车螺纹时常见故障
数控车床螺纹加工常见故障与排除

数控车床螺纹加工常见故障与排除数控车床是一种自动化的机床设备,广泛应用于各个行业,特别是在螺纹加工方面有着重要的作用。
在实际运行中,数控车床在螺纹加工中常常会出现一些故障,这些故障对于生产进程和产品质量都会产生不良影响。
了解这些常见故障,并掌握相应的排除方法,对于提高生产效率和产品质量具有重要意义。
下面将介绍数控车床螺纹加工常见故障以及相应的排除方法。
一、电机故障1. 电机报警螺纹加工过程中,电机可能会报警,导致螺纹加工停止。
这可能是由于电机过载、过热或电流异常等原因引起的。
解决方法是检查电机连接是否松动,调整切削参数,确保电机正常运行。
二、刀具故障1. 刀具损坏螺纹加工中刀具可能会损坏,导致螺纹加工质量下降。
这可能是由于刀具磨损、刀具松动、刀具选择不当等原因引起的。
解决方法是定期更换磨损的刀具,检查刀具连接是否紧固,选择合适的刀具进行螺纹加工。
三、程序故障1. 编程错误螺纹加工中可能会出现编程错误,导致螺纹加工不符合要求。
这可能是由于编程错误、程序跳跃或程序错误设置等原因引起的。
解决方法是仔细检查程序,修正编程错误,并确保程序连续正确运行。
四、液压系统故障1. 液压泵故障螺纹加工中液压泵可能会故障,导致机床无法正常工作。
这可能是由于液压泵损坏、油液污染或管路堵塞等原因引起的。
解决方法是更换损坏的液压泵,定期更换油液,并清理管路。
数控车床螺纹加工常见故障的产生原因多种多样,但大多数故障都可以通过严格控制切削参数、定期检查设备和仔细编程来避免。
及时发现和解决故障也是保证螺纹加工质量和提高生产效率的重要措施。
车削螺纹时常见故障及解决方法

车削螺纹时常见故障及解决方法螺纹车削是机械加工中的一项重要工艺,常用于制作螺栓、螺母等产品。
在车削螺纹过程中,有时会遇到一些常见的故障,如螺纹断裂、螺纹毛刺等问题。
本文将针对这些常见故障,给出相应的解决方法。
一、螺纹断裂螺纹断裂是车削螺纹中最常见的故障之一,主要原因有以下几点:1. 切削量过大。
车削螺纹时,如果一次性切削量过大,容易导致螺纹切削力过大,从而造成螺纹断裂。
2. 车削速度过高。
车削速度过高,会使螺纹材料在车削过程中产生过热现象,从而影响螺纹强度,导致断裂。
3. 切削刃磨损严重。
切削刃磨损严重会导致螺纹车削时切削力不均匀,从而容易引起断裂。
解决方法:1. 合理控制切削量。
在车削螺纹时,应根据工件的材料和尺寸,选择合适的切削量,避免一次性过大的切削力。
2. 控制切削速度。
根据螺纹材料的硬度和热处理情况,选择合适的切削速度,避免过高的车削速度造成螺纹断裂。
3. 及时更换刀具。
定期检查和更换切削刃,保证切削刃的锐利度,避免因刀具磨损产生过大的切削力。
二、螺纹毛刺螺纹毛刺是车削螺纹常见的表面缺陷之一,主要原因有以下几点:1. 加工精度不高。
车削螺纹时,如果刀具偏斜、工件夹紧不稳定等,容易导致精度不高,从而产生毛刺。
2. 切削液不合适。
切削液在车削螺纹时起到冷却、润滑的作用,选用不合适的切削液容易造成毛刺。
3. 刀具磨损严重。
刀具磨损严重会导致切削力不均匀,从而产生毛刺。
解决方法:1. 提高加工精度。
在车削螺纹前,检查刀具和夹持装置,确保工艺参数设置正确,以提高加工精度。
2. 合理选择切削液。
根据螺纹材料的特性和切削条件,选择合适的切削液,保证切削液的冷却和润滑效果,减少毛刺。
3. 及时更换刀具。
定期检查和更换刀具,保证刀具的切削锋利度,减少切削力不均匀引起的毛刺问题。
三、螺纹尺寸不准确螺纹尺寸不准确是车削螺纹常见的质量问题之一,主要原因有以下几点:1. 刀具磨损不均匀。
刀具磨损不均匀会导致切削力不均匀,从而影响螺纹尺寸的精度。
数控车床螺纹加工常见故障与排除

