陶瓷涂层技术在舰船上的应用
船用螺旋桨防腐防污纳米陶瓷涂层技术快速解决方案

2.1 设计方案 1) 针对螺旋桨的工作环境、基体材质、腐蚀介质和腐蚀形式等因素,采用固态金属陶瓷粉末材料制备
纳米陶瓷涂层,产品系列编号为 INF-8307,制备的纳米陶瓷涂层的突出特点有:生产工艺先进,不易老化, 使用安全,耐腐蚀性能优越,内减阻及耐磨性、流动性好,耐候性强,无毒、无害、无污染,施工规范, 用途广泛等。
0引言
螺旋桨是船舶的主要推进器,在使用周期内需长期沉浸于海水中,不仅会受到海水的腐蚀和冲刷,而 且会因海洋生物附着而污损,导致船舶的航速下降和燃油消耗增加[1]。需定期进坞对螺旋桨进行维修,这 不仅会增加维护、维修的费用,而且会威胁到船舶的安全航行。发达国家早已将新型材料技术应用于海工 装备的各个领域,将其作为快速提升装备性能的主要手段,在很多关键领域都形成了技术垄断。如何采用
7) 涂层指标:涂层表面均匀致密,无起皮、鼓包和裂纹等影响涂层使用的缺陷。涂层厚度为 150~200 m;涂层结合强度为 70~80 MPa;涂层孔隙率小于等于 1%;抗空泡剥蚀指标为 0.463 J≈4.0176n0.9R 条件下无空泡,无空泡剥蚀。
赵 健:船用螺旋桨防腐防污纳米陶瓷涂层技术快速解决方案
4) 制备的纳米陶瓷涂层具有表面能低和表面张力小等特征,可有效降低基体表面的黏附概率和结合 力;具有附着物增厚后的自清洁脱落功能,达到抵抗大量生物附着的作用。
5) 采用全自动热喷涂数控设备制备螺旋桨涂层,效率较高,涂层厚度均匀,一次成型,无需加热烘烤 干燥。
6) 在制备纳米陶瓷涂层过程中,对基体的热输入不超过 100℃,不会导致工件变形,不影响螺旋桨的 静平衡和安装使用。
海洋防腐领域应用的重防腐涂料主要有环氧树脂、聚氨酯、富锌底漆、丙烯酸、氯化橡胶、硫氧化合 物和聚硅氧烷等,其中环氧类防腐涂料所占市场份额最大,具体见表 1。
集装箱船总体设计中的船舶防污涂层选择

集装箱船总体设计中的船舶防污涂层选择在集装箱船总体设计中,船舶防污涂层的选择至关重要。
正确选择防污涂层可以有效延长船体的使用寿命,减少维护成本,提高航行效率。
本文将探讨集装箱船总体设计中船舶防污涂层选择的相关问题。
一、防污涂层的重要性船舶防污涂层是为了减少船体表面污物的附着,包括海藻、贝壳、藤壶等生物以及各种污泥、盐渍等,从而降低船体表面的摩擦阻力,提高船舶的航行速度和燃油效率。
选择适合的防污涂层可以大大减少船舶在水下运行过程中的阻力,降低燃油消耗,节约成本。
二、防污涂层的种类目前市面上常见的防污涂层主要包括硅藻泥、硅橡胶、聚硅氧烷等。
每种涂层都有其独特的特性和适用场景。
例如,硅藻泥防污涂层具有良好的附着力和抗污染能力,适用于海水浸泡和海上长期航行的船舶;硅橡胶涂层则具有较强的耐磨性和耐腐蚀性,适用于需要频繁进出港口的船舶。
三、选择原则在选择船舶防污涂层时,需要考虑以下几个因素:1. 航行环境:不同航行环境下的水质、水温和水动力学条件会对防污涂层的选择产生影响。
例如,在海水温度较高、海洋生物较为丰富的地区,需要选择具有良好抗生物附着能力的涂层。
2. 船舶类型:集装箱船作为远洋航行的大型船舶,其防污涂层需要具有较高的耐久性和耐磨性。
因此,在选择防污涂层时,需要考虑船舶的类型和使用环境。
3. 维护成本:不同类型的防污涂层在维护和更新方面的成本也会有所不同。
一般来说,价格较高的高性能涂层在使用寿命和维护周期上更具优势,可以降低维护成本。
四、结论集装箱船总体设计中的船舶防污涂层选择是一个复杂而重要的问题。
正确选择防污涂层可以保护船体,延长使用寿命,降低维护成本,提高航行效率。
在选择防污涂层时,需要综合考虑航行环境、船舶类型和维护成本等因素,以确保选择到最适合的涂层,从而保障船舶的安全运行和经济效益。
化学镀处理中的镀层在军工领域的应用

化学镀处理中的镀层在军工领域的应用随着现代科技的飞速发展,军事科技的发展也越来越快速和多样化。
在不同的军事领域,金属的材质和表面处理也有着不同的技术要求。
其中,化学镀处理技术是一种非常重要的表面处理方式,也是目前应用较为广泛的一种表面处理方式之一。
本文将从化学镀处理的原理、应用特点和军工领域的实际应用等角度进行探讨。
一、化学镀处理的原理化学镀处理是将金属物体浸泡在一定的酸性或碱性溶液中,通过一定的反应过程,在金属表面形成一层具有较好耐腐蚀性、表面平整、细致美观等性能优良的涂层的表面处理方法。
该方法通过控制不同反应条件,可形成锌、铬、铜、银、金、镍等不同金属的薄膜,镀层厚度一般在几微米到几百微米之间,能够有效地改善金属表面的耐腐蚀性、硬度、表面光滑度和美观度等性能。
化学镀处理的原理主要涉及电化学反应和化学反应两种反应机制。
一般情况下,镀层形成的过程是通过溶液中的某些离子(如铬离子、镍离子等)在电位的控制之下,与基体金属表面发生一定的反应,从而在金属表面形成一层不同金属离子的镀层。
