热处理中的涡流及预多频检测技术
现代无损检测技术第5章:涡流检测技术

12×2—103—4—5—6—2×图1 涡流渗透深度与激励频率的关系图2 藕合线圈的互感电路a) 藕合线圈电路b)互感作用电路c) 藕合线圈等效感电路折合阻抗与一次线圈本身的阻抗之和称为图3 交流电路中电压和阻抗平面图线圈等效电路b)电压向量图c)阻抗向量图图4图5 阻抗平面图a)线圈阻抗平面b)归一化阻抗曲线图5 福斯特的假想物理模型表2 不同频率f/fg 的有效磁导率μeff的值表中:f为涡流检测的激励频率,也称之为工作频率,fg 为特征频率。
f/fg为频率比,它是涡流检测中的一个重要参数。
因此归一化电压为:数所决定,即:a)绝对式2-检测线圈3-管材在裂纹)时。
检测线圈就有信号输出,来实现检测目的。
标准的比较式1-参考线圈2-检测线圈4-棒材线圈感应输出急剧变化的信号。
c)自比较式1-参考线圈2-检测线圈3邻桥臂上。
用于管子检测的探头线圈在交流桥路中的位置电桥个参考线圈。
绝对式探头1 2线圈2 3-软定心导板4-接插件5探伤的材料进行检测。
差动式探头1 2线圈2 3-软定心导板4-接插件5-外壳二. 涡流检测的频率选择用于非铁磁性圆柱形棒料的检测频率选择图图中:IACS 为国际退火铜标准图的使用方法如下:1) 在A 线上取棒料电导率σ;2) 在B 线上取棒料直径d ;3) 将这两点间的连线延长使之与C 线相交;4) C 线上的交点垂直向上画直线,与所需的kr 值所对应的水平线相交得到一点;5) 根据交点在频率图(斜线)中的位置,即可读出所需的工作频率。
只要适当调节控制信号OT的相位,使θ2=90º,那么,干扰信号的输出为零,而总的信号输出(OC=OAcosθ1仅与缺陷信号有关,消除了不平衡电桥法工作原理在涡流检测中用作参考标准的人工缺陷的种类和形状检测线圈的阻抗特性表面探头以50Hz的频率检测厚铝板缺陷绝对式探头检测阻抗图b)差动式探头检测阻抗图1、2-裂纹3-表层下洞穴时处理,并将结果在CRT上进行实时显示。
第五章 涡流检测

第五章涡流检测涡流是当金属导体处在变化着的磁场中或在磁场中运动时,由于电磁感应作用而在金属导体内产生的旋涡状流动电流。
(我们在实践中会遇到一些涡流现象,如金属存在电阻,当电流流过金属导体内时会产生焦耳热。
工业上利用这种热效应制动了高频感应电炉来冶炼金属。
这种电炉的炉壁上绕有线圈,当线圈接通高频大功率电源时,炉体内随之产生很强的高频交变磁场。
在炉体放置一定数量的金属,金属中便产生强大的涡流致使金属被加热至熔化。
) 涡流检测具有以下特点:①由于检测是以电磁感应为基础的,探头线圈不需接触工件,因此检测速度快。
(对管、棒材。
每分钟可检测几十米,线材可检测几百米实)易于实现自动化检测。
②对工件表面和近表面的缺陷,有较高的检测灵敏度。
③能在高温状态下,对管、棒、线材和坏料等进行检测。
④涡流检测技术是一种多用途的检测技术,除探伤外,还能测量工件、涂层的厚度、间隙以及工件的机械和冶金性能等。
⑤能提供缺陷的信息。
⑥实验结果可与检测过程同时得到,记录可长时期保存。
由于感生涡流渗入工件的深度与频率的平方根成反比(感生涡流具有趋肤效应)。
这个深度不大,因此,涡流检测目前只能检测表面及近表面的缺陷。
另外,因为影响涡流检测的因素如导电率、磁导率、缺陷、工件形状和尺寸以及探头线圈与工件之间的距离等,要取得所希望得到的检测参数,需要较复杂的信息处理技术。
还有涡流检测对复杂表面的检测效率低。
第一节 涡流检测的物理基础一、材料的导电性(一)材料的导电率根据欧姆定律,沿一段导体流动的电流强度与其两端的电位差成正比。
即:RU I = 根据一定材料的导体,它的电阻与导体长度(L)成正比,与导体的截面积(S)成反比。
即:SL R ρ= 我们称ρ为导体的电导率单位为:(Ω·mm 2/m)或(μ·Ω·cm)(二)影响电导率的因素1.杂质含量如果在导体中掺入杂质,杂质会影响原子的排列,引起电阻率的增加。
2.温度随着导体的温度升高,导体内的原子热振动加剧,自由电子的碰撞机会增加,电阻率随之增加。
热处理过程中的无损检测技术探索

热处理过程中的无损检测技术探
索
热处理过程中的无损检测技术探索
热处理是一种常用的工艺,用于改变材料的性质和结构。
在热处理过程中,无损检测技术是一种重要的工具,用于检测材料是否存在缺陷或异常。
首先,热处理过程中最常用的无损检测技术之一是超声波检测。
超声波检测利用声波在材料中传播的原理,通过检测声波的传播速度和衰减情况来判断材料中是否存在缺陷。
在热处理过程中,超声波检测可以用于检测材料的内部结构是否发生变化,例如晶粒尺寸的改变、相变的发生等。
其次,磁粉检测也是热处理过程中常用的无损检测技术之一。
磁粉检测利用磁场的作用,通过在材料表面涂覆磁粉,并施加磁场,以检测材料表面或近表面的缺陷。
在热处理过程中,磁粉检测可以用于检测材料的表面是否存在裂纹、裂纹的深度和长度等。
另外,涡流检测也是一种常用的无损检测技术。
涡流检测利用导体中的涡流效应,通过在材料表面施加交变磁场,检测材料中的缺陷。
在热处理过程中,涡流检测可以用于检测材料中的细小裂纹、气孔等缺陷。
最后,X射线检测也是常用的无损检测技术之一。
X射线检测利用X射线的穿透能力,通过照射材料并
检测透射或散射的X射线来判断材料中的缺陷。
在热处理过程中,X射线检测可以用于检测材料的密度变化、晶体结构的改变等。
综上所述,热处理过程中的无损检测技术是一种非常重要的工具,可以用于检测材料中的缺陷和异常。
超声波检测、磁粉检测、涡流检测和X射线检测是常用的无损检测技术,它们各有优势和适用范围。
在实际应用中,可以根据具体情况选择合适的无损检测技术,以确保热处理过程的质量和安全。
涡流检测技术概述