数控车床螺纹加工常见故障与排除【摘要】数控车床在螺纹加工过程中常常会出现一些故障,影响加工质量和效率。
主要包括主轴转速偏低、刀具磨损严重、数控系统程序设置错误、主轴与进给轴卡滞以及刀具安装不稳定等问题。
为了解决这些故障,我们可以采取相应的排除方法,如调整主轴转速、更换磨损严重的刀具、检查数控系统程序设置、清理卡滞部件和重新安装刀具。
通过这些措施,可以有效避免常见故障导致的螺纹加工质量下降和生产中断问题,提高数控车床的工作效率和稳定性。
及时排除数控车床螺纹加工过程中的常见故障,对于保证加工质量和提高生产效率具有重要意义。
【关键词】数控车床、螺纹加工、故障、排除、主轴转速、刀具磨损、数控系统程序、主轴卡滞、刀具安装、震动、排除方法1. 引言1.1 数控车床螺纹加工常见故障与排除数控车床螺纹加工是制造业中常见的加工方法,但在实际操作中常常会出现一些故障导致加工质量下降甚至中断。
了解并排除这些常见故障对于提高加工效率和产品质量至关重要。
1. 主轴转速偏低导致螺纹加工质量差:主轴转速过低会导致切削速度不足,影响螺纹加工的精度和表面质量。
解决方法是检查主轴电机和控制系统,确认转速设置正确。
2. 刀具磨损严重导致螺纹加工不准确:经常更换磨损严重的刀具是预防螺纹加工质量下降的关键措施。
定期检查刀具磨损情况,并根据使用情况及时更换。
3. 数控系统程序设置错误导致螺纹加工失误:正确设置数控系统程序是保证螺纹加工准确性的基础。
仔细检查程序设定参数,确保与加工要求一致。
4. 主轴与进给轴卡滞导致螺纹加工中断:定期清洁和润滑主轴与进给轴是预防卡滞的有效方法,确保机床运行顺畅。
5. 刀具安装不稳定导致螺纹加工震动:正确安装刀具并调整刀具固定方式可以有效减少螺纹加工震动,提高加工精度。
排除数控车床螺纹加工常见故障需要综合考虑机床各部分的工作状态,及时发现并解决问题,才能确保加工质量和效率。
2. 正文2.1 1. 主轴转速偏低导致螺纹加工质量差主轴转速偏低是数控车床螺纹加工常见的故障之一,会直接影响到螺纹加工的质量。
车削螺纹时常见故障及解决方法(二篇)
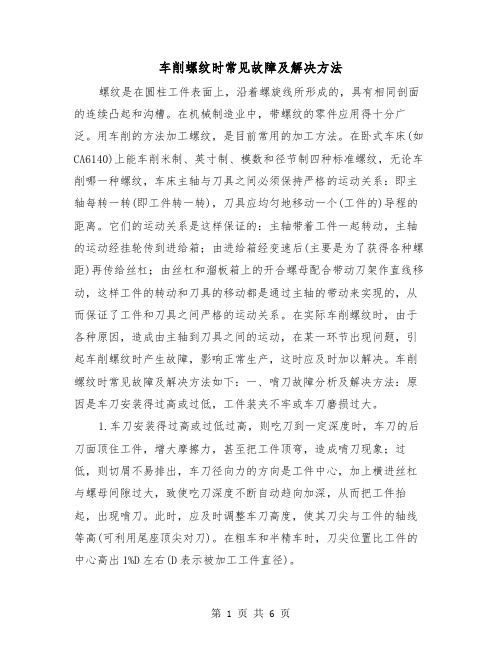
车削螺纹时常见故障及解决方法螺纹是在圆柱工件表面上,沿着螺旋线所形成的,具有相同剖面的连续凸起和沟槽。
在机械制造业中,带螺纹的零件应用得十分广泛。
用车削的方法加工螺纹,是目前常用的加工方法。
在卧式车床(如CA6140)上能车削米制、英寸制、模数和径节制四种标准螺纹,无论车削哪一种螺纹,车床主轴与刀具之间必须保持严格的运动关系:即主轴每转一转(即工件转一转),刀具应均匀地移动一个(工件的)导程的距离。
它们的运动关系是这样保证的:主轴带着工件一起转动,主轴的运动经挂轮传到进给箱;由进给箱经变速后(主要是为了获得各种螺距)再传给丝杠;由丝杠和溜板箱上的开合螺母配合带动刀架作直线移动,这样工件的转动和刀具的移动都是通过主轴的带动来实现的,从而保证了工件和刀具之间严格的运动关系。
在实际车削螺纹时,由于各种原因,造成由主轴到刀具之间的运动,在某一环节出现问题,引起车削螺纹时产生故障,影响正常生产,这时应及时加以解决。
车削螺纹时常见故障及解决方法如下:一、啃刀故障分析及解决方法:原因是车刀安装得过高或过低,工件装夹不牢或车刀磨损过大。
1.车刀安装得过高或过低过高,则吃刀到一定深度时,车刀的后刀面顶住工件,增大摩擦力,甚至把工件顶弯,造成啃刀现象;过低,则切屑不易排出,车刀径向力的方向是工件中心,加上横进丝杠与螺母间隙过大,致使吃刀深度不断自动趋向加深,从而把工件抬起,出现啃刀。
此时,应及时调整车刀高度,使其刀尖与工件的轴线等高(可利用尾座顶尖对刀)。
在粗车和半精车时,刀尖位置比工件的中心高出1%D左右(D表示被加工工件直径)。
2.工件装夹不牢工件本身的刚性不能承受车削时的切削力,因而产生过大的挠度,改变了车刀与工件的中心高度(工件被抬高了),形成切削深度突增,出现啃刀,此时应把工件装夹牢固,可使用尾座顶尖等,以增加工件刚性。
3.车刀磨损过大引起切削力增大,顶弯工件,出现啃刀。
此时应对车刀加以修磨。
二、乱扣故障分析及解决方法:原因是当丝杠转一转时,工件未转过整数转而造成的。
车削螺纹时常见故障及解决方法

车削螺纹时常见故障及解决方法在机械加工中,车削螺纹是一项基本技能。
然而,在操作过程中经常会发生一些故障,例如螺纹深度不够、刀具磨损过快等,这些问题会影响到加工效率和产品质量。
本文将介绍几种常见的车削螺纹故障及其解决方法。
1. 螺纹深度不够螺纹深度不够是一个常见而难以发现的问题,经常在现场加工中出现。
它通常是由于刀具高度不够或车削深度过浅引起的。
以下是解决该问题的方法:•提高刀具高度:可以通过增加支撑刀杆高度或调整刀具上的螺纹垫片来解决。
•增加车削深度:可以通过增加刀具与工件的接触时间或增加刀具超前量来解决。
2. 刀具磨损过快刀具磨损过快通常是由于切削速度太高或切削深度过大引起的。
如果您遇到这种问题,请参考以下建议:•降低切削速度:将切削线速降低到合适的范围内,通常介于5~20 m/min。
•降低切削深度:通过减少车削深度来降低切削负荷。
•更换高质量的刀具:选择具有高刚性和切削耐受性的刀具,可以显著提高刀具的使用寿命。
3. 螺纹折断或错位螺纹折断或错位通常是由于不当的刀具选择、不均匀的切削、机床闲置时间过长和工件内部缺陷引起的。
为了防止发生这种情况,请使用以下技巧:•选择合适的工具:使用专业用于螺纹车削的刀具,确保刀具的角度和尺寸正确。
•均匀切削:确保刀具与工件之间的接触均匀,并避免在工件周边产生太多的压力。
•机床保养:确保机床在加工前和加工后进行适当的保养,防止闲置过长,影响机床的性能。
4. 边角毛刺边角毛刺通常是由于刀尖磨损、粗糙的工件表面和不规则的车刀线轮廓等原因引起的。
如果您的工件出现边角毛刺,可以尝试以下措施:•更换刀具:将刀具钝化或磨损过度的刀具更换为新的刀具。
•改进车床设置:通过改变车床的速度、进给和角度等参数来改善车削表面的粗糙度。
•维护工件表面:对工件表面进行抛光、喷砂或磨削等操作,以改善表面质量。
5. 超出公差范围对于车削螺纹来说,公差范围非常重要。
如果您的工件超出了规定的公差范围,则可能会导致部件的不适合和效率低下。
普通车床螺纹车削常见故障及解决方法(三篇)

