铝合金低熔点共晶物
《铝合金熔铸加工技术原理》(四)
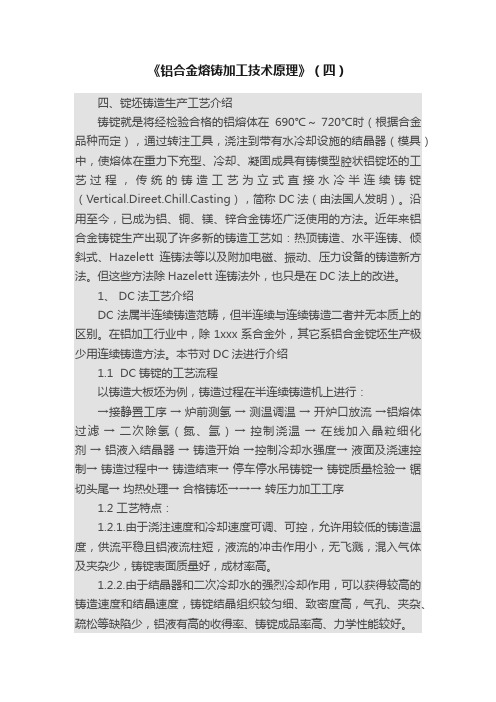
《铝合金熔铸加工技术原理》(四)四、锭坯铸造生产工艺介绍铸锭就是将经检验合格的铝熔体在690℃~ 720℃时(根据合金品种而定),通过转注工具,浇注到带有水冷却设施的结晶器(模具)中,使熔体在重力下充型、冷却、凝固成具有铸模型腔状铝锭坯的工艺过程,传统的铸造工艺为立式直接水冷半连续铸锭(Vertical.Direet.Chill.Casting),简称DC法(由法国人发明)。
沿用至今,已成为铝、铜、镁、锌合金铸坯广泛使用的方法。
近年来铝合金铸锭生产出现了许多新的铸造工艺如:热顶铸造、水平连铸、倾斜式、Hazelett连铸法等以及附加电磁、振动、压力设备的铸造新方法。
但这些方法除Hazelett连铸法外,也只是在DC法上的改进。
1、 DC法工艺介绍DC法属半连续铸造范畴,但半连续与连续铸造二者并无本质上的区别。
在铝加工行业中,除1xxx系合金外,其它系铝合金锭坯生产极少用连续铸造方法。
本节对DC法进行介绍1.1 DC铸锭的工艺流程以铸造大板坯为例,铸造过程在半连续铸造机上进行:→接静置工序→炉前测氢→测温调温→开炉口放流→铝熔体过滤→二次除氢(氮、氩)→控制浇温→在线加入晶粒细化剂→铝液入结晶器→铸造开始→控制冷却水强度→液面及浇速控制→铸造过程中→铸造结束→停车停水吊铸锭→铸锭质量检验→锯切头尾→均热处理→合格铸坯→→→转压力加工工序1.2 工艺特点:1.2.1.由于浇注速度和冷却速度可调、可控,允许用较低的铸造温度,供流平稳且铝液流柱短,液流的冲击作用小,无飞溅,混入气体及夹杂少,铸锭表面质量好,成材率高。
1.2.2.由于结晶器和二次冷却水的强烈冷却作用,可以获得较高的铸造速度和结晶速度,铸锭结晶组织较匀细、致密度高,气孔、夹杂、疏松等缺陷少,铝液有高的收得率、铸锭成品率高、力学性能较好。
1.2.3.生产过程机械化程度高,工人劳动强度较小,生产率高。
1.2.4.工艺条件要求严格,技术性强,熟练掌握难度大。
铝合金热处理基本形式
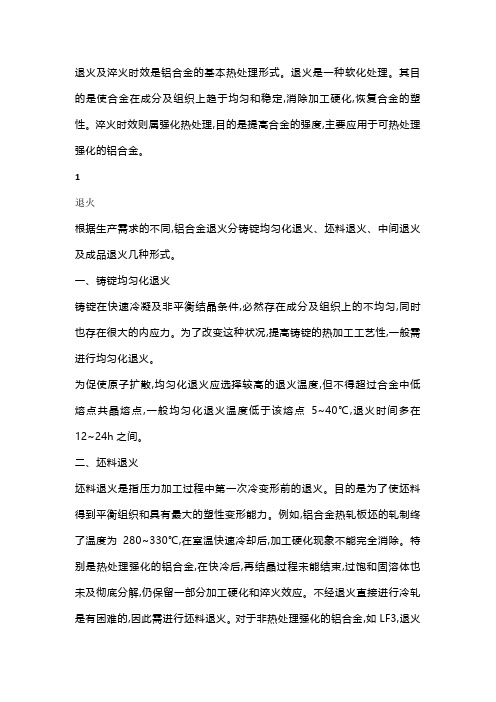
退火及淬火时效是铝合金的基本热处理形式。
退火是一种软化处理。
其目的是使合金在成分及组织上趋于均匀和稳定,消除加工硬化,恢复合金的塑性。
淬火时效则属强化热处理,目的是提高合金的强度,主要应用于可热处理强化的铝合金。
1退火根据生产需求的不同,铝合金退火分铸锭均匀化退火、坯料退火、中间退火及成品退火几种形式。
一、铸锭均匀化退火铸锭在快速冷凝及非平衡结晶条件,必然存在成分及组织上的不均匀,同时也存在很大的内应力。
为了改变这种状况,提高铸锭的热加工工艺性,一般需进行均匀化退火。
为促使原子扩散,均匀化退火应选择较高的退火温度,但不得超过合金中低熔点共晶熔点,一般均匀化退火温度低于该熔点5~40℃,退火时间多在12~24h之间。
二、坯料退火坯料退火是指压力加工过程中第一次冷变形前的退火。
目的是为了使坯料得到平衡组织和具有最大的塑性变形能力。
例如,铝合金热轧板坯的轧制终了温度为280~330℃,在室温快速冷却后,加工硬化现象不能完全消除。
特别是热处理强化的铝合金,在快冷后,再结晶过程未能结束,过饱和固溶体也未及彻底分解,仍保留一部分加工硬化和淬火效应。
不经退火直接进行冷轧是有困难的,因此需进行坯料退火。
对于非热处理强化的铝合金,如LF3,退火温度为370~470℃,保温1.5~2.5H后空冷,用于冷拉伸管加工的坯料、退火温度应适当高一些,可选上限温度。
对于可热处理强化的铝合金,如LY11及LY12,坯料退火温度为390~450℃,保温1~3H,随后在炉中以不大于30℃/h的速度冷却到270℃以下再出炉空冷。
三、中间退火中间退火是指冷变形工序之间的退火,其目的是为了消除加工硬化,以利于继续冷加工变形。
一般来说,经过坯料退火后的材料,在承受45~85%的冷变形后,如不进行中间退火而继续冷加工将会发生困难。
中间退火的工艺制度基本上与坯料退火相同。
根据对冷变形程度的要求,中间退火可分为完全退火(总变形量ε≈60~70%),简单退火(ε≤50%)和轻微退火(ε≈30~40%)三种。
铝合金过烧概述

