铸造工艺基础要点
铸造工艺基础知识及理论

铸造工艺基础知识及理论目录一、基础概念 (2)1.1 铸造的定义与意义 (3)1.2 铸造工艺的种类与应用 (4)二、铸造材料 (6)三、铸造设备 (7)3.1 熔炼设备 (9)3.2 锻造设备 (10)3.3 后处理设备 (11)四、铸造工艺过程 (12)五、铸造工艺设计 (13)5.1 工艺方案的确定 (15)5.2 工艺参数的选择 (16)5.3 工艺文件的编制 (18)六、铸造质量与控制 (20)6.1 铸造缺陷的产生原因及防止措施 (22)6.2 铸造质量检测方法与标准 (23)七、铸造生产与环境 (24)7.1 铸造生产的环保要求 (26)7.2 环保设备的应用与管理 (27)八、现代铸造技术的发展趋势 (28)8.1 快速凝固与近净形铸造技术 (30)8.2 数字化与智能化铸造技术 (31)8.3 生物铸造与绿色铸造技术 (33)一、基础概念铸造工艺是指将熔炼好的液态金属浇入铸型,待其凝固后获得所需形状和性能的金属制品的过程。
它是制造业中非常重要的工艺之一,广泛应用于汽车、航空、建筑、电子等领域。
铸造工艺的基础知识主要包括液态金属的性质、铸型(即模具)的设计与制造、浇注系统、凝固过程以及后处理等。
这些知识是理解和掌握铸造工艺的基本前提。
液态金属的性质:液态金属在铸造过程中的流动性、填充能力、冷却速度等对其最终的产品质量有着决定性的影响。
了解液态金属的成分、温度、粘度等基本性质对于铸造工艺的设计和实践都是非常重要的。
铸型的设计与制造:铸型是形成金属制品形状和内部结构的重要工具。
铸型的设计需要考虑到金属液的流动性和凝固特性,以及制品的精度和表面质量要求。
铸型的制造也需要选用合适的材料,并经过精密加工才能达到设计要求。
浇注系统:浇注系统是连接铸型和液态金属的通道,包括浇口杯、直浇道、横浇道和内浇道等部分。
合理的浇注系统设计可以确保金属液均匀地注入铸型,并有利于热量和气体的排出,从而提高制品的质量和生产效率。
铸造工艺流程培训

铸造工艺流程培训简介铸造工艺是一项重要的制造工艺,广泛应用于各个领域,包括汽车制造、机械制造、航空航天等。
铸造工艺的质量和效率直接关系到产品的质量和成本。
因此,对铸造人员进行专业的工艺流程培训显得尤为重要。
本文将就铸造工艺流程培训的内容、方法和重要性进行探讨。
铸造工艺流程培训的重要性铸造工艺流程的正确操作对产品质量至关重要。
通过铸造工艺流程培训,可以有效提高铸造人员的操作技能,降低因操作失误造成的废品率,提高生产效率,减少成本。
此外,铸造工艺流程的培训还能帮助铸造人员更好地理解工艺流程,提高工作积极性和责任感,从而提升整个生产团队的整体素质。
铸造工艺流程培训内容1.铸造工艺基础知识–铸造的定义和分类–常用铸造材料及其特性–铸造工艺流程概述2.铸造设备操作–注塑机、压铸机等设备的操作方法–设备维护和保养–设备故障处理3.铸造模具制作–模具设计理论–模具制作工艺–模具使用和维护4.铸造工艺流程–熔炼工艺–浇注操作流程–铸件冷却及后续处理铸造工艺流程培训方法1.理论教学通过课堂讲解、幻灯片展示等方式,传授铸造工艺基础知识和操作流程。
2.实操培训利用实际生产中的场景,让学员亲自操作设备、制作模具,模拟真实的工艺流程。
