LF炉外精炼工艺研究与优化
LF炉外精炼

LF炉外精炼随着现代科学技术的发展和工农业对钢材质量要求的提高,钢厂普遍采用了炉外精炼工艺流程,它已成为现代炼钢工艺中不可缺少的重要环节。
由于这种技术可以提高炼钢设备的生产能力,改善钢材质量,降低能耗,减少耐材、能源和铁合金消耗,因此,炉外精炼技术已成为当今世界钢铁冶金发展的方向。
对于炉外精炼技术存在的问题及发展方向有必要进行探讨。
随着炼钢技术的不断进步,炉外精炼在现代钢铁生产中已经占有重要地位,传统的生产流程(高炉→炼钢炉(电炉或转炉)→铸锭),已逐步被新的流程(高炉→铁水预处理→炼钢炉→炉外精炼→VD→连铸)所代替。
已成为国内外大型钢铁企业生产的主要工艺流程,尤其在特殊钢领域,精炼和连铸技术发展得日趋成熟。
精炼工序在整个流程中起到至关重要的作用,一方面通过这道工序可以提高钢的纯净度、去除有害夹杂、进行微合金化和夹杂物变性处理;另一方面,精炼又是一个缓冲环节,有利于连铸生产均衡地进行。
炉外精炼技术在生产中的应用目前得到公认并被广泛应用的炉外精炼方法有:LF法、RH法、VOD法。
而石钢采用的是LF炉外精炼。
LF是1971年由日本大同钢公司发明的,用电弧加热,包底吹氩搅拌。
一、LF炉的主体设备包括:1、变压器及二次回路;2、电极、电极提升柱及电极臂;3、炉盖及抽气罩;4、吹氩搅拌系统;5、钢包及钢包运输车;6、渣料、合金加入及称量系统。
二、炉外精炼技术的特点与功能炉外精炼是指在钢包中进行冶炼的过程,是将真空处理、吹氩搅拌、加热控温、喂线喷粉、微合金化等技术以不同形式组合起来,出钢前尽量除去氧化渣,在钢包内重新造还原渣,保持包内还原性气氛。
炉外精炼的目的是降低钢中的P、S、O、H、N、等元素在钢中的含量,以免产生偏析、白点、大颗粒夹杂物,降低钢的抗拉强度、韧性、疲劳强度、抗裂性等性能。
这些工作只有在精炼炉上进行,。
LF炉有如下独特的精炼功能:1、埋弧加热。
LF炉有3根石墨电极,加热时电极插入渣层中进行埋弧加热,因而辐射热小,减少对包衬的损坏,可减少电弧的热辐射损失,提高热效率,终点温度的精确度≤±5℃。
LF精炼炉高效加热工艺分析及应用探讨
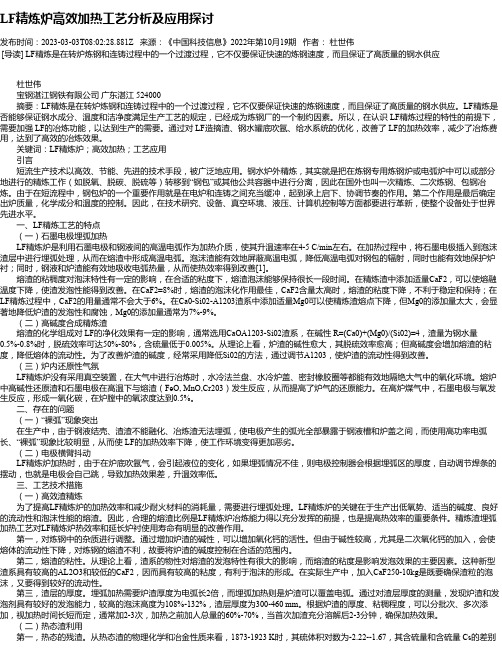
LF精炼炉高效加热工艺分析及应用探讨发布时间:2023-03-03T08:02:28.881Z 来源:《中国科技信息》2022年第10月19期作者:杜世伟[导读] LF精炼是在转炉炼钢和连铸过程中的一个过渡过程,它不仅要保证快速的炼钢速度,而且保证了高质量的钢水供应杜世伟宝钢湛江钢铁有限公司广东湛江 524000摘要:LF精炼是在转炉炼钢和连铸过程中的一个过渡过程,它不仅要保证快速的炼钢速度,而且保证了高质量的钢水供应。
LF精炼是否能够保证钢水成分、温度和洁净度满足生产工艺的规定,已经成为炼钢厂的一个制约因素。
所以,在认识 LF精炼过程的特性的前提下,需要加强 LF的冶炼功能,以达到生产的需要。
通过对 LF造摘渣、钢水罐底吹氩、给水系统的优化,改善了 LF的加热效率,减少了冶炼费用,达到了高效的冶炼效果。
关键词:LF精炼炉;高效加热;工艺应用引言短流生产技术以高效、节能、先进的技术手段,被广泛地应用。
钢水炉外精炼,其实就是把在炼钢专用炼钢炉或电弧炉中可以或部分地进行的精炼工作(如脱氧、脱碳、脱硫等)转移到“钢包”或其他公共容器中进行分离,因此在国外也叫一次精炼、二次炼钢、包钢冶炼。
由于在短流程中,钢包炉的一个重要作用就是在电炉和连铸之间充当缓冲,起到承上启下、协调节奏的作用。
第二个作用是最后确定出炉质量,化学成分和温度的控制。
因此,在技术研究、设备、真空环境、液压、计算机控制等方面都要进行革新,使整个设备处于世界先进水平。
一、LF精炼工艺的特点(一)石墨电极埋弧加热LF精炼炉是利用石墨电极和钢液间的高温电弧作为加热介质,使其升温速率在4-5 C/min左右。
在加热过程中,将石墨电极插入到泡沫渣层中进行埋弧处理,从而在熔渣中形成高温电弧。
泡沫渣能有效地屏蔽高温电弧,降低高温电弧对钢包的辐射,同时也能有效地保护炉衬;同时,钢液和炉渣能有效地吸收电弧热量,从而使热效率得到改善[1]。
熔渣的粘稠度对泡沫特性有一定的影响,在合适的粘度下,熔渣泡沫能够保持很长一段时间。
LF炉精炼研究总结

LF工艺操作LF 是一种拥有电弧加热装置的炉外精炼方法,于1971年由日本特殊钢公司提出,它也被叫做钢包加热炉。
LF主体是一个带有底吹氩的钢包,来自转炉或电炉的钢液(无渣)注入到该钢包内,然后钢包被吊车吊运到钢包车上,运往LF处理工位。
在水冷炉盖下方提供三相电极,盖上水冷炉盖,加入高碱度的复合渣,然后通电,那么常压下即可达到埋弧加热的效果。
由于LF处理方法提供电弧加热、复合渣精炼,吹氩搅拌和合金微调等功能,因此LF精炼可达到以下冶金目的:1)通过还原气氛中高碱度复合渣的精炼,LF有很高的脱硫和脱氧能力,钢液中硫含量和溶解氧可降低到20PPm以下,此外夹杂物也可有效的去除。
2) 钢液电弧加热调整钢液温度,加速复合渣熔化;3) 底吹氩方式达到钢液成分和温度的混匀;4) 依靠自动加料系统对钢液进行成分微调。
加热过程转炉出钢1) 钢包条件钢包应当干净,不附带任何残余炉渣;此外,换包周期不能多于4小时,否则钢包必须烘烤加热到1000-1200℃。
钢包内残余钢液或炉渣会引起钢包温降,失去的热量需LF处理补偿,这些因素在LF电脑模型中都需要考虑进去。
2) 挡渣转炉出钢需要进行挡渣,众所周知转炉顶吹终点,钢液中存在一定含量的溶解氧,它与渣中氧保持平衡。
渣中FeO 和 P2O5含量很高。
当还原剂加入钢包钢液中溶解氧含量降低,钢渣间的氧平衡被打破,渣中 FeO 含量减小。
因为炉渣的氧化性降低,发生回磷现象。
因此为了阻止钢液回磷和保证稳定的LF加热过程,转炉出钢要求挡渣。
3)合金和造渣剂的添加为保证钢液成分,出钢过程中需加入合金和还原剂。
LF加热过程钢包精炼工艺包括几个过程,彼此间相互关联。
对于不同钢种,加热操作不尽相同,且处理过程参数均有相关的标准计算模型。
步骤A:搅拌当钢包抵达LF处理位,接通自动快换接头向钢包提供氩气,根据钢种选择不同的吹氩模式。
a) 吹氩量: 150~300Nl/min步骤B:混匀依据钢种提供不同的混匀方法a) 吹氩量: 300~600Nl/minb) 还原剂:硅铁,铝丸不同混匀模式中,还原剂用量是一定的 (~TS).这个步骤分为两个加热阶段,第一阶段持续1分钟,加热速度越慢越好,温度上升大约3℃/mi n,这是起弧阶段。
LF精炼工艺和效果的研究
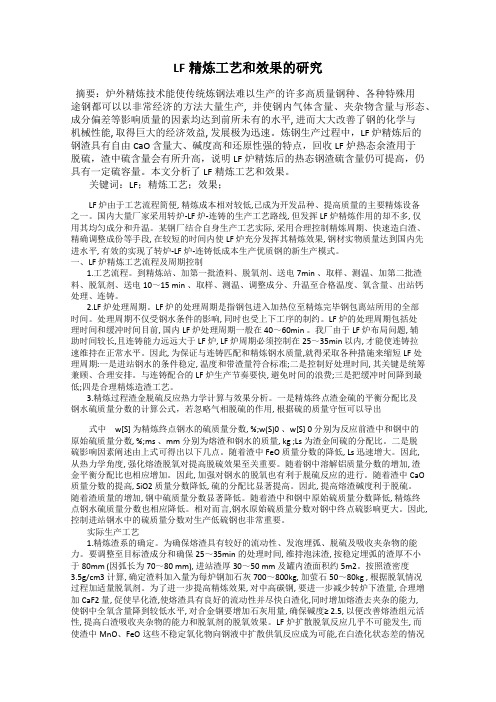
