热挤压凹模
挤压模具的分类

挤压模具的分类挤压模具是一种用于加工金属材料的工具,广泛应用于汽车、航空航天、家电等行业。
按照其结构和用途的不同,可以将挤压模具分为下面几类。
一、冷挤压模具冷挤压模具是指在室温下对金属材料进行挤压加工的模具。
它主要用于生产形状复杂、尺寸精度要求高的零部件,如汽车发动机缸套、铝合金管材等。
冷挤压模具通常由上下模和芯棒组成,通过挤压机将金属材料挤压至模具腔中,经过一系列工序完成加工。
二、热挤压模具热挤压模具是指在高温下对金属材料进行挤压加工的模具。
它主要用于生产大型、长尺寸的金属材料,如铝合金型材、铜管等。
热挤压模具一般由上下模和加热设备组成,通过加热后的金属材料在模具中受到挤压形成所需的截面形状。
三、异形挤压模具异形挤压模具是指用于加工非圆形或复杂形状的金属材料的模具。
它通常由多个模块组成,每个模块负责加工金属材料的一个特定区域。
异形挤压模具广泛应用于汽车车身、航空航天结构件等领域,能够有效提高生产效率和产品质量。
四、管材挤压模具管材挤压模具是指用于加工金属管材的模具。
它主要用于生产各种规格和形状的金属管材,如铝合金管、不锈钢管等。
管材挤压模具一般由多个模块组成,通过挤压机将金属材料挤压成所需的管状形状。
五、复合挤压模具复合挤压模具是指用于加工复合材料的模具。
它主要用于生产复合材料制品,如碳纤维板、玻璃钢制品等。
复合挤压模具通常由上下模和压板组成,通过挤压机将复合材料与增强材料挤压在一起形成所需的形状。
六、背吹挤压模具背吹挤压模具是指用于加工中空形状的模具。
它主要用于生产中空金属制品,如铝合金箱体、铜合金管等。
背吹挤压模具一般由上下模和背吹设备组成,通过背吹压力将金属材料挤压成所需的中空形状。
七、液压挤压模具液压挤压模具是指采用液压系统作为动力源的挤压模具。
它主要用于加工大型或高强度的金属材料,如船舶结构件、桥梁构件等。
液压挤压模具具有挤压力大、稳定性好的特点,能够满足对金属材料的高强度加工需求。
热挤压模具设计与制造基础

热挤压模具设计与制造基础
热挤压是一种常用的金属加工技术,其需要依靠高温和压力来将金属材料挤压成所需形状,这就需要使用热挤压模具。
热挤压模具的设计和制造是热挤压加工中至关重要的环节,直接关系到加工效率和成品质量。
以下是热挤压模具设计与制造的基础知识。
1. 热挤压模具的种类
热挤压模具根据其结构和用途可以分为以下几类:简单模具、复合模具、角模和弯头模。
简单模具和复合模具适用于各种简单形状的挤压件,角模适用于各种角度的挤压件,弯头模适用于弯曲形状的挤压件。
2. 热挤压模具的设计要点
热挤压模具的设计需要考虑以下因素:挤压形状、材料性质、挤压温度、挤压速度、挤压力度、模具材料、模具寿命等。
其中,最重要的是挤压形状和材料性质,这直接关系到成品质量。
3. 热挤压模具的制造技术
热挤压模具的制造需要采用高精度的加工技术和材料。
制造过程中需要注意以下几点:材料的选择和处理、模具结构的设计和加工、表面处理工艺、热处理工艺等。
这些因素直接影响到模具的精度、硬度和寿命。
总之,热挤压模具设计与制造是热挤压加工中不可或缺的环节。
只有加强对模具设计和制造的理解,才能提高热挤压加工的效率和产品质量。
铝型材热挤压模具标准
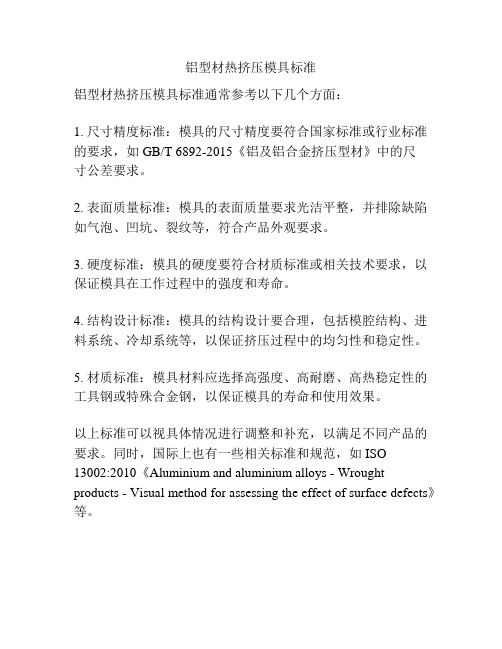
铝型材热挤压模具标准
铝型材热挤压模具标准通常参考以下几个方面:
1. 尺寸精度标准:模具的尺寸精度要符合国家标准或行业标准的要求,如GB/T 6892-2015《铝及铝合金挤压型材》中的尺
寸公差要求。
2. 表面质量标准:模具的表面质量要求光洁平整,并排除缺陷如气泡、凹坑、裂纹等,符合产品外观要求。
3. 硬度标准:模具的硬度要符合材质标准或相关技术要求,以保证模具在工作过程中的强度和寿命。
4. 结构设计标准:模具的结构设计要合理,包括模腔结构、进料系统、冷却系统等,以保证挤压过程中的均匀性和稳定性。
5. 材质标准:模具材料应选择高强度、高耐磨、高热稳定性的工具钢或特殊合金钢,以保证模具的寿命和使用效果。
以上标准可以视具体情况进行调整和补充,以满足不同产品的要求。
同时,国际上也有一些相关标准和规范,如ISO 13002:2010《Aluminium and aluminium alloys - Wrought products - Visual method for assessing the effect of surface defects》等。
