PCB的蚀刻工艺及过程控制
pcb-etch

PCB外层电路的蚀刻工艺一.概述目前,印刷电路板(PCB)加工的典型工艺采用"图形电镀法"(Pattern plating)。
即先在板子外层需保留的铜箔部分上,也就是电路的图形部分上预镀一层铅锡抗蚀层,然后用化学方式将其余的铜箔腐蚀掉,称为蚀刻。
图1所示的,为图形电镀后板子横截面的情况。
在图1状态下,印制板的整体厚度是整个加工过程中之最,以后将逐渐减薄,直到阻焊涂覆工艺。
图1的下一道工艺是去膜,即将铜层上铅锡部分以外的感光保护膜剥离掉。
图2表示了去膜后板子的横截面。
接下去的工艺就是蚀刻。
要注意的是,这时的板子上面有两层铜.在外层蚀刻工艺中仅仅有一层铜是必须被全部蚀刻掉的,其余的将形成最终所需要的电路。
这种类型的图形电镀,其特点是镀铜层仅存在于铅锡抗蚀层的下面。
另外一种工艺方法是整个板子上都镀铜,感光膜以外的部分仅仅是锡或铅锡抗蚀层(见图3)。
这种工艺称为“全板镀铜工艺“。
与图形电镀相比,全板镀铜的最大缺点是板面各处都要镀两次铜而且蚀刻时还必须都把它们腐蚀掉。
因此当导线线宽十分精细时将会产生一系列的问题。
同时,侧腐蚀(见图4)会严重影响线条的均匀性。
在印制板外层电路的加工工艺中,还有另外一种方法,就是用感光膜代替金属镀层做抗蚀层。
这种方法非常近似于内层蚀刻工艺,可以参阅内层制作工艺中的蚀刻。
目前,锡或铅锡是最常用的抗蚀层,用在氨性蚀刻剂的蚀刻工艺中.氨性蚀刻剂是普遍使用的化工药液,与锡或铅锡不发生任何化学反应。
氨性蚀刻剂主要是指氨水/氯化氨蚀刻液。
此外,在市场上还可以买到氨水/硫酸氨蚀刻药液。
以硫酸盐为基的蚀刻药液,使用后,其中的铜可以用电解的方法分离出来,因此能够重复使用。
由于它的腐蚀速率较低,一般在实际生产中不多见,但有望用在无氯蚀刻中。
有人试验用硫酸-双氧水做蚀刻剂来腐蚀外层图形。
由于包括经济和废液处理方面等许多原因,这种工艺尚未在商用的意义上被大量采用.更进一步说,硫酸-双氧水,不能用于铅锡抗蚀层的蚀刻,而这种工艺不是PCB外层制作中的主要方法,故决大多数人很少问津。
PCB工艺外层蚀刻工艺简介

Under Etch
Over Etch
阻剂(锡面)
14
Outer Layer Pattern Creation
蚀刻均匀性
1.设备之确认:喷嘴状况
“定点喷”确认喷嘴状况
基材
2.条件之确认:喷压状况
铜面
“蚀刻点”确认喷压条件
3.蚀刻均匀性:设备/制程条件之整体表征
规格为“Rang=Max-Min<0.4 mil”为允收标准
a.氧化剂:将Sn氧化为SnO b.抗结剂:将SnO转为可溶性结构 c.护铜剂:保护铜面,防止氧化
17
Outer Layer Pattern Creation
检验项目与相关规范
CCD量测 线宽量测仪器
阻抗室量测阻抗(阻抗板) a. Polar type机台 b. TEK type机台
IPQC板面检视 板面质量检查
外层蚀刻(线路蚀刻)
目的:
线路电镀完成后,电路板将送入外层蚀刻线(剥膜、 蚀刻、剥锡段),主要的工作就是将电镀阻剂完全剥除(剥 膜段),将要蚀除的铜曝露在蚀刻液内(蚀刻段)。由于线路 区的顶部已被锡所保护,线路区的线路就能保留下来,再 将锡面剥除(剥锡段),如此整体线路板的表面线路就呈现 出来。典型的剥膜(Stripping)、蚀刻(Etching)、剥锡 (Stripping)生产线,业界统称为”SES Line”
8
Outer Layer Pattern Creation
蚀铜原理(蚀刻液主成分氯化铵/铜离子)
剥膜后蚀刻前
蚀刻中
蚀刻后
蚀铜液 : 碱性蚀刻液
功 用 : 蚀刻速度快且不伤害 金
属阻剂, 主要应用于负片
流程之镀锡(铅)板上
蚀铜液:酸性蚀刻液 功 用:蚀刻速度较慢且不攻击
pcb蚀刻工艺流程

pcb蚀刻工艺流程PCB蚀刻工艺流程。
PCB蚀刻工艺是制作印刷电路板(PCB)的重要工艺之一,它通过化学蚀刻的方式将不需要的部分去除,从而形成电路板上的导线、焊盘等元件。
下面将详细介绍PCB蚀刻工艺的流程及注意事项。
1. 设计电路板图纸。
首先,需要根据电路设计需求,利用CAD软件设计出电路板的图纸。
在设计过程中,需要考虑线路的走向、宽度、间距、焊盘的位置等因素,确保设计的电路板符合实际需求。
2. 制作光阻膜。
在电路板的基材上涂覆一层光阻膜,然后将电路板图纸放置在光阻膜上,经过曝光和显影处理,形成光阻图案。
光阻膜的作用是保护不需要蚀刻的部分,以便后续的蚀刻工艺能够准确进行。
3. 酸洗清洁。
将经过光阻处理的电路板放入酸性溶液中进行酸洗清洁,去除表面的氧化物和杂质,以保证后续的蚀刻能够顺利进行。
4. 化学蚀刻。
将经过光阻处理和酸洗清洁的电路板放入蚀刻机中,通过化学溶液对不需要的部分进行蚀刻。
在蚀刻过程中需要控制蚀刻时间和温度,以确保蚀刻的精度和一致性。
5. 清洗去除光阻。
蚀刻完成后,需要将电路板放入去光阻溶液中清洗,去除残留的光阻膜。
清洗完毕后,再进行烘干处理,以确保电路板表面干净无残留。
6. 检测和修复。
经过蚀刻和清洗后,需要对电路板进行检测,确保线路的完整性和焊盘的质量。
如发现问题,需要及时进行修复处理,以确保电路板的质量符合要求。
7. 表面处理。
最后,需要对电路板进行表面处理,包括防氧化处理、喷锡处理等,以保护电路板的表面和提高焊接性能。
在整个PCB蚀刻工艺流程中,需要严格控制各个环节的参数和质量,确保电路板的质量和稳定性。
同时,还需要注意安全防护措施,避免化学品对人体的伤害。
