绕管换热器(谷风研究)
绕管式换热器的布置及管道设计方案研究

绕管式换热器的布置及管道设计方案研究摘要:换热器设备在化工装置当中的应用是十分广泛的。
在整个工程当中,换热器的数量以及投入的资金都占据着非常大的比例。
并且在整个工程当中也占有着一个十分重要的地位。
绕管式换热器能够适应非常大的温度区间,并且是一种高效紧凑的换热器,能够承受住热量的冲击,并且这种换热器的自身也带有消除热应力的能力。
因此绕管式换热器具有节能环保的特点,近些年来绕管式换热器应用的越来越广泛。
关键词:绕管式;换热器,管道设计换热器可以在工业生产当中完成物料之间热量的传递。
换热器是一种通用的工艺设备,在许多领域当中都广泛应用,比方说化工,炼油和原子能等等。
换热器在化工以及炼油等工业产业当中的应用是非常重要的。
换热器在化工厂的建设投资比重当中,可以占到总投资的10%到20%。
在石油炼厂当中的占投资比例更是高,可以占到全部工艺设备投资的35%到40%。
绕管式换热器属于间壁式管式换热器。
这是从传热原理上进行区分的。
因为管式换热器具有耐高压的性能,而绕管式换热器也具有同样的性能。
不仅如此,绕管式换热器的结构比较紧凑,传热效率也比较高。
绕管式换热器的传热管是非常长的,可以达到50到60米,甚至有一些更长的可以达到150到160米。
这种换热器特别适合应用在低温下的气体分离装置当中,比方说空气分离装置,稀有气体分离装置等等。
一、绕管式换热器的特点和应用对于一些普通的换热器来说,绕管式换热器是有其独特的优势的,绕管式换热器的构成比较特殊。
传热器是按照螺旋的形式交替缠绕在芯筒和外筒之间的空间内的。
绕管式换热器是不存在流动死区的,并且这种换热器的应用范围比较广。
它能适用的温度区间也比较大。
面对热冲击的能力也是非常强的,可以利用自身的特点来消除热应力,紧凑度也比较高。
绕管式换热器和普通换热器还有一个最大的特点。
就是绕管式换热器可以设置多股管,这样一台换热器就可以满足多股流体的同时换热。
正是由于绕管式换热器的这样的特点,现在绕管式换热器在化工装置当中应用的越来越广泛,并且占有了非常重要的位置。
【心得】干完绕管换热器后的心得体会
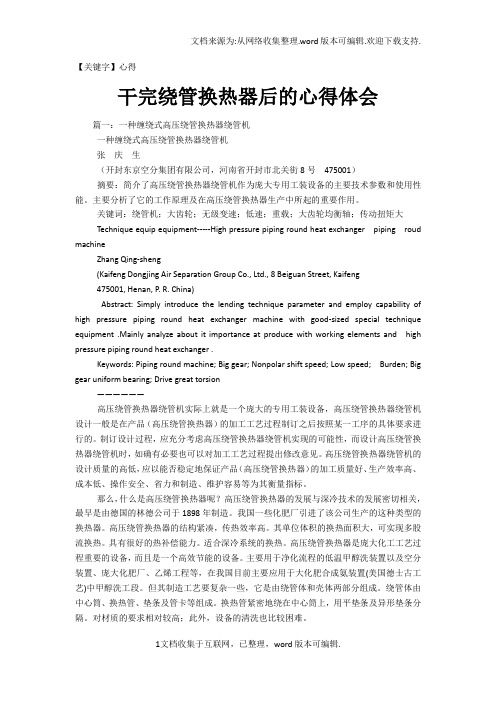
【关键字】心得干完绕管换热器后的心得体会篇一:一种缠绕式高压绕管换热器绕管机一种缠绕式高压绕管换热器绕管机张庆生(开封东京空分集团有限公司,河南省开封市北关街8号475001)摘要:简介了高压绕管换热器绕管机作为庞大专用工装设备的主要技术参数和使用性能。
主要分析了它的工作原理及在高压绕管换热器生产中所起的重要作用。
关键词:绕管机;大齿轮;无级变速;低速;重载;大齿轮均衡轴;传动扭矩大Technique equip equipment-----High pressure piping round heat exchanger piping roud machineZhang Qing-sheng(Kaifeng Dongjing Air Separation Group Co., Ltd., 8 Beiguan Street, Kaifeng475001, Henan, P. R. China)Abstract: Simply introduce the lending technique parameter and employ capability of high pressure piping round heat exchanger machine with good-sized special technique equipment .Mainly analyze about it importance at produce with working elements and high pressure piping round heat exchanger .Keywords: Piping round machine; Big gear; Nonpolar shift speed; Low speed; Burden; Big gear uniform bearing; Drive great torsion——————高压绕管换热器绕管机实际上就是一个庞大的专用工装设备,高压绕管换热器绕管机设计一般是在产品(高压绕管换热器)的加工工艺过程制订之后按照某一工序的具体要求进行的。
绕管换热器

• 2.3缠绕管换热器都是竖直运行,下管板与管子间 易产生间隙腐蚀,这也是较常见的破坏形式之一.因 此,胀接要做到二点:一是要有合适的胀度,消除间 隙,防止腐蚀;二是防止过胀,导致管板塑性变形,降 低了胀接的可靠度. • 2.4九江绕管胀接的胀度在管子穿穿管前进行了试 验,选择80MPa的胀度(75-90MPa之间)
目录:
• 一、绕管换热器的基本介绍 • 二、绕管各部件加工步骤及注 意事项 • 三、操作与维护
一、绕管换热器的基本介绍:
• 1.绕管式换热器是在与管板相连的中心筒上, 以螺旋状交替缠绕数层小直径换热管形成 管束,再 将管束放入壳体内的一种换热器。 • 管束由多层螺旋缠绕的换热管组构成,每 层换热管以相反的方向缠绕,每层换热管 用垫条隔开,垫条厚度由工艺计算的流体 通道要求确定(九江项目采用2mm厚度)并 采用异型垫条控制换热管的螺旋升角。在 设计盘管时同一层使用相同长度的管子绕 制,在同一管程的流道上管子应均匀布置。
• 优点:结构紧 凑、可同时进行多种介质换热、管 内操作压力高、传 热管的热膨胀可自行补偿、换 热器易实现大型化等 特点,因此,成为大型煤化工 装置低温甲醇洗系统的首选换热设备。 • 缺点:主要为检修、清理困难,所以一般用于较清 洁的工艺介质。
• 2.绕管式换热器按其结构特点分为两类:管
程单股流流道型(称为单股流绕管式换热器),
• 1.20绕制完成以后,对绕管体外部使用厚度 为2mm的不锈钢皮进行包裹,以防伤到管 子,等待与筒体进行套装,由此夹套还起 到导流作用,夹套与设备壳体间应保持一 定距离。如下图片:(E1610为例)
2制造过程的控制
2.1盘管的控制.盘管控制的好坏直接影响到换热器 的换热效率,尤其是对结垢情况影响较大.因此,盘管 时必须使层间距适度,没有窄间隙死角,防止局部区域 布置不均匀,造成流体阻塞,降低流体的流通面积. 2.2焊接的控制.缠绕管的损坏形式最常见的是管口 泄漏,这是设备的关键部位.一般缠绕管换热器为了提 高换热效率,采用管子都比较小和薄,焊接容易产生缺 陷.因此,焊接必须严格控制线能量,焊缝要均匀和饱 满.
