无头轧制
轧钢生产中应用的新技术新工艺
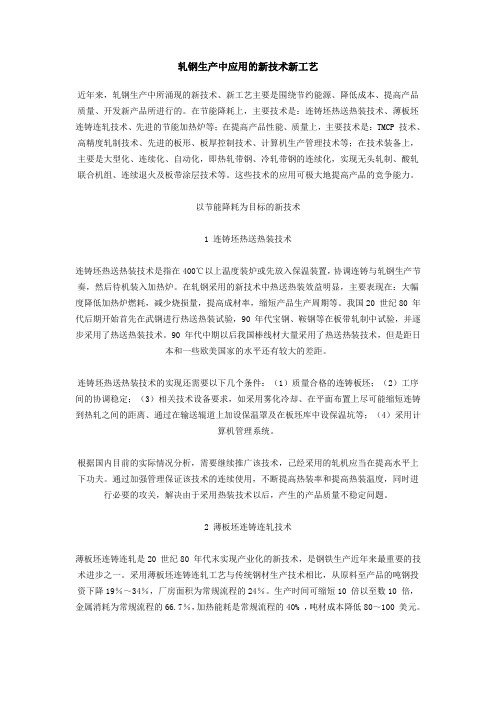
轧钢生产中应用的新技术新工艺近年来,轧钢生产中所涌现的新技术、新工艺主要是围绕节约能源、降低成本、提高产品质量、开发新产品所进行的。
在节能降耗上,主要技术是:连铸坯热送热装技术、薄板坯连铸连轧技术、先进的节能加热炉等;在提高产品性能、质量上,主要技术是:TMCP 技术、高精度轧制技术、先进的板形、板厚控制技术、计算机生产管理技术等;在技术装备上,主要是大型化、连续化、自动化,即热轧带钢、冷轧带钢的连续化,实现无头轧制、酸轧联合机组、连续退火及板带涂层技术等。
这些技术的应用可极大地提高产品的竞争能力。
以节能降耗为目标的新技术1 连铸坯热送热装技术连铸坯热送热装技术是指在400℃以上温度装炉或先放入保温装置,协调连铸与轧钢生产节奏,然后待机装入加热炉。
在轧钢采用的新技术中热送热装效益明显,主要表现在:大幅度降低加热炉燃耗,减少烧损量,提高成材率,缩短产品生产周期等。
我国20 世纪80 年代后期开始首先在武钢进行热送热装试验,90 年代宝钢、鞍钢等在板带轧制中试验,并逐步采用了热送热装技术。
90 年代中期以后我国棒线材大量采用了热送热装技术,但是距日本和一些欧美国家的水平还有较大的差距。
连铸坯热送热装技术的实现还需要以下几个条件:(1)质量合格的连铸板坯;(2)工序间的协调稳定;(3)相关技术设备要求,如采用雾化冷却、在平面布置上尽可能缩短连铸到热轧之间的距离、通过在输送辊道上加设保温罩及在板坯库中设保温坑等;(4)采用计算机管理系统。
根据国内目前的实际情况分析,需要继续推广该技术,己经采用的轧机应当在提高水平上下功夫。
通过加强管理保证该技术的连续使用,不断提高热装率和提高热装温度,同时进行必要的攻关,解决由于采用热装技术以后,产生的产品质量不稳定问题。
2 薄板坯连铸连轧技术薄板坯连铸连轧是20 世纪80 年代末实现产业化的新技术,是钢铁生产近年来最重要的技术进步之一。
采用薄板坯连铸连轧工艺与传统钢材生产技术相比,从原料至产品的吨钢投资下降19%~34%,厂房面积为常规流程的24%。
带钢无头连铸连轧技术(ESP)简介

带钢无头连铸连轧技术(ESP)简介截止2013年底,我国共有70套热轧宽带钢机组己投产,产能达到2.29亿吨,由此产生的能耗巨大。
近年来,为了节能降耗,欧洲、日本和韩国等国家的钢铁企业在努力实现热轧板带减量化制造技术方面进行了大量的研究开发工作并取得显著效果。
其中,开发和发展热轧板带无头轧制技术,进一步提高板带成材率、尺寸形状精度与薄规格超薄规格比例、实现部分〃以热代冷〃、降低辐耗等方面取得显著成绩。
该项技术是钢铁生产技术的又一次飞跃, 代表了当今世界热轧带钢的前沿技术。
1997年浦项和日立联合着手开始研制采用剪切、焊接工艺,进行中间坯连接的带钢无头轧制新工艺。
1998年4月,日本新日铁大分厂研制成功了利用高能激光器对中间板坯实现对焊的钢板无头轧制生产线。
2006-2007年浦项和日立采用剪切、焊接工艺进行中间坯连接的带钢无头轧制新工艺投入工业化生产,这种基于摆剪概念的新型固态连接工艺,实现了无头轧制连接技术的创新。
2009年意大利钢铁企业阿维迪与西门子公司联手打造的世界第一套ESP无头铸轧带钢生产线投产,当年产量达到45万吨。
本文以阿维迪ESP线为例,简要介绍带钢无头连铸连轧的工艺特点及技术优势。
一、ESP工艺流程及主要特点(一)ESP工艺流程介绍阿维迪ESP生产线如图1所示,该项技术是在德马克公司的ISP技术基础上开发的,其生产线中的连铸机采用平行板式直—弧形结晶器,铸坯导向采用铸轧结构,经液芯压下铸坯直接进入初轧机轧制成中厚板,而后经剪切可下线出售,不下线的板坯经感应加热后, 进入五架精轧机轧制成薄带钢,经冷却后卷曲成带卷。
ESP工艺生产线布置紧凑,不使用长的加热炉或克雷莫纳炉,生产线全长仅190m,是世界上最短的连铸连轧生产线。
ii tt UH 电tt BMr MH 泳冷"口谅、勇矗*图1.意大利阿维迪ESP生产线示意图(二)ESP工艺的主要技术特点1 .较高的浇铸速度。
棒线材MI.DA.无头轧制技术介绍

棒线材MI.DA.无头轧制技术介绍赵辉1,2①(1:北京首钢国际工程技术有限公司 北京100043;2:北京市冶金三维仿真设计工程技术研究中心 北京100043)摘 要 本文主要介绍MI.DA.无头轧制技术以及国内应用现状。
以山西建邦MI.DA.生产线为例,详细介绍了MI.DA.无头轧制的生产工艺和装备,总结了MI.DA.无头轧制技术的优缺点,为今后国内新建类似项目给出建议。
关键词 无头轧制 棒材 线材 MI.DA.中图法分类号 TG333 TG335.1 文献标识码 BDoi:10 3969/j issn 1001-1269 2023 06 025IntroductiontoMI.DA.HeadlessRollingTechnologyofBarandWireZhaoHui1,2(1:BeijingShougangInternationalEngineeringTechnologyCo.,Ltd.,Beijing100043;2:MetallurgicalEngineering3-DSimulationDesignEngineeringTechnologyResearchCenterofBeijing,Beijing100043)ABSTRACT MI.DA.headlessrollingtechnologyanditsdomesticapplicationstatusareintroduced.TakingShanxiJianbangMI.DAproductionlineasanexample,theproductionprocessandequipmentofMI.DAheadlessrollingareintroducedindetail,theadvantagesanddisdvantagesofMI.DAheadlessrollingtechnologyaresummarized,andsuggestionsaregivenfornewsimilarprojectsinChinainthefuture.KEYWORDS Headlessrolling Rod Wire MI.DA.1 前言节能降本一直是我国钢铁企业追求的目标,如何在保证产量的同时,降低生产成本,无头轧制工艺是一个很好的选择。
