注塑工艺缺陷及对策
注塑缺陷描述及解决方案

注塑缺陷描述及解决方案引言概述:注塑技术是一种常用的塑料成型工艺,广泛应用于各个行业。
然而,在注塑过程中,常常会出现一些缺陷,如气泡、热胀冷缩、短射等问题,这些缺陷会影响产品的质量和性能。
本文将从五个大点出发,详细阐述注塑缺陷的描述及解决方案。
正文内容:1.注塑缺陷:气泡1.1 气泡的描述:气泡是注塑过程中常见的缺陷之一。
它们通常出现在产品的内部或表面,给产品的外观和性能带来负面影响。
1.2 气泡的解决方案:1.2.1 调整注塑机的压力和温度,确保塑料完全熔化,减少气体残留。
1.2.2 优化模具结构,增加通气口,促使气泡顺利排出。
1.2.3 使用抗气泡剂或改性剂,减少气泡的生成。
2.注塑缺陷:热胀冷缩2.1 热胀冷缩的描述:热胀冷缩是由于注塑过程中塑料的热胀冷缩性质导致的缺陷。
它会导致产品尺寸不准确,甚至造成产品变形。
2.2 热胀冷缩的解决方案:2.2.1 选择合适的塑料材料,具有较小的热胀冷缩系数。
2.2.2 控制模具温度,使得塑料在注塑过程中均匀冷却,减少热胀冷缩的影响。
2.2.3 使用辅助冷却系统,如冷却水或风扇,加速产品冷却过程,减少热胀冷缩。
3.注塑缺陷:短射3.1 短射的描述:短射是指注塑过程中塑料未能充满模具腔体,导致产品缺陷。
短射通常表现为产品的一部分或整个部分未充实。
3.2 短射的解决方案:3.2.1 检查和调整注塑机的注射速度和压力,确保塑料能够充分填充模具腔体。
3.2.2 检查模具的设计和结构,确保流道和出料口的尺寸和位置合理,避免短射现象。
3.2.3 使用模具温度控制系统,确保塑料在注塑过程中保持适当的温度,减少短射的发生。
4.注塑缺陷:毛刺4.1 毛刺的描述:毛刺是指注塑过程中产生的塑料残留物,通常出现在产品的边缘或表面,影响产品的外观和质量。
4.2 毛刺的解决方案:4.2.1 优化模具设计,增加冷却系统,降低模具温度,减少毛刺的生成。
4.2.2 调整注塑机的注射速度和压力,避免过多的塑料残留。
注塑缺陷原因分析与解决方案
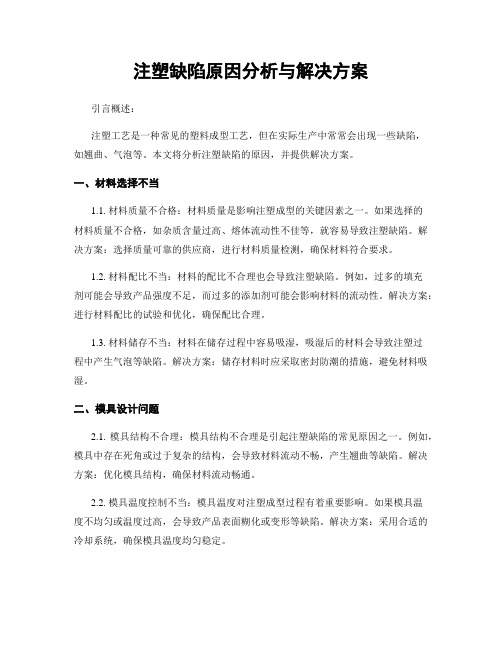
注塑缺陷原因分析与解决方案引言概述:注塑工艺是一种常见的塑料成型工艺,但在实际生产中常常会出现一些缺陷,如翘曲、气泡等。
本文将分析注塑缺陷的原因,并提供解决方案。
一、材料选择不当1.1. 材料质量不合格:材料质量是影响注塑成型的关键因素之一。
如果选择的材料质量不合格,如杂质含量过高、熔体流动性不佳等,就容易导致注塑缺陷。
解决方案:选择质量可靠的供应商,进行材料质量检测,确保材料符合要求。
1.2. 材料配比不当:材料的配比不合理也会导致注塑缺陷。
例如,过多的填充剂可能会导致产品强度不足,而过多的添加剂可能会影响材料的流动性。
解决方案:进行材料配比的试验和优化,确保配比合理。
1.3. 材料储存不当:材料在储存过程中容易吸湿,吸湿后的材料会导致注塑过程中产生气泡等缺陷。
解决方案:储存材料时应采取密封防潮的措施,避免材料吸湿。
二、模具设计问题2.1. 模具结构不合理:模具结构不合理是引起注塑缺陷的常见原因之一。
例如,模具中存在死角或过于复杂的结构,会导致材料流动不畅,产生翘曲等缺陷。
解决方案:优化模具结构,确保材料流动畅通。
2.2. 模具温度控制不当:模具温度对注塑成型过程有着重要影响。
如果模具温度不均匀或温度过高,会导致产品表面糊化或变形等缺陷。
解决方案:采用合适的冷却系统,确保模具温度均匀稳定。
2.3. 模具磨损严重:模具长时间使用后会出现磨损,磨损严重的模具会导致产品尺寸不准确或表面粗糙等缺陷。
解决方案:定期检查和维护模具,及时更换磨损严重的模具部件。
三、注塑工艺参数设置不当3.1. 注射压力过高或过低:注射压力是影响注塑成型的关键参数之一。
如果注射压力过高,会导致产品变形或开裂,而注射压力过低则会导致产品表面光洁度不高。
解决方案:根据产品要求和材料特性,合理设置注射压力。
3.2. 注射速度不合理:注射速度对产品的充填和冷却过程有着重要影响。
如果注射速度过快,会导致产品内部产生气泡或短射,而注射速度过慢则会导致产品表面瑕疵。
注塑成型缺陷及解决方法

注塑成型缺陷及解决方法注塑成型是一种常用的塑料制品生产工艺,但在实际操作过程中,难免会出现一些缺陷。
下面将介绍几种常见的注塑成型缺陷及其解决方法。
1.短射:短射指的是塑料在模腔中注入不完全,导致制品形状不完整或缺少一部分。
短射可能由于注射速度过快或进气不畅引起。
解决方法是调整注塑机的注射速度和压力,确保塑料充分进入模腔,并检查进气口是否畅通。
2.气泡:气泡是指制品表面或内部出现空洞。
气泡的形成可能由于塑料中含有水分、模具开放不当等原因。
解决方法是在注塑前将塑料干燥处理,确保塑料中不含水分,并检查模具密封性以防止气体进入模腔。
3.缩短:缩短是指制品尺寸比设计要小,可能由于塑料收缩不均匀或模具温度不稳定引起。
解决方法是通过调整模具温度和冷却系统,使塑料在注塑过程中均匀收缩,并确保模具温度稳定。
4.色差:色差是指制品表面颜色不均匀,可能由于塑料熔融不充分、颜料添加不均匀等原因。
解决方法是加长塑料的熔化时间,确保塑料充分熔融,并确保颜料充分混合均匀。
5.枝晶:枝晶是指制品表面出现树枝状的纹理,可能由于注塑温度过高或冷却时间不足引起。
解决方法是降低注塑温度,延长冷却时间,确保塑料在注塑过程中充分凝固。
6.毛刺:毛刺是指制品表面出现刺状的尖突物,可能由于模具间隙过大或模具磨损引起。
解决方法是调整模具间隙,确保模具紧密结合,并定期检查模具磨损情况。
