活性石灰焙烧工艺
3.2-16石灰焙烧_1

3.2-16石灰焙烧石灰焙烧是一种重要的石灰生产方法,通过对石灰石进行加热处理,使其发生化学反应,生成石灰。
本文将介绍石灰焙烧的原理、设备、工艺和应用等方面的内容。
一、石灰焙烧的原理石灰焙烧的原理是将石灰石进行加热处理,使其发生分解反应,生成氧化钙(CaO)。
具体的反应方程式为:CaCO3(石灰石)→ CaO(氧化钙)+ CO2(二氧化碳)这个反应是一个热力学上的自发反应,需要提供足够的加热能量才能使反应发生。
二、石灰焙烧的设备石灰焙烧的设备主要包括炉体、加热设备和气体处理设备等。
炉体一般由耐火材料构成,用来容纳石灰石,并提供加热环境。
加热设备一般采用火焰或电加热方式,用来提供加热能量。
气体处理设备主要用来处理焙烧过程中生成的二氧化碳和石灰石中的杂质。
三、石灰焙烧的工艺石灰焙烧的工艺一般分为四个步骤:预热、分解、冷却和存储。
1. 预热:将石灰石放入炉体中,逐渐升温至500-700℃,使石灰石表面开始发生预热反应,提高焙烧效果。
2. 分解:当石灰石表面温度达到800-1100℃时,石灰石开始发生分解反应,生成氧化钙和二氧化碳。
3. 冷却:当石灰石分解反应结束后,需要将产生的氧化钙进行冷却处理。
一般采用自然冷却或通过冷却设备进行快速冷却。
4. 存储:将冷却后的石灰石存储在干燥的环境中,以防止其吸湿变质。
四、石灰焙烧的应用石灰焙烧产生的氧化钙是一种重要的工业原料,广泛应用于建筑、冶金、化工、环保等领域。
1. 建筑领域:氧化钙可用于生产砂浆、混凝土和石膏等建筑材料,具有良好的强度和耐久性。
2. 冶金领域:氧化钙可用于冶炼金属,如铁、铜等,起到脱硫、脱氧等作用。
3. 化工领域:氧化钙可用于生产化肥、漂白粉、造纸等化工产品,具有很高的化学反应活性。
4. 环保领域:氧化钙可用于废气净化、废水处理等环保工艺,具有很强的吸附和中和能力。
综上所述,石灰焙烧是一种重要的石灰生产方法,通过对石灰石进行加热处理,可以产生氧化钙,广泛应用于建筑、冶金、化工、环保等领域。
活性石灰生产工艺
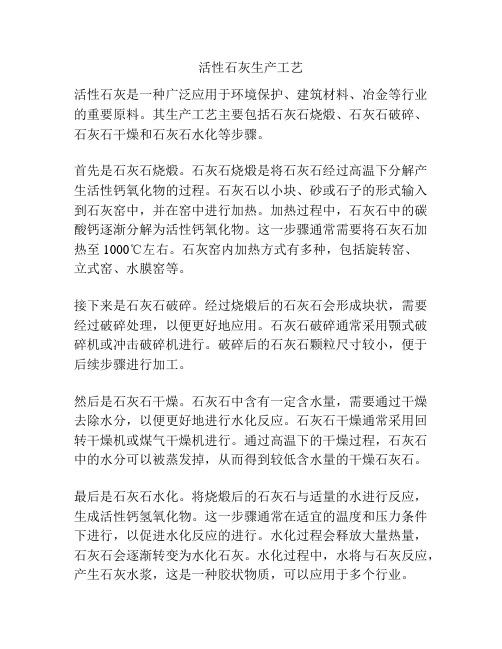
活性石灰生产工艺活性石灰是一种广泛应用于环境保护、建筑材料、冶金等行业的重要原料。
其生产工艺主要包括石灰石烧煅、石灰石破碎、石灰石干燥和石灰石水化等步骤。
首先是石灰石烧煅。
石灰石烧煅是将石灰石经过高温下分解产生活性钙氧化物的过程。
石灰石以小块、砂或石子的形式输入到石灰窑中,并在窑中进行加热。
加热过程中,石灰石中的碳酸钙逐渐分解为活性钙氧化物。
这一步骤通常需要将石灰石加热至1000℃左右。
石灰窑内加热方式有多种,包括旋转窑、立式窑、水膜窑等。
接下来是石灰石破碎。
经过烧煅后的石灰石会形成块状,需要经过破碎处理,以便更好地应用。
石灰石破碎通常采用颚式破碎机或冲击破碎机进行。
破碎后的石灰石颗粒尺寸较小,便于后续步骤进行加工。
然后是石灰石干燥。
石灰石中含有一定含水量,需要通过干燥去除水分,以便更好地进行水化反应。
石灰石干燥通常采用回转干燥机或煤气干燥机进行。
通过高温下的干燥过程,石灰石中的水分可以被蒸发掉,从而得到较低含水量的干燥石灰石。
最后是石灰石水化。
将烧煅后的石灰石与适量的水进行反应,生成活性钙氢氧化物。
这一步骤通常在适宜的温度和压力条件下进行,以促进水化反应的进行。
水化过程会释放大量热量,石灰石会逐渐转变为水化石灰。
水化过程中,水将与石灰反应,产生石灰水浆,这是一种胶状物质,可以应用于多个行业。
综上所述,活性石灰的生产工艺包括石灰石烧煅、石灰石破碎、石灰石干燥和石灰石水化等步骤。
这些步骤的顺序和具体实施方式可以根据不同的工艺要求和生产场所的特点进行调整。
通过这些步骤的合理组合,可以生产出高质量的活性石灰,满足不同行业对该产品的需求。
