酚醛尿烷树脂自硬砂配制及制做
派普使用指南

酚尿烷快速自硬树脂使用指南一、HA酚尿烷快速自硬树脂简介酚基尿烷自硬树脂系统由三个组分组成。
其粘结剂由两个组分组成,PZ-Ⅰ为聚苯醚酚基树脂,PZ-Ⅱ为聚异氰酸脂。
当这两个组分结合时,酚基树脂中的羥基与聚异氰酸脂中的异氰酸根发生反应生成尿烷树脂。
由于这个反应进行得非常缓慢,须加入第三组分即PZ-Ⅲ催化剂(液态胺)来促进,其反应速度在30秒至数十分钟可随意调整。
酚基尿烷树脂除具有其他自硬砂的优点外还具有以下特点:1)提高生产率:由于其反应速度快速,可调性强。
利于组织生产,易于形成流水线规模生产。
2)反应滞后:酚基尿烷树脂砂混好后,在“工作时间”内基本无反应,给制芯造型留有充分的时间,在此时间内砂的流动性好,可生产紧实度高的型芯。
3)高比值工作时间/脱模时间:其比值可达0.8(而呋喃自硬树脂为0.45)制芯完成后可迅速脱模,可大大提高生产率。
4)良好的强度建立模式:本系统无反应中间生成物(水)反应时砂芯内外同时进行,所以脱模后强度均匀不变形,型芯质量良好。
二、原材料砂:须用擦洗硅砂,以○-□为好。
SiO2含量:铸钢>97%;铸铁>90%。
目数根据需要一般铸钢为40-70目;铸铁为50-100目。
粉尘含量<0.5%;水分<0.2%。
砂的适宜温度为23-34℃。
砂的酸碱度以中性砂为好(PH7-8)。
树脂PZ-Ⅰ/PZ-Ⅱ为50/50—60/40,随着PZ-Ⅰ递增PZ-Ⅱ递减,终强度略有下降,但防气孔和毛刺作用加强。
树脂加入量(PZ-Ⅰ+PZ-Ⅱ)可按产品需要而定大约为0.8-2.5%(占砂重)。
催化剂(PZ-Ⅲ)可根据气候、温度而选用不同的型号,冬季潮冷天气使用PZ-Ⅲ3595,加入量为0.8-2.5%(占PZ-Ⅰ)。
春秋温暖季节使用PZ-Ⅲ3550,加入量为1-4%(占PZ-Ⅰ)。
夏季干热使用3500,加入量为2-5%(占PZ-Ⅰ)。
三、配砂将称好的PZ-Ⅲ加入PZ-Ⅰ中搅拌均匀,干砂加入混砂机中,开机运转后将含有PZ-Ⅲ的PZ-Ⅰ加入砂中。
碱酚醛树脂自硬砂

碱性酚醛树脂自硬砂的一些特性英国Borden公司首先开发了有机酯硬化的碱性酚醛树脂自硬砂工艺,并于1981年获得专利,简称a--Set工艺。
其主要特点是混砂、造型、浇注时散发的烟气少,有利于改善环境。
所用的树脂是甲阶酚醛树脂的一种,但含有KOH、NaOH等碱性材料,故通常称之为碱性酚醛树脂。
树脂中的游离的K 、Na。
离子,对于树脂与有机酯发生作用、树脂的交联反应都至关重要。
多种低级酯都可作为硬化剂,应用较广的是碳酸丙烯酯,这也是作用较强的硬化剂。
还可用几种有机酯混合配成作用强弱不同的牌号,以适用于不同的生产条件。
一.树脂的硬化机制在树脂的硬化反应中,首先是树脂中的碱与酯反应,形成碱金属的碳酸盐,释放醇。
树脂中的碱形成碳酸盐后,即处于反应状态,可在常温下发生交联反应,将砂粒粘结,使型砂具有必要的强度。
由于作为硬化剂有机酯是参与树脂硬化反应的组分,不同于硬化剂只起催化作用、不参与反应的其他树脂自硬砂,不能通过改变硬化剂的加入量来调整自硬砂的硬化速率和起模时间。
有机酯的加入量一般为树脂的20~25 ,因树脂和硬化剂的品种而略不同。
树脂加入量不足,则铸型难以硬化;树脂加入量太高,则会感到混成砂和砂型腻滑,而且可能导致铸型一金属界面处发生反应,影响铸件表面质量。
自硬砂的硬化速率和起模时间,应由改变硬化剂的牌号予以调整。
