模具零件表面处理要求
模具表面处理种类与规格

抛光(Polish) 火花纹(Thin Fire Texture) 化学蚀纹(Texture)
蚀纹处理和模具斜度
电镀(Plating) 喷砂(Blasting)
抛光(Polish)
பைடு நூலகம்
SPI - Society of the Plastics Industry 塑料工业协会
Diamond Mold Polishing & Finishing Specifications
0.0508
0.0762 0.1143 0.0762 0.0762 0.0508 0.0889 0.1524 0.0635 0.0508 0.0635
MT-11140
MT-11150 MT-11160
0.0635
0.0698 0.1016
蚀纹处理和模具斜度的关系
Mold-Tech A Mold-Tech B
Ptn.# MT-11200 MT-11205 MT-11210 MT-11215 MT-11220 MT-11225 MT-11230 MT-11235 MT-11240 MT-11245 MT-11250 MT-11255 MT-11260 MT-11265 MT-11270 MT-11275 MT-11280
Plaque #7 Ptn.# Depth(mm) MT325 0.003 MT964 0.003 MT1038 0.002 MT1043 0.002 MT1170 0.0025 MT1192 0.0015 MT1239 0.003 MT1240 0.003 MT1241 0.002 MT1242 0.002 MT1243 0.002 MT1244 0.0025 MT1250 0.003 MT2019 0.0025 MT2020 0.002 MT2028 0.0025 23053 0.002 23064 0.0015
模具注塑表面处理工艺

模具注塑表面处理工艺一、引言模具注塑是一种常用的制造工艺,广泛应用于各行各业。
然而,模具注塑制品的表面质量直接影响着产品的美观度和功能性。
为了提高模具注塑制品的表面质量,必须进行适当的表面处理工艺。
本文将介绍常见的模具注塑表面处理工艺及其应用。
二、喷涂喷涂是一种常见的模具表面处理工艺,通过喷涂一层涂料或涂料膜,可以改善模具表面的光洁度和耐磨性。
喷涂可以分为手工喷涂和自动喷涂两种方式。
手工喷涂适用于小型模具,操作简单,但效果有限;自动喷涂适用于大型模具,可以实现高效、均匀的喷涂。
三、电镀电镀是一种常用的模具表面处理工艺,通过在模具表面镀上一层金属,可以提高模具的硬度、耐腐蚀性和耐磨性。
常见的电镀方法有镀铬、镀镍和镀锌等。
电镀可以有效地延长模具的使用寿命,提高产品的质量和稳定性。
四、抛光抛光是一种常用的模具表面处理工艺,通过使用研磨工具和研磨液对模具表面进行研磨,可以去除模具表面的毛刺和凹陷,使其表面光滑平整。
抛光可以分为机械抛光和手工抛光两种方式。
机械抛光适用于大型模具,可以实现高效的抛光;手工抛光适用于小型模具,可以更好地控制抛光的效果。
五、喷砂喷砂是一种常见的模具表面处理工艺,通过高速喷射砂粒对模具表面进行冲击,可以去除模具表面的氧化层和污垢,提高其表面粗糙度和附着力。
喷砂可以分为干喷砂和湿喷砂两种方式。
干喷砂适用于清除模具表面的污垢和氧化层;湿喷砂适用于改善模具表面的粗糙度和附着力。
六、喷丸喷丸是一种常用的模具表面处理工艺,通过高速喷射金属颗粒对模具表面进行冲击,可以去除模具表面的氧化层和污垢,提高其表面粗糙度和附着力。
喷丸可以分为机械喷丸和压缩空气喷丸两种方式。
机械喷丸适用于清除模具表面的污垢和氧化层;压缩空气喷丸适用于改善模具表面的粗糙度和附着力。
七、氮化处理氮化处理是一种常见的模具表面处理工艺,通过在模具表面注入氮气,使其与模具表面发生化学反应,形成一层硬度高、耐磨性强的氮化层。
氮化处理可以提高模具的使用寿命和耐腐蚀性,适用于高要求的模具制造。
模具加工工艺标准

结构简单:模 具设计应尽量 简单、明了, 方便操作和维 护。
0
0
0
0
1
2
3
4
模具设计的工艺性分析
模具材料的选用:根据产品要求和生产条件选择合适的模具材料,确保模具的耐磨性、 耐腐蚀性和热稳定性。
模具结构的合理性:模具结构设计应简单、紧凑,便于制造、装配、调试和使用,同时 要充分考虑模具的强度和刚性。
热处理工艺流程:预热、加热、保温、冷却和后处理等步骤
热处理工艺参数:加热温度、保温时间、冷却速度等参数对热处理效果的影响
04
模具设计的工艺要求
模具设计的原则
符合产品要求: 模具设计应满 足产品形状、 尺寸和性能的 要求。
加工方便:模 具设计应便于 制造、装配、 检测和维修, 降低制造成本。
