2015年8D报告
8d报告完整版范文3篇
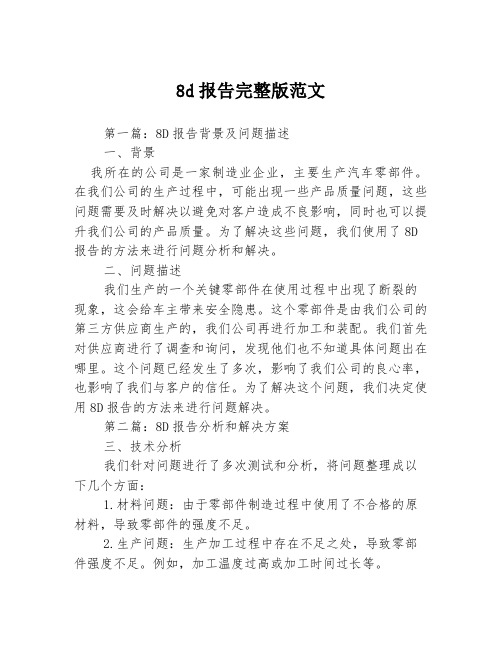
8d报告完整版范文第一篇:8D报告背景及问题描述一、背景我所在的公司是一家制造业企业,主要生产汽车零部件。
在我们公司的生产过程中,可能出现一些产品质量问题,这些问题需要及时解决以避免对客户造成不良影响,同时也可以提升我们公司的产品质量。
为了解决这些问题,我们使用了8D 报告的方法来进行问题分析和解决。
二、问题描述我们生产的一个关键零部件在使用过程中出现了断裂的现象,这会给车主带来安全隐患。
这个零部件是由我们公司的第三方供应商生产的,我们公司再进行加工和装配。
我们首先对供应商进行了调查和询问,发现他们也不知道具体问题出在哪里。
这个问题已经发生了多次,影响了我们公司的良心率,也影响了我们与客户的信任。
为了解决这个问题,我们决定使用8D报告的方法来进行问题解决。
第二篇:8D报告分析和解决方案三、技术分析我们针对问题进行了多次测试和分析,将问题整理成以下几个方面:1.材料问题:由于零部件制造过程中使用了不合格的原材料,导致零部件的强度不足。
2.生产问题:生产加工过程中存在不足之处,导致零部件强度不足。
例如,加工温度过高或加工时间过长等。
3.设计问题:设计过程中没有考虑到应力分布的均匀性,导致零部件在使用过程中容易产生应力过大的现象。
四、解决方案1.材料问题:我们将与供应商重新协商并重新规定原材料标准,以保证原材料的质量。
2.生产问题:我们将对生产过程进行检查和测试,改进加工温度和加工时间,并进一步探究生产中存在的不足之处,以最大程度地提高相关生产能力。
3.设计问题:我们会重新设计零部件,考虑应力分布的均匀性,并对原有零部件进行更加严格的测试和分析以验证新设计的可行性。
第三篇:8D报告措施计划和预防五、措施计划1.与供应商合作并重新规定原材料标准。
2.对生产过程进行检查和测试,并改进加工温度和加工时间。
3.重新设计零部件,考虑应力分布的均匀性,并进行严格的测试和分析。
4.对生产和供应链流程进行跟踪和监控,确保问题不再发生。
ISO9001-2015解决问题8D方法应用程序
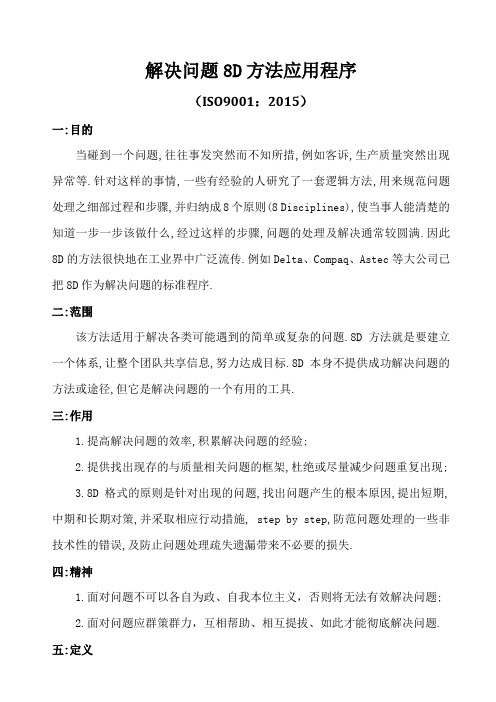
解决问题8D方法应用程序(ISO9001:2015)一:目的当碰到一个问题,往往事发突然而不知所措,例如客诉,生产质量突然出现异常等.针对这样的事情,一些有经验的人研究了一套逻辑方法,用来规范问题处理之细部过程和步骤,并归纳成8个原则(8 Disciplines),使当事人能清楚的知道一步一步该做什么,经过这样的步骤,问题的处理及解决通常较圆满.因此8D的方法很快地在工业界中广泛流传.例如Delta、Compaq、Astec等大公司已把8D作为解决问题的标准程序.二:范围该方法适用于解决各类可能遇到的简单或复杂的问题.8D方法就是要建立一个体系,让整个团队共享信息,努力达成目标.8D本身不提供成功解决问题的方法或途径,但它是解决问题的一个有用的工具.三:作用1.提高解决问题的效率,积累解决问题的经验;2.提供找出现存的与质量相关问题的框架,杜绝或尽量减少问题重复出现;3.8D格式的原则是针对出现的问题,找出问题产生的根本原因,提出短期,中期和长期对策,并采取相应行动措施, step by step,防范问题处理的一些非技术性的错误,及防止问题处理疏失遗漏带来不必要的损失.四:精神1.面对问题不可以各自为政、自我本位主义,否则将无法有效解决问题;2.面对问题应群策群力,互相帮助、相互提拔、如此才能彻底解决问题. 五:定义8D又称团队导向问题解决方法TOPS(Team Oriented Problem Solving),是福特公司处理问题的一种方法,亦适用于制程能力指数低于其应有值时有关问题的解决,它提供了一套符合逻辑的解决问题的方法,同时对于统计制程管制与实际的品质提升架起了一座桥梁。
8D(8 Disciplines)方法包含8个解决问题的步骤.它基于使用描述工具,格式化,分析,量化等工具,从而提供彻底解决问题的指引.主要步骤包括D1:小组成立D2:问题说明D3:实施并验证临时措施D4:确定并验证根本原因D5:选择和验证永久纠正措施D6:实施永久纠正措施D7:预防再发生D8:小组祝贺●问题: 被发现的具体问题,它包括:1.与正常状况相比,属于失常的现象,在这种情况下,需要予以纠正,使其恢复初始正常状况.2.为提高质量的目的而改变目前的状况.●纠正措施:(按ISO8402标准定义)针对现存的不合格项或缺陷所采取的纠正措施,并杜绝或尽量减少重复问题出现.●预防措施:(按ISO8402标准定义)针对潜在的不合格项或缺陷所采取的纠正措施,并杜绝或尽量减少重复问题出现.六:在下列情形中须提交8D报告1.当客户在工厂现场的稽核中发现不合格项或缺陷时,对于严重不良,主要不良及重复发生的次要不良须提交8D报告;2.OQC发现严重不良,主要不良及重复发生的次要不良须提交8D报告;3.当市场上发现有重复发生的产品缺陷时须提交8D报告;4.当ORT(持續性壽命測試)测试过程中发现缺陷时须提交8D报告;5.IPQC在同一生产现场连续发现三个位置相同不良现象或三个原因相同不良现象;6.要对那些需要长期纠正措施来解决的缺陷采取行动时,须提交8D报告;7.相关程序文件明确要求提交8D报告时.七:提交报告时间要求1.在发现问题的24小时内,提交包含所采取的暂时措施描述的8D报告;2.在发现问题的72小时内,提交包含问题发生原因的初步分析的报告. 八:结论8D格式用于监控解决问题的过程,它不是一个详尽的报告或复杂的分析,描述工具,而是一个包含了解决问题的每个步骤的集合,因而可从其中找到经提炼的基本信息.。
外观不良8D报告

