板坯连铸轻压下技术的工艺优化
基于射钉法的板坯连铸工艺优化
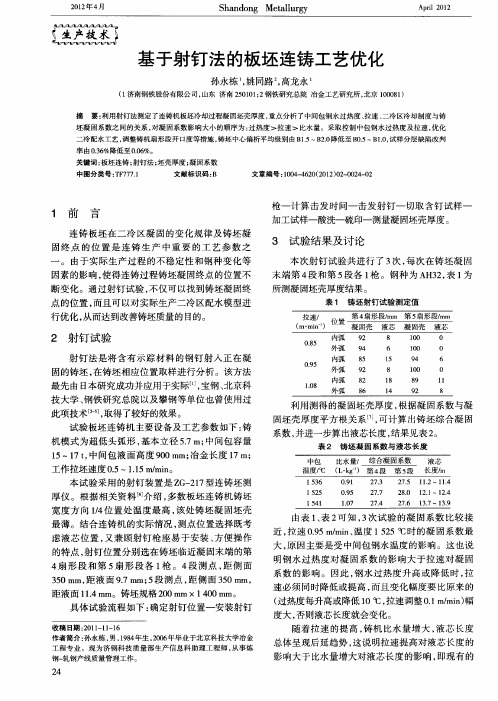
所 测凝 固坯壳厚度结 果 。
表 1 铸坯射钉试验测定值
i
。 位置 ,
6 5
2 射钉试 验
射 钉 法 是将 含 有 示 踪 材料 的钢 钉 射入 正 在 凝
固 的铸 坯 , 在铸 坯 相应 位置 取样进 行 分析 。该方 法
O O
最 先 由 日本研 究成 功并 应用 于实 际n, ]宝钢 、 京科 北 技大 学 、 钢铁研 究 总 院以及 攀钢 等单 位也 曾使 用过 此项技 术陋 ] , 了较好 的效果 。 取得 试 验板 坯 连铸 机 主要设 备及 工艺 参数 如下 : 铸
中包 比水量/ 综合凝 固系数 液 芯 温度/ ℃ ( ・ ) 第 4 Lk 段 第5 段 长度, m
5 0
¨
2 1 ~ ~
¨
1 5~1 , 7 中间包 液 面高 度 90m 冶 金长 度 1 t 0 m; 7m;
工作拉 坯速度 05 . / n . ~1 5 mi。 1m 本 试 验采 用 的射 钉装 置是 Z 一 1 型 连铸 坯测 G 27
o heNa l hO tn c i ue n t i—s O i g Te hn q
压 下 的原理 , 铸坯 的凝 固末端 区域 适 当加 大二 冷 在 配 水 强度 , 以消 除铸 坯 的 中心疏 松 、 缩孔 和 中心 偏 析 为 目的 , 4 将 段后 内弧水量 保持 不变 , 内弧配 水 外 比例适 当增加 , 调整后 比水量增 加约 00 /g . Lk 左右 。 7 3 铸 机 扇 形 段 开 口度 的 优 化 调 整 。 在 目前 ) 08 . m m n . ~11 / i 的正常 拉速 条件 下 , 铸坯 的凝 固末 端 基本集 中在 5 、 段 区域 。根 据铸机 轻压 下技术 的 段 6 基本 原理 , 铸坯 凝 固末端 2~3n的区域 内施 加较 大 I 幅度 ( 2~3m 的机 械 压 力 , 迫 铸 坯坯 壳 挤 压 液 m) 强
炼钢过程中的连铸技术改进与优化

炼钢过程中的连铸技术改进与优化随着现代工业的快速发展,钢铁行业在全球范围内扮演着重要的角色。
炼钢是制造钢材的关键过程之一,而连铸技术在炼钢过程中的应用越来越广泛。
本文将探讨炼钢过程中连铸技术的改进与优化措施,以提高钢材质量和生产效率。
一、连铸技术的基本原理与流程连铸技术是指将炼钢炉中液态钢水直接注入连铸机中,通过结晶器的作用,使其快速凝固为连续坯料。
基本上,连铸技术分为结晶器区、中间区和加热区三个部分。
结晶器区是最重要的部分,其作用是促使钢水迅速凝固形成坯料。
中间区则起到支撑坯料并保持其形状的作用,加热区则用来提供所需的坯料温度。
二、连铸技术改进的原因尽管连铸技术已经成为钢铁生产中主要的浇铸方法,但仍然存在一些问题和潜在的改进空间。
首先,连铸坯料的质量不稳定是一个重要问题。
由于熔铸过程中的各种因素,如温度、流速、结晶器形状等,坯料的结构和性能可能会出现变化。
这导致了产品的不均匀性和不稳定性。
其次,连铸过程中易产生气孔和夹杂物的问题也需要解决。
气孔和夹杂物对钢材的力学性能和外观质量有着显著影响。
此外,传统的连铸技术在能源消耗和生产效率方面也存在一些局限。
例如,冷却设备和传输系统的耗能较高,同时生产线上的工作效率较低。
因此,为了改进钢铁行业的连铸技术,提高生产效率和产品质量,钢铁企业已经采取了一系列的措施。
三、连铸技术改进与优化措施1. 结晶器改进结晶器是连铸技术中最关键的部分,对坯料质量起到决定性的作用。
通过改进结晶器的设计和材料,可以提高坯料的凝固性能和整体质量。
现代连铸技术使用先进的结晶器涂层和陶瓷材料,以减少坯料表面张力和增加热传导率。
此外,优化结晶器的几何形状和冷却系统,可以提高坯料的结晶行为和熔体流动性。
2. 连铸过程控制技术连铸过程中的温度、流速和加热条件等参数对坯料质量有着直接的影响。
通过引入先进的控制技术,如自动化控制系统和实时监测装置,可以实现对连铸过程的精细控制和优化。
自动化系统可以实时监测和调整炉温、浇注速度和结晶器温度等参数,以确保坯料的一致性和质量。
炼钢生产中的连铸工艺优化与质量控制

炼钢生产中的连铸工艺优化与质量控制近年来,随着钢铁行业的快速发展,炼钢生产过程中的连铸工艺优化与质量控制成为了关注焦点。
连铸工艺作为炼钢生产的重要环节,直接关系到钢铁产品的质量和生产效益。
本文从连铸工艺的优化和质量控制两个方面进行探讨,旨在揭示连铸工艺对钢铁生产的重要性,并提出相应的解决方案。
一、连铸工艺的优化连铸工艺是将炼钢过程中的液态钢水直接注入到连续浇铸机模具中,通过快速冷却和凝固形成坯料的过程。
连铸工艺的优化对提高钢铁产品质量、降低能耗和减少生产成本有着重要的影响。
1.流动控制优化在连铸过程中,合理控制钢水的流动速度对保证坯料质量至关重要。
优化连铸工艺中的流动控制,可以通过合理设计浇注室的形状和角度,调整浇注速度,控制冷却水的流量等手段来实现。
同时,配备先进的流动监测设备,实时监测钢水的流动情况,以及时做出调整和干预。
2.结晶器设计优化结晶器是连铸工艺中起着关键作用的部分,其优化设计直接关系到坯料的凝固结晶过程。
合理设计结晶器的出口形状和尺寸,选用合适数量和位置的冷却装置,可以有效控制坯料的凝固过程,避免产生过大的温度梯度和结晶缺陷。
同时,结合数值模拟和实验测试,进一步优化结晶器的设计参数,以提高连铸质量和生产效率。
3.冷却控制优化连铸过程中的冷却控制对坯料的结晶过程起着至关重要的作用。
优化连铸工艺的冷却控制,可以通过合理设置冷却水的流量和温度,调整冷却装置的布置方式,以及根据不同的钢种和规格进行个性化的冷却措施等手段来实现。
同时,结合先进的测温技术和数值模拟方法,对坯料的冷却过程进行实时监控和优化调整,以提高生产效率和坯料质量。
二、质量控制连铸工艺的质量控制是确保钢铁产品质量的关键环节。
通过加强对连铸工艺中关键参数的控制和监测,可以有效提高钢铁产品的一致性和稳定性。
1.温度控制钢水的温度是影响连铸质量的重要因素之一。
通过合理控制铸坯的初始温度和结晶器的冷却控制,可以实现钢水的均匀凝固和避免温度梯度过大造成的结晶缺陷。
连铸轻压下技术