有机酯硬化的酚醛树脂砂,在有机酯的作用下,树脂在常温下只发生部分交联反应,起模时型砂仍然保持一定的塑性,浇注初期还有一短暂的、因受热而再次发生交联反应的过程,也就是通常所说的二次硬化。
二.碱性酚醛树脂自硬砂工艺的优点碱性酚醛树脂自硬砂工艺主要有以下优点。
1.混砂、造型、浇注时散发的烟气少于以酸为硬化剂的呋喃树脂砂、以酸为硬化剂的甲阶酚醛树脂砂和以胺为硬化剂的尿烷树脂砂。
2.由于起模时型砂仍然保持一定的塑性,故起模性能好,型砂不易粘附在模具上,砂型表面比较光洁,模样上的起模斜度也可较小。
3.二次硬化后,砂型的热稳定性较好,厚壁铸件表面上也很少出现脉状纹缺陷。
砂芯制造工艺与技术

醛树脂作粘结剂,配制的型(芯)砂叫做覆膜砂像干砂一样松散。
其制壳的方法有两种:翻斗法和吹砂法(见图1)。
本帖相关图片如下:图 1 顶吹法和底吹法制造壳芯示意图壳法造型、造芯的优点是混制好的覆膜砂可以较长期贮存(三个月以上);无需捣砂,能获得尺寸精确的型、芯;型、芯强度高,质量轻,易搬运;透气性好,可用细的原砂得到光洁的铸件表面;无需砂箱;覆膜砂消耗量小;型、芯可以长期贮放。
尽管酚醛树脂覆膜砂价格较贵,造型、造芯耗能较高,但在要求铸件表面光洁和尺寸精度甚高的行业仍得到一定应用。
通常壳型多用于生产液压件、凸轮轴、曲轴以及耐蚀泵件、履带板等钢铁铸件上:充芯多用于汽车、拖拉机、液压阀体等部分铸件上。
(二)壳型砂用原材料及混制工艺(1)酚醛树脂壳法采用热线塑性酚醛树脂。
它是在苯酚过量(通常苯酚与甲醛的物质的量之比为1:0.75~0.85)及温度在105℃以下缩合制成的。
常用的硬化剂为乌洛托品,学名六亚甲基四胺,即(CH2)6N4,其加入量一般占树脂质量的10~15%。
(2)原砂壳法一般采用硅砂,对于表面质量要求很高的铸件,特别是壁很厚实、易产生粘砂的铸钢件,也常使用鋯砂、铬铁矿砂。
(3)附加物为了改善覆膜砂的性能,有时在覆膜过程中加入某些附加物。
例如加人硬脂酸钙(为砂量的0.25~0.35%),可防止覆膜砂存放期间结块;增加覆膜妙的流动性,制壳时易于顶出等。
加入石英粉(加入量为砂质量的2%左右),可提高覆膜砂的高温强度。
(4)覆膜砂混制工艺酚醛树脂覆膜砂一般以原砂为 100(质量比),酚醛树脂加入量为:对于壳型是3.5~6.0,壳芯是1.5~4.0,另加入乌洛托品和硬酯酸钙。
覆膜砂的混制工艺可分为冷法、温法和热法三种。
其中热法是一种适于大量制备覆膜砂的方法,需要专门设备。
混制时一般为先将加热到130~160℃的砂加到间歇式混砂机中,再加树脂混匀,熔化的树脂包在砂粒表面,当砂温降到105~110℃时,加入乌洛托品水溶液,吹风冷却,再加入硬脂酸钙混匀,经过破碎、筛分备用。
酯硬化碱性酚醛树脂自硬砂

三、铸钢对造型粘结剂的要求
• 铸钢件容易出现的铸造缺陷
气孔 裂纹 粘砂 缩孔 缩松 表面气坑 尺寸公差
• 粘结剂对铸钢铸件的影响
粘土砂:气孔 粘砂 表面气坑 尺寸公差 水玻璃砂:气孔 表面气坑 尺寸公差 树脂砂:气孔 裂纹 粘砂
• 型芯砂应具备的性能
一定的强度(高温、常温) 良好的退让性 高的透气性 低的发气量 好的经济性 环保无毒等
二、铸钢型芯砂的粘结剂
• 分类 无机粘结剂 有机粘结剂 油类粘结剂
1、无机粘结剂 粘土砂(湿型、干型、表干型) 水玻璃砂 水玻璃砂:吹CO2硬化 水玻璃加入量6%~8% 抽真空硬化(VRH)…1.8%~2.5% 有机酯自硬 …1.8%~2.5%
2、有剂粘结剂
