隧道超前小导管施工方案
超前小导管施工
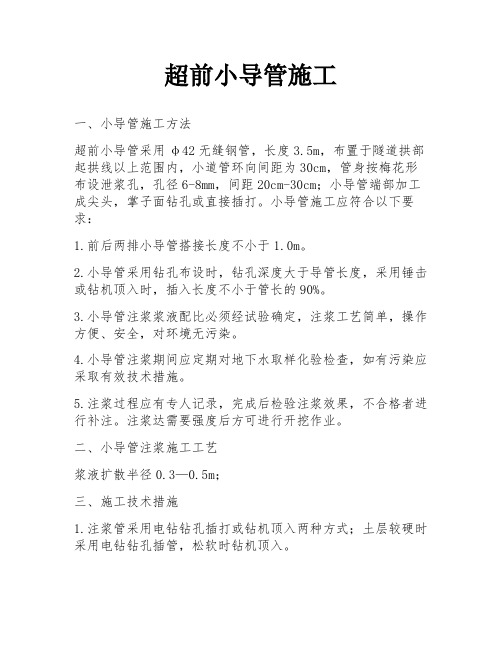
超前小导管施工一、小导管施工方法超前小导管采用φ42无缝钢管,长度3.5m,布置于隧道拱部起拱线以上范围内,小道管环向间距为30cm,管身按梅花形布设泄浆孔,孔径6-8mm,间距20cm-30cm;小导管端部加工成尖头,掌子面钻孔或直接插打。
小导管施工应符合以下要求:1.前后两排小导管搭接长度不小于1.0m。
2.小导管采用钻孔布设时,钻孔深度大于导管长度,采用锤击或钻机顶入时,插入长度不小于管长的90%。
3.小导管注浆浆液配比必须经试验确定,注浆工艺简单,操作方便、安全,对环境无污染。
4.小导管注浆期间应定期对地下水取样化验检查,如有污染应采取有效技术措施。
5.注浆过程应有专人记录,完成后检验注浆效果,不合格者进行补注。
注浆达需要强度后方可进行开挖作业。
二、小导管注浆施工工艺浆液扩散半径0.3—0.5m;三、施工技术措施1.注浆管采用电钻钻孔插打或钻机顶入两种方式;土层较硬时采用电钻钻孔插管,松软时钻机顶入。
2.为防止孔口漏浆,用水泥药卷封堵注浆管与钻孔之间的空隙。
3.为防止注浆管堵塞,影响注浆效果,注浆前先清洗注浆管。
4.压浆管与超前注浆管之间采用方便接头,以便快速安拆。
5.注浆压力由小到大,从开始0MPa升到终止压力1.5MPa,稳压3min,流量计显示注浆量较小时,结束注浆。
6.注浆结束后,拆除注浆接头,迅速用水泥药卷封堵注浆管口,防止未凝固浆液外流。
7.注浆由两侧对称向中间进行,自下而上逐孔注浆,如有窜浆或跑浆时,间隔注浆,最后全部完成注浆。
四、注浆施工技术措施1.严格控制注浆配合比及凝胶时间,初选配合比后,用凝胶时间控制调整配合比,并测定凝结体的强度,选定最佳配合比。
2.严格控制注浆压力,终压必须达设计要求,保持稳压时间,保证浆液渗透范围。
3.注浆完成后要检验注浆效果。
在隧道开挖后可检查注浆固结体厚度,如达不到设计要求时,在注浆时调整注浆参数,改善注浆工艺。
4.注浆过程中,专人记录注浆情况,并根据实际情况调整注浆压力、进度,保证注浆效果。
隧道超前小导管施工方案

隧道施工方案本工程为安徽省滁州市第四水厂引水隧道,本隧道为拱结构隧道。
隧道全长725m,隧道净空(宽×高):2×2.5m,该隧道为泥质粉砂岩夹砂质泥岩。
隧道主要受大气降水和地表水渗入及附近河流渗流补给。
隧道区内地下水补给条件较差,地下水含量高。
隧道涌水量大。
根据滁州地区环境水文化地质条件经验可知,该地地下水对混凝土结构在长期侵入水及干湿交替条件下均具弱腐蚀;对混凝土结构中的钢筋在干湿交替条件下具中腐蚀,长期侵水条件下具微腐蚀;对钢结构具微腐蚀。
场地无污染源,土中的易溶盐已基本溶于水中,土对建筑材料的评价同地下水的腐蚀性评价本隧道为Ⅱ类、III类围岩,地质条件较差,施工中以“弱爆破、少扰动、强支护、早封闭、适时衬砌”为原则,并根据围岩监测结果及时调整施工方案,确保施工安全,保证工程质量。
在施工过程中为保证安全,在进洞前根据现场情况,必须做好超前支护,并且做好引水、截水、排水和挡护设施,防止水害及山体滚石危及安全。
1、进洞前支护土石方开挖后的边坡须做好喷锚支护以及防止山体土石崩塌滚落到洞口造成车和人员的伤亡,洞口顶部必须浇筑挡土墙。
2、施工超前支护为防止石块塌方,必须用锚杆锚住石体,锚杆长度6-8米。
两排纵向与洞口边缘方向呈15°向外插入岩体,每隔300mm一根,两排错开,然后每间隔1米与洞口方向垂直插入岩体,施工要点如下:①选用425号普通硅酸盐水泥,细度模数大于2.5的硬质洁净砂,粒径5~12mm的级配碎石,经化验合格的拌合用水。
喷射砼严格按设计配合比拌和,配合比及搅拌的均匀性每班检查不少于两次。
②喷射前,认真检查隧道断面尺寸,对欠挖部分及所有开裂、破碎、水溶崩解的破碎岩石进行清除和处理,清除浮石和墙角虚碴,并用高压水或风冲洗岩面。
③喷射机安装调试后先注水后通风,清通机筒及管路投料。
连续喂料,经常保持料斗内料满,料斗上设12mm孔径的筛网一道,避免超径骨料进入机内,造成堵管。
三亚绕城公路荔枝沟隧道右线超前小导管施工方案
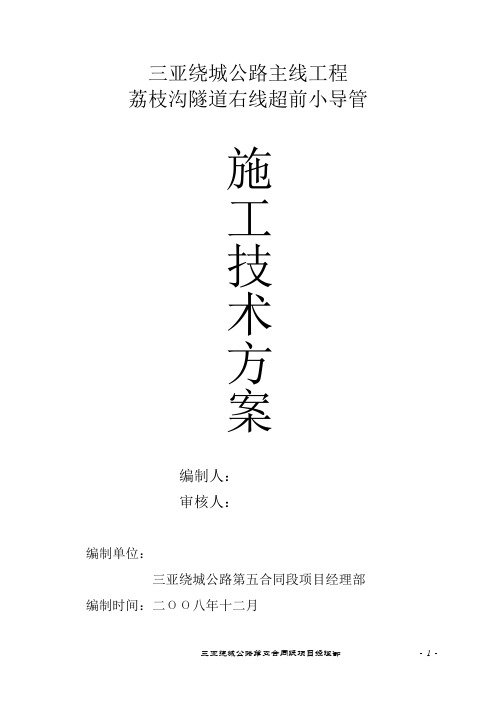
三亚绕城公路主线工程荔枝沟隧道右线超前小导管编制人:审核人:编制单位:三亚绕城公路第五合同段项目经理部编制时间:二ΟΟ八年十二月目目 录录第一章 工程概况 .......................................................... 3 第二章 施工组织及计划 (4)2.1组织机构 .......................................................... 4 2.2施工任务安排 ...................................................... 5 2.3施工进度计划安排 .................................................. 5 2.4劳动力计划安排 .................................................... 5 2.5材料计划安排 ...................................................... 6 2.6设备计划安排 ...................................................... 