加氢反应器设计计算书
国产首台千吨级加氢反应器的设计
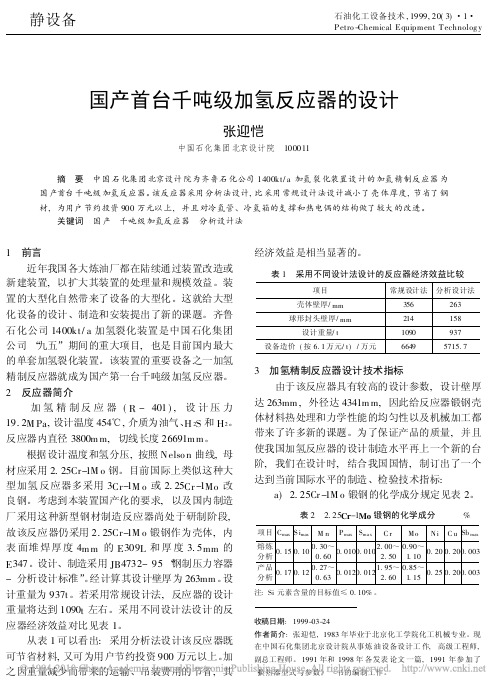
国产首台千吨级加氢反应器的设计张迎恺中国石化集团北京设计院 100011 摘 要 中国石化集团北京设计院为齐鲁石化公司1400kt/a加氢裂化装置设计的加氢精制反应器为国产首台千吨级加氢反应器。
该反应器采用分析法设计,比采用常规设计法设计减小了壳体厚度,节省了钢材,为用户节约投资900万元以上,并且对冷氢管、冷氢箱的支撑和热电偶的结构做了较大的改进。
关键词 国产 千吨级加氢反应器 分析设计法1 前言 近年我国各大炼油厂都在陆续通过装置改造或新建装置,以扩大其装置的处理量和规模效益。
装置的大型化自然带来了设备的大型化。
这就给大型化设备的设计、制造和安装提出了新的课题。
齐鲁石化公司1400kt/a加氢裂化装置是中国石化集团公司“九五”期间的重大项目,也是目前国内最大的单套加氢裂化装置。
该装置的重要设备之一加氢精制反应器就成为国产第一台千吨级加氢反应器。
2 反应器简介 加氢精制反应器(R-401),设计压力19.2M Pa,设计温度454℃,介质为油气、H2S和H2。
反应器内直径3800m m,切线长度26691m m。
根据设计温度和氢分压,按照Nelso n曲线,母材应采用2.25Cr-1M o钢。
目前国际上类似这种大型加氢反应器多采用3Cr-1M o或2.25Cr-1Mo改良钢。
考虑到本装置国产化的要求,以及国内制造厂采用这种新型钢材制造反应器尚处于研制阶段,故该反应器仍采用2.25Cr-1M o锻钢作为壳体,内表面堆焊厚度4m m的E309L和厚度3.5mm的E347。
设计、制造采用JB4732-95“钢制压力容器-分析设计标准”。
经计算其设计壁厚为263mm。
设计重量为937t。
若采用常规设计法,反应器的设计重量将达到1090t左右。
采用不同设计法设计的反应器经济效益对比见表1。
从表1可以看出:采用分析法设计该反应器既可节省材料,又可为用户节约投资900万元以上。
加之因重量减少而带来的运输、吊装费用的节省,其经济效益是相当显著的。
热壁式加氢反应器工艺设计
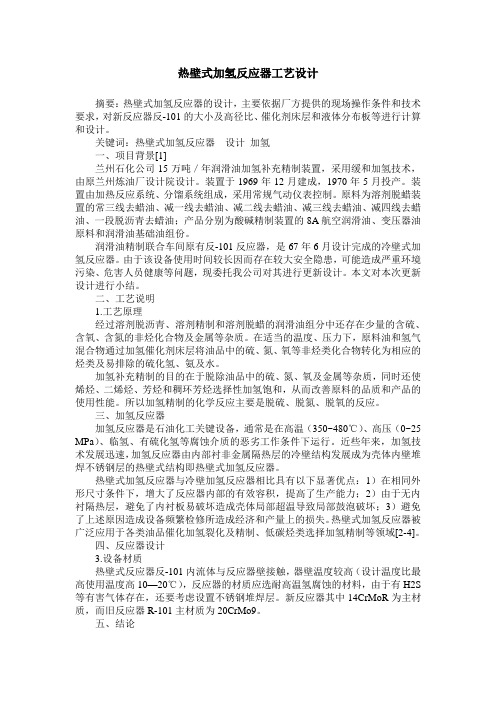
热壁式加氢反应器工艺设计摘要:热壁式加氢反应器的设计,主要依据厂方提供的现场操作条件和技术要求,对新反应器反-101的大小及高径比、催化剂床层和液体分布板等进行计算和设计。
关键词:热壁式加氢反应器设计加氢一、项目背景[1]兰州石化公司15万吨/年润滑油加氢补充精制装置,采用缓和加氢技术,由原兰州炼油厂设计院设计。
装置于1969年12月建成,1970年5月投产。
装置由加热反应系统、分馏系统组成,采用常规气动仪表控制。
原料为溶剂脱蜡装置的常三线去蜡油、减一线去蜡油、减二线去蜡油、减三线去蜡油、减四线去蜡油、一段脱沥青去蜡油;产品分别为酸碱精制装置的8A航空润滑油、变压器油原料和润滑油基础油组份。
润滑油精制联合车间原有反-101反应器,是67年6月设计完成的冷壁式加氢反应器。
由于该设备使用时间较长因而存在较大安全隐患,可能造成严重环境污染、危害人员健康等问题,现委托我公司对其进行更新设计。
本文对本次更新设计进行小结。
二、工艺说明1.工艺原理经过溶剂脱沥青、溶剂精制和溶剂脱蜡的润滑油组分中还存在少量的含硫、含氧、含氮的非烃化合物及金属等杂质。
在适当的温度、压力下,原料油和氢气混合物通过加氢催化剂床层将油品中的硫、氮、氧等非烃类化合物转化为相应的烃类及易排除的硫化氢、氨及水。
加氢补充精制的目的在于脱除油品中的硫、氮、氧及金属等杂质,同时还使烯烃、二烯烃、芳烃和稠环芳烃选择性加氢饱和,从而改善原料的品质和产品的使用性能。
所以加氢精制的化学反应主要是脱硫、脱氮、脱氧的反应。
三、加氢反应器加氢反应器是石油化工关键设备,通常是在高温(350~480℃)、高压(0~25 MPa)、临氢、有硫化氢等腐蚀介质的恶劣工作条件下运行。
近些年来,加氢技术发展迅速,加氢反应器由内部衬非金属隔热层的冷壁结构发展成为壳体内壁堆焊不锈钢层的热壁式结构即热壁式加氢反应器。
热壁式加氢反应器与冷壁加氢反应器相比具有以下显著优点:1)在相同外形尺寸条件下,增大了反应器内部的有效容积,提高了生产能力;2)由于无内衬隔热层,避免了内衬板易破坏造成壳体局部超温导致局部鼓泡破坏;3)避免了上述原因造成设备频繁检修所造成经济和产量上的损失。
钢制加氢反应器的设计

・ (( ・
少约 !"#, 既节省材料, 又方便运输 和 吊 装。 $%&’ 一是从冶 ()*’! " + 钢之所以有较高的应力强度: 炼和锻造工艺技术上保证了钢材的高纯洁、 高致 密、 高均匀性; 二是通过 “锻后热处理” 、 “ 性能热处 理” 这两道关键工序, 得到的是充分的下贝氏体组 织。对于钢材的组织来讲, 若杂质少、 致密性强、 金 相组织均匀, 就能获得较高的强度和韧性; 而下贝 氏体组织本身就具有优良的综合机械性能, 它能将 较高的强度和塑性与韧性很好的配合。下贝氏体 的亚结构高密度位错以及细小碳化物在下贝氏体 铁素体内沉淀析出, 是保证下贝氏体具有优良综合 机械性能的主要原因
" ! ( )*’ $ ,"- $ +"& $ ./) ( )* (), 33 4) 式中元素以 )*
02
01
( 33 4)含量代入。
-)回火脆化倾向评定试验结果 # $ % ,+ $ 5!# $ % ,+!*
表 ! "#$%&’(%" !) 钢的力学性能
& :; !" ( 0 )<= ) 6> (室温) , (室温) , (+,*= ) 6 (室温) 6 (室温) 6 三个试样允许一 9 %’7 %’7 9 %’7 平均值 个试样
!"#$%&’$ ! " ( 钢制加氢反应器的设计
栾海林, 崔云海
(抚顺石油化工设计院, 辽宁 抚顺 摘 !!"##$)
要: 抚顺石化分公司 !%##&’ ( ) 催化柴油中压加氢精制 (改质) 装置中的两台高温高压加氢反应器,
由于采用了抗氢性能好、 应力强度高的 "*+,!-.,! 同时采用了有限元分析设计法, 因此不仅降低 " / 新材料, 了反应器壳体的厚度, 更重要的是提高了反应器的综合技术性能。另外, 对 "*+,!-.,! 新型抗氢钢的推 / " 广应用起到了积极的促进作用。 关键词: 新型抗氢钢; 临氢设备; 分析设计法 中图分类号: 012$$ 文献标识码: (%##%) 3 文章编号: !##$,44#5 #5,##!#,#6
一级加氢反应器制造方案
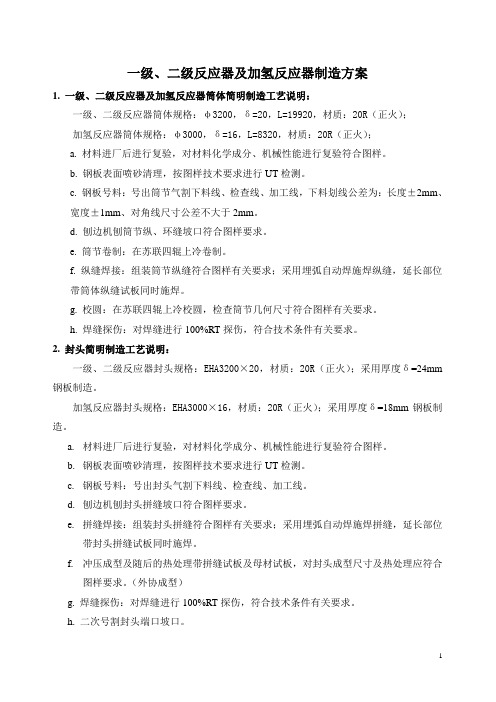
一级、二级反应器及加氢反应器制造方案1. 一级、二级反应器及加氢反应器筒体简明制造工艺说明:一级、二级反应器筒体规格:φ3200,δ=20,L=19920,材质:20R(正火);加氢反应器筒体规格:φ3000,δ=16,L=8320,材质:20R(正火);a. 材料进厂后进行复验,对材料化学成分、机械性能进行复验符合图样。
b. 钢板表面喷砂清理,按图样技术要求进行UT检测。