7.烧焦:烧焦是指塑料在注塑过程中受热过度,产生发黑或炭化的现象。
烧焦可能由于注塑温度过高或注射速度过快引起。
解决方法是降低注塑温度,调整注射速度,确保塑料受热均匀。
总结起来,解决注塑成型缺陷的关键是调整注塑机参数、保证模具质量和稳定性,以及进行适当的后处理工艺。
此外,及时发现和修复模具的损坏也是避免缺陷的重要措施。
注塑缺陷描述及解决方案

注塑缺陷描述及解决方案注塑是一种常用的塑料加工方法,通过将熔化的塑料材料注入模具中,经过冷却固化后得到所需的塑料制品。
然而,在注塑过程中,可能会出现一些缺陷,影响产品的质量和性能。
本文将详细描述常见的注塑缺陷,并提供相应的解决方案。
一、缺陷描述1. 短射(Short Shot):指注塑过程中塑料未充满模具腔体,导致制品缺少某些部分或整体不完整。
解决方案:可能的原因包括模具温度过低、注塑速度过快、塑料材料不足等。
解决方法包括增加模具温度、调整注塑速度、增加塑料材料供给量等。
2. 翘曲(Warping):指注塑制品在冷却后产生变形,失去原本的平整形状。
解决方案:可能的原因包括模具温度不均匀、冷却时间不足、注塑压力过大等。
解决方法包括优化模具设计、增加冷却时间、减小注塑压力等。
3. 气泡(Air Traps):指注塑制品中出现气泡或空洞。
解决方案:可能的原因包括塑料材料中含有水分、注塑压力不稳定、模具排气不畅等。
解决方法包括使用干燥的塑料材料、调整注塑压力、改善模具排气系统等。
4. 热缩(Shrinkage):指注塑制品在冷却后出现尺寸缩小的现象。
解决方案:可能的原因包括模具温度过高、冷却时间不足、塑料材料收缩率不合理等。
解决方法包括降低模具温度、增加冷却时间、选择合适的塑料材料等。
5. 热裂纹(Hot Cracks):指注塑制品在冷却过程中出现裂纹。
解决方案:可能的原因包括注塑温度过高、冷却速度过快、塑料材料选择不当等。
解决方法包括降低注塑温度、控制冷却速度、选择合适的塑料材料等。
二、解决方案1. 优化模具设计:合理设计模具结构,确保充模充型均匀,避免短射、翘曲等缺陷的发生。
2. 控制注塑工艺参数:包括模具温度、注塑速度、注塑压力等。
通过调整这些参数,可以解决短射、翘曲、气泡等缺陷。
3. 选择合适的塑料材料:不同的塑料材料具有不同的性能和特点,选择合适的材料可以避免热缩、热裂纹等缺陷的发生。
4. 增加冷却时间:适当延长注塑制品的冷却时间,有助于避免翘曲、热缩等缺陷的产生。
注塑产品缺陷产生原因及处理方法(五篇模版)

注塑产品缺陷产生原因及处理方法(五篇模版)第一篇:注塑产品缺陷产生原因及处理方法注塑产品缺陷产生原因及处理方法在注塑成型加工过程中可能由于原料处理不好、制品或模具设计不合理、操作工没有掌握合适的工艺操作条件,或者因机械方面的原因,常常使制品产生注不满、凹陷、飞边、气泡、裂纹、翘曲变形、尺寸变化等缺陷。
对塑料制品的评价主要有三个方面,第一是外观质量,包括完整性、颜色、光泽等;第二是尺寸和相对位置间的准确性;第三是与用途相应的机械性能、化学性能、电性能等。
这些质量要求又根据制品使用场合的不同,要求的尺度也不同。
生产实践证明,制品的缺陷主要在于模具的设计、制造精度和磨损程度等方面。
但事实上,塑料加工厂的技术人员往往苦于面对用工艺手段来弥补模具缺陷带来的问题而成效不大的困难局面。
生产过程中工艺的调节是提高制品质量和产量的必要途径。
由于注塑周期本身很短,如果工艺条件掌握不好,废品就会源源不绝。
在调整工艺时最好一次只改变一个条件,多观察几回,如果压力、温度、时间统统一起调的话,很易造成混乱和误解,出了问题也不知道是何道理。
调整工艺的措施、手段是多方面的。
例如:解决制品注不满的问题就有十多个可能的解决途径,要选择出解决问题症结的一、二个主要方案,才能真正解决问题。
此外,还应注意解决方案中的辨证关系。
比如:制品出现了凹陷,有时要提高料温,有时要降低料温;有时要增加料量,有时要减少料量。
要承认逆向措施的解决问题的可行性。
1.6.1 塑料成型不完整这是一个经常遇到的问题,但也比较容易解决。
当用工艺手段确实解决不了时,可从模具设计制造上考虑进行改进,一般是可以解决的。
一、设备方面:(1)注塑机塑化容量小。
当制品质量超过注塑机实际最大注射质量时,显然地供料量是入不敷出的。
若制品质量接近注塑机实际注射质量时,就有一个塑化不够充分的问题,料在机筒内受热时间不足,结果不能及时地向模具提供适当的熔料。
这种情况只有更换容量大的注塑机才能解决问题。
注塑缺陷及其解决方法
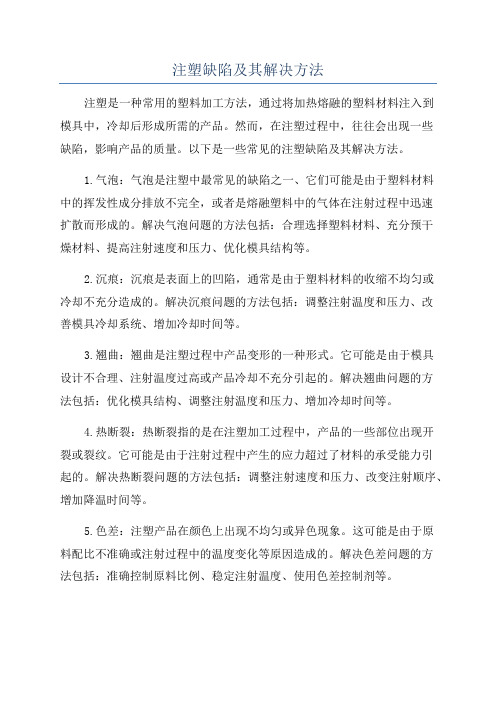
注塑缺陷及其解决方法注塑是一种常用的塑料加工方法,通过将加热熔融的塑料材料注入到模具中,冷却后形成所需的产品。
然而,在注塑过程中,往往会出现一些缺陷,影响产品的质量。
以下是一些常见的注塑缺陷及其解决方法。
1.气泡:气泡是注塑中最常见的缺陷之一、它们可能是由于塑料材料中的挥发性成分排放不完全,或者是熔融塑料中的气体在注射过程中迅速扩散而形成的。
解决气泡问题的方法包括:合理选择塑料材料、充分预干燥材料、提高注射速度和压力、优化模具结构等。
2.沉痕:沉痕是表面上的凹陷,通常是由于塑料材料的收缩不均匀或冷却不充分造成的。
解决沉痕问题的方法包括:调整注射温度和压力、改善模具冷却系统、增加冷却时间等。
3.翘曲:翘曲是注塑过程中产品变形的一种形式。
它可能是由于模具设计不合理、注射温度过高或产品冷却不充分引起的。
解决翘曲问题的方法包括:优化模具结构、调整注射温度和压力、增加冷却时间等。
4.热断裂:热断裂指的是在注塑加工过程中,产品的一些部位出现开裂或裂纹。
