安全带固定点CAE分析
浅析汽车座椅安全带固定点出口认证检测
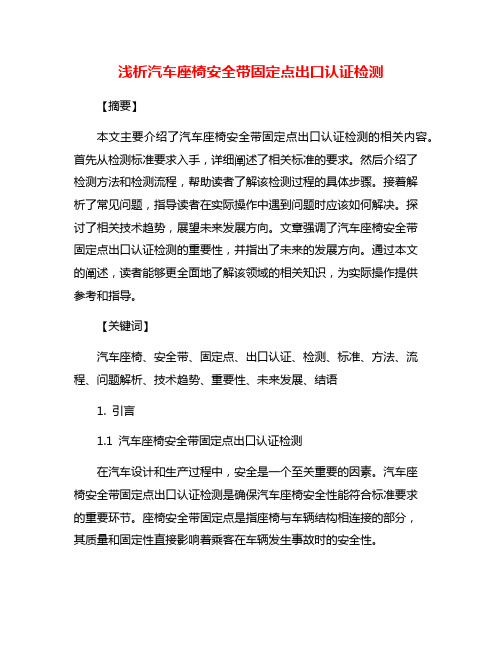
浅析汽车座椅安全带固定点出口认证检测【摘要】本文主要介绍了汽车座椅安全带固定点出口认证检测的相关内容。
首先从检测标准要求入手,详细阐述了相关标准的要求。
然后介绍了检测方法和检测流程,帮助读者了解该检测过程的具体步骤。
接着解析了常见问题,指导读者在实际操作中遇到问题时应该如何解决。
探讨了相关技术趋势,展望未来发展方向。
文章强调了汽车座椅安全带固定点出口认证检测的重要性,并指出了未来的发展方向。
通过本文的阐述,读者能够更全面地了解该领域的相关知识,为实际操作提供参考和指导。
【关键词】汽车座椅、安全带、固定点、出口认证、检测、标准、方法、流程、问题解析、技术趋势、重要性、未来发展、结语1. 引言1.1 汽车座椅安全带固定点出口认证检测在汽车设计和生产过程中,安全是一个至关重要的因素。
汽车座椅安全带固定点出口认证检测是确保汽车座椅安全性能符合标准要求的重要环节。
座椅安全带固定点是指座椅与车辆结构相连接的部分,其质量和固定性直接影响着乘客在车辆发生事故时的安全性。
汽车座椅安全带固定点出口认证检测通过对座椅安全带固定点的结构、材料、连接方式等方面进行检测和评估,以确保其符合相关的国家和行业标准。
这项检测工作对于保障乘客乘坐汽车时的安全具有重要意义,也是汽车生产企业必须严格执行的标准之一。
随着汽车产业的不断发展和技术的日益更新换代,汽车座椅安全带固定点出口认证检测也在不断完善和提升。
各国相关机构和汽车行业组织也在积极探索更先进的检测方法和技术,以确保汽车座椅安全性能达到更高的标准。
只有不断加强座椅安全带固定点出口认证检测工作,才能更好地保障乘客的安全,促进汽车行业的健康发展。
2. 正文2.1 检测标准要求在进行汽车座椅安全带固定点出口认证检测时,检测标准是至关重要的。
检测标准要求涵盖了各种不同方面的内容,以确保汽车座椅安全带固定点的质量和安全性达到国家标准。
检测标准要求对汽车座椅安全带固定点的设计和材料进行严格要求。
驾驶员座椅安全带固定点强度分析报告

安全带锚固点坐标
X
Y
1517.6
-597.3
1459.4
-624.8计位置
Z 993.9
59 216.5
变形图(动画)
变形图(动画)
变形图(动画)
变形图(动画)
变形图(动画)
变形图(动画)
变形图(动画)
变形图(动画)
变形图(动画)
120%加载力保持阶段(时间从 0.16s-0.22s), 三条链的位移曲线基本保持水平,这说明座椅 不再变形,座椅能承受120%加载力。
应力/应变图_左前连杆支架(厚度4.0mm)
材料: S550MC 屈服强度:551.4MPa 极限应力:690MPa 极限应变:13.6%
应力/应变图_左前连杆支架(厚度4.0mm)
材料: S550MC 屈服强度:551.4MPa 极限应力:690MPa 极限应变:13.6%
应力/应变图_左后连杆齿支架(厚度4.0mm)
材料: 16MnCr5 屈服强度:1187MPa 极限应力:1373MPa 极限应变:10.0%
应力/应变图_右前连杆支架(厚度 2.5mm)
材料: ZSTE420 屈服强度:420MPa 极限应力:556.8MPa 极限应变:14.8%
应力/应变图_左前连杆支架(厚度 2.5mm)
材料: QSTE460 屈服强度:460MPa 极限应力:592.8MPa 极限应变:13.1%
材料: QSTE460 屈服强度:460MPa 极限应力:592.8MPa 极限应变:13.1%
应力/应变图_右内滑轨(厚度 1.8mm)
内滑轨存在拉断的风险!