呋喃树脂自硬:树脂加入量0.8%~1.5% 酚脲脘树脂自硬: …1.0%~2.0% 有机酯碱酚自硬: …1.4%~2.0% 吹CO2硬化碱酚: …2.5%~3.5% 冷芯盒树脂: …1.0%~2.0% 热芯盒树脂: …1.5%~2.5% 覆膜砂:酚醛树脂加入量1.0%~3.0% 3、油类粘结剂 植物油 矿物油
5-40min 5-40min
水玻璃:2.5-3.5% 固化剂:0.3-0.5%
5-90min
24h抗拉强度
型芯存放性 高温热塑性
0.6-1.6MPa
好,基本不吸湿 小
0.4-1.2MPa
好,吸湿少 较大
0.4-1.0MPa
一般,有吸湿 大
铸型退让性
发气量 铸件表面质量 尺寸精度
较差
中 好
较好
小 好
4、碱性酚醛树脂砂硬化特性
碱性酚醛树脂砂是一种典型的“渐硬型” 自硬砂,反应过程需要几十分钟到十几个 小时才能完成,通常将24小时的试样强度 作为终强度。硬化时间从理论上说应该是 混砂过程中自树脂与固化剂接触的瞬间开 始计起,但实际生产中,则通常是混好的 砂子自混砂机卸出时开始计起。
树脂自硬砂烘干工艺
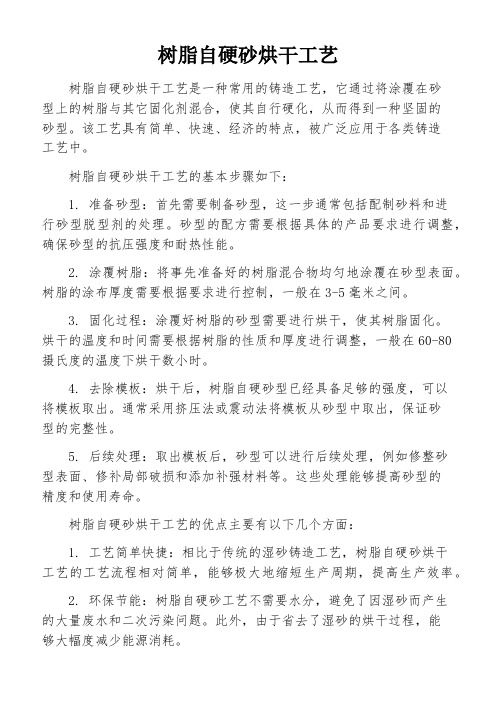
树脂自硬砂烘干工艺树脂自硬砂烘干工艺是一种常用的铸造工艺,它通过将涂覆在砂型上的树脂与其它固化剂混合,使其自行硬化,从而得到一种坚固的砂型。
该工艺具有简单、快速、经济的特点,被广泛应用于各类铸造工艺中。
树脂自硬砂烘干工艺的基本步骤如下:1. 准备砂型:首先需要制备砂型,这一步通常包括配制砂料和进行砂型脱型剂的处理。
砂型的配方需要根据具体的产品要求进行调整,确保砂型的抗压强度和耐热性能。
2. 涂覆树脂:将事先准备好的树脂混合物均匀地涂覆在砂型表面。
树脂的涂布厚度需要根据要求进行控制,一般在3-5毫米之间。
3. 固化过程:涂覆好树脂的砂型需要进行烘干,使其树脂固化。
烘干的温度和时间需要根据树脂的性质和厚度进行调整,一般在60-80摄氏度的温度下烘干数小时。
4. 去除模板:烘干后,树脂自硬砂型已经具备足够的强度,可以将模板取出。
通常采用挤压法或震动法将模板从砂型中取出,保证砂型的完整性。
5. 后续处理:取出模板后,砂型可以进行后续处理,例如修整砂型表面、修补局部破损和添加补强材料等。
这些处理能够提高砂型的精度和使用寿命。
树脂自硬砂烘干工艺的优点主要有以下几个方面:1. 工艺简单快捷:相比于传统的湿砂铸造工艺,树脂自硬砂烘干工艺的工艺流程相对简单,能够极大地缩短生产周期,提高生产效率。
2. 环保节能:树脂自硬砂工艺不需要水分,避免了因湿砂而产生的大量废水和二次污染问题。
此外,由于省去了湿砂的烘干过程,能够大幅度减少能源消耗。
3. 砂型精度高:树脂自硬砂具有优异的粘结力和抗压强度,能够确保砂型的精度和表面质量。
这对于一些对尺寸精度要求较高的铸件来说是非常重要的。
4. 重复使用性强:由于树脂自硬砂的固化剂能够在烘干过程中实现自行硬化,砂型可以反复使用。
这对于批量生产相同零件的铸造工艺来说可以大大降低生产成本。
总之,树脂自硬砂烘干工艺是一种简单、快捷、经济并且环保的铸造工艺。
它能够满足各类铸造产品对精度和表面质量的要求,提高铸造产品的质量和生产效率,是现代工业中广泛采用的一种重要工艺。
树脂自硬砂烘干工艺
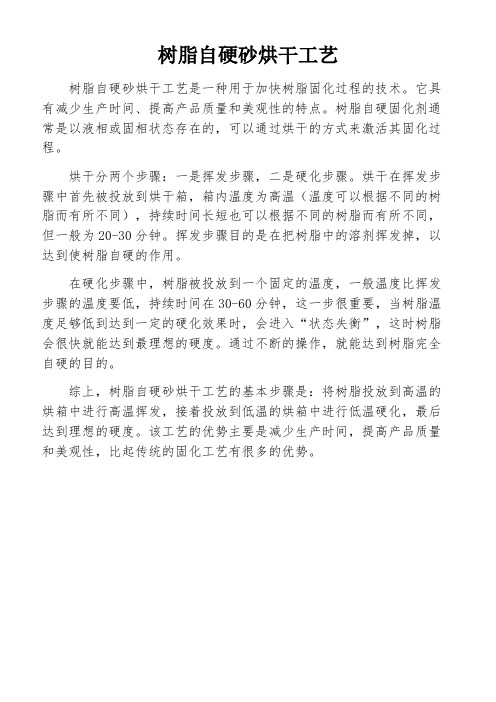
树脂自硬砂烘干工艺
树脂自硬砂烘干工艺是一种用于加快树脂固化过程的技术。
它具有减少生产时间、提高产品质量和美观性的特点。
树脂自硬固化剂通常是以液相或固相状态存在的,可以通过烘干的方式来激活其固化过程。
烘干分两个步骤:一是挥发步骤,二是硬化步骤。