寿命长:模具 设计应保证模 具的使用寿命, 提高模具的可 靠性和稳定性。
根据模具材料选择合适的刀 具类型和刀片材质
考虑刀具的寿命和耐用度, 合理使用刀具补偿功能
掌握刀具的安装与拆卸方法, 确保安全操作
切削参数的优化
切削速度:根据材料和刀具选 择合适的切削速度,以提高加 工效率和降低表面粗糙度。
进给量:适当调整进给量可以 提高切削效率,同时保证加工 质量。
切削深度:合理选择切削深度 可以减少刀具磨损和加工时间, 提高加工精度。
模具加工的重要性
模具加工的精度和稳定性直 接关系到产品的质量和生产 效率,是实现产品批量生产 的关键因素。
模具加工是制造业的重要环节, 对产品生产的质量和效率具有 决ቤተ መጻሕፍቲ ባይዱ性影响。
模具加工技术的发展和应用, 能够推动制造业的技术进步 和产业升级,提高生产效率
和产品质量。
模具制造方面的技术要求(中英文)
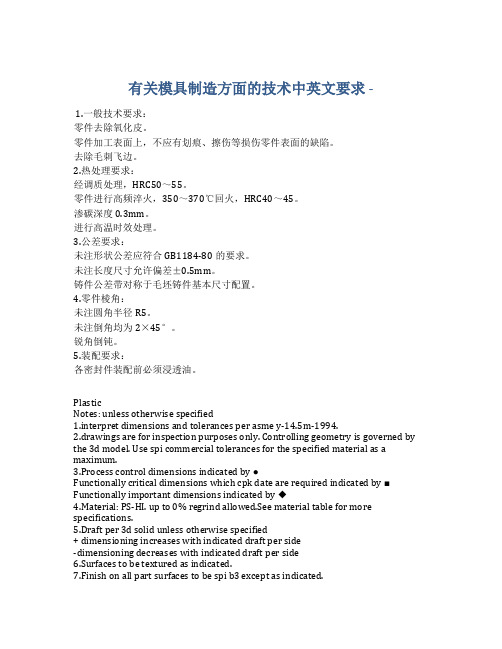
有关模具制造方面的技术中英文要求 -1.一般技术要求:零件去除氧化皮。
零件加工表面上,不应有划痕、擦伤等损伤零件表面的缺陷。
去除毛刺飞边。
2.热处理要求:经调质处理,HRC50~55。
零件进行高频淬火,350~370℃回火,HRC40~45。
渗碳深度0.3mm。
进行高温时效处理。
3.公差要求:未注形状公差应符合GB1184-80的要求。
未注长度尺寸允许偏差±0.5mm。
铸件公差带对称于毛坯铸件基本尺寸配置。
4.零件棱角:未注圆角半径R5。
未注倒角均为2×45°。
锐角倒钝。
5.装配要求:各密封件装配前必须浸透油。
PlasticNotes: unless otherwise specified1.interpret dimensions and tolerances per asme y-14.5m-1994.2.drawings are for inspection purposes only. Controlling geometry is governed by the 3d model. Use spi commercial tolerances for the specified material as a maximum.3.Process control dimensions indicated by ●Functionally critical dimensions which cpk date are required indicated by ■Functionally important dimensions indicated by ◆4.Material: PS-HI. up to 0% regrind allowed.See material table for more specifications.5.Draft per 3d solid unless otherwise specified+ dimensioning increases with indicated draft per side-dimensioning decreases with indicated draft per side6.Surfaces to be textured as indicated.7.Finish on all part surfaces to be spi b3 except as indicated.8.All surfaces to be free of dust. Oil and other contaminants.9.Mold release agents are not allowed.10.Break all sharp edges and corners to maximum 0.2mm radius.11.Flash and parting line mismatch not to exceed 0.1mm.12.Place following part information in this location.塑料品:注释:除非另有说明1.解释尺寸给每asme y-14.5m-1994.定公差2.此草案只用以检查目的,控制几何管理。
冲压模具制造检验技术要求
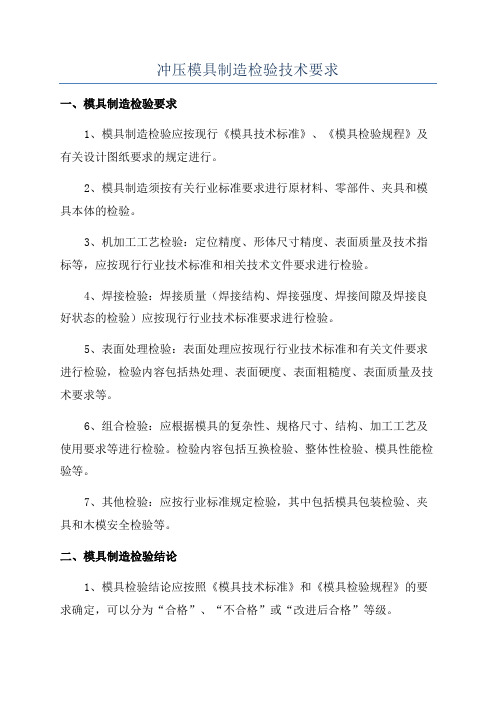
冲压模具制造检验技术要求
一、模具制造检验要求
1、模具制造检验应按现行《模具技术标准》、《模具检验规程》及有关设计图纸要求的规定进行。
2、模具制造须按有关行业标准要求进行原材料、零部件、夹具和模具本体的检验。
3、机加工工艺检验:定位精度、形体尺寸精度、表面质量及技术指标等,应按现行行业技术标准和相关技术文件要求进行检验。