热挤压——精选推荐

热挤压热挤压时加热温度在毛坯金属的再结晶温度以上,且是三向受压,主要用来制造普通等截面的长形件、棒、管、型材等。
很多材料都可以热挤。
常用的热挤压形式如图1所示。
挤压时,坯料放入挤压筒内,在挤压杆的作用下,当压力超过材料的抗力时,便通过模孔变形,从而获得所需工件的形状。
与冷、温挤相比,热挤时变形力小,变形量大,可挤出很复杂的断面。
但模具要求高,热工件表面粗糙度也大。
(a)深孔反挤压 (b)实心反挤压 (c)空心正挤压 (d)实心正挤压 (e)复合挤压 (f )可分凹模径向挤压1-挤压筒 2-凹模 3-挤压杆 4-挤压杆(凸模) 5-凹模 6-芯棒 7-凸模 8-凹模 9-凸模 10-可分凹模 11-凹模套图1 热挤压的各种形式挤压件可直接作为结构件或者切断后予以精加工作为机器零件。
表1为热挤压用材料和制件用途。
表1 热挤压用材料和制件用途1 挤压比与挤压金属流出速度(1)挤压比的计算与选择棒材挤压时的挤压比按下式计算:220d D m式中,D -挤压筒直径;d -挤压棒直径。
管材挤压时的挤压比按下式计算:()14220+--=s s d d D m式中,0D 、d -分别为挤压筒、挤压管材直径; s -挤压管材壁厚。
(2)挤压金属流出速度的选定热挤压时应变硬化和恢复再结晶软化共同决定了抗力和变形量。
常见的挤压速度列于表2。
表2 挤压金属流出速度挤压流出速度和变形程度等工艺参数最佳配合。
钛合金在700℃-1100℃范围内有足够高的塑性,但是它有粘结模具的倾向,因此要求挤压金属流出速度要大。
采用快速压力机和增加变形程度可增加金属流动速度,但增加变形程度与提高变形速度一样,会引起变形区的热量增加。
因此在低温下挤压重要零件时,对变形程度与流动速度应加以限制。
同时挤压流出速度的下限受毛坯在挤压筒中冷却的限制。
根据挤压变形条件的不同,金属流出速度以不小于500mm/s为宜,见表3。
对强度与塑性有相当高要求的重要零件,钛合金毛坯的加热温度必须在ββα⇔+转变点以下。
连接体热挤压工艺及模具设计
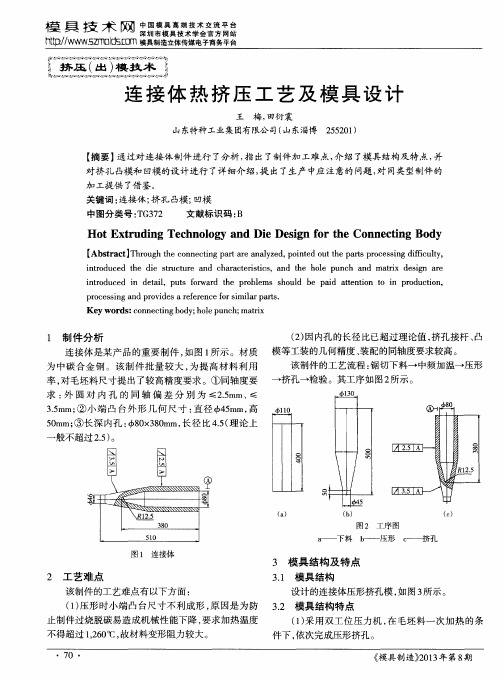
晷 技 网
嘉
连 接 体 热 挤 压 工 艺 及 模 具 设 计
蓄一
王 梅, 田衍震
一
} S P Y - 提供 了借 鉴 。
山东特种工业 集团有 限公 司( 山东淄博
Ho t Ex t r u d i n g T e c h n o l o g y a n d Di e De s i g n f o r t h e Co n n e c t i n g Bo d y
【 A b s t r a c t 】 T h r 0 u g h t h e c o n n e c t i n g p a r t a r e a n a l y z e d , p o i n t e d o u t t h e p a t r s p r o c e s s i n g d i ic f u l t y ,
该制件的工艺流程 : 锯切下料一 中频加温一压形
所示。 率, 对毛坯料尺寸提 出了较高精度要求 。① 同轴度要 一挤孔一检验 。其工序如图2 3 . 5 m m; ② 小端 凸台外形 几何 尺 寸 : 直径 ̄ b 4 5 m m, 高
5 0 m m; ③长深 内孔 :  ̄ b 8 0 x 3 8 0 m m, 长径 比4 . 5 ( 理论上
( 2 ) 因内孔的长径 比已超过理论值 , 挤孑 L 接杆 、 凸 l 制件 分 析 装配的同轴度要求较高。 连接体是某产品的重要制件 , 如图 1 所示。材质 模等工装的几何精度 、 为 中碳合金钢 。该制 件批量较 大 , 为提 高材料利用
求 : 外 圆 对 内 孔 的 同 轴 偏 差 分 别 为 ≤2 . 5 mm、≤
挤压工艺及模具 教学课件 贾俐俐 主编 第七章 热 挤 压
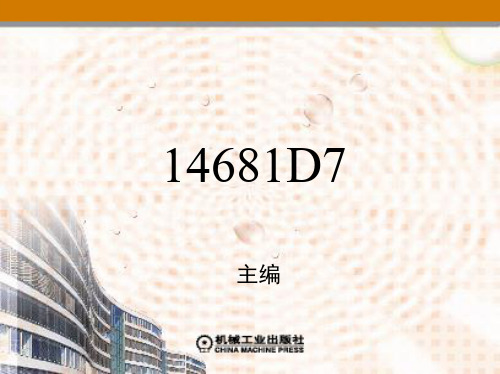
(1) 感应加热
图7-6 中频感应加热原理图
(2) 电阻炉加热
图7-7 电阻炉原理图
二、加热缺陷
1.氧化 钢在非保护性介质中加热时会产生氧化,在钢的表面 上生成氧化皮。 2.脱碳 钢在加热时,表面的碳与炉气中的氧结合,使表面层 含碳量降低,叫做脱碳。 3.过热 加热温度过高或在高温下停留时间过长而造成的奥氏 体晶粒过于粗大的现象,称为过热。 4.过烧 当钢加热到接近熔化温度,并在此温度长时间停留, 不但使奥氏体晶粒粗大,同时由于氧化性气体渗入到晶界使晶 间物质铁、碳和硫等发生氧化,形成易熔共晶体,使晶间联接 破坏,这种加热缺陷称为过烧。
