酸性蚀刻液ppt课件
酸性蚀刻工艺流程教材

用于清洗板材表面,去除残留的蚀刻液和其他杂质。
酸性蚀刻的辅助材料
添加剂
为了改善蚀刻效果,可以在蚀刻液中加入一些 添加剂,如缓蚀剂、加速剂等。
检测试剂
用于检测蚀刻液的浓度和酸碱度,确保其处于 最佳工作状态。
废液处理剂
用于处理蚀刻过程中产生的废液,减少环境污染。
05 酸性蚀刻的环保与安全
酸性蚀刻的环保措施
医疗器械
医疗器械如手术刀、针头 等,通过酸性蚀刻工艺提 高表面的抗滑性和防锈性。
酸性蚀刻的优缺点
优点
酸性蚀刻工艺具有操作简单、成本低 廉、环保等优点,可以快速实现金属 表面的处理,提高金属表面的美观度 和使用性能。
缺点
酸性蚀刻工艺可能会对金属材料产生 一定的腐蚀和损伤,影响金属材料的 机械性能和耐腐蚀性能,因此需要合 理控制蚀刻时间和温度等参数。
废气处理
酸性蚀刻过程中产生的废气应经 过处理后再排放,以减少对大气 的污染。常用的废气处理方法包 括吸附法、吸收法、燃烧法等。
废水处理
酸性蚀刻过程中产生的废水应经 过处理后再排放,以减少对水体 的污染。废水处理方法包括沉淀 法、过滤法、生物处理法等。
废渣处理
酸性蚀刻过程中产生的废渣应进 行妥善处理,以减少对环境的污 染。废渣可以采取填埋、焚烧、 回收利用等方式进行处理。
05
04
酸性蚀刻
将涂布好的金属板材放入酸性蚀刻溶 液中,在一定温度和时间下进行蚀刻。
电路板的酸性蚀刻
总结词
在电子工业中,电路板的制作过程中酸性 蚀刻技术是关键步骤之一,用于形成导电 线路和图案。
后处理
去除抗蚀剂,进行电镀、焊接等处理,完 成电路板的制作。
准备材料
选择合适的基材,如FR4、CEM-1等,并 制备好电路图形。
PCB生产废水分类与处理工艺ppt课件

❖ 氯氧化法(自来水折点加氯原理)。 ❖ 生化法
氯氧化法:很难处理达标,而且费用昂贵。 生物法: 硝化菌把氨氮分解为亚硝酸盐、硝酸盐形式;
生物硝化的费用是低廉的。
主要污染物处理技术——Ni的去除
离子镍的处理方法: Ni2++ 2OH→Ni(OH)2↓ Ksp=10-15.2,pH值>9.5,可达标1.0mg/L。 络合镍的处理 化学镀镍中有次磷酸、亚磷酸、次亚磷酸,会形成络 合镍。 无机络合剂,简单的化学氧化可破坏其结构。
➢ 采用:酸析+厌 氧+好氧工艺去除 COD;
➢ 好氧工艺采用投 药式活性污泥 法”;
➢ 混凝沉淀控制铜 离子浓度。
有机浓液 酸析槽
混凝气浮池 pH调整池
混凝沉淀池 厌氧池
活性污泥池 沉淀池
一般有机废水 排放
废水分类处理工艺
❖生化处理系统的特点:
1、具有同时去除COD、铜、氨氮三大功能。 2、利用微生物破坏鳌合剂和络合剂,使其失去 鳌合、络合能力,释放铜离子。 3、利用厌氧菌将SO42-还原成S2-,生成CuS 沉淀; 4、利用活性污泥的硝化作用去除水中的氨氮。 5、采用“投药式活性污泥法”,防止污泥膨胀, 微生物不受油墨颗粒的影响。
9 OSP废液 沉铜线
10 活化废液 沉铜线;沉金线 11 含镍废液 沉金线
单独收集, 委外处理
内外层前处理线;沉铜线;棕 12 微蚀废液 化线;减铜线;阻焊前处理线;
沉金线;沉银线;OSP
13 含银废液 沉银线 14 含金废液 沉金线
PCB生产废水水质、水量
废水种类 水量
pH
COD (mg/L)
Fenton氧化法原理
化学蚀刻技术ppt课件

安全和停机注意事项
1、先停加热开关(选配有加热的机型), 转动手轮调开刷子与托辊的间隙让风 机运转数秒,用来冷却管状加热器散 发的余热。 2、停传动开关,刷子旋转数秒,让冷 却水冲洗刷子表面将污物冲洗掉。
7
3、关闭水闸阀,停抛刷开关, 并把调速旋钮调至O位。 4、停机后必须切断电源,以 防事故。
12
蚀刻的操作步骤
1、 把要蚀刻的板子放到设备内槽上夹缝中。 2、 打开电源,设置溶液温度。 3、 当设备停止加热,设置蚀刻时间,打开
蚀刻开关,开始蚀刻。 4、 当溶液饱和需要更换时,在蚀刻机后面
有连接水阀可将溶液放出。 13
14
脱膜
脱膜的目的:把蚀刻后的板子上剩下的蓝色 感光油墨去掉。
脱膜机参数设置:温控仪的温度设置34摄氏 度;时间继电器设置时间2分钟。
2
刷板机
用途 : 主要用于基板表面抛光处理, 如铜板,铝板,不锈钢板等,去掉 其表面的氧化物或者指纹等。
3
特点:操作简单,内部结构紧凑。传动 采用直流电机无极调速,速度任意可调 。刷辊采用y系列电机,烘干(选配)采 用远红外电热加热管,使用寿命长,热 效率高,经过刷光后的板子直接可丝印 ,简化了生产环节,对产品质量,节能 方面有独特之处。
3开启水闸阀查看喷出的水流是否畅通水流不畅不能进行工作否则易损坏刷4开启传动开子旋转数秒然后停刷子开关在开传动开关把板子从机器内送出查看刷的板子表面是否宽窄一致两端宽窄不一适当调手轮压力
化学蚀刻技术
7号光盘的内容(一楼PCB制作室)
1
主要内容
1.刷板机介绍 2.刷板机的安全和停机注意事项 3.显影机介绍 4.显影操作步骤 5.脱膜的步骤和安全 6.蚀刻的操作步骤
脱膜过程:脱膜机内部由抗腐蚀泵使脱膜液 双面喷射到板的两侧。
蚀刻工艺(酸性、碱性、微蚀)

