高性能陶瓷涂层制备法
陶瓷薄膜制备方法
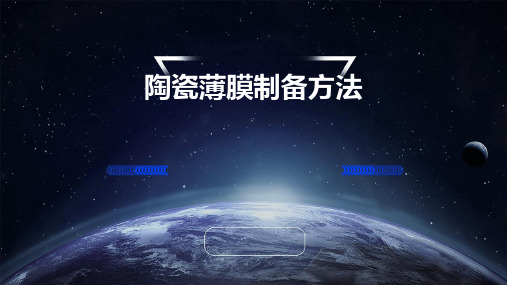
利用喷枪将陶瓷粉末或浆料喷涂在基材上,具有低成本、 高生产效率和制备形状复杂的零件等优点,但附着力较低 ,表面粗糙度较高。
根据应用需求选择制备方法
高性能陶瓷
01
物理气相沉积法和化学气相沉积法适用于制备高性能陶瓷薄膜,
如高温超导、硬质合金和光学薄膜等。
大面积制备
02
化学气相沉积法和溶胶-凝胶法适用于大面积制备陶瓷薄膜,如
陶瓷薄膜的应用领域
机械工业
电子工业
陶瓷薄膜可用于制造切削刀具、磨具、模 具等,提高其耐磨性和使用寿命。
陶瓷薄膜具有良好的绝缘性和热稳定性, 可用于制造电子元件和电路,提高其性能 和稳定性。
航空航天
生物医学
陶瓷薄膜可用于制造高温部件和涂层,提 高其耐高温和抗氧化性能。
陶瓷薄膜具有生物相容性和良好的化学稳 定性,可用于制造人工关节、牙齿等医疗 植入物,提高其耐磨性和使用寿命。
05
溶胶-凝胶法
浸渍提拉法
浸渍提拉法是一种常用的制备陶瓷薄膜的方法,其基本原理是将基片浸入溶胶中,然后慢慢提起,使溶胶在基片上形成一层 薄膜,再经过干燥和热处理,得到所需的陶瓷薄膜。该方法的优点是操作简单、可大面积制备,但缺点是难以制备厚度较小 的薄膜。
浸渍提拉法的关键在于控制溶胶的粘度和表面张力,以及基片的浸渍速度和提起速度。这些因素将直接影响陶瓷薄膜的厚度 和均匀性。
喷雾热解法在制备陶瓷薄膜中的应用
喷雾热解法在制备陶瓷薄膜中具有广泛的应用,如氧化铝 、氧化锆、氧化钛等陶瓷薄膜的制备。通过选择合适的陶 瓷前驱体溶液和热解条件,可以控制陶瓷薄膜的成分、结 构和性能。
在实际应用中,喷雾热解法通常与其他方法结合使用,如 化学气相沉积、物理气相沉积等,以提高陶瓷薄膜的质量 和性能。
金属陶瓷材料的制备及性能研究
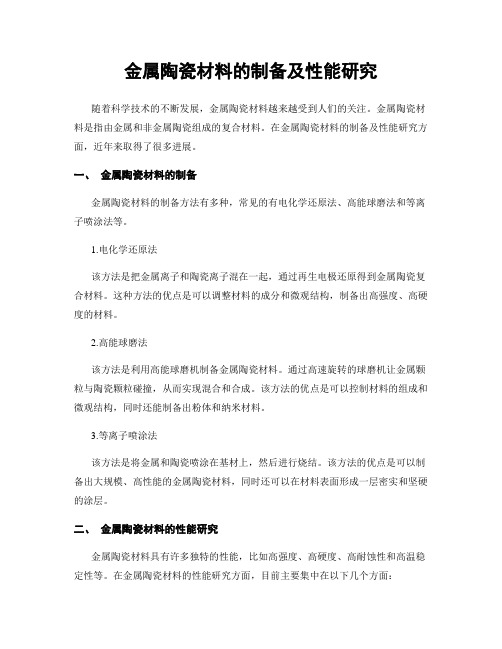
金属陶瓷材料的制备及性能研究随着科学技术的不断发展,金属陶瓷材料越来越受到人们的关注。
金属陶瓷材料是指由金属和非金属陶瓷组成的复合材料。
在金属陶瓷材料的制备及性能研究方面,近年来取得了很多进展。
一、金属陶瓷材料的制备金属陶瓷材料的制备方法有多种,常见的有电化学还原法、高能球磨法和等离子喷涂法等。
1.电化学还原法该方法是把金属离子和陶瓷离子混在一起,通过再生电极还原得到金属陶瓷复合材料。
这种方法的优点是可以调整材料的成分和微观结构,制备出高强度、高硬度的材料。
2.高能球磨法该方法是利用高能球磨机制备金属陶瓷材料。
通过高速旋转的球磨机让金属颗粒与陶瓷颗粒碰撞,从而实现混合和合成。
该方法的优点是可以控制材料的组成和微观结构,同时还能制备出粉体和纳米材料。
3.等离子喷涂法该方法是将金属和陶瓷喷涂在基材上,然后进行烧结。
该方法的优点是可以制备出大规模、高性能的金属陶瓷材料,同时还可以在材料表面形成一层密实和坚硬的涂层。
二、金属陶瓷材料的性能研究金属陶瓷材料具有许多独特的性能,比如高强度、高硬度、高耐蚀性和高温稳定性等。
在金属陶瓷材料的性能研究方面,目前主要集中在以下几个方面:1.力学性能金属陶瓷不仅具有优异的力学性能,而且还能在高温和高压等恶劣环境下保持稳定。
目前,通过力学测试可以评估金属陶瓷材料的强度、硬度、断裂韧性和抗疲劳性等性能。
2.耐腐蚀性能金属陶瓷材料具有优异的耐腐蚀性能,这使它在化工、航空和海洋等领域有着广泛的应用前景。
目前,通过模拟实验和电化学测试等方法可以评估金属陶瓷材料的耐腐蚀性能。
3.热性能金属陶瓷材料具有优异的热性能,能够在高温高压环境下保持结构稳定和性能不变。
目前,通过热重分析和热膨胀等测试方法可以评估金属陶瓷材料的热性能。
总之,金属陶瓷材料在现代工业中具有广泛的应用前景,其制备及性能研究已经成为了一个热门的研究领域。
未来,随着技术的不断发展,金属陶瓷材料将会在更多领域发挥着重要的作用。
高性能新型陶瓷材料的制备与研究

高性能新型陶瓷材料的制备与研究摘要:高性能陶瓷材料的使用温度一般为1400~1500℃,超高温的材料能够达到1800℃以上,主要包含过渡金属的硼化物、碳化物以及石墨、氮化硼等。
高温陶瓷材料主要的优势是熔点较高,具备超高温耐腐蚀性及超高温稳定性,在国防、航天以及容器保护中应用广泛。
目前加强了对Si—B—C—N超高温陶瓷材料的研究,主要应用于超高温涂层材料,制备工艺主要是有机前驱体法,但是因为对超高温稳定机理的理解还需要进一步的加深和研究,其操作严格、成本较高。
因此,加强对新的制备工艺技术的研究,深入探讨超高温稳定化机理将成为未来研究的重要方向和内容。
基于此,对高性能新型陶瓷材料的制备与研究进行研究,以供参考。
关键词:高性能新型陶瓷材料;制备工艺引言从1962年R.L.Coble首先研究并成功生产了高性能的氧化铝复合陶瓷开始,就为复合陶瓷技术开拓了崭新的应用领域。
该类材料不但具备较高的性能,而且耐腐蚀,可在高温高压下正常工作,还拥有其他金属材料所无可比拟的特性,如硬度较高、介电性能优异、低电导率、高温导性好等,从而逐步在照明科技、光学、特种仪表制作、无线电子科技和高温科技等领域得到越来越深入的运用。
1高性能陶瓷材料应用前景陶瓷材料是新材料中的重要分支,在能源、机械、冶金、汽车以及石油化工等各个行业发挥着重要作用,成为工业技术发展中不可或缺的关键材料。
随着社会经济市场的快速发展和国民经济水平的不断提升,工业企业的技术水平也在不断发展和提升,各个行业都迫切的需要大量的高性能陶瓷材料,因此市场前景较为广阔。
陶瓷材料一般情况下分为结构陶瓷、功能陶瓷,有的还分为陶瓷涂层以及陶瓷复合材料等。
目前使用较为广泛的主要是以结构陶瓷和功能陶瓷为主,其中结构陶瓷的优势是耐磨性较强、强度较高,在热机部件、耐磨部件等领域中具有较为广泛的应用。
陶瓷材料在多个领域中都得到了广泛应用,尤其是在高新技术领域,陶瓷材料在其中发挥着非常关键的作用。