1D:团队分析团队:团队长:总监成员:审核团队:团队长:成员:批准人员:供应商领导:2D:问题描述产品型号:发生时间:检验数:产品类型:PCM 异常类别:外观不良不良数:现象:1、2015年9月9日贵司试产HB366481的来料不良图片,其中脏污不良0.99%,定位孔不良104PCS,异物、压伤不良48PCS,不良率1.98%,2、此板为打样试产板,目前我司仓库已无该板库存,在线有小批量试产板6.5K在钻孔工序,将不良信息反馈给产线,重点管控以上不良3D:原因分析1、脏污产生原因:从不良图片分析,此不良为异物反粘板面造成脏污,查询产线生产工具,产线装板使用吸塑盒部分存在胶状物质,容易返粘板面造成脏污2、孔内毛刺、油墨入孔产生原因:此板为无卤素材料,材料脆性较大,钻孔后孔内位置毛刺无法避免,因毛刺未及时处理,阻焊之后孔内油墨不易显影完全,存在油墨残留现象3、黑油物产生原因:从不良图片分析,此不良为黑油印刷前,清洁不足导致,近期无尘车间改造,造成外来杂物增加,生产过程中清洁不到位容易导致杂物残留4、不良流出原因:此板为试产样品,检查人员检板过程中,为尽量满足多交货,针对部分外观缺陷问题板未做报废,导致不良流程4D:应急措施1、此板为试产板,贵司已无该板库存2、我司仓库已无该板库存3、在线6.5K二次打样板,在钻孔工序,项目组重点跟进以上异常5D:已进行的纠正行动验证:1、针对所有吸塑盘进行检查,有脏污、异物的统一挑出清洁,避免异物反粘板面2、目前产线施工改造已经完成,无尘室车间无尘含量达标,黑油每次印刷前,按要求清洁台面网版,防止杂物残留6D:永久纠正行动:1.钻孔后针对毛刺突出不良,安排刮毛刺处理(要求,孔径必须合格),钻孔后增加除胶渣流程,减少孔壁粗糙度2.入检验标准对员工进行培训;7D:防止问题再发生的措施1.针对所有新项目样品研发阶段必须严格执行合同评审制度,针对特殊工艺或软硬结合产品要求研发部门必须组织工程、生产、工艺、品质共同评估工艺及操作可行性,确定相关检验标准和验证方案并形成有效记录和控制计划来指导一线生产;2.所有新产品转批量之前必须出具样品品质记录、客诉记录及过程重要工艺问题点记录经品质经理和技术总监审核、副总批准后方能正式投料生产;8D:解决问题小组工作的认可。
经典8D改善报告

8D Report 8D 报告Supplier:供应商8D-Number Supplier:供应商8D 编号GZ-15-251GZ-15-251Step步骤D0D1D2D3D4.1 and D4.2D5.1 and D5.2D6.1 and D6.2D7D8Target Date:计划完成日期11月11日11月12日11月11日24 Hours 小时11月13日7Days 天11月13日60 Days 天Completion Date:实际完成日期11月11日11月11日11月11日24 Hours 小时11月12日4Days 天14-Nov-15D0Webasto Plant:工厂有限公司Part Name:零件名称Part-No.(Customer):客户零件号Part-No. (Webasto):WRS 零件号Release-No.:图纸批准编号Release-Date: 图纸批准日期LID 34002012/12/19Webasto's Customerstock伟巴斯特客户库存Webasto's in house stock伟巴斯特库存Field售后(质量担保期内)In Transportation运输途中Supplier Stock 供应商库存/5200//5131D1Department 部门2e@Actual:实际完成时间Actual:实际完成时间有限公司8D-Start date:8D 开始日期Report Last Update Dat :8D 更新日期Complaint No. from Customer : 客户投诉编号2015/11/102015/12/18Repeated Claim:重复抱怨Awareness 情况了解Sketch/ Picture 图片简介Vehicle:车型Model:平台KSAInitial Problem Description from Webasto:初步问题描述Total no. of affected bad parts: 可疑品数量和范围Webasto Spezification :伟巴斯特图纸要求Tracibility Code (Lot Number / Date Code /Batch - no. / Order no.) 追溯代码(批号/日期代码/批次/订单号)J51019310Team (Name, Dept., Tel.- No., E-Mail)团队信息(姓名,部门,电话,人数)Name:姓名Telephone 电话E-Mail 邮件XX XX:1355155552122@ XX:157********ei@XXXXX:130767184XX:186********A@ XX :16875185XXContainment Implementation requested by:限定临时遏制措施完成时间2015年11月15日2015年11月13日Countermeasure Implementation requested by:限定纠正措施完成时间2015年11月25日2015年11月20日Problem Timetable问题时间表Team Leader:组长Team Members:组员Champion :高层领导11/11日客户联络电路板外壳表面缺料(如右图描述)Close 8D 关闭8D 报告Task Progress.Indicate target and completiondates.任务进度。
NEC出货问题点检讨-8d报告 - 副本
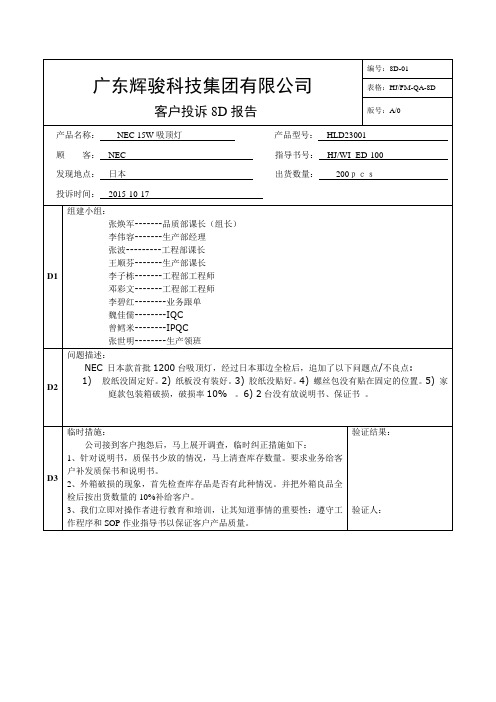
D4 查找根本原因:确定并验证事故发生的根本原因,分析情况如下:1、透明胶带不够力被拉长了,使胶带松动。
