油脂精炼脱臭真空系统新工艺
油脂精炼车间工艺概述

脱色、脱臭常见问题处理
? 1、脱色塔控制温度和压力
? 1)吸附脱色中的操作温度决定于油脂品种操作压力及吸附剂品种及特性 脱色温度超高后会因新生色素而回升变色 2)压力是(—0.9)bar 温度应控制在90℃—130℃
? 2 B2610液位高报的原因
Ab 油中含皂较高
(1) 酸碱量不正确较多。
(2) 离心机碟片较脏或转鼓较脏。
(3) 背压调的过低。
(4) 向心泵开度较小。
(5) 油分离温度不正确,分离效果较差。
(6) 排渣量较小或间隔时间较长。
(7) 油出现乳化现象。
B:白土残油较高
1、 白土质量较差(粒度较小、水分较高、黏度较大)。
2、 白土添加量较多。
3、 过滤饼厚度较厚。
4、 过滤板较脏。
5、 蒸汽质量较差(带水分高)。
6、 蒸汽吹扫压力低。
7、 蒸汽吹扫时间短(质量较好的蒸汽)。
8、 过滤机设备本身因素。
9、 中和油质量较差(磷、皂含量较高)。
C:成品油FFA偏高
1、 汽提效果不佳。
2、 真空度不好。
2 白土用量要合适,满足生产需求即可.
3.过滤机使用要调整好,压力在3.0bar以下
4 过滤器要用规定的过滤袋
5 D2770真空在200 torr以下
6 E2701温度在120 ~130 ℃,E2702温度在180 ~200 ℃,VHE2704的温度在230 ~270℃
7 VHE2703将脱臭油冷却至150 ℃左右,E2600将脱臭油冷却至100 ℃左右,E2706冷却至45 ℃以下
3、 直接汽质量较差(带水多)。
4、 直接汽压力低。
食用油精炼设备脱臭温度、真空度、时间及蒸汽用量的控制

食用油精炼设备脱臭温度、真空度、时间及蒸汽用量的控制油脂的脱臭是根据在同等条件下臭味组分和甘油三酸酯挥发性的不同,在高温高真空条件下,利用水蒸汽蒸馏来脱除油脂中臭味组分的过程。
根据其原理,升高温度、提高真空度、增加水蒸气的用量和延长脱臭时间都有助于脱臭的进行,是提高脱臭效果的有效手段。
但在实际操作时必须考虑这些条件之间的协调及综合成本等问题。
(1)食用油精炼设备脱臭温度的控制:高温有助于去除气味,且缩短时间。
有试验表明,在脱臭温度范围内每升高17°C,可以使脱臭时间缩短一半。
但过高的温度会使部分油脂产生水解或热聚合反应,从而降低油脂的营养价值和氧化稳定性。
但温度过低达不到脱臭的目的,且脱臭后油脂的烟点较低。
一般脱臭温度可控制在230~250°C,脱臭时的高温可通过导热炉加热导热油产生。
在高温下,可同时破坏油脂中的热敏性色素,起到热脱色作用。
试验证明,一般可降低黄3~6,红0.8~1.0。
值得注意的是:脱臭结束后,油脂必须在真空条件下冷却到70°C 以下,才能破真空精滤。
否则会使油脂过氧化值增加,油色会因氧化而发红。
(2)食用油精炼设备脱臭残压的控制:根据脱臭原理,直接蒸汽喷入量与压强成正比。
高真空可以减少直接蒸汽用量,降低油脂水解损失,降低蒸馏分压,有利于臭味组分和游离脂肪酸的挥发。
目前,油脂脱臭时的绝对压力一般在600~133Pa。
兴博粮油如采用间歇式脱臭生产高烹油时控制残压为600Pa,连续精炼和色拉油脱臭的绝对压力为133Pa。
对一个具体的脱臭系统来说,如采用多级蒸汽喷射泵,其真空度和抽气速率大多不能灵活调节,这样要保持稳定的真空效果,维持工作蒸汽压力达到设计压力就十分重要;但如果蒸汽喷射泵运行的其他条件,如冷却水温度发生变化,则工作蒸汽压力也应作相应的调整。
如夏天水温高,工作蒸汽压力需相应提高;冬季水温低,适当降低蒸汽压力仍能满足脱臭所需的真空度和抽气量。
这样既可以减少工作蒸汽的用量,同时也能维持稳定的工作效果。
冰冷真空系统_大型油脂企业的节能减排新技术应用
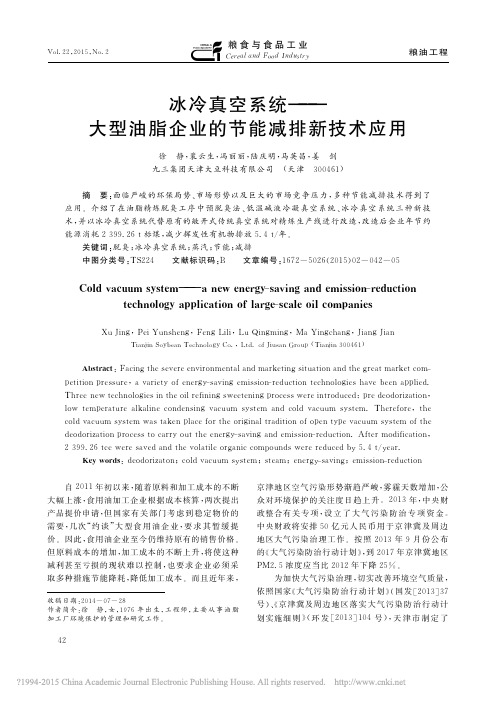
42
粮 食 与 食 品 工 业 Cereal and Food Industry