LF精炼工艺和效果的研究摘要:炉外精炼技术能使传统炼钢法难以生产的许多高质量钢种、各种特殊用途钢都可以以非常经济的方法大量生产, 并使钢内气体含量、夹杂物含量与形态、成分偏差等影响质量的因素均达到前所未有的水平, 进而大大改善了钢的化学与机械性能, 取得巨大的经济效益, 发展极为迅速。
炼钢生产过程中,LF 炉精炼后的钢渣具有自由CaO 含量大、碱度高和还原性强的特点,回收LF 炉热态余渣用于脱硫,渣中硫含量会有所升高,说明LF 炉精炼后的热态钢渣硫含量仍可提高,仍具有一定硫容量。
本文分析了LF精炼工艺和效果。
关键词:LF;精炼工艺;效果;LF 炉由于工艺流程简便, 精炼成本相对较低,已成为开发品种、提高质量的主要精炼设备之一。
国内大量厂家采用转炉-LF 炉-连铸的生产工艺路线, 但发挥LF 炉精炼作用的却不多, 仅用其均匀成分和升温。
某钢厂结合自身生产工艺实际, 采用合理控制精炼周期、快速造白渣、精确调整成份等手段, 在较短的时间内使LF 炉充分发挥其精炼效果, 钢材实物质量达到国内先进水平, 有效的实现了转炉-LF 炉-连铸低成本生产优质钢的新生产模式。
一、LF 炉精炼工艺流程及周期控制1.工艺流程。
到精炼站、加第一批渣料、脱氧剂、送电7min 、取样、测温、加第二批渣料、脱氧剂、送电10~15 min 、取样、测温、调整成分、升温至合格温度、氧含量、出站钙处理、连铸。
2.LF 炉处理周期。
LF 炉的处理周期是指钢包进入加热位至精炼完毕钢包离站所用的全部时间。
处理周期不仅受钢水条件的影响, 同时也受上下工序的制约。
LF 炉的处理周期包括处理时间和缓冲时间目前, 国内LF 炉处理周期一般在40~60min 。
我厂由于LF 炉布局问题, 辅助时间较长,且连铸能力远远大于LF 炉, LF 炉周期必须控制在25~35min 以内, 才能使连铸拉速维持在正常水平。
因此, 为保证与连铸匹配和精炼钢水质量,就得采取各种措施来缩短LF处理周期:一是进站钢水的条件稳定, 温度和带渣量符合标准;二是控制好处理时间, 其关键是统筹兼顾、合理安排。
LF精炼炉高效加热工艺分析与应用
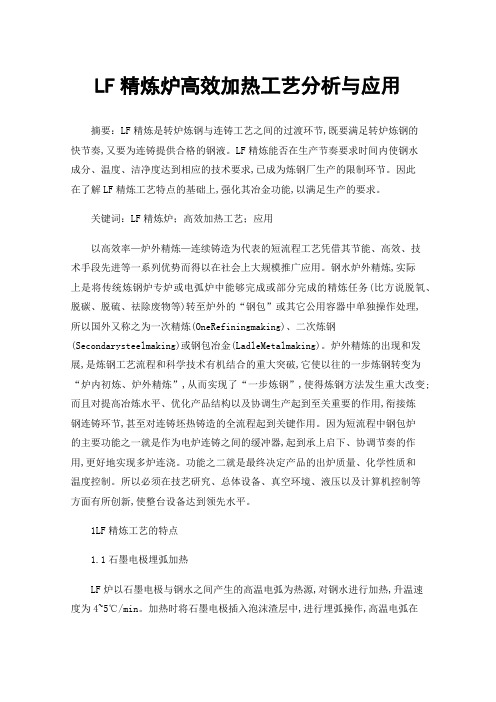
LF精炼炉高效加热工艺分析与应用摘要:LF精炼是转炉炼钢与连铸工艺之间的过渡环节,既要满足转炉炼钢的快节奏,又要为连铸提供合格的钢液。
LF精炼能否在生产节奏要求时间内使钢水成分、温度、洁净度达到相应的技术要求,已成为炼钢厂生产的限制环节。
因此在了解LF精炼工艺特点的基础上,强化其冶金功能,以满足生产的要求。
关键词:LF精炼炉;高效加热工艺;应用以高效率—炉外精炼—连续铸造为代表的短流程工艺凭借其节能、高效、技术手段先进等一系列优势而得以在社会上大规模推广应用。
钢水炉外精炼,实际上是将传统炼钢炉专炉或电弧炉中能够完成或部分完成的精炼任务(比方说脱氧、脱碳、脱硫、祛除废物等)转至炉外的“钢包”或其它公用容器中单独操作处理,所以国外又称之为一次精炼(OneRefiningmaking)、二次炼钢(Secondarysteelmaking)或钢包冶金(LadleMetalmaking)。
炉外精炼的出现和发展,是炼钢工艺流程和科学技术有机结合的重大突破,它使以往的一步炼钢转变为“炉内初炼、炉外精炼”,从而实现了“一步炼钢”,使得炼钢方法发生重大改变;而且对提高冶炼水平、优化产品结构以及协调生产起到至关重要的作用,衔接炼钢连铸环节,甚至对连铸坯热铸造的全流程起到关键作用。
因为短流程中钢包炉的主要功能之一就是作为电炉连铸之间的缓冲器,起到承上启下、协调节奏的作用,更好地实现多炉连浇。
功能之二就是最终决定产品的出炉质量、化学性质和温度控制。
所以必须在技艺研究、总体设备、真空环境、液压以及计算机控制等方面有所创新,使整台设备达到领先水平。
1LF精炼工艺的特点1.1石墨电极埋弧加热LF炉以石墨电极与钢水之间产生的高温电弧为热源,对钢水进行加热,升温速度为4~5℃/min。
加热时将石墨电极插入泡沫渣层中,进行埋弧操作,高温电弧在渣层内产生。
泡沫渣对高温电弧起到屏蔽作用,一方面减少了高温电弧对钢包的热辐射,保护了炉衬;另一方面钢水和炉渣可以有效的吸收电弧热,提高了热效率。
LF炉精炼工艺的探讨
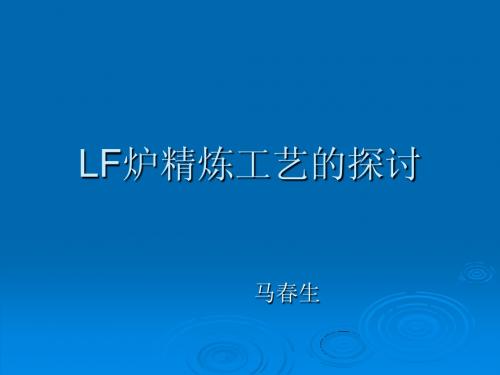
钢包覆盖剂的应用
1、吸附夹杂 2、保温,隔绝空气 3、避免结壳,保持钢包清洁
要求:良好铺展性、保温性、较高熔点
设置挡渣堰坝
改变钢液流动,强制夹杂物上浮
连铸中包渣的应用
中包渣作用: 保温、绝空气、吸附夹杂 半熔融层-10mm
结构:四层结构:
熔融层-5mm
低硅
长效发泡
吸附夹杂
在出钢过程中已经进行了沉淀脱氧,在此主要是 进行扩散脱氧,要求“ 炉渣有良好的还原性能 有良好的发泡性能(埋弧)、节电0.047kwa/t. ℃ 有良好的捕抓、富聚夹杂物的能力,并且有较大 的容量 提高脱氧材料的利用率 对钢包的侵蚀要少
CaF2的应用
。
4Al+3O2→2Al2O3 96 :96 1 :1 3FeO+2Al →Al2O3+3Fe 216:54 4 :1 Fe2O3+2Al=Al2O3+2Fe 160:54 3 : 4 以上计算全部按FeO计算 为考虑SiO2及MnO等与Al的反应及与空氧燃烧,打折扣30%则G=90+22K
CaC2脱氧剂
渣洗
渣洗的目的:降低炉渣氧化性 形成合适的能脱硫能吸收上浮夹杂物的精炼渣 作用:稀释渣中(FeO)量,为LF冶炼创造条件,缩短时间 个别钢中经改质后可不通过LF炉直接送连然(薄板坯) 适合的熔渣组成,以利于保温,隔绝空气和吸附夹杂 便于LF炉起弧,强化钢中进一步脱氧和提高电能利用率 要求:在钢中迅速熔化 表面能力大,能吸附钢中的脱氧产物并使其上浮 12CaO.7Al2O的熔点为1360℃,表面能力系数为8, 并具有一定的脱硫能力,合成渣的基料设想为: 石灰:保证炉渣碱度为3.5-4 萤石:加入6%萤石可适当提高渣流动性 12CaO.7Al2O:在钢中速熔,并能捕捉夹杂物及脱氧产物 脱氧剂(钝化电石):可脱渣中(FeO)并产生气体脱氧产物不污染钢水 CO3发泡,强化搅拌,促进合成渣熔化及夹杂上浮 镁质材料:保证渣中的(MgO)为8%减少渣对钢包的侵蚀
LF精炼炉脱硫工艺制度的研究与优化

LF精炼炉脱硫工艺制度的研究与优化随着科学技术的不断发展,对炼钢生产率、钢的成本、钢的纯净度以及使用性能等方面,都提出了越来越高的要求。
这使传统的炼钢设备和炼钢工艺难以满足需求。
炉外精炼也称二次精炼或钢包冶金,将在常规炼钢炉中完成的精炼任务,部分或全部地移到钢包或其它容器中进行,达到提高钢质量的目的。
LF炉作为炉外精炼设备的一种,具有优异的综合性能,钢液经过LF炉处理可以提高纯净度。
