华北铝,常用铝箔品种退火工艺
铝箔退火热处理工艺的介绍
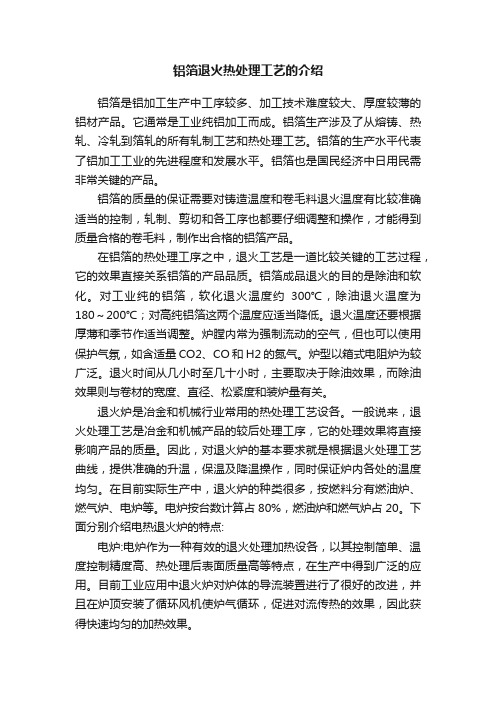
铝箔退火热处理工艺的介绍铝箔是铝加工生产中工序较多、加工技术难度较大、厚度较薄的铝材产品。
它通常是工业纯铝加工而成。
铝箔生产涉及了从熔铸、热轧、冷轧到箔轧的所有轧制工艺和热处理工艺。
铝箔的生产水平代表了铝加工工业的先进程度和发展水平。
铝箔也是国民经济中日用民需非常关键的产品。
铝箔的质量的保证需要对铸造温度和卷毛料退火温度有比较准确适当的控制,轧制、剪切和各工序也都要仔细调整和操作,才能得到质量合格的卷毛料,制作出合格的铝箔产品。
在铝箔的热处理工序之中,退火工艺是一道比较关键的工艺过程,它的效果直接关系铝箔的产品品质。
铝箔成品退火的目的是除油和软化。
对工业纯的铝箔,软化退火温度约300℃,除油退火温度为180~200℃;对高纯铝箔这两个温度应适当降低。
退火温度还要根据厚薄和季节作适当调整。
炉膛内常为强制流动的空气,但也可以使用保护气氛,如含适量CO2、CO和H2的氮气。
炉型以箱式电阻炉为较广泛。
退火时间从几小时至几十小时,主要取决于除油效果,而除油效果则与卷材的宽度、直径、松紧度和装炉量有关。
退火炉是冶金和机械行业常用的热处理工艺设各。
一般说来,退火处理工艺是冶金和机械产品的较后处理工序,它的处理效果将直接影响产品的质量。
因此,对退火炉的基本要求就是根据退火处理工艺曲线,提供准确的升温,保温及降温操作,同时保证炉内各处的温度均匀。
在目前实际生产中,退火炉的种类很多,按燃料分有燃油炉、燃气炉、电炉等。
电炉按台数计算占80%,燃油炉和燃气炉占20。
下面分别介绍电热退火炉的特点:电炉:电炉作为一种有效的退火处理加热设各,以其控制简单、温度控制精度高、热处理后表面质量高等特点,在生产中得到广泛的应用。
目前工业应用中退火炉对炉体的导流装置进行了很好的改进,并且在炉顶安装了循环风机使炉气循环,促进对流传热的效果,因此获得快速均匀的加热效果。
现在电加热退火炉的自动化控制系统技术已经达到了很高的水平,对于温度的准确控制、工艺的检测、自动化的控制等方面相比其他炉子有很大的优势,主要体现在以下几点:1、温度精密控制:辉达工控设计的智能电炉温度控制系统采用集成温度PID调节电路、可控硅及触发电路等一体化的KY系列智能温度控制器,一体化安装,带RS485通讯功能,,分别对每控温区进行温度控制,可满足0-1300℃温度范围内0.5%的控温精度。
退火工艺
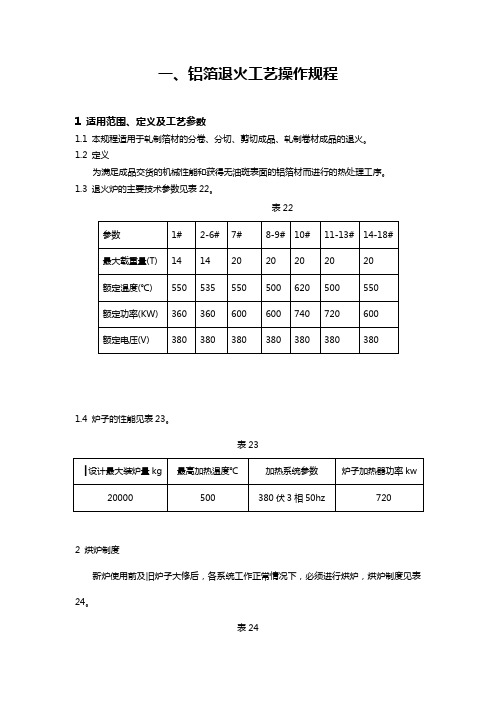
一、铝箔退火工艺操作规程1 适用范围、定义及工艺参数1.1 本规程适用于轧制箔材的分卷、分切、剪切成品、轧制卷材成品的退火。
1.2 定义为满足成品交货的机械性能和获得无油斑表面的铝箔材而进行的热处理工序。
1.3 退火炉的主要技术参数见表22。
表221.4 炉子的性能见表23。
表232 烘炉制度新炉使用前及旧炉子大修后,各系统工作正常情况下,必须进行烘炉,烘炉制度见表24。
表243 操作前准备3.1 接料时按生产卡片核对退火箔卷的合金牌号、状态、批号、规格及数量,•并检查有无碰伤、划伤、串层,发现问题及时解决。
3.2 装炉前应按顺序记录好各卷的批号、合金、规格及重量,避免出炉时混料。
3.3 同炉退火的铝箔按要求放在料架或料筐上。
3.4 工件测温采用外径230mm左右,宽度300mm左右的铝卷模拟块。
工件热电偶插在该卷端部距外圆10-20mm处,深度要求20-30mm。