缠绕管式换热器介绍
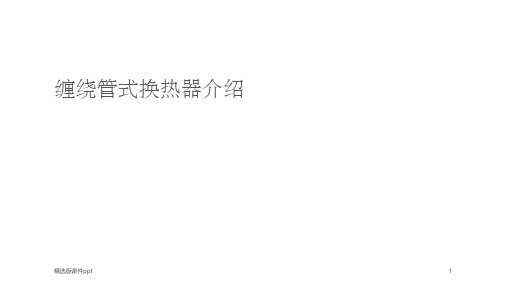
28
中海石油东营石化有限公司
29
盘锦北方沥青燃料有限公司
30
台湾化学纤维股份有限公司
精选版课件ppt
单元名称 40万吨/年重整装置 168万吨/年连续重整装置 80万吨/年连续重整装置 40万吨/年重整装置 330万吨/年连续重整装置 530万吨/年异构化装置 270万吨/年歧化装置 60万吨/年重整装置 2# 120万吨/年重整装置
5. 缠绕管式换热器管、壳程特殊的流态(管程流体方向的冲刷作用及截面方向的二次流;壳程 管间通道的变流速的脉冲流作用)使得换热器本身具有较强的自清洁能力,介质流单位流通截 面大于板壳式换热器,因此抗堵能力强于板壳式换热器。
精选版课件ppt
6
缠绕管式换热器与壳板换热器的比较
6. 若换热器内部出现积垢现象,缠绕管式换热器可以实现管程侧机械清洗以及管、壳程两 侧的化学清洗,而板壳式换热器仅能选择化学清洗,清洗的操作难度大、风险高且效果不 及缠绕管式换热器。
新建/ 改造 新建 新建 新建
替换板换 替换板换
新建 新建 新建 新建 新建
12
缠绕管式换热器在重整芳烃装置的应用
序号 51 52
用户名称 鹤壁世通绿能石化科技发展有限公司
东营威联化学有限公司
53
东营威联化学有限公司
54
中国石化扬子石油化工有限公司
55
宁夏宝廷新能源有限公司
56
中国石油哈尔滨石化分公司
120万吨/年芳烃项目连续重整装置
2018-02
144万吨/年连续重整装置
2018-01
100万吨/年催化重整装置
2018-05
100万吨/年叠合装置 150万吨/年芳烃联合装置(预加氢)
绕管换热器PPT课件
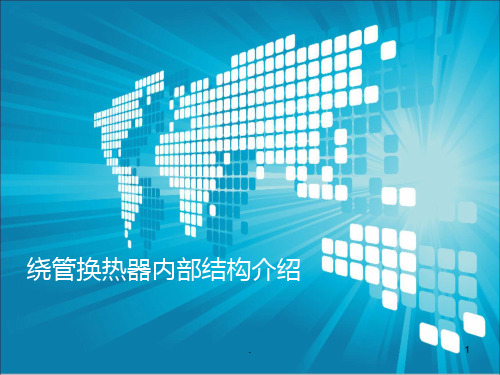
.
2
目录:
• 一、绕管换热器的基本介绍 • 二、绕管各部件加工步骤及注
意事项 • 三、操作与维护
.
3
一、绕管换热器的基本介绍:
• 1.绕管式换热器是在与管板相连的中心筒上, 以螺旋状交替缠绕数层小直径换热管形成 管束,再 将管束放入壳体内的一种换热器。
• 管束由多层螺旋缠绕的换热管组构成,每 层换热管以相反的方向缠绕,每层换热管 用垫条隔开,垫条厚度由工艺计算的流体 通道要求确定(九江项目采用2mm厚度)并 采用异型垫条控制换热管的螺旋升角。在 设计盘管时同一层使用相同长度的管子绕 制,在同一管程的流道上管子应均匀布置。
.
15
1.5介质通道进行标识,检查是否正确以防穿错管
.
16
1.6异型垫条用来确定管子的导程
.
17
1.7平垫条在中心筒上点焊
.
18
1.8中心筒上点焊异形垫条
.
19
1.9垫条点焊
.
20
1.10异形垫条用来固定管子在绕制过程中的导程, 犹如管子绕制过程的行驶轨道
.
21
1.11管箍,用来固定管子
.
5
• 优点:结构紧 凑、可同时进行多种介质换热、管 内操作压力高、传 热管的热膨胀可自行补偿、换 热器易实现大型化等 特点,因此,成为大型煤化工 装置低温甲醇洗系统的首选换热设备。
• 缺点:主要为检修、清理困难,所以一般用于较清 洁的工艺介质。
.
6
• 2.绕管式换热器按其结构特点分为两类:管 程单股流流道型(称为单股流绕管式换热器), 管程多股流流道型(称为多股流绕管式换热 器)。(如图2-1、2-2)
36
.
37
绕管换热器ppt课件

• 2.3缠绕管换热器都是竖直运行,下管板与管子间 易产生间隙腐蚀,这也是较常见的破坏形式之一.因 此,胀接要做到二点:一是要有合适的胀度,消除间 隙,防止腐蚀;二是防止过胀,导致管板塑性变形,降 低了胀接的可靠度.
• 2.4九江绕管胀接的胀度在管子穿穿管前进行了试 验,选择80MPa的胀度(75-90MPa之间)
11
二、绕管各部件加步骤及注意事项
• 1绕管各部件加步骤: • 1.1中心筒组对焊接 • 绕管束中心筒在制造 • 中起支承作用, • 因而要求有一定的强度和刚度, • 中心筒的外 • 径由换热管的最 • 小弯曲半径决定
12
1.2中心筒与管板焊接
13
1.3管板中心距检查≤3mm
14
1.4垫条点焊前对照图纸进行确认管板标识,检查管板介质 通道是否一致
27
1.16绕制中,使用管箍固定中,以防回 弹
28
1.17第一层绕制完,进行表面检查及100%气压试验
29
1.18气压试验压力8.5Mpa
30
1.18第二层绕制前,将垫条点焊在第一层的管箍上
31
第二层管子管箍固定,点焊时注意不要伤到管子
32
第二层的绕制方向与上一层方向相反,依次类推
33
1.19每层绕制完,需要对每一层的直径进行数据测量,对 照图纸,以防绕大。
2
目录:
• 一、绕管换热器的基本介绍 • 二、绕管各部件加工步骤及注
意事项 • 三、操作与维护
3
一、绕管换热器的基本介绍:
• 1.绕管式换热器是在与管板相连的中心筒上, 以螺旋状交替缠绕数层小直径换热管形成 管束,再 将管束放入壳体内的一种换热器。
• 管束由多层螺旋缠绕的换热管组构成,每 层换热管以相反的方向缠绕,每层换热管 用垫条隔开,垫条厚度由工艺计算的流体 通道要求确定(九江项目采用2mm厚度)并 采用异型垫条控制换热管的螺旋升角。在 设计盘管时同一层使用相同长度的管子绕 制,在同一管程的流道上管子应均匀布置。
缠绕管式换热器换热工艺研究

缠绕管式换热器换热工艺研究缠绕管式换热器是一种常用的换热设备,广泛应用于化工、石油、制药、食品等领域。
本文旨在探讨缠绕管式换热器的换热工艺研究,包括其基本原理、性能优势、应用案例以及进一步发展的方向。