聚合物前驱体法

聚合物前驱体法聚合物前体法(polymer precursor method)是一种制备高性能陶瓷和陶瓷复合材料的方法。
该方法允许制备出高品质的陶瓷材料,例如氧化铝(Al2O3)、氮化硅(Si3N4)、碳化硅(SiC)、氧化锆(ZrO2)等。
聚合物前驱体法的核心是合成一种可转化为陶瓷材料的高分子化合物。
这种高分子化合物具有良好的加工性能和较低的转化温度,通常在500℃以下。
在高温条件下,高分子化合物中的有机官能团会被分解,生成与之相应的无机气体或气体混合物。
通过这种方式,高分子化合物被转化为陶瓷材料。
聚合物前驱体法的基本原理是在基体中均匀分散具有大分子量的聚合物(前体),然后通过热分解或热氧化等方法将这种聚合物转化为相应的氧化物或氮化物。
其实质是通过化学反应将聚合物(前驱体)的有机分子分解掉,而留下肥大的无机颗粒。
由于聚合物的使能团可以自由地与不同的无机物相互作用,因此形成不同的颗粒直径和形状。
因此,制备的陶瓷材料具有较为均匀的密度和结构,同时具有较高的韧性和强度。
聚合物前驱体法有很多的应用。
例如,其可用于制备高性能催化剂、气氛传感器、电子器件、摩擦材料和高温涂层等。
与传统的陶瓷制备方法相比,聚合物前驱体法拥有许多优点。
聚合物前驱体法具有较小的非晶区域和较均匀的微结构,这使得制备出的陶瓷材料具有较高的力学性能、抗氧化性能和抗磨损性能。
此外,聚合物前驱体材料的工艺性能也较好,它可以容易地切割、打磨成形、粘接等。
聚合物前驱体法目前已被广泛应用于实际生产生活中,其优点主要在于其在低温下即可完成热分解反应,而且可以有效删除组成的有机炭,聚合物在热分解过程中很容易和其他无机材料成熟,因此制备工艺起来很容易。
聚合物前驱体法的应用前景很广泛,尤其是在微电子、电池、催化剂制备等领域能提高其使用性能和生产效率,能为相应行业的工业化发展打下坚实的基础。
300M钢表面金属陶瓷涂层的制备工艺及性能研究

300M钢表面金属陶瓷涂层的制备工艺及性能研究冯抗屯;肖细军;陈小虎;魏东博;魏祥飞;张平则【摘要】为推进金属陶瓷涂层在飞机起落架表面防护技术中更广泛的应用,制备了IPcote 9183和IPcote 9184两种金属陶瓷涂层并进行了微观组织、力学性能和防腐性能的研究,同时与传统电镀镉钛涂层进行了对比分析.结果表明,IPcote 9183和IPcote 9184金属陶瓷涂层的最佳制备工艺分别为三次喷涂三次表干以及一次固化(三喷三表一固),两次喷涂两次表干以及一次固化(两喷两表一固);与传统电镀镉钛相比,两种金属陶瓷涂层具有良好的综合力学性能;IPcote 9184涂层硬度最高,是IPcote 9183涂层的7倍,电镀镉钛涂层的4倍;IPcote 9183弹性模量最好,IPcote 9184次之,电镀涂层最差;IPcote 9183的结合强度是电镀层的4倍.电镀镉钛试样和IP-cote 9184,9183共同涂覆的试样表面在720 h中性盐雾试验中未出现明显的锈蚀痕迹.【期刊名称】《南京航空航天大学学报》【年(卷),期】2015(047)005【总页数】9页(P687-695)【关键词】金属陶瓷防腐涂层;喷涂;力学性能【作者】冯抗屯;肖细军;陈小虎;魏东博;魏祥飞;张平则【作者单位】中航飞机股份有限公司长沙起落架分公司制造工程部,长沙,410200;中航飞机股份有限公司长沙起落架分公司制造工程部,长沙,410200;南京航空航天大学材料科学与技术学院,南京,211106;南京航空航天大学材料科学与技术学院,南京,211106;南京航空航天大学材料科学与技术学院,南京,211106;南京航空航天大学材料科学与技术学院,南京,211106【正文语种】中文【中图分类】TG174.4起落架结构与机体同寿是现代大型民用飞机的普遍要求,其寿命一般要求达到6万起落。
民用飞机起落架选材主要应用300M钢、高强钛合金及铝合金等高性能材料,对其进行新型高性能表面防护工艺研究十分必要[1]。
纳米结构陶瓷涂层的制备技术
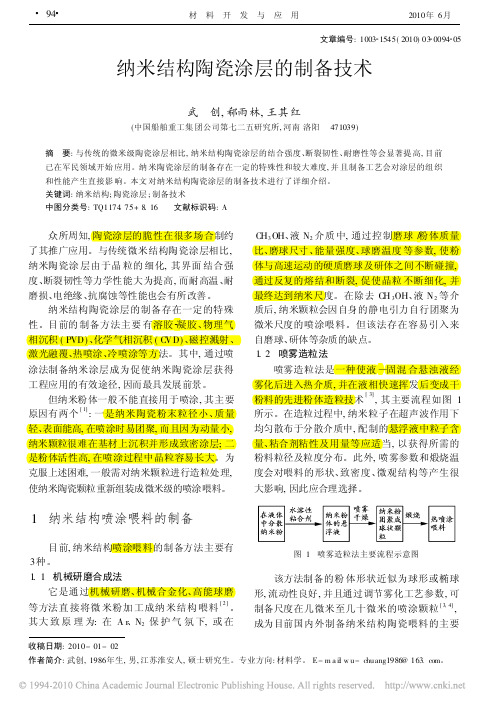
2 . 3 超音速火焰喷涂 ( HVOF ) 超音速火焰喷涂 是利用燃料燃烧膨胀形成 的热气流使喷涂粒子加热并达到极高的飞行速 度后沉积成涂层。由 于喷涂粒子飞行速度高且 火焰温度低 ( 一般约 3000 ∃ ) , 粉末在火焰中受
图 5 溶液先驱体等离子喷涂示意图
热时间比较短 , 目前在制备易于发生相变、 氧 化或分解的材料涂层方面获得广泛应用 , 特别适 合于制备碳化物、 硼化物等纳 米金属陶瓷涂层。 由于碳化物大小影响喷涂过程中的反应过程 , 当 碳化物尺寸下降 至纳 米尺度 时, 其 活性明 显增 强, 易于发生氧化、 还原、 脱碳等反 应, 使涂层中 碳化物的含量降低 , 影响涂层的耐磨性。 HVOF 的火焰速度高、 热能低 , 可有效抑制喷涂过程中 纳米碳化物的分解 , 因此成为制备纳米碳化物涂 层的重要方法。 2 . 4 冷喷涂 冷喷涂是利用高 压气体将粉末粒子高速撞 击并沉积于基 体表面 上形成 涂层的 一种 方法。 在冷喷涂过程中, 压缩气体通常是 H e 、 N 2、 空气 或者它们的混合物 , 在出口处压 力可达到 3 ~ 4 M Pa , 流速可达到超音速。纳米喷涂粉末被输送 到喷嘴前端的气流中, 立即被快速膨胀的气体所 加速 , 以强大的冲击力撞击基材后 , 产生塑性变 形并形成涂层。由于采用较低的喷涂温度 (一般
图 3 微米 /纳 米包覆法主要流程图
如何克服纳米颗粒的团聚是制备包覆粉的 一个难点。粘合剂根据粉料成分及粘性要求 , 一 般选用有机聚合物或溶胶类物质, 但要求其不给 包覆粉带来新的杂 质。该方法所制备的纳米喂 料具有包覆率高、 结合紧密、 流动性好等优点 , 目 前已用于制备纳米 微米复合改性陶瓷涂层