装炉前要采用凉透的模拟块并检查热电偶是否插紧,以及有无破损情况,确认完好时方可装炉。
要求每炉必须安放四根工件热电偶,两根备用。
3.5 开动前应仔细检查加热系统、冷却系统、保护气体发生系统以及仪表等是否正常和安全,确认正常后方可随炉升温。
3.6 每次装炉前,应将炉内以及风机口所剩铝屑及脏物清除干净,否则不能装炉。
4 炉子操作4.1 各批料的退火均为装炉后随炉升温。
4.2 成品退火加热时炉子发生故障或因停电等原因,炉料在炉子停留时间不超过1小时可以补充加热时间,如果超过1小时则应重新退火。
4.3 装炉后炉门放下时,开启上下开启装置,放下后应开动炉门压紧装置。
4.4 调整炉子定温,当温度快达到要求时,应改定温,调到要求温度下恒温,且在此温度下进行保温,并应每小时检查一次各仪表控制情况,做好记录以免仪表失灵而跑温或引起损坏,如有异常,及时找有关人员解决。
4.5 当保温达到要求时间后,开动冷却装置,使其按工艺降到要求出炉的温度后方可出炉。
4.6 出炉时应停电,启动炉门,装卸料车速度应平稳、缓慢,以防炉料因冲击而损伤。
一种2a12铝合金分级退火热处理工艺

一种2a12铝合金分级退火热处理工艺2a12铝合金是一种高强度铝合金,常用于航空航天、汽车制造和机械制造等领域。
为了进一步提高其性能,可以采用分级退火热处理工艺。
分级退火是一种通过不同温度和时间的热处理过程,使合金材料达到理想的力学性能和显微组织结构的方法。
对2a12铝合金进行分级退火热处理,可以提高其强度和塑性,并改善其耐蚀性和耐疲劳性能。
在制备2a12铝合金材料时,需要选择合适的原料和控制合金元素的含量。
然后,将合金材料进行预处理,包括去除氧化皮、清洗和除杂等步骤,以确保材料的纯净度和表面质量。
接下来,将2a12铝合金材料进行固溶处理,即将材料加热至固溶温度,保持一段时间后迅速冷却。
固溶处理的目的是将合金元素溶解在固溶体中,消除合金材料中的析出物和晶界相,并提高其塑性。
然后,对固溶处理后的2a12铝合金进行分级退火处理。
分级退火的温度和时间要根据所需的力学性能进行精确控制。
一般来说,分级退火温度较低,时间较长,可以获得较高的强度和较好的塑性。
在分级退火过程中,合金材料首先经过过饱和固溶处理,使固溶体中的合金元素溶解度超过平衡状态。
然后,将材料冷却到较低温度,使合金元素析出形成细小的沉淀相。
这些沉淀相可以有效地阻碍晶界滑移和晶内滑移,提高材料的强度和硬度。
对分级退火处理后的2a12铝合金进行时效处理,即将材料加热至适当的温度,保持一段时间后迅速冷却。
时效处理可以进一步增强材料的强度和硬度,并提高其耐蚀性和耐疲劳性能。
2a12铝合金的分级退火热处理工艺可以显著提高其力学性能和耐蚀性能。
通过精确控制温度和时间参数,可以获得适合不同应用领域的合金材料。
这种工艺在航空航天、汽车制造和机械制造等领域具有广泛的应用前景。
(完整版)常用铝合金去应力退火热处理工艺规范
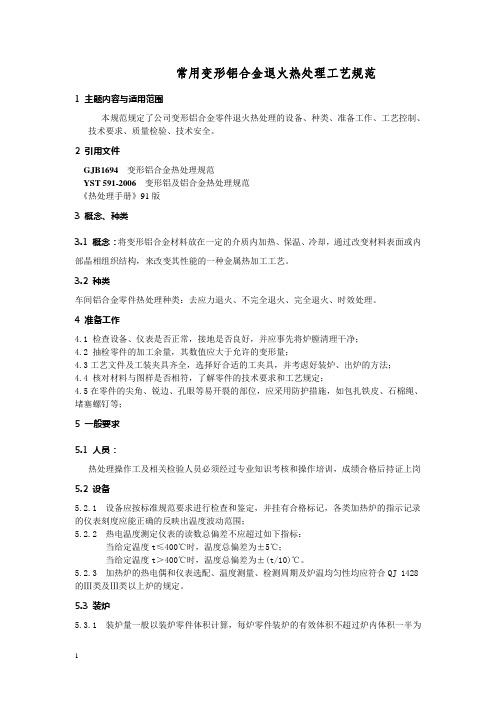
常用变形铝合金退火热处理工艺规范1 主题内容与适用范围本规范规定了公司变形铝合金零件退火热处理的设备、种类、准备工作、工艺控制、技术要求、质量检验、技术安全。
2 引用文件GJB1694变形铝合金热处理规范YST 591-2006变形铝及铝合金热处理规范《热处理手册》91版3 概念、种类3.1 概念:将变形铝合金材料放在一定的介质内加热、保温、冷却,通过改变材料表面或内部晶相组织结构,来改变其性能的一种金属热加工工艺。