烘干在挥发步骤中首先被投放到烘干箱,箱内温度为高温(温度可以根据不同的树脂而有所不同),持续时间长短也可以根据不同的树脂而有所不同,但一般为20-30分钟。
挥发步骤目的是在把树脂中的溶剂挥发掉,以达到使树脂自硬的作用。
在硬化步骤中,树脂被投放到一个固定的温度,一般温度比挥发步骤的温度要低,持续时间在30-60分钟,这一步很重要,当树脂温度足够低到达到一定的硬化效果时,会进入“状态失衡”,这时树脂会很快就能达到最理想的硬度。
通过不断的操作,就能达到树脂完全自硬的目的。
综上,树脂自硬砂烘干工艺的基本步骤是:将树脂投放到高温的烘箱中进行高温挥发,接着投放到低温的烘箱中进行低温硬化,最后达到理想的硬度。
该工艺的优势主要是减少生产时间,提高产品质量和美观性,比起传统的固化工艺有很多的优势。
【精品】四种自硬砂地选择

【关键字】精品四种自硬砂的选择随着我国机械工业产品质量的升级及出口铸件市场的不断扩大,在铸造车间技术改造中,有越来越多的企业首选自硬砂工艺替代原有粘土砂干型铸造工艺。
在本企业技改中如何根据自身的产品特点选择合适的自硬砂工艺及相应设备是技改中普遍关心的核心问题。
笔者结合近几年的实践就这一问题提出一点个人观点与同仁们共同探讨。
1.自硬砂工艺的选择自硬砂工艺是指在常温下,型砂能自行硬化并获得浇注要求强度的造型工艺的统称。
近几年得以较快发展的自硬砂主要有:呋喃树脂自硬砂、碱酚醛脂硬化自硬砂、脲脘树脂自硬砂(Pep—set自硬砂)、脂硬化改性水玻璃自硬砂。
这些自硬砂各有优缺点,应根据各企业不同的生产及产品特点择优选用。
1.1呋喃树脂自硬砂:这是应用最多、最广、工艺最成熟的自硬砂,而且相对铸件成本较低、旧砂利用率高、旧砂再生简单,是技术改造的首选自硬砂工艺。
呋喃树脂砂在灰铁、球铁、铸钢、有色等铸造中都得到极其广泛地应用。
但是由于呋喃树脂砂高温退让性差,树脂中含有较高的N,固化剂中含有S,因此一些壁厚不匀的铸钢件容易造成热裂,厚大铸钢件易造成N气孔,一些高牌号球铁件易造成球化衰退,一些低碳铸钢件还易造成增碳,在选用工艺及选用树脂种类时应引起足够重视。
这种工艺一般用于单件小批量生产性质的铸铁生产中。
1.2碱酚醛脂硬化树脂自硬砂:其是为克服呋喃树脂自硬砂的一些缺点发展起来的,国外称α—set工艺。
由于其完全不含N,固化剂不含S,用于铸钢、合金钢铸件不会产生N气孔、针孔缺陷。
由于碱酚醛树脂砂常温下只有部分树脂发生交联反应,在浇注金属受热时还有一个再硬化的过程,因此这种树脂砂的高温尺寸稳定性好,铸件尺寸精度高,因此在铸钢特别是合金钢件、大型铸钢件的生产上应用愈来愈广。
但碱酚醛树脂砂常温强度较低,树脂加入量较大,铸件成本较高。
碱酚醛树脂砂的硬化剂是有机脂,调节硬化时间只能用脂的品种而不能用加入量调节。
另外酚醛树脂粘度较大,可存放期短,使用中需要注意。
树脂自硬砂工艺设计

树脂自硬砂工艺设计引言:树脂自硬砂是一种常用于金属铸造的砂型材料,其优点包括高精度、高稳定性和良好的表面质量。
在树脂自硬砂工艺设计中,主要考虑材料的选择、模具设计和工艺参数调整等方面。
本文将详细介绍树脂自硬砂工艺设计的相关内容。
一、材料的选择1.酚醛树脂:酚醛树脂具有良好的流动性和耐高温性能,适用于制造复杂形状的铸件。
但由于其收缩率较大,容易导致铸件尺寸不稳定。
2.酚醛砂:酚醛砂是酚醛树脂与石英砂按一定比例混合而成的砂型材料,具有较好的热稳定性和耐磨性。
但由于其粘度较高,需要使用较大的压力来填充砂型。
3.环氧树脂:环氧树脂具有优异的机械性能、耐腐蚀性和耐高温性能,适用于制造耐磨、耐腐蚀的铸件。
