汽车框架式车身焊接变形的控制措施
汽车车架焊接过程焊接变形控制方法
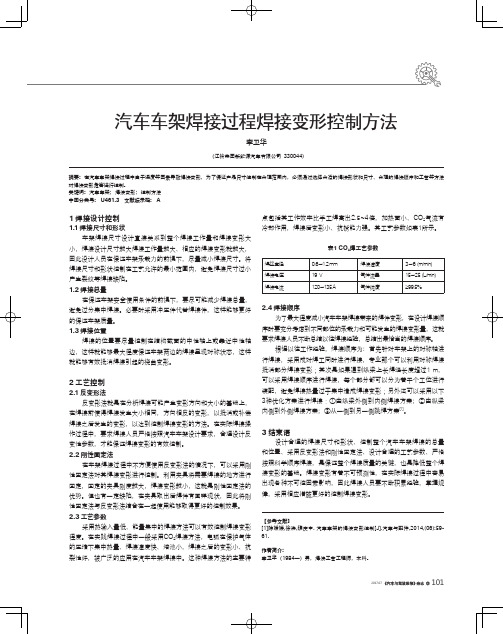
焊接的位置要尽量控制在结构截面的中性轴上或靠近中性轴 边,这样就能够最大程度保证车架两边的焊接呈现对称状态,这样 就能够有效抵消焊接引起的挠曲变形。
语
设计合理的焊接尺寸和形状、控制整个汽车车架焊接的总量 和位置、采用反变形法和刚性固定法、设计合理的工艺参数、严格 按照科学顺序焊接,是保证整个焊接质量的关键,也是降低整个焊 接变形的基础。焊接变形有着不可预测性,在实际焊接过程中容易 出现各种不可控因素影响,因此焊接人员要不断积累经验,掌握规 律,采用相应措施更好的控制焊接变形。
【参考文献】 [1]陈嫒媛,徐浩,魏庆丰. 汽车车架的焊接变形控制[J].汽车与配件,2014,(06):5961.
作者简介: 李卫华(1984—)男,焊接工艺工程师,本科。
2017.07
101
反变形法就是在分析焊接可能产生变形方向和大小的基础上, 在焊接前使得焊接发生大小相同,方向相反的变形,以抵消或补偿 焊接之后发生的变形,以达到控制焊接变形的方法。在实际焊接操 作过程中,要求焊接人员严格按照汽车车架设计要求,合理设计反 变性参数,才能保证焊接变形的有效控制。 2.2 刚性固定法
在车架焊接过程中不方便使用反变形法的情况下,可以采用刚 性固定法对其焊接变形进行控制。利用夹具将需要焊接的地方进行 固定,固定的夹具刚度越大,焊接变形越小,这就是刚性固定法的 优势。但也有一定缺陷,在夹具取出后焊件有回弹现状,因此将刚 性固定法与反变形法结合在一起使用能够取得更好的控制效果。 2.3 工艺参数
1 焊接设计控制 1.1 焊接尺寸和形状
车架焊接尺寸设计直接关系到整个焊接工作量和焊接变形大 小,焊接设计尺寸越大焊接工作量越大、相应的焊接变形就越大, 因此设计人员在保证车架承载力的前提下,尽量减小焊接尺寸。将 焊接尺寸和形状控制在工艺允许的最小范围内,避免焊接尺寸过小 产生裂纹等焊接缺陷。 1.2 焊接总量
铝合金框架车身弧焊焊接应力变形的控制

汽车轻量化 | Auto Lightweight铝合金框架车身弧焊焊接应力变形的控制□奇瑞新能源汽车技术有限公司 / 吴发贵本文主要分析了铝合金框架车身弧焊焊接变形产生的原因,并针对如何有效控制焊接应力变形提出了控制措施。
在没有外力作用的条件下,焊接应力在焊件内部是平衡的。
焊接过程中产生焊接应力和变形的根本原因,是不均匀温度场以及由它引起的局部塑性变形和比热容不同的组织。
当焊接引起的不均匀温度场尚未消失时,所产生的应力和变形称为瞬态焊接应力和变形;焊接温度场消失后的应力和变形称为残余焊接应力和变形。
在以铝合金型材为主的铝合金框架车身的焊接过程中,由于焊接应力与变形引起的焊件形状和尺寸变化,带来产品的连接质量、几何尺寸精度、功能以及生产效率造成的影响比其他行业要大的多,因此,焊接应力变形是车身及其零部件设计和制造中需要重点考虑的问题。
形成原因焊接应力变形,是由多种因素交互作用形成。
在不考虑外部约束的情况下,焊接应力变形产生的机理可表述为:焊接热源引起材料不均匀的局部热过程,局部加热使焊接区域形成熔池,而熔池周边的高温区材料热膨胀受到周围材料的限制,产生不均匀的压缩塑性变形。
冷却过程中,已发生压缩塑性变形的这部分材料,受到周围材料的约束,不能自由收缩,在不同程度上又被拉伸和卸载。
与此同时,熔池凝固收缩时也产生相应的应力与变形;厚度方向的内部相比表面的冷却慢,或经过多次的焊接热过程,形成的残余应力与变形。
焊接应力的分布和大小受焊接方法、工艺参数、焊接结构、焊接材料、约束条件、焊接前后处理等因素的影响而变化。
控制措施下面讨论一下铝合金框架车身弧焊焊接变形的控制。
1. 通过工艺优化设计控制(1)合理拆序铝合金框架车身的结构主要是以铝型材件为主体构成框架,外部覆盖铝板材件形成完整的车身骨架总成。
在工艺设计工序拆分阶段,在节拍允许的前提下,将车身骨架上各零件在空间上进行分散、对称布置;相邻零件分序间隔布置(见图1)。
汽车车架焊接变形及控制方法
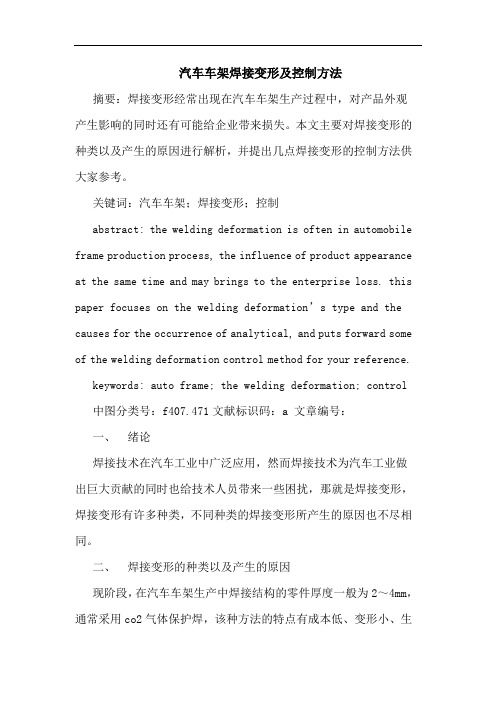
汽车车架焊接变形及控制方法摘要:焊接变形经常出现在汽车车架生产过程中,对产品外观产生影响的同时还有可能给企业带来损失。
本文主要对焊接变形的种类以及产生的原因进行解析,并提出几点焊接变形的控制方法供大家参考。
关键词:汽车车架;焊接变形;控制abstract: the welding deformation is often in automobile frame production process, the influence of product appearance at the same time and may brings to the enterprise loss. this paper focuses on the welding deformation’s type and the causes for the occurrence of analytical, and puts forward some of the welding deformation control method for your reference.keywords: auto frame; the welding deformation; control 中图分类号:f407.471文献标识码:a 文章编号:一、绪论焊接技术在汽车工业中广泛应用,然而焊接技术为汽车工业做出巨大贡献的同时也给技术人员带来一些困扰,那就是焊接变形,焊接变形有许多种类,不同种类的焊接变形所产生的原因也不尽相同。