它可能是由于注射过程中产生的应力超过了材料的承受能力引起的。
解决热断裂问题的方法包括:调整注射速度和压力、改变注射顺序、增加降温时间等。
5.色差:注塑产品在颜色上出现不均匀或异色现象。
这可能是由于原料配比不准确或注射过程中的温度变化等原因造成的。
解决色差问题的方法包括:准确控制原料比例、稳定注射温度、使用色差控制剂等。
6.熔接线:熔接线是由于注塑模具的设计和操作问题导致两个或多个熔融塑料部分相互连接而形成的。
解决熔接线问题的方法包括:调整模具结构,避免部件交汇点过多,调整注射速度和压力等。
总之,注塑缺陷的解决方法主要包括调整材料配比、优化模具结构、控制注射温度和压力、增加冷却时间等。
同时,及时调整机器参数、进行模具维护和清洁,以保证注塑过程的稳定性和可靠性。
通过以上的措施,可以有效减少注塑缺陷,提高产品质量。
注塑缺陷描述及解决方案

注塑缺陷描述及解决方案引言概述注塑是一种常见的塑料加工方法,但在生产过程中常常会出现一些缺陷,影响产品质量和生产效率。
本文将介绍注塑缺陷的常见描述和解决方案。
一、短射1.1 描述:短射是指注塑成型时,塑料材料未充满模具腔体,导致产品表面或内部出现缺陷。
1.2 原因:可能是注射压力不足、模具温度不稳定、料斗内塑料不足等。
1.3 解决方案:增加注射压力、调整模具温度、确保料斗内塑料充足等。
二、气泡2.1 描述:气泡是指产品表面或内部出现的气体孔洞,影响产品的外观和性能。
2.2 原因:可能是注塑过程中塑料材料中含有水分、注射速度过快、模具排气不畅等。
2.3 解决方案:使用干燥塑料材料、减慢注射速度、改进模具结构以提高排气效果等。
三、热缩3.1 描述:热缩是指产品在冷却后尺寸缩小,导致尺寸不稳定或变形。
3.2 原因:可能是模具温度不均匀、冷却时间不足、塑料材料热胀冷缩系数不匹配等。
3.3 解决方案:调整模具温度均匀性、延长冷却时间、选择合适的塑料材料等。
四、毛刺4.1 描述:毛刺是指产品表面出现的细小突起,影响产品的外观和手感。
4.2 原因:可能是模具间隙过大、注射速度过快、模具表面粗糙等。
4.3 解决方案:调整模具间隙、减慢注射速度、提高模具表面光洁度等。
五、色差5.1 描述:色差是指同一批次产品颜色不一致,影响产品的整体美观度。
5.2 原因:可能是塑料材料颜色不均匀、注射温度不稳定、色母添加不均匀等。
5.3 解决方案:使用均匀颜色的塑料材料、稳定注射温度、充分混合色母等。
结论通过对注塑缺陷的描述和解决方案的介绍,可以有效提高注塑产品的质量和生产效率。
在实际生产中,需要根据具体情况采取相应的措施,及时解决问题,确保产品质量和客户满意度。
注塑常见缺陷及解决方法

注塑常见缺陷及解决方法1. 引言在注塑过程中,由于材料、设备、工艺等多种因素的影响,常常会出现一些缺陷。
这些缺陷不仅会影响产品的质量,还可能导致产品性能下降甚至无法使用。
因此,了解注塑常见缺陷及其解决方法对于提高产品质量至关重要。
2. 注塑常见缺陷2.1 短射短射是指注塑过程中,塑料无法充满模具腔体的情况。
造成短射的原因可能是模具设计不合理、注塑机参数设置不当等。
解决方法包括优化模具结构、增加注射压力等。
2.2 气泡气泡是注塑过程中常见的缺陷之一。
气泡的出现可能是由于塑料中含有气体、注塑过程中存在气体进入等原因。
解决方法包括在塑料中加入消泡剂、提高注射速度等。
2.3 热胀冷缩热胀冷缩是指注塑过程中,塑料在冷却过程中由于体积收缩而导致产生应力。
这种缺陷会导致产品变形、尺寸不稳定等问题。
解决方法包括优化模具结构、增加冷却时间等。
2.4 毛刺毛刺是指注塑制品表面出现的突起或凹陷。
毛刺的产生可能是由于模具表面不光滑、注塑过程中存在杂质等原因。
解决方法包括优化模具表面处理、提高注射速度等。
3. 注塑常见缺陷的解决方法3.1 优化模具结构优化模具结构是解决注塑常见缺陷的重要方法之一。
通过对模具的设计进行改进,可以减少短射、热胀冷缩等缺陷的发生。
3.2 控制注射参数注塑过程中的注射参数设置对于产品质量至关重要。
合理的注射压力、注射速度等参数可以有效地解决短射、气泡等缺陷。
3.3 加入添加剂在注塑过程中,可以加入一些添加剂来改善产品的性能。
例如,在塑料中加入消泡剂可以有效地解决气泡缺陷。
3.4 提高冷却时间热胀冷缩是注塑过程中常见的缺陷之一。
通过增加冷却时间,可以使塑料充分冷却,减少热胀冷缩导致的尺寸变化。
4. 结论注塑过程中常见的缺陷包括短射、气泡、热胀冷缩、毛刺等。
通过优化模具结构、控制注射参数、加入添加剂、提高冷却时间等方法,可以有效地解决这些缺陷,提高产品质量。
在实际生产中,需要根据具体情况选择合适的解决方法,并进行不断的改进和优化,以提高注塑产品的质量和竞争力。
注塑缺陷原因分析与解决方案

注塑缺陷原因分析与解决方案一、引言注塑是一种常用的塑料加工方法,广泛应用于各个行业。
然而,在注塑过程中,可能会出现一些缺陷,例如短斑、气泡、翘曲等问题,这些缺陷会影响产品质量和使用寿命。
因此,对注塑缺陷的原因进行分析,并提出相应的解决方案,对于提高产品质量具有重要意义。
二、注塑缺陷原因分析1. 温度控制不当:注塑过程中,温度是一个关键因素。
如果温度过高或过低,都会导致注塑缺陷。
例如,温度过高会导致熔融物流动性增加,易产生短斑;温度过低会导致熔融物流动性降低,易产生翘曲。
2. 压力控制不当:注塑过程中,压力也是一个重要因素。
如果压力过高或过低,都会导致注塑缺陷。
例如,压力过高会导致短斑、气泡等缺陷;压力过低会导致产品密度不足,易产生翘曲。
3. 注塑模具设计问题:注塑模具的设计也会影响产品质量。
