典型的塔板效率经验数据
实验七:精馏塔板效率测定实验

实验七精馏塔塔板效率测定实验一、实验目的1、熟悉精馏单元操作过程的设备与流程;2、了解板式塔结构与流体力学性能;3、掌握精馏塔的操作方法与原理;4、学习精馏塔效率的测定方法。
二、实验原理蒸馏原理是利用混合物中组分间挥发度的不同来分离组分,经多次平衡分离的蒸馏过程称为精馏。
常见的精馏单元过程由精馏塔、冷凝器、再沸器、加料系统、回流系统、产品贮槽、料液贮槽及测量仪表等组成。
精馏塔本身又分为板式精馏塔和填料精馏塔,本产品为板式精馏塔。
可进行连续或间歇精馏操作,回流比可任意调节,也可以进行全回流操作。
在板式精馏塔中,混合液的蒸气逐板上升,在塔顶冷凝后回流液逐板下降。
气液两相在塔板上接触实现热质传递,从而达到分离的目的。
如果在每层塔板上,下降液体与上升蒸气处于平衡状态,则该塔板称为理论板。
然而在实际操作的精馏塔中,由于气液两相在塔板上接触的时间有限,气液两相不可能完全达到平衡,亦即实际塔板的分离效果达不到理论板的作用,因此精馏塔所需要的实际板数总是比理论板数要多。
对于二元物系,如已知其气液平衡数据,则根据精馏塔的原料液组成、进料热状况、操作回流比及塔顶馏出液组成、塔底釜液组成,即可以求出该塔的理论板数N t。
1、精馏塔的正常与稳定操作精馏塔从开车到正常稳定操作是一个从不稳定到稳定、不正常到正常的渐进过程。
因为刚开车时,塔板上均没有液体,蒸汽可直接穿过干板到达冷凝器,被冷凝成液体后再返回塔内第一块塔板,并与上升的蒸汽接触;而后,逐板溢流至塔釜。
首先返回塔釜的液体经过的塔板数最多,达到的气液平衡次数也最多,所以其轻组分的含量必然最高;而第一块塔板上的液体轻组分含量反而会比它下面的塔板上的液体轻组分含量低一些,这就是“逆行分馏”现象。
从“逆行分馏”到正常精馏,需要较长的转换时间。
对实验室的精馏装臵,这一转换时间至少需30分钟以上。
而对于实际生产装臵,转换时间有可能超过2小时。
所以精馏塔从开车到稳定、正常操作的时间也必须保证在30 分钟以上。
板式精馏塔的操作与效率的测定实验报告

2.全塔效率
(4)
式中,NT、NP分别表示达到同样的分离要求所需的理论塔板数和实际塔板数。理论塔板可用M-T图解法求取。
(1)在储料罐中配制一定浓度的来自精溶液(10%~20%)。(2)待塔全回流操作稳定时,打开进料阀,开启进料泵电源,调节进料量至适当的流量。
(3)启动回流比控制器电源,调节回流比R。
(4)当流量,塔顶及塔内温度读数稳定后即可取样分析。
3.乙醇浓度的测定
(1)比重法。根据天平测定比重的方法,分别测出塔顶、塔底试样的比重。并由酒精组分一比重对照表查得酒精质量分数。测完的样品分别倒回回收瓶中。
(2)气相色谱法。
4.注意事项
(1)塔顶放空阀一定要打开。
(2)料液一定要加到设定液位2/3处方可打加热管电源,否则塔釜液位过低会使电加热丝露出、干烧致坏。
(3)部分回流时,进料泵电源开启前务必先打开进料阀,否则会损害进料泵。
六、实验原始数据记录
取得两组数据:
(1)塔顶:0.810(测量得)
质量比:93.44;体积比:95.75(查表得)
(4)当塔顶温度,回流量和塔釜温度稳定约15~30min后,由塔顶取样管和塔底取样口用取样瓶接取适量试样,取样前应先取少量式样冲洗取样瓶两次。取样后用塞子将取样瓶塞严,并使其冷却到室温。塔板上液体取样注射器从所测定的塔板中缓缓抽出,取1mL左右注入事先洗净烘干的针剂瓶中,各个样品尽可能同时取样。
2.部分回流
79.9
精馏塔板效率
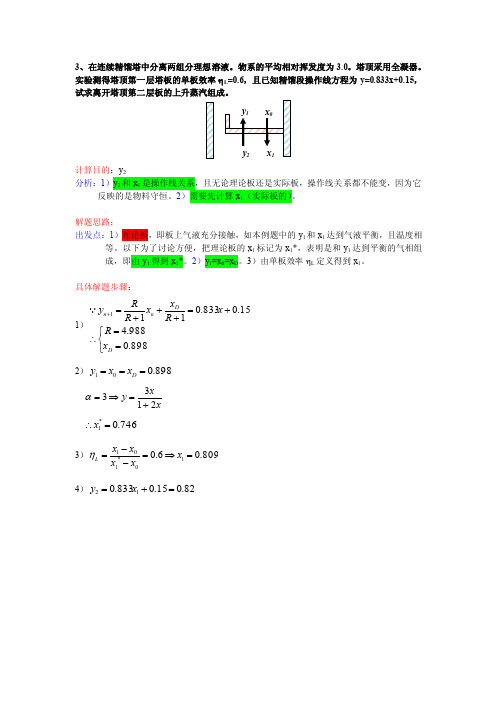
3、在连续精馏塔中分离两组分理想溶液。
物系的平均相对挥发度为3.0。
塔顶采用全凝器。
实验测得塔顶第一层塔板的单板效率ηL =0.6,且已知精馏段操作线方程为y=0.833x+0.15,试求离开塔顶第二层板的上升蒸汽组成。
计算目的:y 2 分析:1)y 2和x 1是操作线关系,且无论理论板还是实际板,操作线关系都不能变,因为它
反映的是物料守恒。
2)需要先计算x 1(实际板的)。
解题思路:
出发点:1)理论板,即板上气液充分接触,如本例题中的y 1和x 1达到气液平衡,且温度相
等。
以下为了讨论方便,把理论板的x 1标记为x 1*,表明是和y 1达到平衡的气相组成,即由y 1得到x 1*。
