彻底解决泵送堵管
泵送混凝土堵管的防治措施
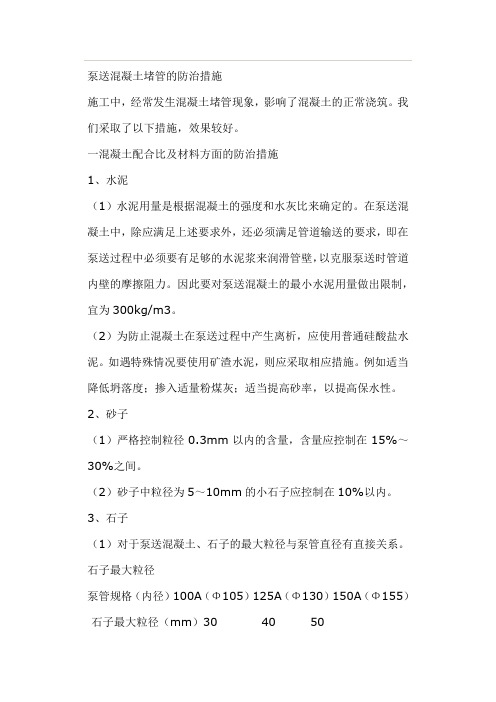
泵送混凝土堵管的防治措施施工中,经常发生混凝土堵管现象,影响了混凝土的正常浇筑。
我们采取了以下措施,效果较好。
一混凝土配合比及材料方面的防治措施1、水泥(1)水泥用量是根据混凝土的强度和水灰比来确定的。
在泵送混凝土中,除应满足上述要求外,还必须满足管道输送的要求,即在泵送过程中必须要有足够的水泥浆来润滑管壁,以克服泵送时管道内壁的摩擦阻力。
因此要对泵送混凝土的最小水泥用量做出限制,宜为300kg/m3。
(2)为防止混凝土在泵送过程中产生离析,应使用普通硅酸盐水泥。
如遇特殊情况要使用矿渣水泥,则应采取相应措施。
例如适当降低坍落度;掺入适量粉煤灰;适当提高砂率,以提高保水性。
2、砂子(1)严格控制粒径0.3mm以内的含量,含量应控制在15%~30%之间。
(2)砂子中粒径为5~10mm的小石子应控制在10%以内。
3、石子(1)对于泵送混凝土、石子的最大粒径与泵管直径有直接关系。
石子最大粒径泵管规格(内径)100A(Φ105)125A(Φ130)150A(Φ155)石子最大粒径(mm)30 40 50(2)石子采用连续级配,保证石子之间的空隙率和砂浆用量;针片状颗粒含量不宜大于10%。
4、砂率砂率为混凝土中粗细骨料之间的关系,砂率变化会使混凝土和和易性产生变化,影响混凝土泵送性。
砂率可按下式计算。
砂率=细骨料/(粗骨料+细骨料)×100%。
泵送混凝土的砂率宜为38%~45%。
5、水灰比水灰比即为混凝土中水与水泥用量的比值,设计配合比时应保证设计强度和泵送混凝土所需的坍落度,且不发生离析。
泵送混凝土的水灰比宜为0.4~0.6。
6、泵送剂泵送剂应根据每盘的用量,提前装袋,保证泵送剂用量的准确。
二、台设备影响泵送效果的防治措施1、砂子、石子由料斗投入配料斗的顺序改为先投石子、再投砂子。
这样可以避免砂子过湿时沾在料斗上,从而保证砂子用量。
2、输送泵地坑不宜过深,输送泵混凝土出口应与地面水平布管高度项适宜,以避免混凝土因出口过低而影响混凝土的初速度。
泵送混凝土堵管爆管的解决办法(8个典型案例分析解决)
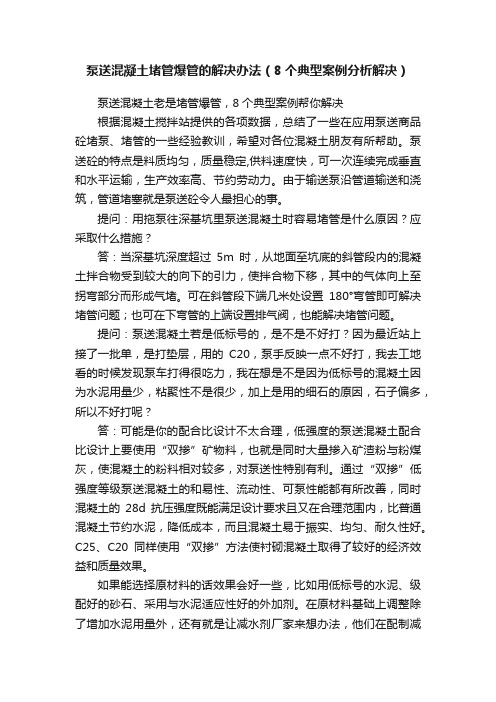
泵送混凝土堵管爆管的解决办法(8个典型案例分析解决)泵送混凝土老是堵管爆管,8个典型案例帮你解决根据混凝土搅拌站提供的各项数据,总结了一些在应用泵送商品砼堵泵、堵管的一些经验教训,希望对各位混凝土朋友有所帮助。
泵送砼的特点是料质均匀,质量稳定,供料速度快,可一次连续完成垂直和水平运输,生产效率高、节约劳动力。
由于输送泵沿管道输送和浇筑,管道堵塞就是泵送砼令人最担心的事。
提问:用拖泵往深基坑里泵送混凝土时容易堵管是什么原因?应采取什么措施?答:当深基坑深度超过5m时,从地面至坑底的斜管段内的混凝土拌合物受到较大的向下的引力,使拌合物下移,其中的气体向上至拐弯部分而形成气堵。
可在斜管段下端几米处设置180°弯管即可解决堵管问题;也可在下弯管的上端设置排气阀,也能解决堵管问题。
提问:泵送混凝土若是低标号的,是不是不好打?因为最近站上接了一批单,是打垫层,用的C20,泵手反映一点不好打,我去工地看的时候发现泵车打得很吃力,我在想是不是因为低标号的混凝土因为水泥用量少,粘聚性不是很少,加上是用的细石的原因,石子偏多,所以不好打呢?答:可能是你的配合比设计不太合理,低强度的泵送混凝土配合比设计上要使用“双掺”矿物料,也就是同时大量掺入矿渣粉与粉煤灰,使混凝土的粉料相对较多,对泵送性特别有利。
通过“双掺”低强度等级泵送混凝土的和易性、流动性、可泵性能都有所改善,同时混凝土的28d抗压强度既能满足设计要求且又在合理范围内,比普通混凝土节约水泥,降低成本,而且混凝土易于振实、均匀、耐久性好。
C25、C20同样使用“双掺”方法使衬砌混凝土取得了较好的经济效益和质量效果。
如果能选择原材料的话效果会好一些,比如用低标号的水泥、级配好的砂石、采用与水泥适应性好的外加剂。
在原材料基础上调整除了增加水泥用量外,还有就是让减水剂厂家来想办法,他们在配制减加剂时会根据你的情况来调整改善的。
例1:泵送剂与水泥相容性差堵管水泥和化学外加剂的相容性是一个重要问题。
泵送混凝土堵管的原因及处理方法