希望以上内容能够对PCB蚀刻工艺有所帮助。
pcb线路蚀刻工艺流程

PCB线路蚀刻工艺流程引言PCB(Printed Circuit Board,印刷电路板)是电子产品中常用的一种重要组成部分,它提供了电子元器件之间的连接和支持。
PCB线路蚀刻是制造PCB的关键工艺之一,它用于将图案化的线路图案刻蚀到铜层上,以实现电路连接功能。
本文将详细描述PCB线路蚀刻的工艺流程,包括准备工作、蚀刻机操作、后处理等环节,以确保流程清晰且实用。
准备工作在进行PCB线路蚀刻之前,需要完成以下准备工作:1.设计文件准备:根据电路原理图和布局图,使用电子设计自动化(EDA)软件绘制PCB设计文件,生成Gerber文件或其他格式的制造文件。
2.PCB板材准备:选择合适的PCB板材,常见的有FR-4玻璃纤维板和金属基板等。
根据设计要求,选取板材的厚度和特性参数。
3.制造文件检查:检查制造文件中是否存在错误或缺陷。
确定文件中的线路、孔径、间距等参数是否符合要求。
4.光敏感涂层应用:将预涂有光敏感感光胶的铜板放入真空台,确保板材表面没有灰尘和杂质。
通过光照曝光可以形成线路图案。
5.线路图案制作:通过暗房曝光或光刻机曝光,将制造文件中的线路图案转移到光敏感感光胶层上。
经过显影和腐蚀等步骤后,可得到铜层上的线路图案。
蚀刻机操作完成准备工作后,可以开始进行蚀刻机操作。
下面是蚀刻机操作的具体步骤:1.蚀刻机准备:根据PCB的尺寸和厚度调整蚀刻机的参数,如液位、温度、速度等。
检查蚀刻机是否正常工作,液体是否充足。
2.保护措施:佩戴防护手套、护目镜等个人防护装备。
在通风良好的环境下操作蚀刻机,避免吸入有害气体。
3.蚀刻机设定:将铜板放入蚀刻机槽中,确保铜板与刻蚀液充分接触。
设置蚀刻时间和温度,以及刻蚀液的喷洒、振动等参数。
4.蚀刻过程:启动蚀刻机,观察蚀刻液对铜层的刻蚀情况。
根据需要定时检查刻蚀情况,确保线路图案刻蚀到合适的深度。
5.刻蚀检查:定期取出样品,检查线路的刻蚀深度和质量。
如果刻蚀不足,可以继续刻蚀;如果刻蚀过度,需要采取补救措施。
pcb线路蚀刻工艺流程

pcb线路蚀刻工艺流程一、前言PCB线路蚀刻工艺是电子制造过程中关键的一步,它决定了电路板上的导电线路是否能够正确连接。
本文将详细介绍PCB线路蚀刻工艺的流程及注意事项。
二、准备工作1. 设计原理图和PCB布局图,将其导入到PCB设计软件中。
2. 在PCB设计软件中添加必要的元件和引脚,进行布局设计。
3. 添加必要的电源线和地线。
4. 添加必要的信号层和填充层。
5. 根据需要添加屏蔽层和丝印层。
6. 导出Gerber文件,准备制作光阻膜。
三、制作光阻膜1. 制作铜片:在铜板上切割出与PCB板大小相同的铜片,并进行打磨处理,使其表面平整光滑。
2. 洗涤铜片:用去污剂清洗铜片表面,并用水冲洗干净。
3. 涂覆光阻:将光阻液均匀地涂抹在铜片上,并在黑暗环境下晾干。
4. 曝光:将导出的Gerber文件放置在曝光机上,将铜片放置在文件上方,进行曝光处理。
5. 显影:将曝光后的铜片放入显影液中,使光阻膜上的未曝光部分被溶解掉。
6. 冲洗:用水冲洗干净显影后的铜片,并用热风干燥。
四、蚀刻1. 准备蚀刻液:将蚀刻液倒入蚀刻槽中,加热至适当温度。
2. 蚀刻前处理:用去污剂清洗铜片表面,并贴上保护胶带,只露出需要蚀刻的线路部分。
3. 开始蚀刻:将处理好的铜片放入蚀刻槽中,等待一定时间后取出。
重复此过程直到所有需要蚀刻的线路都完成。
4. 冲洗和清理:用水冲洗干净已经完成蚀刻的铜片,并去除保护胶带和残留的光阻。
五、钻孔1. 钻孔前处理:用去污剂清洗铜片表面,并在需要钻孔的位置打上标记。
2. 钻孔机操作:将已经标记好的铜片放入钻孔机中,进行钻孔操作。
3. 清理:用吸尘器或者刷子清理干净铜片表面的碎屑。
六、焊接1. 焊接前处理:将需要焊接的元件和引脚插入到对应位置,并用去污剂清洗铜片表面。
2. 焊接机操作:将已经插入元件和引脚的铜片放入焊接机中,进行焊接操作。
七、后续处理1. 检查:对已经完成的PCB板进行检查,确保所有线路和元件都正确连接。
pcb蚀刻工艺流程
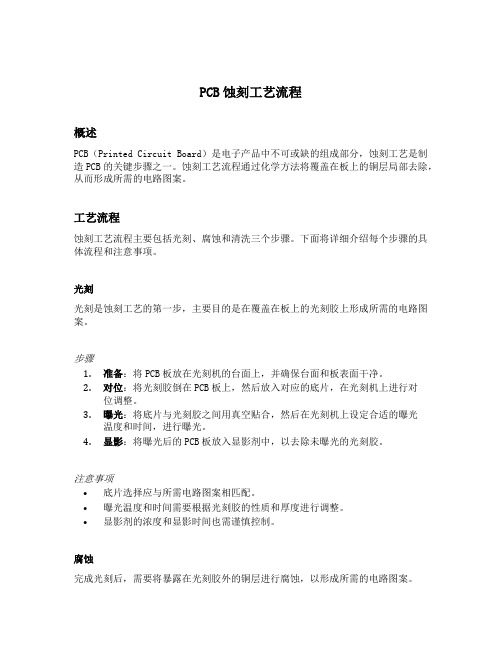
PCB蚀刻工艺流程概述PCB(Printed Circuit Board)是电子产品中不可或缺的组成部分,蚀刻工艺是制造PCB的关键步骤之一。
蚀刻工艺流程通过化学方法将覆盖在板上的铜层局部去除,从而形成所需的电路图案。
工艺流程蚀刻工艺流程主要包括光刻、腐蚀和清洗三个步骤。
下面将详细介绍每个步骤的具体流程和注意事项。
光刻光刻是蚀刻工艺的第一步,主要目的是在覆盖在板上的光刻胶上形成所需的电路图案。
步骤1.准备:将PCB板放在光刻机的台面上,并确保台面和板表面干净。
2.对位:将光刻胶倒在PCB板上,然后放入对应的底片,在光刻机上进行对位调整。
3.曝光:将底片与光刻胶之间用真空贴合,然后在光刻机上设定合适的曝光温度和时间,进行曝光。
4.显影:将曝光后的PCB板放入显影剂中,以去除未曝光的光刻胶。
注意事项•底片选择应与所需电路图案相匹配。
•曝光温度和时间需要根据光刻胶的性质和厚度进行调整。
•显影剂的浓度和显影时间也需谨慎控制。
腐蚀完成光刻后,需要将暴露在光刻胶外的铜层进行腐蚀,以形成所需的电路图案。
步骤1.准备:将光刻胶去除,并确保PCB板表面干净。
2.腐蚀:将PCB板放入腐蚀槽中,并注入蚀刻剂,观察腐蚀过程。
