第6章 高炉煤气净化除尘系统
工艺方法——高炉煤气变压吸附净化系统

工艺方法——高炉煤气变压吸附净化系统工艺简介高炉煤气中含有粉尘、酸性介质和水蒸气等杂质。
因此需经过除尘脱水处理后才能使用。
近年来,全干法布袋除尘技术凭借除尘率高,污染少等诸多优点,成为高炉煤气除尘的首选。
但使用全干法除尘技术,高炉煤气温度过高,无法直接进入变压吸附净化系统。
为此,本系统加入了煤气冷凝器,对煤气降温后再进行脱水,以满足变压吸附净化系统对煤气温度和含湿量的要求。
净化系统加压机入口的煤气温度需降至常温,且温度越低,加压机效率越高。
同时,煤气含湿量对加压机的效率也影响较大。
因此,需进一步降低煤气温度及湿度,以提高加压机效率。
高炉煤气经初步除尘箱、布袋除尘器及TRT/BPRT 后,一部分去往热风炉作为燃料;剩余部分进入冷凝器降温,之后进入脱水器干燥,最后进入变压吸附净化系统,生成CO产品。
本系统进一步降低了煤气温度,同时降低了煤气含湿量。
高炉煤气经降温脱水后,可以直接供给变压吸附净化系统。
本系统包括初步除尘箱、布袋除尘器、TRT/BPRT、减压阀组、冷凝器、脱水器和变压吸附净化系统。
一、初步除尘箱随着高炉利用系数的不断提高,煤气量和含尘量都增大,现有重力除尘器的除尘效率明显降低。
针对目前重力除尘器存在的结构单一,尘粒不能有效沉降等问题,提出了顶端进气、加挡板的方法。
高炉煤气粗除尘采用初步除尘箱,使用重力除尘与旋风除尘结合的方法,利用尘粒的惯性力将固体颗粒从气体中分离出来。
初步除尘箱顶部设有斜向下的进气管,侧面设有出气管。
由于进气方式的改变,含尘气体在除尘器内部产生旋流,很好的结合了旋风除尘的除尘方法,使除尘率提高。
初步除尘箱内设有斜向下的金属筛板,金属筛板的一侧与初步除尘箱的进气管相对,初步除尘箱底板上设有积尘槽。
积尘槽设于金属筛板底端下方,初步除尘箱的出气管位于金属筛板的另一侧,布袋除尘器的进气口与初步除尘箱的出气管连接。
有金属筛板的重力除尘器,含尘气流冲击在挡板上,气流方向发生急剧转变,借助尘粒本身的惯性力作用,使其与气流分离。
高炉煤气除尘系统.

高炉煤气处理系统一.煤气处理包括:(1)除尘;(2)脱水。
二.煤气除尘设备及原理(1)除尘流程a.除尘的原因及目的;高炉冶炼过程中,从炉顶排出大量煤气,其中含有CO、H2、CH4等可燃气体,可以作为热风炉、焦炉、加热炉等的燃料。
但是由高炉炉顶排出的煤气温度为150~300ºC,标态含有粉尘约40~100 g/m3。
如果直接使用,会堵塞管道,并且会引起热风炉和燃烧器等耐火砖衬的侵蚀破坏。
因此,高炉煤气必须除尘后才能作为燃料使用。
b.煤气除尘设备:湿法除尘、干法除尘。
湿法除尘:干法除尘:干法除尘有两种,一种是用耐热尼龙布袋除尘器,另一种是干式电除尘器。
(2)设备a.粗除尘设备:重力除尘器、旋风除尘器重力除尘器:利用自身的重力使尘粒从烟尘中沉降分离的装置。
重力除尘器除尘原理是突然降低气流流速和改变流向,较大颗粒的灰尘在重力和惯性力作用下,与气分离,沉降到除尘器锥底部分。
属于粗除尘。
重力除尘器上部设遮断阀,电动卷扬开启,重力除尘器下部设排灰装置。
重力除尘器是借助于粉尘的重力沉降,将粉尘从气体中分离出来的设备。
粉尘靠重力沉降的过程是烟气从水平方向进入重力沉降设备,在重力的作用下,粉尘粒子逐渐沉降下来,而气体沿水平方向继续前进,从而达到除尘的目的。
在重力除尘设备中,气体流动的速度越低,越有利用沉降细小的粉尘,越有利于提高除尘效率。
因此,一般控制气体的流动速度为1—2m/s,除尘效率为40%一60%。
倘若速度太低,则设备相对庞大,投资费用增高,也是不可取的。
在气体流速基本固定的情况下,重力除尘器设计得越长,越有利于提高除尘效率,但通常不宜超过10m长。
旋风除尘器:除尘机理是使含尘气流作旋转运动,借助于离心力降尘粒从气流中分离并捕集于器壁,再借助重力作用使尘粒落入灰斗。
影响除尘效率的因素1、进气口旋风除尘器的进气口是形成旋转气流的关键部件,是影响除尘效率和压力损失的主要因素。
切向进气的进口面积对除尘器有很大的影响,进气口面积相对于筒体断面小时,进人除尘器的气流切线速度大,有利于粉尘的分离。
大气污染——第六章 主要工业行业废气治理

6.5 电力工业废气治理
1. 燃煤电厂锅炉烟尘治理 2. 燃煤电厂锅炉硫氧化物的治理
项目
碳利用率/% 脱硫率/%
SO2/ (ml/m3)
Nor/ (ml/m3)
排放量
CO/ (ml/m3)
CO2/%
FBC
93
MSFBC
98
75
365
240
478
11.4
95
95
72
400
14.5
O2/%
9.5 3.8
多物循环流化床(MSFBC)与常规流化床(FBC)燃烧的性能比较
6.5 电力工业废气治理
工程实例简介:某热电厂130T/h锅炉烟气循环流化床脱硫改造工程
1.工艺过程
2.工艺原理
3.反应机理
4.技术特点
5.系统构成
(1). 烟气 系统
⑴化工废气的分类
第一类为含无机污染物的废气,主要来自氮肥、磷肥(含硫酸)、无机盐等行业; 第二类为含有机污染物的废气,主要来自有机原料及合成材料、农药、染料、涂料等行业; 第三类为既含无机污染物又含有机污染物的废气,主要来自氯碱、炼焦等行业。
化学工业主要行业废气来源及主要污染物排放
行业 氮肥 磷肥
无机盐 氯碱 有机原料及合成材料
3.治理技术
(1)炉前矿槽的除尘 (2)高炉出铁场除尘 (3)碾泥机室除尘
6.3 钢铁工业废气治理
1.废气来源
炼钢厂废气主要来源于冶炼过程,特别是在吹氧冶炼期产生大量的废气。
2.治理技术
⑴炼钢电炉的烟尘控制 ⑵吹氧转炉烟气的治理
6.3 钢铁工业废气治理
1.钢铁工业废气的特点? 2.简述钢铁工业废气的主要来源。 3.钢铁工业污染源主要来自哪几个环节? 4.钢铁工业废气的主要控制途径?