4、焊接检验:焊接质量(焊接结构、焊接强度、焊接间隙及焊接良好状态的检验)应按现行行业技术标准要求进行检验。
5、表面处理检验:表面处理应按现行行业技术标准和有关文件要求进行检验,检验内容包括热处理、表面硬度、表面粗糙度、表面质量及技术要求等。
6、组合检验:应根据模具的复杂性、规格尺寸、结构、加工工艺及使用要求等进行检验。
检验内容包括互换检验、整体性检验、模具性能检验等。
7、其他检验:应按行业标准规定检验,其中包括模具包装检验、夹具和木模安全检验等。
二、模具制造检验结论
1、模具检验结论应按照《模具技术标准》和《模具检验规程》的要求确定,可以分为“合格”、“不合格”或“改进后合格”等级。
第5章 模具钢料的热处理-模具表面处理技术

第二节模具表面处理工艺概述模具是现代工业之母。
随着社会经济的发展,特别是汽车、家电工业、航空航天、食品医疗等产业的迅猛发展,对模具工业提出了更高的要求。
如何提高模具的质量、使用寿命和降低生产成本,成为各模具厂及注塑厂当前迫切需要解决的问题。
模具在工作中除了要求基体具有足够高的强度和韧性的合理配合外,其表面性能对模具的工作性能和使用寿命至关重要。
这些表面性能指:耐磨损性能、耐腐蚀性能、摩擦系数、疲劳性能等。
这些性能的改善,单纯依赖基体材料的改进和提高是非常有限的,也是不经济的,而通过表面处理技术,往往可以收到事半功倍的效果;模具的表面处理技术,是通过表面涂覆、表面改性或复合处理技术,改变模具表面的形态、化学成分、组织结构和应力状态,以获得所需表面性能的系统工程。
从表面处理的方式上,又可分为:化学方法、物理方法、物理化学方法和机械方法。
在模具制造中应用较多的主要是渗氮、渗碳和硬化膜沉积。
◆提高模具的表面的硬度、耐磨性、摩擦性、脱模性、隔热性、耐腐蚀性;◆提高表面的高温抗氧化性;◆提高型腔表面抗擦伤能力、脱模能力、抗咬合等特殊性能;减少冷却液的使用;◆提高模具质量,数倍、几十倍地提高模具使用寿命。
减少停机时间;◆大幅度降低生产成本与采购成本,提高生产效率和充分发挥模具材料的潜能。
◆减少润滑剂的使用;◆涂层磨损后,还退掉涂层后,再抛光模具表面,可重新涂层。
在模具上使用的表面技术方法多达几十种,从表面处理的方式上,主要可以归纳为物理表面处理法、化学表面处理法和表面覆层处理法。
模具表面强化处理工艺主要有气体氮化法、离子氮化法、点火花表面强化法、渗硼、TD法、CVD化学气相淀积、PVD物理气相沉积、PACVD离子加强化学气相沉积、CVA铝化化学气相沉积、激光表面强化法、离子注入法、等离子喷涂法等等。
下面综述模具表面处理中常用的表面处理技术:一、物理表面处理法:表面淬火是表面热处理中最常用方法,是强化材料表面的重要手段,分高频加热表面淬火、火焰加热表面淬火、激光表面淬火。
D30等径三通注塑模具设计

D30等径三通注塑模具设计D30等径三通注塑模具是一种常用的注塑模具,用于生产管道系统中的三通接头。
在设计这种模具时,需要考虑多个因素,例如模具的尺寸、结构、材料和制造工艺等。
下面是一个关于D30等径三通注塑模具的详细设计说明,总字数超过1200字。
一、模具尺寸设计1.模具整体尺寸:模具的整体尺寸应根据产品的要求确定,通常要考虑到投入产出比和设备的工作空间。
2.管道直径:D30等径三通的直径应根据具体要求确定,尺寸准确度要求较高,所以需要选择合适的工艺和设备。
二、模具结构设计1.模具结构类型:D30等径三通注塑模具结构一般为单模腔或多模腔结构,根据生产需求选择合适的结构类型。
2.模具芯型结构:对于三通注塑模具,通常需要使用可拆卸芯型结构以便于产品的脱模。
三、模具材料选择1.模具材料:选择合适的模具材料是保证模具质量和寿命的关键。
常见的模具材料有P20钢、718钢等。
四、模具制造工艺1.模具结构加工:根据模具设计图纸,分解各个部件,进行加工和装配。
2.模具表面处理:模具表面需要进行打磨和抛光,以确保模具零件的安装精度和表面光洁度。
3.注塑成型工艺:根据模具的设计要求,合理设置注塑机的工艺参数,如注塑温度、注射压力、注射速度等。
五、模具调试和试模1.模具调试:在注塑机上安装和调试模具,调整各个部位的位置和参数,确保模具能够正常运行。
2.试模验证:进行少量试模,检验产品的尺寸精度、外观质量和性能是否符合要求。
六、模具保养和维护1.模具保养:定期清洁和润滑模具,防止生锈和磨损。
2.模具维护:定期检查模具各个部位的磨损程度,及时更换磨损部件,延长模具使用寿命。
以上是关于D30等径三通注塑模具的设计说明,总字数超过1200字。
这种模具的设计需要考虑模具尺寸、结构、材料和制造工艺等多个方面,以确保模具能够满足产品的要求,且具有高精度和稳定性。
