先进复合材料真空袋,热压罐成型技术
先进复合材料热压罐工艺成型过程压力监测技术

先进复合材料热压罐工艺成型过程压力监测技术李艳霞;顾轶卓;李敏;张佐光【摘要】Autoclave is one of the most impor-tant manufacturing processes commonly used to fabricate composite structures with high performances in aeronau-tical and aerospace area. If the cure process is not well controlled, the defects, such as uneven fiber distribution, bridging, waviness, delamination, and deformation, will occur, which seriously affect surface quality, mechanical properties and reliability of composite parts. The pressure monitoring technology during the autoclave process is an important experimental method to guide mould design, cure cycle optimization and the mechanism analysis of de-fect formation, and to improve the manufacturing capabil-ity of composite structures. In this paper, the test methods and their suitability of the pressures shared by ifber, resin, and prepreg stack during the autoclave process are summa-rized.%热压罐工艺是航空航天领域生产高性能复合材料构件最重要的方法,如工艺控制不利可能导致制件存在纤维架桥、屈曲、孔隙、分层、变形等缺陷,从而影响复合材料表面质量、力学性能以及可靠性。
复合材料真空袋压成型工艺

复合材料真空袋压成型工艺复合材料是指将两种或两种以上具有不同化学成份和物理结构的材料在一定的比例和工艺条件下,通过加工制造成能够共同协同作用的新材料。
而真空袋压成型工艺则是将复合材料放在模具内,通过加压将材料压制成需要的形状,而在加压过程中配以真空吸气技术,使材料具有一定的密实度,从而提高复合材料的强度和使用寿命。
真空袋压成型工艺是一种新兴的成型技术,具有以下的优点:1. 减轻设备的负担:真空袋压成型工艺不需要使用大型压力机械设备,只需要制作好前期的模具和真空袋,并配以真空吸气技术,即可轻松完成材料的成型。
3. 降低生产成本:真空袋压成型工艺所需的设备和技术要比其他传统的复合材料生产工艺要简单,成本较低,同时可大量生产相同规格的复合材料,降低生产成本。
4. 提高生产效率:真空袋压成型工艺可以大大提高生产效率,减少对生产流程的不必要限制,加速产品生产的时间,较为理想的解决了传统复合材料生产周期长、工艺繁琐的问题。
真空袋压成型工艺的具体操作步骤如下:1. 准备模具:根据所需的成型产品,制作相应的模具,确保模具的尺寸、形状等符合要求。
2. 制备真空袋:将尺寸比模具大一定量的布料,缝制成可调节长度的袋子形状,袋口需要留出一定的余量,以备后续的成型操作。
3. 切割材料:根据所需的复合材料尺寸,对原材料进行切割。
4. 叠层:将切割好的复合材料进行叠层。
在叠层过程中需要按照一定的顺序和数量进行,确保复合材料的均匀和平整。
5. 布罩真空袋:将叠好的复合材料放入模具中,然后,将真空袋罩在复合材料的表面上。
6. 抽真空:将真空袋里的空气通过吸气口抽取出来,使其成为空心,以增强复合材料的密实度。
7. 闭袋:将真空袋口封好,以确保整个复合材料处在真空状态下。
8. 压制:通过加压的方式,将复合材料进行压制,压制时间、温度和压力等参数需要根据实际情况进行调整。
9. 反压:在压制时结束以后,在一定时间内达到特殊的反压,确保所制造的复合材料状态稳定。
SEET-神鹰-热压罐成型工艺安全性分析

一、热压罐成型工艺热压罐成型技术是航空、航天领城应用最广泛的成型技术之一,它能在宽广范圈内适应各种材料对加工工艺条件的要求。
二、工艺过程包括:1、模具清理和脱模剂涂抹。
2、预浸料裁切与铺叠。
3、真空袋组合系统制作和坯件装袋.真空袋组合系统制作需要采用各种辅助材料,其中包括:真空袋材料(改性尼龙薄膜或聚酸胺薄膜)、橡胶密封胶条、有孔或无孔隔离膜(聚四氟乙烯或改性氟塑料)。
吸胶材料、透气材料、脱模布和周边胶条等。
按图、所示顺序将坯件与各种辅助材料依次组合并装袋,形成真空组合系统。