众所周知, 陶瓷涂层的脆性在很多场合制约 了其推广应用。与传统微米结构陶瓷涂层相比 , 纳米陶瓷涂 层由于晶 粒的 细化, 其界面 结合强 度、 断裂韧性等力学性能大为提高 , 而耐高温、 耐 磨损、 电绝缘、 抗腐蚀等性能也会有所改善。 纳米结构陶瓷涂层的制备存在一定的特殊 性。目前的 制备方法主要 有溶胶 凝胶、 物理气 相沉积 ( PVD) 、 化学气相沉积 ( CVD) 、 磁控溅射、 激光融覆、 热喷涂、 冷喷涂等方法。其中, 通过喷 涂法制备纳米涂层成为促使纳米陶瓷涂层获得 工程应用的有效途径 , 因而最具发展前景。 但纳米粉体一般不能直接用于喷涂 , 其主要 [ 1] 原因有两个 : 一是纳米陶瓷粉末粒径小、 质量 轻、 表面能高, 在喷涂时易团聚, 而且因为动量小, 纳米颗粒很难在基材上沉积并形成致密涂层; 二 是粉体活性高, 在喷涂过程中晶粒容易长大。为 克服上述困难, 一般需对纳米颗粒进行造粒处理, 使纳米陶瓷颗粒重新组装成微米级的喷涂喂料。
高性能陶瓷涂层的制备与应用

高性能陶瓷涂层的制备与应用高性能陶瓷涂层是一种非常有用的表面处理技术,可以为基材提供保护、改善表面性能的功能性材料。
它广泛应用于航空航天、汽车制造、电子设备等领域,对于提高产品的性能和寿命具有重要作用。
一、高性能陶瓷涂层的制备技术1. 物理气相沉积(Physical Vapor Deposition, PVD)物理气相沉积是一种常用的制备高性能陶瓷涂层的技术。
它通过将陶瓷材料蒸发、离子化,然后沉积在基材表面上。
这种方法可以控制材料的成分及微观结构,从而提高涂层的性能。
常见的PVD方法有蒸发、溅射、离子束沉积等。
2. 溶胶-凝胶法(Sol-Gel)溶胶-凝胶法是一种简单、低温、多功能的涂层制备方法。
其原理是通过在溶液中形成“溶胶”,然后经过凝胶化得到一种凝胶状的材料,最后将凝胶烧结成陶瓷涂层。
这种方法可以精确控制涂层的成分、纳米结构以及厚度,因此被广泛应用于光学涂层的制备。
二、高性能陶瓷涂层的应用领域1. 航空航天领域高性能陶瓷涂层在航空航天领域中有着广泛的应用。
例如,在航空发动机中,涂层可以提供高温氧化、腐蚀、磨损、摩擦的保护和减少摩擦阻力的功能。
此外,高性能陶瓷涂层还可用于航天器的热保护和飞行器的气动外形设计。
2. 汽车制造领域在汽车发动机的气缸内壁上应用高性能陶瓷涂层,可以降低摩擦和磨损,提高燃烧效率,减少油耗和排放物的排放。
此外,高性能陶瓷涂层还可用于汽车零部件的磨损和腐蚀保护。
3. 电子设备领域高性能陶瓷涂层在电子设备中也有很多应用。
例如,在集成电路制造中,采用陶瓷介电涂层可以提高电子器件的绝缘性能和可靠性。
此外,高性能陶瓷涂层还可用于显示屏的抗刮伤、反射控制以及导电层的保护。
三、高性能陶瓷涂层的发展趋势1. 纳米涂层技术随着纳米技术的发展,纳米涂层成为高性能陶瓷涂层的一个重要方向。
纳米涂层具有独特的物理、化学和力学性能,可以在不同领域发挥重要作用。
例如,纳米涂层可以增强材料的硬度、抗氧化性能和耐磨性,提高产品的使用寿命。
碳化硅材料的制备与应用

碳化硅材料的制备与应用碳化硅(SiC)作为一种高性能陶瓷材料,在工业和军事领域中具有广泛应用。
它的制备和应用已经引起了人们的广泛关注和研究。
一、制备1. 前驱体法前驱体法是一种重要的制备碳化硅的方法。
通过化学反应合成SiC前驱体,再将前驱体高温热解制备成SiC材料。
前驱体一般分为有机前驱体和无机前驱体两类。
有机前驱体主要指由含硅有机化合物和碳源化合物通过化学反应制备SiC前驱体的方法。
无机前驱体指的是由含硅无机化合物和化学还原剂合成的含硅混合物,然后通过高温处理得到SiC材料。
前驱体法制备的SiC材料具有高度纯度和卓越的性能。
2. 真空热解法真空热解法也是一种常见的制备SiC材料的方法。
在高温(约2000℃)下,将Si和C材料置于真空环境中,通过热解反应制备出碳化硅材料。
该方法制备出的SiC材料晶体结构完整、热稳定性强、机械性能高、导热性好。
二、应用碳化硅材料在工业和军事领域中广泛应用。
以下是一些典型的应用示例:1. 模具材料碳化硅材料因其高温强度和耐腐蚀性能优异,被广泛应用于模具材料的制备中。
例如,用SiC材料制作的玻璃模具,可以在高温环境下保持形状稳定性,使得玻璃制品具有优良的表面光洁度和精度。
2. 焊接材料碳化硅材料可用于高温下的托盘、炉辊和焊接工段等应用。
例如,用碳化硅陶瓷制成的托盘具有优良的机械性能和耐腐蚀性能,在高温烘干和烧结过程中能够保持长期稳定。
3. 功能陶瓷材料碳化硅材料在电子器件和实验仪器等领域中有广泛的应用。
例如,用SiC材料制作的红外吸收陶瓷,具有良好的热稳定性和强大的红外吸收能力,用于红外探测器、红外传感器等的制备。
4. 涂层材料碳化硅材料因其高硬度、高耐磨性和高温稳定性等物理性质优异,被广泛应用于涂层材料的制备中。
例如,用碳化硅薄膜涂层制作的机械零部件,具有优秀的摩擦学和生物相容性,可以用于人工心脏、骨骼等医学器械的制备。
总之,碳化硅材料的制备和应用已经得到了广泛的研究和应用。
高性能陶瓷材料的开发与应用研究
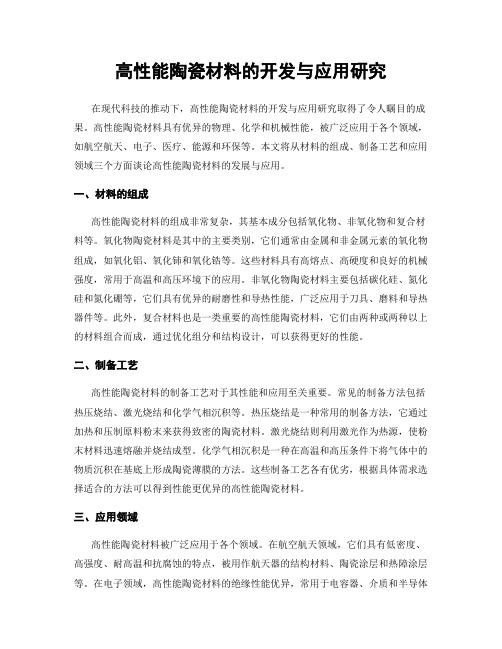
高性能陶瓷材料的开发与应用研究在现代科技的推动下,高性能陶瓷材料的开发与应用研究取得了令人瞩目的成果。
高性能陶瓷材料具有优异的物理、化学和机械性能,被广泛应用于各个领域,如航空航天、电子、医疗、能源和环保等。
本文将从材料的组成、制备工艺和应用领域三个方面谈论高性能陶瓷材料的发展与应用。
一、材料的组成高性能陶瓷材料的组成非常复杂,其基本成分包括氧化物、非氧化物和复合材料等。
氧化物陶瓷材料是其中的主要类别,它们通常由金属和非金属元素的氧化物组成,如氧化铝、氧化铈和氧化锆等。
这些材料具有高熔点、高硬度和良好的机械强度,常用于高温和高压环境下的应用。