普通车床螺纹车削常见故障及解决方法1. 放松刀夹:在车削过程中,如果刀夹没有固定好,会导致刀具松动或者偏位,从而造成螺纹不良。
解决方法是检查刀夹固定螺母是否紧固,如果松动则重新固定。
2. 刀具磨损:长时间使用刀具会磨损,导致刀尖变钝,从而无法进行正常的车削。
解决方法是更换刀具,保持刀具的锐利度。
3. 机床不稳定:如果机床本身存在不稳定的问题,例如床身变形、主轴不平衡等,会导致螺纹加工时产生偏差。
解决方法是定期检测和调整机床,确保其稳定性。
4. 刀具与工件匹配不良:在螺纹车削过程中,刀具与工件的匹配也非常重要。
如果选用的刀具尺寸不合适,就会导致螺纹加工结果不理想。
解决方法是选择合适尺寸的刀具,确保刀具与工件的配合良好。
5. 刀具进给速度不恰当:刀具进给速度过快或者过慢都会影响螺纹加工的质量。
解决方法是根据不同的工件材料和螺纹规格,调整刀具的进给速度,确保加工的质量。
6. 冷却液不适用:在螺纹车削过程中,适当使用冷却液可以降低温度,减少摩擦,提高切削润滑效果,从而改善加工质量。
如果使用的冷却液性质不合适,也会影响螺纹加工结果。
解决方法是选择合适的冷却液,根据加工工件的要求进行选择。
7. 机床刚度不足:机床刚度不足会导致在螺纹车削过程中产生振动和共振,造成螺纹不良。
解决方法是增加机床的刚度,例如加强机床床身的结构,增加加工时的稳定性。
8. 机床零件磨损:长时间使用机床,有些零部件会磨损,例如导轨、导向轨等,会导致加工误差。
解决方法是定期检查和更换机床零部件,保证机床的准确性和稳定性。
总之,普通车床螺纹车削常见故障的解决方法就是:确保刀具的固定和锐利度,稳定机床的结构和性能,选择合适尺寸和质量的刀具,调整进给速度和冷却液的使用,定期检查和维护机床零部件,确保加工质量和效果。
普通车床螺纹车削常见故障及解决方法(二)车床螺纹车削是机械加工中常见的一种加工方式,常用于制作螺纹零件。
然而,在车削过程中,可能会遇到一些常见的故障。
数控车床螺纹加工常见故障与排除

数控车床螺纹加工常见故障与排除
数控车床螺纹加工是一种常见的加工方式,但在实际操作中常常会遇到一些故障。
本文将介绍数控车床螺纹加工常见的故障及其排除方法。
1. 前切刀沿螺纹轴向来回移动导致螺纹不对称。
解决方法:检查前切刀的工作行程,调整其运动参数,使其在加工过程中能够沿螺纹轴向依次前进后退,避免因不对称的运动而导致螺纹加工不均匀。
2. 外径螺纹加工时,切削刃与工件材料磨损严重。
解决方法:检查刀具材料及硬度是否符合加工要求,选择合适的切削刃形状和角度,保持刀具的锋利度,及时更换磨损的刀具。
3. 内径螺纹加工时,工件内孔直径未满足设计要求。
解决方法:检查车床主轴的同心度,修复或更换不满足要求的配件。
要注意切削速度和切削深度的选择,避免加工过程中产生过大的热量。
4. 外径螺纹加工时,表面粗糙度超过允许范围。
解决方法:调整刀具切削速度和进给速度,选择合适的冷却液和润滑剂,以降低切削温度,减少表面粗糙度。
5. 加工过程中,螺纹出现爆裂或开裂。
解决方法:检查工件材料的热处理和质量情况,确保工件内部结构均匀且无气孔、夹杂物等缺陷。
合理选择切削刃形状和角度,避免产生过大的切削力和热量。
解决方法:检查数控车床的精度和稳定性,修复或更换不满足要求的零部件。
调整切削参数,如进给速度、切削速度和刀具角度等,以提高加工精度。
普通车床螺纹车削常见故障及解决方法

普通车床螺纹车削常见故障及解决方法普通车床螺纹车削的常见故障及解决方法非常多,下面将就其中一些常见的故障进行详细介绍:1. 刀具折断:刀具折断是螺纹车削中最常见的故障之一。
主要原因可能是材料刀具的材质不合适、刃口磨损过度、刀具固定不牢等。
解决方法如下:a. 检查刀具的材质是否符合加工材料的要求,选择合适的刀具材质。
b. 定期磨刃,控制刃口磨损程度,确保刀具刃口的锋利度。
c. 确保刀具夹紧牢固,避免刀具松动。
2. 尺寸偏差:尺寸偏差是指车削零件的尺寸与设计要求的尺寸之间的差异。
尺寸偏差可能是由于夹具不稳定、车刀与工件之间的间隙过大、车刀刃口圆周度不好等原因造成。
解决方法如下:a. 检查夹具的夹持是否稳定,并采取稳定的夹持方式。
b. 调整车刀与工件之间的间隙,确保刀具能充分切削工件。
c. 定期磨刃,提高车刀刃口的圆周度。
3. 表面粗糙度不合格:表面粗糙度不合格是指车削零件表面的光洁度不符合设计要求。
造成表面粗糙度不合格的原因主要有切削速度不合理、进给速度不合理、刀具磨损等。
解决方法如下:a. 调整切削速度和进给速度,选择合适的加工参数,提高车削效率和表面质量。
b. 定期更换刀具或磨刃,保持刀具的锋利度。
4. 异常声音:车削过程中出现异常声音通常是由于机床轴承损坏、切削过程中刀具碰撞工件等原因造成的。
解决方法如下:a. 检查机床轴承的使用情况,确保轴承正常工作。
b. 调整切削过程中刀具与工件之间的间隙,避免刀具碰撞工件。
c. 定期对机床进行维护保养。
5. 螺纹无法加工出来:可能的原因包括进给速度过慢、螺纹刀具选择不合适、车削槽设计不合理等。
解决方法如下:a. 调整进给速度,确保切削过程中刀具与工件的相对运动速度达到要求。
b. 选择合适的螺纹刀具,确保刀具能够正确切削螺纹。
c. 对车削槽进行重新设计,确保槽形符合螺纹加工要求。
以上仅是螺纹车削中一些常见的故障及解决方法,实际情况可能因不同的车削工艺和加工材料而有所不同。
数控车床螺纹加工常见故障与排除