这种反应过程属于纯化学反应。
二、化学镀处理的应用特点化学镀处理技术不仅可以应用于纯金属、合金、不锈钢等多种金属材料的处理,还可以处理其他物质,如塑料、陶瓷等。
其在军工领域的应用较为广泛,主要得益于其具有的以下优点:1. 镀层的制备工艺简单、成本低廉,能够进行大范围的批量生产,因此在军工领域大规模应用会更加经济和高效。
2. 镀层质量稳定,具有良好的表面平整度和均匀性,不仅具有优异的防腐、耐磨损、耐氧化等耐用性能,而且能够提升产品的美感和档次。
3. 化学镀处理中对溶液和操作环境要求较低,不必使用高温高压下进行人工板件,减少了环境污染和对人体的危害。
在军工领域中,这种优点尤为重要,因为工厂内环境可能比较恶劣或有一定的保密性要求,其环保要求也比较高。
4. 不同镀层膜的选择多样,可以根据不同的实际应用需求,定制不同材质和厚度的涂层,以满足不同的实际需求。
纳米陶瓷涂层的典型应用领域

纳米陶瓷涂层的一些典型应用领域:飞机发动机、燃气轮机零部件:热障涂层(TBC)被广泛地应用在飞机发动机、涡轮机和汽轮机叶片上,保护高温合金基体免受高温氧化、腐蚀,起到隔热、提高发动机进口温度和发动机推重比作用的一种陶瓷涂层材料。
8YSZ材料被用做热障涂层材料在军用发动机已应用几十年了,它的缺点是不能突破1200o C的使用温度,但现在军用发动机的使用温度已经超过1200o C,因此急需材料方面的突破。
另外,地面燃气轮机的热障涂层材料基本受制于国外,也亟待国产化。
国内外研究指出含锆酸盐的双陶瓷热障涂层被认为是未来发展长期使用温度高于1200o C的最有前景的涂层结构之一。
用纳米结构锆酸盐粉体喂料制备的纳米结构双陶瓷型n-LZ/8YSZ热障涂层的隔热效果明显好于其它现有涂层,与相同厚度的传统微米结构单陶瓷型8YSZ 热障涂层相比,隔热效果提高了70%。
而且,纳米结构的双陶瓷型涂层具有比其它两种涂层层更好的热震性能。
军舰船舶零部件:纳米结构的热喷涂陶瓷涂层早已广泛应用于美国海军装备(包括军舰、潜艇、扫雷艇和航空母舰)上的数百种零部件。
纳米结构陶瓷涂层的强度、韧性、耐磨性、耐蚀性、热震抗力等均比目前国内外商用陶瓷涂层材料中质量好、销量大的美科130涂层的性能显著提高。
有着高出1倍的韧性,高出4-8倍的耐磨性,高出1-2倍的结合强度和抗热震性能和高出约10倍的疲劳性能。
表1给出了纳米结构的热喷涂陶瓷涂层在美国海军舰船上的一些典型应用。
表1 一些美国海军舰船上应用的热喷涂纳米Al2O3/TiO2陶瓷涂层零部件船上系统基体材料使用环境水泵轴储水槽NiCu合金盐水阀杆主柱塞阀不锈钢蒸汽轴主加速器碳钢盐水涡轮转子辅助蒸汽碳钢油端轴主推进发动机青铜盐水阀杆主馈泵控制不锈钢蒸汽膨胀接头弹射蒸汽装置CuNi合金蒸汽支杆潜艇舱门不锈钢盐水流量泵燃料油碳钢燃料油柴油机、工程机械零部件:高性能纳米结构陶瓷涂层可以大幅度提高材料或零部件的硬度、韧性、耐磨性、抗腐蚀性和耐高温性能,因此可广泛应用于柴油发动机、工程机械等领域。
大型潜艇涂料选择与应用案例研究
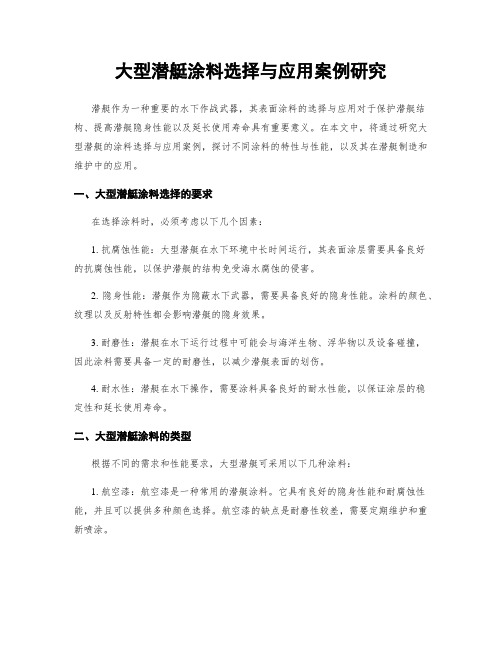
大型潜艇涂料选择与应用案例研究潜艇作为一种重要的水下作战武器,其表面涂料的选择与应用对于保护潜艇结构、提高潜艇隐身性能以及延长使用寿命具有重要意义。
在本文中,将通过研究大型潜艇的涂料选择与应用案例,探讨不同涂料的特性与性能,以及其在潜艇制造和维护中的应用。
一、大型潜艇涂料选择的要求在选择涂料时,必须考虑以下几个因素:1. 抗腐蚀性能:大型潜艇在水下环境中长时间运行,其表面涂层需要具备良好的抗腐蚀性能,以保护潜艇的结构免受海水腐蚀的侵害。
2. 隐身性能:潜艇作为隐蔽水下武器,需要具备良好的隐身性能。
涂料的颜色、纹理以及反射特性都会影响潜艇的隐身效果。
3. 耐磨性:潜艇在水下运行过程中可能会与海洋生物、浮华物以及设备碰撞,因此涂料需要具备一定的耐磨性,以减少潜艇表面的划伤。
4. 耐水性:潜艇在水下操作,需要涂料具备良好的耐水性能,以保证涂层的稳定性和延长使用寿命。
二、大型潜艇涂料的类型根据不同的需求和性能要求,大型潜艇可采用以下几种涂料:1. 航空漆:航空漆是一种常用的潜艇涂料。
它具有良好的隐身性能和耐腐蚀性能,并且可以提供多种颜色选择。
航空漆的缺点是耐磨性较差,需要定期维护和重新喷涂。
2. 橡胶漆:橡胶漆是一种具有良好耐腐蚀性能和隐身性能的涂料。
它可以提供良好的防水性能和抗微生物污染能力。
然而,橡胶漆的耐磨性较差,需要经常进行维护。
3. 聚氨酯涂料:聚氨酯涂料是一种多功能涂料,可以提供良好的耐腐蚀性能、耐磨性和耐水性。
它还具有较好的封闭性能,可以有效防止湿度和盐分对潜艇结构的侵蚀。
4. 氟碳涂料:氟碳涂料具有良好的耐腐蚀性能和耐水性,且不易吸附微生物和污垢。
它还具有较高的耐高温性能和耐紫外线性能,适用于潜艇在极端环境条件下的使用。
