石化公司加氢精制装置设计方案
石蜡加氢精制装置开工方案

加氢精制装置开工方案一、开工说明依据厂物料平衡、节能降耗、降低加工成本等综合考虑后安排决定, 15万吨/ 年石蜡加氢精制装置进行开工。
三、开工注意事项及风险评估开工注意事项1、开工过程要严格按照开工网络和规程进行,严禁乱排乱放,污油必须及时处理干净,否则严禁施工动火。
2、设备、管线的吹扫、置换必须严格按照规程进行,不留死角,按管理区域进行分工、责任,保证开工引油的安全。
3、拆盲板严格按照盲板表进行、专人负责,做好各项拆盲板的记录,保证不漏拆一块盲板,同时要求施工单位拆盲板的工作人员要固定,本着谁装的盲板、谁拆除的原则,防止遗漏。
4、装置内的下水井、地漏必须认真用石棉布封堵好,上面盖上黄土并有记录,每天还需对此进行认真地检查,及时整改不符合要求的下水井、地漏。
5、进入开工施工现场的人员必须按要求着装,戴好安全帽,高处作业系好安全带。
6、夜间要有足够的照明,临时电线必须绝缘良好,不破皮,移动照明要有铁网罩保护。
7、各种施工机具必须安全可靠,发现失灵要立即消除,严禁迁就使用,避免发生意外。
8、开工引油时,严禁大量排入污水管道,油水混合物退到装置外罐区或装置内污油罐。
9、气密过程中,发现泄漏要及时处理,要泄压后再进行处理,严禁带压操作 , 以免发生意外。
10、气密前,关闭系统所有安全阀的保护阀,待气密合格后再打开。
11、高压临氢系统气密时,低压临氢系统放空阀应打开,防止串压、超压。
12、严格控制升降压速度,一般升降压速度不大于1.0MPa/h,以防催化剂破损。
13、系统气密结束后,做好记录,相关人员共同确定并签字。
14、加热炉点火时,对流室通入过热蒸汽经消音器排空,同时 E-203、E-202 通冷却水。
15、250C恒温时,对高压临氢系统各设备进行热紧。
16、当反应器开始升压时,在操作温度升至 135C以前,操作压力不得超过2.18MPa同理当反应器降压时,操作压力降至 2.18MPa以前,其操作温度必须维持在135C以上。
焦化、加氢、制氢方案

目录第一章工艺装置方案 (4)第一节延迟焦化装置 (4)一、装置组成及规模 (4)二、原料及产品方案 (4)三、技术方案选择 (4)四、主要操作条件 (20)五、工艺流程简述 (22)六、自控水平 (26)七、主要设备选择 (30)八、指标及能耗 (37)九、面布置 (40)第二节加氢精制装置 (41)一、概述 (41)二、工艺技术方案 (41)三、要操作条件 (45)四、艺流程简述 (46)五、控水平 (47)六、要设备选择 (52)七、节能原则和措施 (54)八、置平面布置 (55)第三节制氢装置 (56)一、概述 (56)二、原料及产品 (57)三、工艺技术方案 (58)四、主要工艺过程操作条件 (62)五、工艺流程简述 (64)六、自控水平 (66)七、主要设备选择 (72)八、节能措施 (78)九、平面布置 (78)第二章投资估算 (79)第一章工艺装置方案第一节延迟焦化装置一、装置组成及规模本装置主要包括焦化、吸收稳定、吹汽放空、水力除焦、切焦水和冷焦水循环、干气及液化石油气脱硫和液化石油气脱硫醇部分。
装置工程规模100万吨/年,年开工时间按8000小时计。
二、原料及产品方案1、原料来源本装置原料为****石化厂的减压渣油。
2、产品方案主要产品有:干气﹑液化石油气、焦化塔顶油、焦化一线油﹑焦化二线油﹑焦化甩油和石油焦。
三、技术方案选择(一)国内外焦化技术发展趋势1.国外技术进展情况国外延迟焦化技术以美国为代表,比较成熟的有凯洛格(Kellogg)公司、鲁姆斯(ABB Lummus Grest)公司、大陆(Conoco)石油公司和福斯特·惠勒(Foster Wheeler)公司的技术,从近几年设计的延迟焦化装置的套数、液体产品收率和公用工程消耗等方面来看,福斯特·惠勒公司的技术占有一定的优势。
近几年来,国外延迟焦化技术的发展具有如下趋势:(1)焦炭塔反应压力80年代以前,生产普通焦的焦炭塔的设计压力为0.17~0.21MPa(G),目前,焦炭塔的设计压力普遍降低。
加氢精制及制氢联合装置技术方案
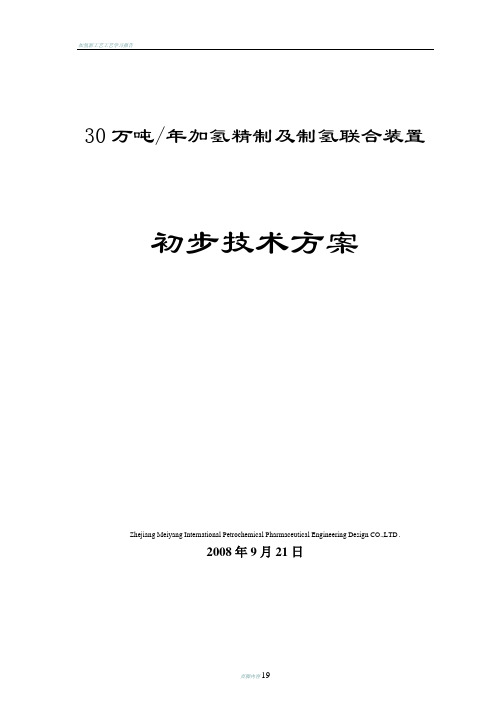
30万吨/年加氢精制及制氢联合装置初步技术方案Zhejiang Meiyang International Petrochemical Pharmaceutical Engineering Design CO.,LTD.2008年9月21日目录第一节工程简述及设计原则 (2)第二节装置规模、原料及产品方案 (3)第三节工艺技术方案及流程简述 (5)第四节装置平面布置 (15)第五节公用工程消耗 (16)第六节投资估算 (18)第七节技术保证 (19)第一节工程简述及设计原则一、工程简述xx公司拟建设30万吨/年汽柴油加氢精制装置,原料组成为15万吨/年催化柴油,11~12万吨/年焦化柴油,3~4万吨/年焦化汽油,根据加氢精制装置的生产规模及产品方案,需配套5000m3n/h制氢装置。
(年操作时数为8000小时)。
二、设计范围及原则1、30万吨/年汽柴油加氢精制装置、5000m3n/h制氢装置按联合装置布置,制氢装置只为汽柴油加氢精制装置供氢。
设计范围为联合装置边界线以内,主要内容包括:加氢的反应、分馏部分,制氢的转化造气、变换和PSA部分,以及联合装置的变配电室和中心控制室。
加氢精制装置的含硫气体送至催化的产品精制装置与催化干气一起脱硫。
脱硫后的气体作为制氢装置的主原料,石脑油作为辅助原料。
2、加氢精制装置的目的以脱硫、脱氮和烯烃饱和为主,不考虑加氢改质。
采用国内催化剂、设备和工艺技术。
3、制氢装置造气单元采用催化干气蒸汽转化制氢专有技术;净化单元采用国内变压吸附(PSA)技术。
4、按年开工8000小时计算小时加工量。
5、严格执行国家有关工程建设质量管理法规,确保装置安全、稳定、长周期运行,减少维护维修的工作量,从而提高整体的经济效益。
6、认真贯彻国家关于环境保护和劳动保护的法规和要求。
认真贯彻安全第一预防为主的指导思想。
对生产中易燃易爆有毒有害物质设置必要的防范措施。
三废排放要符合国家现行有关标准和法规。