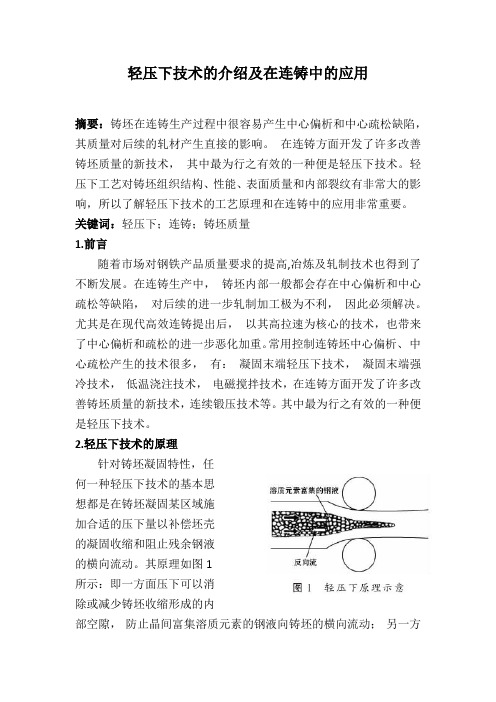
轻压下技术的介绍及在连铸中的应用摘要:铸坯在连铸生产过程中很容易产生中心偏析和中心疏松缺陷,其质量对后续的轧材产生直接的影响。
在连铸方面开发了许多改善铸坯质量的新技术,其中最为行之有效的一种便是轻压下技术。
轻压下工艺对铸坯组织结构、性能、表面质量和内部裂纹有非常大的影响,所以了解轻压下技术的工艺原理和在连铸中的应用非常重要。
关键词:轻压下;连铸;铸坯质量1.前言随着市场对钢铁产品质量要求的提高,冶炼及轧制技术也得到了不断发展。
在连铸生产中,铸坯内部一般都会存在中心偏析和中心疏松等缺陷,对后续的进一步轧制加工极为不利,因此必须解决。
尤其是在现代高效连铸提出后,以其高拉速为核心的技术,也带来了中心偏析和疏松的进一步恶化加重。
常用控制连铸坯中心偏析、中心疏松产生的技术很多,有:凝固末端轻压下技术,凝固末端强冷技术,低温浇注技术,电磁搅拌技术,在连铸方面开发了许多改善铸坯质量的新技术,连续锻压技术等。
其中最为行之有效的一种便是轻压下技术。
2.轻压下技术的原理针对铸坯凝固特性,任何一种轻压下技术的基本思想都是在铸坯凝固某区域施加合适的压下量以补偿坯壳的凝固收缩和阻止残余钢液的横向流动。
其原理如图1所示:即一方面压下可以消除或减少铸坯收缩形成的内部空隙,防止晶间富集溶质元素的钢液向铸坯的横向流动;另一方面,压下可以使液芯中溶质元素富集的钢液沿拉坯方向反向流动,使溶质元素在钢液中重新分配,从而改善中心偏析情况。
在连铸坯凝固过程中,对铸坯施加外力,补偿凝固收缩并破碎已经形成的“晶桥”,使得铸坯内的钢水可以自由地进行流动,就可以最大程度地减少中心偏析和疏松,这就是轻压下技术的工艺原理。
3.轻压下技术的发展及分类3.1轻压下技术的发展轻压下技术始于20世纪70年代末、80年代初,是在20世纪70年代辊缝收缩技术的基础上发展而来的。
目前,连铸坯的轻压下有两种含义:在铸坯凝固末端处进行的轻压下;离凝固末端较远处进行的轻压下,又称带液芯轻压下。
中厚板铸机动态轻压下控制系统优化
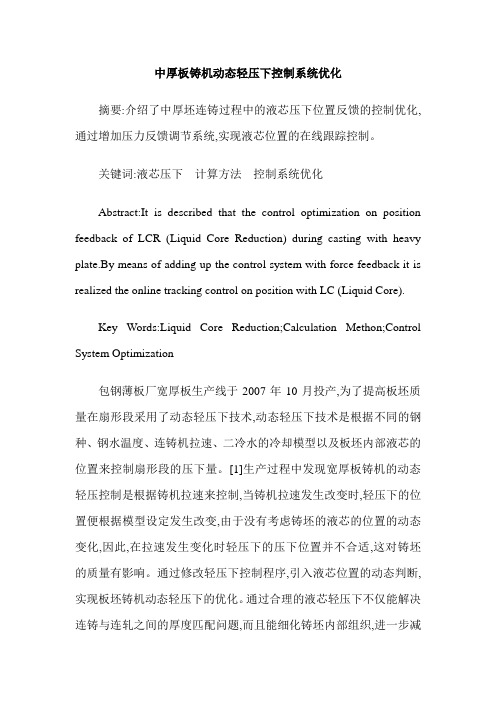
中厚板铸机动态轻压下控制系统优化摘要:介绍了中厚坯连铸过程中的液芯压下位置反馈的控制优化,通过增加压力反馈调节系统,实现液芯位置的在线跟踪控制。
关键词:液芯压下计算方法控制系统优化Abstract:It is described that the control optimization on position feedback of LCR (Liquid Core Reduction) during casting with heavy plate.By means of adding up the control system with force feedback it is realized the online tracking control on position with LC (Liquid Core).Key Words:Liquid Core Reduction;Calculation Methon;Control System Optimization包钢薄板厂宽厚板生产线于2007年10月投产,为了提高板坯质量在扇形段采用了动态轻压下技术,动态轻压下技术是根据不同的钢种、钢水温度、连铸机拉速、二冷水的冷却模型以及板坯内部液芯的位置来控制扇形段的压下量。
[1]生产过程中发现宽厚板铸机的动态轻压控制是根据铸机拉速来控制,当铸机拉速发生改变时,轻压下的位置便根据模型设定发生改变,由于没有考虑铸坯的液芯的位置的动态变化,因此,在拉速发生变化时轻压下的压下位置并不合适,这对铸坯的质量有影响。
通过修改轻压下控制程序,引入液芯位置的动态判断,实现板坯铸机动态轻压下的优化。
通过合理的液芯轻压下不仅能解决连铸与连轧之间的厚度匹配问题,而且能细化铸坯内部组织,进一步减轻铸坯中心偏析,这对于板坯连铸生产的产品尤为重要。
动态轻压下功能用一组铸流扇形段辊缝是动态计算的来控制板坯的先后顺序。
此计算是基于从过程控制系统下载的压下路径和最终位置,以及由板坯凝固模型计算的液芯长度。
板坯连铸机保护浇注工艺优化
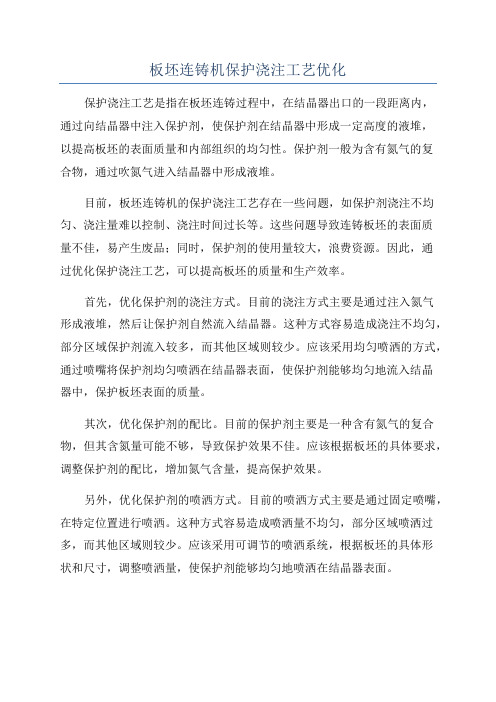
板坯连铸机保护浇注工艺优化保护浇注工艺是指在板坯连铸过程中,在结晶器出口的一段距离内,通过向结晶器中注入保护剂,使保护剂在结晶器中形成一定高度的液堆,以提高板坯的表面质量和内部组织的均匀性。
保护剂一般为含有氮气的复合物,通过吹氮气进入结晶器中形成液堆。
目前,板坯连铸机的保护浇注工艺存在一些问题,如保护剂浇注不均匀、浇注量难以控制、浇注时间过长等。
这些问题导致连铸板坯的表面质量不佳,易产生废品;同时,保护剂的使用量较大,浪费资源。
因此,通过优化保护浇注工艺,可以提高板坯的质量和生产效率。
首先,优化保护剂的浇注方式。
目前的浇注方式主要是通过注入氮气形成液堆,然后让保护剂自然流入结晶器。
这种方式容易造成浇注不均匀,部分区域保护剂流入较多,而其他区域则较少。
应该采用均匀喷洒的方式,通过喷嘴将保护剂均匀喷洒在结晶器表面,使保护剂能够均匀地流入结晶器中,保护板坯表面的质量。
其次,优化保护剂的配比。
目前的保护剂主要是一种含有氮气的复合物,但其含氮量可能不够,导致保护效果不佳。
应该根据板坯的具体要求,调整保护剂的配比,增加氮气含量,提高保护效果。
另外,优化保护剂的喷洒方式。
目前的喷洒方式主要是通过固定喷嘴,在特定位置进行喷洒。
这种方式容易造成喷洒量不均匀,部分区域喷洒过多,而其他区域则较少。
应该采用可调节的喷洒系统,根据板坯的具体形状和尺寸,调整喷洒量,使保护剂能够均匀地喷洒在结晶器表面。
最后,优化保护剂的浇注时间。
目前的浇注时间一般较长,导致保护剂的使用量较大,浪费资源。
应该根据板坯的具体要求,调整浇注时间,使保护剂的使用量能够减少,提高资源利用率。
综上所述,板坯连铸机的保护浇注工艺可以通过优化保护剂的浇注方式、配比、喷洒方式和浇注时间等方面来改善。
通过这些优化措施,可以提高板坯的表面质量和内部组织的均匀性,降低废品率,提高生产效率。