《天津市清新空气行动方案》[1]。这就迫使食用油 加 工企业要采用新技 术,降 低 生 产 过 程 中 挥 发 性 有 机 物 的 排 放 ,从 而 达 到 节 能 减 排 ,保 护 环 境 的 目 的 。 面 对日趋严峻的环境 保 护 和 生 产 成 本 压 力,企 业 必 须
(4)冰冷真空 系 统 的 总 运 行 费 较 低。 虽 然 初 期 投资成本略高,但从长 远 利 益 考 虑,其 节 能 优 势 十
分显著。
2.2 设 计 改 造 2.2.1 设 备 配 置
设计改造内容主要是保留传统的五级蒸汽喷射
系 统 及 配 套 的 污 水 冷 却 塔 ,新 建 1 套 冰 冷 真 空 系 统 。 原有的五级蒸汽喷 射 系 统 位 于 精 炼 车 间 内,配 套 的
Vol.22,2015,No.2
实施节能技术改造。
1 传统脱臭工序真空系统
1.1 脱 臭 工 序 流 程
图 1 油 脂 精 炼 工 艺 流 程 图
精炼车间主要 包 括 酸 炼 碱 炼、脱 色 和 脱 臭 等 工 物质排放,以增强企业市场竞争力和社会责任感。
序(图1)。脱臭是食用油精炼加工过程 中 的 一 个 关 键 工 序 。 引 起 油 脂 臭 味 的 主 要 组 分 是 低 级 的 醛 、酮 、
需要进行节能和 环 保 技 术 改 造。 为 此,我 们 采 用 国
(2)冷 却 水 循 环 量 低 。 由 于 蒸 汽 消 耗 的 少 ,因 此
际先进的冷冻真空工艺,降低蒸汽消耗量,减少异味 所需的冷却水也很少。
43
粮油工程
徐 静 等:冰冷真空系统———大型油脂企业的节能减排新技术应用
油脂干式冷冻真空脱臭技术及装备
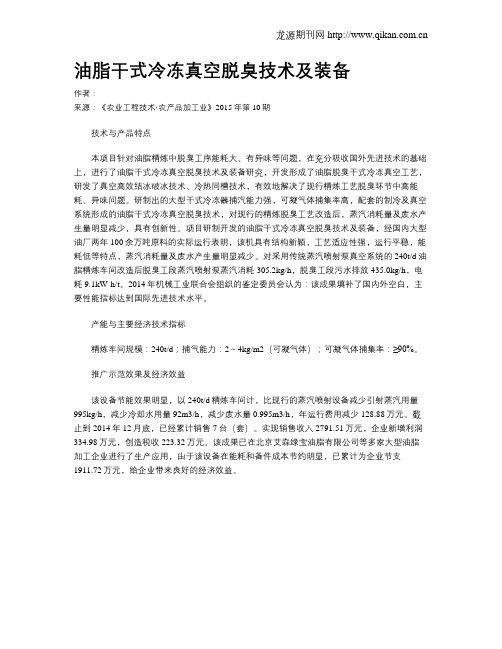
油脂干式冷冻真空脱臭技术及装备作者:来源:《农业工程技术·农产品加工业》2015年第10期技术与产品特点本项目针对油脂精炼中脱臭工序能耗大、有异味等问题,在充分吸收国外先进技术的基础上,进行了油脂干式冷冻真空脱臭技术及装备研究,开发形成了油脂脱臭干式冷冻真空工艺,研发了真空高效结冰破冰技术、冷热同槽技术,有效地解决了现行精炼工艺脱臭环节中高能耗、异味问题。
研制出的大型干式冷冻器捕汽能力强,可凝气体捕集率高,配套的制冷及真空系统形成的油脂干式冷冻真空脱臭技术,对现行的精炼脱臭工艺改造后,蒸汽消耗量及废水产生量明显减少,具有创新性。
项目研制开发的油脂干式冷冻真空脱臭技术及装备,经国内大型油厂两年100余万吨原料的实际运行表明,该机具有结构新颖,工艺适应性强,运行平稳,能耗低等特点,蒸汽消耗量及废水产生量明显减少。
对采用传统蒸汽喷射泵真空系统的240t/d油脂精炼车间改造后脱臭工段蒸汽喷射泵蒸汽消耗305.2kg/h,脱臭工段污水排放435.0kg/h,电耗9.1kW·h/t。
2014年机械工业联合会组织的鉴定委员会认为:该成果填补了国内外空白,主要性能指标达到国际先进技术水平。
产能与主要经济技术指标精炼车间规模:240t/d;捕气能力:2~4kg/m2(可凝气体);可凝气体捕集率:≥90%。
推广示范效果及经济效益该设备节能效果明显,以240t/d精炼车间计,比现行的蒸汽喷射设备减少引射蒸汽用量995kg/h,减少冷却水用量92m3/h,减少废水量0.995m3/h,年运行费用减少128.88万元。
截止到2014年12月底,已经累计销售7台(套)。
实现销售收入2791.51万元,企业新增利润334.98万元,创造税收223.32万元。
该成果已在北京艾森绿宝油脂有限公司等多家大型油脂加工企业进行了生产应用,由于该设备在能耗和备件成本节约明显,已累计为企业节支1911.72万元,给企业带来良好的经济效益。
脱臭冷冻真空系统实践9.28改
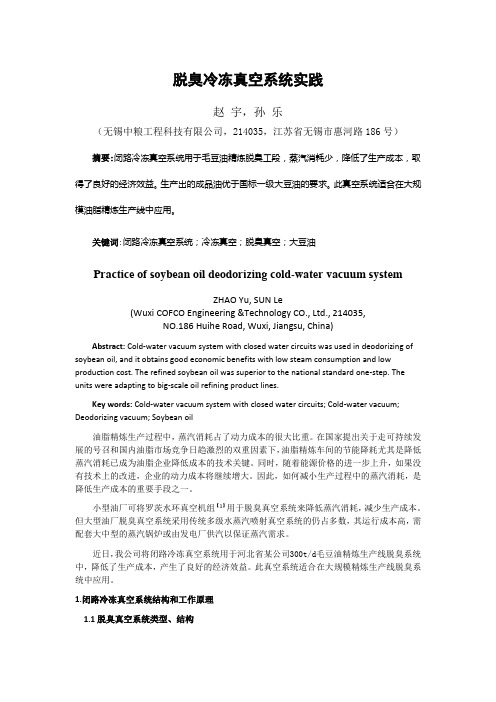
