退火工序质量检验标准细则
软磁合金退火工艺守则

XXX有限公司企业标准软磁合金退火工艺守则Q/XXX011—2006代替Q/XXX456—20041范围本标准规定了软磁合金退火中的材料规格、设备与工具、退火前的准备工作、退火工艺与操作、退火工艺过程控制与质量检查、退火设备的维护与检修、安全注意事项。
本标准适用于U5O软磁合金材料制造的零件在氢气保护气氛中的高温磁性退火处理。
2材料规格1 .1化学成分软磁合金的化学成分见表1。
表1软磁合金的化学成分磁挽:1.2mm软磁合金带。
导磁片:1.0mm、1.5mm软磁合金带。
铁心:①7mm软磁合金棒。
2. 3辅助材料氢气:瓶装原料氢气,纯度299.0%;氧化铝粉、无水酒精、石棉等。
3设备与工具2.1 25KW合金退火炉(附电气控制柜)、氢气纯化装置'烘干炉等。
2.2 炉门安全锁紧装置。
3. 3不锈钢烧舟。
3. 4真空泵、压力表、移动式风扇等。
4退火前的准备工作3.1 零件的准备工作3.1.1 零件的清洗4. 1.1.1零件退火前可根据具体情况采取以下三种方法之一进行清洗:a)表面油污及锈迹较严重的零件,应先在除油槽中去油,再酸洗,且酸洗时间不可过长。
b)表面油污较严重的零件,应在除油槽中去油处理。
c)表面锈迹较严重的零件,应进行酸洗处理,酸洗时间不可过长。
5. 1.1.2零件去油或酸洗后用清水冲洗干净,浸入无水酒精中,取出后进行烘干处理。
4.1.2零件的烘干4.1.2.1 清洗干净的零件应放入烘干炉中烘干。
烘干温度为80°C~100°C,烘干时间根据零件数量及水分多少确定,一般约为2h~3h.4.1.2.2将烘干好的零件及样环装入烧舟中,表面撒上氧化铝粉后立即放入合金退火炉内。
添加的氧化铝粉应适量,过多或过少均会影响退火效果。
4.2氧化铝粉的烘干4.2.1磁性合金零件退火时,零件表面必须覆盖一定量干燥、洁净的氧化铝粉,因此,装炉前要对氧化铝粉进行烘干处理。
4.2.2待烘干的氧化铝粉应装入铁盒中,烘干温度为300°C~400°C,烘干时间视装量多少确定,一般约为2h~3h.4.2.3无论新、旧氧化铝粉在使用前均应进行烘干处理,不可直接使用。
【专业文档】退火工艺守则.doc

退火工艺守则一、退火前的准备:1、进行退火前应将铸件清理干净,内腔不得存有冰、水、铁砂、切屑等杂物。
2、检查炉体各部位、闸门、管路、烟道、鼓风设备等是否完好,烧煤炉的炉渣炉灰应清理干净。
3、检查台车是否牢固,驱动机构是否可靠,润滑部位应定期注油。
4、开炉前应将热电偶及测温仪表校准,并将热电偶均匀放置在炉内的适当位置,以便能测出炉内最大温差。
热电偶的数量不得小于2只,并应配备温度测量仪表。
二、装炉:1、扣件装入专用的退火箱内并将退火箱密封。
2、为防止退火变形,扣件应整齐码放。
3、根据温度分布特点,厚大件装上部,薄壁件壮装下部。
三、退火工艺1、严格按工艺曲线升温或降温并做好记录(附退火工艺曲线图)2、操作者应经常观察炉温变化及时进行调整,升温阶段温差控制在40-60度,高温石墨化保温差控制在20度内,低温石墨化温差控制在15度内。
四、生产安全1、铸件退火箱摆放应平稳不得摇摆,不得超高、超宽。
2、清除场地障碍物,炉子周围不得堆放易燃物。
3、退火炉点火等操作,应按有关操作规程进行。
情感语录1.爱情合适就好,不要委屈将就,只要随意,彼此之间不要太大压力2.时间会把最正确的人带到你身边,在此之前,你要做的,是好好的照顾自己3.女人的眼泪是最无用的液体,但你让女人流泪说明你很无用4.总有一天,你会遇上那个人,陪你看日出,直到你的人生落幕5.最美的感动是我以为人去楼空的时候你依然在6.我莫名其妙的地笑了,原来只因为想到了你7.会离开的都是废品,能抢走的都是垃圾8.其实你不知道,如果可以,我愿意把整颗心都刻满你的名字9.女人谁不愿意青春永驻,但我愿意用来换一个疼我的你10.我们和好吧,我想和你拌嘴吵架,想闹小脾气,想为了你哭鼻子,我想你了11.如此情深,却难以启齿。
其实你若真爱一个人,内心酸涩,反而会说不出话来12.生命中有一些人与我们擦肩了,却来不及遇见;遇见了,却来不及相识;相识了,却来不及熟悉,却还要是再见13.对自己好点,因为一辈子不长;对身边的人好点,因为下辈子不一定能遇见14.世上总有一颗心在期待、呼唤着另一颗心15.离开之后,我想你不要忘记一件事:不要忘记想念我。
常用变形铝合金退火热处理工艺规范标准

常用变形铝合金退火热处理工艺规1 主题容与适用围本规规定了公司变形铝合金零件退火热处理的设备、种类、准备工作、工艺控制、技术要求、质量检验、技术安全。
2 引用文件GJB1694变形铝合金热处理规YST 591-2006变形铝及铝合金热处理规《热处理手册》91版3 概念、种类3.1 概念:将变形铝合金材料放在一定的介质加热、保温、冷却,通过改变材料表面或部晶相组织结构,来改变其性能的一种金属热加工工艺。
3.2 种类车间铝合金零件热处理种类:去应力退火、不完全退火、完全退火、时效处理。