PCB外层电路的蚀刻工艺在印制电路加工中﹐氨性蚀刻是一个较为精细和覆杂的化学反应过程, 却又是一项易于进行的工作。
只要工艺上达至调通﹐就可以进行连续性的生产, 但关键是开机以后就必需保持连续的工作状态﹐不适宜断断续续地生产。
蚀刻工艺对设备状态的依赖性极大, 故必需时刻使设备保持在良好的状态。
目前﹐无论使用何种蚀刻液﹐都必须使用高压喷淋﹐而为了获得较整齐的侧边线条和高质量的蚀刻效果﹐对喷嘴的结构和喷淋方式的选择都必须更为严格。
对于优良侧面效果的制造方式﹐外界均有不同的理论、设计方式和设备结构的研究, 而这些理论却往往是人相径庭的。
但是, 有一条最基本的原则已被公认并经化学机理分析证实﹐就是尽速让金属表面不断地接触新鲜的蚀刻液。
在氨性蚀刻中﹐假定所有参数不变﹐那么蚀刻的速率将主要由蚀刻液中的氨(NH3)来决定。
因此, 使用新鲜溶液与蚀刻表面相互作用﹐其主要目的有两个﹕冲掉刚产生的铜离子及不断为进行反应供应所需要的氨(NH3)。
在印制电路工业的传统知识里﹐特别是印制电路原料的供货商们皆认同﹐并得经验证实﹐氨性蚀刻液中的一价铜离子含量越低﹐反应速度就越快。
事实上﹐许多的氨性蚀刻液产品都含有价铜离子的特殊配位基(一些复杂的溶剂)﹐其作用是降低一价铜离子(产品具有高反应能力的技术秘诀)﹐可见一价铜离子的影响是不小的。
将一价铜由5000ppm降至50ppm, 蚀刻速率即提高一倍以上。
由于在蚀刻反应的过程中会生成大量的一价铜离子, 而一价铜离子又总是与氨的络合基紧紧的结合在一起﹐所以要保持其含量近于零是十分困难的。
而采用喷淋的方式却可以达到通过大气中氧的作用将一价铜转换成二价铜, 并去除一价铜, 这就是需要将空气通入蚀刻箱的一个功能性的原因。
但是如果空气太多﹐又会加速溶液中的氨的损失而使PH值下降﹐使蚀刻速率降低。
氨在溶液中的变化量也是需要加以控制的, 有一些用户采用将纯氨通入蚀刻储液槽的做法, 但这样做必须加一套PH计控制系统, 当自动监测的PH结果低于默认值时﹐便会自动进行溶液添加。
酸性蚀刻工艺流程教材PPT课件

• 随着铜的蚀刻,溶液中的一价铜越来越 多,蚀刻能力很快就会下降,以至最后 失去效能。
• 为了保持连续的蚀刻能力,可以通过各 种方式对蚀刻液进行再生,使一价铜重 新转变成二价铜,达到正常蚀刻的工艺 标准。
.
3.影响蚀刻速率的因素 影响蚀刻速率的因素较多,但影响较大的是蚀刻
度对加速溶液的流动性和减小蚀刻液的粘度,提高蚀刻速率起
着很重要的作用。但温度过高,也容易引起蚀刻液中一些化学
成份挥发,造成蚀刻液中化学组份比例失调,同时温度过高,
可能会造成高聚物抗蚀层的被破坏以及影响蚀刻设备的使用寿
命。因此,蚀刻液温度一般控制在一定的工艺范围内。
.
3. 采用的铜箔厚度:铜箔的厚度对电路图形的导线密度有 着重要影响。铜箔薄,蚀刻时间短,侧蚀就很小;反之, 侧蚀就很大。所以,必须根据设计技术要求和电路图形的 导线密度及导线精度要求,来选择铜箔厚度。同时铜的延 伸率、表面结晶构造等,都会构成对蚀刻液特性的直接影 响。
2)操作方式的控制
视图形导线疏密走向确定放板的方向,确保蚀刻液在基板面流动
快,不会产生蚀刻液堆积的问题。
在蚀刻时将导线密面朝下,导线疏的面朝上,以改善电路图形两
面蚀刻的均匀性。
.
六、 常见故障及处理方法:
故障类型
产生主要原因
解决办法
蚀刻速率降低 蚀刻液出现沉淀
1. 蚀刻液的温度低
2.淋压力过低
3.蚀刻液的化学组份控制失 调 络合剂氯离子不足
达到高的蚀刻质量; • 溶铜量大; • 蚀刻液容易再生与回收,减少污染。 2.蚀刻原理 • 在蚀刻过程中,氯化铜中的二价铜具有氧化性,
能将印制电路板面上的铜氧化成一价铜, 其化学反应如下: 蚀刻反应: Cu+Cucl2→ 2Cucl↓
酸性氯化铜蚀刻液