非氧化物陶瓷材料主要包括碳化硅、氮化硅和氮化硼等,它们具有优异的耐磨性和导热性能,广泛应用于刀具、磨料和导热器件等。
此外,复合材料也是一类重要的高性能陶瓷材料,它们由两种或两种以上的材料组合而成,通过优化组分和结构设计,可以获得更好的性能。
二、制备工艺高性能陶瓷材料的制备工艺对于其性能和应用至关重要。
常见的制备方法包括热压烧结、激光烧结和化学气相沉积等。
热压烧结是一种常用的制备方法,它通过加热和压制原料粉末来获得致密的陶瓷材料。
激光烧结则利用激光作为热源,使粉末材料迅速熔融并烧结成型。
化学气相沉积是一种在高温和高压条件下将气体中的物质沉积在基底上形成陶瓷薄膜的方法。
这些制备工艺各有优劣,根据具体需求选择适合的方法可以得到性能更优异的高性能陶瓷材料。
三、应用领域高性能陶瓷材料被广泛应用于各个领域。
在航空航天领域,它们具有低密度、高强度、耐高温和抗腐蚀的特点,被用作航天器的结构材料、陶瓷涂层和热障涂层等。
在电子领域,高性能陶瓷材料的绝缘性能优异,常用于电容器、介质和半导体器件等。
在医疗领域,高性能陶瓷材料具有生物相容性和耐腐蚀性能,可用于人工关节、人工牙齿和医学检测器件等。
在能源领域,高性能陶瓷材料的高温稳定性和电化学性能优良,被广泛应用于固体氧化物燃料电池、储能器件和太阳能电池等。
陶瓷涂层工艺技术
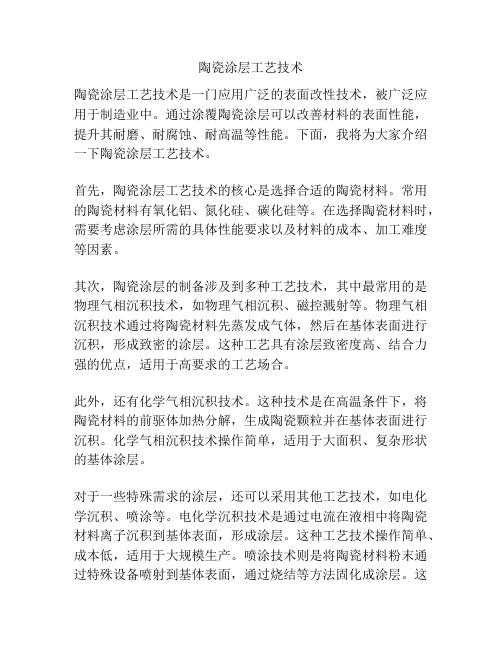
陶瓷涂层工艺技术陶瓷涂层工艺技术是一门应用广泛的表面改性技术,被广泛应用于制造业中。
通过涂覆陶瓷涂层可以改善材料的表面性能,提升其耐磨、耐腐蚀、耐高温等性能。
下面,我将为大家介绍一下陶瓷涂层工艺技术。
首先,陶瓷涂层工艺技术的核心是选择合适的陶瓷材料。
常用的陶瓷材料有氧化铝、氮化硅、碳化硅等。
在选择陶瓷材料时,需要考虑涂层所需的具体性能要求以及材料的成本、加工难度等因素。
其次,陶瓷涂层的制备涉及到多种工艺技术,其中最常用的是物理气相沉积技术,如物理气相沉积、磁控溅射等。
物理气相沉积技术通过将陶瓷材料先蒸发成气体,然后在基体表面进行沉积,形成致密的涂层。
这种工艺具有涂层致密度高、结合力强的优点,适用于高要求的工艺场合。
此外,还有化学气相沉积技术。
这种技术是在高温条件下,将陶瓷材料的前驱体加热分解,生成陶瓷颗粒并在基体表面进行沉积。
化学气相沉积技术操作简单,适用于大面积、复杂形状的基体涂层。
对于一些特殊需求的涂层,还可以采用其他工艺技术,如电化学沉积、喷涂等。
电化学沉积技术是通过电流在液相中将陶瓷材料离子沉积到基体表面,形成涂层。
这种工艺技术操作简单、成本低,适用于大规模生产。
喷涂技术则是将陶瓷材料粉末通过特殊设备喷射到基体表面,通过烧结等方法固化成涂层。
这种工艺技术适用于复杂形状的基体涂层。
最后,制备完涂层后,需要进行涂层性能的检测和评价。
常用的涂层性能测试方法有硬度测试、摩擦磨损测试、抗腐蚀性测试等。
通过这些测试可以评价涂层的性能是否满足要求,并根据需要进行优化。
综上所述,陶瓷涂层工艺技术是一门应用广泛的改性技术,可以显著提升材料的表面性能。
制备好的陶瓷涂层可以用于刀具、航空航天、冶金等领域。
随着科技的发展,陶瓷涂层工艺技术将会继续向更高性能、更复杂形状的涂层发展。
先进陶瓷的6种新型快速烧结技术
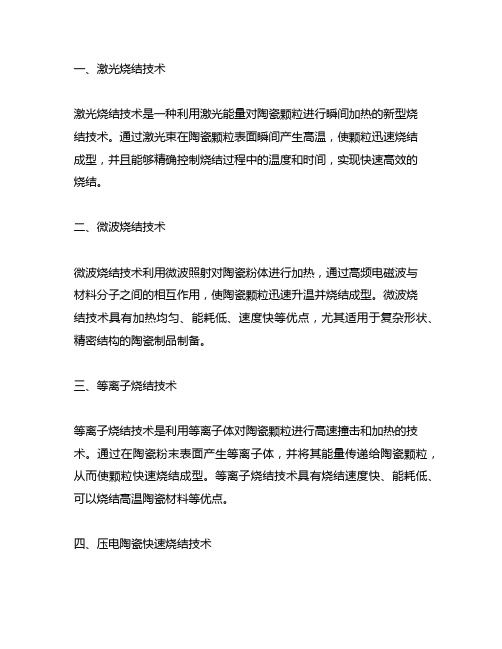
一、激光烧结技术激光烧结技术是一种利用激光能量对陶瓷颗粒进行瞬间加热的新型烧结技术。
通过激光束在陶瓷颗粒表面瞬间产生高温,使颗粒迅速烧结成型,并且能够精确控制烧结过程中的温度和时间,实现快速高效的烧结。
二、微波烧结技术微波烧结技术利用微波照射对陶瓷粉体进行加热,通过高频电磁波与材料分子之间的相互作用,使陶瓷颗粒迅速升温并烧结成型。
微波烧结技术具有加热均匀、能耗低、速度快等优点,尤其适用于复杂形状、精密结构的陶瓷制品制备。
三、等离子烧结技术等离子烧结技术是利用等离子体对陶瓷颗粒进行高速撞击和加热的技术。
通过在陶瓷粉末表面产生等离子体,并将其能量传递给陶瓷颗粒,从而使颗粒快速烧结成型。
等离子烧结技术具有烧结速度快、能耗低、可以烧结高温陶瓷材料等优点。
四、压电陶瓷快速烧结技术压电陶瓷快速烧结技术是一种利用压电作用对陶瓷颗粒进行紧致烧结的技术。
通过施加外加电场,使陶瓷颗粒表面发生压电效应,从而实现颗粒的紧致烧结,烧结速度大大提高,同时制备出的陶瓷制品密度高、性能卓越。
五、等离子喷涂技术等离子喷涂技术是一种利用等离子体对陶瓷粉末进行快速烧结成型的技术。
通过等离子喷涂装置将陶瓷粉末与等离子体混合后,在高温高速气流的作用下迅速烧结成型。
等离子喷涂技术不仅可以实现陶瓷材料的快速烧结,还能够制备出具有优异性能的陶瓷涂层。
六、电磁场烧结技术电磁场烧结技术是一种利用电磁场对陶瓷颗粒进行加热和烧结的技术。
通过在陶瓷颗粒周围建立强磁场或者强电场,使颗粒表面迅速加热并烧结成型。
电磁场烧结技术具有能耗低、烧结速度快、制品性能优异等特点,尤其适用于纳米陶瓷材料的制备。
先进陶瓷的快速烧结技术主要包括激光烧结、微波烧结、等离子烧结、压电陶瓷快速烧结、等离子喷涂和电磁场烧结等多种技术。
这些新型烧结技术都具有烧结速度快、能耗低、制品性能优异等特点,对于提高陶瓷制品的生产效率、降低生产成本、改善产品性能具有重要意义。
随着科技的不断发展和进步,相信这些先进陶瓷的新型快速烧结技术在未来会得到更广泛的应用,为陶瓷制造业带来新的发展机遇。
高性能陶瓷涂层——材料、技术及应用市场

1 主 要的陶瓷涂 层材料及 其应用
半个多世纪 以来+ 用陶瓷涂层改善金 属材料表面 性能所取得的成就在工业领域 中起 到了重要的作用。 通常, 陶瓷涂层一般用于改善金属材料的耐磨损 、 耐腐 蚀和抗高温等性能 , 使它们具有 陶瓷材料 的许多优 良 性能 。将 主要 成份 为 A 、 k 3 g 、 r 、 f 、 k ]A O一 o C2 H o M