2、PE胶纸粘性不强,导致螺丝包在运输过程中受到颠簸而偏离其原来固定的位置。
但是我们生产的时候,每一个工序是完全按照客户样板来制定的作业指导书(SOP)作业的,并且螺丝包是贴在固定的一个位置的。
3、外箱厚度是3.0mm,卡扣的开口位置是3.5mm,卡口孔位尺寸偏小,员工生产包装的时候导致纸箱破损。
验证结果:验证人:张波、李伟容D5 永久性纠正措施:1、让采购寻找粘性更强的PE胶纸来替代现有的PE胶纸。
2、粘贴PE胶纸工位追加粘贴后用手反复按压PE胶纸三次以确保PE胶纸最大面积和底盘粘合。
3、品质抽样时将螺丝包是否固定紧,位置是否正确作为一个重点项目来检查;并在检查时用力晃动灯体以确定螺丝包和PE胶纸与底盘是否粘紧和移位。
4、加长透明封箱胶纸的长度,使其承受力的面积增加。
5、第一、外箱厚度是3.0mm,卡扣的开口位置是3.5mm,卡口孔位尺寸偏小,建议做到4mm。
第二、员工以后生产包装的时候,卡进去再退出来检查一边,检查纸箱是否破损。
6、对产品批次进行严格的数量管控,堵截少放或多放的现象发生。
D6 措施效果验证:1、做震动测试,测试报告随后附上。
2、进行全检,检查外箱卡口位置有无破裂现象。
验证(顾客反馈):D7 预防再发生:1、加强对产品生产和品质监督的管理、加强对员工进行作业指导书的培训。
2、修改作业指导书中的粘贴PE胶纸工位,追加粘贴后用手反复按压PE胶纸三次以确保PE胶纸最大面积和底盘粘合。
3、将封箱透明胶纸的长度再加长25mm,如下图此胶纸需尽量拉紧,尽量拉到底(红线位置)。
4、将封箱透明胶纸的粘贴长度和位置、PE胶纸的粘性和固定位置作为生产品质检查的重点工位来检查确认。
5、纸箱破损的情况严格按照永久性措施执行。
更改后胶纸的长度。
完成日期:2015-10-18 形成标准化:严格按照永久性措施执行。
线路板8D报告
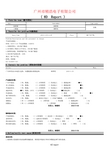
时间:2015-3-24 不良品数量:1440PCS地点:客户生产线机种:单面板ELC-E14067C-01CAction产品临时对策:真因分析:半成品库存: □有,数量: (□ 正常使用 □ 冻结返工 □ 报废处理) ■无仓库库存: □有,数量: (□ 返检后正常使用 □ 冻结返工 □ 禁用 ) ■无索赔品: □有(□ 正常使用 □ 工程变更 □ 转技服 □ 报废处理) □无负责人:林煜明 2015-3-25厂内库存品100%进行返检,问题板挑出报废处理。
林煜明 2015-3-25负责人:林煜明 2015-3-25未入库成品: □有,数量: (□ 正常使用 □ 冻结返工 □ 报废处理) ■无技服品: □有(□ 正常使用 □ 工程变更 □ 报废处理) □无客户材料库存: □有,数量: (□ 正常使用 □ 冻结返工 □ 报废处理) □无VMI库存: □有,数量: (□ 拿回公司返工 □ 在客户端挑选 □ 正常使用) □无在途成品: □有,数量: (□ 正常使用 □ 冻结返工 □ 批退 □ 禁用 ) ■无广州市精浩电子有限公司4.没打真空包装交货。
100%1.表面有黑点。
30%(客户描述)Who 成品库存: ■有,数量:10PCS (□正常使用 □ 冻结返工 ■报废处理) □无1.板面黑点是板面垃圾或油墨渗漏造成。
原因是环境灰尘和丝印模板处理不到位造成。
物料临时对策:2.丝印移位,焊盘大小不均匀。
10%(客户描述)不良状况描述: 。
厂内半成品: □有,数量: (□ 正常使用 □ 冻结返工 □ 报废处理) ■无When3.阻焊层渗透,导致焊接不良。
5%(客户描述)3. Contain the problem (采取应对措施)产线的物料: □有,数量: (□ 正常使用 □ 退仓库 □ 供应商返工 □ 禁用 ) ■无供应商在途品: □有,数量: (□ 正常使用 □ 冻结返工 □ 批退 □ 禁用 ) □无供应商内库存: □有,数量: (□ 正常使用 □ 冻结返工 □ 禁用 ) □无4.Define/verify root cause(原因分析)2.丝印移位是印板时对位不准,网版偏移导致丝印移位。
8D报告完整版范文

8D报告完整版范文8D是一种问题解决方法,通过8个步骤来进行问题的分析和解决。
下面是一个完整版的8D报告,包含对问题的描述、团队成员、问题的分析、解决方案以及实施结果的评估。
1.问题描述:在公司生产线上,发现了一个质量问题,产品出现了大量次品,导致客户抱怨并要求退货。
问题主要体现在产品的外观质量方面,表面容易出现划痕和凹痕。
2.团队成员:该问题的解决由以下团队成员共同参与:-生产部门:负责产品制造的技术人员和操作工-质量控制部门:负责产品质量的技术人员和检验员-客户服务部门:负责与客户沟通和解决问题3.问题的分析:通过团队成员的讨论和原因分析,我们找到了导致产品质量问题的几个主要原因:-工人操作不规范:工人在产品组装和包装时没有按照操作规程进行操作,导致产品出现划痕和凹痕。
-零部件供应商的质量问题:部分零部件的质量不达标,容易导致产品出现质量问题。
-质量控制不严格:质量控制部门在产品质量检验中存在一定的盲区,没有发现产品质量问题。
4.解决方案:基于问题分析,我们提出了以下解决方案来解决产品质量问题:-进行员工培训:对所有参与生产的员工进行质量意识培训和操作规程培训,确保所有员工按照规范进行生产操作。
-与供应商合作:与零部件供应商建立长期合作关系,并要求供应商提供质量合格证明。
对于质量不达标的零部件,及时通知供应商进行更换或修复。
-加强质量控制:质量控制部门要加强对产品质量的检验,制定更为细致的产品质量检验标准,并对产品检测设备进行定期维护和校准。
5.解决方案的实施:我们按照上述解决方案,分别进行了以下实施步骤:-员工培训:与人力资源部门合作,组织了一次质量培训会议,邀请专业培训师对所有员工进行培训,培训内容包括质量的重要性、操作规程和注意事项等。