轧钢生产中新工艺新技术的应用探究

轧钢生产中新工艺新技术的应用探究摘要:我国社会发展迅速,推动了钢铁生产行业的发展,生产工艺越来越先进。
轧钢技术以及产品性能也有较大程度提升。
轧钢生产对于社会经济发展具有直接影响。
本文对于轧钢生产环节新技术和工艺的发展现状做出阐述,并对其在加工生产环节实践应用深度剖析。
关键词:轧钢生产;新工艺;技术应用引言:在社会各领域的发展过程,需要消耗大量钢材,对于轧钢生产品质以及技术应用要求更高。
以往轧钢生产工艺及技术的应用,生产出产品可能和现实需求不相符。
因此,需要结合市场需求,探索轧钢生产全新工艺和技术的应用思路,不断提高轧钢品质,提高生产企业核心竞争力。
一、轧钢生产期间设备和工艺的发展(一)设备方面我国轧钢生产设备的应用方面主要有如下几种:第一,热轧生产线,能够实现连续生产,并且生产过程节能性良好,生产流程紧凑,能够保证连铸、轧钢各工序无缝衔接。
第二,集成宽厚板的轧制生产线,需要使用国内外联合设计生产工艺,引进国外设备,才能完成生产;第三,大型冷轧生产线,像酸洗冷轧就是其中之一,该生产线的运用,对于轧钢工艺以及生产技术多方面发展有直接影响。
(二)技术方面轧钢生产期间,新技术的应用包括节能均温炉,能够实现多元化生产棒线材,既可生产带肋钢筋,还能生产特殊的钢棒与线材,需要将生产期间环境温差考虑其中,确保铸钢环节和轧制工艺运用衔接顺利。
利用DROF生产线,能够有效缩短生产距离,并将产品向缓冲区送入,通过无坯之后,将产品放入轧制机器内,若此环节温度和要求不符,即可自动剔除,确保轧钢品质[1]。
二、轧钢生产中新工艺和新技术的应用(一)品质保证工艺1.TCMP技术在轧钢生产环节,PMCP技术的应用也称机械热控制,具体来讲即指对于金属的奥氏体转化全程加以控制,最终对于金属内部形态以及组织分布综合控制。
轧钢生产时,可按照钢材C曲线,对于温度和加热速率全面控制。
通过“炉、水、空”等不同冷却技术的不同速率控制,获得轧钢终组织。
首钢杯竞赛练习题-金属轧制工(13)

薄板坯连铸连轧无头轧制技术的应用

(TaxgsPax Quaxfeng Sheet Co. , Ltd. , TaxgsPax 063300, Hebei) Abstrcct: Endless rolling technology is avother leap of iron aod steei production technology , renresenting the cotting - enge technology of ho- rollen strin in the worlU, With the rayiO deveNpmen- of the thira generation thin slab continuous costing aod rolling technology characterized by enniess rolling technology , the deveNpment of endless rolling technology for ho- rollen plate chv further improv the yielU of plate aod strin , the acchrach of size aod shape aod the proportion of thin gaoge aod ultra - thin gaoge , reelize partial " heat instead of colU" aod renucc roll consumption. The proccss flow , production line characteristics aod product charac teristics of endless rolling technology are introduccn. Taping Rizhao ESP production line , Shougaog Jingtaog MCCR production line aod Taogshao aonual DSCCR production line as example , the aOvaoWpes aod disabvaoWpes of each production line are comparen. C view of the existing problems of endless rolling , the devetopment aod op/mizz/on direction are put forwara. Key words:thin slab; continuous chsting aod rolling; endless rolling; ESP; MCCR; DSCCR
我国高速线材述评

我国高速线材生产、装备、技术述评0.前言线材是钢铁工业的重要产品之一,它广泛用于各项基础设施建设、建筑工程建设和金属制品行业。
从线材轧机的发展历史来看,20世纪60年代以前,轧制速度达到40m/s之后就很难再提高了。
但是人们追求更为高效的生产工艺以提高轧制速度和成品精度的目标却一直没有停止。
在这一思想的指导下,1966年世界上第一台由美国摩根公司研制成功的高速线材轧机正式生产,给线材生产领域带来了革命性的变化,揭开了高速线材工业化生产的序幕。
我国1987年开始生产高速线材,受消费结构不断升级的影响和消费市场强劲拉动的作用,生产线越建越多,产量快速增长,呈现了在装备上追求高速、单线、无扭、微张力组合,在产品上追求高精度、高品质、大盘重等特点。