二、焊接变形的种类以及产生的原因现阶段,在汽车车架生产中焊接结构的零件厚度一般为2~4mm,通常采用co2气体保护焊,该种方法的特点有成本低、变形小、生产效率高、抗锈、易操作、焊后不清渣、抗氢和抗裂纹能力强、适合全位置焊及易于实现焊接过程的机械化及自动化等。
所以,co2气体保护焊被广泛应用于汽车车架的焊接中。
此外,co2气体保护焊的热量较为集中、热影响去较窄,但是因为母材较薄且焊缝较多,其焊接变形比汽车车身薄板点焊要大。
汽车制造中的焊接变形成因及防治方法研究

汽车制造中的焊接变形成因及防治方法研究摘要:焊接技术是汽车制造行业中的主要技术之一,由于该技术的应用过程中会受到一定因素的相应,导致焊接变形现象的出现,从而对汽车制造质量产生不良影响。
如何有效管控焊接变形现象成为研究的重点,本文对焊接变形的原因以及防治方法展开全面探究。
关键词:汽车制造行业;焊接变形;产生原因;防治方法前言:对焊接技术来讲,其具有工艺简单、效率高、成本低以及精准可靠等特征,所以被广泛应用于汽车制造行业领域。
但是其在应用时,会受到收缩或应力的作用,导致焊接变形现象的出现。
在汽车制造过程中,焊接变形的合理管控是重中之重,所以要采取一定的方法来防治焊接变形现象,本文从以下方面来进行阐述。
1、汽车制造中焊接变形的原因1.1工艺流程缺乏合理性在焊接汽车车身时,特别容易出现长度较长的焊接缝。
这些焊接缝能够分布在车身的各个部位,在焊接这些焊接缝时,若工艺流程缺乏合理性,就会导致焊接变形现象的出现。
例如,当处在焊缝布局缺乏对称性的状况下,则会不断缩短相应的生产线性,从而使得焊接缝出现明显的弯曲变形。
除此之外,若焊接缝截面重心与接头截面重心无法保持重合时,则会在焊接位置处发生角变形现象。
由此可知,伴随着车架上焊接缝数量的不断增加,出现焊接变形的概率也会随之提高。
1.2工装定位可靠性不足在焊接车身时,通常将工装定位的方式应用于绝大部分的焊接位置。
当工装刚性和定位要求之间无法保持一致性时,则会大幅度削弱定位效果,从而在外力的作用下,使得车身出现变形现象。
当出现焊接过程中,这些变形表现尚不明显,但是当焊接位置的温度恢复正常之火,变形现象会更加的明显。
1.3焊接操作不规范在进行车身焊接时,焊接操作的规范性会直接影响焊接质量。
当焊接人员在实际工作中,并未对焊接参数进行严格执行,也会导致焊接变形现象的出现。
通常会对焊接质量产生影响的参数主要包括输入电流、焊条直径以及焊接速度等。
在焊接过程中,如果输入电流相对较大、应用的焊条过粗,以及焊接速度相对较慢,这些都会引发焊接变形现象的出现。
汽车副车架焊接变形及控制方法
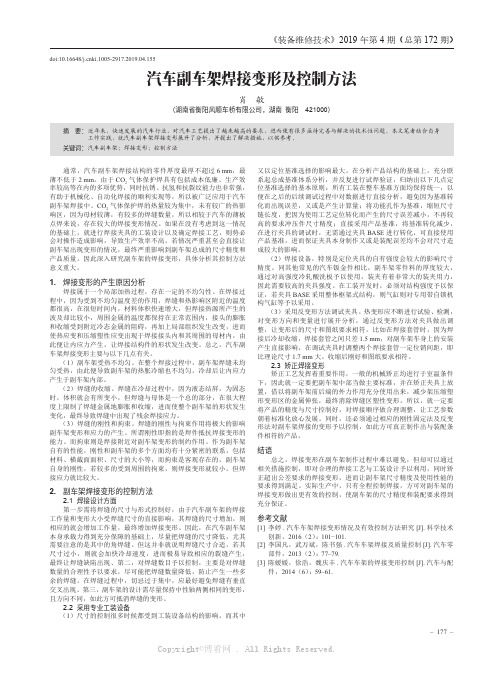
– 177 –《装备维修技术》2019年第4期(总第172期)doi:10.16648/ki.1005-2917.2019.04.155汽车副车架焊接变形及控制方法肖敏(湖南省衡阳风顺车桥有限公司,湖南 衡阳 421000)摘要: 近年来,快速发展的汽车行业,对汽车工艺提出了越来越高的要求,进而便有很多亟待完善与解决的技术性问题。
本文笔者结合自身工作实践,就汽车副车架焊接变形展开了分析,并提出了解决措施,以供参考。
关键词: 汽车副车架;焊接变形;控制方法通常,汽车副车架焊接结构的零件厚度最厚不超过6mm ,最薄不低于2mm 。
由于CO 2气体保护焊具有包括成本低廉、生产效率较高等在内的多项优势,同时抗锈、抗氢和抗裂纹能力也非常强,有助于机械化、自动化焊接的顺利实现等,所以被广泛应用于汽车副车架焊接中。
CO 2气体保护焊的热量较为集中,未有较广的热影响区,因为母材较薄,有较多的焊缝数量,所以相较于汽车的薄板点焊来说,存在较大的焊接变形情况。
如果在没有考虑到这一情况的基础上,就进行焊接夹具的工装设计以及确定焊接工艺,则势必会对操作造成影响,导致生产效率不高,若情况严重甚至会直接让副车架出现变形的情况,最终严重影响到副车架总成的尺寸精度和产品质量。
因此深入研究副车架的焊接变形,具体分析其控制方法意义重大。
1. 焊接变形的产生原因分析焊接属于一个局部加热过程,存在一定的不均匀性。
在焊接过程中,因为受到不均匀温度差的作用,焊缝和热影响区附近的温度都很高,在很短时间内,材料体积快速增大,但焊接热源所产生的波及却比较小,周围金属的温度都保持在正常范围内,接头的膨胀和收缩受到附近冷态金属的阻碍,再加上局部组织发生改变,进而使热应变和压缩塑性应变出现于焊接接头内和其周围的母材内,由此便让内应力产生,让焊接结构件的形状发生改变。
总之,汽车副车架焊接变形主要与以下几点有关。
(1)副车架受热不均匀。
在整个焊接过程中,副车架焊缝未均匀受热,由此便导致副车架的热胀冷缩也不均匀,冷却后让内应力产生于副车架内部。
减少焊接接应力和焊接变形的措施
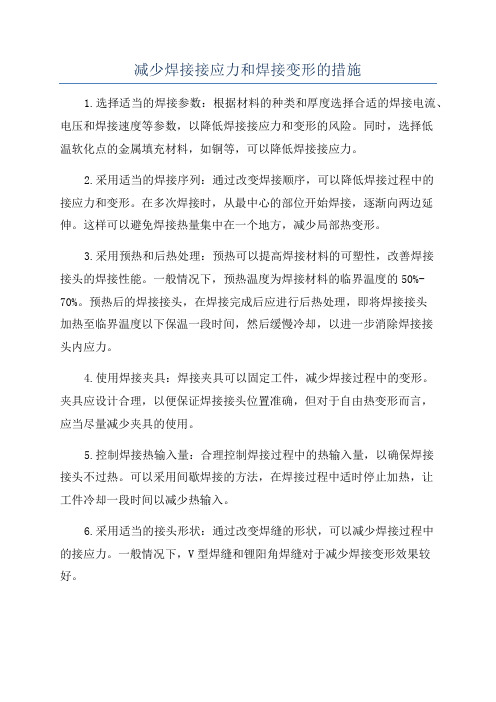
减少焊接接应力和焊接变形的措施1.选择适当的焊接参数:根据材料的种类和厚度选择合适的焊接电流、电压和焊接速度等参数,以降低焊接接应力和变形的风险。
同时,选择低温软化点的金属填充材料,如铜等,可以降低焊接接应力。
2.采用适当的焊接序列:通过改变焊接顺序,可以降低焊接过程中的接应力和变形。
