数控立车专用夹具设计
弯脖长轴的数控夹具设计

弯脖长轴的数控夹具设计0 引言随着社会生产和科学技术的不断进步,各类工业新产品层出不穷。
机械制造产业作为国民工业的基础,其产品更是日趋精密复杂,特别是在宇航、航海、军事等领域所需的机械零件,精度要求更高和形状更为复杂。
普通数控机床难以胜任,即便是高精度的数控机床也得配上相应的数控夹具方能满足加工要求。
本次设计以FANUC数控系统对数控加工中心进行夹具设计及应用。
1 零件结构分析从图1可知,本零件主要由右端13 mm的长轴,左端由8 mm×8 mm的方以及一个带15 °的圆弧面组成,主要加工部位是外圆长轴和另一端带圆弧斜度与8 mm×8 mm方的一个连体,要求左端上表面与长轴右端面垂直。
所有表面粗糙度为R a6.3 um,热处理到HRC30~35,表面处理H.Y。
零件材料为锻件,保证零件有足够的强度、硬度和风度,在外力的作用下,不致于发生意外事故。
综上所述,此零件在在加工时,先检查零件是否有折皱、发纹、裂文、分层等缺陷,然后采用粗、精分开,基准统一、基准重合的原则,确保工艺基准与设计基准重合。
2 夹具的工作原理根据工件的要求,加工25.5 mm的表面要与13 mm的端面垂直,为了达到此尺寸要求,特设计此三爪夹具工装,见图2。
利用此夹具通过花盘安装在数控加工中心四轴上,并且与主轴一起旋转运动,进行铣平面和端面。
三爪夹具由螺盖、定位扳、定位块、定位轴、卡爪,紧固用孔组成夹具体,定位基准则用工件上的8 mm×8 mm的侧面和13 mm的轴面为定位基准。
三爪夹具是把定位螺盖和定位板利用三个螺孔和一个10H7/n6的销孔用三内六角螺钉联结在一起,利用定位块上的2- (50+0.012)mm 孔和2 个精制螺钉装在定位板上, 8 mm 孔里放一个1×6×19的压簧,把定位轴与定位块和定位扳安装在一起,把圆柱销装在定位块上的小槽中,此安装后通过压簧使定位轴起到前后定位滑动作用,最后把卡爪安装在花盘上。
数控加工设备专用夹具设计探究

数控加工设备专用夹具设计探究1. 引言1.1 背景介绍传统的夹具设计主要依靠人工经验和实践,存在着设计周期长、成本高、适用范围狭窄等问题。
研究数控加工设备专用夹具的设计问题,探讨其设计原理和关键技术,对于提高加工效率、降低成本、提高产品质量具有重要意义。
本文将围绕数控加工设备专用夹具的设计展开探究,旨在为相关领域的研究人员和生产从业者提供参考,并推动数控加工设备专用夹具设计技术的进步和发展。
1.2 研究意义数控加工设备专用夹具设计是数控加工领域中不可或缺的重要环节,其设计质量直接影响到数控加工的精度、效率和安全性。
研究专用夹具设计的意义在于提高数控加工设备的加工精度和效率,降低生产成本,同时提高工作人员的工作安全性和舒适度。
通过不断优化专用夹具设计,可以大幅提高产品的加工质量和生产效率,从而增强企业的市场竞争力。
随着科技的不断进步,数控加工设备专用夹具设计也需要不断创新和改进,以适应不断变化的市场需求和技术发展趋势。
深入研究数控加工设备专用夹具设计的意义在于推动相关技术的进步,提升企业的核心竞争力,实现经济效益和社会效益的双赢。
1.3 目的和意义专用夹具在数控加工设备中扮演着至关重要的角色。
其设计质量直接影响到加工精度、生产效率和产品质量。
研究数控加工设备专用夹具设计具有重要的现实意义和理论意义。
对数控加工设备专用夹具设计的探究有助于提高加工效率和降低生产成本。
通过合理设计专用夹具,可以实现工件的快速固定和定位,减少加工过程中的调整和换位时间,提高生产效率,降低生产成本。
专用夹具设计的研究对于提高加工精度和保证产品质量也具有重要作用。
精确的夹具设计可以确保工件的正确位置和稳定夹紧,减少加工过程中的误差,提高加工精度,保证产品质量。
深入研究专用夹具设计的关键技术,可以为提高数控加工设备的自动化程度和智能化水平提供技术支持,促进制造业的发展,提升我国在全球制造业中的竞争力。
探究数控加工设备专用夹具设计具有重要的现实意义和理论意义。
数控加工设备专用夹具设计探究

数控加工设备专用夹具设计探究随着数控加工设备的普及,夹具作为数控加工过程中必不可少的配件,起到了固定工件、提高加工精度及效率的重要作用。
因此,夹具的设计和选择非常重要。
本文将探究数控加工设备专用夹具的设计问题。
一、夹具设计要求夹具是用于夹紧待加工工件的装置,应根据不同的工件特点及其在加工过程中的运动特点来设计。
在设计夹具时,需要考虑以下要求:1.夹紧力要大:夹具拥有足够的夹紧力,以保证工件在加工过程中不会发生相对位移。
2.夹紧面要匀称:夹紧面应计算和设计合理,以保证工件夹紧平稳均衡。
3.夹具对工件表面的损伤要小:夹具设计时应避免对工件表面造成损伤,特别是对外形要求高的工件。
4.夹具刚度要高:夹具刚度高,能够保证加工精度和加工效率。
5.夹具加工精度要高:夹具必须保持加工精度,并且在使用时不会发生变形。
6.夹具结构要简单:夹具必须易于安装和操作,减少加工人员的劳动强度。
1. 夹具定位方式:工件在加工过程中必须定位准确,夹具定位方式占据着至关重要的地位。
定位方式分为机械定位和光学定位两种方式。
机械定位分为直线定位和曲线定位。
夹具上定位孔或定位销,可保证工件位置不变。
光学定位可以采用3D视觉系统或激光测距等,以高精度的方式实现工件的定位。
2. 设计加工便捷性:夹具应具有可换夹机构,以便夹具可以适应不同的加工工件。
同时,夹具的安装、拆卸和调整应该方便,以减少加工人员的劳动强度。
3. 夹具加工性能:夹具应该具有较高的加工性能,这要求夹具必须是高硬度、高强度和高温稳定性的材料。
同时,夹具表面必须具有足够的节油性和防腐能力,以保持夹具的寿命和使用效果。
4. 夹具的材质选择:夹具材质应根据加工工件的特点而定。
比如说对于需要加工的大型铸件,应该选择表面有防腐蚀涂层的铸铁夹具。
对于加工工件表面要求高的,应该选择使用密闭式夹具而不是气动式夹具。
5. 夹具运动特点分析:夹具在加工过程中参与的运动有多种类型,如滑动、旋转、倾斜等。
机床专用夹具及其设计方法
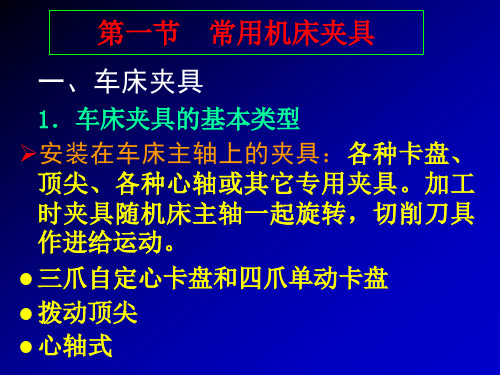
要有快速对刀元件
2、铣床夹 具的构造 主要由夹 具体、定 位板、夹 紧机构、 对刀块、 定向键等 组成
3.铣床夹具的设计
铣床夹具的安装:主要依靠定向键和
百分表校正来提高安装精度。定位键 的结构尺寸已标准化,应按铣床工作 台的T形槽尺寸选定,它和夹具底座 以及工作台T形槽的配合为H7/h6、 H8/h8。两定位键的距离应力求最大
• • • •
1、分度盘锁紧螺母 2、分度盘 3、定位轴 4、压紧螺母
移动式钻模