目前,我国已成为世界上拥有高速线材生产线最多、产量最大的国家,2003年全国线材总产量4007万t,其中高速线材2704.75万t,占67.5%;2004年线材总产量4940.98万t,其中高速线材预计将占75%左右。
1.概况1)至2004年底,我国已有60个高速线材生产厂共77条生产线在生产。
主要设备靠引进的有32条;引进二手设备的有17条;我国自己设计制造的有28条。
这77条生产线中,20世纪80年代建成的有20条;20世纪90年代建成的有36条;21世纪初建成的有21条。
2)按地域划分,东北地区有8条;华北地区有19条;华东地区有28条;中南地区有13条;西南地区有8条;西北地区有3条。
按省市划分,河北省的高线产量最高,2004年产量约占全国高线产量的22%,其次为江苏省、上海市。
沙钢是我国目拥有高速线材生产线最多(4条)产量最高(年260万t)的生产企业。
3)1987年我国高速线材产量实现了零的突破,当年产量为36.06万t。
2004年产量约为3 705万t,18年间高线产量增长了100倍左右。
从1997年开始,我国高速线材产量快速增长,每年平均递增量超过200万t。
无头轧制技术在邢钢二高线厂的应用
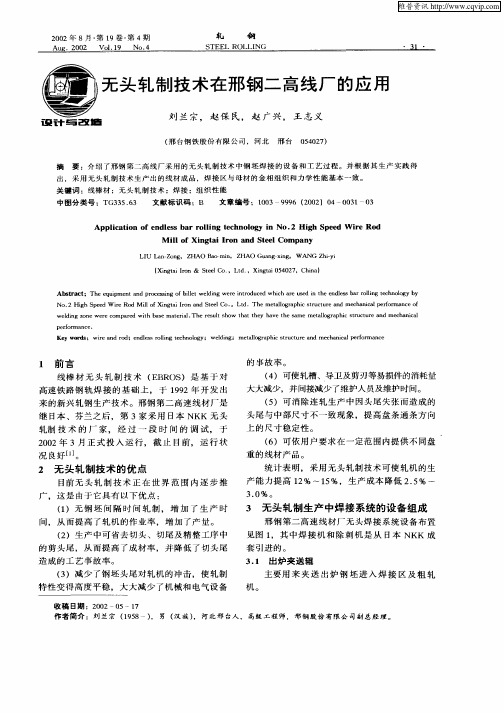
( n ti rn & Se l o ,L d ,X n ti 5 0 7 Xi a Io g te C . t . ig a 0 4 2 ,Chn ) ia
重 的线 材 产 品。
20 0 2年 3月 正 式 投 入 运 行 , 截 止 目前 ,运 行 状
况 良好 … 。
2 无 头 轧 制 技 术 的 优 点
目前 无 头 轧 制 技 术 正 在 世 界 范 围 内逐 步 推
广 .这 是 由于 它 具有 以下优 点 :
统 计表 明, 采用 无 头 轧制 技术 可 使 轧机 的 生
Ab t a t s r c :Th q im e ta d p o e sng o i e l i g we e i to u e i h a e u e n t e e d e s b r r l n e h o o y e e u p n n r c s i fb l t we d n r n r d c d wh c r s d i h n ls a o l g t c n lgy b l i
No. g p e ie Ro i fXi g a r n a d S e l . Lt 2 Hi h S e d W r d M l o n t iI n t l o o C 。 d.Th t l g a hc s r c u e a d me h ia e f r n e o e me al r p i tu t r c a c lp ro ma c f o n n
的 事故 率 。 ( )可使轧槽 、导卫及剪 刃等易损件的消耗量 4 大大减少 ,并间接减少了维护人 员及维护 时间。 ( )可 消除 连 轧 生产 中 因头 尾失 张 而造 成 的 5
无头-半无头轧制技术-康永林-2010[1].11.23
![无头-半无头轧制技术-康永林-2010[1].11.23](https://img.taocdn.com/s3/m/c67c046858fafab069dc026d.png)
的尺寸和板形不良或非稳定轧制引起的质量不良.
9
提高生产率
各板坯连接处的穿带速度可达1000m/min以上,另外,单块坯 轧制中的间歇时间在无头轧制中减为零,由此可显著提高薄 规格轧制效率。
可生产薄
而宽的钢 板和超薄 规格板
10
通过润滑轧制和强制冷却轧制生产新品种
当第一块板坯的头部通过精轧机组后,直到最 后部分板带通过机组的较长时间内都可实现 稳定润滑,因此,在能进行稳定润滑的同时 又可减少材料损耗1/6~1/10 。 在无头轧制时,由于可以对精轧出口处的板带 施加张力,即使采用快速冷却,不存在穿带 和冷却不均问题,由此可得到全长均匀的材 质。
定位
感应加热
对接
连接完成
去毛刺
17
感 应加热连接设备
加热装置
线圈 磁芯
夹持·压接 运行方向
感应电流
压接
升降装置
压接
18
控制磁通
升温速度比率
无控制
连接区边界
材质:SUS 304 尺寸:30t×800w mm
(中心) 宽向距离 (mm)
感应加热铸坯连接的温度分布比率
19
感应加热连接区表面状态及断面组织
7
生 产 率 问 题:
♦精轧生产率最低的是薄规格轧制 ♦单位宽度的轧制量即质量流量不大,所以产量不高 ♦为了提高产量,使稳定轧制速度基本达到其上限约
1500m/min的饱和状态
♦穿带速度提高后,由于穿带问题和头部折迭等引起
的故障率增多,穿带速度的上限约在800m/min左 右,薄规格轧制的生产率基本达到极限状态
无头轧制的中间坯连接技术
叠轧 咬合轧制 铝热焊 锯齿形 机械连接 还原性 火焰处理 直接通电连 接 感应加热 连接 激光连接
轧制概述与工艺

本课程讲授的主要内容: ●轧制概述 ●轧制过程中的力学概述
●轧制过程中的金属变形
●轧制后续的处理技术及设备概述
2
轧制概述
1.轧制概述 2.我国轧钢技术发展 3.无头轧制技术 4.今后我国轧钢领域的发展方向
3
绪论
轧制过程是由轧件与轧辊之间的摩擦力将轧件拉 进不同旋转方向的轧辊之间使之产生塑性变形的过程。
轧制新技术新工艺概述
新一代TMCP技术 无头轧制技术
边部温度控制技术 连铸坯热送热装 无酸洗除鳞技术 板厚、板形自动控制系统 轧制-激光焊接技术
宽厚板轧制
● ● ● ● -
热连轧
● ● ● ● ● -
38
冷轧 棒线材轧制
-
●
-
●
-
-
-
●
●
-
●
-
●
-
39
4.今后我国轧钢领域的发展方向 轧钢领域要向提高热装温度和热装率,开
——咬入角,轧件被咬入轧辊时轧件和轧辊最先
接触点(实际上为一条线)和轧辊中心的连线与 两轧辊中心连线所构成的角度;
