线路板设计规范
PCB印刷电路板设计规范(doc 17页)
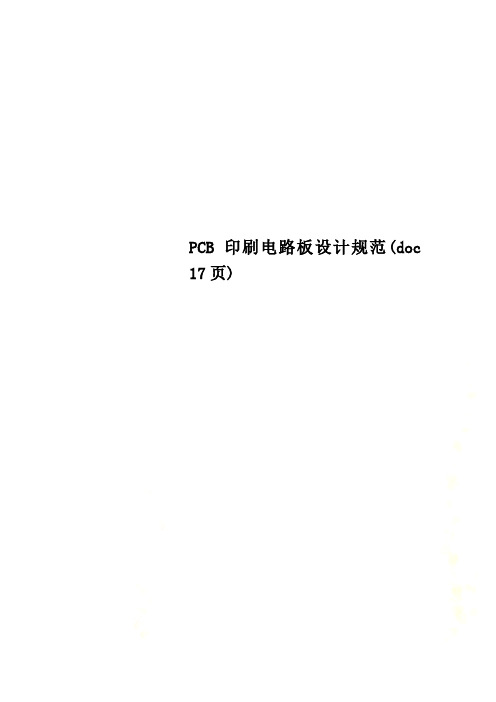
PCB印刷电路板设计规范(doc 17页)印刷电路板(PCB)设计规范1范围本设计规范规定了印制电路板设计中的基本原则、技术要求。
本设计规范适用于电子科技有限公司的电子设备用印刷电路板的设计。
2引用文件下列文件中的条款通过在本规范中的引用成为本规范的条款。
凡是注日期引用的文件,其随后所有的修改单(不包括勘误的内容)或修订版均不适用本规范。
GB 4588.3~88中华人民共和国国家标准:《印刷电路板设计和使用》QJ 3103-99 中国航天工业总公司《印刷电路板设计规范》3定义本标准采用GB2036的术语定义4一般要求关等)这三部分合理地分开,使相互间的信号耦合为最小,元件在印刷线路板上排列的位置要充分考虑抗电磁干扰问题,原则之一是各部件之间的引线要尽量短。
布局应有利于利用自然空气对流方式以散热!5详细要求5.1印制板的选用5.1.1 一般能用单面板就不要用双面板设计。
5.1.2 印板材料常用的有纸板、环氧树脂板、玻璃纤维板及复合材料板等,选用时根据设计的电气特性、机械要求和成本综合考虑,其价格和性能按FR-1、CEM-1、FR-4的顺序依次增加。
5.2印制板的结构尺寸5.2.1形状尺寸印制板的尺寸原则上可以为任意的,但考虑到整机空间的限制、经济上的原因和易于加工、提高生产的效率,在满足空间布局与线路的前提下,力求形状规则简单,最好能做成长宽比例不太悬殊的长方形,最佳长宽比参考为3:2或4:3 。
印制板的两条长边应平行,不平行的要加工艺边,以便于波峰机焊接。
对于板面积较大,容易产生翘曲的印制板,须采用加强筋或边框等措施进行加固,以避免在生产线上生产加工或过波峰时变形,影响合格率。
5.2.2厚度印制板的厚度应根据印制板的功能及所安装的元器件的重量、与之配套的插座的规格、印制板的外形尺寸以及其所承受得机械负荷来选择。
为考虑实用性及经济性,我们应在能满足要求的前提下,尽量选用薄的印制板。
一般而言,带强电的印制板,应选择1.2mm以上的厚度,只有弱电且板型规则面积较小的可选用1mm以下的印制板。
PCB电路设计规范及要求

PCB电路设计规范及要求板的布局要求一、印制线路板上的元器件放置的通常顺序:1、放置与结构有紧密配合的固定位置的元器件,如电源插座、指示灯、开关、连接件之类,这些器件放置好后用软件的LOCK 功能将其锁定,使之以后不会被误移动;2、放置线路上的特殊元件和大的元器件,如发热元件、变压器、IC 等;3、放置小器件。
二、元器件离板边缘的距离:1、画定布线区域距PCB板边≤1mm的区域内,以及安装孔周围1mm内,禁止布线;2、可能的话所有的元器件均放置在离板的边缘3mm以内或至少大于板厚,这是由于在大批量生产的流水线插件和进行波峰焊时,要提供给导轨槽使用,同时也为了防止由于外形加工引起边缘部分的缺损,如果印制线路板上元器件过多,不得已要超出3mm范围时,可以在板的边缘加上3mm的辅边,辅边开V 形槽,在生产时用手掰断即可。
三、高低压之间的隔离:在许多印制线路板上同时有高压电路和低压电路,高压电路部分的元器件与低压部分要分隔开放置,隔离距离与要承受的耐压有关,通常情况下在2000kV时板上要距离2mm,在此之上以比例算还要加大,例如若要承受3000V的耐压测试,则高低压线路之间的距离应在3.5mm以上,许多情况下为避免爬电,还在印制线路板上的高低压之间开槽。
四、元件布局基本规则1. 按电路模块进行布局,实现同一功能的相关电路称为一个模块,电路模块中的元件应采用就近集中原则,同时数字电路和模拟电路分开;2.定位孔、标准孔等非安装孔周围1.27mm 内不得贴装元器件,螺钉等安装孔周围3.5mm(对于M2.5)、4mm(对于M3)内不得贴装元器件;3. 卧装电阻、电感(插件)、电解电容等元件的下方避免布过孔,以免波峰焊后过孔与元件壳体短路;4. 元器件的外侧距板边的距离为5mm;5. 贴装元件焊盘的外侧与相邻插装元件的外侧距离大于2mm;6. 金属壳体元器件和金属件(屏蔽盒等)不能与其它元器件相碰,不能紧贴印制线、焊盘,其间距应大于2mm。
电气工程中的电路板设计规范要求与布局原则

电气工程中的电路板设计规范要求与布局原则电气工程中,电路板设计是至关重要的一环,直接关系到电子设备的性能和稳定性。
良好的电路板设计可以提高信号传输的效率,降低功耗,提升系统的可靠性。
为了满足设计需求,下面将介绍电路板设计的规范要求与布局原则。
一、电路板设计规范要求1. 尺寸和形状:电路板的尺寸和形状应与设备外壳相匹配,确保电路板能够完美安装在设备中。
同时,需要预留足够的空间布局各个元器件和信号走线。
2. PCB层数:根据实际需要,选择适当的PCB层数。
一般情况下,双面布线已经满足大部分应用需求,如果有高密度信号和较复杂布线要求,可以考虑多层布线。
3. 线路宽度和间距:根据电流大小和信号传输速率,合理选择线路宽度和间距。
一般情况下,线路宽度越宽,电阻越小,信号传输越稳定。
而线路间距越大,避免了线间串扰的问题。
4. 禁止过小孔径:过小孔径会导致打孔困难,降低钻孔精度,容易引起掉铜、起焊等问题。
因此,电路板设计中需要遵守合理的孔径规范,以确保制造质量。
5. 接地和屏蔽:合理的接地和屏蔽设计能够有效降低电磁干扰和噪音。
将信号地、电源地和机壳地分离,避免共地和回路间相互干扰。
对敏感信号进行屏蔽处理,提高系统的可靠性。
二、电路板布局原则1. 元器件布局:按照电路流程和信号路径的顺序,合理布置元器件。
将频率较高、噪音敏感的元器件远离信号走线和电源线,减少相互之间的干扰。
同时,遵循最短路径原则,减少信号传输路径的长度,降低传输损耗和延迟。
2. 供电和地引线:合理安排供电和地引线的布局,减少电流的回流路径,降低功耗和电磁干扰。
将供电和地引线尽量贴近元器件,减少回路的面积,提高系统的稳定性。
3. 信号走线:信号走线的布局应遵循最佳布线原则,避免交叉和环行。
对于差分信号,要保持两个信号线的长度一致,减少差异传输引起的相位失真。