3.2 种类车间铝合金零件热处理种类:去应力退火、不完全退火、完全退火、时效处理。
4 准备工作4.1 检查设备、仪表是否正常,接地是否良好,并应事先将炉膛清理干净;4.2 抽检零件的加工余量,其数值应大于允许的变形量;4.3工艺文件及工装夹具齐全,选择好合适的工夹具,并考虑好装炉、出炉的方法;4.4 核对材料与图样是否相符,了解零件的技术要求和工艺规定;4.5在零件的尖角、锐边、孔眼等易开裂的部位,应采用防护措施,如包扎铁皮、石棉绳、堵塞螺钉等;5 一般要求5.1 人员:热处理操作工及相关检验人员必须经过专业知识考核和操作培训,成绩合格后持证上岗5.2 设备5.2.1 设备应按标准规范要求进行检查和鉴定,并挂有合格标记,各类加热炉的指示记录的仪表刻度应能正确的反映出温度波动范围;5.2.2 热电温度测定仪表的读数总偏差不应超过如下指标:当给定温度t≤400℃时,温度总偏差为±5℃;当给定温度t>400℃时,温度总偏差为±(t/10)℃。
5.2.3 加热炉的热电偶和仪表选配、温度测量、检测周期及炉温均匀性均应符合QJ 1428的Ⅲ类及Ⅲ类以上炉的规定。
5.3 装炉5.3.1 装炉量一般以装炉零件体积计算,每炉零件装炉的有效体积不超过炉内体积一半为准。
5.3.2 零件装炉时,必须轻拿轻放,防止零件划伤及变形。
5.3.3堆放要求:a.厚板零件允许结合零件结构特点,允许装箱入炉进行热处理,叠放时允许点及较少的线接触,避免面接触,叠放间隙不小于10mm.b.厚度t≤3mm的板料以夹板装夹,叠放厚度≤25mm,零件及夹板面无污垢、凸点,零件间、零件与夹板间应垫一层雪花纸,以防止零件夹伤。
铝件退火工艺

铝件退火工艺铝件退火工艺是一种常见的金属加工方法,通过加热和冷却的过程,提高铝件的强度和可塑性。
本文将从铝件退火的原理、工艺步骤、应用领域和优势等方面进行介绍。
一、铝件退火的原理铝件退火是利用金属的晶格结构和组织状态的变化,通过控制加热和冷却过程来改变铝件的性能。
当铝件加热到一定温度时,晶格结构发生变化,内部应力得到释放,晶界得到改善,从而提高铝件的塑性和韧性。
二、铝件退火的工艺步骤1. 清洗:将铝件表面的油污、灰尘等杂质清除干净,以保证退火过程中的热传导效果。
2. 加热:将铝件放入加热炉中,提高温度至退火温度,通常在400-500摄氏度之间。
3. 保温:将铝件保持在退火温度下一段时间,以保证铝件内部温度均匀,晶格结构得到充分改善。
4. 冷却:将铝件从退火炉中取出,放置在自然环境中冷却至室温,或者通过水冷等方式加速冷却。
5. 清洗:将退火后的铝件进行清洗,去除表面的氧化物和残留物。
三、铝件退火的应用领域铝件退火广泛应用于航空航天、汽车制造、电子设备等领域。
在航空航天领域,铝件退火可以提高零件的强度和韧性,保证航天器在复杂环境中的可靠运行;在汽车制造领域,铝件退火可以改善零件的塑性,提高汽车的安全性能;在电子设备领域,铝件退火可以提高散热效果,延长电子产品的使用寿命。
四、铝件退火的优势1. 提高铝件的强度和可塑性,使其更加适合加工和使用。
2. 改善铝件的晶界结构,减少晶界的应力集中和断裂风险。
3. 降低铝件的残余应力,提高铝件的稳定性和耐久性。
4. 优化铝件的表面质量,提高产品的外观和精度。
铝件退火工艺是一种重要的金属加工方法,通过控制加热和冷却过程,改变铝件的晶格结构和组织状态,提高其性能和应用价值。
在实际应用中,我们可以根据具体需求和材料特性,选择合适的退火温度和时间,以获得最佳效果。
铝件退火工艺的发展和应用将进一步推动铝合金材料的性能提升和工业技术的进步。