l——接触弧长的水平投影,也叫变形区长度;
F ——接触面水平投影面积,简称接触面积;
l/hm ——变形区形状参数,hm=(H+h)/2(变形
区平均高度)。
简单轧制(理想轧制)
为了便于进行研究分析,对一些轧制条件作出假设和
4
金属材料尤其是钢铁材料的塑性加工,90%以上是通过 轧制完成的。由此可见,轧制工程技术在冶金工业及国民 经济生产中占有十分重要的地位。
5
轧制工艺按照产品类型可以分为板带轧制、管材轧 制、型材轧制以及棒、线材轧制四种基本类型;按生 产工艺可以分为热轧和冷轧工艺;按厚度可分为薄板 ( 厚 度 <4mm) 、 中 板 ( 厚 度 4~20mm) 、 厚 板 ( 厚 度 20~60mm)、特厚板(厚度>60mm,最厚达700mm)。 在实际工作中,中板和厚板通称为“中厚板”。
EWR无头焊接轧制工艺简介

EWR无头焊接轧制工艺简介收藏此信息打印该信息添加:用户投稿来源:未知EWR无头焊接轧制工艺是由达涅利集团开发的革新技术。
该工艺可实现加热炉出口侧小方坯的连续自动化在线焊接过程,从而达到后序轧机的无间断生产,EWR工艺具有如下几方面优势:——增加产能以及设备利用率;——材料收得率高达99%;——降低生产成本(平均:3.5~4.5欧元/t);——改善生产计划,且易于工厂管理。
之所以产生如上优势,主要源于以下几点原因:——取消小方坯之间的间隔时间;——轧制过程中棒材无头尾剪切;——无短尺棒材/短尺头尾;——线材生产过程中无盘卷的修整;——减少堆钢的发生次数;——降低了对维修、备用件以及易耗品的要求。
EWR工艺既可用于新建设备,又可用于对现有设备进行改造;既可用于生产普通钢种,又可用于生产特殊钢种。
对于特殊布置或者空间受到限制的厂房可提供专用的解决方案。
全球EWR设备前两套EWR设备已于1999年在马来西亚SSB和泰国BSI棒材厂投产运行。
目前,该套设备已向全球供应7套,即:——Deacero Celaya棒线材厂(墨西哥),这是北美首条EWR生产线;——唐山钢铁公司棒材厂,这是中国首条EWR生产线;——法国ALPA棒材厂,这是欧洲首条运行的EWR生产线;——涟源钢铁公司,这是中国投产运行的又二条EWR生产线;——中国新疆八一钢铁公司,这是世界首条无头轧制特殊钢线材生产线。
另一条EWR生产线将于2002年夏在希腊哈利沃尔加公司棒材厂投产运行。
EWR工艺描述焊接过程开始于小方坯加热炉出口处。
出加热炉的小方坯首先进行除鳞,而后其前端与已经在粗轧机中轧制的小方坯的尾端实施闪光对焊过程。
运动式焊接头周期从静止位置开始算起,然后其加速直至达到与小方坯相同的速度。
随后其通过与第一机架轧制速度相匹配的速度运动着的两个夹紧装置将后一小方坯的头部锁定到前一小方坯的尾部,而后起动闪光对焊机开始焊接。
一专利系统可实现夹紧小方坯的自动对中,使夹具和小方坯四个面完全接触,从而获得更为均匀的焊接电流。
轧钢棒线材生产技术创新研究

轧钢棒线材生产技术创新研究【摘要】钢铁工业的飞速发展,为用户提供了充足的钢铁产品,使得国内钢材市场逐渐由卖方市场向买方市场过渡。
为了提高市场竞争能力,必须在提高产品质量的同时,降低生产成本,加大企业技术进步,大胆应用近年来出现的新技术、新设备、新工艺,这无疑是增强其竞争能力的有效手段。
棒线材生产已有 200 多年的历史。
尽管板带钢产品比重迅速增加,其生产技术日趋完善,生产成本显著下降,但是棒线材产品仍然占据其独有而不可取代的地位。
正是由于这个原因,其生产技术发展水平正日新月异地飞速发展。
本文主要针对轧钢棒线材生产技术问题进行分析和讨论,望与同行之间交流探讨。
关键词:钢材生产;轧钢技術;棒线材;新技术1轧钢棒线材市场现状目前我国棒线管材行业企业的技术装备水平得到较大提高,特别是二十世纪九十年代以来,我国钢铁工业获得了长足进步:新建的一大批具有世界先进水平的大型高炉、大型转炉和电炉、炉外精炼、连铸、热连轧、冷连轧、涂镀层生产线、冷轧硅钢生产线、高速线材轧机、连续小型棒材轧机的建成投产等,使我国棒线材管行业的装备水平有了显著提高。
特别是我们正在进行的为配合我国家电、轿车、石油、建筑、造船等行业走向世界,钢铁行业“十五”技术改造完成后,再经过“十一五”的努力,我国整个棒线材管工业的工艺和装备水平将会发生新的质的飞跃。
2轧钢棒线材生产工艺概述我国钢铁行业“量喜质忧”现状,表明了相对炼铁和炼钢技术而言,现有的轧钢技术发展相对落后。
因此,加强轧钢技术研究和轧钢专用设备研发,对提升我国钢材整体质量乃至推动钢铁工业进步具有十分重要的意义。
轧钢技术环节,轧钢技术水平和特点主要体现在提高产品质量及附加值、提高生产效率、扩大产品品种、降低成本、节能降耗和环保等方面,以满足下游领域对钢材质量的严格要求。
因此,轧钢技术水平和装备等级是钢铁企业提高产品质量和降低能耗的一个重要环节。
第一,有利于提高钢材质量。
通过精确设计和提高轧机导卫装置装备水平能最大限度解决现有钢材产品在外形、尺寸(直径)等方面存在的问题;通过测径、测温、智能控制轧制系统的研发和装备投入能够大幅降低现有钢材产品在尺寸、面瑕疵方面存在的问题。
无头轧制技术

无头轧制无头轧制技术是指将粗轧后的带坯在中间辊道上焊合起来,并连续不断地通过精轧机的一种技术。
传统的板带热连轧精轧机组生产均以单块中间坯进行轧制,因此,不可避免地要经过进精轧机组时的穿带、加速轧制、减速轧制、抛钢、甩尾等一系列过程。
由此发生的尺寸公差和力学性能的不均匀性很难在原有工艺框架内得到解决。
热轧带无头轧制新技术正是解决这些问题的一项重要的技术突破。
在传统热连轧中,板坯是在精轧机中一块一块地轧制的,带钢的头部在出了精轧机到卷取机之前的这段长度上以及尾部出精轧机后的这段长度上处于无张力的状态,造成每一卷带钢的头尾部分尺寸公差和板形难以保证。
同时,单块坯轧制时因尾部无张力,故在精轧机架间常发生甩尾形成2~3层折迭咬入,从而产生轧辊表面裂纹和压痕伤。
而无头轧制是将大约10块带坯在出粗轧机后的中间辊道上头尾焊合在一起,接着进入精轧机中连续轧制,带坯在恒张力下轧制,因此几何精度和板形不良的比例大幅度下降。
