注塑工艺及缺陷案例全解
注塑成型常见的缺陷和解决方案

注塑成型常见的缺陷和解决方案
与设计有关的原因与改良措施 1、模温不稳定:提供冷却/加热均衡的模具
-
THANKS
欢迎领导来夸我
70%~80%。如在料头附近 发现注射不满,可以解 释为:流体前锋在这
物理原因:熔料的注射 压力和/或注射速度太低, 熔料在射向流长最末
候。实际上,当需要高 注射压力时,保压也应 按比例提高:正常时, 保
些点被阻挡,较厚的地 方先被充满。如此,在 模腔几乎被充满之后, 在
注塑成型常见的缺陷和解决方案
缩水。这是因为内部 仍有热量,它会穿过 外层并对外层产生加 热作用
模壁的地方先冻结, 在制品中心形成内应 力。如果应力太高, 就会导致
到模件内,在模壁和 已凝固的制品外层之 间就会形成沉降。这 些沉降通
制品内产生的拉伸应 力会使热的外层向里 沉降,在此过程中形 成收缩
注塑成型常见的缺陷和解决方案
与加工参数有关的原因与改良措施 1、保压太低:增加保压 2、保压时间太短:延长保压时间 3、模壁温度太高:降低模壁温度 4、熔料温度太高:降低熔料温度,降低料筒温度 与设计有关的原因与改良措施 1、料头横截面太小:增加料头横截面 2、料头太长:缩短料头 3、喷嘴孔太小:增加喷嘴孔径
经典注塑基础和产品缺陷及应对方法(PPT62页)

欠注
欠注是指模具型腔不能被完全填充满的一种现象。
欠注形成原因: 任何阻止聚合物熔体流动或使聚合物注塑量不足的因素均可能导致欠注 现象。这些因素包括:
• 熔体温度、模具温度或注塑压力和速度过低 • 原料塑化不均 • 排气不良 • 原料流动性不足 • 制件太薄或浇口尺寸太小 • 聚合物熔体由于结构设计不合理导致过早硬化
案例分析 (合流痕)
30
案例(合流痕)
31
Underflow effect 潜流
熔接线附近的熔体流动一旦停止或减慢,冻结层厚度就会增加;但是,继续从 熔接线两侧流过来的熔体使得原有的冻结层因受摩擦热而重新熔化。
解决方法
材料 模具设计
• 材料的流动性
• 合理设计模具,保证合适的合流角度。 • 排气口的设计 • 水口的布局和流动长度
12
注塑的基本过程
WET CT 28s
合模 2s
升压 6s 注射 10s
DRY CT+WET CT = CT
保压 12s 冷却 2s
卸压
8s
开模取出 6s
塑化
合模
CT 46s
13
注塑三要素 • 时间: 注塑时间、保压时间、冷却时间、开合模时间、
取出时间、干周期、湿周期,周期等。 • 压力: 注塑压力、保压压力、背压、顶出压力、合模压
注塑机 工艺条件
• 分段注塑有利于合流痕位置的选择。
• 调整注塑速度和分段 • 调整熔体温度 • 调整热流道和热喷嘴的温度 • 顺序阀的使用 • 提高模具温度(可减轻,或者采用高温模具消除熔接痕)
10
注塑的基本原理
• 塑料在螺杆中通过加热和剪切进行熔融 • 推动熔胶进入型腔中以给其定形 • 冷却/结晶此熔胶
注塑工艺及缺陷案例全解
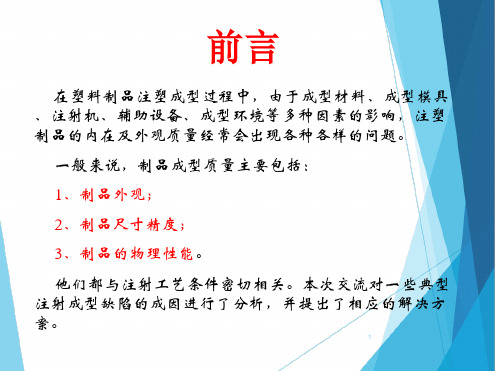
12、虎皮纹
热流道、模温)低; 障; (影响熔体的流动);
产生原因:
1、注射压力、速度低; 2、熔体加工温度(料筒、
3、设备料筒加热圈故障; 4、模具热流道加热圈故
5、原材料融指低; 6、进浇口小; 7、产品肉厚设计太薄
14
13、色纹
产生原因: 1、材料混料 2、料筒清洁不干净 3、背压低 4、干燥筒清洁不干净
20
9
6、银丝
产生原因:
1 、原料干燥温度低、干燥时间短 2 、储料背压低 3 、后松退位置大 4 、料筒及热流道温度高造成原料分解 5 、射胶速度快 6 、模具排气不良 7 、材料水分及低分子含量高
10
8、冷料
产生原因: 1、料温太低 2、背压高、松退小 3、顺序阀开闭设置位置不 当 4、进浇口无冷料阱 5、材料流动性好
15
14、小 4、汤口直径大 5、材料流动性太好
16
16、 产品变形
产生原因: 1、注射压力低、速度慢 2、保压压力低、时间短 3、料量不够 4、冷却时间太短 5、料温、热流道、模温高 6、模具顶出不平衡 7、材料收缩率达 8、产品结构加强筋设计不合理
1
典型注塑缺陷种类
1、缺料 2、飞边 3、缩瘪 4、熔接痕 5、流动痕(亮斑、气痕)
6、银丝
7、烧焦 8、冷料 9、顶出发白 10、拉伤 11、气泡
12、虎皮纹
13、色纹 14、杂质 15、塑丝 16、变形 17、尺寸偏大
18、尺寸偏小
2
成型缺陷影响因素
产品结 构
原材料 成型缺陷影响因素
成型工艺
5、机台模板不平行 6、模具分模面磨损变形产生间隙 7、原料熔融指数太高
6
3、缩瘪
注塑工艺及常见缺陷分析ppt课件
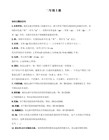
22
气泡 + 拉白
气泡
拉白
现象:表面有气泡孔,真空气泡;通常PC透明料比较 容易出现