脱臭冷冻真空系统实践赵宇,孙乐(无锡中粮工程科技有限公司,214035,江苏省无锡市惠河路186号)摘要:闭路冷冻真空系统用于毛豆油精炼脱臭工段,蒸汽消耗少,降低了生产成本,取得了良好的经济效益。
生产出的成品油优于国标一级大豆油的要求。
此真空系统适合在大规模油脂精炼生产线中应用。
关键词:闭路冷冻真空系统;冷冻真空;脱臭真空;大豆油ZHAO Yu, SUN Le(Wuxi COFCO Engineering &Technology CO., Ltd., 214035,NO.186 Huihe Road, Wuxi, Jiangsu, China)Abstract: Cold-water vacuum system with closed water circuits was used in deodorizing of soybean oil, and it obtains good economic benefits with low steam consumption and low production cost. The refined soybean oil was superior to the national standard one-step. The units were adapting to big-scale oil refining product lines.Key words: Cold-water vacuum system with closed water circuits; Cold-water vacuum; Deodorizing vacuum; Soybean oil油脂精炼生产过程中,蒸汽消耗占了动力成本的很大比重。
在国家提出关于走可持续发展的号召和国内油脂市场竞争日趋激烈的双重因素下,油脂精炼车间的节能降耗尤其是降低蒸汽消耗已成为油脂企业降低成本的技术关键。
油脂精炼车间工艺概述

工艺概述中和段:主要是脱胶脱酸脱水.通过加入电解质磷酸使非亲水磷脂转变成亲水性磷脂胶体并钝化脱除分散相结合在一起的微量金属离子用碱来中和油脂中存在游离脂肪酸等物质反应生成钠皂成絮凝状物通过离心分离去除. 油中的残皂由硅藻土吸附通过过滤而得到中和油脱色段:主要脱除油中的色素.在一定条件下利用白土的吸附性在搅拌器搅拌下使白土与油充分接触最大限度的吸附色素通过过滤机滤去白土和其它杂质而得到脱色油. 脱臭段:主要是脱除油中臭味组分.利用臭味组分和甘三脂的蒸汽压不同在真空高温条件下利用汽提原理把臭味组分从油中分离出来中和段工艺流程图毛油→加热→加酸反应→冷却→加碱反应→蒸汽加热→离心分离→硅藻土吸附皂→真空干燥→过滤→中和油P2500→HX2503→MX2504→TK2505→CO2507→MX2508→T2509 →HX2511→CF2512 →TK2514→DR2517→F2691/2/3/4→T2524 中和油→换热加热→白土脱色→过滤→析气→加热→换热→高温加热→终端加热→脱臭→换热→冷却→抛光过滤→成品P2670→E2600→B2610→F2691/2/3/4→F2695/6→D2770→F2791/2→E2701→VHE27 03→E2702→VHE2704→DEO2710A→DEO2710B→VHE2703→E2600→E2706→F27 93/4 1 中和段工艺说明 1.1 加热器用3bar steam将油加热到65-90℃左右获得最佳反应温度。
1.2 混合器通过搅拌器使油和磷酸混合均匀。
1.3 酸反应罐磷酸把油中非水化磷脂转化为亲水磷脂起电解质作用除去磷脂和色素。
1.4 冷却器用冷水冷却油温将油冷却到40-75℃左右避免油温过高。
1.5 混合器通过搅拌器使油和碱混合均匀。
1.6 碱反应罐碱和油反应除去游离脂肪酸形成皂脚。
1.7 离心机离心除去大部分皂脚。
1.8 脱皂罐: 通过硅藻土吸附油中残余的皂。