一、坯料的加热方法 二、加热缺陷 三、热挤压温度范围的确定 四、钢的加热规范
一、坯料的加热方法
1.火焰加热 它是利用燃料在加热炉内燃烧产生含有大量热能 的高温气体(火焰),通过对流、辐射把热能传递给坯料表面, 通过由表及里的热传导而使金属坯料加热到预定的温度。 2.电加热 电加热是通过把电能转变为热能来加热金属坯料。
14681D7
主编
第七章 热 挤 压
第七章 热 挤 压
第一节 第二节 第三节 第四节 第五节 第六节 第七节 第八节
热挤压概述 热挤压件力的计算 热挤压件的冷却及热处理 热挤压件质量及力学性能
第一节 热挤压概述
1.热挤压工艺与冷挤压工艺相比,具有如下优点 2.与冷挤压工艺相比存在以下不足
二、挤压件图的绘制
1.冷挤压件图的绘制 冷挤压件图是在零件图的基础上考虑到 加工工艺、余量和公差而后绘制的。 2.热挤压件图的绘制 热挤压件图是控制生产过程、设计与制 造模具的依据,热挤压件图是在冷挤压件图的基础上绘制的。
1.冷挤压件图的绘制
图7-5 挤压件图示例
成组热挤压模的设计与应用
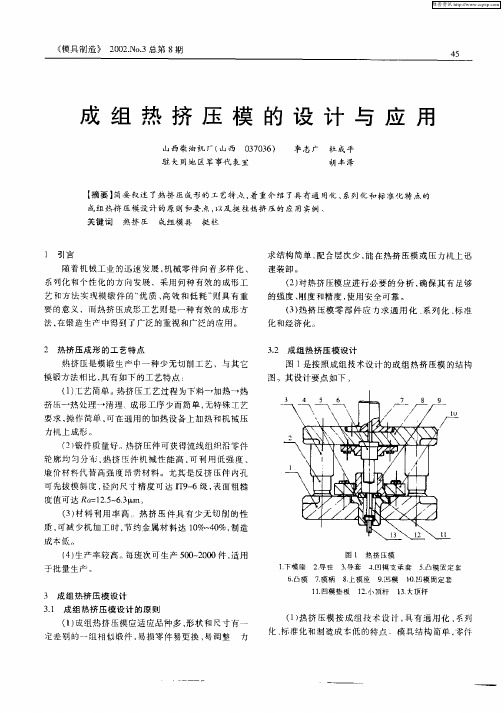
挺柱 在 热挤压 成形 中的变形 是 不 均匀 的 。在 热挤
压 时 和 凸模 接 触 的 坯料 端 和 坯 料 的下 端 一样 变 形 极 小 , 难 变形 区 ; 着 凸模下 降 , 难 变 形 区作 用 及 周 是 随 在 围模腔 的限制 下 ,变形 的金 属 不断地 挤 向简壁部 的下 部 ,使 已成形 筒壁 自下而上 作 刚性移 动 ,是 强烈 变 形 区 , 件成形 主要 依靠 这一 过程 , 形 程度最 大处在 锻 锻 变
() 料利 用 率 高 。热 挤压 件 具 有 少无 切 削 的性 3材 质, 可减 少机 加工 时 , 节约 金属 材 料达 1%~ 0 制 造 0 4 %,
成 本低 。
() 4 生产率 较 高。 每班 次可 生产 50 20 0~ 00件 , 适用
于批量生 产 。
1 下模 座 6凸模 2导 柱 7摸 柄
设 计 外 , 应对 凸模 和 凹模 进 行必要 的润 滑 , 坯料 与 还 使 模具 之 间产生一 层 润滑 膜 , 以起 到冷 却模 具 , 便于 坯料 脱模 , 减少 模具磨 损 与摩 擦 , 降低挤 压 力 和有 利于金 属
的流动与成形 的作 用 。
成 组热挤 压摸设 计 的原则 要 点 , 以及挺 拄热挤 压 的应 用实例 。
关键 词 热挤 压 成组模 具 挺 柱
1 引 言
求结 构 简单 , 配合层 次 少 , 能在 热挤 压模 或 压 力机上 迅 速装 卸 。 () 2 对热 挤 压模 应进 行 必要 的分 析 , 确保 其 有足 够 的强 度 、 刚度 和精度 , 用安 全 可靠 。 使 () 3 热挤 压 模零 部件 应 力 求 通用 化 、 系列 化 、 准 标 化 和经济 化。
热挤压的一次成形技术概述

③ 综合挤 压—— 是指金 属流动方 向与 上凸模运动 方 向 成全方位流动 , 图 5 如 所示 。
收稿 日期 :0 6—1 8 20 2—2
41・
维普资讯
辽 宁 省 交 通 高 等 专 科 学 校 学 报
20 0 7拄
的阻力 , 限制它的流动 。比如说 改变 凸模形状 , 金属 在凹 使 模 内实行倾 向性流动 , 最后 再在 金属加 工时解 决。
② 反挤压 时金 属的流动状态—— 对高于直径 的毛坯进 行反挤压 时 '0 始挤 压 阶段 , 形呈稳 定状 态 , 图 8所 网开 变 如 示, 将毛坯分为 A B C三个 区域。其 中 A为粘滞 区域 , 、、 紧贴 凸模上端 , 呈倒锥形 , 区域 内金 属基本 不发生变 形 。B为 强 烈变形 区, 也就 是说毛坯在此 区域 内将发生强烈变形 。当凸
t { _ { 凸{
…
正挤压是指挤压时金 属流动方 向与 上凸模 运动方 向相
,
,
一
致, 图 1 如 所示 。
反挤压是指挤压时金 属流动方 向与 上凸模 运动方 向相
反 , 图 2所示 。 如
.疆鼎黧 j嚣 撼越 茸“
、
鞠矧 崩崩
图 5 ห้องสมุดไป่ตู้合挤压
图6 坐标 图
、
坯料
… 一 、
\
¨ /
,
{
一 一\ 爿
~ … 、
.
毛坯
、
.