缠绕管式换热器是一种利用外壳与内管之间的介质进行换热的设备。
其基本原理是通过外壳中的流体与内管中的流体进行热量交换。
内外介质各自在不同的管道中流动,通过传热表面的热传递,实现热能的转移。
由于能够充分利用介质之间的纵向流动路径,缠绕管式换热器相比于其他换热器,具有更高的换热效率和热量转移能力。
缠绕管式换热器具有多种性能优势。
首先,由于内外介质是分离的,可以用于介质之间有化学反应、腐蚀性或污染性的情况,从而提高了设备的稳定性和使用寿命。
其次,可根据需要灵活选择管道材质,以满足不同介质的特殊要求。
同时,缠绕管式换热器具有紧凑的结构设计,占地面积小,适用于有限的空间。
此外,该设备具有出色的自清洁功能,能够减少污垢和沉积物的积聚,减小清洗维护频率。
缠绕管式换热器在多个领域得到广泛应用。
在化工领域,可以用于石油炼制、合成氨、甲醇生产等过程中的换热。
在石油行业,可用于石油储运、精炼过程中的换热。
在制药、食品等领域,可以应用于发酵、干燥、蒸馏等工艺的热能转换。
此外,缠绕管式换热器还可用于海水淡化、空调制冷、锅炉余热回收等环保和节能领域。
未来,缠绕管式换热器有望在以下方面进一步发展。
首先,进一步优化换热器的结构设计,提高热传导效率,并减少设备的压降。
其次,探索新的材料和加工工艺,以提高设备的耐腐蚀性和使用寿命。
此外,加强对换热器性能的模拟与优化研究,利用计算流体力学等技术手段,提高热传导和热转移效率。
最后,结合智能化技术发展,实现设备的在线监测与控制,提高换热过程的可靠性和自动化水平。
综上所述,缠绕管式换热器是一种性能优越、广泛应用的换热设备。
随着技术的不断发展,缠绕管式换热器在能源、环保等领域的应用前景十分广阔。
我们期待通过进一步的研究和创新,推动缠绕管式换热器的发展,为工业生产和人类社会的可持续发展做出更大的贡献综上所述,缠绕管式换热器具备出色的自清洁功能,能减少污垢和沉积物的积聚,降低清洗维护频率。
绕管换热器PPT课件
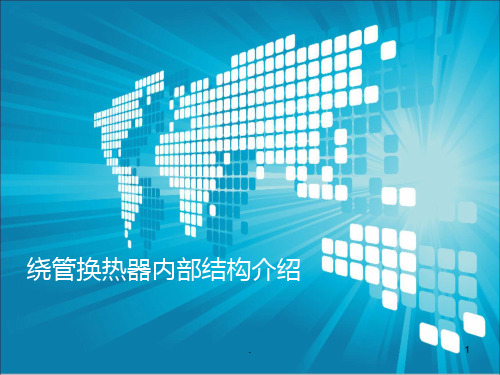
.
27
1.16绕制中,使用管箍固定中,以防回 弹
.
28
1.17第一层绕制完,进行表面检查及100%气压试验
.
29
1.18气压试验压力8.5Mpa
.
30
1.18第二层绕制前,将垫条点焊在第一层的管箍上
.
31
第二层管子管箍固定,点焊时注意不要伤到管子
.
32
第二层的绕制方向与上一层方向相反,依次类推
.
22
1.12管子绕制好一根,管箍进行固定,以防止管子回弹
.
23
1.13管箍固定管子,此处点焊时注意检查是否伤到 管子
.
24
1.14绕制时敲击使用皮锤进行敲击,以防伤到管子
.
25
1.15绕制中
.
26
• 其中,换热管的盘绕角一般为5~20度,例如 E1607盘绕角14-15度。绕管式换热器的特点是结 构紧凑,单位换热面积大,热损小,承压能力高。 一般高压流体在管内流动。换热管大部分呈盘绕 状,盘绕角较小,故管内、管外的清扫很困难, 所以管内、管外不适于走不洁的流体。
绕管换热器内部结构介绍
.
1
绕管换热器的发展史
• 我国20世纪70年代末引进的大化肥装置中采用德 国林德公司低温甲醇洗工艺单元中各有6台绕管换 热器;90年代初引进的德国鲁奇公司低温甲醇洗 工艺单元中各有2台绕管换热器;由于我国尚未掌 握绕管换热器的设计和制造技术,这些引进的装 置中绕管换热器完全依赖国外进口,设备的费用 昂贵。并且随着我国合成氨工业的发展,对低温 甲醇洗装置的需求量增加,对现有装置进行技术 改造实现增产的要求也与日剧增,在此形势下通 过国内科研、设计和制造单位的努力,该类设备 已实现国产化。
绕管换热器技术要求

绕管换热器技术要求首先,绕管换热器应具备良好的换热性能。
这主要包括换热系数和传热面积两个方面。
换热系数是指换热器单位面积内的传热量与温度差的比值,一般来说,换热系数越高,换热效果越好。
传热面积应尽可能大,以增加传热的表面积,从而提高传热效率。
同时,还应尽量减小热损失,避免能量的浪费。
其次,绕管换热器的材料选择也非常重要。
由于绕管换热器广泛应用于各种场合,所以需要根据实际情况来选择不同的材料。
一般来说,不同的介质会对材料产生不同的腐蚀和腐蚀,而不同的工艺条件则对材料的耐压性能提出了要求。
因此,在选择材料时需要综合考虑工艺温度、压力和介质特性等因素,确保材料能够在长时间内保持良好的工作状态。
再次,绕管换热器的结构设计也需要满足一定的要求。
首先,换热器的内外管布置要合理,以确保流体在管道内充分接触和换热。
同时,流体的流动状态也需要考虑,例如流速和流量等因素对换热效果有一定的影响。
另外,管束的尺寸和布置也需要根据实际需求进行设计,以确保换热器的紧凑性和高效性。
此外,绕管换热器还需要考虑清洗和维护的便利性。
由于绕管换热器在使用过程中会产生一定的污垢和结垢,需要定期清洗和维护,以保持其正常工作状态。
因此,在设计时应充分考虑到清洗和维修的便利性,例如加入清洗孔或维修孔等设置,以方便清洗和维护人员的操作。
最后,为了确保绕管换热器的安全性能,还需要考虑相关的安全措施。
例如,在设计时要充分考虑材料的强度和耐压性能,以确保在高压和高温工况下的安全运行。
此外,还需要设置相应的安全阀、温度传感器等装置,及时监测和控制换热器的运行状态,确保不会出现危险事故。
综上所述,绕管换热器技术要求包括换热性能、材料选择、结构设计、清洗维护便利性以及安全性能等多个方面。
通过满足这些技术要求,可以提高绕管换热器的工作效率和安全性,从而满足各行业在换热过程中的需求。
缠绕管式换热器的管理及其应用
