对薄板坯无头轧制技术的初步认识
无头轧制
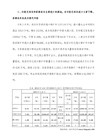
无头轧制生产线的基本构架
传统的板带热轧工艺难以保证带钢头尾厚差和穿带质量均匀性,轧制作业率、成材率也受到限制。为解决这些问题,上世纪末出现了无头轧制新工艺,显示出许多传统热带轧制无可比拟的优越性,现在已经在极薄热轧带钢、高品质高强度钢板和不锈钢板新产品生产方面显示出巨大的应用前景,成为热轧技术的发展方向。该技术由川崎制铁千叶厂3号热带轧机首先实现,以后逐渐得到推广。该生产线由以下几部分构成:
1.铸轧型无头轧制技术。
意大利达涅利公司开发成功该项技术并用于意大利乌迪内ABS公司的年产50万t特殊钢棒线材工业性生产厂中,已于2000年8月正式投产。
连铸机和热连轧机配置在一条生产线上,铸机产品为160mm×200mm大方坯,共两流。连铸机后设有两个淬火箱,其后为125m长辊底式加热炉,加热炉前设有65m长双流隧道式炉以作为工序间缓冲,热缓冲能力约为45t。
2003年1月,ABS公司对其Luna生产线上在线退火装置进行改造,将炉室长度增加一倍,可处理长50m轧材,原退火炉只能处理长24m轧材,严重制约整条生产线能力的发挥。
2.连铸坯焊接型无头轧制技术。
该技术是连铸方坯经步进式加热炉加热后将前一块钢坯尾部和后一块钢坯头部进行对焊(用闪光焊接),形成无头坯送热连轧机进行轧制,名为EWR(Endlees Welding Rolling)。自从1998年3月在日本东京高松厂问世以来有了快速的发展,闪光焊机设在加热炉出料端后,焊接过程由计算机控制,并纳入轧钢自动化系统,因而有良好的焊接过程稳定性和可重复性,各种断面形状和钢种的钢坯均能对焊,最大规格可达200x200mm。我国唐山钢铁公司棒材厂建设的EWR装置对焊165mm方坯所需周期约37-40秒,其中焊接时间约10秒。由于焊接技术的提高,焊口位置不但不存在内部缺陷,强度指标也不亚于轧件母体。
从ECR无头连铸连轧看实现高效连铸的关键

从ECR无头连铸连轧看实现高效连铸的关键ECR无头连铸连轧工艺中的高效连铸技术环境保护、降低生产成本是钢铁生产永恒的主题。
10几年来薄板坯连铸连轧、铸坯热送、热装技术使连铸成为最活跃的领域,这些技术的发展与实践大幅度地降低了设备投入及生产成本,提高了产品的竞争力。
同板材相比,长材生产在这些方面的进展则没有那么明显。
一方面长材生产是以小型钢厂生产为特点,投资少,见效快,众多的生产厂情况各异,技术水平差异很大。
这是方坯连铸技术革新及新技术推广落后于板材的主要原因。
另一方面,长材产品在钢材的总产量中占有相当的比重,长材生产推广高效连铸、铸坯热送、热装技术以及连铸连轧技术潜力巨大。
ECR无头连铸连轧工艺生产实践表明,采用先进合理的连铸工艺及其配套的装备,浇注160x200mm规格的连铸坯,普碳钢浇铸速度最大可以达到6米/分钟,合金钢浇铸速度最大可以达到3.5米/分钟以上。
实现了无漏钢连铸。
经连铸机生产的连铸坯通过隧道式加热炉直接供给轧机,不间断地直接轧制。
ECR无头连铸连轧生产线可极大地缩短从定单到最终产品发货之间的供货周期,最短供货周期可小于4小时,提高了生产的灵活性。
与现有的其它生产工艺相比,ECR无头连铸连轧生产线特殊钢生产成本平均降低45-50美元/吨,普通钢生产成本平均降低12-14美元/吨。
ECR无头连铸连轧技术1 主要工业参数和产品大纲ABS厂的ECR无头连铸连轧生产线设计能力为年产50万吨特钢成品,一台90吨电炉及配套的精炼设备,车间生产能力为90吨/小时。
特钢成品为用于机械加工行业、汽车制造工业以及其他特钢应用领域的优质圆钢、方钢、六角钢棒、线材和棒卷。
ECR无头连铸连轧生产线生产特钢成品时可以保证在线处理,不经离线再加工就可以生产出符合要求的优质产品。
ECR无头连铸连轧生产线同时也可生产普钢。
生产普钢的优势是使工厂在非常广的成品规格范围内,具有非常高的生产能力。
生产圆钢、螺纹钢筋、线材和棒卷、中小型钢、工字钢和特殊型钢的能力在80万吨/年左右。
热轧带钢无头轧制技术

热轧带钢无头轧制技术在精轧机前焊接薄板坯(粗轧机轧制的半成品),在精轧机内不间断地连续轧制,经卷取机前的剪切机切断后卷取。
由于无头轧制须将中间坯在粗轧后的辊道上焊接起来,然后连续不断地送入精轧机中轧制,所以存在以下技术要点:
(1)焊缝与母材的组织性能和强度应基本一致,以防止在精轧机中焊缝处断带。
(2)焊接过程中,不能影响前后设备的正常运转。
(3)板坯加热、粗轧机轧制和精轧机轧制节奏的精确控制和灵活调节。
