酸性蚀刻液培训教材
ETCH(PCB蚀刻培训教材)解析

膜不净;药水浓度高,会导致板面氧化。
褪膜段喷嘴要及时清洗,防止碎片堵塞喷嘴,
影响褪膜质量
二.碱性蚀刻 1.工艺流程 褪膜 蚀刻 新液洗 褪锡
(整孔)
注:整孔工序仅适用于沉金制板
2.工艺原理 -褪膜
定义:用褪菲林液将线路板面上盖住的菲林褪去,露 出未经线路加工的铜面. 经电镀工序后的干膜在碱性褪膜液下溶解或部分成 片状脱落,我司使用的是3% 0.5%氢氧化钠溶液.
水池效应
在蚀刻过程中,线路板水平通过蚀刻机时, 因重力作用在板上面新鲜药液被积水阻挠,无 法有效和铜面反应,称之水池效应。而下面 则无此现象。
蚀刻因子
蚀刻液在蚀刻过程中,不仅向下而且对左右各 方向都产生蚀刻作用,侧蚀是不可避免的。侧蚀宽 度与蚀刻深度之比称之为蚀刻因子。
A 铜线路 B D C
抗蚀层
原理:
CO3-2 + Resist COOH
HCO3- + Resist COO-
CO3-2 主要为Na2CO3 或K2CO3 Resist TOOH为干膜及油墨中反应官能基团 利用CO3-2与阻剂中羧基(COOH)进行酸碱中和反应, 形成COO-和H CO3- ,使阻剂形成阴离子团而剥离。
-蚀刻
³ ° å å » ú × Ô ¶ ¯ Ó Ò ¼ © ¸ × ´ ¿ Ê Ì » ú
400(800) 500X2
Ê Ä Í ¤
480(800)
Na2CO3 ý Å ³ Ý ¼ Á Cu2+± È Ö Ø HCl « Ñ Ë õ Ë ® H2O2 NaOH ý Å ³ Ý ¼ Á
3.2kg 640ml(640ml)
¸× ± ¢
冲板、褪膜、褪菲林换药和补药标准
酸性蚀刻工艺流程教材

用于清洗板材表面,去除残留的蚀刻液和其他杂质。
酸性蚀刻的辅助材料
添加剂
为了改善蚀刻效果,可以在蚀刻液中加入一些 添加剂,如缓蚀剂、加速剂等。
检测试剂
用于检测蚀刻液的浓度和酸碱度,确保其处于 最佳工作状态。
废液处理剂
用于处理蚀刻过程中产生的废液,减少环境污染。
05 酸性蚀刻的环保与安全
酸性蚀刻的环保措施
医疗器械
医疗器械如手术刀、针头 等,通过酸性蚀刻工艺提 高表面的抗滑性和防锈性。
酸性蚀刻的优缺点
优点
酸性蚀刻工艺具有操作简单、成本低 廉、环保等优点,可以快速实现金属 表面的处理,提高金属表面的美观度 和使用性能。
缺点
酸性蚀刻工艺可能会对金属材料产生 一定的腐蚀和损伤,影响金属材料的 机械性能和耐腐蚀性能,因此需要合 理控制蚀刻时间和温度等参数。
废气处理
酸性蚀刻过程中产生的废气应经 过处理后再排放,以减少对大气 的污染。常用的废气处理方法包 括吸附法、吸收法、燃烧法等。
废水处理
酸性蚀刻过程中产生的废水应经 过处理后再排放,以减少对水体 的污染。废水处理方法包括沉淀 法、过滤法、生物处理法等。
废渣处理
酸性蚀刻过程中产生的废渣应进 行妥善处理,以减少对环境的污 染。废渣可以采取填埋、焚烧、 回收利用等方式进行处理。
05
04
酸性蚀刻
将涂布好的金属板材放入酸性蚀刻溶 液中,在一定温度和时间下进行蚀刻。
电路板的酸性蚀刻
总结词
在电子工业中,电路板的制作过程中酸性 蚀刻技术是关键步骤之一,用于形成导电 线路和图案。
后处理
去除抗蚀剂,进行电镀、焊接等处理,完 成电路板的制作。
准备材料
选择合适的基材,如FR4、CEM-1等,并 制备好电路图形。
蚀刻培训教材
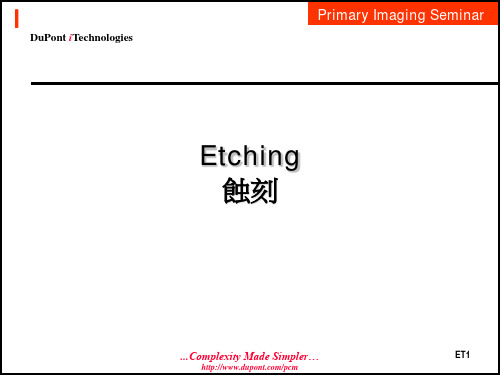
plexity Made Simpler…
/pcm
ET15
l DuPont iTechnologies
plexity Made Simpler…
ET6
/pcm
l DuPont iTechnologies
Primary Imaging Seminar
Oscillating Spray Mechanism (噴灑擺動機構)
INTERLOCKING SINUSOIDAL CURVES OF OSCILLATING SPRAY MECHANISM
5.0
4.5 Y= - 0.2892x2 + 3.2956x + 32.084
4.0 19 IPM Etch Speed (0.483 m/min)
3.5
3.0
A
B
C
D
E
F
G
H
I
J
COLUMN LABEL
plexity Made Simpler…
/pcm
ET19
l DuPont iTechnologies
Primary Imaging Seminar
Cupric Chloride Etchant 氯化銅蝕刻液
Chemistry 化學反應 Critical Variable 重要變數 Process Controls 製程控製 Productivity and Fine Line Variable 產量和細線路的變數 Performance Ratings 性能等級
l DuPont iTechnologies
蚀刻培训讲义
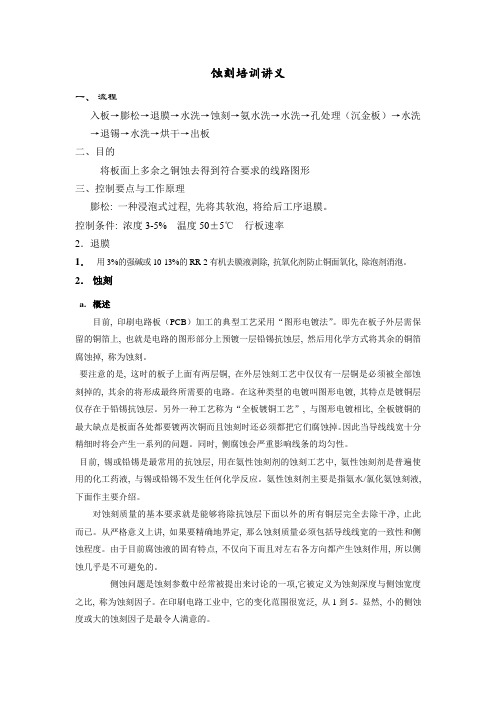