本文在分析研究脱硫的热力学和动力学基础上,结合LF炉的生产实际,对其工艺参数及操作制度进行了研究和优化。
通过控制转炉下渣量、LF炉快速造渣及加快脱硫反应速率等措施,可以实现LF炉生产工序及整个炼钢车间生产工序的高产、优质、低成本。
关键词: LF炉;脱硫;造渣1.1 炉外精炼技术的发展[1]随着现代科学技术的发展和工农业对钢材质量要求的提高,钢厂普遍采用了炉外精炼工艺流程,它已成为现代炼钢工艺中不可缺少的重要环节。
由于这种技术可以提高炼钢设备的生产能力,改善钢材质量,降低能耗,减少耐材、能源和铁合金消耗,因此,炉外精炼技术己成为当今世界钢铁冶金发展的方向,对于炉外精炼技术存在的问题及发展方向有必要进行探讨。
钢中的硫、磷、氢、氧、氮含量大大地影响了钢的性能,如抗拉强度、成型性、可焊性、抗腐蚀性和疲劳性能等。
当钢中硫、磷之和低于0.004%,且氢、氧、氮含量较低时,钢的性能会产生较大的变化,尤其是抗腐蚀性、低温脆性、可焊性和成型性会有几倍甚至几十倍的提高,这比添加合金元素更有效。
为此,作为冶炼高级优质钢的必要手段——炉外精炼,必须有效地脱除杂质元素来提高钢的质量、改善钢的性能。
我国钢铁工业在品种、质量、消耗、成本及劳动生产率等方面与发达国家相比还很落后,主要表现在钢的化学成分波动范围大,硫、磷等有害元素和气体、非金属夹杂物含量相对较高,即钢的纯净度差,从而使钢材的性能不稳定。
随着中国加入世界贸易组织,中国钢材己进入全球化序列。
LF炉精炼工艺优化和设备改造的生产实践

2 L F 炉精炼应用中存在的 问题
在 某炼钢厂应 用L F 炉 之后 ,成 功开发 了多种钢 ,如 高 碳 硬线 钢 、冷 轧 板 、冷 镦钢 等产 品,提 高 了企 业 生产 能
力 ,扩大 了业务类 型 。在炼钢 厂 中某 作业区 中,应 用 了三
座5 0 t 型号的L F 转炉 ,并配有三台连铸机 ,在进行板坯生产
5 9
表1 L F 炉优化 改造前后 的铸坯低倍缺 陷表
炉渣线受 电弧高温影 响,在循环钢 水侵蚀 的作用 下 ,容 易 在包底 中出现穿漏钢 事故 。对钢包 砌筑工 艺进行优化 ,在 进行钢包 砌筑时 ,应 用质量较好 的M g — G 砖 ,提高钢包包底 及渣 线在 精炼过程 中的可靠性 与安全性 。在 该炼钢厂 中 自 优化钢 包砌筑工 艺后 ,大大减 少了穿渣线事 故 ,保证 了精
明显 。
别精炼 的方 式 ,前渣精 炼主要在转 炉 出钢 时处 理,后渣主
要 是在L F 炉 精炼过程 中造渣 。优化后 L F 炉精炼造渣 工艺生 产 流程为 :在 转炉 出钢 的过 程 中,添 加萤石 、石灰 及精炼 渣 等渣 料 ,通过 利用钢水搅 拌作用与 吹氩 搅拌作用 ,能够 完成前 渣精炼 ;在钢水到达氩 站之后 ,考 虑生产钢种 的实
3 . 1 . 1 L F 炉 精炼造 渣工 艺优化 。针对L F 炉在 应用 中 存在 的问题 ,对炼钢 厂造渣工 艺进行综合 分析,研究 出符 合不 同品种钢 的渣 系,从而 改变 了传统 的石 灰加精炼渣 的 生产模式 ,为高附加值 品种钢 的研 发奠定基础 。在 经过L F 炉 精炼造渣 工艺优化之 后,其造渣 工艺形成前渣 与后渣分
2 0 1 3 年第3 5 期
LF精炼炉基本工艺
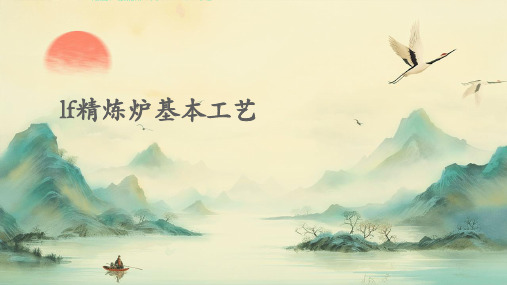
04
lf精炼炉操作要点
安全操作规程
操作前检查
确保炉体、管道、阀门等设备 完好无损,无泄漏现象。
严格控制温度
遵循工艺要求,控制炉内温度 ,避免超温引起设备损坏或安 全事故。
防止气体泄漏
定期检查炉体和管道的密封性 ,确保气体不泄漏,防止中毒 和爆炸。
操作人员培训
操作人员需经过专业培训,熟 悉安全操作规程,掌握应急处
案例二:某有色金属企业lf精炼炉工艺应用
总结词
扩大产品品种、提高生产效率
详细描述
该有色金属企业利用lf精炼炉工艺,成功开发出多种高附加值产品,拓展了市场应用领域。同时,通 过改进工艺参数和设备配置,提高了生产效率和能源利用效率,降低了生产成本。
案例三:某新材料企业lf精炼炉工艺创新
总结词
突破技术瓶颈、提升竞争力
VS
详细描述
该新材料企业针对特定产品需求,创新性 地开发出新型lf精炼炉工艺。通过采用先 进的熔炼技术和材料制备方法,成功突破 了关键材料制备的技术瓶颈,提高了产品 质量和性能,增强了企业在国内外市场的 竞争力。
THANKS
感谢观看
表面处理
对铸锭表面进行清理、修整和抛光等处理,以提高产品的外观质量。
成品检测与包装
检测标准与项目
根据产品标准和客户要求,制定相应的检测标准和项目,对成品 进行全面的质量检测。
检测方法与设备
选择合适的检测方法和设备,确保检测结果的准确性和可靠性。
包装与标识
对合格的成品进行包装和标识,以便于运输、存储和使用。
03
lf精炼炉工艺参数
熔炼温度
熔炼温度
熔炼温度是lf精炼炉工艺中的重要参数,它决定了钢水的温度 和流动性。熔炼温度过高可能导致钢水氧化和氮化,而熔炼 温度过低则可能导致钢水流动性差,影响铸锭质量。
LF炉精炼研究总结
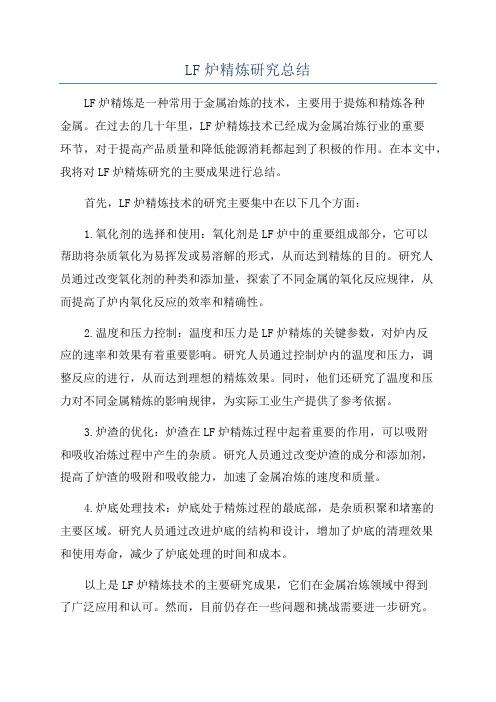
LF炉精炼研究总结LF炉精炼是一种常用于金属冶炼的技术,主要用于提炼和精炼各种金属。
在过去的几十年里,LF炉精炼技术已经成为金属冶炼行业的重要环节,对于提高产品质量和降低能源消耗都起到了积极的作用。
在本文中,我将对LF炉精炼研究的主要成果进行总结。
首先,LF炉精炼技术的研究主要集中在以下几个方面:1.氧化剂的选择和使用:氧化剂是LF炉中的重要组成部分,它可以帮助将杂质氧化为易挥发或易溶解的形式,从而达到精炼的目的。
研究人员通过改变氧化剂的种类和添加量,探索了不同金属的氧化反应规律,从而提高了炉内氧化反应的效率和精确性。
2.温度和压力控制:温度和压力是LF炉精炼的关键参数,对炉内反应的速率和效果有着重要影响。
研究人员通过控制炉内的温度和压力,调整反应的进行,从而达到理想的精炼效果。
同时,他们还研究了温度和压力对不同金属精炼的影响规律,为实际工业生产提供了参考依据。
3.炉渣的优化:炉渣在LF炉精炼过程中起着重要的作用,可以吸附和吸收冶炼过程中产生的杂质。
研究人员通过改变炉渣的成分和添加剂,提高了炉渣的吸附和吸收能力,加速了金属冶炼的速度和质量。
4.炉底处理技术:炉底处于精炼过程的最底部,是杂质积聚和堵塞的主要区域。
研究人员通过改进炉底的结构和设计,增加了炉底的清理效果和使用寿命,减少了炉底处理的时间和成本。
以上是LF炉精炼技术的主要研究成果,它们在金属冶炼领域中得到了广泛应用和认可。
然而,目前仍存在一些问题和挑战需要进一步研究。
首先,LF炉精炼技术的研究主要集中在铁合金的精炼上,而对于其他金属的精炼研究相对较少,需要进一步拓展研究范围。