铝合金的过烧铝合金当加热温度高于低熔点共晶的熔点,使低熔点共晶和晶界复熔的现象叫过烧。
(1)过烧的宏观组织特征。
过烧严重时铸锭和加工制品表面色泽变暗、变黑,有时产生表面起泡。
(2)过烧的显微组织典型特征。
检查铸锭及加工制品是否过烧,只以显微组织特征为依据,其他方法只能作为旁证。
对变形铝合金,根据国家标准,过烧的判定特征有3个,即复熔共晶球、晶界局部复熔加宽和3个晶粒交叉处形成复熔三角形。
用电子显微镜对复熔三角形处组织的研究发现,与复熔产物相接触的基体有梯田花样。
梯田花样是枝晶露头的结晶台阶,与疏松内壁表面上的枝晶露头一样,表明该处的组织已发生过复熔。
一般将过烧程度分为轻微过烧、过烧和严重过烧。
轻微过烧指过烧特征轻微,过烧指过烧特征明显,严重过烧指过烧特征多,晶界严重复熔粗化和平直,低熔点共晶大量熔化和聚集。
轻微过烧判断较难,要判断准确必须有丰富的经验。
(3)过烧形成机理。
变形铝合金中,除α(A1)基体外一般都有几种共晶,根据合金的不同,含有共晶的种类和多少也不同。
如果在一种合金里有几种共晶,每种共晶的熔化温度不尽相同,当把合金从低温升到高温时,熔点最低的共晶必首先熔化,这个共晶熔化的温度称为过烧温度,而这种共晶被称为低熔点共晶,即熔点最低的共晶。
例如2A12合金主要有两种共晶:α(Al)+CuAl2:熔点548℃α(Al)+CuAl2+Al2CuMg(S相):熔点507℃三元共晶的熔点比二元共晶低得多,当合金在较高温度热处理时,三元共晶必首先熔化,其熔化温度(507℃)即为2A12合金的过烧温度。
(4)防止措施:1)严格控制热处理的温度和保温时间;2)高温仪表定期检定,不允许使用检定不合格或超期仪表;3)热处理炉内温度要均匀,炉料不能有油污,摆放要合理;4)操作时要看对合金和卡片。
(5)过烧对性能的影响。
合金过烧后,低熔点共晶在晶界上和基体内复熔又凝固,改变了过烧前该处组织紧密相联的状态,对合金的连续性造成了普遍损害,对合金的力学性能、疲劳和腐蚀性能等都产生严重影响。
A356铸造铝合金相标准

【自学街】国内UG第一交流学习平台QJ/TCA356铸造铝合金金相标准江门市天丞车轮有限公司发布QJ/TC011—2009前言本标准作为天丞车轮有限公司的A356铸造铝合金金相技术标准初次发布。
本标准由天丞车轮有限公司工程技术部提出并归口。
本标准起草单位:天丞车轮有限公司工程技术部本标准主要起草人:何悦贵吴嘉良本标准由天丞车轮有限公司工程技术部负责解释。
签字:批准日期:本标准首次发布日期:2009年12月20日第一部分:A356铸造铝合金变质金相标准1. 范围本标准规定了对A356铸造铝合金铸态变质的分级原则和评级方法。
本标准适用于评定经锶或锑变质的A356铸造铝合金的金相组织。
2. A356铸造铝硅合金变质组织2.1 试样的切取和制备2.1.1 铸态金相试样通常在未热处理的毛坯上取样。
2.1.2 在切取和制备金相试样的过程中用手锯取切,磨削时加注冷却水以保证不使其2组织发生变化。
2.1.3 金相试样经水砂纸、金相纸粗磨、细磨后进行机械抛光,必要时,可进行手工精抛。
2.1.4 经抛光后的金相试样用0.5%氢氟酸水溶液在室温下侵蚀5-10S。
2.2 显微检验2.2.1 用光学金相显微镜评定铸造铝合金的变质组织,其放大倍数为200倍。
2.2.2 显微检验时,应首先通观整个受检面,然后按大多数视场对应级别图进行评定。
2.3 A356铸造铝合金变质组织为未变质、变质不足、变质正常三级。
2.3.1 未变质共晶硅为长尖形、长条状,分布无规律,可有α支晶或少量块状初晶硅,见图一图一共晶硅未变质X2002.3.2 变质不足α支晶与共晶体分布不均匀,共晶硅呈层状分布,有部分短杆状或针状,有个别块状初晶硅。
见图二A、图二B。
图二A 共晶硅变质不足X200图二B 共晶硅变质不足X2002.3.3 变质正常1级变质正常组织(见图三A):α支晶细小与共晶体分布均匀,共晶体成纤维状。
2级变质正常组织(见图三B):α支晶较细与共晶体分布基本均匀,共晶体成纤维状,有部分点状,短条状。
铝合金热处理方法
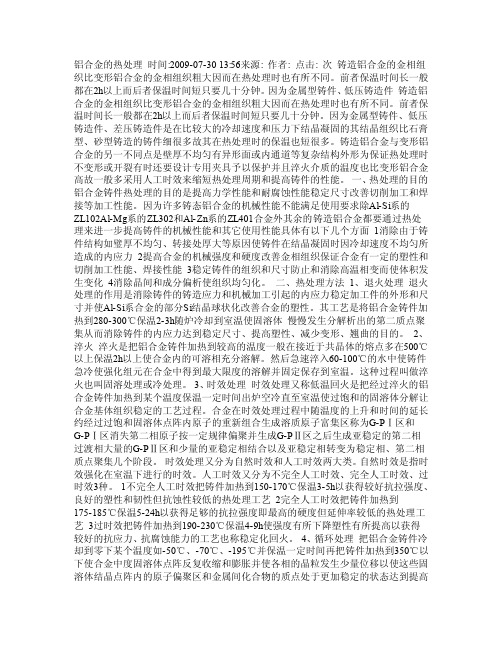