蚀刻培训讲义一、流程入板→膨松→退膜→水洗→蚀刻→氨水洗→水洗→孔处理(沉金板)→水洗→退锡→水洗→烘干→出板二、目的将板面上多余之铜蚀去得到符合要求的线路图形三、控制要点与工作原理膨松: 一种浸泡式过程, 先将其软泡, 将给后工序退膜。
控制条件: 浓度3-5% 温度50±5℃行板速率2.退膜1.用3%的强碱或10-13%的RR-2有机去膜液剥除, 抗氧化剂防止铜面氧化, 除泡剂消泡。
2.蚀刻a.概述目前, 印刷电路板(PCB)加工的典型工艺采用“图形电镀法”。
即先在板子外层需保留的铜箔上, 也就是电路的图形部分上预镀一层铅锡抗蚀层, 然后用化学方式将其余的铜箔腐蚀掉, 称为蚀刻。
要注意的是, 这时的板子上面有两层铜, 在外层蚀刻工艺中仅仅有一层铜是必须被全部蚀刻掉的, 其余的将形成最终所需要的电路。
在这种类型的电镀叫图形电镀, 其特点是镀铜层仅存在于铅锡抗蚀层。
另外一种工艺称为“全板镀铜工艺”, 与图形电镀相比, 全板镀铜的最大缺点是板面各处都要镀两次铜而且蚀刻时还必须都把它们腐蚀掉。
因此当导线线宽十分精细时将会产生一系列的问题。
同时, 侧腐蚀会严重影响线条的均匀性。
目前, 锡或铅锡是最常用的抗蚀层, 用在氨性蚀刻剂的蚀刻工艺中, 氨性蚀刻剂是普遍使用的化工药液, 与锡或铅锡不发生任何化学反应。
氨性蚀刻剂主要是指氨水/氯化氨蚀刻液, 下面作主要介绍。
对蚀刻质量的基本要求就是能够将除抗蚀层下面以外的所有铜层完全去除干净, 止此而已。
从严格意义上讲, 如果要精确地界定, 那么蚀刻质量必须包括导线线宽的一致性和侧蚀程度。
由于目前腐蚀液的固有特点, 不仅向下而且对左右各方向都产生蚀刻作用, 所以侧蚀几乎是不可避免的。
侧蚀问题是蚀刻参数中经常被提出来讨论的一项,它被定义为蚀刻深度与侧蚀宽度之比, 称为蚀刻因子。
在印刷电路工业中, 它的变化范围很宽泛, 从1到5。
显然, 小的侧蚀度或大的蚀刻因子是最令人满意的。
蚀刻退锡培训教材资料
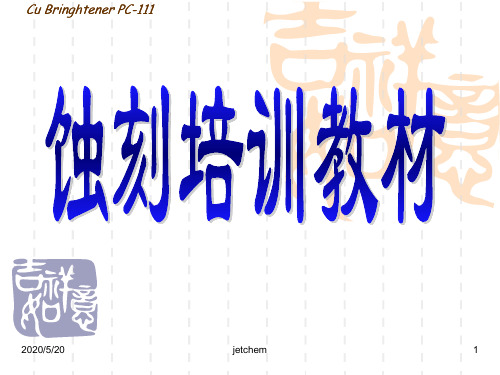
12
Cu Bringhtener PC-111
酸性蚀刻加药器简易图
2019/4/11
jetchem
13
Cu Bringhtener PC-111
四、影响蚀刻速率因素分析
碱性蚀刻速率的影响因素 影响 因素 偏高 偏低 攻击金属抗蚀 层;易沉淀,还 会堵塞泵或喷 嘴,而影响蚀刻 效果。 蚀刻速率低,且 溶液控制困难 控制 范围
2019/4/11 jetchem 10
Cu Bringhtener PC-111
再生方法 氧气或压 缩空气再 生
反应方程式 2Cu2Cl2+4HCl+O2 → 4CuCl2+2H2O
优点 便宜
缺点 再生反应 速率很低
氯气再生
Cu2Cl2+Cl2 → 2CuCl2
成本低, 氯气易溢出, 再生速 会 率快 污染环境 环保易 控制 易分解爆 炸且昂贵
故障类型 蚀刻速率降低
由于工艺参数控制不当引 检查及调整温度、喷淋压力、溶液比重、PH 起的 值和氯化铵的含量等工艺参数到规定值 1、氨的含量过低 2、水稀释过量 3、溶液比重过大 1、调整PH值到达工艺规定值; 2、调整严格按工艺规定执行; 3、排放出部分比重高的溶液,经分析后补 加氯化铵和氨的水溶液,使蚀刻液的比 重调整到工艺允许的范围 1、调整到合适的PH值; 2、调整氯离子尝试到规定值
2019/4/11 jetchem 20
Cu Bringhtener PC-111
水池效应
图3 上下板面喷淋液流向
板面流 向
2019/4/11
jetchem
图4 喷淋液在板面成水池
21
Cu Bringhtener PC-111
蚀刻教材(3F)
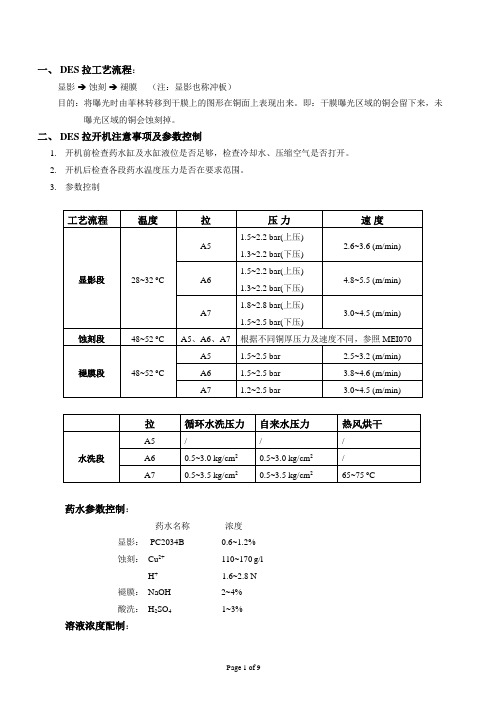
一、DES拉工艺流程:显影→蚀刻→褪膜(注:显影也称冲板)目的:将曝光时由菲林转移到干膜上的图形在铜面上表现出来。
即:干膜曝光区域的铜会留下来,未曝光区域的铜会蚀刻掉。
二、DES拉开机注意事项及参数控制1.开机前检查药水缸及水缸液位是否足够,检查冷却水、压缩空气是否打开。
2.开机后检查各段药水温度压力是否在要求范围。
3.参数控制药水参数控制:药水名称浓度显影: PC2034B 0.6~1.2%蚀刻: Cu2+ 110~170g/lH+ 1.6~2.8 N褪膜: NaOH 2~4%酸洗: H2SO4 1~3%溶液浓度配制:显影缸:A5:10LT A6:25LT A7:25LT褪膜缸:A5:27kg A6:30kg A7:30kg酸洗缸:A5:3LT A6:3LT A7:3LT配药房:显影开料缸:PC2031B 25LT褪膜开料缸:NaOH 25kg三、冲板注意事项:1.在批量冲板前,首先必须做首板,待拉长恢复,首板OK后方可生产。
2.对板面铜厚不一以及光面板/细线板,一定要按照拉长所要求的方式去放板,同时注意板的型号、层次,必须保证不放错板。
3.对于冲大背板,必须站起来冲板;对于板厚小于5mil、H/H以下的板(根据拉长要求)必须带板条冲板。
4.冲板时,板与板之间的距离保持大于2inch(即5.08cm)5.在撕膜时,板两面保护膜要同时撕下。
不允许撕了一面然后再撕另一面,避免菲林碎粘到板面,导致蚀板不净现象。
6.在撕膜时,一定要注意严防撕膜不净的问题发生,且刀片不能划入图形,以防划伤,导致报废。