但由于环氧树脂的固化时间较长,需要较长的工艺周期。
根据具体的铸造要求和制造工艺的特点,选择合适的树脂自硬砂材料。
二、模具设计模具设计是树脂自硬砂工艺设计的关键环节。
正确的模具设计可以确保砂型的精度和稳定性。
1.模具结构:选择合适的模具结构,包括上、下模板和型腔,以及冷却系统。
模具结构应考虑砂型的填充性能和铸件的脱模要求。
2.模具材料:模具材料应具有良好的耐用性和热稳定性,以保证模具的寿命和工艺稳定性。
常用的模具材料包括铸铁、钢和铝合金等。
3.冷却系统:冷却系统的设计可以有效控制模具温度,以提高铸件的尺寸精度和表面质量。
冷却系统应考虑水道的布置和尺寸。
三、工艺参数调整工艺参数调整是树脂自硬砂工艺设计的核心任务,包括树脂与硬化剂的配比、充填压力和固化时间等。
1.树脂与硬化剂的配比:树脂与硬化剂的配比直接影响到树脂的流动性和固化时间。
配比不当会导致砂型填充不充分或固化不完全,从而影响铸件的精度和质量。
2.充填压力:充填压力影响树脂与砂型之间的接触和渗透性。
充填压力过大会破坏砂型,造成铸件表面粗糙;充填压力过小则会导致砂型填充不完全。
3.固化时间:固化时间是树脂自硬砂固化的关键参数,影响铸件的凝固和收缩过程。
固化时间应根据具体的铸件形状和尺寸进行调整,以确保铸件的质量。
自硬砂树脂砂工艺问答

自硬砂树脂砂工艺问答自硬砂树脂砂工艺问答■ 济南圣泉集团股份有限公司张本水李长元朱能山1.为什么磷酸多用作高氮呋喃自硬树脂的固化剂,而很少用作低氮呋喃自硬树脂的固化剂?这是因为低氮高糠醇树脂,采用酸做固化剂时,硬化速度慢,脱模时间长,且强度很低。
高氮低糠醇树脂使用磷酸做固化剂可获得必要的硬化速度。
而且,高氮低糠醇树脂采用磷酸作催化剂可获得很好的终强度。
造成这种结果的原因主要是由于磷酸与糠醇的互溶性差,而与水的亲和力大,使得树脂和催化剂中所含的水分以及树脂在缩聚反应中生成的水不易扩散排出而以磷酸为核心生成水滴残存于树脂膜中,破坏了树脂膜的致密性,故强度较低。
而高氮树脂与水的互溶性好,各种水分不易以磷酸为核心集中为水滴,树脂膜结构好,强度高。
2.为什么酚脲脘自硬树脂的硬透性比呋喃自硬树脂砂好?因为酚脲脘树脂的固化过程是聚合反应,固化过程中不产生小分子的水,不存在因型内外水分的挥发速度不同使其内外固化速度不一致的问题,而呋喃自硬树脂的固化过程是缩聚反应,反应过程中产生水分,因型芯内外的水分蒸发速度不同,导致了其内外固化速度不同,故其硬透性差些。
这也是呋喃自硬树脂砂的固化速度受空气相对湿度影响较大的原因。
3.为什么生产铸铝,铸铜件可以选用高氮呋喃树脂?由于铝、铜金属液对氮几乎不溶解,因此,即使使用高氮树脂在浇注过程中树脂分解产生的氮,也不会被铝、铜金属液吸收,也就不会在凝固过程中因析出氮而形成氮气孔。
因此,生产铸铝、铸铜件可以为潢足溃散性的需要而选用高氮树脂。
4.为什么自硬树脂砂生产重量大的铸件,浇注系统宜于用陶瓷管制作?采用自硬树脂砂造型,当生产重量较大的铸件时,由于浇注时间长,浇注系统在高温金属液的长时间热作用下,易使树脂砂过早溃散丧失强度,造成冲砂缺陷,因此,对重量较大的铸件,浇注系统宜用陶管制作,同时使浇注系统特别是直浇道不易上涂料的问题得到解决。
5.采用自硬树脂砂造型、制芯时,如何确定树脂砂的可使用时间是否满足要求?当采用间歇式混砂机时,树脂砂的可使用时间要大于树脂砂从混好卸砂到用完的这段时间;当采用连续式混砂机造型、制芯时,树脂砂的可使用时间要大于从混砂机的出砂口起始放砂位置到又回到该位置连续放砂的这段时间。