酸性氯化铜蚀刻液1、特性适用于生产多层板内层,掩蔽法印制板和单面印制板,采用的抗蚀剂是网印抗蚀印料、干膜、液体感光抗蚀剂,也适用于图形电镀金抗蚀印制电路板的蚀刻。
电镀金抗蚀层印制电路板的蚀刻:A,蚀刻速率易控制,蚀刻液在稳定的状态下,能达到高的蚀刻质量。
B,溶铜量大。
C,蚀刻液容易再生与回收,减少污染。
2、化学组成:化学组分 1 2 3 4 5Cucl2.2H2O 130-190g/l 200g/l 150-450g/l 140-160g/l 145-180g/lHCL 150-180ml/l 100ml/l 7-8g/l 120-160g/lNaCL 100g/lNH4CL 饱和平共处160g/lH2O 添加到1升添加到1升添加到1升添加到1升添加到1升3、蚀刻原理在蚀刻过程中,氯化铜中的二价铜具有氧化性,能将印制电路板面上的铜氧化成一价铜,其化学反应如下:蚀刻反应:CU+CUCL2→CU2CL2所形成氯化亚铜是不易溶于水的,在有过量的氯离子存在的情况下,能形成可溶性的络离子,其化学反应如下:络合反应:CU2CL2+4CL—→2「CUCL3」2-随着铜的蚀刻,溶液中的一价铜墙铁壁越来越多,蚀刻能力很快就会下降,以至最后失去效果,为保证连续的蚀刻能力,可以通过各种方法进行再生,使一价铜重新转变成二价铜,达到下常工艺标准。
4、影响蚀刻速率的影响。
A、氯离子含量的影响。
蚀刻液的配制和再生都需要氯离子参加,但必须控制盐酸的用量,在蚀刻反应中,生产CU2CL2不易溶于水,而在铜表面生成一层氯化亚铜膜,阻止了反应进行,但过量的氯离子能与CU2CL2络合形成可溶性络离子「CUCL3」2-从铜表面溶解下来,从而提高了蚀刻速率。
B、一价铜的影响微量的一价铜存在蚀刻液中,会显著的隆低蚀刻速率。
C、二价铜含量的影响,通常二价铜离子浓度低于2克离子时,蚀刻速率低,在2克离子时,蚀刻速率就高,当铜含量达到一定浓度时,蚀刻速率就会下降,要保持恒定的蚀刻速率就必须控制蚀刻液内的含铜量,一般都采用比重方法来控制溶液内的含铜量,通常控制比重在1.28—1.295之间(波美度31--330BE’),此时的含铜量为120—150克/升。
酸性氯化铜蚀刻液

酸性氯化铜蚀刻液1.特性 <1.适用于生产多层板的内层和印刷-蚀刻板。
所采用的抗蚀剂是网印抗蚀印料、干膜、液体光致抗蚀剂等;也适用于图形电镀金抗蚀层印制板的蚀刻,但不适于锡-铅合金和锡抗蚀剂。
2.蚀刻速率容易控制,蚀刻液在稳定状态下能达到高的蚀刻质量。
3.溶铜量大4.蚀刻液容易再生与回收,减少污染。
2. 蚀刻过程的主要化学反应在蚀刻过程中,氯化铜中的Cu2+具有氧化性,能将板面上的铜氧化成Cu1+,其反应如下:蚀刻反应:Cu+CuCl2→Cu2Cl2形成的Cu2Cl2是不易溶于水的,在有过量Cl-存在下,能形成可溶性的络离子,其反应如下:络合反应:Cu2Cl2+4Cl-→2[CuCl3]2-随着铜的蚀刻,溶液中的Cu1+越来越多,蚀刻能力很快就会下降,以至最后失去效能。
为了保持蚀刻能力,可以通过各种方式对蚀刻液进行再生,使Cu1+重新转变成Cu2+,继续进行正常蚀刻。
应用酸性蚀刻液进行蚀刻的典型工艺流程如下:印制正相图象的印制板→检查修版→碱性清洗(可选择)→水洗→表面微蚀刻(可选择)→水洗→检查→酸性蚀刻→水洗→酸性清洗例如:5-10%HCl)→水洗→吹干→检查→去膜→|再生水洗→吹干3. 蚀刻液配方蚀刻液配方有多种,1979年版的印制电路手册(Printed Circuits Handbook)中介绍的配方见表10-2。
表10-2 国外介绍的酸性蚀刻液配方组份 1 2 3 4CuCl 2·2H 2O HCl(200Be’)NaCl NH 4Cl H 2O1.42磅 0.6加仑- -2.2M 30ml/加仑4M -2.2M 0.5N 3M-0.5~2.5M 0.2~0.6 M -2.4~0.5 M添加到1加仑注:1磅=454克 1加仑(美制)=3.785升我国采用的蚀刻液配方也有多种,现摘录如下表10-3表10-3 我国采用的酸性蚀刻液配方组份 123CuCl2·2H2O 130-190g/l 200g/l 150-450g/lHCl 150-180ml/l100ml/l- NaCl - 100g/l -NH4Cl - - 饱和H2O蚀刻 液中所采用的氯化物种类不同。
酸性蚀刻液

该方法得到的纳米铜粉因可制备导电涂料和 电磁屏蔽材料而具有更高的附加值
还原剂水合肼溶液具有一定的毒性,且价格较高
酸性蚀刻废液回收利用的方法
电解还原法 该方法是基于电化学原理, 该方法是基于电化学原理 即酸性蚀刻废液中的铜氯络离 子在阴极得到电子还原为铜。 子在阴极得到电子还原为铜。 萃取法 用水、氨水或硫酸 铵溶液洗脱含铜有机相 中的氯离子,然后用硫酸 反萃取含铜有机相,得到 硫酸铜溶液 萃取剂以铜氯配合物 的形式将铜从酸性蚀 刻废液中萃取出来, 相分离后得到萃余液 用含氯离子的水溶液再 生有机相, 再返回萃取 段进行萃取
一、氯化铁/盐酸 氯化铁 盐酸
FeCl3 w/w约40%,HCl约5%,能蚀铜约70克/公升 FeCl 3H O → Fe(OH) + 3HCl 补充HCl防止沉淀 + 3 2 3 蚀刻原理: FeCl3 + Cu → FeCl2 + CuCl -----------(1) FeCl3 + CuCl → FeCl2 + CuCl2--------(2) CuCl2 + Cu → 2CuCl---------------------(3) (3)式取代(1)式进行蚀铜反应 若发生下列反应则会发生沉淀物 4CuCl2 + FeCl2 + O2 → 2CuCl Cu O + FeCl3 (黑绿色)
酸性蚀刻废液回收利用的方法
离子膜电解法
离子膜电解采用离子膜作为物理隔离材料, 离子膜电解采用离子膜作为物理隔离材料 阳极液为酸 性蚀刻废液,阴极液为酸性蚀刻废液稀释 倍后的溶液。 阴极液为酸性蚀刻废液稀释10倍后的溶液 性蚀刻废液 阴极液为酸性蚀刻废液稀释 倍后的溶液。
隔膜电解法
酸性蚀刻液培训教材