铝板带退火工艺
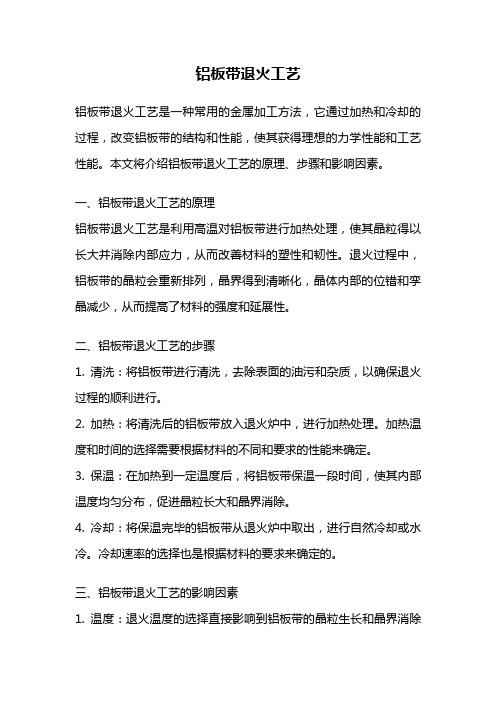
铝板带退火工艺铝板带退火工艺是一种常用的金属加工方法,它通过加热和冷却的过程,改变铝板带的结构和性能,使其获得理想的力学性能和工艺性能。
本文将介绍铝板带退火工艺的原理、步骤和影响因素。
一、铝板带退火工艺的原理铝板带退火工艺是利用高温对铝板带进行加热处理,使其晶粒得以长大并消除内部应力,从而改善材料的塑性和韧性。
退火过程中,铝板带的晶粒会重新排列,晶界得到清晰化,晶体内部的位错和孪晶减少,从而提高了材料的强度和延展性。
二、铝板带退火工艺的步骤1. 清洗:将铝板带进行清洗,去除表面的油污和杂质,以确保退火过程的顺利进行。
2. 加热:将清洗后的铝板带放入退火炉中,进行加热处理。
加热温度和时间的选择需要根据材料的不同和要求的性能来确定。
3. 保温:在加热到一定温度后,将铝板带保温一段时间,使其内部温度均匀分布,促进晶粒长大和晶界消除。
4. 冷却:将保温完毕的铝板带从退火炉中取出,进行自然冷却或水冷。
冷却速率的选择也是根据材料的要求来确定的。
三、铝板带退火工艺的影响因素1. 温度:退火温度的选择直接影响到铝板带的晶粒生长和晶界消除的程度。
过高或过低的温度都会对材料的性能产生不良影响。
2. 保温时间:保温时间的长短决定了铝板带内部温度的均匀性和晶粒长大的程度。
过短的保温时间可能导致晶粒生长不充分,过长的保温时间则会造成能源浪费。
3. 冷却速率:冷却速率对铝板带的组织和性能也有重要影响。
过快的冷却速率可能导致材料内部的残余应力,从而影响材料的强度和韧性。
4. 材料本身:不同材料的退火工艺参数会有所不同,需要根据具体材料的特性来确定合适的工艺参数。
总结:铝板带退火工艺是一种重要的金属加工工艺,通过加热和冷却的过程,可以改善铝板带的力学性能和工艺性能。
在实际应用中,需要根据具体材料的要求,选择合适的退火温度、保温时间和冷却速率,以获得理想的退火效果。
通过合理的铝板带退火工艺,可以使材料具有更好的塑性和韧性,提高其可加工性和使用寿命。
铝箔热处理工艺特点进行真空退火炉的选择

铝箔热处理工艺特点进行真空退火炉的选择书山有路勤为径,学海无涯苦作舟铝箔热处理工艺特点进行真空退火炉的选择铝是一种延展性极佳的金属,经过多次冷轧、合卷、精轧、切边及退火后制成厚度低于0.2 mm 铝箔成品。
铝箔厚度可低至0.004mm,宽度可达2m,卷径在1.5m 左右。
有良好导热性及导电性,在导磁性及防辐射方面表现良好,因而在电力电容器、电缆、家电及医药、香烟、装饰、包装等行业广泛应用。
铝箔为成卷供货,胚料经冷轧及合卷等工序后,必须进行软化退火处理,以消除压延过程中产生的应力,提高拉伸时柔韧性和均匀性,消除开卷时的跑偏率。
铝箔在制造过程中,工艺上采用全油润滑保护,成品对除油有严格控制。
而真空退火具有脱脂及除气作用,能去除残留油脂,因此可显著提高产品质量。
铝与氧具有极高的化学亲和力,在室温下能形成致密的Al2O3 保护膜,由于氧成分在中高真空中仅为0.5%左右,烘烤后可低至0.1%~0.01%,因此可有效防止氧化膜或化合物生成。
同时,在真空炉中处理,能得到光亮表面,且炉温加热均匀,工件变形小,节能无污染等优点,特别对一些活泼金属的热处理尤为适用。
因此铝箔在真空中退火比采用其他热处理方法具有明显优势。
根据铝箔热处理工艺特点进行炉型选择由于铝箔是成卷状态,其热处理要求缓慢加热,慢速冷却。
铝的熔点为660.24 ℃,热膨胀系数(20~100℃)为23.8 乘以10-6/K。
