作业效率手册
效率手册文档

效率手册概述本效率手册旨在帮助读者提高工作和生活的效率。
在现代社会中,时间是一种宝贵的资源,因此在合理利用时间的同时提高效率是非常重要的。
本手册提供了一些实用的建议和技巧,帮助读者更有效地完成任务,提高生产力。
1. 时间管理时间管理是提高效率的关键。
以下是一些时间管理的技巧:•设定目标:设定明确的目标,并将其分解为具体的步骤和里程碑。
这将帮助你更好地规划工作和生活。
•制定计划:在每天或每周的开始时制定一个计划。
列出要完成的任务和优先级,并为每个任务分配适当的时间。
•避免拖延:意识到拖延是效率的敌人。
采取措施避免拖延,例如将任务分解为小的可行性部分,建立时间限制,或寻求他人的帮助和支持。
•优化工作流程:评估工作流程,寻找可以提高效率的机会。
简化流程,消除冗余步骤,并选择合适的工具和技术来支持工作。
•集中注意力:避免分散注意力,集中精力在一项任务上直到完成。
使用专注和时间分配技巧,如番茄工作法(Pomodoro Technique)来帮助保持专注度。
2. 任务管理任务管理是高效工作的关键。
以下是一些任务管理的技巧:•使用任务列表:创建一个任务列表,将所有要完成的任务写下来。
根据任务的优先级进行排序,并不断更新和跟踪任务的进展。
•使用时间管理工具:利用各种时间管理工具,如日历、提醒应用程序或任务管理软件。
这些工具可以帮助你跟踪任务、设置提醒和计划工作。
•委托和分配任务:将适当的任务委托给他人或分配给团队成员,以减轻自己的负担,提高工作效率。
•批处理任务:将类似的任务进行批处理,以减少切换任务的时间和精力。
例如,将相似的电子邮件一并处理,或将相同类型的任务集中在一起处理。
•保持清晰的工作区:创建一个清晰整洁的工作区,摆放必要的工具和资源,并保持桌面和文件整齐有序。
这可以帮助提高工作效率和集中注意力。
3. 通信和协作有效的通信和协作是团队合作和工作效率的关键。
以下是一些通信和协作的技巧:•明确沟通目标:在与他人沟通之前明确自己的沟通目标。
计划夲日程本学习效率手册
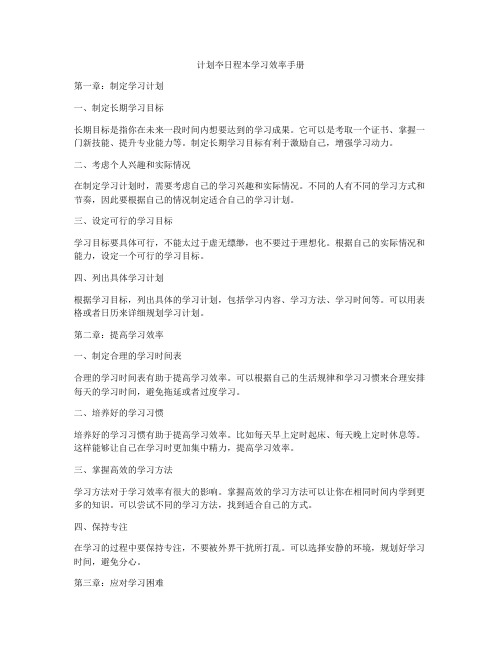
计划夲日程本学习效率手册第一章:制定学习计划一、制定长期学习目标长期目标是指你在未来一段时间内想要达到的学习成果。
它可以是考取一个证书、掌握一门新技能、提升专业能力等。
制定长期学习目标有利于激励自己,增强学习动力。
二、考虑个人兴趣和实际情况在制定学习计划时,需要考虑自己的学习兴趣和实际情况。
不同的人有不同的学习方式和节奏,因此要根据自己的情况制定适合自己的学习计划。
三、设定可行的学习目标学习目标要具体可行,不能太过于虚无缥缈,也不要过于理想化。
根据自己的实际情况和能力,设定一个可行的学习目标。
四、列出具体学习计划根据学习目标,列出具体的学习计划,包括学习内容、学习方法、学习时间等。
可以用表格或者日历来详细规划学习计划。
第二章:提高学习效率一、制定合理的学习时间表合理的学习时间表有助于提高学习效率。
可以根据自己的生活规律和学习习惯来合理安排每天的学习时间,避免拖延或者过度学习。
二、培养好的学习习惯培养好的学习习惯有助于提高学习效率。
比如每天早上定时起床、每天晚上定时休息等。
这样能够让自己在学习时更加集中精力,提高学习效率。
三、掌握高效的学习方法学习方法对于学习效率有很大的影响。
掌握高效的学习方法可以让你在相同时间内学到更多的知识。
可以尝试不同的学习方法,找到适合自己的方式。
四、保持专注在学习的过程中要保持专注,不要被外界干扰所打乱。
可以选择安静的环境,规划好学习时间,避免分心。
第三章:应对学习困难一、认清学习困难学习过程中会遇到各种各样的困难,比如学习内容难度大、学习压力过大等。
要认清学习困难,主动寻找解决方法。
二、寻求帮助遇到学习困难时,不要怕麻烦,可以主动向老师、同学、家人或者学习指导中心寻求帮助。
他们可能会给你一些建议和帮助。
三、调整心态面对学习困难,要调整好自己的心态。