铝合金的热处理时间:2009-07-30 13:56来源: 作者: 点击: 次铸造铝合金的金相组织比变形铝合金的金相组织粗大因而在热处理时也有所不同。
前者保温时间长一般都在2h以上而后者保温时间短只要几十分钟。
因为金属型铸件、低压铸造件铸造铝合金的金相组织比变形铝合金的金相组织粗大因而在热处理时也有所不同。
前者保温时间长一般都在2h以上而后者保温时间短只要几十分钟。
因为金属型铸件、低压铸造件、差压铸造件是在比较大的冷却速度和压力下结晶凝固的其结晶组织比石膏型、砂型铸造的铸件细很多故其在热处理时的保温也短很多。
铸造铝合金与变形铝合金的另一不同点是壁厚不均匀有异形面或内通道等复杂结构外形为保证热处理时不变形或开裂有时还要设计专用夹具予以保护并且淬火介质的温度也比变形铝合金高故一般多采用人工时效来缩短热处理周期和提高铸件的性能。
一、热处理的目的铝合金铸件热处理的目的是提高力学性能和耐腐蚀性能稳定尺寸改善切削加工和焊接等加工性能。
因为许多铸态铝合金的机械性能不能满足使用要求除Al-Si系的ZL102Al-Mg系的ZL302和Al-Zn系的ZL401合金外其余的铸造铝合金都要通过热处理来进一步提高铸件的机械性能和其它使用性能具体有以下几个方面1消除由于铸件结构如璧厚不均匀、转接处厚大等原因使铸件在结晶凝固时因冷却速度不均匀所造成的内应力2提高合金的机械强度和硬度改善金相组织保证合金有一定的塑性和切削加工性能、焊接性能3稳定铸件的组织和尺寸防止和消除高温相变而使体积发生变化4消除晶间和成分偏析使组织均匀化。
二、热处理方法1、退火处理退火处理的作用是消除铸件的铸造应力和机械加工引起的内应力稳定加工件的外形和尺寸并使Al-Si系合金的部分Si结晶球状化改善合金的塑性。
其工艺是将铝合金铸件加热到280-300℃保温2-3h随炉冷却到室温使固溶体慢慢发生分解析出的第二质点聚集从而消除铸件的内应力达到稳定尺寸、提高塑性、减少变形、翘曲的目的。
铸造7075铝合金扁锭的成分优化与控制
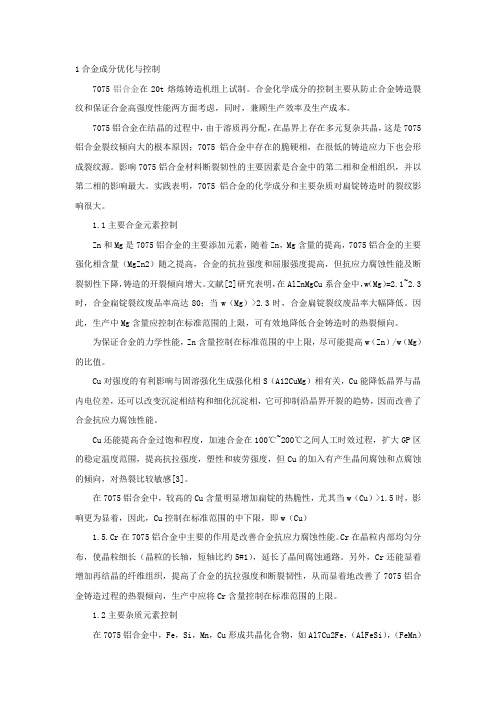
1合金成分优化与控制7075铝合金在20t熔炼铸造机组上试制。
合金化学成分的控制主要从防止合金铸造裂纹和保证合金高强度性能两方面考虑,同时,兼顾生产效率及生产成本。
7075铝合金在结晶的过程中,由于溶质再分配,在晶界上存在多元复杂共晶,这是7075铝合金裂纹倾向大的根本原因;7075铝合金中存在的脆硬相,在很低的铸造应力下也会形成裂纹源。
影响7075铝合金材料断裂韧性的主要因素是合金中的第二相和金相组织,并以第二相的影响最大。
实践表明,7075铝合金的化学成分和主要杂质对扁锭铸造时的裂纹影响很大。
1.1主要合金元素控制Zn和Mg是7075铝合金的主要添加元素,随着Zn,Mg含量的提高,7075铝合金的主要强化相含量(MgZn2)随之提高,合金的抗拉强度和屈服强度提高,但抗应力腐蚀性能及断裂韧性下降,铸造的开裂倾向增大。
文献[2]研究表明,在AlZnMgCu系合金中,w(Mg)=2.1~2.3时,合金扁锭裂纹废品率高达80;当w(Mg)>2.3时,合金扁锭裂纹废品率大幅降低。
因此,生产中Mg含量应控制在标准范围的上限,可有效地降低合金铸造时的热裂倾向。
为保证合金的力学性能,Zn含量控制在标准范围的中上限,尽可能提高w(Zn)/w(Mg)的比值。
Cu对强度的有利影响与固溶强化生成强化相S(A12CuMg)相有关,Cu能降低晶界与晶内电位差,还可以改变沉淀相结构和细化沉淀相,它可抑制沿晶界开裂的趋势,因而改善了合金抗应力腐蚀性能。
Cu还能提高合金过饱和程度,加速合金在100℃~200℃之间人工时效过程,扩大GP区的稳定温度范围,提高抗拉强度,塑性和疲劳强度,但Cu的加入有产生晶间腐蚀和点腐蚀的倾向,对热裂比较敏感[3]。
在7075铝合金中,较高的Cu含量明显增加扁锭的热脆性,尤其当w(Cu)>1.5时,影响更为显着,因此,Cu控制在标准范围的中下限,即w(Cu)1.5.Cr在7075铝合金中主要的作用是改善合金抗应力腐蚀性能。
铝合金电阻点焊所存在的主要问题
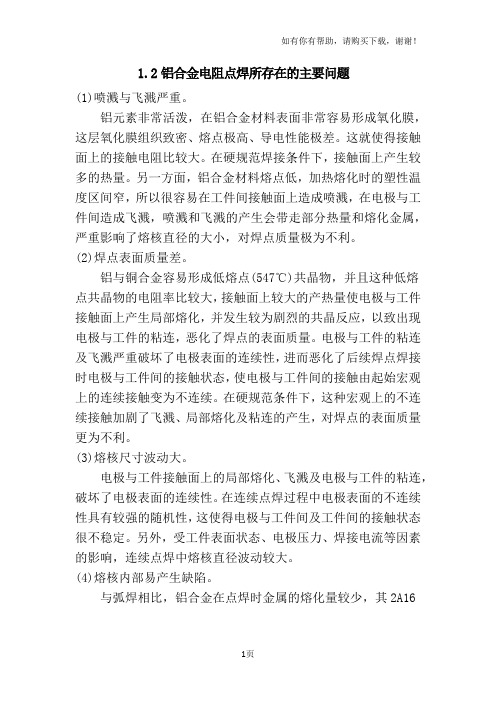
1.2铝合金电阻点焊所存在的主要问题(1)喷溅与飞溅严重。
铝元素非常活泼,在铝合金材料表面非常容易形成氧化膜,这层氧化膜组织致密、熔点极高、导电性能极差。