7.放板时,必须双手拿板,轻拿轻放,发现有板弯或板角翘,一定将其抚平,并放好放正以防卡板。
8.对每够一批量LOT卡时,用一胶片隔开,作为该批板已完的标识。
四、执漏注意事项:1.在检查板面时,必须戴黑色胶手套,手拿板边。
严防显影不净,显影过度,撕膜不净的板流入蚀刻。
2.在操作过程中,必须做到小心操作,不要划伤板面,发现显影不净等不良板时,即时通知冲板员工停放,然后通知拉长解决。
酸性蚀刻工艺流程教材PPT课件

• 随着铜的蚀刻,溶液中的一价铜越来越 多,蚀刻能力很快就会下降,以至最后 失去效能。
• 为了保持连续的蚀刻能力,可以通过各 种方式对蚀刻液进行再生,使一价铜重 新转变成二价铜,达到正常蚀刻的工艺 标准。
.
3.影响蚀刻速率的因素 影响蚀刻速率的因素较多,但影响较大的是蚀刻
度对加速溶液的流动性和减小蚀刻液的粘度,提高蚀刻速率起
着很重要的作用。但温度过高,也容易引起蚀刻液中一些化学
成份挥发,造成蚀刻液中化学组份比例失调,同时温度过高,
可能会造成高聚物抗蚀层的被破坏以及影响蚀刻设备的使用寿
命。因此,蚀刻液温度一般控制在一定的工艺范围内。
.
3. 采用的铜箔厚度:铜箔的厚度对电路图形的导线密度有 着重要影响。铜箔薄,蚀刻时间短,侧蚀就很小;反之, 侧蚀就很大。所以,必须根据设计技术要求和电路图形的 导线密度及导线精度要求,来选择铜箔厚度。同时铜的延 伸率、表面结晶构造等,都会构成对蚀刻液特性的直接影 响。
2)操作方式的控制
视图形导线疏密走向确定放板的方向,确保蚀刻液在基板面流动
快,不会产生蚀刻液堆积的问题。
在蚀刻时将导线密面朝下,导线疏的面朝上,以改善电路图形两
面蚀刻的均匀性。
.
六、 常见故障及处理方法:
故障类型
产生主要原因
解决办法
蚀刻速率降低 蚀刻液出现沉淀
1. 蚀刻液的温度低
2.淋压力过低
3.蚀刻液的化学组份控制失 调 络合剂氯离子不足
达到高的蚀刻质量; • 溶铜量大; • 蚀刻液容易再生与回收,减少污染。 2.蚀刻原理 • 在蚀刻过程中,氯化铜中的二价铜具有氧化性,
能将印制电路板面上的铜氧化成一价铜, 其化学反应如下: 蚀刻反应: Cu+Cucl2→ 2Cucl↓
IDF工序培训教材
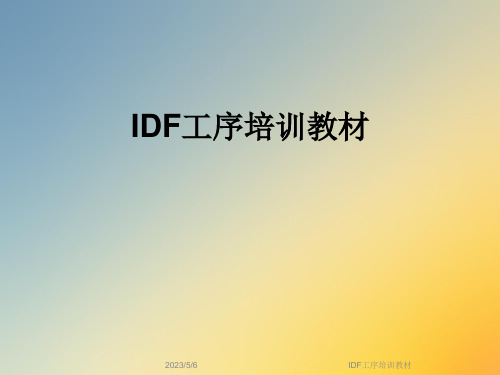
三、涂布(Roller Coating)
1.概述:
将树脂油墨和溶剂的混合物均匀的涂在经过洁净、粗化的覆铜箔板上, 溶剂经过烘箱挥发,使油墨与板牢牢结合。
2.涂布流程:
清洁→进板→涂膜→烘干→冷却→清洁→出板→收板
3.参数控制:
油墨温度:20-26℃ 油墨粘度:35-45 sec 涂布速度:2.5-3.5m/min(视板厚而定) 油墨厚度:9-11um 烘板温度:根据板厚选择对应的温度曲线程序,一般140℃左右。
3.干膜结构:
❖ 聚乙烯垫层:支撑抗蚀层的载体,曝 光后显影前人工除去
❖ 抗蚀层:感光主体
❖ 聚脂盖层:保护膜,避免在卷膜时每 层抗蚀层与垫层之间相互粘连,贴膜 于铜箔前贴膜机将其自动剥离。
4.贴膜三要素:
v 压力:压力过小易导致气泡、贴膜不牢 v 温度:贴膜温度过高,干膜可能变脆、起皱,可能造成挥发成分急剧
v 涂膜面积达到60万平方英尺需更换涂膜轮
四、曝光
1.概述:
在紫外光照射下,药膜进行交联聚 合反应,在板面上初步形成图象。 曝光机都是使用点光源。
2.流程
清洁曝光机→装菲林→放板→抽真空 →自动曝光→收板
3.装菲林:
菲林打孔后装上曝光机自动对位,对 位完成后曝光盘会将菲林吸附其上, 在菲林四周贴上红胶带固定,并在菲 林四周加上厚度合适的垫条。
干膜显影点控制在40-60%,湿膜显影点控制在30-50%。
3.蚀刻
❖ 酸性氯化铜蚀刻液 主要成分为氯化铜、盐酸、氯化钠,通过 添加盐酸和氯酸钠再生
❖ 蚀刻均匀性:平放的板在蚀刻时中间会聚 集药液,中间聚集的药液老化使中间的蚀 刻速度变慢,出现中间蚀刻慢,板边蚀刻 快的现象,要通过喷嘴方向和喷淋压力来 调整蚀刻均匀性。
PCB蚀刻教材(ETCH、工程师培训资料)

对策: 对策:
对于开路在蚀刻段主要原因有: 1、运输轮的擦花 2、压辘会粘起干膜。我们可检查运输轮将变形之运输轮的胶圈更换解决这 问题,同时可定期更换运输轮来预防这一问题的发生。 3、对于压辘粘起干膜,我们要求每天每次开机前用清水清洗压辘,将结晶 盐溶解,同时每星期定时用酒精擦压辘。
短路的成因有: 短路的成因有: 1、显影不干净 2、运输轮本身粘有干膜碎 对策: 对策: 1、对于显影不净可控制显影速度的合理性和采用圆锥形的喷嘴,并保持显 影压力。 2、运输轮本身粘有干膜可停止开风刀来防止 3、油粘在铜板的表面我们可用吸油绵或更换过滤棉蕊来解决。
各种药物在蚀刻液中的必要性及效果。 HCL作用 作用 1、使Cucl转化为Cucl2 2、使蚀刻速度增高。 3、促进蚀刻速度长期稳定化 4、HCL浓度过高会伤Resist H2O2作用 1、使CU+ CU2+起催化作用 2、起再生作用