泵送混凝土堵管的原因及处理方法
泵送混凝土时出现堵管情况是施工中常见的问题之一,主要原因有以下几个方面:
1. 混凝土配合比不合理:混凝土配合比中水灰比过小,粉煤灰含量过高,砂粒过细等都会增加混凝土的黏性,容易堵塞管道。
2. 混凝土含水量过大:混凝土的含水量过大会导致混凝土流动性差,易产生堵塞现象。
3. 混凝土粒径不合适:过大或过小的混凝土颗粒会增加阻力,阻碍混凝土的流动,从而造成堵塞。
4. 管道磨损:长时间使用的泵送管道内壁会产生磨损,导致管道粗糙度增加,容易产生堵塞。
针对堵管问题,可采取以下处理方法:
1. 调整混凝土配合比:合理设计混凝土配合比,增加水灰比和粉煤灰含量,使用适当的砂粒粒径,提高混凝土的流动性,减少堵塞风险。
2. 控制混凝土含水量:在施工中严格控制混凝土的含水量,确保其
流动性能良好,减少堵塞的可能性。
3. 清洗管道:定期对泵送管道进行清洗,去除管道内的混凝土渣滓和堵塞物,保持管道的畅通。
4. 更换管道:如果管道磨损严重,影响混凝土的流动性,应及时更换管道,确保施工的顺利进行。
5. 控制泵送速度:适当控制泵送速度,避免过快或过慢,以减少堵塞的风险。
总之,对于泵送混凝土堵管问题,需要从混凝土配合比、含水量、管道磨损等多个方面进行综合考虑,并采取相应的处理措施,确保施工过程的顺利进行。
【结构设计知识】七大处理方法教您轻松应对泵送混凝土堵管问题

我们只分享有价值的知识点,本文由李雪梅老师精心收编,大家能够下载学习!此行文字能够删除。
【精选构造设计知识】七大办理方法教您轻松应付泵送混凝土堵管问题一、操作不妥简单造成堵管操作人员精力不集中输送泵操作人员在泵送施工中应精力集中,时辰注意泵送压力表的读数,一旦发现压力表读数忽然增大,应立刻反泵2-3个行程,再正泵,堵管即可清除。
若已经进行了反泵、正泵几个操作循环,仍未清除堵管,应实时拆管冲洗,不然将使堵管更为严重。
泵送速度选择不妥泵送时,速度的选择很重点,操作人员不可以一味地图快,有时欲速则不达。
初次泵送时,因为管道阻力较大,此时应低速泵送,泵送正常后,可适合提升泵送速度。
当出现堵管征兆或某一车混凝土的坍落度较小时,应低速泵送,将堵管消灭在萌芽状态。
余料量控制不适合泵送时,操作人员须随时察看料斗中的余料,余料不得低于搅拌轴,假如余料太少,极易吸入空气,致使堵管。
料斗中的料也不可以堆得太多,应低于防备栏,以便于实时清理粗骨料和超大骨料。
当某一车混凝土的坍落度较小时,余料可低于搅拌轴,控制在S管或吸进口以上,以减小搅拌阻力、摇动阻力和吸入阻力。
本方法仅合用于S阀系列混凝土泵。
混凝土的坍落度过小时采纳举措不妥当发现有一斗混凝土的坍落度很小,没法泵送时,应实时将混凝土从料斗底部放掉,若贪恋省事,强行泵送极易造成堵管。
切忌在料斗中加水搅拌。
停机时间过长停机时期,应每隔5~10min(详细时间视当天气温、混凝土坍落度、混凝土初凝时间而定)开泵一次,以防堵管。
关于停机时间过长,已初凝的混凝土,不宜持续泵送。
管道未冲洗洁净上一次泵送完成,管道未冲洗洁净,会造成下一次泵送时堵管。
所以每次泵送完成必定要依据操作规程将输送管道冲洗洁净。
二、管道连结原由致使的堵管管道接法错误很简单致使堵管。
接收时应依据以下原则:管道部署时应按最短距离、最少弯头和最大弯头来布管,尽量减小输送阻力,也就减少了堵管的可能性。
泵出口锥管处,不准直接接弯管,起码应接入5mm以上直管后,再接弯管。
混凝土泵车直管堵管快速解决办法

混凝土泵车直管堵管快速解决办法在混凝土泵车施工过程中,经常会出现堵管现象。
堵管的实质就是混凝土在管道中缺水。
混凝土缺水就会造成堵管。
在正常情况下,如果每个泵送冲程的压力高峰值随冲程的交替而迅速上升,并很快达到设定的压力(32Mpa),正常的泵送循环自动停止,这是只要进行1-2个反泵循环就能排除堵塞。
如循环几次仍无效,则表明已发生严重堵塞应迅速处理。
注意:反泵——正泵操作不能反复多次进行,否则将使堵塞更为严重。
1. 堵管的可能原因及预防处理堵管是一件很麻烦的事,所以对泵车配件直管堵管现象应以预防为主,主要从以下几个方面着手加以防备,减少堵管发生的可能性。
1)、混凝土质量方面:混凝土和易性差,表现为:粗料粒直径太大或标配不符合要求;砂率太低或标配不符合要求;水泥用量不当或质量不符合要求;搅拌不均匀或搅拌时间停留过长;原料吸水性过大,外加剂不适合等。
其粘聚性差,保水性差。
因混凝土质量是造成堵塞的主要原因,所以应加以控制和预防。
2)、管道方面:管子或接头漏水造成输送过程中压力下降或泄压,弯管的弯曲半径过小,管道不一造成凹槽,未对齐。
3)、泵送前根据需要打的方量,对泵车的管道使用相应数量的润管剂进行润滑。
4)、设备方面:液压系统参数调整不当。
5)、操作方面:待料或停机时间过长。
2. 堵管发生后的处理措施堵塞发生后,先进行反泵疏通,若反泵疏通无效则应立即判定堵塞部位,停机清理管路。
堵塞部位判定的方法是:在泵机操作人员进行正泵——反泵操作的同时,其他人员沿输送管道寻找堵塞部位。
一般来说,从泵的出口起至堵塞部位的管段会发生剧烈振动,面堵塞点以后的管路则静止的,堵塞段混凝土被吸动有响声,堵塞点以后无响声,敲打管道,堵塞部位的发闷的声音和密实的感觉。
一旦找到堵塞部位,在进行正——反泵的同时,用木锤敲析该处,有时能恢复畅通,无效应立即拆卸该段管道进行清洗。
如堵塞与判断不准,也可进行分段清洗。
若拆管时,发现管内砼料开始凝结,应毫不犹豫地将所有管接头打开,逐级快速清理,并清洗拖泵,以免混凝土料凝结,无法洹而使混凝土管报废。
泵车堵管处理