无头轧制因穿带和抛尾的减少,可以做到稳定的润滑轧制。
与此同时,稳定的润滑轧制可使轧制力降低,因而可在较低温度下进行轧制,生产出具有良好深冲性能的带钢,并可降低能源消耗。
应用无头轧制法主要应用在型材、盘条和带材的连续轧制生产上。
优点是:(1)可大幅度提高盘条的盘重和轧机产量。
由于消除了每根轧件在各机架咬入瞬间引起的动态降速,连轧过程稳定,张力波动减小,从而为进一步提高轧制速度创造了条件;由于消除了两根相邻轧件之间的间隙时间,轧机利用率显著提高,除换辊和检修外,连续轧制时间可达几个昼夜,轧机作业率可达90%以上,生产能力提高10%~12%;盘条的盘重可根据要求用飞剪任意调节;(2)消除了咬入时因堆拉钢造成的断面尺寸超差和中间轧废,并大量减少切头、切尾的金属消耗,从而使金属收得率提高3%以上,产品质量也得以提高。
当采用钢坯首尾对焊法连续供坯时,焊缝质量良好,各项性能指标与母材基本一致;(3)减少了温度较低的轧件头、尾部分对轧辊和导卫装置的频繁冲击,减少了轧辊磨损,有利于轧机及其传动装置的平稳运转;(4)在实现连续酸洗、动态变规格轧制、连续退火和精整的带钢全连续化冷轧生产线上,为生产高品质、低消耗、多规格的带钢创造了条件(见冷轧板带生产);(5)连续稳定的轧制给整个生产过程的自动控制创造了有利条件。
无头轧制和半无头轧制技术简析

无头轧制和半无头轧制技术是近年来出现的新技术。
无头轧制主要应用在热轧带钢和棒线材生产中,半无头轧制主要应用在薄板坯连铸连轧生产中。
采用传统分块轧制方式的轧机要频繁的咬钢、抛钢和变换轧制速度,造成钢材头、尾部的质量难以保证,轧机作业率较低,对产品尺寸精度的控制也较为困难。
对此,有关科技工作者通过在传统的热轧生产线上设置钢坯对焊机实现精轧连续轧制。
该方法与传统轧制方法相比,成材率可提高0.5%至1.0%;生产率可提高10%至15%;产品质量、精度也有较大进步。
此外,用传统的轧制方法轧薄板时容易出现跑偏、甩尾、浪形等问题,而无头轧制则无此现象,可改善钢带行走的稳定性,可生产0.8-1.0mm带材。
最后,由于避免频繁的咬钢,设备的磨损和废品率也有所下降,可降低2.5%-3%的生产成本。
第一台全连续无头轧制热连轧带钢机是1996年在日本JFE公司千叶厂投用的。
它的轧机组成是:3架粗轧机,7 架精轧机,辊身长2030mm,设计最高轧速为25m/s,年产能力为540万t。
在千叶厂3号轧机全连续无头轧制取得成功经验后,日本新日铁和韩国浦项分别将其大分厂和光阳厂热连轧带钢机改造成能无头轧制的全连续热轧带钢机。
半无头轧制主要用于薄板坯连铸连轧生产线,主要是为生产薄规格热轧带钢设计的,固然其设备配置与传统的薄板坯连铸连轧大体相同,但是技术有很大变化。
比如,采用半无头轧制的CSP生产线,薄板坯出结晶器时的厚度为63mm,经过液芯压下后离开连轧机时连铸坯厚度为48mm。
此时,连铸坯不间断进入隧道式加热炉(传统CSP生产线连铸坯剪断为40多米),加热炉可达300多米(传统CSP生产线为200m);连铸坯均热后进入7机架连轧机组轧制成材。
该生产线的输出冷却辊道分为两段,第一段较短,为30m左右,其中快速冷却水集管为10m左右,冷却段后是超薄带卷取机;第二段为传统的层流冷却和传统的卷取机,主要生产一般规格的热带。
为对生产的成品带钢进行分卷,在每个卷取机前均设有高速飞剪。
棒线材无头焊接轧制设备及其经济效益
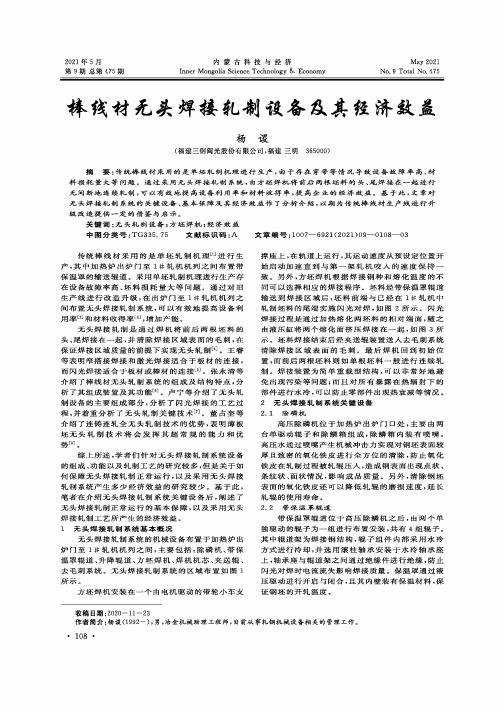
2021年5月第9期总第475期内蒙古科技与经济Inner Mongolia Science Technology&EconomyMay2021No.9Total No.475棒钱材无块焊接孔制殺备m济数蠡杨谡(福建三钢闽光股份有限公司,福建三明365000)摘要:传统棒线材采用的是单坯轧制机理进行生产,由于存在穿带等情况导致设备故障率高、材料损耗量大等问题。
通过采用无头焊接轧制系统,由方坯焊机将前后两根坯料的头、尾焊接在一起进行无间断地连续轧制,可以有效地提高设备利用率和材料收得率,提高企业的经济效益。
基于此,丈章对无头焊接轧制系统的关键设备、基本保障及其经济效益作了分析介绍,以期为传统棒线材生产线进行升级改造提供一定的借鉴与启示。
关键词:无头轧制设备;方坯焊机;经济效益中图分类号:TG335.75文献标识码:A文章编号:1007—6921(2021)09—0108—03传统棒线材采用的是单坯轧制机理E进行生产,其中加热炉出炉门至丄拌轧机机列之间布置带保温罩的输送辐道。
采用单坯轧制机理进行生产存在设备故障率高、坯料损耗量大等问题。
通过对旧生产线进行改造升级,在出炉门至1#轧机机列之间布置无头焊接轧制系统,可以有效地提高设备利用率⑵和材料收得率⑶,增加产能。
无头焊接轧制是通过焊机将前后两根坯料的头、尾焊接在一起,并清除焊接区域表面的毛刺,在保证焊接区域质量的前提下实现无头轧制⑷。
王睿等表明窄搭接焊接和激光焊接适合于板材的连接,而闪光焊接适合于板材或棒材的连接页。
张永清等介绍了棒线材无头轧制系统的组成及结构特点,分析了其组成装置及其功能旳。
卢宁等介绍了无头轧制设备的主要组成部分,分析了闪光焊接的工艺过程,并着重分析了无头轧制关键技术血。
董占奎等介绍了连铸连轧全无头轧制技术的优势,表明薄板坯无头轧制技术将会发挥其超常规的能力和优势凶。
综上所述,学者们针对无头焊接轧制系统设备的组成、功能以及轧制工艺的研究较多,但是关于如何保障无头焊接轧制正常运行,以及采用无头焊接轧制系统产生多少经济效益的研究较少。
线棒材无头轧制技术72
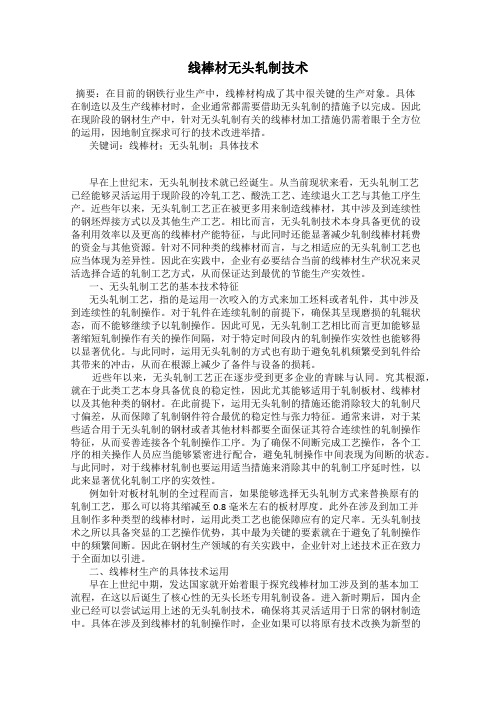
线棒材无头轧制技术摘要:在目前的钢铁行业生产中,线棒材构成了其中很关键的生产对象。
具体在制造以及生产线棒材时,企业通常都需要借助无头轧制的措施予以完成。
因此在现阶段的钢材生产中,针对无头轧制有关的线棒材加工措施仍需着眼于全方位的运用,因地制宜探求可行的技术改进举措。