装袋后应进行真空检漏,确认无误后,便可闭合锁锁热压罐门,升温固化。
1.真空袋.2.透气材料.3.压板04.有孔隔离层5.预浸料叠层,6.有孔脱模布,7.吸胶材料,8.隔离膜面.9.底模板,10.周边挡条.11.周边密封带 12.热压罐金属基板 13.密封胶条,14.真空管路。
4、固化。
各种树脂体系的固化制度,应根据各种不同树脂体系的固化反应特性和物理特性分别给予制定,要慎重考虑加压时机和关闭真空系统的时机。
固化完毕要控制降温速率,以防止因降温速度过快导致制品内部产生残余应力。
5、出罐脱模。
罐内温度降至接近室温时方可出罐脱模。
6、检测与修整。
三、成型过程中的危险性分析由于根据现场使用方介绍,所有预浸料工序均外委完成,该工房主要进行铺料和成型工序,在此仅对成型过程中的危险性进行分析。
1、辅助材料可燃性由下图可以看出,热压罐成型过程的物理化学变化,一般都会达到120-160℃,因此热压罐成型工艺所选择的辅助材料都应该在此温度范围内不应发生化学变化,物理性能稳定。
各种材料均选用阻燃材料,不应存在发生火灾的危险。
2、设备的阻燃性设备的系统分为:罐体、罐门、开门系统、加热系统、冷却系统、加压系统、空气循环系统、真空系统、隔热系统、控制系统等组成,产品的设计均按照国家机电产品安全标准要求设计。
设备的原材料、电气元器件均按照阻燃设计,隔热材料为阻燃材料,不存在发生火灾的隐患。
复合材料成型加工技术---
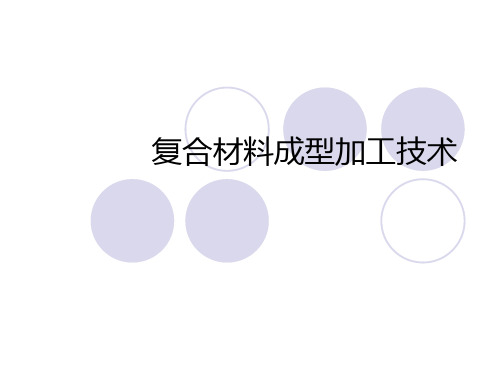
真空袋
1. 过程
制品毛坯 真空袋密封 抽真空 固化 制品
2. 特征 1)工艺简单,不需要专用设备; 2)压力较小,最大为0.1MPa,只适
用厚度1.5mm以下复合材料制品
压力袋成型
压力为0.25~0.5MPa
真空袋-热压罐成型
预浸料成型
预浸料成型(prepreg lay-up)
基本步骤:
设备:要求比RTM高,投资大
模压成型(Compression Molding)
将复合材料片材或模塑料放入金属对模中, 在温度和压力作用下,材料充满模腔,固 化成型,脱模制得产品的方法。
模具预热 模压料称量
涂刷脱模剂 预热
装模
压制 脱模
制品 检验 后处理
BMC模压 SMC、TMC模压 预浸料模压(层压)
多孔膜 密实膜 多孔织物
多孔膜
真空封装系统:透气、隔离、吸胶、透胶系统
适合加工高纤维含量(>60%)复合材料 简单和复杂构型构件均可以加工 高强度和高刚度复合材料均可以加工 劳动强度大,不适于大量加工 构件成本高 在航空和军事用先进复合材料上用途广泛
喷射成型(spray-up process)
包括:
干法缠绕: 预浸纱 湿法缠绕: 纤维纱 半干法缠绕: 纤维纱
加热软化 缠绕 浸胶 缠绕 浸胶 烘干 缠绕
非常适合制作管 状制品,如压力 容器、管道、火 箭发动机壳体、 喷管、化学品储 存罐等
配合CAD系统, 可以制作外形更 为复杂的构件
基本步骤
① 粗纱线轴放置在粗纱架上; ② 几根粗纱从导纱沟中穿过; ③ 固化剂和树脂在容器中混合后倒入树脂浸渍槽中; ④ 在卷绕滚筒上涂覆脱模剂、凝胶涂层,并将卷绕滚筒放
热压罐_VARTM组合成型新工艺设计

的成型条件,或者可以满足立体织物 强度高质量的纤维增强树脂基复合
增强低粘度树脂基复合材料的成型 材料。COMPRIS技术需要一个压
条件。在能够满足包括各种织物形 力容器或热压罐(或者其他提供压力
的手段)来制造复合材料部件。它 实际上就是热压罐与VARTM的组 合技术。
德国DLR German Aerospace Center和INVENT GmbH的技 术人员也进行了相关的研究。他 们同样考虑将热压罐成型工艺和 VA RTM工艺的优点结合在一起。 由此提出了所谓的SLI(Single Line Injection)技术的概念。SLI 是指纤维预成型体抽真空和树脂体 系的注射通过同一根树脂传递管道 进行。
(1)树脂导入与流动方式。 液体成型工艺中树脂的导入方 式和流动方式决定了树脂对纤维的 浸渍质量,是影响制品性能的重要因 素。在普通的RTM成型工艺中,树 脂流动方式均采用平面流动方式,即 树脂的流动前沿以与铺层平面平行 的方向往前推进,流动前锋过后的预 制件中均充满树脂,这种方式适合于 流动路径较短的制品。对于比较大 的制件,流动路径可能要几米甚至十 几米,这时树脂流动的原动力——压 力差会随着流动距离的增加而减弱,
居建国 研究员。在读博士,从事航天领域
先进复合材料及其制造技术的研究工 作20余年。主要研究方向为复合材料 加工工程。
随着复合材料专业的发展,复合 材料制备技术也在不断地发展和完 善。迄今为止,已有的复合材料制备 技术有:手糊或湿法铺覆工艺,真空 袋压、真空成型和热压罐成型工艺, 模压成型工艺,热压/冷压模塑成型 工艺,注射模塑成型工艺,缠绕成型 工艺,拉挤成型工艺,复合材料液体 成型工艺等。
2007年第12期·航空制造技术73
万方数据
真空袋成形工艺
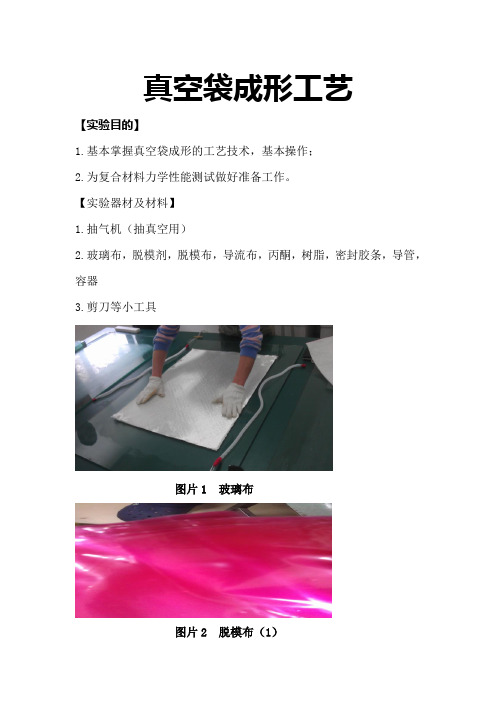