三、大型潜艇涂料应用案例研究以下是两个大型潜艇涂料选择与应用的案例研究:案例1:某型核潜艇表面涂料的选择与应用某型核潜艇使用了聚氨酯涂料作为其表面涂层,这是因为聚氨酯涂料具有优异的耐腐蚀性能和耐水性。
「船体重防腐涂料的使用现状和银圭纳米陶瓷材料的优势分析」

船体重防腐涂料的使用现状和银圭纳米陶瓷材料的优势分析北京银合汇新材料科技有限公司技术工程部主管徐萌1引言从20世纪80年代开始,我国造船业得到了迅猛的发展,占世界造船市场的份额不断扩大,造船业的飞速发展极大的存进了船舶涂料工业的发展,世界著名的船舶涂料生产厂商纷纷进驻中国,几乎都在中国建立了生产基地,设立销售网络。
在大型、多功能船舶方面,外资船舶涂料生产企业,特别是欧洲船舶涂料公司(如国际、佐敦、海虹、式玛)、日本企业(如中涂、关西)等厂商垄断船舶涂料市场,占有95%以上的市场份额。
我国船舶涂料制造商目前也已具备相当规模和技术实力,但整体技术水平仍落后于发达国家,再加上品牌意识不强,其主要市场为国内小渔船、内河船及国内舰艇等。
预计船舶涂料以约7%的速度增长,2013年船舶涂料产量将超过18万t。
2船舶涂料的基本现状船舶涂料是用于船舶及海洋工程结构物各部位,满足防止海水、海洋大气腐蚀和海洋生物附着及其他特殊要求的涂料的统称,随着新技术、新材料的出现,环保法规的日趋严厉,对一些原材料的限制使用,以及船东为减少维修费用、提高船舶的利用率,对防腐涂料的防腐期效要求更长。
因此,需要不断推出新型重防腐涂料来满足实际应用需要。
下面对船体不同部位使用的涂料种类进行分析。
2.1车间底漆当前以环氧富锌车间底漆、环氧铁红车间底漆和无机富锌车间底漆为主,其中无机富锌车间底漆更以其快干、长效、与其他涂料配套好的特点,在大型造船厂得到普遍应用;但此类富锌涂料在进行火工作业时,涂层烧损范围大,高温时易产生锌雾,损害作业人员的身体健康;目前国外开始采用低锌、高耐热的车间底漆,以减少锌雾,降低火工作业时车间底漆的烧损范围,从而降低二次除锈的工作量。
2.2船底及水线防腐涂料由于船底及水线区域涂层长期受海水的浸泡、流水的冲击、干湿交替、阴极剥离作用,并且要求与防污涂料之间有良好的层间附着力,所以传统的单组分氯化橡胶铝粉厚涂底漆、沥青防腐铝粉底漆因防腐效果差,逐渐被双组分环氧防腐涂料所取代,目前以环氧铝粉厚浆涂料、环氧厚浆沥青防腐涂料为主,如国内的HZ-1、HZ-2 环氧煤沥青等船底防腐涂料产品,但随着船东要求涂料的防腐期效越来越长,涂料应有良好的通用性,以及煤焦沥青的致癌嫌疑等原因,环氧煤沥青涂料逐步被纯环氧涂料所取代。
【专题】舰船常用腐蚀防护技术

【专题】舰船常用腐蚀防护技术舰船常见的腐蚀环境为海洋大气、海水、海生物、油污水环境,常见的腐蚀行为是不同金属之间接触产生的电化学腐蚀行为,常见的腐蚀部位为船体、管路、舾装件、设备和装置。
目前常用于舰船腐蚀防护的技术主要有:金属热喷涂、热浸镀、化学镀、涂塑、火焰喷塑、机械能助渗锌、重防腐蚀涂层保护、牺牲阳极保护、外加电流阴极保护等技术。
文/裘达夫海军舰船装备腐蚀防护研究试验中心金属涂镀层技术金属热喷涂热喷涂(锌、铝、锌铝合金)技术是表面工程学的重要组成部分,它是一种表面强化和表面改性的技术,可以使基体表面具有耐磨、耐蚀、耐高温氧化、电绝缘、隔热、防辐射、减磨和密封等性能。
热喷涂技术工艺方法有很多种,其中应用于防腐蚀领域的方法主有火焰喷涂、电弧喷涂、等离子喷涂、爆炸喷涂、超音速喷涂(HVOF)等技术。
金属热喷涂对喷涂用的金属材料有具体的要求,锌应符合GB 470- 83中的Zn-1的质量要求,Zn≥99.99%;铝应符合GB 3190-82 中的L2的质量要求,Al≥99.5%;通常锌铝合金的成分为Zn- Al15,即其合金成分是Zn为85%,Al为15%,其中Zn和Al的成分应分别符合上述标准中所规定的纯度。
目前在舰船防腐蚀工程中应用最多的热喷涂技术主要有火焰喷涂、电弧喷涂。
电弧喷涂电弧喷涂是利用电弧产生的高温作热源,熔化两根作为电极的金属材料,在高压气体雾化后喷涂到被喷涂表面,形成具有防腐蚀性能金属涂层的方法。
电弧喷涂需要喷涂用电源、送丝机构、喷枪(某些喷枪上自带送丝机构)以及连接喷枪与电源之间的电源线。
根据电弧喷涂机的要求,选择符合标准的相应直径(如2mm或3mm)喷涂金属丝材,调整适当的喷涂电流、电压和一定压力的压缩气体,喷涂得到所需的金属涂层,喷涂的涂层孔隙率低,与基体材料的结合强度高。
线材火焰喷涂线材火焰喷涂是利用氧乙炔燃烧火焰作热源,压缩空气带动喷枪内的驱动机构,通过送丝滚轮将线材连续地通过喷嘴中心孔送入火焰,在火焰中被加热熔化,并在压缩空气雾化成细微的颗粒后喷涂到待喷表面。
RKT润滑抗磨陶瓷涂层简介

高含量陶瓷涂层技术是机械表面抗磨-防腐的革新技术与单纯的摩擦損傷、或腐蝕損傷相比较,摩擦-腐蝕損傷对装备(包括各种机械设备、机件在内,以下相同)的危害更严重,预防摩擦-腐蝕損傷的技术难度更大。