4 准备工作4.1 检查设备、仪表是否正常,接地是否良好,并应事先将炉膛清理干净;4.2 抽检零件的加工余量,其数值应大于允许的变形量;4.3工艺文件及工装夹具齐全,选择好合适的工夹具,并考虑好装炉、出炉的方法;4.4 核对材料与图样是否相符,了解零件的技术要求和工艺规定;4.5在零件的尖角、锐边、孔眼等易开裂的部位,应采用防护措施,如包扎铁皮、石棉绳、堵塞螺钉等;5 一般要求5.1 人员:热处理操作工及相关检验人员必须经过专业知识考核和操作培训,成绩合格后持证上岗5.2 设备5.2.1 设备应按标准规要求进行检查和鉴定,并挂有合格标记,各类加热炉的指示记录的仪表刻度应能正确的反映出温度波动围;5.2.2 热电温度测定仪表的读数总偏差不应超过如下指标:当给定温度t≤400℃时,温度总偏差为±5℃;当给定温度t>400℃时,温度总偏差为±(t/10)℃。
5.2.3 加热炉的热电偶和仪表选配、温度测量、检测周期及炉温均匀性均应符合QJ 1428的Ⅲ类及Ⅲ类以上炉的规定。
5.3 装炉5.3.1 装炉量一般以装炉零件体积计算,每炉零件装炉的有效体积不超过炉体积一半为准。
5.3.2 零件装炉时,必须轻拿轻放,防止零件划伤及变形。
5.3.3堆放要求:a.厚板零件允许结合零件结构特点,允许装箱入炉进行热处理,叠放时允许点及较少的线接触,避免面接触,叠放间隙不小于10mm.b.厚度t≤3mm的板料以夹板装夹,叠放厚度≤25mm,零件及夹板面无污垢、凸点,零件间、零件与夹板间应垫一层雪花纸,以防止零件夹伤。
退火热处理规范
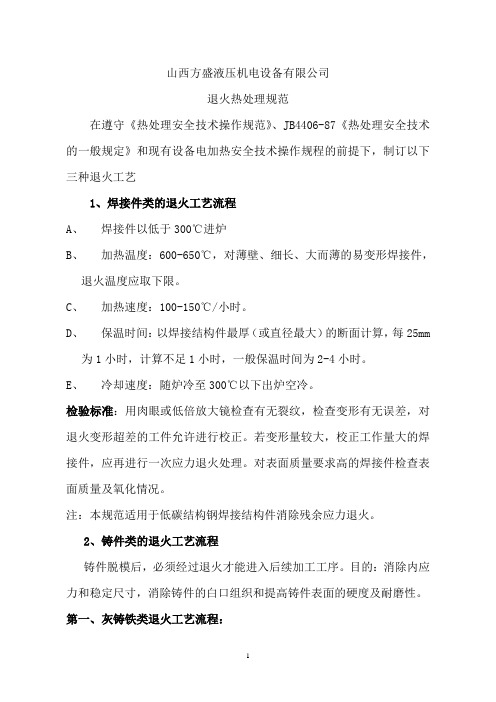
山西方盛液压机电设备有限公司退火热处理规范在遵守《热处理安全技术操作规范》、JB4406-87《热处理安全技术的一般规定》和现有设备电加热安全技术操作规程的前提下,制订以下三种退火工艺1、焊接件类的退火工艺流程A、焊接件以低于300℃进炉B、加热温度:600-650℃,对薄壁、细长、大而薄的易变形焊接件,退火温度应取下限。
C、加热速度:100-150℃/小时。
D、保温时间:以焊接结构件最厚(或直径最大)的断面计算,每25mm为1小时,计算不足1小时,一般保温时间为2-4小时。
E、冷却速度:随炉冷至300℃以下出炉空冷。
检验标准:用肉眼或低倍放大镜检查有无裂纹,检查变形有无误差,对退火变形超差的工件允许进行校正。
若变形量较大,校正工作量大的焊接件,应再进行一次应力退火处理。
对表面质量要求高的焊接件检查表面质量及氧化情况。
注:本规范适用于低碳结构钢焊接结构件消除残余应力退火。
2、铸件类的退火工艺流程铸件脱模后,必须经过退火才能进入后续加工工序。
目的:消除内应力和稳定尺寸,消除铸件的白口组织和提高铸件表面的硬度及耐磨性。
第一、灰铸铁类退火工艺流程:A、去应力退火:将铸件缓慢加热到500-560℃,保温2小时左右,然后以极缓慢的速度随炉冷至150-200℃后出炉。
注意:退火温度过高或保温时间过长,会引起石墨化,降低铸件强度和硬度,这是不适宜的。
B、消除白口、改善切削加工性的退火工艺:将铸件加热到800-900℃,保温2-5小时,使共晶渗碳体发生分解,然后又在随炉缓慢冷却过程中,使二次渗碳体及共析渗碳体发生分解,待随炉缓冷到500-400℃时,再出炉空冷,这样可以改善切削加工性。
若保温后采用较快的冷却速度,可以增加铸件强度和耐磨性。
第二、球墨铸铁类退火工艺流程:A、去应力退火:球墨铸铁的弹性模量以及凝固时收缩率比灰铸铁高,故铸造内应力比灰铸铁约大2倍。
对于不再进行其他热处理的球墨铸铁铸件,都应进行去应力退火。
轴承套圈锻坯退火质量检验规程

轴承套圈锻坯退火质量检验规程1.目的按按GB/T34891-2017《滚动轴承高碳铬轴承钢零件热处理技术条件》标准,对Gr15、GCr15SiMn轴承钢制轴承套圈锻坯退火后轴承零件进行检验和试验,确保未经检验或未经检验合格的产品不转入下道工序和不交付。
2.适用范围适用于经球化退火的Gr15或GCr15SiMn钢制轴承套圈锻坯的工序检验和最终检验。
3.引用标准GB/T34891-2017《滚动轴承高碳铬轴承钢零件热处理技术条件》GB230 《金属洛氏硬度试验方法》GB231 《金属布氏硬度试验方法》GB224 《钢的脱碳深度测定方法》4.1轴承套圈锻坯退火质量检验几点规定4.1.1轴承套圈锻坯退火质量检验由质保部负责执行,进行日常检验工作。
4.1.2检验员应按照图样规定的技术要求和有关标准及工艺文件进行检验。
4.1.3 检验员应把好质量检验关,监督工艺执行情况,防止废品和不良品的转序。
4.1.4 球化退火由专职检验员进行检验,采取随机抽样的方法,一天一次,每个型号规格产品抽检数量不得少于2件。
如发现不合格,应扩大、加倍取样复查。
4.1.5检验硬度前,应将零件表面清理干净,去除氧化皮、脱碳层等,粗糙度达1.6以上。
4.1.6 硬度检验部位根据工艺文件或检验人员确定,一个零件检测硬度应不少于3点,并取其平均值。
4.1.7 球化退火由专职检验员进行抽检,一天一次,每种型号规格产品抽样分析评级的数量不得少于1件。
并做好记录。
4.2轴承套圈锻坯退火质量检验4.2.1 硬度检验4.2.1.1按GB/T34891-2017标准执行,客户有图样文件规定的,按文件规定要求执行检验。