真空袋成形工艺【实验目的】1.基本掌握真空袋成形的工艺技术,基本操作;2.为复合材料力学性能测试做好准备工作。
【实验器材及材料】1.抽气机(抽真空用)2.玻璃布,脱模剂,脱模布,导流布,丙酮,树脂,密封胶条,导管,容器3.剪刀等小工具图片1 玻璃布图片2 脱模布(1)图片3 抽气管【实验过程】一.铺布1.将玻璃布剪成长方形,铺在台面上;2.剪下一条条红色的脱模布,铺在玻璃布的各个边上;3.铺一层脱模布,脱模布比玻璃大,完整的覆盖住整个实验材料4.在脱模布上铺上导流布,用来引流,使树脂可以均匀的走过玻璃布;二.贴密封胶条,铺密封膜在玻璃布外用密封胶条贴一个长方形,并将导管(抽气导管和引树脂导管)紧紧贴在胶条上,两个导管左右分开,引导树脂的导管放在导流布上。
将密封胶条撕开,铺一张密封膜,确保整个密封膜四周密封很好,不漏气,尤其是导管附近,要用胶条贴的很紧,并且密封膜要平整,以确保实验材料加工出来可以很平整。
三.抽真空,引树脂1.先抽一次检测整个真空袋是否漏气,抽气机压强在一段时间内没有变,证明密封良好,如果密封不好,有漏气,则需要继续进行密封工作,直到密封完好为止。
2.确保密封很好之后,开始抽真空。
先将真空袋内的空气抽走,整个真空袋变为扁平状,然后将引流导管插入制作好的树脂混合剂中,开始进行导流。
3.观察导流过程,发现树脂以直线的形式向抽气方向先快后慢的移动,在抽气端的导流布没有完全铺到材料上,是为了控制树脂流动速度,保证树脂可以均匀的铺满整个材料(玻璃布)。
4.等树脂充满后,取出导管,静置一段时间,启封。
启封时注意要慢,一层一层的揭开,不能太快,防止破坏材料。
揭开密封膜,一层一层去掉玻璃布上的其他铺层,轻轻的从台面上撕下制作完成的材料。
四.后续工作1.拆除装置,清洗台面,整理材料,将其剪成小的长方体,用于后来要做的力学实验。
2.制作实验报告,附图片。
【注意事项和实验心得】1.实验前要把台面清理干净,还有实验材料玻璃布要铺的平整。
7复合材料热压罐成型技术解析
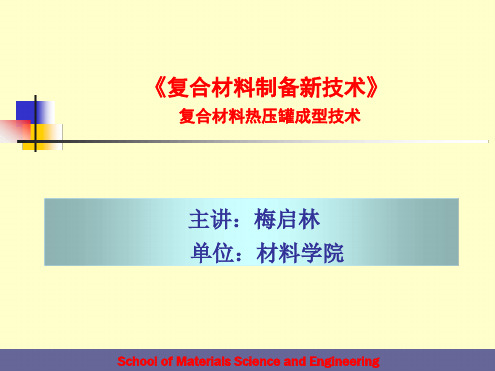
复合材料热压罐成型技术
主讲:梅启林 单位:材料学院
School of Materials Science and Engineering
一、前言
? 热压罐:
航空复合材料制品的主要生产设备,具有整体加热系统的大型压力容器。
? 优点:
(1)大范围内适应各种材料对加工条件的要求 高温环氧175oC,600KPa 聚酰亚胺300~400oC, 1MPa
? 主要工艺过程 (1)均匀稳定树脂膜的制备----关键 (2)树脂熔融浸渍纤维 (3)预浸料冷却 (4)预浸料收卷
School of Materials Science and Engineering
预浸料的性能
? 外观 ? 物理性能
(1)单位面积纤维的质量( GB7192-8)7 (2)树脂含量( GB7192-8)7 (3)挥发分含量( GB6056-8)5 ( 4)粘性(表征预浸料铺覆性和层间粘合性的指标) ( 5)流动度(一定条件下,预浸料树脂可流出的数量占预浸料质量的百分比,
设计力学、理化性能
School of Materials Science and Engineering
预浸料的制备
? 溶液浸渍法(辊筒缠绕法、连续排铺法)
( 1)辊筒缠绕法
特点:
间歇性、设备简单、生产效率低、批量小
实验室或小批量生产
工作原理:
一系列变速机构 ---- 调节辊筒转动、导丝辊丝杠横向移动速度比 ---- 纤维间距
工艺参数:
纤维状态(单丝根数、总纤度、捻度等 ---- 影响浸渍程度和含胶量)
胶液浓度(影响含胶量最严重的因素 ---- 调节胶液密度、温度来控制)
牵引速度
先进复合材料热压罐成型技术

先进复合材料热压罐成型技术苏鹏;崔文峰【摘要】近年来,随着复合材料在航空航天中的广泛应用,其加工制造理论和技术水平在逐步提高.其中,热压罐成型技术是复合材料结构成型中较为成熟的方法,在航空航天产品中广泛应用.但是,由于现代大型飞机中应用的复合材料整体构件轮廓复杂度越来越高,尺寸也越来越大,传统热压罐成型技术已经无法满足制造实际应用需求.因此,为提高制品的质量和工作效率,热压罐成型工艺的改进和优化依然是当前主要的途径.本文根据传统热压罐成型工艺流程和特点,从提高产品质量和效率的角度分析其工艺过程,针对下料环节、温度控制环节、压力控制环节以及模具设计等关键技术,给出现阶段的最新研究进展.【期刊名称】《现代制造技术与装备》【年(卷),期】2016(000)011【总页数】2页(P165-166)【关键词】航空航天;复合材料;热压罐成型技术;温度场控制技术【作者】苏鹏;崔文峰【作者单位】大连长丰实业总公司,大连 116038;大连长丰实业总公司,大连116038【正文语种】中文热压罐成型工艺的工作原理是利用罐内的高温压缩气体产生的压力对复合材料坯料进行加热加压以完成固化成型。
热压罐成型系统是由罐体、冷却系统、真空系统、压力系统、加热系统、密封系统和控制系统构成。