堵管有很多的原因所以也有很多不同的处理方法常见的就是打反泵切莫硬顶那样会堵死的泵送混凝土对材料的要求、预防堵管的措施、堵管原因、堵管处理方法如果是灰料不好首先要退灰打反泵待新灰来后在料斗内搅拌再进行泵送。
必要时还要把料斗里的灰全放掉。
有的灰号比较高像C50、C60 粘稠度大隔上一会不打就会打不动,打料之前先反泵2个行程然后在开始泵送。
把泵管拆下来,用水冲洗,然后接上,从新用沙浆润管,打混凝土。
在等料期间,多打几次空车泵(料斗里要存有料),可有效避免堵管。
以上是个人经验下面是行内的规范处理方法:(一)泵送混凝土的要求:为了提高混凝土的可泵性,保证混凝土泵送能顺利进行,对混凝土材料本身,有下列几项特殊要求:1.用的石子最大粒径不大于输送管径的1/3,但对于卵石可适当加大。
2.在2.5-2.8之间,如过细,增加混凝土拌合物的粘性,影响可泵性;如过粗,则容易离析,产生堵管现象。
3.比设计的原则不变,但要有良好的可泵性,使混凝土拌合物有适合的坍落度,不离析、不泌水,泵送过程中,坍落度损失不大于20mm。
坍落度过小时,增大拌合物对输送管管壁的摩擦阻力;坍落度过大时,则在压力下容易产生离析,都容易引起泵管堵塞。
一般认为,坍落度控制在100-150mm范围内最好(这点有点不太现实,个人认为160-180之间最利于泵送)。
4.土水灰比最好为0.45-0.50,根据泵送管管径和泵送距离不同,最小水泥用量不应小于280-300kg/m?(这个水泥最小用量我个人理解为粉料的用量),砂率可略微大些。
5.善可泵性,并减少混凝土干缩,一般掺入流动化剂外,还可掺入粉煤灰。
(二)预防泵管堵塞的措施1. 择适合泵送混凝土技术条件,根据气温、泵送高度和有关条件来调整混凝土配合比。
2. 严禁在施工现场向搅拌车内加水,更不能向泵机内加水。
3. 控制商品混凝土运输时间,制定合理的配车计划,采取在拌合站和施工现场二次掺入减水剂,以延长混凝土凝结时间。
泵送砼堵管原因分析及控制措施

泵送砼堵管原因分析及控制措施一、泵送砼堵管原因分析:1.液化硬化:砼中掺加过多的外加剂,导致其液化性能过强,泵送过程中砼流动性减弱,粘度增加,易形成堵塞。
控制措施:严格按照砼设计配合比进行施工,掺加外加剂不宜超过设计要求。
2.杂质:砼原材料中的杂质,如砂、石等颗粒过大,会堵塞砼泵的输送管道。
控制措施:加强对原材料的质量控制,确保原材料中的杂质符合相关标准。
3.砂浆、石子分离:砼在泵送过程中,砂浆和石子容易发生分离现象,导致泵送困难。
控制措施:加大搅拌时间,确保砂浆和石子充分混合;采用高性能减水剂,改善砂浆分离现象。
4.输送管道摩擦阻力:输送管道的内壁摩擦力增加,使得砼泵送受阻。
控制措施:定期清洗输送管道,减少管道内壁的摩擦系数;在管道内涂覆一层润滑膜,减少摩擦阻力。
5.管道弯曲半径过小:管道弯曲处过小的弯曲半径会造成砼在流动过程中堵塞。
控制措施:合理设计管道弯曲部分,保证弯曲半径不小于设计要求。
6.泵送距离过长:砼泵送距离过长,使得砼在泵送过程中水分逐渐减少,流动性降低,易产生堵管现象。
控制措施:根据砼设计配合比、泵送距离和泵送时间等因素,合理调整砼的配合比和砼的流动性。
7.泵送速度过快:泵送速度过快,砼在管道中的压力急剧增加,易引起堵管。
控制措施:合理设置泵的泵送速度,确保泵送过程中砼的压力和流速均在设计范围内。
二、泵送砼堵管的控制措施1.严格控制砼设计配合比,确保砼的流动性满足泵送要求。
2.加强原材料的质量控制,确保杂质含量符合相关标准。
3.加强搅拌时间,保证砂浆和石子充分混合,预防砂浆和石子分离。
4.定期清洗输送管道,减少管道内壁的摩擦系数,并在管道内涂覆润滑膜。
5.合理设计管道弯曲部分,保证管道的弯曲半径符合设计要求。
6.根据砼设计配合比、泵送距离和泵送时间等因素,合理调整砼的配合比和流动性。
7.合理设置泵的泵送速度,确保砼在泵送过程中的压力和流速均在设计范围内。
8.加强泵送过程的监控,及时发现问题并采取相应的措施进行处理。
如何化解混凝土泵送堵管问题

如何化解混凝土泵送堵管问题高层建筑等工程、大体积混凝土等工程离不开泵送混凝土,因其具备的施工速度快、施工质量好、施工方便等优点,可以说是"人见人爱";,实际使用中,堵管可是个常见的麻烦事儿,影响质量、降低效率,我们特意整理了泵送混凝土不堵管的秘诀,与您分享。
一、为什么会发生堵管?1材料出了问题主要包括3方面:混凝土离析、骨料粒径过大、余料量控制不当。
〔1〕拌制的混凝土中,粗细骨料之间未满覆水泥浆,胶结作用不充分,那么骨料较为离散,易导致泌水现象。
由于未形成有效的润滑膜,导致骨料与导管、骨料与骨料间摩擦力增大。
〔2〕粗骨料配置不合理,其中存在粒径较大者,导致混凝土整体流动性差。
〔3〕余料量控制缺乏,低于搅拌轴,导致吸入空气,发生堵管现象。
2设备出了问题主要包括2方面:导管发生漏浆、导管内清洗不彻底。
〔1〕假设导管密闭性差发生漏浆,会由于水泥浆的漏出导致混凝土整体流动性差,摩擦力大而导致堵管。
〔2〕前一次泵送结束后未按规定清洗导管,导致导管内不通畅,影响泵送。
以上两种问题均在导管转弯处尤其严重。
3管理出了问题主要包括3方面:速度过快、间歇时间过长、温度影响考虑不充分。
〔1〕首次泵送时未适当放慢速度,导致导管内部摩擦力过大发生堵管。
〔2〕间歇时间过长,导致混凝土在导管内到达初凝状态,使后续泵送受到阻碍,导致堵管。
〔3〕温度影响考虑不充分,对导管的保护不合理,导致水分蒸发过多或被冻结导致堵管。
二、怎么预防堵管?1、严选材料水泥浆量要充足;骨料粒径要严格筛选,卵石最大粒径应小于1/3导管直径,碎石的最大粒径应小于1/4导管直径,含砂率应大于40%;余料量应充足,保持高于搅拌轴。
注意检查混凝土坍落度,不合格者须二次搅拌后使用,一般为8~18cm,距离长、高度大时一般为15cm。
2、严控设备泵送时设专人巡视检查导管密闭性,发现泄露处立即处理修复;每次泵送结束必须清理导管,并设专人检查监督,每次泵送前须先检查导管内是否通畅。
混凝土泵堵管原因分析及控制措施