现象:呈白色将断不断状态。一般出现在薄壁转角处, 薄壁RIB根部。
原因:注塑射速偏高,料筒温度偏高;保压保压时间、 原因:注塑射速射压偏高;保压及保压时间偏高;模
改善对策:注塑降低射速射压、降低料筒温度;模具 增加排气。
现象:表面形成一层薄薄的雾状就是气纹;一般出现 在浇口处
原因:注塑射速偏高,炮筒温度偏低;模具浇口太小, 流道不光滑;
改善对策:注塑降低射速,提高炮筒温度,以及模腔 表面温度;模具加大浇口,改善排气,增加冷料井
20
料花(气花) + 皱纹(波纹)
916模内注塑工艺
通过将切割后的凯夫拉素材放入模具内注塑成形 白色区域为凯夫拉素材,绿色区域为塑胶部分
25
916注塑件主要缺陷
916模内注塑缺陷影响因素
工艺新型
产品设计
模具制作
成型参数
916注塑缺陷的6大因素
机台设备
操作方法
26
27
916注塑件主要缺陷
现象:USB孔、顶部小孔溢胶 因素: 1,模具上外形与切割素材外形相差,尤其是圆角弧度; 2,模具流道设计方式存在缺陷 3,产品设计上存在缺陷 4,注塑参数 对策:依限度区分无需加工与待加工;
料花
皱纹
现象:表面呈银条状或雪花状
原因:注塑射速偏高,炮筒温度偏低,背压偏低,原 料未充分干燥,周期不稳定;
改善对策:注塑降低射速,提高背压、炮筒温度;原 料再烘烤干;使用全自动作业,稳定周期。
注塑缺陷原因和案例分析专题讲座PPT
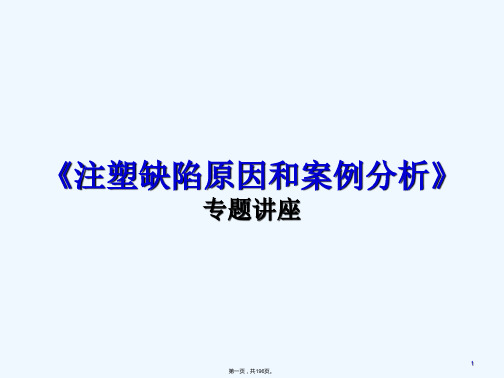
产品重量(g)
44.8 89.6 156.8 291.2 448 627.2 828.8
射胶时间(sec)
0.9 1.3 1.8 3.0 4.3 5.8 7.5
3)保压时间的计算:
保 TDi::压产保时品压间最时(大间Ti厚()s=e0度c.6)(,mD2m+0) .3D
产品最大厚 保压时间(sec) 度(mm)
Tm 成型温度(℃)
Tw
Ts
模具温度(℃)
热变形温度(℃)
• 冷却时间的简略计算方法:
a.模温60 ℃以下时:
理论冷却时间=t(1+2t)
b.模温6Байду номын сангаас ℃以上时:
理论冷却时间=1.3t(1+2t)
(t表示成型品的最大肉厚)。
23
第二十三页,共196页。
• 冷却时间计算的应用举例: 有一种产品,是用PC材料生产的,其最大胶厚t为
4)压力单位换算 1Kg/(cm2)=14.3Psi 1Psi=0.07Kg/cm2 1Mpa=10.2Kg/cm2 1Kg/cm2=98000Pa 1Kg/cm2=98.067KPa=0.9806bar 1bar=1.02Kg/cm2
18
第十八页,共196页。
6.材料温度的设定原则
• 一般材料宜用中等的温度成型,如ABS、PS、PP、PE • 容易过火或较脆的材料宜用稍低的温度,如POM、PVC • 流动性极差的材料宜用稍高的温度,如PC • 模具温度低时可适当调高料温来弥补
热传导系数 mm2/s 0.080 0.105 0.080 0.065 0.090 0.060 0.070 0.070 0.085 0.090 0.090
22
图文解说最常见的11例注塑成型缺陷
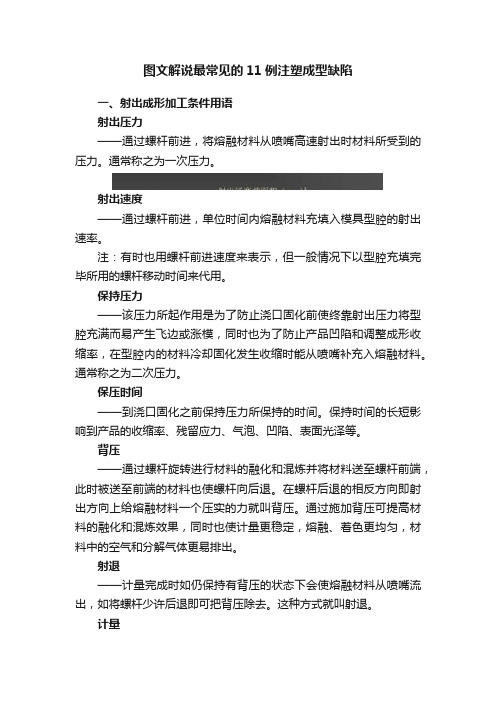
图文解说最常见的11例注塑成型缺陷一、射出成形加工条件用语射出压力——通过螺杆前进,将熔融材料从喷嘴高速射出时材料所受到的压力。
通常称之为一次压力。
射出速度——通过螺杆前进,单位时间内熔融材料充填入模具型腔的射出速率。
注:有时也用螺杆前进速度来表示,但一般情况下以型腔充填完毕所用的螺杆移动时间来代用。
保持压力——该压力所起作用是为了防止浇口固化前使终靠射出压力将型腔充满而易产生飞边或涨模,同时也为了防止产品凹陷和调整成形收缩率,在型腔内的材料冷却固化发生收缩时能从喷嘴补充入熔融材料。
通常称之为二次压力。
保压时间——到浇口固化之前保持压力所保持的时间。
保持时间的长短影响到产品的收缩率、残留应力、气泡、凹陷、表面光泽等。
背压——通过螺杆旋转进行材料的融化和混炼并将材料送至螺杆前端,此时被送至前端的材料也使螺杆向后退。
在螺杆后退的相反方向即射出方向上给熔融材料一个压实的力就叫背压。
通过施加背压可提高材料的融化和混炼效果,同时也使计量更稳定,熔融、着色更均匀,材料中的空气和分解气体更易排出。
射退——计量完成时如仍保持有背压的状态下会使熔融材料从喷嘴流出,如将螺杆少许后退即可把背压除去。
这种方式就叫射退。
计量——射出保压时螺杆前进把材料充满型腔并留有2~5mm的螺杆行程位置(残量)的储料设定量。
如果射出时螺杆位置押到零则会使型腔内的材料冷却固化发生收缩时不能从喷嘴补充入熔融材料而使保压不起作用。
螺杆回转数——单位时间内螺杆回转储料的转数。
螺杆回转的快慢影响到计量储料时间,计量应在冷却时间内完成,如超过冷却时间则要加快回转数。