蚀刻常见的品质问题有: 1、开路 2、短路 3、蚀刻末净 4、线幼 5、蚀刻过度 各种药水控制浓度及工艺参数:Na2CO3 0.7-1.1% HCL 30-35% CU2+ 100-120 g/l NaOH 1.0-4.0% 显影压力为25-30PSI蚀刻太力为35-45PSI 显影的速度控制应保持露铜点50为新进工程师了解蚀刻工艺流程
目录: 目录
蚀刻简介 ----------- 3 蚀刻工艺流程及原理 --------- 4-5 蚀刻常见质问题及对策 -------- 6-9 环保局 -------------------------------10
蚀 刻 简 介:
蚀刻由显影、蚀刻、褪膜三大部份组成。显影为将未曝光部份溶 解,曝光部份保留。显影的决定速度可按露铜点50-70%决定。蚀 刻是将裸露的铜面蚀掉,从而得到我们所需的图形。褪膜是利用强 碱能将干膜溶解原理,将干膜冲洗干净。NaOH浓度控制3-5%。浓 度过高会造成板面氧化,太低又冲洗不干净。
酸性蚀刻液ppt课件

若发生下列反应则会发生沉淀物
4CuCl2 + FeCl2 + O2 → 2CuCl Cu O + FeCl3 (黑绿色)
※目前多使用于铁/镍合金蝕刻,如导线架业,PCB厂较少使用。
酸性蚀刻液的概况
二、氯气/盐酸
最高可蚀刻铜约180克/公升 Cu + CuCl2 → 2CuCl 加入1~3N HCl使反应加快,但盐酸不 参与反应,只有带出消耗。
生成的氯 化亚铜不 易溶于水 在铜的表 面形成膜
阻止反 应进一 步进行
过量Cl-与 氯化亚铜 络合形成 可溶性的 络离子 (CuCl3)2-
从铜表 面上溶 解下来
提高蚀 刻速率
影响蚀刻液的因素
Cu+浓度的影响
根据蚀刻反应机理,随着铜的蚀刻就会形成一价铜离子。 较微量的Cu+就会显著的降低蚀刻速率。
酸性蚀刻液的概况
一、氯化铁/盐酸
FeCl3 w/w约40%,HCl约5%,能蚀铜约70克/公升 ������ FeCl ������ ������ 3 + 3H2O → Fe(OH)3 + 3HCl 补充HCl防止沉淀 蚀刻原理: FeCl3 + Cu → FeCl2 + CuCl -----------(1) FeCl3 + CuCl → FeCl2 + CuCl2--------(2) CuCl2 + Cu → 2CuCl---------------------(3) (3)式取代(1)式进行蚀铜反应
※双氧水贮存/稳定性较困难,而且实际消耗盐酸,比用氯气法成本高
酸性蚀刻液的概况
四、氯酸钠/盐酸
最高可蚀刻铜约180克/公升 3Cu + 3CuCl2 → 6CuCl HCl之酸值控制在2.5N以下 6CuCl + NaClO3 + 6HCl → 6CuCl2 + 3H2O + NaCl 净反应: 3Cu + NaClO3 + 6HCl → 3CuCl2 + 3H2O + NaCl ������ ������ ������ ������ ������ ������ ������ 优点:A 于双氧水法比较,盐酸的反应量相同,但盐酸带出量则因浓度为 2.5N一下而大量减少。 B 氯化钠氧化当量为双氧水的三倍,所以双氧水使用量为氯化钠的三倍。 ������ ������ ������ ������ C 目前国外大量使用成本约低于双氧水法10~15%,而且试用小于4mil细 线生产fine line制作。
GC-300S酸性蚀刻液
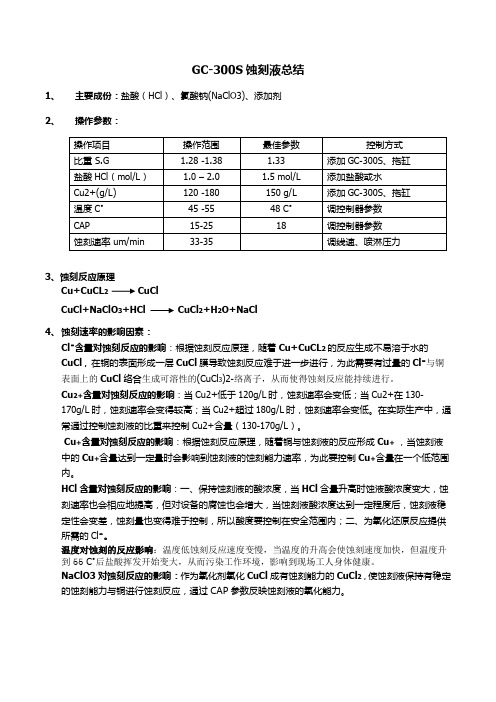
GC-300S蚀刻液总结1、主要成份:盐酸(HCl)、氯酸钠(NaClO3)、添加剂2、操作参数:3、蚀刻反应原理Cu+CuCL2 CuClCuCl+NaClO3+HCl CuCl2+H2O+NaCl4、蚀刻速率的影响因素:Cl¯含量对蚀刻反应的影响:根据蚀刻反应原理,随着Cu+CuCL2的反应生成不易溶于水的CuCl,在铜的表面形成一层CuCl膜导致蚀刻反应难于进一步进行,为此需要有过量的Cl¯与铜表面上的CuCl络合生成可溶性的(CuCl3)2-络离子,从而使得蚀刻反应能持续进行。
Cu2+含量对蚀刻反应的影响:当Cu2+低于120g/L时,蚀刻速率会变低;当Cu2+在130-170g/L时,蚀刻速率会变得较高;当Cu2+超过180g/L时,蚀刻速率会变低。
在实际生产中,通常通过控制蚀刻液的比重来控制Cu2+含量(130-170g/L)。
Cu+含量对蚀刻反应的影响:根据蚀刻反应原理,随着铜与蚀刻液的反应形成Cu+,当蚀刻液中的Cu+含量达到一定量时会影响到蚀刻液的蚀刻能力速率,为此要控制Cu+含量在一个低范围内。
HCl含量对蚀刻反应的影响:一、保持蚀刻液的酸浓度,当HCl含量升高时蚀液酸浓度变大,蚀刻速率也会相应地提高,但对设备的腐蚀也会增大,当蚀刻液酸浓度达到一定程度后,蚀刻液稳定性会变差,蚀刻量也变得难于控制,所以酸度要控制在安全范围内;二、为氧化还原反应提供所需的Cl¯。
温度对蚀刻的反应影响:温度低蚀刻反应速度变慢,当温度的升高会使蚀刻速度加快,但温度升到55 C°后盐酸挥发开始变大,从而污染工作环境,影响到现场工人身体健康。
NaClO3对蚀刻反应的影响:作为氧化剂氧化CuCl成有蚀刻能力的CuCl2,使蚀刻液保持有稳定的蚀刻能力与铜进行蚀刻反应,通过CAP参数反映蚀刻液的氧化能力。