材料: S650MC 屈服强度:650MPa 极限应力:700MPa 极限应变:10.0%
汽车座椅安全带固定点强度分析
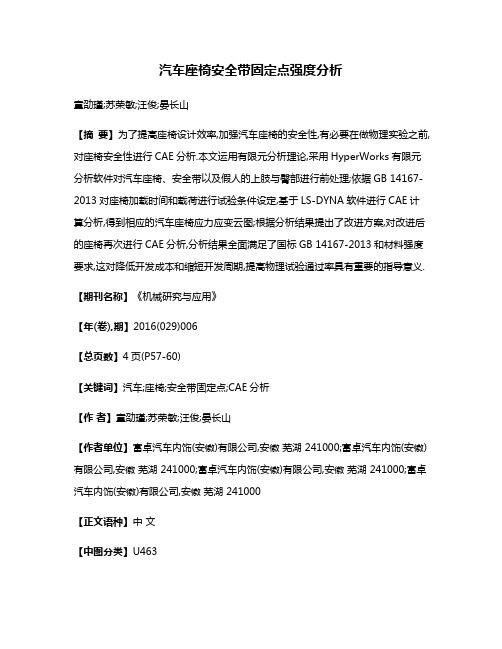
汽车座椅安全带固定点强度分析童劭瑾;苏荣敏;汪俊;晏长山【摘要】为了提高座椅设计效率,加强汽车座椅的安全性,有必要在做物理实验之前,对座椅安全性进行CAE分析.本文运用有限元分析理论,采用HyperWorks有限元分析软件对汽车座椅、安全带以及假人的上肢与臀部进行前处理;依据GB 14167-2013对座椅加载时间和载荷进行试验条件设定,基于LS-DYNA软件进行CAE计算分析,得到相应的汽车座椅应力应变云图;根据分析结果提出了改进方案,对改进后的座椅再次进行CAE分析,分析结果全面满足了国标GB 14167-2013和材料强度要求,这对降低开发成本和缩短开发周期,提高物理试验通过率具有重要的指导意义.【期刊名称】《机械研究与应用》【年(卷),期】2016(029)006【总页数】4页(P57-60)【关键词】汽车;座椅;安全带固定点;CAE分析【作者】童劭瑾;苏荣敏;汪俊;晏长山【作者单位】富卓汽车内饰(安徽)有限公司,安徽芜湖 241000;富卓汽车内饰(安徽)有限公司,安徽芜湖 241000;富卓汽车内饰(安徽)有限公司,安徽芜湖 241000;富卓汽车内饰(安徽)有限公司,安徽芜湖 241000【正文语种】中文【中图分类】U463汽车座椅不仅为乘员提供乘车的舒适性,当汽车发生碰撞时座椅还起着保护乘员生命的作用,汽车安全带固定点的强度是汽车安全性法规中的一个重要指标,是车辆《公告》实验的强制性检测的指标。
在碰撞事故中,安全带固定点周围区域的撕裂或断裂,都是造成人员伤亡的主要原因。
GB 14167-2013《汽车安全带固定点、ISOFIX固定点系统及上拉带固定点》标准要求在规定的时间内承受实验要求的载荷情况下,安全带固定点的强度必须要保证安全带不得脱落,但允许固定点或周围区域有永久变形,包括部分断裂或产生裂纹[1]。
为使座椅在整车碰撞过程中起到较好的保护乘员的作用,很多座椅企业都提出高于目前座椅法规的产品性能要求。
安全带固定点强度CAE分析ppt课件

q 分析结果 (Analysis Results)
四个地脚的应力应变图: Stress and Strain Plot for RH Front Foot
真实屈服应力 Yield Strength
真实极限应力 True UTS
真实极限塑性应变 True Plastic Strain
550MPa 760MPa
火灾袭来时要迅速疏散逃生,不可蜂 拥而出 或留恋 财物, 要当机 立断, 披上浸 湿的衣 服或裹 上湿毛 毯、湿 被褥勇 敢地冲 出去
Platform Model Year
Status TG0
Report No.
Version 01
中排座椅安全带固定点强度CAE分析
Middle Safety-Belt Anchorage Strength Analysis Report
q 分析结果 (Analysis Results)
右侧上滑轨的应力应变图: Stress and Strain Plot for RH Upper Track
真实屈服应力 Yield Strength
真实极限应力 True UTS
真实极限塑性应变 True Plastic Strain
550MPa 760MPa
0.15
结果应力应变值 Results
零件最大应力 Max. stress in component 620.9MPa
零件最大应变 Max过屈服应力,最大应变没有超过极限值,零件没有损坏的风险。 Max Stress exceeding SIGY, Effective plastic strain not exceeding the ultimate value throughout the thickness. No risk.
汽车安全带固定点失效分析及结构优化
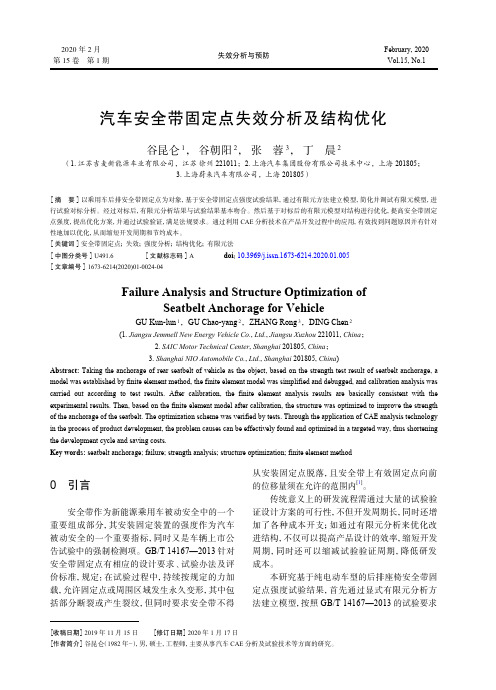
汽车安全带固定点失效分析及结构优化谷昆仑 1, 谷朝阳 2, 张 蓉 3, 丁 晨 2(1. 江苏吉麦新能源车业有限公司,江苏 徐州 221011;2. 上海汽车集团股份有限公司技术中心,上海 201805;3. 上海蔚来汽车有限公司,上海 201805)[摘 要]以乘用车后排安全带固定点为对象,基于安全带固定点强度试验结果,通过有限元方法建立模型,简化并调试有限元模型,进行试验对标分析。
经过对标后,有限元分析结果与试验结果基本吻合。
然后基于对标后的有限元模型对结构进行优化,提高安全带固定点强度,提出优化方案,并通过试验验证,满足法规要求。
通过利用CAE 分析技术在产品开发过程中的应用,有效找到问题原因并有针对性地加以优化,从而缩短开发周期和节约成本。
[关键词]安全带固定点; 失效; 强度分析; 结构优化; 有限元法[中图分类号] U491.6 [文献标志码] A doi :10.3969/j.issn.1673-6214.2020.01.005[文章编号] 1673-6214(2020)01-0024-04Failure Analysis and Structure Optimization ofSeatbelt Anchorage for VehicleGU Kun-lun 1,GU Chao-yang 2,ZHANG Rong 3,DING Chen 2(1. Jiangsu Jemmell New Energy Vehicle Co., Ltd., Jiangsu Xuzhou 221011, China ;2. SAIC Motor Technical Center , Shanghai 201805, China ;3. Shanghai NIO Automobile Co., Ltd., Shanghai 201805, China )Abstract: Taking the anchorage of rear seatbelt of vehicle as the object, based on the strength test result of seatbelt anchorage, a model was established by finite element method, the finite element model was simplified and debugged, and calibration analysis was carried out according to test results. After calibration, the finite element analysis results are basically consistent with the experimental results. Then, based on the