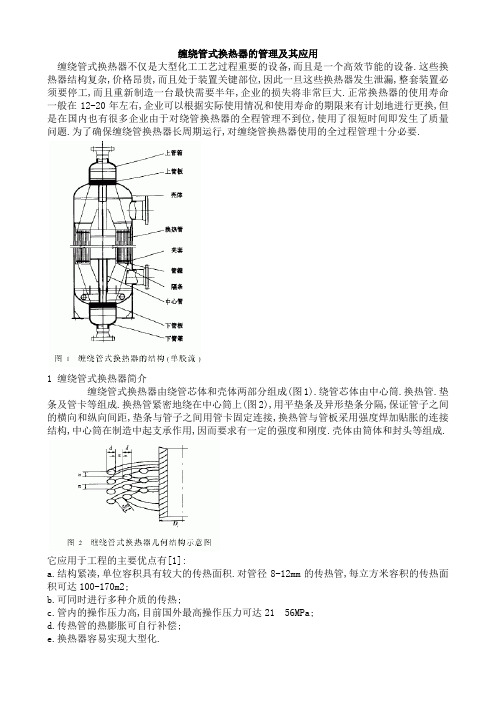
缠绕管式换热器的管理及其应用缠绕管式换热器不仅是大型化工工艺过程重要的设备,而且是一个高效节能的设备.这些换热器结构复杂,价格昂贵,而且处于装置关键部位,因此一旦这些换热器发生泄漏,整套装置必须要停工,而且重新制造一台最快需要半年,企业的损失将非常巨大.正常换热器的使用寿命一般在12-20年左右,企业可以根据实际使用情况和使用寿命的期限来有计划地进行更换,但是在国内也有很多企业由于对绕管换热器的全程管理不到位,使用了很短时间即发生了质量问题.为了确保缠绕管换热器长周期运行,对缠绕管换热器使用的全过程管理十分必要.1 缠绕管式换热器简介缠绕管式换热器由绕管芯体和壳体两部分组成(图1).绕管芯体由中心筒.换热管.垫条及管卡等组成.换热管紧密地绕在中心筒上(图2),用平垫条及异形垫条分隔,保证管子之间的横向和纵向间距,垫条与管子之间用管卡固定连接,换热管与管板采用强度焊加贴胀的连接结构,中心筒在制造中起支承作用,因而要求有一定的强度和刚度.壳体由筒体和封头等组成.它应用于工程的主要优点有[1]:a.结构紧凑,单位容积具有较大的传热面积.对管径8-12mm的传热管,每立方米容积的传热面积可达100-170m2;b.可同时进行多种介质的传热;c.管内的操作压力高,目前国外最高操作压力可达21 56MPa;d.传热管的热膨胀可自行补偿;e.换热器容易实现大型化.2 缠绕管式换热器的工业应用情况在国外,缠绕管式换热器广泛应用于大型空气分离装置的过冷器及液化器(液体氧.液体氨装置),林德公司在合成氨甲醇洗系统中推出的缠绕管换热器系列正是充分发挥了该种换热器的作用.缠绕管式换热器在我国目前主要应用于大化肥合成氨装置(美国德士古工艺)中甲醇洗工段[2],在全国共有近20套此类装置,每套装置中有6台缠绕管式换热器,这些换热器的具体情况见表1.在我国最早十多套装置中的缠绕管换热器大都已更换,其中大都是已到使用寿命限期,但也有不少为管理不善而造成的损坏.表2是一些用户的设备主要损坏原因,表3说明设备损坏原因的百分比.3 缠绕管换热器的使用管理缠绕管换热器的使用管理过程主要有4个方面:制造过程控制,除垢清洗技术的选用,装置运行的有效管理,产品缺陷修复方案的正确运用.3.1 制造过程的控制由于缠绕管换热器的特殊性,使用厂家必须从开始制造进行全过程控制,根据不同的使用场合提出不同的控制要求.主要控制内容:a.管子的选用.目前使用管子为有缝钢管和无缝钢管,有缝钢管可靠性较差,适用于低压;而无缝钢管整体性能较好,但有薄弱区域,必须对接头进行固溶处理.腐蚀性强的介质宜采用无缝钢管;反之,宜采用有缝钢管.盘管直径大宜采用有缝管,直径小宜采用无缝管.b.盘管的控制.盘管控制的好坏直接影响到换热器的换热效率,尤其是对结垢情况影响较大.因此,盘管时必须使层间距适度,没有窄间隙死角,防止局部区域布置不均匀,造成流体阻塞,降低流体的流通面积.c.焊接的控制.缠绕管的损坏形式最常见的是管口泄漏,这是设备的关键部位.一般缠绕管换热器为了提高换热效率,采用管子都比较小和薄,焊接容易产生缺陷.因此,焊接必须严格控制线能量,最好要采用自动焊,焊缝要均匀和饱满.d.缠绕管换热器都是竖直运行,下管板与管子间易产生间隙腐蚀,这也是较常见的破坏形式之一.因此,胀接要做到二点:一是要有合适的胀度,消除间隙,防止腐蚀;二是防止过胀,导致管板塑性变形,降低了胀接的可靠度.缠绕管换热器制造的控制除了上述几个方面外,还有材料的控制.设计的控制等,使换热器产品符合不同企业的生产特点.3.2 除垢技术的选用目前国内企业绕管换热器的损坏大多由于酸洗除垢技术不成熟造成的,其中主要是酸洗方法不当.目前常用的酸洗液主要使用3种,即5%的HCl液.硝酸或氢氟酸以及柠檬酸.其中HCl的酸洗主要用于碳钢,后二者主要用于不锈钢酸洗.硝酸或氢氟酸酸性较强,它利用的是使垢剥落的原理进行除垢,且容易产生腐蚀;而柠檬酸是通过络合作用来除垢,酸性较弱.笔者以甲醇换热器为例分析损坏原因.镇海炼化公司的E9.E10酸洗时,管束材料是碳钢,使用HCl酸液,酸洗后换热器下部的酸液没有及时排尽,使一些残液停留在下管板死区,在大修停工期间产生酸性腐蚀,使管子损坏;上海某化工厂一台36t绕管换热器,使用氢氟酸溶液进行酸洗,由于氢氟酸对焊缝的腐蚀性相当强,酸液渗入到管板接头间隙,导致管头焊缝裂开;宁夏化工厂15E6用HNO3液除垢,HNO3除垢后将产生大量Fe3+,酸洗时间稍长,使Fe3+含量远大于6×10-4的标准值,Fe3+依附于管子产生腐蚀,再加上HNO3酸洗时间长,没有及时排尽,酸液本身就产生较强腐蚀,导致管束损坏.目前,比较成熟的酸洗方法应是采用酸性比较弱的柠檬酸,采用多次少停留的办法,对一台换热器进行多达5-6次酸洗,每次时间短,冲洗干净,使得Fe3+不超标并且及时带走,保证换热器不受腐蚀.除垢清洗技术的正确使用对换热器寿命非常重要,应用管理中必须引起高度重视,采用合理的工艺方案进行酸洗.3.3 装置操作的管理缠绕管由于原料杂质问题引起质量问题的也不少,按照设计要求,缠绕管式换热器用于介质杂质少.容易清洗的场合,因为缠绕管换热器为了追求其紧凑性,管间距与层间距的间距比较小,所以对原料的要求也较高.一旦装置波动等就可能引发原料杂质多而容易造成堵塞.因此,要有效地在操作上做好以下几方面:a.原料的选择.原料的杂质含量必须严格控制,杂质含量增加会使部分杂质粘附于层间的支撑件上,这样随着时间延长,容易造成通道堵塞,致使换热面积大幅降低.b.系统结构设计合理.为防止粗大杂质进入换热器,要在系统的上游增设过滤网,过滤网的目数要视杂质大小而定,原料通过过滤后才能进入换热器,这样防止了原料在管壳程内部造成堵塞.c.