江苏沙钢高炉煤气干法除尘器及除尘工艺系统设计方案
干法除尘技术
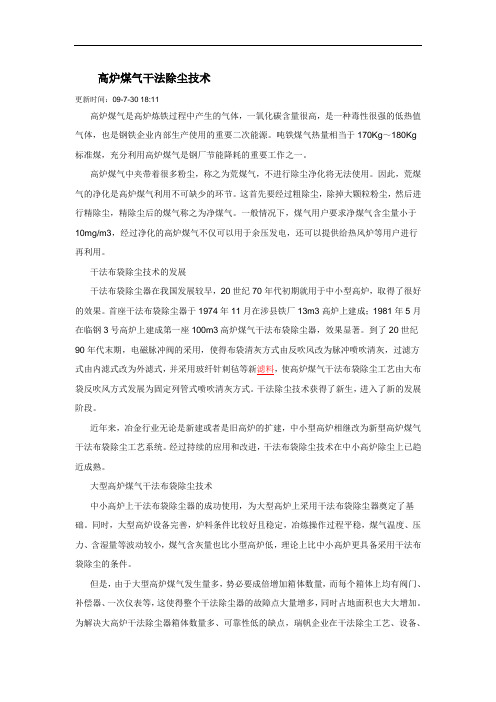
莱钢3#高炉(750 m3)全干式煤气布袋除尘已顺利运行近4年,相比较湿法除尘各项指标效果明显。表2为莱钢3#高炉煤气除尘改造前后的指标对比。
国外应用
据调查,日本在役的大型高炉中,采用了全干法除尘11座、干湿两用的有29座,湿法除尘的有18座。据了解,在日本住友金属工业公司鹿岛厂2# 4800 m3高炉、神户制钢公司加古川厂3# 4500 m3高炉、JFE千叶厂6# 5153 m3高炉均已采用干法除尘。
高炉煤气干法除尘技术优点
更新时间:09-7-31 11:35
高炉煤气干法除尘主要应用技术
更新时间:09-7-30 高炉上的高炉煤气布袋除尘的箱体的直径一般在φ2.6m~φ3.2m之间,个别高炉的箱体的直径做到φ4.0m,在大高炉煤气布袋除尘的箱体基本上采用φ5.2m直径的箱体,在唐钢3200m3高炉上采用了φ6.0m直径的箱体。大直径箱体的应用具有减少投资、节省占地、简化操作等优点,但也带来如下问题:
5)采用气体输送技术,输灰效果好,成本低,且不产生二次污染。
高炉煤气干法除尘工艺流程
更新时间:09-7-30 18:21
目前各高炉采用干式煤气布袋除尘技术的工艺主要有2种:①外滤式脉冲小布袋除尘;②干式煤气布袋除尘。干式煤气布袋除尘采用的是内滤式加压反吹大布袋除尘,该系统在运行中存在对滤袋质量要求较高(目前滤料均为进口) ,系统设备繁多、操作复杂、清灰效果差、反吹时影响高炉顶压等不利因素,后经多年技术改进,现在基本可以满足运行需要,但在全国范围使用较少。而外滤式脉冲小布袋除尘是近几年才发展起来的成熟技术,也是目前国内煤气除尘采用的主流技术,该技术操作简单、除尘效率高、运行稳定安全,图1为该系统工艺。
高炉煤气干法布袋除尘器设计规范

3.1.7除尘器压差
布袋除尘器设计压差应不大于3kPa。
3.1.8布袋除尘类型
煤气布袋除尘分脉冲式布袋除尘和反吹风式大布袋除尘。
3.1.9反吹装置
1脉冲布袋:由脉冲阀、分气包、喷吹管等组成。尺寸与精度应符合行业规定。
2反吹风大布袋:由反吹风机和反吹管路以及过滤蝶阀、反吹蝶阀组成。
3.2.8保温
1 除尘器本体应保温。灰斗部位应有蒸汽或电伴热。
2 荒煤气总管和支管内部宜喷涂不定型耐火材料;净煤气管应外保温。
3.2.9均压管
从净煤气总管引出的炉顶均压管必须设可靠的隔断装置。
3.2.10气源
脉冲喷吹和气力输灰可以采用氮气或煤气加压作为气源。
3 管路应合理设置波纹膨胀器。
4 净煤气管最低点应设排水装置。
3.2.6煤气温度控制
1 煤气温度控制主要由炉顶喷水设施完成,最大能力应将事故高温降至300~350℃以下。
2 炉顶喷水有两种方式:一种是多阀门切换的水量分级调节方式,一种是计算机控制回流阀开度的无级喷水方式。有条件时应优先选择无级喷水方式。
4.1.4按压力容器标准执行
1高炉炉顶最大压力≧0.1 MPa时,箱体按钢制压力容器标准执行
2 除尘器箱体为低压分离容器,喷吹气包为储存容器。
3 有关设计、制造(组焊)、检验及验收、运输、安装、使用均应按照钢制压力容器标准执行。
4.1.5人员资质
1容器的焊接应由持有相应类别的“锅炉压力容器焊工合格证书”的人员担任。
在实际工作温度、湿度、压力下进入除尘器的气体流量。
2.0.3工况系数 working condition coefficient
工况体积与标况体积的比值称为工况系数。
干法净化高炉煤气脉冲布袋除尘器设计
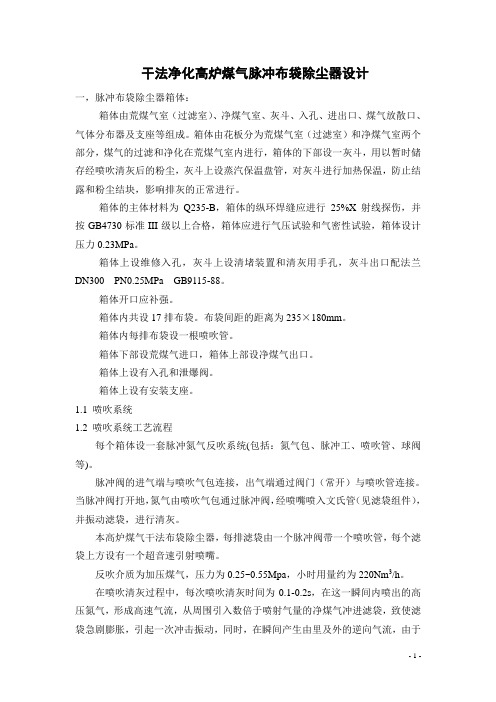
干法净化高炉煤气脉冲布袋除尘器设计一,脉冲布袋除尘器箱体:箱体由荒煤气室(过滤室)、净煤气室、灰斗、入孔、进出口、煤气放散口、气体分布器及支座等组成。
箱体由花板分为荒煤气室(过滤室)和净煤气室两个部分,煤气的过滤和净化在荒煤气室内进行,箱体的下部设一灰斗,用以暂时储存经喷吹清灰后的粉尘,灰斗上设蒸汽保温盘管,对灰斗进行加热保温,防止结露和粉尘结块,影响排灰的正常进行。
箱体的主体材料为Q235-B,箱体的纵环焊缝应进行25%X射线探伤,并按GB4730标准III级以上合格,箱体应进行气压试验和气密性试验,箱体设计压力0.23MPa。
箱体上设维修入孔,灰斗上设清堵装置和清灰用手孔,灰斗出口配法兰DN300 PN0.25MPa GB9115-88。
箱体开口应补强。
箱体内共设17排布袋。
布袋间距的距离为235×180mm。
箱体内每排布袋设一根喷吹管。
箱体下部设荒煤气进口,箱体上部设净煤气出口。
箱体上设有入孔和泄爆阀。
箱体上设有安装支座。
1.1 喷吹系统1.2 喷吹系统工艺流程每个箱体设一套脉冲氮气反吹系统(包括:氮气包、脉冲工、喷吹管、球阀等)。
脉冲阀的进气端与喷吹气包连接,出气端通过阀门(常开)与喷吹管连接。
当脉冲阀打开地,氮气由喷吹气包通过脉冲阀,经喷嘴喷入文氏管(见滤袋组件),并振动滤袋,进行清灰。
本高炉煤气干法布袋除尘器,每排滤袋由一个脉冲阀带一个喷吹管,每个滤袋上方设有一个超音速引射喷嘴。