5、配槽步骤*加入CW水至标准液位,喷淋循环清洗半小时,然后排走。
酸性蚀刻工艺流程教材..
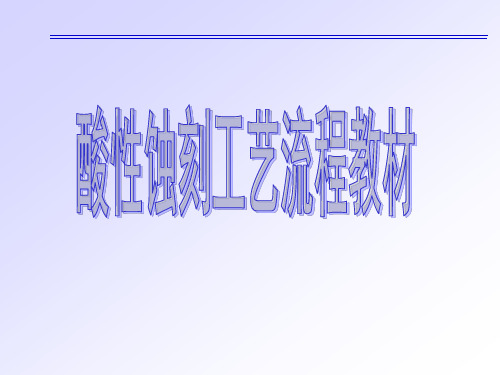
• 在酸性蚀刻的再生系统,就是将Cu+氧化成 Cu++,因此使蚀刻液能将更多的金属铜咬蚀掉。
直觉的联想,在氯化铜酸性蚀刻液中,Cu++ 及Cu+应是以 CuCl2 及CuCl存 在才对,但事实非完全正确,两者事实上是 以和HCl形成的一庞大错化物存在的: Cu° + H2CuCl4 + 2HCl →2H2CuCl3 ------------- (2) 其中H2CuCl4实际是CuCl2和HCl的络合物,而 H2CuCl3则是 CuCl和HCl的络合物
置如果不均衡,会直接影响蚀刻液在板面上的流动速度。同样
如果在同板面上的间隔窄的导线部位和间隔宽的导线部位状态
下,间隔宽的导线分布的部位,蚀刻就会过度。所以,这就要
求设计者在电路设计时,就应首先了解工艺上的可行性,尽量
做到整个板面电路图形均匀分布,导线的粗细程度应尽量相一
致。
5.蚀刻设备的影响(喷淋方式、喷管和喷咀设计、摇摆、喷 淋压力调节等因素) 6.流体力学方面的影响(表面张力、粘度)
温度对蚀刻液特性的影响比较大,通常在化学反应过程中,温
度对加速溶液的流动性和减小蚀刻液的粘度,提高蚀刻速率起 着很重要的作用。但温度过高,也容易引起蚀刻液中一些化学 成份挥发,造成蚀刻液中化学组份比例失调,同时温度过高, 可能会造成高聚物抗蚀层的被破坏以及影响蚀刻设备的使用寿 命。因此,蚀刻液温度一般控制在一定的工艺范围内。
表面张力越小越有利(温度、润湿剂)
蚀刻过程中,随着铜的不断溶解,蚀刻液的粘度就会增加, 使蚀刻液在基板铜箔表面上流动性就差,直接影响蚀刻效果。
四、氯化铜酸性蚀刻液的特性及蚀刻原理 1.特性 • 蚀刻速率易控制,蚀刻液在稳定的状态下,能 达到高的蚀刻质量; • 溶铜量大; • 蚀刻液容易再生与回收,减少污染。 2.蚀刻原理 • 在蚀刻过程中,氯化铜中的二价铜具有氧化性, 能将印制电路板面上的铜氧化成一价铜, 其化学反应如下: 蚀刻反应: Cu+Cucl2→ 2Cucl↓
酸性蚀刻液培训教材

教育訓練教材 惠州联宏化工有限公司 唐青山 13609611662
酸 酸性 性蝕 蝕刻 刻製 製程 程簡 簡介 介
一、酸性蝕刻的應用: 一、酸性蝕刻的應用: 酸性蝕刻,也叫氯化銅酸性蝕刻系統,通常使用於單面板蝕刻、多層 酸性蝕刻,也叫氯化銅酸性蝕刻系統,通常使用於單面板蝕刻、多層 板的內層蝕刻或 流程的外層蝕刻上,因這些製程都用幹膜或液態感 Tenting 板的內層蝕刻或 Tenting 流程的外層蝕刻上,因這些製程都用幹膜或液態感 光油墨作為蝕刻阻劑,而這幾種感光材料相對而言均為耐酸不耐鹼性的特 光油墨作為蝕刻阻劑,而這幾種感光材料相對而言均為耐酸不耐鹼性的特 性,故選用酸性蝕刻。 性,故選用酸性蝕刻。 二、酸性蝕刻的種類: 二、酸性蝕刻的種類: 1 、 H O /HCl 系列。 22 22 1 、 H O /HCl 系列。 、 系列。 2 NaClO /HCl 33 2 、 NaClO /HCl 系列。
顯 顯影 影( (Developing ) Developing)
九、顯影點( )的控制: Break-Point 九、顯影點( Break-Point )的控制: 、由於顯影速度受到很多因素影響,例如:藥液濃度、噴灑壓力、溫度等, 1 、由於顯影速度受到很多因素影響,例如:藥液濃度、噴灑壓力、溫度等, 1 因此我們通常用顯影點的位置來控制正確的顯影速度。 因此我們通常用顯影點的位置來控制正確的顯影速度。 、顯影點是指在顯影過程中,未經曝光聚合的幹膜在與顯影液反應後被沖刷 2 2 、顯影點是指在顯影過程中,未經曝光聚合的幹膜在與顯影液反應後被沖刷 掉,而顯露出銅面時的位置,而称之。現場生產時,顯影點一般控制在顯 掉,而顯露出銅面時的位置,而称之。現場生產時,顯影點一般控制在顯 影槽的 50%~60% 之間。 影槽的 之間。 50%~60% 3 、顯影點及均勻性的測試: 、顯影點及均勻性的測試: 3 為瞭解顯影點和顯影均勻性的情形,則可用下列方法來測試:取幾片 為瞭解顯影點和顯影均勻性的情形,則可用下列方法來測試:取幾片 較大尺寸(如 × )的銅箔基板以正常流程壓好幹膜,撕掉保護膜 20″ 24″ 較大尺寸(如 20″ × 24″ )的銅箔基板以正常流程壓好幹膜,撕掉保護膜 後連續放置(無間距),以正常速度輸送進顯影槽,當第一片板子即將出 後連續放置(無間距),以正常速度輸送進顯影槽,當第一片板子即將出 顯影槽時關閉噴灑,待板子經過水洗後取出,以顯影槽有效噴灑長度為基 顯影槽時關閉噴灑,待板子經過水洗後取出,以顯影槽有效噴灑長度為基 準依次擺放,檢視板面顯影均勻性。 準依次擺放,檢視板面顯影均勻性。
ETCH(PCB蚀刻培训教材)

生产注意事项
1.严格控制退膜液的浓度,以保证干膜以合适的速度和大小 退去,且不易堵塞喷嘴。
2.退膜后水洗压力应大于20PSI,以便除去镀层与底铜间 的残膜和附在板面上的残膜。
3.蚀刻药水压力应在18 ~30PSI,过低则蚀刻不尽,过高则易 打断药水的保护膜,造成蚀刻过度。
