精益生产需要的各类表格及流程图 (2)
精益管理七大流程图生产现场课件
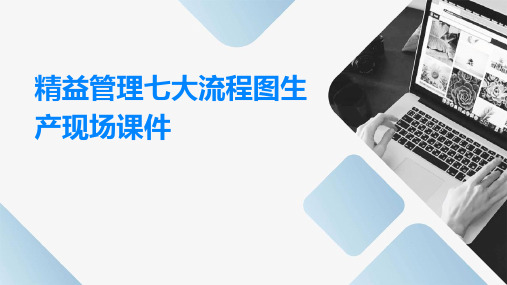
物料流程图能够帮助企业全面了解生产现场的物料流动情况 ,发现和改善物料管理中的问题,提高生产效率,降低成本 ,提升产品质量。
物料流程图的组成要素
设备
各种生产设备、搬 运设备等。
信息流
生产过程中的各种 信息,如计划、调 度、库存等。
物料
包括原料、半成品 、成品等在生产过 程中流动的物料。
人员
现场操作人员、管 理人员等。
对绘制好的流程图进行审核和 优化,确保流程图的准确性和 易读性。
现场信息管理提升措施
建设完善的信息管理系统, 实现信息的自动化采集、存 储、传递和处理,提高信息
处理效率。
1
加强现场信息的实时监控和 预警,及时发现和解决问题 ,避免信息流动中的瓶颈和
延误。
对现场管理人员进行信息管 理的培训和素质提升,提高 其对信息管理的重视度和能 力水平。
原则
精益管理基于五大原则,包括定义价 值、识别价值流、流动、拉动和追求 卓越。这些原则指导企业如何优化流 程、减少浪费,并持续改进。
精益思想与生产管理
以客户需求为导向
精益思想强调通过深入理解客户 需求,避免过度生产和库存积压
,使生产紧密围绕需求进行。
消除浪费
精益思想倡导不断识别和消除生产 过程中的浪费,如等待、运输、过 度加工、库存、不必要的动作等, 以提高效率。
促进持续改进
七大流程图是持续改进的 基础工具,企业可在此基 础上不断寻求提升,实现 精益管理的长远目标。
七大流程图的相互关系
互补关系
七大流程图各有侧重,但彼此之 间存在互补关系,综合运用能更 好地满足生产现场的管理需求。
流程衔接
七大流程图在生产过程中相互衔 接,形成一个完整的管理体系,
精益生产推行方案(伟创力经典内含很多表格)(共86张精选PPT)
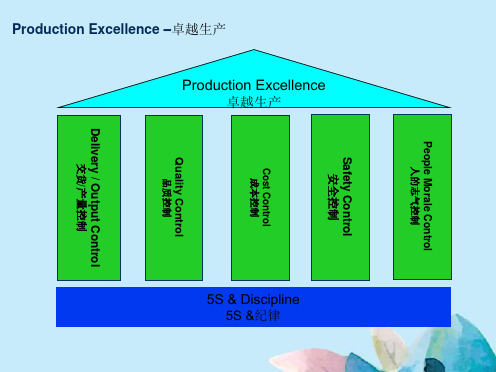
总是想如何能留住关键工位的有经验的员工?
沟通万岁!
精益生产概述
精益生产培训纲要
1 精益生产概述 2 价值和价值流
3 节拍时间生产
4 单件流与标准作业
5 拉动与看板
6 均衡与序列 7 精益工具与精益思想
Actions for Production Material Management (1)生产物料管理行动
Material in/out production floor control:物料进/出生产线控制
- No material out of production without approval from production manager or
要示所有的职员返还各种物料到生产线。
Production MaterБайду номын сангаасal Management/Control:生产物料管理/控制
- Follow up Kanban supermarket rule to pull materials to line. Less material in the
line, better material control;根据看板超市的规则拉物料至生产线,少的物料在生产线,好的物料控制
authorized person; 未经生产经理事授权人员批准的物料不得出生产线。 - Accurate production material in/out record 精确的生产物料进/出记录
(Request all staffs to return all kinds of materials to production floor!)