反吹介质为加压煤气,压力为0.25~0.55Mpa,小时用量约为220Nm3/h。
在喷吹清灰过程中,每次喷吹清灰时间为0.1-0.2s,在这一瞬间内喷出的高压氮气,形成高速气流,从周围引入数倍于喷射气量的净煤气冲进滤袋,致使滤袋急剧膨胀,引起一次冲击振动,同时,在瞬间产生由里及外的逆向气流,由于冲击和逆向气流的作用,附着在除尘布袋外层的粉尘被抖落,而嵌于滤布孔隙的粉尘也被吹掉,滤袋可重新使用。
脉冲(喷吹)时间为0.1~0.2s,脉冲(喷吹)间隔10-15s,脉冲(喷吹)循环周期一般为2.5-4小时(视荒煤气含尘量而定)。
高炉煤气除尘系统
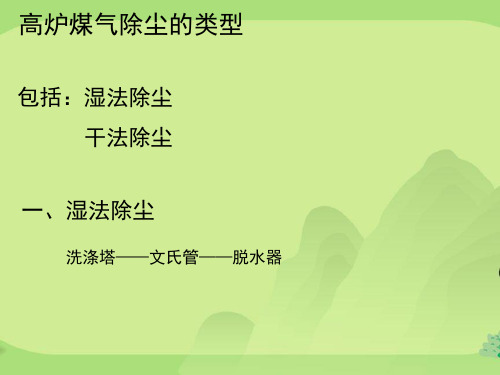
除尘设备及原理-脱水器
三、填料式脱水器
靠煤气流中的水滴与填料相撞失 去动能,从而使水滴与气流分离。
设二层填料——塑料环,每层 厚0.5m,每层塑料环层压力损失为 0.5KPa。
作为最后一级脱水设备,脱水 效率为85%。
除尘系统附属设备-煤气管道
技术部 技术部
技术部 技术部 技术部 技术部
螺旋清灰器
1-筒形给料器 2-出灰槽 3-螺旋推进器 4-喷嘴 5-水和灰泥的出口 6-排气管
除尘设备及原理-粗除尘设备
二、 旋风除尘器
1、工作原理 含尘煤气以10~20m/s的标态
流速从切线方向进入后,产生回 旋运动,灰尘颗粒在离心力作用 下,被抛向器壁积集,并向下运 动进入积灰器。
气流进入脱水器后, 由于气流流速和方向的 突然改变,气流中吸附 有尘泥的水滴在重力和 惯性力作用下沉降,与 气流分离。
脱水器内流速4~6m/s; 进口流速15~20m/s。
2、特点
结构简单,不易堵塞,但脱泥、脱水的效率不高。 安装在文氏管后。
除尘设备及原理-脱水器
二、挡板式脱水器
煤气从切线方向进入后, 经曲折挡板回路,尘泥在离 心力和重力作用下与挡板、 器壁接触被吸附在挡板和器 壁上、积聚并向下流动而被 除去。
谢谢
之间的转换。
(2)1个400mm自动控制蝶式调节阀: 用于细调 ,维持稳定的炉顶压力;
(3)1个250mm常通管:起安全保护作用
除尘系统附属设备-阀
北京天山新材料技术有限责任公司
技术部
高炉休风时关闭,阀盘落下,将高炉与煤气除尘系统隔开。
4、结构 3、溢流文氏管主要参数
高炉煤气除尘系统设计
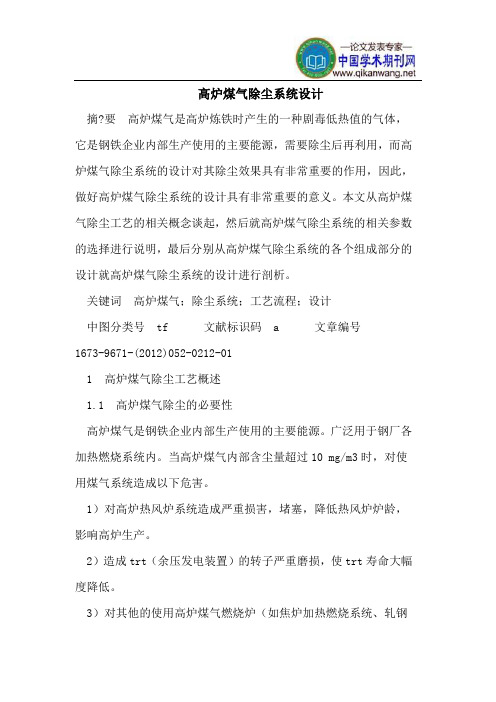
高炉煤气除尘系统设计摘?要高炉煤气是高炉炼铁时产生的一种剧毒低热值的气体,它是钢铁企业内部生产使用的主要能源,需要除尘后再利用,而高炉煤气除尘系统的设计对其除尘效果具有非常重要的作用,因此,做好高炉煤气除尘系统的设计具有非常重要的意义。
本文从高炉煤气除尘工艺的相关概念谈起,然后就高炉煤气除尘系统的相关参数的选择进行说明,最后分别从高炉煤气除尘系统的各个组成部分的设计就高炉煤气除尘系统的设计进行剖析。
关键词高炉煤气;除尘系统;工艺流程;设计中图分类号 tf 文献标识码 a 文章编号1673-9671-(2012)052-0212-011 高炉煤气除尘工艺概述1.1 高炉煤气除尘的必要性高炉煤气是钢铁企业内部生产使用的主要能源。
广泛用于钢厂各加热燃烧系统内。
当高炉煤气内部含尘量超过10 mg/m3时,对使用煤气系统造成以下危害。
1)对高炉热风炉系统造成严重损害,堵塞,降低热风炉炉龄,影响高炉生产。
2)造成trt(余压发电装置)的转子严重磨损,使trt寿命大幅度降低。
3)对其他的使用高炉煤气燃烧炉(如焦炉加热燃烧系统、轧钢加热炉)造成堵塞,甚至损坏。
1.2 高炉煤气除尘工艺流程说明高炉煤气经重力除尘后,由荒煤气主管分配到除尘系统的各箱体中,并进入荒煤气室,颗粒较大的粉尘由于重力作用自然沉降而进入灰斗,颗粒较小的粉尘随煤气上升。
经过滤袋时,粉尘被阻留在滤袋的外表面,煤气得到净化。
净化后的煤气进入净煤气室,由净煤气总管输入煤气管网。
当荒煤气温度大于260℃或低于100℃时,系统将自动关闭所有箱体进口蝶阀,同时打开荒煤气放散阀组,进行荒煤气放散,该过程为无扰切换,并可以有效控制高炉炉顶压力。
随着过滤过程的不断进行,滤袋上的粉尘越积越多,过滤阻力不断增大。
当阻力增大到一定值时,电磁脉冲阀启动,进行脉冲喷吹清灰,喷吹气采用氮气,清理的灰尘落入灰斗然后由高压净煤气(或氮气)将灰尘输送至大灰仓,再由汽车运出厂区。
2 高炉煤气除尘系统相关参数的选择2.1 气量换算q=q标*(273+t)/[273*(1+p)]。
高炉煤气干法布袋除尘及气力输灰系统设计
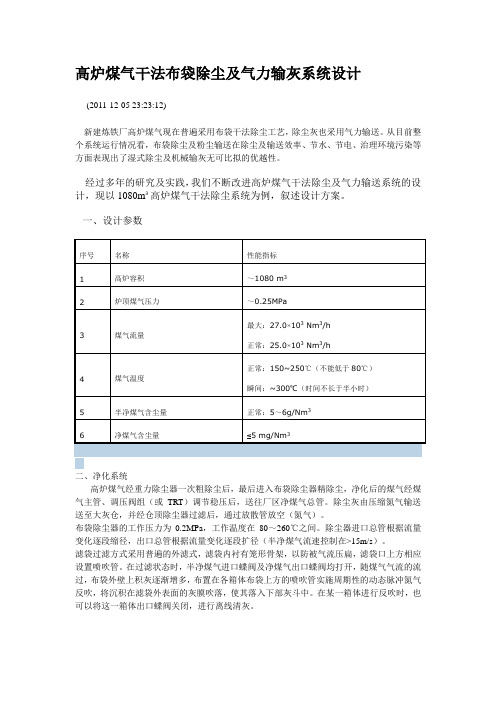
高炉煤气干法布袋除尘及气力输灰系统设计(2011-12-05 23:23:12)新建炼铁厂高炉煤气现在普遍采用布袋干法除尘工艺,除尘灰也采用气力输送。
从目前整个系统运行情况看,布袋除尘及粉尘输送在除尘及输送效率、节水、节电、治理环境污染等方面表现出了湿式除尘及机械输灰无可比拟的优越性。
经过多年的研究及实践,我们不断改进高炉煤气干法除尘及气力输送系统的设计,现以1080m³高炉煤气干法除尘系统为例,叙述设计方案。