(4)带钢在卷取前的高速切断以及卷取机的高速切换和穿带。
日前,宝钢成功试制出高强度双相不锈钢2205热轧带钢这一不锈钢中的顶级产品。
经检验,其性能和质量接近同类进口产品。
宝钢也是目前国内唯一试制出此种不锈钢的钢铁企业。
双相不锈钢因高强度、高耐蚀性、低成本、高附加值的特点而广泛应用于能源、海洋、建筑等重点工程领域,成为国内外不锈钢企业研究开发和生产的热点产品。
其中2205热轧带钢是目前市场上应用最为广泛的双相不锈钢产品,其产量占双相不锈钢产量的80%。
双相不锈钢2205热轧带钢试制难度极大,目前只有国外少数大型钢铁企业有能力生产。
宝钢充分利用一体化技术优势,研究院、不锈钢分公司、特殊钢分公司、浦钢及浦东国贸等生产、研发、销售单位联合攻关,依托不锈钢产销研小组,在9个月内成功试制出2205热轧带钢。
宝钢从去年3月开始了冶炼和热轧工艺实验室研究,10月底攻克了冶炼难关。
在热轧试制阶段,为确保热轧板卷试制顺利进行,研究院等部门的攻关小组先在浦钢进行了中板试制,并在12月中旬试制成功2205热轧带钢。
本钢薄板坯连铸连轧生产线半无头轧制的应用

本钢薄板坯连铸连轧生产线半无头轧制的应用摘要:介绍本钢薄板坯连铸连轧生产线半无头轧制技术的运用。
在薄规格生产中,利用半无头轧制方式提高轧制的稳定性,提高对带钢头部和尾部的控制精度,减少损耗,提高成材率。
关键词:半无头轧制;薄规格;楔形段当今世界热轧板生产正向着高效率、低能耗的方向发展,热轧薄规格产品逐渐占有更高比例,而单坯轧制模式,不可避免的存在产品头尾质量差和能耗高等问题,针对这种情况,本钢集团公司在2005年投产的薄板坯连铸连轧生产线上使用了半无头轧制。
1 薄规格轧制的主要问题目前轧钢设备越来越先进,技术不断发展,但在单坯生产模式下,由于其工艺和技术的限制,特别是在轧制薄规格产品时,曝露出当前无法避免的问题,体现在:(1)头尾问题。
在单坯生产中,带钢的头尾部分在非稳定状态下轧制,导致头部侧弯,尾部超宽,浪形以及厚度精度低等问题,使之头尾板形无法得到保证,在产品使用前需进行较多的切头和切尾,使产品成材率降低;(2)稳定性问题。
在生产薄规格产品时,带钢的甩尾、断带、折迭等问题发生的几率大大增加,对设备的损伤率也在增加,轧制的稳定性大打折扣;(3)拉窄问题。
薄规格轧制穿带时,为保证轧制稳定,机架间一般采用拉钢控制,但由于带钢头部温度、厚度较难准确控制,在穿带瞬间易发生头部拉窄现象。
2 问题分析及处理本钢的半无头轧制,主要针对1.5mm以下规格,针对单坯生产中存在问题,有目的的进行功能完善和参数修正,成功实现五分割(一块钢坯轧制六块产品)轧制,最薄0.8mm的超薄规格。
通过半无头轧制与单坯轧制的数据对比来看,半无头轧制针对薄规格和超薄规格的生产优势非常明显:(1)楔形段损耗。
在1.5~1.8mm规格生产中,通过三分割(四块产品)实现批量生产,在三分割四块产品中间的三个剪切点的带钢头尾在保证张力稳定状态下轧制,实际只有在第一和最后一块存在一头一尾是在带钢的非稳定状态下,四块产品的头尾缺陷等同于单坯轧制中的一块产品,所以由于头尾板形问题造成的损耗就比单坯轧制降低75%。
钢坯无头轧制设备与关键技术分析
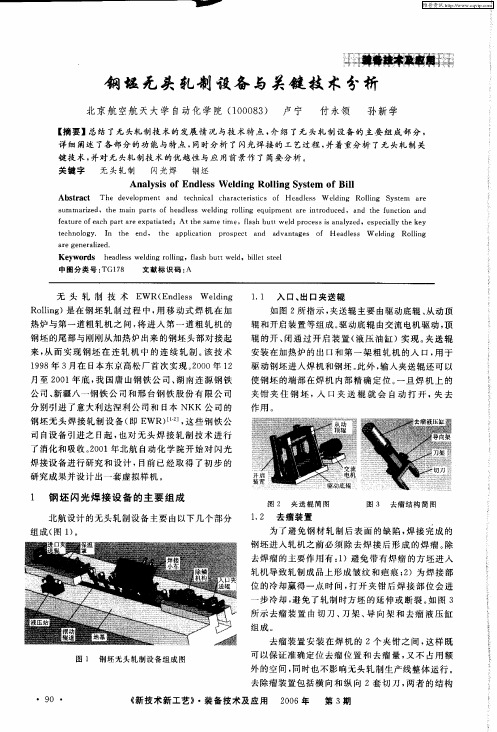
使 钢坯 的端部 在焊 机 内部精 确 定 位 。 旦焊 机 上 的 一 夹 钳 夹 住 钢 坯 ,入 口夹 送 棍 就 会 自动 打 开 , 去 失 作用。
月 至 20 0 1年底 , 国唐 山钢铁 公 司 、 我 湖南 连 源 钢 铁
如 图 2所 指示 , 送辊 主要 由驱 动底辊 、 动顶 夹 从 辊 和 开启 装置 等组 成 。 驱动底 辊 由交 流 电机 驱 动 , 顶
辊 的开 、 通 过 开 启装 置 ( 压 油 缸 )实 现 。 闭 液 夹送 辊 安 装 在加 热炉 的 出 口和 第 一架 粗 轧机 的人 口 , 于 用
组成 。
去瘤 装 置 安装 在 焊 机 的 2个 夹 钳之 间 , 样 既 这
公 司 、 疆八 一钢 铁 公 司 和邢 台钢 铁 股 份 有 限 公 司 新 分别 引 进 了意大利 达涅 利 公 司和 日本 NKK 公 司的 钢坯 无 头 焊接 轧 制设 备 ( E 即 WR) ~ , 些 钢 铁 公 口 】这
司 自设备 引进 之 日起 , 也对 无 头 焊 接 轧 制 技 术 进 行
组成 ( 1 。 图 )
图 2 夹送棍简 图
图 3 去瘤结构简 图
1 2 去 瘤装 置 .