不要灰心丧气,要相信自己的能力,坚持不懈地克服困难。
第四章:健康学习方式一、保持良好的作息良好的作息有助于提高学习效率,可以保证充足的睡眠和休息时间,让你在学习时更有精力和耐心。
中学生学习计划效率手册

中学生学习计划效率手册第一章:学习目标的设定1.1 制定长期学习目标学习计划效率手册的第一步是制定长期学习目标。
长期学习目标是指学生在未来一段时间内想要达到的学习成就,如高考成绩、大学录取等。
在设定长期学习目标时,要根据自己的兴趣和能力制定具体的目标,以激励自己努力学习。
1.2 制定短期学习目标除了长期学习目标外,还要制定短期学习目标,如每学期的考试成绩、每次课堂作业的完成情况等。
短期学习目标的设定有助于学生更好地把握学习进度,提高学习动力。
1.3 目标评估与调整学习计划的目标需要定期评估和调整。
学生可以根据自己的学习情况和成绩来检查目标的完成情况,并做出相应的调整。
比如,如果发现自己的学习目标过高或过低,就需要对目标进行调整,以确保目标的合理性和可实现性。
第二章:学习计划的制定2.1 制定周计划学习计划的第一步是制定周计划。
周计划具体包括每周要完成的学习任务、复习内容和时间安排。
学生可以根据每周的课程安排和自己的学习情况来合理安排学习时间,确保每周的学习任务能够顺利完成。
2.2 制定日计划除了周计划外,还需要制定每天的学习计划。
每天的计划应包括具体的学习内容、复习内容和作业完成情况。
学生可以根据自己的学习进度和计划安排来合理安排每天的学习时间,提高学习效率。
2.3 目标分解与执行学习计划的执行需要对目标进行细化和分解,确保每个学习任务都能够清晰可行。
学生可以将长期学习目标细分为具体的学习任务和时间安排,以便更好地实现学习目标。
第三章:学习方法的选择3.1 主动参与课堂课堂学习是学生学习的重要环节,学生应该在课堂上积极主动参与,注意听讲、做笔记,并与老师和同学进行交流和讨论。
主动参与课堂有助于加深对知识的理解和记忆。
3.2 合理安排复习时间复习是学习的重要环节,学生应该根据自己的学习进度和复习内容合理安排复习时间,如每天安排一定的复习时间,每周对上周的学习内容进行复习等。
3.3 学会总结和归纳学生在学习的过程中应注重总结和归纳,将所学的知识进行梳理和归纳,有助于加深对知识的理解和记忆,提高学习效率。
2012年周月工作效率手册

2012年周月工作效率手册标题:2012 年周月工作效率手册一、引言(一)工作效率的重要性(二)周月工作效率手册的目的二、周月工作效率手册的概述(一)手册的结构和内容(二)使用手册的方法和步骤三、每周工作效率提升(一)周一:规划与准备设定本周目标制定工作计划准备所需资源(二)周二至周四:执行与专注按照计划执行任务避免干扰和分心保持专注和高效(三)周五:总结与反思回顾本周工作进展总结经验教训制定下周计划四、每月工作效率提升(一)每月初:目标设定与规划设定本月目标分解目标为具体任务制定月工作计划(二)月中:监控与调整监控工作进展1. 2. 3. 1. 2. 3. 1. 2. 3. 1. 2. 3. 1.识别问题和挑战及时调整计划(三)月末:总结与评估总结本月工作成果评估工作效率制定下月改进计划五、时间管理技巧(一)优先级排序确定任务的优先级优先处理重要紧急任务(二)时间块管理将时间划分为不同的块为每个任务分配时间块(三)避免拖延认识拖延的原因采取措施克服拖延六、任务管理技巧(一)任务分解将大任务分解为小任务明确每个小任务的目标和步骤(二)任务分配合理分配任务给团队成员明确责任和期限(三)任务跟踪建立任务跟踪系统及时了解任务进展七、沟通与协作技巧(一)有效沟通明确沟通目的选择合适的沟通方式注意沟通技巧2. 3. 1. 2. 3. 1. 2. 1. 2. 1. 2. 1. 2. 1. 2. 1. 2. 1. 2. 3.(二)团队协作建立良好的团队合作关系明确团队成员的角色和职责促进团队成员之间的协作八、自我管理技巧(一)保持积极心态培养积极的思维方式应对压力和挫折(二)持续学习与提升不断学习新知识和技能提升自己的能力和素质(三)保持健康与平衡关注身体健康保持工作与生活的平衡九、案例分析(一)成功案例介绍案例背景采取的措施和方法取得的成果和效益(二)失败案例分析案例背景失败的原因和教训改进的措施和建议十、结论(一)工作效率的重要性(二)周月工作效率手册的作用(三)持续提升工作效率的方法和途径以上是一个根据 2012 年周月工作效率手册编写的文章大纲,你可以根据这个大纲来编写文章,希望对你有所帮助。