高炉煤气净化系统的研究与应用

高炉煤气净化系统的研究与应用摘要:主要介绍高炉煤气净化系统的意义、分类、工作原理以及实际生产中的应用。
关键词:干法布袋除尘;湿法布袋除尘中图分类号:TF5文献标识码:A文章编号:1671-7597(2011)0220065-011、简述钢铁企业的炼铁高炉在生产过程中产生一些副产品高炉煤气,这些煤气作为一种含有热值的能源,如果直接放散,将对环境造成污染。
多年来,由于我国没有先进的技术将回收后的这些煤气进行充分利用,大量的富余煤气只能将其燃烧后排放,俗称“点天灯”,白白浪费了资源。
高炉煤气净化除尘系统是一种对高炉荒煤气进行净化处理的循环利用的系统,通过长时间的使用和研究,现在高炉煤气净化除尘系统一般采用干法布袋除尘和湿法除尘两种技术手段,是典型的节能环保技术,特别对我国大型高炉煤气布袋除尘的推广与发展具有重要意义。
2、分类目前,干法布袋除尘种类的划分,基本上是按照除尘器设备的类型来划分的,大体包括六种类型:2.1MDC、PDC煤磨防爆静电袋式除尘器MDC、PDC煤磨防爆静电袋式除尘器和PDC普通型袋收尘器是一种高效收尘器。
MDC防爆型袋式收尘器采用负压工作,用于煤磨系统收尘,是国家“七五”期间科技攻关项目。
MDC防爆型袋式收尘器采用防静电滤料,机体具有防爆结构,并设有泄压装置,具有防爆性能,适用于煤粉设备系统以及易燃、易爆粉尘的收集,该设备机械动作部件少,维修工作量小,换袋方便,由于采用脉动分室清灰,收尘效率高,能够长期、高效运行,收尘效率在99.8%以上。
PDC普通型收尘器除设有防爆性能外,具有上述同样优点。
可以广泛地应用于水泥、电力、冶金、化工等工作废气的收尘。
如水泥磨、生料磨、矿山破碎、物料提升、运输等扬尘点的收尘均可使用。
2.2PPC气箱式脉冲袋收尘器PPC气箱式脉冲袋收尘器具有二十一世纪先进水平的高效率袋收尘器。
它综合分室反吹和喷吹脉冲清灰各类袋收尘器优点,克服了分室反吹清灰强度不夠,喷吹脉冲清灰和过滤同时进行的缺点,因而扩大了袋收尘器的应用范围,由于这种类型的收尘器的结构有其特点,所以提高了收尘效率,延长了滤袋的使用寿命。
高炉煤气除尘
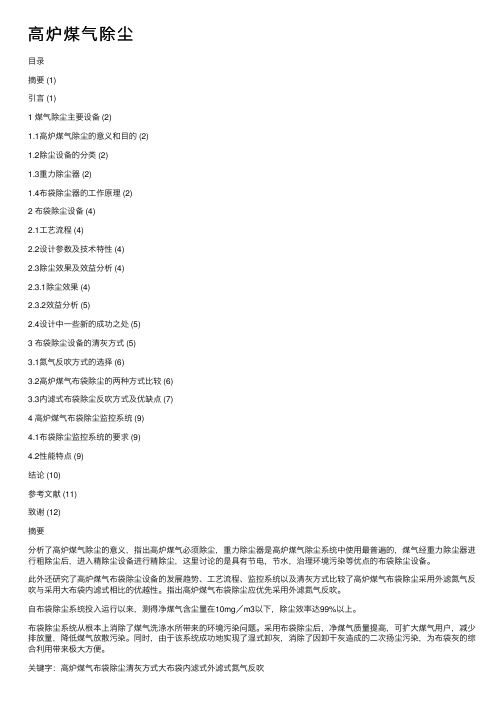
⾼炉煤⽓除尘⽬录摘要 (1)引⾔ (1)1 煤⽓除尘主要设备 (2)1.1⾼炉煤⽓除尘的意义和⽬的 (2)1.2除尘设备的分类 (2)1.3重⼒除尘器 (2)1.4布袋除尘器的⼯作原理 (2)2 布袋除尘设备 (4)2.1⼯艺流程 (4)2.2设计参数及技术特性 (4)2.3除尘效果及效益分析 (4)2.3.1除尘效果 (4)2.3.2效益分析 (5)2.4设计中⼀些新的成功之处 (5)3 布袋除尘设备的清灰⽅式 (5)3.1氮⽓反吹⽅式的选择 (6)3.2⾼炉煤⽓布袋除尘的两种⽅式⽐较 (6)3.3内滤式布袋除尘反吹⽅式及优缺点 (7)4 ⾼炉煤⽓布袋除尘监控系统 (9)4.1布袋除尘监控系统的要求 (9)4.2性能特点 (9)结论 (10)参考⽂献 (11)致谢 (12)摘要分析了⾼炉煤⽓除尘的意义,指出⾼炉煤⽓必须除尘,重⼒除尘器是⾼炉煤⽓除尘系统中使⽤最普遍的,煤⽓经重⼒除尘器进⾏粗除尘后,进⼊精除尘设备进⾏精除尘,这⾥讨论的是具有节电,节⽔,治理环境污染等优点的布袋除尘设备。
此外还研究了⾼炉煤⽓布袋除尘设备的发展趋势、⼯艺流程、监控系统以及清灰⽅式⽐较了⾼炉煤⽓布袋除尘采⽤外滤氮⽓反吹与采⽤⼤布袋内滤式相⽐的优越性。
指出⾼炉煤⽓布袋除尘应优先采⽤外滤氮⽓反吹。
⾃布袋除尘系统投⼊运⾏以来,测得净煤⽓含尘量在10mg/m3以下,除尘效率达99%以上。
布袋除尘系统从根本上消除了煤⽓洗涤⽔所带来的环境污染问题。
采⽤布袋除尘后,净煤⽓质量提⾼,可扩⼤煤⽓⽤户,减少排放量,降低煤⽓放散污染。
同时,由于该系统成功地实现了湿式卸灰,消除了因卸⼲灰造成的⼆次扬尘污染,为布袋灰的综合利⽤带来极⼤⽅便。
关键字:⾼炉煤⽓布袋除尘清灰⽅式⼤布袋内滤式外滤式氮⽓反吹引⾔⾼炉煤⽓布袋除尘系统是近些年发展起来的新⼯艺。
它的优点是⼯艺简单,不消耗⽔,没有⽔质污染的问题。
它的除尘效果较稳定,净煤⽓含尘量能经常保持在10mg/m3以下,并不受⾼炉煤⽓压⼒与流量波动的影响。
毕业设计—高炉煤气除尘净化

第一章概论 (4)1.1 问题的提出 (4)1.2 课题来源、背景及研究对象 (5)1.2.1 课题来源 (5)1.2.2 昆钢6#高炉煤气净化和应用现状 (5)1.2.3 研究对象 (5)1.3 项目意义 (5)第二章设计依据 (6)2.1煤气除尘技术 (6)2.1.1 高炉煤气粗除尘 (6)2.1.2 高炉煤气精除尘 (6)2.1.2.1 高炉煤气湿法除尘 (6)2.1.2.2 高炉煤气干法除尘 (7)2.1.2.3 高炉煤气精除尘工艺比选[1,6] (8)2.2 干法布袋除尘技术 (9)2.2.1 干法布袋除尘技术进展 (9)2.2.1.1国外运用进展 (9)2.2.1.2 国内运用进展 (10)2.2.2 大型干法高炉煤气除尘技术总结 (11)2.2.2.1 工艺线路 (11)2.2.2.2 控温方式 (12)2.2.2.3 布袋除尘灰的输送 (13)2.3 各类除尘器简介 (13)2.3.1 重力除尘器 (13)2.3.1.1 