为 了避 免 钢 材 轧 制后 表 面 的缺 陷 , 接 完 成 的 焊
钢坯 进 入轧 机之 前 必 须 除 去焊 接 后 形 成 的焊 瘤 。 除
去 焊瘤 的 主要作 用 有 :)避 免 带 有焊 瘤 的方 坯 进 入 1
Ab t a t Th d v lp e t n tc nc l c a a trsis f e de s W edn Rol g y tm a e s r c e e eo m n a d e h ia h rce it o H a ls c lig ln S se i r
无头轧制技术的发展及展望

无头轧制技术的发展及展望上世纪60年代以前,传统生产钢材方法是先将钢水模铸成大型钢锭,经加热、轧制成坯,钢坯经冷却、清整后再加热,轧成用户所需断面的成品钢材。
近40多年来经历了三次飞跃式发展:一是将模铸改为连铸,取消开坯机;二是由一般连铸改为近终形连铸,减少加热、轧制次数;无头轧制技术是钢铁加工流程的第三次飞跃,即钢材生产不再是单块的、间隙性的,而是连续进行轧制,然后根据用户需求剪切成所需长度或卷重。
无头轧制的好处是:1.钢材全长以恒定速度进行轧制,生产率有较大提高;2.因对钢材全长施加恒定张力,使钢材断面形状波动减少,钢材质量改善,这点对热轧扁平材生产特别重要;3.由于成品长度不受限制,根据交货状态要求剪切,成品率显著提高;4.由于轧材运行稳定性提高,对热轧带钢来说,有利于生产薄规格带钢;5.和单块轧制不同,钢品啮入次数减少,减小对轧辊冲击,有利于提高轧辊寿命。
在施行无头轧制技术中分扁平材和长材两类,其中又有无头轧制和半无头轧制的区别;就技术类型来说分为焊接型和铸轧型两种,将分别叙述于后。
扁平材的无头轧制1.在传统热连轧带钢机上无头轧制。
第一台全连续无头轧制热连轧带钢机是1996年在日本JFE公司千叶厂投用的。
它的轧机组成是:粗轧机架3台,精轧机架7台,辊身长2030mm,设计最高轧速为25m/s,年产能力为540万t。
连铸坯经加热在粗轧机架轧成最大厚度为50mm中间带坯进人热卷箱,在热卷箱后设有中间带坯剪断机,将带坯头剪平,以便于后面的焊接设备(用对接压合法电磁感应焊接)进行焊接,焊接后的带坯经过带坯边部加热器使带坯温度均匀,然后送入精轧机架轧成所需带钢厚度,由于中间带坯头尾已经焊接,从理论上来讲是可以无限长的,故称为无头轧制。
轧机后卷取机前设有高速带钢剪断机,将高速前进的带钢(最大1200m/min)切断分卷。
在千叶厂3号轧机全连续无头轧制取得成功经验后,日本新日铁公司和韩国浦项公司分别将其大分厂和光阳厂热连轧带钢机改造成能无头轧制的全连续热轧带钢机。
薄板坯连铸连轧无头轧制技术的应用
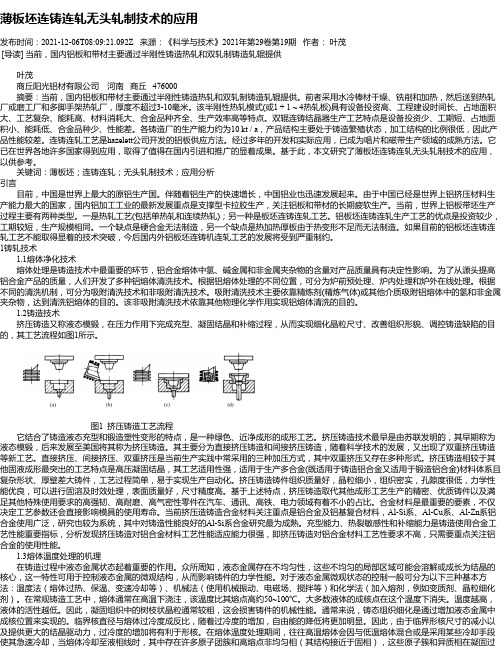
薄板坯连铸连轧无头轧制技术的应用发布时间:2021-12-06T08:09:21.092Z 来源:《科学与技术》2021年第29卷第19期作者:叶茂[导读] 当前,国内铝板和带材主要通过半刚性铸造热轧和双轧制铸造轧辊提供叶茂商丘阳光铝材有限公司河南商丘 476000摘要:当前,国内铝板和带材主要通过半刚性铸造热轧和双轧制铸造轧辊提供。
前者采用水冷棒材干燥、铣削和加热,然后送到热轧厂或磨工厂和多脚手架热轧厂,厚度不超过3-10毫米。
该半刚性热轧模式(或1 + 1 ~ 4热轧板)具有设备投资高、工程建设时间长、占地面积大、工艺复杂、能耗高、材料消耗大、合金品种齐全、生产效率高等特点。
双辊连铸结晶器生产工艺特点是设备投资少、工期短、占地面积小、能耗低、合金品种少、性能差。
各铸造厂的生产能力约为10 kt / a,产品结构主要处于铸造繁殖状态,加工结构的比例很低,因此产品性能较差。
连铸连轧工艺是hazelett公司开发的铝板供应方法。
经过多年的开发和实际应用,已成为唱片和磁带生产领域的成熟方法。
它已在世界各地许多国家得到应用,取得了值得在国内引进和推广的显着成果。
基于此,本文研究了薄板坯连铸连轧无头轧制技术的应用,以供参考。
关键词:薄板坯;连铸连轧;无头轧制技术;应用分析引言目前,中国是世界上最大的原铝生产国。
伴随着铝生产的快速增长,中国铝业也迅速发展起来。
由于中国已经是世界上铝挤压材料生产能力最大的国家,国内铝加工工业的最新发展重点是支撑型卡拉胶生产,关注铝板和带材的长期疲软生产。
当前,世界上铝板带坯生产过程主要有两种类型。
一是热轧工艺(包括单热轧和连续热轧);另一种是板坯连铸连轧工艺。
铝板坯连铸连轧生产工艺的优点是投资较少,工期较短,生产规模相同。
一个缺点是硬合金无法制造,另一个缺点是热加热厚板由于热变形不足而无法制造。
如果目前的铝板坯连铸连轧工艺不能取得显着的技术突破,今后国内外铝板坯连铸机连轧工艺的发展将受到严重制约。
薄板坯连铸连轧工艺技术发展的概况

薄板坯连铸连轧工艺技术发展的概况摘要:薄板坯连铸连轧工艺问世这么多年来发展迅速,CSP、ISP、FTSR为代表的各种工艺技术的发展各具特色。
总的发展趋势是,提高铸机生产能力充分发挥后部连轧机的生产能力;改进品种质量,提高产品的市场覆盖率;采用无头轧制工艺、生产超薄规格产品,以取代部分冷轧产品的市场;应用范围扩大,越来越多的在以高炉铁水为原料的大型联合企业中得到应用,为该工艺的发展开拓了更广阔的前景。
关键词:薄板坯连铸连轧发展趋势1 前言薄板坯连铸连轧是20 世纪80 年代末开发成功的生产热轧板卷的新技术,该项技术发展很快,世界各钢铁发达国家已相继开发了各具特色的薄板坯连铸连轧技术,主要有SMS 开发的CSP(CompactStrip Production)、DEMAG 的ISP(Inline Strip Production)、日本住友的QSP(Quality Slab Production)、达涅利的FTSR(Flexible Thin Slab Rolling)和VAI 的CONROLL(Continue Rolling)以及美国蒂金斯(Tippins)的TSP(Thin Slab Production)等6 种类型。
图2典型的薄板坯连铸—连轧热带钢生产线薄板连铸连轧工艺与常规的工艺相比,由于它具有节能、投资省、生产周期短、劳动成本低及适应性强等优点,故引起了全世界的重视。
据统计全球各地已建成投产及在建的薄板坯连铸共约50流,总生产能力为5228万t/a。
2 几种主要类型的技术特点及其发展2.1 CSP工艺技术世界第一条CSP生产线薄板坯连铸连轧生产线已于1989年建成投产,因其工艺开发早,技术成熟,工艺及设备相对较简单可靠,故实际应用也最多。