效率手册使用心得
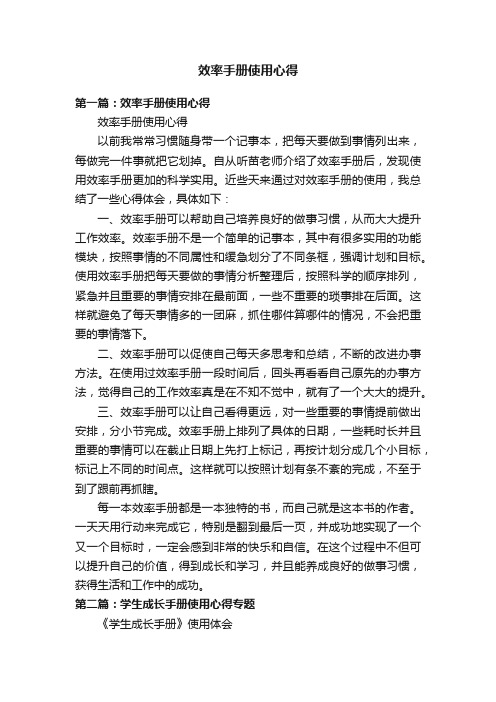
效率手册使用心得第一篇:效率手册使用心得效率手册使用心得以前我常常习惯随身带一个记事本,把每天要做到事情列出来,每做完一件事就把它划掉。
自从听苗老师介绍了效率手册后,发现使用效率手册更加的科学实用。
近些天来通过对效率手册的使用,我总结了一些心得体会,具体如下:一、效率手册可以帮助自己培养良好的做事习惯,从而大大提升工作效率。
效率手册不是一个简单的记事本,其中有很多实用的功能模块,按照事情的不同属性和缓急划分了不同条框,强调计划和目标。
使用效率手册把每天要做的事情分析整理后,按照科学的顺序排列,紧急并且重要的事情安排在最前面,一些不重要的琐事排在后面。
这样就避免了每天事情多的一团麻,抓住哪件算哪件的情况,不会把重要的事情落下。
二、效率手册可以促使自己每天多思考和总结,不断的改进办事方法。
在使用过效率手册一段时间后,回头再看看自己原先的办事方法,觉得自己的工作效率真是在不知不觉中,就有了一个大大的提升。
三、效率手册可以让自己看得更远,对一些重要的事情提前做出安排,分小节完成。
效率手册上排列了具体的日期,一些耗时长并且重要的事情可以在截止日期上先打上标记,再按计划分成几个小目标,标记上不同的时间点。
这样就可以按照计划有条不紊的完成,不至于到了跟前再抓瞎。
每一本效率手册都是一本独特的书,而自己就是这本书的作者。
一天天用行动来完成它,特别是翻到最后一页,并成功地实现了一个又一个目标时,一定会感到非常的快乐和自信。
在这个过程中不但可以提升自己的价值,得到成长和学习,并且能养成良好的做事习惯,获得生活和工作中的成功。
第二篇:学生成长手册使用心得专题《学生成长手册》使用体会为贯彻落实教育部等六部委《关于加强和改进中等职业学校学生思想道德教育的意见》精神,不断增强中等职业学校德育工作的针对性和有效性,积极拓展中职德育工作载体,在2010新学年上海市教育委员会德育处和职教处组织专家编写了《上海市中等职业学校学生成长手册》,经过一个学年的使用展示了每位学生在学习过程中所做的努力和取得的进步,以及反映学生学习成果的一个集合体,同时也是教师观察学生学习成果和学习进步的窗口。
作业效率手册PPT课件
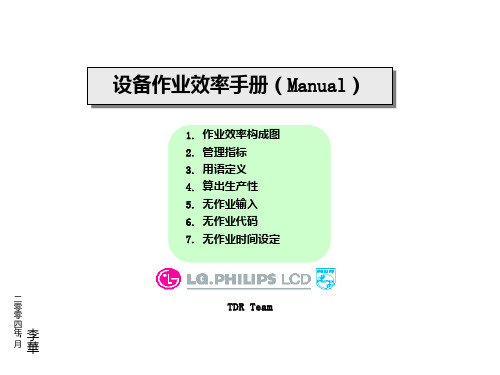
二 零 零 四
年李 月華
设备作业效率手册(Manual)
1. 作业效率构成图 2. 管理指标 3. 用语定义 4. 算出生产性 5. 无作业输入 6. 无作业代码 7. 无作业时间设定
TDR Team
作业效率
算出基准
效率构成图
算出基准
作业率
负荷率
时间驱动率
性能驱动率
(速度驱动率 × 装备驱动率)
Neck Time是指生产线上工序Cycle时间最长的时间, 成为Neck工序的Cycle时间
POL 贴合基准 #1
#2
#3
#4
#5 T/Time(秒) 20.44 19.80 19.75 19.84 23.46 21.50 20.89 22.06 21.96 20.56
1).最大作业时间 是指设备设置在现场的总时间.一台一天24小时为基准(1440分), 分为作业时间和非作业时间.
2). 作业时间 是指最大作业时间中适用于生产上的时间. 在管理上是指除了不能适用于生产的非作业时间的时间.
3). 非作业时间
- 没有适用于生产上的时间.