简介 (13)2.3.1.2 重力除尘的分类与形式 (14)2.3.2 旋风除尘器 (14)2.3.2.1 简介 (14)2.3.2.2 旋风除尘器工作机理 (14)2.3.2.3 旋风除尘器的类型及特点 (15)2.3.2.4 旋风除尘器性能 (17)2.3.3 布袋除尘器 (18)2.3.3.1 概述 (18)2.3.3.2 除尘机理 (18)2.3.3.3 布袋除尘器的分类 (19)2.3.3.4 布袋除尘器的结构形式 (19)2.3.3.5 布袋除尘器的性能 (20)2.3.3.6 布袋除尘器的设计及选型 (21)2.3.3.7 设计进程中采取的计谋[17] (21)2.4 高炉煤气脱硫处置 (22)2.4.1 概述 (22)2.4.2 湿法脱硫技术 (22)2.4.2.1 化学吸收法: (22)2.4.2.2 物理吸收法 (23)2.4.2.3 物理化学吸收法 (23)2.4.2.4 湿式氧化法 (23)2.4.3 干法脱硫 (24)2.4.3.1 膜分离法 (24)2.4.3.2 分子筛法 (24)2.4.2.3 其他方式 (24)2.4.4 微生物法 (25)2.4.5 臭氧氧化法 (25)2.4.6 电化学法 (25)第三章工艺设计计算与选型 (25)3.1重力除尘器设计 (26)3.1.1重力除尘器及粗煤气管道 (26)3.1.1.1粗煤气管道及重力除尘器结构与布置 (26)3.1.1.2 粗煤气管道的布置及要紧尺寸的确信 (27)3.1.1.3重力除尘器的布置及要紧尺寸的确信 (27)3.1.2 粗煤气管道及除尘器设计计算 (27)3.1.2.1粗煤气管道设计计算[15] (28)3.1.2.2重力除尘器尺寸设计计算 (30)3.1.3重力除尘器及粗煤气管道结构与内衬 (34)3.2旋风除尘器设计 (34)3.2.1 旋风除尘器的选择 (35)3.2.2 技术计算 (35)3.2.2.1 除尘器处置风量(工况)计算 (35)3.2.2.2 除尘器结构尺寸计算 (36)3.2.2.3 除尘器压降计算 (38)3.3 布袋除尘器 (39)3.3.1 除尘技术参数 (39)3.3.2 确信布袋除尘器形式 (40)3.3.3 除尘工艺计算 (40)3.3.3.1 除尘器结构尺寸计算 (40)3.3.3.2 除尘器平面布置 (42)3.3.4 反吹清灰工艺设计 (43)3.3.4.1 清灰方式的选择 (43)3.3.4.2 压力损失 (44)3.3.4.3 喷吹气体及参数的选择 (44)3.3.5除尘效率计算 (45)3.3.6 附属设备:储气罐设计 (45)3.3.6.1设计参数 (46)3.3.6.2 容器形式的选择 (46)3.3.6.3 主体几何尺寸的确信 (47)3.3.6.4 水压实验与强度校核 (49)3.3.6.5 支座选型 (49)3.3.6.6储罐尺寸参数汇总 (50)3.3.7 除尘自动操纵系统设计 (50)3.3.7.1 煤气温度操纵系统 (50)3.3.7.2 压差电控仪 (51)3.3.7.3 脉冲操纵仪 (51)3.3.7.4 灰位自动操纵系统 (52)3.3.7.5 箱体自动检漏系统 (52)3.4 高炉煤气脱硫设计 (53)第四章煤气除尘净化经济技术分析 (53)4.1 能源评判及节能方法 (53)4.1.1 能源及能源评判 (53)4.1.2 工序能耗评判 (54)4.1.3 节能方法 (54)4.2 应用成效 (54)4.2.1 节能环保成效好 (54)4.2.2 净煤气质量好 (54)4.3 成效分析 (55)4.3.1 经济效益 (55)4.3.2 环境效益 (55)第五章结论与展望 (56)第六章感想与体会 (57)致谢 (58)参考文献: (59)第一章概论1.1 问题的提出能源一样分为两大类:即一次能源和二次能源。
高炉煤气除尘系统ppt课件
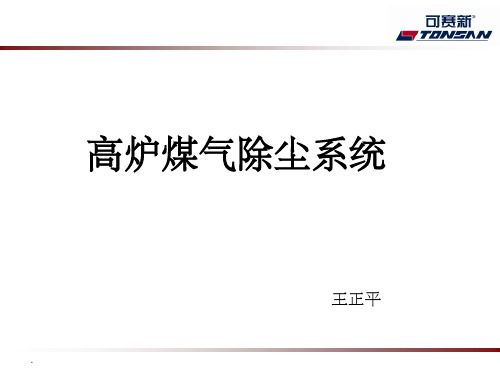
.
除尘设备及原理-半精细除尘设备
3、溢流文氏管主要参数
收缩角 扩张角 喉口长度mm 喉口流速m/s
20º~25理-精细除尘设备
一、文氏管
1、除尘原理 与溢流文氏管相同,只
是通过喉口部位的煤气流速 更大,气体对水的冲击更加 激烈,水的雾化更加充分, 可以使更细的粉尘颗粒得以 湿润凝聚并与煤气分离。
.
除尘设备及原理-精细除尘设备
三、布袋除尘器
为过滤除尘,含尘煤 气流通过布袋时,灰尘被 截留在纤维体上,而气体 通过布袋继续运动,通过 振动或反吹将粉尘清落卸 出,属于干法除尘。
1-布袋; 2-反吹管; 3-脉冲阀; 4-脉冲气包; 5-箱体; 6-排灰口
.
除尘设备及原理-脱水器
一、重力式脱水器
一、高炉炉顶煤气管道
.
除尘系统附属设备-煤气管道
1、 煤气导出管 均匀分布在炉头处。小型高炉有两根,大型高炉有四根。 煤气在导出管内流速为3~4m/s。 导出管倾角应大于50,一般为53。
2、 煤气上升管 导出管上部成对地合并在一起的垂直部分为上升管。 上升管内煤气流速为5~7m/s。
3、 煤气下降管 由上升管通向重力除尘器的一段为煤气下降管。 下降管内煤气流速一般为6~9m/s,下降管倾角大于40。
2、结构示意图
3、旋风除尘特点 旋风除尘器可以除去大于20µm
的粉尘颗粒。
.