finite element model after calibration, the structure was optimized to improve the strength of the anchorage of the seatbelt. The optimization scheme was verified by tests. Through the application of CAE analysis technology in the process of product development, the problem causes can be effectively found and optimized in a targeted way, thus shortening the development cycle and saving costs.Key words: seatbelt anchorage; failure; strength analysis; structure optimization; finite element method0 引言安全带作为新能源乘用车被动安全中的一个重要组成部分,其安装固定装置的强度作为汽车被动安全的一个重要指标,同时又是车辆上市公告试验中的强制检测项。
汽车座椅安全带固定点强度分析

汽车座椅安全带固定点强度分析摘要:汽车座椅靠背有支撑乘员背部的作用,在舒适性评价中有很高的占比,由于靠背远离固定点,且靠背与固定点之间存在多个调节机构,如高调四连杆、靠背调角器、水平调节滑轨等,导致靠背受到震动易产生晃动,对于不同座椅,产生晃动的震动波形也不同。
针对靠背晃动问题综合考虑可行性、工艺性及成本等因素,选取高调四连杆作为研究对象,解决该问题,并提供一种该问题的解决思路。
关键词:汽车座椅;安全带;固定点;强度分析引言汽车座椅是汽车安全件的重要组成部分之一,它不仅可以给乘员提供支撑,还具有保护乘员避免或减少伤害的作用。
汽车座椅安全带固定点试验是车辆《公告》强制性试验项目。
在车辆发生碰撞事故时,如果安全带固定点强度不满足法规要求,则安全带固定点周围区域的撕裂或断裂是会造成人员伤亡。
为使座椅在整车碰撞过程中起到更好的保护作用,许多座椅企业会设计高于法规标准要求的性能产品。
一、汽车座椅概述乘坐汽车的舒适性分静态和动态两个场景。
静态舒适性主要取决于座椅的设计是否符合“人体工程学”。
简单来说,运用“人体工程学”提升座椅的舒适性可以总结为三个要点:座椅设计参考人体测量学数据;座椅具有可调节性,满足不同体型人群需求;座椅的位置与空间相协调。
此外,座椅不宜过软,过软的座椅不仅会对尾椎造成过大压力,导致损伤脊椎健康,还会压迫腿部,不利于血液循环。
以荣获J.D.Power2021大型MPV座椅质量第一的广汽传祺M8的座椅为例,安道拓基于人体工程学设计了高度贴合人体的座椅造型,使得人体与座椅之间的接触面积最大化,并采用多密度多硬度的泡沫给予乘坐者最有力的支撑。
同样在各系细分市场摘得座椅质量冠亚军的福特福克斯和小鹏G3i的座椅亦是如此。
安道拓不仅使得座椅兼具包裹性和支撑性,同时还配备电动腰托,使得不同身形的人群都能调节到最适合自己的支撑点。
蔚来赫赫有名的“女王副驾”同样来自安道拓。
“女王副驾”的座椅配备腿托和脚托,可以说是从上到下都提供舒适的包裹性。
汽车座椅安全带固定点强度分析

t o c k s o f d u mmy .A c c o r d i n g t o t h e GB 1 4 1 6 7 — 2 01 3, t h e t e s t c o n d i t i o n s o f t h e 1 o a d i n g t i me a n d l o a d o f t h e s e a t a r e s e t ,a n d t h e
・
机械研究与应用 ・2 0 1 6 年 第6 期( 第2 9 卷, 总
d o i : 1 0 . 1 6 5 7 6 / j . c n k i . 1 0 0 7 - 4 4 1 4 . 2 0 1 6 . 0 6 . 0 1 8
汽 车 座 椅 安 全 带 固定 点 强 度 分 析
—
DYNA s o f t w a r e .T h e a n a l y s i s r e s u l t s a r e u s e d t o p u t f o r w rd a t h e i mp r o v e me n t s c h e me,a n d C AE a n a l y s i s o f t h e i mp r o v e d
CA E a n a l y s i s o f t h e s e a t s fe a t y b e f o r e t h e p h y s i c a l e x p e r i me n t o f t h e c a r .Ba s e d o n t h e i f n i t e e l e me n t a n a l y s i s t h e o y ,t r h e i f n i t e
关于汽车安全带的固定点强度分析

关于汽车安全带的固定点强度分析摘要:为了进行汽车安全带固定点强度分析,运用有限元分析软件Hypermesh建立白车身、座椅、安全带、人体模块有限元模型。
采用LS-DYNA的显式积分法进行求解,按照国家标准设置规定的载荷,分析结构通过标准的可能性。
验证了运用有限元显式积分分析汽车安全带固定点强度的方法。
关键词:汽车;安全带;固定点;强度引言GB14167-2013《汽车安全带固定点、ISOFIX固定点系统及上拉带固定点》规定中要求,在规定的时间内承受试验要求的载荷情况下,安全带固定点的强度必须要保证安全带不会出现脱落的情况,但允许固定点或者周围区域产生永久变形或者裂纹,且规定安全带上固定点在受力方向的位移不得超过一定的范围。
本文基于此,以国内某车型为例,对安全带固定点的强度进行CAE分析,期望这些分析总结能为汽车车身正向开发提供参考依据。
1 安全带固定点实体模型安全带固定点强度分析的第一步是建立合理的几何模型,表面上理解似乎建立与此相应的整车结构模型要好一些,但不尽然.本研究中基于:①模型复杂、工作量大(计算机时、建模)、周期长;②边界、载荷考虑因素多反倒不利于分析等,采用局部结构几何模型对微型货车安全带固定点强度进行了优化设计分析,大大减轻了建模和计算的工作量。
在考虑与安全带固定点强度相关的驾驶室有关部件和结构之后,用CAD软件UG (Unigraphic)建立了分析腰带固定点强度的几何模型。
其中:驾驶室后围-横梁几何模型由后围、上横梁板、下横梁板以及上、下横梁之间的加强板4个部件所组成.这些部件之间都是以焊接的方式相连接的。
2 有限元模型的建立想要对安全带固定点强度进行分析,首先要创建合理的有限元模型。
由于考虑到整车结构太大,计算机的配置有限,在仿真的过程中应适当的减小分析模型。