(教育/吃饭/假日及休息/工厂施工/定期清扫)
意义
工作时间设备负荷的时间+D3 工作时间设备运转而生产的程度 设备运用于生产目的时间中有效活用的程度 工作时间中设备有效活用的程度
算出工作效率时适用的 T/Time 设备生产良品数量(全体生产量)的时间
(但Tact Time是平均Tact Time)
李华 TDR
3/12
有关作业效率
3.用语的定义
非负荷
驱动时间 Run Time 非驱动
时间 Loss
有效驱动时间 速度 Valid Run Time Loss
中学生效率手册
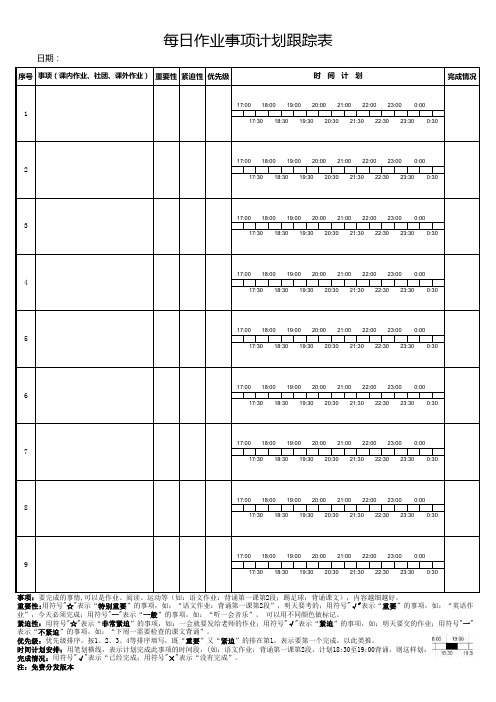
日期:序号事项(课内作业、社团、课外作业)重要性紧迫性优先级完成情况19:3020:3021:3022:30时 间 计 划每日作业事项计划跟踪表217:0017:0018:0019:0020:0021:0022:0023:000:0023:300:30117:3018:3017:000:0017:3018:3019:3020:3021:3022:3023:300:3018:0019:0020:0021:0022:0023:00417:000:0017:3018:3019:3020:3021:3022:3023:300:3018:0019:0020:0021:0022:0023:00317:000:0017:3018:3019:3020:3021:3022:3023:300:3018:0019:0020:0021:0022:0023:00617:000:0017:3018:3019:3020:3021:3022:3023:300:3018:0019:0020:0021:0022:0023:0050:0017:3018:3019:3020:3021:3022:3023:300:3018:0019:0020:0021:0022:0023:00重要性:用符号"☆"表示“特别重要”的事项,如:“语文作业:背诵第一课第2段”,明天要考的;用符号"√"表示“重要”的事项,如:“英语作业”,今天必须完成;用符号"一"表示“一般”的事项,如:“听一会音乐”。
可以用不同颜色做标记。
紧迫性:用符号"☆"表示“非常紧迫”的事项,如:一会就要发给老师的作业;用符号"√"表示“紧迫”的事项,如:明天要交的作业;用符号"一"表示“不紧迫”的事项,如:“下周一需要检查的课文背诵”。
优先级:优先级排序,按1、2、3、4等排序填写,既“重要”又“紧迫”的排在第1,表示要第一个完成,以此类推。
2025年效率手册
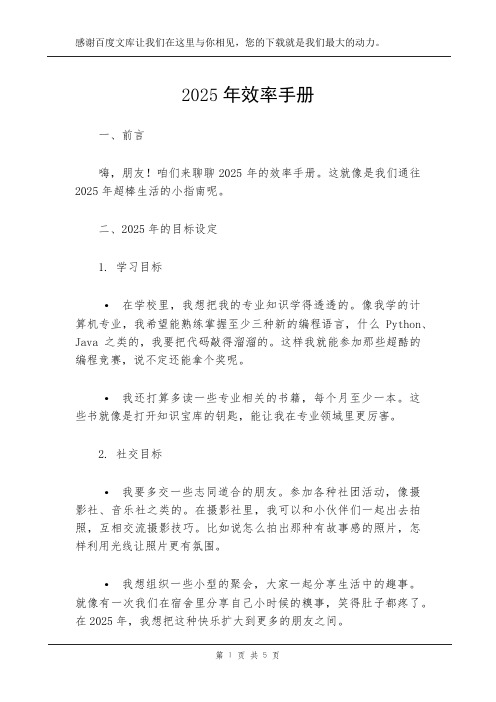
2025年效率手册一、前言嗨,朋友!咱们来聊聊2025年的效率手册。
这就像是我们通往2025年超棒生活的小指南呢。
二、2025年的目标设定1. 学习目标•在学校里,我想把我的专业知识学得透透的。
像我学的计算机专业,我希望能熟练掌握至少三种新的编程语言,什么Python、Java之类的,我要把代码敲得溜溜的。
这样我就能参加那些超酷的编程竞赛,说不定还能拿个奖呢。
•我还打算多读一些专业相关的书籍,每个月至少一本。
这些书就像是打开知识宝库的钥匙,能让我在专业领域里更厉害。
2. 社交目标•我要多交一些志同道合的朋友。
参加各种社团活动,像摄影社、音乐社之类的。
在摄影社里,我可以和小伙伴们一起出去拍照,互相交流摄影技巧。
比如说怎么拍出那种有故事感的照片,怎样利用光线让照片更有氛围。
•我想组织一些小型的聚会,大家一起分享生活中的趣事。
就像有一次我们在宿舍里分享自己小时候的糗事,笑得肚子都疼了。
在2025年,我想把这种快乐扩大到更多的朋友之间。
3. 健康目标•我可不能再像以前一样老是熬夜了。
每天都要保证至少7个小时的睡眠。
晚上11点之前必须上床睡觉,早上7点左右起床。
这样我白天才有精力去做各种事情。
•每周至少去三次健身房。
我想把我的身体练得棒棒的,像那些健身达人一样有肌肉线条。
我可以从简单的有氧运动开始,比如跑步、跳绳,然后再做一些力量训练,像举哑铃之类的。
三、时间管理1. 制定每日计划•每天晚上睡觉前,我会花10 - 15分钟规划一下第二天要做的事情。
我会把事情按照重要性和紧急程度分类。
比如说,第二天有一场重要的考试复习,那这就是既重要又紧急的事情,我会优先安排时间去做。
而像洗衣服这种事情,虽然重要但不紧急,我可以放在下午或者晚上有空的时候去做。
2. 利用碎片时间•在等公交车或者坐地铁的时候,我不再是光刷手机看视频了。
我可以听一些英语听力或者有声书籍。
这样积少成多,我的英语水平也能提高不少呢。
而且在课间休息的10分钟里,我可以简单回顾一下上节课的重点内容,这样知识就能记得更牢。