6 第三章 主要施工方案及施工方法 . (7)3.1主要施工方案 ...................................................... 7 3.2主要施工方法 (7)3.2.1施工工艺流程 ................................................ 7 3.2.2超前小导管设计参数 .......................................... 7 3.2.3钻孔及小导管安装 ............................................ 8 3.2.4注浆 ........................................................ 8 3.2.5注浆异常现象的处理 (9)第四章 质量、安全文明施工保证措施 (9)4.1质量保证措施 (9)4.1.1质量保证组织机构 ............................................ 9 4.1.2质量要求 ................................................... 10 4.1.3质量保证措施 ............................................... 10 4.2安全文明施工保证措施 (11)4.2.1安全文明施工组织机构 ....................................... 11 4.2.2安全文明施工保证措施 (12)三三亚亚绕绕城城公公路路第第五五合合同同段段荔枝沟隧道右线超前小导管施工方案第一章 工程概况荔枝沟隧道为分离式隧道,其起止桩号为:左线K15+025~K16+020,全长995m ;右线YK15+025~YK16+050,全长1025m 。
超前小导管支护要点

超前小导管支护要点导管支护是现代隧道工程中一种常用的支护方法,它能够有效地加固和保护隧道的稳定性。
超前小导管支护是导管支护中的一种特殊形式,它主要用于隧道掌子面的超前工作。
本文将从设计原则、施工方法以及质量控制等方面,详细介绍超前小导管支护的要点。
一、设计原则超前小导管支护的设计需要考虑以下几个原则:1.合理确定导管直径和壁厚,以满足超前工作的要求,并保证支护结构的稳定性。
2.根据地质条件和隧道断面形状,合理确定导管的布设方式和间距。
3.设计导管的连接方式和固定方式,确保导管支护系统的整体稳定性。
4.考虑导管与周围环境的相互作用,如导管与岩体、地下水的相互关系等。
二、施工方法超前小导管支护的施工方法主要包括以下几个步骤:1.导管的制作和加工:根据设计要求,制作导管,并对导管进行加工和处理,以提高其抗压和抗弯能力。
2.导管的布设和安装:根据设计要求,将导管按照一定的布设方式和间距安装在隧道掌子面上,并进行固定。
3.导管的连接:将相邻的导管进行连接,确保导管支护系统的整体稳定性。
4.导管的灌浆:对导管进行灌浆处理,以提高导管的抗压能力和防水性能。
5.导管的检测:对导管进行检测,确保其质量符合设计要求。
三、质量控制超前小导管支护的质量控制主要包括以下几个方面:1.导管的材料:导管的材料应符合相关标准要求,具有足够的强度和耐腐蚀性能。
2.导管的制作和加工:导管的制作和加工应按照相关标准进行,确保导管的尺寸和形状符合设计要求。
3.导管的布设和安装:导管的布设和安装应按照设计要求进行,确保导管的位置和间距符合设计要求。
4.导管的连接:导管的连接应牢固可靠,确保导管支护系统的整体稳定性。
5.导管的灌浆:导管的灌浆应按照相关标准进行,确保灌浆材料的质量和浆液的流动性。
6.导管的检测:导管的检测应包括外观检查、尺寸检测、材料检测等,确保导管质量符合设计要求。
超前小导管支护作为一种有效的隧道支护方法,在隧道工程中具有重要的应用价值。
隧道超前小导管角度定位施工工法(2)

隧道超前小导管角度定位施工工法隧道超前小导管角度定位施工工法一、前言隧道施工是现代城市建设中不可或缺的一环。
为了解决传统隧道施工中存在的问题和缺陷,隧道超前小导管角度定位施工工法应运而生。
本文将对该工法的特点、适应范围、工艺原理、施工工艺、劳动组织、机具设备、质量控制、安全措施、经济技术分析以及工程实例进行详细介绍。
二、工法特点隧道超前小导管角度定位施工工法采用先进的测量和定位技术,能够实现对隧道工作面的精确定位,并准确控制隧道的倾斜和斜度。
该工法具有施工速度快、工程质量高、环境友好、安全可靠等特点。
采用该工法施工的隧道工程不仅能够提高施工效率,还能够减少对地下水、地表建筑物和环境的影响。
三、适应范围隧道超前小导管角度定位施工工法适用于各种隧道工程,特别是在复杂地质条件下的隧道施工中更具有优势。
该工法可适用于不同类型的地质条件,包括软土、湿陷性地层、强风化岩层和断层带等。
此外,该工法还适用于靠近已有建筑物或地下管线的隧道施工,能够降低对周围环境的影响。
四、工艺原理隧道超前小导管角度定位施工工法的工艺原理基于测量和定位技术。
施工前,通过测量和分析地质条件,确定隧道的坡度和斜度要求。
随后,在工作面设置起点导杆,并使用激光仪器精确测量导杆的位置和角度。
在施工过程中,利用导杆的位置和角度信息,控制推进机械的导向,确保隧道工作面能够按照设计要求进行施工。
五、施工工艺隧道超前小导管角度定位施工工法的施工工艺分为准备工作、导向施工、支护施工、喷射混凝土施工和尾巴施工等阶段。