• 移动式钻模用在立式钻床上,先后钻销 工件同一表面上的多个孔,属于小型夹 具。移动的方法有两种:一种式自由移 动,另一种是定向移动,用专门设计的 轨道和定程机构来控制移动的方向和距 离。
滑柱式钻模
滑柱式钻模是一种标准化,规格化的 通用钻模。钻模体可以通用于较大范围 的不同工件。设计时,只需根据不同的 加工对象设计相应的定位。夹紧元件。 因此,可以简化设计工作。另外,这种 钻模不需另行设计专门的夹紧装置,夹 紧工件方便,迅速,适用于不同类型的 各种中小型零件的孔加工,生产中,尤 其是大批量生产中应用较广。
4、钻套的材料
性能要求:高硬度,耐磨 常用材料:T10A T12A CrMn 或20渗 碳淬火 D≤10mm CrMn D<25mm T10A T12A HRC58~64 D≥25mm 20渗碳淬火 HRC58~64
镗模
(一)镗模的特点及其组成 1、特点:镗床夹具称镗模,主要用于加工 箱体类零件上的孔或孔系通过布置镗套, 可加工出较高精度要求的孔或孔系。 与 钻模相比,它有相同之处,但箱体孔系 的加工精度一般要求较高,其本身精度 比钻模高。
l—台肩销 2—快换垫圈 3—螺母
数控立车全自动夹紧工作台的结构设计

数控立车全自动夹紧工作台的结构设计引言:在现代制造业中,数控机床的广泛应用极大提高了生产效率和产品质量。
然而,工件的装夹操作仍然是一个耗时耗力的手动过程。
为了实现自动化生产,设计一种全自动夹紧工作台至关重要。
本文介绍了一种数控立车全自动夹紧工作台的结构设计。
1. 设计目标- 实现工件的快速自动装夹- 保证工件夹紧位置精度和重复定位精度- 兼容不同尺寸和形状的工件- 整体结构紧凑,占用空间小2. 总体结构该工作台由底座、滑台、夹具模块和控制系统组成。
底座提供稳固的安装基础。
滑台在底座上做直线往复运动,用于工件的装卸。
夹具模块安装在滑台上,用于自动夹紧和定位工件。
控制系统负责协调各个部件的动作。
3. 滑台机构滑台采用直线导轨和丝杠传动方式,确保运动平稳、无间隙。
伺服电机驱动丝杠旋转,推动滑台在导轨上往复移动。
行程开关和光电编码器用于滑台的位置检测和控制。
4. 夹具模块夹具模块由多个可调节的卡爪组成,通过液压或气动执行机构驱动卡爪开合。
卡爪采用活动铰链结构,可自适应不同形状的工件。
定位销钉和定位块用于精确定位工件。
可更换不同规格的卡爪,以适应不同工件。
5. 控制系统工业控制器集成运动控制和功能,实现滑台运动和夹具动作的协调控制。
人机界面实现参数设置和状态监视。
安全保护装置如光栅、防护门等确保人身安全。
6. 工作流程(1)滑台移至装卸位置;(2)放置工件,夹具模块自动夹紧;(3)滑台移至加工位置,立车开始加工;(4)加工完成,滑台移至装卸位置,夹具松开,卸下工件。
总结:该数控立车全自动夹紧工作台实现了工件自动装夹,提高了生产效率,减轻了工人劳动强度。
模块化设计使系统具有良好的适应性和灵活性。
未来可进一步优化控制算法和人机交互界面。
数控车床专用夹具的设计

数控车床专用夹具的设计数控车床专用夹具的设计针对车削加工某种特殊零件或某个特殊位置,用三爪或四爪卡盘夹持零件,存在不足或无法满足加工。
根据多年的加工经验,对于这类零件的加工,根据加工特性和使用要求进行了综合分析。
在本道工序加工时,主要应考虑如何保证外形尺寸的条件下,提高劳动生产率,降低劳动强度。
经过分析后,自己动手设计制造了一套夹具,充分发挥原有设备的能力,通过现场使用,达到了预期的效果。
摘要:夹具是加工时用来迅速紧固工件,使机床、刀具、零件保持正确相对位置的工艺装置。
工装夹具是机械加工不可缺少的部件,在机床技术向高速、高效、精密、复合、智能、环保方向发展的带动下,夹具技术正朝着高精、高效、模块、组合、通用、经济方向发展。
关键词:车削专用夹具设计应用夹具又称卡具:在工艺过程中的任何工序,用来迅速、方便、安全地安装工件的装置,都可称为夹具。
例如焊接夹具、检验夹具、装配夹具、机床夹具等。
其中机床夹具最为常见,常简称为夹具。
在机床上加工零件时,为使零件能达到图纸规定的尺寸、几何形状以及与其他的相互位置精度等技术要求,加工前必须将零件装好(定位)、夹牢(夹紧)。
1 、加工零件与加工技术分析最近接到一批外加工零件(铝件),需要在有限的'时间里完成(如图l 所示)。
这批零件虽然简单,但图中M38X1.5螺纹不好加工。
按过去的加工方式,用螺纹铣刀加工虽然也能做到,但是加工质量不好保证,同时加工也麻烦。
2、零件加工设想能否设计出一种夹具,专门用于加工图中M38X1.5螺纹,在使零件的加工过程在保证质量的前提下,变得简单又快捷。
3 、专用夹具的设计专用夹具制造批量极少,一般不经过试制阶段,它的设计全过程,分为两个阶段:第一阶段是从调查研究到图纸设计的阶段,第二阶段是经过制造,调整到修改完善原设计图纸的阶段。
对夹具进行设计需要做到以下几个方面:(1)熟悉零件图纸,了解其形状,尺寸,精度,技术要求;(2)熟悉工艺,了解各工序之间的相互关系,本工序前有关表面粗糙度及位置尺寸,本工序的工艺要求;(3)了解所用设备的特性,精度,有关尺寸及其与夹具连接处的形式;(4)了解所用刀具的有关尺寸及其与夹具配合的要求;(5)了解加工特性。
分析数控加工机械零件中的专用夹具设计
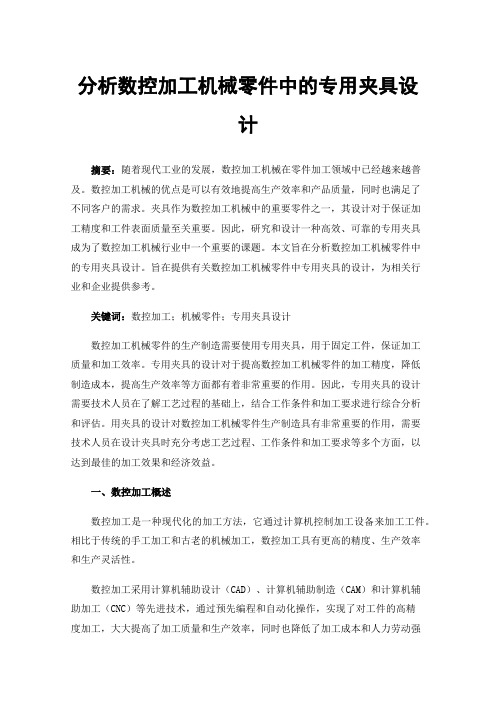
分析数控加工机械零件中的专用夹具设计摘要:随着现代工业的发展,数控加工机械在零件加工领域中已经越来越普及。
数控加工机械的优点是可以有效地提高生产效率和产品质量,同时也满足了不同客户的需求。
夹具作为数控加工机械中的重要零件之一,其设计对于保证加工精度和工件表面质量至关重要。
因此,研究和设计一种高效、可靠的专用夹具成为了数控加工机械行业中一个重要的课题。
本文旨在分析数控加工机械零件中的专用夹具设计。
旨在提供有关数控加工机械零件中专用夹具的设计,为相关行业和企业提供参考。
关键词:数控加工;机械零件;专用夹具设计数控加工机械零件的生产制造需要使用专用夹具,用于固定工件,保证加工质量和加工效率。
专用夹具的设计对于提高数控加工机械零件的加工精度,降低制造成本,提高生产效率等方面都有着非常重要的作用。
因此,专用夹具的设计需要技术人员在了解工艺过程的基础上,结合工作条件和加工要求进行综合分析和评估。
用夹具的设计对数控加工机械零件生产制造具有非常重要的作用,需要技术人员在设计夹具时充分考虑工艺过程、工作条件和加工要求等多个方面,以达到最佳的加工效果和经济效益。
一、数控加工概述数控加工是一种现代化的加工方法,它通过计算机控制加工设备来加工工件。
相比于传统的手工加工和古老的机械加工,数控加工具有更高的精度、生产效率和生产灵活性。