3.停止腐蚀:当所需电路图案的铜层已被完全腐蚀后,及时将PCB板从腐蚀槽中取出并进行下一步处理。
注意事项•腐蚀剂的选择应根据所需腐蚀速度和安全性进行合理选取。
•腐蚀时间的控制需要根据腐蚀剂的性质和腐蚀速度进行调整。
•腐蚀过程中需保持腐蚀剂的温度恒定。
清洗蚀刻后,PCB板上可能残留有光刻胶、腐蚀剂等污染物,因此需要进行清洗以确保电路质量和可靠性。
步骤1.去除光刻胶:将PCB板放入光刻胶去胶剂中,浸泡一段时间后,用刷子轻轻刷洗,直至光刻胶完全去除。
2.清洗腐蚀剂:将PCB板放入清洗槽中,注入清洗液,进行循环清洗。
3.漂洗和烘干:用纯净水对PCB板进行漂洗,然后将其放入烘干机中进行烘干。
注意事项•清洗剂的选择应兼顾去除能力和安全性。
PCB线路板外层电路的蚀刻工艺(蚀刻因子)
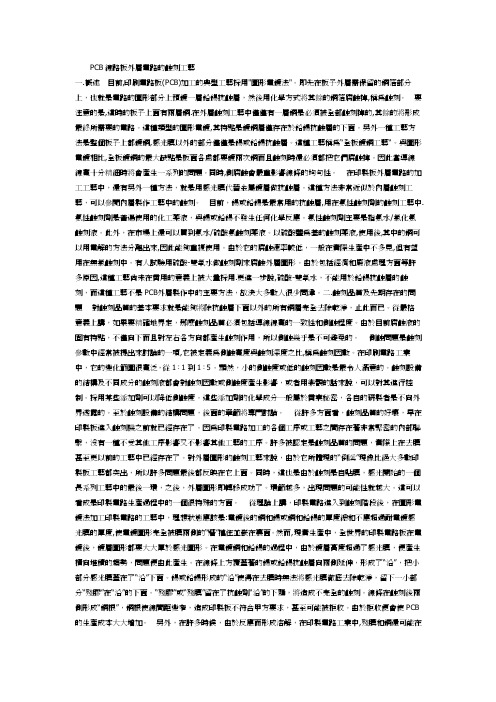
PCB線路板外層電路的蝕刻工藝一.概述目前,印刷電路板(PCB)加工的典型工藝採用"圖形電鍍法"。
即先在板子外層需保留的銅箔部分上,也就是電路的圖形部分上預鍍一層鉛錫抗蝕層,然後用化學方式將其餘的銅箔腐蝕掉,稱為蝕刻。
要注意的是,這時的板子上面有兩層銅.在外層蝕刻工藝中僅僅有一層銅是必須被全部蝕刻掉的,其餘的將形成最終所需要的電路。
這種類型的圖形電鍍,其特點是鍍銅層僅存在於鉛錫抗蝕層的下面。
另外一種工藝方法是整個板子上都鍍銅,感光膜以外的部分僅僅是錫或鉛錫抗蝕層。
這種工藝稱為“全板鍍銅工藝“。
與圖形電鍍相比,全板鍍銅的最大缺點是板面各處都要鍍兩次銅而且蝕刻時還必須都把它們腐蝕掉。
因此當導線線寬十分精細時將會產生一系列的問題。
同時,側腐蝕會嚴重影響線條的均勻性。
在印製板外層電路的加工工藝中,還有另外一種方法,就是用感光膜代替金屬鍍層做抗蝕層。
這種方法非常近似於內層蝕刻工藝,可以參閱內層製作工藝中的蝕刻。
目前,錫或鉛錫是最常用的抗蝕層,用在氨性蝕刻劑的蝕刻工藝中.氨性蝕刻劑是普遍使用的化工藥液,與錫或鉛錫不發生任何化學反應。
氨性蝕刻劑主要是指氨水/氯化氨蝕刻液。
此外,在市場上還可以買到氨水/硫酸氨蝕刻藥液。
以硫酸鹽為基的蝕刻藥液,使用後,其中的銅可以用電解的方法分離出來,因此能夠重複使用。
由於它的腐蝕速率較低,一般在實際生產中不多見,但有望用在無氯蝕刻中。
有人試驗用硫酸-雙氧水做蝕刻劑來腐蝕外層圖形。
由於包括經濟和廢液處理方面等許多原因,這種工藝尚未在商用的意義上被大量採用.更進一步說,硫酸-雙氧水,不能用於鉛錫抗蝕層的蝕刻,而這種工藝不是PCB外層製作中的主要方法,故決大多數人很少問津。
pcb蚀刻工艺流程

pcb蚀刻工艺流程一、前言PCB(Printed Circuit Board)是电子产品中不可或缺的一个部分,它是电路板的主要组成部分之一。
PCB蚀刻工艺是制作PCB必不可少的一个环节,它通过化学反应将未覆盖铜层腐蚀掉,从而形成电路板上所需要的线路。
二、工艺流程1. 制作印刷光阻膜a. 印刷光阻膜是PCB蚀刻工艺中最重要的步骤之一。
首先需要准备好印刷光阻液和印刷机。
b. 将印刷光阻液均匀地涂在铜层上,并通过印刷机进行烘干和曝光处理。
c. 曝光后,将未曝光部分用显影液清洗干净,这样就可以得到需要的图案。
2. 蚀刻处理a. 在完成图案制作后,需要进行蚀刻处理。
首先需要准备好蚀刻液和搅拌器。
b. 将铜板放入蚀刻槽中,并加入足够量的蚀刻液。
启动搅拌器使其均匀混合。
c. 在一定时间内,蚀刻液将会腐蚀掉未覆盖印刷光阻的铜层,从而形成需要的线路。
3. 清洗处理a. 在完成蚀刻后,需要进行清洗处理。
首先需要准备好清洗液和清洗槽。
b. 将PCB放入清洗槽中,并加入足够量的清洗液。
启动搅拌器使其均匀混合。
c. 在一定时间内,清洗液将会将印刷光阻和其他杂质物质清除干净。
4. 钻孔处理a. 钻孔是PCB制作中另一个重要的步骤。
首先需要准备好钻头和钻床。
b. 将PCB放入钻床上,并使用合适大小的钻头进行钻孔。
c. 钻孔后,使用吸尘器将产生的金属屑清除干净。
5. 焊接处理a. 焊接是PCB制作中最后一个步骤。
首先需要准备好焊锡丝和焊锡台。
b. 将焊锡丝加热至熔化状态,并将其涂在需要焊接的元件上。
c. 将元件放置在PCB上,并使用焊锡台进行焊接处理。
三、注意事项1. 在进行印刷光阻膜制作时,需要注意光阻的均匀性和曝光时间。
2. 在进行蚀刻处理时,需要控制好蚀刻液的浓度和温度。
3. 在进行清洗处理时,需要注意清洗液的选择和清洗时间。
4. 在进行钻孔处理时,需要使用合适大小的钻头并注意安全。
5. 在进行焊接处理时,需要注意焊锡丝的熔化状态和元件与PCB之间的接触情况。
电子厂蚀刻部具体工作流程
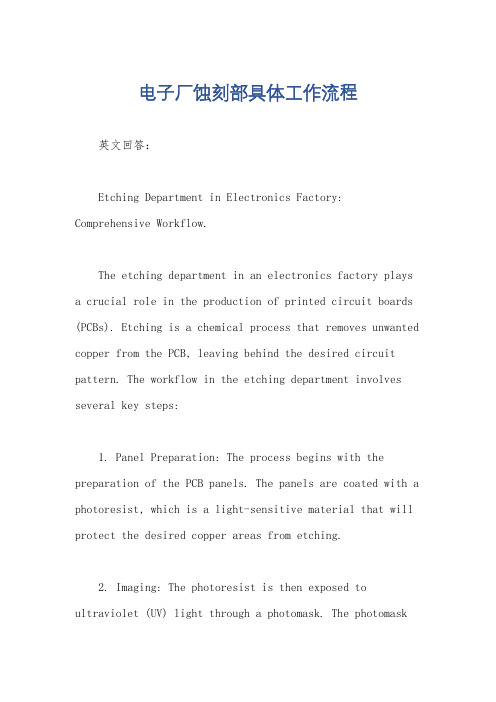