最新研究结果表明,高含量陶瓷涂层技术,是机械表面抗磨-防腐的革新技术。
它能显著地提高装备在摩擦-腐蝕恶劣环境中使用的可靠性、安全性和寿命。
我国航空装备科研人员成功地研制出GKF高含量抗磨-防腐陶瓷塗层(系列),简称GKF高含量陶瓷塗层(系列)。
它的综合性能优良,达到或超过国际市埸上同类产品的先进水平。
1.摩擦-腐蝕損伤的危害在恶劣环境中工作的装备很容易发生各种类型的摩擦損傷、或腐蝕損傷、或摩擦-腐蝕損傷。
其危害十分严重。
“據1998年的統計,在世界主要工業國家由於磨損、腐蝕造成的損失約占國民經濟总產值的3%-5%左右”。
例如,選煤礦業机械的工作環境十分惡劣,選煤機的主要部件-旋流器發生摩擦-腐蝕損傷的現象就非常严重。
据統計,2001年,我國3万噸以上規模的選煤厂有1584個,每年僅旋流器這一种機件损伤所造成的经济损失就高达約有15億人民幣。
又如,煤电厂的冷却水塔因摩擦-腐蚀损伤严重经常需要仃用进行维修,每年造成的经济损失也相当可观。
再如,如果飞机发动机的零、部件一旦发生这种损伤,则可能导致机毁人亡的严重飞行事故。
傳統的防磨損技术或防腐蚀技术,很难满足在恶劣的摩擦-腐蝕环境中使用的机械表面抗磨-防腐的实际需求。
因此,研究机械表面抗磨-防腐新技术具有重要的现实意义。
2.傳統的机械表面防磨損技术傳統的机械表面防磨損技术有多种类型。
它们的主要缺点是:不适用于现埸直接施工,施工难度大,耐磨性一般。
下面介绍几种常用的传统防磨损技术:①铸石技术铸石技术是采用铸石作为表面耐磨材料的一种表面防磨损技术。
以一种天然岩石材料为主要材料,经配料、熔化、成型、结晶和退火等多道工艺制成的耐磨损产品。
缺點:笨重、易碎裂,运送及施工不便,特殊形狀需要定制,成本高。
精细化涂层技术在军工装备中的应用研究
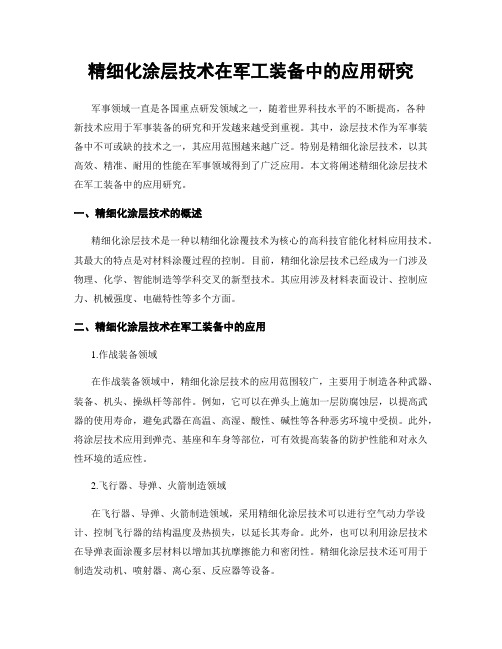
精细化涂层技术在军工装备中的应用研究军事领域一直是各国重点研发领域之一,随着世界科技水平的不断提高,各种新技术应用于军事装备的研究和开发越来越受到重视。
其中,涂层技术作为军事装备中不可或缺的技术之一,其应用范围越来越广泛。
特别是精细化涂层技术,以其高效、精准、耐用的性能在军事领域得到了广泛应用。
本文将阐述精细化涂层技术在军工装备中的应用研究。
一、精细化涂层技术的概述精细化涂层技术是一种以精细化涂覆技术为核心的高科技官能化材料应用技术。
其最大的特点是对材料涂覆过程的控制。
目前,精细化涂层技术已经成为一门涉及物理、化学、智能制造等学科交叉的新型技术。
其应用涉及材料表面设计、控制应力、机械强度、电磁特性等多个方面。
二、精细化涂层技术在军工装备中的应用1.作战装备领域在作战装备领域中,精细化涂层技术的应用范围较广,主要用于制造各种武器、装备、机头、操纵杆等部件。
例如,它可以在弹头上施加一层防腐蚀层,以提高武器的使用寿命,避免武器在高温、高湿、酸性、碱性等各种恶劣环境中受损。
此外,将涂层技术应用到弹壳、基座和车身等部位,可有效提高装备的防护性能和对永久性环境的适应性。
2.飞行器、导弹、火箭制造领域在飞行器、导弹、火箭制造领域,采用精细化涂层技术可以进行空气动力学设计、控制飞行器的结构温度及热损失,以延长其寿命。
此外,也可以利用涂层技术在导弹表面涂覆多层材料以增加其抗摩擦能力和密闭性。
精细化涂层技术还可用于制造发动机、喷射器、离心泵、反应器等设备。
3.海洋装备领域在海洋装备领域中,精细化涂层技术被广泛应用于制造各种海洋设备,如船舶、水下机器人、海底井设备等。
例如,将防腐涂层应用在海洋船舶上,可以避免海洋环境的侵蚀和氧化,延长船体的使用寿命。
三、精细化涂层技术的优势1.性能稳定在精细化涂层技术中,涂覆过程受到高精、高控的专业技术支持,涂层的厚度、成分和结构都能够在非常精准的范围内控制,从而能够保证涂层的性能稳定,并且避免涂层在长时间的使用过程中发生退化。
纳米陶瓷涂层在舰船装备上的应用研究
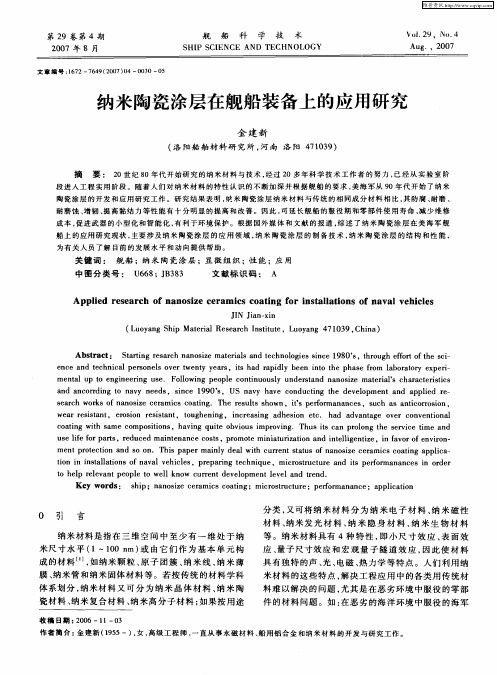
船 上 的 应用 研 究 现 状 , 要 涉 及 纳 米 陶 瓷 涂 层 的 应 用 领 域 , 米 陶 瓷 涂 层 的 制 备 技 术 , 米 陶 瓷 涂 层 的结 构 和 性 能 , 主 纳 纳
me t lu o e gne rn s . F l wi g p o l o tn o sy u d rtn a sz mae il ha a trsis n a p t n i e g u e i o l n e p e c n i u u l n e sa d n no ie o tra’ c r ce tc S i
维普资讯
第2 9卷第 4期
2 0 年 8月 07
文童 编 号 : 6 2— 6 9 2 0 ) 4— 0 0— 5 1 7 7 4 (0 7 0 0 3 0
舰
船
科
学
技
术
Vo . 1 29,No 4 .