此外,研究人员还可以探索不同金属之间相互作用的规律,以提高多金属冶炼的效率和产品质量。
其次,LF炉精炼技术在能源消耗方面仍有待改进。
虽然研究人员已经通过优化炉渣和控制温度等手段降低了能源消耗,但仍需要进一步研究如何提高能源利用率,减少炉内能量的浪费。
最后,随着环境保护意识的提高,金属冶炼行业也面临越来越严格的环保要求。
LF炉精炼工艺机理优化与生产实践论文

LF炉精炼工艺机理优化研究与生产实践摘要:本文针对昆钢lf炉精炼工艺投入使用初期,出现精炼过程质量控制不理想、精炼效果不佳,限制着精炼冶金功能的发挥,钢水质量受到较大影响的突出问题,通过对lf炉精炼原理及冶金功能进行研究分析,对昆钢lf炉精炼工艺控制过程进行了优化,达到理顺精炼生产工艺,改善了钢水洁净度的冶金功能,实现品种钢铸坯实物质量改善和经济技术指标的提升。
关键词:lf炉精炼工艺优化研究生产实践随着我国钢铁工业的快速发展,要求钢材产品向品质优越、多功能、高技术含量和高附加值方向发展,传统的炼钢设备和工艺难于满足要求,因而以lf炉为代表的钢水炉外精炼处理技术在钢铁行业迅速发展[1,2],精炼工艺成为优钢冶炼的关键控制过程。
近年来根据市场需求,昆钢为开发生产45~70中高碳硬线、ml35冷镦钢、k510l汽车大梁钢、x46~x65管线钢等附加值较高的钢铁产品(以下简称“品种钢”),相继引入了lf炉精炼设备、工艺,如何发挥lf炉精炼冶金功能,保证品种钢冶炼质量,成为lf炉投入使用后重要的研究课题。
1、现状与问题1.1 现状与问题昆钢在lf精炼炉建成投产后,实现了在炼钢系统转炉冶炼和lf 炉精炼配连铸的工艺流程,为高附加值品种钢研发生产奠定了基础。
但经过对在生产初期在lf炉开发生产的60~70钢、ml35钢铸坯低倍组织抽样检验(见表1所示)与开发生产ml35、60、70、k510l 钢铸坯低倍硫印夹杂物抽样检验情况(见表2所示)综合统计、分析来看,lf精炼炉的冶金功能未得到充分有效的发挥,钢水lf炉精炼效果及各项技术经济指标不理想,直接影响了品种钢铸坯质量,因此,对lf炉精炼开展工艺优化研究,提高铸坯质量成为亟待解决的突出问题。
1.2 lf精炼炉主要技术参数炼钢系统lf精炼炉主要技术参数见表3所示。
2、lf炉精炼原理及冶金功能2.1 精炼原理lf炉具有较好的脱气去夹杂效果,当氩气通过底吹透气砖吹入钢水后,形成很多小气泡,在钢水较大的静压力作用下,气泡在上浮过程中钢水中的气体不断向气泡中扩散,最后排除钢水;此外,气泡在上浮中加速了非金属夹杂颗粒相互碰撞长大的几率,提高了非金属夹杂物的上浮速度。
冶金工业炉外精炼(LF)的应用分析

冶金工业炉外精炼(LF)的应用分析山西通才工贸有限公司山西临汾 043409摘要:钢液精炼是钢铁生产过程中的重要环节,因为它可以降低氧化合金的利用率。
这意味着,通过精炼,可以减少废料的产生,同时提高钢材的质量。
在过去,精炼通常在转炉内进行,但是,这种方法存在一些问题,例如回收率不均衡等。
为了解决这些问题,炉外精炼(LF)技术被广泛采用。
这种技术可以显著改善钢液的纯度,从而提高钢材的质量。
除了提高钢材的质量,炉外精炼(LF)技术还可以减少转炉内渣量到5%,这意味着这种技术可以提高炉渣的浮率。
这对于钢铁生产是非常重要的,因为高浮率可以减少废料的产生。
炉外精炼(LF)技术在保证钢材稳定生产方面起着举足轻重的作用。
这种技术可以确保钢铁生产的过程中不会出现问题,从而保证钢材的质量和数量。
关键词:冶金工业炉;外精炼(LF);应用1冶金工业中炉外精炼(LF)的应用意义炉外精炼技术在冶金行业中的应用越来越广泛,它在钢铁生产过程中扮演着至关重要的角色。
炉外精炼可以改进热力条件,降低气体压力,改善真空现象。
这样,就可以保证炼钢过程中的温度、压力和气氛等因素的稳定性,从而提高冶金反应速度,保证炼钢过程的均匀性。
此外,炉外精炼可以提高渣钢的反应面积,加快反应速度。
在炉外精炼的过程中,通过对渣钢进行预处理和加入适当的精炼剂,可以提高渣钢的反应活性,使其与精炼剂充分混合,从而促进反应的进行,提高反应效率和产量。
炉外精炼装置具有加热功能,可以精确控制反应条件,满足各阶段的供热要求,实现精细的配方调整。
这样,就可以根据不同的生产需求,对炉外精炼装置进行精细的调节和控制,从而实现最佳的生产效果。
总的来说,炉外精炼技术的应用,不仅可以提高钢铁生产的效率和产品质量,而且可以降低能源消耗和环境污染,具有非常重要的经济和社会效益。
因此,在未来的钢铁生产中,炉外精炼技术将会得到更加广泛的应用和推广。
2炉外精炼(LF)简介钢铁生产是工业生产中非常重要的一环。
lf精炼炉炼钢原理与工艺 -回复

lf精炼炉炼钢原理与工艺-回复精炼炉(LF炉)是用来进行钢液净化和精炼的设备。
它能够有效去除钢液中的杂质,调整化学成分,并改善钢的性能与质量。
本文将一步一步解析LF炉的炼钢原理与工艺,以帮助读者深入了解。
一、LF炉的炼钢原理1.1 钢液净化LF炉主要通过炉后吹氩和加入特定化合物,来净化钢液中的杂质。
炉后吹氩能够有效去除钢液中的气体、硫和磷等杂质,同时还能调整温度和各组分的分布。
加入特定化合物,如石灰和石墨等,可以与杂质反应形成不溶性的化合物,从而使杂质从钢液中分离出来。
1.2 炼钢调温LF炉中,钢液的温度可以通过电加热和氩气吹吐等方式进行调节。
通过炼钢调温,可以使钢液温度达到炉内所需的溶解、反应和转化温度。
调温还能保证钢液的流动性,从而有利于杂质的分离和钢液的均匀化。
1.3 炼钢精炼LF炉的炼钢精炼主要通过吹氧和搅拌来实现。
吹氧能够使钢液中的碳和硅等元素氧化,从而减少钢液中的杂质含量。
搅拌则能促进氧含量均匀分布,加快反应速度,同时还能使钢液中的夹杂物向钢液表面浮动,便于排除。
二、LF炉的炼钢工艺2.1 关键工艺参数选择LF炉的炼钢工艺中,选择合适的工艺参数非常重要。
首先是吹氩时间和吹氧时间的控制,这决定了炉内温度和各元素的氧化程度。
其次是石灰和石墨的用量和添加方式,这直接关系到杂质的去除效果。
此外,还要考虑炉内搅拌方式和速度,以保证炼钢过程的均匀性和高效性。
2.2 炉底吹氩和炉后吹氩LF炉的炼钢工艺中,炉底吹氩和炉后吹氩是常用的操作方式。
炉底吹氩可以促进钢液的流动,帮助气泡和杂质向上浮动,从而增强净化效果。
而炉后吹氩则用于调整钢液中氧的含量,防止二次氧化。
2.3 搅拌技术LF炉中的搅拌技术对炼钢效果起着重要作用。
通常采用电磁搅拌或气体搅拌方式。
电磁搅拌通过电磁感应产生涡流,从而使钢液产生强烈的旋涡,促进各组分的混合和反应。
而气体搅拌则利用气体的冲击和搅拌作用来加速气体的溶解和杂质的分离。
2.4 添加剂的使用LF炉的炼钢工艺中,添加剂的选择和使用也是关键步骤。
优化冶炼工艺,降低LF炉电能消耗

