状态调节。
然后型坯经芯杆转移到吹塑模内,空气经芯杆导入,将型坯吹塑成模型的形状。
瓶子成型完毕以后,转移到排出段。
注塑吹塑成型的优点很多:
无下脚料,尺寸精确,瓶子制成后无需二次加工。
成品瓶子的重量精确度可控制在土0.l克。
瓶颈的形状和瓶子内外成型精度可达± 0.004英寸。
瓶子重量与尺寸的可重复性适于匹配,并易于与灌装线连接。
由于有一定的双轴取向作用,可使多种不同材料的透明度与强度获得改善。
在排出段瓶子受控于一定的方向,从而可进行自动化在线装饰和灌装。
操作人员的工作量很小。
设备
用现有的注塑吹塑成型机进行有盈利的塑料瓶生产时,瓶的大小和形状受到一定限制。
市场上可以买到的注塑吹塑成型机有数种,它们从一段向另一段转移芯杆的方法不同,包括穿棱式的,两位(段)旋转式的,轴向移动式的和三段及三段以上旋转式的。
当今三段或四段旋转机颇受欢迎。
这类设备可分为两大类:即吹塑总成组件,这种组件可以安装在某些工业注塑成型机上;和成套注塑吹塑成型设备,配有塑炼机、液压装置、控制装置和其他配套部件。
这些设备还可进一步区分为:带垂直作往复式螺杆塑炼机的,和带水平往复式螺杆塑炼机的。
垂直式的比往复式的简单得多,在相等的充模速度和较低注射压力下(如有必要)注射量相同时,它的部件少、能耗小、占地少、维修简便。
往复式螺杆塑炼机主要是为注射成型研制的;虽然它的结构比垂直式的复杂,但操作的可靠性较好。
当前的成型机械,包括大型的标准生产装置,可在较高的生产速度下生产出较大的瓶子来;注射装置的完善使聚氯乙烯和含丙烯睛的树脂更易于加工;增加工段(位)
的开发工作正在继续进行。
通常,医药工业和化妆品工业是16央司和更小的注塑吹塑成型塑料瓶的市场。
专
门为这种工艺开发的新原料已经使注塑吹塑成型工厂进入其他市场。
聚丙烯共聚物加
工容易,透明度好,而且成型快,故实际上已经取代了装咳嗽感冒药和漱口剂的玻璃瓶。
其他新型树脂有注塑吹塑级聚氯乙烯均聚物和聚碳酸酯。
这些结晶透明的材料已经比较容易地在垂直螺杆机上进行了加工,也在装有连续柱塞螺杆的水平螺杆机上进行
了加工。
新型的流线型歧管加上改进的含丙烯腈树脂和聚氯乙烯树脂已经使多腔室操作成为现实,尽管这些树脂是热敏性的。
一个8一腔室模具已成功地用于聚氯乙烯加工,数
个12一腔室的模具目前已应用于含丙烯睛树脂瓶的生产。
现有数个公司正要用8一腔室模具生产聚氯乙烯瓶子,它01的材料是经过改性的,以降低其热敏性。
现已明显,采用较大的机器,较高的合模压力和较大的压板面积将能经济地生产出4升以下的塑料瓶。
精确的瓶颈和无下脚料这样的优点将能逐步补偿
工模具的较高成本。
由于机器的发展(增加段数)和模具设计的革新,未来的开发工作将致力于树脂定向性的改善。
模具设计技术的进步已能制造偏颈塑料瓶、方颈塑料瓶,可使瓶底上带
精密的槽,和减少整个瓶壁的厚度,缩短制作时间。
模具设计的发展将使注塑吹塑成型逐步进入家用化学品、玩具,特别是食品容器市场。
本文由塑料瓶 塑料瓶生产厂家 整理
收集提供!。