涡流检测技术概述涡流技术由于具有的很多优点而被广泛应用。
首先,它是非接触检测,而且能穿透非导体的覆盖层,这就使得在检测时不需要做特殊的表面处理,因此缩短了检测周期,降低了成本。
同时,涡流检测的灵敏度非常高。
涡流检测按激励方式和检测原理的不同可以分为单频涡流、多频涡流、脉冲涡流、远场涡流等,下面对这些技术的发展简要的加以介绍。
传统的涡流采用单频激励的方式,主要来对表面及近表面的缺陷进行检测,根据被测材料及缺陷深度的不同,激励频率的范围从几赫兹到几兆赫兹不等,为 了得到良好的检测信号,激励线圈必须在缺陷的附近感应出最大的涡流,感应电 流的大小和激励频率、电导率、磁导率、激励线圈的尺寸和形状以及激励电流的 大小有关,通过测量阻抗或电压的变化来实现对缺陷的检测。
然而,由于其它参数也很敏感,这就影响了对缺陷的检测。
为了克服单频涡流的缺点,1970 年美国人 Libby 提出了多频涡流的技术(Multi-frequency Eddy Current, MFEC),多频涡流是同时用几个频率信号激励探头,较单频激励法可获取更多的信号,这样就可以抑制实际检测中的许多干扰因素,如热交换管管道中的支撑板、管板、凹痕、沉积物、表面锈斑和管子冷加工产生的干扰噪声,汽轮机大轴中心孔、叶片表面腐蚀坑、氧化层等引起的电磁噪声,以及探头晃动提离噪声等。
理论与实践表明,被测工件的缺陷和上述干扰因素对不同频率的激励信号各有不同的反应,可反应出不同的涡流阻抗平面。
利用这一原理,用两个(或多个)不同频率的正弦波同时激励探头,然后由两个(或多个)通道分别进行检波、放大和旋转等处理,此后,通过多个混合单元的综合运算,就可以有效的去除信号干扰,准确的获取缺陷信号。
但是,多频涡流只能提供有限的检测数据,很难以可视化的方式实现对缺陷的成像检测。
70 年代中后期,脉冲涡流技术(Pulsed Eddy Current, PEC)在世界范围内得到广泛的研究,PEC最早由密苏里大学的Waidelich在20世纪50年代初进行研究,脉冲涡流的激励电流为一个脉冲,通常为具有一定占空比的方波,施加在探头上的激励方波会感应出脉冲涡流在被测试件中传播,根据电磁感应原理,此脉冲涡流又会感应出一个快速衰减的磁场,随着感生磁场的衰减,检测线圈上就会感应出随时间变化的电压,由于脉冲包含很宽的频谱,感应的电压信号中就包含重要的深度信息。
(完整版)涡流检测技术

视在电阻
阻抗的归一化
经过归一化处理
后的电阻和电抗都 是无量纲的量,并 且都恒小于1。
归一化阻抗图的特点
• (1)它消除了原边线圈电阻和电感的影响,具有通用性。 • (2)阻抗图的曲线簇以一系列影响阻抗的因素作为参量。 • (3)阻抗图形定量地表示出各影响阻抗因素的效应大小和方向。 • (4)对于各种类型的工件和检测线圈,有各自对应的阻抗图。
进行涡流检测的步骤:(探针式涡流探伤仪为例)
I. 摸清被检零件的裂纹规律
如零件的材料组织与特性、结构形状、制造时的加工方法、装 配位置、使用时间、受力状态、可能产生或经常产生裂纹的部 位、裂纹的方向等。
II. 参考试件的准备和制作
最好采用报废的有自然缺陷(裂纹)的相同零件作为参 考试件。
也可用无自然裂纹的零件,在容易产生疲劳裂纹的部位用机械加 工法,或腐蚀法,或电火花加工人工缺陷的参考试件。
金属试件上涂、压力等的监控; 试件尺寸、形状测量等。
主要应用
• (1)能检测出材料和构件中的缺陷,例如裂纹、折叠、气孔和夹杂等。 • (2)能测量材料的电导率、磁导率、检测晶粒度、热处理状况、材料
的硬度和尺寸等。
• (3)金属材料或零件的混料分选。通过检查其成分、组织和物理性能
涡流检测的主要用途及影响感生涡流的特性的主要因素
目的 探伤
材质试验
厚度及位移 等的测量
检测因素 试件中的裂纹、腐 蚀、凹坑、夹杂、 气泡等
电导率 磁导率
提离效应、厚度效 应、充填效应等
典型应用
管、棒、线、板材等的探伤; 机制件的探伤; 飞机维护及管道系统的维护检查; 疲劳裂纹的监视。
测量金属试件的电磁参数; 金属热处理状态的鉴别; 金属材料的分选; 金属材料成分含量、杂质含量的鉴 别。
简述涡流检测技术.doc

涡流检测技术什么是无损检测?nondestructive testing,NDT,在不损伤构件性能和完整性的前提下,检测构件金属的某些物理性能和组织状态,以及查明构件金属表面和内部各种缺陷的技术。
名词解释:端部效应:在涡流检测中,由于工件的几何形状(边缘)急剧改变而引起邻边磁场和涡流干扰,将掩盖着一定范围的缺陷的检出。
这种现象称之为端部效应。
由于端部效应的存在,在钢管探伤时,当管子的端部(头和尾)进入或离开检测线圈时,对于位于靠近管子端部的缺陷,将失去灵敏度,管子端部通常存在着一段肓区。
阻抗:阻抗是用来评估电子元件特性的一个参数。
阻抗的定义是元件在既定频率下对交流电的总对抗作用。
电磁感应:当穿过闭合导电回路所包围面积的磁通量发生变化时,回路中就会产生感应电流,这种现象叫/Dt此做电磁感应现象。
回路中产生的感应电动势Ei等于所包围面积中磁通量Φ随时间变化的负值,Ei=Dr负值表明闭合回路中感应电流所产生的磁场总是阻碍产生感应电流的磁通的变化,这个方程称为法拉第电磁感应定律。
自感应:当线圈中通以交变电流I时,其所产生的交变磁通量也将在本线圈中产生感应电动势,此现象称=L*Di/Dt(L为自感电动势。
为自感现象,产生的感应电动势称为自感电动势EL互感应:当两个线圈相互靠近,线圈中分别流过交变电流I1和I2的情况下,由线圈1中电流I1所引起的变化的磁场通过线圈2时会在线圈2中产生感应电动势;同样,线圈2中电流I2所引起的变化的磁场通过线圈1时会在线圈1中产生感应电动势,这种两载流线圈相互激起感应电动势的现象称为互感现象.增益:是无线组成部件中电压或功率的增加。
是表征涡流探伤灵敏度的参数之一。
耦合:耦合就是指两个或两个以上的实体相互依赖于对方的一个量度。
磁力线:在磁场中画一些曲线,用(虚线或实线表示)使曲线上任何一点的切线方向都跟这一点的磁场方向相同(且磁感线互不交叉),这些曲线叫磁感线。
磁感线是闭合曲线。
涡流检测技术