这就使得接触面上的接触电阻比较大。
在硬规范焊接条件下,接触面上产生较多的热量。
另一方面,铝合金材料熔点低,加热熔化时的塑性温度区间窄,所以很容易在工件间接触面上造成喷溅,在电极与工件间造成飞溅,喷溅和飞溅的产生会带走部分热量和熔化金属,严重影响了熔核直径的大小,对焊点质量极为不利。
(2)焊点表面质量差。
铝与铜合金容易形成低熔点(547℃)共晶物,并且这种低熔点共晶物的电阻率比较大,接触面上较大的产热量使电极与工件接触面上产生局部熔化,并发生较为剧烈的共晶反应,以致出现电极与工件的粘连,恶化了焊点的表面质量。
电极与工件的粘连及飞溅严重破坏了电极表面的连续性,进而恶化了后续焊点焊接时电极与工件间的接触状态,使电极与工件间的接触由起始宏观上的连续接触变为不连续。
在硬规范条件下,这种宏观上的不连续接触加剧了飞溅、局部熔化及粘连的产生,对焊点的表面质量更为不利。
(3)熔核尺寸波动大。
电极与工件接触面上的局部熔化、飞溅及电极与工件的粘连,破坏了电极表面的连续性。
在连续点焊过程中电极表面的不连续性具有较强的随机性,这使得电极与工件间及工件间的接触状态很不稳定。
另外,受工件表面状态、电极压力、焊接电流等因素的影响,连续点焊中熔核直径波动较大。
(4)熔核内部易产生缺陷。
与弧焊相比,铝合金在点焊时金属的熔化量较少,其2A16铝合金电阻点焊焊点表面缺陷分析与工艺优化导热系数又比较大,所以熔核的冷却速度非常快。
另外,铝合金是非导磁材料,液态熔核区的流动速度非常小,熔核在凝固时极易形成缩孔、缩松和气孔。
虽然这些缺陷对接头强度影响不大,但对接头的疲劳性能却有显著影响。
(5)结合线伸入。
结合线伸入是点焊和缝焊某些高温合金和铝合金时特有的缺陷,是指结合面伸入到熔核中的部分。
对于铝合金,主要是工件表面有强氧化物,焊接过程中通电时间短暂,导致结合面熔合不完整。
关于加铝合金材料DSC热分析中影响因素的探讨

关于加铝合金材料DSC热分析中影响因素的探讨摘要:实验目的:为保证合金材料使用效果,要在不同温度环境下对合金材料进行DSC实验,进而通过线性外推与选择平均数值的方式,明确合金材料在不同温度状态下的相变功率发展趋势。
实验结论:通过一系列DSC实验得知,当升温速率产生转变时,实验材料DSC曲线结构不会出现明显变化,仅仅是随着实验材料升温速率的增加,合金变相功率有所提高。
关键词:DSC热分析;技术原理;测试样品;实验流程铝合金材料由于自身材料属性特点,被广泛使用在建筑、汽车等行业,由于铝合金材料在生产以及制作过程中,普遍需要经历热处理、浇筑、凝固以及冷却等技术工艺,所以想要保证铝合金材料使用效果,则要对其最终性能的影响因素进行详细分析。
一、DSC热分析技术原理差示扫描量热法是我国在60年代所研究的一种热分析方法,该技术是一种在温度控制系统中,详细测量参比物质热量流速温度变化的专业技术手段,简称DSC热分析技术。
DSC热分析技术从测量方式上进行区分,主要分为热功率补偿型以及热量流动型两种,而技术特点则主要包含:测试温度范围较大、测试分辨能力高以及测试灵敏程度强等,加上DSC热分析技术可以定量的测试各种材料热力学数据以及动力学参数,因此技术在科学研究中得到广泛使用。
为了保证DSC热分析技术能够正常运转,需要根据技术特点搭配适合的硬件设备,DSC装置是一种能够精准测量温度变化的精密仪器,该设备运转原理主要包含以下几个方面[1]。
首先,技术人员将测试样品以及参考对比物质放置在相同的热量测试环境下,并且在测试过程中要始终保持测试样品以及参考对比物的温度相同,如果当测试样品产生热效应时,设备则需要利用设备或者温度控制电子元件等零部件,为样品补充热量或者减少热量,确保测量样品与参考对比物的温度差始终保持在0。
此时技术人员需要将设备所产生的热量变化以DSC曲线结构的形式详细记录,为DSC热分析技术提供数据支持。
由此可见,DSC热分析技术在实际运转过程中,该技术是一种将物质内部所需要转换的热流以时间和温度作为测量基础函数,所开展的数据收集热分相技术。
铝及铝合金塑性变形加工的感应加热(上)

铝及铝合金塑性变形加工的感应加热(上)李韵豪【摘要】根据铝及铝合金的热物理参数及特点,简述塑性变形加工铝及铝合金的加热规范、温度范围及保温时间。