精益生产推进计划表

标准化 编写《精益指标体系》 完成项目总结报告 整理主要输出文件 制订后期拓展计划 项目评价和结束会议 5S与目视化管理 QC基本工具应用
培训 (计划内)
班组管理技能提升 详见精益培 标准作业与作业标准 训计划 基础工业工程-IE 全面生产维护-TPM 额外增加
XX电子精益生产 推行计划
21W
22W
23W
24W
25W
26W
27W
28W
29W
30W
31W
32W
33W
34W
35W
36W
37W
38W
39W
40W
41W
42W
43W
44W
45W
46W
47W
48W
49W
50W
51W
52W
53W
XX电子精益生产 推
阶段
项目 倡导者培训 精益生产基本理念 项目成立 精益小组团队组建 精益小组项目启动会议 核心指标设立 指标基线测定 初级及革新目标设定 项目监控 绩效管控 项目进度目视管理板 精益活动月报及例会管理 精益变革过程中管控注意事项 精益改善绩效管理办法制定 现场三定5S活动开展 3定5S标准的建立 制定目视管理基准 现场基础改 建立班组活动园地 善 快速反应质量控制 改善提案活动导入 地标线的标准 车间环境优化 -工序能力时间测量 -现状Layout图 -工序能力平衡分析 -产品批量分析 -全品种作业转换时间测量 -最佳生产模式研讨 设计新的线体布局方案 -确定生产节拍TT -提出布局草案 -计算标准人力 -标准作业组合 -操作平衡分析 -员工多技能评估矩阵 -工位器具标准化 -标准手持设定 -物流供应方案 -方案约束事项检讨及对策
精益生产之分层法、调查表、排列图、鱼骨图ppt课件

P11
SIX SIGMA
⑴ 什么叫鱼骨图
鱼骨图
鱼骨图是[把认为是问题的特性(结果)和给于其影响 的要因(原因)间的关系系统地综合成的鱼骨形状的图]
大骨
小骨 孙骨
中骨
主要原 因
① 最重要的是特性要用结果体系来表示 ② 为了解析要因,将作为原因的要因一直细分到大骨、中骨、小骨、 孙骨
累积 累 不良 积 件数 比
率
33 36.5% 51 56.0 63 69.2 73 80.2 78 85.7 83 91.0
91 100.0
100.0% P10
SIX排S列IG图MA
⑵ 排列图的读解与使用方法
【读解方法】
排列图可以提供如下多种信息: • 不良、失误等的总数有多少? • 它们的大小顺序是如何分布的? • 如果能够在多大程度上减少其中的哪一件,可望在总体上收到多大的效果?
把特性写在右侧,加上方框 “ 画一条带箭头的粗线,称这为椎骨
”;然后从左往右
步骤3
写出构成大骨的原因
从影响特性的各种要因中,找出涵盖面较大的要因,将其 填入大骨。若代表大骨的特性与物品有关,较简便的归纳方法 是列举出4M(作业人员、机械、材料、作业方法)。除此这外, 还可加上测定、环境等因素。将不同的工序(如粗加工、前加 工、后加工等)八成 大骨,也是可以的
螺丝松动
33
距离计积尘
12
外表划伤
18
焊接不良
5
连接不良
10
动作不良
5
间隙不良
3
部件摔落 外表污迹 计 检查合计
2037
不良率
3
2 91
精益生产流程图-CHY(与“过程”相关共33张)

供应商
输入
过程
Start
过程流程图
输出
客户
CTQs
2. 指CTQ确定主要输出,由谁接收的客户,及客户CTQs
输出用名词(例销售电话,建议) 用形容词(例及时的、有识的,正确的)
3. 用头脑风暴确定过程步骤 大字
不要试着理顺序
不要讨论详细的过程步骤
4. 用头脑风暴确定影响过程质量的关键输入 5. 对于每个关键输入,确定“供应商”由谁提供
过程流程图
• 次品 • 库存
• 不必要的过程
7 种浪费/无价值增长的活动
• 等待
• 过量生产 • 转移或运输 • 不必要的动作
浪费是无价值的,只会增加成本及周期
g GEIS SJV 精益生产教材
RE‘的 头脑风暴
过程流程图
带有前缀”RE”的动词
Rework返工
Repeat反复
Reship重装运 Reissue重发货 Rewrite重写
一些基本步骤
定义需提高的过程或服务
- 被分析的过程的开始及结束取得一致意见
使用头脑风暴确定过程步骤
显示流程顺序
- 注意不漏掉基本的或不同的分支
- 在流程中与供应商及客户交流
将流程图改变至与真实流程相符合
流程评估: 目的是什么? 从哪里做起?