模具的设计和制造是一个复杂的过程,需要经验丰富的工程师和专业的制造设备来完成。
五金模具表面处理常见缺陷分析和消除措施
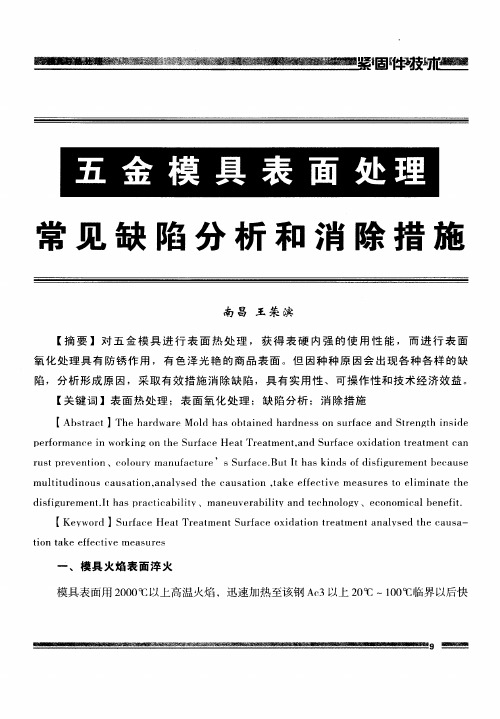
淬火模具不受体积大小 限制 ,可局部
淬硬 ; 淬火畸变小 , 淬火表面清洁无氧化 、 脱
碳;
成本低 、易上 马 、生产效率高 。
经验和最佳工艺参数后投产 ;
仔细观察火色 ,控制淬火加热温度 。 火焰表 面淬火后应及时在 2 0C± 1 0 ̄ 0 ℃ X1 h —2 低温 回火 , 消除淬火 内应力 , 避 免淬裂。
陷 , 分 析 形 成 原 因 , 采 取 有 效 措 施 消 除 缺 陷 ,具 有 实 用 ・ 可 操 作 性 和 技 术 经 济 效 益 。 性、 【 键 词 】表 面 热 处 理 ;表 面 氧 化 处 理 ;缺 陷 分 析 ; 消 除 措 施 关
【 bt c 】 h ad aeM l h s ban dh rn s o ufc n t n t is e A s a t T eh rw r od a o tie ad es nsr ea dSr gh n i r a e d
移 动速 度
1 65
/ m . i m m n
l5 4
1 25
11 0
10 O
9 0
8 0
到该钢 临界温度 A 3 t 以上 1 0 10 0℃ 5 ℃高
温奥 氏体 状 态 ,然 后 急速 冷却 淬火 ,实
模具感应 加热表面淬火 常见 缺陷及防
治措 施 :
2淬硬层 深度不易控制 、受热不均 . 匀、 硬度不均匀 , 主要靠实践经验控制淬 火质量。
防治措施 : 选用精炼钢 、电渣重熔钢或真空熔炼
钢。 它们具有纯度高 、 杂质少 、 晶粒细 、 碳
模具表面技术表面抛光

泽为主要目的的研磨和抛光加工,统称为光整加工。在模具加工中,光整 加工主要用于模具的成形表面,它对于提高模具寿命和形状精度,以及保 证顺利成形都起着重要的作用。 7.1.1 光整加工的特点与应用
模具成形表面的精度和表面粗糙度要求越来越高,特别是高寿命、高 精密模具,其精度发展到要求μm级精度。其成型表面一部分可采用超精 密磨削达到设计要求,但异型和高精度表面都需要进行研磨抛光加工。
辅助研磨抛光工具可以提高研磨抛光效率和减轻劳动强度,但是研磨抛光质量仍 取决于操作者的技术水平。 5. 研磨抛光工艺过程 (一) 研磨抛光余量 研磨抛光余量取决于零件尺寸、原始表面粗糙度、最终精度等要求,原则上研磨 抛光余量只要能去除表面加工痕迹和变质层即可。研磨抛光余量过大,使加工时 间延长,研磨抛光工具和材料消耗增加,加工成本增大;研磨抛光余量过小,加 工后达不到要求的表面粗糙度和精度。当零件的尺寸公差较大时,研磨抛光余量 可以取在零件尺寸公差范围以内(见表7-5)。
(1)普通油石 一般用于粗研磨,它由氧化铝或碳化硅等磨料和黏结剂压 制烧结而成。使用时根据型腔形状磨成需要的形状,并根据被加工表面的粗糙 度和材料硬度选择硬度和粒度。当被加工零件材料较硬时,应该选择较软的油 石,否则反之。当被加工零件表面粗糙度要求较高时,油石要细一些,组织要 致密些。1—抛光套 2—砂轮 3—软轴图7—6 手持电动直杆旋转式研磨抛光工 具
4. 研磨抛光工具图7—3 外圆研磨环1— 研磨套 2—研磨环 3—限位螺钉 4— 调节螺钉 (一)研具材料 研磨抛光时直接和被加工表面接触的研磨抛光工具称为研具。研具的材料
很广泛,原则上研具材料硬度应比被加工材料硬度低,但研具材料过软会使磨 粒全部嵌入研具表面而使切削作用降低。总之,研具材料的软硬程度、耐磨性 应该与被加工材料相适应。1— 芯棒 2—螺母 3—研磨套 4—套图7—4 可调式内圆研磨芯棒
模具常用表面处理

★注:TD处理由于要在高温条件下进行,尺寸大的模具高温下易变 形,因此主要用于我司配套件的小模具使用。
三种表面处理技术介绍
1、模具镀Cr简介
◆镀Cr过程示意图: ◆施行镀Cr的目的 :
1、新车投产时其成形性的尽快稳定化 2.模具品质的稳定化
◆施行镀Cr的优点 :
1.[精度/成形性]:模具的保护(半永久性的维 护模具寿命和精度):降低冲压油 的使用量 2.[品 质] :提高冲压加工的成形性:提高耐磨 性(压痕,粘连) 3.[成 本] :由于对模具材质要求的降低而降低 了模具费用 4.[保 全] :降低保全工数:降低冲压油的使用量
◆应用范围:
TD覆层处理可广泛应用于由于各类磨损所引起的模具与工件或工件与工件之间的拉伤或磨损超差的问题.其中因咬合或粘 结而引起的拉伤或拉毛问题,TD覆层处理是目前世界上最好的解决方法之一.因磨损而引起的工件尺寸超差等问题,通过TD 覆层处理后,提高使用寿命上十倍是很正常的.