数控车床螺纹加工常见故障与排除
数控车床螺纹加工是一种常见的加工操作,但在实际操作中常常会遇到一些故障。
本
文将介绍一些常见的数控车床螺纹加工故障及其排除方法。
首先是切削力过大。
产生这个问题的原因可能是刀具磨损、工件刚度不够或夹具不合理。
解决这个问题的方法是更换刀具、提高工件的刚度或优化夹具结构。
其次是螺纹表面粗糙度过大。
这可能是由于进给速度过快、切削速度不合理或刀具不
锋利造成的。
解决这个问题的方法是调整进给速度和切削速度,并在必要时更换刀具。
另一个常见的问题是螺纹外径变大。
这可能是由于夹紧力不足、通胀量过大或切削力
过大引起的。
解决这个问题的方法是增加夹紧力、控制通胀量或减小切削力。
还有可能遇到工件颤动、螺纹间隙异常、螺纹方向错误等问题。
对于工件颤动问题,
可以通过增加刚性支撑、调整工件夹紧方式或优化切削条件来解决。
对于螺纹间隙异常的
问题,可以检查刀具和夹具的间隙是否合理,以及排除可能的刀具松动等问题。
对于螺纹
方向错误的问题,可以调整进给轴的方向或更换适当的刀具。
数控车床螺纹加工常见故障的排除方法主要是通过调整刀具、夹具和工艺参数来解决。
在实际操作中需要根据具体情况进行分析和判断,不断优化加工过程,确保加工质量和效率。
车削螺纹时常见故障及解决方法

车削螺纹时常见故障及解决方法车削螺纹是机械加工中常用的一种加工方法,用于制作螺纹管、螺纹孔等零件。
然而,在车削螺纹的过程中,常会遇到各种故障,如螺纹形状不符合要求、螺纹表面粗糙等问题。
本文将介绍车削螺纹常见的故障及解决方法。
1. 螺纹形状不符合要求螺纹形状不符合要求是车削螺纹中最常见的问题之一。
原因可能是刀具刃磨不良、刀具进给过快、车床导程不准确等。
解决方法:- 检查刀具刃磨情况,确保刀具的切削刃锋利。
- 调整刀具的进给速度,过快的进给速度会导致螺纹形状不准确。
- 检查车床导程是否准确,必要时进行校准。
2. 螺纹表面粗糙在车削螺纹的过程中,螺纹表面可能会出现粗糙现象,影响螺纹的质量。
解决方法:- 检查车床的切削液供给情况,确保切削液充足,能够起到降温和润滑的作用。
- 调整刀具的进给速度和切削速度,过高的进给速度和切削速度会导致表面粗糙。
- 检查刀具的刃磨情况,确保刀具的刃口尖锐。
3. 刀具刃口出现龟裂刀具刃口出现龟裂是一种常见的故障,会导致螺纹表面的质量下降。
解决方法:- 检查刀具刃口是否过热,过热会导致刃口的变质,进而出现裂纹。
- 调整刀具的进给速度和切削速度,过高的进给速度和切削速度会增加刀具的磨损和热量积聚。
- 使用高质量的刀具,避免刃磨不良或材质不合格的刀具。
4. 螺纹深度不均匀螺纹深度不均匀可能是由于车削过程中切削刃与工件之间的接触不均匀或车床导程不准确导致的。
解决方法:- 检查车床导程是否准确,必要时进行校准。
- 检查刀具刃口的磨损情况,确保切削刃的锋利度和接触面积。
- 调整进给速度和切削速度,使切削刃与工件的接触更加均匀。
5. 刀具与工件之间出现卡紧现象卡紧现象在车削螺纹中比较常见,可能是由于切削刃与工件之间的接触不良或刀具位置不正确导致的。
解决方法:- 检查切削刃与工件的接触情况,确保切削刃能够顺利进入工件。
- 调整刀具的位置,确保切削刃与工件之间的接触面积足够。
总之,在车削螺纹的过程中,经常会遇到各种故障。
数控车床加工双头螺纹时常见故障及解决方法

数控车床加工双头螺纹时常见故障及解决方法螺纹加工是数控车床加工中的重要内容。
但是螺纹加工过程中存在由于操作人员的操作失误导致刀具以及设备受损的问题,使得加工过程中出现很多故障。
本文对利用数控车床加工双头螺纹时的常见问题进行分析,进一步寻找解决的办法,提高数控车床的加工质量。
标签:数控车床;加工螺纹;故障螺纹在机械零件产品上应用极为普遍,螺纹具有连接零件、传动零件、紧固零件的巨大作用。
利用数控车床来加工螺纹是比较常见的螺纹加工方法。
科学技术的发展带动了数控车床技术的不断发展,数控车床在机械加工中起着至关重要的作用,它不仅可以实现精密加工,还能使零件具有同一性,使得零件调试更加便捷高效。
在数控车床上车削螺纹时,常常会因为很多原因使得主轴和刀具之间的正常运动出现问题,进而导致加工零件时出现故障,使得生产不能正常进行。
所以,我们需要对利用车床加工双头螺纹时对常见的问题进行分析。
一、扎刀问题分析在加工零件的过程中,常常因为车刀前角过大导致丝杆间缝隙过大,从而导致产生扎刀问题。
此外,工件装夹不稳定也会产生扎刀。
在长期的加工过程中,经常会出现车刀磨损或者加工时切削用量太大的问题,这些都是车削螺纹时出现故障的原因。
当出现这些问题时,我们需要减效车刀的前角,并通过数控车床的丝杆间隙自动补偿功能补偿机床X轴丝杆间隙。
此外。
还需要对车刀的高度以及工件轴线的高度进行调节。
若是工件装夹不是很稳固,则需要把工件装夹牢固,并同时利用尾座顶尖来增加工件刚性。
当车刀磨损过大而使得切削力增大时,需要及时修磨车刀,达到正常施工的标准。
此外,还需要调整切削用量大小。
二、“乱牙”问题分析“乱牙”问题常常是机床丝杆在转动时工件的转数不是整数而引发的。
数控车床加工时,机床主轴编码器会与主轴同步转动,从而导致同步传动皮带磨损,因此常常会出现仪器检测不到主轴同步真实转速的情况。
此外,编制输入主机的程序错误,X、Y轴丝杆出现磨损也会而引发故障。
在这些问题中,主轴编码器同步皮带磨损,导致主轴同步转速失真,从而产生“乱牙”现象的情况,需要维修机床,尽快更换主轴同步皮带,从而解决故障。
数控车床螺纹加工常见故障与排除