4.2..1.2 球化退火硬度检验宜采用洛氏硬度计HRB标尺检验;GCr15钢制轴承零件退火后合格硬度为GCr15 179~207HBW(压痕直径4.5~4.2mm)或88~94HRBGCr15SiMn179~217HBW(压痕直径4.5~4.1mm)或88~97HRB,检验后作好数据记录。
轴承零件退火质量检查标准

轴承零件退火质量通用技术要求
编号:Q/RBJ07.05-01-2009
1 范围 本 标 准 适 用 于 人 本 集 团 下 属 各 个 轴 承 制 造 公 司 对 轴 承 ( GCr15 、 GCr15SiMn 、 GCr15SiMo、GCr18Mo )套圈退火质量检验。
2 引用标准 2.1《高碳铬轴承钢滚动轴承零件热处理技术条件》 JB/T1255-2001 2.2《滚动轴承零件硬度试验方法》 JB/T7361-2007 2.3《滚动轴承零件脱碳层检查方法》 JB/T7362-2007 2.4《计数抽样检验程序》GB2828-2003
4、验收规则 4.1 硬度及金相组织验收规则
发布时间: 2008 年 07 月 05 日
1/7
实施时间: 2008 年 09 月 01 日
人本集团企业标准
轴承零件退火质量通用技术要求
编号:Q/
判定规则
金相样本数
判定规则
≤5000 5001~30000 30001~70000 70001~110000 110001~160000 ≥160000
3. 技术要求 3.1 轴承零件球化退火技术要求 3.1.1 硬度 GCr15:179~207HB 或 88~94HRB 其它钢种(GCr15SiMn 、GCr15SiMo、GCr18Mo ) :179 ~217HB 或 88 ~97HRB。 3.1.2 显微组织 GCr15:细小,均匀分布的球化组织,按照 JB/T1255 第一级别图评定,2~4 级合格;网 状碳化物按照 JB/T1255 第四级别图评定,不大于 2.5 级合格;脱碳层不应大于单边加工余 量的 1/3 ,所有经过车削加工面不允许有脱贫碳存在。 其它钢种 (GCr15SiMn 、 GCr15SiMo、 GCr18Mo ) : 细小, 均匀分布的球化组织, 按照 JB/T1255 第一级别图评定,2 ~4 级合格;网状碳化物按照 JB/T1255 第四级别图评定,不大于 2.5 级 合格;脱碳层不应大于单边加工余量的 1/3 ,所有经过车削加工面不允许有脱贫碳存在。 注:客户有特殊要求时除外。
退火有什么工艺技术规范

退火有什么工艺技术规范退火是金属加工中一种重要的热处理工艺,它可以改善金属材料的结构和性能,消除内部应力,提高材料的塑性和韧性。
退火工艺一般包括预热、保温、冷却三个步骤,并需要遵循一些工艺技术规范。
下面将介绍一些退火工艺技术规范,以确保退火过程的质量和稳定性。
首先,退火过程中的温度控制非常重要。
一般来说,金属材料的退火温度应该低于其熔点,以避免材料熔化。
同时,退火温度还应根据具体材料的类型和要求进行调整。
常见的金属退火温度范围是600-900摄氏度。
在退火过程中,还需控制预热和保温时间,以确保温度均匀分布和达到所需的组织改变。
其次,退火过程中的冷却速率也需要加以控制。
快速冷却可能引起材料的质变和应力增大,而缓慢冷却则可能导致晶粒长大而失去退火效果。
因此,一般会采用逐渐降温的方法,如将材料放在炉中自然冷却,或者用炉内冷却介质进行冷却。
退火过程中的冷却速率应符合相关的材料标准或需求。
此外,退火过程中的保护措施也需要重视。
针对容易氧化的金属,如铜、铝等,需要采取保护气氛或添加保护剂的措施,以防止材料的表面氧化变质。
常见的保护气氛有氢气、氮气、惰性气体等。
在退火过程中,还需注意退火炉的密封性和炉内环境的干净度,避免外界杂质的污染。
退火后的材料还需要进行相关的试验和检测,以评估退火效果和材料性能。
常见的检测方法包括金相显微镜观察、力学性能测试、显微硬度测试等。
根据不同的材料和要求,还可以进行一些特殊的试验,如晶粒度测定、相组成分析等。
最后,退火过程中的操作和记录也需要符合相关的工艺规范。
每次退火都应制定详细的操作规程,明确各个工艺参数的设定,确保操作的准确性和稳定性。
此外,还需对退火过程进行记录,包括温度、时间、冷却速率等相关数据,以便后续的追溯和分析。
总之,退火工艺的质量和稳定性对于金属材料的性能和使用寿命有着重要的影响。
通过严格遵守工艺技术规范,可以确保退火过程的安全、稳定和可控性,提高材料的质量和使用价值。
退火检测标准ZL16

1、目的:建立制品在制造过程中之管理点和管理方式,以执行制程品质监
测,确保制品品质符合规定要求。
2、范围:
2.1、公司所有退火钱线及精线
2.2、外购之精线。
3、内容:
3.2.脱碳层要求:含碳量大于0.3%的碳钢及中\低碳合金钢,应进行脱碳层检验,
每边总脱碳层深度不得大于公称直径的1.0%,但对直径小于7mm的钢材,一边总脱碳层深度不得大于0.1mm。
3.3.显微组织:晶粒细小,均匀分布的球化组织,针对中、高碳钢及中、低碳
合金钢。
3.4.球化率:按JB/T5074评级4~6级则为合格。
3.5.抽样方案:每炉每柱至少抽一件做测试,抽样原则为每柱上段与下段交叉
抽样方式。
样品由退火炉作业人员取样并填写检验通知单给质量部实验室检测,实验室检测完毕后回执一联检验通知单给退火制程,样品及检验通知单原件保留在质量部实验室,以备查核!