白车身的有限元模型采用壳单元建立,与座椅模型、安全带系统组件、上下人体模块进行装配,白车身模型不带挡风玻璃和侧围玻璃。
CATIA设计汽车安全带锚固点强度分析设置方法4

2维/1维安全带 安全带与block 之间间隙
安全带宽度
网格密度
绕安全带
选择shoulder上的单元(安全 带接触面)点击orient.,在肩 部出现3条线段。点击线段, 将其激活,此时可以拖动。分 别调整这三条线段以使安全带 处于合适的位置。
绕安全带
点击mesh即可生成即可生成安全带网格。
绕安全带
连接的设置及整理
1. 连接的设置 2. 连接的检查和整理
模型细化 Shoulder block 和 Lap block 的摆放 绕安全带 安全带与车身的连接 接触设置 约束添加 加载 基本control card设置
2
4-6 7-11
11 12-15 16-19 20-21 22-29 30-32 33-36 37 38-41 42-43
*注意以上接触都要选择 automatic 类型
接触设置
计算过程中越多的接触会使得收敛困难(implicit),增加计算时间。在定义座椅和车身 自身接触时远离地脚受力的区域和远离大变形可能发生的区域可以不定义接触。
设置接触后,零件之间会有可能发生接触的穿透(penetration)。 可以通过Penetration Check的工具,调整这些穿透。
建立加载曲线,通过Post— xy plots— edit curves
将加载曲线赋给load
选择要定 义的载荷
加载
这里选择先前定义好的载荷曲 线曲线。
基本control card 设置
(1)计算时间根据需要设定
(2)计算步长设定,步长的大小可以根据计算过程中的附加质量来调整。(added mass)
基本分析模型准备
下面是这个分析的几个主要受力位置,截面边界需要离这几个位置远些。
某车型安全带固定点分析及优化

某车型安全带固定点分析及优化Wei Rui;Yuan Hailong【摘要】安全带是汽车安全零部件中重要的零部件之一,国家出台了相关的法律法规对汽车的安全作出明确规定,在试验载荷情况下,安全带固定点的强度必须保证安全带不得从安装固定点处脱落.文章借助于有限元分析软件对安全带固定点强度展开分析和优化,对约束的定义、加载函数的选取、模型建立等进行简要阐述,最后,将仿真结果与实际试验结果进行对比分析,说明仿真计算具有较好的精度,能够满足工程的实际运用.【期刊名称】《汽车实用技术》【年(卷),期】2018(000)023【总页数】3页(P213-215)【关键词】安全带;固定点强度;仿真分析【作者】Wei Rui;Yuan Hailong【作者单位】;【正文语种】中文【中图分类】U462引言汽车的安全性是汽车一项重要的使用性能[1],汽车的安全问题也是当今重要的研究领域之一。
为此,国家也出台了相关的法律法规对汽车的安全作出明确规定,并将汽车部分安全性能列为强制检测的法规项。
其中,安全带作为汽车被动安全的一个重要组成部分,其安全带固定点强度设计必须满足法规要求。
本文以某车型作为研究对象,借助于有限元的方法对某车型的安全带固定点强度进行分析,合理的建立模型、边界的处理、切合实际的对比分析,优化和改进结构,得到较好的效果。
同时将仿真与试验进行对比,得出仿真计算可以得到较好的精度,并且满足工程实际应用的要求。
1 分析模型的建立合理的建立有限元模型对于分析来说至关重要,不但可以减少模型求解对计算资源的需求,减少计算时间,而且可以提高工作效率。
故采用显式计算方法[2]和部分车身模型简化建模的方法来建立安全带固定点强度计算模型,从而大大的降低了建模和计算所需要的时间。
同时借助于有限元分析前处理软件 Hypermesh和Primer建立某车型双人座椅的安全带固定点强度仿真模型。
1.1 模型的建立某车型的白车身有限元模型采用壳单元建立,模型约有39万个单元,40万个节点。
某车型安全带固定点强度对标分析及优化

依据 GB14167—2013要求的试验工况,沿着规定
前提下,尽可能地缩短建模和求解计算的时间。
考虑到整车模型较大,截取白车身部分模型,通过
[2-3]
前处理软件搭建有限元模型 ;有限元模型的零部件
的方向,在模型中对上、下人体模块加载 13.5kN的载 荷,载荷的方向为沿平行于汽车行驶方向(-)且与水 平面( 平面)成 10角的方向;同时对座椅施加相当
安全带作为新能源乘用车被动安全中的一个重要 提高产品设计效率,缩减试验验证周期,降低研发成本
组成部分,其安装固定装置的强度是汽车被动安全的 等。文章基于有限元建模方法建立安全带固定点强度
一个重要指标,同时又是车辆上市公告试验中的强制 分析模型,通过调试模型对标试验,最后通过结构优化
检测项。国家法规标准 GB14167—2013针对安全带固 满足法规要求,并经过试验验证达到了预期效果。
2020(2)
20技20术年聚2焦月
设计·创新
某车型安全带固定点强度 对标分析及优化
1
2
3
谷昆仑 谷朝阳 张蓉
(1.江苏吉麦新能源车业有限公司;2.上海汽车集团股份有限公司技术中心;
3.上海蔚来汽车有限公司)
摘要:为了更加高效地解决某新能源乘用车安全带固定点在实际试验过程中失效的问题,该文基于安全带固定点强度试验
定点有相应的设计要求、试验办法及评价标准。法规规 ! 试验结果分析
定:在试验过程中,持续按规定的力加载,允许固定点
在进行安全带固定点强度试验过程中,发现某车型
或周围区域发生永久变形,其中包括部分断裂或产生 前排安全带上固定点有脱落、开裂现象。经讨论分析,总
裂纹,但同时要求安全带不得从安装固定点脱落,且安 结出固定点失效的主要原因有:1)由于安全带上固定点
安全带固定点强度CAE分析

5184 15321 -599 9027
854 7450 7995
124352 -44523 -7127 -50583 17589 -45269 -24166
分析结果 (Analysis Results)
关键区域螺栓力(Bolt Force):
174190
174191
174172 174173
174171 174189
分析结果 (Analysis Results)
右侧下滑轨的应力应变图: Stress and Strain Plot for RH Lower Track
真实屈服应力 Yield Strength
真实极限应力 True UTS
真实极限塑性应变 True Plastic Strain
550MPa 760MPa
分析目的(Purpose)
考察安装带固定点强度分析性能(To Assess Middle Safety-Belt Strength)
分析工况(Load Case)
基础模型的中排座椅安全带固定点强度分析(Middle Safety-Belt Strength Analysis for Base Model)
CAE 分析结果总结 (CAE Results Summary)
中排座椅安全带固定点强度能满足目标要求。
谢谢!