保压切换——射出压力向保压切换时的时间(螺杆位置)对于成形条件是非常重要的。
通常以充入型腔材料的90~95%作为切换点。
二、射出成形不良原因和对策1. 充填不足--树脂未完全充满型腔使制品有缺损的现象。
[1] 成形品的体积过大i)要使用成形能力大的成形机。
ii)使用成形多腔模具时,关闭部分型腔。
常见注塑件缺陷及解决的方法
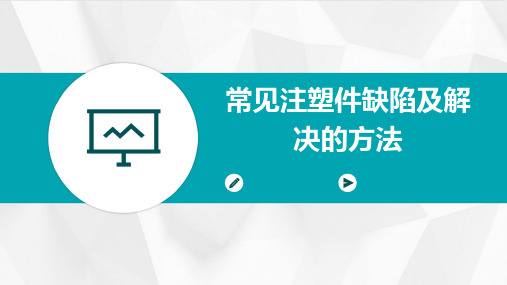
充填不足
01
总结词
充填不足是指注塑件在成型过程中未能完全填满 模具型腔,导致部分区域出现缺料或凹陷。
02
详细描述
充填不足通常是由于注射速度慢、注射压力不足、 模具温度过高或塑料流动性差等原因引起的。
缩痕
总结词
缩痕是指注塑件表面出现凹陷或收缩痕迹,影响 外观和尺寸精度。
详细描述
缩痕通常是由于塑料冷却过程中收缩率不均、模 具温度不均匀或注射压力不足等原因引起的。
常见注塑件缺陷及解 决的方法
目录
• 常见注塑件缺陷 • 注塑件缺陷原因分析 • 解决注塑件缺陷的方法 • 案例分析
01
常见注塑件缺陷
翘曲与扭曲
总结词
翘曲与扭曲是指注塑件形状发生扭曲或弯曲,不符合设 计要求。
详细描述
翘曲与扭曲通常是由于模具设计不合理、塑料收缩率差 异、注射温度和压力不适当等原因引起的。
环境条件的控制Байду номын сангаас
总结词
保持稳定的环境条件对注塑件的质量至关重 要,包括温度、湿度和清洁度等。
详细描述
确保注塑车间温度、湿度稳定,保持环境清 洁、无尘。定期对设备和环境进行清理和消 毒,防止污染和细菌滋生。同时,要关注天 气变化和季节性温差对注塑件质量的影响,
采取相应的措施进行调节。
04
案例分析
案例一:翘曲与扭曲缺陷的解决
材料选择与控制
总结词
选择合适的材料,控制材料质量是解决注塑件缺陷的重要步骤。
详细描述
根据产品使用要求和工艺特性,选择具有良好流动性和成型性的材料。同时, 要确保材料干燥、清洁,无杂质和污染。定期对材料进行质量检查,确保其性 能稳定。
模具优化与维护
精密注塑工艺与产品缺陷解决方案100例PPT模板课件

c
案例21 断 裂
f
案例24 通 水孔位披
锋
9
a
案例25 顶 针印明显
d
案 例 28 镜 片长度尺 寸偏大
2 案例分析
b
案例26 困 气烧焦
e
案 例 29 中 间孔位边 侧夹水线
c
案 例 27 表 面夹线及 内柱少胶
f
案例30 困 气调整困
难
10
2案例分 析
案例31 变形
案例36 进胶口气
纹圈
案例32 面壳底部 行位拉模
a
案例67 顶 白(二)
d
案例70 骨 位困气发
白
2 案例分析
b
案 例 68 侧 边多胶( 披锋)
e
案例71 水 口位气纹
(一)
c
案例69 表 面凹凸不
平
f
案例72 水 口位气纹
(二)
17
2案例分 析
01
案 例 7 3 进胶 点位气纹、
缺胶
04
案例76发 白(二)
02
案例74表 面拉高
05
案 例 7 7 电池 框水口位拖
05
案 例 9 5 内侧 拉伤(二)
03
案例93水 口拉胶粉
06
案例96表 面流纹
21
2案例分析
案例97变形 案例98两侧面顶出变形 案例99外观色差 案例100料流结合处容易断裂
22
感谢聆听
23
7
2案例分 析
01
案例13u形 位夹水线
04
案例16烧 焦
02
案例14困 气烧白
05
案例17内 行位易断
03
超详细注塑缺陷分析ppt课件
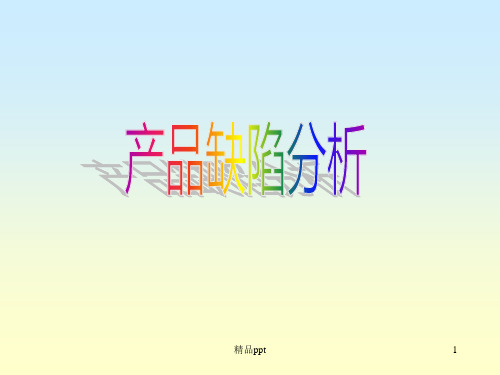
图1. 试样上出现的凹痕
精品ppt
15
(2)凹痕的生成原因
(2-1) 有效保压偏低:树脂填补偏少
在保压过程中,通过保压压力压入来填补因冷却固化→收缩的树脂量。如果因某种原因变成 有效保压偏低=树脂难以填补的状态,则在模具温度偏高时就容易形成凹痕,而在模具温 度偏低时容易形成空洞。
图2. 保压偏低时产生凹痕
图3. 模温引发空洞或凹精痕品ppt
13
(3) 真空空洞的对策
(3-1) 补充树脂
工艺上: · 确认转压点 · 提高保压压力;延长保压时间
模具上: · 增大浇口尺寸 · 增大主流道和分流道的口径 · 浇口应尽可能设在空洞产生部位(较厚部分)的附近
设备上: · 检查螺杆及止回阀三件套是否磨损
(3-2) 减慢表面固化
(2-3) 材料未烘干
图3. 卷入空气
精品ppt
10
(3)气泡的对策
(3-1) 减少空气卷入
1.减少料筒内空气卷入: - 降低螺杆转速 - 提高背压 - 回吸量设定不要过多
2. 减少填充时模腔内空气卷入: - 降低注射速度 - 调整浇口位置, 大小和形状。 - 调整主流道脱模斜度
关键要通过填充试验, 把握住流动样式,然后在此基础上确立相应的对策。
精品ppt
11
4. 空洞
(1)什么是空洞(外观)
是指成型品内部产生空洞的一种现象。 空洞一般发生在产品壁厚最厚处!