涡流密度衰减为其表面密度的 1/e (36.8%) 时对应的深度 渗透深度随被检材料的电导率、磁导率及激励频率的增大而减小。
涡流探伤能够达到的极限深度:
涡流密度仅约为其表面密度的5%时的深度 - 3δ。
3.2.2.2 趋肤效应和渗透深度
Depth Depth
Eddy Current Density
3.4 涡流检测方法
3.4.1 涡流检测一般操作步骤 3.4.2 涡流检测的频率选择 3.4.3 涡流检测信号分析 3.4.4 提离效应及其抑制
3.4.2 涡流检测的频率选择
被检工件材料
非磁性材料:高频,数千赫兹 磁性材料:较低的频率
透入深度要求:频率越低透入深度越大 灵敏度要求(分辨力):频率低灵敏度减小
3.2 涡流检测基础知识
3.2.1 与涡流检测相关的电学 和磁学基本知识
3.2.2 涡流检测技术原理
3.2.1 与涡流检测相关的电学和磁 学基本知识
3.2.1.1 金属的导电性
3.2.1.2 金属的磁特性 3.2.1.3 电磁感应
3.2.1.2 金属的磁特性
磁化:
物质在外磁场作用下感生出磁场的物理过程称为磁化。
while conducting an inspection, signals generated from the test specimen must be compared with known values.
• Reference standards are typically manufactured from the
抑止方法:
多项式拟合法 数字滤波 多频测量 模具支架固定探头
3.5 涡流检测诊断常用标准
1 钛及钛合金管材的涡流检验:GB/T12969.2—1991
涡流检测技术应用

涡流检测技术应用
1 检测线圈 涡流检测设备-检测线圈
(1) 检测线圈分类
穿过式线圈 内通过式线圈 探头式线圈 检测线圈与被检工件的相对位置
涡流检测技术应用
涡流检测设备-检测线圈
(2) 检测线圈的使用方式 按电联接方式的不同, 检测线圈有绝对式和差动式两种使用方式。
涡流检测技术应用
焊缝涡流检测
涡流检测技术应用
焊缝的脉冲激励涡流检测
涡流检测技术应用
阵列涡流
涡流检测技术应用
涡流检测技术应用
涡流检测技术应用
图 线圈等效电路与阻抗向量 (a)电感电阻串联电路(b)电压向量 (c)阻抗向量
涡流检测技术应用
图 线圈等效电路与阻抗向量 (a)电感电阻串联电路(b)电压向量 (c)阻抗向量
a)绝对式 b)标准比较式 c)自比较式 1-参考线圈 2-检测线圈 3-管材 4-棒材
涡流检测技术应用
1、绝对式 只用一个检测线圈进行涡流检测的方式。 仅针对被检测 对象某一位置的电磁特性直接进行检测的线圈, 而不与被检 对象的其他部位或对比试样某一部位的电磁特性进行比较检 测。先对标准试样调零后,再对被检工件进行检测。以这种 方式工作的线圈可用于材质分选和涂层测厚,也可用于材料 探伤。
涡流检测技术应用
3.4 涡流检测的应用
1 涡流探伤
(1) 金属管材探伤 特点:高速、自动化、批量
检测管材的穿过式线圈
1-V型滚轮 2-磁饱和线圈 3管材 4-激励线圈 5-测量线圈
涡流检测技术应用
检测管材的探头式线圈 在线检测
如果管材直径过大,使得缺陷面积在整个被检面积中占的 比例很小时,检测的灵敏度也会显著降低。检测管材的周向裂 纹或当管材的直径超过75 mm时,宜采用小尺寸的探头式线圈以 探测管材上的短小缺陷。探头数量的多少取决于管径的大小。 探头式线圈的优点是提高了检测灵敏度,但其探伤的效率要比 穿过式线圈低。
涡流检测
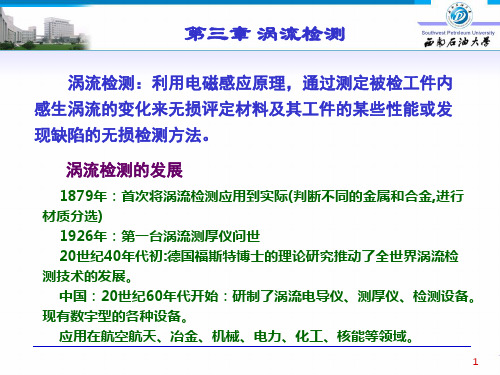
12
(2)按电联接方式分类(P75) a.绝对式:只用一个检测线圈进行涡流检测
适用场合:材质分选、涂层测厚及材料探伤
b.差动式:两个线圈反接在一起进行工作
标准比较式 自比较式
适用场合:管(棒)材表面的局部缺陷。 优缺点比较见P77表3-3。 3.对比试样 作用:检测和鉴定涡流检测仪的性能,如灵敏度、分辨
化就可发现有无缺陷。
5
H1 I1 H2 δ
原线圈的等效阻抗Z变化:
I2
Z Z ( , , , )
被测体电阻率 被测体磁导率 激励电流的频率
线圈与导体间距离
涡流作用原理
6
3.涡流的趋肤效应
趋肤效应:当交变电流通过导体
时,分布在导体横截面上的电流密度 是不均匀的,即表层密度最大,越靠 近截面的中心电流密度越小的现象。 涡流的衰减公式:
硬度HRB
时效硬化铝合金的硬度与电导率的关系
16
(3)混料分选
如果混杂材料或零部件的电导率分布带不相互重合,就可 以利用涡流法先测出混料的电导率,再与已知牌号或状态的材 料和零部件的电导率比较,从而将混料区分开。
注意事项: 1)材料厚度的影响
进行混料分选时,材料厚度至少应为涡流渗透深度的3倍。
2)环境温度的影响
40 0
P 0.5
Fe
Si 1
铜中杂质的含量%
铜中杂质的含量与电导率的关系
15
(2)热处理状态的鉴别 原理:相同的材料经过
电导率(相对值) 1.85 1.80 1.75
1.70 1.65 1.60 1.55 1.50 84 86 88
不同的热处理后不仅硬度不
同,而且电导率也不同。
铝合金
无损检测(NDT)——涡流检测(ET)技术