数控车床螺纹加工常见故障与排除数控车床在螺纹加工中常常会出现一些故障,下面我们就来看一下常见的故障及排除方法。
一、螺纹加工中的常见故障1. 刀具辊削振动当车床进行螺纹加工时,如果刀具出现辊削振动,会导致螺纹形貌粗糙,甚至无法加工出标准的螺纹形状。
2. 螺纹尺寸不准确螺纹加工中常见的问题是螺纹尺寸不准确,严重影响产品质量。
3. 切屑的形成和处理问题在螺纹加工中,切屑是一个很重要的问题,如果切屑无法正常排除,就会影响螺纹的加工质量。
4. 主轴转速异常主轴转速异常也会导致螺纹加工出现问题,影响螺纹加工的精度和表面质量。
1. 刀具辊削振动的排除方法(1)检查刀具的刀柄是否正确安装,刀具刀柄是否松动;(2)检查主轴的同心度,如果主轴同心度不好,就会影响刀具的稳定性;(3)检查切削液的供给,切削液是否充足,是否达到了减少切削温度和摩擦的作用。
2. 螺纹尺寸不准确的排除方法(1)检查刀具的选择是否合适,包括切削刀具的规格和尺寸;(2)检查主轴转速是否准确,不能超出刀具允许的转速范围;(3)检查夹持件是否牢固,夹具是否正确,避免松动导致螺纹尺寸不准确。
3. 切屑的形成和处理问题(1)选择合适的切屑分断方式,根据工件的材料和螺纹尺寸选择合适的切削参数;(2)注意切削刀具的选择和调节,保证刀具的刀尖形状和刃角适合螺纹加工;(3)清洁切屑排放口,保证切屑顺利排出,避免切屑对螺纹加工产生影响。
4. 主轴转速异常的排除方法(1)检查主轴的润滑情况,主轴的润滑情况良好才能保证转速的稳定;(2)检查主轴驱动装置,包括主轴电机、变频器等设备的状态;(3)检查主轴的传动链,保证传动链的正常运转,可以避免主轴转速异常。
总结:数控车床在螺纹加工中常常会出现一些故障,但只要我们掌握了以上的排除方法,就能够很好地解决螺纹加工中的常见问题,保证螺纹加工的质量和效率。
车削螺纹时常见故障及解决方法

车削螺纹时常见故障及解决方法车削螺纹是机械加工中常见的工艺,常见的故障有:1. 切削刀具损坏:车削过程中,切削刀具可能会出现磨损或断裂等问题,导致工件螺纹加工不良。
解决方法是定期检查切削刀具的磨损情况,及时更换磨损严重的刀具。
2. 切削速度不合适:切削速度过高或过低都会导致工件螺纹加工不良。
切削速度过高会导致切削刀具产生过多的热量,容易引起刀具变韧性、变硬度,导致加工螺纹时出现切削刀具折断等现象。
切削速度过低则会使切削进给量过大,造成敲击刀具、加工表面粗糙、切削刃磨损等问题。
解决方法是根据工件材料的硬度、切削刀具材料、螺纹尺寸等因素调整切削速度,保证加工过程中切削刀具和工件之间的匹配。
3. 切削进给量不合适:切削进给量过大会导致工件表面粗糙,切削刃损坏等问题;切削进给量过小则会导致加工效率低下。
解决方法是根据工件材料的硬度、切削刀具材料、切削速度等因素合理选择切削进给量,保证加工过程中切削刃的磨损与切削效率之间的平衡。
4. 工件装夹不牢固:工件装夹不牢固会导致工件在车削过程中产生偏移、震动等问题,使螺纹加工不精确。
解决方法是选择适当的装夹工装和夹具,确保工件在车削过程中保持良好的稳定性和牢固性。
5. 机床刚性不足:机床刚性不足会导致工件在车削过程中产生振动,影响加工精度。
解决方法是选择合适的机床,提高机床的刚性,减少振动对螺纹加工的影响。
6. 不合适的切削液:切削液的选择不合适会导致螺纹加工过程中切削刃和工件之间的磨擦增大,容易产生高温区,使切削刀具过早磨损,加工精度下降。
解决方法是选择合适的切削液,并根据实际情况进行润滑和冷却。
7. 加工参数设置不合理:车削螺纹时,加工参数的设置不合理会导致工件螺纹加工不良。
解决方法是根据工件材料、螺纹尺寸、切削刀具等因素选择合适的加工参数,保证加工过程中切削质量和加工效率的平衡。
8. 操作不当:操作人员的经验和技术水平也会影响螺纹加工的质量。
解决方法是提高操作人员的技术水平,加强培训和学习,熟悉设备的使用和加工工艺,注重操作规范,减少人为因素对螺纹加工的影响。
普通车床加工螺纹时常见故障及解决方法

普通车床加工螺纹时常见故障及解决方法利用普通车床在加工螺纹时经常会出现各种故障,为了保证被加工零件的质量,我们必须知道有哪几类常见故障,并能够对常见故障及时采取解决方法,避免材料的浪费,同时提高普通车床的生产率,降低生产成本。
本文主要分析普通车床加工螺纹时常见的故障,并对常见的故障提出相应的解决方法,以此来提高车床的生产率,降低生产成本。
标签:普通车床;加工螺纹;常见故障螺纹是圆柱表面上有规则螺旋状牙形的连续凸起。
螺纹状的零件需求过大,无形中对加工螺纹提出更高的要求,但是普通车床加工螺纹具有不稳定性,经常遇到各种故障。
1.牙型角不正确在普通车床加工螺纹时经常出现牙型角不正确的问题,其主要原因是不正确的刀尖角、未改变径向前角、车刀安装不正确。
当车床的两个切削刀刃在基面上的投影角度与所要加工的螺纹牙型角不一致时,就会出现加工出的螺纹角度不符合要求的问题。
为了解决这种故障,一般采用角度尺或者样板来测量车床的两个切削刀刃的角度,使其与所要加工的螺纹角度一致,从而得出正确的牙型角。
一般螺纹牙型角包括三角形的螺纹牙型角为60°,梯形的螺纹牙型角为30°,蜗杆的牙型角为40°。
在车床上加工螺纹时,如果车刀不能顺利地将车屑排走,会出现积屑瘤现象,因此导致径向前角增大,所加工出来的螺纹牙型角会比车刀的刀刃角大,严重影响了螺纹的质量。
为了避免这种故障的出现,通常通过修正刀刃角,来保证刀刃角与牙型角一致,保证高精度的螺纹。
车刀安装不正确会导致加工出的牙型角倾斜,通常通过角度尺或者样板来测量角度,正确地安装车刀,以避免这种故障的出现。
2.螺距不正确在普通车床上加工螺纹时经常会出现螺纹的全长不正确、螺纹局部不正确等故障。
一般交换齿轮的计算或者组装出现偏差,或者进给箱、溜板箱的手柄位置发生扳错现象,这些都会导致出现螺纹全长不正确的故障,一般通过检查进给箱或溜板箱的手柄位置或者验算挂轮来解决这个问题。
数控车床螺纹加工常见故障与排除