电子厂蚀刻部具体工作流程英文回答:Etching Department in Electronics Factory: Comprehensive Workflow.The etching department in an electronics factory plays a crucial role in the production of printed circuit boards (PCBs). Etching is a chemical process that removes unwanted copper from the PCB, leaving behind the desired circuit pattern. The workflow in the etching department involves several key steps:1. Panel Preparation: The process begins with the preparation of the PCB panels. The panels are coated with a photoresist, which is a light-sensitive material that will protect the desired copper areas from etching.2. Imaging: The photoresist is then exposed to ultraviolet (UV) light through a photomask. The photomaskdefines the circuit pattern that will be etched. The exposed areas of the photoresist will harden, while the unexposed areas will remain soft.3. Development: The exposed photoresist is then removed using a developer solution. This leaves behind the desired circuit pattern on the PCB panel.4. Etching: The PCB panel is then immersed in an etching solution, which removes the unprotected copper. The etching solution is usually composed of a strong acid, such as hydrochloric acid or ferric chloride.5. Stripping: After etching, the remaining photoresist is removed using a stripping solution. This leaves behind the finished PCB with the desired circuit pattern.6. Inspection: The etched PCBs are then inspected to ensure that they meet the specifications. This involves visual inspection as well as electrical testing.7. Storage: The finished PCBs are stored in acontrolled environment to prevent contamination or damage.中文回答:电子厂蚀刻部详细工作流程。
pcb蚀刻线宽控制

pcb蚀刻线宽控制在PCB蚀刻领域,线宽控制是一项非常重要的技术。
合理而准确地控制线宽可以确保电路板的性能和可靠性。
因此,本文将从蚀刻线宽控制的意义、控制方法和关键技术等方面进行论述。
一、蚀刻线宽控制的意义PCB蚀刻线宽控制是指在蚀刻工艺中,通过一系列合理的措施来控制电路板中导线的宽度,保证导线的精度和一致性。
蚀刻线宽控制的准确性直接影响电路板的功能和性能。
首先,蚀刻线宽控制能够保证电路板的稳定性。
由于电路板中导线的线宽是根据设计要求和信号传输要求确定的,若线宽偏差过大,会导致电路板性能不稳定甚至故障。
其次,蚀刻线宽控制还可以提高电路板的可靠性。
导线线宽的不一致性会导致电流分布不均,产生高阻抗、高温等问题。
通过控制蚀刻线宽,可以避免这些问题的产生,提高电路板的可靠性。
二、蚀刻线宽控制的方法蚀刻线宽控制通常采用以下几种方法:1.工艺参数控制蚀刻线宽控制的首要任务是调整好蚀刻液的组分和浓度、腐蚀液的酸碱度、蚀刻时间等工艺参数。
通过仔细调整这些参数,可以实现对蚀刻线宽的控制。
2.控制基材质量基材质量的好坏直接影响到蚀刻线宽的控制效果。
因此,在生产过程中,要选择质量可靠的基材,并对其进行检测和筛选,以确保电路板的稳定性和可靠性。
3.控制蚀刻液的物理特性蚀刻液的物理特性如粘度、温度等对线宽的控制有一定影响。
因此,在蚀刻过程中,需要对蚀刻液的物理特性进行监测和调控,以实现蚀刻线宽的精确控制。
关键技术1.光刻技术光刻技术是蚀刻线宽控制的核心技术之一。
在光刻工艺中,通过曝光和显影等步骤,将线路图案转移到光刻胶层上,经过酸碱性腐蚀液的腐蚀,最终得到所需的线宽。
2.高精度控制系统高精度控制系统是蚀刻线宽控制的关键。
通过采用先进的自动控制系统、高精度的传感器和仪表,可以实时监测和调整蚀刻过程中的各项参数,从而准确控制线宽的精度。
3.线宽测量技术线宽测量技术是蚀刻线宽控制的重要手段。
通过使用高精度的显微镜、投影仪和像素计算等设备,可以对线宽进行准确测量,并及时调整控制措施。
简述pcb板的工艺制作流程

简述pcb板的工艺制作流程
PCB(Printed Circuit Board)板,即印制电路板,是电子产品的重要组成部分。
以下是PCB 板的工艺制作流程简述:
1. 设计:使用电路板设计软件设计PCB 板的电路图和布局。