准备工作包括地质勘察、起点导杆设置和机具设备准备。
导向施工阶段主要是通过控制推进机械的导向来实现隧道工作面的定位。
支护施工阶段通过设置支护结构来保持隧道的稳定和安全。
喷射混凝土施工阶段主要是对隧道进行喷射混凝土衬砌。
尾巴施工阶段是对隧道施工的收尾工作。
六、劳动组织隧道超前小导管角度定位施工工法的劳动组织需要合理安排施工人员,包括工程师、技术人员和操作人员等。
超前小导管施工方案

超前小导管施工方案1. 引言超前小导管(Microtunneling)是一种在城市地下进行地下管道和隧道施工的技术。
它通过使用专用的设备和工具,在地下进行孔洞开挖,并将管道或隧道段逐渐推进至目标位置。
这种施工方法具有高效、快速和环保的特点,因此在城市地下管道建设中被广泛应用。
本文将介绍超前小导管施工的方案,包括施工准备、设备和工具、施工步骤等内容。
2. 施工准备超前小导管施工前需要进行一系列的准备工作,以确保施工的顺利进行。
2.1 地勘和设计在施工前,需要进行地勘和设计工作。
地勘工作包括对地下地质条件、地下水位和土体性质的详细调查和分析。
设计工作则根据地勘结果和施工要求,确定导管的布置方案和施工参数。
2.2 材料采购和准备在施工前需要准备导管施工所需的材料,包括导管管道、推进液、润滑剂等。
这些材料需要提前采购,并按照要求进行储存和保管。
2.3 准备施工场地在施工前需要选择合适的施工场地,并进行场地的准备工作。
这包括场地平整、排水系统的建设等。
3. 设备和工具超前小导管施工需要使用一系列特定的设备和工具,以保证施工的高效和质量。
3.1 推进机推进机是超前小导管施工中最关键的设备之一。
推进机通过液压系统提供推进力,驱动导管向前推进。
推进机必须具备稳定的推进性能和精确的控制系统。
3.2 推进液供应系统推进液是超前小导管施工中不可或缺的部分。
推进液具有润滑和冲洗作用,可以减少地层摩阻,保证导管的顺利推进。
推进液供应系统包括贮液池、泵和输送管路等。
3.3 给水系统给水系统用于供应工人所需的清洁水和混凝土搅拌所需的水。
给水系统需要具备稳定的供水能力和满足卫生要求。
3.4 排水系统排水系统用于排除由于施工过程中产生的污水、渗水等。
排水系统应具备高效、可靠的排水功能,以保证施工场地的干燥。
4. 施工步骤超前小导管施工主要包括导管的孔洞开挖和推进两个步骤。
以下是典型的施工步骤:1.定位和设置参考点:根据设计要求,确定导管的位置,并设置参考点。
隧道超前小导管施工方案

目录1、工程概况 (1)1.1 概况 (1)1.2 地形、地貌 (1)1.3 气侯、水文 (2)1.4 各隧道围岩长度 (3)2、编制依据及编制原则 (3)2.1 编制依据 (3)2.2 编制原则 (3)3、准备工作及施工计划 (5)3.1 人员及机械 (5)3.2 材料准备 (6)4、超前小导管施工方案 (6)4.1 超前小导管 (7)5、质量保证体系 (11)5.1 质量管理体系及职责 (11)5.2 质量控制要点 (13)6、安全保证体系 (16)6.1组织措施 (16)6.2 隧道施工安全措施 (19)6.3 施工现场用电安全措施 (19)6.4 机械安全措施 (20)7、应急措施 (23)7.1应急准备 (23)7.2应急物资的准备、维护、保养 (25)7.3报告与报警 (25)7.4 应急措施 (26)7.5应急处置程序 (27)7.6现场保护 (28)7.7现场恢复 (28)7.8事故总结 (29)8、环境保护及水土保持技术保证措施 (31)8.1文明施工方案 (32)8.2文明施工保证措施 (32)隧道超前小导管施工方案1、工程概况1.1 概况莆炎高速公路三明段路基土建工程YA3合同段起点 K297+900位于明溪县盖洋镇葫芦形村,接YA2标段终点K297+895.689设短链4.311m,路线由东往西沿山坡展线,设盖洋互通连接S306,穿雷溪隧道,经西瓜墩,设青瑶大桥跨越X796后进入宁化县泉上镇境内,后沿X796布线,经青瑶村,设泉上隧道,路线终点(K309+620)位于宁化县泉上镇,泉上隧道中,与YA4标段起点对接。
YA3标段路线长11.72公里。
本标段内设置隧道共计1.5座:雷溪隧道,左线长1262m,起止桩号为ZK303+613-ZK304+875;右线长1253m,起止桩号为YK303+618-YK304+871。
泉上隧道,左线长1001m,起止桩号为ZK308+629-ZK309+630;右线长990m,起止桩号为YK308+630-YK309+620。
小溪隧道出口超前支护管棚改超前小导管施工方案

小溪隧道出口超前支护管棚改超前小导管施工方案隧道工程中的超前施工是指在进口端隧道穿越完成之前,提前进行一个或者多个地质不稳定段的处理和支护施工。
小溪隧道出口超前支护管棚改超前小导管施工方案如下:一、工程概况小溪隧道位于市区域内,总长为1000米,采用明挖法施工。
隧道出口处存在地质不稳定的问题,需要进行超前支护施工,以确保隧道的稳定和安全。
二、地质勘察在隧道出口段进行了详细的地质勘察,包括地质构造、地层、水文地质等情况的调查,以了解隧道出口段的地质条件和存在的问题。
根据勘察结果,出口段主要存在以下问题:1.出口段地质构造复杂,存在节理和断层。
2.地层岩性较松散,存在倾倒和滑坡的风险。
3.出口段存在地下水的渗流,增加地质灾害的可能性。
三、超前支护方案根据地质勘察结果和出口段的特点,制定了超前支护方案,具体包括以下措施:1. 预应力锚杆:在超前段隧道出口处进行预应力锚杆的施工,以增强岩体的稳定性和承载力。