数控加工采用计算机辅助设计(CAD)、计算机辅助制造(CAM)和计算机辅助加工(CNC)等先进技术,通过预先编程和自动化操作,实现了对工件的高精度加工,大大提高了加工质量和生产效率,同时也降低了加工成本和人力劳动强度。
因此,在涉及到机械零件精度要求较高的领域,如航空、军事、高端制造等,数控加工已经成为主流的加工方法。
在数控加工中,专用夹具是保证加工质量和加工效率的重要装备之一。
通过精心设计夹具可以固定工件,避免在加工过程中产生误差,确保精度要求得到满足。
因此,在数控加工机械零件中,专用夹具的设计是非常关键和必要的一步[1]。
数控车床的夹具设计原理

数控车床的夹具设计原理
数控车床的夹具设计原理主要包括以下几个方面:
1. 夹紧原理:夹具的主要功能是夹住工件,确保工件在加工过程中的稳定性。
夹具通常采用机械夹紧、液压夹紧或气动夹紧等方式,在夹紧过程中要考虑到夹紧力的大小、分布均匀性以及夹紧方式的灵活性等因素。
2. 定位原理:夹具的另一个重要功能是确保工件在加工过程中的准确定位。
夹具设计中要考虑到工件的形状、尺寸以及零件间的相对位置关系,选择适当的定位方式,如销子定位、球锥定位、面板定位等。
3. 支撑原理:数控车床加工过程中,工件需要在夹具内得到合理的支撑,以避免工件在切削力作用下发生变形。
夹具设计中需要考虑到工件的几何特征,确定合适的支撑点,采用支撑块、支撑台等结构形式,提供稳定的支撑面。
4. 切削力分析:夹具设计中还需要考虑到切削过程中产生的切削力,并进行力学分析。
根据切削力的方向和大小,设计夹具的支撑结构,增加夹具的刚性和稳定性,以提高加工精度和表面质量。
5. 运动原理:数控车床加工过程中,夹具需要与机械手、工作台等设备协同工作。
因此,夹具设计中要考虑到夹具的运动特点,确保夹具的操作灵活、方便,与其他设备的运动相匹配。
总之,夹具设计原理在于确保夹具对工件进行牢固夹持和准确定位的同时,提供合理的支撑和增加刚性,以满足数控车床加工过程的要求。
数控机床的工装与夹具设计要点

数控机床的工装与夹具设计要点数控机床是现代制造业中不可或缺的重要设备,而工装与夹具的设计则是数控机床加工过程中至关重要的一环。
本文将从几个方面探讨数控机床的工装与夹具设计要点。
首先,工装与夹具的设计需要考虑到加工工艺的特点。
在数控机床加工过程中,工装与夹具起到定位、夹紧、支撑等作用,因此必须根据被加工工件的形状、尺寸和加工要求来设计。
例如,对于复杂形状的工件,需要设计出相应的定位装置和夹具,以确保工件在加工过程中的稳定性和精度。
其次,工装与夹具的设计需要考虑到加工精度的要求。
数控机床加工的一个重要特点就是高精度,而工装与夹具的设计直接影响到加工精度的实现。
因此,在设计过程中需要充分考虑工装与夹具的刚度、稳定性和精度控制等因素。
例如,可以采用高强度材料制作工装与夹具,以提高其刚度和稳定性;同时,可以采用精密的调整机构来实现加工精度的微调。
此外,工装与夹具的设计还需要考虑到生产效率的要求。
数控机床的出现主要是为了提高生产效率,而工装与夹具的设计也应该与之相适应。
在设计过程中,可以采用标准化和模块化的设计思路,以提高工装与夹具的通用性和可替换性;同时,可以利用自动化技术,如气动、液压等,来实现工装与夹具的自动化操作,进一步提高生产效率。
另外,工装与夹具的设计还需要考虑到安全性和可靠性的要求。
在数控机床加工过程中,由于加工精度的要求较高,工装与夹具的失效可能会导致工件的损坏甚至事故的发生。
因此,在设计过程中需要充分考虑工装与夹具的强度、可靠性和安全性。
例如,可以采用多重保险措施,如设置过载保护装置和紧急停机装置,以确保工装与夹具的安全运行。
最后,工装与夹具的设计还需要考虑到可维护性和成本的要求。
数控机床的使用寿命较长,因此工装与夹具的设计应该考虑到其可维护性。
在设计过程中,可以采用模块化的设计思路,以便更换和维修;同时,可以采用易于加工和成本较低的材料,以降低成本。
综上所述,数控机床的工装与夹具设计要点包括考虑加工工艺特点、加工精度要求、生产效率要求、安全性和可靠性要求、可维护性和成本要求等方面。
数控加工设备专用夹具设计探究
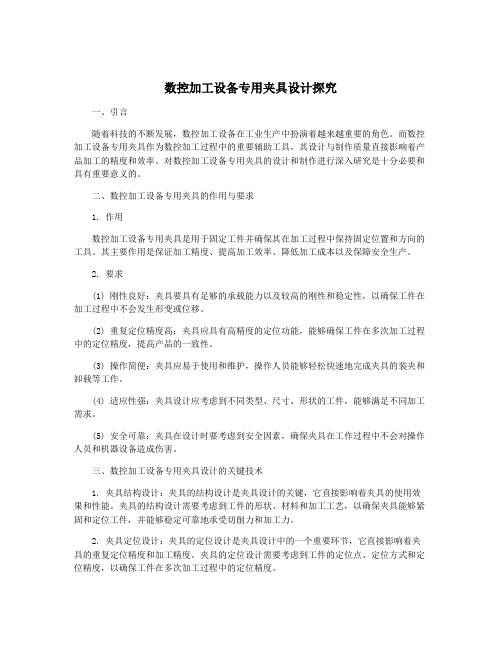
数控加工设备专用夹具设计探究一、引言随着科技的不断发展,数控加工设备在工业生产中扮演着越来越重要的角色。
而数控加工设备专用夹具作为数控加工过程中的重要辅助工具,其设计与制作质量直接影响着产品加工的精度和效率。
对数控加工设备专用夹具的设计和制作进行深入研究是十分必要和具有重要意义的。
二、数控加工设备专用夹具的作用与要求1. 作用数控加工设备专用夹具是用于固定工件并确保其在加工过程中保持固定位置和方向的工具。
其主要作用是保证加工精度、提高加工效率、降低加工成本以及保障安全生产。
2. 要求(1) 刚性良好:夹具要具有足够的承载能力以及较高的刚性和稳定性,以确保工件在加工过程中不会发生形变或位移。
(2) 重复定位精度高:夹具应具有高精度的定位功能,能够确保工件在多次加工过程中的定位精度,提高产品的一致性。
(3) 操作简便:夹具应易于使用和维护,操作人员能够轻松快速地完成夹具的装夹和卸载等工作。
(4) 适应性强:夹具设计应考虑到不同类型、尺寸、形状的工件,能够满足不同加工需求。
(5) 安全可靠:夹具在设计时要考虑到安全因素,确保夹具在工作过程中不会对操作人员和机器设备造成伤害。
三、数控加工设备专用夹具设计的关键技术1. 夹具结构设计:夹具的结构设计是夹具设计的关键,它直接影响着夹具的使用效果和性能。
夹具的结构设计需要考虑到工件的形状、材料和加工工艺,以确保夹具能够紧固和定位工件,并能够稳定可靠地承受切削力和加工力。
2. 夹具定位设计:夹具的定位设计是夹具设计中的一个重要环节,它直接影响着夹具的重复定位精度和加工精度。
夹具的定位设计需要考虑到工件的定位点、定位方式和定位精度,以确保工件在多次加工过程中的定位精度。
3. 夹具力学分析:夹具的力学分析是夹具设计中必不可少的环节,它能够为夹具的结构设计和定位设计提供理论依据和参考。
通过夹具的力学分析可以了解夹具在加工过程中所承受的力和应力分布,为夹具的设计和优化提供依据。
立式数控加工中心的工装夹具设计和优化
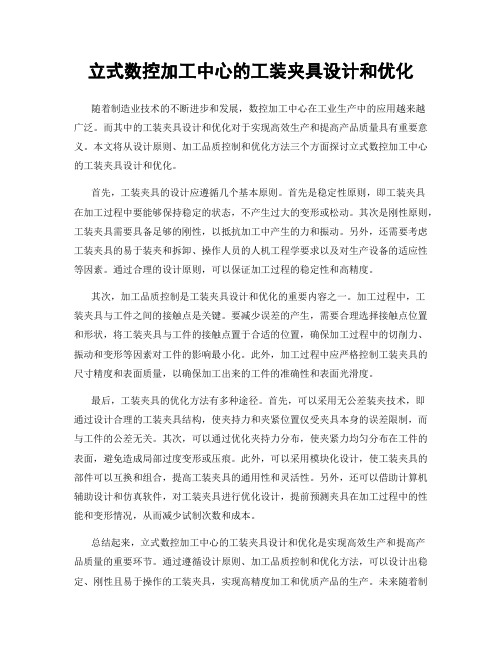
立式数控加工中心的工装夹具设计和优化随着制造业技术的不断进步和发展,数控加工中心在工业生产中的应用越来越广泛。
而其中的工装夹具设计和优化对于实现高效生产和提高产品质量具有重要意义。
本文将从设计原则、加工品质控制和优化方法三个方面探讨立式数控加工中心的工装夹具设计和优化。