3、表面工程技术在汽车模具表面质量改善中得到 广泛应用。
表面工程技术的特点及意义
1、它主要作用于基材表面,对远离表面的基 材内部组织与性能影响不大; 2、廉价性,使普通材料具有特殊性能,节约 贵金属,提高耐磨性和腐蚀性,提高了劳动生 产率,降低生产成本; 3、表面工程技术可以兼有装饰和防护功能; 4、表面工程技术已成为制备新材料的重要方 法,如可以在材料表面制备整体合金化难以做 到的特殊性能合金等。
◆与相关技术的比较 :
通过在工件表面形成一层高硬度的耐磨材料是提高工件 耐磨,抗咬合,耐蚀等性能,从而提高其使用寿命的有效而又 经济的方法,TD覆层处理技术以碳化钒覆层为例,其表面硬度 可达HV3200左右,较传统的表面处理方法如渗碳HV~900;渗氮 HV~1200;镀硬铬HV~1000;甚至渗硼HV 1200~1800等表面处理 的硬度高得多,因此具有远优于这些表面处理方法的耐磨性能。
模具表面处理技术
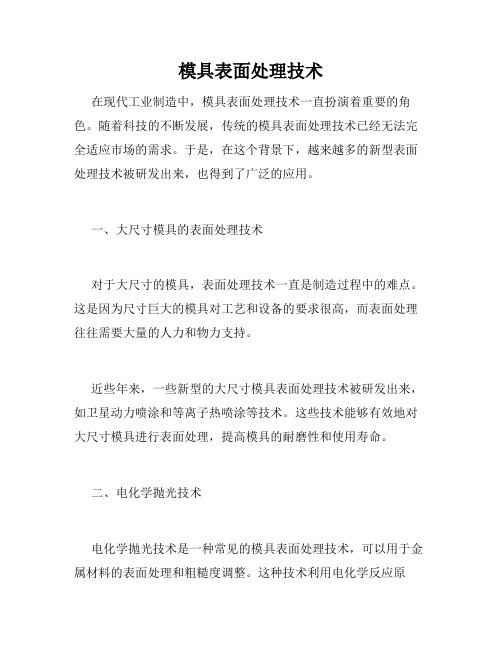
模具表面处理技术在现代工业制造中,模具表面处理技术一直扮演着重要的角色。
随着科技的不断发展,传统的模具表面处理技术已经无法完全适应市场的需求。
于是,在这个背景下,越来越多的新型表面处理技术被研发出来,也得到了广泛的应用。
一、大尺寸模具的表面处理技术对于大尺寸的模具,表面处理技术一直是制造过程中的难点。
这是因为尺寸巨大的模具对工艺和设备的要求很高,而表面处理往往需要大量的人力和物力支持。
近些年来,一些新型的大尺寸模具表面处理技术被研发出来,如卫星动力喷涂和等离子热喷涂等技术。
这些技术能够有效地对大尺寸模具进行表面处理,提高模具的耐磨性和使用寿命。
二、电化学抛光技术电化学抛光技术是一种常见的模具表面处理技术,可以用于金属材料的表面处理和粗糙度调整。
这种技术利用电化学反应原理,将模具表面的局部区域进行阳极和阴极反应,从而达到粗糙度调整和表面抛光的目的。
与传统的机械抛光方法相比,电化学抛光技术具有抛光效率高、加工精度高、处理时间短等优点。
因此,这种技术被广泛应用于各种领域,如航空、汽车、电子等制造领域。
三、光电子平凡技术光电子平凡技术是一种新型的表面处理技术,是光刻和等离子刻蚀技术的综合应用。
这种技术的特点是可以进行细微加工,并且能够保证加工精度高、表面平整度好、加工速度快等优点。
对于微米级别的加工,在传统的机械加工技术中往往难以实现,但在光电子平凡技术中完全可以做到。
因此,这种技术在微米级别的精细加工中有着广泛的应用。
四、沉积氧化技术沉积氧化技术是一种将氧化物沉积到船的表面上的技术。
该技术可以通过模具表面的化学反应,形成一层厚度均匀、钝化性能好的氧化层。
这种技术可以提高模具的抗腐蚀能力和抗磨损能力。
与其他表面处理技术相比,沉积氧化技术可以实现多样化的物理、化学性能以及形貌优异的表面。
因此,这种技术不仅适用于模具制造,还广泛应用于汽车、电子等制造领域。
总之,随着制造业的不断发展和技术的不断更新,模具表面处理技术将会继续提高和创新,应用的领域将会更加广泛,未来的发展前景也将更加宽广。
模具的表面处理技术

1引言
目前 国 内 外 多 采 用 固 体 硼 氮 共 渗 。 这 是 因 为 固 体 硼 氮 共 渗 工 艺 有 许 多 优 点 ,特 别 是 粉 末 硼 氮 共 渗 工 艺 , 渗 后 工 件 表 面 洁
随
舞
净 , 呈 银 灰 色 ,不 粘 附 , 不 需 要 特 殊 设 备 , 用 普 通 电 炉 、 装 采