如果模具设计不合理,例如流道设计不良、冷却系统不完善等,都会导致注塑缺陷的产生。
4. 塑料材料选择不当:不同的塑料材料具有不同的熔点、流动性等特性。
如果选择的塑料材料与产品要求不匹配,也会导致注塑缺陷。
例如,选择的塑料材料熔点过高,容易产生短斑;选择的塑料材料流动性不足,容易产生翘曲。
5. 操作人员技术水平不高:注塑过程需要操作人员具备一定的技术水平。
如果操作人员技术水平不高,不了解注塑工艺的要点,也会导致注塑缺陷的产生。
三、注塑缺陷解决方案1. 温度控制方案:合理控制注塑过程中的温度,根据塑料材料的特性和产品要求,调整熔融温度和模具温度。
可以通过使用温度传感器和温度控制器来实时监测和调整温度,确保温度在合适的范围内。
2. 压力控制方案:合理控制注塑过程中的压力,根据塑料材料的特性和产品要求,调整注射压力和保压压力。
可以通过使用压力传感器和压力控制器来实时监测和调整压力,确保压力在合适的范围内。
3. 注塑模具设计方案:优化注塑模具的设计,确保流道设计合理、冷却系统完善。
可以通过使用CAD软件进行模具设计和模拟分析,优化模具结构,减少缺陷的产生。
注塑常见缺陷及解决方法

注塑常见缺陷及解决方法
注塑是一种广泛应用于制造塑料制品的加工方法,但在实际生产中,由于原材料、工艺、设备等多种因素的影响,常常会出现各种缺陷。
下面是注塑常见缺陷及解决方法的详细介绍。
1. 气泡缺陷
气泡缺陷是注塑制品表面或内部存在的空洞或气泡。
一般由于原料过热、注模压力过高、模具进料不足等原因引起。
解决方法:降低原料温度、减小注射速度、增加进料量、调整模型温度、调整模具结构等。
2. 热胀冷缩缺陷
热胀冷缩缺陷是指塑料制品在注塑时由于热胀冷缩现象而导致的尺寸不稳定的现象。
解决方法:合理选择原材料、调整注塑工艺参数、改变模具结构、加入夹层等。
3. 毛刺缺陷
毛刺缺陷是指注塑制品表面出现的刺状物或毛细孔。
可能是由于模具设计不合理、注塑工艺不当、原材料污染等原因引起。
解决方法:调整模具设计、调整注塑工艺参数、更换清洗原材料。
4. 热裂缺陷
热裂缺陷是指塑料制品在注塑过程中由于温度过高而导致的开裂。
通常是由于原材料性能不佳、注塑工艺参数设置不当等原因引起。
解决方法:更换高品质的原材料、调整注塑工艺参数。
5. 毛边缺陷
毛边缺陷是指塑料制品表面出现的毛边或切口。
通常是由于模具设计不合理、注塑工艺参数不当、原材料品质差等原因引起。
解决方法:调整模具设计、调整注塑工艺参数、更换清洗原材料。
注塑制品的质量直接影响到其使用寿命和市场竞争力。
因此,在注塑生产中,应该重视并及时解决各种缺陷问题。
通过合理优化原材料、模具设计和注塑工艺参数等措施,不仅可以提高注塑制品的质量,还可以降低生产成本,提高企业的经济效益。
注塑缺陷原因分析与解决方案

注塑缺陷原因分析与解决方案引言概述:注塑是一种常见的制造工艺,用于生产各种塑料制品。
然而,在注塑过程中,常常会出现一些缺陷,如短射、气泡、翘曲等问题,影响产品的质量和性能。
本文将分析注塑缺陷的原因,并提出相应的解决方案,以帮助企业提高产品质量和生产效率。
正文内容:1. 原材料选择不当1.1. 塑料材料质量不稳定:不同批次的塑料材料可能存在成分差异,导致注塑过程中的缺陷。
1.2. 塑料材料含水量过高:过高的含水量会导致注塑过程中产生气泡、短射等缺陷。
2. 注塑工艺参数不合理2.1. 注射速度过快:过快的注射速度容易造成短射、气泡等缺陷。
2.2. 注射压力不足:不足的注射压力会导致产品翘曲、尺寸不准确等问题。
2.3. 注射温度不当:过高或过低的注射温度都会影响产品的质量,如翘曲、缩水等缺陷。
3. 模具设计问题3.1. 模具结构不合理:模具的结构设计不合理会导致产品的翘曲、尺寸不准确等缺陷。
3.2. 模具表面处理不当:模具表面的处理不当会导致产品出现划痕、气泡等问题。
4. 注塑机设备问题4.1. 注射机压力不稳定:注射机压力的不稳定会导致产品尺寸不准确、表面不光滑等缺陷。
4.2. 注射机温度控制不准确:温度控制不准确会导致产品翘曲、缩水等问题。
5. 操作人员技术不熟练5.1. 操作不规范:不规范的操作会导致产品尺寸不准确、表面不光滑等缺陷。
5.2. 操作技术不熟练:操作人员对注塑机设备和工艺参数不熟悉,无法及时调整,导致产品质量下降。
总结:通过分析注塑缺陷的原因,我们可以得出以下解决方案:首先,选择稳定的塑料材料,并控制好含水量。
其次,合理调整注塑工艺参数,控制注射速度、压力和温度。
再次,优化模具设计,确保结构合理,表面处理良好。
同时,保证注塑机设备良好的运行状态,调整好注射机压力和温度控制。
最后,加强操作人员的培训和技术水平,确保规范操作,熟练掌握注塑机设备和工艺参数的调整。
通过以上的分析和解决方案,企业可以有效地解决注塑过程中的缺陷问题,提高产品质量和生产效率。
注塑缺陷及解决方法

注塑缺陷及解决方法注塑缺陷及解决方法一设备方面:(1)供料不足。
(2)换料时机筒未清洗干净。
二模具方面:(1)浇口太小或流道太细。
(2)型腔表面粗糙度差。
(3)排气不良或模温过低。
(4)没有冷料井。
三工艺方面:(1)机筒加热不均匀、机筒温度过高或过低。
(2)喷嘴太小或预塑背压太低。
(3)注射速度过大或过小。
(4)塑化不均匀。
四原料方面:(1)原料未干燥处理。
(2)含有挥发性物质。
(3)助剂或脱模剂用量过多。
1.6.11 脱模困难(浇口或塑件紧缩在模具内)一设备方面:顶出力不够。
二模具方面:(1)脱模结构不合理或位置不当。
(2)脱模斜度不够。
(3)模温过高或通气不良。