4、注意事项:
4.1 生产条件查核:
4.1.1 温度2、保温时间3、降温速度4、气体管道、冷却水管道详见《退火
操作说明书》及《退火工艺卡》。
4.2 软化退火,不做球化率级别控管。
4. 3 特殊产品另定。
4. 4 外购精线需与外购单位签订合作协议,检测标准按本规定精线标准检测。
4. 5 生丝直抽线材不做硬度控制。
CA6NM焊后退火

CA6NM(ZG06Cr13Ni4Mo)马氏体不锈钢焊后退火工艺规程1 范围本规程适用于CA6NM(ZG06Cr13Ni4Mo)低碳马氏体不锈钢铸件在台车炉或井式炉中补焊后的退火工艺及质量检验。
本标准适用于山东双轮股份有限公司CA6NM(ZG06Cr13Ni4Mo)低碳马氏体不锈钢铸件的焊后热处理。
2. 规范性引用文件下列文件中的条款通过本标准的引用而成为本标准的条款。
凡是注日期的引用文件,其随后所有的修改单(不包括勘误的内容)或修订版均不适用于本标准,然而,鼓励根据本标准达成协议的各方研究是否可使用这些文件的最新版本。
凡是不注日期的引用文件,其最新版本适用于本标准。
RCC-M(2000版及2002年补遗)压水堆核岛机械设备设计建造规则EJ/T1027-1996 压水堆核电厂核岛机械设备焊接规范GB/T15735-2004 金属热处理生产过程安全卫生要求JB/T10175 热处理质量控制要求Q/SSL Tn45.02-2010 热处理人员资格鉴定规程Q/SSL Tn45.03-2010 热处理设备检验、鉴定规程Q/SSL Tn45.04-2010 热处理质量检验规程Q/SSL Tn45.07-2010 热处理设备管理规程Q/SSL Tn45.08-2010 热处理过程记录与统计规程Q/SSL Tn45.33-2010 热处理炉有效加热区及炉温均匀性检测规程Q/SSL Tn45.37-2010 热处理装炉控制规程3.准备工作3.1检查设备、仪表是否正常,并应事先将炉膛清理干净。
3.2核对材料与图纸是否相符、了解零件的技术要求和工艺规定。
3.3检查零件的加工余量,其数值应大于允许的变形量。
3.4选择好合适的工夹具,适当的装出炉方法。
3.5铸件补焊退火前,肉眼观察,表面不得有裂纹、夹杂、拉裂等缺陷。
3.6铸件补焊退火后进行粗加工。
3.7 热处理工必须熟悉热处理设备的性能,操作方法,热处理工艺要点,并严格执行有关热处理规程、标准、技术文件和热处理工艺等。
热处理各工序的质量检查项目和要求
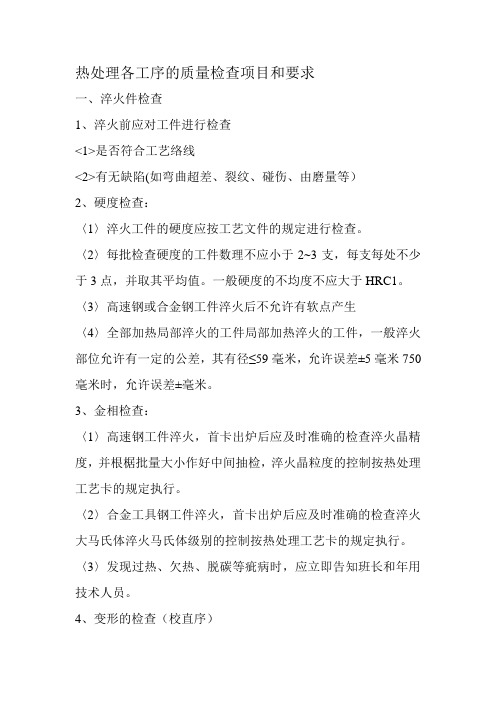
热处理各工序的质量检查项目和要求一、淬火件检查1、淬火前应对工件进行检查<1>是否符合工艺络线<2>有无缺陷(如弯曲超差、裂纹、碰伤、由磨量等)2、硬度检查:〈1〉淬火工件的硬度应按工艺文件的规定进行检查。
〈2〉每批检查硬度的工件数理不应小于2~3支,每支每处不少于3点,并取其平均值。
一般硬度的不均度不应大于HRC1。
〈3〉高速钢或合金钢工件淬火后不允许有软点产生〈4〉全部加热局部淬火的工件局部加热淬火的工件,一般淬火部位允许有一定的公差,其有径≤59毫米,允许误差±5毫米750毫米时,允许误差±毫米。
3、金相检查:〈1〉高速钢工件淬火,首卡出炉后应及时准确的检查淬火晶精度,并根椐批量大小作好中间抽检,淬火晶粒度的控制按热处理工艺卡的规定执行。
〈2〉合金工具钢工件淬火,首卡出炉后应及时准确的检查淬火大马氏体淬火马氏体级别的控制按热处理工艺卡的规定执行。
〈3〉发现过热、欠热、脱碳等疵病时,应立即告知班长和年用技术人员。
4、变形的检查(校直序)工件淬火后变形的检查,应按工艺文件(如“热处理工艺卡”)的规定进行。
达不到技术要求的工件,检查员不得让其转入下序。
二、回火件的检查(回火序)1 硬度检查:〈1〉高速钢工件径545摄氏度三次回后的硬度值应高理规定硬度值的中限。
〈2〉合金工具钢工件回火后的硬度值应符合工艺文件的规定。
2 回火程度的检查:高速钢工件三次回火完毕冷至室温时,应及时检查回火程度。
回火程度力求达到充争,发现回火不足时,不得转序,而应补充回火一次。
合金工具钢工件当工艺文件或图纸有要求时,也应检查回火程度。
三、喷砂件的检查(喷砂序)喷砂应按喷砂工艺守则的规定进行。
喷砂后的工件表面应呈均一的银矿色,不得有锈迹、花斑、碰刃等缺陷。
氧氮化处理应按蒸汽处理工艺守则的规定进行。
蒸汽处理后工件的颜色应呈均匀的蓝黑色,浸油后不得有明显红物、花斑和锈迹。
零件热处理质量检验规程 (2)

一般机械零件热处理质量检验规程总则1.1本规程是工厂编制一般机械零件的热处理质量检验项目、内容及要求的依据之一。
1.2工厂承接的加工件,一般均根据本规程进行质量检验。
如果顾主(客户)另有要求的,或另有标准的,则按顾主的要求或指定行业的标准进行检验。
1.3当工厂认为自己的手段和能力难以达到客户的质量要求时,应事先进行协商,经用户同意,也可按协商标准进行质量检验。
1.4本规程引用标准的参考书目:a)GB1298b)GB1299c)YB9-68d)YB27-77e)《机床零件热处理质量检查规程》1964f)《机床专业金相检验图谱》g)JB2046-79h)JB1255-72i)JB2849-79j)北京齿轮厂汽车齿轮氰化金相检验标准(Z80054)1978k)沪机艺(85)第007号1、热处理质量检验工作的几点规定2.1质管部门负责执行质量检验工作,在热处理各车间(工段或小组)设立检验站,进行日常的质量检验工作。