什么时候做?
由谁来做?
? 如何做?
是必须的?
为何从这里做起?
定义
过程流程图
价值增长的活动
-- 原材料转移或成形或达到客户要求的任何活动
无价值增长的活动
– 准备时间、资源或空间准备、但对产品本身 并不带来任何价值的那些活动
g GEIS SJV 精益生产教材
生产周期
精益生产全套表格
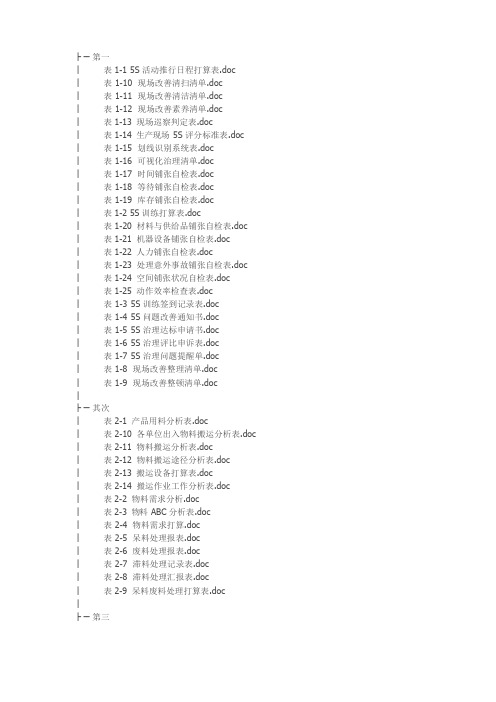
├─第一│表1-1 5S 活动推行日程打算表.doc│表1-10 现场改善清扫清单.doc│表1-11 现场改善清洁清单.doc│表1-12 现场改善素养清单.doc│表1-13 现场巡察判定表.doc│表1-14 生产现场5S 评分标准表.doc │表1-15 划线识别系统表.doc│表1-16 可视化治理清单.doc│表1-17 时间铺张自检表.doc│表1-18 等待铺张自检表.doc│表1-19 库存铺张自检表.doc│表1-2 5S 训练打算表.doc│表1-20 材料与供给品铺张自检表.doc │表1-21 机器设备铺张自检表.doc│表1-22 人力铺张自检表.doc│表1-23 处理意外事故铺张自检表.doc │表1-24 空间铺张状况自检表.doc│表1-25 动作效率检查表.doc│表1-3 5S 训练签到记录表.doc│表1-4 5S 问题改善通知书.doc│表1-5 5S 治理达标申请书.doc│表1-6 5S 治理评比申诉表.doc│表1-7 5S 治理问题提醒单.doc│表1-8 现场改善整理清单.doc│表1-9 现场改善整顿清单.doc│├─其次│表2-1 产品用料分析表.doc│表2-10 各单位出入物料搬运分析表.doc │表2-11 物料搬运分析表.doc│表2-12 物料搬运途径分析表.doc│表2-13 搬运设备打算表.doc│表2-14 搬运作业工作分析表.doc│表2-2 物料需求分析.doc│表2-3 物料ABC 分析表.doc│表2-4 物料需求打算.doc│表2-5 呆料处理报表.doc│表2-6 废料处理报表.doc│表2-7 滞料处理记录表.doc│表2-8 滞料处理汇报表.doc│表2-9 呆料废料处理打算表.doc│├─第三│表3-1 TPM 改善打算.doc│表3-10 改善事例记录.doc│表3-11 简易型提案格式.doc│表3-12 一般型提案格式.doc│表3-13 设备不正常点分析.doc│表3-14 发电机开机前点检表.doc│表3-15 发电机运行中点检表.doc│表3-16 发电机〔房〕周期点检表.doc│表3-17 抱负工厂评价表单.doc│表3-18 TPM 提案评价表.doc│表3-19 TPM 娴熟度评价.doc│表3-2 TPM 推动人员推举表.doc│表3-20 设备综合效率水平评价表.doc│表3-21 设备保修水平自我评价.doc│表3-3 设备自主保全诊断表.doc│表3-4 组装自主保全诊断表.doc│表3-5 自主保全诊断表〔仓库、放置场所〕.doc │表3-6 全员诊断申请书.doc│表3-7 物品报废及处理申请表.doc│表3-8 自主保全活动报告书.doc│表3-9 TPM 会议记录.doc│└─第四表4-1 月份质量问题分析表.doc表4-10 检验托付单.doc表4-11 进厂零件质量检验表.doc表4-12 零件检验报告表.doc表4-13 材料检验报告表.doc表4-14 材料试用检验通知单.doc表4-15 进厂检验状况每日报表.doc表4-16 