空洞的原因大致分为两种:一种是大量气体的混入, 另一种则是厚壁处的的树脂收缩。前者称为“气体空 洞”,后者称为“真空空洞”,以示区别。
图1. 厚壁处出现的空洞
精品ppt
图2. 气体空洞与真空空洞的区别
精品ppt
注塑生产工艺及问题解析

注塑生产工艺及问题解析一、注塑成型工艺过程1、注塑过程完整的注塑过程包括加料、塑化、注射入模、保压冷却和脱模等几个步骤,但究其实质可看做只是塑化和流动/冷却两个过程.(1)塑化这是塑料在料筒内经加热及螺杆旋转剪切达到流动状态并具备良好可塑性的全过程。
螺杆旋转不断地将料斗中落下的料粒拽入料筒的同时螺杆后退让料筒中的料在外电热及剪切摩擦热下进行熔化,最后将已熔融的胶料定量贮存到螺杆端部等待注射.(2)流动与冷却这一过程是指螺杆在油缸作用下前进,将具有流动性和温度均匀的熔胶注入模具开始,而后经过型腔注满,熔体在受控制条件下(如施以保压)冷固定型,直至塑件在模中脱出.a)充满阶段:这一阶段以螺杆开始向前移动起,直玫模腔被熔胶充满.b)压实阶段:这是指熔胶充满模腔时起至螺杆撤回(倒索)为至的阶段.C)倒流阶段:这一阶段是从螺杆后退时开始的,这时模腔内的压力比流道内高,因此就会发生未凝结的熔胶倒流,使模腔内的压力下降.d)冻结后的冻却阶段:这一阶段是指浇口的塑料完全冻结时起到塑件在模内顶出为止.2、成型工艺条件注塑工艺最重要的条件即是影响塑化流动和冷却的温度、压力及相应的各个作用时间。
可以说:要保证塑件质量合格及稳定,必须的条件是准确而稳定的工艺参数。
在调整工艺参数时,原则上按压力--------------- 时间----- 温度的顺序来调机,不应该同时变动两个或以上参数,防止工艺条件紊乱造成塑件质量不稳定.以下是对各工艺参数的说明:(D温度参数注塑成型过程中需控制的温度有料筒温度,喷嘴温度和模具温度,料筒温度及喷嘴温度主要影响塑料的流动和冷却. a)料筒温度:一般自后至前逐步升•高,以使均匀塑化.b)喷嘴温度:通常略低于料筒最高温度,防止喷嘴发生“流涎”现象,但亦不可太低防早凝堵塞.C)模具温度:对塑件内在性能和表现质量影响很大,对于表面要求比较高的胶件模温要求较高.(2)压力参数注塑成型过程中的压力包括塑化压力(背压)和注射压力.a)塑化压力(背压)・保证螺杆在旋转覆位时增加塑化压力使熔胶的温度均匀及把挥发性气体包括空气排出射料缸外.・把附加剂(如:色粉.色种.扩散剂等)与熔胶均匀地混合起来・提供均匀稳定的塑化熔胶以便保证塑件重量稳定.・在保证塑件质量的情况下尽可能低以免徙耗损材料・背压的大小调节视胶料不同而异,一般不超过20KG∕CM2(具体各胶料背压值可参见本工艺资料第一部分有关内容)b)注射压力•克服塑料熔体从料筒流向型腔的滞阻力,给予充模压力及对充入的熔料进行压质.•对于流动性差的塑料,注射压力要取大,对于型腔阻力大的薄壁胶料,注射压力也要取大.⑶时间参数(成型周期)I --- 充模时间—注射时间—I' -- 保压时间----- 1I总冷却时间成型周期 --------- 闭模冷却时间------------------ 1---- 其它时间(如:开模.脱模.喷脱剂等)・注射时间和冷却时间是基本组成部分,其多少对啤塑件的质量有决定性的影响.・充模时间一般不超过IOSo・保压时间较长,与胶件臂厚有关(厚壁取长时间),以保证最小收缩.•冷却时间取决于塑料结晶性,制品料厚,模具温度等因素视具体情形调整.⑷注射速度・注射速度通过调节单位时间内向注射油缸供油多少来实现.•一般说来(在不引负作用的前提下)尽量使用高射速充模,以保证塑件熔接强度及表现质量,而相对低的压力也使塑件内应力减小提高了强度.・用高压低速进料的情况可使流速平稳,剪切速度小,塑件尺寸稳定,避免缩水缺陷.二、塑料模的基本认识塑料模具是注射成型生产中赋予塑料形状所用部件的组合体,塑料模的结构视塑料性质、制件形状、结构以及注射机的不同等因素而可能形式大小差异很大,然而其基本结构大致相同,即主要由浇注系统、成型零件、结构零件三大部分组成.其中浇注系统与成型零件是塑料直接接触的部分,并随塑料制品而变化,它是模具中最重要、最复杂、变化最大、要求表面精度及光洁度最高的部分.**浇注系统&成型零件浇注系统指塑料从喷嘴进入型腔的流道部分,包括:主流道、冷料穴、分流道和浇口等.成型零件指构成成品形状的各零件,包括:动、静模型腔/型芯、排气槽、(成型)顶针等.**典型的模具结构典型的模具结构包括以下几个主要部分:1.主流道:是模具连接注射机喷嘴通至型腔或分流道的一段,主流道进口顶部呈凹形,以便与喷嘴连接.主流道进口直径应略大于喷嘴直径(0.8mm)以免溢料并防止两者连接不准而发生堵截.进口直径根据制品大小而定,一般为Φ4-8πιπι主流道直径应向内扩大,呈3-5角度,以便流道顺利出模.2.分流道:在多型腔模中连接主流道和各个型腔的通道.为使熔料能等速度地充满各型腔,分流道在模里的排列应尽可能等距对称,而分流道的截面积形状/尺寸对熔料的流动有很大影响,且对脱模/造模的难易都有影响.常用的分流道截面形状是梯形或半圆形而且是开在带有脱模杆的半模上.流道的表面必须抛光以减小流动阻力而提供较快速度充模,流道的尺寸决定于塑料品种,制品尺寸及壁厚(具体参见有关数据数据)在满足成型要求的前提下应尽量减少截面积,以免增加水□料的比例及使冷却时间增加,降低了生产效率.3.冷料位:设在主流道末端的空穴,用来容纳喷嘴两次注射之间所产生的冷料,从而防止分流道或水口堵塞.