除尘设备及原理-半精细除尘设备
一、洗涤塔
1、结构 内设三层喷水管,每层
都设有均布的喷头,最上层 逆气流方向喷水,喷水量占 总水量的50%,下面两层则 顺气流方向喷水,喷水量各 占25%。
.
1-煤气导入管; 2-洗涤塔外壳; 3-喷嘴; 4-煤气导出管; 5-人孔; 6-给水管
高炉煤气除尘脱硫脱氯净化系统设计

(论文)摘要高炉煤气是钢铁冶炼的副产物之一。
高炉煤气中含有的CO、HCl、H2S、COS等有毒气体以及大量粉尘,对大气都造成了不可忽视的污染,所以对于高炉煤气的治理刻不容缓。
但在煤气中还存在着可利用的高温高压以及可回收二次利用的有用气体,所以将其除尘脱硫脱氯过程中,对煤气进行进一步利用,将给整个工厂带来巨大的经济效益。
本设计的主要内容是针对标准状况下40万m³/h的高炉煤气流量,对其进行除尘脱硫脱氯的工艺设计,使其满足排放要求。
目前针对高炉煤气脱硫的方法有加氢转化法、氧化法、吸附法和水解法等。
催化水解法是目前应用最为广泛的方法。
目前,国内外关于煤气除尘工艺已经有许多种并都较为成熟。
因此本设计的方案是旋风除尘器对高炉煤气进行粗除尘,再经过布袋除尘器进行进一步除尘。
除尘之后,有机硫转化工艺采用高效水解转化工艺,主要是将有机硫催化水解为硫化氢,然后采用喷淋吸收的方法将硫化氢和氯化物净化去除。
本设计主要针对某1500m³高炉煤气进行除尘脱硫脱氯净化系统的设计,针对该设计主要是在TRT余压发电装置前设置预处理塔和催化水解塔,在TRT余压发电装置前后设置喷淋吸收塔,最终实现该高炉煤气的脱硫脱氯技术要求。
本设计也将估算整个工艺流程所需要的建设成本。
关键词:高炉煤气,湿法脱硫,喷淋水解,旋风除尘,布袋除尘- I -(论文)Design of dedusting desulfurization and dichlorinationpurification systemAbstractBlast furnace gas is one of the main by-products in the process of ironmaking. The CO, HCl, H2S, COS and other toxic gases in blast furnace gas as well as a large amount of dust have caused non-negligible pollution to the atmosphere, so it is urgent to control the blast furnace gas. However, there are still usable high temperature and high-pressure gas in the gas as well as useful gas that can be recycled for secondary use. Therefore, further utilization of the gas in the process of dedusting, desulfurization and dichlorination will bring huge economic benefits to the whole plant.The main content of this design is to design the process of dedusting, desulfurization and dichlorination for the blast furnace gas flow of 400,000 m /h under standard conditions, so as to make it meet the discharge requirements. At present, the main methods of removing organic sulfur from blast furnace gas include hydrogenation and conversion, oxidation, adsorption and hydrolysis. Catalytic hydrolysis is one of the most important methods to remove organic sulfur. At present, there are many kinds of gas dust removal technology at home and abroad. Therefore, the scheme of this design is the cyclone dust collector to the blast furnace gas for coarse dust, and then through the bag filter for further dust. After dust removal, the organic sulfur conversion process adopts efficient hydrolysis conversion process, which is mainly to catalyze the hydrolysis of organic sulfur into hydrogen sulfide, and then to purify hydrogen sulfide and chloride by spray absorption.This design is mainly aimed at the design of a purification system for dedusting, desulfurization and dichlorination of a certain 1500m blast furnace gas. For this design, the pretreatment tower and catalytic hydrolysis tower are set before the TRT residual pressure power generation unit, and the spray absorption tower is set before and after the TRT residual pressure power generation unit, so as to realize the technical requirements of desulfurization and dichlorination of the blast furnace gas. This design also estimates the construction cost required by the whole process.