影响蚀刻速率因素分析
一.酸性氯化铜溶液 影响蚀刻速率的因素有很多,主要是Cl- ,Cu+含
速率易控制
2.主要反应原理
Cu+Cu(NH3)4Cl2 → 2Cu(NH3)2Cl
4Cu(NH3)2Cl + 4NH3H2O + 4NH4Cl + O2 →
4Cu(NH3)4Cl2+6H2O 以上两反应重复进行,因此需要有良好抽气,使喷淋 形成 负压,使空气中的氧气与药液充分混合,从而利于 蚀刻反应进行。注意抽气不可过大,否则造成氨水消耗 量的增大.
技术提升部分
生产线简介 1.内层酸性蚀刻
冲、蚀板、褪菲林生产线机器运行参数
制程 冲板
蚀板
褪膜
速度 药水压力 1.6-3.0m/min 上 28-32Psi
下 28-32Psi 0.9-3.0m/min 上 25-35Psi
下 10-32Psi 1.5-3.0m/min 上 22-35Psi
下 10-30Psi
二价铜离子在碱性环境下极易生成氢氧化铜沉淀, 需加入过量的氨水,使之生成稳定的氨铜错离子团; 过量的氨使反应生成的不稳定Cu(NH3)2Cl 再生成稳 定的具有氧化性的Cu(NH3)4Cl2 ,使反应不断的进行。
生产过程中自动控制通过监测PH值,比重,进行 补加氨水和新液,而达到连续生产的目的。
蚀刻工艺流程及原理
蚀刻工艺之酸性氯化铜蚀刻液

目录摘要 (1)1设计任务书 (2)1.1项目 (2)1.2设计内容 (2)1.3设计规模 (2)1.4设计依据 (2)1.5产品方案 (2)1.6原料方案 (2)1.7生产方式 (3)2工艺路线及流程图设计 (3)2.1工艺路线选择 (3)2.2内层车间工艺流程简述 (4)3 •车间主要物料危害及防护措施 (6)3.1职业危害 (6)3.2预防措施 (6)4. 氯酸钠/盐酸型蚀刻液的反应原理 (7)4.1蚀刻机理 (7)4.2蚀刻机理的说明 (8)4.3蚀刻中相关化学反应的计算 (8)5. 影响蚀刻的因素 (6)5.1影响蚀刻速率的主要因素 (10)5.2蚀刻线参数设计 (10)6主要设备一览表 (12)7车间装置定员表 (13)8投资表 (13)9安全、环保、生产要求 (14)致谢 (15)参考文献 (16)蚀刻工艺之酸性氯化铜蚀刻液摘要:本文介绍了印制电路板制造过程中的酸性氯化铜蚀刻液,并对其蚀刻原理和影响蚀刻的因素进行了阐述。
关键词:印制电路板;酸性氯化铜;蚀刻;分类号:F407.7Brief prin cipies to acid chlori nati on copperetch ing and factors an alysisChen yon gzhou (Tutor:Pi-ya n)(Departme nt of Chemistry and En vir onmen tal Engin eeri ng,Hubei NormalU niversity , Hua ngshi ,Hubei, 435002)Abstract : In this paper acid chlorination etching solution was introduced. Meanwhile the etching principle and the factors affectingthe etchi ng rate bee n expla in.Keywords: PCB;acid chlori nati on copper soluti on; etchi ng蚀刻工艺之酸性氯化铜蚀刻液1设计任务书1.1项目氯酸钠/盐酸蚀刻型蚀刻液及其蚀刻工艺(初步1.2设计内容车间工艺参数设计1.3设计规模1年产:106万FT22年生产日:4000FT23 日生产能力:500000/280=3800 FT2/ 天1.4设计依据依据有关部门下达的实设计任务书或可行性报告的批文,环境影响报告书的批文,资源评价报告的批文,技术引进合同,设计合同,其他文件等1.5蚀刻液主要成分氯酸纳,盐酸,水,其他辅助添加剂。
- 1、下载文档前请自行甄别文档内容的完整性,平台不提供额外的编辑、内容补充、找答案等附加服务。
- 2、"仅部分预览"的文档,不可在线预览部分如存在完整性等问题,可反馈申请退款(可完整预览的文档不适用该条件!)。
- 3、如文档侵犯您的权益,请联系客服反馈,我们会尽快为您处理(人工客服工作时间:9:00-18:30)。
PCB 內層 層製 製作 作流 流程 程 PCB 內 3.曝光
光源
Artwork (底片) Artwork (底片)
4.曝光後
Photo Resist
PCB 內層 層製 製作 作流 流程 程 PCB 內 5.內層板顯影
Photo Resist
6.酸性蝕刻(Power/Ground或Signal)