表1是热压罐各个系统的技术要求,该技术要求的满足可使热压罐罐内压力和温度均匀分布。
热压罐工艺流程:①预浸料下料(裁剪);②铺叠毛坯;③抽真空预压实(坯料与模具贴合);④(组装)固化;⑤(降温)脱模;⑥无损检测;⑦切边打磨;⑧称重。
当前,在热压罐抽真空压实环节借助真空袋与模具之间抽真空形成的负压,对复合材料坯料进行加压。
现已经发展成熟的技术有真空袋成型法、压力袋成型法和双真空袋成型法。
其中,真空袋成型法加压不大于0.1MPa,只适用于薄板制作或者蜂窝夹层结构。
缺点是制品外形表面质量精度较差。
压力袋成型法是通过向橡皮囊构成的压力袋(气压室)内注入压缩气体实现对复材坯料的加压,压力可达0.25~0.5MPa,特点是对模具的刚度和强度要求高,制品的机械性能好于真空袋成型法制品。
再次美化后-2单元4讲热压罐成型-封装
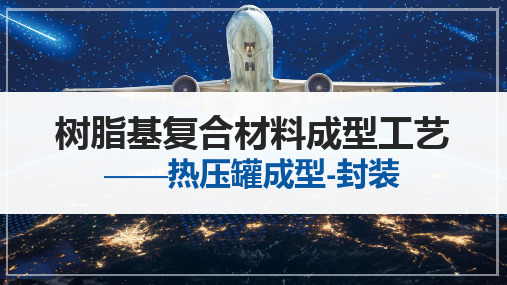
真空袋组成
08 均压板
均压板是有一定刚度的光滑板,它拥有 与成品相同的尺寸和表面形状,并与复 合材料铺层直接接触,主要作用如右:
①使制件与真空袋接触的表面光滑; ②防止排出过多的树脂; ③使转角保持光滑,防止变厚度区域发生褶皱; ④通过轻轻按压可以调整制件的外形; ⑤甚至可以辅助对整个零件上的压力进行重新分配。 均压板可采用金属,若是软模,则是未硫化的橡胶, 可重复使用6~10次。
树脂基复合材料成型工艺
——热压罐成型-封装
学习目标
01
能正确选择真空 袋辅助材料
02
能完成真空袋 的制备
热压罐成型制备的航空复合材料结构 件的成本为1.5~2万元/kg,除了热压 罐初始投资成本高,真空袋辅助材料 的消耗也是很重要的一个因素,下图 为典型固化真空袋系统,你能说出各 序号指代的材料名称和作用吗?
THANK YOU
尺寸:挡条的高度应该比固化后层合板的厚
度稍高,或与层合板、分离膜以及吸胶材料
组成的厚度大致相等。
档
条
真空袋组成
03 热电偶
用于监测固化时的温度变化,以确保生产出 满足规范要求的高质量复合材料零件。每间 隔500mm安放一个热电偶,整个固化体系至 少需要安放两个热电偶。 位置:升温最快和最慢的地方,安放位置不 应破坏零件表面,可放在制品的加工余量处, 或可包住贴于模具上面。
真空袋组成
11 随炉件 13 底模板
如果需要制备随炉件考察固化工艺, 真空袋内还需使用铝板或钢板作为底 模 板 , 铺 叠 200mm×200mm×16 层 平 板随炉件,用于固化脱模后测三点抗 弯强度和层间剪切强度等。
真空袋组成
复合材料热压罐技术原理
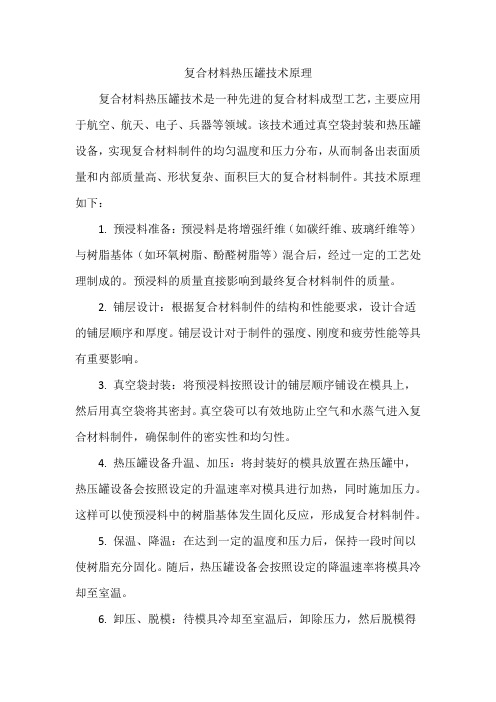
复合材料热压罐技术原理
复合材料热压罐技术是一种先进的复合材料成型工艺,主要应用于航空、航天、电子、兵器等领域。
该技术通过真空袋封装和热压罐设备,实现复合材料制件的均匀温度和压力分布,从而制备出表面质量和内部质量高、形状复杂、面积巨大的复合材料制件。
其技术原理如下:
1. 预浸料准备:预浸料是将增强纤维(如碳纤维、玻璃纤维等)与树脂基体(如环氧树脂、酚醛树脂等)混合后,经过一定的工艺处理制成的。
预浸料的质量直接影响到最终复合材料制件的质量。
2. 铺层设计:根据复合材料制件的结构和性能要求,设计合适的铺层顺序和厚度。
铺层设计对于制件的强度、刚度和疲劳性能等具有重要影响。
3. 真空袋封装:将预浸料按照设计的铺层顺序铺设在模具上,然后用真空袋将其密封。
真空袋可以有效地防止空气和水蒸气进入复合材料制件,确保制件的密实性和均匀性。
4. 热压罐设备升温、加压:将封装好的模具放置在热压罐中,热压罐设备会按照设定的升温速率对模具进行加热,同时施加压力。
这样可以使预浸料中的树脂基体发生固化反应,形成复合材料制件。
5. 保温、降温:在达到一定的温度和压力后,保持一段时间以使树脂充分固化。
随后,热压罐设备会按照设定的降温速率将模具冷却至室温。
6. 卸压、脱模:待模具冷却至室温后,卸除压力,然后脱模得
到复合材料制件。
总之,复合材料热压罐技术原理主要是通过控制温度、压力和时间等参数,实现树脂基体的固化反应,从而制备出具有高性能的复合材料制件。
复合材料双真空袋(DB)成型工艺研究(精)

的缺陷,分别对应层间剪切强度为70. 7MPa和,相比较而言,DB2b工艺和DB2c工艺制备的板材内部质量较好,层间剪切强度得到了显著提高。这表明相应DB工艺平台的设置,使材料的内部质量得到较大的改进。通过光学显微镜对复合材料的显微结构进行观察可了解材料中介于微观和宏观尺度之间的缺陷构成和分布状况,如图6所示,真空袋工艺和DB2a工艺制备的板材中存在较多数量的孔隙,尤其是富树脂区内的孔隙没有充分排除,而DB2b和DB2c工艺制备的板材中孔隙很少。在通常的真空袋工艺制备的复合材料中,孔隙主要来源于树脂配制过程中裹入的空气、树脂中的挥发分或小分子副产物以及预浸料铺贴的操作过程中裹入预浸料片层之间的空气。在铺贴中预压实操作和固化时抽真空虽然可以抽走大部分的空气,但是由于预浸料通常具有一定粘性,预浸料片层会局部粘结在一起,而且真空对毛坯存在一个压实作用,在一定程度上封闭了孔隙排出的通道,并且使预浸料毛坯内部孔隙和毛坯外部的压力梯度降低,减小了孔隙运动的驱动力,因此毛坯中的部分孔隙难以排出而滞留在复合材料中构成缺陷。