无损检测(NDT)——涡流检测(ET)技术郭健【摘要】从涡流检测装置、参考试块和检测方法等方面系统地介绍了涡流检测技术.【期刊名称】《工程与试验》【年(卷),期】2012(052)001【总页数】4页(P36-39)【关键词】涡流;参考试块;人工缺陷;检测线圈【作者】郭健【作者单位】国家试验机质量监督检验中心,吉林长春130062【正文语种】中文【中图分类】TM1541 前言涡流是交变磁场在导电材料中感生的电流,涡流检测是根据导电材料中感应电流原理实现的。
涡流检测主要用于线、棒和管形钢材的无损检测。
涡流检测的目的是检测材料内表面存在的缺欠或评价材料厚度变化的情况。
涡流检测的优点是与被检测工件没有任何物理性质的接触、不需要耦合介质,易于在高速生产线上使用。
本文从检测装置和检测方法等方面系统地介绍涡流检测技术。
2 涡流检测涡流检测分为静态和动态两类,现阶段主要使用的是动态检测技术。
动态检测要求传感器与被检测工件之间能够相对位移,可以用手动或精密机械控制扫查路径的方式实现产品检测。
涡流检测系统主要由涡流检测仪、传感器或探头(检测线圈)、参考试块、连接电缆线、进给装置(包括检测线圈支承台架)、记录单元和磁饱和装置构成。
有时也可以省略磁饱和装置。
涡流检测仪、检测线圈和参考试块是构成涡流检测系统的三要素。
通用涡流检测技术包括:(1)对固定基准点产生的偏差进行测量的绝对测量技术。
基准点由标定程序加以确定,利用基准电压或参考线圈可以提供基准点。
绝对测量法可以依据材料的硬度、尺寸和化学成分等物理特性对被检产品进行等级分选,也可以对连续或逐渐变为非连续的信号加以识别。
(2)比较测量技术,利用两个测量信号的差值(其中一个作为参考信号)对被检产品进行等级分选。
(3)差动测量技术,是由测量位置或相同扫查路径间的差值产生的恒定间隔实现的。
差动测量时,由于被检产品内部信号变化缓慢而使背景噪音信号减少。
(4)双差动测量技术,是使两个差动测量信号相减。
涡流检测方案范文

涡流检测方案范文涡流检测是一种非接触式的无损检测技术,主要用于检测金属材料中的缺陷或特定的材质性质。
它的原理是通过交流电磁场在金属材料中感应涡流,进而检测材料中的缺陷或其他参数。
仪器设备:涡流检测的仪器设备包括探头和检测仪器。
探头是用于产生涡流和接收反馈信号的设备,通常包括电磁线圈和磁芯。
检测仪器主要用于控制和分析探头的信号,常见的有涡流检测仪、信号处理器和数据记录仪等。
检测方法:涡流检测主要有单频和多频两种方法。
单频涡流检测使用恒定频率的交流电磁场,通常适用于简单结构的材料,如金属板或管道等。
多频涡流检测则是通过改变频率来检测不同深度或尺寸的缺陷,适用于复杂结构的材料。
数据分析:涡流检测的数据分析是非常重要的一步,可以通过对检测信号进行处理和分析,确定材料中的缺陷位置和尺寸。
常用的数据分析方法有图像处理、频谱分析和统计分析等。
图像处理可以将检测信号可视化,便于人工分析;频谱分析可以提取信号频率分布信息,辅助缺陷识别;统计分析则用于对多组数据进行比较和判断。
涡流检测方案的应用领域广泛,包括航空航天、汽车制造、电力设备、轨道交通等。
在航空航天领域,涡流检测可以用来检测飞机发动机叶片、涡轮盘和航空材料的缺陷;在汽车制造领域,涡流检测可以检测发动机缸体、传动轴和车身钢板的缺陷;在电力设备领域,涡流检测可以检测电缆接头、发电机线圈和电力装置的缺陷;在轨道交通领域,涡流检测可以用来检测铁轨、列车车轮和牵引设备的缺陷。
总结来说,涡流检测方案是一种非接触式的无损检测技术,应用广泛且效果可靠。
通过仪器设备的选择、检测方法的确定以及数据分析的处理,可以实现对金属材料中缺陷和性质的准确检测。
涡流检测方案在不同领域的应用带来了显著的经济和安全效益,同时也推动了涡流检测技术的不断创新与发展。
涡流检测技术概述