优化冶炼工艺,降低LF炉电能消耗李贵平郝忠安守福秦宝生门志刚(宣钢炼钢厂)摘 要宣钢通过优化转炉、LF炉冶炼工艺,缩短了品种钢精炼周期,不仅降低了精炼成本,提高了劳动生产率,降低了能源的消耗,而且实现了节能减排。
关键词 优化工艺电能消耗Optimization of Steelmaking Process to ReduceLF Electric EnergyLi Guiping Hao Zhong An Shoufu Qin Baosheng Men Zhigang(Steel Making Plant of Xuanhua Steel)Abstract This paper introduced the optimization of BOF and LF steelmaking process in Xuanhua Steel, by which the combustion cycle is shortened. It not only reduced production cost, increased the production, reduced the energy resources consumption, but also realized the energy-saving and emission reduction.Key words optimization, process, electric energy consumption1 前言钢铁工业消耗大量的能源、矿产资源并对人类生存环境造成很大的威胁,因此需要大量降低成本,减少电能消耗量和对环境的污染。
在炼钢生产中,LF炉是能源消耗的重要用电单位,而且电能消耗精炼成本中仅次于耐材成本占据第二位。
因此,降低电能消耗对于节约精炼成本、缩短冶炼时间、节能减排具有重要意义。
2 LF炉电能消耗的机理钢包精炼炉利用电弧加热的目的是使钢液快速升温,并熔化少量的合金添加料和渣料。
炉外精炼LF

炼钢工艺过程造渣:调整钢、铁生产中熔渣成分、碱度和粘度及其反应能力的操作。
目的是通过渣——金属反应炼出具有所要求成分和温度的金属。
例如氧气顶吹转炉造渣和吹氧操作是为了生成有足够流动性和碱度的熔渣,以便把硫、磷降到计划钢种的上限以下,并使吹氧时喷溅和溢渣的量减至最小。
出渣:电弧炉炼钢时根据不同冶炼条件和目的在冶炼过程中所采取的放渣或扒渣操作。
如用单渣法冶炼时,氧化末期须扒氧化渣;用双渣法造还原渣时,原来的氧化渣必须彻底放出,以防回磷等。
熔池搅拌:向金属熔池供应能量,使金属液和熔渣产生运动,以改善冶金反应的动力学条件。
熔池搅拌可藉助于气体、机械、电磁感应等方法来实现。
电炉底吹:通过置于炉底的喷嘴将N2、Ar、CO2、CO、CH4、O2等气体根据工艺要求吹入炉内熔池以达到加速熔化,促进冶金反应过程的目的。
采用底吹工艺可缩短冶炼时间,降低电耗,改善脱磷、脱硫操作,提高钢中残锰量,提高金属和合金收得率。
并能使钢水成分、温度更均匀,从而改善钢质量,降低成本,提高生产率。
熔化期:炼钢的熔化期主要是对平炉和电炉炼钢而言。
电弧炉炼钢从通电开始到炉料全部熔清为止、平炉炼钢从兑完铁水到炉料全部化完为止都称熔化期。
熔化期的任务是尽快将炉料熔化及升温,并造好熔化期的炉渣。
氧化期和脱炭期:普通功率电弧炉炼钢的氧化期,通常指炉料溶清、取样分析到扒完氧化渣这一工艺阶段。
也有认为是从吹氧或加矿脱碳开始的。
氧化期的主要任务是氧化钢液中的碳、磷;去除气体及夹杂物;使钢液均匀加热升温。
脱碳是氧化期的一项重要操作工艺。
为了保证钢的纯净度,要求脱碳量大于0.2%左右。
随着炉外精炼技术的发展,电弧炉的氧化精炼大多移到钢包或精炼炉中进行。
精炼期:炼钢过程通过造渣和其他方法把对钢的质量有害的一些元素和化合物,经化学反应选入气相或排、浮入渣中,使之从钢液中排除的工艺操作期。
还原期:普通功率电弧炉炼钢操作中,通常把氧化末期扒渣完毕到出钢这段时间称为还原期。
低碳含铝钢LF炉精炼工艺及精炼渣的优化

低碳含铝钢LF炉精炼工艺及精炼渣的优化摘要:LF炉精炼是目前重庆钢铁公司高级品种钢生产的关键技术之一,目前重钢LF 炉使用的精炼渣配方单一,限制了LF炉在高级品种钢生产中优势作用的充分发挥,不能满足品种钢生产的需要。
近年来许多钢厂采用LF炉生产低碳含铝钢,如08Al、ML08Al钢种,常反映出钢水脱硫效率较低、铸坯夹杂总量较高、脆性夹杂较多、钢水增氮较多等问题,但是,要充分发挥精炼渣的作用,必须针对不同的钢种,合理设计精炼渣成分,并且在精炼渣的加入制度、LF精炼炉操作工艺方面协调配合,才能达到预期效果。
关键词:LF 精炼; 含铝钢; 渣洗工艺随着洁净钢冶炼技术的不断进步和对钢水洁净度要求的不断提高,LF 作为一种典型的二次精炼手段在炼钢工艺中的作用越来越重要。
其主要功能是加热钢水和快速脱S,结合合成渣精炼技术,能够起到对初炼钢水进一步调质的作用。
采用LF 炉生产含铝钢,常反映出钢水脱S 效率较低、钢中脆性夹杂较多、钢水增N 明显、钢水可浇性差等问题,结合承钢提钒炼钢一厂生产实际,提出含铝钢LF 炉精炼工艺优化。
一、含铝钢粗钢水特点08Al 或ML08Al 是最典型的低碳含铝钢,成品钢[C]= 0.06%∼0.08% (质量分数) ,钢中酸溶铝[Al]=0.02%∼0.06%,而16MnR、A36 等钢种,虽然[C]=0.15%∼0.18%,而酸溶铝含量也在上述范围内.这些钢中含有一定量的酸溶铝,主要是为了细化晶粒、提高韧性采用转炉冶炼这些钢种,出钢时的粗钢水具有以下特点:(1) 转炉出钢钢水[C]含量较低,[O]含量较高,常达到500×10−6∼800×10−6.要将钢水氧脱至较低的水平,则需脱除的氧多,生成的脱氧产物量也多.(2) 转炉终渣FeO 高,若下渣量过大则对后续精炼造白渣工艺带来很大的危害.(3) 在允许增碳量很少的限制下,出钢过程或LF 炉内很少采用电石、碳化硅脱氧,主要采用铝锰铁、钢芯铝、铝块等脱氧,部分钢种允许较高硅含量则采用硅铁或硅锰合金脱氧.若脱氧剂配置不当,使脱氧反应生成的脱氧产物为高熔点固相夹杂,未充分上浮排除,则残留在钢水中危害较大。
LF炉精炼造白渣工艺的研究

LF炉精炼造白渣工艺的研究LF炉是钢铁精炼生产过程中非常重要的精炼设备,在钢铁生产过程中所表现出来的脱硫效率较高、钢液成分的控制更加的精确,并且在生产过程中的经济投入量更低,是当前我国钢铁生产企业广泛运用的技术之一。
造白渣工艺是LF 炉精炼过程中非常重要环节,本文就针对该工艺技术进行分析。
标签:LF炉精炼;造白渣工艺;研究分析伴随当前我国工业化的发展速度,不断加快社会经济的发展,对钢铁材料的生产量以及质量的要求不断提升,有效推动了我国钢铁制造技术的高速发展,这对我国炼钢精炼技术层次和整体的炼钢效果和质量提出了较高的要求。