复合材料双真空袋(DB)成型工艺研究WORD文档使用说明:复合材料双真空袋(DB)成型工艺研究来源于
本WOED文件是采用在线转换功能下载而来,因此在排版和显示效果方面可能不能满足您的应用需求。
如果需要查看原版WOED文件,请访问这里
复合材料双真空袋(DB)成型工艺研究文件原版pdf
通过测试复合材料的层间剪切强度来初步表征工艺过程对复合材料力学性能的影响,测试标准采用JC/T773-1982;通过超声C扫描考察复合材料的内部质量,并结合光学显微镜来观察复合材料中孔隙含量和树脂对纤维的浸渍情况。
复合材料的成型工艺

复合材料的成型工艺复合材料的成型工艺主要包括以下几种:1. 手糊成型工艺:是一种湿法铺层成型法,通过涂刷胶液和铺设纤维织物,在模具上形成一定厚度的层片,然后进行固化。
2. 喷射成型工艺:是将树脂和纤维混合后,通过喷射的方式在模具表面形成一定厚度的层片,再进行固化。
3. 树脂传递模塑技术(RTM技术):将纤维织物放入模具中,然后注入树脂,经过一定的温度和压力条件进行固化,形成复合材料制品。
4. 袋压法成型:是将纤维织物放入密封的袋子里,然后通过压力使纤维织物紧密结合在一起,再经过固化得到复合材料制品。
5. 真空袋压成型:是在袋压法的基础上,通过抽真空的方式排除纤维织物内的空气和水分,提高制品的密实度和质量。
6. 热压罐成型技术:是将预浸料放入金属模具中,通过热压罐的高温高压作用,使预浸料粘结成复合材料制品。
7. 液压釜法成型技术:是将预浸料放入密封的液压釜中,通过液体介质的压力使预浸料紧密结合在一起,再经过固化得到复合材料制品。
8. 热膨胀模塑法成型技术:是将纤维织物放入模具中,利用热膨胀原理使纤维织物紧密结合在一起,再经过固化得到复合材料制品。
9. 夹层结构成型技术:是将两层或更多层预浸料之间夹入一层泡沫材料或其他材料,通过加热加压或抽真空的方式使其粘结成复合材料制品。
10. 模压料生产工艺:是将纤维织物和树脂混合后,经过一定温度和压力条件进行固化,形成模压料,然后将其加工成制品。
11. ZMC模压料注射技术:是将ZMC模压料加热后注入模具中,经过一定的温度和压力条件进行固化,形成复合材料制品。
12. 层合板生产技术:是将多层预浸料按照一定的顺序叠放在一起,然后经过热压或冷压的方式使其粘结成复合材料层合板。
13. 卷制管成型技术:是将纤维织物和树脂混合后,通过卷制机卷制成管状制品。
14. 纤维缠绕制品成型技术:是将纤维织物缠绕在芯模上,然后注入树脂或进行热处理,形成复合材料制品。
15. 连续制板生产工艺:是将预浸料连续通过加热和加压装置,使其连续地粘结成复合材料板材。
先进复合材料真空袋,热压罐成型技术
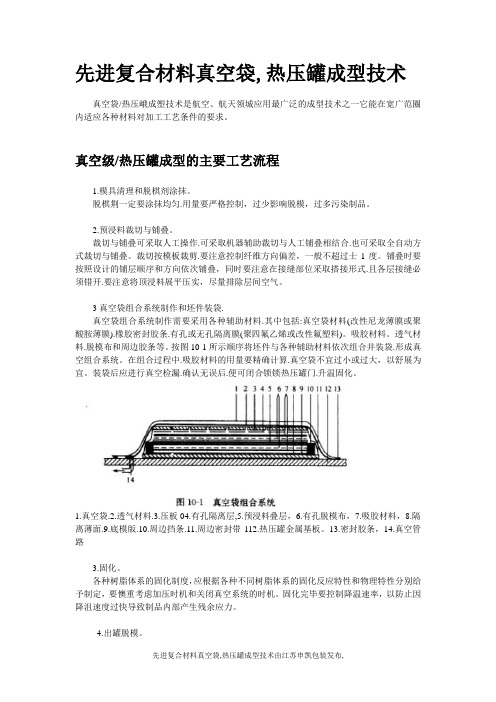
先进复合材料真空袋,热压罐成型技术真空袋/热压峨成塑技术是航空、航天领城应用最广泛的成型技术之一它能在宽广范圈内适应各种材料对加工工艺条件的要求。
真空级/热压罐成型的主要工艺流程1.模具清理和脱棋剂涂抹。
脱棋荆一定要涂抹均匀.用量要严格控制,过少影响脱模,过多污染制品。
2.预浸料裁切与铺叠。
裁切与铺叠可采取人工操作.可采取机器辅助裁切与人工铺叠相结合.也可采取全自动方式裁切与铺叠。
裁切按模板裁剪.要注意控制纤维方向偏差,一般不超过士1度。
铺叠时要按照设计的铺层顺序和方向依次铺叠,同时要注意在接缝部位采取搭接形式.且各层接缝必须错开.要注意将顶浸料展平压实,尽量排除层间空气。
3真空袋组合系统制作和坯件装袋.真空袋组合系统制作需要采用各种辅助材料.其中包括:真空袋材料(改性尼龙薄膜或聚酸胺薄膜).橡胶密封胶条.有孔或无孔隔离膜(聚四氟乙烯或改性氟塑料)。
吸胶材料。
透气材料.脱模布和周边胶条等。
按图10-1所示顺序将坯件与各种辅助材料依次组合井装袋.形成真空组合系统。
在组合过程中.吸胶材料的用量要精确计算.真空袋不宜过小或过大,以舒展为宜。
装袋后应进行真空检漏.确认无误后.便可闭合锁锁热压罐门.升温固化。
1.真空袋.2.透气材料.3.压板04.有孔隔离层,5.预浸料叠层,6.有孔脱模布,7.吸胶材料,8.隔离薄面.9.底模版.10.周边挡条.11.周边密封带112.热压罐金属基板。
13.密封胶条,14.真空管路3.固化。
各种树脂体系的固化制度,应根据各种不同树脂体系的固化反应特性和物理特性分别给予制定,要懊重考虑加压时机和关闭真空系统的时机。
固化完毕要控制降温速率,以防止因降沮速度过快导致制品内部产生残余应力。
4.出罐脱模。
罐内温度降至接近室温时方可出罐脱模。
5.检测与修整。
先进复合材料制品一般都要进行无损探伤检侧。
预没料侧备织物预浸料是热压罐成型的半成品原材料,可采用溶液及演法和热熔浸渍法制造。
1.溶液浸渍法。
复合材料成型工艺大揭秘,你了解几个?