根据地质构造和岩性特点,预应力锚杆的间距为2米,采用直径32mm的钢锚杆,锚固长度为8米。
2.支护管棚:在超前段进行支护管棚的施工,以保证施工过程中的安全和顺利进行。
支护管棚采用U型钢支撑和喷射混凝土的结合方式,U型钢支撑的间距为1米。
支护管棚的高度为2米,宽度为4米。
3.排水系统:针对出口段地下水的渗流情况,设置了排水系统,以降低地下水位和减少地质灾害的风险。
排水系统包括水平排水管和垂直排水井,水平排水管位于支护管棚的顶部,垂直排水井位于管棚的两侧。
四、施工方案根据超前支护方案制定了具体的施工方案,包括施工工序和施工措施:1.施工工序(1)准备工作:搭建施工场地,布置施工设备和材料。
(2)预应力锚杆施工:钻孔、锚杆的安装和锚固。
(3)支护管棚施工:挖掘管棚的开挖,U型钢支撑的安装,喷射混凝土的浇筑。
(4)排水系统施工:布置水平排水管和垂直排水井,安装排水设备。
2.施工措施(1)严密监测:在整个施工过程中,设置监测点对地表沉降、地下水位、支护结构的变形进行监测。
隧道超前小导管施工作业指导书

隧道超前小导管施工作业指导书1.适用范围适用于隧道超前小导管的施工。
2.作业准备作业指导书编制后,在施工前组织技术人员认真学习实施性施工组织设计,阅读、审核施工图纸,熟悉规范和技术标准。
制定施工安全保证措施,提出应急预案。
对参加施工人员进行技术交底及上岗前技术培训,考核合格后持证上岗。
3.技术要求⑴钻孔采用钻孔台车钻孔,钻头采用钻孔直径为50mm的大钻头,钻孔时,外插角控制在1~3°,可根据实际情况调整,钻孔深度应大于钢管长度。
⑵小导管安装钻孔完成后,用高压风管吹除孔内残渣,即可进行插管。
采用锤击或钻机顶入的方法将加工好的导管插入孔内,顶入长度不小于管长的90%。
插管完成后及时安装型钢拱架,将导管尾部焊接在型钢拱架上,使其与拱架形成联合支护体系。
⑶注浆插管后进行注浆,注浆机械采用注浆机,注浆液采用M20水泥浆或水泥砂浆,注浆压力控制在0.5~1.0Mpa以内。
4.施工程序与工艺流程施工工艺流程见下图超前小导管施工工艺流程图5.施工要求5.1 超前小导管设计超前小导管配合型钢钢架使用,应用于隧道Ⅳ、Ⅴ级围岩拱部超前注浆预支护,其纵向搭接长度不小于1m。
超前小导管设计参数:①超前导管规格:符合设计要求;②小导管环向间距40cm;③倾角:外插角1°~3°,可根据实际情况调整;④注浆材料:M20水泥浆或水泥砂浆;⑤设置范围:拱部135°范围。
5.2 超前小导管施工5.2.1 制作钢花管小导管前端做成尖锥形,尾部焊接φ8mm钢筋加劲箍,管壁上每隔10~20cm梅花型钻眼,眼孔直径为6~8mm,尾部长度不小于30cm作为不钻孔的止浆段。
小导管构造见下图。
注浆小导管结构图5.2.2 小导管安装⑴测量放样,在设计孔位上做好标记,用凿岩机或煤电钻钻孔,孔径较设计导管管径大20mm以上。
⑵成孔后,将小导管按设计要求插入孔中,或用凿岩机直接将小导管从型钢钢架上部、中部打入,外露20cm支撑于开挖面后方的钢架上,与钢架共同组成预支护体系。
超前小导管的施工方案

超前小导管施工方案超前小导管管径选用φ42*3.5mm的热轧无缝钢管,长3.5m,外插角10°~15°,管壁每隔25cm交错钻眼,孔口100cm段不钻孔,眼孔直径6mm,采用水泥砂浆或水泥水玻璃浆液灌注,导管环向间距40mm,纵向2.0m一环。
1、超前小导管基本施工方法如下:⑴掌子面封闭:掌子面用C25喷射混凝土封闭。
⑵钻孔、插小导管:进行孔位测量放样,孔位测量做到位置准确,钻孔按放样进行,并设方向架控制钻孔方位,使孔位外插角度符合设计要求。
人工手持风枪一次钻孔完成。
⑶清孔:用高压风、水清洗,吹冲干净孔内砂尘及积水,所有钻孔完成均进行检验。
⑷装入钢管:用风镐将钢管推送入孔。
⑸注浆:注浆顺序由下向上进行,浆液用拌合机搅拌。
注浆浆液以水泥单液浆,其水灰比1∶1,注浆压力为0.5~1.5MPa,水泥标号525号普通硅酸盐水泥。
施工中根据现场试验确定合理的注浆参数。
2、超前小导管施工方法及施工工艺对于小或少水、充填物为块石、碎石、碎屑类松散体,则采用小导管注浆;在采用以上超前注浆和长管棚注浆加固地层的效果欠佳段采用小导管注浆补救。
永定一号隧道Ⅴ级围岩段采用φ42mm小导管超前支护,配合钢架使用,每2榀钢架打一环,环向间距40cm,每根长3.5m,纵向每2 m 设置一环;Ⅴ级围岩双车道每环23根,单车道每环17根,沿隧道开挖轮廓线环向布置并向外倾斜,其倾斜角一般为10~15度左右;注浆压力为0.5~1.0MPa ,纵向前后相邻排导管搭接水平投影长度不小于1.0m ;注浆导管环向间距a=0.4m 。
导管钻φ6mm 注浆孔,间距25cm ,呈梅花形布置,前端加工成锥形,尾部长度不小于100cm 作为不钻孔的止浆段。
超前小导管施工工艺框图见下图准备工作机具准备及检修制作小导管封闭工作面安设小导管钻孔联结管路及密封孔口压水检查达到要求?注浆压力流量达到要求?结束拌浆否否是是超前小导管施工工艺框图为充分发挥机械效能,加快注浆进度,在小导管前安设分浆器,一次可注入3~5根小导管。
隧道超前小导管施工方案

隧道超前小导管施工方案一、编制依据二、工程概况一)、工程简介二)、工程地质概况1、地形地貌隧道区属构造—侵蚀丘陵地貌区,穿越浑圆状山体,沟谷切割较深,多呈“U”型峡谷,自然坡角20~35°。
山脉总体呈东西向,山顶呈圆状,多发育树枝状冲沟,沟内一般无水地表径流。
地表植被不甚发育,多以稀疏林木为主,进口地带有乡间简易公路到达,交通较为不便。