2.2质检工作以专业检验员为主,与生产工人的自检、互检相结合。
2.3在承接业务时,应首先对零件进行外观目测检验,有无裂纹、碰伤、锈蚀斑点。
还应调查制件的原材料,预先热处理、铸造工艺是否恰当,制件尺寸及加工余量是否与图纸相符合,有变形要求的要检查来时的原始变形情况,经修复的模具(堆焊、补焊、砂光等)等制件应说明修复情况并检查登记备查。
必要时应探伤等。
2.4检验人员应按照图纸技术条件、标准、工艺文件、规定的检验项目与方法等,进行首检、中间抽检、成品检验。
应监督工艺过程,及时发现问题,防止产生成批不合格品与废品。
2.5生产工人对成批生产的制件必经首检合格后方可进行生产,生产过程中也应进行中间检验,防止发生问题。
当出现异常情况,应及时向检验、当班领导汇报,并采取积极、妥当的措施纠正。
2、检验内容及方法3.1硬度3.1.1热处理零件均应根据图纸要求和工艺规定进行硬度检验或抽检。
3.1.2光以标准块校对硬度计,确认后方可进行测试硬度。
退火酸洗检查基准

1.适用范围本基准是为了不锈钢热轧产品的品质检查基准(包括外观缺陷分类)进行规定,以下目录(不锈钢热轧产品中黑皮卷Black Coil,白皮卷White Coil,薄带连铸Strip Casting全部包含)1. 使用范围及目录 (1)2. 目的 (1)3. 一般检查 (1)4. 交接检查基准 (5)5. Black Coil(黑皮卷)检查基准 (7)6. 缺陷评点使用基准 (9)7. 尺寸检查基准 (31)8. 板型判定基准 (33)9. 外观综合判定基准 (36)10.异常材处理基准 (38)11. White Coil(白皮卷)外观缺陷分类基准 (41)12.附:热轧及退火酸洗工程各辊直径 (57)2.目的2.1. 按不锈钢热轧退火、酸洗卷的缺陷形态,确定发生原因,消除缺陷的发生原因,防止再发。
消除发生卷的缺陷,不影响后工程的投入及对后工程发生的情报连接,生产出合格的产品为目的。
2.2. 生产不锈钢热轧产品时,为了满足规格以及订单事项进行规定,实施品质检查3.一般检查3.1. 适用范围本基准是为了保证热轧钢带的产品品质,对于检查体系进行规定3.2. 目的规定不锈钢退火酸洗的检查体系,检查作为素材的热轧卷,在操业过程中早期感知品质异常后最小化不良制品的生产3.3. 用语的定义3.3.1 素材检查对从热轧工厂移送到退火酸洗工厂的Coil(黑皮卷)检查后,判断进行CPL,HOT APL或BAF工程与否3.3.2 确认检查作为判定最终制品中充足订单条件与否的检查,为保证制品的外观,尺寸,形状及交货度事项的检查3.3.2.1 CPL(Coil Prepration Line:准备线)检查作为退火酸洗CPL工程上实施的检查,对以Black Coil状态销售的产品判定是否满足订单要求事项的检查3.3.2.2 APL(Annealing and Picking Line:退火酸洗线)检查作为退火酸洗HAPL工程出口检查台上实施的检查,判定通过HAPL的Coil是否满足订单事项或是否需要追加处理工程(APL,CGL,CPL)的检查3.3.2.3 CGL(Coil Grinding Line)检查作为在退火酸洗CGL工程上实施的检查,判定Coil Grinding(以下CG)处理必须材或APL检查时已经判定为CG材处理对象的Coil CG处理后是否适合客户订单事项的检查3.3.3综合判定根据确认检查确认对最终制品的尺寸,外观,形状,化学成分,机械性能等的客户事项满足与否后对制品实施最终判定的检查3.4. 检查体系3.4.1 White Coil(白皮卷)3.4.2 Black Coil(黑皮卷)4.接收检查基准4.1. 适用范围此标准规定对不锈钢Hot-APL Coil(热轧白皮卷) 的接收条件的检查基准及检查方法4.2. 目的对经过STS(不锈钢)退火酸洗的STS HR Coil检查接收要求事项或订单是否满足规格上指定的水准后区别不适合顾客要求品质的素材的目的4.3. 用语定义4.3.1 Skin Pass(表面平整)形状校正为目的的冷轧压延4.3.2 Edge 状态显示Hot-APL Coil的Side Trimming(边部切边)与否4.3.3 Grinding(研磨)指定与否Hot-AP Coil表面Grinding 实施与否4.3.4 垫纸为了保护Hot-APL Coil的表面,卷取时插入纸或塑膜4.3.5 重量垫纸及包装材料除外的制品实重量4.6. 措施方法4.6.1 检查者把检查项目别实绩输入在检查卡和操业电算系统终端机后根据STS退火酸洗综合等级判定基准,在品质判定系统上自动级外判定或取消可能的接收不满足的AP 再处理材判定等5.Black Coil(黑皮卷)检查基准5.1. 适用范围此标准是通过CPL后实施表面检查的关于不锈钢热轧Black Coil制品的检查方法及判定基准的的规定5.1.1 CPL未通板材的表面检查对如下事项以CPL未通板Black Coil制品表面检查未实施,只做Coil的形状检查后出库为原则5.1.2 CPL未通板Black Coil 制品- 内径符合订单情况(与工程班商议后最终处理)- 准备线(CPL)生产尺寸超过订单的情况(工程转换材)- 根据顾客供应规格CPL未通板协议的情况5.2. 目的通过CPL后实施表面检查后判定不锈钢热轧Black Coil制品是否满足顾客要求的表面品质为目的5.3. 