说明书质量检验表.doc表4-17 设备验收单.doc表4-18 特采、让步使用申请单.doc表4-19 退货单.doc表4-2 年度质量问题统计表.doc表4-20 供货商质量统计表.doc表4-21 供给商质量评价表.doc表4-22 供给商质量治理检查表.doc表4-23 供给商根本资料表.doc表4-24 供给商考核表.doc表4-25 供给商现场评审表.doc表4-26 供给商综合评审表.doc表4-27 合格供给商名单.doc表4-28 质量预防费用统计表.doc表4-29 质量鉴定费用统计表.doc表4-3 质量教育年度打算表.doc表4-30 质量内部故障统计表.doc表4-31 质量外部故障统计表.doc表4-32 质量本钱统计报表.doc表4-33 质量本钱统计报表补充资料.doc表4-34 产品质量本钱损失估量表.doc表4-35 质量改进费用汇总表.doc表4-36 取消订单损失报告表.doc表4-37 质量会议工资费用计算表.doc表4-38 质量培训费用计算表.doc表4-39 质量嘉奖费用计算表.doc表4-4 质量教育长期打算表.doc表4-40 不行修复废品损失计算表.doc表4-41 可修复废品损失计算表.doc表4-42 产品质量停工报告表.doc表4-43 质量事故处理费用计算表.doc表4-44 产品降级、降价处理损失报告表.doc表4-45 间接质量费用安排表.doc表4-46 车间质量治理费用月报.doc表4-47 车间质量损失费用月报表.doc表4-48 主要产品单位质量本钱表.doc表4-49 产品质量改进记录表.doc表4-5 本企业产品与竞争对手产品质量比较表.doc表4-50 产品质量改进分析表.doc表4-51 质量因素改善结果记录表.doc表4-6 质量治理小组活动报告表.doc表4-7 质量治理小组会议报告表.doc表4-8 质量治理小组活动成果报告表.doc表4-9 质量治理小组活动企业大会用表.doc│├─第五│表5-1 生产效率记录表.doc│表5-10 标准作业时间争论.doc│表5-11 标准作业时间核定.doc│表5-12 标准作业时间测定.doc│表5-13 流水线工序平衡测定表.doc│表5-14 流水线瓶颈工序分析表.doc│表5-15 流水线非平衡工序分析与改善表.doc│表5-16 流水线各工序动作分析、改善表.doc│表5-17 流水线各工序操作规程指导表.doc│表5-18 流水线关心工装及标识使用考察表.doc │表5-2 设备利用率分析表.doc│表5-3 生产效率不佳缘由分析表.doc│表5-4 生产作业改善打算表.doc│表5-5 生产作业改进建议报告.doc│表5-6 生产作业流程程序图.doc│表5-7 生产作业流程分析.doc│表5-8 人机协作分析表.doc│表5-9 生产时间争论记录表.doc│├─第六│表6-1 工厂设置安全检查表.doc│表6-10 电气安全检查表.doc│表6-11 锅炉安全检查表.doc│表6-12 管线和阀门安全检查表.doc│表6-13 带压及真空排放安全检查表.doc │表6-14 机械安装安全检查表.doc│表6-15 操作安全治理检查表.doc│表6-16 防灾设施安全检查表.doc│表6-17 安全嘉奖通知.doc│表6-18 安全罚款通知.doc│表6-19 分厂安全考核用表.doc│表6-2 工厂平面布置安全检查表.doc│表6-20 打算部门安全考核表.doc│表6-21 企管部门安全考核表.doc│表6-22 