关键词:线棒材;无头轧制;具体技术早在上世纪末,无头轧制技术就已经诞生。
从当前现状来看,无头轧制工艺已经能够灵活运用于现阶段的冷轧工艺、酸洗工艺、连续退火工艺与其他工序生产。
近些年以来,无头轧制工艺正在被更多用来制造线棒材,其中涉及到连续性的钢坯焊接方式以及其他生产工艺。
相比而言,无头轧制技术本身具备更优的设备利用效率以及更高的线棒材产能特征,与此同时还能显著减少轧制线棒材耗费的资金与其他资源。
针对不同种类的线棒材而言,与之相适应的无头轧制工艺也应当体现为差异性。
因此在实践中,企业有必要结合当前的线棒材生产状况来灵活选择合适的轧制工艺方式,从而保证达到最优的节能生产实效性。
一、无头轧制工艺的基本技术特征无头轧制工艺,指的是运用一次咬入的方式来加工坯料或者轧件,其中涉及到连续性的轧制操作。
对于轧件在连续轧制的前提下,确保其呈现磨损的轧辊状态,而不能够继续予以轧制操作。
因此可见,无头轧制工艺相比而言更加能够显著缩短轧制操作有关的操作间隔,对于特定时间段内的轧制操作实效性也能够得以显著优化。
与此同时,运用无头轧制的方式也有助于避免轧机频繁受到轧件给其带来的冲击,从而在根源上减少了备件与设备的损耗。
近些年以来,无头轧制工艺正在逐步受到更多企业的青睐与认同。
究其根源,就在于此类工艺本身具备优良的稳定性,因此尤其能够适用于轧制板材、线棒材以及其他种类的钢材。
在此前提下,运用无头轧制的措施还能消除较大的轧制尺寸偏差,从而保障了轧制钢件符合最优的稳定性与张力特征。
通常来讲,对于某些适合用于无头轧制的钢材或者其他材料都要全面保证其符合连续性的轧制操作特征,从而妥善连接各个轧制操作工序。
轧钢棒材生产线的PLC控制系统

轧钢棒材生产线的PLC控制系统在自动化操纵领域,PLC是一种重要的操纵设备。
目前,世界上有200多厂家生产300多品种PLC产品,应用在汽车(23%),粮食加工(16.4%)、化学/制药(14.6%)、金属/矿山(11.5%)、纸浆/造纸(11.3%)等行业。
上世纪80年代至90年代中期,是PLC进展最快的时期,年增长率一直保持为30%—40%。
在那个时期,PLC在处理模拟量能力、数字运算能力、人机接口能力和网络能力得到大幅度提高,PLC逐步进入过程操纵领域,而且在某些应用上取代了在过程操纵领域处于统治地位的DCS系统。
现今,PLC差不多具有通用性强、使用方便、适应面广、可靠性高、抗干扰能力强,编程简单等特点。
在可预见的今后,PLC 在工业自动化操纵专门是顺序操纵中的主导地位,是其他操纵技术无法取代的。
本文介绍了S7-200 PLC操纵系统在轧钢棒材生产中系统中的应用,着重描述了系统配置及冷床操纵功能。
最后通过,通过测试和实验的成功说明本文研究成果的可行性和可靠性。
关键词:PLC操纵系统;轧钢;棒材生产;冷床顺序操纵;ABSTRACTIn the area of Automation Control,Programmable Logic Controller is an important control equipment.Currently,there are over 200 manufacturers that produce more than 300 varieties of PLC products,which are now applied in auto industry(23%),grain processing(16.4%),chemical&pharmacy(14.6%),metals&mine(11.5%),paper pulp and paper making(11.3%) and many other industries.The PLC develop fastest during the 1980s and the mid-1990s,the value of gross output of PLC increase at the speed of 30%-40% per year.In this period,the PLC technology has developed rapidly in the field of analogy processing,digital quantity operation,man-machine interface,network service,gradually the PLC entered the field of process control because of these,and in some fields the PLC has token the place of Distributed Control System-the once king in the field of process control.And now,the PLC has been equipped with good commonality,ease of use,wide applicability,high reliability,good anti-interference,easy programmability and some other advantages.In the foreseeable future,the PLC will dominate the industrial automation and control,especially Sequence Control,and it can't be replaced by other control technologies.This article will introduce how s7-200 PLC system works in rolling steel bar production,and it focus on describing System Configuration