用语定义热轧中间检查Coil 外观形状检查基准及制品检查Coil外观检查基准参照5.5. 检查基准以及措施方法5.6. 措施事项检查者同STS退火酸洗作业标准进行情报处理6.缺陷评点使用基准6.1. 适用范围本标准是不锈钢热轧产品以及Strip Casting(薄带连铸)产品的外观缺陷检查方法以及判定基准进行规定6.2. 目的为了生产不锈钢退火酸洗Coil,客户规格以及订单用途符合的产品,钢种以及根据订单用途缺陷的种类别钢种别进行评价6.4. 检查基准6.4.1 缺陷Group(分组)6.4.2 缺陷分类体系6.4.3 评点定义(共同)各个评点项目是or要满足伦理条件(为了合格要求满足两个条件)※炼钢Inclusion Line,炼钢Scab,炼钢黑带,热轧异物压入,热轧Chip,炼钢Pin Hole 等个数记录(其他缺陷由长度算出)6.4.4 输入个数以及长度缺陷6.5. 措施方法6.5.1 检查员把在带钢发生的缺陷种类、发生位置及长度或者个数,评分按代码的形式在检查卡上记录,根据发生的长度按主缺陷顺序最大5个缺陷和缺陷率输入系统,缺陷名及评分使用基准是灵活运用缺陷样品,减少检查员之间的评分偏差①根据每个面表面评分基准,计算的表面评分比设计基准不到时,主缺陷为酸洗性缺陷或者细微M型,线型辊印,表面粗糙,Roll疲劳痕,由于氧化皮压入2时AP再酸洗处理②主缺陷不是酸洗性缺陷,允许研磨时判定CG材处理,板型不良及带钢边部损伤,火灾以及边降发生可能材,在平整,转用途或者订货外2级处理③不能研磨材和最终生产完成的产品按本规定的STS退火酸洗综合等级判定基准,STS退火酸洗异常处理基准处理6.5.2 产品担当对AP或者CG材出判定材,再处理原因对客户使用用途,使用时的品质要求水平,可否使用进行认真确认,对再处理判定的合适性经过综合检讨后判定实施6.5.3 缺陷发生位置代码6.5.3.1 压延方向6.5.3.2 宽度方向6.5.4 每个面表面等级评价基准6.5.4.1 表面等级内容-等级计算方法:必须同时满足产品的缺陷率和不良率例:300系时,缺陷率是4%,不良率2%的产品等级:”B”6.5.4.2 判定基准6.5.4.3 表面缺陷计算基准- 缺陷率(%)=(Σ上面或下面的缺陷长度/Coil长度)×100- 不良率(%)=(Σ上面或下面的不良缺陷长度/Coil长度)×100- 缺陷率及不良率计算对象缺陷率:缺陷评点‘2‘以上的缺陷不良率:缺陷评点‘3‘以上的缺陷6.6. 顾客钢种别缺陷率评点适用详细管理基准6.6.1 头、尾宽尺寸超差允许范围6.6.1.1 尺寸超差(订单公差对比)10M允许(仅厚度、宽/表面缺陷现基准适用)6.6.1.2 尺寸超差部分的实际对比平均宽(Mid部)20mm超过或平均厚度(MID部)对比±15%超过时次工程指定及不良部位剪切6.6.2 严重缺陷允许基准6.6.2.1 用途及评点别允许基准6.6.3 厚度以上外允许基准6.6.3.1 比通常厚度减少5%以上的部分超过全部长度的3%时不允许6.6.4 宽偏差部及局部偏差发生部允许基准6.6.4.1 用途别允许基准- 再压用:每10M 局部偏窄3mm以下,全部长度的3%以内发生时允许- 管材/板材用:每10M局部偏窄5mm以下,全部长度的3%以内发生时允许6.7. 1次AP 处理后氧化皮残留的缺陷处理基准-带钢正、反面微细凹凸缺陷部氧化皮挤入缺陷是考虑工程别在供可以判定AP 再处理. 1. 对象缺陷:ML(表面粗糙),MJ(线纹欠 面粗糙), MK(带粗糙),HC(热轧下部面粗糙),HQ(热轧氧化皮脱落),HM(热轧辊疲劳痕),PK(HAPL 麻点痕),HP(热轧线状辊印),HR(热轧粘辊痕)2. 包括酸洗性缺陷的凹凸性缺陷挤入氧化皮时实施AP 再处理后,正品可能的情况,AP 再处理判定6.8. 缺陷检查单位6.9. 记录6.10. 特别管理基准(MES 系统适用)1. 定义:Coil ,Hoop 及Sheet 全制品为对象。
各工序易出现的质量问题及检验控制标准
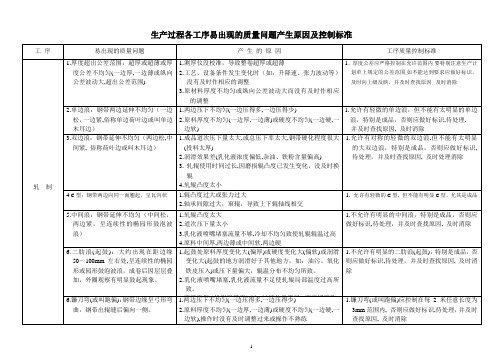
工序
易出现的质量问题
产生的原因
工序质量控制标准
轧制
1.厚度超出公差范围:超厚或超薄或厚度公差不均匀(一边厚,一边薄或纵向公差波动大,超出公差范围)
1.测厚仪没校准,导致整卷超厚或超薄
2.工艺、设备条件发生变化时(如:升降速、张力波动等)没有及时作相应的调整
2.润滑效果差(乳化液浓度偏低,杂油、铁粉含量偏高)
3.轧辊使用时间过长,因磨损辊凸度已发生变化,没及时换辊
4.轧辊凸度太小
1.允许有对称的轻微的双边浪,但不能有太明显的大双边浪,特别是成品,否则应做好标识,待处理,并及时查找原因,及时处理消除
4.C型:钢带两边向同一面翘起,呈瓦沟状
1.辊凸度过大或张力过大
2.原料有异物混入或氧化铁皮压入,酸洗无法去除,或欠酸洗.
3.乳化液被污染,杂油混入严重或铁粉含量过高
4.乳化液浓度太低润滑不良,或乳化液喷嘴堵塞或流量不够
5.轧制压下量过大,导致变形温度太高,乳化液中的轧制油被裂变炭化
1.不允许有明显的黑油污,一旦出现应做好标识,待处理,并及时查找原因,及时消除
工序
2.原料厚度不均匀(一边厚,一边薄)或硬度不均匀(一边硬,一边软)
1.允许有轻微的单边浪,但不能有太明显的单边浪,特别是成品,否则应做好标识,待处理.