2. 制作光绘文件:将设计好的电路图和布局转换为光绘文件,用于制作电路板的底片。
3. 制作底片:使用光绘文件制作电路板的底片,底片上包含了电路板的电路图案。
4. 蚀刻:将底片覆盖在铜板上,通过蚀刻工艺将电路图案转移到铜板上。
5. 钻孔:在电路板上钻出需要连接元件的孔。
6. 电镀:通过电镀工艺在电路板的孔和表面镀上一层铜,以增强电路板的导电性。
7. 阻焊:在电路板的表面涂上一层阻焊剂,以防止电路板上的电路短路。
8. 丝印:在电路板上印刷元件的标识、型号等信息。
9. 切割:将电路板切割成需要的大小和形状。
10. 测试:对电路板进行电气测试,确保电路板的电路正常。
11. 组装:将元件安装到电路板上,完成电子产品的组装。
以上是PCB 板的基本工艺制作流程,不同类型的电路板可能会有一些差异,但总体流程相似。
PCB 板的制作需要高度的精度和技术,每一个环节都需要严格控制,以确保电路板的质量和可靠性。
PCB蚀刻技术及问题的分析

目录摘要 (1)1.引言 (5)2.PCB蚀刻技术 (5)2.1蚀刻方式 (6)2.2喷淋蚀刻的设备 (7)3.蚀刻反应的基本原理及故障和排除方法 (9)3.1酸性氯化铜蚀刻液 (9)3.2碱性氨类蚀刻液 (13)4.常见问题及改善和环境保护 (15)4.1设备的保养 (15)4.2生产过程中应注意的事项 (15)4.3生产安全与环境保护 (16)结语 (16)致谢 (17)参考文献 (17)1. 引言20世纪的40年代,英国人Paul Eisler博士及其助手,第一个采用了印制电路板(Printed Circuit Board,PCB)制造整机——收音机,并率先提出了印制电路板的概念。
经过多年的研究与生产实践,印制电路产业获得了很大的发展。
目前,PCB已广泛用于军事、通信、计算机、自动化等领域,成为绝大多数电子产品达到电路互连不可缺少的主要组成部件。
另外,随着集成电路的发明与应用,电子产品的小型化、高性能化,极大地推动了PCB向多层、深孔、微孔及微导电化的方向发展。
随着PCB工业的发展,各种导线之阻抗要求也越来越高,这必然要求导线的宽度控制更加严格. 在生活中的广泛运用,PCB的质量越来越好,越来越可靠,它是设计工艺也越来越多样化,也更加的完善。
蚀刻技术在PCB设计中的也越来越广泛。
蚀刻技术是利用化学感光材料的光敏特性, 在基体金属基片两面均匀涂敷感光材料采用光刻方法, 将胶膜板上栅网产显形状精确地复制到金属基片两面的感光层掩膜上通过显影去除未感光部分的掩膜, 将裸露的金属部分在后续的加工中与腐蚀液直接喷压接触而被蚀除, 最终获取所需的几何形状及高精度尺寸的产品技术蚀刻技术。
为了我们更好的学习了解PCB蚀刻工序的工艺技术及过程中易出现的问题。
但随着人类的进步和科技的发展,蚀刻技术面临着许多的新的课题,比如环境污染,工艺复杂、不简化,工艺材料对人体有害,部分资源循环利用性不强等。
本文就将结合上述问题对PCB蚀刻技术作些介绍,并对工艺改进途径方面做些探讨。
PCB电镀工艺流程介绍

PCB电镀工艺介绍线路板的电镀工艺,大约可以分类:酸性光亮铜电镀、电镀镍/金、电镀锡,文章介绍的是关于在线路板加工过程是,电镀工艺的技术以及工艺流程,以及具体操作方法.二.工艺流程:浸酸→全板电镀铜→图形转移→酸性除油→二级逆流漂洗→微蚀→二级逆流漂洗→浸酸→镀锡→二级逆流漂洗→逆流漂洗→浸酸→图形电镀铜→二级逆流漂洗→镀镍→二级水洗→浸柠檬酸→镀金→回收→2-3级纯水洗→烘干三.流程说明:(一)浸酸①作用与目的:除去板面氧化物,活化板面,一般浓度在5%,有的保持在10%左右,主要是防止水分带入造成槽液硫酸含量不稳定;②酸浸时间不宜太长,防止板面氧化;在使用一段时间后,酸液出现浑浊或铜含量太高时应及时更换,防止污染电镀铜缸和板件表面;③此处应使用C.P级硫酸;(二)全板电镀铜:又叫一次铜,板电,Panel-plating①作用与目的:保护刚刚沉积的薄薄的化学铜,防止化学铜氧化后被酸浸蚀掉,通过电镀将其加后到一定程度②全板电镀铜相关工艺参数:槽液主要成分有硫酸铜和硫酸,采用高酸低铜配方,保证电镀时板面厚度分布的均匀性和对深孔小孔的深镀能力;硫酸含量多在180克/升,多者达到240克/升;硫酸铜含量一般在75克/升左右,另槽液中添加有微量的氯离子,作为辅助光泽剂和铜光剂共同发挥光泽效果;铜光剂的添加量或开缸量一般在3-5ml/L,铜光剂的添加一般按照千安小时的方法来补充或者根据实际生产板效果;全板电镀的电流计算一般按2安/平方分米乘以板上可电镀面积,对全板电来说,以即板长dm×板宽dm×2×2A/DM2;铜缸温度维持在室温状态,一般温度不超过32度,多控制在22度,因此在夏季因温度太高,铜缸建议加装冷却温控系统;③工艺维护:每日根据千安小时来及时补充铜光剂,按100-150ml/KAH补充添加;检查过滤泵是否工作正常,有无漏气现象;每隔2-3小时应用干净的湿抹布将阴极导电杆擦洗干净;每周要定期分析铜缸硫酸铜(1次/周),硫酸(1次/周),氯离子(2次/周)含量,并通过霍尔槽试验来调整光剂含量,并及时补充相关原料;每周要清洗阳极导电杆,槽体两端电接头,及时补充钛篮中的阳极铜球,用低电流0。
PCB工艺流程说明