涡流检测技术概述资料整理:无损检测资源网沧州市欧谱检测仪器有限公司一、涡流检测原理涡流检测是建立在电磁感应原理基础之上的一种无损检测方法,它适用于导电材料,如果我们把一块导体置于交变磁场之中,在导体中就有感应电流存在,即产生涡流,由于导体自身各种因素(如电导率、磁导率、形状、尺寸和缺陷等)的变化会导致感应电流的变化,利用这种现象而判知导体性质、状态的检测方法,叫做涡流检测方法。
由涡流产生的交流磁场也产生磁力线,其磁力线也是随时间而变化,它穿过激磁线圈时又在线圈内感生出交流电。
因为这个电流方向与涡流方向相反,结果就与激磁线圈中原来的电流方向相同了。
这就是说线圈中的电流由于涡流的反作用而增加了。
假如涡流变化,这个增加的部分(反作用电流)也变化。
测定这个电流变化,从而可得到试件的信息。
涡流的分布及其电流大小,是由线圈的形状和尺寸,交流频率(试验频率),导体的电导率、磁导率、形状和尺寸,导体与线圈间的距离,以及导体表面缺陷等因素所决定的。
因此,根据检测到的试件中的涡流,就可以取得关于试件材质,缺陷和形状尺寸等信息。
二、涡流检测方法涡流检测是把导体接近通有交流电的线圈,由线圈建立交变磁场,该交变磁场通过导体,并与之发生电磁感应作用,在导体内建立涡流。
导体中的涡流也会产生自己的磁场,涡流磁场的作用改变了原磁场的强弱,进而导致线圈电压和阻抗的改变。
当导体表面或近表面出现缺陷时,将影响到涡流的强度和分布,涡流的变化又引起了检测线圈电压和阻抗的变化,无损检测资源网根据这一变化,就可以间接地知道导体内缺陷的存在。
由于试件形状的不同,检测部位的不同,所以检验线圈的形状与接近试件的方式与不尽相同。
为了适应各种检测需要,人们设计了各种各样的检测线圈和涡流检测仪器。
1、检测线圈及其分类在涡流探伤中,是靠检测线圈来建立交变磁场;把能量传递给被检导体;同时又通过涡流所建立的交变磁场来获得被检测导体中的质量信息。
所以说,检测线圈是一种换能器。
涡流检测技术
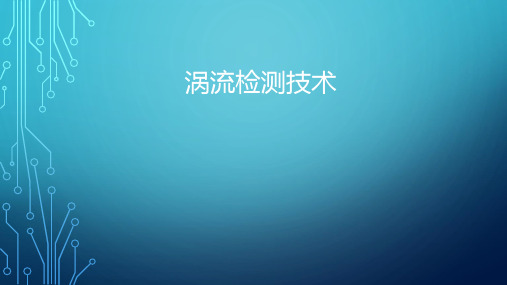
Thank you
涡流检测的主要用途及影响感生涡流的特性的主要因素
目的 探伤
材质试验
厚度及位移 等的测量
检测因素 试件中的裂纹、腐 蚀、凹坑、夹杂、 气泡等
电导率 磁导率
提离效应、厚度效 应、充填效应等
典型应用
管、棒、线、板材等的探伤; 机制件的探伤; 飞机维护及管道系统的维护检查; 疲劳裂纹的监视。
测量金属试件的电磁参数; 金属热处理状态的鉴别; 金属材料的分选; 金属材料成分含量、杂质含量的鉴 别。
金属试件上涂、镀等膜层测量; 板材测厚; 位移、振动测量; 液面位置、压力等的监控; 试件尺寸、形状测量等。
主要应用
• (1)能检测出材料和构件中的缺陷,例如裂纹、折叠、气孔和夹杂等。 • (2)能测量材料的电导率、磁导率、检测晶粒度、热处理状况、材料
的硬度和尺寸等。
• (3)金属材料或零件的混料分选。通过检查其成分、组织和物理性能
当探头从零件的中间部位移动到零件的边缘时,仪器所发生的报警现
象,是由于边缘效应所致,一般不是裂纹信号
当探头扫描移动到局部漆层脱落处,仪器所发出的报警现象,属间隙
效应引起,一般不是裂纹信号
当探头移动到受检部位的形状,或曲率发生变化的区域时,发出的报
警现象,一般不是裂纹信号
在对非磁性材料进行涡流检测过程中,如探头移动到磁性材料附近,
涡流检测的特点
• 优点: • (1)不需耦合剂,对管、棒、线材易于实现自动化。 • (2)对导电材料表面和近表面缺陷的检测灵敏度较高。 • (3)能在高温、高速下进行检测。 • (4)应用范围广,对影响感生涡流特性的各种物理和工艺因素均能实现检测。 • (5)工艺简单、操作容易、检测速度快。
涡流检测基本原理
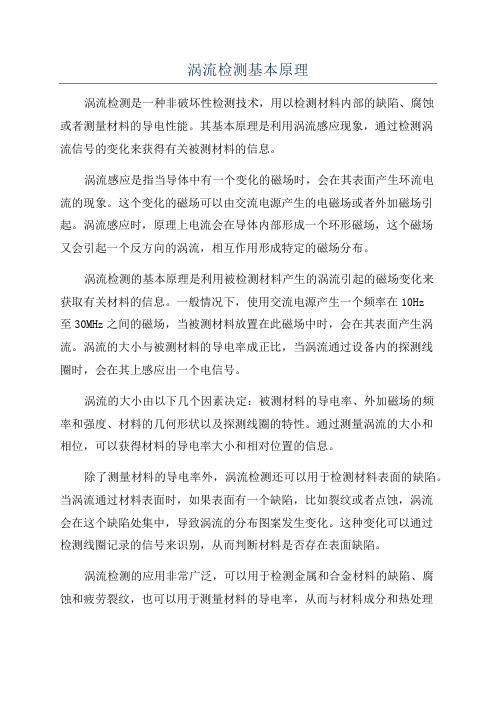
涡流检测基本原理涡流检测是一种非破坏性检测技术,用以检测材料内部的缺陷、腐蚀或者测量材料的导电性能。
其基本原理是利用涡流感应现象,通过检测涡流信号的变化来获得有关被测材料的信息。
涡流感应是指当导体中有一个变化的磁场时,会在其表面产生环流电流的现象。
这个变化的磁场可以由交流电源产生的电磁场或者外加磁场引起。
涡流感应时,原理上电流会在导体内部形成一个环形磁场,这个磁场又会引起一个反方向的涡流,相互作用形成特定的磁场分布。
涡流检测的基本原理是利用被检测材料产生的涡流引起的磁场变化来获取有关材料的信息。
一般情况下,使用交流电源产生一个频率在10Hz至30MHz之间的磁场,当被测材料放置在此磁场中时,会在其表面产生涡流。
涡流的大小与被测材料的导电率成正比,当涡流通过设备内的探测线圈时,会在其上感应出一个电信号。
涡流的大小由以下几个因素决定:被测材料的导电率、外加磁场的频率和强度、材料的几何形状以及探测线圈的特性。
通过测量涡流的大小和相位,可以获得材料的导电率大小和相对位置的信息。
除了测量材料的导电率外,涡流检测还可以用于检测材料表面的缺陷。
当涡流通过材料表面时,如果表面有一个缺陷,比如裂纹或者点蚀,涡流会在这个缺陷处集中,导致涡流的分布图案发生变化。
这种变化可以通过检测线圈记录的信号来识别,从而判断材料是否存在表面缺陷。
涡流检测的应用非常广泛,可以用于检测金属和合金材料的缺陷、腐蚀和疲劳裂纹,也可以用于测量材料的导电率,从而与材料成分和热处理状态相关联。
此外,涡流检测还可以应用在电子元器件、航空航天、汽车制造和石油化工等行业。
涡流检测的优点包括非接触性、快速性、高灵敏度和高精度,同时不会对材料造成任何损伤。
然而,涡流检测也存在一些限制,比如只能用于导电材料,对于非导电材料无法进行有效检测。
此外,涡流检测的精度受到材料特性、外界干扰和设备性能等因素的影响。
总之,涡流检测是一种基于涡流感应原理的非破坏性检测技术,可以用于检测材料的导电率和表面缺陷。
(2021年整理)涡流检测的技术