并及时查找原因,及时消除
3.双边浪:钢带延伸不均匀(两边松,中间紧,俗称荷叶边或叫木耳边)
1.成品道次压下量太大,或总压下率太大,钢带硬化程度很大(投料太厚)
1.不允许有划伤,如发现(特别是成品)必须立即停机检查,做好标识,待处理.若是半成品,划伤轻微,深度≯0.02mm可流转下工序,但要找出原因并消除
退火质量控制措施
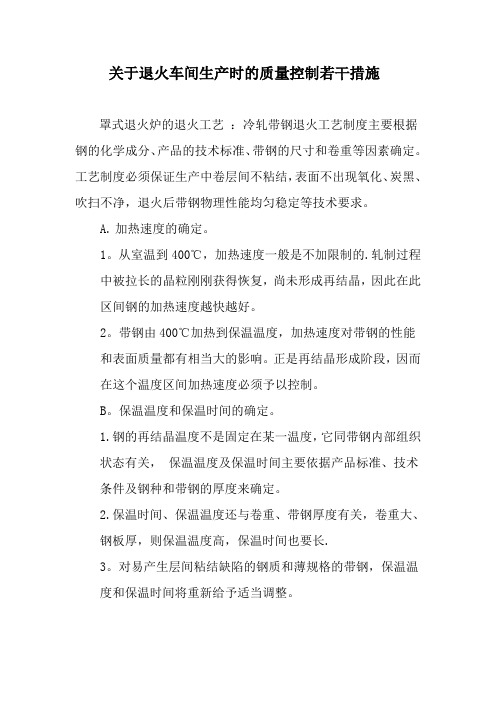
关于退火车间生产时的质量控制若干措施罩式退火炉的退火工艺:冷轧带钢退火工艺制度主要根据钢的化学成分、产品的技术标准、带钢的尺寸和卷重等因素确定。
工艺制度必须保证生产中卷层间不粘结,表面不出现氧化、炭黑、吹扫不净,退火后带钢物理性能均匀稳定等技术要求。
A.加热速度的确定。
1。
从室温到400℃,加热速度一般是不加限制的.轧制过程中被拉长的晶粒刚刚获得恢复,尚未形成再结晶,因此在此区间钢的加热速度越快越好。
2。
带钢由400℃加热到保温温度,加热速度对带钢的性能和表面质量都有相当大的影响。
正是再结晶形成阶段,因而在这个温度区间加热速度必须予以控制。
B。
保温温度和保温时间的确定。
1.钢的再结晶温度不是固定在某一温度,它同带钢内部组织状态有关,保温温度及保温时间主要依据产品标准、技术条件及钢种和带钢的厚度来确定。
2.保温时间、保温温度还与卷重、带钢厚度有关,卷重大、钢板厚,则保温温度高,保温时间也要长.3。
对易产生层间粘结缺陷的钢质和薄规格的带钢,保温温度和保温时间将重新给予适当调整。
C.光亮退火要使带钢无脱碳、无氧化必须进行光亮退火。
退火钢卷防止氧化的关键性问题是必须使保护罩内的气氛和压力满足工艺要求。
D.还要认真搞好冷吹和热吹。
1。
冷吹和热吹的目的是利用保护气体驱走内罩中的空气和钢卷带进的油气水分。
2. 热吹的作用是除了将内罩中的残余气体进一步赶尽之外,更重要的是将板卷带来的乳化液产生的油烟、水蒸气等有害物质全部驱走吹净,避免玷污钢板表面而降低钢板表面质量。
(电解脱脂后的带钢退火时:全氢炉的吨钢耗气量为不低于2.5立方保护气每吨钢,氮氢炉的吨钢耗气量为不低于5立方保护气每吨钢,并控制在有效时段内,才能把带钢表面的挥发物和残留物吹扫干净;对于电耗的控制已经充分优化,利用物理体自身能量恢复带钢组织结构,达到退火目的。
)E。
根据不同技术要求和质量标准,生产工艺由车间与生产部统一协调后由车间主管下达并签字确认及后续质量跟踪与反馈。
正火与退火工艺守则

正火与退火工艺守则结合我厂现有设备和实际生产情况制定本工艺守则,其适用于我厂现有各种原材料及半成品的退火与正火工艺一、准备工作1.检查准备仪表是否正常。
2.核对材料与图纸是否相符,了解零件的技术要求和工艺规定3.对表面不允许氧化脱碳件采取必要的保护措施4.盐炉返修件要清理表面残盐二、工艺规范常用钢材的退火温度见表1常用材料的正火温度见表2有效厚度见《淬火回火工艺守则》保温时间1、电炉保温时间=零件的有效厚度×保温系数2、不同钢种的保温时间见表3●a)碳素钢、合金钢正火的装炉要求在小于或等于工艺温度下装炉,随炉升温,合金结构钢、合金工具钢的退火要求在550℃以下装炉,随炉升温b)高速钢及复杂截面差较大件易低温装炉,且需在550-700℃间均温1-2小时后随炉升温●冷却速度及出炉温度a)碳素钢、合金钢退火后随炉冷却至550℃以下,可出炉空冷b)高合金钢退火冷却速度应不大于100℃/小时,冷却至550℃以下可出炉空冷c)等温退火件等温后随炉冷至550℃以下出炉空冷,对小件及简单件可在等温后直接空冷d)正火件在空气中散开冷却,不允许堆放或置于潮湿有水的地方冷却e)为削除网状碳化物的正火,在700℃以上应采取适当的强制冷却三、加热设备1.我厂退火件、正火件加热主要采用箱式加热炉,对需保护的零件可采用盐炉或渗碳炉2.加热设备及测温装置应符合相关规定四、操作方法及注意事项1.零件装炉时应放在预先设置的有效加热区内,装炉量、装炉方式应保证零件能均匀加热、冷却且不造成缺陷为原则2.装炉后应检查零件与电热元件确无接触方可送电升温3.保温时间是从炉子升到工艺规定温度算起,装炉量大时应适当延长4.对细长薄板件,装炉要特别小心,以防变形五、低温退火1.其工艺参数如下表六、铸铁热处理退火1.针对消除铸铁中白口的问题而制定其工艺参数其工艺参数如下图:2.升温速度控制在80-100℃/小时,降温随炉即可二、调质工艺守则调质是淬火加热加高温回火的操作简称。
退火热处理规范
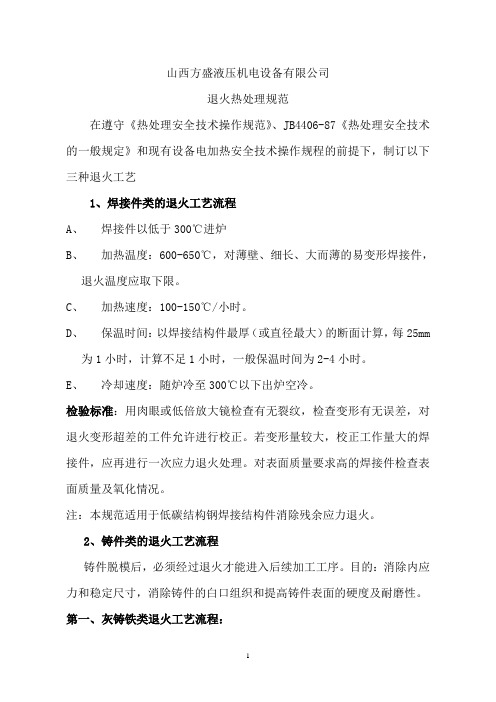
山西方盛液压机电设备有限公司退火热处理规范在遵守《热处理安全技术操作规范》、JB4406-87《热处理安全技术的一般规定》和现有设备电加热安全技术操作规程的前提下,制订以下三种退火工艺1、焊接件类的退火工艺流程A、焊接件以低于300℃进炉B、加热温度:600-650℃,对薄壁、细长、大而薄的易变形焊接件,退火温度应取下限。
C、加热速度:100-150℃/小时。
D、保温时间:以焊接结构件最厚(或直径最大)的断面计算,每25mm为1小时,计算不足1小时,一般保温时间为2-4小时。