c. 钢板号料:号出筒节气割下料线、检查线、加工线,下料划线公差为:长度±2mm、宽度±1mm、对角线尺寸公差不大于2mm。
d. 刨边机刨筒节纵、环缝坡口符合图样要求。
e. 筒节卷制:在苏联四辊上冷卷制。
f. 纵缝焊接:组装筒节纵缝符合图样有关要求;采用埋弧自动焊施焊纵缝,延长部位带筒体纵缝试板同时施焊。
g. 校圆:在苏联四辊上冷校圆,检查筒节几何尺寸符合图样有关要求。
h. 焊缝探伤:对焊缝进行100%RT探伤,符合技术条件有关要求。
2. 封头简明制造工艺说明:一级、二级反应器封头规格:EHA3200×20,材质:20R(正火);采用厚度δ=24mm 钢板制造。
加氢反应器封头规格:EHA3000×16,材质:20R(正火);采用厚度δ=18mm钢板制造。
a.材料进厂后进行复验,对材料化学成分、机械性能进行复验符合图样。
b.钢板表面喷砂清理,按图样技术要求进行UT检测。
c.钢板号料:号出封头气割下料线、检查线、加工线。
d.刨边机刨封头拼缝坡口符合图样要求。
e.拼缝焊接:组装封头拼缝符合图样有关要求;采用埋弧自动焊施焊拼缝,延长部位带封头拼缝试板同时施焊。
f.冲压成型及随后的热处理带拼缝试板及母材试板,对封头成型尺寸及热处理应符合图样要求。
(外协成型)g. 焊缝探伤:对焊缝进行100%RT探伤,符合技术条件有关要求。
h. 二次号割封头端口坡口。
3.法兰的简明制造工艺说明法兰材料为12Cr2Mo1Ⅱ,具体工艺如下:a. 材料进厂后进行复验,对材料化学成分、机械性能进行复验符合图样。
乙炔加氢反应器
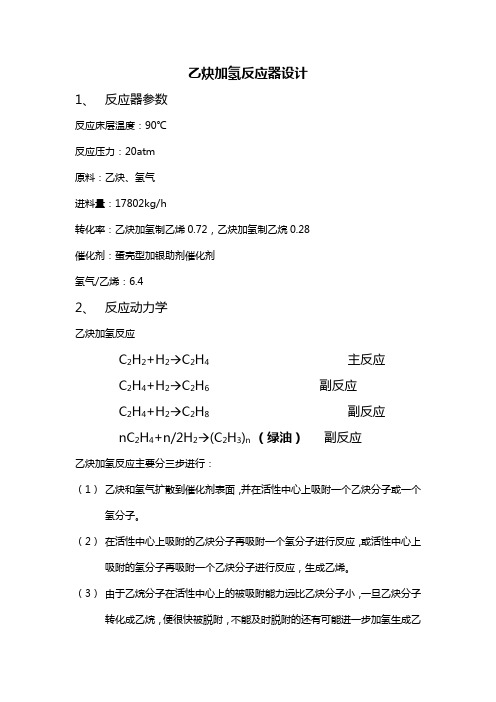
乙炔加氢反应器设计1、反应器参数反应床层温度:90℃反应压力:20atm原料:乙炔、氢气进料量:17802kg/h转化率:乙炔加氢制乙烯0.72,乙炔加氢制乙烷0.28催化剂:蛋壳型加银助剂催化剂氢气/乙烯:6.42、反应动力学乙炔加氢反应C2H2+H2→C2H4 主反应C2H4+H2→C2H6 副反应C2H4+H2→C2H8 副反应nC2H4+n/2H2→(C2H3)n (绿油)副反应乙炔加氢反应主要分三步进行:(1)乙炔和氢气扩散到催化剂表面,并在活性中心上吸附一个乙炔分子或一个氢分子。
(2)在活性中心上吸附的乙炔分子再吸附一个氢分子进行反应,或活性中心上吸附的氢分子再吸附一个乙炔分子进行反应,生成乙烯。
(3)由于乙烷分子在活性中心上的被吸附能力远比乙炔分子小,一旦乙炔分子转化成乙烷,便很快被脱附,不能及时脱附的还有可能进一步加氢生成乙烷然后再脱附,活性中心马上开始下一个乙炔加氢的反应。
催化剂对烃的吸附速度炔烃>双烯烃>烯烃>饱和烷烃催化剂对烃的解吸速度饱和烷烃>烯烃>双烯烃>炔烃通过乙炔加氢生成乙烯和乙烷这个简化串联反应来讨论2222242612H H C H C H C H r r ++>>根据幂数型经验式与动力学方程式关联,乙炔加氢速度可表示为11111ABH r k cc c αβθ=根据阿伦尼乌斯关系式'101/k k e E RT=-式中 A c —乙炔浓度 B c —乙烯浓度 1k —乙炔加氢速度常数T —反应温度对于固定床反应器,催化剂运转时间D 对1k 的影响,11()/'10E k D R Tk k e-+=乙炔加氢生成乙烯的速度式11()/'11110E k D RTABH r k ecc c αβθ-+=同理,乙烯加氢的速度式22()/''22220E k D RTABHr k ecc c αβθ-+=一种用于乙炔加氢制乙烯的蛋壳型催化剂,其特征是以氧化铝为载体采用浸渍法制备活性铝呈蛋壳型分布的负载型催化剂并采用Ag 对蛋壳型Pd/Al 2O 3催化剂进行改性,其特征是负载量是Pd0.01-0.1wt%,Ag 与Pt 原子比是1-5。
加氢反应器强度设计及理论计算
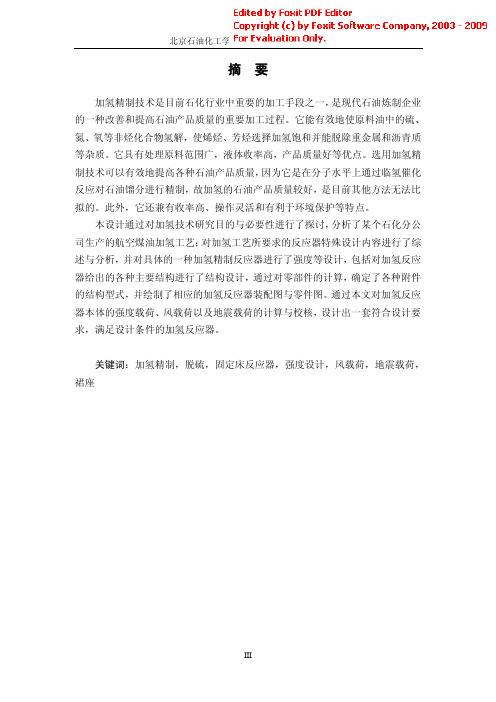
加氢反应器强度设计及理论计算
5.5 加氢反应器几何尺寸....................................................................................41 5.6 加氢反应器强度设计....................................................................................42 5.7 加氢反应器强度校核....................................................................................43 5.8 加氢反应器零部件设计................................................................................45 5.9 加氢反应器人口手孔设计............................................................................47 5.10 加氢反应器设备接口....................................................................................50 5.11 加氢反应器裙座设计....................................................................................53 5.12 地震载荷........................................................................................................63 5.13 风载荷............................................................................................................67 第六章 结 论..........................................................................................................70 参考文献...................................................................................................................... 71 致 谢..........................................................................................................................73 独创性声明.................................................................................................................. 74 学位论文电子版授权使用协议.................................................................................. 74