3.案例分析结合实际案例,剖析铸造工艺中的常见问题及解决方法,帮助学员更好地理解和掌握工艺流程。
4.考核评估通过考试、练习和实际操作评估学员的学习效果,及时发现问题并加以纠正。
结语铸造工艺流程培训对于提高铸造人员的技能水平、提升生产效率、降低成本具有重要意义。
通过系统的培训,铸造人员能够更好地理解和掌握铸造工艺流程,为企业的发展提供坚实的支撑。
希望本文所述内容能为铸造企业开展工艺流程培训提供一定的参考和帮助。
第一章铸造工艺基础

1-3铸造内应力、变形和裂纹
• 铸造内应力:铸件的固态收缩受到阻碍而引起的内应力。 • 残余内应力:一直保持到室温的铸造内应力 • 临时内应力:在冷却过程中暂存的铸造内应力 • 铸造内应力是铸件产生变形和裂纹的基本原因 • 按内应力产生原因不同分为热应力和机械应力 一、铸造内应力的形成 • 介绍热应力和机械应力的产生 1.热应力: • 1)定义:由于铸件的壁厚不均,各部分冷却速度不同,各部分收缩 不一致引起的内应力。 • 2)金属应力状态改变:(金属自高温至室温) • 金属在再结晶温度以上处于塑性状态,在再结晶温度以下处于弹性状 态,再结晶温度是分界点 • 塑性状态降温 弹性状态 • 弹性状态升温 塑性状态
流动性
二、浇注条件 • 1.浇注温度: “决定性”影响 浇温升高充型能力越强 • 实践中可利用此规律对薄壁铸件或流动性较差的合金可适当提高浇温, 提高充型能力 • 浇温也不宜过高,否则易产生缩孔、缩松等缺陷 • 2.充型压力 • 合金受压越大充型能力越强 三、铸型填充条件 • 1.铸型材料: • 铸型导热系数和比热容升高,合金充型能力下降 • 2.铸型温度: • 铸型温度升高减缓冷却速度,充型能力升高 • 3.铸型中气体: • 铸型中气体阻碍液体合金的充型,应减少之.
三、铸件的裂纹与防止 • 铸造内应力超过材料强度极限时产生裂纹 1.热裂 • (1)定义:在高温下形成的裂纹 • (2)形状特征:缝隙宽、形状曲折、缝内呈氧化色 • (3)形成原因:合金完全凝固前固态收缩已开始,晶粒间存在液体, 强度、塑性低 • (4)分布:一般分布在应力集中部位 • (5)主要影响因素:合金性质、铸型阻力 • (6)防止方法①使铸件结构合理②改善铸型和型芯的退让性③减少 浇、冒口对铸件收缩的机械阻碍④内浇口设置符合同时凝固原则⑤减 少合金中有害杂质含量。 2.冷裂 • (1)含义:在低温下形成的裂纹 • (2)形状特征:裂纹细小,呈连续直线状,缝内呈轻微氧化色 • (3)分布:常出现在形状复杂工件的受拉伸部分
铸造培训-铸造基本知识
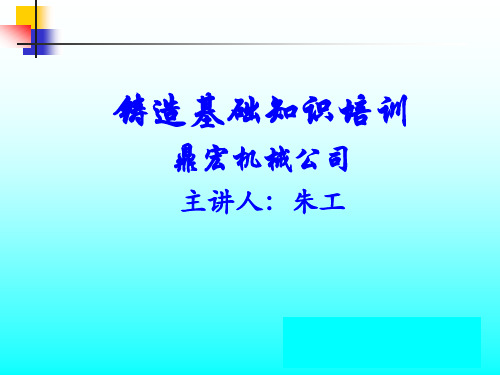
前一页
后一页
回主页
三、铸型充填条件
(1)铸型的材料
(2)铸型温度 铸型温度越高,液态金属与铸型的
温差越小,充型能力越强。 (3)铸型中的气体
前一页
后一页
回主页
§1-2 铸件的凝固与收缩
一、铸件的凝固方式
温度
1. 逐层凝固
2. 糊状凝固 3. 中间凝固 影响铸件凝固方 式的主要因素:
温度
a b c
前一页 后一页 回主页
金属型铸造
金属型铸造是在重力作用下将金属液体浇入金属铸型以 获得铸件的方法。铸型用金属制成,可反复使用,故又称永久 型铸造。
前一页
后一页
回主页
金属型铸造