LF炉在整体的投资费用上相对较低,设备构造比较简单,同时在操作过程中比较灵活,所具备的炼钢效果非常优秀,受到了我国社会各大钢铁企业的广泛运用,LF炉的精炼过程主要是通过电极埋弧加热合成渣,使得LF炉内不具备良好的还原环境,通过这种方式实现了对钢铁的脱硫脱氧以及去除内部杂质,提升钢铁纯度和精度的有效目的。
1 精炼渣的主要作用精炼渣再另单独的精炼过程当中,像钢铁内部加入一些特殊性配比成分的合成渣,从晶粒内部的化学成分构造上来分析,其中常见的精炼渣主要是通过CaO-CaF2 基,CaO-Al2O3 基,CaO-Al2O3-SiO2 基等等重点就低碱度较高的熔渣体系。
在合成渣的电弧加热作用下,合成渣通过固态形式慢慢融化成为液态渣,并且和钢液进行有效的混合,在反应过程当中起到了保温绝热以及精炼钢铁的实际效果。
在反应过程当中所表现出来的作用分为以下几个方面,第一,脱硫作用;第二脱氧作用;第三实现高精度的反应环境;第四,高还原性渣料在LF炉内部的吹氩搅拌作用。
通过这种方式可以有效的提升和钢液之间的混合接触面积,进而充分的发挥出其还原性的作用,在很大程度上提升的脱硫和脱氧的效果。
吹氩搅拌的操作过程当中,会使得钢液内部的杂质不断的向上聚集,并且和残渣接触的部分会被慢慢的吸附,有效实现了对钢鐵液体的净化。
宣钢180tLF炉精炼渣的优化

摘要随着冶金技术的不断发展,对炼钢生产率、炼钢成本、钢的纯净度以及使用性能等方面,都提出了越来越高的要求。
这使传统的炼钢设备和炼钢工艺难以满足需求。
LF炉作为炉外精炼设备的一种,具有优异的综合性能,经过LF炉的二次处理,钢的质量可以得到显著提高。
本文以宣钢炼钢厂180t LF炉的精炼渣系为研究对象,以渣系本身性能的优化为内容。
收集了关于180t LF精炼炉的生产现状,尤其是精炼渣系冶金效果的大量数据。
针对生产实际,对其工艺参数进行了研究和优化。
通过生产试验对比表明,经过优化的LF炉精炼渣,其发泡埋弧效果、脱硫能力均优于先用渣系。
关键词:LF 精炼渣脱硫目录摘要 (1)1绪论 (3)1.1 LF炉外精炼技术的发展 (3)1.2 LF精炼炉主要冶金功能 (4)1.3渣系研究现状。
(4)1.3.1精炼渣的发展方向 (5)1.3.2目前 LF炉常用精炼渣系 (5)2 宣钢180t LF炉精炼工艺现状 (6)2.1宣钢180t LF炉设备性能参数 (6)2.2宣钢180t LF炉工艺流程 (6)2.2.1 LF 炉的入炉要求 (7)2.2.2 LF 炉的工艺要点 (7)2.3 LF炉精炼渣的调查与分析 (8)2.4 课题背景及研究内容 (9)3、LF炉精炼渣的优化研究 (9)3.1 精炼炉渣组分的作用 (9)3.2 LF炉精炼渣系的选择 (12)3.3 优化后主要材料及理化指标 (136)5 结论、 (17)参考文献 (17)1绪论1.1 LF炉外精炼技术的发展炉外精炼又称为“二次精炼”,把传统的炼钢流程分为两步:初炼和精炼。
并在真空、惰性气氛或可控气氛下进行脱氧、脱硫、去气去夹杂、成分微调、控制钢水温度等。
炉外精炼的目的是:脱硫、脱碳、脱气、合金化、夹杂物形态控制和去除、均匀钢水成分和温度、钢水升温等。
最初的炉外精炼用于冶炼高品质特殊钢,1933年Perrin用高碱度合成渣进行炉外脱硫,开创了炉外精炼的先河。
LF炉精炼工艺优化

提钒钢轧二 厂 , 河北 承德 0 6 7 0 0 2 )
摘要 : 精 炼 工 序 采 用 铝 脱 氧 易 产 生钢 水 下 流 不 好 现 象 , 影 响生 产顺 行 ; 铝 脱 氧 的精 炼 成 本 较 高 , 精 炼 周 期 较 长 。对 Al s 没 有 要 求 的钢 种 , 在 转 炉 出钢 过 程 中加 小 粒 灰 、 热 态精炼 钢渣再 利用 、 使 用 非 铝 基 脱 氧 剂
0 67 0 02;2. Te c hn i qu e Ce nt e r,Ch e ng de I r o n a n d St e e l Compa n y, He b e i I r on a n d S t e e l Gr ou p, Che ng de, He be i ,06 7 00 2;3. N o. 3 Va na d i um —Ex t r a c t i n g St e e l Rol l i n g Mi l l ,Ch e n gd e I r o n a nd St e e l Co mp a n y,H e — be i I r o n a n d St e e l Gr o up, Che n g de, He be i ,0 67 0 02;4. N o .2 Va n a d i u m — Ex t r a c t i ng St e e l Ro l l i n g Mi l l ,
210吨LF精炼炉高效造渣技术的研究与应用

210吨LF精炼炉高效造渣技术的研究与应用一、LF精炼炉简介LF(Ladle Furnace)精炼炉是一种常见的精炼设备,主要用于对钢液进行中包精炼,以提高钢液质量,消除不良元素和气体,并控制钢液温度,为连铸工序提供符合要求的熔体。
LF精炼炉由炉体、电炉、冶炼炉、过滤器、电器控制系统等部分组成,具有质量好、操作方便、设备简单等特点。
LF精炼炉在现代钢铁生产中扮演着重要的角色,对钢液的质量和性能提升起着至关重要的作用。
二、LF精炼炉造渣技术研究现状造渣技术是LF精炼炉操作中的一项重要工艺。
传统的造渣技术主要采用气吹造渣或者用吹氧进行造渣,这种技术存在造渣时间长、造渣效果差、造渣成本高等问题。
随着钢铁行业的不断发展,LF精炼炉的造渣技术也在不断创新和改进。
目前,一些先进的造渣技术被引入到LF精炼炉中,如高效造渣剂、优化造渣工艺、改进造渣设备等。
三、高效造渣技术的研究1. 高效造渣剂高效造渣剂是LF精炼炉造渣技术的重要组成部分。
高效造渣剂能够快速吸收和分解渣中的不良元素,减少钢水中的夹杂物,提高钢液的质量。
通过合理选择和使用高效造渣剂,可以减少造渣时间,降低造渣成本,提高造渣效果。
2. 优化造渣工艺优化造渣工艺是LF精炼炉造渣技术研究的重要方向之一。
通过对造渣工艺进行优化调整,可以有效提高造渣效果,减少造渣时间,降低造渣成本。
在具体操作中,可以通过调整造渣剂用量、造渣剂种类、造渣工艺参数等手段来实现工艺的优化。
3. 改进造渣设备为了提高LF精炼炉造渣效果,一些钢铁企业进行了造渣设备的改进。
采用新型的造渣设备,提高设备的造渣效率,减少造渣时间,降低造渣成本。
通过改进造渣设备,可以有效提高LF精炼炉的造渣效果,为后续工序提供优质的钢液。
LF精炼炉高效造渣技术的研究和应用已经在一些钢铁企业得到了广泛的应用,取得了显著的经济效益和社会效益。
