数控机床导轨的设计
数控机床结构与设计7-数控机床的床身与导轨
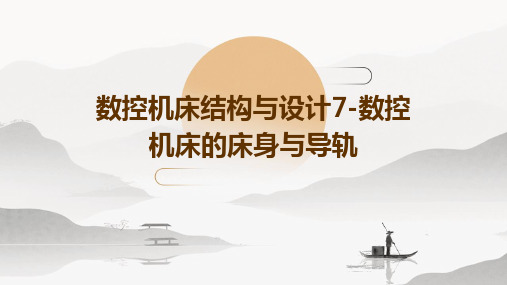
总结词
新型材料的不断涌现为床身与导轨的设 计和制造提供了更多的选择和可能性。
VS
详细描述
例如,高强度铝合金、铸铁、树脂复合材 料等轻质高强材料的应用,可以显著减轻 床身与导轨的重量,提高其动态性能。同 时,新材料的引入也促进了防腐、耐磨和 降低噪声等性能的提升。
智能化、自动化的设计与制造
总结词
智能化和自动化是床身与导轨未来发展的重要方向,有助于提高生产效率和降低成本。
选择依据
选择导轨材料时,需综合考虑使用要求、工作条件、工艺要求和经济性等因素。
导轨的精度与调整
精度
导轨的精度直接影响机床的加工精度,包括几何精度和运动精度。几何精度包括直线度、平面度、相互位置精度 等;运动精度包括运动平滑度、运动速度和加速度等。
调整
为保证导轨的精度,需要进行定期检查和调整。调整内容包括间隙调整、预紧力调整和润滑调整等。间隙调整主 要是为了消除导轨间的间隙,提高导向精度;预紧力调整是通过施加合适的预紧力,提高导轨的刚性和稳定性; 润滑调整则是为了保证导轨的正常润滑,降低摩擦和磨损。
详细描述
通过引入智能传感器、嵌入式系统、云计算等技术,可以实现床身与导轨的实时监测、自动调整和远 程维护等功能。同时,自动化生产线和机器人集成技术的应用,使得床身与导轨的加工制造过程更加 高效和精准。
感谢您的观看
THANKS
02
数控机床导轨
导轨的作用与类型
作用
导轨作为数控机床的重要基础部件,主要起导向和支承作用,保证机床的直线 运动精度和稳定性。
类型
根据不同的分类标准,导轨可分为滑动导轨、滚动导轨和静压导轨等。滑动导 轨又可分为滑动直线导轨和滑动平面导轨。
导轨的材料选择
支撑件与导轨设计
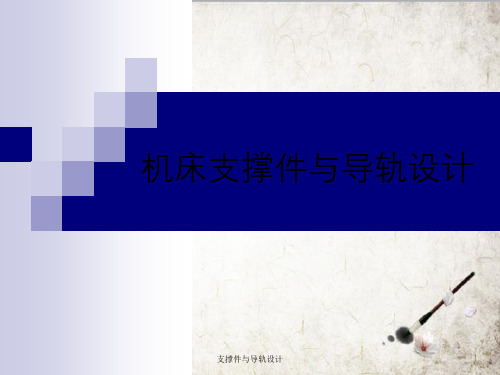
3. 支承件的热变形
改善支承件热变形的措施有: (1)在机床结构方面,采用热对称结构。 (2)在机床上采取热平衡措施。 (3)在机床上采取控制温升的措施。 (4)采用热位移补偿,预测热变形规律,建立数学模型
存入计算机中进行实时补偿。
支撑件与导轨设计
4. 其他要求
支承件设计时还应便于排屑,吊运安全,合理安置液
且动、静摩擦系数相差很小,能防止低速爬行现象;化学
稳定性、抗振性好;耐磨性好,且具有良好的自润滑性;
结构和工艺简单,成本低,维护修理方便等。
失效形式
磨损
疲劳和压溃
支撑件与导轨设计
(1)贴塑导轨
如下图所示,贴塑导轨是在动导轨上粘接上一层塑料导 轨软带,通常与支承导轨上的铸铁导轨或淬硬钢导轨相配 使用。塑料导轨软带是由聚四氟乙烯为基体,加入合金粉 和硫化物等多种填充剂制成的复合材料。
支撑件与导轨设计
a. 提高支撑件自身刚度 正确选择支撑件的截面尺寸 合理布置肋板 合理开窗加盖
b. 提高支撑件连接刚度和局部刚度 支撑件肋条的布置 合理选择支撑件壁厚
a)
b)
c)
d)
e)
f)
g)
图2.56 肋条形式
a)口字型 b)纵横肋条 c)三角形 d)交叉型
e)蜂窝支型撑件与f导)轨设米计字型 g)井字型
a)有翘曲现象
b)有辅助导轨
图2.59 带辅助导轨的床身
1-主轴箱 2-工件 3-工作台 4-溜板 5-床身
支撑件与导轨设计
2)床身的截面形状
床身中常用的几种截面肋板布置如图2.61所示。
a)V形肋
b)对角
c)斜方肋
图2.61 床身截面肋板2所示
数控机床的导轨

数控机床结构与装调工艺
③燕尾形导轨。
可以看成是三角形导轨的变形。 其磨损后不能自动补偿间隙,需用镶条 调整。两燕尾面起压板面作用,用一根 镶条就可调整水平、垂直方向的间隙。 导轨制造、检验和修理较复杂,摩擦阻 力大。当承受垂直作用力时,它以支承 平面为主要工作面,它的刚度与矩形导 轨相近;当承受颠覆力矩时,其斜面为 主要工作面,刚度较低。燕尾形导轨一 般用于要求高度小的多层移动部件。两 个导轨面间的夹角为55。
传动导轨运动的传动链的刚度13数控机床结构与装调工艺数控技术系机制教研室导向精度精度保持性低速平稳性足够的刚度结构工艺性好导轨的刚度是机床工作质量的重要指标它表示导轨在承受动静载荷下抵抗变形的能力若刚度不足则直接影响部件之间的相对位置精度和导向精度另外还使得导轨面上的比压分布不均加重导轨的磨损因此导轨必须具有足够的刚度14数控机床结构与装调工艺数控技术系机制教研室导向精度精度保持性低速平稳性足够的刚度结构工艺性好在可能的情况下应尽量使导轨结构简单便于制造和维护