如果冷料进入型腔则会导致制件内应力加大或机械强度不足,冷料位尺寸一般为Ψ3-10mm,深度6mm左右,为便于脱模(拉出水口),其底部通常都是拉料杆位(脱模杆),拉料杆的头部通常都设计成下凹陷或带有沟槽形成,便于拉出主流道连整个流道系统.4.浇口(入水口)是熔料通过直/分流道后进入型腔的通道,浇口的截面积通常是整个流道系统中截面积最小的部分.内浇口的尺寸形状对制件的质量影响很大,其主要的作用可列述以下几点:1)控制料流速度;2)成型中水口位早凝结可防其倒流;3)使料通过时产生较高的剪切力使料温提升,从而降低其表面粘度,提高其流动性;4)便于制件与流道分离;浇口的形状尺寸和位置设计都须根据塑料品种,制件结构和形状等具体情况做出选择,一般来说,浇口的位置都是开在制件厚壁位(以利补缩)及不影响外观的位置.浇口尺寸设计应考虑熔体的性质.5.型腔是制件在模具中成型的部分,用来构成型腔的零件称为成型零件,一般包含以下:1)凹模 ----- 构成制件外形的成型零件;2)凸模/型芯 ----- 构成制件内部形状,如:沟、孔、槽等;由于熔体进入型腔后产生很高的压力,故对成型零件的材料强度、刚度要求较高,且材料应具耐腐蚀性.成型零件一般都经过热处理提高硬度.注:常用于塑料模的钢材有:718、S-136;而合金模具是用热作钢8407.6.排气位1)开设在模具内的槽形排气位,防止熔料进入型腔时卷入气体.当熔料进入型腔时,原存入型腔的空气及熔料带入的气体必须在料流的尽头通过排气槽向外排出,如排出不完全,则可能会造成件带气孔、熔接痕、充模料不齐,甚至困入高温压缩空气而烧伤胶件的情况出现.2)一般情况下,排气孔既可开设在型腔内熔料流动的尽端,也可开设在模具的分模面上.(在凹模上开一般0.03-0.06mm深,L5-6.Omm宽的槽)3)注射件排气孔是不会有很多熔料渗(迫)出的,因为熔料会在该处冷却固化而自动将通道堵死。
常见注塑缺陷及解决方案

注塑缺陷原因分析与解决方案一、变形/翘曲( Warpage )塑胶件产生翘曲变形,导致制品的效或引起尺寸误差和装配困难;翘曲变形是塑件最严重的质量缺陷之一。
变形产生原因:1、材料:物料收缩率大,如PA+GF的收缩率就很大,流动玻纤取向。
2、模具:(1)产品两侧,型腔与型芯间温度差异较大;(2)模具冷却水路位置分配不均匀,没有对温度很好地进行控制;(3)浇口方式和位置设计不合理,特别加纤料,流动规则很重要;(4)产品粘模引起变形,顶出不平衡导致变形;(5)模具排气不佳,导致模腔内注塑压力大。
3、成型工艺:(1)注塑压力过高或者注射速度过大;(2)料筒温度、熔体温度过高;(3)保压时间过长或冷却时间过短;(4)尚未充分冷却就顶出,由于顶针对表面施压造成翘曲变形。
4、产品结构(1)长条形结构翘曲加剧;(2)产品结构不对称导致不同收缩;(3)产品壁厚不均匀,突变或过薄,导致薄壁部分冷却较快引起翘曲。
解决方案:主要应从产品和模具设计方面着手解决,而依靠成型工艺调整的效果是非常有限的。
1、材料:(1)选择收缩性较小的材料,内部的长条形纤维会顺着流动方向发生取向。
沿着取向方向收缩小、垂直取向方向收缩大,取向引起的收缩不均会导致产品变形;(2)如PA66或PA+GF料都容易变形,评估时特别注意,提前做模流分析。
2、产品结构和模具:(1)由于塑胶从熔体转变为固体体积必然收缩,厚度大收缩大,厚度小收缩相对也小,收缩不均产生的内应力导致产品变形。
只能通过优化产品设计,尽量使产品壁厚均匀;(2)模具的冷却系统设计合理,使得产品能够冷却均匀平衡,控制模芯与模腔的温差。
(3)合理确定浇口位置及浇口类型,可以较大程度上减少产品的变形,一般情况下,可采用多点式浇口,在评估阶段多做几种模流分析方案来验证最小变形;(4)模具设计合理,确定合理的拔模斜度,顶针位置和数量,检查和校正模芯,提高模具的强度和定位精度;(5)改善模具的排气功能。
常见注塑件缺陷及解决方法精品课件
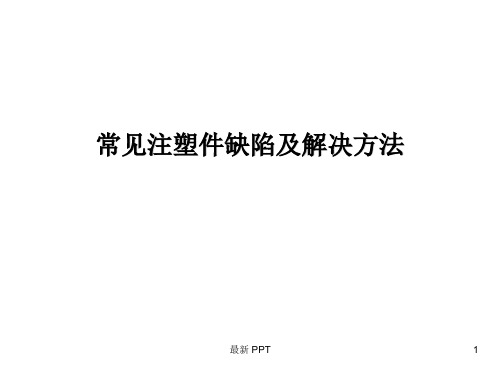
▪
13、生气是拿别人做错的事来惩罚自 己。20.9.2220.9.2209:58:3909:58:39September 22, 2020
▪
14、抱最大的希望,作最大的努力。2020年9月22日 星期二 上午9时58分39秒09:58:3920.9.22
▪
15、一个人炫耀什么,说明他内心缺 少什么 。。2020年9月 上午9时58分20.9.2209:58September 22, 2020
最新 PPT
8
常见注塑件缺陷及解决方法
7.缩 水
产生的原因:
1.加料量不足
2.料温太高
3.产品壁厚尺寸相差大
4.注射及保压时间太短
5.注射压力不够
6.注射速度太快
7.浇口位置不当
解决方法:
1.增加料量
2.降低料温
3.加大注射压力
4.降低注射速度
5.更改浇口位置
最新 PPT
9
常见注塑件缺陷及解决方法
解决方法: 1.二次料回收干净 2.材料按要求烘干(含水率测试) 3.目前采用次料造粒 4.检查射嘴 5.提高模温或料管温度
最新 PPT
3
常见注塑件缺陷及解决方法
2.流纹
产生的原因: 从浇口沿着流动方向,弯曲如蛇行一样的痕迹 它是由于树脂由浇口开始的注射速度过高所导致
解决方法: 1.调低注射速度 2.提高模具温度 ,提高保压力 3.扩大浇口断面尺寸 4. 改变浇口位置(缩短通过浇口后的直进距离) 5.增加排气槽
最新 PPT
11
常见注塑件缺陷及解决方法
10.烧焦
产生的原因:
根据由机械、模具或成型条件等不同的原因引起的 烧伤 主要表面为发黑,像黑碳一样.