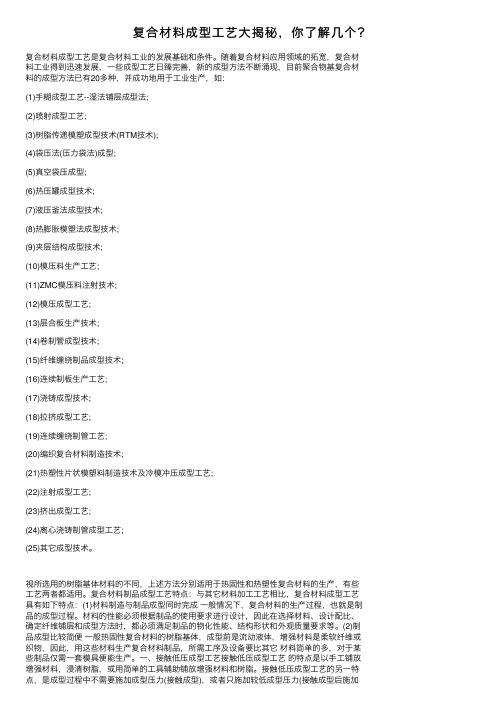
复合材料成型⼯艺⼤揭秘,你了解⼏个?复合材料成型⼯艺是复合材料⼯业的发展基础和条件。
随着复合材料应⽤领域的拓宽,复合材料⼯业得到迅速发展,⼀些成型⼯艺⽇臻完善,新的成型⽅法不断涌现,⽬前聚合物基复合材料的成型⽅法已有20多种,并成功地⽤于⼯业⽣产,如:(1)⼿糊成型⼯艺--湿法铺层成型法;(2)喷射成型⼯艺;(3)树脂传递模塑成型技术(RTM技术);(4)袋压法(压⼒袋法)成型;(5)真空袋压成型;(6)热压罐成型技术;(7)液压釜法成型技术;(8)热膨胀模塑法成型技术;(9)夹层结构成型技术;(10)模压料⽣产⼯艺;(11)ZMC模压料注射技术;(12)模压成型⼯艺;(13)层合板⽣产技术;(14)卷制管成型技术;(15)纤维缠绕制品成型技术;(16)连续制板⽣产⼯艺;(17)浇铸成型技术;(18)拉挤成型⼯艺;(19)连续缠绕制管⼯艺;(20)编织复合材料制造技术;(21)热塑性⽚状模塑料制造技术及冷模冲压成型⼯艺;(22)注射成型⼯艺;(23)挤出成型⼯艺;(24)离⼼浇铸制管成型⼯艺;(25)其它成型技术。
视所选⽤的树脂基体材料的不同,上述⽅法分别适⽤于热固性和热塑性复合材料的⽣产,有些⼯艺两者都适⽤。
复合材料制品成型⼯艺特点:与其它材料加⼯⼯艺相⽐,复合材料成型⼯艺具有如下特点:(1)材料制造与制品成型同时完成⼀般情况下,复合材料的⽣产过程,也就是制品的成型过程。
材料的性能必须根据制品的使⽤要求进⾏设计,因此在选择材料、设计配⽐、确定纤维铺层和成型⽅法时,都必须满⾜制品的物化性能、结构形状和外观质量要求等。
(2)制品成型⽐较简便⼀般热固性复合材料的树脂基体,成型前是流动液体,增强材料是柔软纤维或织物,因此,⽤这些材料⽣产复合材料制品,所需⼯序及设备要⽐其它材料简单的多,对于某些制品仅需⼀套模具便能⽣产。
⼀、接触低压成型⼯艺接触低压成型⼯艺的特点是以⼿⼯铺放增强材料,浸清树脂,或⽤简单的⼯具辅助铺放增强材料和树脂。
复合材料制备技术讲义(5)-热压罐成型实例

T300—3000一40B碳纤维性能
T300/HD58层压板物理及力学性能
4、工艺难点分析
(1)蜂窝夹层结构面层密实度控制问题 蜂窝夹层结构面层密实度较难保证。尤其是采用一步法固化成型时, 由于加压固化的支持面为蜂窝芯,造成复材面板加压不均匀,呈凹凸 状,从而导致面层密实度极不均匀,有的甚至出现局部明显分层,造 成力学性能差,面层传剪能力变弱,直接影响结构的使用性能。采取 三步法热压罐固化工艺及软模技术,保证了面层密实度的要求。 (2)两端框与壳体的装配协调问题 火箭仪器舱处于三级箭体上的重要部位。其前后端框与卫星接口支 架、三级储箱的连接要求极其严格,其对接面平面度、圆度、平行度、 方位扭转误差以及对舱体的纵轴垂直度在图纸和技术条件上均有严格 的规定。我们通过改进钣金工艺方法,设置合理的工艺流程,提高铆 接及装配质量来满足仪器舱的装配要求。
1、仪器舱的结构形式及特点 整体采用碳纤维面板/铝蜂窝夹层结构; 前后端面为铝合金端框,前端面与卫星支架相连、后端面 与三级过渡段和整流罩相协调,舱壁上安装了圆盘支架、电
子程配、数字量变换器、振动传感器,小平台支架、爆炸器 等一系列仪器设备。另外,舱壁上还分布着检查窗等开口;
仪 器 舱 呈 截 圆 锥 形 , 前 框 直 径 为 1248mm , 后 框 直 径 为 2896mm ,高为 1028mm ,截圆锥形壳体与后端面呈 52.3°的 夹角。
5.2 热压罐结构
分大部分:机械部分、功能部分、控制部分。
机械部分包括罐体、底板与小车、气流控制装置、密封装置等;
功能部分包括加热、加压、抽真空及冷却系统;
控制部分包括温度、压力的手动和自动控制系统; 罐体:为圆筒形压力容器,封头采用压制成型,筒身采用钢板卷筒焊制。 筒身由内外筒组成,加热与冷却装置安装在内外筒之间。罐体内装有风 机,使空气通过内外筒涵道强制循环流动。内筒焊有底板,上置轨道和 小车,制品可由小车进出罐体。 加热装置:采用电加热和空气加热。电加热结构紧凑,方便易控。 冷却装置:强制冷却。
聚合物基复合材料及其成型工艺 北京航空航天大学 第4章 热压罐成型工艺

抽真空
隔离材料 复合材料毛 坯 隔离材料 模 具 密封胶带 挡块