特点: •节省造型材料, “一型多铸” •精度高,IT12~IT16,Ra<12.5μm •生产率高 •周期长,成本高,工艺参数严格 •无透气性,浇不到、裂纹等缺陷。
这些有别于砂型铸造的其他铸造方法通称为特种铸造。 金属型铸造
挤压铸造 离心铸造 七 种 常 见 的 特 种 铸 造 方 法
回主页
压力铸造
特种铸造 陶瓷型铸造 低压铸造
前一页 后一页
熔模铸造
熔模铸造
在易熔模样表面包覆若干层耐火材料,待其硬化干燥后, 将模样熔去制成中空型壳,经浇注而获得铸件的一种 成形工艺方法。模样材料多位蜡质,又称为失蜡铸造。
前一页
后一页
回主页
低压铸造
1、低压铸造的工艺过程 :
1)准备合金液和铸型 2)升液,浇注。
3)增压凝固。 4)减压、降液。 5)开型取出铸件。
前一页
后一页
回主页
低压铸造
特点:
•充型压力和速度便于控制,适用于各种铸型;
铸造工艺基础(1)
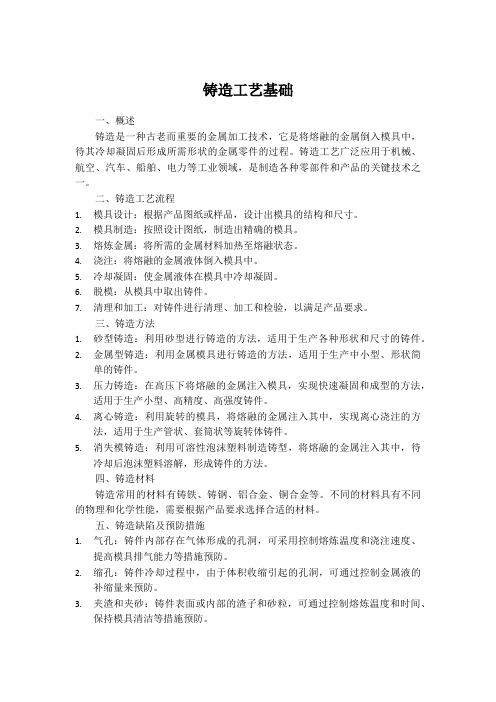
铸造工艺基础一、概述铸造是一种古老而重要的金属加工技术,它是将熔融的金属倒入模具中,待其冷却凝固后形成所需形状的金属零件的过程。
铸造工艺广泛应用于机械、航空、汽车、船舶、电力等工业领域,是制造各种零部件和产品的关键技术之一。
二、铸造工艺流程1.模具设计:根据产品图纸或样品,设计出模具的结构和尺寸。
2.模具制造:按照设计图纸,制造出精确的模具。
3.熔炼金属:将所需的金属材料加热至熔融状态。
4.浇注:将熔融的金属液体倒入模具中。
5.冷却凝固:使金属液体在模具中冷却凝固。
6.脱模:从模具中取出铸件。
7.清理和加工:对铸件进行清理、加工和检验,以满足产品要求。
三、铸造方法1.砂型铸造:利用砂型进行铸造的方法,适用于生产各种形状和尺寸的铸件。
2.金属型铸造:利用金属模具进行铸造的方法,适用于生产中小型、形状简单的铸件。
3.压力铸造:在高压下将熔融的金属注入模具,实现快速凝固和成型的方法,适用于生产小型、高精度、高强度铸件。
4.离心铸造:利用旋转的模具,将熔融的金属注入其中,实现离心浇注的方法,适用于生产管状、套筒状等旋转体铸件。
5.消失模铸造:利用可溶性泡沫塑料制造铸型,将熔融的金属注入其中,待冷却后泡沫塑料溶解,形成铸件的方法。
四、铸造材料铸造常用的材料有铸铁、铸钢、铝合金、铜合金等。
不同的材料具有不同的物理和化学性能,需要根据产品要求选择合适的材料。
五、铸造缺陷及预防措施1.气孔:铸件内部存在气体形成的孔洞,可采用控制熔炼温度和浇注速度、提高模具排气能力等措施预防。
2.缩孔:铸件冷却过程中,由于体积收缩引起的孔洞,可通过控制金属液的补缩量来预防。
3.夹渣和夹砂:铸件表面或内部的渣子和砂粒,可通过控制熔炼温度和时间、保持模具清洁等措施预防。
4.裂纹:铸件冷却过程中产生的裂纹,可通过优化模具设计和制造工艺、控制铸件壁厚等措施预防。
5.组织疏松:铸件内部组织不紧密,可通过控制熔炼温度和浇注温度等措施预防。
铸造工艺学讲义一(基础知识)

一.熔模铸造 二.金属型铸造 三.压力铸造
第五节 零件结构的铸造工艺性
一.铸件结构的合理性 二.铸件结构的工艺性 三.铸造方法对铸件结构的特殊要求
2
前言
商代司母戊鼎