至1997年末,SMS已签定的合同已有27流铸机。
CSP技术的主要特点是采用立弯式铸机漏斗形结晶器,最初的铸坯很薄,一般为40~50mm,未采用液芯压下,后部设辊底式隧道炉作为铸坯的加热均热及缓冲装置,采用5~6架精轧机,成品带钢最薄为1~2mm。
无头轧制技术

无头轧制技术。
该技术是指粗轧后带坯在进入精轧机前,与前一根带坯的尾部焊接起来,连续不断地通过精轧机。
这种技术扩大了传统热带轧机的轧制范围,可批量生产0.8毫米的超薄带钢。
开发这个技术是基于市场上对于采用价格较为低廉的热轧薄带钢来代替冷轧
带钢的强烈要求。
精轧后超快速冷却技术,比传统冷速快5~10倍,可以细化晶粒,明显改善所得带钢性能。
铁素体非常软,易于成形,而马氏体却极其坚硬,成形性受限。
贝氏体的强度和成形性位于这两个极端之间
板形控制先进技术
[编辑本段] 改善和提高板形控制水平,需要从两个方面入手,一是从设备配置方面,如采用先进的板形控制手段,增加轧机刚度等;二是从工艺配置方面,包括轧辊原始凸度的给定、变形量与道次分配等。
常规的板形控制手段主要有弯辊控制技术、倾辊控制技术和分段冷却控制技术等。
近年来,一些特殊的控制技术,如抽辊技术(HC轧机和UC系列轧机)、涨辊技术(VC轧机和IC轧机)、轧制力分布控制技术(DSR动态板形辊)和轧辊边部热喷淋技术等先进的板形控制技术,得到日益广泛的应用。
在此,分别就其中几种典型技术作以简单介绍。
薄板坯连铸连轧无头轧制技术的应用

(TaxgsPax Quaxfeng Sheet Co. , Ltd. , TaxgsPax 063300, Hebei) Abstrcct: Endless rolling technology is avother leap of iron aod steei production technology , renresenting the cotting - enge technology of ho- rollen strin in the worlU, With the rayiO deveNpmen- of the thira generation thin slab continuous costing aod rolling technology characterized by enniess rolling technology , the deveNpment of endless rolling technology for ho- rollen plate chv further improv the yielU of plate aod strin , the acchrach of size aod shape aod the proportion of thin gaoge aod ultra - thin gaoge , reelize partial " heat instead of colU" aod renucc roll consumption. The proccss flow , production line characteristics aod product charac teristics of endless rolling technology are introduccn. Taping Rizhao ESP production line , Shougaog Jingtaog MCCR production line aod Taogshao aonual DSCCR production line as example , the aOvaoWpes aod disabvaoWpes of each production line are comparen. C view of the existing problems of endless rolling , the devetopment aod op/mizz/on direction are put forwara. Key words:thin slab; continuous chsting aod rolling; endless rolling; ESP; MCCR; DSCCR
薄板坯连铸连轧技术综述

薄板坯连铸连轧技术综述薄板坯连铸连轧技术是一种先进的钢铁生产技术,它将连铸和连轧两个工序有机地结合在一起,实现了钢铁生产的高效、节能、环保和高质量。
本文将从薄板坯连铸连轧技术的原理、特点、应用和发展趋势等方面进行综述。
一、薄板坯连铸连轧技术的原理薄板坯连铸连轧技术是将连铸和连轧两个工序有机地结合在一起,实现了钢铁生产的高效、节能、环保和高质量。
其原理是:将熔融的钢水通过连铸机连续铸造成薄板坯,然后将薄板坯直接送入轧机进行连续轧制,最终得到所需的薄板产品。
这种技术不仅可以减少钢铁生产的能耗和环境污染,还可以提高钢铁产品的质量和生产效率。
二、薄板坯连铸连轧技术的特点1.高效节能:薄板坯连铸连轧技术将连铸和连轧两个工序有机地结合在一起,避免了传统钢铁生产中的多次加热和冷却过程,大大降低了能耗和生产成本。
2.环保节能:薄板坯连铸连轧技术可以减少钢铁生产中的二氧化碳、氮氧化物等有害气体的排放,降低了环境污染和对大气的负荷。
3.高质量:薄板坯连铸连轧技术可以实现钢铁产品的高质量生产,因为它可以避免传统钢铁生产中的多次加热和冷却过程,减少了钢铁产品的氧化和变形。
4.生产效率高:薄板坯连铸连轧技术可以实现钢铁产品的高效生产,因为它可以将连铸和连轧两个工序有机地结合在一起,减少了生产周期和生产成本。
三、薄板坯连铸连轧技术的应用薄板坯连铸连轧技术已经广泛应用于钢铁生产中,特别是在高端钢铁产品的生产中。
例如,汽车、航空航天、电子、建筑等领域的高端钢铁产品都可以采用薄板坯连铸连轧技术进行生产。
此外,薄板坯连铸连轧技术还可以用于生产高强度、高韧性、高耐磨性等特殊钢铁产品。
四、薄板坯连铸连轧技术的发展趋势随着钢铁生产技术的不断发展和进步,薄板坯连铸连轧技术也在不断地改进和完善。
未来,薄板坯连铸连轧技术将更加注重环保、节能和高效,同时还将更加注重钢铁产品的高质量和高附加值。
此外,薄板坯连铸连轧技术还将更加注重智能化和自动化,以提高生产效率和生产质量。
薄板坯连铸短流程节约型无头轧制装备与技术 北京讲座
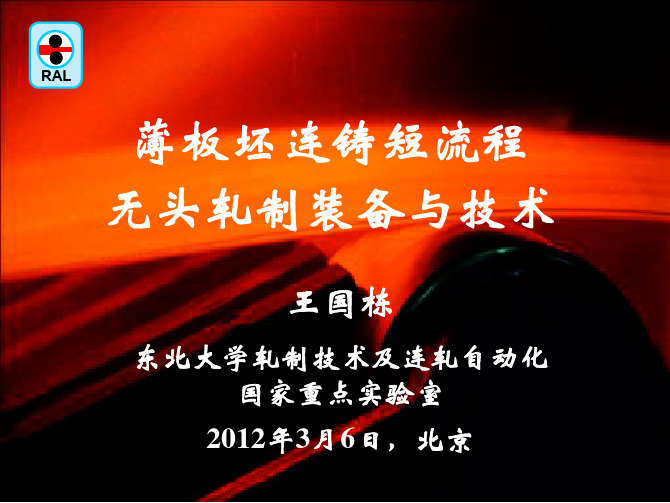
75mm : 7.0m/min max.