SHI CI P S ENCE AND TECHNOL OGY
J N in xn I Ja — i
( u yn hp M t a R sac ntue u yn 7 0 9 C ia L oa gS i ae l eerhIs tt,L oa g4 13 , hn ) i r i
Absr c S atn e a c a o ie mae asa d t c n lg e i c 9 0’ hr u h efr ft e s i t a t: trig r s r h n n sz tr l n e h o o is sn e 1 8 S.t o g f t o c— i o h e c n e h i a ro e so e we t e r n e a d tc n c lpe s n l v rt n y y a s,isha a i l e n i t h ha e fo lb r tr x r— t d r p d y b e no t e p s r m a o a o y e pe i
热喷涂制备氧化钛复合涂层研究现状

第30卷第2期江苏理工学院学报JOURNAL OF JIANGSU UNIVERSITY OF TECHNOLOGY Vo l.30,No.2 Apr.,20242024年4月陶瓷涂层因其耐磨损、耐高温及耐腐蚀等优点,在海洋舰船、航空航天、能源运输、汽车装备等领域具有广泛的应用前景。
然而,单一物相的陶瓷涂层通常脆性较大、结构缺陷较多,在服役过程中易破裂和剥落,其应用受到限制[1]。
目前,陶瓷涂层的性能改善手段主要有优化制备工艺参数和多相添加。
通过添加其他相,可以在保持原物相优异性能的同时,使涂层拥有多种不同的性能,减少孔隙与微裂纹等缺陷含量,拓展其应用范围[2]。
氧化钛复合涂层是指将氧化钛颗粒与其他材料进行复合,由于氧化钛颗粒具有较好的流动性及相容性,因此,作为第二相添加至涂层中可以提高涂层的韧性、硬度、耐磨性和耐腐蚀性能[3]。
热喷涂技术是一种表面强化和修复技术,具有工艺简单、成本低、灵活性高等优点,被广泛应用于零件表面以提升其耐磨损、耐腐蚀、耐高温等性能[4-5]。
近年来,采用热喷涂技术制备氧化钛复合涂层获得了广泛关注,一些学者针对涂层相添加、粉体结构设计等方法,研究了不同复合涂层的综合服役性能及二氧化钛对涂层性能的影响机理。
本文根据氧化钛复合涂层使用的材料种类,将其分为氧化物复合涂层、碳及碳化物复合涂层。
基于此,分别从氧化钛复合涂层、氧化物复合涂层、碳及碳化物复合涂层的制备三个方面,系统综述了国内外在有关氧化钛陶瓷涂层耐磨、耐腐蚀性能强化方面的研究情况,并对氧化钛复合涂层的原理和性能优化方法进行了介绍与分热喷涂制备氧化钛复合涂层研究现状吴海东1,燕玉林2,崔方方1,丛孟启1,高祥涵1,楚佳杰1,韩冰源1(1.江苏理工学院汽车与交通工程学院,江苏常州213001;2.军事科学院战略评估咨询中心,北京100091)摘要:氧化钛复合涂层具有优异的耐磨、耐腐蚀性能,常用于关键机械零部件的表面防护。
金属材料和陶瓷材料

金属陶瓷材料金属材料和陶瓷材料是我们在航空航天、船舶、汽车、日用等行业十分常见的材料,已经融入到我们的方方面面。
金属陶瓷作为金属材料和陶瓷材料研发的一种新型复合材料,兼具金属和陶瓷材料的某些优点,受到科研工作者的广泛关注,是材料领域的研究重点之一。
近年来,金属陶瓷的研究成果越来越多,新品种不断出现,理论体系也日趋成熟。
图1 金属陶瓷航空铝材质手机外壳一、金属陶瓷简介金属陶瓷,是一种由金属或合金和一种或几种陶瓷相所组成的非均质的复合材料,其中后者约占15%~85vol%,当陶瓷含量高于50vol%时,亦可称为陶瓷-金属复合材料。
金属陶瓷(Cermet/Ceramet)是由陶瓷(Ceramics)中的词头Cer/Cera与金属(Metal)中的词头Met结合起来构成。
金属陶瓷的理想结构是弥散且均匀分布的陶瓷颗粒表面被连续薄膜形态的金属相包裹,其中陶瓷相承受机械应力和热应力,通过连续的金属相分散,金属相因呈薄膜状包裹再陶瓷颗粒表面而得到强化,故金属陶瓷作为介于高温合金和陶瓷材料之间的一种高温材料,具有兼顾金属的高韧性、可塑性和陶瓷的高熔点、耐腐蚀和耐磨损等性能。
图2 常见材料化学稳定性与抗热冲击性汇总图3 陶瓷材料和金属材料杨氏模量及断裂强度对比二、金属陶瓷的发展史第一代:二战期间,德国以Ni粘结TiC生产金属陶瓷;第二代:60年代美国福特汽车公司发明的,它添加M o到Ni粘结相中改善TiC和其它碳化物的润湿性,从而提高材料的韧性;第三代:金属陶瓷则将N元素引入合金的硬质相,改单一相为复合相,形成Ti(C,N)固溶体;20世纪80年代,硼化物陶瓷由于具有很高的硬度、熔点和优良的导电性、耐腐蚀性,成为最有发展前途的金属陶瓷。
图4 TiC金属陶瓷组织结构示意图三、金属陶瓷材料匹配的原则1、相间热力学匹配:金属相的加入大幅降低陶瓷的烧结温度,改善期脆性。
纯TiC材料因其烧结温度在2000℃高温,晶粒生长较快,致密度和性能较低,加入Ni-Mo金属作为粘接相,形成TiC-Ni-Mo陶瓷金属,可在1300℃烧结,且致密度和机械性能均有提高,详见图5;图5 Ni-Mo金属含量对TiC-Ni-Mo陶瓷金属断裂强度的影响2、相容性:包括陶瓷与金属材料的热膨胀系数、导热系数、弹性模量等的相容性,如两者热膨胀系数相差过大,造成的内应力会降低材料的热稳定性;图6 Ag金属纳米线、氧化铝陶瓷复合超材料薄膜3、相间热稳定性:金属相与陶瓷相之间无剧烈的化学反应。