加氢精制装置工艺原理与操作

3.空速
空速:指单位时间内通过单位体积催化剂的物 料体积数。空速越高则装置生产能力越大,但 反应物料在反应中停留时间越短,不利于反应 的完全进行,产品质量受到影响。如空速过低 ,则生产能力降低,在反应器中停留时间过长 会增加裂解导致产品收率降低,催化剂上易积 碳。所以空速是有一定限制的,它受到原料油 性质、催化剂使用性能、产品质量要求等因素 限制,不能随便提高或降低。
合反应。如:
CmH2m+2 —→ Cm-nH2(m-n)+2+CnH2n
烷烃
烷烃
烯烃
CnH2n+H2 —→CnH2n+2
烯烃
烷烃
芳烃加氢: 苯
+3H2 -→ 环已烷
中石加化氢经精济制技装术置研工究艺院原(理咨与询操公作司) China Petrochemical Consulting Corporation
Hale Waihona Puke 装置特点三套加氢精制装置全部采用热高分和热低分;采用炉前 混氢工艺;采用常压汽提和减压干燥;石蜡加氢装置和 微晶蜡加氢装置均有原料预处理系统;使用三种不同的 催化剂;润滑油加氢为FV-10,石蜡加氧为RJW一1,微 晶蜡加氢为RJW一2;装置还采用了二台21/4Cr一1Mo材 质的热壁反应器,一台21/4Cr一1Mo材质的冷壁反应器 及一台21/4Cr一1Mo材质的热高分,必须了解在371℃一 493℃温度范围内进行操作所引起的脆化现象,同时必 须了解在温度低于121℃时可能出现的脆性破坏。
硫醇
烷烃
RSR`+2H2-→R`H+RH+H2S
硫醚
加氢精制及制氢联合装置技术方案

30 万吨/ 年加氢精制及制氢联合装置初步技术方案Zhejiang Meiyang International Petrochemical Pharmaceutical Engineering Design CO.,LTD.2008年 9月 21 日目录第一节工程简述及设计原则 (2)第二节装置规模、原料及产品方案 (3)第三节工艺技术方案及流程简述 (5)第四节装置平面布置 (15)第五节公用工程消耗 (16)第六节投资估算 (18)第七节技术保证 (19)第一节工程简述及设计原则一、工程简述xx 公司拟建设30 万吨/ 年汽柴油加氢精制装置,原料组成为15 万吨/年催化柴油,11〜12万吨/年焦化柴油,3〜4万吨/年焦化汽油,根据加氢精制装置的生产规模及产品方案,需配套5000m3n/h 制氢装置。
(年操作时数为8000 小时)。
二、设计范围及原则1 、30 万吨/ 年汽柴油加氢精制装置、5000m3n/h 制氢装置按联合装置布置,制氢装置只为汽柴油加氢精制装置供氢。
设计范围为联合装置边界线以内,主要内容包括:加氢的反应、分馏部分,制氢的转化造气、变换和PSA 部分,以及联合装置的变配电室和中心控制室。
加氢精制装置的含硫气体送至催化的产品精制装置与催化干气一起脱硫。
脱硫后的气体作为制氢装置的主原料,石脑油作为辅助原料。
2、加氢精制装置的目的以脱硫、脱氮和烯烃饱和为主,不考虑加氢改质。
采用国内催化剂、设备和工艺技术。
3、制氢装置造气单元采用催化干气蒸汽转化制氢专有技术;净化单元采用国内变压吸附(PSA技术。
4、按年开工8000 小时计算小时加工量。
5、严格执行国家有关工程建设质量管理法规,确保装置安全、稳定、长周期运行,减少维护维修的工作量,从而提高整体的经济效益。
6、认真贯彻国家关于环境保护和劳动保护的法规和要求。
认真贯彻安全第一预防为主的指导思想。
对生产中易燃易爆有毒有害物质设置必要的防范措施。
柴油加氢精制装置工艺管道管道施工方案

300×104t/a柴油加氢精制装置工艺管道施工方案目录1 编制说明 (1)2 编制依据 (1)3 工艺管道工程量一览表 (1)4 施工应具备的条件及施工准备 (1)5 材料及管件的检验 (2)5.1 一般规定 (2)5.2 阀门的检验 (2)5.3 管件检验 (3)6 管道预制 (3)7 焊接 (4)7.1 坡口的制备 (4)7.2 焊前清理 (5)7.3 焊接方法 (5)7.4 组对要求 (5)7.5 焊接工艺要求 (5)7.6 焊缝检验要求 (7)8 管道安装 (8)8.1 一般规定 (8)8.2 不锈钢管安装 (9)8.3 阀门 (9)8.4 法兰连接 (9)8.5 管廊 (10)8.6 管架 (10)9 管道试压、吹扫 (11)9.1一般规定 (11)9.2试压 (11)9.3 吹扫 (12)10 防腐、保温 (14)11 交工技术资料 (14)12 工程质量保证措施 (15)12.1 工程质量目标 (15)12.2 工程质量保证的原则 (16)12.3 施工过程质量控制 (16)12.4 现场焊接工程质量管理 (19)12.5 现场检测质量管理 (20)12.6 质量保证体系的建立和运行 (21)13 HSE( 健康、安全、环保)管理措施 (22)13.1 项目HSE管理目标 (22)13.2项目HSE管理组织 (23)13.3 项目HSE管理的实施 (25)13.4 安全措施 (28)14 主要施工机具 (29)15 劳动力计划 (30)16 施工进度计划 (30)1 编制说明本方案适用于镇海炼油化工股份有限公司扩建800×104t/a炼油工程蜡油加氢脱硫及柴油加氢精制联合装置300×104t/a柴油加氢精制工艺管道的施工。
包括两个区:反应换热区、压缩机区。
2 编制依据2.1 施工图纸;2.2 《工业管道工程施工施工及验收规范》GB50235-97;2.3 《现场设备、工业管道焊接工程施工及验收规范》GB50236-98;2.4 《石油化工剧毒、可燃介质管道工程施工及验收规范》SH3501-19972.5 《工程建设交工技术文件规定》 SH3503-93;3 工艺管道工程量一览表4 施工应具备的条件及施工准备4.1 施工应具备的条件4.1.1 施工图纸、安装规范、标准、施工方案等资料齐全。
第八章 直馏柴油加氢精制装置

第八章直馏柴油加氢精制装置第一节装置概况及特点一、装置概述直馏柴油加氢精制装置是500×104t/a常减压配套设施,由中国石化集团公司洛阳石化工程公司负责设计、化工部第十一化学建筑安装公司施工。