[ 中图分类号 ]G7 3 '1 4 P 45
[ 标识 码】 文献 B
[ 文章编 号]01  ̄6[ o ) — 06 0 10 一 6o2 2o 01 — 2 o 2
0 引 言
高性 能 的陶瓷涂层 是 一种 具有较 大发 展前 景 的新 型高 温材 料 , 既具 有 高 温 无 机 材 料 的 耐 高 温 、 它 耐磨 损、 耐化学 腐蚀 等优 良 性能 , 又能保持 原有 底 材的结构
而 , 公 司也在 不断 出现 , 新 他们 使 用溶 胶. 凝胶 技术 、 激
图 1 19 97年北美的陶瓷涂层 市场
至陶瓷基体上 , 可形成一大类 具有优 良的综合技术性 能的新材料。切削工具的刀 片就是一个很好的例子,
【 收藕 日期]01 ̄2 204 - 5
维普资讯
22 月 O 年4 O
表 面 技 术
第3 第2 1 期
实验室。例如 , 全部重要 的合金刀具制造公司就在 自 家的实验室 内制造涂层 刀具 , 而大多数 的主要航空发 动机制造厂 家设立实验室是 为了维修和保养 自己的发 动机 。此 外 . 美 国的空军 、 军及船 舶 工业都 自己检 在 海 修他们 的发动机。就规模而言 , 高技术 陶瓷 的服务工 业有 的销售 额 高达 数 百 万美 元 , 的则 为小 作 坊 。近 有 1 来, 0年 由于航 天 和航 空 工 业 的衰 退 , 致 一些 涂 料 导 公司缩小其经营规模 , 甚至关闭, 但也出现 了一些公司 的合并 。可 以预计 , 来 这 一现 象 还将 继 续下 去 。然 将
纤维增强陶瓷基复合材料的制备工艺

纤维增强陶瓷基复合材料的制备工艺纤维增强陶瓷基复合材料因其卓越的力学性能和高温稳定性而在航空航天、汽车、能源等领域得到广泛应用。
制备这种复合材料的方法有很多,以下是其中几种常见的制备工艺:一、预制法预制法是一种制备纤维增强陶瓷基复合材料的方法,其基本步骤包括制备增强纤维预制体、浸渍陶瓷基体材料和烧结或热压等。
在预制法中,增强纤维预制体的制备是关键步骤之一。
根据所需的形状和尺寸,可以采用不同的编织技术,如机织、针织、非织造等方法制成预制体。
增强纤维的选择也至关重要,常用的有玻璃纤维、碳纤维、氧化铝纤维等。
浸渍陶瓷基体材料是将增强纤维预制体浸入陶瓷基体溶液中,使其均匀涂覆在纤维表面。
这一步可以借助浸渍、涂刷或喷涂等方法实现。
陶瓷基体材料的选择应与增强纤维相容,并具有高温稳定性、良好的力学性能和化学稳定性。
最后一步是烧结或热压,通过控制温度和压力,使陶瓷基体与增强纤维紧密结合在一起,形成致密的复合材料。
烧结或热压的条件应根据陶瓷基体和增强纤维的特性进行选择,以确保最佳的结合效果。
预制法的优点在于可以制备形状复杂的复合材料,适用于制备大型部件。
同时,增强纤维预制体的可设计性较高,可以根据实际需求调整纤维的排列和密度,从而优化复合材料的性能。
然而,预制法也存在一些局限性,如增强纤维预制体的制备较为复杂,且陶瓷基体与增强纤维之间的界面结合强度可能较低。
为了提高预制法纤维增强陶瓷基复合材料的性能,可以采取一些措施,如优化增强纤维预制体的制备工艺、选择合适的陶瓷基体材料和优化烧结或热压条件等。
此外,对界面进行改性处理也是提高复合材料性能的有效途径,如采用偶联剂、涂层等方法改善界面结合强度。
二、直接法直接法是一种将增强纤维直接混合到陶瓷基体中的制备工艺。
直接法是一种制备纤维增强陶瓷基复合材料的方法,其基本原理是将增强纤维直接与陶瓷基体材料混合在一起,然后通过热压或注射成型等方法制成复合材料。
在直接法中,首先将增强纤维(如碳纤维、玻璃纤维等)与陶瓷粉末混合在一起,形成均匀的混合物。
高性能陶瓷涂层的制备技术与发展趋势
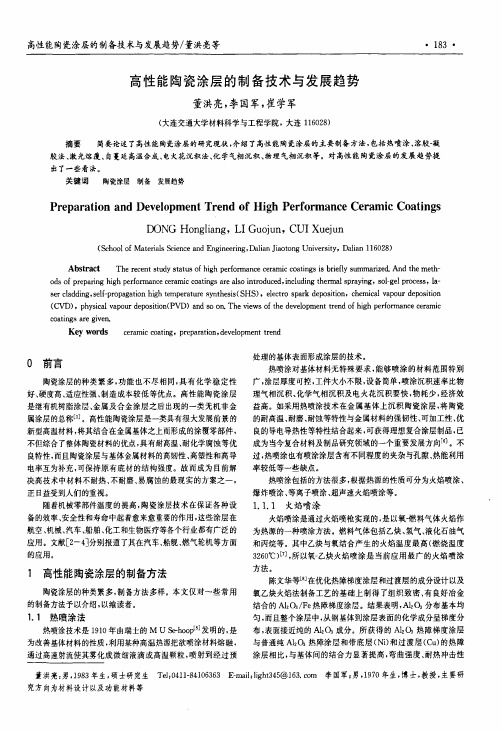
高性能陶瓷涂层的制备技术与发展趋势/董洪亮等183高性能陶瓷涂层的制备技术与发展趋势董洪亮,李国军,崔学军(大连交通大学材料科学与工程学院,大连116028)摘要简要论述了高性能陶瓷涂层的研究现状,介绍了高性能陶瓷涂层的主要制备方法,包括热喷涂、溶胶一凝胶法、激光熔覆、自蔓延高温合成、电火花沉积法、化学气相沉积、物理气相沉积等。
对高性能陶瓷涂层的发展趋势提出了一些看法。
关键词陶瓷涂层制备发展趋势P r epa r a t i on a nd D evel opm ent T r end of H i gh Per f or m ance C er am i c C oat i ngsD O N G H ongl i ang,L I G uoj un,C U I X uej un(School of M at er i a l s S c i e nce a nd E n gi n eer i n g,D al i an Ji aot ong U ni ve r si t y,D a l i a n116028)A bs t ract T h e r ece nt st udy s t a t us of hi gh per form ance ce ra m i c co at i ng s i s br i ef l y s u m m ari zed.A n d t he m et h—ods of pr epar i ng hi gh per form ance ce r am i c coat i ngs ar e al so i nt r oduc ed,i n cl udi ng t her m a l spr ayi ng,sol—gel pr oces s,l a—s e r cl ad di ng,sel f-pr opagat i on hi g h t e m per at ur e s ynt hes i s(SH S),e l e ct ro spar k de pos i t i on,c hem i ca l vapour dep osi t i on(C V D),physi c al va pour dep os i t i on(PV D)and SO on.T he vi e w s of t he deve l opm e nt t r e nd of hi gh per form ance ce ra m i ccoat i ngs ar e give n.K ey w or ds c er am i c coat i ng,pr epa r at i on,deve l opm ent t r end0前言陶瓷涂层的种类繁多,功能也不尽相同,具有化学稳定性好、硬度高、适应性强、制造成本较低等优点。