增加反冲洗装置.在换热器运行过程中,杂质容易向下沉积,一方面堵塞流道,另一方面产生垢下腐蚀,因此在换热器的下部增设反冲洗,通过气泡的形式,搅扰内部的沉积杂质,使杂质一起随介质流走.另外,在装置操作中要特别注重开停车的温度和压力的升降,要严格控制升温的速度和压力的匹配,否则容易造成热胀冷缩不均匀等破坏管头连接.3.4 设备修复方案的正确选用缠绕管换热器一般运行周期较长,但经常出现问题,主要问题有堵塞.管子泄漏和管口泄漏等,正确选择合适的修复方案对装置十分重要.换热器出现堵塞后,疏通的方法有两种:一种是用高压水枪冲洗,主要针对堵塞不是很严重的情况;第二种就是用酸清洗办法,主要用于严重堵塞.如换热器经查出现了管子泄漏,那只有在试压查漏明确的情况下进行堵管.换热器出现了管子泄漏问题,要分两种情况进行修复:管口数量少,则采用堵管办法;管口数量较多,堵管后会严重影响换热效果,则宜选用抽芯补焊的办法修复绕管,缠绕管式换热器的抽芯修复虽然复杂,但修复成功的事例较多.4 缠绕管换热器的应用前景分析缠绕管换热器目前较多地应用于化工领域的深冷装置,如空分和甲醇装置,随着国内对缠绕管换热器研究的深入,国内多家单位不断攻关,扩大缠绕管换热器的应用领域已取得初步的成绩,主要有以下几方面趋势.4.1 缠绕管换热器的大型化由于缠绕管换热器特殊结构设计,它封头小,管子可以长达数百米,目前已开发制造了一些大型的缠绕管换热器.图3(略)为一台德州石化所使用的大型绕管换热器,该换热器尺寸为?1600mm×20000mm,重达60t,换热面积为2000m2,是普通类似壳体换热器的2倍左右.随着装置的大型化,这种缠绕管换热器也要求不断大型化.而普通列管式换热器由于管子限制无法把换热器做大.4.2 缠绕管换热器的高温化缠绕管换热器具有高效的换热性能,但目前基本上应用于深冷装置.从2001年开始合肥通用所等企业开始研究应用于高温场合的缠绕管换热器(图4)(略),并于2002年在镇海炼化投用,这种换热器采用CrMo钢耐高温材料,操作参数见表4.经过几年运行,该换热器的性能完全达到使用要求,质量也较可靠.这种产品的成功应用,使得缠绕管换热器的应用领域大大拓宽,可以从低温应用转向高温应用,只要介质允许,在炼油行业也可以充分发挥绕管换热器的优点[3].4.3 缠绕管换热器的高压化缠绕管换热器目前多应用于壳程压力高,管程压力低的场合,一般壳程压力达到15.0MPa,而管程压力普遍小于 5.0MPa.由于缠绕管换热器设计结构特点是管板小,壳程大,两端入口封头小,该结构能克服普通高压换热器的弊病.普通高压换热器均采用浮头式或U形管式,当压力提高,不仅壳体厚度加大,而且法兰的强度等级要大幅提高,一般的高压换热器如压力大于10MPa,当做到1.4m时,换热器将是非常庞大,法兰也非常厚.而且随着装置的大型化,高压换热器也需要不断扩大,这就给制造带来麻烦,如加氢裂化的锁紧环式高压换热器,管程压力14.5MPa,壳程压力为18.5MPa,直径为1.4m,其中换热器的管箱重量就已达45t,制造非常困难,若改做浮头式换热器则很难保证换热器的密封等要求.因此,随着加氢装置的大型化,锁紧环换热器也要大型化,要向1.6m或1.8m发展,不但制造难度大,而且由于结构庞大,检维修将十分困难.而缠绕式换热器却可通过加长长度来增大面积,而两端的小管板使得连接法兰小,容易制造.目前国内一些单位正在进行研究,以缠绕管式换热器逐步替代炼油行业一些高压换热器,如加氢裂化和重整等装置.4.4 缠绕管换热器的多股化随着应用的成熟,缠绕管换热器逐步实现多股流换热,这是其他换热器无法比拟的特殊性能.一台换热器一种壳程介质可同时跟两种或3种介质同时换热,这样可以大大提高装置的换热效率和换热空间.目前,国内的多股流换热器研究制造逐步开始,已有部分产品投入应用,图5(略)为巴陵石化的多股流换热器[4].4.5 缠绕管换热器的微型化缠绕管式换热器由于其高效的换热性能,它在向大型化发展的同时,也正逐步向微型化发展.在一些空间受到限制的地方,常规换热器达不到热交换的要求,而采用缠绕管换热器能在同样空间可满足要求.正是由于这种良好性能,缠绕管换热器已在微型领域使用.图6是某军工产品使用的缠绕管换热器,由于该军工产品空间有限,经过反复比较,最终选择了这种产品,在有限的空间实现换热.5 结束语缠绕管式换热器是一种新型高效换热器,如何正确地进行设备的全过程管理对装置运行相当重要.并且随着应用的不断成熟,其应用领域日益扩大,将发挥越来越大的作用.。
绕管式换热器的结构形式分析及应用前景
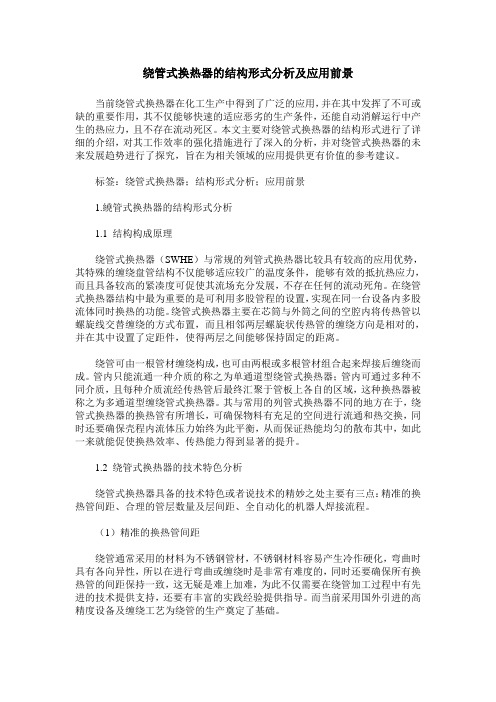
绕管式换热器的结构形式分析及应用前景当前绕管式换热器在化工生产中得到了广泛的应用,并在其中发挥了不可或缺的重要作用,其不仅能够快速的适应恶劣的生产条件,还能自动消解运行中产生的热应力,且不存在流动死区。
本文主要对绕管式换热器的结构形式进行了详细的介绍,对其工作效率的强化措施进行了深入的分析,并对绕管式换热器的未来发展趋势进行了探究,旨在为相关领域的应用提供更有价值的参考建议。
标签:绕管式换热器;结构形式分析;应用前景1.繞管式换热器的结构形式分析1.1 结构构成原理绕管式换热器(SWHE)与常规的列管式换热器比较具有较高的应用优势,其特殊的缠绕盘管结构不仅能够适应较广的温度条件,能够有效的抵抗热应力,而且具备较高的紧凑度可促使其流场充分发展,不存在任何的流动死角。
在绕管式换热器结构中最为重要的是可利用多股管程的设置,实现在同一台设备内多股流体同时换热的功能。