对于高速信号,要避免尖角和突变,采取较圆滑的走线方式,减少信号反射和串扰。
4. 散热和散布:合理的散热设计可以提高电子元器件的工作效率和寿命。
PCB电路板PCB设计规范
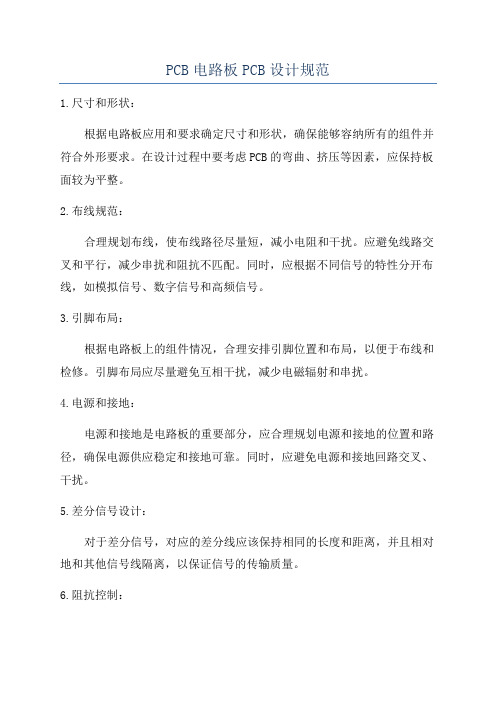
PCB电路板PCB设计规范1.尺寸和形状:根据电路板应用和要求确定尺寸和形状,确保能够容纳所有的组件并符合外形要求。
在设计过程中要考虑PCB的弯曲、挤压等因素,应保持板面较为平整。
2.布线规范:合理规划布线,使布线路径尽量短,减小电阻和干扰。
应避免线路交叉和平行,减少串扰和阻抗不匹配。
同时,应根据不同信号的特性分开布线,如模拟信号、数字信号和高频信号。
3.引脚布局:根据电路板上的组件情况,合理安排引脚位置和布局,以便于布线和检修。
引脚布局应尽量避免互相干扰,减少电磁辐射和串扰。
4.电源和接地:电源和接地是电路板的重要部分,应合理规划电源和接地的位置和路径,确保电源供应稳定和接地可靠。
同时,应避免电源和接地回路交叉、干扰。
5.差分信号设计:对于差分信号,对应的差分线应该保持相同的长度和距离,并且相对地和其他信号线隔离,以保证信号的传输质量。
6.阻抗控制:对于高频信号和差分信号,需要控制PCB的阻抗以保证信号的传输质量。
通过合理布线、选用合适的线宽和间距等方式来控制阻抗。
7.信号层分布:不同信号应分配在不同的信号层上,以减少串扰和互相影响。
如分离模拟信号和数字信号的层,使其相互独立。
8.过孔和焊盘:过孔和焊盘是PCB上的重要部分,需要合理设计和布局,以便于焊接和连接。
过孔应根据设计要求确定尺寸和孔径,焊盘应采用适当的尺寸和形状。
9.元件布局:在布局元件时,应合理安排元件的位置和间距,以便于布线和散热。
同时,要注意元件的方向和引脚位置,以方便组装和检修。
10.标记和说明:在PCB上标注元件的名称、值和引脚功能,以便于使用和维护。
同时,在PCB设计文件中提供详细的说明和注释,方便其他人理解和修改。
总之,PCB设计规范是确保PCB电路板设计的合理性、可靠性和可制造性的重要标准和方法。
通过遵循相关规范,可以有效提高电路板的性能和可靠性,减少故障和制造成本。
PCB可制造性设计规范

PCB可制造性设计规范PCB (Printed Circuit Board)的制造性设计规范是指在设计和布局PCB电路板时所需考虑的一系列规范和标准,以确保电路板的制造过程顺利进行并获得可靠性和性能。
一、尺寸规范1.PCB电路板的尺寸要符合制造商的要求,包括最小尺寸、最大尺寸和板上零部件之间的间距。
2.确保电路板的边缘清晰、平整,并防止零部件或钳具与电路板边缘重叠。
二、层规范1.根据设计要求确定所需的层次和层的数量,确保原理图和布局文件的一致性。
2.定义PCB的地平面层、电源层、信号层和垫层、焊盘层等的位置和规格。
三、元件布局规范1. 合理布局元件,以最小化路径长度和EMI (Electromagnetic Interference),提高电路的可靠性和性能。
2.避免元件之间的相互干扰和干涉,确保元件之间有足够的间距,以便于焊接工序和维修。
四、接线规范1.线路走向应简洁、直接,避免交叉和环形走线。
2.确保信号和电源线路之间的隔离,并使用正确的引脚布局和接线技术。
五、电路可靠性规范1.选择适当的层次和厚度,以确保足够强度和刚度。
2.确保电路板表面和感应部件光滑,以防止划伤和损坏。
六、焊接规范1.在设计中使用标准的焊盘尺寸和间距,以方便后续的手工或自动焊接。
2.制定适当的焊盘和焊缺陷防范措施,以最小化焊接问题的发生。
七、标准规范1. 遵循IPC (Institute for Interconnecting and Packaging Electronic Circuits)标准,以确保PCB的制造符合国际标准。
2.正确标注和命名电路板上的元件和信号,以方便生产和测试。
八、生产文件和图纸规范1.提供准确和详细的生产文件和图纸,包括层叠图、金属化孔、引线表和拼图图等。
2.确保文件和图纸的易读性和可修改性。
九、封装规范1.选择适当的封装类型和尺寸,以满足电路板的要求。
2.避免使用不常见或过于复杂的封装,以确保可靠的元件焊接和连接。
PCB线路板设计规范

PCB线路板设计规范PCB线路板设计规范是为了确保电路板的性能、可靠性和可制造性而制定的一系列规则和要求。
遵循这些规范可以提高电路板的质量,减少故障率,优化设计和制造过程,使电路板能够更好地满足设计要求。
以下是PCB线路板设计规范的一些主要方面:1.外形尺寸和形状:电路板的外形尺寸和形状应符合设计要求,并适合安装在相应的应用设备中。
在设计过程中应注意尺寸的准确性和稳定性,避免设计过大或过小的尺寸。
2.电路板层布局:电路板的层布局应根据电路设计要求来确定。
在布局过程中,应将元件、信号线和电源线等布置在合适的层中,以避免互相干扰。
同时,还应根据电路的复杂程度和频率要求来确定电路板的层数。
3.电路布线规则:电路板的布线应遵循一定的规则,如信号线与电源线的间距、信号线的阻抗控制等。
布线规则的遵循可以减少信号串扰和噪音干扰,提高信号质量和抗干扰能力。
4.元件布置规则:电路板上各个元件的布置应符合一定的规则,如元件之间的间距、元件与边界的距离等。
元件布置规则的遵循可以方便焊接和维修,避免元件之间的相互干扰和短路等问题。
5.焊盘和焊接规则:电路板上焊接点的设计应符合一定的规则,如焊盘大小、已焊盘的间距等。
焊盘的设计合理与否直接影响到焊接质量和可靠性。
同时,还应注意焊接工艺的要求,如正确选择焊接材料、焊接温度和焊接时间等。
6.电源布局和分离规则:电路板上各个电源的布局应合理,避免互相干扰。
同时,还应根据电路的功耗和电流要求来确定电源的容量和类型,保证供电的稳定性和可靠性。
7.防护和绝缘规则:电路板的防护和绝缘要求是确保电路板安全运行的关键。
设计时应注意电路板的防尘、防潮、防静电等问题,并采取必要的安全措施,如绝缘层的加工、防火阻燃材料的选择等。