加氢精制反应器强度计算及特定结构的设计

主 要 参 数
设计 温度 ( ) 最高操作 温度 ( ℃)
设计压力 ( MP a ) ( G )
封头 ,法兰采用整体式法兰结构 ,支撑结构采用裙 座 式 结 构 。 内件 材 料 为 ¥ 3 2 1 6 8 ,对 应 法 兰 材 料 为
阶梯冷却后与经 M i n . P WH T后 的夏 比冲击功为 5 4 J
时对 应 的转 变温度 的增 量 ( 见图 2 ) 。
3 承压 件强度 计算
本文 按 G B 1 5 0 — 1 9 9 8《 钢 制塔式 容器》 的规 定 ,利用 S W6 — 1 9 9 8 计算软件 ,对壳体 、封头 、接 管补强及法兰进行了计算。按 J B / r I ’ 4 7 1 0 — 2 0 0 5《 钢 制塔式容器》 的规定计算 了裙座。其 中的壳体 、封 头的计算完全按照 G B 1 5 0 — 1 9 9 8 执行 ,本文不做具 体介绍。本文仅对开孑 L 补强计算 、法兰设计及人孔 法 兰盖设计 计 算进行 说 明 。
_ |
l l l | 设计s计算
3 4 7 。采用 板 焊 结 构 型式 ,顶 部 和底 部 采用 半 球 形
4 3 0℃。根 据 1 2 C r 2 Mo l 的性 能 ,随着 温度 的增 高 ,
其材料的许用应力降低 ,以此计算 出的结果具有更 大 的裕度 ,从 而 具有 更好 的安 全 l 生。本设 备 的主体
7 \ _ 5 3 8 ℃ \ 5 2 4 \ 4 9 6 , 。 \
l h 1 5 h 2 4 b 6 0 h 】 0 O h
煤焦油加氢反应器的设计

a. 提升管由热壁改为冷壁, 材质由不锈钢改为
表 3 生产情况及经济效益
处理量 项目
t·d- 1 改造前 26314 改造后 361
轻质油收 液化气收 全年利 年纯利
率, %
率, % 润 万元 润 万元
74138
315 15371436
78129
5109 27021392 11641956
T P 347 ( 00C r25N i13 + 00C r20N i10N b ) , ∆= 3 + 2m m 。
由于反应器结构尺寸较小, 吨位不大 (约 17 吨) , 2∀∑ C r21M o 材料用量不多, 国内一时难以找到 这种规格的材料, 如果进口, 交货期又难以保证, 并 且进口材料的最小吨位也有限制。 考虑以上实际情 况, 最后选择稳定型的奥氏体不锈钢 0C r18N i9T i 作为反应器的主体材料。 这种材料在任何温度及氢 分压条件下不产生脱碳, 且耐氢腐蚀, 并且含有稳 定元素 T i, 碳含量较低, 对抗连多硫酸腐蚀有利。因 此这种材料能满足反应条件, 安全可靠, 仅仅是增 加投资约 15 万元; 但从制造工期、制造费用等方面 综合考虑, 选用 0C r18N i11T i 是合适的。 4 结构设计 411 筒体结构
煤焦油加氢反应器的主要内件有入口扩散器、 分配盘、冷氢盘、催化剂支持件、出口收集器等, 其 材料全部选用 1C r18N i9T i。采用目前国内外成熟的 先进结构, 并针对该反应器直径较小, 内件不容易 拆卸等特点, 在结构上充分考虑了拆卸、 安装的方 便。
a. 入口扩散器 入口扩散器的结构如图 3 所示。 它是一种双层 多孔板结构, 两层孔板上的开孔大小和数量不完全 相同。 反应介质在上部锥形体整流后, 经两层孔板 上孔的节流、碰撞作用被扩散到整个反应器截面上, 促进气液相介质充分混合, 以达到精制反应的目的。
加氢精制反应器毕业设计[管理资料]
![加氢精制反应器毕业设计[管理资料]](https://img.taocdn.com/s3/m/a4c8e2bae45c3b3566ec8b92.png)
加氢精制反应器制造工艺设计专业:班级:姓名:学号:时间:指导老师:摘要本设计按照GB150-1998《钢制压力容器》及JB4730-2005《承压设备无损检测》进行制造检验和验收的,并接受《压力容器技术监察规程》监督,此加氢反应器属于III类容器。
,,详细制定了加氢精制反应器的制作工艺流程。
本产品制作工艺说明书中,简要分析了加氢精制反应器的构成;根据材料的特点和产品的结构尺寸制作出适合本产品的工艺流程;详细论述了加氢精制反应器的加工、装配、焊接一系列的工艺流程。
焊接方法主要选用埋弧自动焊与焊条电弧焊。
关键词:加氢精制反应器;制作工艺流程;焊接;AbstractThe design in accordance with the GB150-1998 “Steel Pressure Vessels”and JB4730-2005 “Pressure Equipment NDT”supervision,The hydrogenation reactor vessel belonging to class III. The main materials used in products is , In the discussion on on the basis of welding, elaborated hydrotreating reactor production process。
In the product manual production process, briefly analysis Hydrotreating reactor’s Constitute.According to characteristics of the material and the size of the product structure to Make the process suitable for this discuss Hydrotreating reactor Processing, assembling, welding A series of process, Welding methods selected the submerged arc welding And SMAW.Keywords:hydrotreating reactor; production process; welding,引言加氢精制也称加氢处理,石油产品最重要的精制方法之一。
烃类液相选择加氢用滴流床反应器设计计算
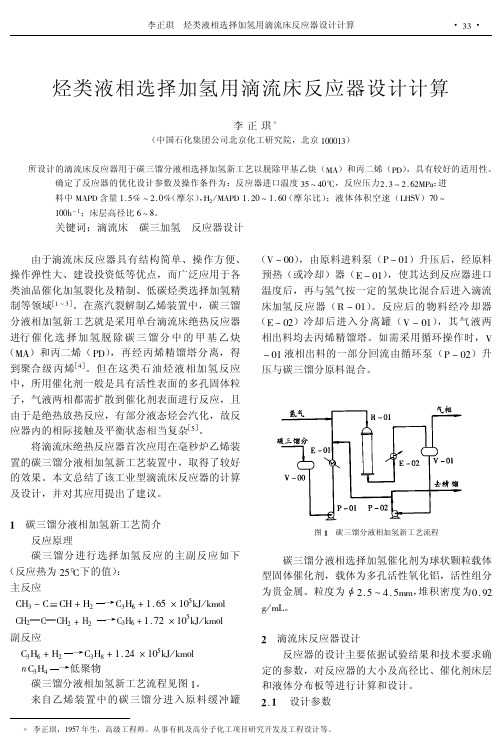
#3=: 4 )* + 2 33 气流导管高度取液柱高度的, + ) 倍:
, + ) 7 ,2- 4 02233,取 1--33
最小量 $ %& $ ’
*2/ + .