自硬树脂砂操作工艺
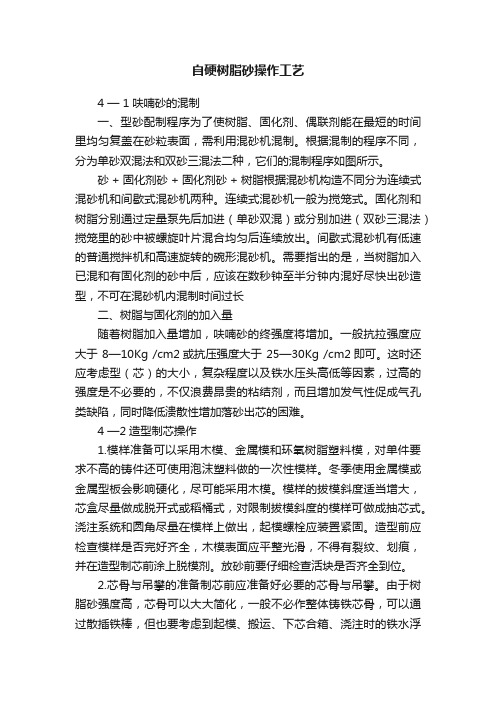
自硬树脂砂操作工艺4 — 1呋喃砂的混制一、型砂配制程序为了使树脂、固化剂、偶联剂能在最短的时间里均匀复盖在砂粒表面,需利用混砂机混制。
根据混制的程序不同,分为单砂双混法和双砂三混法二种,它们的混制程序如图所示。
砂 + 固化剂砂 + 固化剂砂 + 树脂根据混砂机构造不同分为连续式混砂机和间歇式混砂机两种。
连续式混砂机一般为搅笼式。
固化剂和树脂分别通过定量泵先后加进(单砂双混)或分别加进(双砂三混法)搅笼里的砂中被螺旋叶片混合均匀后连续放出。
间歇式混砂机有低速的普通搅拌机和高速旋转的碗形混砂机。
需要指出的是,当树脂加入已混和有固化剂的砂中后,应该在数秒钟至半分钟内混好尽快出砂造型,不可在混砂机内混制时间过长二、树脂与固化剂的加入量随着树脂加入量增加,呋喃砂的终强度将增加。
一般抗拉强度应大于 8—10Kg /cm2或抗压强度大于 25—30Kg /cm2即可。
这时还应考虑型(芯)的大小,复杂程度以及铁水压头高低等因素,过高的强度是不必要的,不仅浪费昂贵的粘结剂,而且增加发气性促成气孔类缺陷,同时降低溃散性增加落砂出芯的困难。
4 —2造型制芯操作1.模样准备可以采用木模、金属模和环氧树脂塑料模,对单件要求不高的铸件还可使用泡沫塑料做的一次性模样。
冬季使用金属模或金属型板会影响硬化,尽可能采用木模。
模样的拔模斜度适当增大,芯盒尽量做成脱开式或稻桶式,对限制拔模斜度的模样可做成抽芯式。
浇注系统和圆角尽量在模样上做出,起模螺栓应装置紧固。
造型前应检查模样是否完好齐全,木模表面应平整光滑,不得有裂纹、划痕,并在造型制芯前涂上脱模剂。
放砂前要仔细检查活块是否齐全到位。
2.芯骨与吊攀的准备制芯前应准备好必要的芯骨与吊攀。
由于树脂砂强度高,芯骨可以大大简化,一般不必作整体铸铁芯骨,可以通过散插铁棒,但也要考虑到起模、搬运、下芯合箱、浇注时的铁水浮力等等对泥芯刚性及强度的要求,放置足够的芯骨,对大泥芯可放入铸铁龙骨,吊攀下钩处注意插横担铁条。
酸催化树脂自硬砂

酸催化树脂自硬砂
工艺特点: ① 型(芯)砂常温固化,节省能源,可使用塑料模、木模; ② 型(芯)强度高,溃散性好; ③ 即可造型,又能制芯; ④ 铸件尺寸精度高,表面质量好; ⑤ 对原砂质量要求高,树脂、固化剂价格高; ⑥ 旧砂可再生回用,利于降低成本; ⑦ 型砂性能对环境(温度、湿度)敏感; ⑧ 特别适合成批、单件小批中大铸件的生产。
酸催化树脂自硬砂
1. 自硬砂的成分 (3)催化剂 决定型砂的硬化速度和硬化终强度。
对于呋喃树脂,常用的催化剂有:
对甲苯磺酸
苯磺酸 磷酸
均为显性催化剂
硫酸已酯
酸催化树脂自硬砂
1. 自硬砂的成分 (3)催化剂
决定型砂的硬化速度和硬化终强度。
硬化 催化剂酸性 越强:
越快
终强度 越低 催化剂的酸性强弱:
酸催化树脂自硬砂
酸催化树脂自硬砂
以呋喃树脂或热固性酚醛树脂为粘结剂,在相应的酸性催 化剂作用下,在室温下自行硬化成形的型(芯)砂。
酸催化树脂自硬砂
以呋喃树脂或热固性酚醛树脂为粘结剂,在相应的酸性催 化剂作用下,在室温下自行硬化成形的型(芯)砂。
铸钢阀体
酸催化树脂自硬催 化剂作用下,在室温下自行硬化成形的型(芯)砂。
混匀
混匀
砂 + 催化剂
+ 树脂(硅烷)
出砂
酸催化树脂自硬砂
3. 自硬砂的硬化特性 树脂自硬砂在混砂时就开始硬化。 根据硬化强度和硬化时间的关系得出硬化特性曲线。
树脂自硬砂硬化24小时的 抗拉强度称为终强度。