同时,通过减少保护剂的使用量,可以节约资源,实现可持续发展。
《改善连铸板坯缺陷的轧制工艺》范文

《改善连铸板坯缺陷的轧制工艺》篇一一、引言随着现代工业的快速发展,钢铁行业作为国民经济的重要支柱,其产品质量和生产效率的提升显得尤为重要。
连铸板坯作为钢铁生产中的重要环节,其质量直接影响到后续轧制工艺的效率和产品质量。
因此,如何有效改善连铸板坯的缺陷,优化轧制工艺,成为了业界关注的焦点。
本文旨在探讨连铸板坯的常见缺陷及原因,并分析轧制工艺的改进措施,以提高钢铁产品的质量和生产效率。
二、连铸板坯常见缺陷及原因分析1. 中心裂纹:中心裂纹是连铸板坯的主要缺陷之一,其形成原因主要是板坯凝固过程中的温度梯度和热应力过大。
此外,铸坯的化学成分、夹杂物、铸机振动等因素也会对中心裂纹的产生造成影响。
2. 表面裂纹:表面裂纹主要出现在板坯的表面,其形成原因包括钢水质量、结晶器振动、二次冷却制度等因素。
此外,钢中合金元素和夹杂物的含量也会对表面裂纹的产生造成影响。
3. 夹渣和夹杂物:夹渣和夹杂物主要来源于钢水的精炼过程和浇注过程中的夹杂物。
此外,铸模的质量、涂料的性能以及连铸机的维护保养也会影响夹渣和夹杂物的产生。
三、轧制工艺的改进措施针对上述连铸板坯的常见缺陷,轧制工艺的改进措施主要包括以下几个方面:1. 优化轧制参数:通过合理设定轧制温度、轧制速度、压下量等参数,使轧制过程更加稳定,减少轧制过程中的变形和裂纹等缺陷的产生。
2. 调整轧辊质量:选用高质量的轧辊,提高轧辊的硬度和耐磨性,减少轧制过程中的磨损和振动,从而降低板坯的表面裂纹和内部缺陷。
3. 强化轧前准备:在轧制前对连铸板坯进行充分的预热和除鳞处理,以去除表面的夹杂物和氧化皮,提高板坯的表面质量。
4. 优化冷却制度:根据板坯的化学成分、尺寸和轧制要求,制定合理的冷却制度,控制板坯的冷却速度和温度分布,以减少中心裂纹和表面裂纹的产生。
5. 引入无损检测技术:在轧制过程中引入无损检测技术,如超声波检测、X射线检测等,对板坯进行实时监测,及时发现并处理缺陷,提高产品的良品率。
板坯连铸机轻压下增压方法和实践

塞泵寿命会大大降低。若更换液压介质,更换 为耐磨阻燃的脂肪酸酯液压介质,费用比较高。 液压系统总体压力提高,系统泄露量加大,电 机耗电量增加。维修工作也将会大大增加。
方法三:连铸液压系统局部改造,采用增 压阀台,局部增加液压系统工作压力,即只对 参与轻压下的几个扇形段增加夹紧压力。增加 增压阀台,改造部分管线,增加轻压下扇形段 的工作压力,将液压压力从 21 MPa 增加到 23~ 24 MPa。原高压泵工作压力维持 21 MPa 不变, 新设计制造增压阀台,对原液压系统局部改造。 该方法与前两个方法比较优点是一次改造投资 低,系统运行费用低,性价比高,效果良好。 本文采用方法三。
余万吨置换产能将于
年投产
据 Mysteel 不完全统计,自 2018 年以来,全 国共发布 96 项产能置换方案,其中 46 项将于 2020 年底前投产,涉及 12 省 (市区),45 家钢 企 。拟 新建 炼钢 产能 7 318.8 万 吨、 炼 铁 产 能 6 837.05 万吨;退出炼钢产能 8 648.28 万吨、炼铁 产能 8 361.23 万吨。拟新建高炉 48 座、转炉 45
若增压后,扇形段夹紧缸阀块上电磁换向 阀泄漏量大,需将序号 3.1 减压阀压力调高,同 时调节增压器入口节流阀,加大增压器入口流 量。
图 1 增压阀台工作原理图 为了防止夹紧阀台上滑阀式换向阀内漏量 大问题,增压后高压油直接与夹紧阀台出口压 力管线连接,并加球阀及单向阀控制。
连铸轻压下工艺优化与实践

连铸轻压下工艺优化与实践杨文清,陈迪庆,白静,潘金保(武钢股份条材总厂,武汉,430083)摘要:本文介绍了轻压下对改善铸坯中心偏析和中心疏松的作用,通过对液芯长度计算,确定压下位置,进行多次试验,并对试验结果进行分析对比,选择最适合的压下方式。
关键字:轻压下;中心偏析;中心疏松1 前言连铸钢水在冷凝过程中,低熔点的物质被推向铸坯中心部位,形成了C、S、P、Mn 等元素的偏析带,该偏析带在液相穴终端存在于底部,形成了中心偏析和中心疏松缺陷。
轻压下技术是连铸坯拉矫时,对带液芯的铸坯施加小的压力的工艺方法。
即在铸坯凝固终端附近,对铸坯施加一定的压下量,使铸坯凝固终端形成的液相穴被破坏,以打断枝晶搭桥。
轻压下工艺能够改善中心偏析和中心疏松,但如果工艺不当,会产生压下裂纹,严重影响连铸坯质量。
武钢条材总厂一炼钢分厂(以下简称“一炼钢”)1#连铸机主要生产高碳钢。
对高碳钢来说,由于碳含量较高造成导热性差、凝固区间大,连铸坯本身容易产生偏析、疏松和缩孔等缺陷,在拉丝和扭转过程中容易引起断裂 [1] 。
受铸机断面大小等条件的制约,铸坯中心碳偏析一直是一炼钢控制难点。
该厂通过对拉矫机设备进行改造,使设备具备更大压下功能,并通过计算液芯长度,调整压下方式,找出最适合的压下量及压下方式。
2 浇注工艺现状一炼钢1#连铸机是五机五流弧形连铸机,主要生产高碳钢,铸机主要工艺参数见下表:目前,高碳钢轻压下压下量为 9mm,从低倍检验看,铸坯存在一定程度中心疏松,铸坯中心碳偏析也一直徘徊在 1.15 左右,与其他炼钢厂相比有很大差距,难以满足日益增长的客户需求。
3 凝固末端计算对高碳钢发生纵裂漏钢的坯壳进行分析,将漏钢坯壳横向切开,测量切开点的坯壳厚度,根据坯壳厚度计算凝固系数,漏钢时浇注工艺如下:漏钢坯壳示意图如下:坯壳厚度测量结果及凝固系数计算如下:注:凝固系数:K=D*(V/L) 1/2 D 为凝固坯壳厚度,V 为拉速,L 为到液面距离取两点的平均凝固系数作为综合凝固系数K,则可计算出液芯长度 L。
新钢板坯连铸工艺参数和动态轻压下工艺优化研究
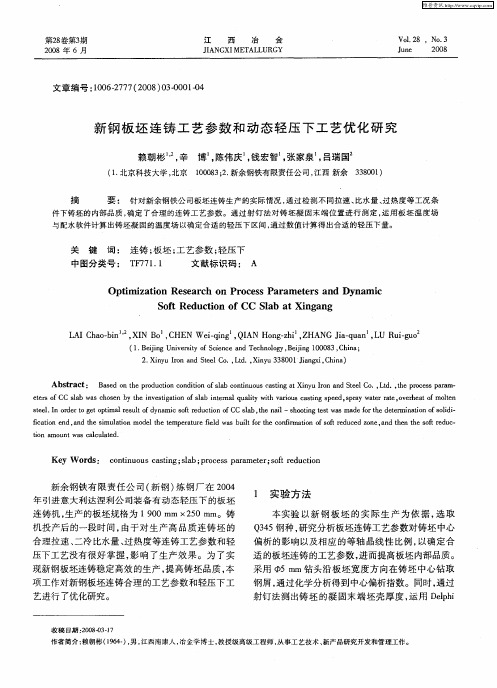
So tRe uc i f CC l b a ng n f d ton o S a tXi a g
L IC a。i ・, I o , HE i ig , I N H n —h , H N i q a L u—u A hobn X N B C N We— n Q A o gzi Z A G J —u n , U R i o q a g Nhomakorabea关
键