-供应商合作:质量控制部门与供应商进行了紧急会议,并要求供应商提供质量合格证明。
部分质量不达标的零部件得到了及时更换和修复。
-质量控制加强:质量控制部门对产品质量检验标准进行了更新,并对产品检测设备进行了定期维护和校准。
8D报告(案例)

将此条款“所发货物必须用托盘装运,且托盘、包装、物料 D5.选择/验证 完好无损,本公司才给以接受,否则,本公司有权拒收,并
XXX有限公司
8D 报告 “质量问题和扣分原因”管控措施
D1. 团队成员 提出者:
成员:
日期:
***公司2015年第一季度质量得分为7(满分为10),扣分原 D2. 问题描述 因为货物包装有问题,物流为节省空间,把货物托盘给拆
了,导致包装受损。
D3. 实施/验证 临时措施
要求供应商下次发货时整改。
D4.确认根本 原因
D8.总结
购合同条款必须强化对包
装、托盘、运输等的违约
负责人 负责人
责任者 责任者
截止日期 2017.7.25 截止日期
2017.7月底
责任。 小组负责人
质量工程 师
批准
备注:附件——修订过的“采购合同”。
第 1 页,共 2 页
XXX有限公司
8D 报告
第 2 页,共 2 页
永久性措施 D6.实施验证
要求供方及时补发货物,本公司保留相关法律责任追究的权
力。”纳入采购合同中。
相关货物托盘、包装、装 负责人 责任者 截止日期
运强制性条款纳入采购合 同。
2017.7.20
D7. 预防再次 要求仓库管理员在收货时
发生
严格执行“采购合同”
与供应商的合作必须依据
“采购合同”为标准,采
CMAR12-307 0C 8D报告填写说明-STA 2015 12 9
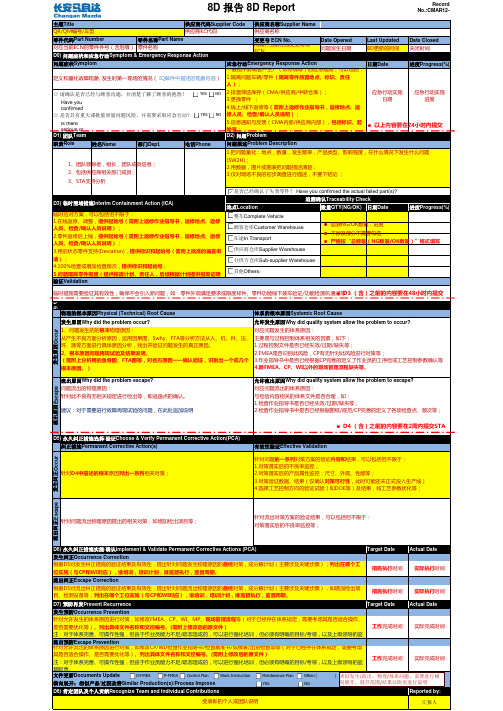
Record No.:CMAR12-307 0C变更号 ECN No.Date OpenedLast Updated Date Closed 问题件当前工程变更等级ECN问题发生日期8D更新的时间关闭时间日期Date进度Progress(%)Have you confirmed with customer and be clear about the complaint?Is there serious or batch quality risk? And take ERA?姓名Name部门Dept.电话Phone数量QTY(NG/OK)日期Date 进度Progress(%)D4) 根本原因Root CauseTarget Date Actual Date Target DateActual DateReported by:汇报人应急行动实施日期应急行动实施进度1.把问题量化:地点,数量,发生频率,产品类型、影响程度,在什么情况下发生什么问题(5W2H);2.用数据,图片或图表把问题描述清楚;3.仅对现场不良的初步调查进行描述,不要下结论 ;临时应对方案,可以包括但不限于:1.在线返修、调整,提供起始号(需附上返修作业指导书,返修地点、返修人员、检查/确认人员说明);2.零件返修后上线,提供起始号(需附上返修作业指导书,返修地点、返修人员、检查/确认人员说明);3.用旧状态零件支持(Deviation),提供标识和起始号(需附上批准的偏差申请);4.100%检查或增加检查频次,提供标识和起始号;5.问题隔离零件报废(提供报废计划、责任人,后续根据计划提供报废证明职责Role问题描述Problem Description定义和量化故障现象, 发生时第一现场的情况( IQ邮件中描述的现象内容)一般指不影响客户生产(如停线等)的应急措施,可以包括:1.隔离问题车辆/零件(隔离零件放置地点、标识、责任人);2.排查筛选库存(CMA/供应商/中转仓库);3.更换零件 ;4.线上/线下返修等(需附上返修作业指导书,返修地点、返修人员、检查/确认人员说明);5.信息通知与反馈(CMA内部/供应商内部),包括标识、起始号;◇ 请确认是否已经与顾客沟通,并清楚了解了顾客的抱怨?◇ 是否具有重大或批量质量问题风险,并需要采取应急行动?D1) 团队Team D2) 问题Problem 在途In Transport问题症状Symptom应急行动Emergency Response Action8D 报告 8D Report主题Title供应商代码Supplier Code 供应商名称Supplier Name QR/QM编号/车型供应商KC代码供应商名称零件代码Part Number零件名称Part Name对应当前ECN的零件件号(含后缀)零件名称D0) 问题症状和应急行动Symptom & Emergency Response Action 供应商仓库Supplier Warehouse 分供方仓库Sub-supplier Warehouse 整车Complete Vehicle 顾客仓库Customer Warehouse D3) 临时围堵措施Interim Containment Action (ICA)追溯确认Traceability Check地点Location是否已经确认了失效零件? Have you confirmed the actual failed part(s)?其他Others :验证Validation物理的根本原因Physical (Technical) Root Cause 体系的根本原因Systemic Root Cause发生原因O c c u r发生原因Why did the problem occur?允许发生原因Why did quality system allow the problem to occur?临时措施需要验证其有效性,确保不会引入新问题,如:零件外观满足要求或限度样件、零件功能线下装车验证/功能检测机通过等1、问题发生的的根本物理原因:从产生不良方面分析原因,运用因果图、5why、FTA等分析方法从人、机、料、法、环、测等方面进行具体原因分析,找出并验证问题发生的真正原因。