教育訓練教材 惠州联宏化工有限公司 唐青山 13609611662
酸 酸性 性蝕 蝕刻 刻製 製程 程簡 簡介 介
一、酸性蝕刻的應用: 一、酸性蝕刻的應用: 酸性蝕刻,也叫氯化銅酸性蝕刻系統,通常使用於單面板蝕刻、多層 酸性蝕刻,也叫氯化銅酸性蝕刻系統,通常使用於單面板蝕刻、多層 板的內層蝕刻或 流程的外層蝕刻上,因這些製程都用幹膜或液態感 Tenting 板的內層蝕刻或 Tenting 流程的外層蝕刻上,因這些製程都用幹膜或液態感 光油墨作為蝕刻阻劑,而這幾種感光材料相對而言均為耐酸不耐鹼性的特 光油墨作為蝕刻阻劑,而這幾種感光材料相對而言均為耐酸不耐鹼性的特 性,故選用酸性蝕刻。 性,故選用酸性蝕刻。 二、酸性蝕刻的種類: 二、酸性蝕刻的種類: 1 、 H O /HCl 系列。 22 22 1 、 H O /HCl 系列。 、 系列。 2 NaClO /HCl 33 2 、 NaClO /HCl 系列。
顯 顯影 影( (Developing ) Developing)
九、顯影點( )的控制: Break-Point 九、顯影點( Break-Point )的控制: 、由於顯影速度受到很多因素影響,例如:藥液濃度、噴灑壓力、溫度等, 1 、由於顯影速度受到很多因素影響,例如:藥液濃度、噴灑壓力、溫度等, 1 因此我們通常用顯影點的位置來控制正確的顯影速度。 因此我們通常用顯影點的位置來控制正確的顯影速度。 、顯影點是指在顯影過程中,未經曝光聚合的幹膜在與顯影液反應後被沖刷 2 2 、顯影點是指在顯影過程中,未經曝光聚合的幹膜在與顯影液反應後被沖刷 掉,而顯露出銅面時的位置,而称之。現場生產時,顯影點一般控制在顯 掉,而顯露出銅面時的位置,而称之。現場生產時,顯影點一般控制在顯 影槽的 50%~60% 之間。 影槽的 之間。 50%~60% 3 、顯影點及均勻性的測試: 、顯影點及均勻性的測試: 3 為瞭解顯影點和顯影均勻性的情形,則可用下列方法來測試:取幾片 為瞭解顯影點和顯影均勻性的情形,則可用下列方法來測試:取幾片 較大尺寸(如 × )的銅箔基板以正常流程壓好幹膜,撕掉保護膜 20″ 24″ 較大尺寸(如 20″ × 24″ )的銅箔基板以正常流程壓好幹膜,撕掉保護膜 後連續放置(無間距),以正常速度輸送進顯影槽,當第一片板子即將出 後連續放置(無間距),以正常速度輸送進顯影槽,當第一片板子即將出 顯影槽時關閉噴灑,待板子經過水洗後取出,以顯影槽有效噴灑長度為基 顯影槽時關閉噴灑,待板子經過水洗後取出,以顯影槽有效噴灑長度為基 準依次擺放,檢視板面顯影均勻性。 準依次擺放,檢視板面顯影均勻性。
GC-300S酸性蚀刻液
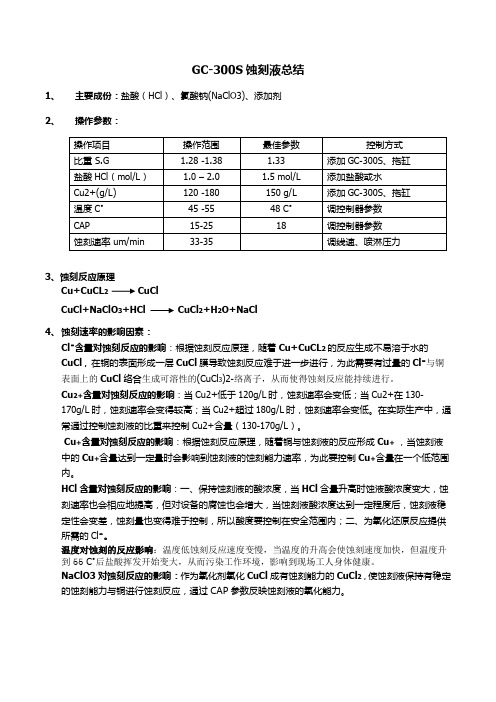
GC-300S蚀刻液总结1、主要成份:盐酸(HCl)、氯酸钠(NaClO3)、添加剂2、操作参数:3、蚀刻反应原理Cu+CuCL2 CuClCuCl+NaClO3+HCl CuCl2+H2O+NaCl4、蚀刻速率的影响因素:Cl¯含量对蚀刻反应的影响:根据蚀刻反应原理,随着Cu+CuCL2的反应生成不易溶于水的CuCl,在铜的表面形成一层CuCl膜导致蚀刻反应难于进一步进行,为此需要有过量的Cl¯与铜表面上的CuCl络合生成可溶性的(CuCl3)2-络离子,从而使得蚀刻反应能持续进行。
Cu2+含量对蚀刻反应的影响:当Cu2+低于120g/L时,蚀刻速率会变低;当Cu2+在130-170g/L时,蚀刻速率会变得较高;当Cu2+超过180g/L时,蚀刻速率会变低。
在实际生产中,通常通过控制蚀刻液的比重来控制Cu2+含量(130-170g/L)。
Cu+含量对蚀刻反应的影响:根据蚀刻反应原理,随着铜与蚀刻液的反应形成Cu+,当蚀刻液中的Cu+含量达到一定量时会影响到蚀刻液的蚀刻能力速率,为此要控制Cu+含量在一个低范围内。
HCl含量对蚀刻反应的影响:一、保持蚀刻液的酸浓度,当HCl含量升高时蚀液酸浓度变大,蚀刻速率也会相应地提高,但对设备的腐蚀也会增大,当蚀刻液酸浓度达到一定程度后,蚀刻液稳定性会变差,蚀刻量也变得难于控制,所以酸度要控制在安全范围内;二、为氧化还原反应提供所需的Cl¯。
温度对蚀刻的反应影响:温度低蚀刻反应速度变慢,当温度的升高会使蚀刻速度加快,但温度升到55 C°后盐酸挥发开始变大,从而污染工作环境,影响到现场工人身体健康。
NaClO3对蚀刻反应的影响:作为氧化剂氧化CuCl成有蚀刻能力的CuCl2,使蚀刻液保持有稳定的蚀刻能力与铜进行蚀刻反应,通过CAP参数反映蚀刻液的氧化能力。
5、配槽步骤*加入CW水至标准液位,喷淋循环清洗半小时,然后排走。
酸性蚀刻液的特性、蚀刻原理