控制铝箔表面与心部温差以减少热应力成为热处理的关键。
真空加热具有升温缓慢、受热均匀、热应力小等特点。
真空状态下, 假如仅靠辐射方式传热,根据斯蒂芬-波尔兹曼定律: 辐射传热能量与绝对温度四次方成正比,因此加热传导速度慢,尤其在低温,加热传导速度更慢,尽管炉子本身升温很快,但被加热工件依然升温缓慢,同时工件不同部位受热不均温差大,工件表面和心部温差也大,加热变形增大。
当通入惰性保。
6061退火工艺

6061退火工艺6061铝合金是一种常用的铝合金材料,具有良好的可加工性、可焊性和耐腐蚀性。
退火是一种常见的热处理工艺,可以改善6061铝合金的力学性能和物理性能。
本文将介绍6061退火工艺的具体步骤和效果。
6061铝合金的退火工艺一般包括两个步骤:预热和保温。
预热是将铝合金材料加热到一定温度,以减少应力和改善可加工性。
保温是在一定温度下保持一段时间,使材料内部的组织发生变化,从而改善其力学性能和物理性能。
首先是预热步骤。
将6061铝合金材料放入炉中,将炉温逐渐升高到约200℃。
预热温度应根据具体合金的成分和要求来确定,一般在150℃至250℃之间。
预热的目的是将材料加热到足够的温度,以减少应力和改善可加工性。
在预热后,进入保温步骤。
将预热后的6061铝合金材料保持在一定温度下,一般保温时间为1至2小时。
保温温度也需要根据具体要求来确定,一般在400℃至500℃之间。
保温的目的是使材料内部的组织发生变化,从而改善其力学性能和物理性能。
6061铝合金经过退火后,其力学性能和物理性能都会有所改善。
首先是强度方面,退火后的6061铝合金的抗拉强度和屈服强度会有所降低,但延伸率和冲击韧性会有所提高。
这是因为退火过程中,材料内部的应力得到释放,晶粒变得更加均匀,从而使材料更加韧性和可塑性。
其次是物理性能方面,退火后的6061铝合金的硬度和强度会有所降低,但电导率和导热性能会有所提高。
这是因为退火过程中,材料内部的晶粒得到再结晶,晶粒尺寸变大,从而导致材料的硬度和强度降低,但晶粒界面的电导路径和热传导路径增加,从而提高了电导率和导热性能。
需要注意的是,6061铝合金的退火工艺需要根据具体要求来确定。
不同的应用领域和要求可能需要不同的退火温度和时间。
此外,退火后的6061铝合金还需要进行后续处理,如冷却和时效处理,以进一步改善其性能。
6061退火工艺是一种常用的热处理工艺,可以改善6061铝合金的力学性能和物理性能。
铝合金退火温度和时间

铝合金退火温度和时间铝合金是一种常见的金属材料,其具有优异的机械性能和良好的可成形性。
但是,在加工过程中,经常需要进行热处理,以满足不同的工艺要求。
其中,退火是一种较为常见的热处理方法,在不同的退火温度和时间下,铝合金材料的性能表现也有所不同。
本文将就铝合金退火温度和时间进行详细介绍。
一、退火温度对铝合金的影响在铝合金的热处理过程中,温度是一个非常重要的参数,不同的温度会对铝合金的各项性能产生不同的影响。
下面是一些常见退火温度对铝合金的影响:1.低温退火(200-300℃)在低温下,铝合金的强度会有所下降,硬度也会减小,但同时屈服强度和延展性会有所提高,这是因为温度较低,材料中的应力得到了充分的松弛。
因此,在某些需要延展性更好的场合,低温退火是一种非常有效的处理手段。
2.中温退火(400-500℃)在中温退火的条件下,铝合金的强度和硬度将会有所下降,延展性和塑性则会有所提升。
但是,在这个温度范围内,铝合金的晶粒尺寸也会逐渐增大,这对于材料的稳定性和均匀性都是不利的。