在感应加热时避免坯料过烧、粗晶等加热缺陷。
提出针对不同牌号铝及铝合金感应加热的频率、功率及加热时间的确定,感应器的设计及参数的计算,铝及铝合金测温及温控问题,最后提出高效节能型感应炉的设计。
【期刊名称】《金属加工:热加工》【年(卷),期】2016(000)003【总页数】5页(P54-57,58)【作者】李韵豪【作者单位】【正文语种】中文从本期开始,《金属加工》杂志锻造栏目,将不定期地刊登作者李韵豪纂写的有关有色金属及其合金塑性变形感应加热的系列论文。
第一篇是关于铝及铝合金,因篇幅较长,分上下两期刊登。
【编者按】常用的有色金属如铝、铜、钛、锆、钽、铌、镁等及其合金因具有一系列非常优异的特性,其塑性变形制品在航空航天、国防、汽车、机车及民用等诸多领域得到越来越广泛的应用。
这些有色金属及其合金塑性变形前的加热,也正由传统火焰炉加热向高效节能的感应加热过渡,更多的锻造厂家已意识到,感应加热是有色金属及其合金诸多加热方式中最先进、最理想的加热方式。
这篇文章是作者根据在与一汽锻造(吉林)有限公司和东风锻造有限公司的专家及工程技术人员进行学术交流后编写而成的。
铝在地球上储量超过铁(5.8%),占地壳构成物质的8.0%,为地球储量最多的金属元素。
世界铝产量在60年前开始超过铜产量,一直居有色金属之首。
当前铝的产量和用量(以重量计)仅次于钢铁,成为人类应用的第二大金属。
用于塑性变形加工的铝合金称之为变形铝合金,本文涉及的铝合金都是变形铝合金。
变形铝合金根据使用性能和工艺性能不同,分为以下5类。
硬铝合金,包括Al-Cu-Ag系(普通硬铝),Al-Cu-Mn系(耐热硬铝)。
超硬铝合金,高强度铝合金,主要为Al-Zn-Mg-Cu系。
防锈铝合金,包括A l-M g系,还有可热处理强化的Al-Zn-Mg-Cu系。
铝合金时效处理工艺说明

铝合金的热处理铸造铝合金的金相组织比变形铝合金的金相组织粗大,因而在热处理时也有所不同。
前者保温时间长,一般都在2h以上,而后者保温时间短,只要几十分钟。
因为金属型铸件、低压铸造件、差压铸造件是在比较大的冷却速度和压力下结晶凝固的, 其结晶组织比石膏型、砂型铸造的铸件细很多,故其在热处理时的保温也短很多。
铸造铝合金与变形铝合金的另一不同点是壁厚不均匀,有异形面或内通道等复杂结构外形,为保证热处理时不变形或开裂,有时还要设计专用夹具予以保护,并且淬火介质的温度也比变形铝合金高,故一般多采用人工时效来缩短热处理周期和提高铸件的性能。
一、热处理的目的铝合金铸件热处理的目的是提高力学性能和耐腐蚀性能,稳定尺寸,改善切削加工和焊接等加工性能。
因为许多铸态铝合金的机械性能不能满足使用要求,除Al-Si 系的ZL102,Al-Mg系的ZL302和Al-Zn系的ZL401合金外,其余的铸造铝合金都要通过热处理来进一步提高铸件的机械性能和其它使用性能,具体有以下几个方面:1 消除由于铸件结构(如璧厚不均匀、转接处厚大等原因使铸件在结晶凝固时因冷却速度不均匀所造成的内应力;2提高合金的机械强度和硬度,改善金相组织,保证合金有一定的塑性和切削加工性能、焊接性能;3稳定铸件的组织和尺寸,防止和消除高温相变而使体积发生变化;4消除晶间和成分偏析,使组织均匀化。
二、热处理方法1、退火处理退火处理的作用是消除铸件的铸造应力和机械加工引起的内应力,稳定加工件的外形和尺寸,并使Al-Si系合金的部分Si结晶球状化,改善合金的塑性。
其工艺是:将铝合金铸件加热到280-300℃,保温2-3h,随炉冷却到室温,使固溶体慢慢发生分解,析出的第二质点聚集,从而消除铸件的内应力,达到稳定尺寸、提高塑性、减少变形、翘曲的目的。
2、淬火淬火是把铝合金铸件加热到较高的温度(一般在接近于共晶体的熔点,多在500℃以上,保温2h以上,使合金内的可溶相充分溶解。
Sm对7050铝合金铸态组织及硬度的影响