(工作规范)工作效率手册
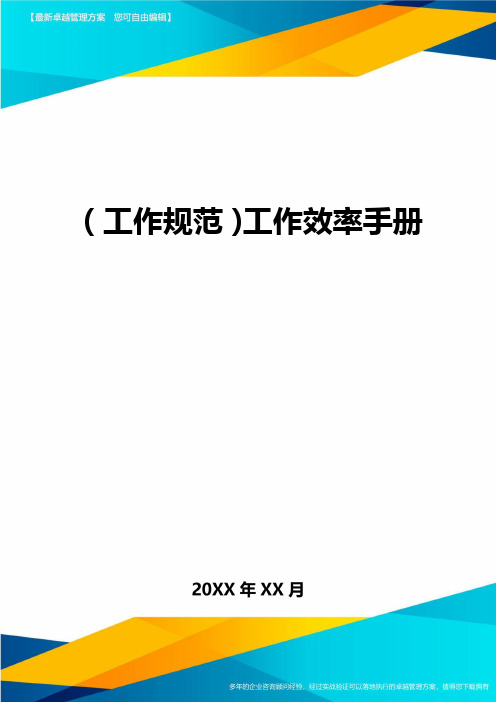
(工作规范)工作效率手册工作效率手册移动办公是提高工作效率的有效途径引言于日益严峻的商业竞争和更加难以预测的市场面前,企业如何才能尽可能地提高且保持其创造力和竞争力呢?这个问题壹直困扰着许多的IT企业地管理者。
过去几年IT产业的沉浮兴衰和风云变换使得情况变得越来越复杂。
这就使得IT 产业的运营者们不得不于其计算机、应用程序甚至网络构架中采取“额外”的措施来最大限度地提高其自身的工作效率,以期能取得较好的业绩和效益。
许多企业的管理者发现,除了建立映射数据中心和网络备份系统外,“移动办公”也已成为壹条提高企业工作效率、促进业务反弹的有效途径。
目前,于商业过程当中,花费于办公室之外的时间越来越多,且且有的业务要分散执行,而公司职员们也分散于总部、分部和甚至是家庭之中。
所以要确保整个企业始终能保持创旺盛的"生产"能力,就应该使企业的每个成员无论身处何处均能够和企业保持联络且能进行有效的工作。
思科公司技术开发部的高级副主管CharlieGiancarlo说:“当用户离开办公桌而处于"移动"过程中的时候,如果他不能够访问其公司的网络资源且能于"移动"中继续办公的话,他就可能丧失某些商业机会。
”为此,思科公司提出了“思科移动办公室”来应对这壹挑战,这是壹系列技术解决方案,能使IT公司为其职员提供安全、高速的移动连接。
那么“移动办公”的效益何于呢?让我们举壹个例子来说明。
航空工业部门对公众旅行制定了越来越来严格的安全规范,以至于许多商业旅行者发现他们于机场的逗留时间越来越长。
如果机场部署了无线局域网,他们就能够通过便携式电脑中的无线局域网适配器和有安全保证的虚拟个人网络客户机软件,安全有效地接入机场的无线局域网,且进而和其公司的网络连接,从而保持了持续办公的能力。
此外,宾馆、会堂也应该为处于移动中的商业人士提供无线或有线以太网连接服务,这样就可保证他们通过因特网访问其公司内部的信息资源。
工作效率手册

工作效率手册工作效率手册第一章:工作效率的重要性工作效率是指在充分发挥能力的基础上,以高质量高产出完成工作的能力。
一个高效率的工作能够提高工作质量、减少工作时间、增加工作满意度,从而带动整个团队或组织的发展。
因此,提高工作效率是每个人都应该关注和追求的目标。
第二章:提高工作效率的原则1.制定明确的工作目标制定明确的工作目标是提高效率的基础。
明确的工作目标可以帮助人们更好地理解自己的工作职责和任务,从而有针对性地安排工作时间和精力。
2.合理安排工作时间合理安排工作时间可以确保工作的连贯性和高效性。
可以通过制定工作计划、优化工作流程、合理分配工作量等方式来提高工作效率。
3.避免拖延和分散注意力拖延和分散注意力是常见的工作效率低下的原因。
通过培养良好的时间管理习惯、集中注意力、合理安排工作优先级等方式可以解决这个问题。
4.合理利用工具和技术合理利用现代化的工具和技术可以大大提高工作效率。
如使用办公软件、通信工具、时间管理工具等,可以帮助人们更好地管理和协调工作。
第三章:提高工作效率的方法1.培养良好的工作习惯良好的工作习惯是提高工作效率的基础。
如早起、定时休息、保持良好的饮食习惯、锻炼身体等,可以保证身心健康,提高工作效率。
2.分析和优化工作流程分析和优化工作流程可以帮助人们找到工作中的瓶颈和问题,并提出解决方案。
例如,通过精简流程、减少多余的环节、合理分配工作等方式,可以提高工作效益。
3.合理分配工作量合理分配工作量可以保证每个人的工作负担适中,并能够更好地发挥每个人的优势。
可以通过团队合作、项目管理等方式来实现。
4.合理安排工作优先级合理安排工作优先级可以保证工作的有序进行,避免任务堆积和延误。
可以通过制定任务清单、设定截止日期、按照重要性和紧急性进行排序等方式来实现。
5.学习和利用新技术学习和利用新技术可以提高工作效率,节省时间和精力。
可以通过参加培训、学习相关技术书籍、与同行交流等方式来提升自己的技术能力。
2017效率手册A4打印版

9月30日(周四)
2017年10月工作记录
10月1日(周一)
10月2日(周一)
10月3日(周二)
10月4日(周三)
10月5日(周四)
10月6日(周五)
10月7日(周六)
10月8日(周一)
10月9日(周一)
10月10日(周二)
10月11日(周三)
10月12日(周四)
10月13日(周五)
11月28日(周二)
11月29日(周三)
11月30日(周四)
2017年12月工作记录
12月31日(周四)
12月1日(周五)
12月2日(周六)
12月3日(周日)
12月4日(周一)
12月5日(周二)