一.双面板工艺流程:覆铜板(CCL)下料(Cut)→钻孔(Drilling)→沉铜(PTH)→全板镀铜(Panel Plating)→图形转移(Pattern)油墨或干膜→图形电镀(Pattern plating)→蚀刻(Etch)→半检IQC→丝印阻焊油墨和字符油墨(SS)或贴阻焊干膜→热风整平或喷锡(HAL)→外形(Pounching)→成检(FQC)→电测试E-TEST→包装(Packaging)二.多层板工艺流程:内层覆铜板(CCL)铜箔(Copper Foil)下料(Cut)→内层图形制作(Inner-layer Pattern)→内层蚀刻(Inner-layer Etch)→内层黑氧化(Black-oxide)→层压or压合制程→钻孔(Drilling)→沉铜(PTH)→全板镀铜(Panel Plating)→外层蚀刻(Outer-layer Etch)→半检IQC→丝印阻焊油墨和字符油墨(SS)或贴阻焊干膜→热风整平或喷锡(HAL)→外形(Pounching)→成检(FQC)→电测试E-TEST→包装(Packaging)=三.流程说明:①下料:从一定板厚和铜箔厚度的整张覆铜板大料上剪出便于加工的尺寸,重量减少大约10-15%;②钻孔:在板上按电脑钻孔程序钻出导电孔或插件孔;板重量大约减少5%;③沉铜:在钻出的孔内沉积一层薄薄的化学铜,厚度大约在0。
3-2um,重量增加较少,目的是在不导电的环氧玻璃布基材(或其他基材)通过化学方法沉上一层铜,便于后面电镀导通形成线路;④全板镀铜:主要是为加厚保护那层薄薄的化学铜以防其在空气中氧化,形成孔内无铜或破洞;⑤图形制作(图形转移):包括内层图形制作,在板上贴上干膜或丝印上图形抗电镀油墨,经曝光,显影后,做出线路图形;重量减少较小。
⑥图形电镀:在已做好图形线路的板上进行线路加厚镀铜,使孔内和线路铜厚达到一定厚度,可以负载一定的电流;重量增加大约15%;⑦蚀刻:包括内层蚀刻,褪掉图形油墨或干膜,蚀刻掉多余的铜箔从而得到导电线路图形;⑧层压:把内层与半固化片,铜箔叠合一起经高温压制成多层板,4层板需要一张内层,两张铜箔;6层板需要两张内层,两张铜箔。
蚀刻工艺(酸性、碱性、微蚀)

PCB外层电路的蚀刻工艺在印制电路加工中﹐氨性蚀刻是一个较为精细和覆杂的化学反应过程, 却又是一项易于进行的工作。
只要工艺上达至调通﹐就可以进行连续性的生产, 但关键是开机以后就必需保持连续的工作状态﹐不适宜断断续续地生产。
蚀刻工艺对设备状态的依赖性极大, 故必需时刻使设备保持在良好的状态。
目前﹐无论使用何种蚀刻液﹐都必须使用高压喷淋﹐而为了获得较整齐的侧边线条和高质量的蚀刻效果﹐对喷嘴的结构和喷淋方式的选择都必须更为严格。
对于优良侧面效果的制造方式﹐外界均有不同的理论、设计方式和设备结构的研究, 而这些理论却往往是人相径庭的。
但是, 有一条最基本的原则已被公认并经化学机理分析证实﹐就是尽速让金属表面不断地接触新鲜的蚀刻液。
在氨性蚀刻中﹐假定所有参数不变﹐那么蚀刻的速率将主要由蚀刻液中的氨(NH3)来决定。
因此, 使用新鲜溶液与蚀刻表面相互作用﹐其主要目的有两个﹕冲掉刚产生的铜离子及不断为进行反应供应所需要的氨(NH3)。
在印制电路工业的传统知识里﹐特别是印制电路原料的供货商们皆认同﹐并得经验证实﹐氨性蚀刻液中的一价铜离子含量越低﹐反应速度就越快。
事实上﹐许多的氨性蚀刻液产品都含有价铜离子的特殊配位基(一些复杂的溶剂)﹐其作用是降低一价铜离子(产品具有高反应能力的技术秘诀)﹐可见一价铜离子的影响是不小的。
将一价铜由5000ppm降至50ppm, 蚀刻速率即提高一倍以上。
由于在蚀刻反应的过程中会生成大量的一价铜离子, 而一价铜离子又总是与氨的络合基紧紧的结合在一起﹐所以要保持其含量近于零是十分困难的。
而采用喷淋的方式却可以达到通过大气中氧的作用将一价铜转换成二价铜, 并去除一价铜, 这就是需要将空气通入蚀刻箱的一个功能性的原因。
但是如果空气太多﹐又会加速溶液中的氨的损失而使PH值下降﹐使蚀刻速率降低。
氨在溶液中的变化量也是需要加以控制的, 有一些用户采用将纯氨通入蚀刻储液槽的做法, 但这样做必须加一套PH计控制系统, 当自动监测的PH结果低于默认值时﹐便会自动进行溶液添加。
pcb蚀刻工艺流程

pcb蚀刻工艺流程PCB蚀刻工艺流程。
PCB蚀刻工艺是印刷电路板制造过程中的重要环节,其质量直接影响到电路板的性能和稳定性。
下面将详细介绍PCB蚀刻工艺的流程及注意事项。
首先,准备工作。
在进行PCB蚀刻之前,需要准备好所需的材料和设备,包括铜板、感光胶板、蚀刻液、蚀刻机等。
确保工作环境整洁,避免灰尘和杂质对蚀刻过程造成影响。
其次,制作感光胶板。
将感光胶板覆盖在铜板上,然后利用光照技术将电路图案转移到感光胶板上。
接着进行显影、蚀刻,将不需要的铜层去除,留下所需的电路图案。
然后,蚀刻。
将处理好的铜板放入蚀刻机中,根据设计要求设定蚀刻时间和温度,启动蚀刻机进行蚀刻。
在蚀刻过程中需要不断观察蚀刻情况,确保蚀刻深度和精度达到要求。
接着,清洗。
蚀刻完成后,将电路板取出,用清洁剂进行清洗,去除表面的感光胶和蚀刻液残留。
清洗后的电路板表面应该干净、光滑,不得有任何杂质和残留物。
最后,检验。
对蚀刻完成的电路板进行检验,包括外观检查、导通测试等,确保电路板质量符合要求。
若发现问题,及时进行修复或重新制作,直到达到要求的标准。
在进行PCB蚀刻工艺流程时,需要注意以下几点:1. 操作规范。
在操作过程中,要严格按照工艺要求进行操作,避免因操作不当导致的质量问题。
2. 设备维护。
定期对蚀刻机等设备进行维护保养,确保设备的正常运转,避免因设备故障影响蚀刻质量。
3. 安全防护。
在蚀刻过程中,要做好安全防护措施,避免腐蚀液溅射造成伤害。
4. 环境控制。
保持蚀刻工作环境的清洁和稳定,避免外界环境对蚀刻过程的影响。