物流密度!$ 31 $ %&
1* + 2
注:!# 4 !# $ ( "! 5 "")
)210 + / */1 + -
(100 + * 0./ + 2
,- + ** ,0( + 2 *. + / , + ,) , + 22 H . H . , + -( - + .( ,--
,- + 0- ,0- + ) ** + 2 , + 01 , + (, H . H . - + .2 - + 1* ,--
,- + -2 ,-2 + - ** + 1 , + 0* , + .* H . H . - + .* - + 1. ,--
* 4 1.-33 +6 4 (!$ *) 7 - + 1.0 4 - + -/)0 30 ’389 4 ,-.-. + (/ %& $ ’)$ */(1 %& $ 31)4 0, + 1 31 $ ’ 由液柱计算公式试差计算得到:
( 4 11
) 4 ,*33
且得 #389 4 ,2-33
! 催化选择加氢反应结果 (,)在不同操作条件下的加氢反应结果 由于本滴流床反应器是作为毫秒炉乙烯装置中
设反应器最大进料量为超过正常进料量 &-. 则:&- ’ % : 1&-. < &= ’ 2! 6" 此时反应器最大空速 < &= ’ 2! 0 - ’ &9 < 2& ’ == 5 8 1
加氢反应器吊盖的相关设计计算

2574734.4 9.748 250985.1093N mm ; 100 6 250985.109 3 24.091MPa [ ] , 210MPa 2 250 安全系数 N1 [ ] / 8.72 。 Mb
由上可知吊装头盖法兰板强度符合要求,此时为设备就 位状态。 2.1 就位状态各截面应力计算 截 面 A-A 的 拉 应 力 为 : σ=G·g/[2×0.16× (0.2-0.16/2)]=67.05MPa<[σ]; 截 面 B-B 的 剪 应 力 为 : τ=G·g/[2×0.16× (0.2-0.16/2)]=67.05MPa<[τ]; 截面 C-C 的拉应力为: σ'=G·g/ (0.16×0.4) =40.23MPa <[σ]; 此处设截面 C-C 处焊道的材料性能与吊盖材料性能相同。 2.2 起吊状态各截面应力计算 2015 年 10 期 199
图 2.2 吊盖起吊状态图 根据吊盖的结构型式和受力条件将吊盖平法兰受力模 型转化为均匀载荷作用下周边简支圆板。根据弹性力学薄板 理论知识,平法兰中心处应力最大。 此时………………(1) ; t2
p K b ………………(2) , 100 其中:P=G·g=262728×9.8=2574734.4N,g=9.8N/Kg, K b 查表得系数为 9.748,t 为吊耳法兰厚度 250mm, 吊耳材质为 Q345R ,[σ]=210MPa,[τ]=140MPa(厚 度>60mm) 。 代入数据:
图 2.1 吊盖就位状态图
技术创新
截 面 A-A 的 拉 应 力 为 : σ=Fk0·g/[0.16× (0.6-0.16)]=24.26MPa<[σ]; 截 面 B-B 的 剪 应 力 为 : τ=Fk0·g/[2×0.16× (0.2-0.16/2)]=44.47MPa<[τ]; 截 面 C-C 的 剪 应 力 为 : τ'=Fk0·g/ ( 0.16×0.4 ) =26.71MPa; 截 面 C-C 的 弯 曲 应 力 为 : σ 弯 曲 =3Fk0·g·0.4/ (2×0.25×0.22)=10.47MPa。 此处设焊缝的许用应力[σ]焊缝与吊耳板的许用拉应 力[σ]的比例系数为 1,则有 σ 弯曲<[σ]焊缝。 3 吊盖螺栓计算 根据设备设备图纸及设计单位提供的有关各类螺栓的 设计文件,吊盖锁紧用螺栓选用为 M80×3×830,数量为 20 套,材质为 25Cr2MoVA,则有其[σ]=σs/1.5=456.6MPa,其 中 σs=684.9MPa。 螺栓的有效直径为 ϕ=76.752mm, 按照吊盖与设备间的摩 擦系为 0.2 对螺栓预紧力进行计算,则有单根螺栓的预紧力 为 FLmin=G·g/(0.2×20)=643683.6N; FLmax=1.05FLmin=675867.78N。 扭矩值按以下公式计算: M=K(P+△P)d………………………(3) Mmin=K(P+△P)d=0.11×(643.6836+5%×643.6836) ×80=5947.64N·m; Mmax=K (P+△P) d=0.15× (675.86778+5%×675.86778) ×80=8515.93N·m。 式中: M——终拧扭矩值,N·m; K——扭矩系数,可取 0.11~0.15; P——设计预拉力,kN; △P——预紧力损失值,宜为预拉力值 5%~10%,kN; d——螺栓公称直径,mm。 3.1 就位状态螺栓受力计算 单根螺栓受到的载荷为 F=G·g/20=128736.72N, 则螺栓 受到的实际应力为 σ1min=(FLmin+F)/S=166.8841MPa; σ1max=(FLmax+F)/S=173.8476MPa,
加氢反应器尺寸设计
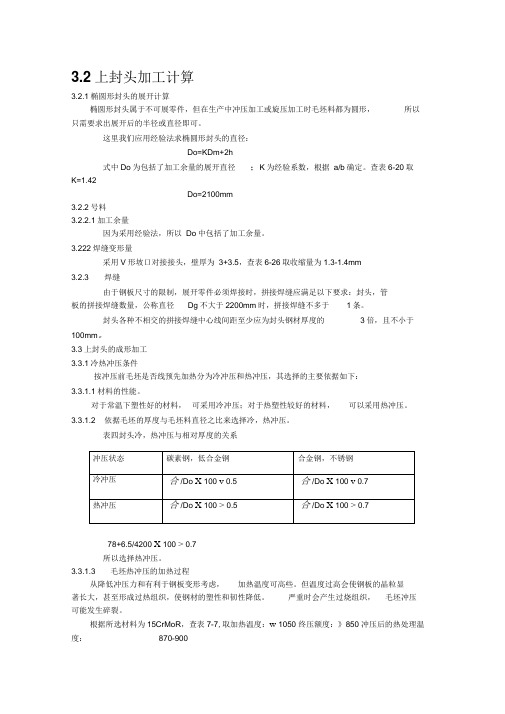
3.2上封头加工计算3.2.1椭圆形封头的展开计算椭圆形封头属于不可展零件,但在生产中冲压加工或旋压加工时毛坯料都为圆形,所以只需要求出展开后的半径或直径即可。
这里我们应用经验法求椭圆形封头的直径:Do=KDm+2h式中Do为包括了加工余量的展开直径;K为经验系数,根据a/b确定。
查表6-20取K=1.42Do=2100mm3.2.2号料3.2.2.1加工余量因为采用经验法,所以Do中包括了加工余量。
3.222焊缝变形量采用V形坡口对接接头,壁厚为3+3.5,查表6-26取收缩量为1.3-1.4mm3.2.3 焊缝由于钢板尺寸的限制,展开零件必须焊接时,拼接焊缝应满足以下要求:封头,管板的拼接焊缝数量,公称直径Dg不大于2200mm时,拼接焊缝不多于1条。
封头各种不相交的拼接焊缝中心线间距至少应为封头钢材厚度的3倍,且不小于100mm。
3.3上封头的成形加工3.3.1冷热冲压条件按冲压前毛坯是否线预先加热分为冷冲压和热冲压,其选择的主要依据如下:3.3.1.1材料的性能。
对于常温下塑性好的材料,可采用冷冲压;对于热塑性较好的材料,可以采用热冲压。
3.3.1.2 依据毛坯的厚度与毛坯料直径之比来选择冷,热冲压。
表四封头冷,热冲压与相对厚度的关系78+6.5/4200 X 100 > 0.7所以选择热冲压。
3.3.1.3 毛坯热冲压的加热过程从降低冲压力和有利于钢板变形考虑,加热温度可高些。
但温度过高会使钢板的晶粒显著长大,甚至形成过热组织,使钢材的塑性和韧性降低。
严重时会产生过烧组织,毛坯冲压可能发生碎裂。
根据所选材料为15CrMoR,查表7-7,取加热温度:w 1050 终压额度:》850 冲压后的热处理温度:870-900冲压加工常用的润滑剂查表7-8,润滑剂选取石墨粉+水冲压过程:将封头毛坯对中放在下模上,然后开动水压机使活动横梁空程向下,当压边圈与毛坯接触后,开动压边钢将毛坯的边缘压紧。
万吨每年催化裂化柴油加氢精制计算书

一、全装置物料平衡1、物料平衡本设计的处理量为95万吨/年,反应阶段为其末期,每年开工时数按8000小时计算。