首先,工装夹具的设计应遵循几个基本原则。
首先是稳定性原则,即工装夹具在加工过程中要能够保持稳定的状态,不产生过大的变形或松动。
其次是刚性原则,工装夹具需要具备足够的刚性,以抵抗加工中产生的力和振动。
另外,还需要考虑工装夹具的易于装夹和拆卸、操作人员的人机工程学要求以及对生产设备的适应性等因素。
通过合理的设计原则,可以保证加工过程的稳定性和高精度。
其次,加工品质控制是工装夹具设计和优化的重要内容之一。
加工过程中,工装夹具与工件之间的接触点是关键。
要减少误差的产生,需要合理选择接触点位置和形状,将工装夹具与工件的接触点置于合适的位置,确保加工过程中的切削力、振动和变形等因素对工件的影响最小化。
此外,加工过程中应严格控制工装夹具的尺寸精度和表面质量,以确保加工出来的工件的准确性和表面光滑度。
最后,工装夹具的优化方法有多种途径。
首先,可以采用无公差装夹技术,即通过设计合理的工装夹具结构,使夹持力和夹紧位置仅受夹具本身的误差限制,而与工件的公差无关。
其次,可以通过优化夹持力分布,使夹紧力均匀分布在工件的表面,避免造成局部过度变形或压痕。
此外,可以采用模块化设计,使工装夹具的部件可以互换和组合,提高工装夹具的通用性和灵活性。
另外,还可以借助计算机辅助设计和仿真软件,对工装夹具进行优化设计,提前预测夹具在加工过程中的性能和变形情况,从而减少试制次数和成本。
总结起来,立式数控加工中心的工装夹具设计和优化是实现高效生产和提高产品质量的重要环节。
通过遵循设计原则、加工品质控制和优化方法,可以设计出稳定、刚性且易于操作的工装夹具,实现高精度加工和优质产品的生产。
数控机床技术中的夹具设计与选择原则
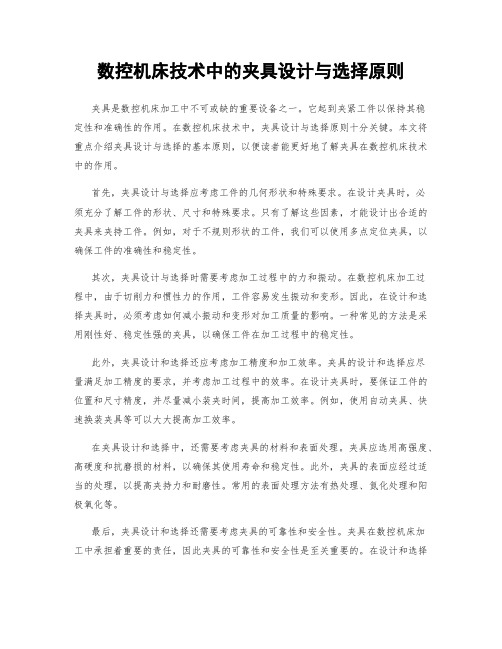
数控机床技术中的夹具设计与选择原则夹具是数控机床加工中不可或缺的重要设备之一。
它起到夹紧工件以保持其稳定性和准确性的作用。
在数控机床技术中,夹具设计与选择原则十分关键。
本文将重点介绍夹具设计与选择的基本原则,以便读者能更好地了解夹具在数控机床技术中的作用。
首先,夹具设计与选择应考虑工件的几何形状和特殊要求。
在设计夹具时,必须充分了解工件的形状、尺寸和特殊要求。
只有了解这些因素,才能设计出合适的夹具来夹持工件。
例如,对于不规则形状的工件,我们可以使用多点定位夹具,以确保工件的准确性和稳定性。
其次,夹具设计与选择时需要考虑加工过程中的力和振动。
在数控机床加工过程中,由于切削力和惯性力的作用,工件容易发生振动和变形。
因此,在设计和选择夹具时,必须考虑如何减小振动和变形对加工质量的影响。
一种常见的方法是采用刚性好、稳定性强的夹具,以确保工件在加工过程中的稳定性。
此外,夹具设计和选择还应考虑加工精度和加工效率。
夹具的设计和选择应尽量满足加工精度的要求,并考虑加工过程中的效率。
在设计夹具时,要保证工件的位置和尺寸精度,并尽量减小装夹时间,提高加工效率。
例如,使用自动夹具、快速换装夹具等可以大大提高加工效率。
在夹具设计和选择中,还需要考虑夹具的材料和表面处理。
夹具应选用高强度、高硬度和抗磨损的材料,以确保其使用寿命和稳定性。
此外,夹具的表面应经过适当的处理,以提高夹持力和耐磨性。
常用的表面处理方法有热处理、氮化处理和阳极氧化等。
最后,夹具设计和选择还需要考虑夹具的可靠性和安全性。
夹具在数控机床加工中承担着重要的责任,因此夹具的可靠性和安全性是至关重要的。
在设计和选择夹具时,应注意夹具的稳定性和可调性,并采取必要的安全措施,以防止夹具松脱或工件脱离夹具导致的事故。
综上所述,夹具设计与选择原则是数控机床技术中至关重要的一环。
合理的夹具设计和选择可以提高工件的加工精度和效率,保证加工质量和安全性。
同时,夹具的材料和表面处理也决定了夹具的使用寿命和稳定性。
机床夹具设计步骤和实例

第2节机床夹具设计实例一、钻夹具的设计实例图2-2-20所示为杠杆类零件图样;图2-2-21所示为本零件工序图;1.零件本工序的加工要求分析①钻、扩、铰φ10H9孔及φ11孔;②φ10H9孔与φ28H7孔的距离为80±0. 2mm;平行度为;③φ11孔与φ28H7孔的距离为15±0. 25mm;④φ11孔与端面K距离为14mm;本工序前已加工的表面如下;①φ28H7孔及两端面;②φ10H9两端面;本工序使用机床为Z5125立钻,刀具为通用标准工具;2.确定夹具类型本工序所加工两孔φ10H9和φ11,位于互成90°的两平面内,孔径不大,工件质量较小、轮廓尺寸以及生产量不是很大,因此采用翻转式钻模;3.拟定定位方案和选择定位元件1定位方案;根据工件结构特点,其定位方案如下;①以φ28H7孔及一组合面端面K和φ10H9一端面组合而成为定位面,以φ10H9孔端外缘毛坯面一侧为防转定位面,限制六个自由度;这一定位方案,由于尺寸885.0mm公差大,定位不可靠,会引起较大的定位误差;如图2-2-22a②以孔φ28H7孔及端面K 定位,以φ11孔外缘毛坯一侧为防转定位面,限制工件六个自由度;为增加刚性,在φ10H9的端面增设一辅助支承,如图2-2-22 b 所示;比较上述两种定位方案,初步确定选用图2-2-22b 所示的方案; 2选择定位元件;①选择带台阶面的定位销,作为以φ28H7孔及其端面的定位元件,如图2-2-23所示;定位副配合取6728g H φ;②选择可调支承钉为φ11孔外缘毛坯一侧防转定位面的定位元件,如图2-2-24a 所示;也可选择如图2-2-24 b 所示移动V 形块;考虑结构简单,现选用图2-2-24a 所示结构;3定位误差计算①加工φ10H9孔时孔距尺寸80±mm 的定位误差计算;由于基准重合,故ΔB =0;基准位移误差为定位孔φ38021.00+mm 与定位销φ38007.0002.0--mm 的最大间隙,故ΔY=+0. 007+mm =;由此可知此定位方案能满足尺寸80±mm 的定位要求; ②加工φ10H9孔时轴线平行度的定位误差计算; 由于基准重合,故ΔB =0;基准位移误差是定位孔φ28H7与定位面K 间的垂直度误差;故ΔY =0.此方案能满足平行度0. 3mm 的定位要求;③加工φ11孔时孔距尺寸15±mm;加工φ11孔时与加工φ10H9孔时相同;此方案能满足孔距15± mm 的定位要求; 4.确定夹紧方案参考夹具资料,采用M12螺杆在φ28H7孔上端面夹紧工件; 5.确定引导元件钻套的类型及结构尺寸 ⑴对φH9孔,为适应钻、铰选用快换钻套;主要尺寸由机床夹具零、部件国家标准GB/T2263-80, GB/T2265-80选取;钻孔时钻套内径φ10028.0013.0++mm 、外径φ15012.0001.0++mm ;衬套内径φ15034.0014.0++mm,衬套外径φ22028.0015.0++mm;钻套端面至加工面的距离取8mm;麻花钻选用φ9. 