绕管式换热器主要在芯筒与外筒之间的空腔内将传热管以螺旋线交替缠绕的方式布置,而且相邻两层螺旋状传热管的缠绕方向是相对的,并在其中设置了定距件,使得两层之间能够保持固定的距离。
绕管可由一根管材缠绕构成,也可由两根或多根管材组合起来焊接后缠绕而成。
管内只能流通一种介质的称之为单通道型绕管式换热器;管内可通过多种不同介质,且每种介质流经传热管后最终汇聚于管板上各自的区域,这种换热器被称之为多通道型缠绕管式换热器。
其与常用的列管式换热器不同的地方在于,绕管式换热器的换热管有所增长,可确保物料有充足的空间进行流通和热交换,同时还要确保壳程内流体压力始终为此平衡,从而保证热能均匀的散布其中,如此一来就能促使换热效率、传热能力得到显著的提升。
1.2 绕管式换热器的技术特色分析绕管式换热器具备的技术特色或者说技术的精妙之处主要有三点:精准的换热管间距、合理的管层数量及层间距、全自动化的机器人焊接流程。
(1)精准的换热管间距绕管通常采用的材料为不锈钢管材,不锈钢材料容易产生冷作硬化,弯曲时具有各向异性,所以在进行弯曲或缠绕时是非常有难度的,同时还要确保所有换热管的间距保持一致,这无疑是难上加难,为此不仅需要在绕管加工过程中有先进的技术提供支持,还要有丰富的实践经验提供指导。
绕管式换热器结构
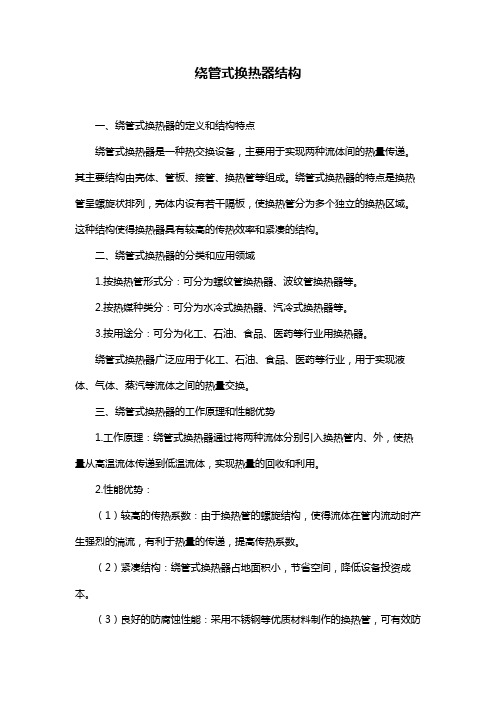
绕管式换热器结构一、绕管式换热器的定义和结构特点绕管式换热器是一种热交换设备,主要用于实现两种流体间的热量传递。
其主要结构由壳体、管板、接管、换热管等组成。
绕管式换热器的特点是换热管呈螺旋状排列,壳体内设有若干隔板,使换热管分为多个独立的换热区域。
这种结构使得换热器具有较高的传热效率和紧凑的结构。
二、绕管式换热器的分类和应用领域1.按换热管形式分:可分为螺纹管换热器、波纹管换热器等。
2.按热媒种类分:可分为水冷式换热器、汽冷式换热器等。
3.按用途分:可分为化工、石油、食品、医药等行业用换热器。
绕管式换热器广泛应用于化工、石油、食品、医药等行业,用于实现液体、气体、蒸汽等流体之间的热量交换。
三、绕管式换热器的工作原理和性能优势1.工作原理:绕管式换热器通过将两种流体分别引入换热管内、外,使热量从高温流体传递到低温流体,实现热量的回收和利用。
2.性能优势:(1)较高的传热系数:由于换热管的螺旋结构,使得流体在管内流动时产生强烈的湍流,有利于热量的传递,提高传热系数。
(2)紧凑结构:绕管式换热器占地面积小,节省空间,降低设备投资成本。
(3)良好的防腐蚀性能:采用不锈钢等优质材料制作的换热管,可有效防止腐蚀,延长设备使用寿命。
(4)易于清洗和维修:换热管间距较大,便于清洗和检修,保证设备运行的稳定性。
四、绕管式换热器的选型和安装维护要点1.选型:根据实际工艺要求,选择合适的换热器类型、换热面积、换热管材料等。
2.安装:安装时应确保换热器壳体、管板、接管等部件连接牢固,遵循相关安装规范。
3.维护:定期检查换热器运行状态,清洗换热管,更换损坏部件,确保设备安全、稳定运行。
总之,绕管式换热器凭借其优异的性能和广泛的应用领域,成为现代工业生产中不可或缺的热交换设备。
缠绕管换热器结构

缠绕管换热器结构缠绕管换热器是一种常见的换热设备,广泛应用于化工、制药、冶金等行业中。
它通过将冷热介质分别流经内外两根缠绕在一起的管道,实现了热量的传递。
本文将从结构、工作原理、优点和应用领域等方面介绍缠绕管换热器。
一、结构缠绕管换热器的主要结构由内管、外管和夹套组成。
内外管分别用冷热介质流经,而夹套则用来传递蒸汽或冷却水等介质,以调节内外管的温度。
内外管之间通过一系列的支撑件固定,确保管道的稳定性。
此外,缠绕管换热器还配备了进出口管道和排污口,方便介质的进出和系统的维护。
二、工作原理缠绕管换热器的工作原理基于热传导的基本规律。
当冷热介质分别流经内外管时,由于温度差异,热量会从温度高的一侧传递到温度低的一侧。
具体而言,热量会从热介质通过内管传递给外管,然后再通过外管传递给冷介质。
这样,热量在内外管之间传递,实现了换热的效果。
三、优点缠绕管换热器相比其他换热设备具有以下优点:1. 效率高:由于缠绕管换热器的内外管紧密缠绕在一起,热量传递的距离短,换热效率高。
这使得它在相同工况下能够实现更高的热量传递效果。
2. 适应性强:缠绕管换热器可以适应不同的工况和介质,包括高温、高压、腐蚀性介质等。
它的结构可以根据实际需求进行调整,以适应不同的工艺要求。
3. 结构简单:相比其他换热设备,缠绕管换热器的结构较为简单,易于制造和维护。
这使得它在实际应用中更加方便灵活。
四、应用领域缠绕管换热器广泛应用于多个行业,包括化工、制药、冶金、食品等。
具体应用领域包括:1. 化工:在化工生产中,缠绕管换热器常用于各种反应器、蒸馏塔等设备中,用于控制和调节介质的温度。
2. 制药:制药过程中需要控制反应的温度和冷却产物,缠绕管换热器可以提供高效的换热效果,满足制药工艺的要求。
3. 冶金:在冶金过程中,缠绕管换热器常用于冷却高温的金属熔融液体,保证冶炼过程的稳定性和安全性。
4. 食品:在食品加工过程中,缠绕管换热器用于调节食品的温度,提高加工效率和产品质量。
绕管式换热器结构
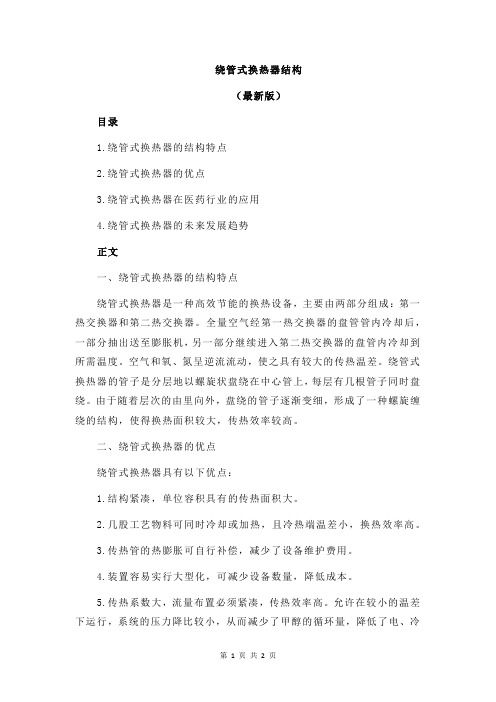
绕管式换热器结构(最新版)目录1.绕管式换热器的结构特点2.绕管式换热器的优点3.绕管式换热器在医药行业的应用4.绕管式换热器的未来发展趋势正文一、绕管式换热器的结构特点绕管式换热器是一种高效节能的换热设备,主要由两部分组成:第一热交换器和第二热交换器。