中国商代晚期的青铜器。1939年于河南安阳殷墟商代晚期墓 出土。因腹内壁铸有“司母戊”三字而得名。该鼎造型庄严雄伟。 长方形腹,每面四边及足上部饰兽面纹。双耳,外侧饰双虎噬人 首纹。四足中空。高133厘米、口长110厘米、口宽79厘米、重 832.84千克。该鼎的化学成分为:铜84.77%,锡11.64%,铅2.79%, 其他0.8%。是中国目前已发现的最大、最重的古代青铜器。
b) 进行去应力退火 铸件机加工之前应先采用时效或去应力退
液态收缩与凝固收缩 主要表现为体积的缩减,
产生缩孔、缩松 固态收缩
导致尺寸减小,产生内 应力和出现裂纹。
18
(三) 影响合金收缩的因素
1. 化学成分 不同成分的合金其收缩率一般也不相同。在常用铸造 合金中铸刚的收缩最大,灰铸铁最小。 2. 浇注温度 合金浇注温度越高,过热度越大,液体收缩越大。 3. 铸件结构与铸型条件 铸件冷却收缩时,因其形状、尺寸的不同, 各部分的冷却速度不同,导致收缩不一致,且互相阻碍,又加之 铸型和型芯对铸件收缩的阻力,故铸件的实际收缩率总是小于其 自由收缩率。这种阻力越大,铸件的实际收缩率就越小。
图1-7 缩松形成过程示意图
21
比较缩孔和缩松的特征
缩孔:集中性,位于上部,呈倒锥形,内表面粗糙。
缩松: 分散性,为细小缩孔,位于铸件壁的轴线区域。
22
2.缩孔、缩松的防止措施 1).定向凝固与同时凝固
按铸件壁厚分布均匀程度不同(即冷却快慢不同),分为: 定向凝固(或称顺序凝固)-薄部先凝固,厚部后凝固,冒口最后 凝固。 同时凝固(厚薄不同部位趋近同时凝固,金属液从薄部引入)。
铝合金铸造基础知识

5 、铝硅合金中其它元素的作用:
镁:可提高强度和屈服极限,提高了合金的切削加工性。 锌:锌在铝合金中能提高流动性,增加热脆性,降低耐蚀性,故应控制锌的含 量在规定范围中。 铁:铁以FeAl3、Fe2Al7和Al-Si- Fe的片状或针状组织存在于合金中,降低 机械性能,这种组织还会使合金的流动 性减低,热裂性增大,但由于铝合金对模具 的粘附作用十分强烈,当铁含量在 0.6%以下时尤为强烈。当超过0.6%后,粘模现 象便大为减轻,故含铁量一般应控制在0.6~1%范围内对压铸是有好处的,但最高 不能超过1.5%。 锰:锰在铝合金中能减少铁的有害影响,能使铝合金中由铁形成的片状或针状 组织变为细密的晶体组织,故一般铝合金允许有0.5%以下的锰存在。含锰量过高时, 会引起偏析。 镍:镍在铝合金中能提高合金的强度和硬度,降低耐蚀性。镍与铁的作用一样, 能减少合金对模具的熔蚀,同时又能中和铁的有害影响,提高合金的焊接性能。 钛:能显著细化铝合金的晶粒组织,提高合金的机械性能,降低合的热裂倾向。
三.铸造基本知识
1、定义:铸造就是液态金属的一种成型方式。 2、铸造的分类: 铸造的种类较多,有传统的砂型铸造、重力铸造、熔模铸造、高压铸造、低压铸造、 消失模具铸造、离心铸造、陶瓷型铸造、连续铸造等。 3、我厂采用的铸造方法主要有以下几种: ⑴、金属型铸造(重力铸造) 金属型铸造又称硬模铸造,它是将液体金属浇入金属铸型,在重力的作用下结晶凝固 以获得铸件的一种铸造方法。凝固顺序是自下而上的。 ⑵、高压铸造 压力铸造是将液态或半液态金属, 在高压作用下, 以高的速度填充压铸模的型腔, 并在压力下快速凝固而获得铸件的一种方法。压铸时常用压力是从几兆帕至几十兆帕 (即几十到几百个大气压) , 填充初始速度在 0.5~70m/s 范围内。因此, 高压和高速 是压铸法与其他铸造法的根本区别, 也是重要特征 。