2、地质岩性根据工程地质调查、钻探及物探资料,本隧道地段围岩主要为元古代武当群(Ptw)2片岩和白垩—第三系(K-E)砾岩;两岩性呈角度不整合接触;斜坡坡面和低洼冲沟内e1+d1)粉质粘土层。
覆盖第四系残坡积(Q43、地震基本烈度隧道场区地震动反应谱特征周期为0.35s,地震动峰值加速度分区属0.05g区,相当于原地震基本烈度VI度区。
依据《公路工程抗震设计规范》(JTJ004-89)有关规定,该隧道可比基本烈度提高一度采取抗震措施。
4、水文特征隧道区地表水系不发育,隧道区多发育树枝状冲沟,沟内一般无地表水径流。
但在雨季会出现短暂地面渗流,流量较小,对隧道施工影响较小。
隧道区地下水类型主要为基岩裂隙水,其次为残坡积碎石质粉质粘土层中的孔隙水。
分部零星、不稳定,水量亦随季节变化。
三)、工程概述隧道净空断面采用三心圆曲墙式衬砌,隧道洞身所穿越围岩为Ⅴ~Ⅲ级及断层带,采用Φ42小导管超前支护辅助施工。
隧道主洞开挖最大尺寸为宽×高=12.92m×10.3m。
隧道衬砌内净空宽度为11.2米。
限界净宽:10.25m,限界净高: 5.0m。
紧急停车带开挖尺寸为宽×高=15.637m×10.94m。
隧道衬砌内净空宽度为14.057米。
限界净宽:13m,限界净高: 5.0m。
四)、施工条件和主要技术标准1.设计标准公路等级:双向四车道高速公路隧道净宽:10.25m隧道净高:5.0m设计速度:80km/h设计荷载:公路-Ⅰ级2.施工条件本隧道为新建左右幅分离式双洞隧道,进口有村村通公路,施工场地宽阔,施工用水取自洞口自然沟,出口有新修的2#施工便道接茶青公路,物资供应方便,交通便利。
隧道超前小导管(含超前锚杆)施工
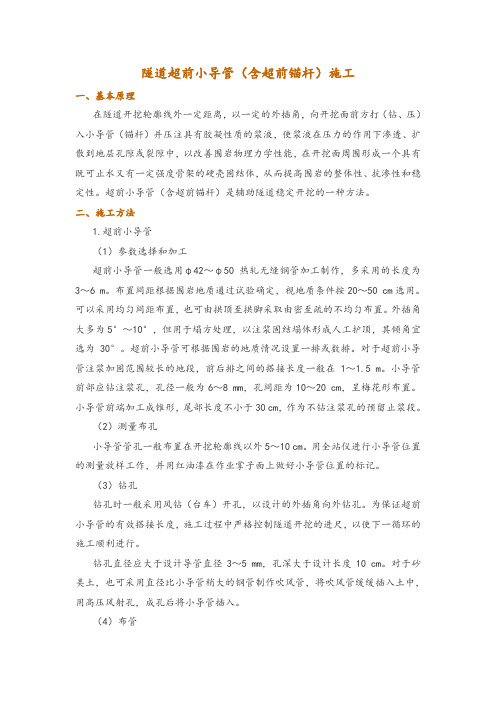
隧道超前小导管(含超前锚杆)施工一、基本原理在隧道开挖轮廓线外一定距离,以一定的外插角,向开挖面前方打(钻、压)入小导管(锚杆)并压注具有胶凝性质的浆液,使浆液在压力的作用下渗透、扩散到地层孔隙或裂隙中,以改善围岩物理力学性能,在开挖面周围形成一个具有既可止水又有一定强度骨架的硬壳固结体,从而提高围岩的整体性、抗渗性和稳定性。
超前小导管(含超前锚杆)是辅助隧道稳定开挖的一种方法。
二、施工方法1.超前小导管(1)参数选择和加工超前小导管一般选用φ42~φ50热轧无缝钢管加工制作,多采用的长度为3~6 m。
布置间距根据围岩地质通过试验确定,视地质条件按20~50 cm选用。
可以采用均匀间距布置,也可由拱顶至拱脚采取由密至疏的不均匀布置。
外插角大多为5°~10°,但用于塌方处理,以注浆固结塌体形成人工护顶,其倾角宜选为30°。
超前小导管可根据围岩的地质情况设置一排或数排。
对于超前小导管注浆加固范围较长的地段,前后排之间的搭接长度一般在1~1.5 m。
小导管前部应钻注浆孔,孔径一般为6~8 mm,孔间距为10~20 cm,呈梅花形布置。
小导管前端加工成锥形,尾部长度不小于30 cm,作为不钻注浆孔的预留止浆段。
(2)测量布孔小导管管孔一般布置在开挖轮廓线以外5~10 cm。
用全站仪进行小导管位置的测量放样工作,并用红油漆在作业掌子面上做好小导管位置的标记。
(3)钻孔钻孔时一般采用风钻(台车)开孔,以设计的外插角向外钻孔。
为保证超前小导管的有效搭接长度,施工过程中严格控制隧道开挖的进尺,以使下一循环的施工顺利进行。
钻孔直径应大于设计导管直径3~5 mm,孔深大于设计长度10 cm。
对于砂类土,也可采用直径比小导管稍大的钢管制作吹风管,将吹风管缓缓插入土中,用高压风射孔,成孔后将小导管插入。
(4)布管钻孔完毕后,通常要对钻孔进行冲洗并检查钻孔孔深、孔径和倾斜度符合设计要求后,方能进行小导管的安装,工程中多采用气水联合法对钻孔进行冲洗。
隧道超前小导管角度定位施工工法

隧道超前小导管角度定位施工工法的理论依据是利用小导管的角度测量精度和精确定位技术来实现隧道的施工。工艺原理主要包括以下方面:1.设置控制点,根据设计要求设置隧道的控制点,并通过全站仪等测量设备进行定位。2.安装小导管,将小导管按照设计要求安装在控制点上,并进行初步调整。3.进行角度测量,利用全站仪等测量设备对小导管进行角度测量,并通过数据处理得到隧道的走向和坡度。4.根据测量结果进行调整,根据测量的数据对小导管进行调整,以保证隧道的施工达到设计要求。
结论
隧道超前小导管角度定位施工工法是一种高效、省时、省力、经济的隧道施工方法。通过合理的劳动组织、科学的工艺原理、严格的质量控制和安全措施,该工法能够在实际工程中取得良好的效果。然而,在使用该工法时,需要结合实际情况进行合理的设计和施工方案制定,以确保施工过程的稳定和成功。同时,对机具设备的选择和使用也需要根据工程的具体要求进行合理搭配和操作。通过对该工法的实际应用和经济技术分析,可以为其他类似工程的施工提供参考和借鉴,促进隧道建设的进一步发展和高效进行。
六、劳动组织
隧道超前小导管角度定位施工工法的劳动组织主要包括以下方面:1.设计人员,负责隧道的设计和施工方案的制定。2.测量人员,负责控制点的设置和角度测量工作。3.施工人员,负责小导管的安装、角度调整以及隧道的挖掘和衬砌工作。4.监理人员,负责对施工过程的监督和质量的控制。
七、机具设备
隧道超前小导管角度定位施工工法所需的机具设备主要包括以下几种:1.全站仪,用于角度测量和数据记录。2.小导管,用于定位和调整。3.挖掘机、推土机等施工机械,用于隧道的挖掘和衬砌工作。
五、施工工艺