2)y 1=x 0=x D 。
3)由单板效率ηL 定义得到x 1。
具体解题步骤:
1)⎩⎨⎧==∴+=+++=
+898.0988.415.0833.0111D D n n x R x R x x R R y 2)898.001===D x x y
x
x y 2133+=⇒=α 746.0*1=∴x
3)809.06.010
*101=⇒=--=x x x x x L η 4)82.015.0833.012=+=x y。
第六节--塔板效率

第六节塔板效率板式塔是以塔板效率表示传质效率的。
§7.6.1塔板效率的不同表示方法及其应用塔板效率通常有三种定义形式。
1)总板效率E T定义(7-30)式中N T——理论板数;N——实际板数。
总板效率表示全塔的平均效率。
由理论板数N T除以E T即得实际所需的塔板数,使用十分方便,故总板效率被广泛采用。
但总板效率并不区分同一个塔中不同塔板的传质效率差别,所以在塔器研究与改进操作中不能满足要求。
2)默弗里板效率以气相浓度变化表示的默弗里板效率的定义式为(7-31)式中y n,y n+1——离开第n块塔板及第n+1块塔板的气相浓度,摩尔分率;y*n——与离开第n块塔板的液相浓度x n呈平衡的气相浓度,摩尔分率。
以液相浓度变化表示的默弗里板效率的定义式为(7-32)式中x n-1,x n——离开第n-1块塔板及第n块塔板的液相平均浓度,摩尔分率;x*n——与离开第n块塔板的气相平均浓度y n呈平衡的液相浓度,摩尔分率。
默弗里板效率用以标明一块塔板的传质效率。
欲测定默弗里板效率,只需在塔板的上、下方取样测其浓度,即可按定义算出,由此可判断该塔板操作状况的优劣。
当液相流过塔板时,若传质效率高且液相返混程度小,塔板上液相有明显的浓度差,则默弗里板效率值可能大于1;若液相返混严重,塔板上液相浓度比较均匀,默弗里板效率则小于1。
通常因液相总存在返混,所以默弗里板效率小于1。
默弗里板效率又称单板效率。
参看图7-28。
左图表示通过第n块塔板前后的气液浓度。
右图中“a-c-b”表示一个实际的“梯级”。
E mV是长度与长度之比,E mL是长度与长度之比。
根据默弗里板效率可直接用作图法求取实际塔板数。
现以已知不同液相浓度时的E mV值为例说明之。
在“y-x”图中在操作线与平衡线间任意作数条垂直于x轴的直线,并按已知默弗里板效率值在这些直线中取内分点。
如图7-29中在直线中取c点,c点位置需满足(注意E mV依不同x而异)。
第六节--塔板效率

第六节塔板效率板式塔是以塔板效率表示传质效率的。
§7.6.1塔板效率的不同表示方法及其应用塔板效率通常有三种定义形式。
1)总板效率E T定义(7-30)式中N T——理论板数;N——实际板数。
总板效率表示全塔的平均效率。
由理论板数N T除以E T即得实际所需的塔板数,使用十分方便,故总板效率被广泛采用。
但总板效率并不区分同一个塔中不同塔板的传质效率差别,所以在塔器研究与改进操作中不能满足要求。
2)默弗里板效率以气相浓度变化表示的默弗里板效率的定义式为(7-31)式中y n,y n+1——离开第n块塔板及第n+1块塔板的气相浓度,摩尔分率;y*n——与离开第n块塔板的液相浓度x n呈平衡的气相浓度,摩尔分率。
以液相浓度变化表示的默弗里板效率的定义式为(7-32)式中x n-1,x n——离开第n-1块塔板及第n块塔板的液相平均浓度,摩尔分率;x*n——与离开第n块塔板的气相平均浓度y n呈平衡的液相浓度,摩尔分率。
默弗里板效率用以标明一块塔板的传质效率。
欲测定默弗里板效率,只需在塔板的上、下方取样测其浓度,即可按定义算出,由此可判断该塔板操作状况的优劣。
当液相流过塔板时,若传质效率高且液相返混程度小,塔板上液相有明显的浓度差,则默弗里板效率值可能大于1;若液相返混严重,塔板上液相浓度比较均匀,默弗里板效率则小于1。
通常因液相总存在返混,所以默弗里板效率小于1。
默弗里板效率又称单板效率。
参看图7-28。
左图表示通过第n块塔板前后的气液浓度。
右图中“a-c-b”表示一个实际的“梯级”。
E mV是长度与长度之比,E mL是长度与长度之比。
根据默弗里板效率可直接用作图法求取实际塔板数。
现以已知不同液相浓度时的E mV值为例说明之。