熔模铸造的工艺设计要点及注意事项
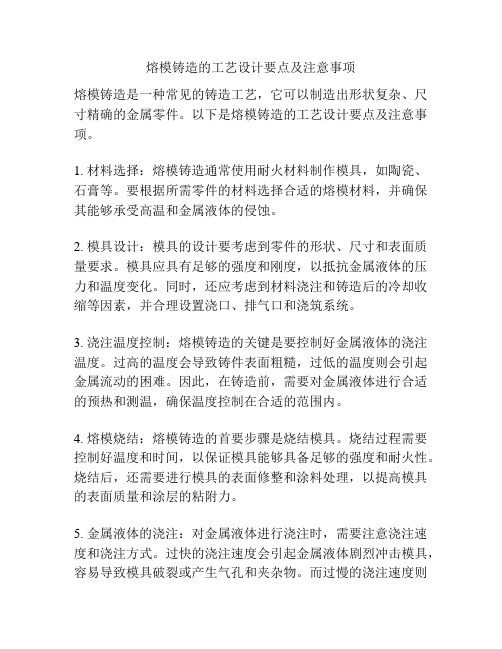
熔模铸造的工艺设计要点及注意事项熔模铸造是一种常见的铸造工艺,它可以制造出形状复杂、尺寸精确的金属零件。
以下是熔模铸造的工艺设计要点及注意事项。
1. 材料选择:熔模铸造通常使用耐火材料制作模具,如陶瓷、石膏等。
要根据所需零件的材料选择合适的熔模材料,并确保其能够承受高温和金属液体的侵蚀。
2. 模具设计:模具的设计要考虑到零件的形状、尺寸和表面质量要求。
模具应具有足够的强度和刚度,以抵抗金属液体的压力和温度变化。
同时,还应考虑到材料浇注和铸造后的冷却收缩等因素,并合理设置浇口、排气口和浇筑系统。
3. 浇注温度控制:熔模铸造的关键是要控制好金属液体的浇注温度。
过高的温度会导致铸件表面粗糙,过低的温度则会引起金属流动的困难。
因此,在铸造前,需要对金属液体进行合适的预热和测温,确保温度控制在合适的范围内。
4. 熔模烧结:熔模铸造的首要步骤是烧结模具。
烧结过程需要控制好温度和时间,以保证模具能够具备足够的强度和耐火性。
烧结后,还需要进行模具的表面修整和涂料处理,以提高模具的表面质量和涂层的粘附力。
5. 金属液体的浇注:对金属液体进行浇注时,需要注意浇注速度和浇注方式。
过快的浇注速度会引起金属液体剧烈冲击模具,容易导致模具破裂或产生气孔和夹杂物。
而过慢的浇注速度则会导致金属液体凝固不完全。
此外,还需注意金属液体的均匀浇注,避免产生冷隔。
6. 冷却和晾热处理:在铸造完成后,需要对铸件进行冷却和晾热处理。
冷却过程应缓慢进行,以防止因温度变化引起的热应力和变形。
晾热处理有助于提高铸件的机械性能和组织均匀性。
总之,熔模铸造的工艺设计要点及注意事项包括材料选择、模具设计、浇注温度控制、熔模烧结、金属液体的浇注和冷却晾热处理等。
合理的工艺设计能够确保铸件的质量和精度,提高生产效率和产品品质。
继续写:7. 模具温度控制:熔模铸造中,模具温度的控制是非常重要的。
模具的温度过高会导致模具磨损加剧,模具寿命减少,并且可能引起铸件的气孔和缺陷。
- 1、下载文档前请自行甄别文档内容的完整性,平台不提供额外的编辑、内容补充、找答案等附加服务。
- 2、"仅部分预览"的文档,不可在线预览部分如存在完整性等问题,可反馈申请退款(可完整预览的文档不适用该条件!)。
- 3、如文档侵犯您的权益,请联系客服反馈,我们会尽快为您处理(人工客服工作时间:9:00-18:30)。
铸造工艺基础知识一、铸造方法常见的铸造方法有以下几种:1、砂型铸造:砂型铸造是将原砂和粘结剂、辅助材料按一定比例混制好以后,用模型造出砂型,浇入液体金属而形成铸件的一种方法。
砂型铸造是应用最普遍的一种铸造方法。
2、熔模铸造:熔模铸造又称“失蜡铸造”,通常是在蜡模表面涂上数层耐火材料,待其硬化干燥后,将其中的蜡模熔去而制成型壳,再经过焙烧,然后进行浇注,而获得铸件的一种方法。
由于获得的铸件具有较高的尺寸精度和表面粗糙度,所以又称“熔模精密铸造”。
3、金属型铸造:金属型铸造又称硬模铸造,它是将液体金属用重力浇注法浇入金属铸型,以获得铸件的一种铸造方法。
所以又称“重力铸造”。