1.热压罐工艺原理
热压罐内的气源示意图
z z的待成型构件
构件推入热压罐内
1.热压罐工艺原理
(1)升温速率α1、α2 (2)降温速率β (3)第一恒温平台Tcons1-tcons1 (4)第二恒温平台Tcons2-tcons2 (5)真空压力Pvac (6)外加压力Papp (7)加压时机tapp
罐内温度
要求达到:罐内各点温差≤5oC,升温速率1-8oC/min 可调 罐内温度制度可按树脂体系的固化温度和制件大小确定, 一般为两阶段加温、恒温工艺
热压罐 的冷却
降温过程对复合材料制造质量也有重要影响 循环水冷却,降温速率0.5-6oC/min 可调
3 热压罐系统的组成
罐内 压力 真空 系统
压力可达1.5-2.5MPa,误差不大于0.05MPa 设有安全防爆装置
3 模具材料
一般性要求
• • • • • • •
耐温性:180℃长期使用 耐压性:0.7MPa长期使用 升温速率均匀 尺寸精度要求 表面光洁度与硬度要求 能够定位和支撑成型构件 热膨胀系数尽量与复合材料相近
• • • • • •
耐溶剂清洗 便于机械加工 气密性好 重量轻 尺寸与运输空间相容 使用方便,易维护
钢
橡胶
碳纤维 其热膨胀系数与所成型复合材料构件一致,质量轻,材料模量高,模具 刚度大;适用于高精度的大型构件的成型,但材料成本高,耐温低,表 复合材料 面易划伤,有吸湿问题 玻璃纤维 质量轻,材料价格低;但材料模量低,模具刚度差;一般用于简单成型 复合材料 或型面要求不高的结构
3 模具材料-模具的分类
相关术语
一种用于热压罐成型的真空袋封装方法[发明专利]
![一种用于热压罐成型的真空袋封装方法[发明专利]](https://img.taocdn.com/s3/m/cd4b74d86394dd88d0d233d4b14e852458fb399d.png)
(19)中华人民共和国国家知识产权局(12)发明专利申请(10)申请公布号 (43)申请公布日 (21)申请号 201811158253.6(22)申请日 2018.09.30(71)申请人 航天特种材料及工艺技术研究所地址 100074 北京市丰台区云岗北里40号院(72)发明人 汪东 武海生 王国勇 柯红军 李丽英 田正刚 赵跃杰 (74)专利代理机构 北京格允知识产权代理有限公司 11609代理人 谭辉(51)Int.Cl.B29C 70/34(2006.01)B29C 70/54(2006.01)(54)发明名称一种用于热压罐成型的真空袋封装方法(57)摘要本发明涉及一种用于热压罐成型的真空袋封装方法,包括以下步骤:将经浸渍的预成型构件放置在模具靠近中央的位置;在预成型构件上依次放置隔膜布和透气毡;在预成型构件的外边缘和模具的外边缘之间沿着模具周边涂覆至少一圈密封腻子和至少一圈密封粘接剂;利用所述至少一圈密封腻子和至少一圈密封粘接剂将真空袋封装在所述模具上;通过导气槽对真空袋抽真空,并利用抽真空所形成的真空压力使所述至少一圈密封粘接剂固化。
采用本发明技术的封装方法能够显著提高在室温下的真空袋封装成功率,并有效减少现有技术中复合材料高温固化成型时的真空渗漏现象,提高了成型复合材料产品的质量和合格率,具有显著的经济效益。
权利要求书1页 说明书5页 附图1页CN 109094052 A 2018.12.28C N 109094052A1.一种用于热压罐成型的真空袋封装方法,其特征在于,所述方法包括以下步骤:(1)将经浸渍的预成型构件放置在模具靠近中央的位置,所述模具具有用于抽真空的导气槽;(2)在预成型构件上依次放置隔膜布和透气毡;(3)在预成型构件的外边缘和模具的外边缘之间沿着模具周边涂覆至少一圈密封腻子和至少一圈密封粘接剂,所述至少一圈密封腻子相对于所述至少一圈密封粘接剂位于外圈,所述至少一圈密封粘接剂相对于所述至少一圈密封腻子位于内圈,并且所述导气槽位于所述至少一圈密封粘接剂的内侧;(4)利用所述至少一圈密封腻子和至少一圈密封粘接剂将真空袋封装在所述模具上;(5)通过导气槽对真空袋抽真空,并利用抽真空所形成的真空压力使所述至少一圈密封粘接剂固化。
- 1、下载文档前请自行甄别文档内容的完整性,平台不提供额外的编辑、内容补充、找答案等附加服务。
- 2、"仅部分预览"的文档,不可在线预览部分如存在完整性等问题,可反馈申请退款(可完整预览的文档不适用该条件!)。