在多次焊接时,从最中心的部位开始焊接,逐渐向两边延伸。
这样可以避免焊接热量集中在一个地方,减少局部热变形。
3.采用预热和后热处理:预热可以提高焊接材料的可塑性,改善焊接接头的焊接性能。
一般情况下,预热温度为焊接材料的临界温度的50%-70%。
预热后的焊接接头,在焊接完成后应进行后热处理,即将焊接接头加热至临界温度以下保温一段时间,然后缓慢冷却,以进一步消除焊接接头内应力。
4.使用焊接夹具:焊接夹具可以固定工件,减少焊接过程中的变形。
夹具应设计合理,以便保证焊接接头位置准确,但对于自由热变形而言,应当尽量减少夹具的使用。
5.控制焊接热输入量:合理控制焊接过程中的热输入量,以确保焊接接头不过热。
可以采用间歇焊接的方法,在焊接过程中适时停止加热,让工件冷却一段时间以减少热输入。
6.采用适当的接头形状:通过改变焊缝的形状,可以减少焊接过程中的接应力。
一般情况下,V型焊缝和锂阳角焊缝对于减少焊接变形效果较好。
7.选择适当的焊接方式:对于大型工件,可以采用多层焊接或间断焊接的方式进行,以减少焊接材料的热量。
对于特殊形状的工件,可以选择其他焊接方法,如电阻焊、激光焊等。
8.控制冷却速度:焊接完成后,要注意控制冷却速度,避免过快的冷却。
可以采用包裹式焊接,焊接完毕后用保温材料将焊接接头包裹起来,使其缓慢冷却,以减少残余应力。
焊接变形控制措施

焊接变形控制措施1. 引言焊接是常见的金属连接工艺,它在制造业中起着重要的作用。
然而,焊接过程中会产生热量,导致工件变形。
焊接变形不仅会影响工件的外观,还可能导致尺寸偏差、失配和应力集中等问题。
因此,为了控制焊接变形,需要采取一系列措施来减少其影响。
本文将介绍焊接变形的控制措施,包括减少焊接热输入、优化焊接顺序和采用辅助支撑等方法。
这些措施可以帮助工程师在焊接过程中有效控制变形,提高焊接质量。
2. 减少焊接热输入焊接热输入是导致焊接变形的主要原因之一。
当焊接电流和电压较高时,焊接过程中产生的热量也较大,会使焊接接头局部加热,导致热膨胀引起变形。
因此,减少焊接热输入是一种常用的焊接变形控制措施。
以下是减少焊接热输入的方法:•降低焊接电流和电压:通过调节焊接电流和电压的大小,可以控制焊接热输入的大小。
降低电流和电压可以减少焊接过程中的热量产生,从而减少变形的可能性。
•采用脉冲焊接技术:脉冲焊接技术可以使焊接电流周期性变化,从而降低焊接热输入。
这种技术可以减少焊接热量和热膨胀,有效控制焊接变形。
•使用预热和间歇焊接:在焊接之前,可以对焊接接头进行预热,以提高材料的可塑性和焊接质量。
间歇焊接是指在焊接过程中,将焊接接头暂停冷却一段时间,再继续焊接。
这种方法可以有效控制焊接热输入,减少变形。
3. 优化焊接顺序焊接顺序是影响焊接变形的另一个重要因素。
不同焊接顺序会导致不同的温度梯度和热应力,进而影响变形的大小和方向。
因此,优化焊接顺序是控制焊接变形的一项重要措施。
以下是优化焊接顺序的方法:•从焊接应力较小的区域开始焊接:焊接过程中,焊接接头会受到热应力的影响,从而引起变形。
通过从焊接应力较小的区域开始焊接,可以减少焊接接头受力不均匀引起的变形。
•分割大尺寸焊接接头:对于大尺寸的焊接接头,可以将其分割成若干个小接头进行焊接。
这样可以减少焊接接头的热输入,降低焊接变形的风险。
•控制焊接速度和温度:在焊接过程中,合适的焊接速度和温度可以减少焊接接头的热输入,进而减少焊接变形。
提高客车车身骨架焊接质量的措施

402007-12城市车辆在客车车身制造过程中,在车身骨架的六大片组焊后普遍存在变形问题,它是提高客车车身质量和提高焊接组合装配生产效率的主要瓶颈之一。
焊接质量影响车身骨架变形直接导致客车工艺车身校正工作量加大,而且校正造成车身骨架局部凹凸不平,直接影响整车骨架强度。
甚至导致车身骨架不得不进行返工,大大降低了生产效率。
因此,必须保证一定的尺寸和形状精度要求,以提高客车车身骨架焊接质量。
1 提高车身骨架零部件的制作精度零部件的制造精度是车身焊接质量的基础。
现在的车身骨架大部分由矩形管构成,选购的骨架材料应当满足精度要求,矩形管的断面不能有超差现象。
在胎具上的定位面是经过调整检验后达到技术要求的,如果断面超差会影响定位精度,其超差部分会在定位的另一面显示出来,组焊后的骨架表面会产生凹凸不平的现象。
同时,管材不能扭曲,特别是对于长杆件尤为重要,对直线度超差的长杆必须按直线度公差的要求进行校直处理。
车身骨架零部件的制作首先从切割开始,切割精度有2个方面,一是尺寸精度,另一个是切割面与骨架轴线的垂直度。
如果切割精度超差,与超差零件相连的零件则无法提高客车车身骨架焊接质量的措施内容提要:在客车车身制造过程中,在车身骨架的六大片组焊后普遍存在变形问题,它是提高客车车身质量和提高焊接组合装配生产效率的主要瓶颈之一,这些将直接影响整车骨架强度。
本文主要介绍提高客车车身焊接质量的工艺措施。
关键词:客车 车身骨架 焊接 控制马正培装配。
如果勉强装配,过紧部位可能因挤压力过大产生变形;间隙过大部位可能因焊缝处的金属深化区加大,冷却后收缩,产生超量的变形。
许多企业采用砂轮无齿锯切割,精度一般不易保证,因为无齿锯片在高速旋转时会抖动,而且抖动量因砂轮磨损量不同而变化,切割时的切口宽度不一致,无法满足高质量加工要求。
为了保证切口的精度,应采用有齿锯片加工设备进行切割,有齿锯片加工设备其锯片刚度大、刃口锋利、重复性好、转速低、没有抖动现象,因此切口宽度一致;同时,它还有定尺机构,其定位准确,可以保证加工尺寸精度。