混凝土泵堵管原因分析及控制措施混凝土泵是一种将混凝土从搅拌站输送到施工现场的设备。
然而,由于各种原因,混凝土泵在工作过程中可能会出现管道堵塞的情况。
本文将就混凝土泵堵管的原因进行分析,并介绍相应的控制措施。
一、堵管原因分析1.混凝土质量问题:如果混凝土的配合比例不合理,或者掺有过多的泥浆和杂质,就容易造成堵管。
此外,混凝土中的颗粒过大,也容易导致泵管堵塞。
2.施工操作不当:在施工过程中,如果操作不当,例如混凝土泵的进料速度过大、管道弯曲角度过小、管道内的气压不稳定等,都会导致混凝土泵堵塞。
3.泵送距离过远:混凝土泵的管道长度限制了泵送距离。
如果超过了泵送距离的限制,就容易造成堵管现象。
二、控制措施1.选用合适的混凝土:在施工前应根据实际情况选择合适的混凝土配合比例,并确保混凝土的质量符合要求。
此外,混凝土中的颗粒大小应适中,以免造成管道堵塞。
2.加强施工管理:在施工过程中,应加强对混凝土泵的操作指导,确保操作人员按照正确的方式进行操作。
例如,控制混凝土泵的进料速度和管道的弯曲角度,保持管道内的气压稳定等。
3.控制泵送距离:在施工前应对泵送距离进行合理规划,确保不超过混凝土泵的管道限制。
如果需要泵送距离较远,可以适当增加泵送设备或采用其他辅助措施,如分段泵送、增加管道直径等。
除了以上的控制措施之外,还可以采用以下几种方法来解决混凝土泵堵管问题:1.冲击管道:如遇到轻微的堵塞情况,可以通过向堵塞部位喷水或用气压冲击的方式进行疏通。
2.更换泵送管道:如堵塞较严重,无法通过冲击疏通,则需要更换泵送管道。
3.清洗管道:定期对混凝土泵的管道进行清洗,以去除管道内的混凝土残留物,并保持管道畅通。
总之,要想有效控制混凝土泵堵管问题,首先需要保证混凝土的质量和施工操作的正确性。
此外,合理规划泵送距离、定期清洗管道等措施也是必不可少的。
只有通过科学有效的控制措施,才能降低混凝土泵堵管的发生率,提高施工效率。
泵送混凝土施工堵管成因及防治措施

泵送混凝土施工堵管成因及防治措施1.中建八局西北公司,陕西西安 7100002.浙江江南工程管理股份有限公司,浙江杭州 310000随着泵送混凝土泵技术的的广泛应用,极大地提高了混凝土施工的效率,节约了建筑成本。
但随着近年来建筑物建筑高度越来越高,逐渐提上了混凝土泵送的高度和泵送难度,导致混凝土堵管与爆管的事件时有发生,严重影响施工的进度与施工的质量,已成为业内一个公认的问题。
本文将依据工程实际,并结合作者的观察与思考,对泵送混凝土过程堵管的常见原因进行深入分析,并有针对性的给出具体的防治措施以及施工管理建议。
1.施工人员操作原因导致堵管1.泵送速选择不当对于混凝泵送建设项目,泵送速度的选择是成功泵送的关键。
应根据混土实际情实时调节泵送速度,并选择在刚开始是低速泵送,然后逐渐加速,最后正常泵送。
速度过大或过小都可能造成管道堵塞。
泵送速度的设定需要在可控范围内。
管道清洗和管道润滑混凝后上泵第一次泵送时,应以适当的1.1.管路未清洗,润滑不彻底抽水施工操作人员的专业技能还不够。
泵送前未按要求对管道进行清洗润滑,或管道清洗润滑不彻底,造成管道堵塞。
1.1.停机时间过长停机时间过长(一般不超过5-10分钟),在一定条件下,如混凝土不能及时供给。
在间歇过程中,管道残余剩料将会在管道内初步凝结。
初凝会增加泵送阻力并导致管道堵塞。
在建设项目集中的地区和施工旺季,这是造成管道堵塞的主要原因。
1.1.管道内壁清洗不干净每次混凝土输送完毕后,都必须用足量的水将管壁内残留的碎石、砂浆冲洗干净,并在输送管道出入口封堵防尘。
必要时全线洗净,将布设的弯头拆下人工清洗。
否则,管壁内积压的残渣会越来越厚,极易造成泵机泵送阻力增大而出现爆管及堵管。
接管前应检查管壁厚度,较薄的及时更换新管,并确保卡扣接头紧密。
2管道连接原因导致堵管管道连接或弯头部分,在泵送过程中经常发生管道堵塞,为了减少泵送阻力,抑制管道堵塞风险的发生应遵循以下原则:距离最短,混泥土泵与施工地点,尽量按两点间最短路线布置管线;尽量减少弯头的使用,并且在使用弯头时,尽量使用大角度弯头,且避免连续转弯的的设计。
泵送混凝土施工堵管成因及防治措施

0引言在大型的建筑工程领域,常常会遇到一些复杂的施工场景人员无法有效施工作业,如混凝土的运输在复杂的工况环境下会对施工带来诸多挑战,既有施工安全隐患,也会拖延施工时间,对混凝土的质量带来影响。
因此,为了更好的满足工程类项目对混凝土的需求,便出现了泵送混凝土施工技术,这种技术的出现解决了混凝土在复杂环境的运输问题,使得混凝土可以及时运输到各种工况,同时提高作业的效率与质量。
不过泵送混凝土施工常常出现故障问题,常见的问题包括了堵管、管道破裂等,需要解决这一问题就需要对泵送运输过程进行全面研究,分析具体原因。
因此,这里就围绕着泵送混凝土施工堵管成因做研究,并给出策略参考。
1人员操作上引发的泵送堵管问题1.1工况中不合理的泵型选择与工作条件在复杂的工况作业中,操作人员需要对工况环境做全面、细致的研究了解泵送的作业环境,特别是地质、气象、自然因素,同时考虑到泵送的高度、距离、压力等因素,合理的选择负责工作条件的泵送类型与设备。
只有根据具体情况合理进行分析才能满足于泵送的工作要求,但在实际工程中很多工作人员并没有充分考虑这些因素导致泵送堵管问题出现。
1.2操作人员在工作中不集中的工作一般来说,泵送混凝土施工在很多工地是在夜间进行,这段时间很多工人存在疲倦、工作不仔细、不认真,甚至出现危险事故等现象,导致对泵送设备的操作人员无法根据泵送的实际情况及时进行压力表的读取,对相关操作的调整,而这种忽视泵送设备运行的行为,很容易导致泵送的混凝土出现堵管问题。
通常出现压力表读表异常问题,需要马上反泵2~3个行程,再正泵这样可以反复操作解决堵管问题,但实际上工作人员的疏忽,并没有进行操作若做了以上内容没解决问题,还需要拆除管道进行全面清洗作业。
1.3不合理的对混凝土材料加水很多工地都会对混凝土有明确的使用要求与存储要求,不过混凝土受到调配方式、时间、温度等情况混凝土的各方面性能都容易发生改变,通常发生改变需要及时通知混凝土站试验技术人。
混凝土泵堵管处理