分析结果 (Analysis Results)
四个地脚的应力应变图: Stress and Strain Plot for RH Front Foot
真实屈服应力 Yield Strength
真实极限应力 True UTS
真实极限塑性应变 True Plastic Strain
550MPa 760MPa
中排座椅安全带固定点强度分析
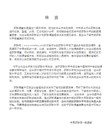
图1:安全带固定点有限元模型图
3
中排座椅安全带固定点强度分析
2、安全带固定点强度边界条件
GB14167安全带固定点强度法规规定,法规要求利用模拟织带的装置,对连接到固定点上的上 人体模块施加一个与X轴成15°的13500N的载荷。与此同时,对连接到固定点上的下人体模块 施加一个与X轴成15°的13500N的载荷。给座椅总成质量20倍的力。以尽可能快的速度加载值 规定值,并至少持续0.2s(其中红色代表约束位置,约束自由度123456)
图2:安全带固定点强度边界条件图
4
中排座椅安全带固定点强度分析
3、安全带固定点强度分析结果
安全带固定点应力云图
5
中排座椅安全带固定点强度分析
3、安全带固定点强度分析结果
C柱内板安装点处最大塑性应变0.066 小于材料DC03最大塑性应变0.300
安全带地板安装孔最大塑性应变0.168 小于材料DC04最大塑性应变0.295
6
中排座椅安全带固定点强度分析
4、结论
综上,安全带安装点各部件最大拉伸应变率均小于材料断裂拉伸率,满足设计要求。
7
中排座椅安全带固定点强度分析
8
安全带固定点强度边界条件图5中排座椅安全带固定点强度分析33安全带固定点强度分析结果安全带固定点应力云图6中排座椅安全带固定点强度分析33安全带固定点强度分析结果c柱内板安装点处最大塑性应变0066小于材料dc03最大塑性应变0300安全带地板安装孔最大塑性应变0168小于材料dc04最大塑性应变02957中排座椅安全带固定点强度分析44结论综上安全带安装点各部件最大拉伸应变率均小于材料断裂拉伸率满足设计要求
4、结论--------------------------------------------------7
某车型安全带固定点强度分析及结构优化

Reports汽车工业研究·季刊2020年第3期某车型安全带固定点强度分析及结构优化▶◀……………………………………………………………………………谷昆仑郝朝利程啸引言随着我国汽车行业设计制造水平和大众消费水平的不断提高,人们对整车被动安全性能的要求越来越高。
安全带是汽车被动安全中的一个重要组成部分,其安装固定点的强度既是被动安全的一个关键指标,同时又是车辆公告试验强制检查项目。
GB14167-2013针对安全带固定点有专门的具体的设计要求、试验方法和评价标准。
法规要求:在规定的时间内,持续按规定的力加载,允许固定点或周围区域有永久变形,包括部分断裂或产生裂纹,安全带不得从安装固定点脱落,并且上部有效固定点向前位移不得超过允许的范围[1]。
传统的开发流程通过大量的试验反向验证设计的正确性,不仅开发周期长,还增加了设计成本;通过仿真分析来改进结构,可以提高产品设计效率,缩短开发周期,减少试验次数,降低设计成本。
本文基于公司自主研发的某款乘用车后排座椅安全带固定点,使用显式有限元分析方法,按照GB14167-2013的试验要求加载,对安全带固定点强度进行CAE分析,为结构设计及优化提供依据。
有限元模型基于三维软件CATIA 完成汽车后排座椅、安全带、假人上肢和臀部的几何建模,截取白车身部分模型,通过前处理软件搭建有限元模型[2,3];有限元模型的零部件主要网格尺寸的大小为5mm ,同时为了提高CAE 分析的精度,对安全带固定点的关键受力区域的网格进行细化,并使用全积分单元;对白车身相关的钣金件采用shell 单元建立白车身有限元模型,焊点采用MAT100材料的HEXA 单元进行模拟,安全带固定点处的螺栓采用实体单元模拟,其余处的螺栓采用Rigid 单元进行模拟。
根据各组件之间的实际接触情况,在仿真模型里定义相应的图1后排安全带固定点强度有限元模型35Reports汽车工业研究·季刊2020年第3期接触关系,包括板件之间的自接触、焊点与板件间的绑定、人体模块与安全带、螺栓与板件之间的面面接触等[4,5]。
汽车座椅安全带固定点强度分析及骨架轻量化设计
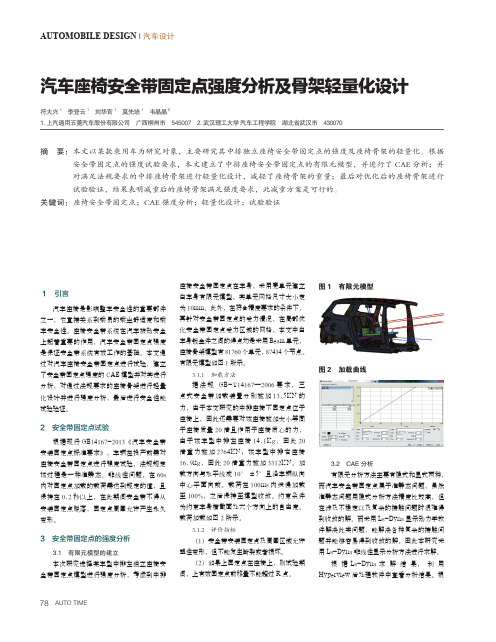
图 5 主驾座椅左后脚应变 图 6 副驾座椅上固定点应变
图 3 主驾安全带上固定点应变
AUTOMOBILE DESIGN | 汽车设计
时代汽车
脚 处 的 强 度, 座 椅 左 后 安 装 脚 处 的 材 料 由 SCM435 改 为 QSTE420, 厚 度 由 2.5mm 改 为 3.0mm,如图 9 所示。对改进后的模型重 新进行安全带固定点的强度分析,如图 10 所 示,计算应变 0.046,而抗拉应变为 0.2,故 安全带固定点的强度满足要求。 图 9 改进模型
AUTOMOBILE DESIGN | 汽车设计
汽车座椅安全带固定点强度分析及骨架轻量化设计
符大兴 1 李登云 1 刘华官 1 莫先培 1 韦晶晶2 1. 上汽通用五菱汽车股份有限公司 广西柳州市 545007 2. 武汉理工大学 汽车工程学院 湖北省武汉市 430070
摘 要:本文以某款乘用车为研究对象,主要研究其中排独立座椅安全带固定点的强度及座椅骨架的轻量化。根据 安全带固定点的强度试验要求,本文建立了中排座椅安全带固定点的有限元模型,并进行了 CAE 分析;并 对满足法规要求的中排座椅骨架进行轻量化设计,减轻了座椅骨架的重量;最后对优化后的座椅骨架进行 试验验证,结果表明减重后的座椅骨架满足强度要求,此减重方案是可行的。
3 安全带固定点的强度分析
3.1 有限元模型的建立 本次研究选择某车型中排左独立座椅安 全带固定点模型进行强度分析,考虑到中排
座椅安全带固定点在车身,采用壳单元建立 白车身有限元模型,其单元网格尺寸大小定 为 10mm。此外,在符合精度要求的条件下, 再针对安全带固定点的受力情况,在局部优 化安全带固定点受力区域的网格,本文中白 车身钣金件之间的焊点均是采用 Beam 单元, 座椅骨架模型有 81760 个单元,87434 个节点。 有限元模型如图 1 所示。
基于后排乘员胸压的安全带固定点位置分析
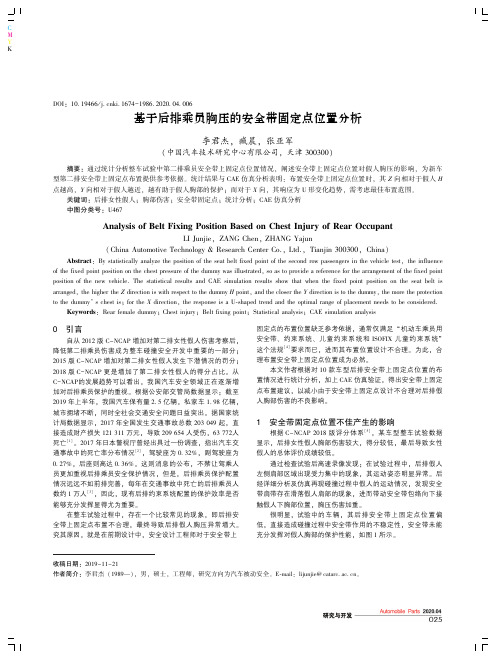
收稿日期:2019-11-21作者简介:李君杰(1989 ),男,硕士,工程师,研究方向为汽车被动安全㊂E⁃mail:lijunjie@catarc ac cn㊂DOI:10 19466/j cnki 1674-1986 2020 04 