12月6日(周三)
12月7日(周四)
12月8日(周五)
12月9日(周六)
12月10日(周日)
12月11日(周一)
6月19日(周一)
6月20日(周二)
6月21日(周三)
6月22日(周四)
6月23日(周五)
6月24日(周六)
6月25日(周日)
6月26日(周一)
6月27日(周二)
6月28日(周三)
6月29日(周四)
6月30日(周五)
2017年7月工作记录
7月30日(周日)
7月31日(周一)
7月1日(周六)
7月2日(周日)
7月3日(周一)
7月4日(周二)
7月5日(周三)
7月6日(周四)
7月7日(周五)
7月8日(周六)
7月9日(周日)
7月10日(周一)
7月11日(周二)
7月12日(周三)
7月13日(周四)
工作安排工具效率手册

工作安排工具效率手册一、时间管理工具时间管理工具是提高工作效率的重要工具之一。
我们可以利用各种时间管理工具来规划我们的工作日程和时间。
例如,日历应用程序可用于记录和跟踪重要日期和事件。
时间跟踪应用程序可以记录我们的工作时间和时间分配情况。
扫描应用程序可以将我们的纸质文件和笔记转换为可搜索的数字文件。
所有这些工具都可以帮助我们更好地管理时间和提高工作效率。
二、任务管理工具任务管理工具可以帮助我们更好地组织和跟踪我们的任务。
这些工具可以帮助我们将任务分配给不同的人、设置任务优先级以及跟踪任务完成情况。
常用的任务管理工具包括微软的To-Do、Todoist、Trello等。
三、项目管理工具项目管理工具是帮助我们组织和管理大型复杂项目的工具。
这些工具可以帮助我们跟踪任务、设置期限、协调团队成员、制定计划等等。
著名的项目管理工具包括JIRA、Asana、Basecamp等。
四、文件管理工具文件管理工具是帮助我们组织和管理文件的工具。
我们可以使用这些工具来整理我们的电子邮件、文档、图片、音频和视频等等。
这些工具不仅可以帮助我们更快、更轻松地查找文件,而且可以帮助我们更好地跟踪和管理文档的版本。
常用的文件管理工具包括Google Drive、Dropbox、OneDrive等。
五、团队协作工具团队协作工具是帮助我们协作和合作的工具。
我们可以使用这些工具来与团队成员分享资料、商讨问题、制定计划等等。
著名的团队协作工具包括Slack、Microsoft Teams、Zoom、Webex等。
六、通知提醒工具通知提醒工具可以帮助我们提醒和跟踪各种关键事件和活动。
例如,我们可以使用提醒工具来提醒我们工作会议、重大事件、工作截止日期等。
Maple Mind、Wunderlist等都是很好的通知提醒工具。
总之,以上的各种工具都可以帮助我们更好地管理时间、任务、文件和项目等方面,提高工作效率。
我们可以根据自己的需要选择适合自己的工具,并加以应用,以达到更高效的工作效果。
工作效率手册

索引:经理人工作效率提升的32个细节 细节百分百01: 培养自信形象的几点建言/14 细节百分百02: 准备工作最好与工作本身有关联/33 细节百分百03: 借高兴事情刺激工作惰绪/37 细节百分百04: 先列必须做的事,再决定顺序/53 细节百分百05: 在名片背面书写有关他的信息/61 细节百分百06: 利用情绪良好的时段提高工作效率/65 细节百分百07: 感到效率低下时休息三分钟/73 细节百分百08: 把自己从文件堆中解放出来/77 细节百分百09: 注意网络礼仪/90 细节百分百10: 经常整理电脑中的碎片,以提高其运行速度/93 细节百分百11: 总目标订立的影响因素/114 细节百分百12: 合理利用交通时间/121 细节百分百13: 只要早一点出门,就可以掌握更多时间/123 细节百分百14: 站着开会可以节省很多时间/127 细节百分百15: 把日常工作“格式化”/130 细节百分百16: 影响人的行为举止因素/133 细节百分百17: 请他人做事时,必须说明做法及意图/135 细节百分百18: 头一次最重要/138 细节百分百19: 大胆放手地让下属施展才华/143 细节百分百2O: 端平“一碗水”能有效驾驭全局/150 细节百分百21: 让下属充满“自己的存在被认可的心情”/155 细节百分百22: 善于规划可及远景以鼓舞下属/159 细节百分百23: 有助授权的技巧/167 细节百分百24: 让下属向你积极汇报/169 细节百分百25: 提前一周将材料分发到与会者手中/186 细节百分百26: 赴会中留意自己无声的语言/188 细节百分百27: 员工参与制定绩效考评标准途径/192 细节百分百28: 绩效考评三要点/196 细节百分百29: 经理人使用秘书应注意问题/207 细节百分百30: 策划战略、战术是决定