装置于1992年8月交付生产,1993年1月投料试车。
2000年2月份在第二周期开工检修中,分馏系统增加了氢气气提线,使装置初步具备了航煤加氢精制的能力。
2000年三季度装置自控系统工程进行改造,横河—西仪公司的CENTUM-CS3000集散型控制系统替代原来的DⅢ型常规仪表,实现了实时数据采集、显示、控制、记录、打印等功能。
根据分公司安排,2003年2月7日开车,4月7日按计划停工,截止2004年3月25日直柴加氢装置间断开工5次,目前装置正常运行。
二、装置规模及组成装置设计处理能力为80×104t/a,开工时间8000 h/a,加工常压蒸馏装置直馏柴油,氢源来自连续催化重整装置,产品为精制柴油、粗汽油等。
装置占地面积6032平方米,由反应部分、分馏部分、循环氢压缩机部分和公用工程四大部分组成。
三、装置工艺流程特点1、原料油缓冲罐(V-3201)采用重整氢气履盖措施,以防止原料油与空气接触,从而减轻高温部位结焦的程度。
2、反应器R-3201采用热壁式反应器,并采用新型的内部结构,使进入催化剂床层的物流分配和催化剂床层的径向温度分布均匀,反应器内催化剂为单床层,不设置冷氢盘管。
3、采用三相(油、气、水)分离的立式高压分离器。
4、混合氢与原料油在E-3201前混合,这样可提高换热器的换热效果,减少炉管结焦的程度。
5、为了充分回收反应流出物的热量,降低装置能耗,反应流出物换热至132ºC后进入反应流出物空冷器A-3201。
6、为防止铵盐析出堵塞管路和设备,在反应流出物空冷器A-3201和反应流出物/原料油换热器E-3202/C的上游均设有除盐水注入点。
7、分馏部分采用双塔汽提流程,脱硫化氢汽提塔T-3201采用蒸汽汽提,产品分馏塔T-3202采用重沸炉汽提;脱硫化氢汽提塔顶回流罐V-3205气体至催化裂化装置(Ⅰ)加氢干气脱硫装置,产品分馏塔顶回流罐V-3206粗汽油直接经泵送至常减压蒸馏装置。
石油化工厂里的工艺-制氢装置及工艺

制氢装置及工艺
本套装置采用烃类水蒸气制氢方法,我公司采用的原料是炼厂干气和水蒸气在催化剂上进行反应,产生的氢气在经过变压吸附将氢气提浓,外送氢气纯度达到99.9%。
主要包括以下几个过程。
1、干气脱硫部分
进入脱硫部分的原料气,首先进入加氢反应器(R4001),发生将有机硫转化为无机硫,然后再进入氧化锌脱硫反应器(R4002A.B)脱氯段脱除原料中的氯,最后进入氧化锌脱硫段,在此氧化锌与硫化氢发生脱硫反应。
精制后的气体要求硫含量小于0.5ppm,烯烃小于1%(V)、氯小于0.2ppm 进入转化部分。
2、转化部分
精制后的原料气按水碳比不小于3.2与水蒸汽混合,再经转化炉(F4001)对流段预热,进入转化炉辐射段。
在催化剂的作用下,发生复杂的水蒸汽转化反应,从而生产出氢气、甲烷、一氧化碳、二氧化碳和水的平衡混合物。
主要反应有:
C n H m + nH2O = nCO +(n+m/2)H2①
CO + 3H2 = CH4 + H2O △H o298=-206kJ/mol ②
转化反应是强吸热反应,转化炉内温度高达900度。
3、中变部分
由转化部分来的转化气进入中温变换反应器(R4003),在催化剂的作用下发生变换反应:
CO+H2O=CO2+H2△H o298=-41.4KJ/mol
将变换气中CO含量降至3%左右,同时继续生产氢气。
中变气经过汽包给水换热器(E4002A.B、E4003)、低温热水换热器(E4004)进行热交换回收部分余热后,再经中变气水冷却器(E4005)冷却至35℃左右,经分水后进入PSA 部分。
年产200万吨柴油加氢精制装置静设备的安装工程施工设计方案

年产200万吨柴油加氢精制装置静设备安装施工方案目录1 前言 (1)1.1编制依据 (3)2 工程概况及特点 (4)2.1工程概况 (4)2.2工程特点 (4)3 施工技术方案 (5)3.1施工程序 (5)3.2设备安装主要原则 (5)3.3基础验收 (6)3.4设备到货验收 (7)3.5立式设备安装 (7)3.6塔盘安装 (9)3.7卧式设备安装 (10)3.8换热器安装 (11)3.9塔器、容器类设备的清理封闭 (12)3.10焊接 (12)4 主要技术质量标准 (13)4.1混凝土基础验收质量要求 (13)4.2钢结构基础验收质量要求 (14)4.3设备找正质量要求 (14)5质量保证措施 (14)5.1静设备质量监督计划 (14)6 HSE保证措施 (20)7安全隐患及对策(JHA分析表) (21)8施工设备、计量器具、机具计划 (25)8.1施工设备需用计划一览表 (25)8.2施工量器具计划一览表 (25)8.3施工工机具需用计划一览表 (26)8.4 施工手段用料一览表 (26)9 施工计划 (27)附件:柴油加氢精制装置静设备一览表 (27)1 前言1.1 编制依据1.1.1 中国石油天然气华东勘察设计研究院设计的中国石油宁夏石化公司200万吨/年柴油加氢精制装置设备施工图。
1.1.2 中国石油天然气第七建设公司编制的中国石油宁夏石化公司200万吨/年柴油加氢精制装置施工组织设计及冬季施工技术方案。
1.1.3 有关施工标准及验收规范。
1.1.3.1 GB150-1998《钢制压力容器》1.1.3.2 JB/T4710-2005《钢制塔式容器》1.1.3.3 GB151-1999《钢制管壳式换热器》1.1.3.4 SH3532-2005《石油化工换热设备施工及验收规范》1.1.3.5 SH3524-2009《石油化工钢制塔、容器现场组焊施工工艺标准》1.1.3.6 JB\T4709-2000《钢制压力容器焊接规程》1.1.3.7 TSG R0004-2009《固定式压力容器安全技术监察规程》1.1.3.8 HGJ209-83《中低压化工设备施工及验收规范》1.1.3.9 HGJ208-83《高压化工设备施工及验收规范》1.1.3.10 HGJ211-85《化工塔类设备施工及验收规范》1.2适用范围本方案仅适用于中国石油宁夏石化公司200万吨/年柴油加氢精制装置静设备的安装施工。
北方某炼油厂渣油加氢处理装置方案设计

北方某炼油厂渣油加氢处理装置方案设计
一、工艺流程