全量空气经第一热交换器的盘管管内冷却后,一部分抽出送至膨胀机,另一部分继续进入第二热交换器的盘管内冷却到所需温度。
空气和氧、氮呈逆流流动,使之具有较大的传热温差。
绕管式换热器的管子是分层地以螺旋状盘绕在中心管上,每层有几根管子同时盘绕。
由于随着层次的由里向外,盘绕的管子逐渐变细,形成了一种螺旋缠绕的结构,使得换热面积较大,传热效率较高。
二、绕管式换热器的优点绕管式换热器具有以下优点:1.结构紧凑,单位容积具有的传热面积大。
2.几股工艺物料可同时冷却或加热,且冷热端温差小,换热效率高。
3.传热管的热膨胀可自行补偿,减少了设备维护费用。
4.装置容易实行大型化,可减少设备数量,降低成本。
5.传热系数大,流量布置必须紧凑,传热效率高。
允许在较小的温差下运行,系统的压力降比较小,从而减少了甲醇的循环量,降低了电、冷量和蒸汽的消耗。
三、绕管式换热器在医药行业的应用绕管式换热器在医药行业中的应用十分广泛,可用于原料药、中间体的冷却或加热等工艺过程。
由于医药行业对产品质量和生产环境的要求较高,绕管式换热器具有良好的密封性能和易清洗的特点,符合医药行业的严格标准。
四、绕管式换热器的未来发展趋势随着节能减排的需求和工艺技术的不断提高,绕管式换热器在未来的发展趋势将更加明显。
缠绕管式换热器技术特色及介绍

缠绕管式换热器技术特色及介绍缠绕管式换热器(Spiral Wounded Heat Exchanger)相对于普通的列管式换热器具有不可比拟的优势,适用温度范围广、适应热冲击、热应力自身消除、紧凑度高,由于自身的特殊构造,使得流场充分发展,不存在流动死区,尤其特别的,通过设置多股管程(壳程单股),能够在一台设备内满足多股流体的同时换热。
缠绕管式换热器是一款高效紧凑的换热器,不但可以利用余热,在节能环保方面也具有很重要的作用。
换热器的结构形式复杂,造价成本高,并且位于装置的关键部位。
缠绕管式换热器相对于普通的列管式换热器具有不可比拟的优势,其适用的温度范围广,适应热冲击,能够自身消除热应力,紧凑度非常高,由于自身具有特殊的构造,使得其流场充分发展,不存在流动死区,其中更特别的是,通过设置多股管程(壳程单股),能够在一台设备内满足多股流体的同时换热。
绕管式换热器是在芯筒与外筒之间的空间内将传热管按螺旋线形式交替缠绕而成的,相邻两层螺旋状传热管的螺旋方向是相反的,并采用具有特殊形状的定距件,使之能够保持一定的间距。
技术特色缠绕管式换热器的三大技术特色或者说是技术精髓为:精准的换热管间距、合理的管层数量以及层间距、全自动化的机器人焊接流程。
1、精准的换热管间距不绣钢管材因为其材质的而导致了在弯曲或者缠绕的时候很难具有塑性,为实现所有换热管的间距都是统一的这要求带来了很大的困难,这就要求我们在加工时需要完备的技术和丰富的经验,而正是原装的高精度设备和顶尖的缠绕工艺为我们机械的生产提供了基础。
2、合理的管层数量以及层间距在换热管束缠绕时,每层相对的管径都在发生着变化,盘绕角度又要保持一致,要保证每根换热管的长度基本相同确实是很难做到的。
而设计师设计出了每层换热管不同数量,以及合理的层间距就很好地攻克了这—难题,同时也解决了复杂换热条件下的流道要求。
3、全自动化的机器人焊接流程在设备生产的过程当中,采用全自动化的机器人焊接,以保证所有焊点尤其是在管板焊接都实现了标准统一,安全性能高。
绕管式换热器在连续重整装置的应用

三、绕管换热器在连续重整装置的应用
设备操作与维护: 在操作中一旦发现管、壳程介质混流或出口温度异常等迹象,应停工检修,并对
设备做彻底检查。检查前应及时通知供应商,在技术人员的参与指导下,制订合理的 维修方案方可进行检漏和补焊。
设备长期操作后,若发现热介质出口温度升高或管、壳程阻力降明显增加,应清 除积垢,请根据结垢介质选用合适的化学溶剂清洗管、壳程的结垢。清洗后必须立即 排净清洗液。
性
抗冲击能力
一般,板通道间易沉积。 严格控制升降温速率
抗热冲击、工况波动能力弱,对温差、压 差、升降温速率等波动都可能导致损伤。
强,具有自清洗能力。 并无特别限制升降温速度。
强
三、绕管换热器在连续重整装置的应用
第一台用在PX装置和连续重整装置的绕管换热器,2009年12月由洛阳石化工 程有限公司和镇海石化建安工程公司、合肥通用机械研究院、华锦集团共同研究, 在华锦集团公司50万吨/年连续重整装置投用。
综合以上,更换绕管换热器后满足生产需求,同时热端温差达到了预期的效果; 由于装置运行时间较短,标定时间较短,后期车间将持续对更换后的绕管换热器运 行工况及效果监控。
三、绕管换热器在连续重整装置的应用
三、绕管换热器在连续重整装置的应用
三、绕管换热器在连续重整装置的应用 流动方式: 1.管程冷介质从下部循环氢入口+进油口流入,从上部 冷侧出口流出; 2.壳程热介质从上侧 热流入口流入,从下侧 热侧出口流出。
三、绕管换热器在连续重整装置的应用
5月份,重整装置更换绕管换热器后,随着重整装置调整加工量经标定装置加工 负荷,装置满负荷情况下绕管换热器热端温差 20℃左右(设计热端温差: 31℃), 产氢量随之达到使用需求;前期加工负荷仅仅能提到 70%,但板式换热器热端温 差高达 54℃(设计热端温差: 55℃)。
缠绕管式换热器

管路复杂度
大型LNG绕管式换热器: 常温的天然气从换热器的底部进入管程,从
过冷的LNG从顶部流出,壳侧内的流体为制冷剂,且从顶 部进入。
4大型LNG绕管式换热器
应用场合:大型陆上天然气液化厂和大型LNG-FPSO ( 浮式 生产储存卸货装置)中的主低温换热器。
液化能力:液化能力已经由最初的100万吨LNG/年增到780 万吨LNG/年。
谢谢!