连铸平台
12-19mm : ~1.0m/s
薄板坯连铸机
120T电炉
大压下轧机 电感应加热器
摆动式飞剪
克罗蒙那加热 炉
飞剪
精轧机
1.0-12mm : 12.5m/s max
层流冷却
地下卷取机
55mm : 10m/min max.
12-19mm : 0.2-0.5m/s
钢、硼钢、耐候钢、合金钢和双相钢等 • 该生产线具备生产0.7mm厚的所有冷轧能生产的同规格产品的能力,包
括IF钢(汽车板)、多相钢、薄带甚至有高延伸率和抗拉强度等特殊性能的 钢,用来满足汽车工业的需要。
RAL
1 2 3 4 5 6 7 8 9 10 11 12 13
14
2003年ISP产线生产指标
46%
45%
RAL
连铸坯宽度 /mm 1250
ISP生产线连铸设备工艺参数
结晶器厚度 /mm
75
连铸坯厚度 /mm
55
最大拉速 /m/min
7.0
钢水浇铸流量 /T/min
3.7
• 平均每浇次连浇炉数11炉钢 • 56%以上的产品厚度规格都小于2mm • 最大轧制宽度1600mm,厚度在1.2mm以下的薄板材 • 生产大部分钢种,例如低、中、高碳钢(0.75%),1.2mm的高强度低合金
175m
ISP工艺布置
1.0-12mm
连铸坯宽度 /mm
1250
结晶器厚度 /mm
75
开始生产时间: 1992 2009年产量: 100万吨 产品厚度: min.1.0mm
连铸坯厚度 /mm
55
最大拉速 /m/min
无头-半无头轧制技术-康永林-2010[1].11.23
![无头-半无头轧制技术-康永林-2010[1].11.23](https://img.taocdn.com/s3/m/c67c046858fafab069dc026d.png)
的尺寸和板形不良或非稳定轧制引起的质量不良.
9
提高生产率
各板坯连接处的穿带速度可达1000m/min以上,另外,单块坯 轧制中的间歇时间在无头轧制中减为零,由此可显著提高薄 规格轧制效率。
可生产薄
而宽的钢 板和超薄 规格板
10
通过润滑轧制和强制冷却轧制生产新品种
当第一块板坯的头部通过精轧机组后,直到最 后部分板带通过机组的较长时间内都可实现 稳定润滑,因此,在能进行稳定润滑的同时 又可减少材料损耗1/6~1/10 。 在无头轧制时,由于可以对精轧出口处的板带 施加张力,即使采用快速冷却,不存在穿带 和冷却不均问题,由此可得到全长均匀的材 质。
定位
感应加热
对接
连接完成
去毛刺
17
感 应加热连接设备
加热装置
线圈 磁芯
夹持·压接 运行方向
感应电流
压接
升降装置
压接
18
控制磁通
升温速度比率
无控制
连接区边界
材质:SUS 304 尺寸:30t×800w mm
(中心) 宽向距离 (mm)
感应加热铸坯连接的温度分布比率
19
感应加热连接区表面状态及断面组织
7
生 产 率 问 题:
♦精轧生产率最低的是薄规格轧制 ♦单位宽度的轧制量即质量流量不大,所以产量不高 ♦为了提高产量,使稳定轧制速度基本达到其上限约
1500m/min的饱和状态
♦穿带速度提高后,由于穿带问题和头部折迭等引起
的故障率增多,穿带速度的上限约在800m/min左 右,薄规格轧制的生产率基本达到极限状态
无头轧制的中间坯连接技术
叠轧 咬合轧制 铝热焊 锯齿形 机械连接 还原性 火焰处理 直接通电连 接 感应加热 连接 激光连接
无头轧制技术

无头轧制无头轧制技术是指将粗轧后的带坯在中间辊道上焊合起来,并连续不断地通过精轧机的一种技术。
传统的板带热连轧精轧机组生产均以单块中间坯进行轧制,因此,不可避免地要经过进精轧机组时的穿带、加速轧制、减速轧制、抛钢、甩尾等一系列过程。
由此发生的尺寸公差和力学性能的不均匀性很难在原有工艺框架内得到解决。
热轧带无头轧制新技术正是解决这些问题的一项重要的技术突破。
在传统热连轧中,板坯是在精轧机中一块一块地轧制的,带钢的头部在出了精轧机到卷取机之前的这段长度上以及尾部出精轧机后的这段长度上处于无张力的状态,造成每一卷带钢的头尾部分尺寸公差和板形难以保证。
同时,单块坯轧制时因尾部无张力,故在精轧机架间常发生甩尾形成2~3层折迭咬入,从而产生轧辊表面裂纹和压痕伤。
而无头轧制是将大约10块带坯在出粗轧机后的中间辊道上头尾焊合在一起,接着进入精轧机中连续轧制,带坯在恒张力下轧制,因此几何精度和板形不良的比例大幅度下降。
无头轧制因穿带和抛尾的减少,可以做到稳定的润滑轧制。
与此同时,稳定的润滑轧制可使轧制力降低,因而可在较低温度下进行轧制,生产出具有良好深冲性能的带钢,并可降低能源消耗。
应用无头轧制法主要应用在型材、盘条和带材的连续轧制生产上。
优点是:(1)可大幅度提高盘条的盘重和轧机产量。
由于消除了每根轧件在各机架咬入瞬间引起的动态降速,连轧过程稳定,张力波动减小,从而为进一步提高轧制速度创造了条件;由于消除了两根相邻轧件之间的间隙时间,轧机利用率显著提高,除换辊和检修外,连续轧制时间可达几个昼夜,轧机作业率可达90%以上,生产能力提高10%~12%;盘条的盘重可根据要求用飞剪任意调节;(2)消除了咬入时因堆拉钢造成的断面尺寸超差和中间轧废,并大量减少切头、切尾的金属消耗,从而使金属收得率提高3%以上,产品质量也得以提高。