入方:①原料油=8000%10010109534⨯⨯⨯=118750公斤/小时=248000%10010954⨯⨯⨯=2850吨/天 ②重整氢=8000%70.210109534⨯⨯⨯=3206公斤/小时=248000%70.210954⨯⨯⨯=77吨/天 出方:①精制柴油=118750×96.95%=115128公斤/小时=2850×96.95%=2763吨/天②粗汽油=118750×1.52%=1805公斤/小时=2850×1.52%=43吨/天③高分排放气=118750×1.78%=2114公斤/小时=2850×1.78%=51吨/天④低分排放气=118750×0.31%=368公斤/小时=2850×0.31%=8.8吨/天⑤回流罐排放气=118750×2.084%=2475公斤/小时=2850×2.084%=59吨/天⑥溶于水中的硫化氢=118750×0.022%=26公斤/小时=2850×0.022%=0.6吨/天⑦溶于水中的氨气=118750×0.024%=28.5公斤/小时=2850×0.024%=0.7吨/天⑧设备漏损=118750×0.01%=12公斤/小时=2850×0.01%=0.3吨/天 2、化学耗氢量计算①计算杂质脱除率a)硫脱除率=18001801800-×100%=90%b)氮脱除率=26158261-×100%=77.8%c)硫醇硫脱除率=15115-×100%=93.3%d)氧脱除率(以酸度计算) 原料油含氧率=8642.01001656/108.53⨯⨯⨯-×100%=0.00192%精制油含氧率=8595.01001656/1014.03⨯⨯⨯-×100%=0.0000463%氧脱除率=00192.00000465.000192.0-×100%=97.58%e)烯烃饱和率(以溴价计算)烯烃饱和率=5.201.45.20-×100%=80%②化学耗氢量计算a) 每脱掉1%的硫消耗12.5Nm 3H 2/m 3原料油加氢脱硫耗氢量=8642.0100%901018005.126⨯⨯⨯⨯-=2.34Nm 3/T2.34×118750/22.4×10002=25kg/hr b) 每脱掉1%的氮消耗53.7Nm 3H 2/m 3原料油加氢脱氮耗氢量=8642.0100%8.77102617.536⨯⨯⨯⨯-=1.26Nm 3/T1.26×118750/22.4×10002=13kg/hr c) 每脱掉1%的氧消耗44.6Nm 3H 2/m 3原料油加氢脱氧耗氢量=8642.0100%6.971092.16.445⨯⨯⨯⨯-=0.0967Nm 3/T0.0967×118750/22.4×10002=1kg/hr d) 烯烃饱和耗氢量烯烃饱和耗氢量=(20.5-4.1)×10×22.4/160=22.96Nm 3/T22.96×118750/22.4×10002=243kg/hre) 饱和1%的芳烃消耗5.0Nm 3H 2/m 3原料油芳烃饱和耗氢量=8642.0568.05.411.43⨯⨯-)(=6.29Nm 3/T6.29×118750/22.4×10002=67kg/hrf) 每脱掉1%的硫醇硫消耗12.5Nm 3H 2/m 3原料油硫醇硫耗氢量=8642.0100%3.9310155.126⨯⨯⨯⨯-=0.02Nm 3/T0.0202×118750/22.4×10002=0.2kg/hr g) 加氢裂解耗氢量原料油裂解程度为3%,每裂解1分子原料,消耗3分子氢加氢裂解耗氢量=34.197%31000⨯×3×22.4=10Nm 3/T10.22×118750/22.4×10002=108kg/hr总化学耗氢量=2.34+1.26+0.0967+22.96+6.29+0.0202+10.22=43Nm 3/T =24.81+13.36+1.025+243.44+66.69+0.214+108.36=458kg/hr重量分数:加氢脱硫:899.45781.24×100%=5.42%加氢脱氮:899.45736.13×100%=2.92%加氢脱氧:899.457025.1×100%=0.22%烯烃饱和:899.45744.243×100%=53.16%芳烃饱和:899.45769.66×100%=14.56%硫醇脱硫:899.457214.0×100%=0.05%加氢裂解:899.45736.108×100%=23.66%3、化学反应放热量a).加氢脱硫反应放热量=600kcal/Nm 3×2.34Nm 3/T=1404kcal/T 1404kcal/T×118.75T/hr=166725kcal/hrb).加氢脱氮反应放热量=600kcal/Nm 3×1.26Nm 3/T=756kcal/T 756kcal/T×118.75T/hr=89775kcal/hrc).加氢脱氧反应放热量=600kcal/Nm 3×0.0967Nm 3/T=58.02kcal/T58.02kcal/T×118.75T/hr=6890kcal/hrd).加氢烯烃饱和反应放热量=1260kcal/Nm 3×22.96Nm 3/T=28929.6kcal/T28930kcal/T×118.75T/hr=3435438kcal/hre).加氢芳烃饱和反应放热量=540kcal/Nm 3×6.29Nm 3/T=3396.6kcal/T3397kcal/T×118.75T/hr=403394kcal/hrf).加氢裂解反应放热量=450kcal/Nm 3×10.22Nm 3/T=4599kcal/T4599kcal/T×118.75T/hr=546131kcal/hr总的反应放热量∑=1404+756+58.02+28930+3397+4599=39144kcal/T=166725+89775+6889.875+3435437.5+403393.75+546131.25=4648352.375kcal/hr重量分数:加氢脱硫:%59.3%100391441404=⨯加氢脱氮:%93.1%10039144756=⨯加氢脱氧:%15.0%1003914402.58=⨯烯烃饱和:%95.73%100391446.28929=⨯芳烃饱和:%68.8%100391446.3396=⨯加氢裂解:%76.11%100391444599=⨯4、纯氢平衡表入方:新氢=5.51095%7.27⨯⨯×2×87.68%/8000=1022kg/hr10002427.1022⨯=25T/d出方:化学耗氢量=458kg/hr 100024899.457⨯=10.99T/d排放耗氢量=5.675.2113×2×80.86%=525.9kg/hr1000249.525⨯=13T/d溶解耗氢(包括低分排放和回流罐排放):低分罐=11.18125.368×43.10%×2=18kg/hr回流罐=46.4475.2474×2.03%×2=2.kg/hr溶解耗氢总量∑=17.52+2.26=20kg/hr10002478.19⨯=0.47472T/d机械漏损:入方-出方=1022.27-(457.899+525.9+19.78)=18.691kg/hr100024691.18⨯=0.449T/d重量分数:化学耗氢:27.1022899.457×100%=44.79%排放耗氢:27.10229.525×100%=51.44%溶解耗氢:27.102278.19×100%=1.93%机械漏损:27.1022691.18×100%=1.83%5、硫化氢的物料平衡产生H 2S :3432%901018001187506⨯⨯⨯⨯-=204kg/hr 10002440.204⨯=5T/d排放H 2S :①高分排放:34%6.05.675.2113⨯⨯=66kg/hr ②低分排放:34%55.211.18125.368⨯⨯=18kg/hr③回流罐排放:34%85.446.4475.2474⨯⨯=92kg/hr④水中溶解:26kg/hr (在装置总物料平衡中已计算)⑤粗汽油中溶解:204.40-(66.34+17.62+91.79+26.125)=2.5kg/hr重量分数:高分排放:%10040.20466⨯=32.46%低分排放:10040.20418⨯%=8.62%回流罐排放:10040.20492⨯%=44.90%水中溶解:10040.20426⨯%=12.78%粗汽油中溶解:10040.2045.2⨯%=1.24%二、反应器的工艺设计入口温度为320℃,入口压力为4.0Mpa ,取塔径为3.4m ,出口压力为3.9Mpa ,选用固定床轴向冷壁式反应器,已知数据如下:表一在压力为4.0Mpa 时,温度与气化率和热焓的对应关系如下:加氢反应器入口注:物料包括原料油,新氢和循环氢表二在不同压力下,气化率与温度和热焓之间的对应关系如下:注:物料包括加氢生成油,反应生成气和循环氢图一3.90Mpa 下焓值与温度对应关系 图二3.90Mpa 下气化率与温度对应关系表三不同气化率下的油气平均分子量图三不同气化率的油气平均分子量1.催化剂装填体积(选空速=2.5h -1)空速=催化剂的体积时的体积油在C 20︒=催V 8000/2.86410957⨯=2.5催V ∴=54.96m 3假设D=3.4m ,则L=2V 4D π催⨯=24.314.396.544⨯⨯=5.06m 2.