数控车床螺纹加工常见故障与排除一、螺纹加工常见故障1. 螺纹粗糙:在螺纹加工过程中,螺纹表面出现了明显的毛刺和颗粒,影响了螺纹的质量。
2. 螺纹尺寸偏差:螺纹加工后,螺纹的实际尺寸偏离了设计要求,无法满足工件的使用要求。
3. 螺纹轮廓不清晰:螺纹加工后,螺纹的轮廓模糊不清,无法清晰地看到每一个螺纹的线条。
4. 螺纹断裂:螺纹加工时,由于一些原因导致螺纹在加工过程中发生了断裂,影响了工件的加工质量和完整性。
5. 螺纹错位:在螺纹加工过程中,螺纹的位置和角度偏离了设计要求,造成了螺纹错位的情况。
1. 螺纹粗糙排除方法:(1)检查数控车床的刀具质量和刀具安装情况,确保刀具锋利、刀尖角度正确、刀具无损伤。
(2)检查工件材料,如果工件表面有氧化物或划痕,应及时清洁和修磨。
(3)检查数控车床的切削速度和进给速度,根据不同的工件材料和螺纹规格调整合适的加工参数。
2. 螺纹尺寸偏差排除方法:(1)检查数控车床的加工程序、螺纹加工工艺和刀具使用情况,确保符合设计要求。
(2)检查数控车床的定位和夹持装置,保证工件的安装和夹持准确。
(3)对数控车床进行定位修正和参数调整,确保加工尺寸与设计要求一致。
3. 螺纹轮廓不清晰4. 螺纹断裂5. 螺纹错位三、结语螺纹加工是数控车床加工过程中非常重要的工序之一,其加工质量直接关系到工件的使用效果和产品质量。
及时发现并排除螺纹加工的故障对于生产而言是至关重要的。
本文对数控车床螺纹加工常见故障与排除方法进行了分析和总结,希望对相关行业人士有所帮助。
在实际生产中,除了以上列举的故障之外,还会存在其他不同的故障情况,因此需要结合实际情况进行适当的解决方法。
建议操作人员加强数控车床的操作培训,提高技术水平和专业知识,以保证数控车床的正常运行和加工质量。
数控车床螺纹加工常见故障与排除

数控车床螺纹加工常见故障与排除
数控车床是一种高精度的加工设备,广泛应用于各种行业的零部件加工中。
螺纹加工是数控车床的常见加工工艺之一,但在实际操作中,经常会出现各种故障。
本文将结合数控车床螺纹加工的特点,总结常见的故障原因和解决方法,以帮助操作人员更好地应对这些问题。
1. 螺纹加工尺寸不准确
问题原因:螺纹加工尺寸不准确的原因可能有很多,包括设备故障、工件材料问题、刀具磨损等。
解决方法:检查数控车床的设备状态,确保设备正常运转。
然后,检查工件材料,确保其质量符合要求。
检查刀具的磨损情况,确定刀具是否需要更换。
2. 螺纹加工表面粗糙
问题原因:螺纹加工表面粗糙可能是由于刀具磨损、切削参数设置不合理、刀具进给速度过快等原因导致的。
解决方法:检查刀具的磨损情况,确定刀具是否需要更换。
然后,检查切削参数的设置,包括切削速度、进给速度和切削深度等,进行合理调整。
3. 螺纹加工过程产生振动
解决方法:调整切削参数,增加切削速度、减小进给速度,使切削过程更加稳定。
然后,检查工件夹持方式,确保工件夹持牢固,避免产生振动。
5. 螺纹加工过程中出现卡刀
数控车床螺纹加工过程中出现的故障通常都是可以通过合理的调整和维护来解决的。
操作人员在实际操作中要密切关注设备运行状况、刀具磨损情况、工件材料质量等因素,及时发现并解决问题,确保螺纹加工的顺利进行。
普通车床螺纹车削常见故障及解决方法

普通车床螺纹车削常见故障及解决方法螺纹车削是机械加工中非常重要的一项工艺,通常在各种零部件的制造过程中都需要进行螺纹车削。
然而,在螺纹车削过程中,常常会出现一些故障,如刀具磨损、精度偏差、刀具掉刃等。
本文将针对普通车床螺纹车削中的常见故障进行分析,并提供相应的解决方法。
一、刀具磨损刀具磨损是螺纹车削最常见的故障之一,主要表现为刀尖磨损、后角磨损以及侧刃磨损。
刀具磨损会导致工件表面粗糙度增大、尺寸偏差增加等问题。
解决方法:1.定期检查刀具的磨损情况,及时更换磨损严重的刀具。
2.选择合适的刀具材料,提高刀具的耐磨性能。
3.加强刀具的润滑,减少磨损。
4.使用合适的切削参数,减少刀具的磨损。
二、精度偏差精度偏差是指螺纹车削过程中工件的实际尺寸与设计尺寸之间的差异。
精度偏差可能来自于车床本身的误差,也可能是由于操作不当或刀具磨损造成的。
解决方法:1.定期检查车床的准直度,及时调整车床的各个零部件,确保车床的准确度。
2.合理选择刀具,根据工件的要求选择适当的切削速度和进给速度,减小精度偏差。
3.加强操作人员的技术培训,提高操作人员的技能水平。
三、刀具掉刃刀具掉刃是螺纹车削中的一个严重故障,会导致螺纹质量不合格,同时也对安全造成威胁。
解决方法:1.选择优质的刀具,确保刀具的质量。
2.加强刀具的紧固力,定期检查刀具是否松动。
3.根据切削工况合理选择刀具的进给速度和切削深度。
4.在进给过程中避免突然变速,防止刀具发生震动。
5.定期检查刀具的磨损情况,及时更换磨损严重的刀具。
四、切削液问题切削液在螺纹车削过程中起到冷却、润滑、清洁的作用,然而切削液的质量差或使用不当会引起一系列问题,如工件表面粗糙度增大、刀具磨损加快等。
解决方法:1.选择合适的切削液,根据加工材料的不同,选择适当的切削液种类。
2.合理调节切削液的浓度和温度。
3.加强对切削液的管理,定期更换切削液。
4.根据切削工况,调整切削液的喷射方式和位置。
总结起来,普通车床螺纹车削中常见的故障包括刀具磨损、精度偏差、刀具掉刃以及切削液问题。
数控车床螺纹加工常见故障与排除