(4)浇道壁或型腔表面粗糙。
(5)喷嘴与模具进料口吻合不服帖或喷嘴直径大于进料口直径。
三工艺方面:(1)机筒温度太高或注射量太多。
(2)注射压力太高或保压及冷却时间长。
四原料方面:润滑剂不足。
1.6.12 翘曲变形一模具方面:(1)浇口位置不当或数量不足。
(2)顶出位置不当或制品受力不均匀。
二工艺方面:(1)模具、机筒温度太高。
(2)注射压力太高或注射速度太快。
(3)保压时间太长或冷却时间太短。
三原料方面:酞氰系颜料会影响聚乙烯的结晶度而导致制品变形。
四制品设计方面:(1)壁厚不均,变化突然或壁厚过小。
(2)制品结构造型不当。
1.6.13 尺寸不稳定一设备方面:(1)加料系统不正常。
(2)背压不稳或控温不稳。
(3)液压系统出现故障。
二模具方面:(1)浇口及流道尺寸不均。
(2)型腔尺寸不准。
三工艺方面:(1)模温不均或冷却回路不当而致模温控制不合理。
(2)注射压力低。
(3)注射保压时间不够或有波动。
(4)机筒温度高或注射周期不稳定。
四原料方面:(1)换批生产时,树脂性能有变化。
(2)物料颗粒大小无规律。
(3)含湿量较大。
(4)更换助剂对收缩律有影响。
1.6.14 龟裂汽白《注塑缺陷及解决方法》。
注塑缺陷描述及解决方案
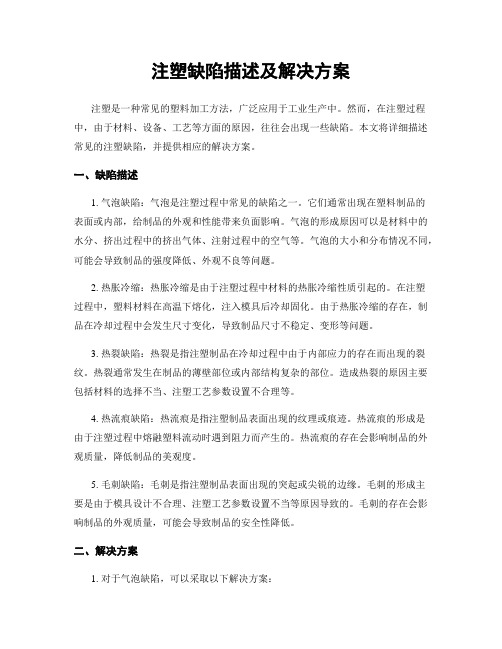
注塑缺陷描述及解决方案注塑是一种常见的塑料加工方法,广泛应用于工业生产中。
然而,在注塑过程中,由于材料、设备、工艺等方面的原因,往往会出现一些缺陷。
本文将详细描述常见的注塑缺陷,并提供相应的解决方案。
一、缺陷描述1. 气泡缺陷:气泡是注塑过程中常见的缺陷之一。
它们通常出现在塑料制品的表面或内部,给制品的外观和性能带来负面影响。
气泡的形成原因可以是材料中的水分、挤出过程中的挤出气体、注射过程中的空气等。
气泡的大小和分布情况不同,可能会导致制品的强度降低、外观不良等问题。
2. 热胀冷缩:热胀冷缩是由于注塑过程中材料的热胀冷缩性质引起的。
在注塑过程中,塑料材料在高温下熔化,注入模具后冷却固化。
由于热胀冷缩的存在,制品在冷却过程中会发生尺寸变化,导致制品尺寸不稳定、变形等问题。
3. 热裂缺陷:热裂是指注塑制品在冷却过程中由于内部应力的存在而出现的裂纹。
热裂通常发生在制品的薄壁部位或内部结构复杂的部位。
造成热裂的原因主要包括材料的选择不当、注塑工艺参数设置不合理等。
4. 热流痕缺陷:热流痕是指注塑制品表面出现的纹理或痕迹。
热流痕的形成是由于注塑过程中熔融塑料流动时遇到阻力而产生的。
热流痕的存在会影响制品的外观质量,降低制品的美观度。
5. 毛刺缺陷:毛刺是指注塑制品表面出现的突起或尖锐的边缘。
毛刺的形成主要是由于模具设计不合理、注塑工艺参数设置不当等原因导致的。
毛刺的存在会影响制品的外观质量,可能会导致制品的安全性降低。
二、解决方案1. 对于气泡缺陷,可以采取以下解决方案:a. 在材料加工前,对原料进行干燥处理,以减少材料中的水分含量。
b. 在注塑过程中,控制好挤出和注射过程中的温度和压力,避免产生气泡。
c. 优化模具设计,合理设置通气孔,以便将气泡排出。
2. 对于热胀冷缩问题,可以采取以下解决方案:a. 在模具设计中考虑材料的热胀冷缩性质,合理设置模具尺寸和结构,以减少尺寸变化。
b. 控制注塑过程中的温度和冷却时间,避免过快的冷却导致热胀冷缩问题。
常见注塑缺陷及解决方案

注塑缺陷原因分析与解决方案一、变形/翘曲( Warpage )塑胶件产生翘曲变形,导致制品的效或引起尺寸误差和装配困难;翘曲变形是塑件最严重的质量缺陷之一。
变形产生原因:1、材料:物料收缩率大,如PA+GF的收缩率就很大,流动玻纤取向。
2、模具:(1)产品两侧,型腔与型芯间温度差异较大;(2)模具冷却水路位置分配不均匀,没有对温度很好地进行控制;(3)浇口方式和位置设计不合理,特别加纤料,流动规则很重要;(4)产品粘模引起变形,顶出不平衡导致变形;(5)模具排气不佳,导致模腔内注塑压力大。
3、成型工艺:(1)注塑压力过高或者注射速度过大;(2)料筒温度、熔体温度过高;(3)保压时间过长或冷却时间过短;(4)尚未充分冷却就顶出,由于顶针对表面施压造成翘曲变形。
4、产品结构(1)长条形结构翘曲加剧;(2)产品结构不对称导致不同收缩;(3)产品壁厚不均匀,突变或过薄,导致薄壁部分冷却较快引起翘曲。
解决方案:主要应从产品和模具设计方面着手解决,而依靠成型工艺调整的效果是非常有限的。
1、材料:(1)选择收缩性较小的材料,内部的长条形纤维会顺着流动方向发生取向。
沿着取向方向收缩小、垂直取向方向收缩大,取向引起的收缩不均会导致产品变形;(2)如PA66或PA+GF料都容易变形,评估时特别注意,提前做模流分析。
2、产品结构和模具:(1)由于塑胶从熔体转变为固体体积必然收缩,厚度大收缩大,厚度小收缩相对也小,收缩不均产生的内应力导致产品变形。
只能通过优化产品设计,尽量使产品壁厚均匀;(2)模具的冷却系统设计合理,使得产品能够冷却均匀平衡,控制模芯与模腔的温差。
(3)合理确定浇口位置及浇口类型,可以较大程度上减少产品的变形,一般情况下,可采用多点式浇口,在评估阶段多做几种模流分析方案来验证最小变形;(4)模具设计合理,确定合理的拔模斜度,顶针位置和数量,检查和校正模芯,提高模具的强度和定位精度;(5)改善模具的排气功能。
注塑缺陷原因分析与解决方案

注塑缺陷原因分析与解决方案一、引言注塑是一种常见的塑料加工方法,广泛应用于各个行业。
然而,在注塑过程中往往会浮现一些缺陷,如短射、气泡、热缩等。