⑤平-平-三 角形组合
是用于重型龙门刨床工作台导轨的一种形式,三角形导轨主 要起导向作用,平导轨主要起承载作用,不需用镶条调整间隙。
数控机床的导轨 数控技术系机制教研室
数控机床结构与装调工艺
3)圆周运动导轨
主要用于圆形工作台、转盘和转塔头架等旋转运动部件。 ①平面圆环导轨 。 ②锥形圆环导轨 。 ③V形圆环导轨 。
数控机床的导轨 数控技术系机制教研室
数控机床结构与装调工艺
三、导轨的基本要求
导向精度 精度保持性 低速平稳性 足够的刚度 结构工艺性好
在可能的情况下,应尽量使导轨结 构简单,便于制造和维护。
对于刮研导轨,应尽量减少刮研量。 对于镶装导轨,应做到更换容易。
大型精密数控直线滚动导轨磨床整体结构布局设计分析
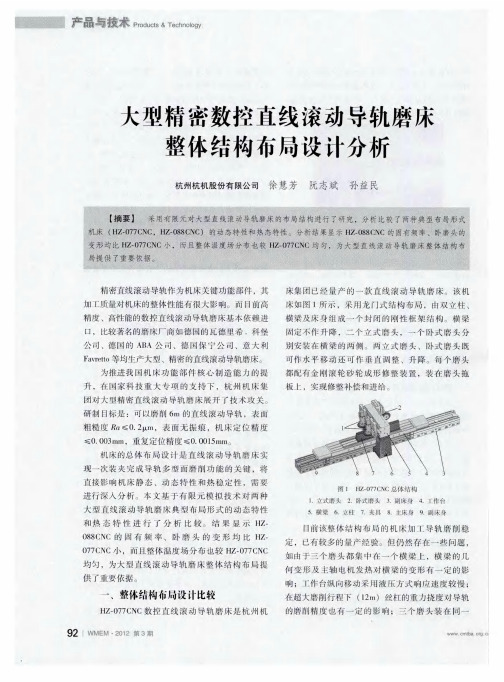
翱羧恭
应力为 6 . M a 9 8 P ,立柱与横梁等大型部件应 力值基
本上在 0 1 P 左右。 .M a
离 了该机床主轴最大转速 (8 0/ ) 10 rm 。
( )从 温度场 分布来 看 ,H 一7 C C的温度 3 Z07 N 场分布与 H 一8 C C的分 布相似 ,H 一8 C C温 Z08 N Z08 N
图 2 H - 8 C C总 体 结 构 Z0 8 N
床身 的摆动与扭转 。
5 副 床身 .
1 .卧式 磨 头
2 立 式磨 头 . 7 .立柱
3 横梁 .
4 .夹具
6 .工作 台
8 床身 .主
9 .副床 身
H 一8 C C采 用 龙 门式 结 构 布 局 ,由立 柱 、 Z0 8 N
择 Sl 16与 Sl 17混 合 划 分 ,接 触 单 元选 择 od8 i od8 i
C N A7 O T 14和 T R E 7 。H 一7 C C分析模 型的 A G 10 Z 07 N 总节点数 :3933 5 7 ,接 触单元 数 :1 2 ,实体单 860
元 :166 1 Z 0 8 N 9 6 。H . 8 C C分 析 模 型 的总 节 点 数 :
t T l 。e o &c g
羧
鬻
横梁下 ,由于 磨削 时 的振 动互 相耦 合 ,振动 耦 合 下磨 削表 面质量 不 易控制 。 因而 在 原先 的 总体 布
局 基 础 上 ,较 难 达 到 国 家 科 技 重 大 专 项 的技 术 指
二 、有限元数值模拟
1 .动 力学分 析在 线修 整 ,卧式 磨 头用 于磨 削 导轨 基 面及
重载导轨上平面 内的圆弧面 。 与 H 一7 C C导轨磨 床 的结 构设计 整体 布局 Z07 N 方案相 比,H .8 C C的特点是 : Z0 8 N ( )把卧式磨 头装 在横梁前 侧 的另一 立柱上 , 1 使立卧磨头距离拉近 ,缩短将近 11 。 I " 1 ( )缩短床身 、纵 向进 给 导轨 及 纵 向丝杆 将 2
数控机床液体静压导轨结构的优化设计
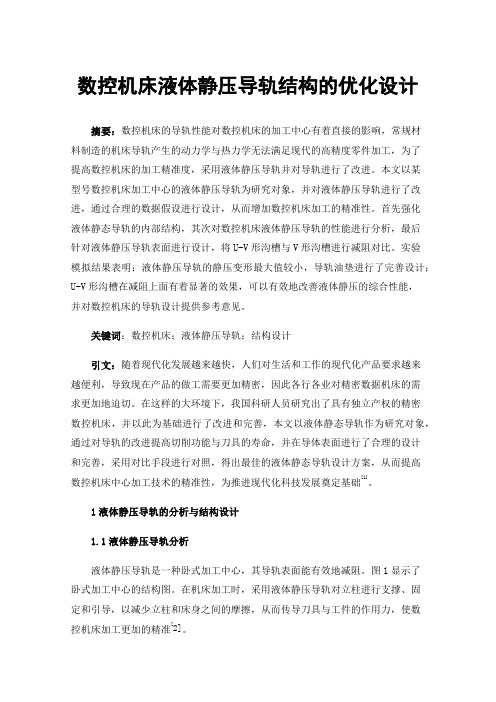
数控机床液体静压导轨结构的优化设计摘要:数控机床的导轨性能对数控机床的加工中心有着直接的影响,常规材料制造的机床导轨产生的动力学与热力学无法满足现代的高精度零件加工,为了提高数控机床的加工精准度,采用液体静压导轨并对导轨进行了改进。
本文以某型号数控机床加工中心的液体静压导轨为研究对象,并对液体静压导轨进行了改进,通过合理的数据假设进行设计,从而增加数控机床加工的精准性。
首先强化液体静态导轨的内部结构,其次对数控机床液体静压导轨的性能进行分析,最后针对液体静压导轨表面进行设计,将U-V形沟槽与V形沟槽进行减阻对比。
实验模拟结果表明:液体静压导轨的静压变形最大值较小,导轨油垫进行了完善设计;U-V形沟槽在减阻上面有着显著的效果,可以有效地改善液体静压的综合性能,并对数控机床的导轨设计提供参考意见。
关键词:数控机床;液体静压导轨;结构设计引文:随着现代化发展越来越快,人们对生活和工作的现代化产品要求越来越便利,导致现在产品的做工需要更加精密,因此各行各业对精密数据机床的需求更加地迫切。