掺
/ 、 、
① 轴 向挤压——指金属流动方 向与 上凸模运 动方 向平 行, 是最常见 的热挤压工艺 , 又分为正挤压 、 反挤压和复合挤
汽车轮毂轴管热挤压模具设计分析

汽车轮毂轴管热挤压模具设计分析摘要:对汽车轮毂轴管零件热挤压各工序金属变形特点进行理论分析,介绍各工序变形时金属的流动规律、金属成形时易形成弊端的原因,并提出解决方案。
关键词:轮毂轴管热挤压模具设计1 压型模设计1.1 压型工序金属变形特点压型工序又称制坯工序,在热挤压工艺中是重要的一个环节,压型是在封闭的模腔内进行的,当压型凸模与坯料接触后,在力的作用下,金属开始发生塑性变形并很快消除毛坯同挤压凹模之间的径向间隙而充满凹模,此时坯料高度开始降低,断面增大,金属在向水平方向流动的同时又向下流动,在三向不均匀压应力的作用下,金属内部存在微观缺陷得以消除。
同时,金属的塑性和致密性也得到了改善。
1.2 压型工序中易出现的问题汽车轮毂轴管在压型过程中易出现的主要问题是下端充不满,这是因为金属变形流动时,沿横向流动的金属先水平外流,与模壁接触后,部分金属才开始转向内角处流动,因此,金属变形流动规律决定于沿横向内角处是最难充满的地方。
另外,下顶杆和凹模腔配合过分紧密,高压空气溢不出、凹模孔内积有大量的氧化皮也是下端充不满的原因之一。
2 镦挤成形模设计2.1 镦挤成形工序金属变形特点镦挤成形工序是汽车轮毂轴管复合挤压工艺中最为关键的一道。
镦挤成形时,坯料在上下模闭合后,凸模开始与坯料接触,金属由于模具内腔空间较大,变形后的坯料呈现轻微的鼓形,随着挤压进一步深入。
在凸模的作用下,坯料上部的金属在内形冲头转角处产生分流,一部分金属向上流动不断形成工件的侧壁,另一部分向凹模的内侧壁方向流动以逐渐充满凹模(即金属在向水平方向移动的时,也向轴向移动)在压力的作用下,轴向移动的金属被迫也做水平方向移动。
在此变形阶段由于毛坯的自由表面较多,金属的流动较为便利,随着变形的继续压型冲已深入凹模内,模具对坯料逐渐形成一个完全封闭的空间,坯料的自由表面大幅减少,与模具接触表面温度也逐渐降低。
坯料外表面金属的流动速度小于坯料内部金属的流动速度,导致工件外表面台阶过渡处难于充满,此过程实质上是一个复合挤压的过程。
汽车轮毂轴管热挤压模具设计分析

创 新 技 术
汽 车轮 毂 轴管 热 挤 压模 具 设计 分析
周凤 婵 ( 河南工业和信 息化职 业学院 4 5 4 0 0 0 )
摘 要: 对 汽车轮毂轴管零件热挤压备工序金属变形特点进行理论分析, 介 绍各工序变形时金属的流动规律 , 金属成形时易形 成弊端的原因,
充满 凹模 , 此 时 坯 料 高 度 开始 降 低 , 断面 增 后 , 成 形 法兰 的 压 头与 坯 料 也 开始 接 触 , 向 大, 金 属 在 向水 平方 向流 动 的 同时 又 向下 流 下 的压 力将 迫使 部 分 金 属 沿 着与压 头 相 同 反挤压 工序 无法 将内孔 直接 冲 成通 孔 , 需 留一定 厚度 的 挤 余金 属 在 专 门的 冲 底 模 动, 在 三 向不 均 匀 压应 力的 作用 下 , 金属 内 的方 向 ( 即 向下 ) 流动 , 这 样 向上 、 向下 的 两 中冲 穿。 针对 本 文 而 言 , 将 要 冲 除 挤 余金 属 部 存 在 微 观 缺 陷 得以 消 除 。 同时 , 金 属 的塑 股 金 属 对流 最终 在 R 过 渡 处汇 集形成 折 叠 。 ( 连皮) 的工 件放 人 冲底 凹模 中 , 随 着 设 备 性 和 致 密性 也得 到 了改 善 。 ( 2 ) 金属流动速度不一致而形成 。 在 更 换 工作 横梁 的 下移 , 使 冲底 凸模 与 工件 的挤 余 1 . 2 压 型 工 序 中易出现 的问题 凸 模时 , 由于 凸模 处 于 室 温 状 态 , 造 成 与 凸 金 属 ( 连皮) 接触, 在 压 力的 作用 下, 工件对 汽 车 轮 毂 轴 管在 压 型 过 程 中 易出现 的 模 接 触 的 坯 料 表 层 温 度 下 降 , 致使 这一 部 挤 余 金 属 ( 连皮) 发 生 剪切 作 用 , 待应 力 达 主要 问题 是下 端 充不满 , 这是 因为金 属 变形 分 金属 流 动速 度 变慢 , 而 与之 相 邻 的中 间较 到 剪切 破 坏 强 度 时, 挤 余金 属 ( 连皮) 就 被 流动时, 沿 横 向流 动 的 金 属 先 水平 外流 , 与 快 的 金 属 带 着流 速 较 慢 的 金 属 一 起 流 动 , 切 离挤 压 件而 落 下 , 挤压 件仍 回留在 冲底 凹 模壁 接 触 后 , 部 分金 属才 开始 转 向 内角处流 由于 流 速 的差 异 , 最 终 在 流动 阻 力最 大 处 R 模内。 在 这 个 过 程 中, 冲 底 凹模 起 着 支 承 挤 动, 因此 , 金 属 变形 流 动 规 律 决 定 于沿 横 向 过 渡 区域形 成 折 叠。( 3 ) 一 部 分金 属 被 压 入 压 件 的作用 , 而 冲底 凸模 则 起 刀刃的 作用 。 内角 处 是 最 难 充 满 的 地 方 。 另外 , 下 顶 杆 和 另一部 分 金 属内 形成 。 由于热 挤 压工 艺设 计 4 . 2 精整 内孔 工 序易 出现 的 问题 凹模 腔 配 合 过 分 紧 密 , 高压 空气 溢 不 出、 凹 不合理, 零 件 内腔 复杂 , 预 冲孔 直 径 偏 小 , 在 工件精 整内 孔阶 段, 主 要 存 在 问题 是 将 预冲 孔后 表 面 已氧 断 面 质量 , 模 孔 内积 有 大 量 的氧 化 皮 也 是 下端 充不 满 在 扩孔 或 成形 法 兰 时, 因为 断 面质 量 的好 坏 , 直接 影 响
热挤压模具设计与制造基础
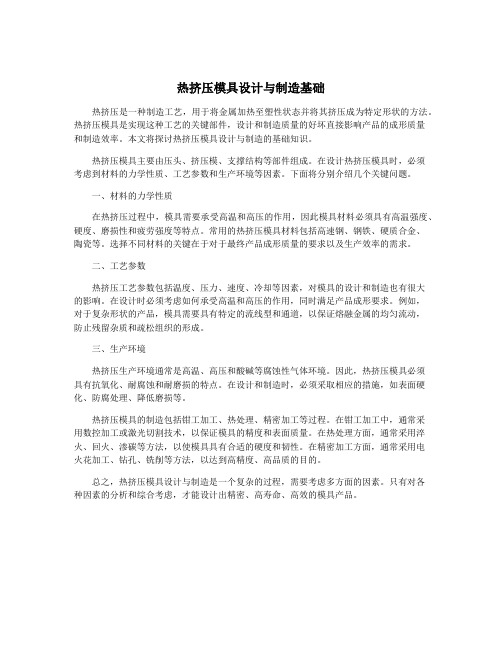
热挤压模具设计与制造基础热挤压是一种制造工艺,用于将金属加热至塑性状态并将其挤压成为特定形状的方法。
热挤压模具是实现这种工艺的关键部件,设计和制造质量的好坏直接影响产品的成形质量和制造效率。
本文将探讨热挤压模具设计与制造的基础知识。
热挤压模具主要由压头、挤压模、支撑结构等部件组成。
在设计热挤压模具时,必须考虑到材料的力学性质、工艺参数和生产环境等因素。
下面将分别介绍几个关键问题。