ofbe i ng m ed u , n tt ng m e u . a tvaor p c ng m a e i1I sve y c m i a a r t e et tdi im irdi di m c i t , a ki t ra .ti r he c lhe tteam ntm hod t t c n obti a r ha a an lye ofgo o ri sThe r la e a t b  ̄ bor nird e a e w a od pr pe te . eibl nd sa l o ti i d c s sobti d o t u f c y pa k bo on ti i .Bo on ti i d c s s a ne n he s r a e b c r ird ng r ird e a e i c om po e b b on o poun (Fe B 、 Fe ) a r n ii na ne.The e r h g ha dne s nd w e r r ssa e. g s d y or c m d 2 B nd t a sto lzo r a e i h r s a a e it nc ood c r i n or oso
箱密 封加热 , 工艺操作 简单 、渗 后工件不需 清洗、渗剂重 复使 用性 好 、成本较低 ,渗层厚 度与组织易控制 。
模具制作技术要求规范

精密模具技术要求版本 1.0修订历史日期版本描述作者V1.0 精密模具技术要求目录1 分模表 (4)2 新开模具必须满足产品生产要求 (4)3 模具具体要求 (4)3.1 模架技术要求 (4)3.2 模仁技术要求 (6)3.3 滑块等抽芯技术要求 (7)3.4 顶出系统要求 (8)3.5 冷却或加热系统要求 (10)3.6进料系统要求 (10)3.7 排气系统要求 (10)3.8 保养要求 (11)3.9其它要求 (11)4 设计评审 (11)5 交样要求 (11)6 验收标准 (12)7 完成时间 (12)1 分模表项目需制作精密塑胶模具套,分模要求及产品表面工艺处理请参照附件《项目塑胶模具分模表》。
2 新开模具必须满足产品生产要求2.1 外观件用肉眼观察不能有熔合线、熔接痕、气泡、烧焦、缺料、缩痕、毛边、气纹、伤痕、顶白、变形等模具或成型缺陷。
2.2 总成产品包含多按钮时,除与色板、皮纹板等对比外,各按钮之间、按钮与安装板之间色泽、纹理、间隙、面差还应保持一致,肉眼观察应无可视性差别。
2.3 总成产品须在模具T2前全部整改到位(包括间隙面差调整、DV试验及小批量验证等)。
2.4 T1试模后的产品全尺寸及功能测试必须符合《北京远特科技股份有限公司》产品图纸要求。
2.5 模具的P.L线(面),在产品上只允许留有一条线,不允许在同一个面(含曲面)上的分模线有断差,P.L线位置的选择须避开按钮行程。
2.6外观零件的A面除满足以上要求外,不可有进浇口,顶针等痕迹。
2.7外观件、滑动装配部位的导槽、导轨等精密装配件表面的粗糙度为Ra0.2um 以内。
2.8产品外表面均需达到表面粗糙度Ra0.2um,其它特殊外观件以产品图要求为准。
2.9模具各零部件非胶位及装配位棱边均须要设计工艺倒角,且倒角要求统一、美观。
3 模具具体要求3.1 模架技术要求3.1.1 模架采用龙记标准(含)以上等级的标准模架,材料45#以上钢材。
模具装配的技术要求
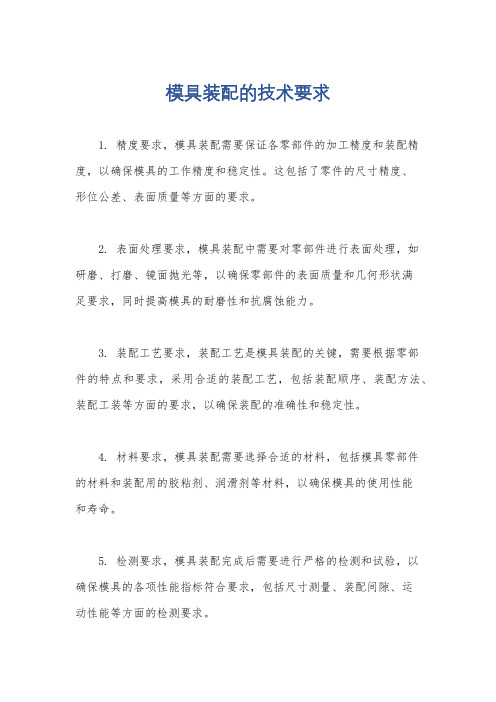
模具装配的技术要求
1. 精度要求,模具装配需要保证各零部件的加工精度和装配精度,以确保模具的工作精度和稳定性。
这包括了零件的尺寸精度、
形位公差、表面质量等方面的要求。
2. 表面处理要求,模具装配中需要对零部件进行表面处理,如
研磨、打磨、镜面抛光等,以确保零部件的表面质量和几何形状满
足要求,同时提高模具的耐磨性和抗腐蚀能力。
3. 装配工艺要求,装配工艺是模具装配的关键,需要根据零部
件的特点和要求,采用合适的装配工艺,包括装配顺序、装配方法、装配工装等方面的要求,以确保装配的准确性和稳定性。
4. 材料要求,模具装配需要选择合适的材料,包括模具零部件
的材料和装配用的胶粘剂、润滑剂等材料,以确保模具的使用性能
和寿命。
5. 检测要求,模具装配完成后需要进行严格的检测和试验,以
确保模具的各项性能指标符合要求,包括尺寸测量、装配间隙、运
动性能等方面的检测要求。