该装置采用针对渣油的加氢处理技术,主要包括以下几个过程:
1. 渣油预处理:将原油加热至适宜温度,去除其中的轻质组分。
2. 加氢反应器:将经过预处理的渣油与一定量的氢气进行反应,生成较轻质的液态产品。
3. 分离器:将反应后的产物进行分离,得到液态产品和再循环的氢气。
4. 催化剂再生:将反应器床中的催化剂进行再生,保持其活性。
二、主要设备
1. 温度控制系统:用于控制温度,确保反应器内油气回流的正常运行。
2. 进料泵:将预处理后的渣油送入反应器中。
3. 氢气压缩机:将低压的氢气压缩到适宜的压力送入反应器。
4. 反应器:包括反应器床、壳体、附属设备等,是加氢反应的主要设备。
5. 分离器:用于将反应后的产物进行分离得到液态产品和再循环的氢气。
6. 催化剂再生设备:用于再生反应器床中的催化剂,以确保催化剂的活性。
三、技术经济指标
1. 生产能力:处理能力为200万吨/年。
2. 产品质量:汽油产量为35%,柴油产量为45%,润滑油产量为10%,其他产品产量为10%。
3. 能耗指标:加氢反应器设备选用先进高效的反应器,计算单元燃料能消耗为1300千焦/千克。
4. 工艺投资:预计总投资为2.5亿元。
5. 投资回收期:预计在5年内实现投资回收。
加氢精制装置工艺

用于生产满足相应标准规范的石油产品。加氢精 制能使原料油中的含硫、氮、氧等非化合物氢解, 使烯烃、芳烃加氢饱和并能脱除金属和沥青质等 杂质,具有处理原料范围广、液体收率高、产品 质量好等优点。 加氢精制主要用于二次加工装置焦化汽油、焦化 柴油的精制,也用于原油直馏汽油、柴油的精制。
主要设备流程框图主要设备流程框图反应系统反应系统原油罐区原油过滤器原料流出物进料加热炉加氢反应器高压分离器低压分离器氢气脱硫化氢循环氢压缩机主要设备流程框图主要设备流程框图分馏系统分馏系统不凝气去脱硫不凝气去脱硫流出物流出物放空气去火炬放空气去火炬汽提蒸汽汽提蒸汽汽油出装置汽油出装置精制柴油出装置精制柴油出装置脱硫化氢塔塔顶回流罐分馏塔分馏塔顶回流罐加氢精制设备一览表加氢精制设备一览表ff20012001反应进料加热炉反应进料加热炉ff20022002rr20012001反应器反应器cc20012001脱硫化氢塔脱硫化氢塔cc20022002分馏塔分馏塔dd20012001原料油缓冲罐原料油缓冲罐dd20022002高压分离器高压分离器dd20032003低压分离器低压分离器dd20042004脱硫化氢顶回流罐脱硫化氢顶回流罐dd20052005分馏塔顶回流罐分馏塔顶回流罐dd20062006dd20072007循环氢入口分液罐循环氢入口分液罐dd2008ab2008ab硫化剂罐硫化剂罐dd200200
9.5原料性质对加氢过程的影响
• 原料油的的性质影响加氢精制反应的深度
和放出热量的大小,是决定氢油比和反应 温度的主要依据,原料油中烯烃含量和干 点上升,会加快催化剂结焦; • 氮含量上升,要降低空速或提高温度,压 力以保证精制产品质量,烯烃和硫化物加 氢反应热大,温升高,耗氢大,要适当调 高氢油比
自-汽、柴加制氢精制装置开工方案2011.7 .

岚桥石化80万吨/年汽、柴加制氢精制装置开工方案第一联合装置车间二○一一年七月编写说明本开工方案是根据现有基础设计资料,结合首次开工过程中遇到的实际情况进行编制,适用于岚桥港口石化有限公司汽、柴油加氢精制装置的开工之用。
主要用于操作人员的培训学习与开工指导。
此方案编写不尽完备,待日后装置出现的具体生产情况,根据最终详细设计资料、设备随机资料进行补充编写。
编者2011 年7 月目录第一章公用工程系统投用 (2)第二章高压系统气密 (3)第三章原料系统和分馏系统气密 (4)第四章分馏系统油联运 (6)第五章装置开工 (7)第六章开工过程事故预想方案 (9)第七章开工过程HSE 管理 (24)第一章公用工程系统投用一、循环水系统投用1、通知调度、供排水等有关单位,准备引循环水进装置2、确定装置内流程,开循环水地上线高点放空,将管线内的存气排出。
3、排水将循环水送至装置界区阀前,缓慢打开循环水进出装置界区阀。
4、环水地上管线及冷却器高点放空,将管线内的存气排出,见气后及时关闭放空阀。
5、循环水接线进行检查确认,,循环水总线、各分支线畅通,无漏点。
6、用循环水。
二、新鲜水系统的引入1、通知调度、供排水等有关单位,准备引新鲜水进装置。
2、确定装置内流程。
3、打开新鲜水进装置总阀,检查有无漏点,将新鲜水引进装置。
三、除盐水系统的投用1、通知调度、及有关单位,准备引除盐水进装置。
2、确定装置内流程。
3、装置外给水至总管线,打开进装置界区阀。
四、1.0MPa蒸汽系统的投用1、通知调度、锅炉及有关单位,准备引1.0MPa蒸汽进装置。
2、从装置外缓慢引1.0MPa蒸汽先在界区阀前排凝放空。
3、确定装置内流程,伴热疏水暂现场排放,凝结水系统投用后及时改去凝结水系统。
4、将1.0MPa蒸汽引入装置,注意装置内管线沿路疏水。
五、、0.6MPa氮气系统的投用1、通知调度及有关单位,准备引1.0MPa氮气进装置。
2、确定装置内流程,确定装置内相关盲板盲死,防止串至其他管线。
加氢装置安全设计(石化加氢珍藏版) 文档全文预览

加氢装置装置安全
v 装置设计阶段与安全方面设计的相关内容:
v 1---项目论证以及可行性研究阶段: v 岩土工程详细勘察报告、安全评价报告、环境影响报告书(譬如110 v 万吨/年汽油加氢装置的卫生防护距离为1500米,加氢裂化详堪不彻 v 底有暗沟 ,公众参与调查等情况)。 v 2---初步设计至项目中交阶段: v 在初步设计中必须包括安全设施、环境专篇、消防专篇、职业卫生以 v 及概算中必须包括安全环保的概算。并开始组织HAZOP分析或PHA v 分析。施工图阶段进行须进行60%,90%的施工图3D审查以及最 v 终的施工图会审。 v 3---竣工验收、开工阶段及以后: v 组织专家审核试生产方案、具备相应资质的安全评价机构进行建设项 v 目竣工安全验收评价、环保验收评价。开工前须完成三查四定 v (punch list),完成投用前安全检查PSSR,废催化剂安全填埋或有资 v 质委托方的回收处理 .