- III -(论文)Key Words:blast furnace gas,Wet desulfurization,cyclone dust removal,bag dust removal,spray hydrolysis- IV -(论文)目录摘要 (I)Abstract ........................................................................................................................ I II1 引言 (1)2 研究背景 (2)2.1 课题背景 (2)2.2 研究意义 (2)2.3 高炉煤气常见除尘工艺 (3)2.3.1 重力除尘技术 (3)2.3.2 旋风除尘技术 (3)2.3.3 离心湿式除尘技术 (4)2.3.4 布袋除尘技术 (4)2.3.5 电除尘技术 (4)2.4 脱氯工艺综述 (5)2.4.1 高炉煤气中氯元素的主要来源 (5)2.4.2 高炉煤气中HCl的危害 (5)2.4.3 高炉煤气中HCl脱除办法 (6)2.5 脱硫工艺综述 (6)2.5.1 加氢转化法 (7)2.5.2 氧化法 (7)2.5.3 催化水解法 (7)3 工程设计 (8)3.1 设计内容 (8)3.2 设计方法 (10)4 工艺设计及其计算 (12)4.1 旋风除尘器设计 (12)4.1.1 确定旋风除尘器处理气体量 (13)4.1.2 旋风除尘器结构尺寸计算 (13)4.1.3 除尘器压降计算 (15)4.1.4 除尘率与除尘量计算 (15)4.2 布袋除尘器设计 (18)4.2.1 确定布袋除尘器处理气体量 (18)4.2.2 除尘器尺寸结构计算 (18)- V -(论文)4.2.3 压力损失 (20)4.2.4 除尘效率 (21)4.2.5 布袋除尘器的平面布置 (22)4.3 水解塔设计计算 (23)4.3.1 物料平衡计算 (23)4.3.2 催化剂的设计 (24)4.3.3 水解塔结构设计 (26)4.4 喷淋塔设计计算 (27)4.4.1 通过喷淋塔的流量计算 (28)4.4.2 喷淋塔尺寸计算 (28)4.4.3 喷淋塔喷淋系统设计 (28)4.4.4 喷淋系统选型设计 (29)4.4.5 碱液循环池设计 (30)4.4.6 喷淋塔壁厚设计 (30)5 经济分析 (31)5.1 经济分析的目的和意义 (31)5.2 建设成本估算 (31)5.2.1 旋风除尘器设备成本 (31)5.2.2 布袋除尘器设备成本 (32)5.2.3 水解塔和喷淋塔设备成本 (32)5.2.4 其他费用 (33)6 结论 (34)参考文献 (35)附录A (37)在学取得成果 (39)致谢 (41)- VI -(论文) - VII -(论文)1引言近年来,随着我国工业技术的不断创新进步,构建循环经济型产业体系,加快环保产业的发展被成为国家发展的新方向。
高炉煤气干法除尘系统介绍

上海瑞帆环境工程有限公司
高炉煤气干法布袋除尘器应用技术 主要内容
高炉煤气特性
高炉煤气净化发展过程
干法布袋除尘器系统介绍
瑞帆企业
高炉煤气干法布袋除尘器应用技术
高炉煤气的特性
高炉煤气是高炉炼铁时产生的气体,是一种剧毒低热值的气体,发热 值为2800~3500KJ/m3,是钢铁企业内部生产使用的主要能源。需要除 尘后再利用。 高炉气体相比其他气体具有以下特性: ①温度较高 正常:150℃ (90~250℃ ), 短时高温320℃ , 事故时500℃~700℃ ②压力高 1000m3以下压力~0.15MPa 1000~2000m3压力为0.15~0.22MPa 2000m3以上压力为0.2~0.28MPa 处理煤气的设备满足压力容器的条件,属于压力容器的范围GB150。 除尘器是一个个独立的圆筒状,而不是环境除尘器的方形。 ③剧毒 含有约22%-26%的CO
除尘器箱体:
1、除尘器箱体按照GB150《钢制压力容器》进行设计。 箱体为园形筒状结构,直径为φ5232mm,设计压力为 0.3MPa,箱体材料为Q235-B 。壁厚16mm 。 2、在出气支管上设有一套安全放散装置,在检修时打 开,用来置换出煤气。 3、箱体进气、出气支管上均安装有大拉杆横向波纹补 偿器、气动三偏心蝶阀、带人孔短接、电动盲板阀。 4、箱体上设置4个人孔,方便检修。 5、箱体上设有8个支座,支撑箱体。 6、箱体上设吹扫系统一套,分别设在进、出气口、灰 斗底部和格子板上的人孔上,起清除局部积灰和置换 作用。 7、箱体上设有人工灰尘检侧口一个,方便取样化验。 8、灰斗锥度41度,远小于灰尘安息角,方便卸灰。并 设有仓壁震动器、氮气炮和氮气反送等装置 ,保证卸 灰通畅。
高炉煤气除尘系统的设计
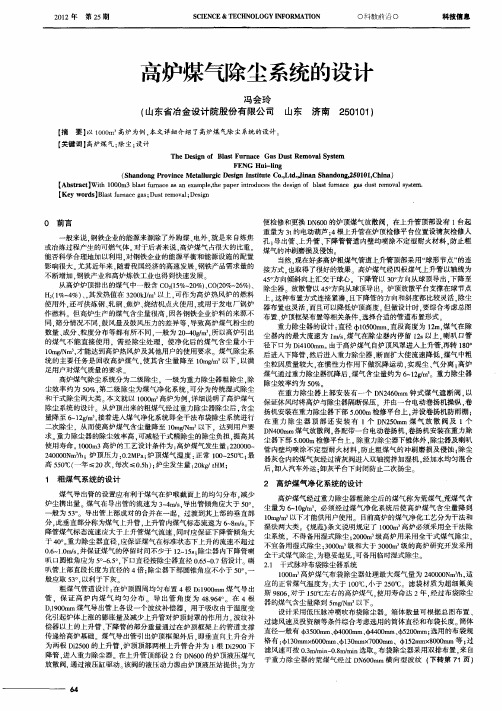
0 前 言
一
或冶炼过程产生的可燃气体。 对于后者来说 , 高炉煤气 占很大的 比重。 能否科学合理地加 以利用 . 对钢铁 企业的能源平 衡和能源设施 的配置 影 响很大 。 尤其 近年来 , 随着我 国经济的高速发展 . 钢铁产 品需求量的 不断增加 . 钢铁产业和高炉炼铁工业也得 到快速发展 从高炉炉顶排 出的煤气中一般含 C 2 5 2 %)C (0 2 %) 0( %~ 0 、 02 %~ 6 、 1 H (%~ %) . 1 4 、其发热值在 3 0 k/ 以上 , 2 0Jm3 可作为高炉热 风炉的燃料 使用外 , 还可供炼钢 、 轧钢 、 焦炉 、 烧结机点火使用 , 或用于发电厂锅炉 作燃料 。但高炉生产的煤气含尘量很高 . 因各钢铁企业炉料的来源不 同. 筛分情况不 同. 鼓风量及鼓风压力的差异等 . 导致高炉煤气粉尘 的 数量 、 成分 、 粒度分布等都有所不 同 , 一般 为 2 ~ 0/ 3所 以高炉引 出 0 4 gm , 的煤气 不能直接 使用 ,需经 除尘处 理 .使净化后 的煤气 含尘量小于 1m / m , 0g s N 才能达到高炉热风炉及其他用户的使用要求 煤气 除尘系 统 的主要任务 是回收高炉煤气 . 使其含 尘量降至 1m / s 0 g 以下 . m 以满 足用户对煤气质量 的要求 高 炉煤气 除尘系统分为二级除尘 .一级为重力除尘器粗除尘 . 除 尘效率约为 5 %. 0 第二级除尘为煤气 净化系统 . 分为传统湿式除尘 可 和于式 除尘两大类 本文就 以 10 m 高炉为例 . 00 s 详细说明了高炉煤气 除尘 系统 的设计 从炉顶 出来 的粗煤气经过重力除尘器除尘后 . 含尘 量降至 6 1 g s - 2/ . m 接着进入煤气净化系统 即全干法布袋 除尘 系统进行 二次除尘 . 而使高炉煤气含尘量 降至 1m / m 以下 . 到用户要 从 0g s N 达 求。 重力除尘器的除尘效率 高 . 可减轻干式精除尘的除尘负担 . 提高其