炼油去臭工艺流程
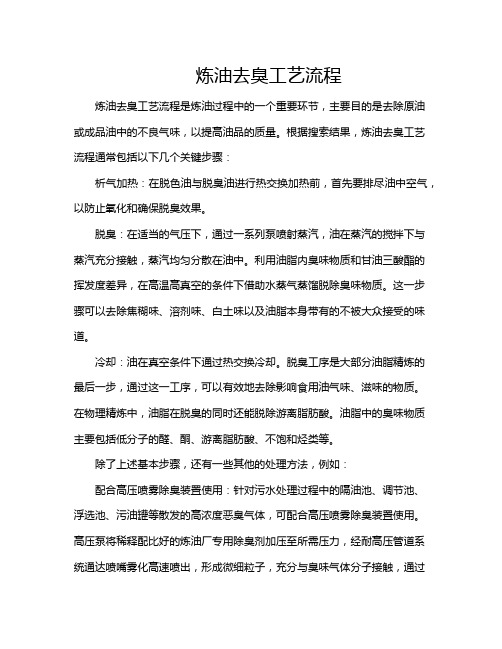
炼油去臭工艺流程
炼油去臭工艺流程是炼油过程中的一个重要环节,主要目的是去除原油或成品油中的不良气味,以提高油品的质量。
根据搜索结果,炼油去臭工艺流程通常包括以下几个关键步骤:
析气加热:在脱色油与脱臭油进行热交换加热前,首先要排尽油中空气,以防止氧化和确保脱臭效果。
脱臭:在适当的气压下,通过一系列泵喷射蒸汽,油在蒸汽的搅拌下与蒸汽充分接触,蒸汽均匀分散在油中。
利用油脂内臭味物质和甘油三酸酯的挥发度差异,在高温高真空的条件下借助水蒸气蒸馏脱除臭味物质。
这一步骤可以去除焦糊味、溶剂味、白土味以及油脂本身带有的不被大众接受的味道。
冷却:油在真空条件下通过热交换冷却。
脱臭工序是大部分油脂精炼的最后一步,通过这一工序,可以有效地去除影响食用油气味、滋味的物质。
在物理精炼中,油脂在脱臭的同时还能脱除游离脂肪酸。
油脂中的臭味物质主要包括低分子的醛、酮、游离脂肪酸、不饱和烃类等。
除了上述基本步骤,还有一些其他的处理方法,例如:
配合高压喷雾除臭装置使用:针对污水处理过程中的隔油池、调节池、浮选池、污油罐等散发的高浓度恶臭气体,可配合高压喷雾除臭装置使用。
高压泵将稀释配比好的炼油厂专用除臭剂加压至所需压力,经耐高压管道系统通达喷嘴雾化高速喷出,形成微细粒子,充分与臭味气体分子接触,通过
破坏水分子被膜,捕捉恶臭粒子,并通过除臭液的功能有益菌生长,分解、乳化并氧化污染物质,达到长期稳定脱臭的目的。
配合喷淋塔+活性炭装置使用:这是一种结合物理吸附和化学中和的方法,通过喷淋塔和活性炭装置去除恶臭气体。
干式-冷凝真空脱臭系统在食用油精炼过程中的应用
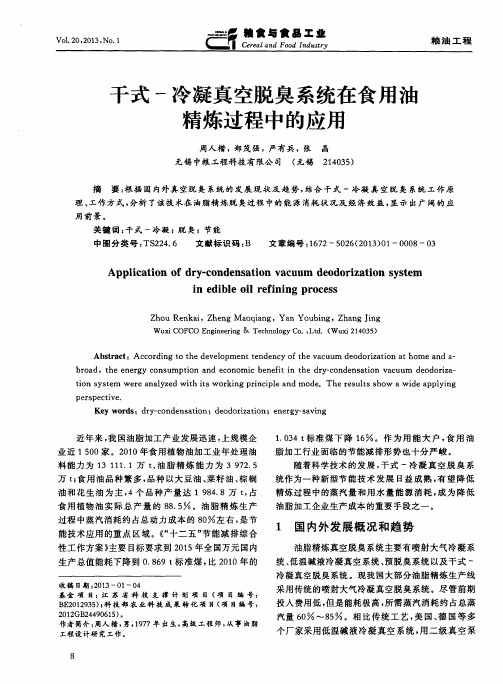
无锡 中粮 工程 科技有 限公 司 ( 无锡
摘
2 1 4 0 3 5 )
要: 根据 国内外真 空脱 臭 系统 的 发展 现 状及 趋 势 , 结合 干式 一冷凝 真 空脱 臭 系统 工作 原
理、 工作 方式 , 分析 了该技术在 油脂精 炼脱 臭过程 中的 能源 消耗状 况及 经济 效 益 , 显 示 出广 阔的应 用前 景 。 关键 词 : 干式 一冷凝 ;脱 臭 ;节能 中 图分 类 号 : T S 2 2 4 . 6 文献标 识码 : B 文章编 号 : 1 6 7 2 —5 0 2 6 ( 2 0 1 3 ) 0 1 —0 0 0 8 —0 3
收 稿 日期 : 2 0 1 3—0 1—0 4
1 国 内外 发 展概 况和 趋 势
油 脂精炼 真空脱 臭系统 主要 有喷射 大气 冷凝 系 统、 低 温碱液 冷凝真 空系统 、 预脱 臭 系统 以及 干式 一
冷凝 真空脱 臭系统 。现我 国大部 分油 脂精炼 生 产线
基 金 项 目: 江 苏 省 科 技 支 撑 计 划 项 目 ( 项 目 编 号: B E 2 0 1 2 9 3 5 ) , 科 技 部 农 业 科 技 成 果 转 化 项 目( 项 目编 号 :
冰冷真空系统——大型油脂企业的节能减排新技术应用

冰冷真空系统——大型油脂企业的节能减排新技术应用徐静;裴云生;冯丽丽;陆庆明;马英昌;姜剑【摘要】面临严峻的环保局势、市场形势以及巨大的市场竞争压力,多种节能减排技术得到了应用.介绍了在油脂精炼脱臭工序中预脱臭法、低温碱液冷凝真空系统、冰冷真空系统三种新技术,并以冰冷真空系统代替原有的敞开式传统真空系统对精炼生产线进行改造,改造后企业年节约能源消耗2 399.26 t标煤,减少挥发性有机物排放5.4t/年.【期刊名称】《粮食与食品工业》【年(卷),期】2015(022)002【总页数】5页(P42-46)【关键词】脱臭;冰冷真空系统;蒸汽;节能;减排【作者】徐静;裴云生;冯丽丽;陆庆明;马英昌;姜剑【作者单位】九三集团天津大豆科技有限公司天津300461;九三集团天津大豆科技有限公司天津300461;九三集团天津大豆科技有限公司天津300461;九三集团天津大豆科技有限公司天津300461;九三集团天津大豆科技有限公司天津300461;九三集团天津大豆科技有限公司天津300461【正文语种】中文【中图分类】TS224自2011年初以来,随着原料和加工成本的不断大幅上涨,食用油加工企业根据成本核算,两次提出产品提价申请,但国家有关部门考虑到稳定物价的需要,几次“约谈”大型食用油企业,要求其暂缓提价。