汽车副车架焊接变形的控制方法
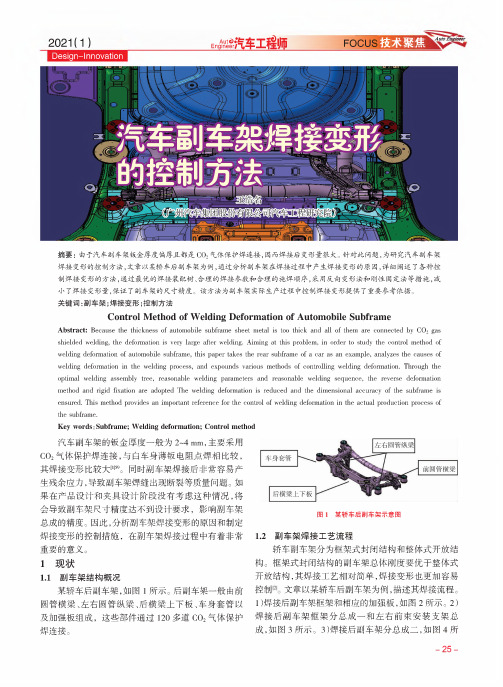
2021(1)E点韶汽车工穩师FOCUS亦*—汽-王浩名(广州汽车集团般份有限公司汽车工程研究院)In摘要:由于汽车副车架钣金厚度偏厚且都是co#气体保护焊连接,因而焊接后变形量很大。
针对此问题,为研究汽车副车架焊接变形的控制方法,文章以某轿车后副车架为例,通过分析副车架在焊接过程中产生焊接变形的原因,详细阐述了各种控制焊接变形的方法,通过最优的焊接装配树、合理的焊接参数和合理的施焊顺序,采用反向变形法和刚性固定法等措施,减小了焊接变形量,保证了副车架的尺寸精度。
该方法为副车架实际生产过程中控制焊接变形提供了重要参考依据。
关键词:副车架;焊接变形;控制方法Control Method of Welding Deformation of Automobile Subframe Abstract:Because the thickness of automobile subframe sheet metal is too thick and all of them are connected by C07gas shielded welding,the deformation is very large after welding.Aiming at this problem,in order to study the control method of welding deformation of automobile subframe,this paper takes the rear subframe of a car as an example,analyzes the causes of welding deformation in the welding process,and expounds various methods of controlling welding deformation.Through the optimal welding assembly tree,reasonable welding parameters and reasonable welding sequence,the reverse deformation method and rigid fixation are adopted The welding deformation is reduced and the dimensional accuracy of the subframe is ensured.This method provides an important reference for the control of welding deformation in the actual production process of the subframe.Key words:Subframe?Welding deformation?Control method汽车副车架的钣金厚度一般为2〜4mm,主要采用CO2气体保护焊连接,与白车身薄钣电阻点焊相比较,其焊接变形比较大22。
浅谈焊接结构件焊接变形的控制

浅谈焊接结构件焊接变形的控制
焊接是一种常见的金属加工方法,广泛应用于制造业中的各种结构件的制造中。
焊接
过程中会产生焊接变形,严重影响焊接结构件的形状和精度。
如何控制焊接变形成为焊接
技术中的一个重要问题。
焊接变形的产生主要有三个原因:热应力、组织相变和收缩。
焊接过程中,焊接区域
受到高温的热影响,导致焊接区域的材料膨胀,形成一定的热应力。
在焊接过程中,由于
材料的物理状态发生改变,可能会引起组织相变,进而产生焊接变形。
在焊接完成后,焊
缝周围的材料会发生冷却收缩,导致结构件发生变形。
为了控制焊接变形,可以采取以下几种措施。
可以采用后焊加热的方法。
通过在焊接
完成后对焊接区域加热,可以使焊接区域重新达到高温状态,减少焊接变形。
可以选择适
当的焊接顺序。
焊接顺序应该从内向外进行,以减少引起热应力和收缩的影响。
还可以通
过预设焊接变形来控制焊接变形。
预设焊接变形是通过在设计和加工过程中,根据结构件
的形状和要求,预先设置焊接变形的方式。
可以采用剪切焊接或者滚焊接等焊接方法,以
减少焊接变形的产生。
除了以上控制焊接变形的方法外,还可以通过选择合适的焊接工艺参数来控制焊接变形。
可以调整焊接速度、焊接电流和焊接角度等参数,以控制焊接过程中的热应力和收缩。
还可以采用预热和后热处理的方法,通过控制材料的温度分布和组织结构,减少焊接变
形。
汽车车架焊接变形的控制

汽车车架焊接变形的控制汽车车架焊接变形的控制是汽车制造行业一项非常关键的工艺。
焊接变形的控制是汽车制造过程中的一个重要步骤,它直接影响到汽车的整体稳定性和可靠性。
因此,正确地控制汽车车架焊接变形对于确保汽车安全上路具有重要意义。
通常来说,汽车车架焊接变形被分成三种类型:热熔变形、变位变形和冷缩变形。
热熔变形是强度高且成本低的焊接变形,它一般适用于热浸锌钢等车辆车架材料。
变位变形是指将焊接件固定在模具中,然后在受力后产生变形的一种方式。
冷缩变形是指在焊接件受到冷却的作用下,出现变形的一种方式。
首先,确定汽车车架材料的特性是汽车车架焊接变形控制的基础。
不同材料有不同的变形特性,这也决定了热熔、变位和冷缩焊接变形控制的方式。