三、顯影液的濃度: 三、顯影液的濃度: 目前業界常用的顯影液是以無水碳酸鈉( )加純水配製而成, Na CO 22 33 目前業界常用的顯影液是以無水碳酸鈉( Na CO )加純水配製而成, 濃度一般為 1~2% (質量比),但為了細線路的製作,緩和反應速度,降低 濃度一般為 (質量比),但為了細線路的製作,緩和反應速度,降低 1~2% Under-cut 1.0%±0.2% 。較高藥液濃度可容許 Under-cut,現在顯影液的濃度多控制在 ,現在顯影液的濃度多控制在 1.0%±0.2% 。較高藥液濃度可容許 較高幹膜負荷量,但不容易清洗乾淨,且操作範圍較小;反之,過低的藥 較高幹膜負荷量,但不容易清洗乾淨,且操作範圍較小;反之,過低的藥 液濃度所能承受的幹膜負荷量較小。因此,正確的藥液濃度應與幹膜廠商 液濃度所能承受的幹膜負荷量較小。因此,正確的藥液濃度應與幹膜廠商 研究,依照其幹膜特性來配製。而藥液濃度的檢驗可利用酸鹼滴定來分析。 研究,依照其幹膜特性來配製。而藥液濃度的檢驗可利用酸鹼滴定來分析。 重點是:為維持槽液濃度的穩定性,確保顯影品質,必須設置自動添加, 重點是:為維持槽液濃度的穩定性,確保顯影品質,必須設置自動添加, 一般以偵控槽液的 pH 值作自動添加,或計片、計面積添加。 一般以偵控槽液的 值作自動添加,或計片、計面積添加。 pH 四、顯影溫度: 四、顯影溫度: 顯影液溫度是影響顯影速度的最大變數,一般都控制在 30±2 ℃,需 顯影液溫度是影響顯影速度的最大變數,一般都控制在 ℃,需 30±2 依幹膜種類而定。由於操作時藥液因泵浦的壓縮作用產生大量的熱能會促 依幹膜種類而定。由於操作時藥液因泵浦的壓縮作用產生大量的熱能會促 使溫度升高,致使有顯影過度的可能,因此顯影槽需加裝冷卻水管來保持 使溫度升高,致使有顯影過度的可能,因此顯影槽需加裝冷卻水管來保持 適當的溫度;而溫度過低時,又可能會造成顯影不潔,因此需加裝加熱器 適當的溫度;而溫度過低時,又可能會造成顯影不潔,因此需加裝加熱器 使溫度能達到操作範圍,而得到最佳的顯影效果。 使溫度能達到操作範圍,而得到最佳的顯影效果。
二、 二、顯影的作業條件: 顯影的作業條件:
操作參數 顯影液濃度 顯影溫度 顯影液pH 顯影段噴灑壓力 顯影點 水洗水溫度 水洗段噴灑壓力 操作範圍 1~2%之碳酸鈉(重量比) 30 ±2 ℃ 10.5~10.7 1.5~2.5kg/cm2 50~60% 20~30℃ 1.5~2.5kg/cm2
顯 顯影 影( (DevelBiblioteka ping ) Developing)
三、 三、酸性蝕刻製作流程: 酸性蝕刻製作流程:
1 、單面板: 、單面板: 1 銅面前處理→印刷線路→烘烤固化→酸性蝕刻→去墨 銅面前處理→印刷線路→烘烤固化→酸性蝕刻→去墨 、內層和外層( 流程): 2 2 、內層和外層( Tenting Tenting 流程): 銅面前處理→壓膜 銅面前處理→壓膜 → → 曝光→顯影 曝光→顯影 →酸性蝕刻 →酸性蝕刻→去膜 →去膜
顯 顯影 影( (Developing ) Developing)
內 內層 層製 製作 作流 流程 程簡 簡介 介
基 基板 板
壓 壓膜 膜
壓膜後 壓膜後
曝 曝光 光
顯 顯影 影
蝕 蝕銅 銅
去 去膜 膜
PCB 內層 層製 製作 作流 流程 程 PCB 內 1.下料裁板(Panel Size)
COPPER FOIL
Epoxy Glass
2.內層板壓乾膜(光阻劑)
Photo Resist
顯 顯影 影( (Developing ) Developing)
八、噴灑系統: 八、噴灑系統: 1 、搖擺方式:有噴盤來回鋸動式搖擺,及噴管定點自轉式搖擺。噴灑系統設 、搖擺方式:有噴盤來回鋸動式搖擺,及噴管定點自轉式搖擺。噴灑系統設 1 計搖擺的目的是使藥液能夠均勻、迅速地噴灑到板面,加快藥液的交換與 計搖擺的目的是使藥液能夠均勻、迅速地噴灑到板面,加快藥液的交換與 反應速度,從而得到良好的均勻性與反應速率。 反應速度,從而得到良好的均勻性與反應速率。 2 、噴管間距與噴嘴間距:噴管與噴管的間距是否合理,主要是看噴嘴的噴灑 、噴管間距與噴嘴間距:噴管與噴管的間距是否合理,主要是看噴嘴的噴灑 2 面積是否能夠完全,此會影響顯影的均勻性;而噴嘴與噴嘴的間距是否合 面積是否能夠完全,此會影響顯影的均勻性;而噴嘴與噴嘴的間距是否合 理,則會影響顯影的速度。 理,則會影響顯影的速度。 3 、噴嘴的選用:水平線的噴嘴一般可分為兩種類型,即圓錐型( Cone ) 、噴嘴的選用:水平線的噴嘴一般可分為兩種類型,即圓錐型( ) 3 ConeType Type 和扇型( )。圓錐型噴嘴的特點是噴灑面積廣,可得到較佳的均 Fan 和扇型( FanType Type )。圓錐型噴嘴的特點是噴灑面積廣,可得到較佳的均 勻性,但衝擊力小,容易造成顯影不潔。而扇型噴嘴噴灑面積雖小,但衝 勻性,但衝擊力小,容易造成顯影不潔。而扇型噴嘴噴灑面積雖小,但衝 擊力較大,顯影效果較佳。因此針對細線路或內層板,以選擇使用扇型噴 擊力較大,顯影效果較佳。因此針對細線路或內層板,以選擇使用扇型噴 嘴較適合,因密集線路區需較高的藥液衝擊力來清除線路間的殘渣;而內 嘴較適合,因密集線路區需較高的藥液衝擊力來清除線路間的殘渣;而內 層板因未鑽孔,上板面容易產生水池效應( Pudding ),若噴灑壓力不夠會 層板因未鑽孔,上板面容易產生水池效應( ),若噴灑壓力不夠會 Pudding 造成上板面顯影不潔,易導致蝕刻不淨等異常。 造成上板面顯影不潔,易導致蝕刻不淨等異常。 、不論用何種類型的噴嘴,最重要的是兩個噴嘴的噴灑面積是否能夠重疊 4 4 、不論用何種類型的噴嘴,最重要的是兩個噴嘴的噴灑面積是否能夠重疊 ( Overlapping ),以達到均勻且乾淨的顯影效果。 ( ),以達到均勻且乾淨的顯影效果。 Overlapping