催化剂的当量直径(所选催化剂为mm 62.1⨯Φ)D p =6×F V =6×3323323106102.12)102.1(4/106)102.1(4/-----⨯⨯⨯⨯+⨯⨯⨯⨯⨯⨯⨯πππ=1.64×310-m 3.循环氢(选氢油比=300) 氢油比=油混合氢V V =2.864/8000/1095V 7⨯混合氢=300混合氢V ∴=41223.1Nm 3 混合氢w =混合氢V /22.4×M =18.64.221.41223⨯=11373.16kg/hr循环氢w =混合氢w -新氢w =11373.16-3206.25=8166.91kg/hr4.D E =0.335.反应器入口温度下物料的气化率和氢分压作4.0Mpa 下的H m ~t 、e w %~t 图,查得t=320℃时,e w =21%,H m =262.0Kcal/kg 由图可得:当e w =21%时,油气M =160.5g/mol入口2p H =总p ×油气纯氢纯氢m m m +=4.0×油气M e w⨯+⨯11875018.6/16.11373%08.83)18.6/(11373.16=3.06Mpa6.反应器出口温度及气化率根据热量衡算得:(原料油混合氢w w +)入口m H +Q×95%=(原料油混合氢w w +)出口m H(11373.16+118750)×262.0+39144×118750×310-×95%=(11373.16+118750)出口m H出口m H =295.94Kcal/kg作t ~H m 、e w %~H m 图,查得出口w e =36.0%,出口t =356℃ 7.出口氢分压反应生成气m =循环氢m +[1-(96.95%+1.52%)]×原料油m=1187500153.091.8166⨯+=9983.785kg/hr 由图可得:当e w =36.0%时,油气M =168g/mol出口2p H =总p ×油气原料油反应生成气反应生成气(M e w /%)52.1%95.96m 95.7/m %60.7795.7/m ⨯+⨯+⨯=3.9×168%0.369847.011875095.7/785.9983%60.77)95.7/(9983.785⨯⨯+⨯=2.52Mpa8..气体密度v ρt =(进口t +出口t )/2=(320+356)/2=338℃w e =(进w e +出w e )/2=(21%+36%)/2=28.5%气w =混合氢w +原料油w ×w e =11373.16+118750×28.5%=45216.91kg/hr 气V =[混合氢混合氢M w +油气原料油M e w w⨯]×22.4×869.995.31⨯×273273t +=[18.611373.16+25.164%5.28187501⨯]×22.4×869.995.31⨯×273273338+ =2631.72m 3/hr v ρ=气气V w =72.263191.45216=17.18kg/m 39.空塔线速u假设D=3.4m ,则S==(π/4)D 2=9.075m 2 u=S气V =3600075.972.2631⨯=0.081m/sec10.混合物粘度查分子量为164.25、温度为338℃下,石油馏分蒸汽粘度为i z =0.0082厘泊Tr=)()(K c K T T =40.182.33273338=+Pr=05.3297.195.3Pc P == 根据Tr 与Pr 氢的粘度图得2iH z =0.013厘泊[2]=193.052H 粘度:iy 总p p 2H =25.164%5.2811875018.616.11373%08.8318.616.11373⨯+⨯=0.747 混z =∑∑0.5iii0.5ii my z m y =5.05.05.05.005.193747.012747.00082.005.193747.01013.02747.0⨯-+⨯⨯⨯-+⨯⨯)()(=9.31×310-厘泊 11.求hv G =w e m m ⨯+原料油混合氢=11373.16+118750×28.5%=45216.91kg/hrL G =)(原料油w e 1m -=118750×(1-28.5%)=84906.25kg/hrL G /v G =84906.25/45216.91=1.878 v G =45216.91kg/hr=24.34/2048.091.45216⨯⨯π=1020.5磅/2尺·hr 根据v G 与L G /v G 关系图查得:h=0.18=1.133239.19.05])3.2/18.01(1064.1318.067.0[18.033.01000/1021.907.018.17103.6+⨯⨯⨯+⨯-⨯⨯⨯⨯⨯---)()( =0.1034Pa/m12.检验①=LpΔ0.1034Pa/m ,在0.023~0.115Pa/m 范围内 ②15.14.306.5D L >== ③=⨯=L Lp p ΔΔ0.1034×5.06=0.523 kg/cm 2<0.84kg/cm 完全符合要求。
加氢反应器强度设计及理论计算

加氢反应器强度设计及理论计算首先,加氢反应器是一种重要的化工设备,用于在高压和高温条件下进行加氢反应。
在设计加氢反应器的强度时,需要考虑以下几个因素:1.反应器压力:加氢反应器通常工作在较高的压力下,因此在设计中需要考虑到反应器的压力承受能力。
可以根据反应器内部的压力梯度和材料的强度参数来计算反应器的最大允许工作压力。
2.反应器温度:加氢反应器的工作温度通常较高,因此需要确保材料能够在高温下保持足够的强度。
可以根据材料的高温强度参数和热传导性能来计算反应器的温度分布和热应力。
3.反应器应力:加氢反应器的应力主要包括静态应力和热应力。
静态应力是由于压力和温度差异引起的;热应力是由于由于温度不均匀引起的。
可以通过有限元分析和应力分析来计算反应器内部的应力分布,并确保应力处于安全范围内。
在进行加氢反应器强度设计和理论计算时,还需考虑以下几个关键的技术要点:1.材料选择:根据反应器的工作条件和介质性质,选择适当的材料。
常见的材料包括高强度钢、合金钢和不锈钢等。
2.壁厚计算:根据反应器的内径、工作压力和材料强度参数,计算反应器的最小壁厚,以确保其能够承受工作压力。
3.焊缝和连接件分析:对于焊接连接的部分,需要进行焊缝的强度和疲劳分析,以保证其结构的安全性。
4.热传导分析:对于高温反应器,需要进行热传导分析,以评估反应器壁的温度分布和热应力。
5.有限元分析:通过有限元分析方法,对反应器进行结构强度分析,包括应力、应变和变形等。
综上所述,加氢反应器的强度设计和理论计算是确保反应器结构安全可靠的重要环节。
通过合理选择材料,进行压力、温度和应力等方面的分析,可以为反应器的设计提供重要的参考依据,以确保其在工作条件下的可靠运行。
超重型加氢反应器吊盖设计及相关计算
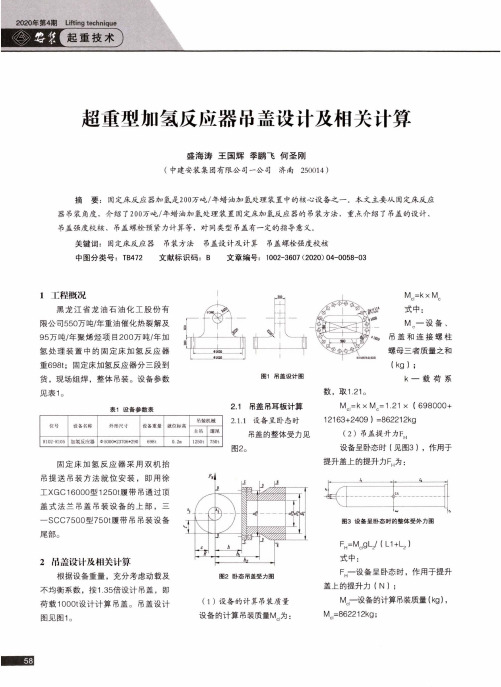
2020年第4期Lifting technique起重技术1超重型加氢反应器吊盖设计及相关计算盛海涛王国辉季鹏飞何圣刚(中建安装集团有限公司一公司济南250014)摘要:固定床反应器加氢是200万吨/年蜡油加氢处理装置中的核心设备之一.本文主要从固定床反应器吊装角度,介绍了 200万吨/年蜡油加氢处理装置固定床加氢反应器的吊装方法,重点介绍了吊盖的设计、吊盖强度校核、吊盖螺栓预紧力计算等,对同类型吊盖有一定的指导意义。
关键词:固定床反应器吊装方法吊盖设计及计算韦盖螺栓强度校核中图分类号:TB472 文献标识码:B文章编号:1002-3607 (2020) 04-0058-031工程槪况黑龙江省龙油石油化工股份有限公司550万吨/年重油催化热裂解及95万吨/年聚烯烃项目200万吨/年加氢处理装置中的固定床加氢反应器重698t;固定床加氢反应器分三段到货,现场组焊,整体吊装。
设备参数 见表1。
图1吊盖设计图M c l=kxMc式中:M。
_设备、吊盖和连接螺柱螺母三者质量之和(kg );k—载荷系数,取1.21。