其次,汽车车架焊接变形控制的重要因素是焊接工艺,包括温度、焊接时间、焊接速度和焊接类型等。
有效的控制可以确保焊接件的变形量最小,从而提高汽车质量,提升汽车的可靠性。
此外,为了减少汽车车架焊接变形的控制难度,可以采用激光焊接、高频电弧焊接等技术。
激光焊接可以大大改善焊接速度和焊接效果,并可有效抑制焊接变形。
高频电弧焊接可以提高焊接强度,减少焊接缝宽度,同时可有效抑制汽车车架焊接变形。
最后,实施正确的质量管理是确保汽车车架焊接变形控制的关键。
汽车制造企业应建立一套系统的质量管理体系,定期检查焊接工艺,严格控制产品的质量,确保汽车车架焊接变形控制的质量。
综上所述,汽车车架焊接变形的控制是一项极其复杂的工艺,必须涉及到多种因素。
汽车制造企业应建立严格的质量管理体系,综合运用热熔、变位和冷缩焊接技术,正确选择焊接工艺,运用激光焊接、高频电弧焊接技术,有效控制汽车车架焊接变形,确保汽车的可靠性和安全性;此外,确保正确的质量管理也是汽车安全生产的必要条件,质量管理要求应适应汽车行业的发展。
浅淡防止行车梁焊接变形的措施

浅淡防止行车梁焊接变形的措施一、从设计方面控制焊接残余变形1、合理选择构件截面提高构件的抗变形能力设计结构时要尽量使构件稳定,截面对称,薄壁箱形的内板布置要合理,特别是两端的内隔板要尽量向端部布置;构件的悬出部分不易过长;构件放置或吊起时,支承部位应是有足够的刚度等。
较容易变形或不易矫正的结构形式要避免采用。
可采用各种型钢,弯曲件和冲压件(如工字梁,槽钢和角铁)代替焊接结构,对焊接变形大的结构尽量采用铆接和螺栓连接。
对一些易变形的细长杆件或结构可采用临时工艺筋板,冲压加强筋,增加板厚等形式提高板件的刚度。
如从控制变形的角度考虑,钢桥结构的箱形薄壁结构的板材不宜太薄,否则焊成箱形后,无论整体变形还是局部变形都比较大,而且矫正困难。
因此,箱形钢结构的强度不但要考虑板厚,刚度和稳定性,而且考虑制造和安装过程中的变形也是很重要的。
2、合理选择焊缝尺寸和布置焊缝的位置焊缝尺寸过大不但增加了焊接工作量,对焊件输入的热量也多,而且也增加了焊接变形。
所以,在满足强度和工艺要求的前提下,尽可能的减少焊缝长度尺寸和焊缝数量,对连续焊缝在保证工件不相互窜动的前提下,可采用局部点固焊缝;对无密封要求的焊缝,尽可能采用断续焊缝。
但对易淬火钢要防止焊缝尺寸过小产生淬硬组织等。
设计焊缝时,尽量设计在构件中心轴的附近和对称于中性轴的位置,使产生的焊接变形尽可能的相互抵消。
如工字梁其截面是对称的,焊缝也对称于工字梁截面的中性轴。
焊接时只要焊接顺序选用合理,焊接变形就可以得到有效的拉制,特别是挠曲变形可以得到有效的控制。
3、合理选择焊缝的截面和坡口形式要做到在保证焊缝承载能力的前提下,设计时应尽量采用焊缝截面尺寸小的焊缝。
但要防止因焊缝尺寸过小,热量输入少,焊缝冷却速度快易造成裂纹、气孔、夹渣等缺陷。
因此,应根据板厚,焊接方法,焊接工艺等合理的选择焊缝尺寸。
此外,要根据钢结构的尺寸大小、形状等选择坡口形式。
如平板对接焊缝,一般选用对称的坡口,对于直径和板厚都较大的圆形对接筒体,可采用非对称坡口形式控制变形。
小车架焊接变形的控制技术
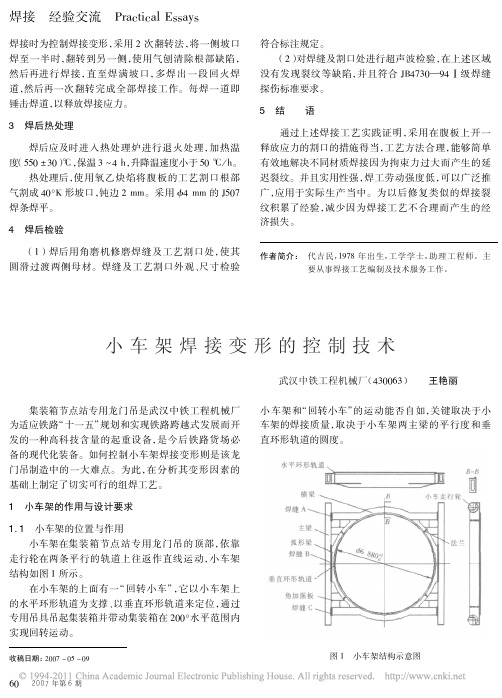
!""# 年第 $ 期
( 立) 后纵 ( 平) 。先焊上下盖板内的焊缝, 后焊裸露在 表面的焊缝; 先焊结构的横 ( 立) 焊缝, 后焊结构的纵 ( 平) 焊缝。垂直焊缝与水平焊缝相交时先焊垂直焊 缝。平行焊缝同时同方向焊接。尽量采用对称焊接, 焊缝分布不对称时先焊焊缝较少的一侧。长焊缝采取 从中间向两端分段退焊。多层焊时, 各层之间的焊缝 方向应相反, 其接头应相互错开。各部分单独组焊时 尽量使焊缝能比较自由地收缩。 %" #$ 焊接工艺 ( $ )主梁、 横梁的上下翼板与腹板的焊缝均采用 . 形坡口, 预留间隙 $ / # "", 采取 ! 层或多层施焊。 (# ) 采用 -0# 气体保护焊, 1’&23#45 焊丝, 直径 电压 #’ / #) .; 其 !$6 # ""。打底焊电流 $&’ / ##’ +, 余各层电流 ##’ / #7’ +, 电压 #) / #& .。 ( ! )由于主梁的截面不大 ( )$’ "" ( %$’ "" ) 且 比较长 ( & 7)’ "") , 故直线度!! "" 难以控制。为此 将整个主梁做成 ! 段, 中间用法兰联接。组焊时, 先将 两处的法兰上好, 把两端和中间视作一个整体进行放 样、 组装、 焊接。 ( ) )在大组装时, 采用 # 名焊工沿圆弧直径方向 对称同时同方向施焊, 最好一次焊完, 避免重复受热增 加变形。 ( 7 )在焊接垂直和水平环形轨道时, 采取跳焊法, 由两人一段圆弧一段圆弧进行施焊。 ( * )小车架定位焊完成后, 一方面先在四角弧形 梁外定位焊工艺板和角支撑, 另一方面在图 $ 的水平、 垂直方向焊刚性固定 “ 十字撑” , 以增强其刚性并检测 调整变形, 防止焊接过程中因焊接应力过大导致焊接 变形。 ( % )由于弧形梁焊接时一般都会引起 弧 长 的 收 缩, 故在焊前组装时先增大弧形梁内圆弧半经 # "" 左 右,以补偿弧长的收缩。 &$ 结$ $ 论 通过分析小车架变形的因素, 选择了合理的焊接 参数和组装顺序, 制定了合理的焊接工艺, 采取了刚性 固定、 反变形控制等控制变形的有力措施。此工艺不 仅达到设计要求、 保证了质量, 而且缩短了工期, 达到 了事半功倍的效果, 为今后类似结构的焊接变形控制 提供了参考。