Sm对7050铝合金铸态组织及硬度的影响李缨缤;郭二军;王丽萍;冯义成;姜文勇;贾桂龙【摘要】主要研究了稀土Sm对7050铝合金的显微组织和硬度的影响.通过分别向7050铝合金中加入百分含量为0%、0.5%、1.0%、1.5%、2.0%、2.5%的Sm,探究不同Sm含量对铝合金铸态显微组织、硬度的影响.结果表明,铸态7050铝合金中Zn、Mg、Cu、Sm等元素偏聚在晶界处,形成了含有η相(MgZn2)、T 相(AlZnMgCu)的低熔点共晶组织.Sm对合金共晶组织有明显变质作用.含Sm量在2.0%时,其组织明显细化,硬度也提高,稀土Sm对7050铝合金组织有一定的细化作用.添加适量的稀土Sm能够细化7050铝合金晶粒,提高合金的硬度,但添加过量的稀土Sm不仅使合金的晶粒变得粗大而且使合金的硬度降低.【期刊名称】《哈尔滨理工大学学报》【年(卷),期】2016(021)005【总页数】5页(P20-23,28)【关键词】7050铝合金;Sm;显微组织;硬度【作者】李缨缤;郭二军;王丽萍;冯义成;姜文勇;贾桂龙【作者单位】哈尔滨理工大学材料科学与工程学院,黑龙江哈尔滨150040;哈尔滨理工大学材料科学与工程学院,黑龙江哈尔滨150040;哈尔滨理工大学材料科学与工程学院,黑龙江哈尔滨150040;哈尔滨理工大学材料科学与工程学院,黑龙江哈尔滨150040;哈尔滨理工大学材料科学与工程学院,黑龙江哈尔滨150040;哈尔滨理工大学材料科学与工程学院,黑龙江哈尔滨150040【正文语种】中文【中图分类】TG146.27XXX系铝合金属具有质量轻、比强度高、加工性能好等特点,被广泛应用于航空航天工业、船舶制造、民用交通领域等[1-8].随着我国现代航空航天工业和交通事业的高速发展,对7XXX系铝合金的性能提出了更高要求[9],从而促进了国内研究者对7XXX系铝合金的研究.7050为7XXX系超高强度铝合金,亦称超硬铝,主要应用于机身框架、舱壁、机翼蒙皮、加强筋、起落架支撑部件等.国内资源丰富的铝及其合金作为典型的轻质金属,在军工与民用领域都是重要的材料.近些年来,主要研发超硬铝,及添加稀土细化剂在7XXX系铝合金中的作用机制[10-13].稀土元素加入到铝合金中可起到微合金化的作用;此外,它与氢等气体和许多非金属有较强的亲和力,能生成熔点高的化合物,因此它能够起到除氢、精炼、净化作用;同时,稀土元素化学活性极强,它可以在长大的晶粒界面上选择性地吸附,阻碍晶粒的生长,使晶粒细化,具有变质的作用[14].目前稀土元素的晶粒细化作用逐渐引起人们的重视.有关稀土对铝硅合金变质作用的研究和应用的报道不断增多,充分肯定了稀土元素对共晶硅的良好变质作用,但稀土Sm对7050铝合金具体作用形式及机理的研究文献较少.本研究选取7050铝合金为研究对象,采用金属型铸造,研究微量Sm对其铸态组织及硬度的影响.试验主要原材料包括:7050铝合金、Al-20%Sm中间合金.合金的熔炼在井式电阻炉中进行,使用石墨坩埚.将经预热的铝锭加入已经升温至740℃的坩埚中,保温45~50 min.待合金完全熔化后,加入Al-20%Sm中间合金到坩埚中,并升温至750℃,保温20 min后,加入3%的专用固体除气剂进行除气,将炉温调至720℃静置15~20 min,取出坩埚,扒渣,浇入经450℃预热后的金属型模具中,型腔尺寸为160 mm×130 mm×20 mm.待冷却后取出,并在铸件上标注编号.合金原料、工具在使用前需450℃烘干水分.金相显微组织用OLYMPUS-GX71 型金相显微镜观察,腐蚀剂为2.5%HCl+1.25%HF+1.25%HNO3+95%H2O.采用FEI Sirion 2000扫描电镜进行试样表面形貌观察.试验所用XRD衍射仪型号为X′Pert PRO.试验参数为:试验电压为40 kV,采用Cu靶,扫描速度为8°/min,扫描范围20~90°.采用HB-3000C型布氏硬度计量器测量试样硬度.测试前要求试样表面及对面平整,测试面经抛光机粗抛过,确保数据真实性.实验载荷为62.5 Kgf,压头直径为2.5 mm,施压时间8 s,保压时间为15 s.每个试样至少取3个点测硬度值取平均值作为最后测量结果.图1是对铸态条件下的含2.0%Sm铝合金进行X射线衍射试验所得到的XRD图谱.通过对其进行物相检索分析得出,含2.0%Sm合金的主相主要由α-Al基体和MgZn2相组成.可以看到并没有出现常见的T(AlZnMgCu)相、含钐相的衍射峰,这主要可能是由于这些相太少,未检测到或无法在XRD图谱中显示出来.后面将通过SEM及EDS来具体分析.不同Sm含量的7050铝合金铸态显微组织如图2所示,合金化的7050铝合金本身组织就十分的细小见图1(a),通过Sm的不断添加使得7050合金的晶粒得到进一步细化,细化效果比较明显,同时析出相增多.