三个重要性能指标: t3 — 可使用时间 t5 — 起模时间 σ24— 终强度
酸催化树脂自硬砂
酸催化树脂自硬砂
5. 自硬砂的旧砂再生 再生的目的:
碱酚醛树脂自硬砂
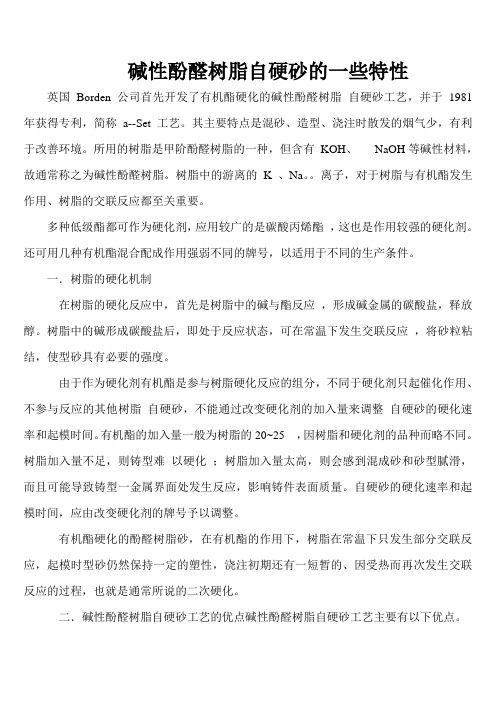
碱性酚醛树脂自硬砂的一些特性英国Borden公司首先开发了有机酯硬化的碱性酚醛树脂自硬砂工艺,并于1981年获得专利,简称a--Set工艺。
其主要特点是混砂、造型、浇注时散发的烟气少,有利于改善环境。
所用的树脂是甲阶酚醛树脂的一种,但含有KOH、NaOH等碱性材料,故通常称之为碱性酚醛树脂。
树脂中的游离的K 、Na。
离子,对于树脂与有机酯发生作用、树脂的交联反应都至关重要。
多种低级酯都可作为硬化剂,应用较广的是碳酸丙烯酯,这也是作用较强的硬化剂。
还可用几种有机酯混合配成作用强弱不同的牌号,以适用于不同的生产条件。
一.树脂的硬化机制在树脂的硬化反应中,首先是树脂中的碱与酯反应,形成碱金属的碳酸盐,释放醇。
树脂中的碱形成碳酸盐后,即处于反应状态,可在常温下发生交联反应,将砂粒粘结,使型砂具有必要的强度。
由于作为硬化剂有机酯是参与树脂硬化反应的组分,不同于硬化剂只起催化作用、不参与反应的其他树脂自硬砂,不能通过改变硬化剂的加入量来调整自硬砂的硬化速率和起模时间。
有机酯的加入量一般为树脂的20~25 ,因树脂和硬化剂的品种而略不同。
树脂加入量不足,则铸型难以硬化;树脂加入量太高,则会感到混成砂和砂型腻滑,而且可能导致铸型一金属界面处发生反应,影响铸件表面质量。
自硬砂的硬化速率和起模时间,应由改变硬化剂的牌号予以调整。
有机酯硬化的酚醛树脂砂,在有机酯的作用下,树脂在常温下只发生部分交联反应,起模时型砂仍然保持一定的塑性,浇注初期还有一短暂的、因受热而再次发生交联反应的过程,也就是通常所说的二次硬化。
二.碱性酚醛树脂自硬砂工艺的优点碱性酚醛树脂自硬砂工艺主要有以下优点。
1.混砂、造型、浇注时散发的烟气少于以酸为硬化剂的呋喃树脂砂、以酸为硬化剂的甲阶酚醛树脂砂和以胺为硬化剂的尿烷树脂砂。
2.由于起模时型砂仍然保持一定的塑性,故起模性能好,型砂不易粘附在模具上,砂型表面比较光洁,模样上的起模斜度也可较小。
3.二次硬化后,砂型的热稳定性较好,厚壁铸件表面上也很少出现脉状纹缺陷。
- 1、下载文档前请自行甄别文档内容的完整性,平台不提供额外的编辑、内容补充、找答案等附加服务。
- 2、"仅部分预览"的文档,不可在线预览部分如存在完整性等问题,可反馈申请退款(可完整预览的文档不适用该条件!)。
- 3、如文档侵犯您的权益,请联系客服反馈,我们会尽快为您处理(人工客服工作时间:9:00-18:30)。
酚醛尿烷树脂自硬砂配制及
砂型制作工艺
为获得表面面光洁,尺寸精确、形状完整、轮廓清晰的铝铸件,并达到劳动条件好,环境污染小,节约能源,提高市场竞争能力,故选用树脂砂工艺。
1. 本规定适用于本厂树脂自硬砂配制砂型制作。
2. 对原材料的要求:
2.1原砂性能,选用1SC-2SC 40/70-70/140-(0)的擦洗砂,要求含水分≤0.2%,含泥量≤0.5%,以减少树脂消耗,确保砂型的干强度。
2.2本公司铝合金铸造选用酚醛尿烷树脂作粘贴剂,主要由两部分组成,PEPSET、CPⅠ—5140、CPⅡ—5235=50/50,两者发生聚合反应使型砂硬化,具体特性见表:
要求:树脂含水量<5%,氧化铁含量2-3%(可防气孔)。
3. 混砂设备:JQ300型高效立式混砂搅拌机(简易型)0.3m/碾。