数控车床螺纹加工常见故障与排除数控车床螺纹加工是数控车床上的一项常见工艺,常用于加工各种螺纹零件和紧固件。
但是在实际生产过程中,经常会出现各种故障,严重影响工件加工质量和生产效率。
本文将结合实际生产经验,介绍数控车床螺纹加工常见故障及其排除方法。
一、螺纹加工误差过大螺纹加工误差过大是数控车床螺纹加工中最常见的问题之一。
主要原因包括以下几个方面:1. 刀具与工件间距不合适。
如果刀具间距太大或太小,都会导致螺纹加工误差过大。
此时应调整刀具与工件的间距,使之保持适当的接触。
2. 刀具磨损严重。
磨损严重的刀具在加工过程中容易发生抖动和偏移,从而导致螺纹加工误差。
此时应及时更换刀具,保持良好的切削状态。
3. 工件表面粗糙度过大。
工件表面粗糙度过大时,将影响切削质量和加工精度,从而导致螺纹加工误差过大。
此时应尽可能提高工件表面粗糙度,以提高加工精度。
1. 加工参数设定错误。
如果加工参数设定不正确,将导致螺纹加工张力过大。
此时应调整加工参数,以保证加工质量和稳定性。
2. 刀具与工件配合不紧密。
如果刀具与工件之间存在间隙或配合不紧密,在加工过程中容易产生振动和偏离,从而导致螺纹加工张力过大。
此时应调整刀具与工件的配合方式,以保证切削稳定性。
3. 刀具刃口质量不良。
如果刀具刃口质量不良,容易导致切削质量下降,从而影响螺纹加工稳定性和张力。
此时应选择质量良好的刀具刃口,并注意刃口磨削和清洁。
三、螺纹加工切削声音异常1. 刀具质量不佳。
如果刀具质量不佳,包括硬度、韧性等方面都不能满足要求,容易导致切削声音异常。
此时应选择更好的刀具,并注意刀具日常维护和保养。
2. 刀具安装不到位。
如果刀具安装不到位,容易产生震动和偏移,从而导致切削声音异常。
此时应检查刀具安装位置,确保刀具安装正确,运转稳定。
3. 工件材质不合适。
如果工件材质不合适,容易产生过度磨损和加工难度大等问题,从而导致切削声音异常。
此时应选择合适的材料,并确保工件之间的接触牢固。
数控车床螺纹加工常见故障与排除
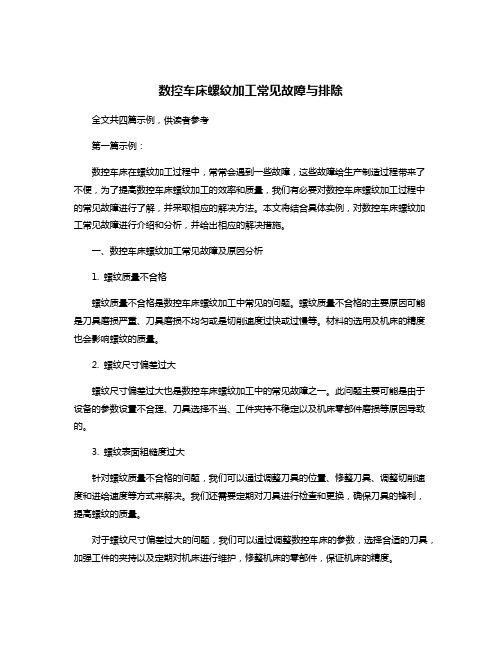
数控车床螺纹加工常见故障与排除全文共四篇示例,供读者参考第一篇示例:数控车床在螺纹加工过程中,常常会遇到一些故障,这些故障给生产制造过程带来了不便,为了提高数控车床螺纹加工的效率和质量,我们有必要对数控车床螺纹加工过程中的常见故障进行了解,并采取相应的解决方法。
本文将结合具体实例,对数控车床螺纹加工常见故障进行介绍和分析,并给出相应的解决措施。
一、数控车床螺纹加工常见故障及原因分析1. 螺纹质量不合格螺纹质量不合格是数控车床螺纹加工中常见的问题。
螺纹质量不合格的主要原因可能是刀具磨损严重、刀具磨损不均匀或是切削速度过快或过慢等。
材料的选用及机床的精度也会影响螺纹的质量。
2. 螺纹尺寸偏差过大螺纹尺寸偏差过大也是数控车床螺纹加工中的常见故障之一。
此问题主要可能是由于设备的参数设置不合理、刀具选择不当、工件夹持不稳定以及机床零部件磨损等原因导致的。
3. 螺纹表面粗糙度过大针对螺纹质量不合格的问题,我们可以通过调整刀具的位置、修整刀具、调整切削速度和进给速度等方式来解决。
我们还需要定期对刀具进行检查和更换,确保刀具的锋利,提高螺纹的质量。
对于螺纹尺寸偏差过大的问题,我们可以通过调整数控车床的参数,选择合适的刀具,加强工件的夹持以及定期对机床进行维护,修整机床的零部件,保证机床的精度。
螺纹表面粗糙度过大的问题,可以通过合理调整切削参数,如切削速度和进给速度,以及定期对刀具进行修整和更换,保证刀具的质量和锋利度。
还可以对工件进行合理夹持,保证工件的稳定性。
第二篇示例:数控车床螺纹加工常见故障与排除随着科技的不断发展,数控车床在工业生产中的应用越来越广泛,尤其在螺纹加工方面,数控车床具有高效、精准的加工特点,得到了广泛的应用。
在实际的生产过程中,由于各种原因,数控车床螺纹加工也会遇到一些常见的故障问题。
本文将针对数控车床螺纹加工常见故障进行介绍,并提供相应的故障排除方法,希望能为相关从业人员提供一些帮助。
1. 螺纹形状不准确螺纹形状不准确是数控车床螺纹加工中常见的故障之一。
- 1、下载文档前请自行甄别文档内容的完整性,平台不提供额外的编辑、内容补充、找答案等附加服务。
- 2、"仅部分预览"的文档,不可在线预览部分如存在完整性等问题,可反馈申请退款(可完整预览的文档不适用该条件!)。
- 3、如文档侵犯您的权益,请联系客服反馈,我们会尽快为您处理(人工客服工作时间:9:00-18:30)。
车削螺纹时常见故障及解决方法
螺纹是在圆柱工件表面上,沿着螺旋线所形成的,具有相同剖面的连续凸起和沟槽。
在机械制造业中,带螺纹的零件应用得十分广泛。
用车削的方法加工螺纹,是目前常用的加工方法。