在“y-x”图中在操作线与平衡线间任意作数条垂直于x轴的直线,并按已知默弗里板效率值在这些直线中取内分点。
如图7-29中在直线中取c点,c点位置需满足(注意E mV依不同x而异)。
精馏塔的塔板效率

•根据雾沫夹带对板效率的影响,在工程上一般建议使 e'M不V 超过0.1。这样对
于表观效率的降低程度一般在10%之内。
L'M
(3)板效率与全塔效率的关系
当操作线和平衡线都是直线时
Nth
ln
1 a
1 A
1
N pr
ln 1
A
A LV M
M,板上摩尔分数时气液相平衡的斜率
A,操作线斜率与平衡线斜率之比
②板效率MV或Ml (莫菲里效率)
实际上的摩尔分数变化与平衡时应达到的摩尔分数变化之比
对于气体 MV
y n y n 1
y
* n
y n1
yn*
yn
Yn-1
对于液体
ML
xn1 xn xn1 xn*
xn
yn
Xn+1
Xn*
xn
③ 点效率OV
塔板上某点处实际上的摩尔分数变化与平衡时应达到的 摩尔分数变化之比 板效率是板上各点效率数值积分结果的一种表达形式
OV
Байду номын сангаас
y n
y
* J
yn1 yn1
(2)雾沫夹带对板效率的影响(表观效率)
由于雾沫夹带的结果,使一部分 高沸点组分含量多的液相直接被 带到上一层塔板,从而降低了上 一层塔板上的低沸点组分的摩尔 分数,抵消了部分精馏的效果。
a
MV
1
e'MV L'M
e',单位鼓泡面积的夹带量
L'M,单位鼓泡面积的液相流量
5.8 空气二元系精馏过程的计算
5.8.1 精馏塔的塔板效率 5.8.2 用y-x图解法求双级精馏塔的理论塔板数
化工实验精馏实验单板效率计算

化工实验精馏实验单板效率计算精馏是一种重要的分离和纯化技术,在化工实验中被广泛应用。
在精馏过程中,通过加热和冷却装置,将混合物中的组分按照其沸点的差异进行分离,从而获得所需纯化的物质。
精馏实验中,板塔效率是评价精馏塔分离性能的重要指标之一、本文将详细介绍精馏实验中板塔效率的计算方法。
板塔效率是指在一定条件下,塔板上产生的蒸馏液与塔板上所存在的组分间的传质情况。
计算板塔效率的方法主要有理论计算和实验计算两种。
理论计算方法是利用传质方程和物料平衡方程,结合扩散系数和溶解度等参数,通过数学模型计算得到。
而实验计算方法则是通过实际进行精馏实验,测量实验数据后,利用实验结果进行计算。
常用的实验计算方法包括:用塔板温度测定法、用馏头和下塔液的成分测定法、用馏液进出口温度比辐射法等。
其中,用塔板温度测定法是最为常用的实验计算方法之一、它基于塔板上蒸馏液和下塔液的物质平衡,通过测量不同塔板上的温度,计算得到塔板效率。
在实验中,首先需要确定实验所使用的精馏塔的塔板数。
其次,对精馏塔进行加热,使混合物开始蒸发。
然后,通过温度计等仪器测量各塔板上的温度,记录数据。
根据实验数据,可以通过下述的计算公式来计算板塔效率:塔板效率=(x进-x出)/(x进-x平衡)其中,x进和x出分别为进塔液和出塔液的组分浓度,x平衡为精馏塔平衡液的组分浓度。
需要注意的是,实验计算方法的精确程度受多种因素的影响,如实验操作技巧、仪器的准确度等。
因此,在进行板塔效率的计算时,需要进行多次实验,取平均值,使结果更加准确。
此外,为了进一步提高实验计算方法的精确性,还可以采用其他辅助手段,如红外光谱和质谱等仪器的应用,以辅助测量组分浓度。
总之,板塔效率的计算是精馏实验中一个重要的步骤,对于评价精馏技术的有效性具有重要意义。
通过实验计算方法,可以有效地获得精馏塔的分离性能,为其进一步优化提供依据。
Hysys流程调试的一样技术

Hysys 模拟计算故障调试的通用技术1.第一检查solver(求解器)是不是处于Hold(保留)模式。
只要模拟进程中连接碰到问题,求解器就会处于Hold 模式。
当处于HOLD 模式时,本来尚未求解的物流及单元操作可能会显现to be solved 字样,(反之亦然),这可能会造成麻烦,若是不注意会难以处置。
当求解器处于HOLD 模式时, "Holding..."会出此刻HYSYS 状态条中,同时工具条红灯会亮,按绿灯那么求解器会从头激活。
2.认真检查HYSYS 提供的连接错误的详细信息。
他们通常会帮你找到问题的来源。
所有的连接错误与以下图很像3.要调整模拟计算时物流的流动方向。
例如,若是进料从左侧进入,它告诉你哪里出了问题这里告诉你操作新计算值它告诉你老的计算结果产品从右边抽出,要进行左右调整。