ZL_CD2313 德赛西威8D报告 20150318

D8
我们将继续跟踪贵司的下一步生产情况, 不遗余力的配 合贵司的相关测试。 我们将本着“客户第一、用户至上”的原则,以严格、 科学、系统的管理,向顾客提供更好的产品和服务。 Date:
王善喜
2015-03-18
7
反馈品 CD2313(REA1)0dB 波形
反馈品 CD2313(REA1) -1.25dB 波形
2
反馈品 CD2313(REA1)-2.5dB 波形
样品 CD2313(RLA3)0dB 波形
样品 CD2313(RLA3)-1.25dB 波形 B)室温 16℃,IIC 波形如下:
样品 CD2313(RLA3) -2.5dB 波形
反馈品 CD2313(REA1)-1.25dB 波形 F)高温 80℃,IIC 波形如下:
反馈品 CD2313(REA1)-2.5dB 波形
样品 CD2313(RLA3)-1.25dB 数据
-2.5dB(有应答)
反馈品 CD2313(REA1)-1.25dB 数据
6
-2.5dB(有应答)
Failure conclusion 通过常温,高低温的多项功能测试可以看出,现在这块客诉失效的 IC 与正常 良品一样,功能正常,没有复现该产品的失效现象,失效机理还待进一步解剖分析 研究。 Chosen permanent corrective action(s): D5 Implement corrective action(s): D6 Action(s) to prevent recurrence: D7 Close , congratulate your team: Responsible: Date: Signature Team Leader: Responsible:
8D报告

问题来源:天津HWN
发现日期:2015/6/17
编号:PZ150617-01
1.问题描述:
异物、披锋、刀纹
2.组成小组:黄安华、曾丽艳、杨海峰
3.临时对策:
责任人
完成日期
1.库存部分进行全检
曾丽艳
2015.06.17
遏制措施效果验证:
验证人
日期
已完成库存全检
黄安华
2015.06.17
4.寻找和确认根本原因:
1.此批落料是CNC机台第一次加工,由于正面保护胶纸黏度不够,部分产品在CNC最后收尾阶段偏动,出现披锋
2、异物属于未搽干净的胶,由于手工点胶无法控制胶量,导致部分溢胶,擦拭员工用无尘布的同一个地方接连作业10pcs以上所致。
3、侧面刀纹,属于刀具使用时间过长,磨损过大导致
5.选择永久措施:
责任人
完成日期
1.后续落料更改为冲压
2、要求升级K9侧按键SOP,里面增加:无尘布同一位置擦拭不得超出5-7pcs
3、规定每把刀具定额生产数量
小宝
马建明
杨海峰
1预计7/1模具OK 2下批生产前
3、24号
6.永久措施效果验证:
1.待验证
2.待验证
3.待验证
验证人:
验证时间:
7.系统预防措施:
责任人
完成日期C监督检查擦拭岗位员工实际执行
黄安华
曾丽艳
每批次
8.证据清单:
二维码无法识别8D报告

标红部分二维码编码相同, 全部是GJF1434501290875
D0
D1
D2
D3
D4
D5
D6
ቤተ መጻሕፍቲ ባይዱ
D7
D8
? D4 Root Cause(s) and Escape Point(s) 分析根本原因 证据2:不良件没有扫描的证据
重新生成箱号为712箱的120件产品的二维码,通过对比,没有与不良产品二维 码相同的
? D1 Team 成立小组 ? D2 Problem Description 问题描述 ? D3 Interim Containment Action(s) 临时围堵措施 ? D4 Root Cause(s) and Escape Point(s) 分析根本原因 ? D5 Chosen Permanent Corrective Action(s) 选择永久纠正措施 ? D6 Implemented Permanent Corrective Action(s) 执行永久纠正措施 ? D7 Systemic Prevent Recommendations 系统性的预防措施建议
BMTY06 二维码无法识别调查分析报告
D0
D1
D2
D3
D4
D5
D6
D7
D8
Guangdong Hongtu(nantong) Diecasting Co.,Ltd
GM responsible team 2015-3-29
1
content 目录
? D0 Symptom(s) and Emergency Response Action(s) 影响及紧急反应对策
不良件所在箱号 712
不良件下箱日期12.11
8D报告励国-恒东辉-2015-12-31

更改的文件类型(Change the file type):
FMEA(失效模式及效果分析)x控制计划(Control Plan)
X操作指引(Work Instruction)
X检验指引(Inspection Instruction)
图纸(Drawing)规格(SPEC)
负责人(Responsible):完成时间(Target Date):
D4.原因分析(Cause Analysis):
不良原因(DefectCause):
人为(Man)x设备(Equipment)x材料(Material)
环境(Environment)x方法(Method/Workmanship)
设计(Designer)客户Leabharlann 作(CustomerHandling)
分析员签名(Signature):李永思完成时间(Target Date):2015-12-31
D5.长期对策(Long TermCorrective Action):
1、廷长波峰浸锡时间,降低连输速度,
2、以及波峰焊的日常维护保养。