一、设计参数序号名称性能指标1高炉容积~1080 m32炉顶煤气压力~0.25MPa最大:27.0×103 Nm3/h3煤气流量正常:25.0×103 Nm3/h正常:150~250℃(不能低于80℃)4煤气温度瞬间:~300℃(时间不长于半小时)5半净煤气含尘量正常:5~6g/Nm36净煤气含尘量≤5 mg/Nm3二、净化系统高炉煤气经重力除尘器一次粗除尘后,最后进入布袋除尘器精除尘,净化后的煤气经煤气主管、调压阀组(或TRT)调节稳压后,送往厂区净煤气总管。
除尘灰由压缩氮气输送送至大灰仓,并经仓顶除尘器过滤后,通过放散管放空(氮气)。
布袋除尘器的工作压力为0.2MPa,工作温度在80~260℃之间。
除尘器进口总管根据流量变化逐段缩径,出口总管根据流量变化逐段扩径(半净煤气流速控制在>15m/s)。
滤袋过滤方式采用普遍的外滤式,滤袋内衬有笼形骨架,以防被气流压扁,滤袋口上方相应设置喷吹管。
在过滤状态时,半净煤气进口蝶阀及净煤气出口蝶阀均打开,随煤气气流的流过,布袋外壁上积灰逐渐增多,布置在各箱体布袋上方的喷吹管实施周期性的动态脉冲氮气反吹,将沉积在滤袋外表面的灰膜吹落,使其落入下部灰斗中。
在某一箱体进行反吹时,也可以将这一箱体出口蝶阀关闭,进行离线清灰。
反吹方式采用脉冲氮气反吹,可在线反吹,也可离线反吹,也可实现定时或定压差反吹操作制度,清除布袋外壁的积灰。
毕业设计—高炉煤气除尘净化

第一章概论 (4)1.1 问题的提出 (4)1.2 课题来源、背景及研究对象 (5)1.2.1 课题来源 (5)1.2.2 昆钢6#高炉煤气净化和应用现状 (5)1.2.3 研究对象 (5)1.3 项目意义 (5)第二章设计依据 (6)2.1煤气除尘技术 (6)2.1.1 高炉煤气粗除尘 (6)2.1.2 高炉煤气精除尘 (6)2.1.2.1 高炉煤气湿法除尘 (6)2.1.2.2 高炉煤气干法除尘 (7)2.1.2.3 高炉煤气精除尘工艺比选[1,6] (8)2.2 干法布袋除尘技术 (9)2.2.1 干法布袋除尘技术进展 (9)2.2.1.1国外运用进展 (9)2.2.1.2 国内运用进展 (10)2.2.2 大型干法高炉煤气除尘技术总结 (11)2.2.2.1 工艺线路 (11)2.2.2.2 控温方式 (12)2.2.2.3 布袋除尘灰的输送 (13)2.3 各类除尘器简介 (13)2.3.1 重力除尘器 (13)2.3.1.1 简介 (13)2.3.1.2 重力除尘的分类与形式 (14)2.3.2 旋风除尘器 (14)2.3.2.1 简介 (14)2.3.2.2 旋风除尘器工作机理 (14)2.3.2.3 旋风除尘器的类型及特点 (15)2.3.2.4 旋风除尘器性能 (17)2.3.3 布袋除尘器 (18)2.3.3.1 概述 (18)2.3.3.2 除尘机理 (18)2.3.3.3 布袋除尘器的分类 (19)2.3.3.4 布袋除尘器的结构形式 (19)2.3.3.5 布袋除尘器的性能 (20)2.3.3.6 布袋除尘器的设计及选型 (21)2.3.3.7 设计进程中采取的计谋[17] (21)2.4 高炉煤气脱硫处置 (22)2.4.1 概述 (22)2.4.2 湿法脱硫技术 (22)2.4.2.1 化学吸收法: (22)2.4.2.2 物理吸收法 (23)2.4.2.3 物理化学吸收法 (23)2.4.2.4 湿式氧化法 (23)2.4.3 干法脱硫 (24)2.4.3.1 膜分离法 (24)2.4.3.2 分子筛法 (24)2.4.2.3 其他方式 (24)2.4.4 微生物法 (25)2.4.5 臭氧氧化法 (25)2.4.6 电化学法 (25)第三章工艺设计计算与选型 (25)3.1重力除尘器设计 (26)3.1.1重力除尘器及粗煤气管道 (26)3.1.1.1粗煤气管道及重力除尘器结构与布置 (26)3.1.1.2 粗煤气管道的布置及要紧尺寸的确信 (27)3.1.1.3重力除尘器的布置及要紧尺寸的确信 (27)3.1.2 粗煤气管道及除尘器设计计算 (27)3.1.2.1粗煤气管道设计计算[15] (28)3.1.2.2重力除尘器尺寸设计计算 (30)3.1.3重力除尘器及粗煤气管道结构与内衬 (34)3.2旋风除尘器设计 (34)3.2.1 旋风除尘器的选择 (35)3.2.2 技术计算 (35)3.2.2.1 除尘器处置风量(工况)计算 (35)3.2.2.2 除尘器结构尺寸计算 (36)3.2.2.3 除尘器压降计算 (38)3.3 布袋除尘器 (39)3.3.1 除尘技术参数 (39)3.3.2 确信布袋除尘器形式 (40)3.3.3 除尘工艺计算 (40)3.3.3.1 除尘器结构尺寸计算 (40)3.3.3.2 除尘器平面布置 (42)3.3.4 反吹清灰工艺设计 (43)3.3.4.1 清灰方式的选择 (43)3.3.4.2 压力损失 (44)3.3.4.3 喷吹气体及参数的选择 (44)3.3.5除尘效率计算 (45)3.3.6 附属设备:储气罐设计 (45)3.3.6.1设计参数 (46)3.3.6.2 容器形式的选择 (46)3.3.6.3 主体几何尺寸的确信 (47)3.3.6.4 水压实验与强度校核 (49)3.3.6.5 支座选型 (49)3.3.6.6储罐尺寸参数汇总 (50)3.3.7 除尘自动操纵系统设计 (50)3.3.7.1 煤气温度操纵系统 (50)3.3.7.2 压差电控仪 (51)3.3.7.3 脉冲操纵仪 (51)3.3.7.4 灰位自动操纵系统 (52)3.3.7.5 箱体自动检漏系统 (52)3.4 高炉煤气脱硫设计 (53)第四章煤气除尘净化经济技术分析 (53)4.1 能源评判及节能方法 (53)4.1.1 能源及能源评判 (53)4.1.2 工序能耗评判 (54)4.1.3 节能方法 (54)4.2 应用成效 (54)4.2.1 节能环保成效好 (54)4.2.2 净煤气质量好 (54)4.3 成效分析 (55)4.3.1 经济效益 (55)4.3.2 环境效益 (55)第五章结论与展望 (56)第六章感想与体会 (57)致谢 (58)参考文献: (59)第一章概论1.1 问题的提出能源一样分为两大类:即一次能源和二次能源。
高炉煤气除尘脱硫脱氯净化系统设计

(论文)摘要高炉煤气是钢铁冶炼的副产物之一。
高炉煤气中含有的CO、HCl、H2S、COS等有毒气体以及大量粉尘,对大气都造成了不可忽视的污染,所以对于高炉煤气的治理刻不容缓。
但在煤气中还存在着可利用的高温高压以及可回收二次利用的有用气体,所以将其除尘脱硫脱氯过程中,对煤气进行进一步利用,将给整个工厂带来巨大的经济效益。
本设计的主要内容是针对标准状况下40万m³/h的高炉煤气流量,对其进行除尘脱硫脱氯的工艺设计,使其满足排放要求。
目前针对高炉煤气脱硫的方法有加氢转化法、氧化法、吸附法和水解法等。
催化水解法是目前应用最为广泛的方法。
目前,国内外关于煤气除尘工艺已经有许多种并都较为成熟。
因此本设计的方案是旋风除尘器对高炉煤气进行粗除尘,再经过布袋除尘器进行进一步除尘。
除尘之后,有机硫转化工艺采用高效水解转化工艺,主要是将有机硫催化水解为硫化氢,然后采用喷淋吸收的方法将硫化氢和氯化物净化去除。
本设计主要针对某1500m³高炉煤气进行除尘脱硫脱氯净化系统的设计,针对该设计主要是在TRT余压发电装置前设置预处理塔和催化水解塔,在TRT余压发电装置前后设置喷淋吸收塔,最终实现该高炉煤气的脱硫脱氯技术要求。
本设计也将估算整个工艺流程所需要的建设成本。
关键词:高炉煤气,湿法脱硫,喷淋水解,旋风除尘,布袋除尘- I -(论文)Design of dedusting desulfurization and dichlorinationpurification systemAbstractBlast furnace gas is one of the main by-products in the process of ironmaking. The CO, HCl, H2S, COS and other toxic gases in blast furnace gas as well as a large amount of dust have caused non-negligible pollution to the atmosphere, so it is urgent to control the blast furnace gas. However, there are still usable high temperature and high-pressure gas in the gas as well as useful gas that can be recycled for secondary use. Therefore, further utilization of the gas in the process of dedusting, desulfurization and dichlorination will bring huge economic benefits to the whole plant.The main content of this design is to design the process of dedusting, desulfurization and dichlorination for the blast furnace gas flow of 400,000 m /h under standard conditions, so as to make it meet the discharge requirements. At present, the main methods of removing organic sulfur from blast furnace gas include hydrogenation and conversion, oxidation, adsorption and hydrolysis. Catalytic hydrolysis