生产调度部门安全考核表.doc │表6-23 设备工具部门安全考核表.doc │表6-24 动力部门安全考核表.doc│表6-25 产品设计部门安全考核表.doc │表6-26 安保部门安全考核表.doc│表6-27 人事部门安全考核表.doc│表6-28 工艺部门安全考核表.doc│表6-29 物资治理部门安全考核表.doc │表6-3 建筑标准安全检查表.doc│表6-30 后勤部门安全考核表.doc│表6-4 车间环境安全检查表.doc│表6-5 厂内运输安全检查表.doc│表6-6 原、材、燃料安全检查表.doc│表6-7 工艺操作安全检查表.doc│表6-8 生产设备安全检查表.doc│表6-9 仪表治理安全检查表.doc。
5S管理流程含图(卓越生产)

5S管理流程图生产车间包装车间品管部仓库组后勤财务人事作业内容拟定5S推行计划并实施组织各部门主管组成5S管理小组定期对员工进行5S培训5S管理小组依据5S推行计划定期对现场进行稽查汇总稽查结果将所有区域5S缺点汇总并采取相应改进措施由过程总负责人进行改进有效性跟踪(下次检查将上次5S缺点部分进行重点稽查)将5S相关资料存档使用表单5S详细计划流程表培训PPT,培训考核表5S现场考核表5S现场缺点(含图片,详细地点,改进措施、限期时间、责任人)图片资料,5S推行计划计划拟定计划建立5S管理小组宣导5S内容(进行5S培训现场稽查缺点汇总改进措施验证确认检查核实记录保存5S检查实施细则1、每周定时定点(如:每周五10:30-11:20)对所有厂区进行5S检查,由过程总负责人组织各部门主管在会议室集合进行分工(区域分工或项目分工);2、对厂区进行5S检查,过程中发现问题及时指出并现场告知区域负责人并给出整改建议和期望达成效果,由记录员做图片文字记录;3、检查完成后集合会议室对本次检查中发现的问题做总结;4、由记录员在当天将图片文字通过纸质档发到相应负责人手中;5、在下周5S检查中对上周5S缺点进行分工核实改进情况并检查新出现5S缺点,检查结束后对针对为改进点对相应区域负责人扣除对应绩效分数。
6、将稽查图片和文字用PPT形式保存。
例1:5S例2:安全。
精益七大任务流程图

点检的实施率 ·根据计划表实施的点检 ·4S·设备清扫· 给油·螺栓 紧固 等
TPS·少人化·生产周 期 ·均衡化·库存削减 T等PM 频发突发停机 时间、次数 长时间停机削减活动
看板检查表
设备停机(频发、长 时间)状况表
自主保全计划 各工序设备挂牌、取 牌状况表
设备停机时的 对应手册
管理监督者手册等
•不良情况联络书集
•工序诊断检查表 •问题对策一览表 •活动记录存根 •质量改善计划表
•个人机能评价表 •个人成长表 •个人能力提高表
3、案例分享(生产)
目的
结果指标
活动内容
活动指标
活动手段
准时化 生产
保证产 量
可动率
可动率 (GSPS)
产量完成率 (SPH)
在丰田
维持活动
TPS
标准作业的遵守
各级别教育、TPS教育表
4、案例分享(设备)
目的
结果指标
活动内容
必要的 时候开 动设备
《代表指标KPI》 ·可动率
(每台的故障次 数) (故障时间)
辅助KPI ·MTBI ·MTTR
维持活动
固定业务
日常保养 法定点检 备用件把握
活动指标
日常点检实施情况 法定点检实施情况
备用件库存情况
活动手段
日常点检一览表 法定点检表
成本改善计划表
在丰田
人才育成
培养能够清楚人才 体系和将其推进的 人才
去成本核算小组 实际操作成本体 系和推进方法