因此,食用油企业至今仍维持原有的销售价格。
但原料成本的增加,加工成本的不断上升,将使这种减利甚至亏损的现状难以控制,也要求企业必须采取多种措施节能降耗,降低加工成本。
而且近年来,京津地区空气污染形势渐趋严峻,雾霾天数增加,公众对环境保护的关注度日趋上升。
2013年,中央财政整合有关专项,设立了大气污染防治专项资金。
中央财政将安排50亿元人民币用于京津冀及周边地区大气污染治理工作。
按照2013年9月份公布的《大气污染防治行动计划》,到2017年京津冀地区PM2.5浓度应当比2012年下降25%。
为加快大气污染治理,切实改善环境空气质量,依照国家《大气污染防治行动计划》(国发[2013]37号)、《京津冀及周边地区落实大气污染防治行动计划实施细则》(环发[2013]104 号),天津市制定了《天津市清新空气行动方案》[1]。
图解各类油脂脱臭工艺及设备

图解各类油脂脱臭工艺及设备油脂脱臭工艺及设备1、间歇式脱臭时间长(8h)、耗蒸汽量大、热能利用率低。
蒸馏釜形式,高径比为2,油层下部有直接蒸汽盘管;中央循环管,蒸汽从中央循环管上部喷出,强制循环。
2、半连续脱臭相当于多层间歇脱臭器重叠组成而成,脱臭过程被分割为若干个独立的单元,每层的液层降低。
层叠式如图6-42。
3、连续式脱臭形式很多,主要有层板式、填料式、水平浅盘式脱臭塔等。
为防止油流短路,有的采用折流隔板强制导向装置、蒙马泵等。
(一)间歇式脱臭工艺及设备图1间歇式脱臭系统图2双壳体塔半连续式脱臭系统图3单壳体塔半连续式脱臭工艺(三)连续式脱臭工艺图4连续水平式浅盘连续脱臭工艺图6带浮阀塔板的连续脱臭工艺图7连续式多容器脱臭工艺(四)填料薄膜脱臭工艺图11连续薄膜式脱臭工艺脱臭设备(一)脱臭器:多层脱臭塔、填料式脱臭塔、组合塔多层式脱臭塔A多层式脱臭塔B填料脱臭塔组合式脱臭塔(二)辅助设备1、析气器待脱臭油中,一般溶解有1/万-5/万的氧气,需在高温脱臭之前脱除。
析气器的型式有多种,70℃。
2、换热器用于冷热油热交换——热量回收、加热高温油。
利用高压蒸汽加热时,特别要注意耐高压、热补偿问题。
板式换热器热效果好,因垫片密封问题,用于低温液—液换热。
螺旋板不如板式换热效果好,可用于高温、无垫片泄露,但难以清理。
列管换热效率最低,但可拆卸头部,容易清理,常用。
3、脂肪酸捕集器采用低温(60℃)脂肪酸对高温脱臭馏出气体直接冷凝,将脂肪酸等高沸点组分冷凝回收,减少冷凝水的污染。
脂肪酸捕集器由脂肪酸喷头、旋风分离室和分离挡板组成。
4、屏蔽泵输送高温油脂的气密泵,防止空气空气对高温油脂的氧化,在高真空条件下运行。
主要特点:泵与电机为一整体结构,定子与转子都用薄金属罩密封,所有通向外界的联接处均使用密封片或O型密封环进行密封,从而有效地防止了泵运转时的空气泄漏,避免了高温油脂与氧的接触。
5、真空装置(1)水喷射真空泵、机械真空泵、汽-水串联真空泵;极限真空度较低(700mmHg),用真空度要求不高、抽气量大工序。
植物油脂精炼脱臭工艺真空系统的改进

直接喷淋低温冷凝水 , 达到冷凝高温蒸汽的 目的 , 从而建立每个
喷射泵 的压缩 比, 并逐渐升 到常压 , 满足一定 的冷凝效果 , 构建 合理 的压缩 比( 一般不超过 1 ) 2 是蒸汽喷射泵高效 运行 的关键 。
2真 空度 的影 响 因素 .