8.环境适应性和可靠性要求:电路板的环境适应性和可靠性要求是根据实际应用环境和可靠性要求来制定的。
设计时应考虑电路板的工作温度范围、振动和冲击等因素,并采取必要的措施,如选择适应性材料和加强电路板的结构,以提高电路板的可靠性。
线路板设计规范
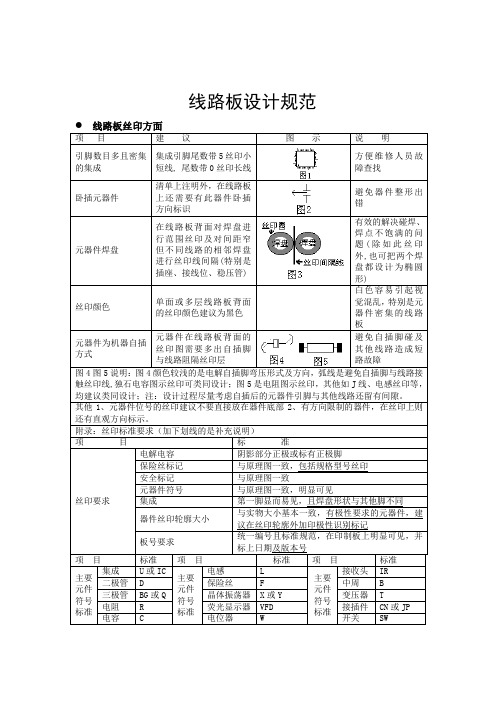
线路板设计规范●线路板合拼板原则1、拼板尽量以机型为单位,一套单面板拼成一大板,一套多层板也拼成一大板。
2、线路板四周(一般考虑波峰链爪夹持的两边即可)设计宽度为3mm的工艺夹持边,在工艺夹持边内不应有任何焊盘和器件,如若确实因板面尺寸受限制,不能满足以上要求,或采用的是组装方式,可采取四周加边框的制作方法,留出工艺夹持边,待焊接完成后,手工掰除边框。
合拼板要求不影响器件安装,拆板时不易拆断铜箔走线,合拼板尺寸最小不小于150Ⅹ80mm,最大不大于330Ⅹ250mm,根据自插机台的现状,合拼板最大的长度可适当放宽,不局限在330mm,但一旦合拼板过长,直接将导致线路板波峰变形;3、合拼后的线路板边缘有缺口,且需首先送入机插轨道,需要增加附加板,避免线路板送入轨道时卡断,附加板与线路板缺口边衔接方式用邮票孔。
●线路板定位孔考虑印板工艺边3mm和工艺孔8mm范围内区禁止排放器件(补焊件除外),印板工艺孔如下图要求所示。
注:AB两个孔孔径为Φ4,单位为mm。
●线路板焊盘及波峰考虑1、多层线路板安装孔建议只在正面加焊盘,不需要使用金属化孔,可避免波峰后安装孔锡封,单面板和多层板的安装孔焊盘形状建议为右图样式;2、在线路板增加波峰方向的箭头丝印,波峰方向与焊盘开槽方向的关系如图6。
同一板上或同一并板上的焊盘开槽方向要保持一致。
3、开槽焊盘有:接线位、荧光屏管脚、安装孔及一些因拼板后空间限制或凸出线路板边缘的器件;4、正面贴片元件引脚焊盘可以短一些;相反,背面焊盘长度可以适当长一些,或使用半圆型焊盘,以改善焊接质量;5、避免大面积连体裸露铜箔线路存在,如确需可用绿油进行间隔,避免拉尖焊点出现;6、加ICT(在线测试)点:各单面板、多层板,原则上在每一线路上都要加单独的测试点测试点焊盘>1.0mm,两测试点中心距>2.5mm。
7、另外为了提高补焊工作效率,建议在插座、接线位外增加一个吃锡焊盘,如下图8、贴片集成厚度较薄的,引脚向内弯曲的,尽量设计在线路板正面(仅限多层线路板),如设计在背面,波峰后引脚碰焊严重,不好补焊,且在插件过程,部分贴片集成会脱离胶点与线路板;同样,贴片排阻尽量不设计在线路板背面,以免虚焊或脱落。
某公司PCB设计规范样本

某公司PCB设计规范样本1. 引言PCB(Printed Circuit Board,印刷电路板)是现代电子设备中常见的一种重要组成部分,它承载着电子元器件,并提供了电子元器件之间的电气连接。
为了保证PCB的质量和可靠性,某公司制定了一套严格的PCB设计规范样本,本文将介绍该规范样本的具体内容和要求。
2. PCB设计规范2.1 PCB尺寸和层数根据不同的应用需求,PCB的尺寸和层数会有所不同。
在某公司的设计规范样本中,PCB的尺寸通常不超过20cm×20cm,并且层数不超过4层。
若需要超出这个范围,需要额外申请和审批。
2.2 PCB布局和布线2.2.1 元器件布局•元器件应按照电路图要求合理布局,尽量缩短信号传输路径,降低信号干扰。
•元器件之间应保留足够的间距,以便于安装和维修。
•高功率元器件和高频元器件应与敏感元器件保持一定的间距,防止互相干扰。
2.2.2 信号和电源平面•PCB上应划分信号和电源平面,以降低信号串扰和提供稳定的电源供应。
•信号和电源平面之间应保持一定的距离,以减少互相干扰。
2.2.3 信号走线•信号走线应尽量保持短、直、对称。
•临近平面的信号线应与平面保持一定距离,以减少互电容和互感。
•若有高速信号或高频信号,应采取差分走线或者层间引线走线方式,以减少信号衰减和串扰。
2.3 焊盘和焊接2.3.1 焊盘设计•焊盘的大小应根据元器件引脚的尺寸和数量合理确定,避免太小或太大。
•焊盘的形状应选择圆形或方形,避免使用带尖角的形状。
2.3.2 焊盘与元器件引脚的间距•焊盘与元器件引脚之间应保留一定的间距,避免短路或接触不良。
2.3.3 焊接工艺•焊接工艺应符合IPC标准,并采用无铅焊接方式。
•焊接时应遵循良好的工艺控制,如控制温度、焊接时间和焊接扩展量等。
2.4 丝印和字体2.4.1 PCB丝印•PCB上的丝印应清晰、易读,方便组装和维修。
•丝印的颜色应与PCB背景颜色形成明显对比,以提高可视性。
FPC设计规范

1.1目的规范本公司FPC(柔性线路板)设计标准,提高设计员的设计水平,及工作效率。
1.2 范围适用于本公司FPC(柔性线路板)设计1.3 职责研发部:学习和应用FPC(柔性线路板)设计规范于开发新产品中。
1.4 定义无FPC设计规范与注意事项1FPC机构设计规范1.1LCD与FPC压合处要求如上图所示A:表示FPC成型边到LCD PIN顶端要差0.10mm.B:表示FPC PIN要比LCD压合PIN长0.10-0.20mm.C:此处只给正负0.10mm的公差.D:对位PIN到FPC两侧边不小于0.5mm.E:FPC PIN反面的PI覆盖膜距FPC PIN不小于0.3mm.F:此处只给正负0.20mm的公差.G:如果是FPC 需要从玻璃处弯折或是弯折距离<0.8mm如上图所示:A:双面胶要耐高温,长度最好能和FPC相等.T= 0.05mm.最好是3M厂商生产的,可靠性较好.B:宽度用2.50正负0.30mm的即可.C:FPC出PIN要用月牙边,便于焊接.D:FPC出PIN要有漏锡过孔,孔单边焊盘不小于0.15mm,便于焊接.E:FPC PIN正反面不能相等,要正反面相差0.20-0.30mm,正反面不能出阻焊层.注:此连接方式最终要符合客户要求.1.3FPC与主板插拔处要求(以HIROSE为例)如上图所示:A:此处公差一定要控制在正负0.07mm以内, 重点尺寸.B:此处公差一定控制在正负0.20mm以内.C:此处只给正负0.10mm的公差.D:此处公差一定控制在正负0.20mm以内.E:倒角非常重要,一定要有,否则可能接触不良.F:补强材料要硬,一般用宇部厂商生产的.较软的补强装配时金指会断裂.G:此处厚度在0.19-0.21较好,重点尺寸.注:以上是以HIROSE的连接器为例,具体项目要参考客户连接器规格书.1.4FPC与主板以公母座连接器连接如上图所示:A:焊盘设计以连接器规格说明为准,辅助焊盘不能少。