参与机构会议的策划培训 等
4、案例分享(人事)
目的
结果指标
活动内容
活动指标
培养、 活用人 才
精益七大任务(流程图)课件

整理、整顿、清扫、清洁、素养,提高现场 管理水平和效率。
通过可视化手段,使管理过程更加直观和便 捷。
制定标准操作流程,规范员工操作,提高工 作效率。
减少换模时间,提高生产效率。
通过设计或采用防错装置,避免生产中出业通过采用精益生产方式,优化生产线布局,减少生产过程中的浪费,实现了生产效率 的提高和成本的降低。
提升员工满意度
通过关注员工需求和工 作条件,提高员工满意 度和工作积极性。
促进企业可持续发展
通过精益生产,实现企 业可持续发展,保持竞 争优势。
精益生产原则
价值导向
以客户需求为导向,将客户的价值需求转化 为企业内部的生产要求。
标准化作业
流动化作业
通过优化生产流程,实现生产过程的连续性 和高效性。
通过标准化作业,提高生产效率和产品质量。
标准化作业实施步骤
分析现状
对生产现场的作业情况进行全面的了解和 分析,找出存在的问题和瓶颈。
评估效果
对标准化作业的实施效果进行评估,发现 问题并及时进行调整和改进。
制定标准
根据分析结果,制定出相应的作业标准, 包括作业人员、作业顺序、作业方法、作 业时间、检验手段和安全注意事项等。
实施推行
在生产现场实施新的作业标准,并进行持 续的监督和改进。
VS
详细描述
JIT生产方式强调在必要的时间和地点, 仅生产必要数量的产品,以满足客户需求。 通过减少浪费、提高生产效率和产品质量, JIT生产方式可以帮助企业实现可持续发 展和提高竞争力。
谢谢聆听
明确要分析的产品族,确保其具 有相似的工艺、生产过程和价值流。
制定改进措施
基于分析结果,制定针对性的改 进措施,如优化工艺流程、减少 库存等。
生产中使用的各种表格

生产中使用的各种表格
生产中使用的表格种类很多,以下是一些常见的生产表格:
1.生产计划表:用于安排生产计划,包括产品名称、数量、生产日
期等信息。
2.物料需求计划表:根据生产计划表,计算出所需物料种类、数量、
采购时间等信息。
3.生产进度表:记录生产进度,包括各工序的完成情况、生产数量、
生产日期等信息。
4.质量控制表:用于记录产品质量检测数据,包括检测项目、标准
值、实际值、判定结果等信息。
5.设备维护表:记录设备的维护情况,包括设备名称、维护时间、
维护内容等信息。
6.人员考勤表:记录生产人员的考勤情况,包括姓名、出勤时间、
工作内容等信息。
7.生产日报表:汇总当日的生产情况,包括生产计划完成情况、设
备运行情况、质量问题等信息。
8.不良品处理表:记录不良品的处理情况,包括不良品数量、原因、
处理措施等信息。
9.工艺流程表:详细描述产品的生产工艺流程,包括各工序的操作
方法、设备要求、检测标准等信息。
10.产品BOM表:列出产品所需的物料清单,包括物料名称、规格型
号、数量等信息。
以上表格可以根据实际需要进行调整和修改,以满足生产管理的需要。
绘制状态流程图精益生产【共24张PPT】

三、理想的未来状态流程图
• 2.理想的未来状态流程图
顾客的声 音
流回路中 的先导者
价值流中 的先导者
均衡化的生产日报表
生产控制部门
供应商
流程
流程
流程
流程
流回路顾
拉动
流
客
拉动
流
客户
价值流顾 客
流回路
价值流
流回路
• 练习题:
• 1. 什么是价值流?(30分) • • 2. 精益生产流程有什么特征?(30分)
价值流经理是负责主持精益活动研讨会的理 想人选.