在这样的大环境下,我国科研人员研究出了具有独立产权的精密数控机床,并以此为基础进行了改进和完善,本文以液体静态导轨作为研究对象,通过对导轨的改进提高切削功能与刀具的寿命,并在导体表面进行了合理的设计和完善,采用对比手段进行对照,得出最佳的液体静态导轨设计方案,从而提高数控机床中心加工技术的精准性,为推进现代化科技发展奠定基础[1]。
1液体静压导轨的分析与结构设计1.1液体静压导轨分析液体静压导轨是一种卧式加工中心,其导轨表面能有效地减阻。
图1显示了卧式加工中心的结构图。
在机床加工时,采用液体静压导轨对立柱进行支撑、固定和引导,以减少立柱和床身之间的摩擦,从而传导刀具与工件的作用力,使数控机床加工更加的精准[2]。
图1 卧式加工中心结构示意图例如,在一个经典的车床加工过程中,其主要的加工程序中:切削量f=0.5mm/r,则切削速度 vc=150 m/min,其它的参数都是通过参考相关的设计手册得到的。
导轨的设计与选择
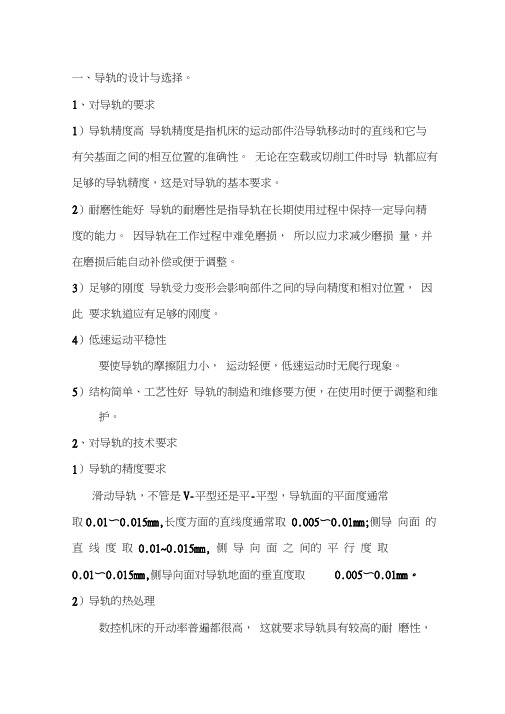
一、导轨的设计与选择。
1、对导轨的要求1)导轨精度高导轨精度是指机床的运动部件沿导轨移动时的直线和它与有关基面之间的相互位置的准确性。
无论在空载或切削工件时导轨都应有足够的导轨精度,这是对导轨的基本要求。
2)耐磨性能好导轨的耐磨性是指导轨在长期使用过程中保持一定导向精度的能力。
因导轨在工作过程中难免磨损,所以应力求减少磨损量,并在磨损后能自动补偿或便于调整。
3)足够的刚度导轨受力变形会影响部件之间的导向精度和相对位置,因此要求轨道应有足够的刚度。
4)低速运动平稳性要使导轨的摩擦阻力小,运动轻便,低速运动时无爬行现象。
5)结构简单、工艺性好导轨的制造和维修要方便,在使用时便于调整和维护。
2、对导轨的技术要求1)导轨的精度要求滑动导轨,不管是V-平型还是平-平型,导轨面的平面度通常取0.01〜0.015mm,长度方面的直线度通常取0.005〜0.01mm;侧导向面的直线度取0.01~0.015mm, 侧导向面之间的平行度取0.01〜0.015mm,侧导向面对导轨地面的垂直度取0.005〜0.01mm。
2)导轨的热处理数控机床的开动率普遍都很高,这就要求导轨具有较高的耐磨性,以提高其精度保持性。
为此,导轨大多需要淬火处理。
导轨淬火的方式有中频淬火、超音频淬火、火焰淬火等,其中用的较多的是前两种方式。
二、导轨的种类和特点导轨按运动轨迹可分为直线运动导轨和圆运动导轨;按工作性质可分为主运动导轨、进给运动导轨和调整导轨;按接触面的摩擦性质可分为滑动导轨、滚动导轨和静压导轨等三大类。
1)滑动导轨:是一种做滑动摩擦的普通导轨。
滑动导轨的优点是结构简单,使用维护方便,缺点是未形成完全液体摩擦时低速易爬行,磨损大,寿命短,运动精度不稳定。
滑动导轨一般用于普通机床和冶金设备上。
2)滚动导轨的特点是:摩擦阻力小,运动轻便灵活;磨损小,能长期保持精度;动、静摩擦系数差别小,低速时不易出现"爬行"现象,故运动均匀平稳。
数控龙门导轨磨床总体方案设计

The grinder can process a variety of surfaces, such as inner, outer cylindrical surface and a conical surface, plane, tooth profile of involute spiral surface and various surface, forming surface. Grinder of many types, according to the nature of their work can be divided into: external grinder, internal grinder, surface grinder, grinding machine tools and some special grinding machine. Thread grinder, grinding machine, such as spherical spline grinding machine, grinder and centerless grinder. Rail grinding machine is a kind of according to the nature of the work out of the grinder.