在你尽力调试上游操作之前,下游操作没有错误这是超级重要的。
3. Always debug(调试) simulations in the direction of the process flow. For example, if the feed streams enter on the left and product streams exit on the right, debug from left to right. It is important that downstream operations be error-free before you attempt to debug upstream operations.当调试流程的时候必然要注意流程的方向。
例如,假设进料物流在左,出料物流在右,调试的时候就从左向右检查。
不然若是下游的操作单元犯错了而你却试图调试上游的操作单元,后果就会愈来愈乱了。
4. HYSYS Workbook是超级方便的调试工具。
你能够迅速地判定哪些模拟变量是用户规定的(蓝色),哪些变量是计算生成的(黑色)。
Hysys流程调试的一般技巧
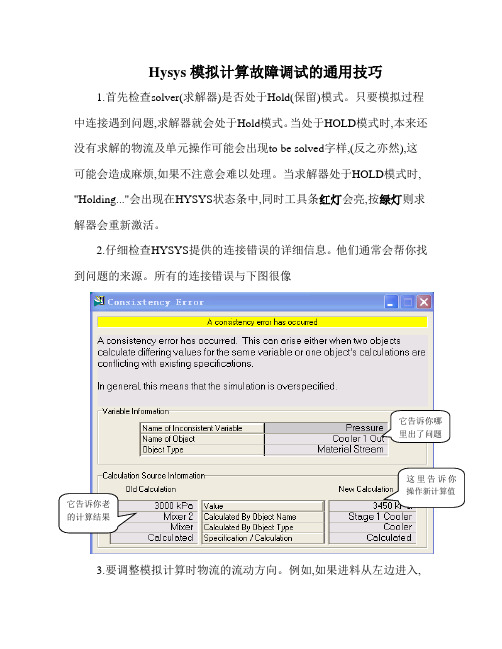
Hysys 模拟计算故障调试的通用技巧1.首先检查solver(求解器)是否处于Hold(保留)模式。
只要模拟过程中连接遇到问题,求解器就会处于Hold 模式。
当处于HOLD 模式时,本来还没有求解的物流及单元操作可能会出现to be solved 字样,(反之亦然),这可能会造成麻烦,如果不注意会难以处理。
当求解器处于HOLD 模式时, "Holding..."会出现在HYSYS 状态条中,同时工具条红灯会亮,按绿灯则求解器会重新激活。
2.仔细检查HYSYS 提供的连接错误的详细信息。
他们通常会帮你找到问题的来源。
所有的连接错误与下图很像3.要调整模拟计算时物流的流动方向。
例如,如果进料从左边进入,产品从右边抽出,要进行左右调整。
在你努力调试上游操作之前,下游操作没有错误这是非常重要的。
3. Always debug(调试) simulations in the direction of the process flow. For example, if the feed streams enter on the left and product streams exit on the right, debug from left to right. It is important that downstream operations be error-free before you attempt to debug upstream operations.当调试流程的时候一定要注意流程的方向。
例如,假如进料物流在左,出料物流在右,调试的时候就从左向右检查。
否则如果下游的操作单元出错了而你却试图调试上游的操作单元,后果就会越来越乱了。
4. HYSYS Workbook是非常方便的调试工具。
你能够迅速地判定哪些模拟变量是用户规定的(蓝色),哪些变量是计算生成的(黑色)。
要记住Workbook要准确描述实际的条件,求解器不能处于HOLD模式。
(完整word版)典型的塔板效率经验数据

典型的塔板效率经验数据
石油化工
塔名称塔板效率(%)
塔名称塔板效率(%)
脱乙烷塔60~65
二甲苯分离塔90~95
高压脱乙烷塔50~60
苯/甲苯/二甲苯分离塔75~85
脱丙烷塔65~75
苯/异丙苯分离塔50~55
脱丁烷塔75~85
吸收塔20~35
脱异丁烷/脱戊烷塔80~90 解吸塔(再沸器供热) 40~50
乙烷/乙烯分离塔85~90 解吸塔(蒸汽汽提) 20~30
丙烷/丙烯分离塔90~95 气体汽提塔7~10
丁烷/丁烯分离塔85~95 干燥塔15
戊烷/戊烯分离塔85~95
化工及其它
塔名称塔板效率(%) 塔名称塔板效率(%)醋酸乙烯装置聚乙烯醇装置
醋酸精馏塔60~70 聚醋酸乙烯分离塔(聚合一塔) 50~60
醋酸乙烯精馏塔55~65 醋酸乙烯/甲醇分离塔(聚合二塔)50~55乙醛汽提塔20~25 醋酸乙烯分离塔(聚合三、四塔) 60~70