注塑件不良情况图解大全.docx
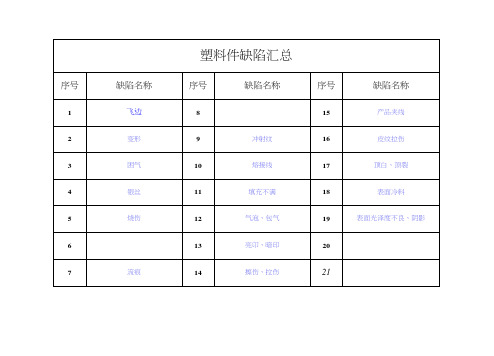
缺陷名称变形缺陷等级C缺陷释义由于制件内部分子排列取向及冷却收缩不均匀,导致制件形状、尺寸发生改变,称为变形。
缺陷图片模具类型产生原因解决方法塑料模2、制件形状设计不合理,薄厚不均情况允许的情况下,修改制件,使之符合成型工艺3、进料口位置不合理,熔料直接冲击型芯,两侧受力不均更改进料口位置4、注射工艺不合理(料温、模温低,注射压力小,注射速度快,保压时间不足)调整注射工艺5、型腔不同部位温差大,冷却不均合理控制模温,保证模具型腔整体温度趋于平衡6、供料不足或过量定量供料1、冷却时间不足,模温高增加冷却时间,降低模温7、模具顶出设置位置不合理调整顶出机构位置缺陷名称困气缺陷等级B缺陷释义模具注塑时,制件成型的尽头位置出现的因气蚀而发亮的现象。
缺陷图片模具类型塑料模产生原因1、模具排气不良2、原料内含水分或挥发物过多3、浇口设置不合理(流动存在死角)4、注射压力大/注射速度快解决方法增加排气或合理安排顶杆.镶块,利用间隙充分排烘干原料更改浇口位置调整注射压力/注射速度5、制件结构原因(壁厚落差大)调整制件结构缺陷名称银丝缺陷等级A缺陷释义制件表面沿熔料流动方向产生的银白色纹理(针状条纹或片状云母纹),称为银丝。
缺陷图片模具类型产生原因解决方法1、原料内含水分或挥发物过多烘干原料2、模具型腔内有水清除模具型腔内水分3>模具型腔内润滑油.脱模剂用量使用过多合理使用润滑剂及脱模剂塑料模4、制件壁厚不均,融料从薄壁流入厚壁时膨胀、挥发物气化与模具表面接触液化成银丝改善塑件设计,使厚薄壁均匀过渡,符合工艺性5.配料不当,混有异物或不熔料,发生分层脱离配料时注意纯度6、模温低,注射压力小,注射速度低。
使融料填充慢,冷却快,易形成银白色或白色反射光的薄层提高模温,加大注射压力和加快注射速度缺陷名称流痕模具类型产生原因解决方法塑料模1、浇口尺寸小增大浇口尺寸2、注射速度过快适当降低注射速度3、模温低提高模温4、注射压力过大合理控制注射压力5、浇口位置不当更改浇口位置缺陷名称冲射纹缺陷等级产品一级面:A类; 产品二级面:B类; 产品三级面:C类;缺陷释义当高速熔料经过喷嘴、流道、浇口等狭窄区域后,进入相对开放的型腔,接触型腔表面而固化,接着被随后的熔料推挤,从而残留蛇形痕迹。
21个注塑成型缺陷问题与解决方案

21个注塑成型缺陷问题与解决方案缺陷之一:料头附近有黯晕表观在料头周围有可辨别的环形—如使用中心式浇口则为中心圆,如使用侧浇口则为同心圆,这是因为环形尺寸小,看上去像黯晕。
这主要是加工高粘性(低流动性)材料时会发生这种现象,如PC、PMMA和ABS等。
物理原因如果注射速度太高,熔料流动速度过快且粘性高,料头附近表层部分材料容易被错位和渗入。
这些错位就会在外层显现出黯晕。
在料头附近,流动速度特别高,然后逐步降低,随着注射速度变为常数,流动体前端扩展为一个逐渐加宽的圆形。
同时在料头附近为获得低的流体前流速度,必须采用多级注射,例如:慢—较快—快。
目的是在整个充模循环种获得均一的熔体前流速度。
通常以为黯晕是在保压阶段熔料错位而产生的。
实际上,前流效应的作用是在保压阶段将熔料移入了制品内部。
与加工参数有关的原因与改良措施:1、流速太高采用多级注射:慢-较快-快2、熔料温度太低增加料筒温度,增加螺杆背压3、模壁温度太低增加模壁温度与设计有关的原因与改良措施:1、浇口与制品成锐角在浇口和制品间成弧形2、浇口直径太小增加浇口直径3、浇口位置错误浇口重新定位注塑成型缺陷之二:锐边料流区有黯区表观成型后制品表面非常好,直到锐边。
锐边以后表面出现黯区并且粗糙。
物理原因如果注射速度太快,即流速太高,尤其是对高粘性(流动性差)的熔体,表面层容易在斜面和锐边后面发生移位和渗入。
这些移位的外层冷料就表现为黯区和粗糙的表面。
与加工参数有关的原因与改良措施:流体前端速度太快采用多级注射:快-慢,在流体前端到达锐边之前降低注射速度与设计有关的原因与改良措施:模具内锐角过渡提供光滑过渡缺陷之三:表面光泽不均表观虽然模具具有均一的表面材质,制品表面还是表现为灰黯和光泽不均匀。
物理原因注射成型生产的制品表面多少是模具表面的翻版。
表面粗糙取决于热塑性材料本身,它的粘性、速度设置以及成型参数如注射速度、保压和模温。
因而,由于仿制的表面粗糙度的原因,制品表面会出现为灰黯、较黯或光滑。
注塑常见产品缺陷及解决方法ppt课件
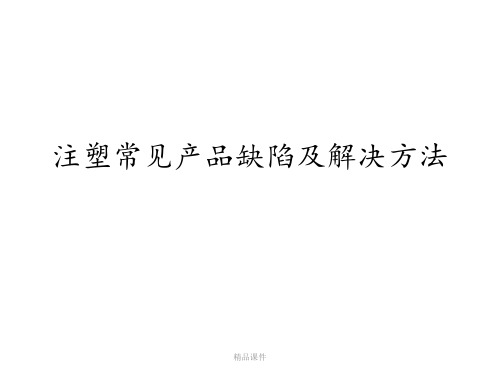
精品课件
走料不齐
原因: 1.注塑压力太低. 2.注塑速度太慢. 3.注塑时间太短. 4.保压压力过小. 5.保压时间过短. 6.保压切换位置过早. 7.模具疏气不良. 8.模具表面温度太低. 9.熔胶温度过低. 10.物料粘度过高.