数控机床结构与设计7——数控机床的床身与导轨
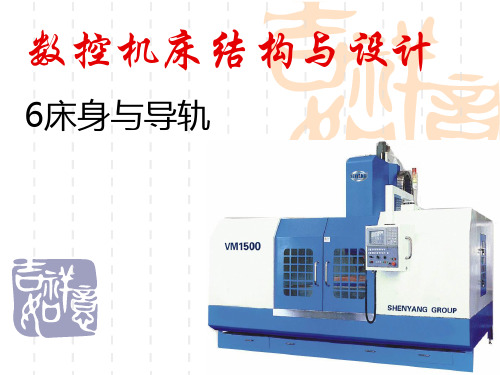
图6-5 AG床身的结构形式
(a)整体结构,(b)框架结构, (c)分块结构
6,2 贴塑滑动导轨设计
滑动导轨具有结构简单,制造方便,接触 刚度大的优点。但传统滑动导轨摩擦阻力 大,磨损快,动静库擦系数差别大,低速 时易产生爬行现象。除简易型数控机床外, 在其它数控机床上已不采用,在数控机床 上常用带有耐磨粘贴带覆盖层的滑动导轨 和新型塑料滑动导轨。它们具有良好的摩 擦性能及使用寿命长的特点,尤其是靼料 导轨将有代替滚动导轨的趋势。
图6-4 铸造床身的封砂结构
(a)旧结构 (b)新结构
6. 1.4 床身的结构设计
AG(人造花岗石)材质是一种新型休身材质, 它除了具有好的阻尼性能(阻尼为灰铸铁的 8~10倍)外,还具有尺寸稳定性好、抗腐 蚀性强、制造成本低等优点,与灰铸铁比, 它热容量大,热导率低,构件的热变形小; AG床身的后期加工量很少,这样可以大大 减少占用大型机床加工时间和加工成本, 并能节约大量金屑,如一个磨床床身就可 以节约90%左右的金属材料。
6. 3.1 静压导轨的结构
按静压导轨的结构形式可分为两大类。开 式静压导轨和闭式静压导轨两类。按供油 方式可分为恒压供油和恒流供油两类。 1.开式静压导轨是指不能限制工作台从 导轨上分离的静压导轨,如图6—13所示, 这种导轨的载荷总是指向导轨,不能承受 相反方向的载荷,并且不易达到很高的刚 性。这种静压导轨用于运动速度比较低的 重型机床。
床身式立式铣床
3.较好的热稳定性
对数控机床来说,尤其是高精度数控机床, 热稳定性已成了一个突出问题,必须在设 计上要作到使整机的热变形较小,或使热 变形对加工精度的影响较小。
6.1.2 床身的结构
1.床身结构 根据数控机床的类型不同,床身的结构 形式有各种各样的形式。例如数控车床床 身的结构 形式有平床身、斜床身、平床身 斜导轨和直立床身等四种类型,在数控车 床一章中已作介绍,另外这种斜床身结构 还能设计成封闭式断面,这样大大提高了 床身的刚度,如图6—1所示。
3.8 导轨设计

(四)导轨间隙的调整 导轨面间的间隙对机床工作性 能有直接影响,如间隙过大,将影 响运动精度和平稳性,间隙过小、 运动阻力大,导轨的磨损加快。 为保证导轨具有合理间隙,磨 损后又能方便地调整。
1、压板 压板用来调整辅助导轨面的间隙, 承受颠覆力矩,用配刮垫片来调整间隙
2、镶条 镶条用来调整矩形导轨和燕尾 形导轨的侧向间隙,镶条应放在导 轨受力较小的一侧。 常用的镶条有平镶条和斜镶条二 种:①平镶条截面为矩形或平行四 边形,厚度均匀相等,由螺钉调整 间隙 易变形、刚度低,目前少用。 图3-力分布不均时,采用不对称导 轨。
3、燕尾形导轨 燕尾形导轨可承受较大颠覆力 矩,导轨的高度较小,结构紧凑, 间隙调整方便,但刚度较差,加工、 检验、维修不大方便。 适用于受力小、层次多,要求 间隙调整方便的部件。
4、圆柱形导轨 圆柱形导轨制造方便,工艺性 好,但磨损后较难调整和补偿间隙, 主要用于受轴向负荷的导轨,应用 较少。 四种截面的导轨尺寸已标准化
1、滚动导轨的类型 滚珠:点接触、承载能力差、 刚度低、 用于小载荷 按 图3-118a 滚 动 滚柱:线接触、承载能力大、 体 刚度好、用于大载荷 分 图3-118b 滚针:线接触、常用于 径向载荷小的导轨 图3-118c
循环式
按循环方式分
非循环式 循环式滚动导轨的滚动体在运 行过程中,沿自己的工作轨道和返 回轨道作连续循环运动
闭式导轨: 借助于压板使导轨能承受较 大的颠覆力矩的作用 压板1、2 e、f为主导轨面,压板1、2形成辅助导轨面g、h
普通滑动导轨 滑动导轨 静压导轨 II 按摩擦性质分 卸荷导轨 滚动导轨
(二)导轨应满足的基本要求 导轨应满足精度高、承载能力大、 刚度好、摩擦阻力小、运动平稳、 精度保持性好、寿命长、结构简单、 工艺性好、便于加工、装配调整和 维修、成本低。
第十二章 机床导轨的设计
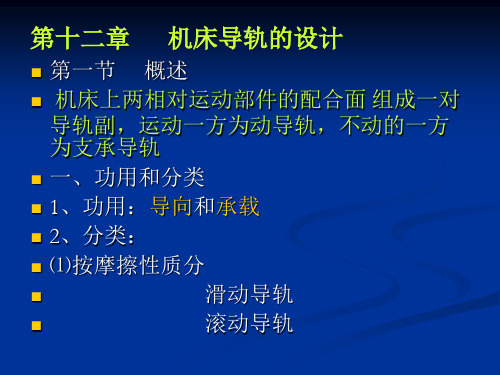
第四节
滑动导轨的验算