真空环境下。 在实际生产中 , 连续的高温天气容易造成开式冷却 水塔降温困难 , 真空系统真空度降低 , 导致产量下降 。认真分析 影响脱臭工段真空系统真空度的因素并加 以解决 ,对提高产品
质 量 和 产 量 有着 重大 的意 义 。
1 . 真空系统 的组成及工作原 理 北 海粮油 6 0 d物理精 炼工 段真空 系统 由两 个 中间冷 凝 0t / 器 与三级蒸汽喷射真空泵 以及一台真空水环泵所组成 。蒸汽喷 射真空泵 内设有拉瓦尔喷嘴 , 汽经分汽包流 向各个 喷射器 , 蒸 管 道 中流速约为几十米 , 当蒸汽通过喷射器 中的拉瓦尔喷嘴时 , 汽
植物油脂精炼脱臭 工艺真 空 系统 的改进
王万祥 朱成志 张 博 潘立 霞
摘要 关键词 分析 植物油脂物理精 炼脱臭工艺在夏 季真 空系统 真空度 降低 的原 因, 结合 60/ 0t d物理精 炼工段现状 , 采取 改进措施 精炼生产 真空系统 改进
B
取 得 了预 期 效 果 。
升 高对真 空系 统 的影 响主要 表现
为以下两方面。
( ) 冷 凝 效 果 的 影 响 1对
在 正常生产 的情 况下 , 一级冷 凝器要求下水 的温度在 3 ℃以下 , 7
正常工 况一级 冷凝 器上水 温度 比
下水温度低 5 ℃,二级冷凝 器的下 水温度要在 4 q以下 , 5c 正常工况时 上水温度 比下水温度低 1o。 1 在夏 C
食用油精炼设备脱臭温度、真空度、时间及蒸汽用量的控制

食用油精炼设备脱臭温度、真空度、时间及蒸汽用量的控制食用油精炼设备脱臭温度、真空度、时间及蒸汽用量的控制油脂的脱臭是根据在同等条件下臭味组分和甘油三酸酯挥发性的不同,在高温高真空条件下,利用水蒸汽蒸馏来脱除油脂中臭味组分的过程。
根据其原理,升高温度、提高真空度、增加水蒸气的用量和延长脱臭时间都有助于脱臭的进行,是提高脱臭效果的有效手段。
但在实际操作时必须考虑这些条件之间的协调及综合成本等问题。
(1)食用油精炼设备脱臭温度的控制:高温有助于去除气味,且缩短时间。
有试验表明,在脱臭温度范围内每升高17°C,可以使脱臭时间缩短一半。
但过高的温度会使部分油脂产生水解或热聚合反应,从而降低油脂的营养价值和氧化稳定性。
但温度过低达不到脱臭的目的,且脱臭后油脂的烟点较低。
一般脱臭温度可控制在230~250°C,脱臭时的高温可通过导热炉加热导热油产生。
在高温下,可同时破坏油脂中的热敏性色素,起到热脱色作用。
试验证明,一般可降低黄3~6,红0.8~1.0。
值得注意的是:脱臭结束后,油脂必须在真空条件下冷却到70°C 以下,才能破真空精滤。
否则会使油脂过氧化值增加,油色会因氧化而发红。
(2)食用油精炼设备脱臭残压的控制:根据脱臭原理,直接蒸汽喷入量与压强成正比。
高真空可以减少直接蒸汽用量,降低油脂水解损失,降低蒸馏分压,有利于臭味组分和游离脂肪酸的挥发。
目前,油脂脱臭时的绝对压力一般在600~133Pa。
兴博粮油如采用间歇式脱臭生产高烹油时控制残压为600Pa,连续精炼和色拉油脱臭的绝对压力为133Pa。
对一个具体的脱臭系统来说,如采用多级蒸汽喷射泵,其真空度和抽气速率大多不能灵活调节,这样要保持稳定的真空效果,维持工作蒸汽压力达到设计压力就十分重要;但如果蒸汽喷射泵运行的其他条件,如冷却水温度发生变化,则工作蒸汽压力也应作相应的调整。
如夏天水温高,工作蒸汽压力需相应提高;冬季水温低,适当降低蒸汽压力仍能满足脱臭所需的真空度和抽气量。
植物油精炼工艺流程

植物油精炼工艺流程
1.脱酸
植物油中的游离脂肪酸会影响油质的稳定性和口感,因此需要进行脱酸处理。
通常采用碱炼法,将植物油与碱溶液进行反应,将游离脂肪酸中的游离酸根络合物生成沉淀,以去除游离脂肪酸。
2.脱臭
植物油中含有一些挥发性有机物和异味物质,需要进行脱臭处理以改善油品的质量。
脱臭通常采用真空蒸馏法,将油加热至一定温度,通过蒸汽将挥发性物质蒸发,然后在低温下冷凝回收,达到去除异味的目的。
3.脱色
植物油中可能含有一些色素,如胡萝卜素、叶绿素等,需要通过脱色处理来改善油的外观。