一、材料的力学性质在热挤压过程中,模具需要承受高温和高压的作用,因此模具材料必须具有高温强度、硬度、磨损性和疲劳强度等特点。
常用的热挤压模具材料包括高速钢、钢铁、硬质合金、陶瓷等。
选择不同材料的关键在于对于最终产品成形质量的要求以及生产效率的需求。
二、工艺参数热挤压工艺参数包括温度、压力、速度、冷却等因素,对模具的设计和制造也有很大的影响。
在设计时必须考虑如何承受高温和高压的作用,同时满足产品成形要求。
例如,对于复杂形状的产品,模具需要具有特定的流线型和通道,以保证熔融金属的均匀流动,防止残留杂质和疏松组织的形成。
三、生产环境热挤压生产环境通常是高温、高压和酸碱等腐蚀性气体环境。
因此,热挤压模具必须具有抗氧化、耐腐蚀和耐磨损的特点。
在设计和制造时,必须采取相应的措施,如表面硬化、防腐处理、降低磨损等。
热挤压模具的制造包括钳工加工、热处理、精密加工等过程。
在钳工加工中,通常采用数控加工或激光切割技术,以保证模具的精度和表面质量。
在热处理方面,通常采用淬火、回火、渗碳等方法,以使模具具有合适的硬度和韧性。
在精密加工方面,通常采用电火花加工、钻孔、铣削等方法,以达到高精度、高品质的目的。
总之,热挤压模具设计与制造是一个复杂的过程,需要考虑多方面的因素。
只有对各种因素的分析和综合考虑,才能设计出精密、高寿命、高效的模具产品。
挤压过程中常见的缺陷和对策
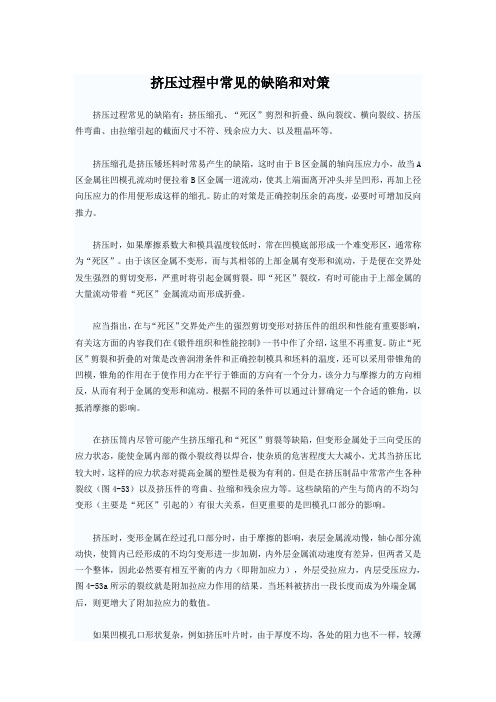
挤压过程中常见的缺陷和对策挤压过程常见的缺陷有:挤压缩孔、“死区”剪烈和折叠、纵向裂纹、横向裂纹、挤压件弯曲、由拉缩引起的截面尺寸不符、残余应力大、以及粗晶环等。
挤压缩孔是挤压矮坯料时常易产生的缺陷,这时由于B区金属的轴向压应力小,故当A 区金属往凹模孔流动时便拉着B区金属一道流动,使其上端面离开冲头并呈凹形,再加上径向压应力的作用便形成这样的缩孔。
防止的对策是正确控制压余的高度,必要时可增加反向推力。
挤压时,如果摩擦系数大和模具温度较低时,常在凹模底部形成一个难变形区,通常称为“死区”。
由于该区金属不变形,而与其相邻的上部金属有变形和流动,于是便在交界处发生强烈的剪切变形,严重时将引起金属剪裂,即“死区”裂纹,有时可能由于上部金属的大量流动带着“死区”金属流动而形成折叠。
应当指出,在与“死区”交界处产生的强烈剪切变形对挤压件的组织和性能有重要影响,有关这方面的内容我们在《锻件组织和性能控制》一书中作了介绍,这里不再重复。
防止“死区”剪裂和折叠的对策是改善润滑条件和正确控制模具和坯料的温度,还可以采用带锥角的凹模,锥角的作用在于使作用力在平行于锥面的方向有一个分力,该分力与摩擦力的方向相反,从而有利于金属的变形和流动。
根据不同的条件可以通过计算确定一个合适的锥角,以抵消摩擦的影响。
在挤压筒内尽管可能产生挤压缩孔和“死区”剪裂等缺陷,但变形金属处于三向受压的应力状态,能使金属内部的微小裂纹得以焊合,使杂质的危害程度大大减小,尤其当挤压比较大时,这样的应力状态对提高金属的塑性是极为有利的。
但是在挤压制品中常常产生各种裂纹(图4-53)以及挤压件的弯曲、拉缩和残余应力等。
这些缺陷的产生与筒内的不均匀变形(主要是“死区”引起的)有很大关系,但更重要的是凹模孔口部分的影响。
挤压时,变形金属在经过孔口部分时,由于摩擦的影响,表层金属流动慢,轴心部分流动快,使筒内已经形成的不均匀变形进一步加剧,内外层金属流动速度有差异,但两者又是一个整体,因此必然要有相互平衡的内力(即附加应力),外层受拉应力,内层受压应力,图4-53a所示的裂纹就是附加拉应力作用的结果。
t10a冷冲模(凹模)热处理工艺方法

t10a冷冲模(凹模)热处理工艺方法t10a冷冲模(凹模)热处理工艺方法一、引言在制造业中,冷冲模(凹模)是一类常见而重要的模具,在金属冷镦、冷挤压、冲剪等加工过程中扮演着关键的角色。
而为了提高冷冲模的硬度和耐磨性,热处理工艺方法就显得尤为重要。
本文将深入探讨t10a冷冲模(凹模)热处理工艺方法,并对其进行全面的评估和分析,以期帮助读者更好地理解和应用于实践。
二、t10a冷冲模(凹模)的特性和需求t10a冷冲模(凹模)是一种由高碳钢t10a制成的模具材料。
相较于其他材料,t10a具有良好的韧性和可塑性,但硬度和耐磨性相对较低。
为了满足冷冲模在长时间重复使用中的高强度和耐久性要求,采取热处理工艺方法是不可或缺的。
三、t10a冷冲模(凹模)的热处理工艺方法针对t10a冷冲模(凹模)的热处理工艺方法,主要包括退火、正火、淬火和回火等步骤。
1. 退火退火是最基本也是最常用的热处理工艺方法。
通过加热材料至适当温度后冷却,可以软化t10a冷冲模(凹模)的组织,提高其可塑性和韧性。
当t10a冷冲模需要进行加工和修复时,退火工艺尤为重要。
2. 正火正火是提高t10a冷冲模(凹模)硬度和耐磨性的重要方法。
通过将材料加热到一个适当的温度区间(通常介于700℃至900℃之间)并进行适当的保温时间后迅速冷却,可以使t10a冷冲模的组织发生相应的改变,从而提高硬度和耐磨性。
3. 淬火淬火是t10a冷冲模(凹模)热处理中的关键步骤。
通过将材料迅速浸入冷却介质(如水、油或盐水中)进行快速冷却,可以使t10a冷冲模的组织发生强烈的变化,从而获得高硬度和强度。
然而,需要注意的是,淬火过程中的温度、冷却介质和冷却速率等参数需根据具体情况进行合理选择。
4. 回火回火是在淬火后进行的一种热处理方法。
通过加热t10a冷冲模(凹模)至一定温度,然后保持一定时间后进行冷却,可以减轻材料内部应力,并调整其硬度和韧性之间的平衡。
回火过程中的温度和时间控制是关键,需要根据实际需求选择合适的条件。
套筒热挤压工艺与模具设计

零件尺寸精度超出了热挤压所能达到的要求 , 需 面不许有剪切毛刺。 加放机加 工余量 。根据 图 1 的产 品零 件 图 , 可知 D = () 2 加热 。加热设备选用 中频感 应加热炉 , 钢温
3m Hd 6/l 1 4 查 资 料 得 单 边 余 量 为 不低于 1 0 %, 9 m, /= 0 = . 。 3 9 , 0 采用流水加热 , 2 坯料 中心与表 面的温
2 紧紧连接 。 由沉套 2 和顶杆 1 组成顶 出机构 , l 0 9 在
气垫 的作用下将挤压件从 凹模 内顶 出。沉套 2 的一 0 部分伸出下模座 , 为了降低合模高度 。将热挤压模 是