- 3、如文档侵犯您的权益,请联系客服反馈,我们会尽快为您处理(人工客服工作时间:9:00-18:30)。
先进复合材料真空袋,热压罐成型技术
真空袋/热压峨成塑技术是航空、航天领城应用最广泛的成型技术之一它能在宽广范圈内适应各种材料对加工工艺条件的要求。
真空级/热压罐成型的主要工艺流程
1.模具清理和脱棋剂涂抹。
脱棋荆一定要涂抹均匀.用量要严格控制,过少影响脱模,过多污染制品。
2.预浸料裁切与铺叠。
裁切与铺叠可采取人工操作.可采取机器辅助裁切与人工铺叠相结合.也可采取全自动方式裁切与铺叠。
裁切按模板裁剪.要注意控制纤维方向偏差,一般不超过士1度。
铺叠时要按照设计的铺层顺序和方向依次铺叠,同时要注意在接缝部位采取搭接形式.且各层接缝必须错开.要注意将顶浸料展平压实,尽量排除层间空气。
3真空袋组合系统制作和坯件装袋.
真空袋组合系统制作需要采用各种辅助材料.其中包括:真空袋材料(改性尼龙薄膜或聚酸胺薄膜).橡胶密封胶条.有孔或无孔隔离膜(聚四氟乙烯或改性氟塑料)。
吸胶材料。
透气材料.脱模布和周边胶条等。
按图10-1所示顺序将坯件与各种辅助材料依次组合井装袋.形成真空组合系统。
在组合过程中.吸胶材料的用量要精确计算.真空袋不宜过小或过大,以舒展为宜。
装袋后应进行真空检漏.确认无误后.便可闭合锁锁热压罐门.升温固化。
1.真空袋.
2.透气材料.
3.压板0
4.有孔隔离层,
5.预浸料叠层,
6.有孔脱模布,
7.吸胶材料,
8.隔离薄面.
9.底模版.10.周边挡条.11.周边密封带112.热压罐金属基板。
13.密封胶条,14.真空管路
3.固化。
各种树脂体系的固化制度,应根据各种不同树脂体系的固化反应特性和物理特性分别给予制定,要懊重考虑加压时机和关闭真空系统的时机。
固化完毕要控制降温速率,以防止因降沮速度过快导致制品内部产生残余应力。
4.出罐脱模。
罐内温度降至接近室温时方可出罐脱模。
5.检测与修整。
先进复合材料制品一般都要进行无损探伤检侧。
预没料侧备
织物预浸料是热压罐成型的半成品原材料,可采用溶液及演法和热熔浸渍法制造。
1.溶液浸渍法。
通常采用辊筒卷绕方法生产。
织物状态、胶液浓度、卷绕速度和卷绕张力对预浸料的含胶量有重要影响.烘干温度和卷绕速度对预浸料的挥发份和预固化度有重要影响.该工艺浸渍渗透性好.但固化后产品致密性差.空隙率高,力学性能偏低,生产成本高,环境污染严重。
2.热熔浸渍法.
热熔浸渍也称树脂膜浸渍,其主要优点:纤维排纱平直均匀,含胶最、带宽、带厚均能精确控制。
热压浸演。
浸渍效果好,纱束之间无间隙.有利于降低制品的空隙率:无溶剂挥发,劳动环境好等.热熔浸渍是在专用热熔浸渍机上进行。
机器开动后,牵引辊牵引上下隔离纸与连续纤维同步移动.此时被加热到熔融状态的树脂通过涂膜辊均匀涂覆到上下隔离纸相对应的单面上,上下隔离纸上的胶膜将纤维夹在中间.通过加压辊将熔融树脂压浸到纤维中间,经过冷却,最后将上下隔离纸和预浸带分别收卷待用.预浸料的含胶量可通过调节刮胶辊与涂膜辊之间的间隙和调节温度、走纸速度来控制.
热压系统与成型模具
1.热压罐系统。
热压罐系统是根据复合材料成型工艺条件设计的。
通常由如下分系统组成:压力容器;加热及气体循环系统;气体加压系统;真空系统。
控制系统;冷却系统和装卸系统组成。
2.成型模具,
热压罐成型模具要求模具材料在制品成型沮度和压力下能保持适当性能,同时还要考虑到棋具成本、寿命、梢度、强度、质最、机械加工性、热胀系数、尺寸德定性、表面处理及导热系数等。
模具的制造可选择铝、钢、镍合金、电沉积镶和碳/环氧复合材料等。
热压罐成型工艺模拟
在热压罐成型工艺过程中,将发生以下主要物理、化学变化:①树脂在纤维中流动,以促使树脂充分浸透纤维;②纤维增强网络压实,以保证复合材料构件中纤维体积分数最大化;
③合适的固化压力,以抑制树脂基体中孔隙的形成;④合适的固化温度周期。
以确保树脂充分固化。
所有这些物理化学过程,均可以通过建立树脂流动模型、纤维形变模型、纤维庆实模型、孔隙形成模型、热传递模型等进行工艺
模拟,并把这些模型统一集成到固化工艺优化的软件系统中。
热压罐成型技术可用来制作军机的主承力构件,如机身、抓盒、方向舵、升降舵、垂尾、平尾等。
在卫星和运载火箭上也有广泛用途。