4、低压铸造:低压铸造是液体金属在压力作用下由下而上的充填型腔,以形成铸件的一种方法。
由于所用的压力较低,所以叫低压铸造。
5、压力铸造:压力铸造简称压铸,是在高压作用下,使液态或半液态金属以较高的速度充填压铸型型腔,并在压力作用下凝固而获得铸件的一种方法。
.6、离心铸造:离心铸造是将液体金属浇入旋转的铸型中,使液体金属在离心力的作用下充填铸型和凝固成形的一种铸造方法。
7、连续铸造:连续铸造是将熔融的金属不断浇入一种叫做结晶器的特殊金属型中,凝固了的铸件连续不断的从结晶器的另一端拉出,从而获得任意长度或特定长度铸件的一种方法。
8、消失模铸造:消失模铸造是采用泡沫气化模造型,浇注前不用取出模型,直接往模型上浇注金属液,模型在高温下气化,腾出空间由金属液充填成型的一种铸造方法。
也叫“实型铸造”。
二、零件结构的铸造工艺性分析零件结构的铸造工艺性通常指的是零件的本身结构应符合铸造生产的要求,既便于整个铸造工艺过程的进行,又利于保证产品质量。
对产品零件图进行分析有两方面的作用:第一,审查零件结构是否符合铸造生产的工艺要求。
因为零件的设计者往往不完全了解铸造工艺。
如发现结构设计有不合理的地方,就要与有关方面进行研究,在不影响使用要求的前提下,予以改进。
这对简化工艺过程、保证质量及降低成本均有极大作用。
第二,在既定的零件结构条件下,考虑在铸造过程中可能出现的主要缺陷,在工艺设计中采取相应工艺措施予以避免。
(一)从避免缺陷方面审查铸件结构的合理性.1、铸件应有合理的壁厚每一种合金都有其适宜的壁厚范围。
壁厚太薄,容易出现浇不足;太厚,容易出现晶粒粗大,机械性能降低。
2、铸件收缩时不应有严重阻碍,注意壁厚的过渡和铸造圆角铸件厚薄相接、拐弯、交接之处,都应采取逐渐过渡和转变的形式,并应采用较大圆角相连接,以免造成突然转变以及应力集中,引起裂纹等缺陷。
对于牌号较高、收缩大的合金铸件尤其注意,以防止因严重阻碍铸件收缩而造成裂纹。
3、内壁厚度应小于外壁厚度铸件内部的筋和壁等,散热条件较差,因此应比外壁薄些,以便使整个铸件的外壁和内壁能均匀的冷却,防止产生内应力和裂纹。
4、壁厚力求均匀,减少厚大部分,防止形成热节如果壁厚不均匀,铸件冷却也不均匀,在交接处易产生内应力、易于形成缩松、缩孔和裂纹。
5、有利于补缩和实现顺序凝固对于厚大件,应根据零件特点,设置冒口,进行补缩。
6、注意防止铸件的翘曲变形对于细长件、大的平板件,在铸件收缩时,由于冷却不一致,很容易引起翘曲变形。
应多布置加强筋,防止此类变形。
7、避免水平方向出现较大的平面在浇注时,水平大平面液流上升速度很慢,较长时间烘烤铸型顶面,极易造成夹砂、浇不足等缺陷,也不利于金属夹杂物和气体的排.出。
(二)从简化铸造工艺过程角度审查零件结构的工艺性1、改进妨碍起模的凸台、凸缘、筋板的结构铸件侧壁上的凸台(搭子)、凸缘、筋板等,常常妨碍起模,不得不增加砂芯。
所以,尽量改进,以简化铸造模具。
2、尽量取消铸件外表侧凹铸件侧壁上如有凹入部分,常常妨碍起模,不得不增加砂芯。
所以,尽量改进,以简化铸造模具。
3、改进铸件内腔结构,减少砂芯数量4、减少和简化分型面尽量采用平直分型面,减少曲面分型。
5、有利于砂芯的固定和排气底面有利于砂芯固定,顶面有利于砂芯排气。
6、去除不必要的圆角有些外圆角对铸件质量影响不大,但却对造型和制芯等工艺过程有不良效果,应予以去除。