安装在液压机上时 , 需在下模座 2 下面增加一个 中间 1 有孔 的附加垫板 , 沉套 2 下部伸进 附加垫板 的孑 内; 0 L 若热挤压模安装在 曲柄压力机上时 , 沉套 2 下部伸进 O
大 于 02 rm。 .5 a
() 4 热处理 。采用余热退火处理 , 挤压 件退火处
图 1 套筒零件 图 2 套筒热挤压件
理后的硬度为 2 7 20 B 0 ~ 4H 。
() 5 清理 。热处理后挤压件应进 行酸洗清理 , 清 理后 的挤压件表 面不许有 过蚀麻 点和残 留氧化铁皮 根据体 积相 等的原则和挤压件体积 ( 上 1 加 %的 存在。 烧损量 ) 初步算得坯料 尺寸 为6 5 5 . m, , 3 x 4 r 再加 上 2 a 挤压成形工步如图3 所示。 下料负公差 0 m 确定下料尺寸为¥ 5 5 . m。 . m, 7 3x4 m 9
・
经计算得到挤压件体积为 5, 7 m 。 1 3m 6
4 6・
《 模具制造)0 1 2 1 年第8 期
C MMC
锥面锁紧两半凹模闭式挤压模具

墨 冲压模技术
2 联轴器 叉闭式挤压模具
吉普车传动万 向轴联 轴器又锻件如 图3 所示 。原来 采用开
式 模 锻 生 产 ,坯 料 加 热 后 、 一 般 经 制 坯 、 预 锻 和 终 锻 成 形 。
然 后再 进行切 除飞边 ,清理 和校 正等工序 。现采 用闭式正 向
分 流 挤 压 模 锻 工 艺 ,热 好 的 坯 料 . 模 锻 成 形 。 材 料 消 耗 由 次
开 式模锻 的 18 k 降 到 13 k .2 g . 0 g, 材 料 利 用 率 提 高 了 3 % , 0 比 在 可 分 凹 模 中 挤 压 制 坯 然 后 精 整 成 形 的 材 料 利 用 率 提 高
1 % ~ 1 % ,且 锻 件 质 量 高 、 尺 寸 精 确 。 0 5
3 两端带法兰筒形件 闭式挤压模具
图 5 示 为 两 端 带 法 兰杯 形 件 。 使 用 圆 锥 自锁 式 纵 向对 分 所
凹 模 闭 式 挤 压 模 具 可 以 获 得 极 限 偏 差 为 mm 、 机 械 加 工 余 量
( )清 理 飞边 , 采 用 小 间 隙 切 边 模 切 除 沿 可 分 凹模 的 分 4
冲压模技术 爱
w ww u d c l e mo l r n l -
锥 面 锁 紧 两 半 凹 模 闭 式 挤 压 模 具
L ki he t o hal-c oc ng t w f one c os xt usi e di l ed e r on di e
面 上 装 有 两 半 凹模 1 。 装 在 活 塞 l 上 的 顶 杆 8 往 复直 线 运 4 1 的 动 就 保 证 了两 半 凹 模 的 上 升 和 下 降 。上 升 时 两 半 凹模 被 螺 钉 固 定 在 模 套 上 的 滑 板 5 开 ,这 些 滑 板 还 可 限 制 两 半 凹模 的上 分 升 , 当 两 半 凹 模 下 降 和 合 拢 时 ,装 在 一 个 半 凹模 上 的专 用 定
挤压第七章 热 挤 压

二、热挤压件的热处理
图7-16 退火和正火加热温度范围 1—完全退火 2—正火 3—球化退火 4—低温回火
第八节 热挤压件质量及力学性能
1.温度对热挤压件质量的影响 挤压坯料温度发生变化,会造成 收缩率不一致,影响热挤压件的尺寸精度。 2.挤压件断面形状的影响 挤压件的断面形状越复杂,冷收缩时 的不均匀性也越大。 3.润滑条件的影响 选用润滑性能好和粘附能力强的润滑剂时, 可在坯料表面保持很均匀的润滑膜,模具表面平滑时,则挤压 件尺寸精度也高且表面粗糙度值低。 4.氧化对表面质量的影响 钢料加热到开始挤压温度后就已超过 了钢的剧烈氧化温度,坯料表面都会生成一层氧化皮。
二、模具结构设计
图7-9 热正挤压模 1—凹模 2—凸模 3—顶杆导套 4—下模座 5—垫板 6—导柱 7—导套
8—凹模固定座 9—上模座 10—固定螺母 11—凸模垫板
二、模具结构设计
图7-10 热反挤压模 1—螺母 2—凸模固定圈 3—卸料板 4—凸模 5—凹模 6—顶
料杆 7—凹模固定座 8—顶杆 9—弹簧 10—螺栓
二、热挤压用的玻璃润滑剂
1) 玻璃在加热过程中没有明显的熔点,随着温度升高它逐渐软化,直至成为液体。 2) 玻璃熔化后的粘度随温度的升高而降低,不同成分的玻璃有不同的粘度-温度特性。 3) 玻璃使用的温度范围很广,从450~2200℃范围内都可采用玻璃作润滑剂。 4) 玻璃不与金属起化学作用,而且化学稳定性很好。
1.火焰加热
它是利用燃料在加热炉内燃烧产生含有大量热 能的高温气体(火焰),通过对流、辐射把热能传 递给坯料表面,通过由表及里的热传导而使金 属坯料加热到预定的温度。
2.电加热
(1) 感应加热 是交变电流通过感应线圈产生感应交变磁场,进而感应出交变电场。 (2) 电阻炉加热 是利用电流通入炉内的电热体所产生的热量,以辐射与对流传热的 方式来加热金属坯料。
挤压模具设计书说明书

铜合金压气缸的热挤压工艺及模具设计摘要铜合金压气缸的生产方法常见的有管料的切削加工,离心铸造后切削加工,热挤压法。
热挤压法生产材料利用率最高,生产效率最高,产品质量最高。
本文分析热挤压工艺及模具设计。
热挤压工艺分析综述:铜合金的热挤压温度根据经验可以定为730℃。
压气缸的毛坯件属于杯形件的一种,因此采用的是反挤压。
若采用一次挤压成形则所需挤压力和变形程度太大。
因此采用两次反挤压,第一次将棒料挤压成为杯形件,切削加工成空心圆柱形。
再经过第二次反挤压将内孔扩大,外径不变。
经过两次反挤压得到挤压件成形毛坯。
模具设计分析综述:两序挤压则需要两套挤压模具。
两套模具采用通用凹模,结构简单。
第一套模具凸模采用一般的反挤压凸模结构。
第二套模具需要有模芯结构,模芯可以是固定式的也可以是活动式的。
本次设计将模芯设计为固定式的即凸模和模芯一体式的。
设计成整体式的好处是结构简单,生产效率高。
与此同时,顶件器只需设计成中空的即可,当凸模压下时,模芯正好进入顶件器的内腔中。