3.高温退火(500℃以上)高温退火可以将铝合金材料中的晶界松弛,从而进一步提升延展性和塑性,适合于加工性要求较高的场合。
但是,若退火温度过高,晶粒尺寸将进一步增大,就会出现烧结现象,这将导致铝合金材料的强度和硬度不断下降。
二、不同时间对铝合金的影响在铝合金的退火过程中,时间也是一个极其重要的参数。
下面是简要介绍不同退火时间对铝合金材料的影响:1.短时间退火短时间的退火(如1小时),可以有效地改善铝合金的加工性,有利于成型和机械加工,同时能提高材料的韧性和塑性。
2.长时间退火长时间的退火(如8小时以上),可以使晶粒继续生长和沉积,这会对铝合金的强度和硬度产生不利的影响。
但是,长时间的退火却能够进一步提高材料的韧性、塑性,同时也有利于材料的稳定性和综合性能。
三、结论综上所述,铝合金的退火温度和时间对于材料的性能表现都有着非常重要的影响。
铝箔退火工艺的选择

铝箔退火工艺的选择所谓退火制度,即退火工艺参数,指的是退火过程中的加热速度,加热温度,保温时间、冷却速度等,在生产条件下,铝箔退火制度是根据退火炉的结构和生产能力、装炉量的大小和铝箔在炉内的放置方法以及对铝箔性能的要求来确定的。
1、加热速度所谓加热速度一般是指单位时间内所升高的温度,在退火工艺参数中,加热速度似乎是个不足轻重的参数,但不能很好的根据不同情况选择合适的加热速度,对产品的质量、炉子的利用率、及生产周期都有可能带来不良影响。
确定加热速度所要考虑的因素如下:(1)炉量装炉量越大,即炉料越多,则若要保持各部分温度均匀,使产品的性能均匀一致,就需要较长的均热时间,因而加热速度应相应的慢一些,反之,若装炉量少时,加热速度可适当提高。
(2)铝箔规格的大小从理论上讲铝箔的宽度越宽卷径越大热传导性越差,则加热速度就应相应的慢一些,这是因为,体积大,导热性不好的铝箔,若其加热速度太快,有可能造成铝箔中心部位与表面温度差别太大,由于热涨冷缩的原因,使得铝箔中心部位与表面的体积变化有很大差异,因而会产生很大的热应力,从而造成铝箔热鼓变形等不良后果。
(3)晶粒度快速加热易于得到细小均匀的再结晶组织,3021合金的清水箔在退火过程中极易出现晶粒不均匀现象,(局部位置晶粒十分粗大),其原因同铸锭组织中锰偏析有直接关系。
晶粒四周和晶内锰浓度的差异,扩大了再结晶温度区间,降低了生核率,从而容易产生粗晶,防止这种现象的措施之一,就是快速加热。
3021合金退火时,晶粒组织对加热速度是敏感的。
快速加热可缩小再结晶区间。
使间界和晶内同时生核,因而容易获得细小均匀的晶粒组织。
(4)缓慢的加热速度有利于防止铝箔粘连。
(5)生产效率从生产效率来考虑,加热速度应越快越好,在实际生产中,退火过程中的加热时间约占整个退火周期的1/3---1/5左右(利乐及建筑用箔除外)。
因此,加热速度对退火生产效率的影响是不可忽视的,但提高加热速度应在兼顾上述几个因素的基础上进行。
铝及铝合金的热处理退火处理

铝及铝合金的热处理退火处理
铝及铝合金的热处理退火处理
目的:
展伸用材料包括压延用材料,挤压用材料及锻造用材料,通常其制造程序为:
熔铸→热加工→冷加工→材料成品
在热加工或冷加工的过程中,材料发生加工硬化的情况,使强度变大或导致加工硬化的情况,使强度变大或导致加工性减低。
为消除这些加工硬化,于冷加工前,中或后所施的热处理即为退火处理,其目的在使材料具有使用上所需要的程度。
分类:
由于退火条件的不同而分:
1、部分退火:
仅消除部份加工硬化,处理温度在再结晶温度以下,实际温度则视强度而定,强度愈高则处理温度较低。
2、完全退火:
处理温度在材料的再结晶温度或稍高使材料发生再结晶而完全消除加工硬化,亦使强度达到最低的状态。
退火处里就时机而分:
1、中间退火:
再冷加工开始之前或冷加工过程中,所加的退火处理,通常为完全退火,其目的在恢复其加工性,使接下去的加功能较顺利,及控制其组织状态,俾能适合于最终成品的要求。
2、最终退火:
主要目的再调整成品最后的强度水平亦即调整炼度。
-1/1-。
国产高纯铝箔最终退火工艺对表面立方织构度的影响

・17・摘要本文主要研究了再结晶退火工艺对国产高纯铝箔表面立织构度的影响。
研究结果表明:改变退火工艺能够提高铝箔表面的立方织构度,在400℃左右短时间退火能够获得较高的立方织构度,继续提高温度或延长保温时间立方织构度几乎不再改变。
关键词高压阳极箔;退火;立方织构度中图法分类号TG 1560前言铝箔表面的立方织构度(Cube T exture ,简称CT )是指箔表面立方取向((100)<001>)的晶粒所占比例,它是衡量铝电解电容器用高压箔性能的一个重要指标[1,2],高的立方织构度是获得高比容的前提[3],进口退火箔能够达到85%~95%,而国产箔(使用厂家退火)仅能达到60%左右[4]。
国内电容器厂家用箔大部分依靠进口。
进口一吨高压箔需要一万美元,一吨国产箔只需人民币六万元。
国内高压箔的研究重点就是国产化。
目前国内的研究侧重于腐蚀形成工艺,忽视了对铝箔退火工艺的研究,导致在生产中,高压箔都采用高温长时间退火工艺(580℃×18h ),既降低生产效率,又浪费能源。
本文主要研究国产高压箔的再结晶退火工艺对微观结构的影响。
1试验条件和方法1.1试验材料试验材料见表1。
表1试验材料及成分1.2退火工艺将铝箔裁成50 ×20 试样,在氩气保护下退火,设备为高温定硫定碳炉。
加热前对炉膛进行排气4m in ,氩气流量为1L/m in ,正常升温过程中,氩气流量0.5L/m in ,用DRE -2型电阻炉温度控制器控温,T DG C5/05型调压器调节加热速率。
保温结束后停气随炉冷至200℃以下,取出试样置于干燥器内备用。
具体退火工艺如下:1.采用B 、C 、D 三种箔分别在250℃、270℃、300℃、320℃、350℃、360℃、370℃、380℃、400℃、450℃、500℃保温60m in ,加热功率均为60V ×8A ,研究退火温度的影响。
2.采用B 、C 两种铝箔试验,研究退火保温时间的影响。
铝材退火工艺规程

1.3~2.99
3t以下
200℃/3h+490℃/3h+400℃/3h
3t以上
200℃/3h+510℃/3h+400℃/3h
≥3.0
3t以下
200℃/3h+510℃/3h+400℃/3h
3t以上
200℃/3h+520℃/3h+400℃/3h
H24
0.2~1.9
200℃/3h+370℃/3h+300℃/4h
2.3 5052退火制度
状态
厚度mm
重量
工艺制度
O
0.2~1.9
3t以下
200℃/3h+450℃/5h+380℃/2h
3t以上
200℃/3h+460℃/5h+380℃/2h
1.3~2.99
3t以下
200℃/3h+460ቤተ መጻሕፍቲ ባይዱ/5h+380℃/2h
3t以上
200℃/3h+460℃/5h+380℃/3h
220℃/4h+350℃/4h+280℃/5h
4t以上
220℃/4h+350℃/4h+290℃/5h
O
0.2~1.9
3t以下
200℃/3h+460℃/4h+400℃/3h
3t以上
200℃/3h+480℃/4h+400℃/3h
1.3~2.99
3t以下