(完整)涡流检测的技术编辑整理:尊敬的读者朋友们:这里是精品文档编辑中心,本文档内容是由我和我的同事精心编辑整理后发布的,发布之前我们对文中内容进行仔细校对,但是难免会有疏漏的地方,但是任然希望((完整)涡流检测的技术)的内容能够给您的工作和学习带来便利。
同时也真诚的希望收到您的建议和反馈,这将是我们进步的源泉,前进的动力。
本文可编辑可修改,如果觉得对您有帮助请收藏以便随时查阅,最后祝您生活愉快业绩进步,以下为(完整)涡流检测的技术的全部内容。
目录涡流检测技术及进展 (2)涡流检测自然裂纹与信号处理 (5)压力容器列管涡流检测技术的研究 (9)金属锈蚀的涡流检测 (11)涡流检测技术及进展1 引言涡流检测是建立在电磁感应原理基础上的无损检测方法。
如图1,已知法拉第电磁感应定律,在检测线圈上接通交流电,产生垂直于工件的交变磁场。
检测线圈靠近被检工件时,该工件表面感应出涡流同时产生与原磁场方向相反的磁场,部分抵消原磁场,导致检测线圈电阻和电感变化。
若金属工件存在缺陷,将改变涡流场的强度及分布,使线圈阻抗发生变化,检测该变化可判断有无缺陷。
随着微电子学和计算机技术的发展及各种信号处理技术的采用,涡流检测换能器、涡流检测信号处理技术及涡流检测仪器等方面出现长足发展.2 涡流检测的信号处理技术提高检测信号的信噪比和抗干扰能力,实现信号的识别、分析和诊断,以得出最佳的信号特征和检测结果.2。
1 信号特征量提取常用的特征量提取方法有傅里叶描述法、主分量分析法和小波变换法。
傅里叶描述法是提取特征值的常用方法。
其优点是,不受探头速度影响,且可由该描述法重构阻抗图,采样点数目越多,重构曲线更逼近原曲线。
但该方法只对曲线形状敏感,对涡流检测仪的零点和增益不敏感,且不随曲线旋转、平移、尺寸变换及起始点选择变化而变化.用测试信号自相关矩阵的本征值和本征矢量来描绘信号特征的方法称为主分量分析法,该方法对于相似缺陷的分辨力较强.小波变换是一种先进的信号时频分析方法。
涡流检测技术
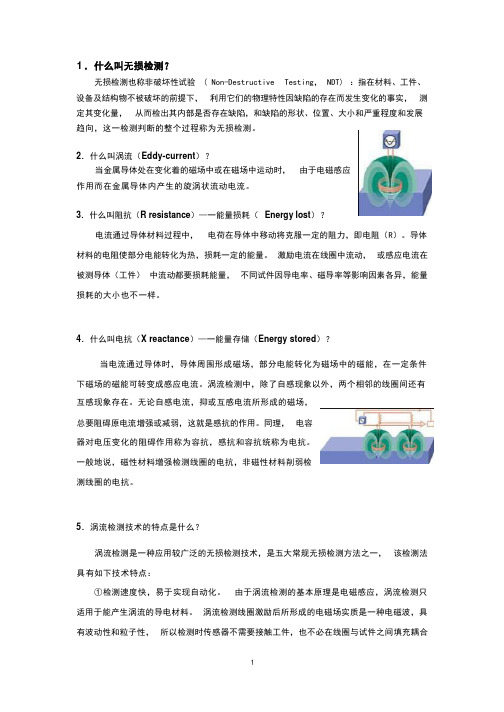
1无损检测也称非破坏性试验( Non-Destructive Testing, NDT) :指在材料、工件、设备及结构物不被破坏的前提下,利用它们的物理特性因缺陷的存在而发生变化的事实,测定其变化量,从而检出其内部是否存在缺陷,和缺陷的形状、位置、大小和严重程度和发展趋向,这一检测判断的整个过程称为无损检测。
2.什么叫涡流(Eddy-current)?当金属导体处在变化着的磁场中或在磁场中运动时,由于电磁感应作用而在金属导体内产生的旋涡状流动电流。
3.什么叫阻抗(R resistance)—一能量损耗(Energy lost)?电流通过导体材料过程中,电荷在导体中移动将克服一定的阻力,即电阻(R)。
导体材料的电阻使部分电能转化为热,损耗一定的能量。
激励电流在线圈中流动,或感应电流在被测导体(工件)中流动都要损耗能量,不同试件因导电率、磁导率等影响因素各异,能量损耗的大小也不一样。
4.什么叫电抗(X reactance)—一能量存储(Energy stored)?当电流通过导体时,导体周围形成磁场,部分电能转化为磁场中的磁能,在一定条件下磁场的磁能可转变成感应电流。
涡流检测中,除了自感现象以外,两个相邻的线圈间还有互感现象存在。
无论自感电流,抑或互感电流所形成的磁场,总要阻碍原电流增强或减弱,这就是感抗的作用。
同理,电容器对电压变化的阻碍作用称为容抗,感抗和容抗统称为电抗。
一般地说,磁性材料增强检测线圈的电抗,非磁性材料削弱检测线圈的电抗。
5.涡流检测技术的特点是什么?涡流检测是一种应用较广泛的无损检测技术,是五大常规无损检测方法之一,该检测法具有如下技术特点:①检测速度快,易于实现自动化。
由于涡流检测的基本原理是电磁感应,涡流检测只适用于能产生涡流的导电材料。
涡流检测线圈激励后所形成的电磁场实质是一种电磁波,具有波动性和粒子性,所以检测时传感器不需要接触工件,也不必在线圈与试件之间填充耦合剂,因此检测速度快,对管、棒材的探伤每分钟可检查几十米;对丝、线材的探伤每分钟可达几百米,甚至上千米,因此,易于实现自动化检测。
涡流检测实验报告总结(3篇)
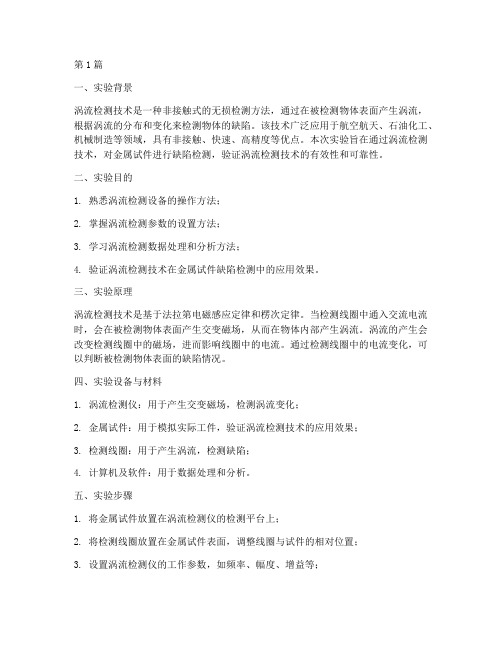
第1篇一、实验背景涡流检测技术是一种非接触式的无损检测方法,通过在被检测物体表面产生涡流,根据涡流的分布和变化来检测物体的缺陷。
该技术广泛应用于航空航天、石油化工、机械制造等领域,具有非接触、快速、高精度等优点。
本次实验旨在通过涡流检测技术,对金属试件进行缺陷检测,验证涡流检测技术的有效性和可靠性。
二、实验目的1. 熟悉涡流检测设备的操作方法;2. 掌握涡流检测参数的设置方法;3. 学习涡流检测数据处理和分析方法;4. 验证涡流检测技术在金属试件缺陷检测中的应用效果。
三、实验原理涡流检测技术是基于法拉第电磁感应定律和楞次定律。
当检测线圈中通入交流电流时,会在被检测物体表面产生交变磁场,从而在物体内部产生涡流。
涡流的产生会改变检测线圈中的磁场,进而影响线圈中的电流。
通过检测线圈中的电流变化,可以判断被检测物体表面的缺陷情况。
四、实验设备与材料1. 涡流检测仪:用于产生交变磁场,检测涡流变化;2. 金属试件:用于模拟实际工件,验证涡流检测技术的应用效果;3. 检测线圈:用于产生涡流,检测缺陷;4. 计算机及软件:用于数据处理和分析。
五、实验步骤1. 将金属试件放置在涡流检测仪的检测平台上;2. 将检测线圈放置在金属试件表面,调整线圈与试件的相对位置;3. 设置涡流检测仪的工作参数,如频率、幅度、增益等;4. 启动涡流检测仪,观察检测线圈中的电流变化;5. 分析电流变化,判断金属试件表面的缺陷情况;6. 改变检测参数,观察电流变化,验证参数对检测结果的影响;7. 记录实验数据,进行数据处理和分析。
六、实验结果与分析1. 在实验过程中,发现金属试件表面存在明显的缺陷,涡流检测仪能够准确检测出缺陷的位置和大小;2. 通过调整涡流检测仪的工作参数,发现参数对检测结果有显著影响。
适当调整参数,可以提高检测精度和灵敏度;3. 实验结果表明,涡流检测技术在金属试件缺陷检测中具有较好的应用效果,可以满足实际工程需求。
多频涡流