碳化硅反应烧结的工艺
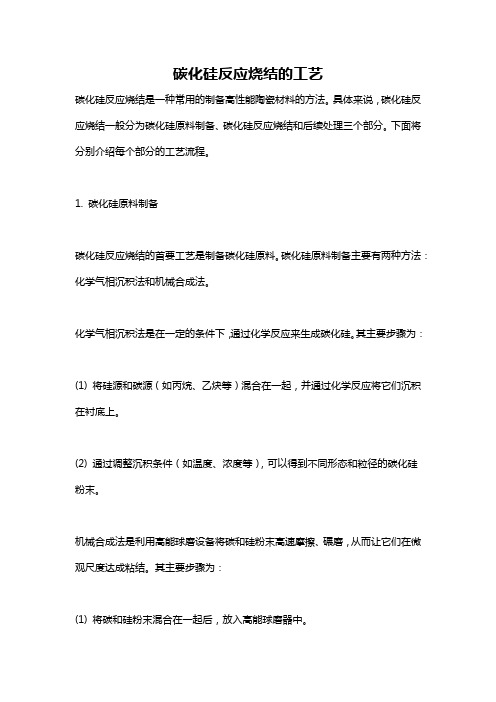
碳化硅反应烧结的工艺碳化硅反应烧结是一种常用的制备高性能陶瓷材料的方法。
具体来说,碳化硅反应烧结一般分为碳化硅原料制备、碳化硅反应烧结和后续处理三个部分。
下面将分别介绍每个部分的工艺流程。
1. 碳化硅原料制备碳化硅反应烧结的首要工艺是制备碳化硅原料。
碳化硅原料制备主要有两种方法:化学气相沉积法和机械合成法。
化学气相沉积法是在一定的条件下,通过化学反应来生成碳化硅。
其主要步骤为:(1) 将硅源和碳源(如丙烷、乙炔等)混合在一起,并通过化学反应将它们沉积在衬底上。
(2) 通过调整沉积条件(如温度、浓度等),可以得到不同形态和粒径的碳化硅粉末。
机械合成法是利用高能球磨设备将碳和硅粉末高速摩擦、碾磨,从而让它们在微观尺度达成粘结。
其主要步骤为:(1) 将碳和硅粉末混合在一起后,放入高能球磨器中。
(2) 调整球磨条件(如球磨时间、转速等),并加入球磨介质(如钢球)进行球磨。
(3) 通过调整球磨条件,可以得到不同尺寸和形态的碳化硅粉末。
2. 碳化硅反应烧结在碳化硅原料制备完成后,就可以进行碳化硅反应烧结的工艺了。
碳化硅反应烧结的主要工艺流程包括:混合、压制、硅碳反应和烧结。
(1) 混合:将碳化硅粉末与助烧结剂(如Al2O3、Y2O3等)混合在一起,并加入少量的粘结剂(如聚乙烯醇),使其变成可塑性较好的膏状物。
(2) 压制:将混合后的膏状物经过压制成型,一般采用等静压(CIP)或热等静压(HIP)等方法。
(3) 硅碳反应:将压制后的坯体在高温下与硅源进行反应,生成较高含量的SiC。
碳来源为碳化硅粉中残留的自由碳和助烧结剂。
(4) 烧结:将硅碳反应后的坯体进行高温烧结处理,使其变得致密且强度优良。
烧结温度一般在2200~2400之间,时间较长,可有助于进一步提高其强度和密度。
3. 后续处理在完成碳化硅反应烧结后,还需要进行一些后续处理工艺。
后续处理主要包括:抛光、涂层和烤结。
(1) 抛光:通过机械方式或电化学方式进行抛光,使其表面更为光滑。
过饱和浸渍法

过饱和浸渍法过饱和浸渍法是一种常见的材料表面处理方法,它可以使材料表面形成一层均匀、致密、具有良好性能的涂层。
该方法的原理是将材料浸泡在过饱和的溶液中,使其表面吸附上溶液中的物质,然后通过热处理或其他方法使其形成致密的涂层。
过饱和浸渍法的优点在于可以制备出具有高质量、高性能的涂层,而且制备过程简单、成本低廉。
该方法适用于各种材料的表面处理,如金属、陶瓷、玻璃等。
下面将详细介绍过饱和浸渍法的原理、制备过程及应用。
一、原理过饱和浸渍法的原理是利用溶液中的物质在材料表面形成一层致密的涂层。
当材料浸泡在过饱和的溶液中时,溶液中的物质会在材料表面形成一个临界核,然后逐渐生长形成涂层。
涂层的形成过程受到多种因素的影响,如溶液浓度、温度、浸泡时间等。
二、制备过程过饱和浸渍法的制备过程包括以下几个步骤:1.准备溶液:将所需的物质溶解在适量的溶剂中,制备出过饱和的溶液。
2.清洗材料:将待处理的材料进行清洗,去除表面的污垢和氧化物等。
3.浸泡材料:将清洗后的材料浸泡在过饱和的溶液中,使其表面吸附上溶液中的物质。
4.热处理:将浸泡后的材料进行热处理,使其表面形成致密的涂层。
5.冷却:将热处理后的材料进行冷却,使其表面涂层固化。
三、应用过饱和浸渍法在材料表面处理中有着广泛的应用。
以下是一些常见的应用领域:1.金属表面处理:过饱和浸渍法可以使金属表面形成一层致密、耐腐蚀的涂层,提高其耐腐蚀性能。
2.陶瓷表面处理:过饱和浸渍法可以使陶瓷表面形成一层致密、耐磨损的涂层,提高其耐磨性能。
3.玻璃表面处理:过饱和浸渍法可以使玻璃表面形成一层致密、耐磨损的涂层,提高其耐磨性能和透光性能。
4.纳米材料制备:过饱和浸渍法可以制备出具有高质量、高性能的纳米材料。
过饱和浸渍法是一种简单、有效的材料表面处理方法,具有广泛的应用前景。
随着科技的不断发展,该方法将会在更多的领域得到应用。
高强度金刚釉粒混合技术
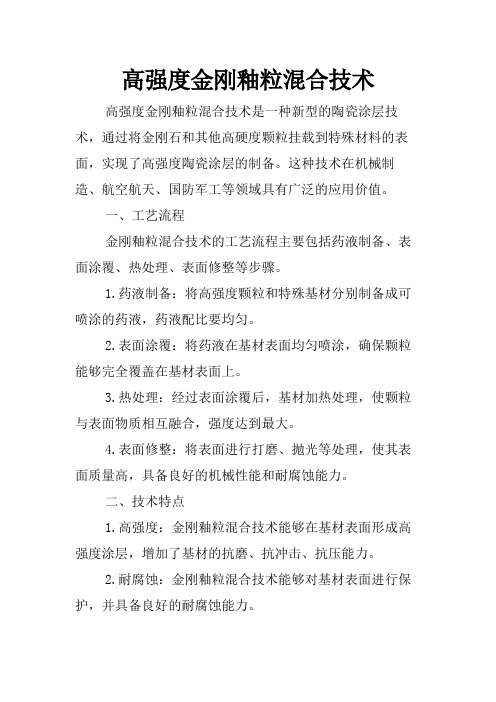
高强度金刚釉粒混合技术高强度金刚釉粒混合技术是一种新型的陶瓷涂层技术,通过将金刚石和其他高硬度颗粒挂载到特殊材料的表面,实现了高强度陶瓷涂层的制备。
这种技术在机械制造、航空航天、国防军工等领域具有广泛的应用价值。
一、工艺流程金刚釉粒混合技术的工艺流程主要包括药液制备、表面涂覆、热处理、表面修整等步骤。
1.药液制备:将高强度颗粒和特殊基材分别制备成可喷涂的药液,药液配比要均匀。
2.表面涂覆:将药液在基材表面均匀喷涂,确保颗粒能够完全覆盖在基材表面上。
3.热处理:经过表面涂覆后,基材加热处理,使颗粒与表面物质相互融合,强度达到最大。
4.表面修整:将表面进行打磨、抛光等处理,使其表面质量高,具备良好的机械性能和耐腐蚀能力。
二、技术特点1.高强度:金刚釉粒混合技术能够在基材表面形成高强度涂层,增加了基材的抗磨、抗冲击、抗压能力。