酸性蝕刻製程工藝介紹
教育訓練教材 惠州联宏化工有限公司 唐青山 13609611662
酸 酸性 性蝕 蝕刻 刻製 製程 程簡 簡介 介
一、酸性蝕刻的應用: 一、酸性蝕刻的應用: 酸性蝕刻,也叫氯化銅酸性蝕刻系統,通常使用於單面板蝕刻、多層 酸性蝕刻,也叫氯化銅酸性蝕刻系統,通常使用於單面板蝕刻、多層 板的內層蝕刻或 流程的外層蝕刻上,因這些製程都用幹膜或液態感 Tenting 板的內層蝕刻或 Tenting 流程的外層蝕刻上,因這些製程都用幹膜或液態感 光油墨作為蝕刻阻劑,而這幾種感光材料相對而言均為耐酸不耐鹼性的特 光油墨作為蝕刻阻劑,而這幾種感光材料相對而言均為耐酸不耐鹼性的特 性,故選用酸性蝕刻。 性,故選用酸性蝕刻。 二、酸性蝕刻的種類: 二、酸性蝕刻的種類: 1 、 H O /HCl 系列。 22 22 1 、 H O /HCl 系列。 、 系列。 2 NaClO /HCl 33 2 、 NaClO /HCl 系列。
顯 顯影 影( (Developing ) Developing)
五、顯影壓力: 五、顯影壓力: 幹膜與顯影液發生化學反應時會產生膨脹現象( ),因此需要適 Swelling 幹膜與顯影液發生化學反應時會產生膨脹現象( Swelling ),因此需要適 當的壓力 來 沖刷掉表面已作用過的浮層,使乾淨之顯影液能繼續與幹膜產生 當的壓力 來 沖刷掉表面已作用過的浮層,使乾淨之顯影液能繼續與幹膜產生 化學反應,而 不 至於發生水池效應。而針對細線路而言,顯影時適當的噴灑 化學反應,而 不 至於發生水池效應。而針對細線路而言,顯影時適當的噴灑 22 壓力應在 之間。 1.5~2.5kg/cm 壓力應在 1.5~2.5kg/cm 之間。 六、水質硬度: 六、水質硬度: 一般自 來 水或地下水因含有礦物質及污垢, 若 長期使用容易與幹膜結合 一般自 來 水或地下水因含有礦物質及污垢, 若 長期使用容易與幹膜結合 形成硬垢,造成噴嘴或噴管阻 塞 ,影響噴灑面積,最後導致顯影 不 潔。因此 形成硬垢,造成噴嘴或噴管阻 塞 ,影響噴灑面積,最後導致顯影 不 潔。因此 建議使用純水搭配碳酸鈉配製成顯影液,會是最佳選。而水洗水一般也選用 建議使用純水搭配碳酸鈉配製成顯影液,會是最佳選。而水洗水一般也選用 經過處理的軟水。 經過處理的軟水。 七、過濾: 七、過濾: 顯影槽的噴灑系統加裝過濾裝置的主要目的在於避免幹膜殘渣堵塞噴嘴 顯影槽的噴灑系統加裝過濾裝置的主要目的在於避免幹膜殘渣堵塞噴嘴 而造成顯影不潔;另也是防止膜屑、膜渣經過噴灑反沾到板面上,造成後續 而造成顯影不潔;另也是防止膜屑、膜渣經過噴灑反沾到板面上,造成後續 的蝕刻不淨或星點狀殘銅,致使生產品質不良,增加 檢測的工作量。 AOI 的蝕刻不淨或星點狀殘銅,致使生產品質不良,增加 AOI 檢測的工作量。
Photo Resist
PCB 內層 層製 製作 作流 流程 程 PCB 內 7.去乾膜 ( Strip Resist)
PCB 內層 層製 製作 作流 流程 程 PCB 內
1、基板
铜箔 基材
2、塗布/壓膜
干/湿膜 铜箔
基材
PCB 內層 層製 製作 作流 流程 程 PCB 內
3、曝光
底片 铜箔 干/湿膜
顯 顯影 影( (Developing ) Developing)
九、顯影點( )的控制: Break-Point 九、顯影點( Break-Point )的控制: 、由於顯影速度受到很多因素影響,例如:藥液濃度、噴灑壓力、溫度等, 1 、由於顯影速度受到很多因素影響,例如:藥液濃度、噴灑壓力、溫度等, 1 因此我們通常用顯影點的位置來控制正確的顯影速度。 因此我們通常用顯影點的位置來控制正確的顯影速度。 、顯影點是指在顯影過程中,未經曝光聚合的幹膜在與顯影液反應後被沖刷 2 2 、顯影點是指在顯影過程中,未經曝光聚合的幹膜在與顯影液反應後被沖刷 掉,而顯露出銅面時的位置,而称之。現場生產時,顯影點一般控制在顯 掉,而顯露出銅面時的位置,而称之。現場生產時,顯影點一般控制在顯 影槽的 50%~60% 之間。 影槽的 之間。 50%~60% 3 、顯影點及均勻性的測試: 、顯影點及均勻性的測試: 3 為瞭解顯影點和顯影均勻性的情形,則可用下列方法來測試:取幾片 為瞭解顯影點和顯影均勻性的情形,則可用下列方法來測試:取幾片 較大尺寸(如 × )的銅箔基板以正常流程壓好幹膜,撕掉保護膜 20″ 24″ 較大尺寸(如 20″ × 24″ )的銅箔基板以正常流程壓好幹膜,撕掉保護膜 後連續放置(無間距),以正常速度輸送進顯影槽,當第一片板子即將出 後連續放置(無間距),以正常速度輸送進顯影槽,當第一片板子即將出 顯影槽時關閉噴灑,待板子經過水洗後取出,以顯影槽有效噴灑長度為基 顯影槽時關閉噴灑,待板子經過水洗後取出,以顯影槽有效噴灑長度為基 準依次擺放,檢視板面顯影均勻性。 準依次擺放,檢視板面顯影均勻性。