高温陶瓷涂层在航空航天喷涂的前景

高温陶瓷涂层在航空航天喷涂的前景随着科技的飞速进步和全球航天航空产业的蓬勃发展,高性能材料的应用成为了推动这一领域持续创新的关键因素。
高温陶瓷涂层作为航空航天领域不可或缺的先进材料之一,其在提升发动机效率、延长零件寿命、减轻结构重量等方面的显著优势,使其在航空航天喷涂领域的前景日益凸显。
本文将从六个方面深入探讨高温陶瓷涂层在航空航天喷涂的广阔前景。
一、技术创新推动性能升级高温陶瓷涂层的持续研发是推动其在航空航天领域应用的关键。
近年来,随着纳米技术、复合材料科学及计算材料学的发展,新型高温陶瓷涂层不断涌现,这些涂层不仅耐热性更强,而且具有更好的抗氧化性和抗腐蚀性。
例如,YSZ(氧化钇稳定的氧化锆)和MCrAlY(M代表镍、钴等金属元素)涂层因优异的热障性能和环境耐受性,在涡轮叶片、燃烧室等高温部件上的应用日益广泛,显著提高了发动机的工作温度上限,进而提升了燃料效率和推力。
二、轻量化需求促进材料革新在航空航天领域,减轻飞行器重量是永恒的追求,这直接关系到燃油经济性和飞行性能。
高温陶瓷涂层因密度低、强度高的特点,成为实现结构轻量化的重要途径。
通过精密的喷涂技术,可以在保持或增强原有部件强度的同时,有效减轻重量,这对于飞机和等航天器而言意义重大。
此外,轻质陶瓷基复合材料的开发,如碳化硅基陶瓷涂层,不仅减轻了重量,还提高了整体结构的热稳定性和抗冲击性。
三、环境适应性与长寿命设计航空航天设备常面临极端恶劣的运行环境,如高速气流、高温、高压及空间辐射等,这对材料的耐用性提出了极高的要求。
高温陶瓷涂层因其出色的环境适应性和长寿命设计而受到青睐。
它们能有效抵抗高温氧化、热腐蚀和磨损,显著延长发动机核心部件的使用寿命,减少维修频次,降低整体运营成本。
特别是在太空探索任务中,耐久可靠的涂层更是确保航天器安全稳定运行的基础。
四、成本效益分析与经济性考量尽管高温陶瓷涂层的研发和应用初期较大,但其长期经济效益明显。
通过提高发动机效率和延长部件寿命,减少了维护和更换频率,从而在整体上降低了运营成本。
先进陶瓷材料 在航空航天领域 的应用与发展趋势 探讨

先进陶瓷材料在航空航天领域的应用与发展趋势探讨航空航天领域作为科技进步的标志之一,对材料的性能要求极高。
其中,先进陶瓷材料以其出色的物理、化学和机械性能在航空航天领域中得到广泛应用。
本文将讨论先进陶瓷材料在航空航天领域应用的现状和未来发展趋势。
先进陶瓷材料在航空航天领域具有许多独特的优势。
首先,先进陶瓷材料具有出色的高温性能。
高强度、高硬度和耐高温的特性使得它们能够承受极端的温度和压力环境,这在航空航天领域中尤为重要。
其次,先进陶瓷材料具有出色的耐腐蚀性能。
在航天器的推进系统和结构材料中,陶瓷材料可以抵御氧化、磨损、腐蚀和压力等不良环境的侵蚀。
此外,先进陶瓷材料还具有轻量化的特点,可以减轻航天器的重量,提高其载荷能力和燃料效率。
目前,先进陶瓷材料在航空航天领域主要应用于以下几个方面。
首先是发动机部件。
陶瓷复合材料被广泛应用于航空发动机的高温结构部件中,如涡轮叶片、涡轮转盘和燃烧室壁等。
这些部件要求耐高温、耐磨损和耐腐蚀,而陶瓷材料的优异性能正好能够满足这些要求。
其次是导向系统。
陶瓷轴承和磁悬浮技术的应用使得航天器能够在高速、高温和高精度环境下稳定运行。
再次是热防护材料。
陶瓷热防护材料可以接受高热流密度,确保航天器在大气层再入过程中不受热烧灼或损坏。
最后是航空器外壳和结构件。
陶瓷复合材料可以减少航空器的重量,并提供良好的抗冲击和抗磨损性能,以确保航天器的安全和可靠性。
然而,尽管先进陶瓷材料在航空航天领域中的应用已经取得了一定的成就,但仍然面临一些挑战,限制了其进一步发展。
首先是制造工艺。
陶瓷材料的制造过程较为复杂,包括高温烧结、成型和精加工等步骤,制造成本高且易造成材料的裂纹和缺陷。
其次是材料的可靠性和寿命。
陶瓷材料容易出现疲劳和开裂等问题,影响其在航空航天领域的应用。
此外,陶瓷材料与金属材料之间的界面问题也需要得到解决,以改善不同材料之间的粘结力和相容性。
为了克服这些挑战,先进陶瓷材料在航空航天领域的发展趋势主要有两个方向。
军用涂料和涂层研究与应用进展
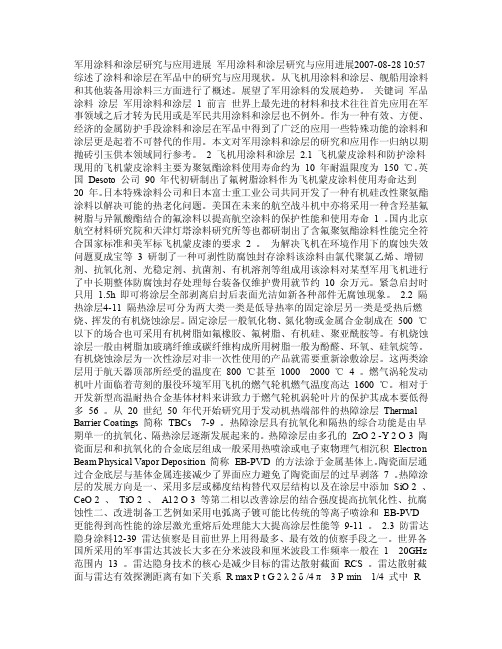
军用涂料和涂层研究与应用进展军用涂料和涂层研究与应用进展2007-08-28 10:57综述了涂料和涂层在军品中的研究与应用现状。
从飞机用涂料和涂层、舰船用涂料和其他装备用涂料三方面进行了概述。
展望了军用涂料的发展趋势。
关键词军品涂料涂层军用涂料和涂层1 前言世界上最先进的材料和技术往往首先应用在军事领域之后才转为民用或是军民共用涂料和涂层也不例外。
作为一种有效、方便、经济的金属防护手段涂料和涂层在军品中得到了广泛的应用一些特殊功能的涂料和涂层更是起着不可替代的作用。
本文对军用涂料和涂层的研究和应用作一归纳以期抛砖引玉供本领域同行参考。
2 飞机用涂料和涂层2.1 飞机蒙皮涂料和防护涂料现用的飞机蒙皮涂料主要为聚氨酯涂料使用寿命约为10 年耐温限度为150 ℃。
英国Desoto 公司90 年代初研制出了氟树脂涂料作为飞机蒙皮涂料使用寿命达到20 年。
日本特殊涂料公司和日本富士重工业公司共同开发了一种有机硅改性聚氨酯涂料以解决可能的热老化问题。
美国在未来的航空战斗机中亦将采用一种含羟基氟树脂与异氰酸酯结合的氟涂料以提高航空涂料的保护性能和使用寿命1 。