· 排放气温度≤240 ℃的工艺状况。
· UOP泄压合格标准为: · 低速泄压为:泄压3.5MPa/5min. 高速泄压为:泄压5.5MPa/5min
加氢装置装置安全
·
加氢装置装置安全设计
· 1---关于紧急泄压系统的设计:
· 1---5)反应器内构件、高压换热器内件、循环氢脱硫塔内件,反应器内
· 装瓷球应考虑快速紧急泄压时的差压变化冲击。所以,加氢裂化与渣油
· 加氢的瓷球就有耐温度急变≥800℃的质量要求,有急速减压测试通过
· 率≥99%的质量要求。
· 汽油加氢紧急泄压的设计参数为:
· 紧急泄放流量:53.666t/h, 泄放背压:0.1MPa, 泄放气平均分子量:
· 69.03。
· 加氢裂化紧急泄压得设计参数为:
汽油加氢装置原理简介
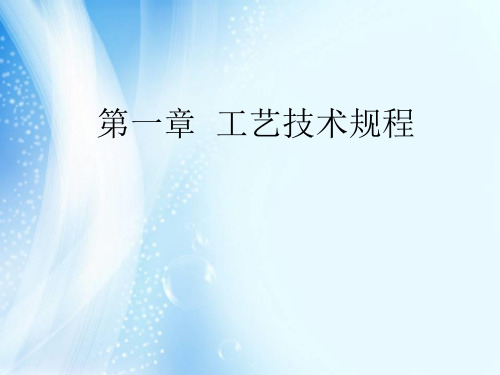
汽油加氢装置
稳定塔顶部产物经稳定塔顶空冷器(A-9202)冷却至55℃后进入稳定塔顶回流 罐(D-9203)。罐顶酸性气体经稳定塔顶气体冷却器(E-9204)冷却后送至硫磺装 置富气再生塔,回流罐底油由稳定塔顶回流泵(P-9203A/B)送回稳定塔顶部作 回流,回流罐底部含硫污水与加氢脱硫反应产物分离罐(D-9202)含硫污水合 并后送出装置。在稳定塔顶管线注入缓蚀剂,最大限度减少设备腐蚀。稳定塔底 物料一部分经稳定塔底重沸器(E-9205)加热后返回稳定塔,另一部分经重汽油产 品泵(P-9204A/B)和稳定塔进料/稳定塔底油换热器(E-9203A/B/C)换热后与
装置设置紧急泄压系统。
汽油加氢装置
3 原料及产品 原料油来自催化裂化汽油,制氢单元所需的氢气由化肥厂氢氮气、重整氢气 提供,产品为低硫汽油,副产品为燃料气。 4 工艺原理
装置采用低压固定床加氢工艺,通过优化工艺条件最大程度降低烯烃的饱和
及因烯烃饱和而带来的辛烷值损失。预加氢的主要目的是将二烯烃转化为单烯 烃,轻的硫化物转化为重的硫化物。预加氢反应产物分离为轻、重汽油组分, 重汽油送至加氢脱硫部分,进行深度脱硫。加氢脱硫后的重汽油与轻汽油混合 作为精制汽油产品。
汽油加氢装置
一、装置简介
1 设计能力
装置设计规模为8万吨/年,年开工时间为8400小时,装置主要组成分为 催化汽油脱砷与选择性加氢单元、分馏单元、加氢脱硫单元、稳定塔单元、 循环氢脱硫和溶剂再生单元、制氢单元和公用工程几个部分组成。装置操 作弹性60%-110%。 2 装置特点 装置由中国石油工程建设公司新疆设计分公司设计,采用DSO-M催化汽 油加氢脱硫降烯烃组合技术,装置预加氢部分催化剂为GHC-22B,加氢脱 硫部分催化剂为GHC-11,原料油过滤,原料油保护,空冷器前注水,催化 剂采用器外再生,设催化剂预硫化设施,为确保操作人员和装置的安全,
加氢精制及制氢联合装置技术方案

30万吨/年加氢精制及制氢联合装置初步技术方案Zhejiang Meiyang International Petrochemical Pharmaceutical Engineering Design CO.,LTD.2008年9月21日目录第一节工程简述及设计原则 (2)第二节装置规模、原料及产品方案 (3)第三节工艺技术方案及流程简述 (5)第四节装置平面布置 (15)第五节公用工程消耗 (16)第六节投资估算 (18)第七节技术保证 (19)第一节工程简述及设计原则一、工程简述xx公司拟建设30万吨/年汽柴油加氢精制装置,原料组成为15万吨/年催化柴油,11~12万吨/年焦化柴油,3~4万吨/年焦化汽油,根据加氢精制装置的生产规模及产品方案,需配套5000m3n/h制氢装置。
(年操作时数为8000小时)。
二、设计范围及原则1、30万吨/年汽柴油加氢精制装置、5000m3n/h制氢装置按联合装置布置,制氢装置只为汽柴油加氢精制装置供氢。
设计范围为联合装置边界线以内,主要内容包括:加氢的反应、分馏部分,制氢的转化造气、变换和PSA部分,以及联合装置的变配电室和中心控制室。
加氢精制装置的含硫气体送至催化的产品精制装置与催化干气一起脱硫。
脱硫后的气体作为制氢装置的主原料,石脑油作为辅助原料。
2、加氢精制装置的目的以脱硫、脱氮和烯烃饱和为主,不考虑加氢改质。
采用国内催化剂、设备和工艺技术。
3、制氢装置造气单元采用催化干气蒸汽转化制氢专有技术;净化单元采用国内变压吸附(PSA)技术。
4、按年开工8000小时计算小时加工量。
5、严格执行国家有关工程建设质量管理法规,确保装置安全、稳定、长周期运行,减少维护维修的工作量,从而提高整体的经济效益。
6、认真贯彻国家关于环境保护和劳动保护的法规和要求。
认真贯彻安全第一预防为主的指导思想。
对生产中易燃易爆有毒有害物质设置必要的防范措施。
三废排放要符合国家现行有关标准和法规。
柴油加氢精制设计书

柴油加氢精制一.物料平衡1. 全装置物料平衡本设计催化柴油处理量为100万吨/年,反应阶段为其末期,年开工时数为8000小时。
装置总物料平衡表 (年开工时数以8000小时/年)注: 粗汽油包括0.03 的溶解气在由∑入方=∑出方,得设备漏损为0.01% < 1%.2. 化学耗氢量 1) 杂质脱除率a) 硫脱除率 =18001801800-×100% = 90%b) 氮脱除率 =26158261-×100% = 77.78% c) 氧脱除率(以酸度计算) 原料油含氧率 =8642.01005616108.53⨯⨯⨯⨯-×100% = 0.00192%精制油含氧率 = 8595.010056161014.03⨯⨯⨯⨯-×100% = 0.0000463%氧脱除率=00192.00000465.000192.0-×100% = 97.58%d) 烯烃饱和率(以溴价计算)烯烃饱和率=1.45.20-×100% = 80%2) 化学耗氢量a) 脱硫耗氢每脱掉1%的硫消耗12.5Nm 3H 2/m 3原料油加氢脱硫耗氢量=8642.0100%901018005.126⨯⨯⨯⨯- = 2.34 Nm 3/T 原料油2.34×125000/22.4×10002=26.152kg/hr b) 脱氮耗氢每脱掉1%的氮消耗53.7Nm 3H 2/m 3原料油加氢脱氮耗氢量=8642.0100%8.77102617.536⨯⨯⨯⨯- = 1.26 Nm 3/ T 原料油1.26×125000/22.4×10002=14.078kg/hr c) 脱氧耗氢每脱掉1%的氧消耗44.6Nm 3H 2/m 3原料油加氢脱氧耗氢量=8642.0100%6.971092.16.445⨯⨯⨯⨯- = 0.0966Nm 3/ T 原料油0.0966×125000/22.4×10002=1.078kg/hr d) 烯烃饱和耗氢量烯烃饱和耗氢量=(20.5-4.1)×10×22.4/160 = 22.96 Nm 3/T 原料油22.96×125000/22.4×10002=256.25kg/hr e) 芳烃饱和饱和1%的芳烃消耗5.0Nm 3H 2/m 3原料油芳烃饱和耗氢量=8642.0568.05.411.43⨯⨯-)(=6.29 Nm 3/ T 原料油6.29×125000/22.4×10002=70.254kg/hrf) 加氢裂解耗氢量原料油裂解程度为3%,每裂解1分子原料,消耗3分子氢加氢裂解耗氢量=34.197%31000⨯×3×22.4 = 10.22Nm 3/T 原料油10.22×125000/22.4×10002=114.017kg/hr各类加氢反应的耗氢量汇总表3. 