关键词:反挤压,压气缸,模具设计,模芯Copper Alloy Cylinder Pressure of Hot Extrusion Technologyand Die DesignABSTRACTCopper alloy pressure cylinder production methods common pipe material cutting processing, machining after centrifugal casting, hot extrusion method. Hot extrusion method is the highest utilization rate of materials, the highest production efficiency,and the highest quality of product . In this paper, hot extrusion technology and die design is analysed.Hot extrusion technology analysis were reviewed: Copper alloy can be classified as 730℃hot extrusion temperature according to the experience. Pressure cylinder of a blank parts belong to the cup, so the backward extrusion is used. If using an extrusion forming ,the needed extrusion and deformation degree is too large. so the backward extrusion shoud be used twice.The first extrusion will make the bar become the cup, and then, make the cup become the hollow cylindrical by machining. After second backward extrusion will enlarge the inner hole, and the outside diameter is constant.After twice backward extrusion,we can get the bloom.Mold design analysis were reviewed: The two order squeezing requires two sets of extrusion dies Two sets of mould adopt general concave die. The first set of mould punch adopts general backward extrusion punch die structure. A second set of mould need a mold core structure, mold core can be stationary or activities. This design will design for fixed the punch mold core and mold core one-piece. Design into integral advantage is simple structure, high production efficiency at the same time, top pieces simply designed to be hollow, when the convex mold, mold core right into the lumen of top pieces.KEY WORDS: backward extrusion, cylinder pressure, mold design, mold core目录前言 (1)第一章热挤压技术的介绍 (2)§1.1 热挤压工艺的实质 (2)§1.2 热挤压工艺的特点 (2)§1.3 热挤压工艺的主要过程: (3)第二章工艺分析及制定 (4)§2.1 产品零件分析 (4)§2.2 挤压件图制定 (4)§2.3 工艺方案分析 (5)§2.4 毛坯形状及尺寸选择 (6)第三章坯料的处理 (8)§3.1 坯料加热方法 (8)§3.2 加热温度 (8)§3.3坯料润滑 (9)第四章变形量和挤压力 (11)§4.1 影响挤压力主要因素 (11)§4.2 变形程度 (12)§4.3 挤压力 (12)§4.4 热挤压设备选用原则 (13)§4.5 热挤压设备选用 (14)第五章模具结构设计 (15)§5.1 挤压模具设计的基本要求 (15)§5.2 反挤压凸模的设计 (16)§5.3热反挤压凹模的设计 (17)§5.4热挤压凸模固定板的设计 (19)§5.5 顶出装置的设计 (20)§5.6模具结构原理 (21)§5.7模具材料的选择 (22)结论 (25)参考文献 (26)致谢 (28)前言压气缸户外断路器中的关键零件,要求“三高”即高的导电率、高的硬度和高的强度,以降低能耗和提高产品的可靠性。
一种碲化铋温差电材料用热挤压模具[实用新型专利]
![一种碲化铋温差电材料用热挤压模具[实用新型专利]](https://img.taocdn.com/s3/m/e14482d65727a5e9856a61f7.png)
专利名称:一种碲化铋温差电材料用热挤压模具专利类型:实用新型专利
发明人:任卫,姜洪义,周微
申请号:CN200920278242.1
申请日:20091223
公开号:CN201592203U
公开日:
20100929
专利内容由知识产权出版社提供
摘要:一种碲化铋温差电材料用热挤压模具,属于热电材料技术领域。
具体涉及一种热挤压模具。
其特征是挤压模具由上挤压筒、凹模、下挤压筒构成;上挤压筒和下挤压筒之间通过法兰盘连接,凹模放在下挤压筒内。
本实用新型结构简单,制作方便,采用不锈钢为模具材料,利用此模具热挤压温差电材料,材料内部的晶体取向有了明显的改善。
申请人:钢铁研究总院
地址:100081 北京市海淀区学院南路76号
国籍:CN
代理机构:北京华谊知识产权代理有限公司
代理人:吕中强
更多信息请下载全文后查看。
- 1、下载文档前请自行甄别文档内容的完整性,平台不提供额外的编辑、内容补充、找答案等附加服务。