总之,PCB蚀刻工艺流程是一个关键的环节,需要严格按照标准操作,确保电路板质量达到要求。
只有在每个细节都做到位,才能生产出高质量的印刷电路板。
pcb软板制造工艺流程

pcb软板制造工艺流程PCB软板制造工艺流程是指将软板制造过程中所需的各项工艺进行串联,形成一个完整的生产流程。
下面是一个大致的PCB软板制造工艺流程,供参考:一、原材料准备1.1:挤出膜准备:将聚酰亚胺作为基材,进行挤出膜制备。
1.2:涂布:将挤出膜切割成需要的尺寸,然后在表面涂布蚀刻胶。
二、图形制作2.1:曝光:将制作好的电路图按一定的规则制作到透明的基材上。
2.2:显影:将曝光后的基材通过显影的方式去掉不需要的电路图案。
2.3:蚀刻:将显影后的基材放入酸浴中进行蚀刻,将不需要的金属层去除。
三、制架3.1:冲孔:将制作好的软板放置在冲孔机上,按照需求冲孔。
3.2:固定:将冲孔好的软板放置在制架上,通过固定工艺将其固定在位。
四、覆铜4.1:钛靶溅射:将软板放入真空腔室中,通过钛靶溅射技术在软板表面形成钛层。
4.2:电铜:在钛层上通过电镀的方式制作出一层厚度适中的铜层。
五、复合5.1:去除保护层:将覆铜后的软板放入酸浴中清洗,去除保护层。
5.2:薄化:将复合前的软板放入薄化机中进行薄化处理。
六、全割6.1:切割:将复合后的软板放置在切割机上,按照需要的尺寸进行切割。
七、压合7.1:装夹:将切割好的软板放置在高温高压机中,进行装夹处理。
7.2:压合:通过高温高压的方式将软板中的各个层次进行压合。
八、成型8.1:冲孔:将压合好的软板放置在冲孔机上,按照需要进行冲孔。
8.2:裁剪:将冲孔好的软板放置在裁剪机上,按照需要进行裁剪。
九、测试9.1:电性能测试:将制造好的软板进行电性能测试,检查是否符合要求。
9.2:外观检查:对制造好的软板进行外观检查,确保无明显的缺陷。
十、包装10.1:清洁:对测试合格的软板进行清洁处理。
10.2:包装:将清洁好的软板进行包装,以便运输、存储等操作。
以上所述为PCB软板制造工艺的主要流程,实际生产中还需要结合具体的需求进行调整和优化。
同时,为了保证产品质量,还需要进行严格的质量控制和监测。
- 1、下载文档前请自行甄别文档内容的完整性,平台不提供额外的编辑、内容补充、找答案等附加服务。
- 2、"仅部分预览"的文档,不可在线预览部分如存在完整性等问题,可反馈申请退款(可完整预览的文档不适用该条件!)。
- 3、如文档侵犯您的权益,请联系客服反馈,我们会尽快为您处理(人工客服工作时间:9:00-18:30)。
PCB的蚀刻工艺及过程控制
印刷线路板从光板到显出线路图形的过程是一个比较复杂的物理和化学反应的过程,本文就对其最后的一步--蚀刻进行解析。
目前,印刷电路板(PCB)加工的典型工艺采用"图形电镀法"。
即先在板子外层需保留的铜箔部分上,也就是电路的图形部分上预镀一层铅锡抗蚀层,然后用化学方式将其余的铜箔腐蚀掉,称为蚀刻。
一.蚀刻的种类
要注意的是,蚀刻时的板子上面有两层铜。
在外层蚀刻工艺中仅仅有一层铜是必须被全部蚀刻掉的,其余的将形成最终所需要的电路。
这种类型的图形电镀,其特点是镀铜层仅存在于铅锡抗蚀层的下面。
另外一种工艺方法是整个板子上都镀铜,感光膜以外的部分仅仅是锡或铅锡抗蚀层。
这种工艺称为“全板镀铜工艺“。
与图形电镀相比,全板镀铜的最大缺点是板面各处都要镀两次铜而且蚀刻时还必须都把它们腐蚀掉。
因此当导线线宽十分精细时将会产生一系列的问题。
同时,侧腐蚀会严重影响线条的均匀性。
在印制板外层电路的加工工艺中,还有另外一种方法,就是用感光膜代替金属镀层做抗蚀层。
这种方法非常近似于内层蚀刻工艺,可以参阅内层制作工艺中的蚀刻。
目前,锡或铅锡是最常用的抗蚀层,用在氨性蚀刻剂的蚀刻工艺
中.氨性蚀刻剂是普遍使用的化工药液,与锡或铅锡不发生任何化学反应。
氨性蚀刻剂主要是指氨水/氯化氨蚀刻液。
此外,在市场上还可以买到氨水/硫酸氨蚀刻药液。
以硫酸盐为基的蚀刻药液,使用后,其中的铜可以用电解的方法分离出来,因
此能够重复使用。
由于它的腐蚀速率较低,一般在实际生产中不多见,但有望用在无氯蚀刻中。
有人试验用硫酸-双氧水做蚀刻剂来腐蚀外层图形。
由于包括经济和废液处理方面等许多原因,这种工艺尚未在商用的意义上被大量采用.更进一步说,硫酸-双氧水,不能用于铅锡抗蚀层的蚀刻,而这种工艺不是PCB外层制作中的主要方法,故决大多数人很少问津。
二.蚀刻质量及先期存在的问题
对蚀刻质量的基本要求就是能够将除抗蚀层下面以外的所有铜
层完全去除干净,止此而已。
从严格意义上讲,如果要精确地界定,那么蚀刻质量必须包括导线线宽的一致性和侧蚀程度。
由于目前腐蚀液的固有特点,不仅向下而且对左右各方向都产生蚀刻作用,所以侧蚀几乎是不可避免的。
侧蚀问题是蚀刻参数中经常被提出来讨论的一项,它被定义为侧蚀宽度与蚀刻深度之比, 称为蚀刻因子。
在印刷电路工业中,它的变化范围很宽泛,从1:1到1:5。
显然,小的侧蚀度或低的蚀刻因子是最令人满意的。
蚀刻设备的结构及不同成分的蚀刻液都会对蚀刻因子或侧蚀度
产生影响,或者用乐观的话来说,可以对其进行控制。
采用某些添加剂可以降低侧蚀度。
这些添加剂的化学成分一般属于商业秘密,各自的研制者是不向外界透露的。
从许多方面看,蚀刻质量的好坏,早在印制板进入蚀刻机之前就已经存在了。
因为印制电路加工的各个工序或工艺之间存在着非常紧密的内部联系,没有一种不受其它工序影响又不影响其它工艺的工序。