and cooling bed stly,tests and experiments show that the research results this article describes are practical and reliable.Key words:PLC control system; steel rolling; bar production;sequence control of the cooling bed;目录第一章绪论 01.1 课题研究背景和意义 01.2 国内外进展状况与进展趋势 (2)第二章可编程操纵器简介 (9)2.1 可编程操纵器的进展历史 (9)2.2 PLC的特点 (10)2.3 PLC的工作原理 (11)2.4 PLC的体系结构 (12)2.5 PLC操纵程序设计 (15)第三章轧钢棒材生产线冷床操纵系统的硬件设计部分 (17)3.1 硬件组成及操纵要求 (17)3.2 PLC输入、输出的安排 (19)第四章系统软件设计部分 (25)4.1 系统流程设计图 (25)4.2 顺序功能图 (25)4.3 PLC程序 (26)第五章结论 (32)致谢 (33)参考文献 (34)第一章绪论钢棒材是经济建设中必不可少的一种材料,钢棒材品种繁多,广泛应用于汽车制造、电气机械、船舶制造工业、大跨度桥梁、高层建筑等社会生活各个方面。
- 1、下载文档前请自行甄别文档内容的完整性,平台不提供额外的编辑、内容补充、找答案等附加服务。
- 2、"仅部分预览"的文档,不可在线预览部分如存在完整性等问题,可反馈申请退款(可完整预览的文档不适用该条件!)。
- 3、如文档侵犯您的权益,请联系客服反馈,我们会尽快为您处理(人工客服工作时间:9:00-18:30)。
无头轧制生产线的基本构架
传统的板带热轧工艺难以保证带钢头尾厚差和穿带质量均匀性,轧制作业率、成材率也受到限制。为解决这些问题,上世纪末出现了无头轧制新工艺,显示出许多传统热带轧制无可比拟的优越性,现在已经在极薄热轧带钢、高品质高强度钢板和不锈钢板新产品生产方面显示出巨大的应用前景,成为热轧技术的发展方向。该技术由川崎制铁千叶厂3号热带轧机首先实现,以后逐渐得到推广。该生产线由以下几部分构成:
1.铸轧型无头轧制技术。
意大利达涅利公司开发成功该项技术并用于意大利乌迪内ABS公司的年产50万t特殊钢棒线材工业性生产厂中,已于2000年8月正式投产。
连铸机和热连轧机配置在一条生产线上,铸机产品为160mm×200mm大方坯,共两流。连铸机后设有两个淬火箱,其后为125m长辊底式加热炉,加热炉前设有65m长双流隧道式炉以作为工序间缓冲,热缓冲能力约为45t。
2003年1月,ABS公司对其Luna生产线上在线退火装置进行改造,将炉室长度增加一倍,可处理长50m轧材,原退火炉只能处理长24m轧材,严重制约整条生产线能力的发挥。
2.连铸坯焊接型无头轧制技术。
该技术是连铸方坯经步进式加热炉加热后将前一块钢坯尾部和后一块钢坯头部进行对焊(用闪光焊接),形成无头坯送热连轧机进行轧制,名为EWR(Endlees Welding Rolling)。自从1998年3月在日本东京高松厂问世以来有了快速的发展,闪光焊机设在加热炉出料端后,焊接过程由计算机控制,并纳入轧钢自动化系统,因而有良好的焊接过程稳定性和可重复性,各种断面形状和钢种的钢坯均能对焊,最大规格可达200x200mm。我国唐山钢铁公司棒材厂建设的EWR装置对焊165mm方坯所需周期约37-40秒,其中焊接时间约10秒。由于焊接技术的提高,焊口位置不但不存在内部缺陷,强度指标也不亚于轧件母体。
无头轧制技术是指将粗轧后的带坯在中间辊道上焊合起来,并连续不断地通过精轧机的一种技术。 传统的板带热连轧精轧机组生产均以单块中间坯进行轧制,因此,不可避免地要经过进精轧机组时的穿带、加速轧制、减速轧制、抛钢、甩尾等一系列过程。由此发生的尺寸公差和力学性能的不均匀性很难在原有工艺框架内得到解决。热轧带无头轧制新技术正是解决这些问题的一项重要的技术突破。在传统热连轧中,板坯是在精轧机中一块一块地轧制的,带钢的头部在出了精轧机到卷取机之前的这段长度上以及尾部出精轧机后的这段长度上处于无张力的状态,造成每一卷带钢的头尾部分尺寸公差和板形难以保证。同时,单块坯轧制时因尾部无张力,故在精轧机架间常发生甩尾形成2~3层折迭咬入,从而产生轧辊表面裂纹和压痕伤。而无头轧制是将大约10块带坯在出粗轧机后的中间辊道上头尾焊合在一起,接着进入精轧机中连续轧制,带坯在恒张力下轧制,因此几何精度和板形不良的比例大幅度下降。无头轧制因穿带和抛尾的减少,可以做到稳定的润滑轧制。与此同时,稳定的润滑轧制可使轧制力降低,因而可在较低温度下进行轧制,生产出具有良好深冲性能的带钢,并可降低能源消耗。
棒线材无头轧制技术有三种类型:一是铸轧型无头轧制技术。将方坯连铸机和热连轧机结合在一条生产线上连铸连轧棒线材的新工艺称为Luna无头铸轧技术。二是连铸坯焊接型无头轧制技术。将在步进炉加热好的钢坯进行焊接,成为无头坯送往轧机进行轧制。三是中间坯焊接型无头轧制技术。将经粗轧机架轧制后的中间坯(由45mm左右)进行焊接,在中轧、精轧机中可提高12%-16%,生产成本降低2.5%-3.0%,棒材定尺率接近100%,金属收得率提高约l%,从轧件品质分析,因为仅有一个头部,所以能明显减少轧制纵向尺寸和性能不均现象。
除新建轧机外,在现有现代化连续棒材轧机上可以新增无头轧制装置,如唐钢棒材厂即属于改造项目,总投资210万美元。
3.中间坯焊接型无头轧制技术。
该项技术系将经粗轧机架轧成的中间坯头尾焊接后送中轧、精轧机轧制,类似传统热轧带钢机装设的无头轧制装置。新工艺由日本大和钢公司在其所属东部事业所开发成功。作业时间共30-70秒,其中焊接时间5.5秒,中间坯断面φ45mm,长36m。
该技术开发成功,使东部事业所轧制能力提高约20%,冷坯发生率减少,热坯使用率由75%增到9l%,燃料消耗减少,成材率有较大提高。