PCB设计规范范文

PCB设计规范范文pcb设计规范PCB(Printed Circuit Board)设计规范是指在进行电路板设计时,应遵循的相关规范和要求。
遵循这些规范可以确保设计的精度和可靠性,并提高生产的效率和质量。
以下是一些常见的PCB设计规范。
1.尺寸和布局规范:2.电路分布规范:在布局电路时,需要将功能相似的电路元件归为一组,并保持它们之间的距离尽可能短,以便减少信号传输时的干扰。
同时,需要将高频电路和低频电路分开,以避免相互干扰。
3.电源规范:在PCB设计中,电源线路应注意保持稳定的供电。
此外,对于高频电路和模拟电路,需要提供相应的电源滤波器和去耦电容,以降低噪声和交叉干扰。
4.信号走线规范:为了保证信号传输的稳定性和可靠性,需要遵循一些信号走线的规范。
信号线应尽量避免走并行,并尽量保持直线走向。
对于高频信号,应采用差分走线方式,并与地线或屏蔽层相邻,以减少干扰。
5.地线规范:地线在PCB设计中起到连接、屏蔽和引流的作用。
因此,需要确保地线宽度足够,且与信号线保持相邻,并尽量缩短长度。
在布局时,需要将地线划分为数个区域,以避免大面积的地线循环引起的回流问题。
6.散热规范:对于功耗较大的电路或存在散热问题的电路元件,需要考虑散热的设计。
可以通过增加散热片、散热器或增大散热面积来提高散热效果。
7.符号和标注规范:8.禁忌规范:在PCB设计过程中,需要遵循一些禁忌规范,以避免常见的错误。
例如,避免信号线和电源线重叠,避免不必要的直角走线,避免不合理的走线方式等。
总结:。
PCB线路板设计规范
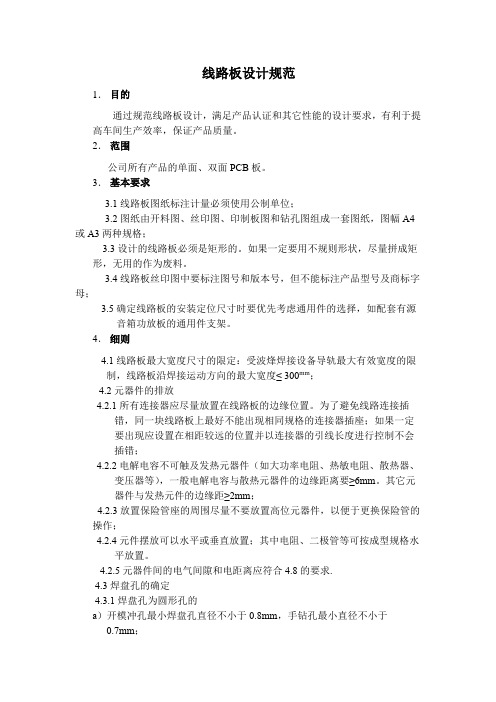
线路板设计规范1.目的通过规范线路板设计,满足产品认证和其它性能的设计要求,有利于提高车间生产效率,保证产品质量。
2.范围公司所有产品的单面、双面PCB板。
3.基本要求3.1线路板图纸标注计量必须使用公制单位;3.2图纸由开料图、丝印图、印制板图和钻孔图组成一套图纸,图幅A4或A3两种规格;3.3设计的线路板必须是矩形的。
如果一定要用不规则形状,尽量拼成矩形,无用的作为废料。
3.4线路板丝印图中要标注图号和版本号,但不能标注产品型号及商标字母;3.5确定线路板的安装定位尺寸时要优先考虑通用件的选择,如配套有源音箱功放板的通用件支架。
4.细则4.1线路板最大宽度尺寸的限定:受波烽焊接设备导轨最大有效宽度的限制,线路板沿焊接运动方向的最大宽度≤ 300mm;4.2元器件的排放4.2.1所有连接器应尽量放置在线路板的边缘位置。
为了避免线路连接插错,同一块线路板上最好不能出现相同规格的连接器插座;如果一定要出现应设置在相距较远的位置并以连接器的引线长度进行控制不会插错;4.2.2电解电容不可触及发热元器件(如大功率电阻、热敏电阻、散热器、变压器等),一般电解电容与散热元器件的边缘距离要≥6mm。
其它元器件与发热元件的边缘距≥2mm;4.2.3放置保险管座的周围尽量不要放置高位元器件,以便于更换保险管的操作;4.2.4元件摆放可以水平或垂直放置;其中电阻、二极管等可按成型规格水平放置。
4.2.5元器件间的电气间隙和电距离应符合4.8的要求.4.3焊盘孔的确定4.3.1焊盘孔为圆形孔的a)开模冲孔最小焊盘孔直径不小于0.8mm,手钻孔最小直径不小于0.7mm;b)焊盘孔直径统一系列规格为:φ0.7,φ0.8,φ0.9,φ1.0,φ1.2,φ1.4,φ1.6,φ1.8,φ2.0,φ2.2……c)焊盘孔系列规格的取值标准:即焊盘孔直径与入孔异体直径的最大间隙取值范围在0.15mm~0.2mm之间。
4.3.2焊盘孔为矩形孔的a)矩形焊接体最大对边直径≤1.2mm的按4.3.1开圆孔处理;b)矩形焊接体最大对边直径>1.2mm的,开矩形焊盘孔;焊接体与矩形孔的配合间隙在0.15mm~0.2mm之间。
PCB电路板PCB布线设计规范

PCB电路板PCB布线设计规范
PCB布线设计是电路设计中非常重要的一环,直接影响到电路性能和稳定性。
因此,需要遵循一些规范来进行布线设计。
以下是一些常见的PCB布线设计规范:
1.信号与地线分离:将信号线和地线尽量分开布线,避免干扰。
信号线和地线在不同的电层上布线,可以减小互相之间的干扰。
2.短小直接:信号线尽量布线得短小直接,可以减小信号损耗和传输延迟。
3.避免过长的信号线:过长的信号线会引入较大的电感和电容,从而影响电路性能。
因此,应尽量避免信号线过长。
4.保持恒定的信号宽度:在布线过程中,应保持信号线的宽度尽量恒定,以确保信号的稳定性和一致性。
5.信号线间距适当:信号线之间的间距应适当,太过靠近容易引起串扰或互电感现象。
6.使用适当的层间切换:多层PCB布线时,可以使用层间切换来减小信号线之间的干扰。
但层间切换要尽量少用,以减少通过不同层间穿越的信号线。
7.地线设计:地线在PCB中起到了引导回路和屏蔽作用,因此地线设计很重要。
应保证地线的宽度足够,接地点要均匀分布,并尽量避免地线之间过于靠近。
8.电源线布线:电源线在布线时要尽量分离,以减小电源线对信号线
的干扰。
在布线过程中,应思考电源线和地线如何合理地布局,以避免干扰。
9.差分信号线:对于差分信号线,要保持其长度和布线路径尽量相等,以减小差分信号间的相位差。
10.避免尖锐的走线:布线时应避免尖锐的转角,可以使用45度角来
减小信号的反射和干扰。
以上是一些常见的PCB布线设计规范,但在具体的设计中还需要根据
实际情况和需求来进行调整。
PCB设计规范参考

PCB设计规范参考在进行PCB(Printed Circuit Board,印刷电路板)设计时,遵循一些规范和标准是非常重要的,这有助于确保设计的质量和可靠性。