is one of the most important methods to remove organic sulfur. At present, there are many kinds of gas dust removal technology at home and abroad. Therefore, the scheme of this design is the cyclone dust collector to the blast furnace gas for coarse dust, and then through the bag filter for further dust. After dust removal, the organic sulfur conversion process adopts efficient hydrolysis conversion process, which is mainly to catalyze the hydrolysis of organic sulfur into hydrogen sulfide, and then to purify hydrogen sulfide and chloride by spray absorption.This design is mainly aimed at the design of a purification system for dedusting, desulfurization and dichlorination of a certain 1500m blast furnace gas. For this design, the pretreatment tower and catalytic hydrolysis tower are set before the TRT residual pressure power generation unit, and the spray absorption tower is set before and after the TRT residual pressure power generation unit, so as to realize the technical requirements of desulfurization and dichlorination of the blast furnace gas. This design also estimates the construction cost required by the whole process.- III -(论文)Key Words:blast furnace gas,Wet desulfurization,cyclone dust removal,bag dust removal,spray hydrolysis- IV -(论文)目录摘要 (I)Abstract ........................................................................................................................ I II1 引言 (1)2 研究背景 (2)2.1 课题背景 (2)2.2 研究意义 (2)2.3 高炉煤气常见除尘工艺 (3)2.3.1 重力除尘技术 (3)2.3.2 旋风除尘技术 (3)2.3.3 离心湿式除尘技术 (4)2.3.4 布袋除尘技术 (4)2.3.5 电除尘技术 (4)2.4 脱氯工艺综述 (5)2.4.1 高炉煤气中氯元素的主要来源 (5)2.4.2 高炉煤气中HCl的危害 (5)2.4.3 高炉煤气中HCl脱除办法 (6)2.5 脱硫工艺综述 (6)2.5.1 加氢转化法 (7)2.5.2 氧化法 (7)2.5.3 催化水解法 (7)3 工程设计 (8)3.1 设计内容 (8)3.2 设计方法 (10)4 工艺设计及其计算 (12)4.1 旋风除尘器设计 (12)4.1.1 确定旋风除尘器处理气体量 (13)4.1.2 旋风除尘器结构尺寸计算 (13)4.1.3 除尘器压降计算 (15)4.1.4 除尘率与除尘量计算 (15)4.2 布袋除尘器设计 (18)4.2.1 确定布袋除尘器处理气体量 (18)4.2.2 除尘器尺寸结构计算 (18)- V -(论文)4.2.3 压力损失 (20)4.2.4 除尘效率 (21)4.2.5 布袋除尘器的平面布置 (22)4.3 水解塔设计计算 (23)4.3.1 物料平衡计算 (23)4.3.2 催化剂的设计 (24)4.3.3 水解塔结构设计 (26)4.4 喷淋塔设计计算 (27)4.4.1 通过喷淋塔的流量计算 (28)4.4.2 喷淋塔尺寸计算 (28)4.4.3 喷淋塔喷淋系统设计 (28)4.4.4 喷淋系统选型设计 (29)4.4.5 碱液循环池设计 (30)4.4.6 喷淋塔壁厚设计 (30)5 经济分析 (31)5.1 经济分析的目的和意义 (31)5.2 建设成本估算 (31)5.2.1 旋风除尘器设备成本 (31)5.2.2 布袋除尘器设备成本 (32)5.2.3 水解塔和喷淋塔设备成本 (32)5.2.4 其他费用 (33)6 结论 (34)参考文献 (35)附录A (37)在学取得成果 (39)致谢 (41)- VI -(论文) - VII -(论文)1引言近年来,随着我国工业技术的不断创新进步,构建循环经济型产业体系,加快环保产业的发展被成为国家发展的新方向。