(3)卷取箱:为了避免焊接时后续带坯的到达出现误差,设置了将中间坯卷成卷状的卷取箱,作为焊接前的缓冲设备。卷取箱具有卷取、缓冲、开卷三个卷位,并带有两套开卷器,可弥补粗、精轧的轧制时间差。
(4)带坯焊接机:中间坯的头尾对焊是保证无头轧制成功的关键环节,要求对焊时间短,焊缝与母材的冶金组织和性能接近。千叶厂用电磁感应对接焊合法连接带坯。焊机在一个20米长的辊道上运动。当切好头尾的带坯进入焊机后,焊机首先在两块带坯的接合处上方定好位,并以与带坯相同的速度运行,然后夹具夹住带坯的头尾,并使带坯的头尾之间仅有几个毫米的间隙。此时2500kW的电感应加热器启动,加热两个带坯的端部,在3~5秒内使带坯端部温度急升到约1600℃,然后对压装置对接两端。在端部完全焊合后,夹具打开,带坯继续向前进入去毛刺机,同时焊合机返回到入口侧的起始位置以焊接下一块带坯。在焊接装置的后面布置有一台带有特殊刀头的旋转式去毛刺机,专门去除焊接处的隆起部位。
无头轧制技术的发展及展望
上世纪60年代以前,传统生产钢材方法是先将钢水模铸成大型钢锭,经加热、轧制成坯,钢坯经冷却、清整后再加热,轧成用户所需断面的成品钢材。近40多年来经历了三次飞跃式发展:一是将模铸改为连铸,取消开坯机;二是由一般连铸改为近终形连铸,减少加热、轧制次数;无头轧制技术是钢铁加工流程的第三次飞跃,即钢材生产不再是单块的、间隙性的,而是连续进行轧制,然后根据用户需求剪切成所需长度或卷重。无头轧制的好处是:
从技术上来讲,Luna无头铸轧技术给长材轧制工艺带来了一场革命性变化,它实现了从连铸、连轧、在线热处理、表面精整到在线检查的全连续化;全部工序都实现了计算机控制,从订单下达到成品入库全部生产过程不超过4小时。ABS公司吨钢材成本较常规技术减少约40美元。
工厂产品规格为圆钢Φ20-100mm,圆钢盘卷φ15-50mm和相应规格的方钢。钢种有碳素钢、表面硬化钢、低合金钢、调质钢、轴承钢、弹簧钢和不锈钢。
(1)加热炉:在无头轧制中,必须保证后续带坯与前一块带坯同时处于焊接装置处。为此,千叶厂装备了高能力的步进梁式加热炉,快速输出速度达每分钟2米,专用于高温板坯直接热装,保证后续带坯及时供应。
(2)粗轧机:无头轧制要求粗轧和精轧轧制时间必须互相匹配,因此要求粗轧机的轧制速度很高。千叶厂粗轧机的最大轧制速度可达每分钟340米。
5.和单块轧制不同,钢品啮入次数减少,减小对轧辊冲击,有利于提高轧辊寿命。
在施行无头轧制技术中分扁平材和长材两类,其中又有无头轧制和半无头轧制的区别;就技术类型来说分为焊接型和铸轧型两种,将分别叙述于后。
扁平材的无头轧制
1.在传统热连轧带钢机上无头轧制。
第一台全连续无头轧制热连轧带钢机是1996年在日本JFE公司千叶厂投用的。它的轧机组成是:粗轧机架3台,精轧机架7台,辊身长2030mm,设计最高轧速为25m/s,年产能力为540万t。连铸坯经加热在粗轧机架轧成最大厚度为50mm中间带坯进人热卷箱,在热卷箱后设有中间带坯剪断机,将带坯头剪平,以便于后面的焊接设备(用对接压合法电磁感应焊接)进行焊接,焊接后的带坯经过带坯边部加热器使带坯温度均匀,然后送入精轧机架轧成所需带钢厚度,由于中间带坯头尾已经焊接,从理论上来讲是可以无限长的,故称为无头轧制。轧机后卷取机前设有高速带钢剪断机,将高速前进的带钢(最大1200m/min)切断分卷。
生产线能以单流或双流生产,在单流生产时,连铸坯可以是14m以上的任意长度,在连铸和连轧两工序间不进行任何切割,实际上实现了半无头轧制。当双流生产时,连铸坯要切割成45m长交替送到隧道式炉中,然后送入辊底式加热炉加热和均热。
轧机由18架粗、中轧和预精轧机架及3架三辊RSB减定径机架组成,在精轧机前后装备有控温轧制所需的必要设施,包括在线热处理的淬火及回火(退火)设施。
我国华菱集团涟源钢铁公司新建薄板坯连铸连轧生产线即是按上述半无头轧制工艺设计建设的。由德国西马克·德马克公司供货,投产8个月后即成功创造世界同类型生产线半无头轧制268m长坯的最长纪录以及生产出厚度为0.78mm特薄热轧带卷,涟钢均热炉长291.15m,是目前世界上最长的均热炉。
棒、线材无头轧制
2.在棒线材无头轧制技术中,以连铸坯焊接型无头轧制应用最多,在泰国、马来西亚、墨西哥、西班牙等国若干长材生产厂都得到采用,我国第一家采用该技术的是唐山钢铁公司棒材厂,新疆八一钢铁公司和湖南涟源钢铁公司也采用了该项技术,但在实际生产中出现一些问题和要求,一是提供无缺陷连铸坯是应用此项技术的前提条件;二是钢坯对焊成功率主要取决于对接钢坯端面几何形状的一致性。目前一些钢厂对焊率不高主要是由于火焰切割的坯料端面不整齐和铸坯断面脱矩造成的,因此该项技术使用率不高,绝大部分仍采用常规轧制。但无头轧制优越性十分明显,连铸坯焊接型无头轧制新增设备不多,投资额不大,结构和操作不很复杂,具有进一步推广使用的前景。
在千叶厂3号轧机全连续无头轧制取得成功经验后,日本新日铁公司和韩国浦项公司分别将其大分厂和光阳厂热连轧带钢机改造成能无头轧制的全连续热轧带钢机。
由于中间带坯焊接操作过程比较复杂,对中间坯头尾可搭接性能要求较高,因而这项技术还没有在全球范围内迅速推广。据对千叶厂考察该轧机的情况介绍,由于市场原因,千叶3#热连轧带钢机实际年产量为300—350万t (设计年产能力540万t的55%-65%),采用无头轧制产品的月产量不足4万t。随着生产经验的积累和对新技术的掌握和改进,相信这项技术将会发挥更大的作用。
(5)精轧机:无头轧制工艺,要求精轧机不仅有足够的轧制力,而且必须有强有力的板凸度和板厚控制能力。千叶厂的7架精轧机均为PC轧机,后4架精轧机还设置了轧制中可调整交叉角度的机构,以确保有灵活的控制能力。另外,在精轧机出口侧配置了X射线测厚仪,以进行高精度的板厚控制。
(6)高速飞剪和卷取机:高速带钢飞剪位于卷取机前,可按照用户要求对带钢进行剪切分段。高速飞剪采用偏心轴结构,与带钢速度同步剪切,既能迅速切断高速运行的带钢,又不影响后续带钢的前进。生产线上布置有2台地下卷取机,采用液压夹送辊技术,可高速交替卷取带钢。