以下是一些常见的PCB设计规范的参考,以及它们的重要性。
1.尺寸和形状规范:确定PCB的尺寸和形状是设计过程中的首要任务之一、这些规范在很大程度上取决于特定应用的要求。
PCB尺寸和形状的规范有助于确保PCB适应所需的物理空间,并与其他系统组件正确连接。
2.加工工艺规范:合适的PCB加工工艺对于确保PCB的质量和可靠性非常重要。
这些规范包括焊接、制板、压合等方面的要求。
使用符合标准的加工工艺,可以确保PCB在生产过程中不会出现问题,并且能够在长期使用中保持稳定性。
3.电气规范:电气规范指的是关于PCB电路和信号传输的规范。
例如,电源轨迹的宽度、信号差分对距离的要求等。
遵循电气规范可以确保电路的电气性能符合设计要求,并减少电磁干扰和其他信号问题的产生。
4.元件布局规范:正确的元件布局对于PCB性能和可靠性至关重要。
这包括确保元件之间足够的空间,以免相互干扰;布局良好的地平面和电源平面,以提供稳定的地和电源;元件的定位和安装方向等。
5.焊接规范:在PCB制造过程中进行焊接是非常重要的步骤。
合适的焊接规范可以确保焊接质量良好,并减少焊接缺陷的发生。
这包括选择合适的焊接工艺、检查焊接质量、确保焊点间距正确等。
6.外观规范:PCB的外观规范非常重要,特别是对于涉及外部观感的应用。
这包括PCB板表面的丝印、防焊等图案的规范,以及PCB边缘的处理等。
7.补偿规范:在高频电路设计中,必须考虑传输线的补偿。
补偿规范包括考虑传输线的长度和传输速度,以及设计合适的终端匹配电路,以确保信号传输的准确性和稳定性。
8. EMS(Electromagnetic Susceptibility,电磁干扰抗扰度)规范:在电子设备中,电磁干扰是一个常见的问题。
EMS规范涵盖了设计抑制电磁干扰的措施,包括良好的地平面设计、电源线滤波、添加抑制电容等。
PCB设计规范(最新版本)

印刷电路板〔PCB〕设计标准一:适用范围:本标准适用于我司CAD设计的所有印刷电路板〔简称:PCB〕二:目的:1. 本标准规定我司PCB设计流程和设计原那么,为PCB设计者提供必须准那么2. 提高PCB设计质量和效率,提高PCB的可生产性,可测性,可维护性。
三:设计任务受理:1. 电子工程师接到上级分配的新产品开发工程时,首先填写?新产品PCB设计进度表?。
然后根据新产品要求完成电路原理图设计,并通过电子组及软件组审核。
2 . 对于设计电路中不常用元件,先通过查公司ERP,如果没有库存,那么需要在第一时间写申购单申请所需元器件,保证新产品开发进度。
3. 要求构造组负责人员提供正确的PCB构造图及3D效果图,在导入构造图过程中须与构造工程师沟通,了解各筋位线分层情况及定位孔位置等等信息。
4. 对于常规产品的设计,那么可根据原有的资料进展LAYOUT,须注意样品单上产品的交期。
四:设计过程:1 创立网络表:1. PCB设计人员根据具体的CAD设计软件创立符合要求的网络表。
2. 确定元器件封装〔PCB FOOTPRINT〕,对于新元件需根据元器件资料制作相应封装。
3. 引入网络表创立PCB板设计文件。
2 元器件布局1. 根据构造图设计板框尺寸,按构造要求定位元器件,并按要求给予尺寸标注。
比方:PCB板厚,PCB的外形尺寸等等。
2. 根据构造图和生产实际要求设计制止布线区。
3. 根据产品要求合理选取板材,定义板层。
4. 布局的根本原那么:a). 按照<先大后小,先难后易,先整体,后局部>的布局原那么,重要的单元电路,核心元器件应优先布局。
b). 布局应参考电原理图,根据信号流向规律按排主要元器件。
c). 布局应尽可能满足:连线尽可能短,高电压,大电流信号线与低电压,小电流信号线完全分开。
d). 板面元器件均匀分布,重心平衡,版面美观的标准优化布局。
5. 布局过程中的元件放置:a). 同类型插装元器件在X或Y方向上应朝一个方向放置,便于生产和检验。
PCB板设计规范
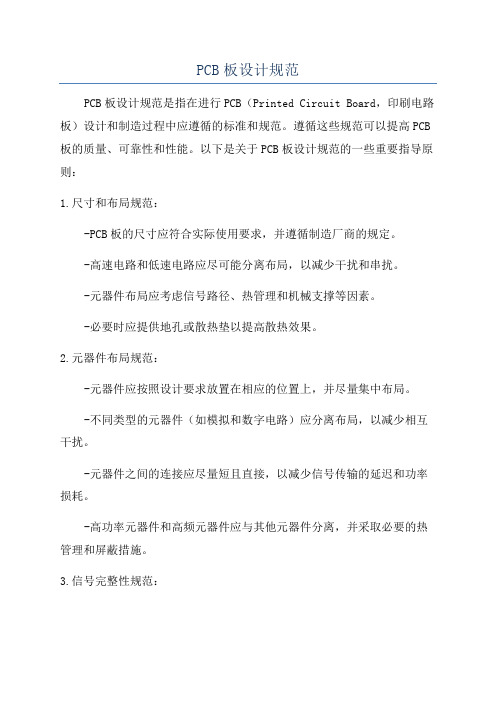
PCB板设计规范PCB板设计规范是指在进行PCB(Printed Circuit Board,印刷电路板)设计和制造过程中应遵循的标准和规范。
遵循这些规范可以提高PCB 板的质量、可靠性和性能。
以下是关于PCB板设计规范的一些重要指导原则:1.尺寸和布局规范:-PCB板的尺寸应符合实际使用要求,并遵循制造厂商的规定。
-高速电路和低速电路应尽可能分离布局,以减少干扰和串扰。
-元器件布局应考虑信号路径、热管理和机械支撑等因素。
-必要时应提供地孔或散热垫以提高散热效果。
2.元器件布局规范:-元器件应按照设计要求放置在相应的位置上,并尽量集中布局。
-不同类型的元器件(如模拟和数字电路)应分离布局,以减少相互干扰。
-元器件之间的连接应尽量短且直接,以减少信号传输的延迟和功率损耗。
-高功率元器件和高频元器件应与其他元器件分离,并采取必要的热管理和屏蔽措施。
3.信号完整性规范:-控制线、时钟线和高速信号线应尽可能短,且避免平行走线,以减少串扰和时钟抖动。
-高速信号线应采用阻抗匹配技术,以确保信号的正确传输和减少反射。
-高速差分信号线应保持恒定的差分阻抗,并采用差分匹配技术,以减少干扰和降低功耗。
4.电源和接地规范:-电源线和地线应尽可能粗,以降低电阻和电压降。
-电源和地线应尽量采用平面形式,以减少电磁干扰和提供良好的电源和接地路径。
-多层PCB板应设有专用层用于电源和接地,以提高板层的抗干扰能力和电源噪声的影响。
5.焊接规范:-设计带有相应的焊接垫和焊盘,以便于元器件的焊接和可靠连接。
-焊盘和焊接垫的尺寸应符合元器件和制造工艺的要求,并考虑到热膨胀和热应力等因素。
-导线和焊盘间的间距应符合焊接工艺的要求,以确保焊接质量和可靠性。
6.标记和文档规范:-PCB板应有清晰的标记,包括元器件名称、值和位置、网络名称等。
-为了提供必要的参考和维护,应有详细的PCB设计文档,包括原理图、布线图和尺寸图等。
总的来说,遵循PCB板设计规范可以提高PCB板的可靠性、性能和一致性,减少制造和调试过程中的问题和风险。