006基于后排乘员胸压的安全带固定点位置分析李君杰,臧晨,张亚军(中国汽车技术研究中心有限公司,天津300300)摘要:通过统计分析整车试验中第二排乘员安全带上固定点位置情况,阐述安全带上固定点位置对假人胸压的影响,为新车型第二排安全带上固定点布置提供参考依据㊂统计结果与CAE仿真分析表明:布置安全带上固定点位置时,其Z向相对于假人H点越高,Y向相对于假人越近,越有助于假人胸部的保护;而对于X向,其响应为U形变化趋势,需考虑最佳布置范围㊂关键词:后排女性假人;胸部伤害;安全带固定点;统计分析;CAE仿真分析中图分类号:U467AnalysisofBeltFixingPositionBasedonChestInjuryofRearOccupantLIJunjie,ZANGChen,ZHANGYajun(ChinaAutomotiveTechnology&ResearchCenterCo.,Ltd.,Tianjin300300,China)Abstract:Bystatisticallyanalyzethepositionoftheseatbeltfixedpointofthesecondrowpassengersinthevehicletest,theinfluenceofthefixedpointpositiononthechestpressureofthedummywasillustrated,soastoprovideareferenceforthearrangementofthefixedpointpositionofthenewvehicle.ThestatisticalresultsandCAEsimulationresultsshowthatwhenthefixedpointpositionontheseatbeltisarranged,thehighertheZdirectioniswithrespecttothedummyHpoint,andtheclosertheYdirectionistothedummy,themoretheprotectiontothedummy schestis;fortheXdirection,theresponseisaU⁃shapedtrendandtheoptimalrangeofplacementneedstobeconsidered.Keywords:Rearfemaledummy;Chestinjury;Beltfixingpoint;Statisticalanalysis;CAEsimulationanalysis0㊀引言自从2012版C-NCAP增加对第二排女性假人伤害考察后,降低第二排乘员伤害成为整车碰撞安全开发中重要的一部分;2015版C-NCAP增加对第二排女性假人发生下潜情况的罚分;2018版C-NCAP更是增加了第二排女性假人的得分占比㊂从C-NCAP的发展趋势可以看出,我国汽车安全领域正在逐渐增加对后排乘员保护的重视㊂根据公安部交管局数据显示:截至2019年上半年,我国汽车保有量2 5亿辆,私家车1 98亿辆,城市拥堵不断,同时全社会交通安全问题日益突出㊂据国家统计局数据显示,2017年全国发生交通事故总数203049起,直接造成财产损失121311万元,导致209654人受伤,63772人死亡[1]㊂2017年日本警视厅曾经出具过一份调查,指出汽车交通事故中的死亡率分布情况[2],驾驶座为0 32%,副驾驶座为0 27%,后座则高达0 36%㊂这则消息的公布,不禁让驾乘人员更加重视后排乘员安全保护情况,但是,后排乘员保护配置情况远远不如前排完善,每年在交通事故中死亡的后排乘员人数约1万人[3],因此,现有后排约束系统配置的保护效率是否能够充分发挥显得尤为重要㊂在整车试验过程中,存在一个比较常见的现象,即后排安全带上固定点布置不合理,最终导致后排假人胸压异常增大㊂究其原因,就是在前期设计中,安全设计工程师对于安全带上固定点的布置位置缺乏参考依据,通常仅满足 机动车乘员用安全带㊁约束系统㊁儿童约束系统和ISOFIX儿童约束系统 这个法规[4]要求而已,进而其布置位置设计不合理㊂为此,合理布置安全带上固定点位置成为必然㊂本文作者根据对10款车型后排安全带上固定点位置的布置情况进行统计分析,加上CAE仿真验证,得出安全带上固定点布置建议,以减小由于安全带上固定点设计不合理对后排假人胸部伤害的不良影响㊂1㊀安全带固定点位置不佳产生的影响根据C-NCAP2018版评分体系[5],某车型整车试验数据显示,后排女性假人胸部伤害较大,得分较低,最后导致女性假人的总体评价成绩较低㊂通过检查试验后高速录像发现:在试验过程中,后排假人左侧肩部区域出现受力集中的现象,其运动姿态明显异常㊂后经详细分析及仿真再现碰撞过程中假人的运动情况,发现安全带肩带存在滑落假人肩部的现象,进而带动安全带包络向下接触假人下胸部位置,胸压伤害加重㊂很明显,试验中的车辆,其后排安全带上固定点位置偏低,直接造成碰撞过程中安全带作用的不稳定性,安全带未能充分发挥对假人胸部的保护性能,如图1所示㊂图1㊀安全带上固定点位置偏低的影响示意2 安全带上固定点布置位置统计分析2 1㊀实车安全带上固定点位置布置统计本文作者对10款不同型号的车型安全带上固定点位置进行统计,因涉及不同车型,为方便对比分析,目标值采用安全带上固定点坐标与后排女性假人理论H点坐标的差值进行对比分析,如表1所示㊂表1㊀安全带上固定点与后排假人理论H点的差值mm车型编号ΔxΔyΔz车型1405247693车型2341.212307.54568.134车型3301.454259.33650.254车型4766.02163.173576.645车型5475.203225.431527.597车型6362243524车型7292.88272.32602.36101车型8284.76289.185612.598车型9441189537车型10354178499.52 2㊀安全带上固定点不同坐标下伤害值变化根据安全带上固定点3个不同方向的坐标值,对比实车碰撞结果中后排女性假人胸部伤害及得分情况㊂首先,根据Z方向的坐标情况,进行对比分析,如表2所示㊂表2㊀安全带上固定点Z方向差值对应后排假人胸部伤害情况车型编号Δz/mm胸部压缩量/mm得分652446.690.15527.59742.660.42456034.81.062568.13434.851.0547602.3610134.11.128612.598281.63650.25424.781.86169326.751.7953718.11210499.528.7581.54㊀㊀根据安全带上固定点与后排女性假人H点Z方向的差值,对车型1 车型8进行排序(固定点位于C柱上,Z向位移差由小到大),得出伤害值的变化规律㊂不难发现:随着安全带上固定点位置的提高,后排女性假人胸部压缩量有明显减小的变化趋势,相应得分提高,呈线性变化关系㊂车型9和车型10第二排安全带上固定点位于座椅靠背上,所以Z向差值较小,但二者的变化,依然遵循上述规律㊂文献[6]中指出:安全带D环偏下㊁偏后导致安全带对假人胸部的约束偏强,对假人腰部的约束偏弱,假人胸部刚度偏低㊂这与表2中车型1 车型8的变化规律相对应㊂但随后文中又提出,D环位置布置在C柱上要好于布置在座椅靠背上[6]㊂通过观察试验车型9和车型10不难发现, D环位置布置在C柱上要好于布置在座椅靠背上 的结论存在一定的可推敲性,安全带固定点Y向距离是否影响后排女性假人胸部伤害,值得进一步分析㊂根据安全带上固定点与后排女性假人H点Y方向的差值,对车型1 车型10实车碰撞结果中后排女性假人胸部伤害及得分情况进行对比分析,如表3所示:随着安全带上固定点与后排女性假人H点Y方向的差值变化,假人胸部伤害不是明显的线性变化关系,但随Δy的增大,整个伤害趋势走向呈现逐渐上升的趋势,如图2所示㊂表3㊀安全带上固定点Y方向差值对应后排假人胸部伤害情况车型编号Δy/mm胸部压缩量/mm得分5225.43142.660.42624346.690.1124726.751.73259.3324.781.867272.3234.11.128289.185281.62307.5434.851.054422334.81.06918918.1121017828.7581.54图2㊀安全带上固定点Y方向变化对应胸部伤害变化车型9和车型10第二排安全带上固定点位于座椅靠背上;车型4后排安全带固定点位于C柱与后风窗横梁交点位置,介于C柱和座椅靠背的中间位置,车型4安全带固定点位置如图3所示㊂所以,无论第二排安全带固定点是布置在C柱上,还是布置在座椅靠背附近,均需要充分考虑安全带上固定点Y向距离,以减小因安全带布置因素对假人胸部伤害的不良影响㊂由于安全带上固定点位于座椅靠背附近时,其X向受到座椅靠背上边缘的限制,研究意义不大,所以对于Δx,文中只分析第二排安全带上固定点位于C柱的情况,如表4所示㊂图3㊀车型4安全带上固定点位置表4㊀安全带上固定点X方向差值对应后排假人胸部伤害情况车型编号Δx/mm胸部压缩量/mm得分8284.76281.67292.8834.11.123301.45424.781.862341.21234.851.054636246.690.1140526.751.75475.20342.660.42㊀㊀由表4可知:随着安全带上固定点与后排女性假人H点X方向差值的增大,假人胸部伤害无规律性变化,但胸压伤害值较小区域集中在Δx较小的区域内,这表明,当D环安装位置在C柱上时,第二排安全带固定点的位置偏向前方略好,但对于此无明显规律的情况,后续还需仿真手段辅助获取进一步的变化规律㊂3 