词 : 连铸 ; 坯 ; 板 工艺 参 数 ; 压 下 轻
文献 标识 码 : A
中图分类号 : T 7 1 1 F 7 .
Op i z to s a c n o e s Pa a e e s a d Dy mi tmi a i n Re e r h o Pr c s r m t r n na c
连铸 机 , 产 的板坯规 格 为 190mm× 5 m。铸 生 0 2 0m
机投产后的一段时间 , 由于对生产高品质连铸坯的
合 理 拉速 、 二冷 比水量 、 热 度等 连铸 工艺 参 数和 轻 过 压 下工 艺没 有很 好 掌 握 , 响 了生 产 效 果 。 为 了实 影 现 新钢 板坯连 铸稳 定 高效 的生 产 , 高铸 坯 品质 , 提 本 项 工作 对新 钢板坯连 铸 合理 的工艺 参数 和 轻压 下工
( . e igU ie i f c neadT c nl y B in 0 03 C ia 1 B in nvrt o i c n eh o g ,e i 10 8 , hn ; j sy S e o jg
2 XnuI na dSel o ,t. Xnu3 80 i glC ia . i r n t . Ld , iy 3 0 1 a x, hn ) y o eC Jn
年 引进意大 利达 涅利 公 司装备 有 动态 轻压 下 的板 坯
《2024年改善连铸板坯缺陷的轧制工艺》范文

《改善连铸板坯缺陷的轧制工艺》篇一一、引言在钢铁工业中,连铸板坯是关键的产品之一。
其质量和性能直接影响后续产品的质量与使用寿命。
然而,由于生产工艺和设备等因素,连铸板坯常常会出现各种缺陷,如裂纹、夹杂、偏析等。
这些缺陷不仅影响产品的性能,还可能对生产过程造成不利影响。
因此,改善连铸板坯的轧制工艺,减少其缺陷,对于提高产品质量和效率具有重要意义。
本文将就如何改善连铸板坯的轧制工艺,减少其缺陷进行探讨。
二、连铸板坯常见缺陷及原因分析1. 裂纹:裂纹是连铸板坯最常见的缺陷之一,主要是由于结晶器冷却不均、拉速过快或过慢、钢水成分不均等因素导致的。
2. 夹杂:夹杂是连铸板坯中常见的质量缺陷,主要是由于钢水中的夹杂物未能有效去除或夹杂物在结晶过程中进入板坯。
3. 偏析:偏析是指板坯内部化学成分不均匀,主要由于冶炼过程中熔体成分控制不当或冷却速度不均所致。
三、改善轧制工艺以减少连铸板坯缺陷1. 优化轧制工艺参数根据连铸板坯的成分、尺寸和性能要求,制定合理的轧制工艺参数。
这包括轧制速度、轧制力、轧辊温度等。
通过优化这些参数,可以改善板坯的内部组织和性能,减少缺陷的产生。
2. 严格控制轧制过程中的温度制度在轧制过程中,要严格控制轧辊和板坯的温度。
过高的温度可能导致板坯表面粗糙度增加,过低的温度则可能导致轧制力增加和内部裂纹的产生。
因此,需要合理设置轧辊的冷却水和润滑系统,保证合适的温度制度。
3. 加强轧机设备的维护和检修轧机设备的性能对连铸板坯的质量有重要影响。
因此,需要定期对轧机设备进行维护和检修,确保其正常运行。
这包括对轧辊的磨损情况进行检查和更换,对润滑系统进行清洗和更换油品等。
4. 引入先进的轧制技术随着科技的发展,许多先进的轧制技术被广泛应用于钢铁工业中。
例如,采用高精度轧制技术可以减少板坯的尺寸偏差和形状缺陷;采用热连轧技术可以减少中间环节的冷却和加热过程,降低热应力和组织不均匀性等。
这些技术的应用可以有效提高连铸板坯的质量和减少缺陷的产生。
涟钢板坯连铸轻压下技术的研究与应用
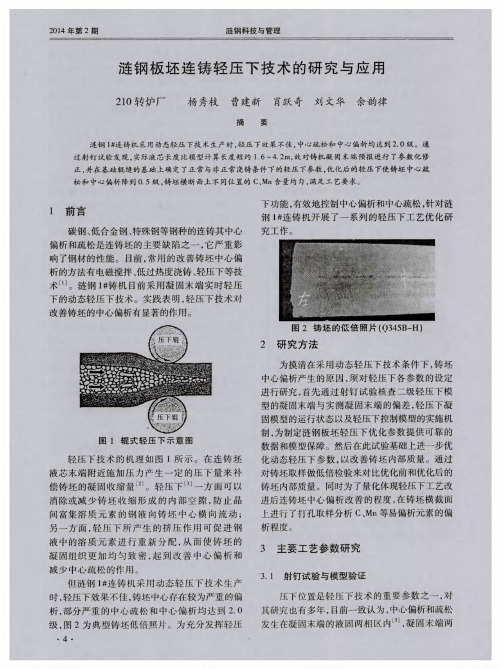
随拉速的变化较大 , 故轻压下 的参数设定也应 随 拉速 变化 , 实 际上 l # 连 铸机 轻 压下 控 制 系统 也 是 通过 拉速 的 变化来 实现辊 缝 的动态调 整 。
3 . 3 轻压 下 参数优 化
低倍照片。从 图中可以看出, 优化后 , 铸坯中心质
量 明显 改善 , 中心 疏松 和 中心偏 析基本 消失 , 其 中
浇铸 、 尾 坯 减速 、 事故减速、 恢 复等 ) 下, 对“ 轻 压 下 恒速 辊缝 ” 进 行修 正 执行 ; 同时 , 对 事 故 以 外 的 变 速做 限制 。
・
见由于轻压下的作用 , 局部地方枝晶被压缩变形 、 甚 至折断 。
如 图 8所示 , 在 铸 坯 横 断 面 上 不 同位 置 打 孔 取样 进行 C、 Mn易偏 析元 素化 学 分 析 , 以 了解 轻 压 下优化 后元 素 的偏析 情况 。
① ②
a . 预报模型与实际生产有偏差 , 其中实际凝
固末 端 比模 型计 算 位 置 短 约 1 . 6—4 . 2 m, 故 对铸 机凝 固末 端预 报进 行 了参 数化 修正 。 b .涟 钢基础 辊 缝能 够 满 足 生产 , 并 在 此 基础 上确 定 了正 常 与 非 正 常 浇 铸 条 件 下 的 轻 压 下 参 数, 实 践证 明优 化后 的轻 压下 效果 显著 。 C .优 化后 , 铸 坯 中心 质 量 明 显 改 善 , 中心 疏
系统中, 并在操作界面实现最佳轻压下工艺的控
制 。2 0 1 1 年 9 月 ~1 1月 对 Q 3 4 5 系 列 钢 种
3 0 ℃
拉速 、 过热度
l _ O m/ mi n
2 5  ̄ C 3 0 ℃ 拉速\ 过热度
薄板坯连铸带液芯轻压下技术

第39卷 第2期2004年2月 钢 铁I RON AND ST EELV o l.39,N o.2Feb ruary2004薄板坯连铸带液芯轻压下技术袁集华(钢铁研究总院连铸技术国家工程研究中心,北京100081)摘 要 就薄板坯连铸带液芯轻压下过程的设备条件、控制系统、工艺要求、生产操作方式、铸坯的质量等做了简要的概述。
结构合理的扇形段和能力恰当的液压缸、先进的PL C控制系统是轻压下的技术关键;稳定及合适的连铸工艺亦是带液芯轻压下不可缺少的基本前提;扇形段采用平行缓慢方式挤压带液芯的铸坯是稳定生产的有效措施;薄板坯连铸带液芯轻压下对铸坯质量的影响比较小。