国内北京航空材料研究院和天津灯塔涂料研究所等也都研制出了含氟聚氨酯涂料性能完全符合国家标准和美军标飞机蒙皮漆的要求2 。
为解决飞机在环境作用下的腐蚀失效问题夏成宝等3 研制了一种可剥性防腐蚀封存涂料该涂料由氯代聚氯乙烯、增韧剂、抗氧化剂、光稳定剂、抗菌剂、有机溶剂等组成用该涂料对某型军用飞机进行了中长期整体防腐蚀封存处理每台装备仅维护费用就节约10 余万元。
紧急启封时只用 1.5h 即可将涂层全部剥离启封后表面光洁如新各种部件无腐蚀现象。
2.2 隔热涂层4-11 隔热涂层可分为两大类一类是低导热率的固定涂层另一类是受热后燃烧、挥发的有机烧蚀涂层。
固定涂层一般氧化物、氮化物或金属合金制成在500 ℃以下的场合也可采用有机树脂如氟橡胶、氟树脂、有机硅、聚亚酰胺等。
纳米材料在舰船涂料中的应用前景广阔

纳米材料在舰船涂料中的应用前景广阔纳米材料在海军舰船装备领域中有很大的应用前景,舰船涂料是其中一个重要的应用方向。
一、隐身涂层舰船涂料的一个非常重要的作用是作为舰船隐身材料的一部分,纳米材料的特殊效应为隐身材料提供新的途径和新的吸波机理。
据研究,纳米多层复合膜( 包括多层颗粒膜、无机/有机多层复合膜、金属/电介质多层复合膜等) 有望成为制备高强度和具有一定频宽微波吸收的新型材料。
美国某公司将一种超细陶瓷球粉体用于装备的保护涂层中,可提供装备的隐形能力,还可以涂覆在电子设备上以对付电子干扰。
对雷达波的吸收率可达99%,而厚度仅是微米级。
纳米氧化铝、氧化铁、氧化硅和氧化钛的复合粉体与高分子纤维结合对中红外光波段有很强的吸收性能,这种复合体对该波段的红外探测器有很好的屏蔽作用。
将这类材料添加到涂料中,既具有优良的吸收雷达波的特性,又有良好的吸收和耗散红外线的性能,具有明显的隐身功能。
潜艇伪装涂料的技术关键是涂料的湿反射率和耐老化性。
应用纳米级的深色颜料,如碳黑、铁黑和其它深色颜料可能是降低伪装涂料的湿反射率和耐老化性的有效途径之一。
二、船壳漆及船底防污涂料纳米二氧化硅的团聚体是一种无定型白色粉末,表面状态呈三维网状结构。
具有极强的紫外线吸收、红外光反射特性,能提高涂料的抗老化性能。
纳米二氧化钛也具有吸收紫外线的效应,可提高涂料的耐老化性。
它们都可以作为发展超耐候的船壳漆的主要添加剂。
船舶防污涂料一直是船舶涂料中性能最为特殊、研究技术难度最大的材料之一,由于世界各国对环境保护的要求日益重视,在全面禁止使用有机锡防污剂的期限已为确定的时机,开发新型高效的防污剂已成为各国船舶漆研究人员的关注目标。
采用纳米级防污剂,如纳米氧化亚铜、纳米氧化锌等可能是一个有效的途径,或者采用微胶囊技术,用一种水溶性的树脂材料将纳米防污剂细粉包覆形成微粒,再配制在涂料中,在实际应用中,由于海水的作用使微胶囊逐渐溶解,缓慢而有效地释放出防污剂以达到稳定长效的防污功能。
船舶行业的船舶涂装与防腐技术

船舶行业的船舶涂装与防腐技术船舶行业是全球贸易和物流领域的核心,而有效的船舶涂装与防腐技术对于保护船舶结构并延长使用寿命至关重要。
本文将介绍船舶涂装与防腐技术的重要性以及一些常用的涂装和防腐方法。
在船舶行业中,船舶的外部涂装是保护船体结构免受水下生物附着、海水侵蚀、腐蚀以及其他环境影响的一种重要方式。
船舶涂装有助于减少摩擦阻力,提高船舶速度和燃油效率,并减少船体产生的振动和噪音。
同时,涂层还能改善船舶外观,并在市场竞争中提升船舶的价值。
为了确保船舶涂装的质量和效果,船舶行业采用了多种涂装方法。
常见的涂装方法包括喷涂、滚涂和刷涂。
喷涂技术通常用于大型船舶,它可以快速而均匀地将涂料施于船体表面。
滚涂和刷涂则更常用于小型船舶或特定部位的涂装,这些方法可以更好地适应船体的曲线和凹凸处。
船舶的防腐技术也是至关重要的,特别是对于长期暴露在海洋环境中的船舶。
腐蚀是导致船舶结构损坏的主要因素之一,它会导致金属材料的质量下降和力学性能的降低。
因此,船舶行业不仅需要对船体表面进行防腐处理,还需要对内部金属结构进行防腐。
为了满足防腐需求,船舶行业采用了多种防腐方法。
热喷镀是一种常用的方法,通过将熔化的金属颗粒喷涂在船体表面形成一层坚固的防腐层。
此外,电泳涂覆、热浸镀、喷镀和刷涂等方法也被广泛应用于船舶的防腐处理。
除了涂装和防腐技术,船舶行业还注重环保和可持续发展。
在过去,一些船舶涂料中的有害物质会对海洋生态环境造成负面影响。
为了减少对环境的污染,船舶行业开始采用环保型涂料,这些涂料更加环保且具有相同的高性能和防腐功能。
此外,船舶行业还致力于研发创新的船舶涂装与防腐技术。
例如,自修复涂料是一种新型涂料,它可以在涂层受损时自动修复,并提供更长的涂层使用寿命。
一些新型防腐涂料还具有防污性能,可以减少海洋生物附着并降低风险。
总之,船舶涂装与防腐技术在船舶行业中起着关键的作用。
通过采用适当的涂装方法和防腐技术,船舶可以获得更好的保护,并延长其使用寿命。
舰船内燃机热障层参数敏感度理论和计算
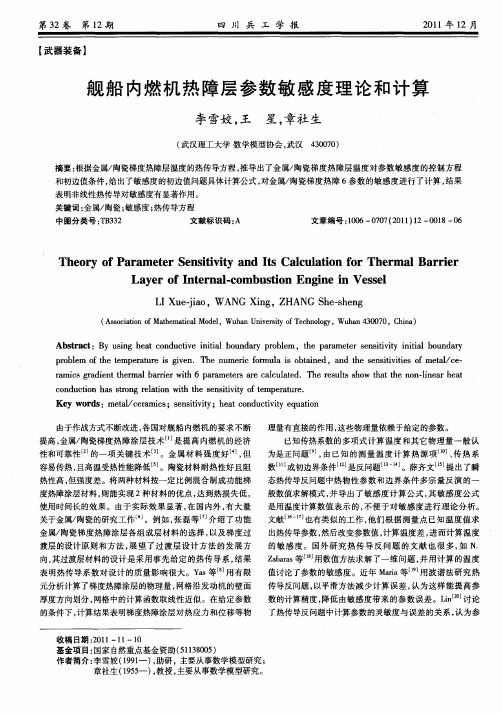
Ab ta t y u ig h a o d cie ii a o n ay po lm ,t e p rmee e st i nt lb u d r sr c :B s e tc n u t nt lb u d r rbe n v i h aa tr sn ivt iia o n a i y i y