滑动导轨应验算导轨的压强和压强的分布 压强——耐磨性 压强分布——磨损的均匀性和是否采用压 板 步骤:1、受力分析 2、计算压强 一、受力分析 以数控车床刀架纵导轨为例 P247
导轨所受外力:重力、切削力、牵引力等 F c—切削力 F f—进给力 F p—背向力 FQ—牵引力 W—重力 通过静力方程求解 分别对 X、Y、Z 坐标取矩得:
当 6M/FL=1,即 M/FL=1/6 时 P min=0 P max=2Pav 压强按三角形分布
这是一种使动导轨与支承导轨在全长接触 的临界状态 如压强分布属上述情况,则均可采用开式 导轨
当 6M/FL>1,即 M/FL>1/6 时,主导轨 面上将有一段长度不接触,实际接触长度 为:Lj
⑶燕尾形导轨:
承载较大的颠覆力矩,导轨的高度较小, 结构紧凑,间隙调整方便。但刚度性较差, 加工检验维修都不大方便。 适于受力小、层次多、要求间隙调整方便 的部位 ⑷圆柱形导轨:
制造方便,工艺性好,但磨损后较难调整 和补偿间隙。主要用于受轴向负荷的轨, 应用较少
2、导轨的组合形式 (1)双三角形导轨:不需要鑲条调整间隙, 接触刚度好,导向性和精度保持性好,但 工艺性差,加工、检验和维修都不方便
f W—载荷/速度系数 无冲击振动 v≤15m/min时, f W=1~1.5 轻冲击振动 15<v≤60m/min f W=1.5~2 有冲击振动 v>60m/min f W=2.0~3.5 如果寿命以小时计,则
第十二章机床导轨的设计介绍

⑶燕尾形导轨:
承载较大的颠覆力矩,导轨的高度较小, 结构紧凑,间隙调整方便。但刚度性较差, 加工检验维修都不大方便。 适于受力小、层次多、要求间隙调整方便 的部位 ⑷圆柱形导轨:
制造方便,工艺性好,但磨损后较难调整 和补偿间隙。主要用于受轴向负荷的轨, 应用较少
2、导轨的组合形式 (1)双三角形导轨:不需要鑲条调整间隙, 接触刚度好,导向性和精度保持性好,但 工艺性差,加工、检验和维修都不方便
1、塑料软带 主要是氟塑料导轨软带,粘接在动导轨上 组成:以聚四氟乙烯为基体,添加一定比 例的耐磨材料 优点:摩擦系数低,约为铸铁—铸铁的1/3 动、静摩擦系数相近,防爬性能好 耐磨性可提高 1~2倍 可自润滑 磨损可更换,磨粒可嵌入塑料 局部压强很大的导轨不宜采用
三、有色金属 有色金属作导轨主要是镶装结构 材料特点是耐磨性较高,可防止撕伤,保 证运动的平稳性和移动精度 与铸铁的支承导轨相搭配,多用于重型机 床的动导轨上 主要牌号:锡青铜 ZQSn6-6-3 铝青铜 ZQAl 9-4
四、塑料 在动导轨上镶装塑料 特点: 摩擦系数低、耐磨性高、抗撕伤能力强、 低速时不易出现爬行、加工性和化学稳定 性好、工艺简单、成本低 应用范围: 在各类机床上都有应用,特别是用在精密 机床、数控和重型机床的动导轨上
二、圆周运动导轨 回转运动导轨的截面形状有三种: 平面环形、锥面环形和双锥面环形导轨。 (1)平面环形导轨: 结构简单、制造方便、能承受较大的轴向 力,但不能承受径向力,因而必须与主轴 联合使用,由主轴来承受经向载荷
(2)锥面环形导轨:
第4章 机床导轨设计_原第六章_

第四章机床导轨设计第一节 概 述一、导轨的功用和分类机床上两相对运动部件的配合面组成一对导轨副,不动的配合面为支承导轨,运动的配合面为动导轨。
导轨副的主要功用是导向和承载,为此,导轨副只许具有一个自由度。
导向原理如图4—1所示。
图4—1导向原理导轨副按下列性质分类。
1.运动轨迹(1) 直线运动导轨导轨副的相对运动轨迹为一直线。
如普通车床的溜板和床身导轨。
(2) 圆周运动导轨导轨副的相对运动轨迹为一圆,如立式车床的花盘和底座导轨。
2.摩擦性质(1) 滑动导轨其中有静压导轨、动压导轨和普通滑动导轨,它们的共同特点是导轨副工作面之间的摩擦性质为滑动摩擦。
(2) 滚动摩擦导轨副工作面之间装有滚动体,使两导轨面之间为滚动摩擦。
3.工作性质(1) 主运动导轨动导轨作主运动,导轨副间的相对运动速度高。
(2) 进给运动导轨动导轨作进给运动,导轨副之间的相对运动速度低。
(3) 移置导轨实现部件之间的相对位置调整,在机床工作时无相对运动。
(4) 卸荷导轨采用机械、液压或气压办法减轻支承导轨的负荷,降低静、动摩擦系数,以提高导轨的耐磨性、低速平稳性和运动精度。