隧道超前小导管角度定位施工工法的施工工艺主要包括以下阶段:1.设置控制点,根据设计要求确定隧道的控制点,并进行测量和标定。2.安装小导管,根据控制点的位置和要求,将小导管安装在合适的位置,并进行初步调整。3.进行角度测量,使用全站仪等测量设备对小导管进行角度测量,并记录相关数据。4.根据测量结果进行调整,根据测量的数据对小导管进行调整,以保证隧道的走向和坡度达到设计要求。5.进行隧道的挖掘和衬砌,根据小导管的定位结果进行隧道的挖掘和衬砌工作。6.完成隧道施工,根据设计要求完成隧道的施工工作。
超前小导管

超前小导管一、施工方法1、超前小导管施工方法(1)施工步骤①画出孔位→②钻孔→③安装钢管→④孔口止浆塞→⑤喷砼形成止浆墙→⑥注浆→⑧注浆结束、拆除注浆系统(2)施工方法①按设计间距画出需布设的孔位,YT28风钻钻孔,高压风水清孔;②直接用钻机利用杆尾连接套将钢管沿设计孔位和外插角打入围岩,孔口安装止浆塞,钢管应从紧靠开挖面的格栅拱架腹部穿过,尾部与格栅焊连;③喷砼封闭拱架及其周围开挖面作为止浆墙;④采用注浆泵定量注浆。
2、系统锚杆及辅助钢筋网施工新开岭隧道系统锚杆Ⅴ级围岩一般段使用φ25中空注浆锚杆,长3.5m。
现将施工工艺和方法陈述如下:(1)施工顺序①钻孔→②清孔→③插入锚杆→④安设止浆塞、垫板及排气管→⑤配制浆液→⑥注浆→⑦铺设钢筋网(2)施工方法①画眼:开挖断面检查合格后,按设计要求在岩面栅画出本次锚杆孔位。
②钻孔:采用YT28风钻或锚杆钻机钻孔。
钻孔技术要求:孔径φ38~45mm;开口偏差小于2%;孔深比锚杆插入部分长3~5cm。
③将锚杆慢慢插入距孔底3~5cm处。
杆体插入后,孔口安装止浆塞,垫板,并设置排水孔。
④配制浆液:水泥砂浆粘结剂配合比为,水泥:砂=1:1,水灰比0.35-0.45,水泥采用P0.32.5新鲜硅酸盐水泥,砂径不大于2.5mm,并掺入0.5~1%FDN早强减水剂,5%氧化镁膨胀剂。
⑤注浆:运用配套的锚杆专用注浆机向孔内注入早强砂浆,注浆压力调整在0.5~Mpa,使浆液慢慢注入,当排水孔有浆液流出时,关闭排气孔,稳定注入3~5分钟后停止注浆。
⑥铺设钢筋网:钢筋网用φ6mm、8mm钢筋,网格为20cm,网片铺设随岩面起伏铺贴。
钢筋网与锚杆交叉点采用焊接,钢筋网保护层大于2.5cm。
(3)施工技术措施①开挖后,立即检查围岩面,初喷混凝土,及时施作系统锚杆。
②锚杆原材料规格、长度、直径符合设计要求,锚杆杆体不能有油污或其它不符合规范要求的缺陷。
锚杆孔位。
孔深及布置形式符合设计要求,注浆用浆液通过试验确定,凝结锚固强度不低于设计值。
超前小导管施工作业指导书

超前小导管施工作业指导书一、超前小导管的作用及适用条件超前小导管适用于V级围岩、Ⅳ级围岩浅埋段、软弱地层及断层破碎带的拱部注浆预支护。
其目的是加固周边一定范围围岩,与刚架组合成预支护系统,控制软弱围岩变形量。
本隧道工程超前支护采取单排和双排超前小导管支护,与钢架联合使用,单排外插角为10°,环向间距40cm。
双排外插角为10°和40°,环向间距为30cm,并注浆。
二、施工工艺及方法(一)超前小导管施工作业流程图(二)施工工艺及方法1、测量放线技术室按照设计尺寸在掌子面绘出开挖轮廓线,并在开挖轮廓线上按设计间距定出小导管中心位置,标出钻杆方向。
2、钻孔小导管钻孔采用手风钻造孔。
钻孔时采用普通钻杆,钻头采用直径Φ50钎头,以满足成孔后孔径大于钢管直径3~5mm 的要求。
钻孔时严格按定出的孔位进行,施钻过程中及时观察钻杆方向及外插角度,当发现方向及外插角偏差较大时应予以调整。
以保证钻孔按设计要求完成,小导管能起到预期的支护效果。
3、小导管制作及安装超前小导管采用壁厚3.5mm 、外径42mm 、长4.5m 及壁厚5mm 、外径50mm 、长5m 的热轧无缝钢管制成。
并在小导管前部钻注浆孔,孔径6~8mm ,孔间距15cm ,呈梅花型布置,前端加工成锥形,尾部留长度不小于30cm ,作为不钻孔的止浆段。
小导管的加工在钢筋加工场完成。
小导管制作大样图小导管安装在现场由锤击打入或钻机顶入,要求顶入长度不小于设计长度的90%。
小导管安装完成后及时用高压风将钢管内的砂石吹干净,并用塑胶泥封堵孔口及周围裂隙,必要时在小导管附近及工作面喷射混凝土,以防止工作面坍塌。
小导管安装完成后及时报质检工程师和监理工程师检查签认。
4、注浆小导管注浆采用水泥浆液,其施工配合比为1:1(重量比),根据隧道内围岩情况,注浆时取压力为0.5~1.0Mpa。
注浆过程中及时观察掌子面围岩情况,并根据吸浆量及压力上升情况,当两者之一达到设计规定时可结束注浆作业。
超前小导管注浆施工方案
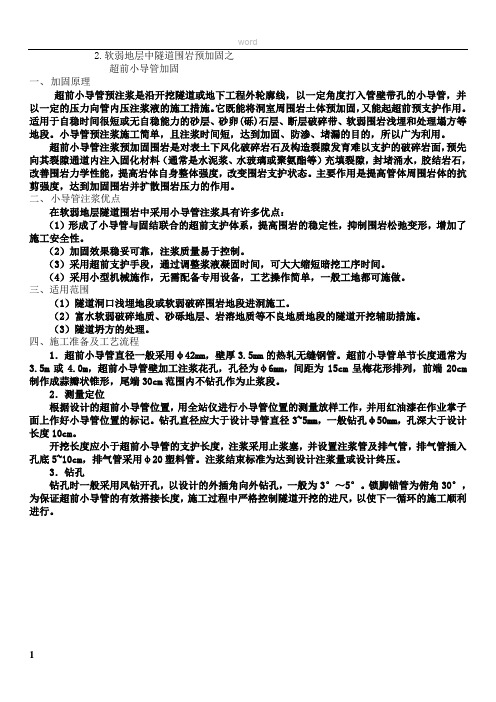
word2.软弱地层中隧道围岩预加固之超前小导管加固一、加固原理超前小导管预注浆是沿开挖隧道或地下工程外轮廓线,以一定角度打入管壁带孔的小导管,并以一定的压力向管内压注浆液的施工措施。
它既能将洞室周围岩土体预加固,又能起超前预支护作用。
适用于自稳时间很短或无自稳能力的砂层、砂卵(砾)石层、断层破碎带、软弱围岩浅埋和处理塌方等地段。
小导管预注浆施工简单,且注浆时间短,达到加固、防渗、堵漏的目的,所以广为利用。
超前小导管注浆预加固围岩是对表土下风化破碎岩石及构造裂隙发育难以支护的破碎岩面,预先向其裂隙通道内注入固化材料(通常是水泥浆、水玻璃或聚氨酯等)充填裂隙,封堵涌水,胶结岩石,改善围岩力学性能,提高岩体自身整体强度,改变围岩支护状态。
主要作用是提高管体周围岩体的抗剪强度,达到加固围岩并扩散围岩压力的作用。