高炉煤气干法除尘系统介绍

上海瑞帆环境工程有限公司
高炉煤气干法布袋除尘器应用技术 主要内容
高炉煤气特性
高炉煤气净化发展过程
干法布袋除尘器系统介绍
瑞帆企业
高炉煤气干法布袋除尘器应用技术
高炉煤气的特性
高炉煤气是高炉炼铁时产生的气体,是一种剧毒低热值的气体,发热 值为2800~3500KJ/m3,是钢铁企业内部生产使用的主要能源。需要除 尘后再利用。 高炉气体相比其他气体具有以下特性: ①温度较高 正常:150℃ (90~250℃ ), 短时高温320℃ , 事故时500℃~700℃ ②压力高 1000m3以下压力~0.15MPa 1000~2000m3压力为0.15~0.22MPa 2000m3以上压力为0.2~0.28MPa 处理煤气的设备满足压力容器的条件,属于压力容器的范围GB150。 除尘器是一个个独立的圆筒状,而不是环境除尘器的方形。 ③剧毒 含有约22%-26%的CO
除尘器箱体:
1、除尘器箱体按照GB150《钢制压力容器》进行设计。 箱体为园形筒状结构,直径为φ5232mm,设计压力为 0.3MPa,箱体材料为Q235-B 。壁厚16mm 。 2、在出气支管上设有一套安全放散装置,在检修时打 开,用来置换出煤气。 3、箱体进气、出气支管上均安装有大拉杆横向波纹补 偿器、气动三偏心蝶阀、带人孔短接、电动盲板阀。 4、箱体上设置4个人孔,方便检修。 5、箱体上设有8个支座,支撑箱体。 6、箱体上设吹扫系统一套,分别设在进、出气口、灰 斗底部和格子板上的人孔上,起清除局部积灰和置换 作用。 7、箱体上设有人工灰尘检侧口一个,方便取样化验。 8、灰斗锥度41度,远小于灰尘安息角,方便卸灰。并 设有仓壁震动器、氮气炮和氮气反送等装置 ,保证卸 灰通畅。
高炉煤气干法布袋除尘设计规范
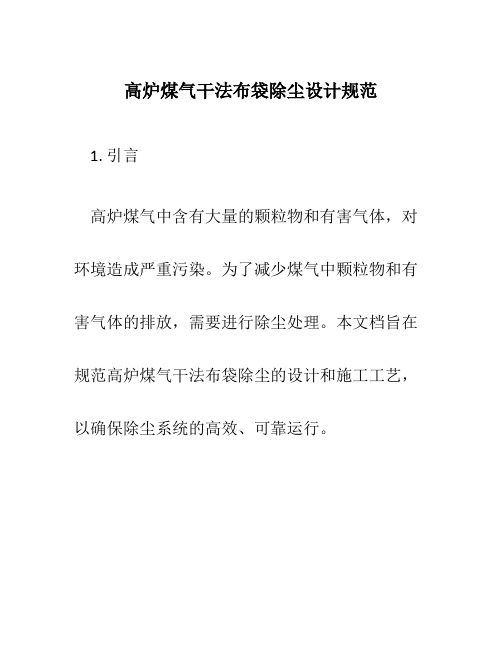
高炉煤气干法布袋除尘设计规范1. 引言高炉煤气中含有大量的颗粒物和有害气体,对环境造成严重污染。
为了减少煤气中颗粒物和有害气体的排放,需要进行除尘处理。
本文档旨在规范高炉煤气干法布袋除尘的设计和施工工艺,以确保除尘系统的高效、可靠运行。
2. 设计要求2.1. 颗粒物排放浓度根据国家标准,高炉煤气的颗粒物排放浓度应不超过X mg/m³。
除尘系统的设计应能够实现这一要求,并在正常运行条件下保持稳定。
2.2. 除尘效率除尘系统的设计应能够实现高炉煤气中颗粒物的有效去除,使排放的煤气中颗粒物浓度降至符合国家标准的要求。
2.3. 运行稳定性除尘系统应具备良好的运行稳定性,能够适应高炉煤气流量和成分的变化,并保持较高的除尘效率。
2.4. 设备可靠性除尘系统的设计应考虑设备的可靠性,确保设备能够长时间稳定运行,减少故障和维修频率。
3. 设计原则3.1. 工艺选择高炉煤气干法布袋除尘可采用反吹式除尘器或脉冲喷吹除尘器。
选择合适的除尘工艺应考虑煤气流量、颗粒物特性、设备可靠性和维护费用等因素。
3.2. 布袋材料选择布袋材料应能够耐受高温和化学腐蚀,并具备较高的除尘效率和阻力稳定性。
常用的布袋材料有聚酯纤维、聚酰胺纤维、玻璃纤维等,根据煤气成分和温度选择合适的材料。
3.3. 布袋排列方式布袋的排列方式应能够充分利用布袋的过滤面积,提高除尘效率。
常见的布袋排列方式有单排式、双排式和多排式,具体选择要根据煤气流量和颗粒物浓度等因素进行合理设计。
3.4. 除尘系统布局除尘系统的布局应符合工艺流程,确保煤气能够顺利进入除尘设备,并经过有效的除尘处理。
除尘器的进出口应设置合适的导流装置,减少煤气中的液相和颗粒物。
3.5. 除尘器清灰系统设计清灰系统的设计应能够及时有效地清除布袋上的积灰,以保证布袋的清洁和通气性。
清灰方式可采用反吹、脉冲喷吹或机械振动等方法,要根据实际情况选择合适的清灰方式。
4. 施工要求4.1. 设备材质和焊接工艺除尘设备的主要材质应符合国家标准,具备良好的耐腐蚀性和机械强度。
- 1、下载文档前请自行甄别文档内容的完整性,平台不提供额外的编辑、内容补充、找答案等附加服务。
- 2、"仅部分预览"的文档,不可在线预览部分如存在完整性等问题,可反馈申请退款(可完整预览的文档不适用该条件!)。
- 3、如文档侵犯您的权益,请联系客服反馈,我们会尽快为您处理(人工客服工作时间:9:00-18:30)。
江苏沙钢高炉煤气干法除尘器及除尘工艺系统设计方案江苏沙钢380m 3高炉煤气干法除尘器及除尘工艺系统设计方案作者:耿存友前言高炉煤气净化分为湿法除尘和干法除尘俩类,根据我国的能源和环保政策,干法除尘属于环保节能项目,位于国家钢铁行业当前首要推广的“三干壹电”(高炉煤气干法除尘、转炉煤气干法除尘、干熄焦和高炉煤气余压发电)之首。