丙酮萃取塔15~20 甲醇回收塔(回收一塔) 55~65洗涤塔30~40 甲醇回收塔(回收二、三塔) 50~60。
塔板效率经验计算

典型的塔板效率经验数据石油化工塔名称塔板效率 (%)塔名称塔板效率 (%)脱乙烷塔 60~65二甲苯分离塔 90~95高压脱乙烷塔 50~60苯/甲苯/二甲苯分离塔 75~85脱丙烷塔 65~75苯/异丙苯分离塔 50~55脱丁烷塔 75~85吸收塔 20~35脱异丁烷/脱戊烷塔 80~90 解吸塔(再沸器供热) 40~50乙烷/乙烯分离塔 85~90 解吸塔(蒸汽汽提) 20~30丙烷/丙烯分离塔 90~95 气体汽提塔 7~10丁烷/丁烯分离塔 85~95 干燥塔 15戊烷/戊烯分离塔 85~95化工及其它塔名称塔板效率 (%) 塔名称塔板效率 (%) 醋酸乙烯装置聚乙烯醇装置醋酸精馏塔 60~70 聚醋酸乙烯分离塔(聚合一塔) 50~60醋酸乙烯精馏塔 55~65 醋酸乙烯/甲醇分离塔(聚合二塔) 50~55乙醛汽提塔20~25 醋酸乙烯分离塔(聚合三、四塔) 60~70丙酮萃取塔15~20 甲醇回收塔(回收一塔) 55~65洗涤塔30~40 甲醇回收塔(回收二、三塔) 50~60 在ASPENPLUS模拟软件中,关于塔板效率的问题,模拟软件普遍采用默认值。
一般模拟软件在回归计算时候,在采用简捷计算和精确计算的模式时,塔板效率的预设就不同了,在精确计算模式,一般可以人工修改这个值。
塔板效率属于经验值,这和软件的内部默认还不一样。
例如当建立设计模式精算时,塔板效率是有一个范围的,可是实际中,往往可以突破这个范围。
例如,默认的塔板效率最高可能就是100%,而实际中,特定的塔系确有设计为100%以上的情况,主要是看实际的情况而定。
计算塔板效率可以有公式计算:有公式可算,一般可以使用D_B 法和O‘connel法塔板效率的计算Murphree效率(实验研究用的比较多,设计计算用的比较少)实际塔板上物料进出口浓度差与达到平衡时浓度差之比:全塔效率:在一定回流比和要求之下,所需理论板数与实际板数之比1、Drickaner-Bradford 法E0=0.17-0.616LOG(u)2、O‘connell方法(用的最多)E0= 49{ ua}-0.25u-塔顶底平均温度下进料的黏度a—轻重关键组分的平均相对挥发度3、其他方法AICHE方法(1958)Winckle方法(1963)吸收塔的效率最低,大约只有10-30%;解吸塔和吸收蒸出塔在30-45之间;一般的塔在60—90%之间。
浙大化工原理实验筛板塔精馏操作及效率测定

浙大化工原理实验筛板塔精馏操作及效率测定1. 实验介绍实验室中经常使用精馏技术来分离混合物。
筛板塔是常用的一种精馏设备,本实验旨在通过筛板塔对乙醇-水的混合物进行分离,并测定精馏塔的效率和塔板数。
2. 实验步骤2.1 实验装置实验装置如下图所示:____________________________________| || 冷凝器 ||____________________________________|| || 筛板塔 ||____________________________________|| || 气相色谱 ||____________________________________|| || 蒸发器 ||____________________________________|2.2 实验步骤1.将乙醇-水混合物加入蒸发器中,并加热至混合物开始汽化2.汽化后的混合物进入精馏塔,并接受冷凝器冷却后变为液态乙醇和水3.通过精馏塔塔板的温度变化进行分离,不断取出不同温度下的液态乙醇和水4.使用气相色谱对不同温度下的液态物质进行分析,得到各自的组成5.统计分离过程中每个塔板上的液体量,并计算出塔板的数目和塔的效率3. 实验结果分析实验数据如下表所示:温度(℃) 乙醇(%) 水(%) 塔板液位(L)78 66.22 33.78 0.0482 60.19 39.81 0.1786 51.80 48.20 0.4090 40.70 59.30 0.5394 23.62 76.38 0.4498 8.13 91.87 0.21100 1.20 98.80 0.08根据数据可以得出以下:1.随着温度的升高,乙醇的浓度逐渐降低,水的浓度逐渐升高。