当采用钢坯首尾对焊法连续供坯时,焊缝质量良好,各项性能指标与母材基本一致;(3)减少了温度较低的轧件头、尾部分对轧辊和导卫装置的频繁冲击,减少了轧辊磨损,有利于轧机及其传动装置的平稳运转;(4)在实现连续酸洗、动态变规格轧制、连续退火和精整的带钢全连续化冷轧生产线上,为生产高品质、低消耗、多规格的带钢创造了条件(见冷轧板带生产);(5)连续稳定的轧制给整个生产过程的自动控制创造了有利条件。
薄板坯无头连铸连轧生产线运行现状

薄板坯无头连铸连轧生产线运行现状2021年6月,世界第一条薄板坯无头连铸连轧生产线(ESP)在意大利阿尔维迪公司克莱蒙纳厂正式投入工业化运行。
这是历史上首次以连续不间断的生产工艺通过薄板坯连铸连轧设备从钢水直接生产出热轧带卷。
该设备基于阿尔维迪ISP技术,能够实现钢水热能最大程度的开发利用。
这套新的铸轧生产设备是世界上生产热轧带钢最紧凑的生产线,总长仅有190m,连铸和轧制工艺直接串联,显著降低成本。
而且,ESP生产线是第一条能够在7min内完成从钢水到地下卷曲机上的全连续生产线。
这套设备额定产能为200万t/a,生产带卷最宽可达1600mm,最薄可达0.8mm。
所生产的薄规格和超薄规格热轧带卷可以直接进行下游生产加工。
ESP无头带钢生产线能够生产从低碳钢到高碳钢以及合金钢的完整产品系列,包括高等级优质钢种,比如高硅钢和用于制造汽车车身面板的IF钢。
ESP无头带钢生产线拥有众多先进的技术和系统,主要包括:其中包括液芯压下以及动态辊缝调宽和轻压下等工艺包,从而确保最佳内部铸流质量。
铸机直接与配有AGC和辊形控制的3机架四辊大压下轧机相连;在单独控制设置点的基础上,感应加热炉可在1100℃~1200℃的温度范围内灵活地将传送钢带均匀加热。
精轧机配有SmartCrown辊以确保带钢具有非常好的平直度。
钢带在走出最后一个机架后,由层流冷却系统进行冷却,从而根据需要调整带钢的力学特点。
钢带经高速剪切机剪切后,由三个地下卷曲机中的一个进行卷取,单卷重量可达32t。
整条生产线完全由集成的1级和2级自动化系统控制,该系统可以全面调节所有铸轧操作。
另外还有一个全面质量控制系统进行辅助,可确保产品达到所需的质量标准。
与传统薄板坯连铸连轧工艺相比,ESP无头带钢生产线所需的能源和水消耗大幅降低。
根据最终产品的不同,能量消耗可降低50%~70%,水消耗可减少60%~80%。
1 技术背景将薄板坯连铸工艺和热轧工艺串联起来,直接生产热轧带钢的技术诞生于20世纪90年代前后。
无头轧制和半无头轧制技术简析

无头轧制和半无头轧制技术是近年来出现的新技术。
无头轧制主要应用在热轧带钢和棒线材生产中,半无头轧制主要应用在薄板坯连铸连轧生产中。
采用传统分块轧制方式的轧机要频繁的咬钢、抛钢和变换轧制速度,造成钢材头、尾部的质量难以保证,轧机作业率较低,对产品尺寸精度的控制也较为困难。
对此,有关科技工作者通过在传统的热轧生产线上设置钢坯对焊机实现精轧连续轧制。
该方法与传统轧制方法相比,成材率可提高0.5%至1.0%;生产率可提高10%至15%;产品质量、精度也有较大进步。
此外,用传统的轧制方法轧薄板时容易出现跑偏、甩尾、浪形等问题,而无头轧制则无此现象,可改善钢带行走的稳定性,可生产0.8-1.0mm带材。
最后,由于避免频繁的咬钢,设备的磨损和废品率也有所下降,可降低2.5%-3%的生产成本。
第一台全连续无头轧制热连轧带钢机是1996年在日本JFE公司千叶厂投用的。
它的轧机组成是:3架粗轧机,7 架精轧机,辊身长2030mm,设计最高轧速为25m/s,年产能力为540万t。
在千叶厂3号轧机全连续无头轧制取得成功经验后,日本新日铁和韩国浦项分别将其大分厂和光阳厂热连轧带钢机改造成能无头轧制的全连续热轧带钢机。
半无头轧制主要用于薄板坯连铸连轧生产线,主要是为生产薄规格热轧带钢设计的,固然其设备配置与传统的薄板坯连铸连轧大体相同,但是技术有很大变化。
比如,采用半无头轧制的CSP生产线,薄板坯出结晶器时的厚度为63mm,经过液芯压下后离开连轧机时连铸坯厚度为48mm。
此时,连铸坯不间断进入隧道式加热炉(传统CSP生产线连铸坯剪断为40多米),加热炉可达300多米(传统CSP生产线为200m);连铸坯均热后进入7机架连轧机组轧制成材。
该生产线的输出冷却辊道分为两段,第一段较短,为30m左右,其中快速冷却水集管为10m左右,冷却段后是超薄带卷取机;第二段为传统的层流冷却和传统的卷取机,主要生产一般规格的热带。
为对生产的成品带钢进行分卷,在每个卷取机前均设有高速飞剪。
钢坯无头轧制设备与关键技术分析
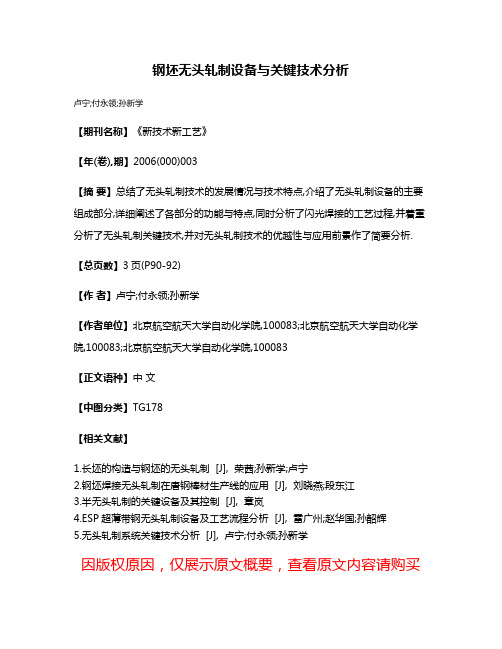
钢坯无头轧制设备与关键技术分析
卢宁;付永领;孙新学
【期刊名称】《新技术新工艺》
【年(卷),期】2006(000)003
【摘要】总结了无头轧制技术的发展情况与技术特点,介绍了无头轧制设备的主要组成部分,详细阐述了各部分的功能与特点,同时分析了闪光焊接的工艺过程,并着重分析了无头轧制关键技术,并对无头轧制技术的优越性与应用前景作了简要分析.【总页数】3页(P90-92)
【作者】卢宁;付永领;孙新学
【作者单位】北京航空航天大学自动化学院,100083;北京航空航天大学自动化学院,100083;北京航空航天大学自动化学院,100083