三、造型、制芯方法产品零件设计结束后,应根据产品结构及铸造厂的实际情况,确定合理的造型、制芯方式。
以下简单介绍当前广泛应用的各种造型、制芯方式。
(一)造型方法、手工造型(手工粘土砂、手工树脂砂)1.手工造型适宜于简单、小批量多品种铸件。
砂型硬度低,表面粗糙度、尺寸精度差,效率低。
2、普通机器造型(Z145、Z148、Z1410等)普通机器造型适宜于批量较大、产品要求较高的铸件。
砂型硬度中等,表面粗糙度、尺寸精度较好,效率较高。
3、高压造型(平压头、成型压头、多触头)高压造型适宜于批量不大、尺寸较大的铸件。
砂型硬度高、表面粗糙度、尺寸精度较好,效率较高。
4、水平分型流水线造型(静压线、KW线)水平分型流水线造型适宜于大批量、复杂铸件。
砂型硬度很高、表面粗糙度、尺寸精度很好,效率很高。
5、垂直分型流水线造型(DISA线)垂直分型流水线造型适宜于大批量、尺寸中等及较小的铸件,尤其适宜于球铁件。
砂型硬度很高、表面粗糙度、尺寸精度很好,效率很高。
(二)制芯方法1、手工制芯(粘土砂、合脂油、树脂砂)手工制芯适宜于简单、小批量铸件。
表面粗糙度、尺寸精度差,效率低。
2、热芯盒制芯(6kg、12kg、25kg、40kg、100kg)热芯盒制芯是将混制好的热芯砂(或覆膜砂)通过热芯盒射芯机℃下保温一段时间,然后开模取出成220-260射入热芯盒模具内,在.品砂芯的一种制芯方式。
热芯盒制芯目前应用广泛,它的适用范围很广,几乎所有砂芯都可以用它制作。
砂芯强度很高,表面粗糙度、尺寸精度很好,效率很高。
3、壳芯盒制芯壳芯盒制芯是将成品覆膜砂通过壳芯机射入壳芯盒模具内,待周边形成8mm左右硬壳后,旋转,倒出剩余余砂,在220-260℃下保温一段时间,然后开模取出成品砂芯的一种制芯方式。
壳芯盒制芯应用范围也很广泛,主要应用于简单、圆周类砂芯。
砂芯强度很高,表面粗糙度、尺寸精度很好,效率很高。
4、冷芯盒制芯冷芯盒制芯是将混制好的冷芯砂通过冷芯盒射芯机射入冷芯盒内,然后吹入气体(三乙胺或二氧化硫)固化的一种制芯方式,因为它在常温下固化,所以叫冷芯盒制芯。
冷芯盒制芯是目前应用最广泛的一种制芯方式,几乎所有砂芯都可以用它制作。
砂芯强度很高,表面粗糙度、尺寸精度很好,效率很高。
砂芯发气量低、溃散性好。
四、砂型铸造铸件浇注位置的确定铸件的浇注位置是指浇注时铸件在型内所处的位置。
浇注位置的确定是铸造工艺设计中重要的一环,关系到铸件的质量能否得到保证,也涉及铸件尺寸精度以及造型工艺过程。
、铸件的重要加工面应朝下或呈侧立面1.这是因为气孔、非金属夹杂物等容易出现在上表面,铸件向下的底面和侧立面通常比较光洁,出现缺陷的可能性小,而且底面组织致密。
2、尽可能使铸件的大平面朝下,以避免形成夹砂和夹杂缺陷对于大的平板类铸件,必要时可采用倾斜浇注,以增加液体金属的上升速度,防止夹砂缺陷。
3、应保证铸件能充满铸件很薄的部分应朝下。
4、应有利于实现顺序凝固对厚薄不均、易于形成缩孔、缩松或质量要求较高的铸件,浇注位置的选择应有利于实现顺序凝固。
5、应尽可能避免使用吊砂、吊芯或悬臂式砂芯6、应使合箱位置、浇注位置和铸件的冷却位置相一致针对手工生产,与机器造型及流水线造型无关。
五、分型面的选择分型面是指两半铸型相互接触的表面。
除了实型铸造法以外,都要选择分型面。