2.耐腐蚀:金刚釉粒混合技术能够对基材表面进行保护,并具备良好的耐腐蚀能力。
3.防护:金刚釉粒混合技术能够采取不同的涂覆方式,形成具备不同防护作用的涂层,满足不同工业领域的需求。
4.可靠性:金刚釉粒混合技术生产的陶瓷涂层具备高度可靠性,能够长期稳定工作,有效提高生产效率。
三、应用领域在机械加工、航空航天、国防军工等领域,金刚釉粒混合技术都具有广泛的应用价值。
1.机械加工领域:各种机械加工过程中经常需要对钢、铝等金属材料进行表面处理,增加其硬度、强度等机械性能。
金刚釉粒混合技术能够有效地针对这些要求进行表面涂层制备。
2.航空航天领域:在航空航天领域中,需要高强度、耐腐蚀、轻质的涂层材料。
金刚釉粒混合技术可以精细地制备出这种陶瓷涂层,以应对各种挑战。
3.国防军工领域:在国防军工领域中,需要使用具有高强度、抗冲击、抗磨、抗腐蚀等特性的涂层材料来保护作战装备。
金刚釉粒混合技术能够为此提供高效的涂层解决方案。
总之,高强度金刚釉粒混合技术的应用非常广泛,未来还有很大的发展空间。
随着科技的不断发展,金刚釉粒混合技术的涂层材料颗粒的种类、工艺制备方法、表面修整等技术将不断升级,为工业领域的新一代高性能涂层提供更优秀的解决方案。
- 1、下载文档前请自行甄别文档内容的完整性,平台不提供额外的编辑、内容补充、找答案等附加服务。
- 2、"仅部分预览"的文档,不可在线预览部分如存在完整性等问题,可反馈申请退款(可完整预览的文档不适用该条件!)。
- 3、如文档侵犯您的权益,请联系客服反馈,我们会尽快为您处理(人工客服工作时间:9:00-18:30)。
6
硫酸亚铁的络合
镀液的配制
原料铝粉的预处 理
施镀 等 后续处理
化学镀装置
7
硫酸亚铁的络合 定量称取硫酸亚铁、酒石酸钠及柠檬酸,分别用一定量的蒸馏水溶解。 充分溶解后将三者混合均匀,约20min后滴加一定体积的浓氨水调节PH 为碱性,一般PH>9 镀液的配制 定量称取亚磷酸钠,用一定量的蒸馏水完全溶解后,在剧烈搅拌下加 入制备的络合溶液中,然后用NaOH溶液调节PH值到规定值。将调节好 的镀液移入容量瓶,用蒸馏水调节镀液体积至规定值后,将镀液倒入烧 杯,加入少量明胶和硫脲,搅拌均匀。 原料铝粉的预处理 将1.2g氟化钠溶于100ml去离子水中;在完全溶解的氟化钠中加入 5~6ml 1mol/L的盐酸,搅拌均匀,配置成预处理液。将原料铝粉加入 预处理液中,室温下超声振荡5min;用酸度计测定其PH至10左右。
10
等离子喷涂系统
11
涂层断面结构示意图
12
图层中气孔形成过程示意图
涂层内缺陷产生示意图
13
四、陶瓷涂层制备的其他方法
1、溶胶—凝胶法
三种常用的溶胶工艺流程
14
1、溶液制备及溶胶化学
通常使用金属的烃氧化物(如四乙氧硅烷、硼酸三甲酯和乙醇钛)和金属 盐(如碳酸钡、硝酸镁和氯化铜等)作原材料。 当使用金属烃氧化物作原料时,将某种醇盐(即金属烃氧化物)和水加入 一种能互溶的溶剂中,并添加适宜的催化剂。醇盐发生水解反应,形成金属的 烃键(M-OH)化合物,方程式如下: M(OR)X + H2O = (RO)X—1M-OH + ROH 接着,该化合物的烃键与醇盐的配合体之间发生凝胶反应,如方程式 (RO)X-1M-OH + (OR)XM = (RO)X-1M—O—M(RO)X-1 + R(OH) 或者在两个烃基配合体之间发生凝聚反应,如下式:
化学镀具有以下特点:
(1)镀层非常的均匀,化学镀液的分散力接近100%,无明显地边缘效应, 几乎是基材(工件)形状的复制,因此特别适合复杂形状工件、腔体件、深 孔件、盲孔件、管件内壁等表面施镀。 (2)通过敏化、活化等前处理,化学镀可以在非金属(非导体)如玻璃、 塑料、陶瓷及半导体材料表面上进行。 (3)工艺、设备简单,容易实现。 (4) 化学镀是靠基材的自催化活性起镀,其镀层结合力好。
2、根据气相沉积时发生的化学反应,可分为两类:
(1) 热分解法 一般是在单温区炉中,在真空或惰性气氛下,将放置待镀工件的衬底,加热 至所需温度,然后导入反应性气体使之发生热分解,并在工件上沉积出固态镀层。 (2) 化学合成法 将待镀工件放置在反应器的衬垫上,加热衬件到一定的温度,使导入反应器 的两种或更多种气态反应物发生化学反应,并在取件基体表面形成固态镀膜的工 艺。
(RO)X-1M—OH + (RO)X-1M—OH = (RO)X—1M—O—M(RO)X-1 + HOH
这些反应形的结果形成一种“金属—氧—金属”键桥,它构成任何氧化物陶瓷 结构的骨架。凝聚过程继续进行,使金属—氧—金属的交联密度增大,直到产 生凝胶或沉淀。
15
2、溶胶的涂覆
一旦一种适宜而稳定的溶胶溶液被合成,一定要在溶胶发生胶凝之前进行 涂覆。涂覆方法有浸涂、旋转涂覆、喷涂和锟涂等。 浸渍是将基体浸入涂料溶液中,然后将基体从胶体中提出,将残液刮去或 让残液滴流,形成薄膜。 旋转涂覆是将涂液置于一个静态或缓慢旋转的基体上,然后基体迅速加速 旋转,转速达每分钟数千转,产生很大的离心力,从而使所有附着不良的涂液 被甩掉,在机体上留下一层薄薄的的陶瓷膜。 喷涂法是采用高压惰性气体通过喷枪喷嘴喷射溶胶溶液,将其雾化成气溶 胶,加速喷涂到基体上形成涂层。 锟涂法是用一个锟子将胶体溶液推滚涂覆到基体上形成涂层。
8
施镀
将配置的镀液放入恒温水浴中加热。把预处理后的铝粉加入镀液中,开 始搅拌烧杯中镀液,达到规定时间后停止搅拌。搅拌完成后,可把镀液放 到冷水中静置5~10min
后续处理 化学镀获得的复合粉体沉积到容器底部,须经清洗、烘干后,才可以进行 其他性能测试,步骤如下: ① 用抽滤装置抽滤,分离滤液和复合粉体。 ② 用蒸馏水和无数乙醇交替清洗粉体3~4次,直到中性。 ③ 将清洗干净的复合粉体置于真空干燥箱中,在80℃下干燥3h取出粉末。
19
3、CVD反应器
20
4、CVD技术特点
优点:
1、能够沉积非常高纯度的材料。 2、CVD沉积能获得外延的等轴晶体,能够生长大型单晶材料,具有独特的晶 体结构特性。 3、CVD沉积时一种非线性沉积工艺,其反应气体包围制件的各个部位,因而 可以在复杂形状制件的表面轮阔上均匀地沉积涂层,覆盖能力特别强。 4、与PVD沉积相比,CVD沉积设备比较简单。常压CVD沉积不需要真空系统, 即使低压CVD,其真空度亦不高。 5、具有仅次于等离子喷涂的搞的冲击能,涂层致密,能沉积到遮护位区。
9
2 3 2、等离子喷涂制备Fe-Al/Al O 梯度涂层 2 3 2O3 ④ Fe-Al +75%Al2O3 +50%Al
①Fe-Al
②Fe-Al +25%Al O
③ Fe-Al ⑤Al2O3
以Q235钢为基体材料,经表面预处理后,采用等离子喷涂设备,主气与送粉
气为氩气,副气为氢气,将不同成分的粉料依次喷涂在基体上,制备了FeAl/Al2O3梯度涂层。
在涂层形成过程中,粉体在等离子焰流的作用下被融化或部分熔化或达到软
化状态,发生反应形成金属间化合物,在等离子焰流的作用下被加速,当具有一 定速度的喷射粒子到达基体表面时,喷射粒子以一定的动能冲击基体表面,在产 生碰撞的瞬间,粒子的动能转化为热能传给基体,并与基体的粗糙表面紧密接触 产生变形,且迅速冷凝而收缩,呈扁平状黏结在基体的表面上。撞击后的凝固冷 却过程中,薄片粒子继续受外部环境和喷枪的热气流影响,随后下粒子撞击在前 一粒子上,形成第二层薄片,通过已形成的薄片向基材或涂层进行热传导。喷涂 粒子连续不断地冲击在基体表面上并产生上述过程。在粒子和表面之间和粒子与 粒子之间就会相互交错地黏结在一起而形成涂层。
23
3、重力分离(反应熔融附着)法燃烧合成内衬陶瓷涂层
工艺过程 依据铝热反应式: 2Al + Fe2O3 Al2O3 + 2Fe + 836 kJ/mol 将一定粒度的Al粉和Fe2O3粉按比例配置好后,装入混料机中充分混合,取出烘 干装入管内,加压使其达到一定密度。 在铝热剂的上部点火。在高反应热的作用下, 反应持续进行,反应速度在10mm/s左右,生 成AL2O3和Fe熔体,在铝热剂上部形成熔池。 由于相当大的密度差别,熔池发生重力分离, 密度大的Fe下沉,密度小的AL2O3浮于熔池上 部。因AL2O3的高熔点,液相停留时间短,随 着液面下降,AL2O3熔体与金属管内壁接触部 位首先冷却凝固并与金属管壁牢固结合,形 成陶瓷涂层内壁。随着反应界面的下降,就 在管内壁形成连续陶瓷涂层,直到全部管子 内壁形成内衬陶瓷涂层。密度大的Fe熔体和 多余的陶瓷熔体一起从管子下部孔处排除, 冷却后得到内村陶瓷涂层的复合弯管。
2、PVD气相沉积过程基本步骤
(1)首先是选择或合成合适的待镀材料 早先的物理气相沉积以蒸发镀单一 金属为主,如Cr、Cu、Ag、Zn、Fe、Co、Ni等。随着PVD技术的发展,欲制 特定成分的合金和化合物,则需将材料熔炼或合成,制成靶材料。 ① 将凝聚相(固相或液相)转变成气相蒸汽。 ② 沉积化合物时,作为该化合物的某些组分可以以气体或蒸汽形态引入真 空室中,以便各组分之间发生反应 (2) 将待镀材料的蒸汽传递到集体上。 (3) 随着蒸汽或气体的凝聚产生镀膜的生核或长大。
6、通过仔细选择化学反应物及化学反应,能够防止镀膜产生氢脆。 缺点:
1、沉积温度一般比PVD沉积高。 2、对反应物质或气体的纯度要求高。 3、为了获得高蒸汽压,有时采用金属卤化物、金属有机化合物作反应物质, 因而在沉积过程中会排出有害气体。 4、难于在热敏性材料(塑料)上用CVD沉积镀膜。 5、工件尺寸受反应室尺寸限制。
燃料 + 氧化剂 = 化合物 + 热量 燃烧合成反应通过不同的点火方式引燃,使燃料的氧化剂发生化学反应并释 放出大量的热量,产生稳态或非稳态的燃烧波或燃爆,使热量和反应迅速蔓延, 直至反应产物形成,达到无反应状态自动熄灭,完成固体燃烧合成的全过程。
22
2、离心法SHS燃烧合成内村陶瓷涂层
将铝热剂反应物(Fe2O3 + 2Al)置于钢 管内使钢管旋转,然后将铝热剂点燃。 铝热剂发生燃烧反应并放出大量的热, 使燃烧合成产物(Al2O3 + Fe)融化。 在离心力的作用下,由于铁的密度比氧 化铝大的多,因此熔体中铁和氧化铝发 生分离,铁水和钢管内壁首先熔焊在一 起,氧化铝凝聚在钢管内壁的最内侧, 形成内村Al2O3陶瓷涂层的复合钢管。
二、应
用
4
5
三、等离子喷涂法制备Fe-Al/Al2O3复合陶瓷涂层
1、化学镀法制备Fe包覆Al复合粉体
化学镀(electroless plating)又称无电解镀:
在无外加电源的情况下,采用合适的还原剂在具有催化活性的基体表 面将同一溶液中金属离子还原为金属原子后,依靠化学吸附作用在基体表 面形成牢固吸附且结构致密的镀层,若沉积金属对还原剂具有催化性,则 会不断地沉积出金属,实质上是自催化氧化还原反应。
高性能陶瓷涂层制备方法
1
目
录
2
一、高性能陶瓷涂层概述
高性能陶瓷是继有机树脂、金属及合金之间涌现出来的一类非金 属无机涂层总称。随着宇航、电子、军工等尖端科学技术的发展,近 半个世纪以来特别是20世纪90年代以来,得到了持续高速的发展。与 整体结构陶瓷材料相比,高性能涂层能有机地将金属材料的强韧性、 易加工性、导电导热性等和陶瓷材料的耐高温性、高耐磨、高耐腐等 特点结合起来,发挥两类材料的综合优势。且能够在钢铁有色金属、 玻璃、树脂板等多种基体材料上沉积,其中可用于制备陶瓷涂层的材 料品种也很多,包括各种氧化物和复合氧化物、碳化物、硼化物、氮 化物、硅化物以及金属陶瓷和金属间化合物。 但是,陶瓷深层也存在着其固有缺点:①陶瓷涂层塑性变形能力 差,对应力集中和裂纹敏感、抗热震和抗疲劳性能差;②陶瓷涂层材 料与金属材料的膨胀系数、热导率差别大,使用中产生不同的应力状 态,影响其使用寿命。③涂层与基体之间为机械嵌合或分子力结合, 存在结合强度不同。