一、基础知识
• 5.使用绘图工具 • 绘制价值流图的工具很简单,只需一支笔和一张纸.顺着物料和信息
• 的流程收集关键数据,并进行分析,就可绘制出价值流图. • 绘制出价值流图很重要的原则是在现场,一直在用铅笔画图,最后再 • 画正式图.画正式图时,仍然便用铅笔.铅笔绘制意味着可以随时可以 • 修改,也代表着绘图人员不将心力放在电脑上,而是在现场进行随时 • 可修正的真实数据与现况观察.
一、基础知识
• 价值流图示例``
一、基础知识
• 2.价值流图作用 • A.价值流图是一个很有用的一项精益工具,从图
中可凸显流程中的浪费. B.可以帮助我们看出相互连接的流程链,并展望
未来精益价值流. C.方便拟出详细的改善行动计划. D. 使所有人了解整个流程,从而有共同的目标。
一、基础知识
• 3. 价值流图与生产流程图的区别
的声音。
法,可能是•一张卡片,一致个下腾空游的空工间序或一存部货车.增加.
“价值流图”(value
• 信息流予以简化。
stream要ma使ppin得g). 价值流“精益”,必须抑制过量生产.
制衣厂精益生产全流程图
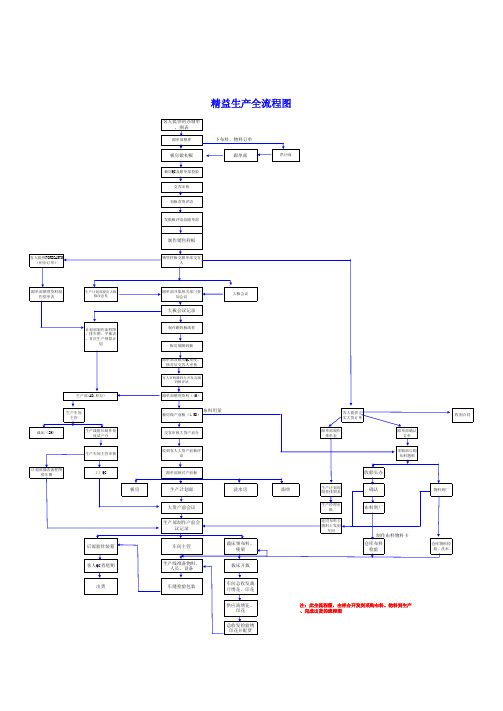
布料用量
板房做产前板(4.5D)
交客审核大货产前办
收到客人大货产前板评 语
跟单部核对产前板
生产计划部
大货产前会议 生产部制作产前会
议记录
车间主管
生产线准备物料、 人员、设备
车缝检验包装
洗水房
裁床领布料、 唛架
裁床开裁 车间总收发裁 片绣花、印花 供应商绣花、
印花 总收发检验绣
印花并配货
划
生产部(AD.样办)
生产车间 主管
裁床(2H)
生产线组长制作量 度试产办
计划部修改流程图 排车图
生产车间主管审核
工厂QC
板房
后部验针装箱 客人QC查尾期
出货ห้องสมุดไป่ตู้
跟单部召集相关部门参 加会议
大板会议记录
大板会议
制作跳码板纸样
板房做跳码板
跟单部及板房QC量度、 核对后交客人审核
客人审核跳码办并发出跳 码板评语
客人提供FORECASTS (初步订单)
精益生产全流程图
客人提供初办制单 、图表
跟单部整理
板房做初板
板房QC及跟单部检验 交客审核
初板查货评语
下布料、物料订单 跟单部
供应商
发批板评语给跟单部
制作销售样板
销售样板交跟单部交客 人
跟单部整理资料制 作排单表
生产计划部提出大板 修改意见