酸性蚀刻液的特性、蚀刻原理1.三氯化铁蚀刻液①特性:三氯化铁蚀刻液用来蚀刻铜、铜合金及铁、锌、铝和铝合金等;适用于网印抗蚀印料、液体感光胶、干膜和金镀层等抗蚀层的印制电路板蚀刻,但不适用于镍、锡及锡铅合金等抗蚀层。
工艺稳定、操作方便、成本低。
但污染严重,废液处理困难。
②化学组成三氯化铁蚀刻液化学组成体三氯化铁按配方要求的百分重量比放入含少量盐酸的水溶液中,在不断搅拌下完全溶解成茶红色液体。
测量其比重或波美度。
然后静止24小时后过滤使用。
特别注意事项:由于固体三氯化铁)沉淀。
易于水解成深黄色氢氧化铁(Fe(0H)3反应式:FeC1+3H2 0→Fe(0H)3+3HCl3所以在配制时先要在水中加适量的盐酸,使反应向左进行,从而抑制水解发生。
由于配制中产生盐酸气体有刺激性,需要在抽风的工作条件下进行。
配制好的溶液以PH≥5为宜。
一般控制溶液浓度在波美度38-42Be0。
(1)蚀刻原理:三氯化铁蚀刻液对铜箔的蚀刻是一个氧化—还原反应过程。
在铜表面三价铁使铜氧化成氯化亚铜。
同时三价铁被还原成二价铁,其反应如下:FeC13+Cu→FeC12+CuC1氯化亚铜具有还原性,可以和三氯化铁进一步发生反应生成氯化铜。
其反应式如下:FeC13+CuC1→FeC12+CuC12二价铜具有氧化性,与铜发生氧化反应:CuC12+Cu→2CuC1所以,三氯化铁蚀刻液对铜的蚀刻是靠Fe3+和Gu2+共同完成的。
其中三价铁的蚀刻速率快,蚀刻质量好;而二价铜的蚀刻速率慢,蚀刻质量差。
新配制的蚀刻液中只有三价铁,蚀刻速率较快。
但随着蚀刻反应的进行,三价铁不断消耗,而二价铜不断增加。
当三价铁消耗掉35%时,二价铜已增加到相当大的浓度,这时三价铁和二价铜对铜的蚀刻量几乎相等;当三价铁消耗掉50%时,二价铜的蚀刻作用由次要地位而转变成主要地位,此时的蚀刻速率慢,这时要考虑蚀刻液的更新问题。
在印制电路板的实际生产中,表示蚀刻液的活度不是采用三价铁的消耗量来度量,而是用蚀刻液中的含铜量(克/升)来度量。
酸性蚀刻液主要成分

酸性蚀刻液主要成分
酸性蚀刻液是一种常见的化学腐蚀剂,它可以有效地在金属或其他金属表面上腐蚀出形状精确的特殊形状。
通常用于零件抛光、硬化表面处理及成型表面处理等。
1.一般成分:
(1)氯化物:对金属表面有腐蚀作用,如氯化钠、氯化钾、氯化铵、氯化氢和其它氯化物。
(2)硝酸盐:强酸性,有腐蚀作用,如硝酸钠、硝酸钾、硝酸铵、硝酸铅和其它硝酸盐。
(3)磷酸盐:有腐蚀作用,如磷酸钠、磷酸钾和其它磷酸盐。
(4)亚硝酸盐:有腐蚀作用,如亚硝酸钠、亚硝酸钾和其它亚硝酸盐。
2.添加剂:
(1)抑制剂:可防止腐蚀剂强烈反应而形成一氧化氮,如磷酸、氟化物和其它抑制剂。
(2)助剂:可增加液体的可控性,如二氧化硅、磷酸二铵、EDTA 等。
(3)调节剂(稳定剂):可稳定液体的pH,如氢氧化钾、硼酸钾和碳酸钠等。
3.其他成分:
(1)抗氧剂:可抑制氧溶液的氧化作用,如柠檬醛、环氧乙烷等。
(2)防腐剂:可延长液体的寿命,如醋酸钠、柠檬酸、双羟脂等。
(3)调香剂:有一定的芳香气味,如苯醇、柠檬醛等。
酸性蚀刻工艺流程教材PPT课件

直觉的联想,在氯化铜酸性蚀刻液中,Cu++ 及Cu+应是以 CuCl2 及CuCl存 在才对,但事实非完全正确,两者事实上 是以和HCl形成的一庞大错化物存在的:
Cu° + H2CuCl4 + 2HCl →2H2CuCl3 ------------(2) 其中H2CuCl4实际是CuCl2和HCl的络合物,而 H2CuCl3则是 CuCl和HCl的络合物
5.蚀刻设备的影响(喷淋方式、喷管和喷咀设计、摇摆、喷 淋压力调节等因素)
6.流体力学方面的影响(表面张力、粘度)
表面张力越小越有利(温度、润湿剂) 蚀刻过程中,随着铜的不断溶解,蚀刻液的粘度就会增加, 使蚀刻液在基板铜箔表面上流动性就差,直接影响蚀刻效果。
四、氯化铜酸性蚀刻液的特性及蚀刻原理 1.特性 • 蚀刻速率易控制,蚀刻液在稳定的状态下,能
达到高的蚀刻质量; • 溶铜量大; • 蚀刻液容易再生与回收,减少污染。 2.蚀刻原理 • 在蚀刻过程中,氯化铜中的二价铜具有氧化性,
能将印制电路板面上的铜氧化成一价铜, 其化学反应如下: 蚀刻反应: Cu+Cucl2→ 2Cucl↓
• 所形成氯化亚铜是不易溶于络离子,其化学反应如下:
在反应式(2)中可知HCl是消耗品。(2)式可以简化成以下两个 反应式。 Cu°+ H2CuCl4 → 2H2CuCl3 + CuCl (不溶) ---------- (3) CuCl + 2HCl → 2H2CuCl3 (可溶) ---------- (4) (3)式中因产生CuCl沉淀,会阻止蚀刻反应继续发生,但因 HCl的存在溶解 CuCl,维持了蚀刻的进行。由此可看出HCl是 氯化铜蚀刻中的消耗品,而且是蚀刻速度控制的重要化学品。
蚀刻安全生产专题培训PPT课件