2.精馏塔共分成6个塔板,各个塔板上的液位呈现出为一定的分布规律。
3.精馏塔的效率高,能够较好地将混合物分离,得到较为纯净的物质。
4.本实验通过筛板塔对乙醇-水的混合物进行了精馏分离,并测定了精馏塔的效率和塔板数。
塔板效率计算公式

塔板效率计算公式
塔板效率是用于评估塔板(也称为填料层或浮法层)在萃取塔或分离塔中的性能的指标。
它通常表示为塔板的分离效果或传质效率。
塔板效率的计算公式可以根据具体的塔板设计和操作条件而有所不同。
以下是一种常见的计算公式,称为Murdock公式:
塔板效率 = (实际分离高度 / 理论分离高度) × 100%
其中,
•实际分离高度是指在塔板上发生液相和气相之间传质分离的高度。
•理论分离高度是指理论上需要的高度,以实现完全的液相和气相传质分离。
需要注意的是,塔板效率的计算方法可以因不同的分离塔类型(如萃取塔、蒸馏塔等)以及使用的填料材料和操作参数而有所差异。
因此,在具体的应用中,可能会使用特定的塔板效率计算方法或经验公式来评估实际情况下的分离效果。
化工原理-6.5实际塔板的效率

• 导航栏 • 一、单板数率(冒夫里效率)go • 二、总板效率(全塔效率)go • 三、实际塔板数 go
一、单板数率(冒夫里效率)
• 每块实际塔板,气液接触面积和接触时 间都是有限的,因而离开实际塔板的气 液两相并不能达到平衡。这就是说,一 块实际板起不了一块理论板的作用。
• 气液经过一块理论板的提浓是y*-y,而 经过一块实际板的提浓是y`-y,
n-1
y*
xn-1
n
y
xn*
n+1
x 理论板
n-1
y'
xn-1
x:进入、离开 n板的液相
n
y
xn
y:进入、离开 n板的气相
n+1
x 实际板
• 令 为单板效率,那么
一块实际板的提浓 一块理论板的提浓
y y y*y
yn yn1 yn* yn1
1
(1)
(1)式说明了一块实际板和一块理论板的 区别。
二、总板效率(全塔效率)
• 总板效率是达到同样分离效果所需要的理论板数与 实际板数之比。
N理
N实
(ቤተ መጻሕፍቲ ባይዱ)
总板效率是用于全塔的,也可用于精馏段和提馏 段。但由于影响塔板效率的因素十分复杂,故迄今 为止,还没有得到一个较为满意的求取总板效率的 关系式。比较可靠的数据来自生产及中间试验的直 接经验,即从生产塔或中间试验塔测定的总板效率 用作设计的依据。
互值成得平注衡意的的,是故:塔塔釜釜应的看作上是升一蒸块气1y0w0与%釜的液理浓论度板x。w因是 此,当已知N理(包括釜)求N实时,
要注意:
N实
N理 1
1
(3)
• 总板效率便于工程上计算实际塔板数,但完 全是经验表示法。它将各单板的效率等起来 了,(实际上各板上的流体性质即操作状况各 不相同,∴各板效率也不相同)。因此,总效 率是各单板效率的平均值。
板式塔和填料塔对比

1.1.1.1填料塔与板式塔的比较表8-2 精馏塔的主要类型及特点类型板式塔填料塔结构特点每层板上装配有不同型式的气液接触元件或特殊结构,如筛板、泡罩、浮阀等;塔内设置有多层塔板,进行气液接触塔内设置有多层整砌或乱堆的填料,如拉西环、鲍尔环、鞍型填料等散装填料,格栅、波纹板、脉冲等规整填料;填料为气液接触的基本元件操作特点气液逆流逐级接触微分式接触,可采用逆流操作,也可采用并流操作设备性能空塔速度(亦即生产能力)高,效率高且稳定;压降大,液气比的适应范围大,持液量大,操作弹性小大尺寸空塔气速较大,小尺寸空塔气速较小;低压时分离效率高,高压时分离效率低,传统填料效率较低,新型乱堆及规整填料效率较高;大尺寸压力降小,小尺寸压力降大;要求液相喷淋量较大,持液量小,操作弹性大(续表)制造与维修直径在600mm以下的塔安装困难,安装程序较简单,检修清理容易,金属材料耗量大新型填料制备复杂,造价高,检修清理困难,可采用非金属材料制造,但安装过程较为困难适用场合处理量大,操作弹性大,带有污垢的物料处理强腐蚀性,液气比大,真空操作要求压力降小的物料1.1.1.2板式塔塔型选择一般原则:选择时应考虑的因素有:物料性质、操作条件、塔设备性能及塔的制造、安装、运转、维修等。
1)下列情况优先选用填料塔:a.在分离程度要求高的情况下,因某些新型填料具有很高的传质效率,故可采用新型填料以降低塔的高度;b.对于热敏性物料的蒸馏分离,因新型填料的持液量较小,压降小,故可优先选择真空操作下的填料塔;c.具有腐蚀性的物料,可选用填料塔。