3、确保产品引脚表面焊盘稳定性(严格按照工艺制程,杜绝SMT红胶,以及污染物)。
1、在显微镜下观察客户提供的样品,未发现氧化现象,见图片:
2、将客户提供的材料样品做可焊性试验;引脚焊点外观饱满光亮,没有发现上锡不良现象。
3、综上分析过程,在其上锡焊接工艺上找原因,通常此类不良问题出现在波峰焊的第一波峰扰流波上锡不良。
4、PCB焊盘和该SOD原件金属接触面积比例较大,留有的上锡区间面积较小,需要适度外延焊盘,目前对策是增加SMT贴片精度定位。
1、新产品上线前,必须由工程确认,品质确认,跟进(跟进结果出产品试产报告)。
注塑、吹塑产品8D报告模板
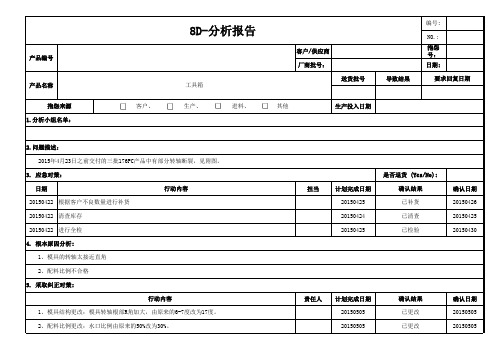
6.效果确认: 1、模具更改的位置之前和之后的对比。 2、配料比例之前的标准书和更改后标准书。 3、之前产品和改模之后产品的对比。见附图。 7. 恒久对策(防止再发生对策): 责任人 计划完成日期 20150505 20150505 20150505 确认结果 已培训 已培训 已更改 确认日期 20150505 20150505 20150505
1、产品设计阶段充分考虑批产时可能出现的各种问题,将隐患消灭在开发阶段。见附件(培训记录)。 2、其他类似产品结构,在不影响装配的情况下R角尽量加大。 3、更新配料标准书。 8.向小组祝贺(问题关闭): 相关文件更改: 作业指导书 检验指导书 控制计划 图纸
过商 产品编号 厂商批号: 送货批号 产品名称 抱怨来源 1.分析小组名单: 客户、 工具箱 生产、 进料、 其他 导致结果
编号: NO.: 抱怨号: 日期: 要求回复日期
生产投入日期
2.问题描述: 2015年4月23日之前交付的三批176PC产品中有部分转轴断裂,见附图。 3. 应急对策: 日期 20150422 根据客户不良数量进行补货 20150422 清查库存 20150422 进行全检 4. 根本原因分析: 1、模具的转轴太接近直角 2、配料比例不合格 5. 采取纠正对策: 行动内容 1、模具结构更改:模具转轴根部R角加大,由原来的6-7度改为17度。 2、配料比例更改:水口比例由原来的50%改为30%。 责任人 计划完成日期 20150505 20150505 确认结果 已更改 已更改 确认日期 20150505 20150505 行动内容 担当 计划完成日期 20150425 20150424 20150425 是否退货 (Yes/No): 确认结果 已补货 已清查 已检验 确认日期 20150426 20150425 20150430
平面度不良对策报告_8D报告案例

Approved madeWang LiuTo:STT-A Fax:ATTN:CC:Phone:Date:2015-5-6RE:win deformation causing Flotaing on Board由于产品不良给贵司带来的麻烦深表歉意,收到贵司的信息后,我们立即展开调查。
Very sorry for the defect makes you getting in trouble, while received your information, we investigated the matter immediately反馈日:2011-3-3Feedback date: 2011-3-3品名:1-842-700-11ITEM NO: 1-842-700-11不良内容:组品平面度不良Defect content: Pre-case founded win deformation causing floating on board不良率:7%Defect rate: 7%発生原因(happen reason)根据客户寄送的不良样品,内部用PCB板进行了确认。
1.标示平面度在0.6mm以下所有样品,插入PCB后均没有翘起,是OK品。
2.标示平面度超过0.6mm的所有样品,框架面明显变形,插入PCB后均有明显翘起,而且不能插入插板。
3.框架面变形推定发生原因之一可能为工序中拿取不注意导致。
工序F插座铆装或插板检验时拔取不规范可以再现类似的产品变形。
4.另外还有可能为落下品混入。
The un-plat defect samples have been sent to my company, and confirm it with our PCB board.Confirm result:1.The marked un-flatness of the parts below 0.6mm seems no obvious gap between the parts and PCB. It is OK parts.2.The marked un-flatness of the parts over 0.6mm bent obviously,the gap is very obvious between the parts and PCB after inserting into the PCB3. We think the bent maybe caused for the careless when the part was take out from thejig in the caulking process. They can be reappeared for the abnormal operation whendrawing off the parts in the F connector caulking or jig check process .4. And also maybe it is the defect parts mixed which had been dropped to the floor before.流出原因(outflow reason):1. 该产品的平面度没有在图纸上明确定义,因此内部并无列入管控。