PCB线路板设计规范

PCB线路板设计规范1.尺寸和形状:2.层次结构和层数:根据电路的复杂程度和信号传输要求,选择适当的层数和层次结构设计。
多层线路板可以提高信号的传输速度和抗干扰能力。
3.布局和走线:合理的布局和走线是确保线路板性能稳定和可靠的重要因素。
布局应考虑到信号传输的路径和距离,避免信号串扰和电流回环。
同时,还要合理安排元件的位置,方便组装和维修。
4.电源和地线分布:电源和地线的设计是PCB线路板中最关键和常见的问题。
电源线和地线应尽量短且粗,以降低线路的电阻和电感。
同时,应按照规定的顺序布置和连接电源和地线。
5.信号传输线的匹配和阻抗控制:对于高频信号或差分信号传输线,需要进行信号匹配和阻抗控制。
匹配和阻抗控制可以提高信号传输的质量和稳定性,减少信号的失真和干扰。
6.元件布局和封装选择:合理的元件布局可以减少线路板的面积和线路长度,提高线路板的稳定性和性能。
同时,要选择合适的元件封装,确保元件与线路板之间的连接可靠。
7.温度和热量控制:8.防静电保护:在PCB线路板设计中,要考虑到防静电的问题,以避免静电对元件和电路的损坏。
可以采用电路设计和元件封装等手段来进行防静电保护。
9.标志和标注:在PCB线路板上应标注清晰的标志和标注,以方便组装、维修和调试。
标志和标注应包括线路板的名称、版本号、日期等信息。
10.制造和测试可行性:在设计PCB线路板时,要考虑到制造和测试的可行性。
应选择合适的材料和制造工艺,以确保线路板的质量和可靠性。
同时,要设计适合的测试点和测试方法,方便对线路板进行测试和调试。
总之,PCB线路板设计规范是确保线路板性能和可靠性的基本要求。
根据具体的应用需求和制造工艺,可进一步完善并优化线路板设计规范。
PCB外形及拼板设计规范

PCB外形及拼板设计规范PCB外形及拼板设计规范对于PCB设计来说非常重要,它决定了电路板的形状和组件的摆放位置。
在设计过程中,必须遵循一系列的规范和标准,以确保电路板的质量和可靠性。
以下是PCB外形及拼板设计规范的一些重要方面。
1.PCB外形尺寸:PCB外形应根据所需的装配和使用环境进行设计。
在确定外形尺寸时,需要考虑电路板的固定方式和与其他组件的连接方式。
尺寸通常使用毫米或英寸作为单位,并应明确标注在PCB图纸上。
2.边缘修整:PCB的边缘通常需要进行修整,以确保电路板的平整度和美观度。
修整方式可以是直线型、圆弧型或其他特定形状,但必须考虑到边缘修整过程对电路板的影响。
3.安装孔:在PCB边缘的适当位置应设置安装孔,用于固定电路板。
安装孔的形状和数量应根据具体需求进行设计,并且与所需固定方式相匹配。
4.边缘保护:为了保护电路板免受环境的损坏,可以在PCB边缘添加边缘保护层。
这可以是无铅焊料、覆盖层或其他材料。
边缘保护层的设计应确保其性能和稳定性。
5.禁止区域:在PCB设计过程中,需要确定禁止区域,即不允许放置组件或走线的区域。
这些区域通常是特定的电路、连接器或机械部件占据的区域。
禁止区域可以在PCB图纸上用标记或颜色进行明确表示。
6.元器件布局:在进行拼板设计时,需要根据电路图和元器件的特性合理布局各个组件。
布局应考虑清晰的信号链路、最短的信号路径、避免干扰和良好的散热等因素。
同时,对于高频、高压和高功耗的元器件,还需要考虑合适的间距和隔离措施。
7.极性标识:在PCB设计过程中,需要正确标识元器件的极性,以免安装错误或连接错误。
极性标识可以通过文字、符号或颜色进行表示,并应明确标注在PCB图纸上。
8.过孔布局:在设计PCB时,还需要合理布局过孔,以确保电路板的结构强度和连接可靠性。
过孔布局应考虑到特定元器件的要求,避免与其他走线或元器件冲突。
总之,PCB外形及拼板设计规范是确保电路板质量和可靠性的基础。
公司PCB设计规范

公司PCB设计规范PCB设计规范是现代电路设计的重要组成部分,它对保证电路的品质、生产效率和设计成本等方面具有重要的作用。
为了确保公司生产的PCB设计符合规范要求,我们需要建立一套完整的PCB设计规范。
一、规范的内容PCB设计规范应包括以下内容:1.设计固定参数:包括PCB厚度、金属化孔壁厚度、印刷电路板(PCB)尺寸、焊盘间距、引脚排列等。
这些参数对于设计电路的尺寸和布局非常重要,需要在设计前定义清楚。
2.热量和尺寸限制:PCB设计需要考虑热量传递和排放,尤其是在高压和高频电路中,需要特别注意。
因此,在规范中需要约定热量和尺寸的限制条件,以确保设计符合实际需求。
3.层级规定:在PCB设计中,常常会涉及到不同电路层的设计和布局,这时需要约定不同电路层的名称和编号,并定义所在电路板的顺序、颜色、布线等等。
4.标称值和偏差规定:在PCB设计中,各元件的标称值和偏差会对设计造成很大影响,因此需要定义各元件的标称值和偏差范围。
5.重点部分的细节规定:对于设计中一些比较特殊的部分,如高压射频、高速信号传输等,需要定义设计的参数和限制。
这些细节规定有助于确保重点部分的设计符合实际要求。
二、规范的实施为了确保规范的有效实施,公司需要建立相应的管理体系。
具体措施如下:1.明确责任:规范的实施需要有明确的责任人。
由部门主管或生产管理人员负责制定规范,并确定实施的计划和步骤。
2.培训和普及:为了让所有参与设计的人员能够理解和遵守规范,公司需要开展相应的培训和普及工作。
可以通过内部培训、讲座、技术交流等方式进行普及,让人员了解和掌握规范的要求。
3.监督检查:在实施过程中需要对设计文档进行监督检查,确保设计符合规范。
监督检查的方式可以通过审核、抽查等,查出不符合规范要求的设计文档,及时进行改正。
4.完善修改:规范随着技术和工艺的变化而不断完善,一旦有新的要求和调整,需要及时进行修改和更新,确保规范与实际情况相符。
三、规范带来的好处1.提高生产效率:规范可以固定设计参数和部分设计细节,减少重复设计、修改和排版,同时通过提高设计的质量,减少产生错误、漏洞和灾难的概率,从而提高生产效率。
pcb设计规范

pcb设计规范PCB设计规范是指在进行PCB(印刷电路板)设计时需要遵守的一系列规范和要求。