二、导轨应满足的基本要求1.导向精度主要是指动导轨运动轨迹的精确度。
影响导向精度的主要因素有:导轨的几何精度和接触精度、导轨的结构形式、导轨及其支承件的刚度和热变形、静(动)压导轨副之间的油膜厚度及其刚度等。
2.精度保持性主要由导轨的耐磨性决定。
耐磨性与导轨的材料、导轨副的摩擦性质、导轨上的压强及其分布规律等因素有关。
3.刚度包括导轨的自身刚度和接触刚度。
导轨的刚度不足会影响部件之间的相对位置和导向精度。
导轨刚度主要取决于导轨的形式、尺寸、与支承件的连接方式及受力状况等因素。
4.低速运动平稳性动导轨作低速运动或微量位移时易产生摩擦自激振动,即爬行现象。
爬行会降低定位精度或增大被加工工件表面的粗糙度的值。
三、导轨的主要失效形式1.磨损①磨粒磨损。
这里的磨粒是指导轨面间存在的坚硬微粒,可能是落人导轨副间的切屑微粒或是润滑油带进的硬颗粒;也可能是导轨面上的硬点或导轨本身磨损所产生的微粒。
直线导轨的结构设计(含滚动导轨)
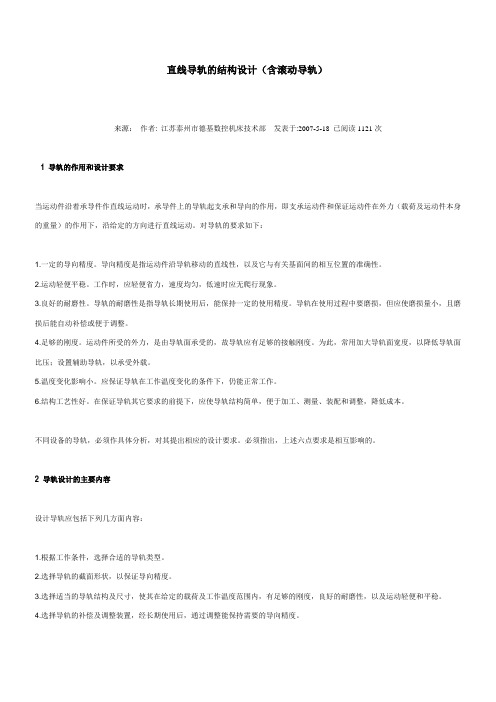
直线导轨的结构设计(含滚动导轨)来源:作者: 江苏泰州市德基数控机床技术部发表于:2007-5-18 已阅读1121次1 导轨的作用和设计要求当运动件沿着承导件作直线运动时,承导件上的导轨起支承和导向的作用,即支承运动件和保证运动件在外力(载荷及运动件本身的重量)的作用下,沿给定的方向进行直线运动。
对导轨的要求如下:1.一定的导向精度。
导向精度是指运动件沿导轨移动的直线性,以及它与有关基面间的相互位置的准确性。
2.运动轻便平稳。
工作时,应轻便省力,速度均匀,低速时应无爬行现象。
3.良好的耐磨性。
导轨的耐磨性是指导轨长期使用后,能保持一定的使用精度。
导轨在使用过程中要磨损,但应使磨损量小,且磨损后能自动补偿或便于调整。
4.足够的刚度。
运动件所受的外力,是由导轨面承受的,故导轨应有足够的接触刚度。
为此,常用加大导轨面宽度,以降低导轨面比压;设置辅助导轨,以承受外载。
5.温度变化影响小。
应保证导轨在工作温度变化的条件下,仍能正常工作。
6.结构工艺性好。
在保证导轨其它要求的前提下,应使导轨结构简单,便于加工、测量、装配和调整,降低成本。
不同设备的导轨,必须作具体分析,对其提出相应的设计要求。
必须指出,上述六点要求是相互影响的。
2 导轨设计的主要内容设计导轨应包括下列几方面内容:1.根据工作条件,选择合适的导轨类型。
2.选择导轨的截面形状,以保证导向精度。
3.选择适当的导轨结构及尺寸,使其在给定的载荷及工作温度范围内,有足够的刚度,良好的耐磨性,以及运动轻便和平稳。
4.选择导轨的补偿及调整装置,经长期使用后,通过调整能保持需要的导向精度。
5.选择合理的润滑方法和防护装置,使导轨有良好的工作条件,以减少摩擦和磨损。
6.制订保证导轨所必须的技术条件,如选择适当的材料,以及热处理、精加工和测量方法等。
3 导轨的结构设计1. 滑动导轨(1) 基本形式(见图21-10)图21-10三角形导轨:该导轨磨损后能自动补偿,故导向精度高。
广州机床导轨施工方案设计
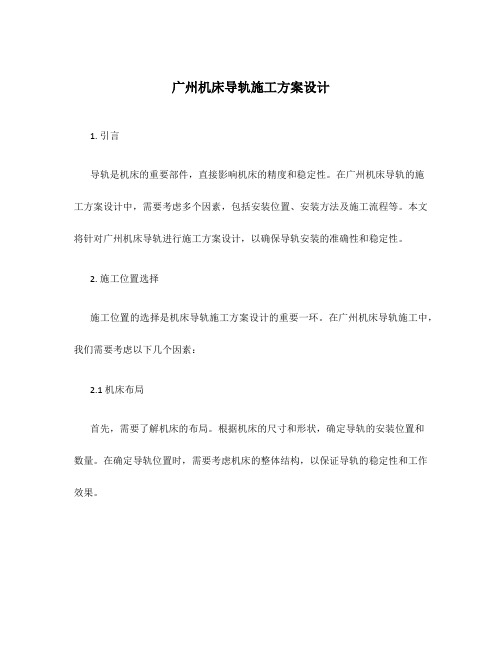
广州机床导轨施工方案设计1. 引言导轨是机床的重要部件,直接影响机床的精度和稳定性。
在广州机床导轨的施工方案设计中,需要考虑多个因素,包括安装位置、安装方法及施工流程等。
本文将针对广州机床导轨进行施工方案设计,以确保导轨安装的准确性和稳定性。
2. 施工位置选择施工位置的选择是机床导轨施工方案设计的重要一环。
在广州机床导轨施工中,我们需要考虑以下几个因素:2.1 机床布局首先,需要了解机床的布局。
根据机床的尺寸和形状,确定导轨的安装位置和数量。
在确定导轨位置时,需要考虑机床的整体结构,以保证导轨的稳定性和工作效果。
2.2 环境因素其次,需要考虑施工环境,包括温度、湿度、噪音等因素对导轨的影响。
在广州地区特殊的气候条件下,我们需要在施工方案中考虑合适的防护措施,以确保导轨的使用寿命和性能。
2.3 维修和保养便利性最后,还需要考虑导轨的维修和保养便利性。
选择适当的施工位置可以方便后期的维修和保养工作,减少施工期间对导轨的损坏和干扰。