因为填料塔可采用非金属材料,如陶瓷、塑料等;d.容易发泡的物料,宜选用填料塔。
2)下列情况优先选用板式塔:a.塔内液体滞液量较大,操作负荷变化范围较宽,对进料浓度变化要求不敏感,操作易于稳定;b.液相负荷较小;c.含固体颗粒,容易结垢,有结晶的物料,因为板式塔可选用液流通道较大的塔板,堵塞的危险较小;d.在操作过程中伴随有放热或需要加热的物料,需要在塔内设置内部换热组件,如加热盘管,需要多个进料口或多个侧线出料口。
化工原理实验报告四板效率
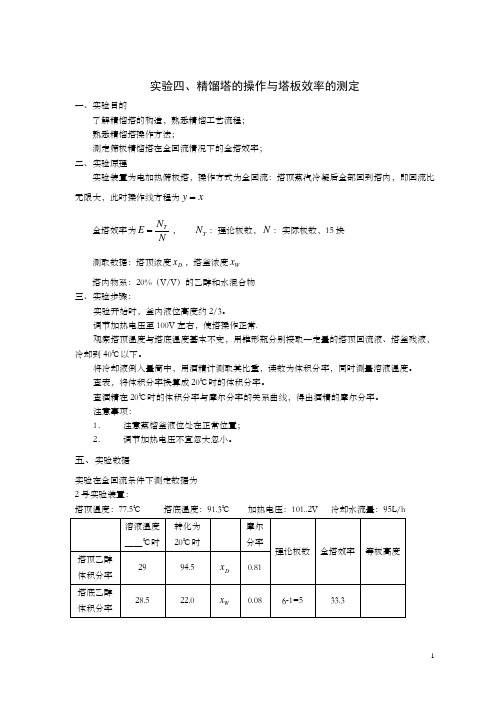
实验四、精馏塔的操作与塔板效率的测定一、实验目的了解精馏塔的构造,熟悉精馏工艺流程;熟悉精馏塔操作方法;测定筛板精馏塔在全回流情况下的全塔效率;二、实验原理实验装置为电加热筛板塔,操作方式为全回流:塔顶蒸汽冷凝后全部回到塔内,即回流比无限大,此时操作线方程为x y = 全塔效率为N N E T=, T N :理论板数,N :实际板数,15块测取数据:塔顶浓度D x ,塔釜浓度W x塔内物系:20%(V/V )的乙醇和水混合物三、实验步骤:实验开始时,釜内液位高度约2/3。
调节加热电压至100V 左右,使塔操作正常.观察塔顶温度与塔底温度基本不变,用锥形瓶分别接取一定量的塔顶回流液、塔釜残液,冷却到40℃以下。
将冷却液倒入量筒中,用酒精计测取其比重,读数为体积分率,同时测量溶液温度。
查表,将体积分率换算成20℃时的体积分率。
查酒精在20℃时的体积分率与摩尔分率的关系曲线,得出酒精的摩尔分率。
注意事项:1.注意蒸馏釜液位处在正常位置; 2. 调节加热电压不宜忽大忽小。
五、实验数据实验在全回流条件下测定数据为2号实验装置:塔顶温度:77.5℃ 塔底温度:91.3℃ 加热电压:101..2V 冷却水流量:95L/h1号实验装置:塔顶温度:77.5℃ 塔底温度:91.8℃ 加热电压:102.4V 冷却水流量:78L/h六、数据处理与讨论根据以上测定数据,用图解法求出2号实验装置全塔的理论板数为6-1=5。
0.00.10.20.30.40.50.60.70.80.9 1.00.00.10.20.30.40.50.60.70.80.91.0y x附图1. 图解法求2号实验装置理论板层数计算全塔效率E=5/15=33.3%1号实验装置全塔的理论板数为12-1=11。
0.00.10.20.30.40.50.60.70.80.9 1.00.00.10.20.30.40.50.60.70.80.91.0y x附图1. 图解法求1号实验装置理论板层数计算全塔效率E=11/15=73.3%讨论:2号实验装置与1号实验装置的全塔效率相差很大,从操作条件看,只有冷却水流量不同,其它基本相同。
实验六 板式精馏塔板效率的测定

4.6板式精馏塔板效率的测定(Ⅰ)全回流精馏塔一﹑实验目的1.了解精馏装置的基本流程及筛板精馏塔的结构,熟悉精馏操作方法;2. 测定全回流条件下总板效率(或单板效率)。
二﹑基本原理精馏塔是分离均相混合物的重要设备。
衡量板式精馏塔分离性能,一般用总板效率表示:pTN N E =(4-31) 式中:E —总板效率;N T —理论板层数; N P —实际板层数。
理论板层数N T 的求法可用M-T 图解法。
本实验是使用乙醇-水二元物系在全回流条件下操作,只需测定塔顶流出液组成x D 和釜液组成x w ,即可用图解法求得N T ,实际板层数N p 为已知,所以利用式(4-30)可求得塔效率E .若相邻两块塔板设有液体取样口,则可通过测定液相组成x n-1和x n 求得第n 块板在全回流下的单板效率E mL 。
*11nn nn mL x x x x E --=-- (4-32)而全回流时,y n =x n-1式中:x n-1—离开上块板的液相中易挥发组分摩尔分率; x n ―离开下块板的液相中易挥发组分摩尔分率;y n ―离开下块板的气相中易挥发组分摩尔分率; x n *―与y n 成平衡的液相组成摩尔分率,以x n-1作为气相组成在平衡线上查得。
三、装置与流程实验装置为一小型筛板塔见图4-13。
原料液在蒸馏釜2中被加热汽化进入塔体4,与回流液在塔板上进行热、质交换后进入塔顶冷凝器5,冷凝为饱和液体后,又全部回流到塔内,由取样口7取样分析馏出液组成,从塔釜取样分析釜液组成。