二、小导管注浆优点在软弱地层隧道围岩中采用小导管注浆具有许多优点:(1)形成了小导管与固结联合的超前支护体系,提高围岩的稳定性,抑制围岩松弛变形,增加了施工安全性。
(2)加固效果稳妥可靠,注浆质量易于控制。
(3)采用超前支护手段,通过调整浆液凝固时间,可大大缩短暗挖工序时间。
(4)采用小型机械施作,无需配备专用设备,工艺操作简单,一般工地都可施做。
三、适用范围(1)隧道洞口浅埋地段或软弱破碎围岩地段进洞施工。
(2)富水软弱破碎地质、砂砾地层、岩溶地质等不良地质地段的隧道开挖辅助措施。
(3)隧道坍方的处理。
四、施工准备及工艺流程1.超前小导管直径一般采用φ42mm,壁厚3.5mm的热轧无缝钢管。
超前小导管单节长度通常为3.5m或4.0m,超前小导管壁加工注浆花孔,孔径为φ6mm,间距为15cm呈梅花形排列,前端20cm 制作成蒜瓣状锥形,尾端30cm范围内不钻孔作为止浆段。
2.测量定位根据设计的超前小导管位置,用全站仪进行小导管位置的测量放样工作,并用红油漆在作业掌子面上作好小导管位置的标记。
钻孔直径应大于设计导管直径3~5mm,一般钻孔φ50mm,孔深大于设计长度10cm。
- 1、下载文档前请自行甄别文档内容的完整性,平台不提供额外的编辑、内容补充、找答案等附加服务。
- 2、"仅部分预览"的文档,不可在线预览部分如存在完整性等问题,可反馈申请退款(可完整预览的文档不适用该条件!)。
- 3、如文档侵犯您的权益,请联系客服反馈,我们会尽快为您处理(人工客服工作时间:9:00-18:30)。
注浆:注浆压力控制在0.5〜I.OMPa,并随时排除孔中空气,保证锚
杆砂浆饱满。
c.挂网
按设计要求加工钢筋网,随受喷面起伏铺设,并将钢筋网同定位锚 杆固定牢固,钢筋网与受喷面的间隙以3cm左右为宜。砼保护层厚度应 大于2cm。
钢架的架设应由专人按规定的信号进行指挥,随时观察围岩动态或 喷射砼的情况,防止落石,坍塌引起伤人事故。
在架设钢架前应采用垫板将钢架基础找平,架设时,应将钢架与定 位锚杆固定,用纵向连接筋连接牢固,防止发生钢架倾覆或扭转。
当紧固顶部连接螺栓,楔紧钢架时,作业人员应以正确的姿势站在 平稳,牢固的脚手架上,并配带安全防护用具防止发生坠落事故。
施工要点如下:
1选用425号普通硅酸盐水泥,细度模数大于2.5的硬质洁净砂, 粒径5〜12mm的级配碎石,经化验合格的拌合用水。喷射砼严格按设 计配合比拌和,配合比及搅拌的均匀性每班检查不少于两次。
2喷射前,认真检查隧道断面尺寸,对欠挖部分及所有开裂、破碎、 水溶崩解的破碎岩石进行清除和处理,清除浮石和墙角虚碴,并用高压 水或风冲洗岩面。
风压和喂料量, 应根据喷射部位不同, 以及采用的喷射机型号进行 调整。
4喷射砼的养护:喷射砼终凝2小时后,进行喷水养护,养护时间 不少于14天。爆破作业距喷射砼完成时间不小于4小时。
有水地段喷射砼采取如下措施:
当水点不多时, 可设导管引排水后再喷射砼; 当涌水量范围较大时, 可设小导管注浆止水,然后再喷砼;当涌水严重时可设置泄水孔,边排 水边喷砼。
(1)钻孔:钻孔工艺流程见下图
施工要点如
下:
1 在开挖外 轮廓线以外施作C25砼拱作为长 管棚导向墙,使用 水平液压钻机施 钻。经过几次接杆 完成长管棚钻孔。钻孔时随着孔深的增长,需要对回转扭矩、冲击力及 推力进行控制和协调,尤其是推力要严格控制,不能过大。
2为了确保钻杆接头有足够的强度、 刚度和韧性,钻杆联接套应与 钻杆同材质,两端加工成内螺扣(钻杆首尾端外螺扣) ,联接套的最小 壁厚》10mm。连接套及连接方式见右图。
c.使用水平液压钻机施作大管棚施工时,用于钻引导孔的冲击钻头
①127Байду номын сангаасm,在顶管大臂的凿岩机上安装与管棚直径相应的钢管顶进联 接套。
d.顶管作业: 先将钢管安放在大臂上后, 凿岩机要对已钻好的引导 孔,低速推进钢管,其冲击压力控制在1 8-22Mpa,推进压力控制在4.0-6.0Mpa。
e.接管:当第一根钢管推进孔内,孑L外剩余30-40cm时,开动凿
对钢架应随时检查,如发现扭曲,压屈现象或征兆时,必须及时采 取加固措施。必要时应使其他人员撤到安全地带,防止因坍塌造成伤亡 事故。
e大管棚超前支护
引水隧道为H、III类围岩,设计采用了①108大管棚超前支护。根 据我单位同类工程的施工经验,拟采用水平钻机施作较为经济,不仅速 度快,而且作业安全。注浆部分参照小导管注浆工艺。
8引导孔直径应比棚管外径大15-20mm,孔深要大于管长0.5m以上。
9钻孔达到要求深度后,按同样方法拆卸钻杆,钻机退回原位。
(2)顶管:
1施工工艺流程见下图。
2顶管工艺
采用大孔引导和管棚钻进相结合的工艺,即先钻大于棚管直径的引 导孔,然后利用改装后钻机的冲击和推力,将安有工作管头的棚管沿引
导孔钻进,接长棚管,直至孔底。
为防止钻杆在推力和振动力的双重作用下, 上下颤动,导致钻孔不直, 钻孔时,应把扶直器套在钻杆上,随钻杆钻进向前平移。
3钻孔前由测量工准确画出钻孔位置
4施钻时,钻机大臂必须顶紧在掌子面上, 以防止过大颤动,提高
施钻精度
5钻机开孔时钻速宜低,钻深20cm后转入正常钻速。
6第一节钻杆钻入岩层尾部剩余20-30cm时钻进停止,用两把管
钳人工卡紧钻杆(注意不得卡丝扣),钻机低速反转,脱开钻杆。钻 机沿导轨退回原位,人工装入第二根钻杆,并在钻杆前端安装好联接套,
钻机低速送至第一根钻杆尾部,方 向对准后联接成一体。
每次接长钻杆,均可按上述方
法进行。
7换钻杆时,要注意检查钻杆 是否弯曲,有无损伤,中心水孔是 否畅通等,不符合要求的应更换以确保正常作业