后排安全带上固定点布置位置仿真验证分析为验证上述实车试验显示的规律,同时寻求第二排安全带固定点布置范围,故进行仿真验证,观察假人胸部伤害变化规律㊂仿真验证采用简化二阶梯形波加载整车模型进行验证㊂简化二阶梯形波如图4所示㊂Δx㊁Δy㊁Δz的调节范围参考女性假人H点距离肩部的尺寸,如图5所示㊂图4㊀简化二阶梯形波图5㊀H点距离肩部边缘的尺寸仿真验证矩阵见表5㊂表5㊀仿真验证矩阵mmZ向距离差Δz胸压Y向距离差Δy胸压X向距离差Δx胸压45031.8410023.1123033.0450029.1015024.9128031.0855025.8420026.2633028.7760026.2625027.1238027.1465024.1030028.8340026.6570022.7535037.6743026.3775021.6348026.6380019.6653028.0958029.97由表5可知:(1)随着第二排安全带固定点距假人H点Z方向距离的增大,第二排女性假人胸部压缩量呈现减小趋势,所以Δz越大越有利,但是需要考虑实车安装的可行性㊂结合实车安全带固定点布置情况,得出第二排安全带上固定点Z方向布置的参考范围为600 700mm㊂此范围适用于安全带上固定点位于C柱上的情况,不包含安全带上固定点位于座椅靠背上的情况;(2)随着第二排安全带固定点距假人H点Y方向距离的增大,第二排女性假人胸部压缩量呈现增大趋势,所以Δy越小越有利㊂结合实车安全带固定点布置情况,得出第二排安全带上固定点Y方向布置的参考范围为150 300mm;(3)随着第二排安全带固定点距假人H点X方向距离的增大,第二排女性假人胸部压缩量呈现先减小后增大趋势,其变化规律近似U形,存在最佳可选范围,非线性变化㊂即在一定范围内,呈现出安全带上固定点越靠前㊁越有利,比如430580mm这个区域;但是超过一定范围,随着安全带上固定点继续前移,胸压反而增大,这是因为,安全带固定点过度向前,肩带更容易滑落肩部,加大安全带对假人胸部的载荷,进而加重胸部伤害,比如230 400mm这个区域㊂综合考虑两段变化规律,得出第二排安全带上固定点X方向布置的参考范围为300 480mm㊂胸部压缩量曲线变化如图6 图9所示㊂图6㊀胸部压缩量响应Δz变化图7㊀胸部压缩量响应Δy变化图8㊀胸部压缩量响应Δx变化 情况1图9㊀胸部压缩量响应Δx变化 情况24㊀结论通过对实车第二排安全带上固定点的布置情况进行统计,以降低第二排女性假人胸部伤害为目的,分别对安全带上固定点X㊁Y㊁Z三个方向与第二排女性假人H点之间的距离差进行研究,同时结合CAE仿真验证其统计的变化规律,从中得到以下结论:(1)第二排安全带上固定点布置在C柱上时,其布置在较高位置好于较低位置㊂结合实车安全带固定点布置情况,得出第二排安全带上固定点Z方向布置的参考范围为600 700mm㊂(2)第二排安全带上固定点Y方向接近假人的位置好于远离假人的位置㊂结合实车安全带固定点布置情况,得出第二排安全带上固定点Y方向布置的参考范围为150 300mm㊂(3)第二排安全带上固定点X方向距离Δx线性变化,在一定范围内,安全带上固定点在C柱上靠前位置好于靠后位置,但在另一范围内,其情况相反,所以存在最优范围㊂综合考虑不同的变化规律,得出第二排安全带上固定点X方向布置的参考范围为300 480mm㊂参考文献:[1]国家统计局国家数据[EB/OL].http://data.stats.gov.cn/easyquery.htm?cn=C01&zb=A0S0D02&sj=2018.[2]世界卫生组织道路交通伤害[EB/OL].https://www.who.int/violence_injury_prevention/road_traffic/zh/.[3]吴云腾,葛如海,杨工作,等.正面碰撞下轿车后排乘员伤害的仿真研究[J].车辆与动力技术,2011(3):22-25.WUYT,GERH,YANGGZ,etal.Simulationoninjurytorearseatpassengerundercarfrontcrashcondition[J].Vehicle&PowerTechnology,2011(3):22-25.[4]全国汽车标准化技术委员会.机动车乘员用安全带㊁约束系统㊁儿童约束系统和ISOFIX儿童约束系统:GB14166-2013[S].北京:中国标准出版社,2013.[5]中国汽车技术研究中心有限公司.C-NCAP管理规则[Z],2018:23-26.[6]商恩义,乌秀春.基于女性假人胸部伤害的后排安全带固定点位置[J].上海电机学院学报,2017,20(4):237-243.SHANGEY,WUXC.Fixingpositionofrear⁃rowseatbeltbasedonchestinjuryoffemaledummy[J].JournalofShanghaiDianjiUniversity,2017,20(4):237-243.。
- 1、下载文档前请自行甄别文档内容的完整性,平台不提供额外的编辑、内容补充、找答案等附加服务。
- 2、"仅部分预览"的文档,不可在线预览部分如存在完整性等问题,可反馈申请退款(可完整预览的文档不适用该条件!)。
- 3、如文档侵犯您的权益,请联系客服反馈,我们会尽快为您处理(人工客服工作时间:9:00-18:30)。
9005 9007 9009
9001
螺栓力 Bolt Force Summary
螺栓号 螺栓轴力
螺栓剪切力
Bolt. Axial Force (N) Shear Force (N)
9001
1034
-834
9002 9003 9004 9005 9006 9007 9008
-1871 -387 133 -200 -771 -535 252
分析结果 (Analysis Results)
材料为QSTE380零件最大应力应变: Max. Stress and Strain Parts
真实屈服应力 Yield Strength
真实极限应力 True UTS
真实极限塑性应变 True Plastic Strain
380MPa 590MPa
安装点安全带处受力曲线(Belt Plot):
2000061
2000059
2000038
分析结果 (Analysis Results)
安装点安全带处受力曲线(Belt Plot):
1000148 1000128
1000091
分析结果 (Analysis Results)
关键区域螺栓力(Bolt Force):
1817 -2727 -311 152 -158 -572 -426 212 143
-962 -2027 -165 -270 -142 1596 405 -521 -323
分析结果 (Analysis Results)
关键区域螺栓力(Bolt Force):