4. 砂型的配制:
4.1配比
4.1.1树脂如入比例:
C P Ⅰ—5140 酚醛树脂 50% ————— = ————— = ———— CP Ⅱ—5235 异氰酸脂 50%
4.1.2加入量:
注: (1)重要部分的型砂取加入量的上限;
(2)原砂含水分和含泥量低者取加入量的下限;
(3)气温低于0℃时,可以加入占树脂总量0.19的催化剂CP —5300。
4.2拌砂工艺:
2~3分钟 1~1.5分钟 原砂+CP Ⅰ— 5140 ———— +CP Ⅱ—5235 ———— 出砂 混 混
注:必须以搅拌均匀为止,CP Ⅱ未加入者,可以适当停留或多拌2钟。
4.3发现两种组合搅拌不均匀而成团者,必须调匀才可使用。
4.4可使用时间与脱模时间(参考):
注: a 可使用时间:是指自型砂混和好后,可供制芯(型)开始到不能制出
合格的砂芯(型)为止的时间;
b 脱模时间:是指自硬砂树脂砂型混合后,可供制芯(型)开始,到可满意的将砂芯(型)从模具中拔出为止的时间间隔。
4.5硬化的散砂不准再铲入搅拌机中使用,必须清除。
5. 酚醛尿烷树脂自硬砂造型工艺要点:
5.1准备工作
5.1.1操作者在熟悉铸造工艺文件的基础上,查对工艺装备是否齐全,
几何形状尺寸是否正确,有无损伤或遗漏,浇冒口模型是否符合工艺规定。
5.1.2配备的冷铁种类、尺寸、数量要符合要求,放置要准确,冷铁表
面要经清理,撒砂、烘烤处理,有油污、锈蚀和未烤干者禁止使用。
5.1.3铸模及附件上附着的灰砂、水分、油污等应清理干净。
5.2造型操作要点
5.2.1严格控制吃砂量,厚大件≯100mm、中等件≯80mm,小件
≯50mm,分型必须平整,以免增加纵向高度。
5.2.2型腔模具凹角处必须用手塞紧,分层紧实。
确保冷铁位置正确
与铸模工作面紧贴,浇冒口不被椿跑,出气孔畅通。
5.2.3在分层椿砂时,要严防用椿砂棍猛椿分层街接处已初始硬化的
砂层,以防损坏。
5.2.4严格掌握可使用时间,每批搅拌好的树脂砂必须在一定时间内
使用完,已开始硬化的砂子不准用,同时立即轻敲浇冒口模型,以免取出困难。
5.2.5下型放置的地面砂层要松软,均匀、平整、并划通气沟,防止
顶坏砂型。
5.2.6掌握脱模时间,应在适当的时候起模(参考表2),开箱前划好
定位线。
5.2.7修型时按图纸进行,该倒圆处则倒,不可用涂料修补较厚的损
坏处,用树脂砂修补。
5.2.8铸型型腔(含浇冒口)按图纸\工艺要求修整完毕后,用压缩空
气吹净后,用刷或喷GAC945醇基涂料,并点火自然,对于型腔复杂尖角较多者,可稍停1—2分钟后再点火,防止烧枯。
5.2.9要求醇基涂料含水量<5%,涂料前需要搅拌10分钟以上,涂料
后5分钟以内可以点燃。
6. 配箱浇注
6.1清理型(芯)表面浮砂,用压缩空气吹净,用喷灯表干砂型(芯)表面,切忌烧枯局部型腔。
6.2配箱前用喷灯表干型面数次,手触无湿感,发现未化学硬化的树脂黑点,有可燃的高发气性大的杂物,应立即清除干净。
6.3用刮刀、断锯条等工具轻刮型(芯)表面局部堆积的浮砂或涂层,并用软布轻抹至无浮物。
最后用压缩空气吹净所有型面。
6.4合箱前,必须实行自检,互检和专检相结合,型腔是否符合图纸、工艺和标准的要求。
6.5可用湿砂围封浇口杯,用石棉绳封堵,防止跑水。
合箱完成后,
注意上、下型缩紧,压重和掩箱工作,防止抬箱跑火。
6.6浇注时必须备足金属液,注意挡渣引气,遵循慢-快-慢,始终充满浇口杯,防止断流飞溅,及时补充冒口。
6.7铸型排列整齐留出浇注通道。
GAC—945醇基涂料必须远离火。