2018年工作效率手册
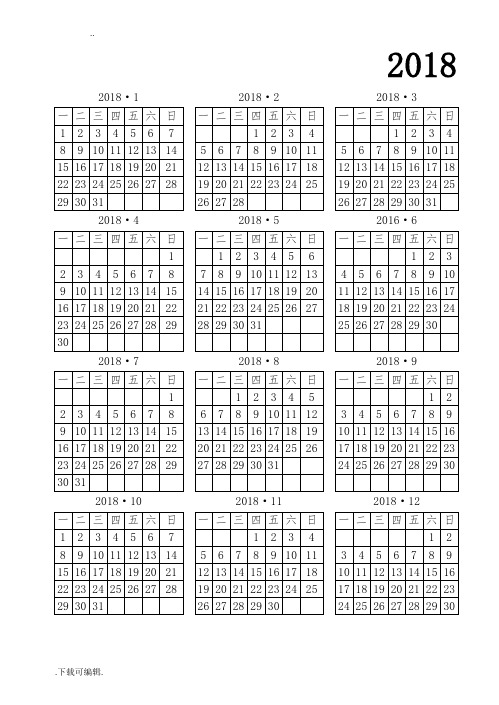
2018年2月3日
星期六·腊月十八
2018年2月4日
星期日·腊月十九
立春
2018年2月5日
星期一·腊月二十
2018年2月6日
星期二·腊月廿一
2018年2月7日
星期三·腊月廿二
2018年2月8日
星期四·腊月廿三
小年
2018年2月9日
星期五·腊月廿四
2018年2月10日
星期六·腊月廿五
2018年2月11日
2018
2018·1
2018·2
2018·3
一
二
三
四
五
六
日
一
二
三
四
五
六
日
一
二
三
四
五
六
日
1
2
3
4
5
6
7
1
2
3
4
1
2
3
4
8
9
10
11
12
13
14
5
6
7
8
9
10
11
5
6
7
8
9
10
11
15
16
17
18
19
20
21
12
13
14
15
16
17
18
12
13
14
15
16
17
18
22
23
24
25
26
27
28
19
20
21
星期三·正月十三
2018年3月1日
星期四·正月十四
- 1、下载文档前请自行甄别文档内容的完整性,平台不提供额外的编辑、内容补充、找答案等附加服务。
- 2、"仅部分预览"的文档,不可在线预览部分如存在完整性等问题,可反馈申请退款(可完整预览的文档不适用该条件!)。
- 3、如文档侵犯您的权益,请联系客服反馈,我们会尽快为您处理(人工客服工作时间:9:00-18:30)。
李华 TDR
2/12
有关作业效率
2.管理指标
指标名 负荷率 时间运转率 性能运转率 工作效率 基准 Tact Time 有效运转时间 算出公式 负荷实绩÷ 工作时间 驱动时间÷ 负荷时间 有效运转时间÷ 驱动时间 有效运转时间÷ 工作时间
全 员投入的Model/Line的 最近实绩 全 体生产量×Tact Time
计划停止/开发
非负荷
作业等待/质材品质/ 前后工程品质
Down/更换/自工程品质/ Model Change/清扫/停电
非驱 动
有效驱动时间 (生产产品) 良品有效驱 动时间 废弁/ RW
速度 Loss
良品率
▲ M工厂 6大 Loss
时间驱动率× 性能驱动率× 良品率
* 生产综合效率 (OPE : Overall Production Effectiveness ) : 是在最大作业时间中表示 良品对生产寄予的程度 并且将设备最大生产力
算出基准
算出基准
算出基准 (%)
作业时间 最大作业时间 负荷时间 作业时间 驱动时间 负荷时间 有效驱动时间 驱动时间 收率 × (1 – Rework率) 时间驱动率× 性能驱动率× 负荷率
作业率
作业时间 负荷率 负荷时间 时间驱动率 驱动时间 性能驱动率
(速度驱动率 × 装备驱动率)
非作业 时间
1).最大作业时间 是指设备设置在现场的总时间.一台一天24小时为基准(1440分), 分为作业时间和非作业时间.
2). 作业时间
是指最大作业时间中适用于生产上的时间. 在管理上是指除了不能适用于生产的非作业时间的时间. 3). 非作业时间 - 没有适用于生产上的时间. (教育/吃饭/假日及休息/工厂施工/定期清扫) - 计划停止(新型号开发Test/未Loading) ※ 未Loading: 生产实绩超过计划数量而发生设备剩余时间. ※ 新型号开发: 由于开发新的产品或设备在试生产过程中而造成的一系列停机。 4). 负荷时间 是指作业时间中设备负荷的时间.负荷由使用设备而生产的产品的有无来判断.
停机 时间
返工 工时
时间 损失 能率 损失
节拍时间 : Tact Time 标准时间(工分) : Standard Time 不开机时间 :培训/休息/计划不开机 :不生产 标准时间=实质时间×(1+宽裕率) 不运转时间 :型号变更/工作准备/材料供不上/质量问题 :设备以外原因 生产线平衡率 停机时间 :设备故障/设备保养/备件更换 :设备原因 马表法 : Stop Watch 无效运转时间 :速度损失(瞬间停机等原因) ECRS : 剔(除)、合(并)、(重)排、简化
工程品质
设备能够正常运转,但生产 如:POL贴合程度,ACF附着程度, 出的产品为不良品或可能为不良 Bonding不良等等。 品时,需要对设备进行检查调整。
人员品质
前/后工程品质TROU BLE操作者品质
生产操作人员的操作错误, 误操作等。
如:把上POL错投到下POL里,POL投 反,按键按错等,主要为OP的操作 失误,PM的误操作做为Down处理。
李华 TDR
4/12
有关作业效率
5). 非负荷时间 因设备外在的因素而不动作的时间.采取措施后马上会负荷的时间.