有时是平面,有时是曲面。
1、应尽量使铸件全部或大部置于同一半型内两半型铸件总是或多或少有一些错移,影响铸件尺寸精度。
2、应尽量减少分型面的数目此指手工多箱造型。
、便于下芯、合箱及检查型腔尺寸3.因此,应尽量把主要砂芯放在下半砂箱中。
4、应注意减轻落砂、清理和机械加工的工作量应尽量减小分型面飞边、披缝。
六、砂芯设计砂芯设计在铸造工艺中很关键,它直接影响着铸件的尺寸精度以及相互关联尺寸。
1、涂料层厚度应根据每个厂家的具体情况、涂料种类,确定相应的涂料层厚度。
在模具设计中予以增加涂料层厚度。
2、芯头间隙应根据芯头大小和具体结构,选择合理的芯头间隙。
一般控制在0.1-0.5mm之间。
上芯头间隙大,下芯头间隙小。
3、芯头斜度为方便合箱,砂芯芯头要设计拔模斜度。
一般上芯头斜度大,下芯头斜度小。
4、特殊定位芯头对于有方向要求的圆芯头,必须设计缺口定位,以保证产品内部形状方向准确。
5、压环设计为保证砂型能紧紧压住砂芯,经常在上模样芯头顶面设计一圈半圆凹沟,造型后在上模型形成一凸起环形砂,合箱后能紧紧压住砂芯,芯头定位牢固。
.6、防压环设计在模样水平芯头靠近模样的根部,设计凸起圆环,高度为0.5-1mm,宽度为5-10mm。
造型后,相应部位形成一下凹的环状缝隙。
下芯、合箱时,它可防止此处砂型被压塌,因而可防止掉砂缺陷。
7、挤砂槽设计在下模样芯头边缘设计一道凸起圆环,深度约2-5mm。
造型后,在砂型内形成一环凹槽,用来存放个别散落砂粒。
七、铸造工艺参数设计1、铸造收缩率影响铸造收缩率的因素很多,如:合金的种类及成分,铸件冷却、收缩时受到阻力的大小,冷却条件的差异等。
每个铸造厂家,应根据自己的生产条件,确定合适的铸造收缩率。
一般,铸铁取1℅。
2、机械加工余量在铸件加工表面上留出的、准备切去的金属层厚度,称为机械加工余量。
机械加工余量应根据铸件大小、造型方式所达到的铸件精度、加工表面所处的浇注位置、铸件结构而确定。
3、拔模斜度影响拔模斜度的因素也很多。
如:铸件大小、模样高度、模样的表面粗糙度、造型方式等。
一般取30′- 3°。
4、最小铸出孔及槽应根据模具表面粗糙度、拔模斜度、孔的深度等,来确定最小铸.出孔及槽。
铸铁件流水线造型能铸出12-15mm的最小孔及槽。
5、工艺补正量对于需加工孔的圆凸台、棋子,设计图纸尺寸往往偏小,铸造时需人为加大尺寸,此即工艺补正量。
6、分型负数对于干模及树脂砂生产的大铸件,在合箱时为了防止跑火,在分型面处常常用石棉绳或其它东西密封,容易垫高砂型,影响铸件尺寸。
所以设计模样时,往往在分型面处人为减小模样尺寸,此即分型负数。
7、反变形量在铸造较大平板类、床身类铸件时,由于冷却速度的不均匀性,铸件冷却后常出现变形。
在制造模样时,按铸件可能产生变形的相反方向做出反变形模样,使铸件冷却后变形的结果正好将反变形抵消。
此予变形量即反变形量。
8、砂芯负数大芯盒制芯时,由于分盒面接触面积太大,制出的砂芯总是或多或少有一定披缝,砂芯尺寸比模具尺寸大。
所以,设计芯盒时,人为减小一定尺寸,此即砂芯负数。
射芯机制芯一般取0.2-0.3mm。
八、浇注系统设计1、浇口杯设计(1)浇口杯形状浇口杯形状分为漏斗形和池形两大类。
漏斗形简单,挡渣作用小,主要用于池形浇口杯挡渣作用较好,主要用于小型铸铁件及铸钢件。