常见的方法是通过吸附剂,如活性炭、白土等,将色素吸附,并将其从油中分离出来。
4.去酸价
酸价是油脂中游离脂肪酸的含量指标。
为了保证植物油的品质,需要将酸价降至一定水平。
一般采用碱中和法,将植物油与碱溶液进行反应,将游离脂肪酸中的游离酸根络合物生成沉淀,通过此方法降低酸价。
5.去杂质
植物油中可能含有一些杂质,如胶质、沉淀物等,需要进行去除。
常见的方法有沉淀法、过滤法等。
通过这些方法可以将杂质从油中分离出来,提高油的纯度。
6.精炼
精炼是将植物油的质量进一步提升的过程。
常见的方法有膜处理、蒸汽蒸馏、冷冻结晶等。
通过这些方法可以去除植物油中的杂质、异味物质等,提高油品的稳定性和质量。
以上是植物油精炼的主要工艺流程,通过这些工艺可以提高植物油的质量和口感,满足人们对健康食品的需求。
- 1、下载文档前请自行甄别文档内容的完整性,平台不提供额外的编辑、内容补充、找答案等附加服务。
- 2、"仅部分预览"的文档,不可在线预览部分如存在完整性等问题,可反馈申请退款(可完整预览的文档不适用该条件!)。
- 3、如文档侵犯您的权益,请联系客服反馈,我们会尽快为您处理(人工客服工作时间:9:00-18:30)。
采用二级蒸汽喷射泵和水环真空泵联用提供脱臭工段真空,同时对进入脱臭真空 系统的游离脂肪酸等可凝性气体采用低温碱液冷凝和捕集的方式,以减少蒸汽消耗和 废水排放量。
3 油脂脱臭低温碱液真空系统
3.2主要工艺影响因素 3.2主要工艺影响因素 3.2.1脱臭真空系统碱液pH值的选择 3.2.1脱臭真空系统碱液pH值的选择 脱臭真空系统碱液pH 研究pH对脱臭馏出物由气相成为液相效果的关系。
某300t/d精炼油厂水、电、汽消耗在油脂精炼动力成本中所占比例
动力消耗比例图 2.5%
17.4%
总动力成本:53.9元/吨油 水:0.2×6.7=1.34元/吨油占:2.5%
80.1%
电:13×0.72=9.36元/吨油占: 17.4%
水 电 蒸汽
蒸汽:0.27×160=43.2元/吨油占:80.1%
因此,提高企业市场竞争力,必须降低动力成本、降低蒸汽耗量
1油脂精炼真空系统现状
精炼车间真空系统 脱溶多采用三级蒸汽喷射泵或水喷射泵;脱色采用水喷射泵;脱臭真空系 统多数采用四级蒸汽喷射泵;干式冷凝真空系统或低温碱液真空系统等在一 些企业也有采用。 国内绝大多数油脂生产脱臭工段采用传统的四级蒸汽喷射泵。 多级蒸汽喷射泵的每级喷射器所喷射出的混合气体为被 抽气体与工作蒸汽的混合物,除末级排入大气外,都进入后一 级喷射器,增加了后一级的负载,或造成泵的工作性能变坏。 因此,多级蒸汽喷射泵常在两级喷射器间安装大气冷凝器,将混 合气体中的大部分可凝气体进行冷凝。
24
95
谢 谢
19
研究加碱方式、 研究加碱方式、 及不同系统加 碱效果
3 油脂脱臭低温碱液真空系统
3.2.3 其他研究内容 (2)高浓度废水排出密闭的真空系统的研究。
高浓度 废水排 出方式
PH
3 油脂脱臭低温碱液真空系统
3.2.3 其他研究内容 (3)收集罐的研究。研究不同结构和加热方式对捕集液体收集和排出的效果。
综上所述,就目前国内外油脂脱臭真空系统技术水平和发展状况, 综上所述,就目前国内外油脂脱臭真空系统技术水平和发展状况,低温碱液真空 系统因其技术成熟度较高、效果显著, 系统因其技术成熟度较高、效果显著,是国内油脂行业降低能源消耗的首选技术 。Biblioteka 3 油脂脱臭低温碱液真空系统
3.1工艺流程 3.1工艺流程
PH对捕集效 PH对捕集效 果的影响
结论:碱液pH在7.5~8
3 油脂脱臭低温碱液真空系统
3.2.2捕集液温度的确定 3.2.2捕集液温度的确定 研究捕集温度与脱臭馏出物(脂肪酸等)由气相降低温度成为液相效果的关系
T对捕集效 果的影响
结论:捕集液温度10℃
3 油脂脱臭低温碱液真空系统
3.2.3 其他研究内容 (1)液碱的加入方式的研究。 液碱的加入方式的研究。
1油脂精炼真空系统现状
传统工艺真空设备--四级蒸汽喷射泵流程和设备示意图:
1油脂精炼真空系统现状