9004
9003 9006 9008
9002
(Force =1.35KN) 后排座椅自身施加向前20g加速度(Rear Seat Frame loading 20g Acceleration in X
Direction)
Force
Fixed
Time/s
后排座椅安全带固定点强度CAE分析目标(CAE Target of Rear SafetyBelt Strength Analysis)
内容(Contents)
FE模型创建(FE Model Setup) CAE分析目标(CAE Targets) CAE分析结果(CAE Results)
➢ 能量检查(Energy Checking) ➢ 分析结果(Results) ➢ 分析结果总结(CAE Results Summary)
分析结果 (Analysis Results)
材料为QSTE420零件最大应力应变: Max. Stress and Strain Parts
真实屈服应力 Yield Strength
真实极限应力 True UTS
真实极限塑性应变 True Plastic Strain
420MPa 620MPa
-1836 254 154 141 -891 -588 512
9009
189
170
分析结果(Analysis Results)
考察项目 (Items)
Middle Seat
安全带固定点最大塑性应变 Max plastic strain
1.4%
Target 15%
≤ Target Good
≤ 1.1*Target Warning
分析结果 (Analysis Results)
靠背骨架最大应力应变: Max. Stress and Strain Parts
真实屈服应力 Yield Strength
真实极限应力 True UTS
真实极限塑性应变 True Plastic Strain
235MPa 500MPa
0.05
结果应力应变值 Results
零件最大应力 Max. stress in component 369.7MPa
零件最大应变 Max. strain in component
0.00047
最大应力超过屈服应力,最大应变没有超过极限值,零件没有损坏的风险。 Max Stress exceeding SIGY, Effective plastic strain not exceeding the ultimate value throughout the thickness. No Risk.
8005 8004
8007
8006
8009
8008
8003
8001
8002
螺栓力 Bolt Force Summary
螺栓号 螺栓轴力
螺栓剪切力
Bolt. Axial Force (N) Shear Force (N)
8001 8002 8003 8004 8005 8006 8007 8008 8009
Platform Model Year
Status
Report No.
Version 01
后排座椅安全带固定点强度CAE分析
Rear Safety-Belt Anchorage Strength Analysis Report
For Decision For Information/Update For Reference
分析目的(Purpose)
考察安装带固定点强度分析性能(To Assess Rear Safety-Belt Strength)
分析工况(Load Case)
基础模型的后排座椅安全带固定点强度分析(Rear Safety-Belt Strength Analysis for Base Model)
分析结果 (Analysis Results)
调角器扭矩曲线(Recliner Torsion Plot):
分析结果 (Analysis Results)
安装点安全带处受力曲线(Belt Plot):
1000083
1000157 1000139
分析结果 (Analysis Results)
后排座椅安全带固定点强度分析模型描述 (FE Model Setup)
FE模型信息 (Information of FE Model):
模型质量 Total Mass [kg]
模型节点数 Node Number
模型单元数 Element Number
FE Model
51.8 34919 34232
谢
零件最大应力 Max. stress in component 480.5MPa
零件最大应变 Max. strain in component
0.009
最大应力超过屈服应力,最大应变没有超过极限值,零件没有损坏的风险。 Max Stress exceeding SIGY, Effective plastic strain not exceeding the ultimate value throughout the thickness. No Risk.
0.15
结果应力应变值 Results
零件最大应力 Max. stress in component 406.8MPa
零件最大应变 Max. strain in component
0.014
最大应力没有超过屈服应力,最大应变没有超过极限值,零件没有损坏的风险。 Max Stress not exceeding SIGY, Effective plastic strain not exceeding the ultimate value throughout the thickness. No Risk.
≥ 1.1*Target
Unacceptable
CAE 分析结果总结 (CAE Results Summary)
模型后排座椅安全带固定点仅有中间位置卷收器设定在座椅靠背上, 其余安装点均设定在车身上(车身默认为刚性体);
后排座椅在安全带固定点分析工况下,车身受力较小,最大效塑性应 变为1.4%;后排座椅安全带固定点强度满足目标要求。
卷收器最大应力应变: Max. Stress and Strain Parts
真实屈服应力 Yield Strength
真实极限应力 True UTS
真实极限塑性应变 True Plastic Strain
420MPa 620MPa
0.15
结果应力应变值 Results
零件最大应力 Max. stress in component 169.3MPa
零件最大应变
Max. strain in component
0
最大应力没有超过屈服应力,最大应变没有超过极限值,零件没有损坏的风险。 Max Stress not exceeding SIGY, Effective plastic strain not exceeding the ultimate value throughout the thickness. No Risk.
最大应力应变的零件: Max. Stress and Strain Parts
最大应力出现在调角器左侧外支架 处,应力值为:584.6Mpa
Max. stress: 584.6Mpa
最大塑性应变出现在左侧地脚内支 架处,应变值为:1.4%
Max. plastic strain: 1.4%
分析结果 (Analysis Results)
考察项目 (Items)
安全带固定点最大塑性应变 Max plastic strain
Target 15%
能量检查(Energy Checking)
分析结果(Analysis Results)
Top
Front
Iso
后排安全带固定点强度分析动态图
分析结果 (Analysis Results)
FE模型信息 (Information of FE Model)