关键词 薄板坯连铸 带液芯轻压下中图法分类号 T F77717 文献标识码 ATH IN S LAB CAST ING W ITH L IQU I D CORE RED UCT I ONYU AN J ihua(N ati onal Engineering and R esearch Cen ter fo r Con tinuou s Casting T echno logy,Cen tral Iron and Steel R esearch In stitu te,Beijing100081)ABSTRACT T he equ i pm en t,con tro l system,techn ical requ irem en ts,op erati on m ode and p rod2 uct quality of th in slab casting w ith liqu id co re reducti on(L CR)are in troduced1T he segm en ts w ith reasonab le design,cylinders w ith su itab le cap acity,and advanced PL C system are the key p arts fo r L CR1T he stab le and su itab le casting techno logies are also the p reconditi on s fo r L CR1 In the segm en ts the liqu id co re th in slab shou ld be squeezed slow ly and p arallelly1L CR has a lit2 tle effect on th in slab quality1KEY WORD S th in slab casting,liqu id co re reducti on1 前言带液芯轻压下技术已成为薄板坯连铸连轧工艺流程中的一个重要组成部分,并已成熟地应用于实际生产过程中。
板坯连铸轻压下技术的研究与应用

电磁搅拌、 低过热度浇铸 、 轻压下等技术。实 践表明, 轻压下技 术对改善铸坯 的中心偏 析有 显 著 的作用 , 钢 1铸 机 目前 就 是采 用 根 据 涟 #
凝 固末端进行 实时轻压下 的动态 轻压下技术 。
图 2 铸 坯 的 低 倍 照 片 ( 3 5 H) Q 4 B—
2 研究方法
9 . l 7 1 7 4. 8 2 . 9 5 O 0 .7 2 4 2 87
图 3 凝 固末 端 两 相 示 意 图
从 表 2中可 以看 出 , 钉试 验 得 到 的凝 射
为摸 清在采 用 动 态 轻压 下 技 术 条 件 下 , 铸坯 中心 偏析 产 生 的原 因 , 对 轻 压下 各 参 须
图 1 辊 式 轻 压 下 示 先通 过 射 钉 试 验 核 故
查 二级轻 压下模 型 的凝 固末 端 与实测 凝 固末
轻压下 技术 的 机理 如 图 1所 示 : 连铸 在
量方面均有优势, 但中心偏析和疏松是 连铸
坯 的 主要缺 陷 之 一 , 它严 重 影 响 了钢 材 的性 能 。 目前 , 常用 的改善铸坯 中心偏析 的方 法有
20级 , 2为典型铸坯低倍 照片。为充分 . 图 发挥 轻压 下功 能 , 效地 控 制 中心偏 析 和 中 有
心疏 松 , 对 1连铸 机 开展 了一 系列 的轻 压 针 # 下工 艺优 化研究 工作 。 ,
促 进钢 液 中的 溶质 元 素 进行 重 新 分 配 , 而 从 使 铸坯 的凝 固组 织 更 加 均匀 致 密 , 到 改 善 起
中心偏 析 和减少 中心疏 松 的作 用 。
涟 钢 1 连 铸 机 采用 动 态 轻 压 下 技 术 生 # 产时 , 压下 效果 不佳 , 坯 中心存 在较 为严 轻 铸 重 的偏 析 , 部分 中心 疏松 和 中心偏 析 均 达 到
应用轻压下技术提高连铸坯质量的研究
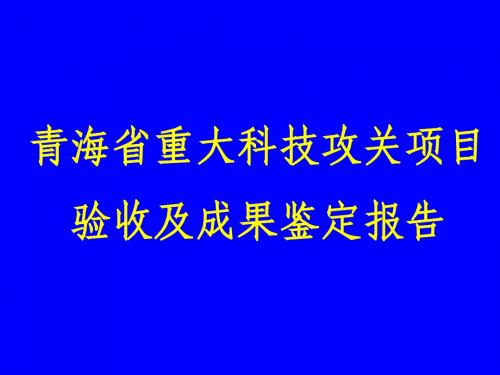
压下量,mm; L—辊距,mm;ε许用应变,≤0.15% 由公式(1)可以看出,对一定的辊列布置情况,附加 应变与压下量成正比,与凝固坯固坯壳的厚度成正比。 (2).物理模拟 (3).数值模拟
轻压下工艺的应用
• Danieli公司在试验中证实,在相同液芯率的 条件下,枝晶间的内部横向裂纹随着压下量 的增加成正比增加。曼内斯曼—德马克公司 的ISP工艺在二冷区扇形段液芯铸坯下拉速为 常数时,认为带液芯铸坯减薄是由逆向挤出 液芯实现的,坯壳宽面的纵向变形很小。 • 日本福山钢厂1986年4月在4号板坯连铸机上 安装了由分段辊组成的小间隙的轻压下扇形 段,最佳轻压下率0.9mm/min,试验的结果表 明不但可以减少大的宏观偏析,而且半宏观 偏析级别也明显地减少。
采用优化的连铸轻压下工艺生产的试验轴承钢连铸坯中心碳 偏析指数平均达到1.09级,中心疏松平均0.94级,一般疏松 平均0.87级,缩孔平均0.47级。与攻关前的指标相比:中心 碳偏析平均降低0.11,中心疏松平均降低1.86级,缩孔平均 降低1.53级。各项指标达到项目考核技术指标。
2 技术报告
青海省重大科技攻关项目 验收及成果鉴定报告
应用轻压下技术 提高连铸坯质量的研究
项目编号:2004-G-110 管理部门:青海省科学技术厅 承担单位:西宁特殊钢股份有限公司 协作单位:青海博世冶金研究所
1.1 项目简介 高碳的轴承钢、弹簧钢、碳素工具钢是西宁特钢的主导产品, 其年产量约占西钢年总产量的20%,在国内占有较大的市场份额。 长期以来,西钢一直采用模注工艺生产这些钢。模注工艺生产的钢 成材率低,生产成本高,表面质量差;采用连铸工艺生产的特殊钢 表面质量好,成材率显著提高,极大地节约生产成本,因此,连铸 成为当今特殊钢生产的主流。 西宁特钢于1997年引进美国康卡斯特的合金钢大方坯连铸机, 经过调试、试生产于1999年开始生产轴承钢、弹簧钢、碳素工具钢 等高碳的特殊钢。虽然连铸钢的表面质量较模注钢有了很大的改善 ,但因高碳钢固液两相区较其它钢种宽,在连铸坯的凝固过程中由 于选分结晶和凝固收缩导致富集溶质的钢液向中心的宏观流动而引 起中心偏析,同时由于枝晶“搭桥”,下部钢液在凝固收缩过程中 得不到上部钢液的补充,形成残余缩孔和中心疏松等缺陷,并伴随 产生中心的正或负偏析。
常规板坯连铸轻压下技术的发展与应用.