外观不良8D报告

主题:外观不良(脏污、定位孔不良、黑油下异物等)1D:团队分析团队:团队长:总监成员:审核团队:团队长:成员:批准人员:供应商领导:2D:问题描述产品型号:发生时间:检验数:产品类型:PCM 异常类别:外观不良不良数:现象:1、2015年9月9日贵司试产HB366481的来料不良图片,其中脏污不良0.99%,定位孔不良104PCS,异物、压伤不良48PCS,不良率1.98%,2、此板为打样试产板,目前我司仓库已无该板库存,在线有小批量试产板6.5K在钻孔工序,将不良信息反馈给产线,重点管控以上不良3D:原因分析1、脏污产生原因:从不良图片分析,此不良为异物反粘板面造成脏污,查询产线生产工具,产线装板使用吸塑盒部分存在胶状物质,容易返粘板面造成脏污主题:外观不良(脏污、定位孔不良、黑油下异物等)2、孔内毛刺、油墨入孔产生原因:此板为无卤素材料,材料脆性较大,钻孔后孔内位置毛刺无法避免,因毛刺未及时处理,阻焊之后孔内油墨不易显影完全,存在油墨残留现象3、黑油物产生原因:从不良图片分析,此不良为黑油印刷前,清洁不足导致,近期无尘车间改造,造成外来杂物增加,生产过程中清洁不到位容易导致杂物残留4、不良流出原因:此板为试产样品,检查人员检板过程中,为尽量满足多交货,针对部分外观缺陷问题板未做报废,导致不良流程4D:应急措施1、此板为试产板,贵司已无该板库存2、我司仓库已无该板库存3、在线6.5K二次打样板,在钻孔工序,项目组重点跟进以上异常5D:已进行的纠正行动验证:主题:外观不良(脏污、定位孔不良、黑油下异物等)1、针对所有吸塑盘进行检查,有脏污、异物的统一挑出清洁,避免异物反粘板面2、目前产线施工改造已经完成,无尘室车间无尘含量达标,黑油每次印刷前,按要求清洁台面网版,防止杂物残留6D:永久纠正行动:1.钻孔后针对毛刺突出不良,安排刮毛刺处理(要求,孔径必须合格),钻孔后增加除胶渣流程,减少孔壁粗糙度2.入检验标准对员工进行培训;主题:外观不良(脏污、定位孔不良、黑油下异物等)7D:防止问题再发生的措施1.针对所有新项目样品研发阶段必须严格执行合同评审制度,针对特殊工艺或软硬结合产品要求研发部门必须组织工程、生产、工艺、品质共同评估工艺及操作可行性,确定相关检验标准和验证方案并形成有效记录和控制计划来指导一线生产;2.所有新产品转批量之前必须出具样品品质记录、客诉记录及过程重要工艺问题点记录经品质经理和技术总监审核、副总批准后方能正式投料生产;8D:解决问题小组工作的认可主题:外观不良(脏污、定位孔不良、黑油下异物等)1、分析团队对2D意见/时间、审核团队对2D意见/时间(2D出来2小时内应经审核团队长确认);客诉现象和客户反馈一致/王成谷/2015/9/112、审核团队对3D意见/时间;原因分析属实确认OK / /2015/9/113、审核团队对4D意见/时间;临时应急措施得当 / /2015/9/114、审核团队对5D意见/时间;纠正措施有效已实施 /2015/9/115、审核团队对6D意见/时间;流程卡已按新工艺制作、相关检验标准已下发检验工序/(代)/2015/9/116、审核团队对7D意见/时间;预防措施合理 /李伟正(代)/2015/9/11批准:审核:拟制:。
汽车行业8d报告案例
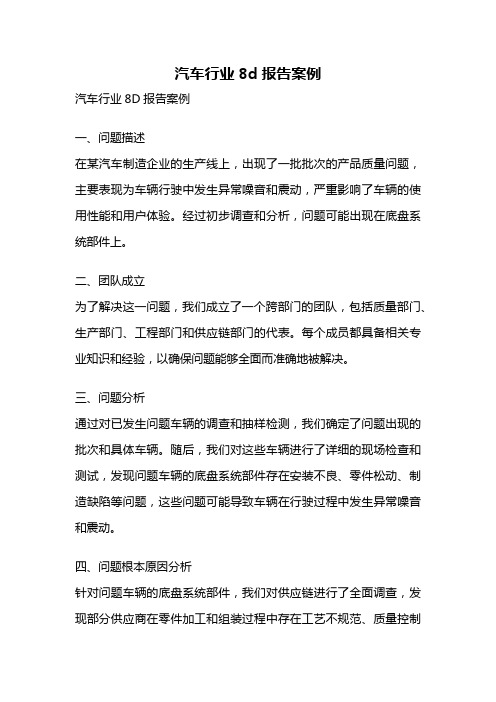
汽车行业8d报告案例汽车行业8D报告案例一、问题描述在某汽车制造企业的生产线上,出现了一批批次的产品质量问题,主要表现为车辆行驶中发生异常噪音和震动,严重影响了车辆的使用性能和用户体验。
经过初步调查和分析,问题可能出现在底盘系统部件上。
二、团队成立为了解决这一问题,我们成立了一个跨部门的团队,包括质量部门、生产部门、工程部门和供应链部门的代表。
每个成员都具备相关专业知识和经验,以确保问题能够全面而准确地被解决。
三、问题分析通过对已发生问题车辆的调查和抽样检测,我们确定了问题出现的批次和具体车辆。
随后,我们对这些车辆进行了详细的现场检查和测试,发现问题车辆的底盘系统部件存在安装不良、零件松动、制造缺陷等问题,这些问题可能导致车辆在行驶过程中发生异常噪音和震动。
四、问题根本原因分析针对问题车辆的底盘系统部件,我们对供应链进行了全面调查,发现部分供应商在零件加工和组装过程中存在工艺不规范、质量控制不严格的问题。
这些问题导致了底盘系统部件的质量不稳定,从而引发了车辆的异常噪音和震动。
五、制定纠正措施针对问题车辆的底盘系统部件,我们制定了以下纠正措施:1.与供应商加强合作,要求其加强工艺控制和质量管理,确保零件加工和组装的准确性和稳定性。
2.对受影响的车辆进行召回,重新检查和更换底盘系统部件,以消除问题。
3.制定更严格的质量检测标准和流程,确保问题不再出现。
六、纠正措施的实施我们与供应商密切合作,对其工艺进行了全面审查和改进。
同时,我们组织了专门的团队对受影响的车辆进行召回和维修工作,确保底盘系统部件的质量问题得到彻底解决。
此外,我们还建立了更加严格的质量检测标准和流程,以防止类似问题再次出现。
七、效果验证经过纠正措施的实施,我们对受影响车辆进行了再次检测和测试。
结果显示,车辆的异常噪音和震动问题得到了有效解决,车辆的使用性能和用户体验得到了明显改善。
八、预防措施为了避免类似问题的再次发生,我们制定了以下预防措施:1.与供应商建立长期稳定的合作关系,加强对其工艺和质量管理的监督。
8D报告案例分析幻灯片

2
17
D8——结案并祝贺
? 1. 此问题已经完全处理清楚,可以结案(close)
? 2. 并且今天晚上叫张三、李四、王五老婆一 起庆祝团队成功。
? 经过八个步骤后,整个处理过程就算彻底清楚 和完整了,问题的原因找到了,对应措施也出来 了,问题也解决了,可以保证以后不会再出现这 类事情了。
2
18
感谢聆听!