煤气净化系统
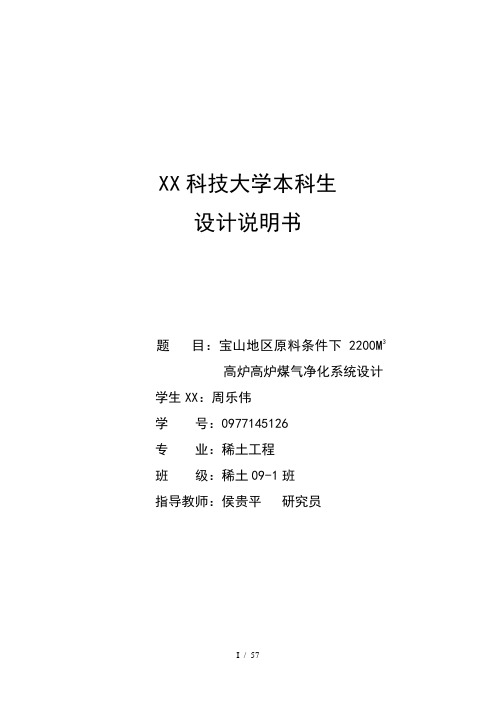
XX科技大学本科生设计说明书题目:宝山地区原料条件下2200M3高炉高炉煤气净化系统设计学生XX:周乐伟学号:0977145126专业:稀土工程班级:稀土09-1班指导教师:侯贵平研究员宝山地区原料条件下2200M3高炉煤气净化系统设计摘要高炉煤气净化系统是高炉的重要组成部分。
本设计对炼铁工艺和高炉炉型进行了详细的计算,并对煤气除尘设备和除尘系统的平面布置进行了设计。
其中设备主要包括重力除尘器和布袋除尘器。
本设计采用的是先进的干法布袋除尘器技术,详细阐述了布袋除尘器的分类、结构设计、清灰装置设计、温度控制装置设计、灰斗和卸灰装置的设计及TRT的选择。
关键词:高炉煤气:净化:布袋除尘器Baoshan material conditions of 2200M3 blast furnace gaspurification systemAbstractBlast furnace gas purification system is an important ponent Of furnace. The design for the blast furnace ironmaking process and carried out detailed calculations, gas and dust removal equipment and layout of the system was designed. The equipment includes gravity and bag house dust. This design uses advanced dry bag filter technology, elaborated bag house classification, structural design,cleaning equipment design, temperature control device design, hopper and discharging device design and the choice of TRT.Key words: blast furnace: purification: bag filter目录摘要 (I)Abstract........................................................... I I 第一章文献综述.. (1)1.1 概述 (1)1.2 高炉炼铁 (2)1.2.1 高炉炼铁的技术进步 (2)1.2.2 高炉炼铁面临的问题及改善措施 (3)1.3 高炉煤气 (4)1.3.1 高炉煤气简介 (4)1.3.2 高炉煤气净化回收的必要性 (4)1.3.3 高炉煤气净化工艺 (5)1.3.4 主要除尘器特点及除尘工艺比较 (6)1.3.5 三种除尘器的比较 (7)1.3.6 布袋除尘结构和除尘机理 (7)1.4 设计方案确定 (8)第二章炼铁工艺计算及主要参数选择 (10)2.1 原始数据整理计算 (10)2.1.1 原料成分 (10)2.1.2 燃料成分见表 (10)2.2 配料计算 (11)2.2.1 冶炼条件确定 (11)2.2.2 吨铁矿石用量计算 (11)2.2.3 生铁成分计算 (11)2.2.4 石灰石用量计算 (12)2.2.5 渣量及炉渣成分分析 (12)2.3 物料平衡计算 (13)2.3.1 风量计算 (14)2.3.2 煤气组成及煤气量计算 (14)2.3.3 考虑炉料的机械损失后实际入炉量 (16)2.3.4 编制物料平衡表 (17)2.4 高炉热平衡计算 (17)2.4.1 热量收入Q收 (17)2.4.2 热量支出 (18)2.4.3 编制热量平衡表 (20)第三章炉型计算及参数选择 (22)3.1 日产铁量计算 (22)3.2 炉缸尺寸计算 (22)3.3 炉缸高度计算 (22)3.3.1 渣口高度计算 (22)3.3.2 风口计算 (22)3.4 死铁皮层厚度 (23)3.5 炉腰直径、炉腹嚼、炉腹高度计算 (23)3.6 炉身角、炉身高度、炉喉高度 (23)3.7 校核炉容 (24)第四章重力除尘器设计 (27)4.1 粗煤气管道 (27)4.1.1 粗煤气管道布置及主要尺寸计算 (27)4.1.2 设计除尘器参考的数据: (27)4.2 高炉煤气发生量与煤气含尘量的计算 (28)4.2.1 炼铁工艺计算数据 (28)4.2.2 重力除尘器及管道设计 (28)4.3 煤气管道设计 (28)4.3.1 除尘器及煤气管道中煤气流速 (28)4.3.2 导出管设计 (28)4.3.3 上升管设计计算 (29)4.3.4 下降管设计计算 (29)4.3.5 放散管直径 (29)4.3.6 高炉炉顶管道设计参数 (30)4.4 重力除尘器的设计 (30)4.4.1 重力除尘器的设计要求 (30)4.4.2 重力除尘器部分设计参数选择 (30)4.4.3 重力除尘设备尺寸的选择 (30)4.4.4 积灰量及灰斗设计 (32)4.4.5 出口含尘浓度 (32)4.4.6 重力除尘器参数 (32)4.5 除尘器及粗煤气管道设备 (32)4.5.1 煤气遮断阀 (32)4.5.2 清灰阀及煤气灰搅拌机 (33)第五章布袋除尘器设计 (34)5.1 布袋除尘器形式 (34)5.2 滤料的选择 (34)5.3 清灰方式的确定 (35)5.4 过滤气体速度、过滤面积、滤袋尺寸、滤袋数目的确定 (35)5.5 除尘器平面布置 (36)第六章除尘系统附属设备 (38)6.1 阀门 (38)6.1.1 煤气遮断阀 (38)6.1.2 煤气放散阀 (38)6.1.3 煤气调节阀组 (39)6.1.4 叶形插板 (40)第七章余压发电 (41)7.1 煤气余压回收装置的工艺流程及特点 (41)7.1.1 工艺流程 (41)7.1.2 煤气余压回收装置的主要特点 (42)7.2 TRT的基本结构和工作原理 (42)7.2.1 TRT的基本结构 (42)7.2.2 TRT的工作原理 (43)7.3 TRT的运行操作过程及注意事项 (43)7.3.1 TRT启动 (43)7.3.2 TRT运行 (44)7.3.3 TRT停机 (44)第八章除尘器中的自动控制系统 (46)8.1 温度自动控制系统 (46)8.2 电压差控制仪 (46)8.3 脉冲控制仪 (46)8.4 箱体自动检漏 (47)参考文献 (48)致谢 (50)第一章文献综述1.1 概述高炉发源于中国,高炉何时在我国发明,各路专家尚无统一意见.有人推断是公元前8世纪[1,2],现在己有出土的铸铁实物,证实了这一推断[3],是世界上最早掌握冶铁技术少数文明古国之一欧洲出现高炉约在170年以后。