混凝土泵堵管处理
混凝土泵堵管处理主要有以下几种方法:
1. 停止泵送:当混凝土泵堵管时,首先需要停止泵送,以避免产生更大的堵塞。
2. 清理管道:使用适当的工具,如短管、弹簧杆等,将堵塞在管道中的混凝土清理出来。
可以使用水压冲击或者手动清理的方式。
3. 高压清洗:使用高压水射流清洗管道,将堵塞物冲洗出来。
这种方法适用于管道内有较多的沉积物或固结混凝土。
4. 倒转泵送:有时候可以通过改变泵送方向,将堵塞物推出来。
这种方法适用于管道内的堵塞较为轻微。
5. 使用化学溶解剂:根据具体情况,可以使用化学溶解剂来溶解混凝土堵塞物,然后再用水冲洗清理管道。
6. 拆卸管道:当以上方法都无效时,可以考虑拆卸管道进行清理。
这需要施工人员具备相应的技术和工具,且会带来一定的时间和人力成本。
需要注意的是,在进行任何处理之前,应确保施工人员的安全,并且按照相关标准和规定进行操作。
泵送混凝土堵泵、堵管的成因及解决方法分析
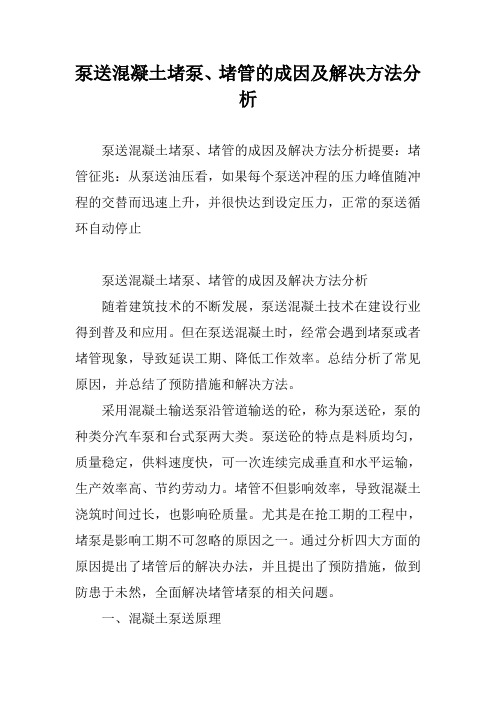
泵送混凝土堵泵、堵管的成因及解决方法分析泵送混凝土堵泵、堵管的成因及解决方法分析提要:堵管征兆:从泵送油压看,如果每个泵送冲程的压力峰值随冲程的交替而迅速上升,并很快达到设定压力,正常的泵送循环自动停止泵送混凝土堵泵、堵管的成因及解决方法分析随着建筑技术的不断发展,泵送混凝土技术在建设行业得到普及和应用。
但在泵送混凝土时,经常会遇到堵泵或者堵管现象,导致延误工期、降低工作效率。
总结分析了常见原因,并总结了预防措施和解决方法。
采用混凝土输送泵沿管道输送的砼,称为泵送砼,泵的种类分汽车泵和台式泵两大类。
泵送砼的特点是料质均匀,质量稳定,供料速度快,可一次连续完成垂直和水平运输,生产效率高、节约劳动力。
堵管不但影响效率,导致混凝土浇筑时间过长,也影响砼质量。
尤其是在抢工期的工程中,堵泵是影响工期不可忽略的原因之一。
通过分析四大方面的原因提出了堵管后的解决办法,并且提出了预防措施,做到防患于未然,全面解决堵管堵泵的相关问题。
一、混凝土泵送原理混凝土泵是通过管道依靠压力输送混凝土的施工设备,混凝土泵液压系统一般为高压大流量系统。
正常情况下,混凝土在泵送管道中心形成柱状流体,呈悬浮状态流动。
流体表面包有一层水泥浆,水泥浆层作为一种润滑剂与管壁接触,骨料之间基本上不产生相对运动。
当粗骨料中的某些骨料运动受阻,后面的骨料运动速度因受影响而渐渐滞缓,致使管道内粗骨料形成集结,支撑粗骨料的砂浆被挤走,余下来的间隙由小骨料填补。
这样,骨料密度增大,使该段管道内集合物沿管道径向膨胀,水泥浆润滑层被破坏,运动阻力增大,速度变慢,直至运动停止而产生堵塞。
泵送过程中由于压力作用,一部分水泥砂浆被挤向外层,在粗骨料与管壁之间形成一个润滑层。
砼只有保持这种状态,泵造才能顺利进行。
二、混凝土输送泵堵管原因分析1、进料(混凝土)的原因导致堵管。
堵管征兆:从泵送油压看,如果每个泵送冲程的压力峰值随冲程的交替而迅速上升,并很快达到设定压力,正常的泵送循环自动停止,主油路溢流阀发出溢流响声,就表明已经堵管。
浅谈泵送混凝土堵管现象解决方法