80022.0-mm;2对φ11孔,钻套采用快换钻套;钻孔时钻套内径φ11034.0016.0++mm 、外径φ18012.0001.0++mm,衬套内径φ18034.0016.0++mm,外径φ26028.0015.0++mm ;钻套端面至加工面间的距离取12mm;麻花钻选用φ10. 80027.0-mm;各引导元件至定位元件间的位置尺寸分别为15±mm 和18±0. 05mm,各钻套轴线对基面的直线度允差为;6.夹具精度分析与计算由图2-2-22可知,所设计夹具需保证的加工要求有:尺寸15±mm ;尺寸80±mm ;尺寸14mm 及φ10H9孔和φ28H7孔轴线间平行度允差等四项;除尺寸14mm,因精度要求较低不必进行验算外,其余三项精度分别验算如下;1尺寸80±mm的精度校核;定位误差ΔD,由前已计算,已知Δ=;定位元件对底面的垂直度误差ΔA=;钻套与衬套间的最大配合间隙ΔT1=0. 033mm;衬套孔的距离公差ΔT2=;麻花钻与钻套内孔的间隙X2=;衬套轴线对底面F的垂直度误差ΔT3=0. 05mm;因而该夹具能保证尺寸80±0. 2mm的加工要求;2尺寸15±0. 25mm的精度校核;ΔD=0. 041mm,ΔA=0. 03mm,ΔT1=0. 033mm;衬套孔与定位元件的距离误差ΔT2=;麻花钻与钻套内孔的间隙X=;因而尺寸15±mm能够保证;3φ10H9轴线对φ25H7轴线的平行度的精度校核;ΔD=0. 03mm,ΔA=0. 03mm;衬套对底面F的垂直度误差ΔT=0. 05mm;因而此夹具能保证两孔轴线的平行度要求;7.绘制夹具总图根据已完成的夹具结构草图,进一步修改结构,完善视图后,绘制正式夹具总装图,如图2-2-23所示;8.绘制夹具零件图样从略;9.编写设计说明书 从略;二、铣床夹具设计实例图2-2-25所示为轴套类零件的零件图样;现需设计铣两槽52.00+mm 的铣夹具;1.零件本工序的加工要求分析本工序的加工要求,在实体上铣出两通槽,槽宽为52.00+mm,槽深为2703.0-mm,两槽在圆周方向互成60°±30′角度,表面粗糙度为Ra1. 25μm;本工序之前,外圆φ60021.0002.0++mm 、内孔φ32039.00+mm 及两端面均已加工完毕; 本工序采用φ5mm 标准键槽铣刀在X5l 立式铣床上,一次装夹六件进行加工; 2.确定夹具类型本工序所加工的是两条在圆周互成60°角的纵向槽,因此宜采用直线进给带分度装置的铣夹具;3.拟定定位方案和选择定位元件 1定位方案;①以φ32039.00+mm 内孔作为定位基准,再选孔端面为定位基准,限制工件五个自由度;如图2-2-26a 所示;为定②以φ60021.0002.0++mm 外圆位基准 以长V 形块为定位元件,限制4个自由度;如图2-2-26 b 所示;方案②由于V 形块的特性,所以较易保证槽的对称度要求,但对于实现多件夹紧和分度较困难;方案①的不足之处是由于心轴与孔之间有间隙、不易保证槽的对称度,且有过定位现象;但本工序加工要求井不高,而工件孔和两端面垂直精度又较高,故过定位现象影响不大;经上述分析比较,确定采用方案①;2选择定位元件;根据定位方式,采用带台肩的心轴;心轴安装工件部分的直径为φ32g6009.0025.0--mm,考虑同时安装6个工件,所以这部分长度取112mm,由于分度精度不高,为简化结构,在心轴上做出六方头,其相对两面间的距离尺寸取28g6007.0020.0+-mm,与固定在支座上的卡块槽28H7021.00+mm 相配合;加工完毕一个槽后,松开并取下心轴,转过相邻的一面再嵌入卡块槽内即实现分度;心轴通过两端φ25H6mm 柱部分安装在支座的V 形槽上,并通过M16螺栓钩形压板及锥面压紧,压紧力的方向与心轴轴线成45°角;mm 定位误差分析如下;3定位误差计算;工序尺寸270-5.0由于基准重合ΔB=0由于定位孔与心轴为任意边接触,则因此定位精度足够;由于加工要求不高,其他精度可不必计算;4.确定夹紧方案根据图2-2-26所示心轴结构,用M30螺母把工件轴向夹紧在心轴上;心轴的具体结构如图2-2-27所示;5.确定对刀装置1根据加工要求,采用GB/T2242-80直角对刀块;塞尺符合GB/T2244-mm;80,基本尺寸及偏差20014-.02计算对刀尺寸H和B如图2-2-28所示,计算时应把尺寸化为双向对称偏差,即6.夹具精度分析和计算本夹具总图上与工件加工精度直接有关的技术要求如下;定位心轴表面尺寸φ32g6;定位件与对刀间的位置尺寸±mm,±mm;定位心轴安装表面尺寸φ25h6;mm;对刀塞尺厚度尺寸20-014.0分度角度60°±10′;定位心轴轴线与夹具安装面、定位键侧平面间的平行度公差为0. lmm;分度装置工作表面对定位表面的对称度公差为0. 07mm;分度装置工作表面对夹具安装面垂直度公差为;对刀装置工作表面对夹具安装面的平行度和垂直度公差为0. 07mm;mm的精度分析;1尺寸270-5.0ΔD=0. 064mm定位误差前已计算;ΔT=0. 16mm定位件至对刀块间的尺寸公差;ΔA=1.0×20mm=定位心轴轴线与夹具底面平行度公差对工件尺寸的影233响;mm尺寸;故此夹具能保证270-5.02对60°±30′的精度分析;分度装置的转角误差可按下式计算;故此分度装置能满足加工精度要求;7.绘制夹具总图图2-2-27所示为本夹具的总装图样;8.绘制夹具零件图样从略;9.编写设计说明书从略;。
剖析数控立车的装夹装置与装夹设计事项

剖析数控立车的装夹装置与装夹设计事项数控立车的夹头被称之为弹性夹头或者是筒夹。
是一种用来装置在立车上的一种用来紧固钻头是一种筒形的夹具。
也是一种用来固定加固需要改造的零件的一种固定装置。
数控车床夹头也是具有相同的特性,其作用也是为了紧固和夹持相应的工件。
数控立车的夹头的三大重要参数是精度、夹持力和夹持范围。
精度是用来掌控夹持柄类工具的跳动量,以保证加工孔的精度。
夹持力是为了保证夹持的柄类工具不打滑,防止由于柄类工具的打滑而无法工作。
一般情况下用于台钻上的夹头精度要求高一些,而用于手电钻上的夹头精度相对低一些。
夹持范围是用来掌控夹头夹持工具最小和的直径,以便充足工作需要。
正常情况下,夹持范围只比夹头的规格大0.5mm左右即可。
假如超的过大,将大大挥霍材料,提高夹头的生产成本。
最小夹持范围理论上是可以做到很小,但是过小将使生产厂家的废品率上升,加添成本。
所以综合各方面情况,将6、10、13、16、20mm的夹头的夹持范围定为0.8—6、0.8—10、1.5—13、3—16、5—20比较合理。