高炉除尘系统
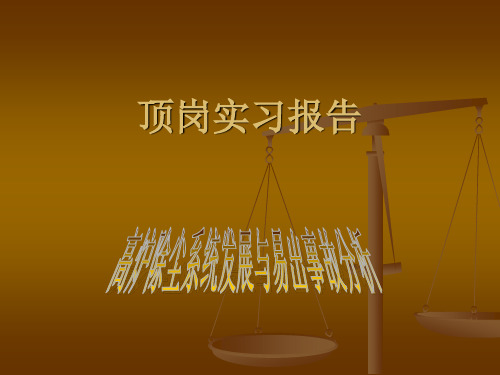
摘
要
大气环境的主要因素之一,将微细粒子的控制纳入国家标准只是时间问题。目前电除尘器捕集微细 粒子的效率很低,对小于10μm的尘粒,其捕集率只有60%左右,高炉煤气除尘净化在炼铁生产中有 重要的作用,每吨生铁产出高炉荒煤气约 1660Nm3,是钢铁厂重要的二次能源。高炉荒煤气含尘 量高,经过煤气净化系统后使高炉煤气含尘量从 6-12g/m3 降到 10mg/m3 以下供用户使用 本次的实习报告大约总结了近几十年高炉煤气除尘的发展以及“易发生的事故的分析”,指出高炉煤 气除尘技术是高炉发展的主要辅助系统,“袋式除尘”,“干法除尘”,并提出若干关于高炉煤气 除尘中系统易发生的事故,除尘技术是实现煤气净化技术关键。在此基础上,进一步阐述了高炉除尘 在设备高效化、长寿化和终点控制智能化等方面的技术进步。袋式除尘设备迅速大型化,用于钢铁、 水泥、火电行业的袋式除尘设备,许多单机的处理烟气量都超过100万m3/h,过滤面积超过两万 m2,其中火电行业的袋式除尘器单机最大处理烟气量超过300万m3/h,过滤面积在4万~5万m 2以 上。在设备规模大型化的同时注入了新的技术,使袋式除尘器的气流分布、气流组织和结构合理及 安全化等方面都有了显著进步 通过多年实践,对布袋除尘工艺系统的主要技术问题都有很深的认识和掌握,从工艺技术,滤料性 能,设备选型及质量,检测控制等方面采取措施,确保生产运行的可靠性,先进性,高炉煤气干式 除尘技术在我国走过一段漫长的道路,现在已经到了成熟阶段,高炉煤气应采用除尘才能做到节能 减排、综合利用。
ห้องสมุดไป่ตู้
高炉煤气净化均采用了干法布袋除尘工艺。干法布袋除尘具有除尘效 率高、净煤气含尘量低、质量好的特点。经过干法除尘的净煤气对煤 气用户大有益处。同时, 配合 TRT余压发电, 也进一步提高了能 源利用效率。但是, 在实际的运行过程中由于高炉生产和干法除尘的 各自特殊性, 也由于设备设计存在着许多问题和缺陷, 从而影响了干 法除尘的正常运行和高炉正常生产。干法除尘使用 的 布 袋 对 环 境 温 度 要 求严 格, 工作温度只能在 90~280 ℃之间, 温度过高 会烧坏布袋, 温度低会使布袋结露。正常情况下, 稳定顺行的高炉所 产生的高炉煤气完全可以满足干法除尘的温度要求。各高炉在正常生 产时, 炉顶温度基本稳定在。 高炉煤气是高炉在冶炼过程中产生的一 种可燃气体,也是冶金工业中可以回收利用的四种煤气之一。按我国 目前的生产水平,每炼1吨生铁约产生1700~2000m3的高炉煤气, 其热值在3000~3500kJ/m3之间、温度在250℃~300℃之间,显 热平均约为400kJ/m3。另外,高压高炉炉顶煤气的压力为(1.5~ 2.0)×105Pa,该压力能相当于100kJ/m3的热能。因此,利用高 炉煤气的潜热和显热是节约能源、发展循环经济的重要途径,因此得 到专有关部门的高度重视。我国是采用高炉煤气干法袋式除尘最早的 国家之一,至今已有40多年的历史。早在家和2005年我国高炉煤气 的利用率已达100%。本文重点介绍并分析了我国高炉煤气干法除尘 技术发展的三个阶段 。
- 1、下载文档前请自行甄别文档内容的完整性,平台不提供额外的编辑、内容补充、找答案等附加服务。
- 2、"仅部分预览"的文档,不可在线预览部分如存在完整性等问题,可反馈申请退款(可完整预览的文档不适用该条件!)。
- 3、如文档侵犯您的权益,请联系客服反馈,我们会尽快为您处理(人工客服工作时间:9:00-18:30)。
2. 工作原理 工作时溢流水箱的水不断沿溢流口流入收 缩段,保持收缩段至喉口连续地存在一层水膜, 当高速煤气流通过喉口时与水激烈冲击,使水 雾化,雾化水与煤气充分接触,使粉尘颗粒湿 润聚合并随水排出,并起到降低煤气温度的作 用。
3. 溢流文氏管主要设计参数
收缩角 20º~25º 扩张角 6º~7º 喉口长度,mm 300 喉口流速,m/s 50~70 喷水量, 3m3 t/10 3.5~4.0 溢流水量,t/103m3 0.5
6 高炉煤气净化除尘系统
6.1煤气除尘系统概述
一、煤气除500m3 ,其发热值一 般为3360~4200kj/m3,但是,由炉顶排出的煤气中一般 含有20~40mg/m3(标态)的灰尘,如不经净化处理直接送 至用户使用,会造成管道、燃烧器堵塞及设备的磨损,加 快耐火材料的熔蚀,降低蓄热器的效率。
四、煤气除尘工艺的分离
包括湿法除尘和干法除尘两种。
一. 湿法除尘: 1、塔文工艺:
高炉
重力除尘器 洗涤塔
二级文氏管
高压阀组
脱水器
净煤气管网
TRT
2、双文工艺
高炉
重力除尘器
一级文氏管 二级文氏管
高压阀组
脱水器
净煤气管网
TRT
3、环缝洗涤器(比肖夫煤气清洗工艺)
高炉
重力除尘器
环缝洗涤器
脱水器
旁通阀
(6)高炉煤气纯干法布袋除尘占地小,运行费用低。 (7)干式除尘器对介质适应性强,使用范围广。
6.2 煤气除尘设备及原理
6.2.1 粗除尘设备
一. 重力除尘器 1. 除尘原理: 煤气经中心导入管后,气流突然转向,流 速突然降低,煤气中的灰尘颗粒在惯性力和重 力作用下沉降到除尘器底部。
2. 结构示意图
2. 影响除尘效率的因素
(1)喉口处煤气流速:
当耗水量一定时,喉口流速越高则除尘效 率越高;
(2)耗水量有关: 当喉口流速一定时,耗水量多,除尘效率 也相应提高。
3. 特点
处理煤气量大,除尘效率高,出口煤气含 尘量低,但压力损失较大,适用于高压高炉。
二. 静电除尘器
1. 除尘原理: 当气体通过两极间的高压电场时,由 于产生电晕现象而发生电离,带阴离子的 气体聚集在粉尘上,在电场力作用下向阳 极运动,在阳极上气体失去电荷向上运动 并排出,灰尘沉积在阳极上,用振动或水 冲的办法使其脱离阳极。 负极为电晕极,正极为沉淀极。
煤气中的灰尘,又叫瓦斯灰,含铁30~50%,炭10~20%, 回收后可作为烧结原料。 高炉必须设置炉顶煤气余压发电装置,可以充分利用高炉 炉顶煤气的压力能和气体显热进行发电,同时还可提高煤 气质量,减少噪声对环境的污染,是一项环保型的高效节 能装置。
二、煤气除尘设备的分类