3. 导轨安装方法选择导轨的安装方法包括对接焊接、膨胀螺栓和膨胀螺钉等。
在广州机床导轨施工方案设计中,我们需要根据导轨的尺寸、工作载荷、环境要求等因素来选择合适的安装方法。
3.1 对接焊接对接焊接是一种常见的导轨安装方法。
在广州机床导轨施工中,适用于导轨较大且工作载荷较重的情况。
通过焊接,可以确保导轨与机床的牢固连接,提高导轨的稳定性和使用寿命。
3.2 膨胀螺栓膨胀螺栓是另一种常用的导轨安装方法。
它适用于导轨较小且工作载荷较轻的情况。
膨胀螺栓的安装过程相对简单,能够快速固定导轨,但相比于对接焊接,膨胀螺栓的牢固性和稳定性较差。
3.3 膨胀螺钉膨胀螺钉是一种更为灵活的导轨安装方法。
它适用于导轨较小且安装环境有限的情况。
膨胀螺钉可以通过压力使螺钉与孔壁紧密连接,提供了可靠的固定效果,同时又不会对机床产生损坏。
4. 施工流程施工流程是广州机床导轨施工方案设计的核心部分。
合理的施工流程可以确保导轨的精确安装,提高机床的工作效率和精度。
- 1、下载文档前请自行甄别文档内容的完整性,平台不提供额外的编辑、内容补充、找答案等附加服务。
- 2、"仅部分预览"的文档,不可在线预览部分如存在完整性等问题,可反馈申请退款(可完整预览的文档不适用该条件!)。
- 3、如文档侵犯您的权益,请联系客服反馈,我们会尽快为您处理(人工客服工作时间:9:00-18:30)。
数控机床导轨的设计
作者:王佳蕊张琳琳
来源:《科学与财富》2015年第36期
摘要:导轨是机床的关键部件之一,其性能好坏,将直接影响机床的加工精度、承载能力和使用寿命。
其功用是支承并引导运动部件沿一定的轨迹运动,它承受其支承的运动部件和工件(或刀具)的质量和切削力。
关键词:数控机床;导轨;设计
引言
按机床的运动性质,大多数机床都是进给运动导轨,其导轨副之间的相对运动速度较低,本机床进给运动为刀架的上下运动、刀架在横梁的左右运动以及整个横梁的上下升降运动,采用的是矩形导轨,使用镶条来调整各部件间的间隙。
静压导轨是将具有一定压强的润滑油,经节流器,通入动导轨的纵向油槽中,形成承载油膜,将导轨副的摩擦面隔开,实现液体摩擦,这种靠液压系统产生的压力油形成承载油膜的导轨称为静压导轨。
静压导轨的优点是:摩擦系数为0.005~0.001,机械效率高;由于有油膜作用,不会产生粘着磨损,导轨精度保持性好;油膜有均化表面误差的作用,相当于提高了制造精度;油膜的阻尼比大,一般为0.04~0.06,因此静压导轨抗震性能较好;静压导轨低速运行平稳,防爬行性能良好。
但是静压导轨结构复杂,需要一套完整的液压系统,维修也相当困难。
因此,静压导轨适用于具有液压传动系统的精密机床和高精度机床的水平进给运动导轨。
本文设计机床导轨为立式车床的立柱导轨,主要承载横梁的升降,采用滑动导轨能够满足精度传动要求。
1.滑动导轨的截面形状
导轨的主要功能是导向,动导轨必须按照导向轨迹进行运动,因此必须限定除沿静导轨面移动的另外五个自由度。
支承导轨制造或安装在立柱、横梁等支承件上,接触导轨面的宽度远小于其导轨的长度,根据定位原理,可以视导轨为窄定位板,只能限制沿y轴移动和绕x轴转动的两个自由度;可以利用两窄板(a和b)定位方法,在一个坐标面中形成一个定位平面,可以限制沿y轴的移动和绕X轴、Z轴转动的三个自由度;要准确导向,还需要限制沿X轴的移动和绕y轴的转动,因此,需增加另一坐标面上的窄支承平面c。
从而形成最基本的双矩形导轨。
该矩形导轨结构简单,容易制造,刚度和承载能力大,安装调整方便。
但是其缺点是导轨面易磨损且不能够自动补偿,且需要增加间隙调整机构。
这种导轨广泛用于普通精度机床和中型机床中,如数控机床。
为使C面定位可靠,保证导向精度,应用镶条调整c面与动导轨结合面之间的间隙。
导轨面模型如图1.1所示。
图1.1横梁矩形导轨面
2.导轨间隙的调整
辅助导轨副间的间隙调整一般是用精磨压板来调整导轨副间的间隙。
而调整矩形导轨问的间隙常用斜镶条和平镶条来调整。
虽然平镶条制造较斜镶条较为容易,但是,当其与导轨面配合时就会出现累积的间隙误差,调整较为麻烦,现已不常用。
而斜镶条斜面与动导轨配合斜面在长度方向上斜度相等,倾斜方向相反,这样可以纵向移动镶条调整导轨横向间隙。