计划部制作流程图 、排车图、平衡表 、首次生产预算计
跟单
客人提供正 实大货订单
跟单部制作 排单表
跟单部确认 订单
采购部订购 布料物料
生产计划部 制作排期表
生产经理审 批
连同布料卡 物料卡发到
生产工厂流程图WPS文字 文档
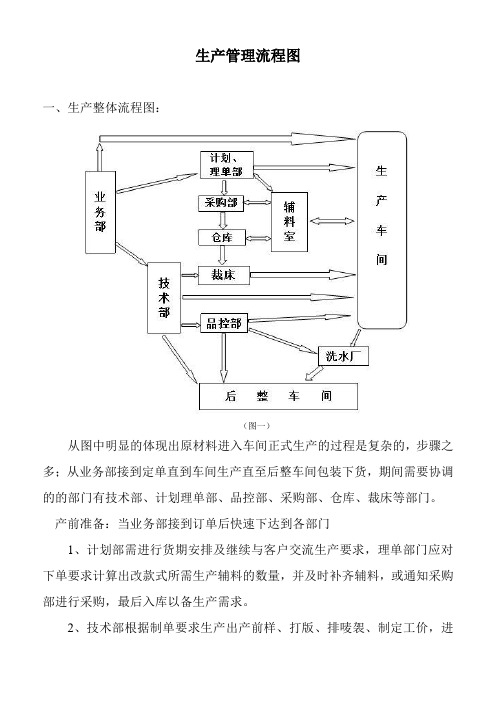
生产管理流程图一、生产整体流程图:(图一)从图中明显的体现出原材料进入车间正式生产的过程是复杂的,步骤之多;从业务部接到定单直到车间生产直至后整车间包装下货,期间需要协调的的部门有技术部、计划理单部、品控部、采购部、仓库、裁床等部门。
产前准备:当业务部接到订单后快速下达到各部门1、计划部需进行货期安排及继续与客户交流生产要求,理单部门应对下单要求计算出改款式所需生产辅料的数量,并及时补齐辅料,或通知采购部进行采购,最后入库以备生产需求。
2、技术部根据制单要求生产出产前样、打版、排唛袈、制定工价,进行技术分解,发放制单及样裤到相应部门,在生产过程中起技术、质量监督。
3、裁床为车间提供生产原材料,也就是说是车间生产的质量第一关,为防止生产过程中出现裁片大小不一、遗漏或丢失、缩水、色差等问题,裁床接到制单后,应依严格据制单要求,到仓库认领生产原材料;开裁时应根据制单要求松布时间松布,唛袈要求裁剪大小;编号、绑票应清晰明了;送去绣、印花要及时并严格要求期间所用时间,以免影响整体生产进度;验片员应严格要求,验片过程中应如有出现问题应及时提出来;裁片交接员定要轻点交接裁片数量并做记录。
4、辅料室接到制单时,应及时到仓库领好生产所需辅料做好产前准备,跟踪车间生产辅料需求,做好记录,应配合理单部、仓库及时上报或领取辅料,尽量避免应辅料欠缺从而导致车间停产货期延误。
5、品控部,从布料进仓验布—裁床—车间生产—洗水厂—后整车间,对生产质量的监督起的重大的作用,布料质量的把控,生产过程中质量的把控,成品抽检,洗水跟踪,成品进仓,环环相扣;召开产前会议的重要性,根据制单要求,对样裤技术分析,生产细节要求,对各组产前样的检验;为加强生产质量的提高,应定期召开各组检验员会议或培训以加强提高检验员的素质、技能,了解质量对生产的重要性,为生产的第一要素,能更好的把控质量;为更好的加强提高生产质量,品控部所产开的质量评比应秉着公开、公正、公平的原则,多方面的评比,出现问题应及时指出并纠正,奖惩分明,有效的提高了生产质量。