塌 落度 来确 定 的 , 一般 而 言在 5 ~ 1 0 mi n便 需要 开 泵 一 次 。 如 果
停 机 的 时 间 过 长 么 那 么很 容 易 导 致 管 道 内 混 凝 土 的 凝 结 . 这
随 着 我 国基 础设 施 步 伐 的 加 快 .在 工程 建设 大 体 积 混 凝 土 浇
在正常情况 下, 该 混 凝 土 以柱 体 的形 式进 行 流 动 . 该 柱 体
( 1 ) 在 进 行 管 道 的 布 置 时应 当确 保 布置 的 管道 最短 . 对 于
形 成 在 管 泵送 流 体 流 动 的 悬 浮 液 中心 。 其 表 面涂 有 一 层 流 体 灌浆 , 灌 浆 层被 作 为 其 与 管 壁 之 间接 触 的 润 滑 剂 . 在混凝 土的
1 概 述
泵 送 混 凝 土 是 在 混 凝 土 浇 筑施 工过 程 中利 用 混 凝 土 泵 车
( 4 ) 停 歇 时 间 过 长 。 在 一 般 的 泵送 过 程 中 。 停 机 的 时 间 并
不是 固定 的 , 需要 根 据 当地 的 具 体 温度 、 混 凝 土初 凝 时 间 以及
和 输 送 管 道 把 成 品 混 凝 土 直 接 送 入 仓 的 一 种 混 凝 土 输 送 方 式, 其具有速度 快、 效率高、 节省人力、 能连 续作业等 的特点 。
在 管 道 连 接 的 过 程 中一 定 要 遵 从 相 应 的连 接 方 法 。如 果 管 道 连接 错 了那 么 便 会 容 易产 生堵 管 。连 接 管道 时具 体 需要
遵守以下几个原则 :
送 混凝 土 对设 备 、 原材料、 操 作 都 具 有 较 高要 求 。
2 堵管 原因分析
超高层泵送混凝土堵管原因及防治措施
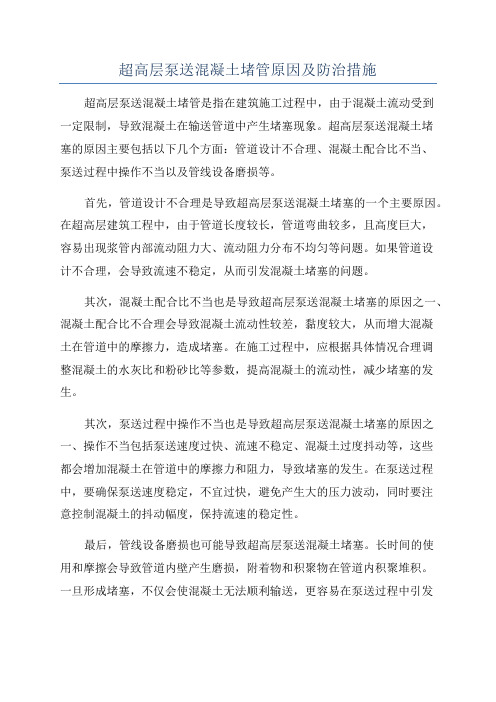
超高层泵送混凝土堵管原因及防治措施超高层泵送混凝土堵管是指在建筑施工过程中,由于混凝土流动受到一定限制,导致混凝土在输送管道中产生堵塞现象。
超高层泵送混凝土堵塞的原因主要包括以下几个方面:管道设计不合理、混凝土配合比不当、泵送过程中操作不当以及管线设备磨损等。
首先,管道设计不合理是导致超高层泵送混凝土堵塞的一个主要原因。
在超高层建筑工程中,由于管道长度较长,管道弯曲较多,且高度巨大,容易出现浆管内部流动阻力大、流动阻力分布不均匀等问题。
如果管道设计不合理,会导致流速不稳定,从而引发混凝土堵塞的问题。
其次,混凝土配合比不当也是导致超高层泵送混凝土堵塞的原因之一、混凝土配合比不合理会导致混凝土流动性较差,黏度较大,从而增大混凝土在管道中的摩擦力,造成堵塞。
在施工过程中,应根据具体情况合理调整混凝土的水灰比和粉砂比等参数,提高混凝土的流动性,减少堵塞的发生。
其次,泵送过程中操作不当也是导致超高层泵送混凝土堵塞的原因之一、操作不当包括泵送速度过快、流速不稳定、混凝土过度抖动等,这些都会增加混凝土在管道中的摩擦力和阻力,导致堵塞的发生。
在泵送过程中,要确保泵送速度稳定,不宜过快,避免产生大的压力波动,同时要注意控制混凝土的抖动幅度,保持流速的稳定性。
最后,管线设备磨损也可能导致超高层泵送混凝土堵塞。
长时间的使用和摩擦会导致管道内壁产生磨损,附着物和积聚物在管道内积聚堆积。
一旦形成堵塞,不仅会使混凝土无法顺利输送,更容易在泵送过程中引发管道破裂,造成严重后果。
为了预防这种情况的发生,应定期检查管道内壁情况,及时清洁和更换磨损的管道。
针对上述问题,可以采取以下防治措施:1.合理设计管道:在超高层建筑施工中,要进行合理设计管道,尽量减少弯曲处,降低管道内摩擦阻力。
2.调整混凝土配合比:根据具体情况,合理调整混凝土的水灰比和粉砂比等参数,提高混凝土的流动性。
3.规范操作:在泵送过程中,要确保操作规范,泵送速度稳定,不宜过快,避免产生大的压力波动。
浅谈泵送砼堵管故障分析及其排除方法

浅谈泵送砼堵管故障分析及其排除方法泵送砼堵管是在砼输送过程中常见的故障现象之一、堵管会导致砼输送中断、设备损坏,甚至造成事故发生。
因此,及时分析和排除泵送砼堵管故障非常重要。
泵送砼堵管的原因有很多,如砂浆水泥比例过高、砂浆中添加的外加剂使用不当、砂浆中颗粒过大、管道内部结渣等。
下面就几种常见的故障原因及其排除方法进行详细分析。
首先,砂浆水泥比例过高是导致泵送砼堵管的常见原因之一、当水泥与砂浆的比例过高时,砂浆会变得过于黏稠,导致堵管。
解决这个问题的方法是调整砂浆中水泥的用量,使其与砂浆中其他成分的比例适当。
其次,砂浆中添加的外加剂使用不当也是导致泵送砼堵管的原因之一、外加剂的使用不当会导致砂浆粘度过高,使得砂浆无法顺利通过管道。
解决这个问题的方法是使用合适的外加剂,并按照说明书中的比例进行加入。
同时,还需要根据具体情况调整外加剂的用量。
此外,砂浆中颗粒过大也会引起泵送砼堵管。
过大的颗粒会堵塞管道,从而使砼无法正常通过。
解决这个问题的方法是控制砂浆中颗粒的大小,确保其能够顺利通过管道。
如果发现颗粒过大,可以进行筛分或调整砂浆的配比,以减小颗粒的尺寸。
最后,管道内部结渣也是泵送砼堵管的常见原因之一、随着砼的输送,管道内壁会逐渐结成固体,形成结渣堵塞。
解决这个问题的方法是定期清洗管道,以确保管道内部的畅通。
清洗管道时可以使用高压水射流进行冲洗,或者使用特殊的清洗剂进行清洗。
综上所述,泵送砼堵管故障的分析及排除方法主要包括调整砂浆配比、使用合适的外加剂、控制砂浆颗粒大小和定期清洗管道等。
通过及时发现故障原因,采取相应的排除方法,可以有效避免泵送砼堵管故障的发生,确保砼输送的安全和正常进行。
泵送混凝土砼堵管解决方法

泵送混凝土砼堵管解决方法
一、原因
(1)砼和易性差,离析,砼稀散。
(2) 砼拌合物塌落度小(干粘)。
(3)砼拌合物抓底、板结。
(4)采用单粒级石子,石子粒径太大,泵送管道直径小。
(5)石子针片状多。
(6)泵车压力不够,或是管道密封不严密。
(7) 胶凝材料少,砂率偏低。
(8)弯管太多。
(9)管中异物未除尽。
(10)搅拌砼时,不均匀,水泥成块未松散成水泥浆。
(11)第一次泵送砼前未用砂浆润滑管壁。
二、解决途径
(1)检查砼输送管道的密切性和泵车的工作性能,使其处于良好的工作状态。
(2)检查管道布局,尽量减少弯管,特别是≤90°的弯管。
(3)泵送砼前,一定要用砂浆润滑管道。
(4)检查石子粒径、粒形是否符合规范、泵送要求。
(5)检查入泵处砼拌合物的和易性,砂率是否适合,有无大的水泥块,拌合物是否泌水、抓底或板结等现象,若有,采取相应的措施(见砼泌水、离析问题)。
(6)检查入泵处砼塌落度、黏聚性是否足够,若塌落度不足,则适量提高砼外加剂的掺量,或在入泵处掺加适量的高效减水剂,若是砼黏聚性不足,则适量增大砂率或是掺加适量的Ⅱ级粉煤灰。
(7)检查砼的初始塌落度是否≥20cm,若是砼塌落度损失快而引起的砼堵泵现象,则应首先解决砼损失问题。
泵送混凝土堵管的成因及预防措施研究