(作业等待/前后工程品质/断货) 6). 驱动时间
负荷时间中自身原因被迫生产中断的时间. 7). 非驱动时间 负荷时间中进行的各种交换,设备故障, 设备PM,电算故障以上等的时间. - 计划PM ※计划PM: 与生产Team协议的PM(Production Maintenance) 8). 有效运转时间
8 21.70 81.48% 3244
9 23.77 82.34% 2993
10 21.96 82.54% 3247
11 20.85 77.02% 3192
※生产性: 生产数/line.天 = 1440分×60(秒) × 作业效率÷Mix T/T 速度LOSS:速度loss就是指生产时间去除无作业时间后除以实际Neck T/T后减去实际生产数量, 所得数量就是速度loss数量!
Line 别 Neck 工序基准 Mix T/Time(秒) 平均工作效率 生产性/Line.日(台)
1 20.44 77.96% 3295
2 22.04 81.68% 3202
3 19.75 78.24% 3423
5 21.90 70.68% 2788
6 25.39 75.65% 2574
7 21.50 77.47% 3114
Line 别 Neck 工序基准 Mix T/Time(秒)
#1 20.44
#2 22.04
#3 19.75
#4
#5 #6 #7 #8 #9 #10 21.90 25.39 21.50 21.70 23.77 21.96 20.85
李华 TDR
6/12
有关作业效率
2) Neck 工厂基准生产性 ( 生产数/Line天) Neck Time是指生产线上工序Cycle时间最长的时间, 成为Neck工序的Cycle时间
设备作业效率手册(Manual)
1. 作业效率构成图 2. 管理指标
3. 用语定义
4. 算出生产性 5. 无作业输入 6. 无作业代码
7. 无作业时间设定
二 零 零 四 年 月 7
TDR Team
李 華
作业效率 效率构成图
最大作业时间(24Hr)
项目
作业率 负荷率 时间 驱动率 性能 驱动率 良品率 作业效率 设备综合 效率 (OEE) 生产综合 效率 (OPE)
OEE× 作业率× 负荷率
年初的理论Capa为基准 出现成果的指标
李华 TDR
1/12
有关作业效率
1.作业效率构成图
最大作业时间 MAX Work Time 비조업 非作业 时间 시간
非负荷
- MAX作业时间: 以一天24小时计算,1440分钟。
作业时间
Work Time
-非作业时间 : 未Loading,,计划停止,教育,朝 会,休务 -非负荷时间 : 作业等待,,缺货,前后工程品质,
负荷时间
Load Time
时间
驱动时间 Run Time
非驱动
Loss
-非驱动时间 :作业准备、M/C,设备故障, 交换 ,
电算故障,定期清扫,交接班 计划PM
-无效运转时间(速度Loss) : 不到2分钟的无作 业,没有输入的设备Loss. ※ 无作业发生现基准:2分钟以上(02年9月基准)
有效驱动时间 Valid Run Time
由设备工程原因引起 如到了对设备进行清扫的时间,设 备已经由于其它的原因停下来了, 不需要输入定期清扫 仅在交接班和生产前的准备工作时 输入 具体原因具体输入
定期清扫
定期清扫
在规定的时间段,需要对设备 进行停机并进行清扫 在交接班规定的一个时间段 内输入 由于更换材料时间过长而造成了 设备的Down机,需进行无作业输 入 设备自身的故障。(如碰撞,设 备不动作,传感器故障,Error连 续发生等。) 程序故障,电脑死机,鼠标键盘 失灵等。
设备为生产而所需的时间 = 生产数量 × Tact Time
※ 良品,不良品无关 (TAB只考虑投入数量,不考虑是否为良品或不良品) 9). 速度 Loss (有效运转时间) 运转时间中对生产没有贡献的时间. (速度低下,空旋转, 瞬间停止,Error , 连接拖延等)
李华 TDR
5/12
有关作业效率
意
义
工作时间设备负荷的时间+D3 工作时间设备运转而生产的程度 设备运用于生产目的时间中有效活用的程度 工作时间中设备有效活用的程度 算出工作效率时适用的 T/Time 设备生产良品数量(全体生产量)的时间 (但Tact Time是平均Tact Time)
李华 TDR
3/12
有关作业效率
3.用语的定义
POL 贴合基准 #1 #2 #3 #4 #5 #6 #7 #8 #9 #10 Mix T/Time(秒) 20.44 19.80 19.75 19.84 23.46 21.50 20.89 22.06 21.96 20.56 TAB 贴合基准 #1 #2 #3 #4 #5 #6 #7 #8 #9 #10 Mix T/Time(秒) 19.50 20.28 19.58 21.59 25.39 21.46 21.70 23.77 20.00 20.85 PCB 贴合基准 #1 #2 #3 #4 #5 #6 #7 #8 #9 #10 Mix T/Time(秒) 20.09 22.04 19.15 21.90 23.46 21.30 19.91 20.91 21.37 20.75
备注
如:月末盘点,周休等。 目前主要在PCB段发生,PCB的TT比T AB的要快。 很少发生 当问题是由于人员问题造成时输入 具体资材 具体输入
待作业
后工程T/T差值 B/A Tray断货
缺料
断货
资材品质
前/后工程品质TROU BLE品质
前/后工程品质TROU BLE 设备/工程品质
具体资材 具体输入
李华 TDR
7/12
有关作业效率
设备运转效率
设备运转效率=时间运转率×性能运转率(×良品率) =有效运转时间÷工作(开机)时间 时间运转率=(工作时间-不运转时间-停机时间)÷工作时间 =实质运转时间÷工作(开机)时间 性能运转率=(设备节拍时间×生产量) ÷实质运转时间 有效运转时间=设备节拍时间×生产量 最大工作时间 : Max Working Time 工作(开机)时间 : Working Time 运转时间 : Loading Time 实质运转时间 有效运转时间 良品 不良 品 无效运 转时间 不运转 时间 .不开机 时间