? 1. 早晨上班出门前一定要检验水龙头是否关闭。
? 2. 以后洗蔬菜时一定要把烂蔬菜叶丢到垃圾 筐里,并且要把地面清理干净。
? 3. 早晨洗脸时不能带电话在身上。在洗脸过程 中,就算电话铃响起也不能接。直到洗漱完毕后 才能接听手机。
? 责任人:小王
? 预计完成时间:2015年2月10日
? 验证人:小王老婆
? 问“为什么吸不上油来?”答“因为油泵轴磨损、松动了。”
? 问“为什么磨损了呢?”再答“因为没有安装过滤器,混进了铁屑等杂质。”
? 经过连续五次不停地问“为什么”,才找到问题的真正原因和解决的方法,
在油泵轴上安装过滤器。
? 如果我们没有这种追根究底的精神来发掘问题,我们很可能只是换根保险
丝2 草草了事,真正的问题还是没有解决。
2
5
D1——成立改善小组:
? 马上叫上住在隔壁的几个同事,组成事故处理 小组。
? 小组成员:
张三、
李四、
小王。
2
6
D2——问题描述:
? 小王家中被水淹,家中所有摆放在地上的物品 都浸在水中(不良率100%)。
? 如:草席、被子和书本等。
27Leabharlann D2——问题描述:What
什么问题?/当前状况是什么?
When
- 1、下载文档前请自行甄别文档内容的完整性,平台不提供额外的编辑、内容补充、找答案等附加服务。
- 2、"仅部分预览"的文档,不可在线预览部分如存在完整性等问题,可反馈申请退款(可完整预览的文档不适用该条件!)。
- 3、如文档侵犯您的权益,请联系客服反馈,我们会尽快为您处理(人工客服工作时间:9:00-18:30)。
问题描述Statement of Nonconformance 填写Interpolation Discipline 2 ** 16949:2015 There is not fully effective in the calibarion process(STATEMENT OF NONCONFORMITY) 在计量过程不是完全有效的(不符合项) In the machining workshop, some of the equipments are not re-calibrated prior to expire. Such as, caliper S/N 184840, micro-caliper S/N 041176.(OBJECTIVE EVIDENCE) 在机加工车间,部分用于机加工的量具在过期前没有进行再次校准。(客观证据) Is not a serious nonconformities : 不是一个严重不符合项 : 1. The equipment is used only for machining process, the subsequent products for measurement and in the period of validity of caliper and micrometer are assembled before the inspection; 2. Product quality qualification; 3. Customers don't have any complaints about the quality of the product; 1. 这些设备只用于机加工工序,后续的产品都用已经计量并且在有效期内的卡尺和千分尺进行装配前的检验; 2. 成品质量合格; 3. 顾客没有任何的关于产品质量的投诉;
Discipline 行动
3
围堵措施Remedy Actions
填写Interpolation
***
1. 质量部对过期前没有进行再次校准的量具列入周期鉴定计划内,并送至国家认可的实验室进行 鉴定。 2. 对其他量具进行检查,以防类似事故发生。 1. 质量部已对过程检验的,过期前没有进行再次校准的量具送至国家认可的实验室进行了鉴定, 并取得证书。 2. 经过对其他量具的检查,没有类似事故。 5 确认根本原因Identification Root Cause 填写Interpolation ***
Discipline
7 预防措施 Preventive Actions
填写Interpolation
***
由管代对质量部制定的检具效验计划的执行情况进行监督 Amend documents to prevent happen similar nonconformity. 证据列表 Discipline 8 《效验证书》 《监视和测量设备控制程序》培训记录 修改后的《监视和测量设备控制程序》 填写Interpolation ***
*******公司 Discipline 参ห้องสมุดไป่ตู้部门 Department 团队成员 Member 1 组长 **
8D改进报告 The Report of 8D Improvement
团队组成 Team Compose 技术部 ** 质量部 ** 填写Interpolation
编号Number ****** Date ****
验证 4 Discipline
1.在监视和测量设备控制程序中,虽然明确要求编制计量器具的检定计划,并按计划要求进行检定,但是没有规定相 关责任人,以及完成情况进行监督,导致部分计量器具没有进行检定。 纠正措施Corrective Actions 填写Interpolation Discipline 6 *** 1.对监视和测量设备控制程序文件进行修订,明确规定:"新购计量检测设备的周期检定,由计量管理员按《计量器 具周期检定计划》在计划检定日前5天通知计量器具各使用部门做好准备,确定具体检定日期并实施检定,管代对其 完成情况进行监督"。 2.对修改后的文件进行学习。 验证 1.对文件修改完毕。 2.对质量部相关人员进行《监视和测量设备控制程序》培训完毕,并有效。