在卧式车床(如CA6140)上能车削米制、英寸制、模数和径节制四种标准螺纹,无论车削哪一种螺纹,车床主轴与刀具之间必须保持严格的运动关系:即主轴每转一转(即工件转一转),刀具应均匀地移动一个(工件的)导程的距离。
它们的运动关系是这样保证的:主轴带着工件一起转动,主轴的运动经挂轮传到进给箱;由进给箱经变速后(主要是为了获得各种螺距)
再传给丝杠;由丝杠和溜板箱上的开合螺母配合带动刀架作直线移动,这样工件的转动和刀具的移动都是通过主轴的带动来实现的,从而保证了工件和刀具之间严格的运动关系。
在实际车削螺纹时,由于各种原因,造成由主轴到刀具之间的运动,在某一环节出现问题,引起车削螺纹时产生故障,影响正常生产,这时应及时加以解决。
车削螺纹时常见故障及解决方法如下:
一、啃刀
故障分析:原因是车刀安装得过高或过低,工件装夹不牢或车刀磨损过大。
解决方法:
1、车刀安装得过高或过低:过高,则吃刀到一定深度时,车刀的后刀面顶住工件,增大摩擦力,甚至把工件顶弯,造成啃刀现象;过低,则切屑不易排出,车刀径向力的方向是工件中心,加上横进丝杠与螺母间隙过大,致使吃刀深度不断自动趋向加深,从而把工件抬起,出现啃刀。
此时,应及时调整车刀高度,使其刀尖与工件的轴线等高(可利用尾座顶尖对刀)。
在粗车和半精车时,刀尖位置比工件的中心高出1%D左右(D表示被加工工件直径)。
2、工件装夹不牢:工件本身的刚性不能承受车削时的切削力,因而产生过大的挠度,改变了车刀与工件的中心高度(工件被抬高了),形成切削深度突增,出现啃刀,此时应把工件装夹牢固,可使用尾座顶尖等,以增加工件刚性。
3、车刀磨损过大:引起切削力增大,顶弯工件,出现啃刀。
此时应对车刀加以修磨。
二、乱扣
故障分析:原因是当丝杠转一转时,工件未转过整数转而造成的。
解决方法:
1、当车床丝杠螺距与工件螺距比值不成整倍数时:如果在退刀时,采用打开开合螺母,将床鞍摇至起始位置,那么,再次闭合开合螺母时,就会发生车刀刀尖不在前一刀所车出的螺旋槽内,以致出现乱扣。
解决方法是采用正反车法来退刀,即在第一次行程结束时,不提起开合螺母,把刀沿径向退出后,将主轴反转,使车刀沿纵向退回,再进行第二次行程,这样往复过程中,因主轴、丝杠和刀架之间的传动没有分离过,车刀始终在原来的螺旋槽中,就不会出现乱扣。
2、对于车削车床丝杠螺距与工件妇距比值成整倍数的螺纹:工件和丝杠都在旋转,提起开合螺母后,至少要等丝杠转过一转,才能重新合上开合螺母,这样当丝杠转过一转时,工件转了整数倍,车刀就能进入前一刀车出的螺旋槽内,就不会出现乱扣,这样就可以采用打开开合螺母,手动退刀。
这样退刀快,有利于提高生产率和保持丝杠精度,同时丝杠也较安全。
三、螺距不正确
故障分析:螺纹全长或局部上不正确,螺纹全长上螺距不均匀或螺纹上出现竹节纹。
解决方法:
1、螺纹全长上不正确:原因是挂轮搭配不当或进给箱手柄位置不对,可重新检查进给箱手柄位置或验算挂轮。
2、局部不正确:原因是由于车床丝杠本身的螺距局部误差(一般由磨损引起),可更换丝杠或局部修复。
3、螺纹全长上螺距不均匀:原因是:丝杠的轴向窜动、主轴的轴向窜动、溜板箱的开合螺母与丝杠不同轴而造成啮合不良、溜板箱燕尾导轨磨损而造成开合螺母闭合时不稳定、挂轮间隙过大等。
通过检测:如果是丝杠轴向窜动造成的,可对车床丝杠与进给箱连接处的调整圆螺母进行调整,以消除连接处推力球轴承轴向间隙。
如果是主轴轴向窜动引起的,可调整主轴后调整螺母,以消除后推力球轴承的轴向间隙。
如果是溜板箱的开合螺母与丝杠不同轴而造成啮合不良引起的,可修整开合螺母并调整开合螺母间隙。
如果是燕尾导轨磨损,可配制燕尾导轨及镶条,以达到正确的配合要求。
如果是挂轮间隙过大,可采用重新调整挂轮间隙。
4、出现竹节纹:原因是从主轴到丝杠之间的齿轮传动有周期性误差引起的,如挂轮箱内的齿轮,进给箱内齿轮由于本身,制造误差、或局部磨损、或齿轮在轴上安装偏心等造成旋转中心低,从而引起丝杠旋转周期性不均匀,带动刀具移动的周期性不均匀,导致竹节纹的出现,可以修换有误差或磨损的齿轮。
四、中径不正确
故障分析:原因是吃刀太大,刻度盘不准,而又未及时测量所造成。
解决方法:精车时要详细检查刻度盘是否松动,精车余量要适当,车刀刃口要锋利,要及时测量。
五、螺纹表面粗糙
故障分析:原因是车刀刃口磨得不光洁,切削液不适当,切削速度和工件材料不适合以及切削过程产生振动等造成功。
解决方法是:正确修整砂轮或用油石精研刀具;选择适当切削速度和切削液;调整车床床鞍压板及中、小滑板燕尾导轨的镶条等,保证各导轨间隙的准确性,防止切削时产生振动。
总之,车削螺纹时产生的故障形式多种多样,既有设备的原因,也有刀具、操作者等的原因,在排除故障时要具体情况具体分析,通过各种检测和诊断手段,找出具体的影响因素,采取有效的解决方法。