化学蚀刻过程人体与化学药水接 触时的救治方法代码
代码的救治方法
班组长的安全生产职责(一)
▪ 认真执行有关安全生产的各项规定,模范 遵守安全操作规程,对本班组工人在生产 中的安全和健康负责。
▪ 根据生产任务、生产环境和工人思想状况 等特点,开展安全工作。对新调入的工人 进行岗位安全教育,并在熟悉工作前指定 专人负责其安全。
和,洁地 作规执 须 设不,点 业程行 遵 备使不和 的,安 守 ,用随设 现听全 以 正自便备 象从规 下 确己拆、 作指章 安Leabharlann 职生 责产 (操 一作 )工
人 安 全 生 产
▪
▪ ▪
行人对有 积及 境提术学 为安上权 极时 的合水习 提全级拒 参反 劳理平安 出、单绝 加映 动化,全 批健位接 事、 条建积知 评康和受 故处 件议极识 或的领违 抢理 。,开, 控错导章 救不 改展提 告误人指 工安 善技高 。决忽挥 作全 作术操
蚀刻安全生产专题培训
培训主要内容(一)
一、安全生产的定义 ▪ 安全生产指生产经营活动中的人身安全和
财产安全。 ▪ 人身安全指:保障人的安全、健康、舒适
的工作,称之为人身安全。 ▪ 财产安全:消除损坏设备,产品和其它一
切财产的危害因素,保证生产正常进行。
培训主要内容(二)
▪ 化学蚀刻过程宊发事故的紧急救治方法 ▪ 操作员安全生产职责
班组长的安全生产职责(二)
组织本班组工人学习安全生产规程,检查 执行情况,教育工人在任何情况下不违章 蛮干。发现违章作业,立即制止。
经常进行安全检查,发现问题及时解决。 对不能根本解决的问题,要采取临时控制 措施,并及时上报。全班组工人认真分析, 提出防范措施。
▪ ▪
▪
蚀刻工艺之酸性氯化铜蚀刻液

蚀刻⼯艺之酸性氯化铜蚀刻液⽬录摘要 (1)1设计任务书 (2)1.1项⽬ (2)1.2设计内容 (2)1.3设计规模 (2)1.4设计依据 (2)1.5产品⽅案 (2)1.6原料⽅案 (2)1.7⽣产⽅式 (3)2 ⼯艺路线及流程图设计 (3)2.1⼯艺路线选择 (3)2.2内层车间⼯艺流程简述 (4)3.车间主要物料危害及防护措施 (6)3.1职业危害 (6)3.2预防措施 (6)4.氯酸钠/盐酸型蚀刻液的反应原理 (7)4.1蚀刻机理 (7)4.2蚀刻机理的说明 (8)4.3蚀刻中相关化学反应的计算 (8)5.影响蚀刻的因素 (6)5.1影响蚀刻速率的主要因素 (10)5.2蚀刻线参数设计 (10)6 主要设备⼀览表 (12)7车间装置定员表 (13)8投资表 (13)9安全、环保、⽣产要求 (14)致谢 (15)参考⽂献 (16)蚀刻⼯艺之酸性氯化铜蚀刻液摘要:本⽂介绍了印制电路板制造过程中的酸性氯化铜蚀刻液,并对其蚀刻原理和影响蚀刻的因素进⾏了阐述。
关键词:印制电路板;酸性氯化铜;蚀刻;分类号:F407.7Brief principies to acid chlorination copperetching and factors analysisChen yongzhou (Tutor:Pi-yan)(Department of Chemistry and Environmental Engineering,Hubei NormalUniversity , Huangshi ,Hubei, 435002)Abstract: In this paper acid chlorination etching solution was introduced. Meanwhile the etching principle and the factors affecting the etching rate been explain.Keywords: PCB;acid chlorination copper solution;etching蚀刻⼯艺之酸性氯化铜蚀刻液1设计任务书1.1项⽬氯酸钠/盐酸蚀刻型蚀刻液及其蚀刻⼯艺(初步1.2设计内容车间⼯艺参数设计1.3设计规模1年产:106万FT22年⽣产⽇:4000FT23⽇⽣产能⼒:500000/280=3800 FT2/天1.4设计依据依据有关部门下达的实设计任务书或可⾏性报告的批⽂,环境影响报告书的批⽂,资源评价报告的批⽂, 技术引进合同,设计合同,其他⽂件等1.5蚀刻液主要成分氯酸纳,盐酸,⽔,其他辅助添加剂。
蚀刻液 (2)
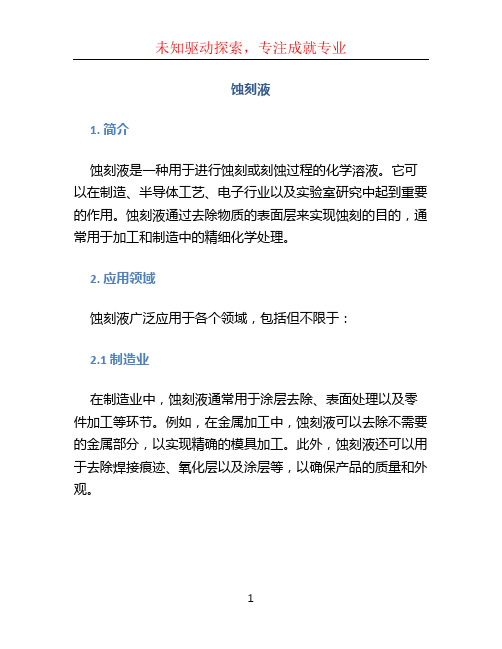
蚀刻液1. 简介蚀刻液是一种用于进行蚀刻或刻蚀过程的化学溶液。
它可以在制造、半导体工艺、电子行业以及实验室研究中起到重要的作用。
蚀刻液通过去除物质的表面层来实现蚀刻的目的,通常用于加工和制造中的精细化学处理。
2. 应用领域蚀刻液广泛应用于各个领域,包括但不限于:2.1 制造业在制造业中,蚀刻液通常用于涂层去除、表面处理以及零件加工等环节。
例如,在金属加工中,蚀刻液可以去除不需要的金属部分,以实现精确的模具加工。
此外,蚀刻液还可以用于去除焊接痕迹、氧化层以及涂层等,以确保产品的质量和外观。
2.2 半导体工艺在半导体工艺中,蚀刻液被广泛用于刻蚀、清洗和去除杂质等工艺步骤。
蚀刻液在半导体工艺中的应用主要是为了制造微细结构和图案,例如芯片和电路板的制造过程。
2.3 电子行业在电子行业中,蚀刻液用于去除电路板上的铜、镀金、镀银以及其他金属材料。
蚀刻液通过蚀刻的方式,可以制作出精细的电路图案和线路结构,以提高电子设备的性能和功能。
2.4 实验室研究在科学研究和实验室领域,蚀刻液常用于材料表面的微观结构分析和样品制备。
科研人员可以通过蚀刻液来观察材料表面的形态和组织结构,以及进行材料的表面改性和修复。
3. 主要类型蚀刻液的种类繁多,不同类型的蚀刻液具有不同的化学成分和蚀刻特性。
以下是一些常见的蚀刻液类型:3.1 酸性蚀刻液酸性蚀刻液是最常见和广泛使用的一类蚀刻液。
它通常由酸和一些辅助剂组成,具有高效的蚀刻速率和较好的选择性。
酸性蚀刻液广泛应用于金属加工、半导体工艺以及电子行业等领域。
3.2 碱性蚀刻液碱性蚀刻液是另一类常见的蚀刻液。
它主要由碱性物质和一些添加剂构成,具有强腐蚀性和高蚀刻速率。
碱性蚀刻液常用于去除金属表面的氧化层和其他杂质。
3.3 有机蚀刻液有机蚀刻液主要由有机酸和一些有机溶剂组成。
它与传统的酸性蚀刻液相比,具有更低的蚀刻速率和更好的选择性。
有机蚀刻液在一些对精度和细节要求较高的应用中得到了广泛应用。
酸性蚀刻液分析方法