粗除尘设备:粒度为100~60μm及其以上的颗 粒除尘设备,除尘后含量<10g/m3;如重力除 尘器、旋风除尘器 半精细除尘设备:粒度为60~20μm及其以上 的颗粒除尘设备,除尘后含量<1g/m3;如洗 涤塔、溢流文氏管(一级文氏管) 粗除尘设备:粒度为<20μm及其以上的颗粒 除尘设备,除尘后含量<10mg/m3;如二级文 氏管、布袋除尘器、静电除尘器
(1)内滤型布袋除尘器
大多数高炉都采用此种布袋除尘器。箱体内装 圆筒形布袋若干条,为内滤式,一座高炉由3 ~6个除尘器组成,也有的采用8~10个箱体。一
般采用玻璃纤维滤袋,直径为230mm,250mm
和300mm三种。高炉容积大的选取较大直径,
布袋长度与直径的比值一般为25~30。
布袋除尘器示意图
三. 评价煤气除尘设备的主要指标: 1. 生产能力
指单位时间处理的煤气量,一般用 每小时所通过的标准状态的煤气体积流 量来表示。
2. 除尘效率 指标准状态下单位体积的煤气通过除 尘设备后所捕集下来的灰尘重量占除尘前 所含灰尘重量的百分数。
m1 m2 100 % m1
式中
——除尘效率,%;
6.2.2 半精细除尘设备
一. 洗涤塔
1. 结构:
内设三层喷水管,每层都设有均布的喷头, 最上层逆气流方向喷水,喷水量占总水量的50 %,下面两层则顺气流方向喷水,喷水量各占 25%。
结构图:
空心洗涤塔一般由普 通钢板焊制而成。中 间部分为圆形筒体, 上下两端为锥形。上 端锥面平夹角为450 , 下部锥面水平倾斜角 为600 左右,以便污 泥顺利排出。圆形筒 体直径按煤气流速 1.8~2.5m/s 确 定 , 高度按气流在塔内停 留 10~15s 时 间 考 虑 。 一般洗涤塔的高径比 为4~5。
1-布袋; 2-反吹管; 3-脉冲阀; 4-脉冲气包;
5-箱体;
6-排灰口
工艺流程是:含尘的煤气由除尘器的进气管进入箱 体,经过分配板进入布袋,将灰尘滤下,煤气穿过布 袋壁进人箱体变成净煤气由出口管引出,当灰膜增厚 到影响过滤时。进行反吹。
反吹有3种方式:放散反吹、调压反吹和加压反吹。
放散反吹通过放散煤气进行反吹,会浪费一部分煤 气,造成二次污染,因此已很少采用;
4、溢流文氏管与洗涤塔相比,具有结构简单、 体积小除尘效率高,水耗小等优点,但是压头损 失和煤气出口温度较高。
6.2.3 精细除尘设备
一. 文氏管(二级)
1. 除尘原理:
与溢流文氏管相同,只是通过喉口部 位的煤气流速(90~120m/s)更大,气体 对水的冲击更加激烈,水的雾化更加充分, 可以使更细的粉尘颗粒得以湿润凝聚并与 煤气分离。
1. 工作原理
含尘煤气以10~20m/s的标态流速从切线 方向进入后,在煤气压力能的作用下产生回旋 运动,灰尘颗粒在离心力作用下,被抛向器壁 积集,并向下运动进入积灰器。
2. 结构示意图
旋风除尘器
3. 特点: 除尘效率可达95%,可以除去大 于20µ m的粉尘颗粒,压力损失较大, 为500~1500Pa。
调压反吹由于易引起炉顶压力波动,且压力控制不 太稳定,往往造成效果不佳,也很少采用;
加压反吹需增加加压机等设施,投资较高,一般为 大型高炉布袋除尘系统采用。
进气方式有两种:上进气式的气流方向和灰尘 降落的方向一致,反吹时有利于灰尘降落,但 灰斗部分易形成煤气死区,温度低,易结露, 卸灰困难;下进气式的反吹效果差,但灰斗温 度高,易卸灰。 为了防止灰尘在布袋上凝结和在箱体壁上结块, 箱体外面应包以耐火纤维、石棉等保温材料, 并在壁上安装振动器,便于卸灰。
2. 结构形式: 有单管式、套筒式和平板式三种类型。
a-单管式;b-板式;c-套筒式
3. 影响除尘效率的因素
(1)荷电尘粒的运动速度。
(2)沉淀极比表面积愈大除尘效率愈高。
概念:沉淀极比表面积是指在1s内净化1m3煤 气所具有的沉淀极面积。 (3)煤气流速与入口煤气含尘量。 (4)喷水冲洗沉淀极上的尘粒,可以提高除 尘效率。 ( 5)灰尘本身的性质和数量。
干式除尘器的特点
(1)高炉煤气采用干法除尘可以多回收和利用煤气显热。 (2)高炉煤气采用干法除尘可以提高煤气的热值和理论燃烧温 度,从而降低了燃料消耗。
(3)高炉煤气采用干法除尘可以节约水、电。
(4)高炉煤气采用干法除尘和干式TRT发电量可增加35%~40 %。
(5)干法除尘效率高。大型高炉干式布袋除尘后净煤气含尘量 一般在3mg/m3 以下,平均不超过1mg/m3 ,而湿式除尘 后 净 煤 气 含 尘 量 一 般 在 5~10mg/m3 , 有 的 甚 豪 会 超 过 10mg/m3。
(2)脉冲型布袋除尘器
这是一种高效外滤 式布袋除尘器。采 用压缩气喷吹进行 反吹,自动化程度 高,过滤负荷比大 袋滤型高,相对体 积小,效率高。喷 吹气源用氮气或其 他非氧化气体。
工作原理:
含尘煤气由除尘器下部沿箱体壁切线方向,向下成一 定角度进人,在下部形成旋流并上升,此过程能除去 部分粗尘粒。上升旋流在导流板处被阻挡重新分布, 继续上升,到达布袋后粉尘被阻留在袋外,煤气穿过 布袋壁进人袋内,向上由袋口和箱体顶部出口管出箱 体。为防止布袋被气流从外压扁,袋内装有支撑框架。 反吹采用氮气,减压后进入脉冲反吹装置。在装置内, 由 电 磁 阀 控 制 脉 冲 阀 迅 速 开 启 , 开 启 时 间 为 65 ~85ms。此瞬间氮气通过脉冲阀进入喷吹管,并从管 内小孔垂直向下喷人布袋内,同时从四周带人大量的 净煤气,使袋胀鼓,抖落掉附着在袋外的尘粒,达到 清除灰膜的目的。
(4)排灰装置——螺旋清灰器
螺旋清灰器
1-筒形给料器;2-出灰槽;3-螺旋推进器;4-喷嘴; 5-水和灰泥的出口;6-排气管
3. 特点:
(1)除尘效率可达到80%,可以除去粒度 大于30μm的灰尘颗粒,出口煤气含尘可降 到2~10g/m3; (2)阻力损失较小,一般为50~200Pa。
二. 旋风除尘器
4. 水封排污装置
5. 特点
(1)结构简单,投资小,建设速度快, 不易堵塞,已维修等。 (2)除尘效率80~90%;压力损失80~ 200Pa ,除尘后含尘量<1g/m3。
二. 溢流文氏管 1. 结构
溢流文氏管示意图 1-煤气入口;
2-溢流水箱;
3-溢流口; 4-收缩管; 5-喉口; 6-扩张管
m1、m2——分别为入口和出口煤气标态 含尘量,g/m3
3. 压力降 指煤气压力能在除尘设备内的损失, 以入口和出口的压力差表示。
4. 水的消耗和电能消耗
水、电消耗一般以每处理1000m3标态 煤气所消耗的水量和电量表示。
对高炉煤气除尘设备的要求是:生产能力大, 除尘效率高,压力损失小,耗水量和耗电量少, 密封严和耐高压等。 高炉煤气除尘系统总的发展趋势是降低系统气 流阻损,提高除尘设备的除尘效率,发展余压 透平发电。鉴于干法除尘具有净煤气含尘量低, 多回收炉顶煤气能量等优势,因此,高炉设计 应采用煤气干式除尘装置。