镶条应保证有适当的长度余量,以保证镶条斜面与动导轨面有足够的接触面,从而有利于传动平稳;镶条平面与支承导轨面、镶条斜面与动导轨斜面配拉削后,截去长度余量,固定在动导轨上,如图2.1所示。
我们采用图示调整方式通过配合精度可以避免镶条在运动时的窜动。
图2.1斜镶条的间隙调整
3.提高滑动导轨耐磨性措施
铸铁是一种成本低,有良好的减震性和耐磨性,易于铸造和切削加工的材料,因此常用于机床的大件的铸造。
一般铸造出的导轨其耐磨性较低,容易粘着磨损,
导轨寿命较低,所以常在浇注导轨时加入少量的如硅、锰等的孕育剂,在灰铸铁中加入磷、铜等细化晶粒的元素,浇注完成后对其表面进行高频淬火等措施,都可以提高导轨的耐磨性。
同时,我们注意到,导轨副应采用不同的材料制造,或者相同的材料不同的热处理方法,这样可以提高导轨副的耐磨性,防止粘着磨损。
本机床立柱导轨,主要承受横梁的重力,切削力基本被其抵消,因此机床导轨有向外被拉的趋势是主要使机床损坏的原因。
由于本次设计的机床精度较高,导轨副传动需要有较高的传动要求,采用耐磨铸铁导轨副,导轨面需进行刮研处理,还需要保证动导轨面的硬度要比其支承导轨面的硬度低20~40HBW,镶条需要贴导轨软带,主要是导轨软带具有良好的摩擦特性,又具有青铜和钢的刚性和导热性,应用也日趋广泛。
提高导轨导轨耐磨性还要有精度保证,长导轨副我们采用精磨,短导轨副采用刮削方式,这样可以保证导轨面的耐磨性。
同时动导轨的滑移速度较低,我们选用导轨面的压强小于
0.2MPa.m/min,此种压强下可以降低导轨面的磨损速度。
此外,良好的润滑环境是导轨副长期工作的保障,为了提高动压效应,改善摩擦状态,需在导轨面开横向油槽,这样可以储存更多的润滑油,提高了动压效应。
又由于是垂直导轨,我们采用N46号全损耗系统供油。
4刀架丝杠的特性
滚珠丝杠传动系统是一个以滚珠作为滚动媒介的滚动螺旋传动的体系。
滚珠丝杠副是将丝杠螺母皆加工成凹半圆弧形螺纹,在螺纹之间放入滚珠形成的。
当丝杠、螺母相对转动时,滚珠沿螺旋滚道滚动,螺纹摩擦为滚动摩擦,从而提高了传动精度和传动机械效率。
为了防止滚珠从螺母中滚出来,在螺母的螺旋槽两端设有回程引导装置,使滚珠能自动返回其入口循环流动。
滚珠丝杠副的特性:滚珠丝杠传动系统的传动效率高,是普通滑动丝杠系统的2-4倍,功率消耗也只有滑动丝杠螺母副的0.25-0.35,所以能以较小的扭矩得到较大的推力,由于具有运动可逆性,亦可由直线运动转为旋转运动;滚珠丝杠传动系统为点接触滚动运动,工作时灵敏度高、启动时无颤动、摩擦阻力也较小,当传动系统其余部件的刚度足够,微量进给运动几乎可以达到同步效果;滚珠丝杠传动是点接触,系统运动中产生较小温度,轴向拉伸可以消除间隙,对丝杠进行预拉伸可以大大消除热伸长,因此可以基本消除重复定位精度导致的误差;钢球滚动接触处均经硬化(HRC58~63)处理,并经精密磨削,滚珠在传动槽中做循环运动,相对磨损甚微,故具有较高的使用寿命和精度保持性;由于滚珠丝杠副具有很好的同步效果,使用几套相同的丝杠副就可以同时传动几个相同的部件或装置,实现传动系统的同步工作。
刀架在低速进给过程中会受到摩擦阻力的作用出现不均匀的跳跃现象,速度时快时慢,特别在刀架左右点动的过程中出现也会出现这种现象,我们称之为爬行现象。
造成这种情况的大多原因是由于系统中各零部件的刚度不够而造成的弹性变形,或者导轨面的润滑不充分等原因造成的。
这种现象会影响机床的加工精度,定位精度,爬行严重时会造成机床不能正常工作。
因此,我们需分析并确定减少危害机床爬行现象的措施。
出现爬行现象的主要原因是横梁导轨面上的动摩擦因素小于其静摩擦因素,且动摩擦因素随滑移速度的增加而减小以及传动系统的弹性变形。
结论
导轨作为机床的关键部件之一,其性能好坏,将直接影响机床的加工精度、承载能力和使用寿命。
本文从介绍了导轨的类型、横截面积形式。
阐述了导轨间隙的调整方法和提高滑动导轨耐磨性措施。
并在文章最后介绍了与导轨向关联的刀架及其刀架丝杠的特征,对导轨的设计具有一定的意义。
参考文献
[1]李晓华.数控机床的产生及其特点与发展趋势[J].承德职业技术学院学报,2007(2):106-109
[2]朱南峰.五轴数控加工中心在木制品与家具生产中的应用.见:朱南峰等.2007全国木材加工技术与装备发展研讨会论文集.南京,2007。