一.酸性蚀刻液分析方法:1、 铜离子:取1ml 槽液,加纯水100ml ,加5ml 冰醋酸,加5gKI 并溶解,用0.1N-Na 2S 2O 3滴定至淡黄色时,加淀粉指示剂1ml ,继续用0.1N-Na 2S 2O 3滴定至无色透明为终点。
计算公式:Cu 2+(g/l)=6.35×ml 数×0.1N-Na 2S 2O 3浓度 0.12. 测该溶液的PH 值和比重3. HCl取1ml 槽液,加纯水50ml ,加甲基橙指示剂2滴,用0.2N-NaOH 滴定,颜色由红变黄色为终点.计算公式:HCl (当量)=ml×N NaOH4. H 2O 2浓度的分析方法a. 取样10ml 蚀刻液,用50ml 纯水稀释,再加入10%的硫酸5ml ,用0.1N 高锰酸钾滴定,溶液呈红色15秒不变色即可。
b. 计算:体积百分数:高锰酸钾滴定毫升数×0.43质量百分数:高锰酸钾滴定毫升数×0.17浓度(g/l)=质量百分数×10二.镀铜电镀液①铜金属及硫酸铜取样1ml,加水100ml,加浓氨水5ml,加PAN指示剂,用0.05M的EDTA滴定至蓝色变为绿色。
硫酸铜=ml×160×C(无结晶水)②硫酸取样2ml,加水100ml,加MO 3~4滴,用0.2N的NaOH 滴定至红色变橙色。
硫酸=ml×4.9×f三.氟硼酸系列锡铅镀液①亚锡取样2ml,加水100ml,加浓HCl 2ml, 加2克NaHCO3,加淀粉指示剂1~2ml,用0.1N的I2标准液滴定至蓝色。
亚锡=ml×2.967×f②氟硼酸取样1ml,不放水用1N-NaOH滴定至浑浊为终点氟硼酸=ml×17.56×f×5③二价铅用AA测。
- 1、下载文档前请自行甄别文档内容的完整性,平台不提供额外的编辑、内容补充、找答案等附加服务。
- 2、"仅部分预览"的文档,不可在线预览部分如存在完整性等问题,可反馈申请退款(可完整预览的文档不适用该条件!)。
- 3、如文档侵犯您的权益,请联系客服反馈,我们会尽快为您处理(人工客服工作时间:9:00-18:30)。
若发生下列反应则会发生沉淀物
4CuCl2 + FeCl2 + O2 → 2CuCl Cu O + FeCl3 (黑绿色)
※目前多使用于铁/镍合金蝕刻,如导线架业,PCB厂较少使用。
酸性蚀刻液的概况
二、氯气/盐酸
最高可蚀刻铜约180克/公升 Cu + CuCl2 → 2CuCl 加入1~3N HCl使反应加快,但盐酸不 参与反应,只有带出消耗。
生成的氯 化亚铜不 易溶于水 在铜的表 面形成膜
阻止反 应进一 步进行
过量Cl-与 氯化亚铜 络合形成 可溶性的 络离子 (CuCl3)2-
从铜表 面上溶 解下来
提高蚀 刻速率
影响蚀刻液的因素
Cu+浓度的影响
根据蚀刻反应机理,随着铜的蚀刻就会形成一价铜离子。 较微量的Cu+就会显著的降低蚀刻速率。
酸性蚀刻液的概况
一、氯化铁/盐酸
FeCl3 w/w约40%,HCl约5%,能蚀铜约70克/公升 ������ FeCl ������ ������ 3 + 3H2O → Fe(OH)3 + 3HCl 补充HCl防止沉淀 蚀刻原理: FeCl3 + Cu → FeCl2 + CuCl -----------(1) FeCl3 + CuCl → FeCl2 + CuCl2--------(2) CuCl2 + Cu → 2CuCl---------------------(3) (3)式取代(1)式进行蚀铜反应
※双氧水贮存/稳定性较困难,而且实际消耗盐酸,比用氯气法成本高
酸性蚀刻液的概况
四、氯酸钠/盐酸
最高可蚀刻铜约180克/公升 3Cu + 3CuCl2 → 6CuCl HCl之酸值控制在2.5N以下 6CuCl + NaClO3 + 6HCl → 6CuCl2 + 3H2O + NaCl 净反应: 3Cu + NaClO3 + 6HCl → 3CuCl2 + 3H2O + NaCl ������ ������ ������ ������ ������ ������ ������ 优点:A 于双氧水法比较,盐酸的反应量相同,但盐酸带出量则因浓度为 2.5N一下而大量减少。 B 氯化钠氧化当量为双氧水的三倍,所以双氧水使用量为氯化钠的三倍。 ������ ������ ������ ������ C 目前国外大量使用成本约低于双氧水法10~15%,而且试用小于4mil细 线生产fine line制作。