本文将对注塑缺陷的原因进行分析,并提出相应的解决方案,以匡助企业提高产品质量和生产效率。
二、注塑缺陷原因分析1. 短射短射是指注塑过程中无法将塑料彻底填充模具腔体的现象。
短射的原因可能包括以下几点:- 模具设计不合理:模具的流道设计不合理或者过小,导致塑料无法充分流动。
- 注塑参数设置不当:注塑机的注射速度、压力等参数设置不当,影响了塑料的充填性能。
- 塑料材料选择不当:选择的塑料材料流动性差,导致无法充分填充模具腔体。
2. 气泡气泡是指注塑制品中浮现的气体会萃的现象。
气泡的原因可能包括以下几点:- 塑料材料含水量高:塑料材料含水量高会在注塑过程中产生蒸汽,形成气泡。
- 注塑机排气不畅:注塑机排气系统不畅,无法及时排出注塑过程中产生的气体。
- 模具设计不合理:模具中存在死角或者过小的通气孔,导致气体无法顺利排出。
3. 热缩热缩是指注塑制品在冷却后发生尺寸变化的现象。
热缩的原因可能包括以下几点:- 注塑温度过高:注塑温度过高会导致塑料在冷却后收缩过大。
- 模具温度不均匀:模具的温度分布不均匀,导致注塑制品冷却不均匀,进而引起热缩。
- 塑料材料热性能不稳定:选择的塑料材料热性能不稳定,导致注塑制品在冷却后发生尺寸变化。
三、注塑缺陷解决方案1. 短射解决方案- 模具设计合理化:优化模具的流道设计,增加流道的截面积,确保塑料能够充分流动。
- 注塑参数优化:根据塑料材料的特性,合理设置注塑机的注射速度、压力等参数,保证塑料充填模具腔体。
- 选择合适的塑料材料:根据产品的要求,选择流动性好的塑料材料,提高充填性能。
2. 气泡解决方案- 塑料材料干燥处理:在注塑过程前,对塑料材料进行干燥处理,降低含水量,减少气泡的产生。
- 注塑机排气系统改进:优化注塑机的排气系统,增加排气孔的数量和大小,提高排气效果。
注塑工艺 注塑成型缺陷分析及不良解决对策
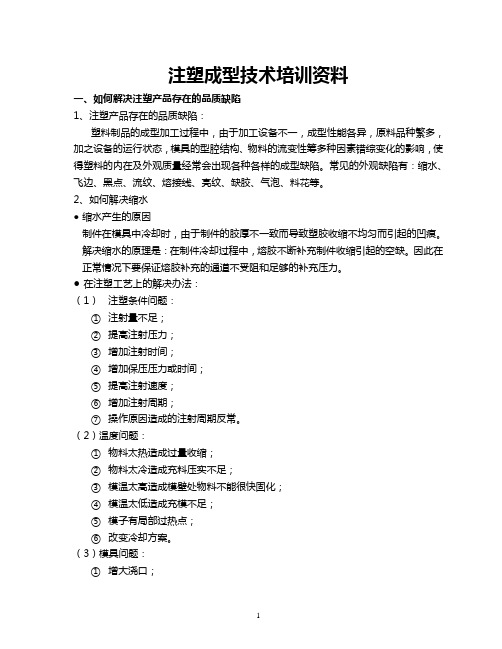
注塑成型技术培训资料一、如何解决注塑产品存在的品质缺陷1、注塑产品存在的品质缺陷:塑料制品的成型加工过程中,由于加工设备不一,成型性能各异,原料品种繁多,加之设备的运行状态,模具的型腔结构、物料的流变性筹多种因素错综变化的影响,使得塑料的内在及外观质量经常会出现各种各样的成型缺陷。
常见的外观缺陷有:缩水、飞边、黑点、流纹、熔接线、亮纹、缺胶、气泡、料花等。
2、如何解决缩水●缩水产生的原因制件在模具中冷却时,由于制件的胶厚不一致而导致塑胶收缩不均匀而引起的凹痕。
解决缩水的原理是:在制件冷却过程中,熔胶不断补充制件收缩引起的空缺。
因此在正常情况下要保证熔胶补充的通道不受阻和足够的补充压力。
●在注塑工艺上的解决办法:(1)注塑条件问题:①注射量不足;②提高注射压力;③增加注射时间;④增加保压压力或时间;⑤提高注射速度;⑥增加注射周期;⑦操作原因造成的注射周期反常。
(2)温度问题:①物料太热造成过量收缩;②物料太冷造成充料压实不足;③模温太高造成模壁处物料不能很快固化;④模温太低造成充模不足;⑤模子有局部过热点;⑥改变冷却方案。
(3)模具问题:①增大浇口;②增大分流道;③增大主流道;④增大喷嘴孔;⑤改进模子排气;⑥平衡充模速率;⑦避免充模料流中断;⑧浇口进料安排在制品厚壁部位;⑨如果有可能,减少制品壁厚差异;⑩模子造成的注射周期反常。
(4)设备问题:①增大注压机的塑化容量;②使注射周期正常;(5)冷却条件问题:①部件在模内冷却过长,避免由外往里收缩,缩短模子冷却时间;②将制件在热水中冷却。
3、如何解决飞边●产生飞边的原因:产品溢边往往由于模子的缺陷造成,其他原因有:注射力大于锁模力、物料温度太高、排气不足、加料过量、模子上沾有异物等。
●如何判断产生飞边的原因:在一般情况下,采用短射的办法。
即在注塑压力速度较低、不用保压的情况下注塑出制件90%的样板,检查样板是否出现飞边,如果出现,则是模具没有配好或注塑机的锁模压力不足,如果没有出现,则是由于注塑条件变化而引起的飞边,比如:保压太大、注射速度太快等。
注塑缺陷原因分析及改善对策
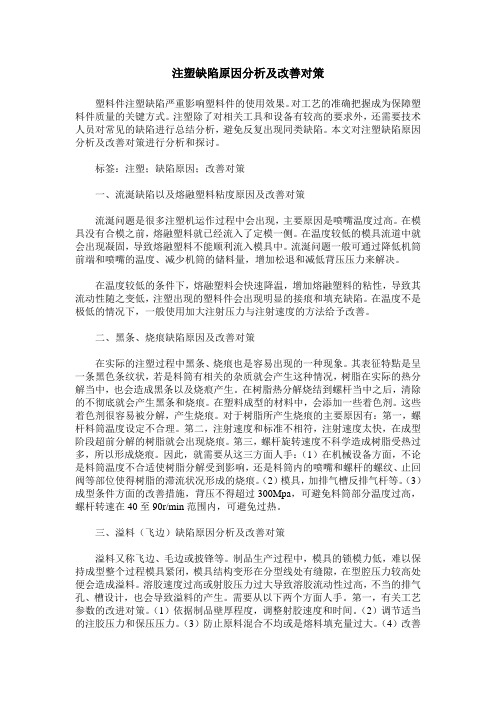
注塑缺陷原因分析及改善对策塑料件注塑缺陷严重影响塑料件的使用效果。
对工艺的准确把握成为保障塑料件质量的关键方式。
注塑除了对相关工具和设备有较高的要求外,还需要技术人员对常见的缺陷进行总结分析,避免反复出现同类缺陷。
本文对注塑缺陷原因分析及改善对策进行分析和探讨。
标签:注塑;缺陷原因;改善对策一、流涎缺陷以及熔融塑料粘度原因及改善对策流涎问题是很多注塑机运作过程中会出现,主要原因是喷嘴温度过高。
在模具没有合模之前,熔融塑料就已经流入了定模一侧。
在温度较低的模具流道中就会出现凝固,导致熔融塑料不能顺利流入模具中。
流涎问题一般可通过降低机筒前端和喷嘴的温度、减少机筒的储料量,增加松退和减低背压压力来解决。
在温度较低的条件下,熔融塑料会快速降温,增加熔融塑料的粘性,导致其流动性随之变低,注塑出现的塑料件会出现明显的接痕和填充缺陷。
在温度不是极低的情况下,一般使用加大注射压力与注射速度的方法给予改善。
二、黑条、烧痕缺陷原因及改善对策在实际的注塑过程中黑条、烧痕也是容易出现的一种现象。
其表征特點是呈一条黑色条纹状,若是料筒有相关的杂质就会产生这种情况,树脂在实际的热分解当中,也会造成黑条以及烧痕产生。
在树脂热分解烧结到螺杆当中之后,清除的不彻底就会产生黑条和烧痕。
在塑料成型的材料中,会添加一些着色剂。
这些着色剂很容易被分解,产生烧痕。
对于树脂所产生烧痕的主要原因有:第一,螺杆料筒温度设定不合理。
第二,注射速度和标准不相符,注射速度太快,在成型阶段超前分解的树脂就会出现烧痕。