1泵送混凝土出现堵管的原因1.1泵送剂与水泥相容性差导致堵管水泥和泵送剂的相容性能不良针对化学外加剂和水泥之间相容性的分析,其是重要的一个问题存在。
工程实践表明:普通的泵送剂匹配于C3A值低于8%的水泥,当水泥中C3A值大于8%且远距离运输的情况下,坍落度大打折扣[1],造成泵送困难、堵管。
经更换水泥后,泵送再也没有因为急凝、外加剂与水泥的不相容以及较快的坍落度损失等情况出现而受到影响。
可见选择合适的泵送剂在远距离运输泵送混凝土施工中至关重要。
1.2水泥生产过程中的管理不当引起混凝土急凝大多数的水泥厂都属于立窑生产模式,因而在磨机过程中添加石膏时,会因为受到天气因素的影响,使得石膏没有分类别的在料仓中存放,当半水石膏和二水石膏混在一起时,再加上雨水的作用,必然会使二水石膏粘连在一起。
此时工作人员就不愿意选择二水石膏,而是会选择半水石膏或者不粘的硬石膏,甚至将二水石膏全部替换成硬石膏。
众所周知,石膏能够对硅酸盐硬化的速度和凝结的时间起到控制作用,但是该作用是与石膏在水泥中所存在的含量和形态密切相关的,石膏形态的不同其溶解度也会有差异,随之会有不相同的外加剂适应性,相应的,会明显降低减水能力,有时还可能因为较快流动度损失的原因使石膏凝结的过程出现异常。
1.3不达标的砂颗粒,使得堵塞反复出现有的碎石厂为了使自家颗粒达到相关级配标准,就用水冲洗机制砂,冲走粉料,待筛除细小的颗粒后,就只有5%左右的剩余,此时将砂平均的粒径提高到了2%,然而依然没有改善可泵性,反而在同一条件下增多了堵管现象。
笔者从相关的试验中了解到:当砂中具有较高的石粉含量时,不但不会下降强度,还会提高;相对于粗骨料而言,细骨料对于混凝土的可泵性较大,因而能够顺利的在混凝土输送的管中流动,并且管壁因为受到砂浆润滑的作用,会使粗骨料总是在灰浆中悬浮。
针对于这样的现象需要通过破碎机间隙进行调整,在破碎机中将经水冲洗后的破碎河卵石放入,此时需要用亚甲蓝对其含泥量进行编订,得到的结果是一千一百零四,筛分的结果是零一三一五,并且能够达到15%左右的颗粒余量,明显改善了镀管现象。
混凝土泵堵管的解决方案