国外研究现状:年产大于780万吨的单体绕管式换热器和对 FPSO进行结构改进,以适应海上情况
国内研究现状:开封空分正在研发200-300万吨/年LNG的大 型绕管式
4大型LNG绕管式换热器
绕管式换热器的关键技术
材料
结构
传热计算
换热管
(高负荷) (耐低温)
管板 (适应性)
国内 空白
重量 铜或奥氏体不锈钢
结构
连接技术
换热管和管板连接: 强度胀接+密封或焊贴胀+强度焊; 连接性能检验:拉脱、连接和低温
换热管与中心筒的连接:铝垫条无法直接固定在中心筒上, 第一层管仅作为垫条固定使用
热负荷均匀 预冷段、液化段和过冷段热负荷合理分配,互相协调
应力载荷均匀
中心筒缠绕技术:芯体总层数是49层,为了解决芯体受力 不均匀问题,在缠绕到第35层时增加第二个中心筒。通过 翼板把两个中心与壳体连接在一起
在传热模型建立上,考虑弯曲率和扭转率对管内流 动的影响。
结果表明,与弯曲率相比,扭转率对管内的流动影 响极小。弯曲率使流动截面出现两个旋转方向不同 的漩涡,而扭转率只是使一个漩涡的中心角度发生 扭转,失去对称性。
管内流动几何模型
2绕管式换热器
壳侧传热与流动研究
- 1、下载文档前请自行甄别文档内容的完整性,平台不提供额外的编辑、内容补充、找答案等附加服务。
- 2、"仅部分预览"的文档,不可在线预览部分如存在完整性等问题,可反馈申请退款(可完整预览的文档不适用该条件!)。
- 3、如文档侵犯您的权益,请联系客服反馈,我们会尽快为您处理(人工客服工作时间:9:00-18:30)。
技术研究
2
目录:
• 一、绕管换热器的基本介绍 • 二、绕管各部件加工步骤及注
意事项 • 三、操作与维护
技术研究
3
一、绕管换热器的基本介绍:
• 1.绕管式换热器是在与管板相连的中心筒上, 以螺旋状交替缠绕数层小直径换热管形成 管束,再 将管束放入壳体内的一种换热器。
• 管束由多层螺旋缠绕的换热管组构成,每 层换热管以相反的方向缠绕,每层换热管 用垫条隔开,垫条厚度由工艺计算的流体 通道要求确定(九江项目采用2mm厚度)并 采用异型垫条控制换热管的螺旋升角。在 设计盘管时同一层使用相同长度的管子绕 制,在同一管程的流道上管子应均匀布置。
技术研究
12
1.2中心筒与管板焊接
技术研究
13
1.3管板中心距检查≤3mm
技术研究
14
1.4垫条点焊前对照图纸进行确认管板标识,检查管板介质 通道是否一致
技术研究
15
1.5介质通道进行标识,检查是否正确以防穿错管
技术研究
16
1.6异型垫条用来确定管子的导程
技术研究
17
1.7平垫条在中心筒上点焊
技术研究
18
1.8中心筒上点焊异形垫条
技术研究
19
1.9垫条点焊
技术研究
20
1.10异形垫条用来固定管子在绕制过程中的导程, 犹如管子绕制过程的行驶轨道
技术研究
21
1.11管箍,用来固定管子
技术研究
22
1.12管子绕制好一根,管箍进行固定,以防止管子回弹
技术研究
23
1.13管箍固定管子,此处点焊时注意检查是否伤到 管子
技术研究
5
• 优点:结构紧 凑、可同时进行多种介质换热、管 内操作压力高、传 热管的热膨胀可自行补偿、换 热器易实现大型化等 特点,因此,成为大型煤化工 装置低温甲醇洗系统的首选换热设备。
• 缺点:主要为检修、清理困难,所以一般用于较清 洁的工艺介质。
技术研究
6
• 2.绕管式换热器按其结构特点分为两类:管 程单股流流道型(称为单股流绕管式换热器), 管程多股流流道型(称为多股流绕管式换热 器)。(如图2-1、2-2)
技术研究
7
(图2-1)单股流绕管式换热器
序号 名称
序号 名称
1
下管箱
5
壳体
2
下管板
6
外套筒
3
中心筒
7
上管板
4
管束
8
上管箱
技术研究
8
单股流绕管换热器实物图(E1610热再生塔进料加热器)
技术研究
9
(图2-2)多股流绕管式换热器
序号 名称
序号 名称
1
下管箱
5
壳体
2
下管板
6
外套筒
3
中心筒
7
上管板
4
管束
绕管换热器内部结构介绍
技术研究
1
绕管换热器的发展史
• 我国20世纪70年代末引进的大化肥装置中采用德 国林德公司低温甲醇洗工艺单元中各有6台绕管换 热器;90年代初引进的德国鲁奇公司低温甲醇洗 工艺单元中各有2台绕管换热器;由于我国尚未掌 握绕管换热器的设计和制造技术,这些引进的装 置中绕管换热器完全依赖国外进口,设备的费用 昂贵。并且随着我国合成氨工业的发展,对低温 甲醇洗装置的需求量增加,对现有装置进行技术 改造实现增产的要求也与日剧增,在此形势下通 过国内科研、设计和制造单位的努力,该类设备 已实现国产化。
技术研究
4
• 缠绕管式换热器由绕管芯体和壳体两部分组成。 绕管芯体由中心筒.换热管.垫条及管卡等组成.换 热管紧密地绕在中心筒上,用平垫条及异形垫条 分隔,保证管子之间的横向和纵向间距,垫条与管子 之间用管卡固定连接,换热管与管板采用强度焊加 贴胀的连接结构,中心筒在制造中起支承作用,因而 要求有一定的强度和刚度.壳体由筒体和封头等组 成。
技术研究
33
1.19每层绕制完,需要对每一层的直径进行数据测量,对 照图纸,以防绕大。
技术研究
34
• 1.20绕制完成以后,对绕管体外部使用厚度 为2mm的不锈钢皮进行包裹,以防伤到管 子,等待与筒体进行套装,由此夹套还起 到导流作用,夹套与设备壳体间应保持一 定距离。如下图片:(E1610为例)
技术研究
40
胀接试验胀度80MPa
技术研究
41
胀接后PT检查
•
技术研究
42
• 2.5换热管做水下气密性试验, • 注意试验用水,水中氯离子含量≤25mg/L
技术研究
39
• 2.3缠绕管换热器都是竖直运行,下管板与管子间 易产生间隙腐蚀,这也是较常见的破坏形式之一.因 此,胀接要做到二点:一是要有合适的胀度,消除间 隙,防止腐蚀;二是防止过胀,导致管板塑性变形,降 低了胀接的可靠度.
• 2.4九江绕管胀接的胀度在管子穿穿管前进行了试 验,选择80MPa的胀度(75-90MPa之间)
技术研究
24
1.14绕制时敲击中
技术研究
26
• 其中,换热管的盘绕角一般为5~20度,例如 E1607盘绕角14-15度。绕管式换热器的特点是结 构紧凑,单位换热面积大,热损小,承压能力高。 一般高压流体在管内流动。换热管大部分呈盘绕 状,盘绕角较小,故管内、管外的清扫很困难, 所以管内、管外不适于走不洁的流体。
8
上管箱
技术研究
10
多股流绕管式换热器实物图(E1606洗涤塔段间冷 却器)
技术研究
11
二、绕管各部件加步骤及注意事项
• 1绕管各部件加步骤: • 1.1中心筒组对焊接 • 绕管束中心筒在制造 • 中起支承作用, • 因而要求有一定的强度和刚度, • 中心筒的外 • 径由换热管的最 • 小弯曲半径决定
技术研究
27
1.16绕制中,使用管箍固定中,以防回 弹
技术研究
28
1.17第一层绕制完,进行表面检查及100%气压试验
技术研究
29
1.18气压试验压力8.5Mpa
技术研究
30
1.18第二层绕制前,将垫条点焊在第一层的管箍上
技术研究
31
第二层管子管箍固定,点焊时注意不要伤到管子
技术研究
32
第二层的绕制方向与上一层方向相反,依次类推
技术研究
35
技术研究
36
技术研究
37
技术研究
38
2制造过程的控制
2.1盘管的控制.盘管控制的好坏直接影响到换热器 的换热效率,尤其是对结垢情况影响较大.因此,盘管 时必须使层间距适度,没有窄间隙死角,防止局部区域 布置不均匀,造成流体阻塞,降低流体的流通面积.
2.2焊接的控制.缠绕管的损坏形式最常见的是管口 泄漏,这是设备的关键部位.一般缠绕管换热器为了提 高换热效率,采用管子都比较小和薄,焊接容易产生缺 陷.因此,焊接必须严格控制线能量,焊缝要均匀和饱 满.