反应放热a) 加氢脱硫反应放热量=600 kcal/ Nm 3×2.34 Nm 3/T =1405.92kcal/T1405.92 kcal/T×125T/hr=175740kcal/hrb) 加氢脱氮反应放热量=600 kcal/ Nm 3×1.26 Nm 3/T =756.84kcal/T756.84kcal/T×125T/hr=94605kcal/hrc) 加氢脱氧反应放热量=600 kcal/ Nm 3×0.0966 Nm 3/T =57.95kcal/T57.95kcal/T×125T/hr=7243.5kcal/hrd) 加氢烯烃饱和反应放热量=1260 kcal/ Nm 3×22.96 Nm 3/T=28929.6kcal/T28929.6kcal/T×125T/hr=3616200kcal/hre) 加氢芳烃饱和反应放热量=540 kcal/ Nm 3×6.29 Nm 3/T =3399.19kcal/T3399.19kcal/T×125T/hr=424899kcal/hrf) 加氢裂解反应放热量=450 kcal/ Nm 3×10.22 Nm 3/T =4597.16kcal/T4597.16 kcal/T×125T/hr=574644.38 kcal/hr反应放热计算汇总表4. 纯氢消耗量汇总a) 入方:新氢=5.510100%7.27⨯⨯×2×87.68%/8000 = 1076.073kg/hr100024073.1076⨯=25.83T/db) 出方:化学耗氢量=481.829kg/hr100024829.481⨯=11.56T/d排放耗氢量=5.62225×2×80.86% = 553.58kg/hr10002458.553⨯=13.29T/d溶解耗氢(包括低分排放和回流罐排放):低分罐=11.185.387×43.10%×2=18.444kg/hr回流罐=46.442605×2.03%×2=2.379kg/hr∑=18.444+2.379=20.823kg/hr100024823.20⨯=0.4998T/d机械漏损=1076.-(481.829+553.58+20.823)=19.841kg/hr100024841.19⨯=0.476T/d加氢精制装置纯氢消耗量汇总表5. 硫化氢平衡 a) 入方:3432%901018001250006⨯⨯⨯⨯-=215.16kg/hr10002416.215⨯=5.16T/db) 出方:高分排放:34%6.05.62225⨯⨯=69.83kg/hr T/d 68.110002483.69=⨯低分排放:34%55.211.185.387⨯⨯=18.55kg/hr T/d 45.010002455.18=⨯回流罐排放:3485.446.442605⨯⨯=96.62kg/hr T/d 32.210002462.96=⨯水中溶解:27.50kg/hrT/d 66.010002450.27=⨯漏损:215.16-(69.83+18.55+96.62+27.50)=2.66kg/hr氢装置硫化氢平衡表二.反应器设计入口温度为280℃,入口压力为4.0Mpa,出口压力为3.9Mpa,已知数据如下:加氢反应器入口注:物料包括原料油,新氢和循环氢注:物料包括加氢生成油,反应生成气和循环氢气化率e(%)平均分子量w10 15520 16030 165注:气相油平均分子量图1 不同气化率的油气平均分子量图2 3.90Mpa下焓值与温度对应关系图3 3.90Mpa 下气化率与温度对应关系1. 催化剂装填体积空速=催化剂的体积时的体积油在C 20︒=催V 8000/2.864101007⨯=2.5催V ∴=57.86 m 32. 催化剂当量直径所选催化剂为RN-1催化剂(mm 62.1⨯Φ)D p =6×F V =6×3323323106102.12)102.1(4/106)102.1(4/-----⨯⨯⨯⨯+⨯⨯⨯⨯⨯⨯⨯πππ=1.6364×310-m 3. 循环氢和混合氢流量氢油比=油混合氢V V =2.864/8000/10100V 7⨯混合氢=300混合氢V ∴=43392.73Nm 3/hr 混合氢w =混合氢V /22.4×M =18.64.2243392.73⨯=11971.74kg/hr 循环氢w =混合氢w -新氢w =11971.74-3375=8596.74kg/hr4. 入口氢分压作4.0Mpa 下的H m ~t 、e w %~t 图,查得t=320℃时,e w =20.5%,H m =263Kcal/kg 由图可得:当e w =20.5%时,油气M =160.25g/mol入口2p H =总p ×油气纯氢纯氢m m m +=4.0×油气M e w⨯+⨯12500018.6/74.11971%08.83)18.6/(11971.74=3.070Mpa5. 反应器出口温度计算根据热量衡算得:(原料油混合氢w w +)入口m H +Q=(原料油混合氢w w +)出口m H(11971.74+125000) ×263+4.893×106=(11971.74+125000)出口m H 出口m H =298.72Kcal/kg作t ~H m 、e w %~H m 图,查得出口w e =37.3%,出口t =358℃ 6. 出口氢分压反应生成气m =混合氢m +[1-(96.95%+1.49%)]×原料油m=12305074.11971125000-+=13921.74kg/hr由图可得:当e w =37.3%时,油气M =168.65g/mol出口2pH =总p ×油气原料油反应生成气反应生成气(M e w /%)49.1%95.96m 95.7/m %60.7795.7/m ⨯+⨯+⨯=3.9×65.168%3.3712305095.7/74.13921%60.77)95.7/(13921.74⨯+⨯=2.619Mpa7. 气体密度t =(进口t +出口t )/2=(358+320)/2=339℃w e =(进w e +出w e )/2=28.9%mol g /45.164M =气w =混合氢w +原料油w ×w e =11971.74+125000×28.9%=48096.74kg/hr 气V =[混合氢混合氢M w +油气原料油M e w w⨯]×22.4×869.995.31⨯×273273t +=[18.611971.74+45.164%9.28250001⨯]×22.4×869.995.31⨯×273273339+=2778.34 m 3/hrv ρ=气气V w =17.31 kg/m 38. 