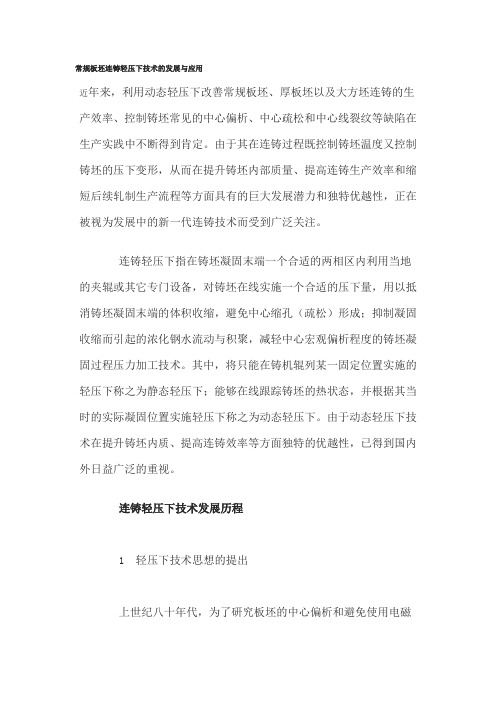
常规板坯连铸轻压下技术的发展与应用近年来,利用动态轻压下改善常规板坯、厚板坯以及大方坯连铸的生产效率、控制铸坯常见的中心偏析、中心疏松和中心线裂纹等缺陷在生产实践中不断得到肯定。
由于其在连铸过程既控制铸坯温度又控制铸坯的压下变形,从而在提升铸坯内部质量、提高连铸生产效率和缩短后续轧制生产流程等方面具有的巨大发展潜力和独特优越性,正在被视为发展中的新一代连铸技术而受到广泛关注。
连铸轻压下指在铸坯凝固末端一个合适的两相区内利用当地的夹辊或其它专门设备,对铸坯在线实施一个合适的压下量,用以抵消铸坯凝固末端的体积收缩,避免中心缩孔(疏松)形成;抑制凝固收缩而引起的浓化钢水流动与积聚,减轻中心宏观偏析程度的铸坯凝固过程压力加工技术。
其中,将只能在铸机辊列某一固定位置实施的轻压下称之为静态轻压下;能够在线跟踪铸坯的热状态,并根据其当时的实际凝固位置实施轻压下称之为动态轻压下。
由于动态轻压下技术在提升铸坯内质、提高连铸效率等方面独特的优越性,已得到国内外日益广泛的重视。
连铸轻压下技术发展历程1 轻压下技术思想的提出上世纪八十年代,为了研究板坯的中心偏析和避免使用电磁搅拌所带来的中心白亮带问题,新日铁公司曾尝试在凝固末端的扇形段人为加大辊缝收缩量(约0.6-0.8mm/m),发现其对控制板坯鼓肚和中心偏析有比较明显的效果。
这就是所谓的板坯静态轻压下,静态轻压下必须与拉速很好配合才能具有比较稳定的工艺效果,应用过程中有很大的局限性。
此后,新日铁和NKK 还分别研究了一些变异的轻压下途径,如NKK 提出人为鼓肚轻压下的概念,并将此应用在该公司福山6 号板坯连铸机上。
新日铁也提出过圆盘凸型辊轻压下法,其做法是把夹辊的中间部分做成凸台。
不难发现,由于上述轻压下工艺一直没能摆脱静态轻压下固有的局限性,实际生产中,难以很好地发挥作用,所以这些技术一直难以推广应用。
但它为凝固过程通过辊缝控制来改善铸坯内部质量提供了发展思路。
南钢超低头板坯连铸机轻压下技术的实现
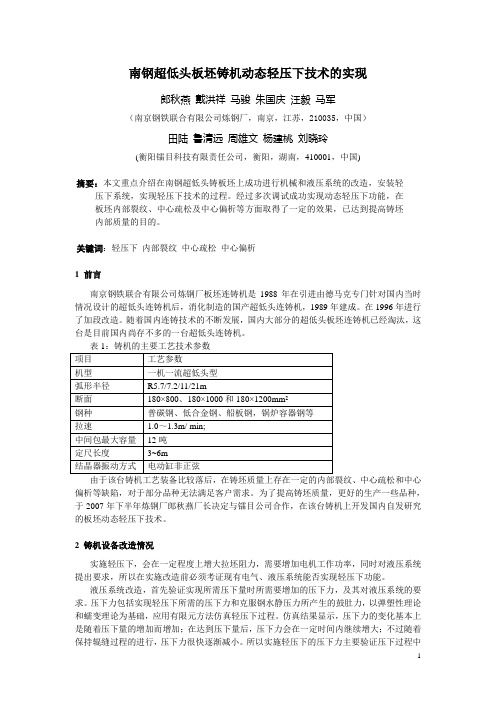
南钢超低头板坯铸机动态轻压下技术的实现郎秋燕戴洪祥马骏朱国庆汪毅马军(南京钢铁联合有限公司炼钢厂,南京,江苏,210035,中国)田陆鲁清远周雄文杨建桃刘晓玲(衡阳镭目科技有限责任公司,衡阳,湖南,410001,中国)摘要:本文重点介绍在南钢超低头铸板坯上成功进行机械和液压系统的改造,安装轻压下系统,实现轻压下技术的过程。
经过多次调试成功实现动态轻压下功能,在板坯内部裂纹、中心疏松及中心偏析等方面取得了一定的效果,已达到提高铸坯内部质量的目的。
关键词:轻压下内部裂纹中心疏松中心偏析1 前言南京钢铁联合有限公司炼钢厂板坯连铸机是1988年在引进由德马克专门针对国内当时情况设计的超低头连铸机后,消化制造的国产超低头连铸机,1989年建成。
在1996年进行了加段改造。
随着国内连铸技术的不断发展,国内大部分的超低头板坯连铸机已经淘汰,这台是目前国内尚存不多的一台超低头连铸机。
由于该台铸机工艺装备比较落后,在铸坯质量上存在一定的内部裂纹、中心疏松和中心偏析等缺陷,对于部分品种无法满足客户需求。
为了提高铸坯质量,更好的生产一些品种,于2007年下半年炼钢厂郞秋燕厂长决定与镭目公司合作,在该台铸机上开发国内自发研究的板坯动态轻压下技术。
2 铸机设备改造情况实施轻压下,会在一定程度上增大拉坯阻力,需要增加电机工作功率,同时对液压系统提出要求,所以在实施改造前必须考证现有电气、液压系统能否实现轻压下功能。
液压系统改造,首先验证实现所需压下量时所需要增加的压下力,及其对液压系统的要求。
压下力包括实现轻压下所需的压下力和克服钢水静压力所产生的鼓肚力,以弹塑性理论和蠕变理论为基础,应用有限元方法仿真轻压下过程。
仿真结果显示,压下力的变化基本上是随着压下量的增加而增加;在达到压下量后,压下力会在一定时间内继续增大;不过随着保持辊缝过程的进行,压下力很快逐渐减小。
所以实施轻压下的压下力主要验证压下过程中出现的最大值。
再通过分析机架受力模型:辊子受到铸坯作用力为均布载荷,受四个夹紧油缸力为集中载荷,可计算轻压下所需的油缸压强:压下2mm,8MPa;3mm,15MPa;4mm,18MPa;5mm,24MPa;6mm,34MPa。
超轻镁合金板坯直冷连铸数值模拟及工艺优化的开题报告
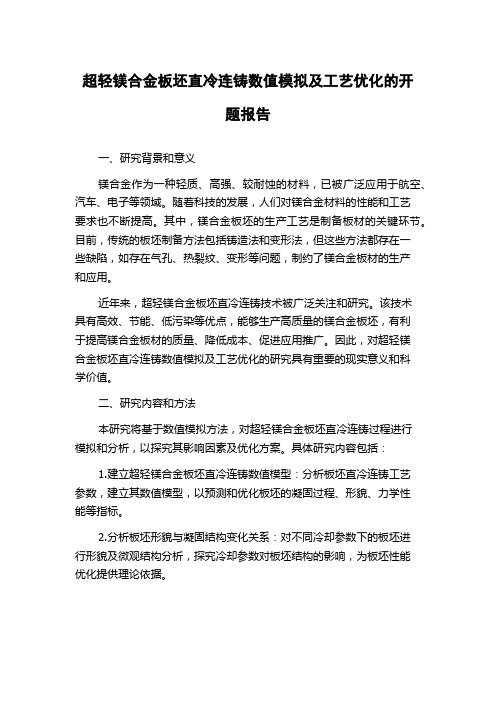
超轻镁合金板坯直冷连铸数值模拟及工艺优化的开题报告一、研究背景和意义镁合金作为一种轻质、高强、较耐蚀的材料,已被广泛应用于航空、汽车、电子等领域。
随着科技的发展,人们对镁合金材料的性能和工艺要求也不断提高。
其中,镁合金板坯的生产工艺是制备板材的关键环节。
目前,传统的板坯制备方法包括铸造法和变形法,但这些方法都存在一些缺陷,如存在气孔、热裂纹、变形等问题,制约了镁合金板材的生产和应用。
近年来,超轻镁合金板坯直冷连铸技术被广泛关注和研究。
该技术具有高效、节能、低污染等优点,能够生产高质量的镁合金板坯,有利于提高镁合金板材的质量、降低成本、促进应用推广。
因此,对超轻镁合金板坯直冷连铸数值模拟及工艺优化的研究具有重要的现实意义和科学价值。
二、研究内容和方法本研究将基于数值模拟方法,对超轻镁合金板坯直冷连铸过程进行模拟和分析,以探究其影响因素及优化方案。