表1设备参数表位号设备名称外形尺寸设备重量就位标高吊装机械主吊遛尾R102-R105加氢反应器05000*23706*29069810.2m1250t750t 2.1吊盖吊耳板计算2.1.1设备呈卧态时吊盖的整体受力见图2。
Mcl=k x Mc=1.21 x( 698000+12163+2409 ) =862212kg(2)吊盖提升力F h设备呈卧态时(见图3 ),作用于固定床加氧反应器采用双机抬吊提送吊装方法就位安装,即用徐 工X G C16000型1250t履带吊通过顶 盖式法兰吊盖吊装设备的上部,三 —S C C7500型750t履带吊吊装设备 尾部。
2吊盖设计及相关计算根据设备重量,充分考虑动载及 不均衡系数,按1.35倍设计吊盖,即荷载1000t设计计算吊盖。
吊盖设计 图见图1。
(1)设备的计算吊装质量设备的计算吊装质量%为:提升盖上的提升力FH S:F^gL^I U+L j式中:F H_设备呈卧态时,作用于提升盖上的提升力(N );Md_设备的计算吊装质量(kg),Mcl=862212k g;58Lifting technique 总第334期f起重技?^ ^G—吊装所在地的重力加速度,g=9.8m/s2;L,一设备重心至提升力FH的水平距离(mm ). 1^=94351X101;L2_设备重心至遛尾力F T的水平距离(mm), L2= 13805mm。
加氢反应器设计计算书
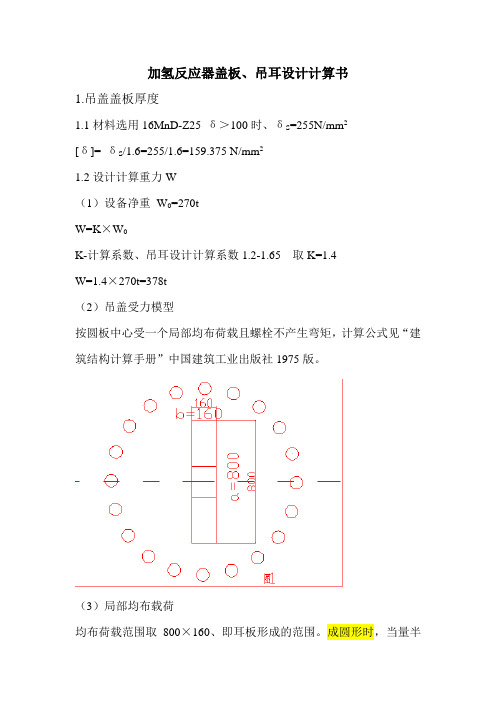
加氢反应器盖板、吊耳设计计算书1.吊盖盖板厚度1.1材料选用16MnD-Z25 δ>100时、δS=255N/mm2[δ]= δS/1.6=255/1.6=159.375 N/mm21.2设计计算重力W(1)设备净重W0=270tW=K×W0K-计算系数、吊耳设计计算系数1.2-1.65 取K=1.4W=1.4×270t=378t(2)吊盖受力模型按圆板中心受一个局部均布荷载且螺栓不产生弯矩,计算公式见“建筑结构计算手册”中国建筑工业出版社1975版。
(3)局部均布载荷均布荷载范围取800×160、即耳板形成的范围。
成圆形时,当量半径为r。
r=a+b1/4×0.875=800+160/4×0.875=274.3mm均布荷载q=W/πr2=378×104/π×274.32=16.0N/mm21.3盖板应力计(1)盖板计算半径为螺栓圆半径R=635mm(2)β=r/R=274.3/635=0.432(3)б=(6 /h2)×(qr2/16)[4-(1-μ)β2-4(1+μ)Inβ]式中μ-泊桑比μ=0.3 h盖板厚度取h=160mmб=(6/2002) ×(16×274.32/16)[4-(1-0.3)×0.4322-4(1+0.3)In0.432] =11.286×(3.869+4.365)=92.929N/mm2<159.375N/mm22耳板尺寸2.1采用单耳板形式尺寸见图22.2危险断面应力计标(设备直立状态时)(1)A-A断面、按曲梁计算M=pl/8 式中p-每个耳板受力p=k1×W式中k1-双吊耳受力不均匀系数k1=1.1 单吊耳k1=1.0 P=W=378tl-耳板环梁中径l=(700-188)/2+188=444mmM=378×104×444/8=20979×104N·mmW=b1h12/6=160×2562/6=5747627mm3б=M/W=120.04N/mm2<[б]=159.375N/mm2(2)焊缝处拉应力б=p/a×b1×k2式中a耳板长a=800 b1-耳板厚b1=160k2-焊缝系数k2=0.7б=378×104/800×160×0.7=42.19N/mm2<[б]安全3设备起吊时耳板抗弯计标3.1起吊时耳板根部骤变.见图2 B-B截面设起吊时起吊力为1/2设备吊装计算应力μ=(p/2)×l1=378×104×400/2=75600×104 N·mmW=b1a2/6=160×8002/6=1707×104mm3б=M/W=44.29N/mm2<[б]4设备起吊时设备管口骤变设备管口尺寸φ外=1050 φ内=777、厚度136.5mm位置D-D截面见图3取k1-吊装动载系数k1=1.1μ=k1×(W0/2)×l=1.1×270×104×(700-100+600)/2=178200×104 N·mmW=π(D4-d4)/32D=π(10504-7774)/(32×1050)=7952.96×104mm3б=M/W=22.4N/mm2<[б]设备管口材料9/4Cr-1MoбB=505. бs=300. [б]1=1505设备起吊时、封头处局部应力(1)按封头处接管φ=1316与封头结合处位置计算M t=k1(W0/2)l1=1.1(270×104/2) ×1300=193050×104 N·mm(2)应力计算公式取自“化工设备元件骤变计算”化学工业部设备设计技术中心站1989.4第十章“局部应力”切向弯矩M产生的应力б=C t(M t/t2Rβ)式中R-壳体中间半径R=1932-39=1893mmt-封头厚度t=78mm壳体参数γ=R/t=1893/78=24.27β=0.875r0/R=0.875[1316/﹙1893×2﹚]=0.304式中r0-接管外半径,有补强圈时按补强圈外半径(此处按补强圈计、即r0=1316/2)由γ及β查图97,得C t=0.49б=0.49(193050×104/782×1893×0.304)=270.18N/mm2设备封头材料9/4Cr-1Mo[б]1=150N/mm2由于б<2[б]1,故安全。
加氢反应器R301
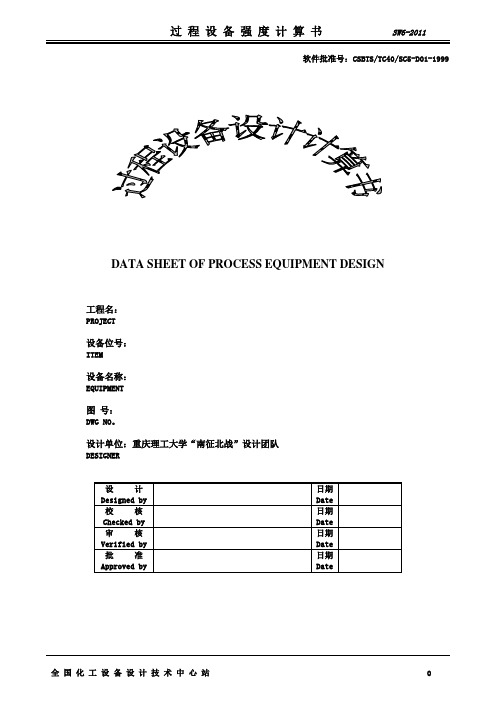
0.30
mm
腐蚀裕量C2
2.00
mm
焊接接头系数
1.00
压力试验时应力校核
压力试验类型
液压试验
试验压力值
pT= 1.25p =2.1327(或由用户输入)
MPa
压力试验允许通过的应力t
T0.90s=292.50
MPa
试验压力下封头的应力
T= =102.09
MPa
校核条件
TT
校核结果
合格
钢板负偏差C1
0.00
mm
腐蚀裕量C2
2.00
mm
焊接接头系数
1.00
压力试验时应力校核
压力试验类型
液压试验
试验压力值
pT= 1.25p =2.1327(或由用户输入)
MPa
压力试验允许通过的应力t
T0.90s=333.00
MPa
试验压力下封头的应力
T= =106.83
MPa
校核条件
TT
校核结果
合格
491.83
搅拌轴计算轴径mm
备注
内筒体内压计算
计算单位
重庆理工大学“南征北战”设计团队
计算所依据的标准
GB 150.3-2011
计算条件
筒体简图
计算压力pc
2.30
MPa
设计温度t
230.00
C
内径Di
1760.00
mm
材料
Q345R(板材)
试验温度许用应力
189.00
MPa
设计温度许用应力t
173.40
名义厚度n
mm
18
17
材料名称
加氢计算公式
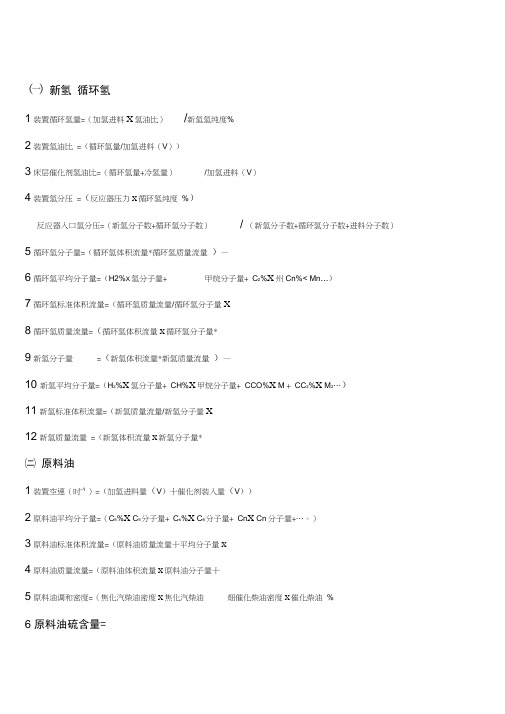
㈠新氢循环氢1装置循环氢量=(加氢进料X氢油比)/新氢氢纯度%2装置氢油比 =(循环氢量/加氢进料(V))3床层催化剂氢油比=(循环氢量+冷氢量)/加氢进料(V)4装置氢分压 =(反应器压力X循环氢纯度%)反应器入口氢分压=(新氢分子数+循环氢分子数)/ (新氢分子数+循环氢分子数+进料分子数)5循环氢分子量=(循环氢体积流量*循环氢质量流量)—6循环氢平均分子量=(H2%X氢分子量+ 甲烷分子量+ C2%X州Cn%< Mn…)7循环氢标准体积流量=(循环氢质量流量/循环氢分子量X8循环氢质量流量=(循环氢体积流量X循环氢分子量*9新氢分子量=(新氢体积流量*新氢质量流量)—10 新氢平均分子量=(H2%X氢分子量+ CH%X甲烷分子量+ CCO%X M + CC2%X M2…)11新氢标准体积流量=(新氢质量流量/新氢分子量X12新氢质量流量 =(新氢体积流量X新氢分子量*㈡原料油1装置空速(时-1)=(加氢进料量(V)十催化剂装入量(V))2原料油平均分子量=(C5%X C5分子量+ C s%X C6分子量+ Cn X Cn分子量+…。