混凝土泵堵管的解决方案在混凝土的泵送施工中,最令人头疼的问题便是堵管。
造成堵管的原因有哪些?如何预防?我们总结了如下所述几点原因,并提出预防措施。
1 操作不当容易造成堵管1.1 操作人员精力不集中输送泵操作人员在泵送施工中应精力集中,时刻注意泵送压力表的读数,一旦发现压力表读数突然增大,应立即反泵2-3个行程,再正泵,堵管即可排除。
若已经进行了反泵(正泵几个操作循环,仍未排除堵管,应及时拆管清洗,否则将使堵管更加严重。
1.2 泵送速度选择不当泵送时,速度的选择很关键,操作人员不能一味地图快,有时欲速则不达。
首次泵送时,由于管道阻力较大,此时应低速泵送,泵送正常后,可适当提高泵送速度。
当出现堵管征兆或某一车混凝土的塌落度较小时,应低速泵送,将堵管消灭在萌芽状态。
对中联集团HBT105.21.286RS系列混凝土泵,泵送速度的大小是通过调节调速阀来实现的,对三一集团HBT120C-2120D系列混凝土泵,泵送速度的大小是通过调节排量的大小来实现的。
1.3 余料量控制不适当泵送时,操作人员须随时观察料斗中的余料,余料不得低于搅拌轴,如果余料太少,极易吸入空气,导致堵管。
料斗中的料也不能堆得太多,应低于防护栏,以便于及时清理粗骨料和超大骨料。
当某一车混凝土的塌落度较小时,余料可低于搅拌轴,控制在“S”管或吸入口以上,以减小搅拌阻力、摆动阻力和吸入阻力。
本办法仅适用于“S”阀系列混凝土泵。
1.4 混凝土的塌落度过小时采取措施不当当发现有一斗混凝土的塌落度很小,无法泵送时,应及时将混凝土从料斗底部放掉,若贪图省事,强行泵送极易造成堵管。
切忌在料斗中加水搅拌。
1.5 停机时间过长停机期间,应每隔5~10min(具体时间视当日气温、混凝土塌落度、混凝土初凝时间而定)开泵一次,以防堵管。
对于停机时间过长,已初凝的混凝土,不宜继续泵送。
1.6 管道未清洗干净上次泵送完毕,管道未清洗干净,会造成下一次泵送时堵管。
所以每次泵送完毕一定要按照操作规程将输送管道清洗干净。
- 1、下载文档前请自行甄别文档内容的完整性,平台不提供额外的编辑、内容补充、找答案等附加服务。
- 2、"仅部分预览"的文档,不可在线预览部分如存在完整性等问题,可反馈申请退款(可完整预览的文档不适用该条件!)。
- 3、如文档侵犯您的权益,请联系客服反馈,我们会尽快为您处理(人工客服工作时间:9:00-18:30)。
导言
因受场地的限制,泵送铺设线路较长,弯管较多,这一场景无法改变;也有混凝土级配、作业面工作穿插耽误的“间歇”时间等多种因素,导致现场泵管受堵时有发生。
混凝土输送泵管的堵塞也使混凝土在初凝后也无法进行第二次浇筑混凝土,这也给混凝土结构质量造成不同程度的质量缺陷。
堵管原因
壹
1、操作不当
(1)泵送速度选择不当。
泵送时,速度的选择很关键,操作人员不能一味的图快,欲速则不达,首次泵送时,由于管道阻力较大,此时应低速泵送,泵送正常后,可适当提高泵送速度。
当出现堵管征兆或某一车混凝土的坍落度较小时,应低速泵送,将堵管消灭在萌芽状态。
(2)余料量控制不当。
泵送时,操作人员须随时观察斗中的余料,余料不得低于搅拌轴,如果余料太少,极易吸入空气,导致堵管。
料斗中的料
也不能堆得太多,应低于防护栏,以便于及时清理粗骨料和超大骨料。
当某一车混凝土的坍落度较小时,余料可低于搅拌轴,控制在“S”管或吸入口以上,以减小搅拌阻力、摆动阻力和吸入阻力。
本办法仅适用于“S”阀系列混凝土泵。
(3)混凝土的坍落度过小时采取措施不当。
当发现有一斗混凝土的坍落度很小,无法泵送时,应及时将混凝土从斗料底部放掉,若图省事,强行泵送极易造成堵管。
2、管道连接
管道接法错误很容易导致堵管。
接管时应遵循以下原则:管道布置时应按最短距离、最少弯头和最大弯头来布管,尽量减少输送阻力,也就减少了堵管的可能性。
泵出口锥管处,不可直接连接弯管,应接入1段直管后,再接弯管。
泵送中途接管时,每次只能加接1根,且应用水润滑管道内壁,并排尽空气,否则极易造成堵管。
垂直向下的管道,出口处应装设防离析装置,预防堵管。
高层泵送时,水平管路的长度一般应不小于垂直管路长度的15%,且应在水平管路中接入管路截止阀。
停机时间超过5min时,应关闭截止阀,防止混凝土倒流,导致堵管。
由水平转垂直时的90°弯管,弯曲半径应大于500mm。
3、混凝土或砂浆离析
混凝土或砂浆遇水时,极易造成离析。
有事在泵送砂浆时,便发生堵管现象,就是因为砂浆与管道中的水直接接触后,砂浆离析而引起的。
预防办法是:泵前用水湿润管道后,从管道的最低点将管道接头松开,将余水全部放掉,或者在泵水之后泵送砂浆之前,放入一海绵球,将砂浆与水分开。
泵送完毕清洗管道时,也要放入一海绵球,将水与混凝土分开,否则极易造成堵管。
4、局部漏浆
由于砂浆泄漏掉,一方面影响混凝土的质量,另一方面漏浆后,将导致混凝土的坍落度减小和泵送压力的损失,从而导致堵管。
漏浆的原因主要有以下几种。
(1)输送管道接头密封不严。
输送管道接头密封不严,管卡松动或密封圈损坏而漏浆。
此时应紧固管卡或更换密封圈。
(2)眼镜板和切割环之间的间隙过大。
眼镜板和切割环磨损严重时,二者之间的间隙变大。
当间隙大于10%时,须通过调整异形螺栓来缩小眼镜板和切割环之间的间隙,若已无法调整,应立即更换磨损件。
本办法适用于“S”阀系列混凝土泵。
(3)混凝土泵活塞磨损严重。
操作人员应经常观察水箱中的水是否浑浊,有无砂浆,一旦发现水已浑浊或水中有砂浆,表明混凝土活塞已经磨损,此时应及时更换活塞,否则将因漏浆和压力损失而导致堵管,同时还会加剧活塞和输送缸的磨损。
(4)因混凝土输送缸严重磨损而引起的漏浆。
若每次更换活塞后,水箱中的水很快就变浑浊,而活塞是好的,则表明输送缸已磨损,此时需更换输送缸。
5、不合格的泵送混凝土
(1)混凝土的坍落度过大或过小。
混凝土坍落度的大小直接反映了混凝土流动性的好坏,混凝土的输送阻力随着坍落度的增加而减小。
泵送混凝土的坍落度一般在8~300px范围内,对于长距离和大高度的泵送一般需严格控制在375px左右。
坍落度过小,会增大输送压力,加剧设备磨损,并导致堵管。
坍落度过大,高压下混凝土易离析而造成堵管。
(2)含砂率过小、粗骨料级配不合理。
细骨料按来源可分为:河砂、人工砂(即机制砂)、海砂、山砂,其中河砂的可泵性最好,机制砂的可泵性最差。
细骨料按粒径可分为:粗砂、中砂、细砂,其中中砂的可泵性最好。
粗骨料按形状可分为:卵石、碎石,卵石的可泵性好于碎石。
骨料的最大粒径与输送管道的最小口径也有关系,卵石的最大粒径应小于1/3口径,碎石的最大粒径应小于1/4口径,否则也易引起堵管。
由于材料的不同,细骨料的含量(即含砂率)、粗骨料的级配都存在一个最佳值。
通常情况下,含砂率不宜太低,应大于40%,大粒径粗骨料的含量不宜过高。
合理地选择含砂率和确定骨料级配,对提高混凝土的泵送性能和预防堵管至关重要。
(3)水泥用量过少或过多。
水泥在泵送混凝土中,起胶结作用和润滑作用,同时水泥具有良好的保水性能,使混凝土在泵送过程中不易泌水,水泥的用量也存在一个最佳值,若水泥用量过少,将严重影响混凝土的吸入性能,同时使泵送阻力增加,混凝土的保水性变差,容易泌水、离析和发生堵管。
另外,水泥用量与骨料的形状也有关系,骨料的表面积越大,需要包裹的水泥浆也应该越多,相应地水泥的含量就越大。
因此,合理地确定水泥的用量,对提高混凝土的可泵性、预防堵管也很重要。
(4)外加剂的选用不合理,使混凝土的可泵性和流动性变差,从而导致堵管。
解决方案和改进措施
贰
(1)强化水泥生产管理的工作:不能混堆处理水泥厂的原材料,需要将水泥磨机配料的管理工作加强;在相关品种比例的遵循下对掺量后的水泥进行分类;需要将出库后的水泥温度控制在80℃左右的范围,装进罐车内的混凝土温度要低于60℃,避免因为急凝现象的发生使得堵管形成。
(2)由于各种因素导致泵送混凝土水灰比过大导致离析进而最终引起输送泵堵管的预防管理主要体现在:在用砂石搭棚时,需要注意W/C不会受到砂石含水率的影响;在罐车清洗以后,存在于罐体内的水需要全部倾倒出来,并保持干净;当在调凝的过程中使用外加剂时,需要对使用量有所掌握,在灌内实际混凝土量的遵循下,对混凝土水泥的使用量进行预算,坍落
度状况,加入原泵送剂立方量的1/5,加入次数不能超过3次,以免外加剂叠加超过掺量,使混凝土异常缓凝。
要严禁直接向罐车内加水。
(3)由于水泥初凝时间不够引起的堵管的预防管理主要是直接联系工地浇筑泵和调度之间的关系,将车距调好,以便加大坍落的损失;在夏季时节最好选用缓凝型的泵送剂,并确保在初凝的时间内完成泵送混凝土。
(4)质量管理的加强:待实验室测定了现场的实际情况后再进行混凝土泵送,对于那些没有达到要求的泵送坍落度,需要通过外加剂进行调配,并建立严格的惩罚制度,严禁有人私自向混凝土内加水。
(5)堵管的排查与清堵,使用铁锤对管道进行锤击,管内若有尖叫刺耳或者沉闷的声音发出,就说明找到了堵塞点;或者在泵机出口的位置,有专人一节节的排查,若在压力下有砂浆滑出,就一直排查直到没有滑出砂浆才停止,笔者根据自身的经验认为,在管道的两节之间是最容易发生堵塞的。
堵塞料斗:采取反泵方式,逆流输送混凝土便会将正常的泵送恢复,若料口被大块的堵死,即使是反泵也会不能够将该问题解决的,此时就必须采用人工排通的方式。
堵塞排料口:所倒入的稀混凝土需要具备较大的流动度,随后反反复复的进行正反泵的操作,若还是堵塞就采取人工治理的措施。
清洗:完成混凝土泵送以后,需要及时将输送管和混凝土泵清洗干净,便于二次使用,摩擦力的减小。