现代多而杂的制造环境中,大多数工厂都经过严格的培训、认真的学习一些新设备的加工及运动原理、架构特点和使用技巧,只有这样才能便利操作。
特别是对一些较的技术体系更是如此,就比如在好多机床方面都会应用到夹头,它具有弹性,因此也叫作弹性夹头,是一种用来固定一些零件的固定装置。
它的种类也可以分为很多类,比如气动夹头,常见的弹簧夹头,夹紧夹头等。
虽然很小巧,但是在机械运动中却发挥着很大的作用,如一些机器内部的阀门弹簧,还有汽车离合器里面的掌控弹簧,它们能掌控机械的运动。
另外还有缓冲弹簧,它是存在于一些由于运动会产生力的装置内部,它的作用就是能够汲取产生的震动和撞击的能量。
在一些较为精致的机械物品里的钟表弹簧,它能够储存和把输出的能量转换为动力。
现在的时代也是一个机械时代,各种机械的加工及制造也越来越脱离了原有的局限,更加的新奇和有效。
数控加工专用卡爪夹具设计
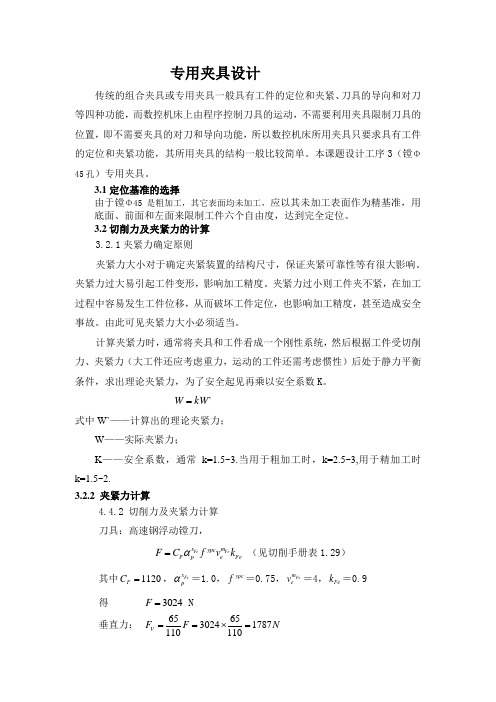
专用夹具设计传统的组合夹具或专用夹具一般具有工件的定位和夹紧、刀具的导向和对刀等四种功能,而数控机床上由程序控制刀具的运动,不需要利用夹具限制刀具的位置,即不需要夹具的对刀和导向功能,所以数控机床所用夹具只要求具有工件的定位和夹紧功能,其所用夹具的结构一般比较简单。
本课题设计工序3(镗Φ45孔)专用夹具。
3.1定位基准的选择由于镗Φ45是粗加工,其它表面均未加工,应以其未加工表面作为精基准,用底面、前面和左面来限制工件六个自由度,达到完全定位。
3.2切削力及夹紧力的计算 3.2.1夹紧力确定原则夹紧力大小对于确定夹紧装置的结构尺寸,保证夹紧可靠性等有很大影响。
夹紧力过大易引起工件变形,影响加工精度。
夹紧力过小则工件夹不紧,在加工过程中容易发生工件位移,从而破坏工件定位,也影响加工精度,甚至造成安全事故。
由此可见夹紧力大小必须适当。
计算夹紧力时,通常将夹具和工件看成一个刚性系统,然后根据工件受切削力、夹紧力(大工件还应考虑重力,运动的工件还需考虑惯性)后处于静力平衡条件,求出理论夹紧力,为了安全起见再乘以安全系数K 。
`kW W =式中W`——计算出的理论夹紧力;W ——实际夹紧力;K ——安全系数,通常k=1.5~3.当用于粗加工时,k=2.5~3,用于精加工时k=1.5~2. 3.2.2 夹紧力计算4.4.2 切削力及夹紧力计算 刀具:高速钢浮动镗刀,Fe Fe x m ypc F p e Fe F C f v k α= (见切削手册表1.29) 其中1120F C =,Fe x p α=1.0,ypcf=0.75,Fe m e v =4,Fe k =0.9得 3024F = N 垂直力: 656530241787110110V F F N ==⨯=在计算时,必须考虑安全系数,1234K K K K K = 由(切削手册表1.29~1.35)可知1 1.5K =2 1.1K =3 1.1K =4 1.1K =所以,1234 1.5 1.1 1.1 1.1K K K K K ==⨯⨯⨯=1.9965' 1.996517873573F KF N ==⨯= 3.3夹具设计及操作的简要说明如前所述,在设计夹具时,应注意提高劳动生产率。
数控加工设备专用夹具设计探究
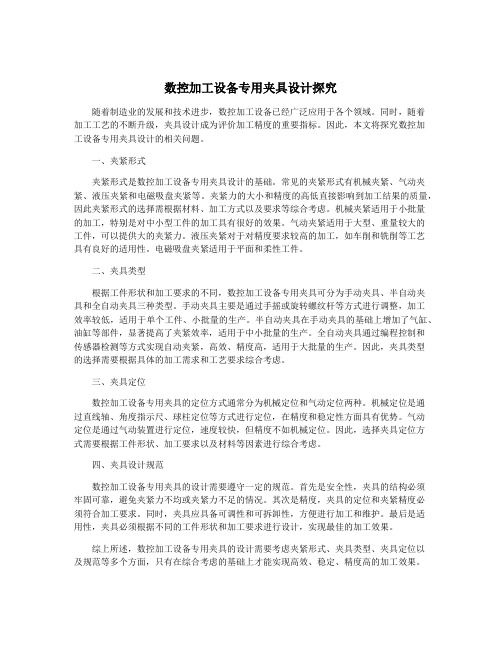
数控加工设备专用夹具设计探究随着制造业的发展和技术进步,数控加工设备已经广泛应用于各个领域。
同时,随着加工工艺的不断升级,夹具设计成为评价加工精度的重要指标。
因此,本文将探究数控加工设备专用夹具设计的相关问题。
一、夹紧形式夹紧形式是数控加工设备专用夹具设计的基础。
常见的夹紧形式有机械夹紧、气动夹紧、液压夹紧和电磁吸盘夹紧等。
夹紧力的大小和精度的高低直接影响到加工结果的质量,因此夹紧形式的选择需根据材料、加工方式以及要求等综合考虑。
机械夹紧适用于小批量的加工,特别是对中小型工件的加工具有很好的效果。
气动夹紧适用于大型、重量较大的工件,可以提供大的夹紧力。
液压夹紧对于对精度要求较高的加工,如车削和铣削等工艺具有良好的适用性。
电磁吸盘夹紧适用于平面和柔性工件。
二、夹具类型根据工件形状和加工要求的不同,数控加工设备专用夹具可分为手动夹具、半自动夹具和全自动夹具三种类型。
手动夹具主要是通过手摇或旋转螺纹杆等方式进行调整,加工效率较低,适用于单个工件、小批量的生产。
半自动夹具在手动夹具的基础上增加了气缸、油缸等部件,显著提高了夹紧效率,适用于中小批量的生产。
全自动夹具通过编程控制和传感器检测等方式实现自动夹紧,高效、精度高,适用于大批量的生产。
因此,夹具类型的选择需要根据具体的加工需求和工艺要求综合考虑。
三、夹具定位数控加工设备专用夹具的定位方式通常分为机械定位和气动定位两种。
机械定位是通过直线轴、角度指示尺、球柱定位等方式进行定位,在精度和稳定性方面具有优势。
气动定位是通过气动装置进行定位,速度较快,但精度不如机械定位。
因此,选择夹具定位方式需要根据工件形状、加工要求以及材料等因素进行综合考虑。
四、夹具设计规范数控加工设备专用夹具的设计需要遵守一定的规范。
首先是安全性,夹具的结构必须牢固可靠,避免夹紧力不均或夹紧力不足的情况。
其次是精度,夹具的定位和夹紧精度必须符合加工要求。
同时,夹具应具备可调性和可拆卸性,方便进行加工和维护。
数控加工设备专用夹具设计探究

数控加工设备专用夹具设计探究
数控加工设备专用夹具是一种用于固定工件和刀具的装置,它通过夹持工件,保持其稳定性和精度,使得数控加工设备能够准确地进行加工。
夹具的设计对于加工质量和效率起着至关重要的作用。
本文将探究数控加工设备专用夹具的设计。
数控加工设备专用夹具的设计需要考虑工件的形状和尺寸。
夹具的设计应该与工件的特点相匹配,以确保工件能够被安全、稳定地夹持。
对于形状复杂的工件,可以采用可调节的夹具设计,以适应不同尺寸和形状的工件。
夹具的设计还需要考虑工件的加工要求。
不同的工件需要不同的夹持方式,以满足其加工要求。
对于需要进行多边加工的工件,可以设计成多面夹具,以保证加工精度和稳定性。
夹具的设计还需要考虑加工工艺和刀具的选择。
夹具的设计应该考虑到加工工艺的要求,以便提供适当的工作空间和夹持力。
夹具的设计还应该考虑到刀具的选择,以确保夹具可以容纳不同类型和尺寸的刀具,并保持刀具与工件的正确定位。
夹具的设计也需要考虑到操作人员的需求。
设计人员应该考虑到夹具的易用性和安全性,以便操作人员能够方便地夹持和调整工件,同时保证操作人员的安全。
夹具的材料选择也是设计的一个重要方面。
夹具需要使用耐磨、耐腐蚀的材料,以确保其使用寿命和稳定性。