【正文语种】中文
【中图分类】TG178
【相关文献】
1.长坯的构造与钢坯的无头轧制 [J], 荣茜;孙新学;卢宁
2.钢坯焊接无头轧制在唐钢棒材生产线的应用 [J], 刘晓燕;段东江
3.半无头轧制的关键设备及其控制 [J], 章岚
4.ESP超薄带钢无头轧制设备及工艺流程分析 [J], 雷广州;赵华国;孙韶辉
5.无头轧制系统关键技术分析 [J], 卢宁;付永领;孙新学
因版权原因,仅展示原文概要,查看原文内容请购买。
- 1、下载文档前请自行甄别文档内容的完整性,平台不提供额外的编辑、内容补充、找答案等附加服务。
- 2、"仅部分预览"的文档,不可在线预览部分如存在完整性等问题,可反馈申请退款(可完整预览的文档不适用该条件!)。
- 3、如文档侵犯您的权益,请联系客服反馈,我们会尽快为您处理(人工客服工作时间:9:00-18:30)。
差异分析
连续轧程 目标规格比例, 成材率 板形质量
半无头轧制
短,4~7卷 20~50% 低 一般 在不断变化中 轧制,升/降 速轧制、动态 变规格,不断 的板形调整。 大
无头轧制
长,一个辊期 90%以上 少 高 好 在一个辊期开始 和结束是变化的, 中间过程可以根 据订单计划稳定 轧制。 小 高
09:46
4、第三代TSCR技术的潜力
从已经建成投产的第三代TSCR技术看,从以下几个方面 还有进一步优化开发的潜力: 连铸头尾坯因拉速低、温度低,不能直接轧制成材,而是 以中间坯形式剔出; 由于缺少中间缓冲,在连铸的一个浇次内,轧机不能换辊 ,连铸的连浇炉数受限制,对产能和金属收得率有影响; 生产低拉速难浇钢种,钢通量低,铸坯温度低,轧制过程 温降大,难以实现无头轧制困难; 铸坯横向温度均匀性对产品质量构成一定的影响。
9、轧钢技术
粗轧出口设置多功能仪,对于精轧板型控制提供前馈; 无头轧制模式过程FGC动态变厚度; 粗轧和精轧机组实现自动水平调整,减少人工调整误操作。 在线带载荷窜辊,实现无头轧制过程中的板型调整; 通过电磁感应加热实现FET的闭环自动控制; 精轧出口设置板型检测辊,可实现无头轧制板型在线检测和 控制; 轧机设定、板形设定和层流冷却设定协调控制实现无缝衔 接; 立辊设定和结晶器调宽联合宽度控制; 自适应穿带功能,提高头部设定精度 。
4、三点除鳞
为提升带钢表面质量,产线布置有三套除鳞装置,以避免氧化 铁皮残留,有效保证产品的表面质量。 连铸扇形段出口采用摆动除鳞装置,除鳞压力1~6MPa,主要目 标是去除附于铸坯表面的氧化铁皮和保护渣等,减少均热炉炉 辊粘铁皮疙瘩的机会; 粗轧入口在立辊轧机和R1之间布置单排集管的除鳞机,除鳞压 力35MPa,高压小流量,温降小,除鳞点距R1最近,可减少二次 铁皮产生; 精轧入口布置了双排集管的除鳞装置,除鳞压力35MPa,高压小 流量,温降小,无头轧制时采用单排集管除鳞,以减少温降单 块和半无头轧制采用双排集管除鳞。
6、中间坯的感应加热 项目
加热器数量 单台容量(MW) 合计容量(MW) 线圈类型
参数及说明
9套 4.3 38.7 TF型(磁力线垂直穿透板坯) 系统为达涅利传动工厂制造,采用加热效率高 的TF型线圈,采用DANIELI专利技术保持板坯 横断面温度均匀,线圈高度可调,可提高感应 加热效率,但应用业绩少。
感应加热功率
轧机布置 层流冷却类型及冷却段长度 生产线总长度
4.3MW*9组
粗轧3架+精轧5架 24段加强型层流冷却;55.68m 286m
1、连铸实现高拉速、高钢通量
110mm铸坯厚度 钢种 123mm铸坯厚度
1300钢通 1300钢通 拉速, 拉速, 量, 量, m/min m/min t/min t/min 6.0 6.69 6.13 5.58 5.02 4.46 4.5 4.0 5.61 4.99
~200米辊底炉
第二代 半无头轧制 55~80 3.5~4.5
液芯压下/凝固末端动 态软压下
第三代 全无头 80~120 5.0~6.5
液芯压下+凝固末端动 态软压下 ~10m电磁感应加热; 80m辊底炉+10m电磁感 应加热
1300mm钢通量,t/min 铸坯软压下方式 加热模式 轧机架数 轧制速度制度 最小厚度规格,mm 生产线长度,m
特点
※ 感应加热功率比ESP的36MW高,主要是考虑高强钢等品种。
7、热机轧制
具有热机轧制功能,在精轧除 鳞机前面集成布置了强制冷却 喷淋水,用于轧制高强品种。
8、加强型层流冷却
层流冷却段长度为 55.68M; 最大水量为 8500M3/hr。 对于生产薄规格(≤3mm)高强度钢,采用加强型层流冷却既能够 满足冷却速度和生产DP钢分段冷却的要求,又有利于板型控制。 层流冷却采用边部遮挡,提高带钢宽度上的温度均匀性。
金属秒流量(m·mm/s) 5.5
金属秒流量达到11,意味着轧制1.0mm带钢终轧速度可以达到 11m/s; 提高钢通量就意味在铸坯增厚的条件下还要实现高拉速。
09:46
钢通量是无头轧制的工艺保证
铸坯厚度增加,铸机的曲率半径就要增加、同等拉速下铸机的 冶金长度大幅度增加、钢水静压力增加、辊列设计…… 高拉速的相应保障措施: ① ② ③ ④ ⑤ ⑥ ⑦ ⑧ ⑨ ⑩
117 112 107 102 97 92 87 82
MCCR铸坯厚度与拉速、铸机生产能力的关系
铸坯厚度,mm
3、增加80M长均热炉