结合文[15]可知,晶界上的析出相主要为η(MgZn2)+T(AlZnMgCu)相,晶内析出相主要是为η(MgZn2)相,是合金中的主要强化相.在晶粒内部还有一些细小的点状的第二相粒子,该相粒子的尺寸很小,属于含Sm相,在合金结晶时作为非自发晶核,起细化晶粒作用.当Sm含量很低时,Sm主要固溶于铝基体,含Sm相质点少,组织细化不明显,随着Sm含量增加,含Sm相颗粒增多,形核率提高,但Sm含量超过一定量,含Sm颗粒数目增加不明显,但尺寸增大颗粒聚集,晶界变粗,细化效果减弱.添加稀土Sm是铝合金晶粒细化的主要原因.用直线截点法算出0%Sm、0.5%Sm、1.0%Sm、1.5%Sm、2.0%Sm、2.5%Sm晶粒的平均尺寸分别为38.89 μm、36.94 μm、31.82 μm、29.17 μm、25.93 μm、30.49 μm.可见,在含Sm量达到2.0%左右时,晶粒尺寸最小,晶粒数量增多,晶粒得到明显细化,继续加入,晶粒反而变粗.7050铝合金铸态条件下的SEM显微组织如图3所示.可以发现,Al-Zn-Mg-Cu 铝合金主要有两种不同的相组成:一种是等轴状的α-Al基体;另一种就是主要存在于晶界上的断续网状析出相,其中析出相以3种形态存在,一种是以层片状的形式呈块状连续存在于晶界上,一种就是以点状弥散分布在α-Al基体晶粒内,另一种就是以棒状断续分布于α-Al基体晶粒内.进一步分析SEM照片可以发现,在一定含量的范围内,随Sm的加入量增加,呈块状分布于晶界上的析出相分布更加均匀更加纤细,同时α-Al固溶体中的点状相的数量不断增加;而且随着Sm含量的增加,不管是在合金晶界上还是α-Al基体内的析出相,它们的不连续程度都不断增加;当超过2.0%Sm后,合金材料的析出相又开始呈大块状聚集.所以,可以认为微量Sm的加入,可明显改善7050铝合金铸态析出相的分布,使合金析出相的分布更均匀,并且随Sm的加入量增加,析出相的数量明显的增多.含2.0%Sm的铝合金铸态条件下扫描照片及不同形态的第二相进行EDS能谱分析如图4,数据结果如表1所示.从图4可以看出,铸态铝合金基体上主要析出相形状有棒状、点状、片状,其析出相不同位置的化学成分也不尽相同.基体主要是含Al、Zn、Mg、Cu元素(见Point c).棒状的主要成分由Al、Zn、Mg、Cu、Sm组成(见Point b和f),它们的成分含量也基本相同,是含Sm相;还有棒状由Al、Zn、Mg三中元素组成,可能是MgZn2相存在(见Point d).尺寸较小的圆点和片状的主要成分由Al、Zn、Mg、Cu、Sm元素组成(见Point g和h),也是含Sm相.团絮状的为夹渣,含有一些杂质(见Point e).通过能谱分析,Sm加入到铝合金后主要是以第二相的形式存在,铝基体几乎不含有Sm元素.硬度是反应合金性能的重要依据.不同Sm含量的硬度如表2所示.从表2可知,随着Sm的加入,7050铸态铝合金的硬度增加,但开始变化不大,主要是Sm固溶于合金中,强化效果不明显;结合图3和4可知,少量的Sm固溶于铝合金中主要是起到细化铝合金的作用,强化效果不明显,因此对硬度影响不大;Sm含量达到2.0%时,Sm的点、棒状析出物明显增多,硬度达到最大值.继续加入Sm,析出相逐渐变成片状,是导致硬度下降的主要原因.1)不加Sm的7050合金铸态组织为α(Al)基体相、晶间α(Al)+η(MgZn2)共晶相、晶内游离η(MgZn2)相、少量T(AlZnMgCu)相.2)Sm元素的加入,细化了试验合金组织中的α(Al)基体晶粒尺寸,对合金晶间共晶组织α(Al)+η(MgZn2)有明显的变质作用.同时,α(Al)晶内析出的细点状弥散相数量随Sm量的增加而增多.稀土Sm能够细化铝合金晶粒,随着Sm的加入,铝合金组织逐渐得到细化,Sm含量在2.0%时晶粒最为细小,继续加入又变得粗化.3)7050铝合金中的主要相为η(MgZn2)、T(AlZnMgCu).Sm加入后,主要以第二相的形式存在,基体基本不含Sm.Sm含量在0.5%~2.0%之间,含Sm相主要呈点、棒状,7050铝合金硬度呈上升趋势,在Sm含量为2.0%处达到最高,超过此含量,片状含Sm相明显变多,硬度开始下降.[6] 李春梅,陈志谦,程南璞,等. 7055超高强、超高韧铝合金力学性能分析[J].金属热处理,2008(1):100-104.。