它是为了确保PCB设计能够满足电路功能、可靠性、性能和制造要求而制定的一套准则。
下面是一个包括以下几个方面的PCB设计规范的简要介绍:布局规范、连接规范、尺寸规范、排线规范、屏蔽规范、引脚规范、焊盘规范、维护规范、供电规范、阻抗控制规范、信号完整性规范和电磁兼容规范等。
一、布局规范:1. 分区:将电路分成不同区域,例如:模拟区和数字区,以保证信号隔离和降低干扰。
2. 元件间距:为了防止短路和易于维修,元件之间应有足够的间距。
3. 元件定位:同一类元件应按一定方向或排列位置的顺序来布置,方便组装和维护。
4. 散热:大功率元件应注意散热,通过散热铺铜、散热片等方式来确保元件正常工作。
二、连接规范:1. 自上而下:信号在PCB板上的走向应该尽量遵循由上到下的原则,使得PCB板的布线更加整洁、直观。
2. 避开高频:要尽量避免高频信号和低频信号之间的相互干扰,可以使用屏蔽或扩大引脚间的距离来降低干扰。
3. 引脚的选择:应该根据现有的条件优先选择靠近与所连接元件引脚的导线,减少有钟信号线的影响。
三、尺寸规范:1. PCB板的大小:要注意PCB板的大小与所在设备的大小相匹配,确保PCB板可以适应所在设备中的空间限制。
2. 引脚排列的紧凑性:要选择适当的引脚封装,使得PCB板的线路布线更加紧凑,减小占用空间。
四、排线规范:1. 频率分离:要分离高频和低频信号,以减少信号之间的干扰。
2. 避免平行:尽量避免平行排线,以减少互相之间的串扰。
3. 差分信号的布线:对差分信号进行特殊配置,使两个信号线的长度、宽度和间距保持一致,以减少干扰。
五、屏蔽规范:1. 地平面:在PCB板的一层铜皮上进行足够的地线平面,以减少地线的串扰。
2. 分离高频和低频信号:在高频和低频信号之间设置屏蔽层,以降低互相之间的干扰。
六、引脚规范:1. 引脚类型:根据元件的类型和功能,选择适当的引脚类型,例如标准引脚、表面贴装引脚或插针引脚等。
- 1、下载文档前请自行甄别文档内容的完整性,平台不提供额外的编辑、内容补充、找答案等附加服务。
- 2、"仅部分预览"的文档,不可在线预览部分如存在完整性等问题,可反馈申请退款(可完整预览的文档不适用该条件!)。
- 3、如文档侵犯您的权益,请联系客服反馈,我们会尽快为您处理(人工客服工作时间:9:00-18:30)。
电热
--
√
√
√
√
遥控器
√
√
--
--
加工性能
一般
一般
良
优
优
介电性能
一般
一般
良
良
优
阻燃性
无
有
有
有
有
机械性能
差
差
良
良
优
耐热耐湿性能
差
差
一般
优
优
耐漏电痕迹性和 差
耐金属离子迁移性
差
优
良
良
价格
低
低
中
高
高
1.2 过去存在的问题点调查如表 2、表 3 所示 表 2 贴片线路板过去存在的问题点
焊盘尺寸
图14 V型槽 表4
材质
纸基板 (t=T/2)
残留尺寸:t 切口深度:c
玻璃布基板 残留尺寸:t 复合材料基板
~ (t=0.4 0.6) 切口深度:c
T = 0.8
0.4
+0.10 0
0.2
+0 -0.05
0.4 ±0.10
0.2 ±0.05
板 T = 1.0 0.5 ±0.10 0.25 ±0.05 0.4 ±0.10 0.3 ±0.05
图5 2.2.7 刚硬角度的处理 2.2.7.1 铜箔走线部分处理(尽可能圆弧化)
2.2.7.2 焊盘走线处理
图 6 铜箔走线
图 7 焊盘走线 2.2.8 PCB 板固定与铜走线处理(防止铜箔受固定钢轴影响破损)
图8 2.2.9 铜箔、导线宽部分与窄部分过渡处理
3
Q/KJ J03403—2004
图9 2.2.10 无焊盘的孔应把孔周围的铜箔去掉,间距为 0.5mm
曲线或形状复杂的用铣槽或邮票孔等加工方式加工,尺寸如图 15 所示。邮票孔严禁金属化。 邮票孔要加在板子的最前面或最后面,且有细线的地方要把邮票孔移走。
7
图 15 邮票孔样式 2.6.2 线路板缺口部分处理
对于部分有缺口的 PCB 板,缺口部分作如下处理
Q/KJ J03403—2004
图 16 2.6.3 外形锐角部分的处理,如图 17 所示。
b、PCB 板运行过程中要防止弯曲变形;
c、波峰焊焊接时要保持固定的空间。
3 手插的标准化要求
3.1 PCB 板的部品摆放领域:元件本体在 PCB 上正投影以白(黑)油丝印标示,距离板边应≥
8.0mm。
图 21
9
3.2 重量大部品摆放(维持 PCB 板整体的重量均衡)
Q/KJ J03403—2004
焊盘和机插孔距离
贴片元器件间距
元器件焊盘尺寸设计不规范, 导致连焊虚焊增多;贴片三极 管的焊盘没加收锡孔,导致过 波峰焊时不粘锡(只过回流焊 的板子不需加开锡槽、收锡孔
和收锡焊盘 )
个别贴片元器件焊盘和机插 孔距离过小,导致在机插过程 中,碰伤或者损坏贴片元器件
小于安全距离,导致连焊现象 增多,引脚间距小于 0.5mm 的 贴片类芯片过波峰焊时,导致
3)、V型槽残留尺寸的调整要求 a、 焊接工程(机插机、贴片机、运送带)中拼版不受破坏。 b、 不使用分割工装时,能手动分割。 c、 使用分割工装时能分割。 d、 厚度为1.0mm以下的基板,由于V型槽存在的加工精度偏差,基板强度与基板易于分割之间
的平衡点难以掌握,试作时应充分验证。 2.6.1.3 邮票孔的设计
2 线路板通用设计标准化的要求
2.1 线路板字符的规定
2.1.1 元器件字符的规定参见青岛海尔科技有限公司企业标准 Q/KJ J03201-2002
2.1.2 元器件面标记符号图见附录 A、附录 B。
2.1.3 在电源铜走线上标明电压值(如 d.c+5V、d.c+12V),地铜走线上标明 GND 等标记。
“020031033000357 KF(R)-26/36GW/N(F) VER:A”,具体如图 1 所示:
图 1 线路板标记字符及位置 2.1.6 遥控器线路板版面(反)丝印线路板的专用号、标准描述及版本号。 2.2 走线要求 2.2.1 强电导线间距应不小于 4mm。 2.2.2 强弱电之间导线间距不小于 8mm。 2.2.3 铜箔间最小间距及铜箔最小宽度.