干法布袋除尘代替湿法除尘将是壹大趋势。
因此,我们在引进和吸收国内外各家先进技术的基础上,经过多年大量分析和研究设计出壹套高效经济、安全可靠、实用方便的高炉煤气干法布袋除尘工艺系统及高炉煤气干法布袋除尘器,且于2003年在江苏沙钢三座380m 3高炉上得到了应用和验证,目前,整个系统运行状况良好,操作简单,维护方便。
以下着重介绍此高炉煤气除尘器及除尘工艺系统设计方案。
1。
工艺系统组成及工作原理1.1 工艺系统组成及工艺流程(见图壹)江苏沙钢三座380m 3高炉高炉煤气干法布袋除尘工艺系统组成分为:高炉煤气干法布 袋除尘系统和高炉煤气干法布袋除尘系统支架平台(见图二,此图为其中俩座高炉煤气除尘系统平台第三座平台为后期设计且列连在这个平台之上)俩部份。
江苏沙钢380m3高炉煤气除尘工艺系统图二1.1.1高炉煤气干法布袋除尘系统主要由:荒煤气进气总干管路系统(主要由总干管和膨胀节组成)、九个进气支管路系统(主要由进气支管、液动式盲板阀、气动式密封蝶阀等组成)、九个筒式除尘器箱体(主要由净煤气室、荒煤气室、本体锥形灰斗、中间卸灰球阀、中间灰斗、卸灰球阀、星型卸料器、布袋脉冲喷吹装置、灰斗脉冲清堵装置、安全防爆装置、人孔检修装置等组成),九个出气支管路系统(主要由出气支管、液动式盲板阀、气动式密封蝶阀等组成)、净煤气出气总干管路系统(主要由总干管和膨胀节组成)、输灰系统(由链运机组成)、安全放散管路系统、蒸汽旁管加热及保温系统、氮气管路系统、液压管网系统(由液压站、管网及各式阀组成,为各液动阀门提供动力、各液脂润滑点提供润滑脂)、料位监测系统、温度监测系统、差压监测系统、出气总干管煤气流量、含量监测系统、环境煤气浓度监测报警系统、电气、仪表及自动化控制系统.1.1.2钢结构支撑平台主要由:基础立柱及钢梯、承重平台和中间灰斗等部件检修平台、安全通道、顶部检修平台等组成。
1.2工艺系统工作原理高炉煤气经重力除尘后,由荒煤气进气总干管路分配到各进气支管经液动式盲板阀、气动式密封蝶阀进入布袋除尘器各箱体锥形灰斗中,且进入荒煤气室,颗粒较大的粉尘由于重力和速度在特殊结构的进气管口的作用下自然沉降而进入灰斗,颗粒较小的粉尘随煤气上升。
经过滤袋时,粉尘被阻留在滤袋的外表面,煤气得到净化。
净化后的煤气进入净煤气室,由净煤气出气总干管路输入煤气管网。
当荒煤气温度过高或过低(系统温度监测系统控制)时,此时系统将自动关闭荒煤气进气总管上的气动式密封蝶阀,同时打开荒煤气进气总干管路上放散阀组,进行荒煤气放散,荒煤气放散阀组亦可有效控制高炉炉顶压力。
随着过滤过程的不断进行,滤袋上的粉尘越积越多,过滤阻力不断增大(系统压力差压监测系统控制)。
当阻力增大(或时间)到壹定值时,电磁脉冲阀启动,进行脉冲喷吹清灰,脉冲清灰的喷吹气体采用氮气(安全),清理的灰尘落入本体锥形灰斗。
当本体锥灰斗中的灰尘累积到壹定量(由料位计控制)时,中间卸灰球阀自动启动,灰尘经中间卸灰球阀卸入中间灰斗,大部份的高温灰尘在中间灰中冷却降温,但中间灰斗的灰尘达到壹定的高度(由料位计控制)时,下部的卸灰球阀、星型卸料器自动启动,灰尘经卸料器卸入输灰链运机再将灰尘输送至灰仓,由汽车运出厂区。
但除尘器滤袋破损设系统净煤气出口管道上装有煤气含尘量分析仪,可在线连续检测净煤气含尘量,同时设在各除尘器箱体单元上的差压变送会发差压变化信号能及时准确的发现破损布袋的箱体,维修人可自行关闭对应该除尘器箱体单元进、出气支管上的液动式盲板阀和气动式密封蝶阀,打开该除尘器箱体单元各放散阀,进行煤气入散,然后,打开净煤气室上方的椭圆封头盖更换滤袋。
,1.3工艺系统结构特点1)每座380m3高炉煤气干法布袋除尘装置是由九个除尘器箱体单元且联组合而成,三座380m3高炉煤气干法布袋除尘装置安置在壹座整体钢结构支架平台上,平台结构紧凑、布局合理、钢耗少经济,既节省了用地面积和空间又稳定、安全、可靠。
2)除尘器箱体采用单元体结构,九个除尘器箱体单元体用进、出煤气总干管且联组成壹座高炉的除尘器系统,荒煤气总管设总进气管电动切换蝶阀,荒、净煤气总管上各设总检修电动盲板阀。
系统重要阀门壹律采用冶金行业耐高温、耐高压、防泄漏、防爆型阀门,电器元器件均选用防爆型的。
为了防止热变形甚至涨裂,在荒、净煤气总管和袋式除尘器之间各设置1个波纹管补偿器,管网布置合理大大的减少了占地面积、系统运行阻力,节约了运行成本,提高了效益。
3)放散及安全防爆系统设计布置合理,实际使用时,但系统内部温度超出设计的范围时放散系统及时放散;系统内部压力超出设计的安全范围时,安全防爆阀便能自动爆破,有效的保护了设备和人身财产安全。
4)净煤气室采用分体法兰连接,检修安全方便。
(注意:在单元检修或更换滤袋或袋笼时,先必须关闭该单元进、出气支管上的检修盲板阀,打开放散阀将净煤气室中的煤气放净,必要时通入氮气驱赶煤气,再拧开法兰螺钉拆除净煤气室上部的椭球形盖,或打开各检修门孔晾尽煤气,检修人员方可进入,确保人身安全高度的净煤气室更换滤袋或袋笼。