精品课件
走料不 齐
解决方法: 1.注塑中断后重新开机,可 能前几啤会报废. 2.提高注塑和补缩压力. 3.提高注塑量和注塑速度.( 注塑压力要足够) 4.提高模具温度. 5.提高料温. 6.清洁模具的疏气系统. 7.检查料垫是否足够. 8.调节适合的保压转换点( 填充至95%-99%). 9.检查浇口和炮嘴有没有被 堵塞.
精品课件
困 气
原因: 1.注塑速度过快. 2.背压过高. 3.疏气不足,气体包封. 4.流道尺寸偏小. 5.熔体温度过高,需降低剪 切. 解决方法: 1.降低注塑速度. 2.清洁困气位置的疏气槽. 3.降低锁模力. 4.降低保压压力. 5.降低螺杆的转速. 6.降低熔胶温度.
精品课件
困气
烧
发
黑
白
精品课件
变形
解决方法: 1.加长冷却时间. 2.加长保压时间. 3.增加或降低注塑压力. 4.增加或降低模温. 5.根据产品变形的方向适当 的设置不同的前后模温(变 形趋向模温高的一側) 6.采用多段保压,高到低或 低到高设置保压压力.
精品课件
夹具(定型模)
精品课件
热水机&冷水机
精品课件
此课件下载可自行编辑修改,供参考! 感谢您的支持,我们努力做得更好!
精品课件
精品课件
柱位的缩水
精品课件
喷 射纹
原因: 1.注塑速度过慢或过快. 2.注塑压力太低. 3.保压时间过长. 4.模具冷却不均已. 5.模具浇口附近温度较低. 6.模具表面温度太低. 7.模具浇口尺寸太小. 8.浇口位置设计不合理. 9.浇口流程过长. 10.熔胶温度过低. 解决方法: 1.降低注塑速度(多级注塑). 2提高料温,提高模具温度. 3.提高浇口的深度(为壁厚的 60%-80%比较安全) 4.改用扇形浇口.
注塑工艺 注塑成型缺陷分析及不良解决对策
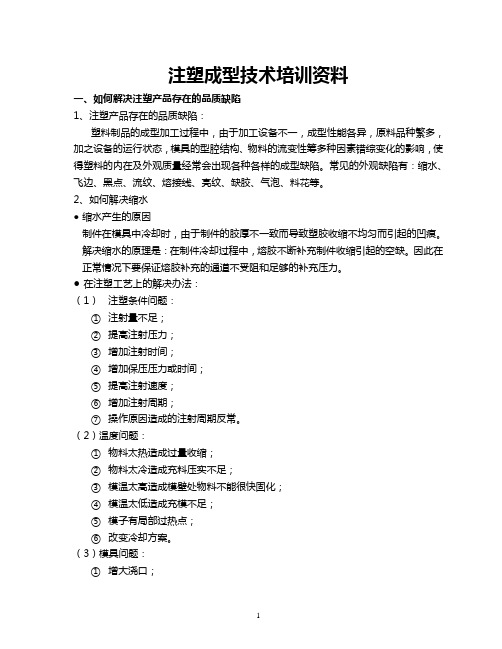
注塑成型技术培训资料一、如何解决注塑产品存在的品质缺陷1、注塑产品存在的品质缺陷:塑料制品的成型加工过程中,由于加工设备不一,成型性能各异,原料品种繁多,加之设备的运行状态,模具的型腔结构、物料的流变性筹多种因素错综变化的影响,使得塑料的内在及外观质量经常会出现各种各样的成型缺陷。
常见的外观缺陷有:缩水、飞边、黑点、流纹、熔接线、亮纹、缺胶、气泡、料花等。
2、如何解决缩水●缩水产生的原因制件在模具中冷却时,由于制件的胶厚不一致而导致塑胶收缩不均匀而引起的凹痕。
解决缩水的原理是:在制件冷却过程中,熔胶不断补充制件收缩引起的空缺。
因此在正常情况下要保证熔胶补充的通道不受阻和足够的补充压力。
●在注塑工艺上的解决办法:(1)注塑条件问题:①注射量不足;②提高注射压力;③增加注射时间;④增加保压压力或时间;⑤提高注射速度;⑥增加注射周期;⑦操作原因造成的注射周期反常。
(2)温度问题:①物料太热造成过量收缩;②物料太冷造成充料压实不足;③模温太高造成模壁处物料不能很快固化;④模温太低造成充模不足;⑤模子有局部过热点;⑥改变冷却方案。
(3)模具问题:①增大浇口;②增大分流道;③增大主流道;④增大喷嘴孔;⑤改进模子排气;⑥平衡充模速率;⑦避免充模料流中断;⑧浇口进料安排在制品厚壁部位;⑨如果有可能,减少制品壁厚差异;⑩模子造成的注射周期反常。
(4)设备问题:①增大注压机的塑化容量;②使注射周期正常;(5)冷却条件问题:①部件在模内冷却过长,避免由外往里收缩,缩短模子冷却时间;②将制件在热水中冷却。
3、如何解决飞边●产生飞边的原因:产品溢边往往由于模子的缺陷造成,其他原因有:注射力大于锁模力、物料温度太高、排气不足、加料过量、模子上沾有异物等。
●如何判断产生飞边的原因:在一般情况下,采用短射的办法。
即在注塑压力速度较低、不用保压的情况下注塑出制件90%的样板,检查样板是否出现飞边,如果出现,则是模具没有配好或注塑机的锁模压力不足,如果没有出现,则是由于注塑条件变化而引起的飞边,比如:保压太大、注射速度太快等。
注塑制品缺陷的原因分析与解决对策PPT课件
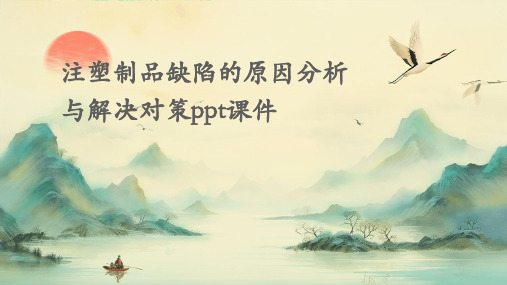
原因分析
针对每种缺陷类型, 分析其产生的原因, 从材料、工艺、模具、 设备等方面进行深入 探讨。
解决对策
针对每种缺陷类型, 提出具体的解决对策, 包括工艺优化、模具 改进、设备维护等方 面。
案例分析
通过实际案例的介绍 和分析,进一步说明 原因分析和解决对策 的应用和实践效果。
02
注塑制品缺陷概述
注塑制品缺陷的定义和类型
提高注塑制品的质量和降低生产成本, 有助于提升企业的竞争力,赢得市场 和客户的信任。
减少缺陷品和废品的产生,降低生产 成本,提高生产效率和经济效益。
报告的结构和内容
报告目的和背景
介绍报告的目的、背 景和意义,为后续内 容打下基础。
注塑制品缺陷类型
列举常见的注塑制品 缺陷类型,如缩水、 翘曲、银纹等。
定义
注塑制品缺陷是指在注塑成型过 程中,由于各种原因导致制品出 现不符合设计要求或影响使用性 能的缺陷。
类型
常见的注塑制品缺陷包括填充不 足、翘曲变形、缩痕、银纹、气 孔和熔接痕等。
注塑制品缺陷的常见问题
填充不足