焊接变形与控制措施

科技论坛焊接变形与控制措施李海涛(天津电力机车有限公司,天津300452)我们在焊接的过程中,焊件的局部温度会急剧上升。
构件由此会遭到损坏。
这是导致焊件变形的一个重要原因。
所以,我们可以从这里下手,来修护这种变形。
为了提高焊接的质量,可以通过观察焊接结构和焊接艺术进行修改还有焊接的技术等等。
1焊接变形与焊接应力产生的原因从实践观察中,我们观察到,导致焊接变形最主要的原因是焊缝里产生了变形应力。
焊接应力是什么呢?它就是焊接构件由于焊接而产生的应力。
前文我们也提到过,是因为焊接的时候产生不一样的温度,会引起局部发生塑性变形,而且比容不一样的组织也会使焊件发生焊接应力和变形。
焊接构件在焊接过程中会产生形状和尺寸的变化,导致这种变化的原因是在焊接的过程产生内应力。
焊接变形会对焊件产生极大的外观影响。
所以,我们要想改善这种现象,就要从焊接的过程和焊件的设计下手!以下介绍一些变形的原因。
1.1焊缝金属的收缩产生的变形我们焊接金属相当于给金属加热,金属之后会冷却,冷却的时候,金属会由液态转换为固态,体积会有,大的变化。
但是处于焊缝里的金属因为地方比较狭窄,自由伸缩性比较差,所以会导致变形。
就是这个原因会引起整个焊件的变形。
焊缝局部形成堵塞,会导致焊缝中的结晶部分会产生先后的收缩,先结晶的部分会阻止后结晶的部分,这个原因也会导致焊接应力与变形。
1.2焊件不均匀受热产生变形1.2.1焊件在加热过程中,会受到不均匀加热,如果温度达到构件的屈服点,构件就会产生变形。
等到冷却后,焊件就可能会有残留变形。
1.2.2加热的时候,焊缝和他的周围区域会产生压缩性收缩。
冷却的时候,压缩塑性变形区会产生相应的收缩。
1.2.3焊接过程中及焊接结束后,焊件的应力分布是不均匀的。
在焊接过程中和焊接结束的时候,应力不均匀的分布在焊件上,这个时候的残余应力是拉应力,一般会作用于焊缝和他的附近的地方。
1.3焊缝的刚性和拘束我们还发现了,对焊件应力与变形有较大的影响还有焊缝的刚性和拘束。
焊接变形的控制与矫正

焊接变形的控制与矫正一、引言在焊接工艺中,焊接变形是一个常见的问题。
焊接变形指的是在焊接过程中,由于热膨胀和收缩等原因导致工件发生形状和尺寸上的变化。
这种变形不仅会影响工件的外观和精度,还会对其机械性能产生负面影响。
因此,控制和矫正焊接变形是保证焊接质量的重要措施。
二、焊接变形的原因1. 焊接过程中产生的热膨胀和收缩在焊接过程中,电弧或火焰所产生的高温会使得工件局部区域发生热膨胀,而当温度降低时,则会发生收缩。
由于金属具有较高的线膨胀系数,在加热或冷却时容易发生体积变化,从而导致工件产生形状和尺寸上的变化。
2. 材料本身性能差异不同材料具有不同的线膨胀系数、弹性模量等物理特性,这些特性差异也会导致在同样条件下不同材料在加热或冷却时发生不同的形变。
3. 焊接残余应力在焊接过程中,由于热膨胀和收缩等原因,工件内部会产生残余应力。
这些应力会导致工件变形并且可能会影响其机械性能。
三、焊接变形的类型1. 直线型变形直线型变形是指焊缝沿着直线方向发生的变形。
这种变形常见于长条状或板材状工件上。
2. 弧形型变形弧形型变形是指焊缝沿着弧线方向发生的变形。
这种变形常见于圆环状或球体状工件上。
3. 扭曲型变形扭曲型变形是指焊接后工件整体扭曲或者局部扭曲的现象。
这种现象常见于薄壁管材或者异型工件上。
四、控制焊接变形的方法1. 设计合理的结构和加工方式在设计工件结构时,可以采取一些措施来减少焊接时产生的热膨胀和收缩。
例如,在设计过程中可以采用对称结构,减少单侧加热量;或者通过设置冷却装置来控制焊接区域的温度。
2. 选择合适的焊接工艺参数在焊接过程中,选择合适的焊接工艺参数也可以减少焊接变形。
例如,通过降低电流和增加电极间距来减少热输入量;或者采用脉冲焊接技术来控制热输入量。
3. 使用夹具和支撑物使用夹具和支撑物可以有效地减少焊件的变形。
在夹持过程中,应该注意夹紧力不要过大或过小,并且应该尽可能使得工件受力均匀。
4. 焊前预处理在进行焊接之前,可以采取一些预处理措施来减少变形。
车身骨架焊后变形的矫正方法技师论文

车身骨架焊后变形的矫正方法姓名:单位:地址:电话:邮编:目录一摘要 (2)二引言 (3)三1.车身骨架的组成 (3)2.焊接应力与变形 (4)3.车身骨架焊后残余变形的矫正方法 (5)四结束语 (8)五参考文献 (8)摘要:在客车生产过程中,车身骨架是由异形钢管焊接而成,由于焊接过程中受热不均匀的缘故,异形钢管都会在不同程序上发生弯曲变形。
这种变形影响客车面板的粘贴与客车的质量以及车身的流线美,所以对车身骨架要进行平整度调整,这种调整用专业术语来讲,叫钣金。
通过多年的工作经验,运用钣金的技术,用火焰对骨架弯曲部分加热的方法进行矫正,确保了客车的质量。
关键词:车身骨架平整度调整焊接火焰加热矫正车身骨架焊后变形的矫正方法引言在客车生产过程中,车身骨架是由异形钢管焊接而成,由于受热不均匀的缘故,异形管都会在不同程序上发生弯曲变形。
针对这种变形要进行平整度的调整,通过多年的工作经验,总结出了用加热的方法矫正车身骨架,防止变形的措施。
1.车身骨架的组成车身骨架(车笼),是由以下五部分组成:一、两个侧围(大栅);二、前围;三、后围;四、顶盖;五、底盘。
而这些部件都是由许多长短不一的异形钢焊接而成,然后再将这些部件进行合拢,就形成了车身骨架。
车身骨架上粘贴上面板,形成了车身。