)5)滤袋采用FMS9806(抗结露、耐高温、耐酸腐蚀氟美斯)滤袋,使用寿命长。
6)采用氮气脉冲喷吹清堵技术,可在不停机的状况下清除中间球阀或下部球阀及星型卸料器的堵塞。
7)净煤气出口管道上装有煤气含尘量分析仪,可在线连续检测净煤气含尘量,同时设在各除尘器箱体单元上的差压变送会发差压变化信号能及时准确的发现破损布袋的箱体。
8)采用环境煤气浓度监测报警系统,实时监控工作场所的煤气浓度,保证了人身安全。
9)钢结构平台设计了安全通道,安全更有保障。
10)除尘器单体上增加了蒸汽加热旁管和整体保温,确保系统正常运行,及使在不常的低温状态下也能启动蒸汽供给加热除尘器箱体内的气体,防止滤袋结露。
11)DCS控制系统性能优越,动态模拟监控,直观方便。
2.高炉煤气干法除尘器的设计简介2.1高炉煤气干法除尘器选型用于高炉煤气净化的袋式除尘器,是高炉煤气干法除尘的核心,它的设计必须能同步解决防燃、防爆、防泄漏、防高温烧袋、耐高压、耐酸腐蚀、抗结露糊袋、粉尘收集和输送不能扬尘等诸多问题,同时要求具有良好的运行稳定性和可靠性。
我们根据多年治理粉尘除尘系统的设计经验,结合这三座高的自身工艺特点,选用LCDM-456长袋低压脉冲袋式除尘器1套,每座高炉设计成9个独立单元,额定处理能力196990(21888x9)m3/h,最大处理能力246240m3/h。
这样的设计充分理由是:壹是除尘系统随高炉正常运转率要达到100%。
也就是说要确保高炉生产的连续性,袋式除尘器就必须有效运行,在线检修不停机,且确保煤气通过能力和除尘效率。
二是提高单炉产量和冶炼利用系数同样是我们的首要目标,即使冶炼强度增加使荒煤气流量再增加25%,这套除尘系统仍然能够满足需要;三是提倡单元无故障时全系统在线运行,各单元负荷轻,煤气通过快,系统总运行阻力低,不易结露;同时有利于提高产铁量和提高除尘效率,对热风炉等下游燃气设备的良性运行也有好处。
2.1.2除尘器主要参数LCDM-456脉冲袋式除尘器1台(9个单元)筒体规格:Φ3424×9500×12(直径×筒高×壁厚)单元数:9个独立圆柱形筒体滤袋材质:FMS9806(抗结露、耐高温、耐酸腐蚀氟美斯)滤袋规格:Φ130×6000(直径×长度)滤袋条数:9×186条=1674条(单元数×每单元条数)过滤面积:4104.0m2(每单元456m2)过滤风速:≤0.8m/min(最高允许≤1m/min)处理含尘煤气能力:额定196990m3/h,最大246240m3/h(工况)设备总阻力:2500-5000Pa允许入口含尘浓度:≤200g/m3设计出口浓度:≤30mg/Nm3允许入口温度:100-250℃喷吹压力:0.3-0.4MPa2.1.3除尘器结构特点LCDM-456脉冲袋式除尘器其主要技术特点是按防燃、防爆、防泄漏、耐高温、耐高压、耐酸腐蚀、抗结露。
各单元既可联动,又可完全独立地且联外挂于荒(含尘)、净(无尘)煤气总管之间等要求设计的,特别适应高含尘浓度、高温含湿煤气除尘。
其结构分为:⑴除尘器单元上部筒体:即净气室,包括上筒体、椭球头盖、防爆阀、高强度花板、净化检修门、脉冲喷吹组件、单元出气支管、电动清灰切换蝶阀、检修放散阀等。
根据不同处理流量和要求,袋式除尘系统外挂若干个不同规格的单元。
⑵除尘器单元中部筒体:即过滤室,又称袋室,包括滤袋、袋笼及密封组件、袋室检修门、含尘煤气进气管、进气管电动检修盲板阀等。
因煤气温度虽高于水露点,但经常低于酸露点,为了预防结露和腐蚀,所有除尘器外表面必须保温。
重⑶除尘器单元下部锥斗及排灰结构:包括积灰锥斗、锥斗排灰球阀、锥斗检修孔、脉冲清灰装置;中间灰斗、中间灰斗排灰球阀、脉冲清灰装置等。
重要阀门壹律采用冶金行业耐高温、耐高压、防泄漏、防爆型阀门,电器元器件均选用防爆型的。
单元下部锥斗、中间灰斗仍安装了粉尘射线料位仪、排灰振打器等,蒸汽加热管等,以防灰尘板结和堵灰。
中间灰斗排出的干态粉尘可用加湿卸灰机输送到指定地点。
⑷电控:采用PLC进行清、排灰自动控制,超温、超压、堵灰、滤袋破损等自动报警;可显示各单元工作状态、压力和流量等参数;可预留控制接口和全厂总监控电脑系统联机;亦可根据用户要求选用DCS等其它控制方式。
⑸防腐:煤气的酸腐蚀性是壹个不可忽视的问题。
所有筒体和管道和煤气接触的内壁均按《化工设备防腐规程》用耐高温、抗酸特种铝粉漆喷涂3次,所有不和煤气接触的外壁喷涂1-2次。
确保袋式除尘器主体寿命15年之上。
⑹压缩氮气气源:取用氮气为脉冲清灰、脉冲清堵、各气动阀门提供气源,且设置储气罐。
3结论我们在江苏沙钢三座380m3高炉煤气干法除尘系统上采用的是大直径除尘器箱体、氮气脉冲技术、合理的滤料选择,仍应用荒煤气放散阀组、现场煤气浓度监测报警、进气口灭火阻尼结构的设计使进入袋室的高温大颗粒预先沉降等技术,延长了布袋除尘中设备及滤袋的使用寿命,有效地保证了高炉的正常生产。
高炉煤气干法除尘节约用水量,提高了高炉煤气余压发电设施发电量,减少了环境污染,降低了高炉的工序能耗,给企业创造了可观的经济效益和社会效益。
投稿人:耿存友Email:gcyanhui@二〇壹〇年十二月八日。