四级蒸汽喷射泵系统优缺点: 优点:结构简单、使用寿命长、抽气能力大、对粉尘不敏感等 劣点:蒸汽耗量大,冷却水耗量大;废水量大,污染环境;喷嘴容 易磨损、喷射器容易被腐蚀 冷却水耗量与水温度有关,以30℃冷却水为例,其四级蒸汽真 空泵系统总的蒸汽消耗大约为0.08kg/kg原料油 ;夏季生产时,因 冷却水温度偏高导致真空泵的效率降低,能源浪费比较突出。研究 表明:当水温降低3℃,可减少15%以上的蒸汽消耗 。
蒸汽 电 水
3 油脂脱臭低温碱液真空系统
3.3 经济效益分析
◆ 300t/d精炼生产线改造后经济效益:
项目
消耗指标
水消耗(元/t油) 0.2 56.38元/t油 0.1 33.15元/t油 23.23元/吨油 41.2%
电消耗(元/t油) 12
蒸汽消耗(元/t油) 290
消耗量(改造前) 总动力成本(改造前) 消耗量(改造后) 总动力成本(改造后) 总动力成本降低 总动力成本降低
3 油脂脱臭低温碱液真空系统
3.3 经济效益分析
指标名称 蒸汽耗量 水消耗 电耗 吨油消耗指标 95kg/t油 0.1m3/t油 24kwh/t油 节能成效 降低50% 污水排放量减少50% 增加100%
3 油脂脱臭低温碱液真空系统
3.3 经济效益分析 ◆ 300t/d精炼生产线改造后经济效益:
油脂精炼脱臭真空系统新工艺
西安油脂科学研究设计院
1油脂精炼真空系统现状
我国目前的能源利用率为40%~50%,发达国家为70%~75%。 “十二五”规划纲要确立的节能减排目标
《产业结构调整目录》(2011年本)
国内植物油厂脱臭真空系统蒸汽消耗量约占整个精炼车间蒸汽耗量的60%。
1油脂精炼真空系统现状
2.油脂精炼真空新技术 油脂精炼真空新技术
2.2低温碱液真空系统 2.2低温碱液真空系统 ▲采用蒸汽喷射泵和水环真空泵联用满足脱臭真空度的要求; ▲采用低温碱液冷凝真空系统抽出游离脂肪酸等可凝性气体; ▲采用碱水捕集使捕集液循环使用,减少废水排放。 2.3其他 2.3其他
罗茨液环真空系统 :采用低噪音、低震动型罗茨真空泵和液环真空泵组成的真空系统, 震动小、噪音低;只消耗电力和水,不消耗蒸汽 。。。尚未实现工业化应用
★ 综合节能效果达到40% ★ 年直接节约生产成本200万元以上
元/吨油
精炼车间原动力消耗: 精炼车间原动力消耗: 水:0.2立方/吨油 立方/ 电:12度/吨油 12度 蒸汽:290公斤/吨油 蒸汽:290公斤/ 公斤
50 40 30 20 10 0
原系统 新系统
改造后精炼车间动力消耗: 改造后精炼车间动力消耗: 水:0.1立方/吨油 立方/ 电:24度/吨油 24度 蒸汽:95公斤/ 蒸汽:95公斤/吨油 公斤
2.油脂精炼真空新技术 油脂精炼真空新技术
2.1干式冷凝真空系统 2.1干式冷凝真空系统 原理:在水的三相点以下,水只发生升华与凝华相变。油脂脱臭的绝压低于水的三相点 压力,因此油脂脱臭干式冷凝器对工艺蒸汽中可凝气的捕集是通过凝华实现的。
从连续式油脂脱臭塔顶部出来的脂 肪酸和水蒸汽混合气体被吸入两台交替 使用的干式冷凝器中(由机械真空泵将 此两台干式冷凝器抽成真空),混合气 体在冷凝器内被冷凝后进人解冻器,被 完全解冻融化成液体后进人分层器,分 别得到脂肪酸和水。而制冷剂则在干式 冷凝器中与脂肪酸一水蒸汽的混合气体 作间接的热交换,由液体状态经吸热变 成气体再被抽出.经压缩、冷凝后恢复 成液态再次使用。
2.油脂精炼真空新技术 油脂精炼真空新技术
2.1干式冷凝真空系统 2.1干式冷凝真空系统 优点:由于不使用多级蒸汽喷射泵、大气冷凝器等装置,不仅节约了设备投资, 也节省了大量的抽真空用的蒸汽和大气冷凝器用的冷却水,具有比传统的四级 蒸汽喷射泵系统更高的节能效果。 目前, 油脂干式冷凝真空技术在欧洲油脂企业中得到广泛应用, 成为油脂 精炼的标配设备。 德国Korting、丹麦NiroAtlas(尼鲁阿特拉斯,GEA)、比利 时Desmet及美国Graham 公司在该项技术方面处于领先地位。 因投资成本较高,国内暂无企业采用该技术。