p o lm f h e e au e i ie . T e n me i o mu a i o t i e r b e o e tmp r t r s gv n t h u r fr l s b an d,a d t e s n i vt s o t l c — c n h e s i i e fmea/ e t i r mi sg a in e a are i a a tr e c lu a e .T e r s l h w t a h o —i e rh a a c r d e t h r l b rirw t 6 p r mee sa a c l td t m h r h e u t s o h t e n n l a e t s t n
关 于金属/ 陶瓷的研究工作 J 。例如 , 张磊 等 介绍 了功能 金 属/ 陶瓷梯 度热 障涂层各 组成层材 料 的选择 , 以及梯度过
渡层 的设计 原则 和方 法 , 望 了过 渡层设 计 方法 的发 展方 展
aa s 驯 a 并 向, 其过渡层材料的设计是采用事先给定的热传导系, 结果 Zbr 等¨ 用数值方法求解 了一 维 问题 , 用计算 的温 度 表 明热传 导系 数对设计 的质 量影 响很大 。Y s a 等 用有 限 元分析计算 了梯度热 障涂层 的物理量 , 网格沿 发动机 的壁 面 厚度方 向划分 , 中的计算函数取线性 近似。在给定参 数 网格
船舶涂装工艺及涂层质量探讨
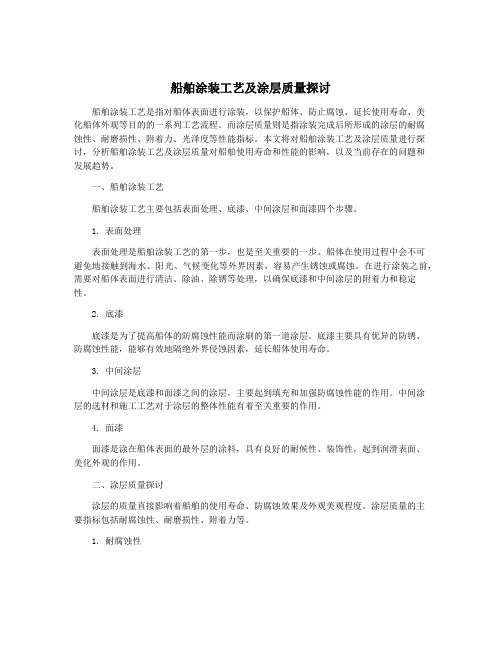
船舶涂装工艺及涂层质量探讨船舶涂装工艺是指对船体表面进行涂装,以保护船体、防止腐蚀、延长使用寿命、美化船体外观等目的的一系列工艺流程。
而涂层质量则是指涂装完成后所形成的涂层的耐腐蚀性、耐磨损性、附着力、光泽度等性能指标。
本文将对船舶涂装工艺及涂层质量进行探讨,分析船舶涂装工艺及涂层质量对船舶使用寿命和性能的影响,以及当前存在的问题和发展趋势。
一、船舶涂装工艺船舶涂装工艺主要包括表面处理、底漆、中间涂层和面漆四个步骤。
1. 表面处理表面处理是船舶涂装工艺的第一步,也是至关重要的一步。
船体在使用过程中会不可避免地接触到海水、阳光、气候变化等外界因素,容易产生锈蚀或腐蚀。
在进行涂装之前,需要对船体表面进行清洁、除油、除锈等处理,以确保底漆和中间涂层的附着力和稳定性。
2. 底漆底漆是为了提高船体的防腐蚀性能而涂刷的第一道涂层。
底漆主要具有优异的防锈、防腐蚀性能,能够有效地隔绝外界侵蚀因素,延长船体使用寿命。
3. 中间涂层中间涂层是底漆和面漆之间的涂层,主要起到填充和加强防腐蚀性能的作用。
中间涂层的选材和施工工艺对于涂层的整体性能有着至关重要的作用。
4. 面漆面漆是涂在船体表面的最外层的涂料,具有良好的耐候性、装饰性,起到润滑表面、美化外观的作用。
二、涂层质量探讨涂层的质量直接影响着船舶的使用寿命、防腐蚀效果及外观美观程度。
涂层质量的主要指标包括耐腐蚀性、耐磨损性、附着力等。
1. 耐腐蚀性船舶在海洋环境中容易受到海水、盐雾等因素的侵蚀,因此涂层的耐腐蚀性是船舶涂装的重要性能之一。
耐腐蚀性能好的涂层能够有效地延长船舶的使用寿命,降低维修成本。
2. 耐磨损性在航行过程中,船舶表面会不可避免地受到海浪、碰撞等因素的磨损,因此涂层的耐磨损性能是至关重要的。
优秀的耐磨损性能可以有效地保护船体涂层,延长涂层的使用寿命。
3. 附着力涂层与金属表面的附着力直接影响涂层的使用性能。
良好的附着力能够确保涂层的稳定性和耐久性,保证涂层与船体的紧密连接。
陶瓷材料在海洋工程领域的应用前景

陶瓷材料在海洋工程领域的应用前景海洋工程作为一种重要的工程领域,涉及到海域资源的开发与利用,海洋环境的保护与治理,以及海洋交通与通信等多个方面。
而陶瓷材料作为一种特殊的材料,在海洋工程领域中有着广泛的应用前景。
陶瓷材料具有许多优异的性质,例如高强度、耐高温、耐腐蚀、绝缘性能等,这些性质使其在海洋工程中具备许多独特的应用优势。
首先,陶瓷材料可以被用作海洋平台和海上装备的结构材料。
由于海洋环境中存在着高盐度、潮湿、氧化性、腐蚀性等恶劣条件,一般的金属材料很难承受这样的环境,容易发生腐蚀和疲劳破坏。
而陶瓷材料以其优异的抗腐蚀性能和高耐久性,可以在这种严酷的环境下长期稳定运行,如用于海洋平台的防污涂层和舷窗材料,可以有效保护平台的结构,并提高其使用寿命。
其次,陶瓷材料还可以在海洋工程中用于海洋资源的开发与利用。
例如,在海底矿产资源的开采中,陶瓷材料可以被用来制造高压泵、阀门、管道等设备,因为陶瓷材料具有耐磨损、耐高压、耐腐蚀等特点,可以有效地提高设备的性能和寿命。
此外,陶瓷材料还可以应用于海洋能源开发中的液化天然气储罐和海洋风电装备等领域,这些应用不仅可以提高能源利用效率,还可以减少对环境的污染。
此外,陶瓷材料还可以在海洋环境治理中发挥重要作用。
由于陶瓷材料具有优异的耐高温性能,因此可以被应用于海洋环境中的高温区域,如废水处理厂和烟囱的内衬材料。
此外,陶瓷材料还可以用于海洋油污治理中的吸附材料和分离膜材料。
这些应用可以有效地降低海洋环境中的污染物浓度,提高环境质量。
虽然陶瓷材料在海洋工程领域中具有许多应用优势,但在实际应用中还存在一些挑战和问题。
首先,陶瓷材料相对于传统金属材料来说,具有较高的生产成本,这在一定程度上限制了其在海洋工程中的推广和应用。
其次,陶瓷材料的力学性能相对较差,容易出现脆性断裂等问题,在结构设计和使用过程中需要加以合理考虑。
此外,陶瓷材料的加工和制造工艺相对较为复杂,对设备和技术要求较高,这也对其应用前景造成了一定的限制。