总的来说,模具装配的技术要求包括精度要求、表面处理要求、装配工艺要求、材料要求和检测要求等多个方面,只有严格按照这
些要求进行装配,才能保证模具的质量和性能。
常用塑胶模具的表面处理方法

目前常用的塑胶模具外表处理方法有氮化、电镀、晒纹及喷砂。
其中氮化与电镀是一种提高模具寿命的方法,而晒纹与喷砂那么是一种模具外表的装饰方法。
一、氮化氮化分为渗氮和氮碳共渗。
此种工艺的最大优点是热处理温度低〔一般是500—600℃〕,热处理后变形小,生成氮化物层很硬,使模具的耐磨性及抗咬合性提高。
模具的耐蚀性耐热性及抗疲劳强度有很大改善。
1.渗氮:渗氮的方法分为气体渗氮、液体渗氮、固体渗氮、离子渗氮等。
我们目前比拟常用的是气体渗氮,是将氨气〔NH3〕通入约550℃的炉中,靠氨气分解所得的氮渗入钢中。
氮化时间较长,一般浅层每小时大约在0.015-0.02mm左右,深层渗氮速度每小时约0.005-0.015mm。
而在高合金钢中,由于合金元素含量较多,氮的扩散速度低,渗氮速度会较上述数据低。
气体渗氮的时间〔工件小于300X300X50mm〕一般为8-9小时,渗层深度为0.1-0.2mm之间,渗氮后的外表硬度为HV850—1200之间〔HRC65-72〕,且外表颜色泛亮。
2.氮碳共渗:即就是我们所说的软氮化,也称之为液氮。
氮碳共渗温度比渗氮温度稍高,对渗层硬度不会造成很大的影响。
也不会增加渗层脆性,但可增加扩散速度。
氮碳共渗一般采用570℃左右为好,低碳钢可以在600℃以上进行氮碳共渗,以获得较厚的化合物层。
氮碳共渗的最初3小时内渗层深度增加最快,超过6小时后,渗层深度增加不很明显,因而氮碳共渗的时间一般不超过6小时。
氮化层的深度一般为0.05-0.100mm,外表硬度为HV1000〔RC68以上〕外表颜色呈深灰色。
3.氮化对材料的一些要求:〔1〕在氮化温度下,只要不发生退火的材料均可进行氮化。
〔2〕含铬量比拟高的金属〔如420、S136、2083、M300〕等均不可进行气氮〔因含铬过高气体难以打入到钢材里面〕。
4.氮化以后的一些现象—0.03mm〕的白亮层,且比拟软,此层必须打磨掉以后工件才能恢复到它原来的尺寸,取掉此层后的硬度也是最硬的。
塑料模具加工标准

在塑料加工工业和塑料成型机配套中,塑料模具是一种赋予塑料制品以完整构型和精确尺寸的工具。
塑料加工方法众多,其中一个步骤出现小小的失误都可能导致加工制品失败。
现把塑料模具加工标准整理如下:◆1.小于2020的模胚,a、b板之间需要做撬模坑;大于2020的模胚所有模板包括顶针板间都要做撬模坑。
◆2.模胚导柱导套要加工排气槽,以防导柱导套拉伤。
◆3.模具上不得有尖角,需要倒角处理。
特别指明的地方除外。
塑料模具加工标准汇总◆4.内模和模具零件未经同意不得有烧焊。
◆5.模具产品的外围必须要在适当的位置开排气槽,排气槽规格请参考模具设计手册。
◆6.尽可能避免使用打磨机在模具上打磨,如果非要用打磨机加工,必须用油石省光(特别是分型面)◆7.内模胶位面的表面处理必须依照bom表,或者其它正式通知的技术要求执行。
非胶位面上的加工纹路(线切割,铣床,cnc锣床,火花机)也要用油石省亮。
◆8.所有内模材料,模胚等级要求必须依据订单,或者设计审核过程中正式确认的技术要求进行采购。
必须提供材质证明,如果是硬模,必须提供热处理报告。
所有相关证明。
◆9.所有模具的前后内模,镶件,行位,斜顶,直顶(推块),铲鸡等需要在底面或者侧面加工一个腰圆形的坑位,把材料名和硬度刻出来。
◆10.行位,推块,铲鸡,唧嘴等重要易磨损零件必须进行氮化加硬处理。
◆11.行位必须有定位。
定位方式有弹弓,波珠,hasco(dme)标准行位夹等等,具体需要按照各个项目的要求。
行位需要有压条,耐磨板。
压条,耐磨板必须使用耐磨硬料,需要加上油槽。
◆12.行位斜导柱必须压紧,不能转动和松动。
斜导柱尾部必须要加工成半球形或圆锥台形,有利于保证行位正常运动。
同一行位上有两支或者两支以上斜导柱的,斜导柱的长度、大小和倾斜度必须相同。