通过高效造渣技术的应用,可以显著提高钢水的质量和性能,降低生产成本,提高生产效率,提高企业的竞争力,实现经济效益和环保效益的双赢。
- 1、下载文档前请自行甄别文档内容的完整性,平台不提供额外的编辑、内容补充、找答案等附加服务。
- 2、"仅部分预览"的文档,不可在线预览部分如存在完整性等问题,可反馈申请退款(可完整预览的文档不适用该条件!)。
- 3、如文档侵犯您的权益,请联系客服反馈,我们会尽快为您处理(人工客服工作时间:9:00-18:30)。
山西冶金SHANXI METALLURGY总第178期2019年第2期Total 178No.2,2019试(实)验研究DOI:10.16525/l4-1167/tf.2019.02.15LF 炉外精炼工艺研究与优化卢彬I,郑瑾2,陈亮2,席晓利2,徐伟1(1.河钢乐亭钢铁有限公司,河北唐山063000;2.河北钢铁股份有限公司唐山分公司,河北唐山063000)摘 要:针对唐钢一钢轧厂15() tLF 炉外精炼冶炼工艺进行系统性研究并进行优化,通过优化LF 炉外精炼脱氧工艺、推行LF 炉快速冶炼工艺、提升LF 终点成分控制能力、改进创新钙处理工艺等一系列改进关键工艺技术措施的实施与集成,唐钢一钢轧厂LF 炉外精炼工艺得到全面优化与改进,最大程度的发掘了 LF 炉外精炼的潜力,提高了钢水质量,为以后生产高品质钢打下扎实的基础。
关键词:优化工艺能力中图分类号:TF703.5 文献标识码:A 文章编号:1672-1152( 2019 )02-0037-031应用背景钢包炉外精炼炉(LF )是由日本特殊钢铁公司在1971年开发研制的,早先以精炼处理特殊钢为主,是一种以电弧加热、氨气搅拌和渣精炼为核心的钢 包精炼炉生产技术、由于LF 精炼具有多种冶炼功能和使用中的灵活性,在普钢生产厂也得到广泛的应用。
在我国,随着连铸的全面推广,LF 炉外精炼也迅 速地发展起来,LF 所处理的钢种几乎涉及从特殊品种钢到普通钢种的绝大部分钢种。
随着钢铁行业竞争的日益严峻,如何提高冶炼效率,提升钢水纯净 度、降低冶炼成本已成为各钢厂LF 炉外精炼重点发 展及攻关的项目。
2总体思路及技术方案2.1总体思路根据目前一钢轧厂LF 冶炼工艺现状,优化改善LF脱氧工艺.加快造渣速率.提升钢水纯净度降低冶炼成 本;研究推行LF 快速冶炼工艺,减少LF 精炼冶炼 时间,降低精炼过程中的物料及能源消耗;提升LF精炼终点成分控制能力,提高钢种成分命中率,实现各钢种窄成分控制,在保证钢种成分命中的同时最大程 度降低冶炼成本;优化精炼钙处理工艺,提高含钙包 芯线的吸收率,提高钢水改质效果,降低钙处理成本。
2.2技术方案2.2.1 LF 脱氧工艺的改进与创新 2.2.1.1钢渣的氧化性的分析与优化1)降低钢水终点氧含量及转炉下渣量。
中高碳收稿日期:2019-03-07第一作者简介:卢彬(1986—),中级工程师,从事工作:钢铁冶金工艺研究。
钢氧位控制在320x10"左右,低碳钢氧位控制在520x10"左右。
转炉采用挡渣锥进行挡渣出钢,安装转炉下渣检测装置。
确保钢包下渣量不大于80 mm 。
2)优化转炉合金脱氧制度。
根据转炉终点氧值,在出钢1/5或1/4时加入猛铁、铝猛钛或钢砂铝对钢 水进行预脱氧。
在合金加入后,加入石灰顶渣的加入量为2 kg/t ,对钢水进行渣洗,预造渣。
2.2.1.2造渣脱氧物料的研究与优化根据现有冶炼钢种的特点,引进了新型脱氧物 料:铝钙复合脱氧造渣剂。
此脱氧剂中铝呈细小片状分布于脱氧球中,相对接触面积较大,在有效的融入 钢渣迅速对钢渣进行脱氧同时,还能避免因包盖除 尘将铝片吸走所带来的不必要损失,并且通过与CaO 结合,在剧烈铝氧反应的过程中起到加速脱硫的效果。
通过使用铝钙复合脱氧剂对钢渣进行脱氧操作,钢渣中的FeO 、Mn 0含量明显降低,脱氧作用明显。
脱氧物料成本较使用正常料情况下降低0.70 元I 。
2.2.1.3 LF 冶炼过程中钢包底吹氮的优化制定合理的底吹氨制度、精确控制冶炼过程吹 氮流量能有效提高夹杂物上浮速率,提高钢水纯净度,缩短冶炼时间。
基于以上几点,热轧部对底吹氮 设备进行了升级改造,对冶炼过程中不同阶段的氮气流量进行了量化规定:进站钢包接好氮气管后及 时吹氮,站外待冶炼阶段按50-200 Umin 控制.静吹 弱搅拌;过程流量100-300 IVmin,做到钢水不裸露,钢渣面轻微波动;给电升温过程中等强度搅拌过程流量300-600 L/min 控制,保证埋弧效果的同时,均 匀钢水温度;脱氧脱硫强搅拌过程流量按800-山西冶金E mail:sxyjbjb@ 第42卷•38•1000LVmin控制,加快冶炼节奏,提高冶炼效率。
通过LF脱氧工艺优改进与创新,加快了还原渣的成渣速度,提高了精炼渣吸附夹杂的能力,为夹杂物上浮提供充足的时间,有效降低了钢中氧化物夹杂含量,通过对SPHC/SPHD脱氧程度较深的钢种取样分析,出站w(T[0])基本控制在30x10"以下;有效的提高了钢水质量。
通过新型复合脱氧剂的使用,有效地降低了精炼脱氧成本,脱氧物料降低成本0.7元/t。
2.2.2LF快速冶炼工艺的研究与推广随着钢铁市场竞争的日益激烈,钢铁企业进入“微利”时代,在现有设备基础上提高普通钢种冶炼效率对企业发展将起到重要的推动作用,LF炉外精炼作为不可缺少的一个环节,其精炼效率直接影响到整个冶炼效率,为进一步提高精炼冶炼效率,更好地满足下道工序的产能要求,一钢轧厂采取以下措施实现了LF快速冶炼工艺。
2.2.2.1铁水预处理及转炉工艺的优化1)提高入炉铁水脱硫率、扒渣率、严格控制入炉原料质量,降低转炉终点S含量,减轻精炼脱硫压力。
2)优化炉后脱氧造渣制度,将原有顶渣脱氧制度进行优化改进,固化出钢过程合金料、脱氧剂、顶渣的加入顺序,对钢水进行预脱氧、预造渣。
2.2.2.2对LF精炼进站条件的优化提高转炉成分和温度合格率,终点度命中率达到93%以上。
大包成分命中率达到95%以上。
2.2.2.3优化生产组织模式为减少转炉一精炼一连铸钢水运行过程中的温降,要求转炉一精炼蹲钢时间控制在20min以内,精炼一连铸待浇时间控制在15min以内。
减少钢包周转数量,由原来的15个减少至13个,优化了钢包包况。
2.2.2.4热态渣循环利用热态钢渣的循环利用,减少了LF造渣剂的消耗,提高了LF供电初期的稳定性和热效率;有利于提高钢包寿命,降低耐材消耗;提高了金属收得率,目前热态渣回收率已提高至93%以上。
2.2.3LF冶炼工艺的优化2.2.3.1快軽渣工艺对于无浇余或加灰较多炉次,进站加入部分复合脱氧造渣剂(见表1),调整渣中A12O3含量,增加钢渣流动性,增强钢渣夹杂物吸附能力;采用新型铝钙复合脱氧剂对钢渣进行脱氧,加快白渣形成速度;改善熔渣物料结构,以前主要使用萤石对钢渣黏度进行调节,萤石不仅价格较高,且融化过程会造成大量的温度损失,故引进新型熔渣物料:萤石面、熔渣剂,此新型物料价格便宜,CaF含量较高,且呈粉末状分布,减少融化温降的同时能有效加速钢渣粘度的调节。