多频涡流检测
普通的涡流检测是用单个频率的激励信号进行检测,然而它由于只有一个频率的原因,所以很难去除一些外在的干扰信号。
而多频涡流检测则是在探头加上两个或两个以上的激励频率信号,通过调节信号幅度、相位和波形则可以消去一些外在不必要的干扰信号。
这对于检测一些有支撑板和支撑架的情况时效果特别明显,其可以消去支撑架等带来的干扰,使得检测结果更加的精确。
这在工业上带支撑架的热交换器管等在役的检测中应用尤为广泛。
涡流检测中,被检工件影响线圈阻抗(或感应电压)的因素很多,如:金属工件的材质、缺陷形状、电导率,磁导率以及在役检测中的工况(如管道的支撑板,飞机铝蒙皮)和检测探头的晃动、提离等都会对涡流信号产生影响。
根据不同的检测任务,这些作用参数有的必须被检测并计算出来.有的则视为干扰信号,必须予以剔除。
为达到这一日的.在涡流捡测中就需增加鉴别分选信号手段以便获得更多的试验变量,抑制多种干扰因素影响,提高检测的分辨率与可靠性,对被检工件作出正确评价。
多频涡流检测的基本原理。
信息传输理论中,香农一哈特(Shannon.Hartley)定理指出:一个信号所传输的信息量同信号的频带宽度以及信噪比的对数成正比。
在信息的传输过程中,使用频率的数量越多(即频带),获取的信息量越大。
因此,可根据所需检测的作用参数(如缺陷,镀层厚度等)和所要排除的干扰信号(如支撑扳、蒙皮和提离等),适当选取多个频率组合的电流去激励检测线圈,然后对受作用参数调制的输出信号按多个检测通道加以放大,分别进行解调,并把解调信号的各个分量以指定的方式组合起来.综合分析处理。
多频去噪示意图。
涡流检测技术的探讨