在车身的外表面进行涂装、喷漆,就形成具有流线美丽,光滑而平整的大客车车身外表面。
车身的外表面平整度的要求不仅是从坚实耐用的角度还是从美观的流线角度要求都是很严格的。
车身骨架不仅在部件生产过程中还是在合拢过程中,由于在焊接过程中受热不均匀,异形铁管都会在不同程度上发生一些变化,而这些变化中,弯曲变形是最常见的一种变化。
车身骨架的弯曲,对下道工序车身蒙皮粘贴,对整个车身平面的平整度影响很大,对整个客车的质量,以及车身的流线美,影响很大。
所以需要用钣金的技术对其进行平整度的调整。
下面对变形的原因进行一下分析。
2.焊接应力与变形物体受到外力作用发生变形的同时,在其内部会出现一种抵抗变形的力,这种力叫做内力,物体由于受到内力的作用,在单位截面上出现的内力就叫做应力。
- 1、下载文档前请自行甄别文档内容的完整性,平台不提供额外的编辑、内容补充、找答案等附加服务。
- 2、"仅部分预览"的文档,不可在线预览部分如存在完整性等问题,可反馈申请退款(可完整预览的文档不适用该条件!)。
- 3、如文档侵犯您的权益,请联系客服反馈,我们会尽快为您处理(人工客服工作时间:9:00-18:30)。
连接板
异型管
车架横梁
中立柱
图 5 连接板的焊缝位置
侧围下横梁
2 工艺措施
2.1 反变形法 反变形法是事先估计好焊接结构变形的大小和方向, 然后
在组合( 点 固 焊) 时 给 予 一 个 相 反 方 向 的 变 形 来 抵 消 焊 接 的 变
形, 这是使焊后构件保持设计要求的一种工艺方法, 也是汽车 车身总成生产中较常用的一种控制变形方法。
Abs tract: At present, the CAD (Computer Aided Design)/ CAE (Computer Aided Engineering) technology has advanced by leaps and bounds , manufacturing industry has provided the technology hold out big and powerful to machinery. The main body of a book take the reduction gear design as example , set forth CAD/CAE technology application in designing that in machinery. Key words : Reduction gear; Design that; Apply
既增加了构件和焊接的工作量, 还因焊接变形大而增加了校正
工时。因此, 适当增加管壁厚度或增大管径, 减少筋板, 车身净
质量稍大一些也是比较经济的。另外, 合理选择筋板形状, 适当
安排筋板位置, 也可以减少焊缝, 达到提高筋板加固的效果。
1.5 合理的焊缝位置
收稿日期: 2007- 10- 20 作者简介: 陈大军( 1971—) , 男, 湖南岳阳人, 主任工程师, 研究方向: 车身设计与焊接;
侧围下横梁
车架纵梁
下车体横梁
图 6 下车体横梁、纵梁和侧围总成的焊接顺序 图 6 所示为下车体横梁先焊接在车架纵梁上, 属于下车体
图 7 侧围下横序梁、中立柱和车架横梁的焊接顺序 图 7 所示为侧围下横梁和中立柱组合成侧围总成, 然后和 车架横梁所属的下车体焊合成车身总成。在试制过程中发现, 侧围下梁和中立柱焊接牢固后, 和车架横梁搭接处翘曲很多, 造成搭接不好。经过调整工艺路线, 侧围下横梁和中立柱先点 定位置, 在侧围下横梁和车架横梁焊接牢固后, 再加焊侧围下 横梁和中立柱, 这样就解决了焊接变形问题。 在产品生产过程中, 这种现象会经常发生。我们不应拘泥 于产品设计中所分的模块, 而要根据实际情况几时调整工艺路 线, 这样才能生产出合格的产品。
况而定, 如果太大, 两个零件离空太多, 就没办法焊接了, 而且 还会对车身的强度和刚度产生不利影响。 1.3 合理的焊接方法
焊缝尺寸直接关系到车身的焊接工作量和焊接变形大 小, 焊缝尺寸大, 焊接工作量则大, 焊接变形也大。因此, 在保证 车身承载能力的情况下, 应尽量减小焊缝尺寸, 但并不是说焊 缝尺寸越小越好。若焊缝尺寸太小, 则冷却速度会加快, 容易产 生 裂 纹 、热 影 响 区 硬 度 过 高 等 焊 接 缺 陷 。 应 在 保 证 焊 接 质 量 的 前提下 , 按 板 厚( 管 壁 厚) 来 选 取 工 艺 上 允 许 的 最 小 焊 缝 尺 寸 。 在保证强度的前提下, 能够用点焊的地方就一定要用点焊, 这 样可以尽量减少焊接变形。如图 4 的 V2 前 隔 板 总 成 中 , 注 意 到这里钣金件居多, 所以设计成运用点焊进行焊接的零件结 构, 但供应商承制的时候, 没仔细进行工艺分析和熟悉零件, 就 大量采用 CO2 保护 焊 , 且 焊 缝 密 度 很 大 , 造 成 零 件 总 成 生 产 出 来后, 变形非常大, 且零件局部也产生了很严重的波纹状, 再加 上零件本身的制造误差, 使得最初的 OTS 零 件 基 本 上 没 办 法 使用。
3 矫正工艺