- 2、"仅部分预览"的文档,不可在线预览部分如存在完整性等问题,可反馈申请退款(可完整预览的文档不适用该条件!)。
- 3、如文档侵犯您的权益,请联系客服反馈,我们会尽快为您处理(人工客服工作时间:9:00-18:30)。
第七章 热挤压
热挤压的基本形式
第七章 热挤压
第二节 热挤压坯料的加热
挤压前对坯料进行加热的目的:提高金属的塑性、降低变形 抗力、使金属易于流动,并使零件获得良好的组织性能。 一、坯料的加热方法
1、火焰加热 利用燃料在加热炉内燃烧产生含有大量热能的高温气体,通过 对流、辐射把热能传递给坯料表面,通过由表及里的热传导而使金属坯料加热 到预定的温度。 燃料种类:固体燃料(煤、焦碳等)、液体燃料(石油等)、气 体燃料(天然气、煤气等)。 优点:燃料来源方便、加热炉造价较低,对坯料适应性广等。 缺点:劳动条件较差、加热速率较慢、加热炉温度难以控制,还生产较大的金 属烧损,对环境也有较大影响。
电阻加热炉的加热温度受电热体的限制,热效率比感应加热低得多,加热 速率也较慢。但它对坯料的适应性非常广,特别是适应加热有色金属坯料。另 外,该法也可以采用保护性气体实现少无氧化加热。
第七章 热挤压
二、加热缺陷
1、氧化 钢在非保护性介质中加热时会产生氧化,在钢的表面上生成氧化皮。 降低挤压件表面质量、嵌在挤压件中形成凹坑,造成金属烧损。 措施:快速加热、控制炉内气氛或保护性介质。 保护性介质分为:气体保护介质(纯惰性气体)、液体保护介质(玻璃熔体)
第七章 热挤压
1、开始挤压温度的确定 就提高金属的塑性和 低变形抗力而言,钢的热挤压开始温度越接近 固相线越有利,但加热温度过高会出现过热、过 烧缺陷。因此,碳钢的开始挤压温度应低于碳碳平衡相图固相线150-250℃。此温度下,钢的 组织为单相奥氏体,塑性好,变形抗力,易于较 大程度的挤压。
2、结束挤压温度的确定 在确定结束挤压温度 时,既要保证钢具有足够塑性,又要使挤压件能 够获得良好的组织性能。为了保证完全再结晶, 使挤压件获得细晶粒组织,钢的结束挤压温度应 高于其再结晶温度。
4、过烧 当钢加热到接近熔化温度,并在此温度长时间停留,不但使奥氏体 晶粒粗大,同时由于氧化性气体渗入到晶界使晶间物质Fe、C元素等发生氧化, 形成易熔共晶体,使晶间联接破坏,这种加热缺陷称为过烧。
坯料一旦过烧,只能报废。
5、开裂 坯料内部的温度差会导致温度应力,并且只有当坯料的断面出现温 度梯度且处于弹性状态时,即坯料温度低于550℃时才会出现温度应力。当温 度应力超过该温度下的抗拉强度时,就会产生裂纹,即加热开裂。
第七章 热挤压
2、电加热 电加热是通过把电能转变为热能来加热金属坯料。常见的方法有: 感应电加热、接触电加热和电阻炉加热等。
(1)感应电加热 将金属坯料置于交变电场中,在坯料内产生感应电流而达到 加热的目的。
特点:加热速度快、氧化烧损少(少于0.5%)、热效率高、炉温可控易于实 现自动化加热。
加热电源分为工频(50Hz)、中频(50-10000Hz)和高频(10000Hz以上)三种。
第七章 热挤压
第七章 热挤压
四、钢的加热规范
钢的加热规范,是指钢料从装炉开始到加热完了的整个过程,对加热炉温 度和钢料随时间变形的规定。
包括:加热速率、加热温度、加热时间和保温时间等内容。 制定加热规范的原则是:在保证坯料不会开裂的条件下,加热速率越快越 好,加热时间越短越好。 感应加热是坯料通过电流自身发热的,其温度应力很小,一般不会出现开 裂。这里指的加热规范主要是火焰炉的加热。
第七章 热挤压
(1)对于截面直径小于120mm的碳钢和合金钢,不存在开裂危险,可以炉子的最 大加热速率加热,直到开始挤压温度。一般的加热时间可用下式计算:
t=(0.4-0.6)d 其中,t为加热时间(min);d为钢料直径或为非圆截面坯料的最短边长(mm)。
(2)对截面直径大于120mm的碳钢和低合金钢,加热一般分为两段进行。室温至 800℃必须缓慢加热,加热时间可按t=0.4d计算;在800℃左右保温一段时间, 使之均匀热透,然后再以较快的速率加热至开始挤压温度,其加热时间可按 t=(0.2-0.3)d计算。
和固体保护性介质(玻璃粉等)。
2、脱碳 钢加热时,表面的碳与炉气中的氧结合,使表面层含碳量降低。 含碳量越高越容易脱碳。 措施:与防止氧化的措施相同。
第七章 热挤压
3、过热 加热温度过高或在高温下停留时间过长而造成的奥氏体晶粒过于粗 大的现象。
对于过热不严重的钢,通过大变形量的锻造可以得到改善。如果热挤压件 冷却后仍然是粗晶粒的过热组织,可以采用正火处理来加以纠正。
第七章 热挤压
本章主要介绍热挤压坯料的加热、热挤压的润滑、模具结构 及材料、热挤压件的冷却及热处理等。
第一节 热挤压概述
热挤压是将材料加热到再结晶温度以上的某个温度进行的挤压。
1、热挤压与冷挤压相比,具有以下优点 (1)热挤压时金属塑性好,降低变形抗力,总挤压力大大下降; (2)热挤压时可以连续成型,有利于提高生产效率。
集肤效应:当坯料进行感应加热时,内部产生的电流密度是断面分布是不 均匀的,中心电流密度小,表层电流密度大。
当加热频率增加时,可以提高加热的剧烈程度,但加热层的深度减少。因 此,加热大直径的棒料要采用较低频率的感应加热炉。
第七章 热挤压
(2)电阻炉加热 利用电流通入炉内的电热体所产生的热量,以辐射与对流传 热的方式来加热金属坯料。其加热的形式与火焰加热类似。
加热速率越快,坯料截面尺寸越大,导热性能越差,则温度应力越大,开 裂的危险性也越大。
第七章 热挤压
三、热挤压温度范围的确定
热挤压温度范围,是指开始挤压温度与结束挤压温度之间的一段温度区间。 确定热挤压温度范围的基本原则: (1)在热挤压温度范围内金属应具有良好的塑性和较低的变形抗力; (2)能挤压成形具有良好组织性能和力学性能的工件; (3)热挤压温度范围尽可能宽一些,以便在一次加热后完成数道变形工步,以 提高生产效率。
第七章 热挤压
2、热挤压与冷挤压相比,存在以下不足 (1)由于热挤压在较高的温度下成形,对模具材料的耐热性提出 了较高的要求; (2)热挤压件的表面质量不佳,尺寸精度较低; (3)热挤压后,工件必须进行热处理。
热挤压工艺的主要过程:坯料制备→坯料加热→挤压成型(预成 形、终成形)→后续工序(冲孔、校正或精压) →挤压件热处理→ 表面处理→精加工。