E、冷却速度:随炉冷至300℃以下出炉空冷。
检验标准:用肉眼或低倍放大镜检查有无裂纹,检查变形有无误差,对退火变形超差的工件允许进行校正。
若变形量较大,校正工作量大的焊接件,应再进行一次应力退火处理。
对表面质量要求高的焊接件检查表面质量及氧化情况。
注:本规范适用于低碳结构钢焊接结构件消除残余应力退火。
2、铸件类的退火工艺流程铸件脱模后,必须经过退火才能进入后续加工工序。
目的:消除内应力和稳定尺寸,消除铸件的白口组织和提高铸件表面的硬度及耐磨性。
第一、灰铸铁类退火工艺流程:A、去应力退火:将铸件缓慢加热到500-560℃,保温2小时左右,然后以极缓慢的速度随炉冷至150-200℃后出炉。
注意:退火温度过高或保温时间过长,会引起石墨化,降低铸件强度和硬度,这是不适宜的。
B、消除白口、改善切削加工性的退火工艺:将铸件加热到800-900℃,保温2-5小时,使共晶渗碳体发生分解,然后又在随炉缓慢冷却过程中,使二次渗碳体及共析渗碳体发生分解,待随炉缓冷到500-400℃时,再出炉空冷,这样可以改善切削加工性。
若保温后采用较快的冷却速度,可以增加铸件强度和耐磨性。
第二、球墨铸铁类退火工艺流程:A、去应力退火:球墨铸铁的弹性模量以及凝固时收缩率比灰铸铁高,故铸造内应力比灰铸铁约大2倍。
对于不再进行其他热处理的球墨铸铁铸件,都应进行去应力退火。
玻璃压型产品退火后的检验标准

玻璃压型产品退火后的检验标准本标准适用于压型产品退火后的寸法检验、外观检验与内在质量检验、数据测试及应力检验和UV检验的标准。
1、寸法检验:1.1检验内容:产品图面中标有公差的规格及R。
1.2检验依据:产品图。
1.3检验方法:抽检、全检。
1.3.1抽检数量按GB2828执行,合格质量水平为AQL1.0;客户订货时有特别要求的,按客户要求执行。
1.3.2在抽检判定为不合格后,寸法检验结束。
1.3.3若抽检判定为不合格,则进行全数检验。
2、外观与内在质量检验:2.1检验内容:折叠、裂纹、变形、形状不完整、飞边、厚薄差、破边、表面杂质、气泡、结石。
2.2检验依据:2.2.1一般情况按客户产品图进行检验;2.2.2在产品图中没有规定的情况下,按公司《压型毛坯检验标准》进行检验。
2.3检验条件:用肉眼在100瓦的白炽灯下进行产品检验。
2.4检验方式:抽检、全检。
2.4.1抽检数量按GB2828执行,合格质量水平为AQL1.0;客户订货时有特别要求的,按客户要求执行。
2.4.2在抽检判定合格后,外观检验结束。
2.4.3若抽检判定为不合格,则进行全数检验。
3、数据测试及应力检验:3.1检验内容:nd、vd、应力3.2检验依据:3.2.1一般情况按客户产品图进行检验;3.2.2在产品图中没有规定的情况下,按公司《压型毛坯检验标准》进行检验。
3.3检验条件:3.3.1 nd、vd测试在V棱镜折光仪上进行。
3.3.2应力检测在应力仪上进行。
3.4检验方法:抽检、全检。
3.4.1抽检数量按“每炉上、中、下各一件”执行,nd、vd不合格判定为0,即不允许有不合格,若测试中发现有不合格,则重新退火;3.4.2应力不合格判定数为0,但是发现不合格产品后应进行全数检验,对不合格产品返工重新退火。
4、UV检验:4.1检验内容:二次压型产品的荧光颜色。
4.2检验依据:①同一批号产品;②同一零件产品。
4.3检验条件:在紫外光线照射下。
- 1、下载文档前请自行甄别文档内容的完整性,平台不提供额外的编辑、内容补充、找答案等附加服务。
- 2、"仅部分预览"的文档,不可在线预览部分如存在完整性等问题,可反馈申请退款(可完整预览的文档不适用该条件!)。
- 3、如文档侵犯您的权益,请联系客服反馈,我们会尽快为您处理(人工客服工作时间:9:00-18:30)。
退火工序质量检验标准细则
一、检验范围:
监督退火工艺的执行情况及退火后成品的质量检验:
1、退火温度,升温时间,保温时间;
2、退火后产品的表面质量及硬度检测;
二、检验标准:
1、按退火工艺要求,对退火温度、升温时间、保温时间进行监督检查,并
做好工艺检查记录;
2、硬度要求应符合表2的规定
HRB
定
三、检查范围:
A、表面质量,用肉眼观察退火后钢带表面的颜色及氧化程度,用90°弯曲实
验检验,弯曲时不得有片状剥落,但允许有粉状剥落。
光亮退火钢带用肉眼观察表面应为银白色。
B、通过取样检验钢带的性能。
原则上规定每卷钢带均须取样用以做表面硬度
检测。
特殊情况须质检员跟随取样。
C、所取试样一次试验全部合格(可允许有不超过总量5%的个别不合格),或
有个别不合格的须对不合格品进行再取样。
如仍不合格则须进行其他处理(回火等);
四、检查工作要求:
1、按生产计划对退火前带钢认真检查,规格与生产通知单不符的须与上游
工序仔细核对。
如不知产品适合用途且找不到相关生产通知,则不予装炉;
2、取样时同时用肉眼和手感检查带钢是否粘连,发现有粘连后应立即挑出;
3、取样时应使试样保持原始状态,不能人为变形。
应详细检查,不允许有规定之外的其他缺陷;
4、对合格品要认真进行标识,并且按照相应要求填写工艺流程卡;
5、不合格品应明确标识,注明不合格原因,隔离分放,并及时上报生产部;。