在车身总成的焊接过程中, 虽然在结构设计和工艺上采取 多种措施来控制施焊中所产生的焊接变形, 但由于焊接过程的 特点和焊接工艺的复杂性, 还是会或多或少地产生焊接变形。 为此, 必须对超过设计要求的焊接变形进行局部工艺矫正, 如 角 变 形 、弯 曲 变 形 和 波 浪 变 形 等 。 对 于 车 身 结 构 的 整 体 变 形 如纵向和横向收缩( 总尺寸缩短) , 只能通过下料或装配时预放 余量来补偿。机械矫正法是在室温条件下, 对焊接件施加外力, 使构件压缩塑性变形区的金属伸展, 减少或消除焊缝区的塑性 变形, 达到矫正变形的目的, 如下车体焊接完后要对两根大梁 前端进行弯曲矫正。在实际操作中, 还应注意自然时效的作用, 必须通过经验积累和严格检验的手段来保证矫正的精度。
[下转第 110 页]
106
Equipment Manufactring Technology NO.12, 2007
若强度不满足要求, 则需修改轴的结构直至满足强度要求 为止。轴的强度校核过程为: 轴的受力分析→ 画出轴在水平面 内的弯距图→ 画出轴在垂直面内的弯距图→合成弯距图 →扭 距图 →弯、扭 组 合 图 →确 定 2- 3 个 危 险 截 面 分 别 进 行 强 度 校 核。此过程计算量与作图量都较大。为了提高轴的设计效率, 缩 短 设 计 周 期 , 现 在 工 程 实 际 中 经 常 使 用 CAE 技 术( 如 ANSYS 等) 对轴进行校核, 根据轴的材料属性、负载条件、边界条件, 并 对轴进行有限元网格划分等, 给定条件后进行求解运算, 可得 出最大应力, 然后此最大应力与许用应力比较, 若最大应力小 于许用应力, 则轴的结构满足要求。若最大应力大于许用应力,
杨文静( 1980—) , 男, 湖北荆门人, 助理工程师, 研究方向: 车身设计。
105
Equipment Manufactring Technology NO.12, 2007
如图 5 所示, 连接板面积原来与同它焊在一起的异型管截 面是同样大小的, 在试制时发现, 在进行焊接后再打磨, 原来的 焊缝基本上就被打磨掉了, 只有很小的部分熔焊在一起, 已经 没什么联结强度了。后来才改成现在这个形状, 连接板面积比 异型管截面稍小一点, 有对称的两条边可以牢固地焊接在异型 管上。可见合理的选择焊缝位置, 不但可以减少焊接变形, 同时 对焊接强度也会有很大提高。
总成。侧围下横梁属于侧围总成中, 这里隐藏了侧围中其他的 零件。正常的工艺路线是下车体横梁先焊接在车架纵梁上, 然 后 侧 围 总 成 再 和 下 车 体 总 成 进 行 焊 接 。但 是 在 实 际 操 作 过 程 中 发现, 如果下车体横梁先和车架纵梁焊接牢固, 横梁的两端会 向下弯曲近 10mm, 在和侧围总成拼焊的 时 候 和 侧 围 下 横 梁 搭 接不好。经过和工艺人员协商, 调整焊接顺序, 在下车体焊接过 程中, 下车体横梁和纵梁只是焊接一点, 点定一下位置, 在下车 体和和侧围总成先焊接好之后, 再来加焊牢固, 这样就避免了 焊接变形。
在试制过程中发现在连接件处经常离空, 尚未找到有效的解决
办法, 只好从设计角度保留理论的公称尺寸, 再根据现场实际
情况在后立柱总成中预留合理的公差, 终于解决了这个问题。
在侧围总成中的中立柱长度方向也遇到了同样的问题, 也是采
取了同样的办法, 均得以解决。这里的公差一定要根据实际情
后立柱总成
此零件为 后立柱总 成和行李 箱支撑梁 的连接件
The CAD/CAE Te chnology Hபைடு நூலகம்ts the Ta rge t in Ma chine ry De s ign Applying
ZHANG Xi- qin ( Changzhou Electromechanical Instiute of Vocation and Technology, Chanzhou Jiangsu 213164, China)
则需修改轴的结构, 有必要再用一次 CAE 分析。 CAE 技术除了可对产品 结 构 进 行 强 度 分 析 外 , 还 可 进 行
刚度分析、散 热 能 力 分 析 、疲 劳 和 蠕 变 分 析 、抗 冲 击 试 验 模 拟 、 跌落试验模拟等。
随着科学技术的不断发展与进步, 制造业正向数字化、智 能化、网络化 、全 球 化 方 向 发 展 , 产 品 的 生 产 周 期 越 来 越 短 , 新 产品的上市速度越来越快, 机械设计与机械制造的效率对产品 的开发效率也就起着决定性的影响。所以利用先进的 CAD/CAE 技术进行机械设计与分析更省事、省力, 也更经济。
加控制, 结果是保证了尺寸精度, 达到了装配要求。
关键词: 焊接; 变形; 控制措施; 尺寸精度
中图分类号: TG4
文献标识码: B
文章编号: 1672- 545X( 2007) 12- 0105- 02
汽车的框架式车身大量采用异型管作零件, 生产中导致焊 接工艺较差, 基 本 上 只 能 采 用 手 动 作 业 的 CO2 保 护 焊 进 行 焊 接作业, 导致劳动强度大, 易于产生较大的焊接变形, 这就要求 对 焊 接 工 艺 及 控 制 焊 接 变 形 问 题 进 行 优 化 设 计 。以 下 是 笔 者 在 设计和生产过程中采取的一些措施, 实践证明达到预期效果。
行李箱支撑梁
图 3 后立柱总成与行李 箱支撑梁的搭接
1.4 合理的焊缝数目
图 4 前隔板总成的 点焊零件结构
在车身结构中力求焊缝数量合理, 焊缝不宜过分集中, 尽
量避免两条或三条焊缝垂直交叉,长条的焊缝要合理分成若干
小段进行焊接。有时为了减小整车的净质量, 采用壁厚较薄的
钢管加筋板来焊接车身, 以提高车身稳定性和刚性, 其实这样
焊接顺序对焊接结构的变形有很大影响。焊接顺序合理,
焊接变形可以通过自由收缩, 互相抵消; 焊接顺序不合理, 焊接