6063铝合金真空钎焊用铝基钎料的研究

6063铝合金真空钎焊用铝基钎料的研究航天制造技术年 ,, 月第 , 期 ,,,,,,,, 铝合金真空钎焊用铝基钎料的研究北京航星机器制造公司于文花由于,,,,铝合金的熔点较低(接近,,,,,钎料的液相线温度),焊接过程中易发生晶粒长文摘大、溶蚀等现象,,,,,,,,,钎料无法满足,,,,铝合金真空钎焊的要求。
利用,,降低熔点的作用,同时加入,,、,,合金元素,通过正交试验的方法研究了合金元素,,、,,、,,对铝基钎料性能的影响。
结果表明,随着合金元素,,、,,含量的增加,其熔点大大降低,同时钎料的铺展性能也有明显改善, ,,,,铝合金钎焊接头强度有所增强。
真空钎焊铝基钎料 ,,,,铝主题词合金, 引言钎焊用钎料既要具有较低的熔点,又要保持良好的机械性能。
我国机载多卜勒雷达天线是采用国产 LF21 本文的研究思想是利用 Cu 降低熔点的作用,铝合金真空钎焊(Al-Si-Mg 钎料)而成的,但其同时加入 Ni 部分替代铜,使钎料保持较好的机械缺点是强度较低,不及美国机载雷达( 6061 铝合性能和抗腐蚀性能。
用实验的方法,研究 Cu、Si、金)的 1/2,这使天线抗冲击变形能力大大下降, Ni 含量变化对 Al-Si-Cu-Ni 钎料熔点、铺展性能严重影响了雷达的接收和使用效果。
为了提高机和接头性能的影响,最后用电镜扫描和能谱分析载多卜勒雷达天线的强度,可采用高强度铝合金,的方法分析了新钎料和真空钎焊接头的微观组其中 6063 铝合金各种机械性能完全可以满足机织。
载多卜勒雷达天线对材料的要求。
但由于 6063 铝合金的熔点较低( 固相线温度 615 ? ),与 , 实验材料及内容Al-Si-Mg 钎料的液相线温度(577?)接近,焊接过程中易发生晶粒长大、溶蚀等现象。
所以研实验所用母材是 6063 铝合金。
钎料的配制 2.1 制低熔点的铝基钎料是高强度机载多卜勒雷达天根据铜的含量对 Al-Si-Cu 合金的硬度和液相线制造的关键。
铝合金缺陷

铸锭缺陷一、疏松当熔体结晶时,由于基体树枝晶间液体金属补充不足或由于存在未排出的气体(主要为氢气),结晶后在枝晶内形成的微孔称疏松。
低倍组织特征:形状不规则、分散装的黑色针孔,边部参差不齐,多带棱角,似锯齿状。
显微组织特征:沿枝晶分布、有棱角形的黑洞,疏松愈严重,黑洞数量愈多,尺寸也愈大。
主要产生原因:1、合金的开始凝固温度与凝固终了温度相差很大,即过渡带宽,使补缩和气体逸出困难;2、熔体过热、停留时间长,吸收大量气体;3、静置时间不够,精炼除气不彻底;4、空气湿度大,燃气、燃油水分大;5、原材料潮湿,有油污、水分。
二、光亮晶粒在宏观组织中存在着色泽光亮的树枝状组织称为光亮晶粒。
对光线无选择性。
断口组织特征:亮色絮状物。
显微组织特征:粗大枝晶网状组织,网络稀薄,含有的低熔点共晶较少,该组织硬度低于正常组织。
主要产生原因:1、铸造过程中,漏斗孔距底部过高,漏斗预热不好;2、铸造开始时漏斗底部粘铝,铸造过程中落入铸锭中;3、铸造温度低,铸造速度慢,使漏斗底中易产生底结。
三、羽毛状晶由于熔体过热等原因在铸锭宏观组织中形成的类似羽毛状的金属组织,称为羽毛状晶。
低倍组织特征:由许多平行的细条组成,类似羽毛,呈扇形分布;断口组织呈片状。
显微组织特征:枝晶网络较细,化合物分布比较连续,在偏光下观察可看到由很多的薄片组成,每个薄片又有明暗两部分。
主要产生原因:1、熔体过热或液体金属冷却时间过长,晶核数量减少;2、铸造温度过高;3、晶粒细化剂加入量少。
四、气孔当熔体中氢含量较大且除气不均匀时,使氢气以泡状存在,并在金属凝固后被保留下来,在金属内形成空腔,即气孔。
气孔在铸锭中的分布没有规律,常与疏松伴生。
组织特征:内表面光滑明亮的圆形或椭圆形孔洞。
主要产生原因:1、合金的开始凝固温度与凝固终了温度相差很大,即过渡带宽,使补缩和气体逸出困难;2、熔体过热、停留时间长、熔体没覆盖或覆盖不好等,吸收大量气体;3、铸造温度低,铸造速度快,冷却强度小,熔体中的气体逸出困难;4、静置时间不够,精炼除气不彻底;5、空气湿度大,燃气、燃油水分大;6、原材料潮湿,有油污、水分。