混合物黏度油气原料油混合氢纯氢原料油混合氢)油气(包含氢气中杂质)(M e m 8308.0118.6m m e m m M ww ⨯+-⨯-⨯+=5.4164%.9281250008308.0118.611971.742%08.8318.611971.74289.01250004.719711⨯+-⨯⨯⨯-⨯+=)(=81.978 mol g /查81.978 mol g /,温度为339℃下,石油馏分蒸汽粘度为i z =0.0145厘泊【1】Tr=)()(K c K T T=43.182.33273339=+Pr=045.3297.195.3Pc P == 根据Tr 与Pr 氢的粘度图得2iH z =0.0143厘泊[1]2H 摩尔分数:i y =总p p 2H =45.164%9.2812500018.674.11971%08.8318.674.11971⨯+⨯=0.746 混z =∑∑0.5iii0.5ii my z m y =5.05.05.05.0978.81746.012746.00145.0978.81746.010143.02746.0⨯-+⨯⨯⨯-+⨯⨯)()(=0.0144厘泊 9. 空塔线速取D=3.6m ,则u=S气V =23.6π25.034.2778⨯⨯=288.77 m/hr =0.0802 m/s 10. 液体滞留量v G =w e m m ⨯+原料油混合氢=11971.74+125000×28.9%=48096.74kg/hrL G =)(原料油w e 1m -=125000×(1-28.9%)=88875kg/hr L G /v G =1.8478 v G =48096.74kg/hr=25.34/2048.048096.74⨯⨯π=1085.00磅/2尺·hr 根据v G 与L G /v G 关系图查得:h=0.1551.13p 1.09.19.05])3.2/1(367.0[h E 103.6h D h z u L p p v ++⨯-⨯⨯=∴-)(ρΔ混 1.1331.039.19.05])3.2155.01(10636.13155.067.0[155.033.0100107.00802.031.17103.6+⨯⨯⨯+⨯-⨯⨯⨯⨯⨯=---)()(=0.1085Pa/m11. 校核①=LpΔ0.1085Pa/m ,在0.~0.115Pa/m 围 ②17.16.301.6D L >== ③=⨯=L L p p ΔΔ0.1085×6.01=0.6519kg/cm 2<0.84kg/ cm 2,符合要求。
- 1、下载文档前请自行甄别文档内容的完整性,平台不提供额外的编辑、内容补充、找答案等附加服务。
- 2、"仅部分预览"的文档,不可在线预览部分如存在完整性等问题,可反馈申请退款(可完整预览的文档不适用该条件!)。
- 3、如文档侵犯您的权益,请联系客服反馈,我们会尽快为您处理(人工客服工作时间:9:00-18:30)。
石化公司加氢精制装置设计方案—、概述(一)设计规模及开工时数公称规模50X104 t/a年开工时数80hr(二)项目范围装置边由反应(包括压缩机)、循环氢脱硫、分馏、公用工程等部分组成,燃料气脱硫及溶剂再生由全厂统一考虑。
(三)原料1、原料油:本装置加工原料为焦化塔顶油、焦化一线油。
2、氢气:装置所需新氢由制氢装置提供。
(四)产品1、化工轻油加氢后轻馏份油作为高质的化工轻油出厂。
2、4#燃料油侧线轻油加氢后作为高质的4#燃料油,硫含量小于5ppm。
二、工艺技术方案(一)确定技术方案的原则1、采用国内先进的工艺技术及催化剂。
2、米用先进合理、成熟可靠的工艺流程。
3、选用性能稳定、运转周期长的机械设备。
4、提高自动控制、安全卫生和环境保护水平。
(二)国内外加氢技术现状加氢精制是指油品在催化剂、氢气和一定的压力、温度条件下,含硫、氮、氧的有机化合物分子发生氢解反应,烯烃和芳烃分子发生加氢饱和反应的过程。
加氢精制的目的是脱硫、脱氮和解决色度及贮存安定性的问题,满足日益严格的环保要求。
常规的加氢精制工艺已有几十年的历史,技术上非常成熟。
新进展主要体现在高活性、高稳定性、低成本新型催化剂的研究和开发上。
荷兰AKZO公司目前最好的脱硫催化剂是KF-752和KF-840.KF-752的活性已是60年代中期相应产品的1.7倍,多用于直馏原料。
对于二次加工原料则采用KF-840O埃克森研究和工程公司(ER&E)于1992年实现商业应用的催化剂RT-601,采用新型A12O3载体,使用先进的促进剂浸渍技术,催化剂活性高,特别适合于加工重质、劣质原料。
在加工直硫柴油时,活性与市场上最好的催化剂相当。
独联体的列宁石油化工科学生产联合体开发的KrM-70催化剂也具有很高活性。
在压力为3.0MPa,空速为3.0h-i,温度为350°C时,可将直硫柴油的硫含量由1.03%降至0.26m%,脱硫率达到99.7%o国内近年来也已开发了多种具有世界先进水平的、高性能的馏分油加氢精制催化剂。
催化剂的外型及适用范围见表4-3-4o表4-3-4国产加氢精制催化剂的外型及适用范围抚顺石油化工研究院在已有FH-5, FH-5A 等加氢精制催化剂的基础上,成功开发了新一代劣质二次加工油品加氢精制催化剂FH-98该催化剂于1999年成功地应用到大庆石化总厂四套工业装置上,其中两套为柴油加氢精制装置、两套为汽油加氢精制装置。
工业应用结果表明,FH-98催化剂具有高的脱硫、脱氮活性。
石油化工研究院开发的新一代加氢脱硫、脱氮、脱芳催化剂RN-10是RN-1催化剂的换代产品。
该催化剂依据脱硫、脱氮机理,以改性Al 2O 3为载体,Ni 、W 为加氢活性组元,比RN-1具有更高的脱硫、脱氮和芳烃饱和活性及良好的活性稳定性及再生性能。
以高硫的中东油、高氮的胜利催化柴油为原料,脱氮活性比RN-1高10%以上;脱硫活性高33%。
该剂于1997年4月在广石化20X 104t/a 催化柴油加氢精制装置上首次工业应用。
并通过石化总公司的鉴定。
目前我国正在运转的加氢精制装置,绝大部分完全由国内自行设计和建造。
国内加氢精制装置的工程技术已十分成熟。
(三)工艺技术方案的选择本装置加工的原料为焦化汽柴油的混合油,混合原料的硫含量和漠价均较高。
根据加工原料的情况和产品质量的要求,本装置选择加氢精制工艺,反应部分采用冷高分流程,设置循环氢脱硫设施,分馏部分采用双塔流程。
催化剂可选用国产FH-98催化剂、RN-10催化剂或其它性能催化剂。
(四)工程技术特点1、加氢精制催化剂可采用国产FH-98催化剂、RN-10催化剂或国内其它性能相当的催化剂。
2、反应部分采用冷高分流程,采用立式油、水、气三相高压分离器。