200℃/3h+480℃/5h+400℃/3h
3t以上
3t以下
5a02退火工艺
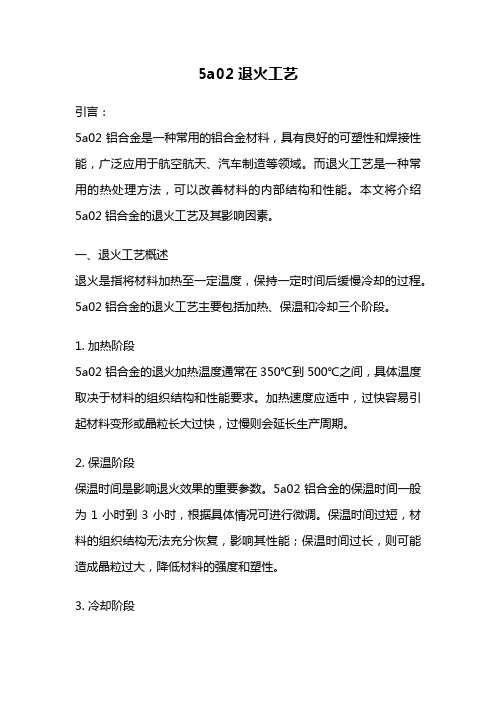
5a02退火工艺引言:5a02铝合金是一种常用的铝合金材料,具有良好的可塑性和焊接性能,广泛应用于航空航天、汽车制造等领域。
而退火工艺是一种常用的热处理方法,可以改善材料的内部结构和性能。
本文将介绍5a02铝合金的退火工艺及其影响因素。
一、退火工艺概述退火是指将材料加热至一定温度,保持一定时间后缓慢冷却的过程。
5a02铝合金的退火工艺主要包括加热、保温和冷却三个阶段。
1. 加热阶段5a02铝合金的退火加热温度通常在350℃到500℃之间,具体温度取决于材料的组织结构和性能要求。
加热速度应适中,过快容易引起材料变形或晶粒长大过快,过慢则会延长生产周期。
2. 保温阶段保温时间是影响退火效果的重要参数。
5a02铝合金的保温时间一般为1小时到3小时,根据具体情况可进行微调。
保温时间过短,材料的组织结构无法充分恢复,影响其性能;保温时间过长,则可能造成晶粒过大,降低材料的强度和塑性。
3. 冷却阶段退火后的材料需要进行缓慢冷却,以充分消除内部应力,保证材料的性能稳定。
一般采用空冷或水冷的方式进行冷却,具体根据材料的尺寸和要求来选择。
冷却速度过快可能导致材料变形或开裂,冷却速度过慢则会影响生产效率。
二、影响因素5a02铝合金的退火工艺受多种因素影响,以下是几个重要的影响因素:1. 温度退火温度是影响材料性能的关键因素之一。
温度过低无法使材料充分软化,温度过高则容易引起晶粒长大过快。
因此,选择合适的退火温度对于保证材料的性能至关重要。
2. 保温时间保温时间决定了材料的组织结构和性能恢复的程度。
保温时间过短,材料的晶粒和组织结构无法充分恢复;保温时间过长,则可能造成晶粒长大过大,影响材料的性能。
因此,保温时间的控制需要根据具体材料和要求来确定。
3. 冷却方式退火后的材料需要进行适当的冷却,以消除内部应力并保证材料的性能稳定。
根据材料的尺寸和要求,可以选择空冷或水冷的方式进行冷却。
冷却速度过快可能导致材料变形或开裂,过慢则会降低生产效率。
铝线退火工艺
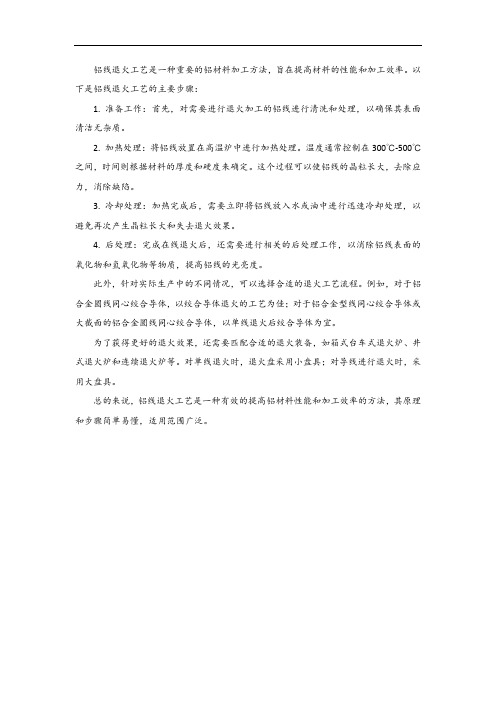
铝线退火工艺是一种重要的铝材料加工方法,旨在提高材料的性能和加工效率。
以下是铝线退火工艺的主要步骤:
1. 准备工作:首先,对需要进行退火加工的铝线进行清洗和处理,以确保其表面清洁无杂质。
2. 加热处理:将铝线放置在高温炉中进行加热处理。
温度通常控制在300℃-500℃之间,时间则根据材料的厚度和硬度来确定。
这个过程可以使铝线的晶粒长大,去除应力,消除缺陷。
3. 冷却处理:加热完成后,需要立即将铝线放入水或油中进行迅速冷却处理,以避免再次产生晶粒长大和失去退火效果。
4. 后处理:完成在线退火后,还需要进行相关的后处理工作,以消除铝线表面的氧化物和氢氧化物等物质,提高铝线的光亮度。
此外,针对实际生产中的不同情况,可以选择合适的退火工艺流程。
例如,对于铝合金圆线同心绞合导体,以绞合导体退火的工艺为佳;对于铝合金型线同心绞合导体或大截面的铝合金圆线同心绞合导体,以单线退火后绞合导体为宜。
为了获得更好的退火效果,还需要匹配合适的退火装备,如箱式台车式退火炉、井式退火炉和连续退火炉等。
对单线退火时,退火盘采用小盘具;对导线进行退火时,采用大盘具。
总的来说,铝线退火工艺是一种有效的提高铝材料性能和加工效率的方法,其原理和步骤简单易懂,适用范围广泛。