R
R
N
H H
R
R
R
立昌
N
松下 板材的纤维方向
日立
8
Q/KJ J03403—2004
图 18 板材方向 2.7.2 传送方向,如图 19 所示。要求:L>W。(L:线路板拼板总长度,W:线路板拼板总宽度)
不良
良
图 19 线路板的传送方向
2.7.3 PCB 板的焊接方向
为防止过波峰焊时,尽量减少元器件的各引脚之间的连焊,通常把主要集成块的焊接方向
5
Q/KJ J03403—2004
图 11 拼板大小及定位要求 2.5.3 定位孔分主定位孔和副定位孔,尺寸如图 12 所示。
2-R2
主定位孔
副定位孔
图 12 定位孔
2.5.4 线路板主工艺边上丝印 PCB 移动方向,以箭头“ ”标示,尺寸如下:
2.6 PCB 板外形设计 2.6.1 拼版的设计 2.6.1.1 拼版形式,PCB 板的外形以长方形为准 对于特殊形状的线路板要采用特定的连接方式,如图 13 所示:
铜箔是制造覆铜板的关键材料,必须有较高的导电率及良好的焊接性。铜箔越薄,越容
易蚀刻和钻孔,特别适合于制造线路复杂的高密度的印制板。
虚焊现象增多
丝印问题
表 3 线路板设计过去问题点调查表
开关设计
收锡焊盘
元件排列
电解电容、接插件 等在线路板上的 符号太小,导致插 上元件后,不能准 确的辨别方向。
按键、轻触开关等设计 在较窄的工艺边那一 端,导致过波峰焊时易
出现故障
排插座、芯片等在 首尾两端不加收锡焊 盘,导致过波峰焊时
易造成连焊
多个元器件没有采用 交叉排列的方式,导 致过波峰焊时元件连 焊
4
Q/KJ J03403—2004 2.3 电源线(层)和接地线(层)的设计 2.3.1 单面或双面印制电路板上有大面积电源区和接地区时(面积超过直径为 25mm 圆的区 域),应局部开窗口,以免大面积铜箔的印制电路板在浸焊或长时间受热时,产生铜箔膨胀、 脱落现象或影响元件的焊接质量。 2.3.2 大面积电源区或接地区的元件连接盘,应设计成如图 12 所示形状,以免大面积铜箔传 热过快,影响元件的焊接质量,或造成虚焊。 2.4 元件布局要求 2.4.1 元件尽可能有规则地分布排列,以得到均匀的组装密度。 2.4.2 大功率元件周围不应布置热敏元件,要留有足够的距离,原则上元件体底部到 PCB 的 距离应≥3.0mm。电解电容与散热器的距离≥5.0mm。 2.4.3 需要安装较重的元件时,应安排的靠近印制电路板支承点的地方,使印制电路板的翘 曲度减至最小。 2.4.4 元件排列的方向和疏密程度应有利于空气的对流。 2.4.5 原则上跳线或元件表面不加装元件,不能避开的,要在技术条件中明确界定所加元件 体的限度浮高标准,避免波峰焊后修整元件体浮高。 2.5 线路板基本尺寸设计 2.5.1 拼版要求,如图 11 所示。 拼板大小: a. 50*50mm~330*250mm(L*W)(有贴片工序);
b. 50*50mm~508*371mm(L*W)(无贴片工序); 建议最优拼版边长为:147mm、197mm、247mm、297mm 板厚要求:0.5 mm~2.0mm,优选 1.6mm。 2.5.2 工艺边设计 工艺边宽度要求:a 为主工艺边宽度,b 为副工艺边宽度。 机插线路板:a=7mm~10mm,b=0 mm~5mm。 贴片线路板:a= 10mm,b=0 mm~5mm。工艺边宽度小于 5mm,MARK 点可做到线路板上,保证 MARK 点到线路板工艺边缘的距离应不小于 5mm.按键开关、轻触开关等原则上要设计在 10mm 那一端。
1
Q/KJ J03403—2004 2.1.4 接插件、线应注明其作用或功能或颜色的主关键字,以示区分,用英文或汉语拼音字母 表示,不应出现汉字。对于带端子的线束以其端子的方向为标准。 2.1.5 在工艺边上应印上线路板的专用号、电脑板型号、版本号、线路板过波峰焊时的移动方 向,以箭头“ ”标示。例如:
不良
良
图 17 外形锐角部分的处理方式
2.7 线路板板材方向及焊接方向
2.7.1 板材纹路方向
板材纹路方向即线路板板中加强纤பைடு நூலகம்的走向。覆铜箔板的纤维为线状,板材方向为纤
维的走向。覆铜箔板的纤维为网状,则板材无方向性,如玻璃布板都无方向性。沿着板材
方向,线路板的机械性能增强。常用板材的方向如图 18 所示。
(正确)
(错误)
图 22
3.3 IC 下面以不设跨线为最佳。如果设计时,注意跨线的对称及 IC 放置后的平衡性。
(错误)
图 23
3.4 重加焊设计
3.4.1 对于较大或较重的部件,其焊盘应设计为菊花状(发散状)。
3.4.2 线路设计时,如计算不能承受负载电流,可裸露线路铜箔或加宽线路,要求过波峰焊
后满足负载电流标准要求,确因两种方式不能达标,应改用多根跳线或导线连接方式,线束
Q/KJ J03403—2004
1 线路板设计现状的分析
1.1 电脑板选用的板材及板材的性能特性如表 1 所示:
表 1 机插电脑板及选用板材性能对应表
电脑板
XPC0
FR-1
板材 CEM-1
CEM-3
空调
--
√
√
√
冰箱
--
--
--
√(主控)
洗衣机
--
√