3、采用炉前混氢方案,提高换热器效率和减缓结焦程度。
4、采用热壁反应器,设三个催化剂床层。
5、反应器入温度通过调节加热炉燃料来控制,床层入温度通过调节急冷氢量来控制。
6、为尽量减少换热器结垢和防止反应器顶部催化剂床层堵塞,以及提高换热器传热效率和延长运转周期,罐区原料油储罐采用惰性气体保护。
装置内设置小于25 u自动反冲洗过滤器对原料油进行过滤。
并对原料油缓冲罐采用惰性气体覆盖措施,以防止原料油与空气接触。
在原料油中注入阻垢剂。
7、反应流出物空冷器入处设注水设施,避免铵盐在低温部位的沉积。
8、分馏部分采用双塔流程。
9、催化剂按器外再生考虑。
10、采用新型双壳程换热器,提高换热器传热效率,使反应流出物及柴油产品进空冷器温度尽可能低,提高加热炉入温度,减小加热炉负荷,降低装置能耗。
11、脱硫化氢汽提塔顶设注缓蚀剂设施,以减轻塔顶流出物中硫化氢对汽提塔顶系统的腐蚀。
12、新氢压缩机采用电动往复式,两台,一开一备。
循环氢压缩机采用中压蒸汽背压透平驱动,一台。
13、催化剂预硫化采用装置内液相硫化方法。
三、要操作条件表4-3-5主要操作条件四、艺流程简述(一)反应部分焦化汽柴油由焦化装置送至原料油缓冲罐,经泵升压至1.0MPa后,进入原料自动反冲洗过滤器,滤去杂质后进入滤后原料油缓冲罐,再由反应进料泵抽出,升压至9.5MPa,与氢气(新氢压缩机出的新氢与循环氢压缩机出的循环氢混合后的氢气)混合,经反应产物与混氢油换热器与反应产物进行换热,升温至225°C (末期为270°C);然后经反应进料加热炉加热至290C(末期为340C)左右,自上而下进入加氢精制反应器,在反应器中,原料油和氢气在加氢催化剂的作用下,进行加氢脱硫、脱氮、烯烃饱和等加氢精制反应。
从加氢精制反应器出来的反应产物(初期335C左右,末期380C左右),经混氢油与反应产物换热器、低分油与反应产物换热器分别与混氢油和低分油换热后,换热到130C左右,进入反应产物空冷器,为了防止加氢反应生成的硫化物和氨在低温下生成铵盐,堵塞和腐蚀空冷器及管道,在空冷器前注入除氧水(生产正常后改用蒸汽凝结水),冷却到50C左右进入高压分离器进行油、气、水三相分离。
高压分离器顶部气体进入循环氢脱硫塔,经与25%的MDEA溶液逆向接触,脱出大部分硫化氢后,进循环氢压缩机压缩升压至9.5MPa,与新氢压缩机来的新氢混合后,返回反应系统。
从高压分离器中部出来的生成油减压后进入低压分离器中,继续进行油、气、水三相分离,油相去分馏系统部分;气体送出装置至脱硫。
从高压分离器及低压分离器底部出来的含硫含氨污水经减压后,送至酸性水汽提处理。
(二)分馏部分低分油依次经低分油与精制柴油换热器和反应产物与低分油换热器换热到202C左右后,进入脱硫化氢汽提塔18层塔盘进料,塔底吹3.5MPa的过热蒸汽2.5t/h,以汽提出生成油中的硫化氢。
塔顶气相178°C依次进入脱硫化氢汽提塔顶空冷器、脱硫化氢塔顶冷凝器冷凝冷却后进入脱硫化氢塔顶回流罐。
液体经分水后,作为塔顶回流,调节塔顶温度;脱出的酸性气体送出装置至脱硫,含硫污水送至酸性水汽提处理。
从塔底出来的脱硫化氢后的汽柴油,自压至分馏塔进料与精制柴油换热器,与精制柴油换热至221C,进入分馏塔,分离汽油和柴油。
分馏塔的热源由重沸炉提供,由分馏塔底重沸炉泵抽出精制柴油,经分馏塔底重沸炉加热至3C左右返塔供热;塔底产品由精制柴油泵抽出,经分馏塔进料与精制柴油换热器、低分油与精制柴油换热器换热至124C,再经精制柴油空冷器冷至50C出装置。
塔顶油汽164C经分馏塔顶空冷器、分馏塔顶冷凝冷却器冷凝冷却至40C后进入分馏塔顶回流罐。
液体分水后,其中一部分作为塔顶回流,调节塔顶温度,另一部分作为精制汽油送出装置。
(三)催化剂预硫化为了提高催化剂活性,新鲜的或再生后的催化剂在使用前都必须进行预硫化。
设计采用液相预硫化方法,以低硫直馏柴油为硫化油,DMDS为硫化剂。
催化剂预硫化结束后,硫化油通过不合格油线退出装置。
五、控水平(一)、自动控制水平1、装置对自动控制的要求加氢精制装置属于高温、高压、临氢条件下操作的二次加工装置,工艺过程较复杂,产品质量要求高,生产过程必须平稳、安全、长周期操作。
综合装置的工艺特点、生产规模及仪表控制系统现状,结合目前仪表自动化技术不断更新、仪表自动化水平不断提高的特点和今后仪表的发展趋势,装置的自动控制系统将选用一套先进的集散控制系统(以下简称DCS),所有重要参数送DCS进行显示、记录、调节、报警,实现装置的集中监视/控制。
考虑到操作的安全、可靠,为本装置设置一套紧急停车及安全联锁系统(以下简称ESD),以确保人员和设备的安全。
建成后该装置的自动控制水平将达到目前国内外同类型装置的先进水平。
2、装置的自动控制水平(1)、装置采用DCS监视、控制和操作,实现工艺生产的过程控制。
DCS融合了计算机技术、通讯技术和图形显示技术,以微处理器为核心,对生产过程进行集中操作管理和分散控制,具有精确度高,可靠性好和维护工作量少等特点,可为实现先进控制和优化控制创造良好的环境。
装置采用ESD实现工艺生产的紧急停车与安全联锁控制。
(2)、为便于生产管理上的需要,采用集中控制,控制系统全部安装在中心控制室内,中心控制室内设机柜室、操作室、工程师站室、计算机室、仪表维修室、DCS值班室、UPS室、空调机室及辅助房间。
(3)、通过设置应用计算机或上位计算机。
在实施基本控制、多参数综合操作与管理的基础上,逐步实现先进控制和优化控制。
(4)、可实现全厂的分级管理,在本装置建立基本控制级,在基本控制级的基础上,进一步实现先进控制和优化控制,并逐步实现工厂计算机过程控制和计算机信息管理系统一体化(即管控一体化CIMS-Computer Integrated Management System),对生产过程进行模拟计算、实时优化、调度、排产、计划、决策等。
(5)、设置必要的成熟可靠的质量分析仪表,对生产过程中的关键参数进行监测、控制,以提高产品收率,保证产品质量,并为实施先进控制打好基础。
(6)、进出生产装置的原料及产品,辅助系统及公用工程等设置相应的计量仪表。
3、主要安全技术措施(1)、本装置生产过程中的物料多为易燃、易爆介质,根据防爆等级划分和全装置的统一考虑,装置内的仪表尽量选用本质安全型,配用安全栅构成本质安全防爆系统;当所需仪表无本质安全等级时则选用隔爆仪表,隔爆仪表的防爆等级不应低于dIICT4.(2)、根据工艺特点和要求,为防止可能出现的重大人身事故、重大设备事故和重大经济损失,为保证操作人员和装置的安全,除DCS的超限报警措施外,为装置和机组设置具有冗余容错功能的紧急停车及安全联锁系统(ESD&SIS,以下简称ESD)以实现事故的预报警、报警及联锁停车。
(3)、根据装置的特点、工艺需要及防爆要求,在有可能有易燃、易爆及有毒气体泄露的危险场所,设置可靠的可燃性气体/有毒气体检测仪表,与DCS构成报警系统。