第三,螺杆旋转速度不科学造成树脂受热过多,所以形成烧痕。
因此,就需要从这三方面人手:(1)在机械设备方面,不论是料筒温度不合适使树脂分解受到影响,还是料筒内的喷嘴和螺杆的螺纹、止回阀等部位使得树脂的滞流状况形成的烧痕。
(2)模具,加排气槽反排气杆等。
(3)成型条件方面的改善措施,背压不得超过300Mpa,可避免料筒部分温度过高,螺杆转速在40至90r/min范围内,可避免过热。
注塑缺陷原因分析与解决方案

注塑缺陷原因分析与解决方案一、引言注塑工艺是一种常用的塑料加工方法,广泛应用于各个领域。
然而,在注塑过程中,常常会出现一些缺陷,如气泡、翘曲、短射等问题,严重影响产品的质量和性能。
因此,对注塑缺陷的原因进行分析,并提出相应的解决方案,对于提高产品质量和生产效率具有重要意义。
二、注塑缺陷的原因分析1. 模具设计不合理:模具是注塑过程中的关键因素之一,模具的设计不合理会导致产品缺陷。
例如,模具中存在过于复杂的结构、不合理的冷却系统等,都可能引起产品的翘曲、短射等问题。
2. 塑料材料选择不当:不同的塑料材料具有不同的物理性能和熔融特性,选择不当会导致产品缺陷。
例如,选择的塑料材料熔点过高或过低,都会影响产品的成型效果。
3. 注塑工艺参数设置错误:注塑工艺参数的设置对于产品质量至关重要。
例如,注射压力、注射速度、保压时间等参数的设置不当,都会导致产品的缺陷,如气泡、短射等。
4. 模具磨损和老化:长时间使用的模具会出现磨损和老化现象,导致产品的尺寸精度下降。
此外,模具的使用寿命过长也会影响产品质量。
5. 注塑设备故障:注塑设备的故障也是导致产品缺陷的原因之一。
例如,注射机的温度控制不准确、压力控制不稳定等,都会对产品的成型效果产生影响。
三、注塑缺陷的解决方案1. 模具设计优化:通过对模具的结构进行优化设计,减少复杂结构的使用,合理设计冷却系统,可以有效降低产品缺陷的发生率。
2. 塑料材料选择合理:根据产品的要求和特性选择合适的塑料材料,确保其熔融特性和物理性能与产品的要求相匹配。
3. 注塑工艺参数优化:通过合理设置注塑工艺参数,如注射压力、注射速度、保压时间等,控制好温度和压力的变化,可以提高产品的成型效果。
4. 定期维护和更换模具:定期对模具进行维护,及时更换磨损和老化的部件,可以保证模具的精度和使用寿命,提高产品的质量。
5. 定期检查和维护注塑设备:定期检查注塑设备的温度控制、压力控制等系统,确保其正常工作,减少设备故障对产品质量的影响。
注塑缺陷原因分析与解决方案

注塑缺陷原因分析与解决方案引言概述:注塑工艺是一种常见的制造工艺,广泛应用于各个行业。
然而,在注塑过程中,常常会出现一些缺陷,如短射、气泡、翘曲等问题。
本文将从原因分析和解决方案两个方面,详细介绍注塑缺陷及其解决方法。
一、短射问题1.1 原因分析:短射是指注塑制品在充模过程中未能完全填充模腔,导致制品出现不完整或缺陷。
其主要原因包括:1.1.1 注射速度过快:过快的注射速度会导致熔融塑料在进入模腔之前已经开始凝固,从而无法完全填充模腔。
1.1.2 模具温度不合适:模具温度过低会导致塑料熔融不完全,无法充分填充模腔。
1.1.3 压力不足:注塑机的射胶压力不足会导致塑料无法充分填充模腔。
1.2 解决方案:针对短射问题,可以采取以下解决方案:1.2.1 调整注射速度:根据具体情况,适当调整注射速度,以确保塑料能够完全填充模腔。
1.2.2 控制模具温度:通过调整模具温度,确保塑料能够充分熔融,提高注塑质量。
1.2.3 增加射胶压力:适当增加注塑机的射胶压力,以保证塑料能够充分填充模腔。
二、气泡问题2.1 原因分析:气泡是注塑制品中常见的缺陷之一,其主要原因包括:2.1.1 塑料中含有气体:在塑料加工过程中,如果塑料中含有气体,会在注塑过程中形成气泡。
2.1.2 注射过程中的气体:注射过程中,如果注射速度过快,会产生气泡。
2.1.3 模具温度不稳定:模具温度不稳定会导致塑料熔融不均匀,从而产生气泡。
2.2 解决方案:针对气泡问题,可以采取以下解决方案:2.2.1 塑料预处理:在注塑前对塑料进行预处理,去除其中的气体,以减少气泡的产生。
2.2.2 控制注射速度:控制注射速度,避免过快注射导致气泡产生。
2.2.3 稳定模具温度:通过控制模具温度,确保塑料能够充分熔融,减少气泡的产生。
三、翘曲问题3.1 原因分析:翘曲是指注塑制品在冷却后出现变形或弯曲的现象,其主要原因包括:3.1.1 冷却不均匀:冷却不均匀会导致注塑制品不均匀收缩,从而产生翘曲。
- 1、下载文档前请自行甄别文档内容的完整性,平台不提供额外的编辑、内容补充、找答案等附加服务。
- 2、"仅部分预览"的文档,不可在线预览部分如存在完整性等问题,可反馈申请退款(可完整预览的文档不适用该条件!)。
- 3、如文档侵犯您的权益,请联系客服反馈,我们会尽快为您处理(人工客服工作时间:9:00-18:30)。
构启闭阀芯。
喷嘴的选择应根据加工的塑料性能及成型 制品的特点来考虑。
注射成型机规格表示
1.注射容积表示法 例如: XS-ZY500即表示该机属塑料(S)成型机(X)
类,螺杆式(Y)注射机(Z),机器的注射容积 为500 cm3 。
2.合模力表示法 :
15 SZ6300/1000 1070
135
40.4
175.4
16 SZ8000/1000 1200
135
40.4
175.4
备注
宁波海天 集团生产 (注塑中心
在用)
S Z系 列
注塑机的选择
主要考虑三个方面:
1.塑件的重量:应是≤注塑机额定最大注塑量的80%,≥注 塑机额定最大注塑量的30%。 2.塑件垂直于注塑方向最大投影面积×零件确定的单位面积模 内压力(公斤/平方厘米)≤80%的注塑机最大额定锁模力。 3.模具的外形尺寸:(长、宽、高)
由上可知,注塑材料能否通过注塑工艺,成为 合格零件取决于下列因素:
1.设计因素:选材是否合理、结构是否合理,尺寸精度是 否合理。
2.设备因素:设备的大小,参数控制的精度与稳定性如何。
3.模具因素:型腔排列及数量,流道形式(热、冷),浇 口形式,冷却水道布局,顶出方式,分型面的确定,抽芯 机构形式,模具材料及热处理表面处理。
15
8.25
23.25
10 SZ-300/160
145
18.5
9.25
27.75
11 SZ500/200
173
22
15.55 37.55
12 SZ-1000/300 325
37
24.5
61.5
13 SZ-2500/500 570
40
28.1
68.1
14 SZ-4000/800 770
110
40.4
150.4
15
9.3
24.3
3 HTF200X1
18.5
12.45 32.75
4
SZ-25/20
35
7.5
2.6
10.1
5
SZ-40/25
50
7.5
4.5
12
6
SZ-60/40
70
11
4.7
15.7
7
SZ-100/80
95
11
6
17
8 SZ-160/100
105
15
7.25
22.25
9 SZ-200/120
120
3.注射容积与合模力共同表示法例如: SZ-200/120即表示塑料注射机(SZ),理论注
射容积为200cm3,合模力为120(KN)
塑料注射成型机的功率参数
序号
型号
注射速 油泵电机 电热功 总功率 率(g / s) 功率(K W) 率(K W) (K W)
1
HTF86X1
11
5.7
17.2
2 HTF160X1
注塑机构
螺杆:螺杆式注射机的重要部件。 作用:对粒料进行输送、加热及机械搅拌、压实、塑化和施压注射。
螺杆在料筒内旋转时,首先将料斗来的塑料卷入料筒内,并逐 步由螺杆将其向前推送、压实、排气和塑化,熔融的塑料不断地被 推送至螺杆头部与喷嘴之间,螺杆本身受熔体的反作用力而缓慢后 退,当料筒头部积存的塑料熔体达到一次注射量时,螺杆停止转 动,接着螺杆被液压或机械力推动向前,将熔体注射进入模内。
2、塑料零件质量缺陷的成因
形成塑料零件质量缺陷的因素有下列方面: 1、原料缺陷 2、设计缺陷 3、加工设备缺陷 4、模具缺陷 5、加工工艺缺陷
下面就上述五个方面有重点的加以阐述(其中 设计缺陷已在塑料零件设计概论一文中已有阐述 不再讨论)。特别是在注塑加工工艺方面。
3、注塑机结构、动作原理介绍
注塑设备是注塑工艺的基础,要了解注塑工艺就必须了解注塑机 的结构及动作原理:
类型:
(1)直通式喷嘴
正常喷嘴,呈短管状,压力和热量损失小,不 易产生滞料和分解,不用附设加热装置。
延伸式喷嘴(可看作是正常喷嘴的加长型), 需添设加热装置。适合加工高粘度塑料。
(2)自锁式喷嘴
防止熔料的流涎或回缩,对喷嘴通道实行 暂时封锁。
弹簧式自锁喷嘴: 依靠弹簧压合喷嘴体内的阀芯来实现封
锁,有效地杜绝流涎现象。
锁模机构
锁模机构具有调模及锁模功能: 其动作功能是:装模、调模、试锁模、试注射、再调模、再注
射直至调模合格。
前
调模机构
动模装在动模板 定模装在定模板
喷嘴是联结料筒和模具的桥梁:
其作用是:
注射时引导料筒内的塑料进入模具,由于喷嘴 的内孔自进口逐渐向出口收敛,可使塑料融体流 速剧增,并因此具备了相应零件所需的工艺射程。
注塑机的基本作用:
1.加热塑料,使其达到熔融状态; 2.对熔融塑料施加高压,以注射的形式充满模具型腔,并在冷 却后将塑件推出型腔,形成合格的塑料零件。
注塑成型的工艺过程:
特点:一次成型外形复杂,尺寸精确、带有嵌件的制品,适 应性强,生产效率高。易于全自动化生产,经济、先进。
注射成型工艺具体描述:经干燥的塑料原料(粒料)加入料 斗,粒料从料斗进入加热的料筒,旋转的螺杆将进入螺纹槽内 的粒料边搅拌边推进向前,经逐级加热进入料筒前端,至熔融 状态后,在螺杆的推动下经喷嘴注入闭合的塑模中,充满塑模 的熔料在受压的状态下,经冷却(热塑性塑料)或加热(热固 性塑料)固化后,保持注塑模型腔所赋予的形状,打开模具取 出制品,由此完成一个模塑周期。
4.工艺因素:材料是否预热去湿,预塑加料量,温度,时 间,压力等参数控制是否合理,注塑速度,螺杆转速,顶 出速度,背压调节是否合理,是否需要整形及后处理等等。
5.良好的沟通与协调:产品设计,模具设计,注塑工艺, 表面处理,检测试验等相关部门间沟通与协调十分必要。
6.特殊注塑工艺的采用:如气体辅助,蒸汽辅助注塑等。
注塑工艺陷及对策
培训讲义 沈平
1、注塑工艺概述
注塑(注射)成型是塑料加工行业,最主要的 加工方式之一,它是使用原料厂家,专门为注塑 行业生产的,由设计人员选定的有机高分子材料。
使用专用设备(注塑机),采用针对特定零件设 计的模具(注塑模),在特定的工艺条件下(温 度、时间、注塑压力、速度),将高分子材料在 粘流态下压入注塑模,材料在模内凝固冷却定型 后出模,或经二次加工成为合格零件的过程,称 为注塑成型工艺过程。
注塑机的锁模力:
其定义为:合模终结熔料注入模腔时,注塑机模板对模具形 成的最终锁紧力。是注塑机最常用的参数之一。锁模力不足时 会产生“飞边(披锋)”。
选机型时应确保制品加工所需锁紧力,小于机器的锁模力。 锁紧力通常用型腔内平均压力与模腔投影面积的乘积来计算。 其中型腔内平均压力一般取20—40Mpa,具体要根据塑料特性、 制品要求、制品流长比等因素来确定。