许多被认定是蚀刻质量的问题,实际上在去膜甚至更以前的工艺中已经存在了。
对外层图形的蚀刻工艺来说,由于它所体现的“倒溪”现像比绝大多数印制板工艺都突出,所以许多问题最后都反映在它上面。
同时,这也是由于蚀刻是自贴膜,感光开始的一个长系列工艺中的最后一环,之后,外层图形即转移成功了。
环节越多,出现问题的可能性就越大。
这可以看成是印制电路生产过程中的一个很特殊的方面。
从理论上讲,印制电路进入到蚀刻阶段后,在图形电镀法加工印制电路的工艺中,理想状态应该是:电镀后的铜和锡或铜和铅锡的厚度总和不应超过耐电镀感光膜的厚度,使电镀图形完全被膜两侧的“墙”挡住并嵌在里面。
然而,现实生产中,全世界的印制电路板在电镀后,镀层图形都要大大厚于感光图形。
在电镀铜和铅锡的过程中,由于镀层高度超过了感光膜,便产生横向堆积的趋势,问题便由此产生。
在线条上方覆盖着的锡或铅锡抗蚀层向两侧延伸,形成了“沿”,把小部分感光膜盖在了“沿”下面。
锡或铅锡形成的“沿”使得在去膜时无法将感光膜彻底去除干净,留下一小部分“残胶”在“沿”的下面。
“残胶”或“残膜”留在了抗蚀剂“沿”的下面,将造成不完全的蚀刻。
线条在蚀刻后两侧形成“铜根”,铜根使线间距变窄,造成印制板不符合甲方要求,甚至可能被拒收。
由于拒收便会使PCB的生产成本大大增加。
另外,在许多时候,由于反应而形成溶解,在印制电路工业中,残膜和铜还可能在腐蚀液中形成堆积并堵在腐蚀机的喷嘴处和耐酸泵里,不得不停机处理和清洁,而影响了工作效率。
三.设备调整及与腐蚀溶液的相互作用关系
在印制电路加工中,氨性蚀刻是一个较为精细和复杂的化学反应过程。
反过来说它又是一个易于进行的工作。
一旦工艺上调通,就可以连续进行生产。
关键是一旦开机就需保持连续工作状态,不宜干干停停。
蚀刻工艺在极大的程度上依赖设备的良好工作状态。
就目前来讲,无论使用何种蚀刻液,必须使用高压喷淋,而且为了获得较整齐的线条侧边和高质量的蚀刻效果,必须严格选择喷嘴的结构和喷淋方式。
为得到良好的侧面效果,出现了许多不同的理论,形成不同的设计方式和设备结构。
这些理论往往是大相径庭的。
但是所有有关蚀刻的理论都承认这样一条最基本的原则,即尽量快地让金属表面不断的接触新鲜的蚀刻液。
对蚀刻过程所进行的化学机理分析也证实了上述观点。
在氨性蚀刻中,假定所有其它参数不变,那么
蚀刻速率主要由蚀刻液中的氨(NH3)来决定。
因此用新鲜溶液与蚀刻表面作用,其目的主要有两个:一是冲掉刚刚产生的铜离子;二是不断提供进行反应所需要的氨(NH3)。
在印制电路工业的传统知识里,特别是印制电路原料的供应商们,大家公认,氨性蚀刻液中的一价铜离子含量越低,反应速度就越快.这已由经验所证实。
事实上,许多的氨性蚀刻液产品都含有一价铜离子的特殊配位基(一些复杂的溶剂),其作用是降低一价铜离子(这些即是他们的产品具有高反应能力的技术秘诀),可见一价铜离子的影响是不小的。
将一价铜由5000ppm降至
50ppm,蚀刻速率会提高一倍以上。
由于蚀刻反应过程中生成大量的一价铜离子,又由于一价铜离子总是与氨的络合基紧紧的结合在一起,所以保持其含量近于零是十分困难的。
通过大气中氧的作用将一价铜转换成二价铜可以去除一价铜。
用喷淋的方式可以达到上述目的。
这就是要将空气通入蚀刻箱的一个功能性的原因。
但是如果空气太多,又会加速溶液中的氨损失而使PH值下降,其结果仍使蚀刻速率降低。
氨在溶液中也是需要加以控制的变化量。
一些用户采用将纯氨通入蚀刻储液槽的做法。
这样做必须加一套PH计控制系统。
当自动测得的PH结果低于给定值时,溶液便会自动进行添加。
在与此相关的化学蚀刻(亦称之为光化学蚀刻或PCH)领域中,研究工作已经开始,并达到了蚀刻机结构设计的阶段。
在这种方法
中,所使用的溶液为二价铜,不是氨-铜蚀刻。
它将有可能被用在印制电路工业中。
在PCH工业中,蚀刻铜箔的典型厚度为5到10密耳(mils),有些情况下厚度则相当大。
它对蚀刻参量的要求经常比PCB工业中的更为苛刻。
四.关于上下板面,导入边与后入边蚀刻状态不同的问题
大量的涉及蚀刻质量方面的问题都集中在上板面上被蚀刻的部分。
了解这一点是十分重要的。
这些问题来自印制电路板的上板面蚀刻剂所产生的胶状板结物的影响。
胶状板结物堆积在铜表面上,一方面影响了喷射力,另一方面阻挡了新鲜蚀刻液的补充,造成了蚀刻速度的降低。
正是由于胶状板结物的形成和堆积使得板子的上下面图形的蚀刻程度不同。
这也使得在蚀刻机中板子先进入的部分容易蚀刻的彻底或容易造成过腐蚀,因为那时堆积尚未形成,蚀刻速度较快。
反之,板子后进入的部分进入时堆积已形成,并减慢其蚀刻速度。
五.蚀刻设备的维护
蚀刻设备维护的最关键因素就是要保证喷嘴的清洁,无阻塞物而使喷射通畅。
阻塞物或结渣会在喷射压力作用下冲击版面。
假如喷嘴不洁,那么会造成蚀刻不均匀而使整块PCB报废。
明显地,设备的维护就是更换破损件和磨损件,包括更换喷嘴,喷嘴同样存在磨损的问题。
除此之外,更为关键的问题是保持蚀刻机不存在结渣,在许多情况下都会出现结渣堆积.结渣堆积过多,甚至会对蚀刻液的化学平衡产生影响。
同样,如果蚀刻液出
现过量的化学不平衡,结渣就会愈加严重。
结渣堆积的问题怎么强调都不过分。
一旦蚀刻液突然出现大量结渣的情况,通常是一个信号,即溶液的平衡出现问题。
这就应该用较强的盐酸作适当地清洁或对溶液进行补加。
残膜也可以产生结渣物,极少量的残膜溶于蚀刻液中,然后形成铜盐沉淀。
残膜所形成的结渣说明前道去膜工序不彻底。
去膜不良往往是边缘膜与过电镀共同造成的结果。