四、操作步骤1. 熟悉精馏装置的流程和结构,以及所需的控制仪器表盘的布置情况,检查蒸馏釜中料液量是否适当,釜内液面高度控制在液面计的2/3左右。
2. 检查电源并接通电源,加热釜液。
用调压器调节加热功率(电流以3~4A 为宜),注意观察塔顶和塔釜的温度变化,塔顶第一块板上开始有回流时,打开冷却水,冷却水用量以能将蒸汽全凝为宜。
3. 打开塔顶放空阀8排出不凝性气体,塔板上鼓泡正常、温度稳定即表明操作稳定,可开始取样。
筛板塔的操作与塔板效率的测定实验
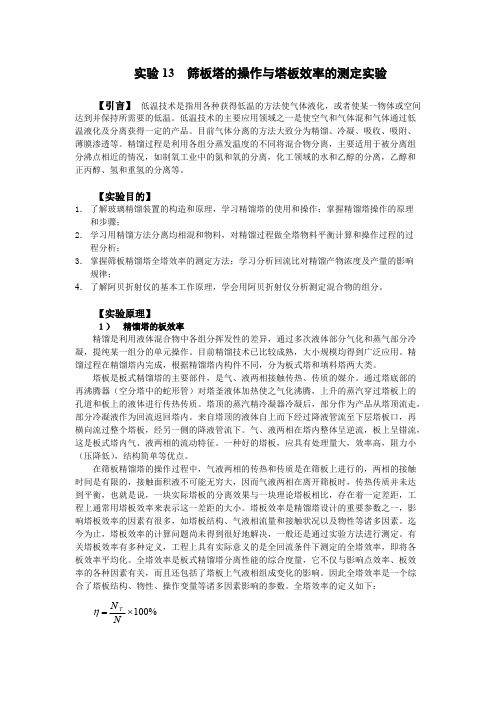
实验13 筛板塔的操作与塔板效率的测定实验【引言】 低温技术是指用各种获得低温的方法使气体液化,或者使某一物体或空间达到并保持所需要的低温。
低温技术的主要应用领域之一是使空气和气体混和气体通过低温液化及分离获得一定的产品。
目前气体分离的方法大致分为精馏、冷凝、吸收、吸附、薄膜渗透等。
精馏过程是利用各组分蒸发温度的不同将混合物分离,主要适用于被分离组分沸点相近的情况,如制氧工业中的氮和氧的分离,化工领域的水和乙醇的分离,乙醇和正丙醇、氢和重氢的分离等。
【实验目的】1.了解玻璃精馏装置的构造和原理,学习精馏塔的使用和操作;掌握精馏塔操作的原理和步骤;2.学习用精馏方法分离均相混和物料,对精馏过程做全塔物料平衡计算和操作过程的过程分析;3.掌握筛板精馏塔全塔效率的测定方法;学习分析回流比对精馏产物浓度及产量的影响规律;4.了解阿贝折射仪的基本工作原理,学会用阿贝折射仪分析测定混合物的组分。
【实验原理】1) 精馏塔的板效率精馏是利用液体混合物中各组分挥发性的差异,通过多次液体部分气化和蒸气部分冷凝,提纯某一组分的单元操作。
目前精馏技术已比较成熟,大小规模均得到广泛应用。
精馏过程在精馏塔内完成,根据精馏塔内构件不同,分为板式塔和填料塔两大类。
塔板是板式精馏塔的主要部件,是气、液两相接触传热、传质的媒介。
通过塔底部的再沸腾器(空分塔中的蛇形管)对塔釜液体加热使之气化沸腾,上升的蒸汽穿过塔板上的孔道和板上的液体进行传热传质。
塔顶的蒸汽精冷凝器冷凝后,部分作为产品从塔顶流走,部分冷凝液作为回流返回塔内。
来自塔顶的液体自上而下经过降液管流至下层塔板口,再横向流过整个塔板,经另一侧的降液管流下。
气、液两相在塔内整体呈逆流,板上呈错流,这是板式塔内气、液两相的流动特征。
一种好的塔板,应具有处理量大,效率高,阻力小(压降低),结构简单等优点。
在筛板精馏塔的操作过程中,气液两相的传热和传质是在筛板上进行的,两相的接触时间是有限的,接触面积液不可能无穷大,因而气液两相在离开筛板时,传热传质并未达到平衡,也就是说,一块实际塔板的分离效果与一块理论塔板相比,存在着一定差距,工程上通常用塔板效率来表示这一差距的大小。
- 1、下载文档前请自行甄别文档内容的完整性,平台不提供额外的编辑、内容补充、找答案等附加服务。
- 2、"仅部分预览"的文档,不可在线预览部分如存在完整性等问题,可反馈申请退款(可完整预览的文档不适用该条件!)。
- 3、如文档侵犯您的权益,请联系客服反馈,我们会尽快为您处理(人工客服工作时间:9:00-18:30)。
典型的塔板效率经验数据
石油化工
塔名称塔板效率 (%)
塔名称塔板效率 (%)
脱乙烷塔 60~65
二甲苯分离塔 90~95
高压脱乙烷塔 50~60
苯/甲苯/二甲苯分离塔 75~85
脱丙烷塔 65~75
苯/异丙苯分离塔 50~55
脱丁烷塔 75~85
吸收塔 20~35
脱异丁烷/脱戊烷塔 80~90 解吸塔(再沸器供热) 40~50
乙烷/乙烯分离塔 85~90 解吸塔(蒸汽汽提) 20~30
丙烷/丙烯分离塔 90~95 气体汽提塔 7~10
丁烷/丁烯分离塔 85~95 干燥塔 15
戊烷/戊烯分离塔 85~95
化工及其它
塔名称塔板效率 (%) 塔名称塔板效率 (%) 醋酸乙烯装置聚乙烯醇装置
醋酸精馏塔 60~70 聚醋酸乙烯分离塔(聚合一塔) 50~60
醋酸乙烯精馏塔 55~65 醋酸乙烯/甲醇分离塔(聚合二塔) 50~55
乙醛汽提塔20~25 醋酸乙烯分离塔(聚合三、四塔) 60~70
丙酮萃取塔15~20 甲醇回收塔(回收一塔) 55~65
洗涤塔30~40 甲醇回收塔(回收二、三塔) 50~60。