◆13.斜顶座位必须使用耐磨硬料。
斜顶必须加工油槽,斜顶座一般用2510或cr12加硬到hrc40-45度,因为斜顶座受到的是冲击负荷,所以不能太硬否则会断裂,并在所有的直角位置倒角c角。
模具表面处理种类及规格
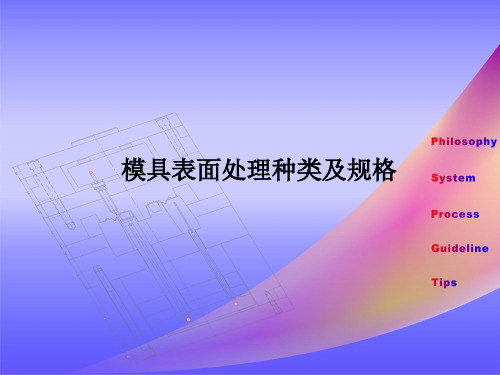
Plaque #7 Ptn.# Depth(mm) MT325 0.003 MT964 0.003 MT1038 0.002 MT1043 0.002 MT1170 0.0025 MT1192 0.0015 MT1239 0.003 MT1240 0.003 MT1241 0.002 MT1242 0.002 MT1243 0.002 MT1244 0.0025 MT1250 0.003 MT2019 0.0025 MT2020 0.002 MT2028 0.0025 23053 0.002 23064 0.0015
(轻微高光面,良好ቤተ መጻሕፍቲ ባይዱ 轻微高光面, 模,用在装饰要求不高 的场合) 的场合) (非高光面,良好脱模, 非高光面,良好脱模, 也是砂纸和钻石抛光的 头道工序) 头道工序)
喷砂抛光
(网点和纹理表面) 网点和纹理表面)
SPIA-1
(高质量外观或者 镜片模具) 镜片模具)
SPIB-1
SPIC-1
SPID-1
Diamond Mold Polishing & Finishing Specifications
Types of Finishes Current SPI Finish Numbers
#1 Diamond Buff 钻石膏, (#1钻石膏,光学要求) 钻石膏 光学要求) #3 Diamond Buff 钻石膏, (#3钻石膏,镜面) 钻石膏 镜面) #6 Diamond Buff 钻石膏, (#6钻石膏,镜面) 钻石膏 镜面) #15 Diamond Buff 钻石膏, (#15钻石膏,镜面) 钻石膏 镜面) 600 Grit 砂纸, (600砂纸,光面) 砂纸 光面) 400 Grit 砂纸, (400砂纸,光面) 砂纸 光面) 320 Grit 砂纸, (320砂纸,光面) 砂纸 光面) 600 Stone 油石, (600油石,光面) 油石 光面) 400 Stone 砂纸, (400砂纸,光面) 砂纸 光面) 320 Stone 砂纸, (320砂纸,哑面) 砂纸 哑面) #11 Glass Bead 粗玻璃砂) (#11粗玻璃砂) 粗玻璃砂 #240 Aluminum Oxide Blast (#240氧化铝) 氧化铝) 氧化铝 #24 Aluminum Oxide Blast 氧化铝) (#24氧化铝) 氧化铝
- 1、下载文档前请自行甄别文档内容的完整性,平台不提供额外的编辑、内容补充、找答案等附加服务。
- 2、"仅部分预览"的文档,不可在线预览部分如存在完整性等问题,可反馈申请退款(可完整预览的文档不适用该条件!)。
- 3、如文档侵犯您的权益,请联系客服反馈,我们会尽快为您处理(人工客服工作时间:9:00-18:30)。
模具零件的表面粗糙度要求
内容来源网络,由“深圳机械展(11万㎡,1100多家展商,超10万观众)”收集整理!更多cnc加工中心、车铣磨钻床、线切割、数控刀具工具、工业机器人、非标自动化、数字化无人工厂、精密测量、数控系统、3D打印、激光切割、钣金冲压折弯、精密零件加工等展示,就在深圳机械展
模具零件的表面粗糙度要求
模具零件表面质量的高低用表面粗糙度衡量,通常以R a(µm)表示。
R a数值愈小,表示其表面质量愈高。
模具零件的工作性能如耐磨性、抗蚀性及强度等,在很大程度上受其表面质量的影响。
模具零件的表面质量越高,其寿命也越长。
但从另一方面看,对模具零件表面质量要求过高,则增加了模具制造成本。
因此,应合理选用模具零件的表面粗糙度。
模具零件常用的表面粗糙度要求列于下表,可供模具设计时参考。
等展示,就在深圳机械展。