力为2.0Mpa。浅埋地段及围岩破碎且富水地段,建议在钢管内应先放 置①20钢筋笼,再向管内充填水泥砂浆用以加强管棚的刚度。
e.超前小导管预注浆
(1)施工方法:
采用现场加工小钢管,喷射砼封闭岩面,用凿岩机钻孔再装钢管或 用凿岩机直接将小钢管打入岩层,按设计要求注浆。注浆顺序为先注无 水孔,后注有水孔,从拱顶顺序向下进行。工艺流程见下图:
钢拱架安装左右偏差应小于5cm,倾斜角应小于2°。控制钢拱架 受力情况的薄弱环节在于节点联结螺栓, 定位锚杆及纵向连结筋, 因此, 所有螺栓要上齐,旋紧、拧好,必须安设垫片后再拧紧螺栓,按设计焊 连定位锚杆和纵向连接筋,确保安装质量。
钢架施工中的安全注意事项 在搬运过程中,应将钢架构件绑扎牢固,以免发生碰伤人,车辆倾 覆,构件坠落等事故。
3钢管顶进的作业要点
a.管件制作:管棚采用①108无缝钢管,管棚接长时先将第一根
钢管顶入钻好的孔内,再逐根联接。事先加工好的管节联接套,要预先
焊接在每节钢管两端, 便于联接。 第一根钢管前端要焊上合金钢片空心 钻头,以防管头顶弯或劈裂。
b.接长管件应满足管棚受力要求, 相邻管的接头应前后错开, 避免 接头在同一断面受力。
隧道施工方案
本工程为安徽省滁州市第四水厂引水隧道,本隧道为拱结构隧道。
隧道全长725m,隧道净空(宽X高):2X2.5m,该隧道为泥质粉砂岩
夹砂质泥岩。隧道主要受大气降水和地表水渗入及附近河流渗流补给。 隧道区内地下水补给条件较差,地下水含量高。隧道涌水量大。
根据滁州地区环境水文化地质条件经验可知,该地地下水对混凝土 结构在长期侵入水及干湿交替条件下均具弱腐蚀;对混凝土结构中的钢 筋在干湿交替条件下具中腐蚀,长期侵水条件下具微腐蚀;对钢结构具 微腐蚀。
超前小导管预注浆参数选择参考:注浆压力0.5〜I.OMpa,水泥浆 水灰比1:1,水泥标号为425号。施工中每孔注浆量达到设计注浆量 时,或注浆压力达到在1.0Mpa时,可以结束注浆。超前小导管尾端焊 于型钢支架腹部。
(3)施工注意事项:导管应在开挖轮廓线上按设计位置及角度打入,孔位误差不得大于10cm,角度误差不得大于3° ,超过允许误差时, 应在距离偏大的孔间 补管后再注浆。
3喷射机安装调试后先注水后通风,清通机筒及管路投料。连续喂 料,经常保持料斗内料满,料斗上设12mm孔径的筛网一道,避免超 径骨料进入机内,造成堵管。喷射时,先注水(注意喷嘴要朝下,避免 水流入输料管),后送风, 然后上料, 根据受喷面和喷出的拌和物情况调 整注水量,以喷后易粘着,回弹小和表面呈湿润光泽为度。
1、进洞前支护 土石方开挖后的边坡须做好喷锚支护以及防止山体土石崩塌滚落到 洞口造成车和人员的伤亡,洞口顶部必须浇筑挡土墙。
2、施工超前支护
为防止石块塌方,必须用锚杆锚住石体,锚杆长度6-8米。两排纵
向与洞口边缘方向呈15°向外插入岩体,每隔300mm一根,两排错 开,然后每间隔1米与洞口方向垂直插入岩体,
喷射顺序:采取分段、分块,先墙后拱,自下布上的顺序,进行喷 射作业。隧道内沿纵向3〜4m为一段,每2m宽为一片。
喷射时,喷嘴做缓慢的螺旋形运动,使喷射料束运动轨迹呈环形螺 旋式移动,旋转直径约20〜30cm,自喷射面的下部开始,水平旋转喷 射,喷料要一圈压半圈,喷至段尾时上移返回,同时要求一排压排,如 此往复喷射。喷射时如有个别受喷面凹洼不平应先喷该处,大致找平。
d.钢架
安装工艺流程见下图。
钢拱架安装工艺流程图
安装前分批检查验收加工质量(结构尺寸、焊接情况是否符合要求)
清除底脚处浮碴,超挖处加设钢(木)垫块,其中间段接头板用砂子埋 住,以防砼堵塞接头板螺栓孔。
按给定的中线,水平标高,标准间距垂直架立,支撑钢架应与围岩
尽量靠近,留2〜3cm的间隙做保护层,当钢架与围岩间隙较大时,安 设鞍形砼垫块,确保岩面与拱架密贴。
钢管每根实际打入长度不得短于设计长度,否则开挖1米后补管、 注浆。
检查钻孔、打管质量时,应画出草图,以孔位编号、逐孔、逐根检 查并认真填写记录。
单孔注浆量不得小于计算值的80%,超过偏差必须补管注浆。
在注浆过程中,如发生串浆现象时,则安装止浆塞或采用多台注浆 机同时注浆。
水泥浆压力突然升高,则可能发生堵塞,应停机检查,泵压正常后 再进行注浆。进浆量很大,但压力长时间不升高,则应调整浆液浓度及配 合比,缩短凝结时间,进行小泵量低压注浆或间歇注浆,使浆液在裂隙 中有相对停留时间,以便凝胶。
施工过程中,拌料严格按设计配合比及拌和方法拌和, 计量要准确, 特别是外加剂的用量,必须满足设计要求。运输道路保证畅通,照明用 电要有保证,风压、水压要稳定。
质量控制和检查
喷射砼强度及抗渗性:通过工地喷大板,切割制取试件检查,或直 接喷到无底试模中制成试件检查。
与岩面的粘结力检测:在工地预留试件,用直接拉拔法试验或喷大 板切割试块做劈裂试验求得强度值。
喷射厚度控制:以锚杆外露部分作为标记进行检查或喷射时插入长 度比设计值厚度长5cm的铁丝、纵横向1〜2m设一根作施工控制。
b.锚杆
采用①22砂浆锚杆,施工程序如下图:
钻孑L—
N
孔道注浆
插入锚杆
1
安装止浆塞
开挖后先进行第一层喷射砼施工,待该层砼终凝并形成一定强度后, 按设计要求布置锚杆位置,用红油漆标示清楚。
岩机反转, 使顶进联接套与钢管脱离,凿岩机退回原位,人工装上第二 节钢管, 大臂重新对正,凿岩机缓慢低速前进对准第一节钢管端部 (严 格控制角度),人工持链钳进行钢管联接,使两节钢管在联接套处联成 一体。凿岩机再以冲击压力和推进压力低速顶进钢管。