具体研究内容包括:1.建立超轻镁合金板坯直冷连铸数值模型:分析板坯直冷连铸工艺参数,建立其数值模型,以预测和优化板坯的凝固过程、形貌、力学性能等指标。
2.分析板坯形貌与凝固结构变化关系:对不同冷却参数下的板坯进行形貌及微观结构分析,探究冷却参数对板坯结构的影响,为板坯性能优化提供理论依据。
3.优化板坯制备工艺:基于数值模拟结果,结合实验数据,分析制备工艺参数对板坯性能的影响,提出优化方案,以提高板坯质量和制备效率。
采用物理数值模型的理论分析和实验方法相结合,对板坯的制备工艺进行优化,探究不同工艺参数对板坯性能的影响及优化方案,揭示板坯形貌与微观结构的关系和机制,以期实现超轻镁合金板坯直冷连铸工艺的高效化、精细化、低成本化。
三、研究成果预期本研究将通过对超轻镁合金板坯直冷连铸数值模拟及工艺优化的研究,得到以下几方面预期成果:1.建立镁合金板坯直冷连铸数值模型,预测和优化板坯制备工艺,提高板坯质量和制备效率。
2.探究不同冷却参数对板坯的形貌及微观结构的影响和机制,为制备高质量镁合金板材提供理论依据。
铝合金板坯连铸PIV模拟及工艺优化的开题报告

铝合金板坯连铸PIV模拟及工艺优化的开题报告开题报告一、选题的背景铝合金作为一种重要的结构材料,广泛应用于航空、汽车、建筑等领域。
铝合金板坯的生产过程中,连铸是一项重要的工艺环节,直接影响板坯的质量和生产效率。
在连铸过程中,流场的运动特性是决定板坯形状和表面质量的关键因素。
因此,铝合金板坯连铸流场的研究和优化具有重要意义。
二、选题的目的和意义本课题旨在通过PIV(粒子图像测速)技术对铝合金板坯连铸中的流场进行研究和分析,并对连铸过程中的工艺参数进行优化,以实现铝合金板坯的高质量生产。
该研究对于铝合金板坯生产的质量提高和生产效率的提高具有重要意义。
三、研究内容和方法本研究将采用PIV技术对铝合金板坯连铸中的流场进行测量和分析。
具体包括以下研究内容:1.铝合金板坯连铸的工艺流程和流场特性的理论研究。
2.在实验室连铸装置中进行仿真实验,通过PIV测量连铸过程中的流场流速场和流线,分析流场特性和影响因素。
3.基于PIV实验数据,采用数值模拟对连铸流场进行建模和仿真,探究工艺参数对流场特性的影响,并优化工艺参数,以提高铝合金板坯的质量和生产效率。
四、预期成果本研究预期达到以下成果:1.对铝合金板坯连铸流场的结构和运动特性进行了深入研究,建立了完整的理论模型。
2.采用PIV技术对实验室连铸过程中的流场进行了测量和分析,获取了大量的实验数据和实测结果。
3.通过数值模拟和优化实验,分析了工艺参数对连铸流场的影响,提出了优化建议。
4.提出了铝合金板坯连铸生产的工艺优化方案,为铝合金板坯生产的质量和效率提高提供科学的参考和依据。
五、研究计划及预期进度本研究计划分为以下阶段:1.阶段一(两周):对铝合金板坯连铸流场的结构和运动特性进行理论研究和模型建立。
2.阶段二(四周):在实验室连铸装置中进行PIV实验,获取流场实测数据。
3.阶段三(四周):基于PIV实验数据,建立数值模拟模型,方案并进行数值模拟仿真分析。
4.阶段四(两周):分析数值模拟和实验结果,优化连铸工艺参数,提出优化建议。
- 1、下载文档前请自行甄别文档内容的完整性,平台不提供额外的编辑、内容补充、找答案等附加服务。
- 2、"仅部分预览"的文档,不可在线预览部分如存在完整性等问题,可反馈申请退款(可完整预览的文档不适用该条件!)。
- 3、如文档侵犯您的权益,请联系客服反馈,我们会尽快为您处理(人工客服工作时间:9:00-18:30)。
板坯连铸轻压下技术的工艺优化
在板坯凝固过程中产生的中心偏析直接影响成品的质量,轻压下技术已成为改善中心偏析的重要手段。
本文介绍了板坯连铸动态轻压下技术的原理,通过对压下位置、压下效率、压下量等关键参数的分析,阐述了动态轻压下控制的基本策略。
标签:板坯;轻压下;工艺
引言:
随着国内钢产量的过剩,人们对钢铁产品质量的要求越来越高,连铸坯中心偏析和中心疏松等缺陷是影响钢材质量的主要因素之一。
碳钢、低合金钢、特殊钢等钢种的连铸其中心偏析和疏松是连铸坯的主要缺陷之一,它严重影响了钢材的性能。
目前,常用的改善铸坯中心偏析的方法有电磁搅拌、低过热度浇铸、轻压下等技术。
轻压下被视为一种有效解决中心偏析的技术,在国内的钢厂,通过引进、合作开发得到了广泛应用。
一、轻压下技术的基本原理
为了较少中心偏折,在进行板坯铸造的过程中,必须要采取一定的的措施来使得未凝固的钢液减少流动,而轻压下技术的应用正是为了解决这一问题。
在板坯的末端区域选择较为合理的压下力,对钢液的流动进行阻止,保证在最后的凝固中心区域中的组织成分均匀,从而使得中心偏折的现象得到缓解。
但是在选择亚下力的过程中,要保证其适当性,过大反而会增加钢液的流动,起到相反的作用,并且使得设备的磨损加剧。
一般情况下,使用的压力都比较轻微(一般压下量在2mm—4mm之间)。
在轻压下技术中,又可将其分为静态轻压下和动态轻压下两种。
静态轻压下指的是只能在铸机的某一个固定位置实施轻压下;而动态轻压下则指的是可以在对板坯的实际凝固位置进行在线跟踪实施轻压下。
轻压下的效果与压下位置是否合适有着密切的关系,在进行压下位置的选择时,要尽可能地靠近板坯的凝固终点(假如已经完全凝固,就没有再进行轻压下的意义;如果仍然处于液态,则只能起到将板坯进行压薄的作用),如下图(图1)所示。