夹具的材料选择还应考虑到其与加工过程中产生的高速切削力的相容性。
数控加工设备专用夹具的设计是一个复杂的过程,需要考虑多个因素。
只有设计人员在考虑到工件的形状和尺寸、加工要求、加工工艺、刀具选择、操作人员需求和材料选择等多个方面时,才能设计出适合的夹具,从而确保加工质量和效率。
数控机床夹具的设计与制造

数控机床夹具的设计与制造数控技术的广泛应用,促进了数控机床的快速发展,给制造业发展带来了很大的便利。
作为数控加工的关键板块,数控机床夹具更是发挥着重要作用。
正确的设计和制造数控机床夹具,不仅可以提高加工效率,降低成本,还可以提高产品的质量和精度。
那么,如何进行数控机床夹具的设计和制造呢?一、夹具设计在夹具的设计中,关键步骤为工作原理的确定和夹具的工作方式的选择。
对于机床夹具的设计,在考虑表面损耗和使用寿命的前提下,主要考虑以下几点:1.夹紧力的确定夹具的夹紧力度直接影响产品的加工精度和质量。
夹紧力大小要根据所加工的产品情况和工艺规定灵活设置,夹紧力不宜过大或过小。
2.结构形式的选择数控机床夹具的结构形式可以根据产品形状和特点来选择不同的结构形式。
常见的有钳子夹具、卡盘夹具、万向夹具和手柄夹具等。
二、夹具制造制造夹具需要在夹具设计之后,进行制造流程规划和夹具加工工艺的制定。
现代夹具制造已经采用高效的加工工艺,包括数控加工、电化学加工、电火花加工和激光加工等。
夹具制造的关键要素包括夹具板材的选择、制造夹具的顺序和夹具部件的制造。
1.夹具板材的选择通常数控夹具板材的选择包括钢板、铝板和铜板等。
不同板材的加工方法和选择都会直接影响到夹具的质量和使用寿命,因此对板材的质量和规格要求也很高。
2.顺序制造在数控夹具的制造中,先制造夹具的核心部件,例如夹爪和夹持口等,然后制造夹具的支架。
最后安装好所有部件即可。
3.夹具部件制造制造夹具的各个部件的过程中,需要注意以下几方面的问题:①夹爪加工:需要掌握夹爪加工的基本知识和配合加工的技术。
②制造夹紧口:夹紧口的制造应尽可能保持精度和平衡性,在制造时应注重提高加工技术。
③方便操作:夹具的操作方便性和快捷性也是制造过程中必须考虑到的。
夹具的精度显然是一个重要的问题,所以制造加工夹具的过程中需要非常注重精度和质量的控制。
夹具制造并非简单的加工过程,需要制造者具备丰富的技术经验和精准的加工技能。
数控立车专用夹具设计
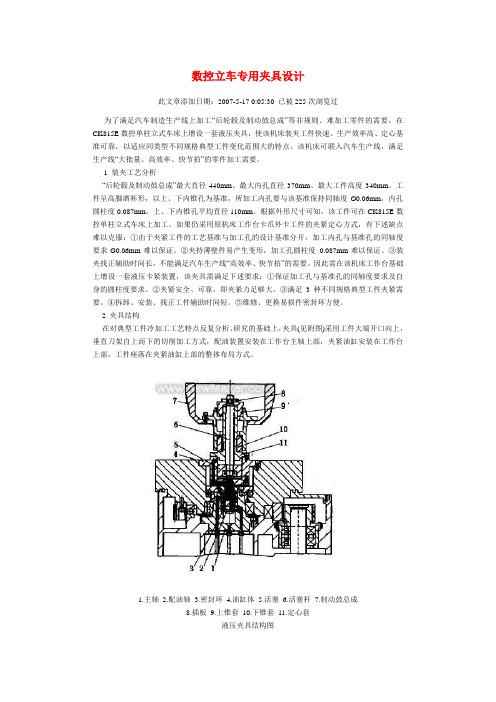
数控立车专用夹具设计此文章添加日期:2007-5-17 0:05:30 已被225次浏览过为了满足汽车制造生产线上加工“后轮毂及制动鼓总成”等非规则、难加工零件的需要,在CK815E数控单柱立式车床上增设一套液压夹具,使该机床装夹工件快速、生产效率高、定心基准可靠,以适应同类型不同规格典型工件变化范围大的特点。
该机床可联入汽车生产线,满足生产线“大批量、高效率、快节拍”的零件加工需要。
1 装夹工艺分析“后轮毂及制动鼓总成”最大直径440mm、最大内孔直径370mm、最大工件高度340mm。
工件呈高脚酒杯形,以上、下内锥孔为基准,所加工内孔要与该基准保持同轴度Ø0.06mm,内孔圆柱度0.087mm,上、下内锥孔平均直径110mm。
根据外形尺寸可知,该工件可在CK815E数控单柱立式车床上加工。
如果仍采用原机床工作台卡爪外卡工件的夹紧定心方式,有下述缺点难以克服:①由于夹紧工件的工艺基准与加工孔的设计基准分开,加工内孔与基准孔的同轴度要求Ø0.06mm难以保证。
②夹持薄壁件易产生变形,加工孔圆柱度0.087mm难以保证。
③装夹找正辅助时间长,不能满足汽车生产线“高效率、快节拍”的需要。
因此需在该机床工作台基础上增设一套液压卡紧装置,该夹具需满足下述要求:①保证加工孔与基准孔的同轴度要求及自身的圆柱度要求。
②夹紧安全、可靠,即夹紧力足够大。
③满足3种不同规格典型工件夹紧需要。
④拆卸、安装、找正工件辅助时间短。
⑤维修、更换易损件密封环方便。
2 夹具结构在对典型工件冷加工工艺特点反复分析、研究的基础上,夹具(见附图)采用工件大端开口向上,垂直刀架自上而下的切削加工方式,配油装置安装在工作台主轴上部,夹紧油缸安装在工作台上部,工件座落在夹紧油缸上部的整体布局方式。
1.主轴2.配油轴3.密封环4.油缸体5.活塞6.活塞杆7.制动鼓总成8.插板9.上锥套10.下锥套11.定心套液压夹具结构图该夹具布局方式有如下特点:①满足了典型工件加工内孔精度的要求。
- 1、下载文档前请自行甄别文档内容的完整性,平台不提供额外的编辑、内容补充、找答案等附加服务。
- 2、"仅部分预览"的文档,不可在线预览部分如存在完整性等问题,可反馈申请退款(可完整预览的文档不适用该条件!)。
- 3、如文档侵犯您的权益,请联系客服反馈,我们会尽快为您处理(人工客服工作时间:9:00-18:30)。
数控立车专用夹具设计
此文章添加日期:2007-5-17 0:05:30 已被225次浏览过
为了满足汽车制造生产线上加工“后轮毂及制动鼓总成”等非规则、难加工零件的需要,在CK815E数控单柱立式车床上增设一套液压夹具,使该机床装夹工件快速、生产效率高、定心基准可靠,以适应同类型不同规格典型工件变化范围大的特点。
该机床可联入汽车生产线,满足生产线“大批量、高效率、快节拍”的零件加工需要。
1 装夹工艺分析
“后轮毂及制动鼓总成”最大直径440mm、最大内孔直径370mm、最大工件高度340mm。
工件呈高脚酒杯形,以上、下内锥孔为基准,所加工内孔要与该基准保持同轴度Ø0.06mm,内孔圆柱度0.087mm,上、下内锥孔平均直径110mm。
根据外形尺寸可知,该工件可在CK815E数控单柱立式车床上加工。
如果仍采用原机床工作台卡爪外卡工件的夹紧定心方式,有下述缺点难以克服:①由于夹紧工件的工艺基准与加工孔的设计基准分开,加工内孔与基准孔的同轴度要求Ø0.06mm难以保证。
②夹持薄壁件易产生变形,加工孔圆柱度0.087mm难以保证。
③装夹找正辅助时间长,不能满足汽车生产线“高效率、快节拍”的需要。
因此需在该机床工作台基础上增设一套液压卡紧装置,该夹具需满足下述要求:①保证加工孔与基准孔的同轴度要求及自身的圆柱度要求。
②夹紧安全、可靠,即夹紧力足够大。
③满足3种不同规格典型工件夹紧需要。
④拆卸、安装、找正工件辅助时间短。
⑤维修、更换易损件密封环方便。
2 夹具结构
在对典型工件冷加工工艺特点反复分析、研究的基础上,夹具(见附图)采用工件大端开口向上,垂直刀架自上而下的切削加工方式,配油装置安装在工作台主轴上部,夹紧油缸安装在工作台上部,工件座落在夹紧油缸上部的整体布局方式。
1.主轴
2.配油轴
3.密封环
4.油缸体