影响蚀刻液的因素
影响蚀刻速率 主要因素 Cl-的浓度 Cu+的浓度 Cu2+的浓度 蚀刻液的温度
Cl-浓度的影响
当盐酸浓度升高时 蚀刻时间减少 盐酸浓度不可超过6N, 高于6N盐酸的挥发量 大且对设备腐蚀,并且 随着酸浓度的增加,氯 化铜的溶解度迅速降低
添加Cl-可以提高蚀刻速率的原因 氯化铜 溶液中 发生铜 的蚀刻
※目前业界最常用的即为H2O2/HCl系统和NaClO3/HCl系统这两种酸 性蚀刻液。
酸性蚀刻液的概况
酸性蚀刻反应原理分析
以NaClO3/HCl系统为例 1.1、蚀铜反应:铜可以三种氧化状态存在,板面上的金属铜Cu0,蚀刻槽液 中的蓝色离子Cu2+ ,以及较不常见的亚铜离子Cu+ 。金属铜Cu0可在蚀刻槽 液中被Cu2+氧化而溶解,见下面反应式(1) 3Cu + 3CuCl2 → 6CuCl ------------- (1) 1.2、再生反应:金属铜Cu0被蚀刻槽液中的Cu2+氧化而溶解,所生成的2Cu+ 又被自动添加进蚀刻槽液中的氧化剂和HCl经过系列反应氧化成Cu2+,而这些 Cu2+又继续跟板面上的金属铜Cu0发生反应,因此使蚀刻液能将更多的金属铜 Cu0咬蚀掉。这就是蚀刻液的循环再生反应,见下面反应式(2) 6CuCl + NaClO3 + 6HCl → 6CuCl2 + 3H2O + NaCl ------------- (2) 1.3、净反应: 3Cu + NaClO3 + 6HCl → 3CuCl2 + 3H2O + NaCl ------------- (3)
实际生产中通常采用比重法,控制铜含量为120~150克/升
酸、碱性蚀刻液的比较
性能对比
碱性蚀刻液 控制 蚀刻速度 补充药液 自动控制成本 毒性
温度、比重及PH值 约1mil/min 氨水 低 低 因有金属馁错合物, 较不易处理
酸性蚀刻液
温度、比重、HCl及ORP(氧化/还原电位) 约0.5mil/minH2 Nhomakorabea2、HCl
高
高
PH调整即可分离出铜渣
水洗水处理
在蚀刻操作中要保持Cu+的含量在一个低的范围内 Cu2+浓度的影响
Cu2+浓度低于2mol/L时 蚀刻速率较低 2mol/L时速率较高 随着蚀刻反应的不断 进行,蚀刻液中铜的 含量会逐渐增加 铜含量增加到一定浓度 时,蚀刻速率就会下降
为了保持蚀刻液具有恒定的蚀刻速率 必须把溶液中的含铜量控制在一定的范围内
适用领域 抗蚀剂
������干膜、液态光致抗蚀剂等
������ 1.蚀刻速率易控制, 蚀刻液在稳定 状态下能达到高的蚀刻质量 2.溶铜量大 3.蚀刻液容易再生与回收, 从而减 少污染
������
主要特点
1.蚀刻速率快,可达70μm/min以上 侧蚀小 2.溶铜能力高, 蚀刻容易控制 3.蚀刻液能连续再生循环使用, 成本低
酸性蚀刻液
酸、碱性蚀刻液的比较
组成与特点
碱性蚀刻液 主要成分
氯化铜、盐酸、 氯化钠或氯化胺 一般适用于多层印制板的外层 电路图形的制作或微波印制板 阴板法直接蚀刻图形的制作
酸性蚀刻液
氯化铜、氨水、氯化氨, 补助成 分为氯化钻、氯化钠、氯化胺或 其它含硫化合物以改善特性 一般适用于多层印制板的内层 电路图形的制作及纯锡印制板 的蚀刻 图形电镀之金属抗蚀层如镀覆金、 ������ 镍、锡铅合金
2CuCl + Cl2 → 2CuCl2
净反应: Cu + Cl2 → CuCl2
※ 因为氯气管理比较困难,目前只有在美国比较大的PCB厂使用
三、双氧水/盐酸
最高可蚀刻铜约160克/公升 Cu + CuCl2 → 2CuCl HCl的酸值控制在2~3N 2CuCl + H2O2 + 2HCl → 2CuCl2 + 2H2O 净反应:Cu + H2O2 + 2HCl →CuCl2 + 2H2O