在静态轻压下,要求板坯的凝固终点必须落在辊列的固定位置,但是早实际生产中却难以进行准确控制。
除此之外,在事先设定的扇形段辊缝参数也不能够在浇铸过程中进行调整,由此就会使得轻压下效果达不到理想的效果。
与静态轻压下技术相比,动态轻压下具有更多的优越性,它能够对板坯凝固终点进行实时跟踪,能够在线对扇形段辊缝参数进行修改,并且可以对压下量进行调整。
二、轻压下技术的升级后的技术特点
(一)所有扇形段均具备轻压下功能(包括弧形段和水平段),在使用过程
中可以根据现场生产情况对可实施轻压下区域进行设置,随机确定需要投入轻压下扇形段的位置;
(二)灵活地对动态轻压下实施过程中的主要压下参数(理论压下区域和压下量)进行人工干预,有利于在生产新钢种时开展相关的实验研究,同时可以根据不同钢种的特点确定具体压下状态;
(三)可以根据设定的矫直点温度和铸机出口温度对铸机的目标表面温度曲线自动进行理论计算,有利于针对新钢种的开发获得合理的二冷水相关控制参数以及更好地实施动态二冷配水技术;
(四)进一步完善轻压下扇形段压下时序控制算法,更加有利于轻压下过程的合理实施和对扇形段设备的有效保护;
(五)针对扇形段辊缝的标定,除已有的在线标定方法以外,新增加了离线标定功能,可以在维修区将扇形段位移传感器标定完成后再安装到线上。
三、轻压下工艺参数的优化研究
(一)射钉试验研究
压下位置是轻压下技术的重要参数之一,位置合适与否直接影响铸坯的中心偏析情况。
射钉法是将示踪材料的钢钉击入正在凝固的坯壳,然后在铸坯相应位置取样进行分析。
钢钉为普碳钢,钢钉上有两道含有硫化物的沟槽。
钢钉中低熔点的硫化物在铸坯液相穴中会迅速完全扩散,因此可用酸侵蚀和硫印的方法处理含钢钉低倍,并根据硫化物的扩散情况测量出铸坯的液芯厚度和凝固壳厚度。
(二)数学模拟
通过建立数学模型对同一断面不同拉速下及不同过热度下的凝固过程进行计算,得到的结果如图2所示。
其中图2-a是过热度为25℃,断面为1310mm×230mm时,三种不同拉速下对应的不同凝壳厚度,从图中可知,随着拉速的提高,凝固末端位置向后移;图2-b是在拉速为1.1m/min时,不同过热度下凝壳厚度的变化情况,可见随着过热度的增加,凝固末端向后推移,但是变化幅度不大。
(三)轻压下参数优化
在正常浇铸条件下,铸坯规格一定,浇铸速度也基本稳定,在每一个稳定的工作拉速时,依据辊缝设定表都能确定铸机的辊缝值,在浇铸生产的大多数时间里(典拉速浇注)能够正常应用,并具有一定的灵活性。
这种辊缝值是在特定拉速下在基础辊缝的基础上设定的轻压下辊缝。
通过研究认为,基础辊缝的设定值基本可以满足连铸机的生产要求,故沿用原基础辊缝值。
1.压下量
压下量一般是指轻压下过程中对铸坯的总压下量,总压下量的設定必须满足几个条件:1)总压下量能够完全补偿铸坯的凝固收缩,防止富集溶质剩余液相的流动;2)压下量不能产生内部裂纹,轻压下引起的应力必须少于固液界面处的热塑性;3)压下量不能对铸机辊子寿命产生不利影响。
此外总压下量的设定的时候也要考虑到液的厚度,液芯厚度增加,必然在凝固收缩的时候,收缩量大,需要的总压下量也会随之增大。
总压下量越大,中心偏析效果越好。
连铸坯产生内部裂纹原因是固液相界面是零强度、属于典型的脆性区,所以进行相应的压下量压下时造成的变形量超过某一极限,就产生了内部裂纹,而变形量的确定则通过单位长度上的压下量来确定,即是用压下率(拉坯方向单位长度的压下量,mm/m)来体现,在实践生产中是对整个扇形段进行压下,所以压下率是通过每个扇形段上的压下量来计算的,一般情况下,板坯轻压下压下率合适范围为0.5~1.1mm/m。
2.压下区间
3.压下速率
压下速率(VR)是指单位时间的压下量,mm/s,在实际的轻压下过程中,铸坯的变形是非连续的,所谓的压下速率的控制只能通过对总压下量的分解来实现,即在每对压辊上均采用一个不会产生裂纹的较小压下量,铸坯经多对压辊分步压下之后,来实现总压下量。
最佳压下速率是指能够补偿铸坯凝固收缩时的数值,根据钢种不同物性和钢坯不同断面可以计算出铸坯不同温度收缩量,然后结合凝固模型,判断不同机架处收缩量来给定压下量。
最后完成压下速率的分配。
实际压下速率大于最佳压下速率,压下段单位时间压下量大于铸坯能承受的收缩变形量,容易引起裂纹;实际压下速率小于最佳压下速率,则对富集溶质的钢液的回流均匀化会有一定的影响,减弱中心偏析改善效果。
四、结束语
在实际的钢材生产过程中,轻压下技术已经越来越多的被应用,并且已经成为改善板坯中心偏折的重要手段。
动态轻压下技术的冶金原理是利用数学模型在线计算铸坯凝固末端位置,从而实施一定的压下量,防止两相区域溶质的富集,达到改善内部质量的目的。
所以,对于轻压下技术的应用,需要生产技术人员充分做好各方面的策略准备,对其进行经验总结,使其得到优化,提高工作效率与质量,促进钢铁行业的向前发展。
参考文献:
[1]杨晓江.薄板坯连铸技术的特点及其在唐钢的发展[J].钢铁技术,2002,01:15-23+14.
[2]祭程,朱苗勇.连铸机动态轻压下技术的开发与应用[A].本溪钢铁集团公司、中国金属学会连续铸钢分会.品种钢连铸坯质量控制技术研讨会论文集[C].本溪钢铁集团公司、中国金属学会连续铸钢分会,2008:6.
[3]杨拉道,关杰,张奇,曾晶,髙琦,马玉堂.板坯连铸动态轻压下工艺模型论述[J].重型机械,2010,S1:21-27.。