5.活塞
6.活塞杆
7.制动鼓总成
8.插板9.上锥套10.下锥套11.定心套
液压夹具结构图
该夹具布局方式有如下特点:①满足了典型工件加工内孔精度的要求。
上锥套9、下锥套10的锥面角度按典型工件内孔实际锥度配磨,保证接触率达到80%以上,夹具与工作台之间的定心止口高精度配合,工作台中心孔装配自车。
通过上述措施使得工件加工内孔中心,工件上下内锥基准孔中心,工作台回转中心保持一致,保证了工件加工内孔与基准孔之间的同轴度要求及工件内孔的圆柱度要求。
②夹紧安全可靠。
由于夹紧油缸布置在工作台上部,充分利用了工作台中心孔的空间,可以选择到理想的夹紧油缸直径以满足夹紧力的需要。
上、下锥套9、10部分开有槽口,当压紧时斜面能较紧密地压合在工件的斜面上,增加摩擦力。
③可以满足3种不同规格典型工件的夹紧需要。
该夹具共设计了3套上、下锥套9和10,可方便地更换以满足夹紧不同工件的需要。
④拆卸、安装、找正工件的辅助时间短。
工件夹紧时在液压阀控制下,油缸上端通有压力油,活塞拉杆6拉紧上锥套9把工件牢固地固定在定心套11上;工件放松时,油缸下端来油,活塞拉杆向上运动,将上锥套9同时顶出,拆下上锥套9上面的马蹄形插板8,拔出上锥套9,此时可拆卸工件。
由于该夹具采用了自动定心内夹工件的夹紧方式,缩短了安装、找正工件的辅助时间。
⑤维修机床方便。
由于该夹具布置在工作台下部,可方便地更换易损件密封环。
另外,配油装置与油缸体间距小,配油轴悬臂短,回转时径向跳动小,相对延长了密封环的使用寿命。
⑥机床主轴即为配油装置的配油体,提高了主轴刚度,使管路联结更加简单,油缸上端盖即为定心套,油缸体通过定心止口直接把合在工作台上。
通过上述巧妙的设计,提高了该夹具的定心精度,满足了零件的加工精度要求。
3 设计计算
1) 切削力和切削扭矩的计算
a. 切削力Pz
Pz= CPz·tXPz·S YPz·KµPz (N)
式中t——切削深度,mm。
t=1.5mm
s——进给量,mm/r。
s=0.8mm/r
典型工件为铸铁件,采用硬质合金刀具车削内孔,查取各项系数为:CPz=902,XPz=1,YPz=0.75,KµPz=1,代入式(1)得Pz=1145N。
b. 最大切削扭矩M切
M切=Pz*D工件/2
式中D工件——工件内孔最大加工直径,D工件=0.37m
代入式(2)得M切=211.8N·m。
2) 活塞杆拉力F拉和油缸直径D油缸的计算
a. 摩擦扭矩M摩取M摩=S·M切
式中S——安全系数,S=1.3
代入式(3)得M摩=275.34N·m。
b. 锥面摩擦力F摩
F摩= (M摩/2 )/(D锥/2)
式中D锥——锥面平均直径,D锥=0.11m
代入式(4)得F摩=2503N。
c. 活塞杆拉力F拉
F拉= F摩/ sinα·µ
式中α——锥面角度,α=30°µ——摩擦系数,µ=0.15
代入式(5)得F拉=33373N。
d. 油缸直径D油缸
D油缸=[ 4F拉/πP+d杆2]½
式中d杆——活塞杆直径,经计算取d杆=0.04m
P——压力油压力,P=3.5×106N/m2
代入式(6)得D油缸=0.1172m。
设计中取油缸直径D油缸=0.12m。
在D油缸=0.12m时,M摩=284N·m。
M摩>M切。
该夹具与原机床一起装配、试切工件成功,顺利出厂,现已联结在汽车生产线上,正式投入生产使用,得到用户一致好评。
机床夹具发展趋势
此文章添加日期:2007-5-17 0:03:01 已被312次浏览过
夹具是机械加工不可缺少的部件,在机床技术向高速、高效、精密、复合、
智能、环保方向发展的带动下,夹具技术正朝着高精、高效、模块、组合、通用、
经济方向发展。
一、高精
随着机床加工精度的提高,为了降低定位误差,提高加工精度,对夹具的制造精度要求更高。
高精度夹具的定位孔距精度高达±5μm,夹具支承面的垂直度达到0.01mm/300mm,平行度高达0.01mm/500mm。
德国demmeler(戴美乐)公司制造的4m长、2m宽的孔系列组合焊接夹具平台,其等高误差为±0.03mm;精密平口钳的平行度和垂直度在5μm以内;夹具重复安装的定位精度高达±5μm;瑞士EROWA柔性夹具的重复定位精度高达2~5μm。
机床夹具的精度已提高到微米级,世界知名的夹具制造公司都是精密机械制造企业。
诚然,为了适应不同行业的需求和经济性,夹具有不同的型号,以及不同档次的精度标准供选择。
二、高效
为了提高机床的生产效率,双面、四面和多件装夹的夹具产品越来越多。
为了减少工件的安装时间,各种自动定心夹紧、精密平口钳、杠杆夹紧、凸轮夹紧、气动和液压夹紧等,快速夹紧功能部件不断地推陈出新。
新型的电控永磁夹具,加紧和松开工件只用1~2秒,夹具结构简化,为机床进行多工位、多面和多件加工创造了条件。
为了缩短在机床上安装与调整夹具的时间,瑞典3R夹具仅用1分钟,即可完成线切割机床夹具的安装与校正。
采用美国Jergens(杰金斯)公司的球锁装夹系统,1分钟内就能将夹具定位和锁紧在机床工作台上,球锁装夹系统用于柔性生产线上更换夹具,起到缩短停机时间,提高生产效率的作用。
三、模块、组合
夹具元件模块化是实现组合化的基础。
利用模块化设计的系列化、标准化夹具元件,快速组装成各种夹具,已成为夹具技术开发的基点。
省工、省时,节材、节能,体现在各种先进夹具系统的创新之中。
模块化设计为夹具的计算机辅助设计与组装打下基础,应用CAD技术,可建立元件库、典型夹具库、标准和用户使用档案库,进行夹具优化设计,为用户三维实体组装夹具。
模拟仿真刀具的切削过程,既能为用户提供正确、合理的夹具与元件配套方案,又能积累使用经验,了解市场需求,不断地改进和完善夹具系统。
组合夹具分会与华中科技大学合作,正在着手创建夹具专业技术网站,为夹具行业提供信息交流、夹具产品咨询与开发的公共平台,争取实现夹具设计与服务的通用化、远程信息化和经营电子商务化。
四、通用、经济
夹具的通用性直接影响其经济性。
采用模块、组合式的夹具系统,一次性投资比较大,只有夹具系统的可重组性、可重构性及可扩展性功能强,应用范围广,通用性好,夹具利用率高,收回投资快,才能体现出经济性好。
德国demmeler(戴美乐)公司的孔系列组合焊接夹具,仅用品种、规格很少的配套元件,即能组装成多种多样的焊接夹具。
元件的功能强,使得夹具的通用性好,元件少而精,配套的费用低,经济实用才有推广应用的价值。
专家们建议组合夹具行业加强产、学、研协作的力度,加快用高新技术改造和提升夹具技术水平的步伐,创建夹具专业技术网站,充分利用现代信息和网络技术,与时俱进地创新和发展夹具技术。
主动与国外夹具厂商联系,争取合资与合作,引进技术,这是改造和发展我国组合夹具行业较为行之有效的途径。