表1复合脱氧造渣剂理化指标%项目w(A1)w(A12O3)w(CaO)w(SiO2)w(MgO)w(C)灼减指标27-3030〜453~9W5W10W3W52.2.3.2强调一次性喂铝脱氧工艺根据现场情况要求精炼采用一次性喂铝对钢水进行脱氧,二次对钢中铝进行微调的方式,减少精炼铝线喂入次数,要求精炼根据进站Ah含量,一次性喂入铝线,达到钢中w(Al*)M230xl0“,减少或避免二次补铝,加快了精炼脱氧节奏,为夹杂物上浮提供了有利条件,提高了钢水质量。
通过LF快速冶炼的推广,LF冶炼时间大幅降低,在保证钢水质量的同时,精炼最短时间缩短至25min,精炼电耗也显著降低,由原来的28kWh/t降低至26kWh/t;通过一次性喂铝工艺的推广,目前冶炼SPHC-次喂铝率达到40%,二次喂铝以内炉数占总炉数的70%,减少了钙处理前铝线喂入量,加快了精炼脱氧节奏,为夹杂物上浮提供了有利条件,提高了钢水质量;萤石面、熔渣剂使用量站全部调渣物料的65%,并逐步继续提高所占比例,最终替代萤石。
2.2.4终点成分控制能力优化与提升1)控制转炉下渣量,提升转炉大包Al s含硫量。
2)控制热态钢渣回收量,制定相应标准。
3)清理钢包,保证钢包洁净。
4)控制合金物料计入时间,保证脱氧完毕后加入合金物料。
5)引用碳线、硼铁线、钛铁线等包芯线提升控制精度。
LF处理钢水成分合格率达到100%,w(C)、w(Mn)窄成分命中率99%以上。
2.2.5钙处理工艺的优化与创新钙处理就是把钙线通过喂丝机喂入钢水中,利用钢包底吹氮系统,促进钢水的均匀化,可以把脱氧产生的高熔点的脆性A12O3夹杂物变为低熔点的钙铝酸盐夹杂(如12CaO-7Al2O3),有效的促进夹杂物上浮,提高钢水洁净度。
2019年第2期卢 彬,郑 瑾,陈 亮,等:LF 炉外精炼工艺研究与优化• 39 •钙处理对LF 精炼保证可浇性方面起到至关重 要的作用,通过对精炼过程的严格控制基本杜绝了连铸在浇钢过程中的水口堵塞问题,但钙处理成本 较高,为进一步降低成本,我部对钙处理工艺进行了逐步优化,提高了钙线吸收率,降低了钙处理成本。
2.2.5.1钙铝包芯线优化引进新型的复合钙铝包芯线,此种钙线的生产 工艺是用纯钙锭高压热拔抽拉成的纯钙棒,用钢壳 包裹而成,在钢棒表面在包裹一层铝粒,再排线。
复合钙铝比钙铁线优势明显,如喂线时间短,喂线前后温降小,钙在钢水临界深度以下停留时间较长,收得率比不同钙铁线高,喂线量减少50%。
2.2.5.2新型喂丝导管的使用受转炉出钢量、钢包包龄、回浇余量的影响,每 炉钢的净空都有所区别,过大的钢包净空严重影响喂丝导管与钢渣界面的距离。
导管与钢渣界面距离 越大,钙线的喂入深度也就越浅,钢渣界面收钙蒸汽 影响翻腾就越剧烈,钙线的吸收率就越低。
根据实际生产情况设计新型升降式喂丝导管(见图1),可根 据不同的钢水净空进行上下调节,有效弥补了钢包 净空对钙线吸收率产生的影响。
通过以上优化措施,目前平均钙线百米增钙量(质量分数)10.87x10?吸收率22.2%01-1改进前1-2改进后图1升降式隈丝导管3实施效果钢水质量得到明显提升.各钢种命中率达到100%,窄成分命中率达到99%以上,岀站w (T[O])基本控制在(20-30)x10^之间,提高了产品洁净度及 稳定性;冶炼效率显著提高,LF 冶炼时间大幅降低, 精炼最短时间缩短至25 min,已能满足日产1.5万t的生产任务;能源物料消耗成本降低,物料消耗累计 减少1 489.4万元,能源消耗累计降低400万元。
4结语通过优化LF 炉外精炼脱氧工艺、推行LF 炉快速冶炼工艺、提升LF 终点成分控制能力、改进创新 钙处理工艺等一系列改进关键工艺技术措施的实施与集成.热轧部LF 炉外精炼工艺得到全面优化与改进,最大程度的发掘了 LF 炉外精炼的潜力,提高了 钢水质量,为以后生产高品质钢打下有力基础。
(编辑:苗运平)Research and Optimization of LF Out-of-furnace RefiningProcessLu Bin 1, Zheng Jin 2, Chen Liang 2, Xi Xiaoli 2, Xu Wei 1(1. Hegang Leting Iron and Steel Co., Ltd., Tangshan Hebei 063000; 2. Tangshan Branch,Hebei Iron and Steel Co., Ltd., Tangshan Hebei 06300)Abstract : Systematic research and optimization of 150 t LF out-of-furnace refining and smelting process in No.l steelrolling plant of Tangshan Iron and Steel Company were carried out. By optimizing LF out-of-fumace refining and deoxidizing process, implementing LF fast smelting process, enhancing LF end-point composition control capability,and improving innovative calcium treatment process, a series of key technological measures were implemented andintegrated to improve LF out-of-fumace refining process in No.l steel rolling plant of Tangshan Iron and SteelCompany. The potential of LF out-of-fumace refining is explored to the greatest extent by surface optimization andimprovement, and the quality of steel is improved, which lays a solid foundation for the production of high quality steelin the future.Key words : optimizing; process;capability。