涡流检测技术的探讨常用的换热金属管包括铁磁性的碳钢和合金钢钢管以及非铁磁性的不锈钢钢管、等等。
涡流检测方法主要包括制造过程中的铁磁性钢管和非铁磁性金属管材的涡流检测技术、在用铁磁性钢管的远场涡流检测技术、在用非铁磁性金属管的涡流检测技术和金属压力容器壳体焊缝表面裂纹的复平面分析涡流检测技术。
一.涡流检测的国家标准目前国内普遍开展的是制造过程中各种金属管的涡流检测,并制定了如下检测标准:GB/T 5126 铝及铝合金冷拉薄壁管材涡流探伤方法GB/T 5248 铜及铜合金无缝管涡流探伤方法GB/T 7735 钢管涡流探伤检验方法GB/T 12604 .6 无损检测术语涡流检测GB/T 12969 .2 钛及钛合金管材涡流检验方法GB/T 14480 涡流探伤系统性能测试方法JB 4730 锅炉、压力容器及压力管道无损检测目前开展较多的为在用换热器非铁磁性金属管检测工作则刚刚开始,但这两方面均无现成的检测标准,目前在JB 4730 修订报批稿的第六部分中已经加入这两方面的内容。
二.新制铁磁性钢管的涡流检测对新制钢管进行涡流检测的目的,主要是控制钢管的产品质量,发现钢管上可能存在的通孔和表面裂纹等缺陷。
检测通孔的方法通常采用穿过式线圈,检测表面裂纹的方法通常采用扁平放置式线圈。
铁磁性钢管检测必须具有磁饱和装置,以便对检测线圈的检测区域施加足够强的磁场,使其磁导率趋于常数。
铁磁性钢管涡流检测的频率范围一般在1-500kHz 之间。
(一)检测方法穿过式线圈检测钢管,一般为多线圈结构,多线圈可以是分列式或初级线圈、双差动线圈等。
扁平放置式线圈检测,为线圈旋转钢管轴向移动的扫查方式,钢管旋转线圈轴向移动的扫查方式,使用这种方法时,钢管的外径没有限制。
(二)对比试样对比试样应与被检对象具有相同或相近规格、牌号、热处理状态、表面状态和电磁性能。
采用对比槽形试样时,槽的形状为纵向矩形槽,平行于钢管的主轴线。
槽的宽度≯1 .5mm ,长度为25mm ,其深度为管子公称壁厚的5 %,最小深度为0.3mm ,最大深度为1.3mm 。
涡流检测3

涡流检测
第二节 ET的阻抗分析法
一 检测线圈的阻抗分析 ㈠ 检测线圈阻抗 检测线圈—线圈1 试件—线圈2或次级线圈
涡流检测阻抗分析
涡流检测
试件(线圈2或次级线圈)中涡流方向与 线圈1(初级线圈或激磁线圈)电流方向相反
涡流检测阻抗分析
当交变的涡流作用 于线圈1时,会产生感 生电流,且方向与涡流 相反,与原电流方向相 同,使线圈1中电流增 加,这必然会引起阻抗 的变化
L2 )
R1 jX
式中:ω为交变电流频率;
2M 2
( R2 Rr ) L
2 2 2 2
( R2 Rr -j L2 )
为等效阻抗Ze
涡流检测阻抗分析
讨论: ① 当次级线圈开路,R2+Rr
涡流检测
∞(远离被
检对象),则空载阻抗Z=Z0=R1+jωL1 ② 当R2+Rr K2=M2/L1L2 0时,
涡流检测阻抗分析
涡流检测
2 圆柱体直径d:d改变时,将引起f / fg 和η的变化,使线圈阻抗变化 3 相对磁导率μr:μr变化,会影响
μeff而且对线圈阻抗影响与d相同
4 检测频率:频率变化,线圈阻抗变 化最佳的频率>特征频率fg若干倍
涡流检测阻抗分析
5 缺陷:先制成评价 缺陷:先制成评价 5 实际缺陷特征的类比图 实际缺陷特征的类比图 表。随裂纹宽、深比的 表。随裂纹宽、深比的 增加,线圈阻抗越来越 增加,线圈阻抗越来越 向 “ 直径效应 ” 方向变 向 “ 直径效应 ” 方向变 化。 “ 裂纹效应 ” 与 “ 直径 化。 “ 裂纹效应 ” 与 “ 直径 效应 ” 曲线之间的夹角越 效应 ” 曲线之间的夹角越 大,裂纹宽、深比越 大,裂纹宽、深比越 小,裂纹危害性越大 小,裂纹危害性越大
- 1、下载文档前请自行甄别文档内容的完整性,平台不提供额外的编辑、内容补充、找答案等附加服务。
- 2、"仅部分预览"的文档,不可在线预览部分如存在完整性等问题,可反馈申请退款(可完整预览的文档不适用该条件!)。
- 3、如文档侵犯您的权益,请联系客服反馈,我们会尽快为您处理(人工客服工作时间:9:00-18:30)。
热处理中的涡流及预多频检测技术
在大型汽车公司的大型热处理淬火车间中,传动系统用的齿轮零件连续进
行表面渗碳淬火,产量非常大。
在此之前,需要通过随机抽样,将零件切开、
抛光后在金相显微镜下检查淬硬层深度。
在通常条件下,每一个班次要抽取4 次,进行每次11 件的破坏性检测,因此每天总计要破坏零件132 件。
这种方法存在以下问题: 1.在热处理过程不好或失败的情况下,为了保证没有不合格
产品出库,需要增加进行破坏性检测的齿轮零件数量; 2.检测结果非实时,至
少需要等30min; 3.只有切开的零件才能100%确认是否合格; 4.检测的前提是假设同一批次工件的性能一致; 5.由于进行破坏性检测,因此解决问题的成
本高。
由以上问题可知,我们需要一种无损检测程序来提高硬度及淬硬层深
度检测的效率,而且这种方法仅需破坏非常少的零件。
用户应用了一种采用“PMFT(预防性多频技术)”的涡流检测系统。
安装了第一套齿轮零件检测系统后,用户又安装了两套系统,其中一套用于齿轮,另一套用于轴类检测。
无
损检测方法的经济性计算由文中表可看出,成本计算基于采用德国IBG 公司EDDYLINER P 涡流系统之后节省的金相检测劳动力成本、破坏性检测工件成本以及切割锯条的成本。
其他重要因素(如节省的耗材、延误的检测结果以及
增加的对可疑批次进行破坏性检测的成本)没有计算成本,仅作主观考虑。
无损检测系统的技术基础该无损检测系统的技术基础是IBG 公司发明的快速
多频涡流检测方法,一般称为“预防性多频检测”,简称为“PMFT”。
该系统的
优点如下:1.由于采用PMFT 预多频方法,系统非常可靠; 2.检测灵敏度高;
3.重复性好,标定件的测量值(如电压向量值等)可以进行长期保存;
4.检测设置简单,工厂的工人经过短期培训即可操作;
5.维护简单;
6.每个工件检测时间仅数秒钟,速度很快;
7.可为检测过的工件及标定工件建立文档;
8.当。