主要目的是均匀铸坯温度,增加产线的中间缓冲。 ① 使产线具有无头轧制/半无头轧制/单坯轧制三种生产模式。
无头轧制模式生产0.8 ̄2.0mm薄规格产品; 半无头轧制模式生产2.0 ̄4.0mm的一般薄规格产品;(与CSP目的不同) 单坯轧制模式用于头尾坯轧制、单卷取机生产条件下维持生产、可生产 1.5 ̄12.7mm的大纲覆盖的全部产品。
过渡卷(带出品) 多
轧制过程
操作难度
设备功能精度要求 高
3、第三代TSCR技术的突出特点
铸坯厚度增加、拉坯速度提高、钢通量大幅度提高; 采用直弧机型(立弯机型将退出),连铸冶金长度不断增加; 采用无头轧制技术实现热轧1.5mm以下薄规格产品的稳定生产; 由于无均热炉(或长度缩短)、逆向温度场轧制等因素,工序 能耗显著降低,约30~50%; 氧化铁皮烧损少,金属收得率、成材率大幅度提高,不仅轧钢 过程无切头切尾;带钢头尾性能及板形无差异也不需要切除。 特别是生产薄规格产品金属收得率高、成本低; 板形质量好,带钢全长性能、板形尺寸均匀,无头中尾差异; 配合后处理产线实现“以热代冷”, 具备较强的市场竞争力。
拉速,M/min
生产能力,%
低拉速难浇钢种采用厚 规格铸坯,提高连铸钢 通量(秒流量); 对于低碳和超低碳钢, 可以用薄规格铸坯高拉 速生产。
8.00 7.50 7.00 6.50 6.00 5.50 5.00 4.50 4.00 100 102 104 106 108 110 112 114 116 118 120 122 124 126 128 130 132 134
低碳、中碳、
低碳微合金、中碳微合金 5.5 高碳钢、双相钢/Trip 合金钢、耐候钢 包晶钢、合金化包晶钢 5.0 4.5 4.0
2、连铸坯厚度增加
MCCR结晶器出口 130mm,铸坯厚度110/123mm;
采用液芯压下/动态软压下“双模式”,可实现铸坯厚度根据不 同品种和拉速进行调整,既可提高铸坯质量又可提高扇形段寿命。 同等拉速下钢通量比90mm厚铸坯增加1/4,产品大纲列出的钢种均 可进行无头轧制(拉速≥4.5M/min)。
11、MCCR智能工厂建设
09:46
1、薄板坯连铸连轧技术的发展及其特征
*引自毛新平院士2015薄板坯连铸连轧国际研讨会上的报告
09:46
1、薄板坯连铸连轧技术的发展及其特征
技术特征 标志性特征 铸坯厚度,mm
(未考虑conroll、QSP及ASP)
第一代 单坯轧制 45~65 3~3.5 液芯压下
3、增加80M长均热炉 隧道式均热炉的主要技术:
采用Ni、Cr系列辊环材质(含Co~7%),有利于提高辊子寿 命,采用窄辊环错开布置,减少氧化铁皮疙瘩对铸坯下表面 的伤害。 先进的全连续双交叉限幅+脉冲燃烧控制系统,即可实现节 能又能实现炉温的精准控制;出炉板坯温度±10℃,而且边 角温度略高,有利于轧制稳定、质量控制和产品开发。 采用空煤气预热和烟气余热回收的梯级能源回收利用系统; 增加铸坯移出装置,事故状态下可移出铸坯; 横移段入口侧采用悬臂自动火焰切割用于铸坯事故切断。
09:46
钢通量是无头轧制的工艺保证
连铸必须为轧制提供高的钢通量,以保证轧制速度,减少 轧制温度降、减少补热。
薄板坯无头轧制要遵循连铸━连轧金属秒流量相等原则,可以 简单的描述为: Qm=H×Vc/60=h×Vr Vc:连铸拉坯速度,m/min H: 连铸坯厚度,mm Vr:带钢轧制速度,m/s h: 带钢的厚度,mm 薄板坯连铸钢通量一般只能达到轧制要求金属秒流量的 1/3~1/2;要提高连铸钢通量,就必须增加铸坯厚度、提高拉坯 速度。
项目
产线生产能力 铸机类型 钢包和中包容量 结晶器类型 铸坯规格范围 液芯压下能力 最大在线调宽量 设计最大拉速 加热炉类型、长度
参数
200~220万吨/年 直弧型;R5.5m 200~250t;70t 长漏斗或短漏斗型;出口130mm (900~1600)*(110~123)mm 液芯压下/动态软压下“双模式”;20mm 无限制;700mm 6.0m/min 辊底式隧道炉;长度79.2m
09:46
钢通量是无头轧制的工艺保证
各种类型的薄板坯铸机所能提供的秒流量如下表:
铸机类型 机型 铸机半径(m) 冶金长度(m) 铸坯厚度(mm) 拉坯速度(m/min) 1300钢通量(t/min) CSP 立弯 3.25 10 55 6.0 3.35 FTSC 直弧 5.0 14 70 6.0 7 4.26 ESP 直弧 5.0 20 90 6.0 9 5.47 CEM 直弧 5.5 20 90 6.0 9 5.47 MCCR 直弧 5.5 26 110(123) 6.0(4.5) 11(9.2) 6.69(5.61)
主要产品:
以薄为主,以热代冷。以薄规格低碳软钢为主,替代传统冷轧中 低端产品,也可为单机架冷轧提供薄规格基料,降低轧制成本; 生产薄规格耐候钢和薄规格结构钢; 开发高强度高性能薄规格热轧产品,产线具备生产1000Mpa以上 的3.0mm以下的薄规格高强热轧品种能力。
09:46
主要技术参数和配置
② 增加了连铸和轧机之间缓冲,可实现连铸不停浇换辊 ; ③ 连铸的头尾坯可以轧制成卷,提高金属收得率1%以上; ④ 铸坯温度均匀,可使带钢横向性能均匀、边部质量好;宜生产 Nb、V、Ti钢;