)3原料油标准体积流量=(原料油质量流量十平均分子量X4原料油质量流量=(原料油体积流量X原料油分子量十5原料油调和密度=(焦化汽柴油密度X焦化汽柴油畑催化柴油密度X催化柴油%6 原料油硫含量=7原料油烯烃含量=㈢加氢精制耗氢计算1化学耗氢①还原1%硫氮氧为H2S NH3和H2O,并饱和除去硫氮氧化学耗氢:硫m 3原料油氮m 3原料油氧m 3原料油②饱和单烯烃,每降低一个单位溴价耗氢,对原料油比重到,低的为M5高的为M.饱和双烯烃耗氢增大一倍。
④化学耗氢计算公式V~2 = + + + (。
- 1、下载文档前请自行甄别文档内容的完整性,平台不提供额外的编辑、内容补充、找答案等附加服务。
- 2、"仅部分预览"的文档,不可在线预览部分如存在完整性等问题,可反馈申请退款(可完整预览的文档不适用该条件!)。
- 3、如文档侵犯您的权益,请联系客服反馈,我们会尽快为您处理(人工客服工作时间:9:00-18:30)。
加氢反应器盖板、吊耳设计计算书
1.吊盖盖板厚度
1.1材料选用16MnD-Z25 δ>100时、δS=255N/mm2
[δ]= δS/1.6=255/1.6=159.375 N/mm2
1.2设计计算重力W
(1)设备净重W0=270t
W=K×W0
K-计算系数、吊耳设计计算系数1.2-1.65 取K=1.4
W=1.4×270t=378t
(2)吊盖受力模型
按圆板中心受一个局部均布荷载且螺栓不产生弯矩,计算公式见“建筑结构计算手册”中国建筑工业出版社1975版。
(3)局部均布载荷
均布荷载范围取800×160、即耳板形成的范围。
成圆形时,当量半
径为r。
r=a+b1/4×0.875=800+160/4×0.875=274.3mm
均布荷载q=W/πr2=378×104/π×274.32=16.0N/mm2
1.3盖板应力计
(1)盖板计算半径为螺栓圆半径R=635mm
(2)β=r/R=274.3/635=0.432
(3)б=(6 /h2)×(qr2/16)[4-(1-μ)β2-4(1+μ)Inβ]
式中μ-泊桑比μ=0.3 h盖板厚度取h=160mm
б=(6/2002) ×(16×274.32/16)[4-(1-0.3)×0.4322-4(1+0.3)In0.432] =11.286×(3.869+4.365)=92.929N/mm2<159.375N/mm2
2耳板尺寸
2.1采用单耳板形式尺寸见图2
2.2危险断面应力计标(设备直立状态时)
(1)A-A断面、按曲梁计算
M=pl/8 式中p-每个耳板受力p=k1×W
式中k1-双吊耳受力不均匀系数k1=1.1 单吊耳k1=1.0 P=W=378t
l-耳板环梁中径
l=(700-188)/2+188=444mm
M=378×104×444/8=20979×104N·mm
W=b1h12/6=160×2562/6=5747627mm3
б=M/W=120.04N/mm2<[б]=159.375N/mm2
(2)焊缝处拉应力
б=p/a×b1×k2
式中a耳板长a=800 b1-耳板厚b1=160
k2-焊缝系数k2=0.7
б=378×104/800×160×0.7=42.19N/mm2<[б]安全3设备起吊时耳板抗弯计标
3.1起吊时耳板根部骤变.见图2 B-B截面
设起吊时起吊力为1/2设备吊装计算应力
μ=(p/2)×l1=378×104×400/2=75600×104 N·mm
W=b1a2/6=160×8002/6=1707×104mm3
б=M/W=44.29N/mm2<[б]
4设备起吊时设备管口骤变
设备管口尺寸φ外=1050 φ内=777、厚度136.5mm
位置D-D截面见图3
取k1-吊装动载系数k1=1.1
μ=k1×(W0/2)×l=1.1×270×104×(700-100+600)/2=178200×104 N·mm
W=π(D4-d4)/32D=π(10504-7774)/(32×1050)=7952.96×104mm3
б=M/W=22.4N/mm2<[б]
设备管口材料9/4Cr-1MoбB=505. бs=300. [б]1=150
5设备起吊时、封头处局部应力
(1)按封头处接管φ=1316与封头结合处位置计算
M t=k1(W0/2)l1=1.1(270×104/2) ×1300=193050×104 N·mm
(2)应力计算公式取自“化工设备元件骤变计算”化学工业部设备设计技术中心站1989.4第十章“局部应力”
切向弯矩M产生的应力
б=C t(M t/t2Rβ)
式中R-壳体中间半径R=1932-39=1893mm
t-封头厚度t=78mm
壳体参数γ=R/t=1893/78=24.27
β=0.875r0/R=0.875[1316/﹙1893×2﹚]=0.304
式中r0-接管外半径,有补强圈时按补强圈外半径(此处按补强圈计、即r0=1316/2)
由γ及β查图97,得C t=0.49
б=0.49(193050×104/782×1893×0.304)=270.18N/mm2
设备封头材料9/4Cr-1Mo[б]1=150N/mm2
由于б<2[б]1,故安全。
6螺栓受力计算
6.1本设备顶接管使用20个H80×3双头螺栓,材料25Cr2MoV A
бB=805 бS=685 [б]1=254 (查GB150得到)
6.2设备起吊时螺栓预紧力
(1)设备起吊时重力为p2=378t/2=189t
(2)螺栓预紧力后产生的摩擦力应大于起吊重力
F×f≥p2×k3
式中F-螺栓预紧力
f-钢对钢摩擦力系数,对干摩擦,取f=0.2
k3-预紧力增加系数k3=1.2
F=p2k2/0.2=189×1.2/0.2=1134t
(3)每个螺栓的预紧力
F1=F/20=56.7t
(4)设备直立后螺栓受力
F2=p2/20=378t/20=18.9t<F1
(5)每个螺栓受许拉力
θ=π×[δ]2=π×(762/4) ×254=1151677N=115t>F1
故螺栓拉力满足要求。
技术要求
1.材料件号 1.盖板16MnD-Z25并应符合厚度方向性能钢板
GB5313-85要求
件号2.耳板16MnD 件号3.小吊耳16Mn
2.件号1应经100%超声波检查,符合GB/T2970-91 Ⅱ级合格。
3.本次设备吊装在乌市冬季,故吊耳材料采用16MnD低温用钢材。
4.耳板与盖板丁字焊缝采用半U型双面焊,坡口尺寸允许按所用工
艺适当调正,焊接前应有焊接工艺评定,焊前应予垫及后垫,采
用低氢型焊条。
5.T型焊缝在组对时点焊时允许设支撑、焊接开始后应撤去,焊缝不
应在拘束条件下焊接。
焊接过程中应两侧交替进行,防止耳板歪斜。
一侧焊缝焊接一部分后,焊接另一侧。
不应使用碳弧气刨,应采用砂轮磨光机,后进行着色检查、合格后继续焊接。
必要时增加中间过程的着色检查。
6.T字缝净100%超声波检查,Ⅱ级合格,然后作整体热处理,温度
625℃±25℃,保持8小时。
7.盖板焊接后如不平度超过2‰,应对盖板螺母处宽度160mm范围
进行加工,或划出φ160圆平面,以使螺母与盖板接触良好。
8.每个螺母预紧力56.7t
安装使用说明
1.本次使用单耳板式吊盖,其中制造中使用16MnD-Z25为Z向性能
钢板,由于吊盖厚度大,容易与焊缝与盖板间产生层状撕裂,所以采用Z向性能钢板。
防止产生层状撕裂的措施。
(1)减少该处应力,即扩大接触面积。
(2)采用Z向钢板,由于该材料中硫的含量少(Z25要求硫≤0.007),远小于16MnD中0.030要求。
故金属晶格处非金属夹杂物少,晶格结合强度高,抗层间撕裂能力大。
Z向性能钢板有三个等级,Z15、Z25、Z35,即断面收缩率15%、25%、35%(在钢板厚度方向性能)
(3)焊接时,结构不应拘束,防止产生过大内应力。
(4)焊后整体热处理,以消除大部分焊接应力。
2.盖板与管口装配时只允许螺母处接触,每个螺柱预紧力为56.7t
3.盖板、卡环、绳扣螺栓配合尺寸及注意事项件附图。
4.本次盖板计算可参阅公司“技术进步2008-Z”圆形提升盖板设计
计算,本次用材料力学计算方式并未用钢结构设计中荷载规范要求,故许用应力取δs/1.6。
如果使用中将管口密封部位接触,按该文要计算螺栓产生的弯矩,此时盖板应力会比本计算增大将一倍。
本计算公式仅按平板计标,最大应力发生在中心部位,未考虑耳板的加强作用,故实际使用应该安全。