由于注射量不足或模具设计不合理,导致制 品某些部位未完全填充。
翘曲变形
由于冷却不均匀或顶出系统设计不合理,导致 制品翘曲变形。
04
解决对策
材料选择与控制
总结词
合适的材料选择是避免注塑制品缺陷 的关键。
详细描述
在选择注塑材料时,应考虑其物理性 能、化学性能和加工性能,以确保其 满足产品设计和生产要求。同时,应 定期对原材料进与优化
总结词
模具设计不合理是导致注塑制品缺陷的重要原因。
详细描述
注射温度、压力、时间等参数不当
注射温度、压力、时间等参数设置不当会影响塑料的流动和成型,导致制品出现 各种缺陷。
- 1、下载文档前请自行甄别文档内容的完整性,平台不提供额外的编辑、内容补充、找答案等附加服务。
- 2、"仅部分预览"的文档,不可在线预览部分如存在完整性等问题,可反馈申请退款(可完整预览的文档不适用该条件!)。
- 3、如文档侵犯您的权益,请联系客服反馈,我们会尽快为您处理(人工客服工作时间:9:00-18:30)。
6、银丝
产生原因:
1 、原料干燥温度低、干燥时间短 2 、储料背压低 3 、后松退位置大 4 、料筒及热流道温度高造成原料分解 5 、射胶速度快 6 、模具排气不良 7 、材料水分及低分子含量高
10
8、冷料
产生原因: 1、料温太低 2、背压高、松退小 3、顺序阀开闭设置位置不 当 4、进浇口无冷料阱 5、材料流动性好
前言
在塑料制品注塑成型过程中,由于成型材料、成型模具 、注射机、辅助设备、成型环境等多种因素的影响,注塑 制品的内在及外观质量经常会出现各种各样的问题。
一般来说,制品成型质量主要包括:
1、制品外观;
2、制品尺寸精பைடு நூலகம்;
3、制品的物理性能。
他们都与注射工艺条件密切相关。本次交流对一些典型 注射成型缺陷的成因进行了分析,并提出了相应的解决方 案。
18
17、 尺寸偏大
产生原因:
1 、注射压力高、速度快 2 、保压压力高、时间长 3 、料量大 4 、留模冷却时间太长 5 、模具放缩量错误 6 、材料加工温度低(收缩小) 7 、材料收缩率小
19
18 、 尺寸偏小
产生原因:
1、注射压力低、速度慢 2、保压压力低、时间短 3、料量小 4、留模冷却时间短 5、模具放缩量错误 6、材料加工温度高(收缩大) 7、材料收缩率大
13
12、虎皮纹
热流道、模温)低; 障; (影响熔体的流动);
产生原因:
1、注射压力、速度低; 2、熔体加工温度(料筒、
3、设备料筒加热圈故障; 4、模具热流道加热圈故
5、原材料融指低; 6、进浇口小; 7、产品肉厚设计太薄
14
13、色纹
产生原因: 1、材料混料 2、料筒清洁不干净 3、背压低 4、干燥筒清洁不干净
7
4、熔接痕
产生原因:
1、注射压力、速度低、保压压力、 速度低
2、料温(料筒、热流道)、模温 低
3、顺序阀打开设置不当 4、浇口设置不当 5、模具排气不良 6、材料流动性差
8
5、流动痕(亮斑、气痕)
产生原因:
1 、注射压力高、速度快、 2 、料温(料筒、热流道)、模温高 3 、顺序阀打开设置不当 4 、模具排气不良 5 、材料流动性太好
5、机台模板不平行 6、模具分模面磨损变形产生间隙 7、原料熔融指数太高
6
3、缩瘪
产生原因:
1 、注射压力、速度低、保压压力、速度低 2 、储料量不够(背压小) 3 、射胶时间短(时间转保压) 4 、冷却时间短 5 、料温(料筒、热流道)、模温高 6 、模温机故障 7 、螺杆计量不准 8 、材料收缩率大 9 、产品肉厚设计太厚
20
注塑机及周边设 备
模具
3
4
1、缺料
产生原因: 1、注射压力、速度低 2、料量不够 3、料温、模温低 4、设备能力不足 5、射嘴对中性差(漏料) 6、止逆阀磨损,损坏 7、模具排气不良 8、模具热流道加热故障 9、模具热流道漏胶 10、原料流动性差
5
2、飞边
产生原因: 1、注射压力、速度大
2、料量太多 3、料温、模温高 4、锁模力小
15
14、 塑丝
产生原因: 1、料温高、模温高 2、冷却时间短 3、背压高、松退小 4、汤口直径大 5、材料流动性太好
16
16、 产品变形
产生原因: 1、注射压力低、速度慢 2、保压压力低、时间短 3、料量不够 4、冷却时间太短 5、料温、热流道、模温高 6、模具顶出不平衡 7、材料收缩率达 8、产品结构加强筋设计不合理
11
9、顶出发白(顶杆印)
产生原因: 1、注射压力高、速度快 2、保压压力高、时间长 3、料量大 4、模温低 5、顶出速度快 6、模具顶出不平衡 7、拔模斜度设计太小
12
10、产品拉伤
产生原因: 1、注射压力高、速度快 2、保压压力高、时间长 3、料量大 4、模温低 5、开模一段速度过快 6、模具拔模斜度小 7、母模面皮纹太深 8、模具分型线磨损 9、材料收缩率小
1
典型注塑缺陷种类
1、缺料 2、飞边 3、缩瘪 4、熔接痕 5、流动痕(亮斑、气痕)
6、银丝
7、烧焦 8、冷料 9、顶出发白 10、拉伤 11、气泡
12、虎皮纹
13、色纹 14、杂质 15、塑丝 16、变形 17、尺寸偏大
18、尺寸偏小
2
成型缺陷影响因素
产品结 构
原材料 成型缺陷影响因素
成型工艺