浅谈活性石灰的应用及生产工艺

浅谈活性石灰的应用及生产工艺摘要活性石灰具备晶粒小、CO2含量低、孔隙率高、活性高、容重低等特点。
是一种优质轻烧石灰,在炼钢、环保等方面有广泛的应用。
为控制活性石灰生产质量,本文对活性石灰的应用及生产工艺进行了深入分析。
关键词活性石灰;应用;生产工艺引言石灰是钢铁生产过程中重要的造渣剂。
控制钢铁生产质量,一定要保证石灰质量符合标准生产质量要求。
鉴于我们国家冶金冶炼技术的优化创新,对活性石灰的活性提出了更高的要求。
传统的活性石灰生产工艺和生产设备已不能满足当代活性石灰的质量要求。
活性石灰生产的产业结构和生产工艺有待完善。
调整、采取使用当代活性石灰生产工艺,选择合适的生产设备,确保活性石灰生产质量得到提升,满足当代工业领域的生产需要。
一、活性石灰的应用活性石灰普遍作用于许多行业。
化学工业中一些不可或缺的钙盐,如电石、烧碱、硝酸钙等,主要是用石灰通过相应的化学加工制成的。
石灰石通过相应的工序可制成粉状碳酸钙。
该材料纯度较高,可被认为是塑料、化妆品等相应产品的填料。
在农业生产领域,生石灰常被用来配置农药,而石灰在中和土壤酸度、改善土壤整体结构、为植物的健康生长予以充足的钙质方面也发挥着至关重要的作用,非常具有价值。
活性石灰的特点主要表现在体积小、密度低、孔隙率大、化学纯度高,这些都是其活性高的原因。
相关实践结果表明,发展转炉炼钢,借助活性石灰的应用,能够减少吹氧时间,提升钢水收得率,降低石灰消耗量,还能够促进脱硫脱硫。
磷的作用对提升钢的质量起着不可或缺的作用。
从某种角度看来,这对于冶金行业,活性石灰是一种非常常见的材料。
在我国冶金行业产业组织不断调整的背景下,冶金冶炼工艺技术也逐步提高,这使得冶金行业对活性石灰质量的要求比以往更加严格,特别是活性石灰的活性石灰,应当需要它的活性。
一定要大于350ml。
生产活性石灰所采取使用的传统工艺已难以满足当前的实际需求。
因此,石灰行业进行大规模结构调整是必然趋势。
二、活性石灰生产工艺1、原料储运将粒度约30mm的石灰石从矿山运至生产区。
活性钙的生产工艺
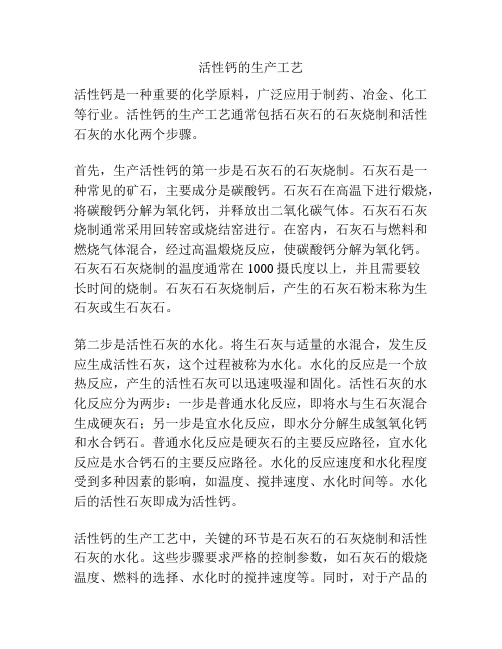
活性钙的生产工艺活性钙是一种重要的化学原料,广泛应用于制药、冶金、化工等行业。
活性钙的生产工艺通常包括石灰石的石灰烧制和活性石灰的水化两个步骤。
首先,生产活性钙的第一步是石灰石的石灰烧制。
石灰石是一种常见的矿石,主要成分是碳酸钙。
石灰石在高温下进行煅烧,将碳酸钙分解为氧化钙,并释放出二氧化碳气体。
石灰石石灰烧制通常采用回转窑或烧结窑进行。
在窑内,石灰石与燃料和燃烧气体混合,经过高温煅烧反应,使碳酸钙分解为氧化钙。
石灰石石灰烧制的温度通常在1000摄氏度以上,并且需要较长时间的烧制。
石灰石石灰烧制后,产生的石灰石粉末称为生石灰或生石灰石。
第二步是活性石灰的水化。
将生石灰与适量的水混合,发生反应生成活性石灰,这个过程被称为水化。
水化的反应是一个放热反应,产生的活性石灰可以迅速吸湿和固化。
活性石灰的水化反应分为两步:一步是普通水化反应,即将水与生石灰混合生成硬灰石;另一步是宜水化反应,即水分分解生成氢氧化钙和水合钙石。
普通水化反应是硬灰石的主要反应路径,宜水化反应是水合钙石的主要反应路径。
水化的反应速度和水化程度受到多种因素的影响,如温度、搅拌速度、水化时间等。
水化后的活性石灰即成为活性钙。
活性钙的生产工艺中,关键的环节是石灰石的石灰烧制和活性石灰的水化。
这些步骤要求严格的控制参数,如石灰石的煅烧温度、燃料的选择、水化时的搅拌速度等。
同时,对于产品的质量和稳定性也需要进行控制,以保证活性钙的品质达到要求。
总之,活性钙的生产工艺包括石灰石的石灰烧制和活性石灰的水化两个步骤。
通过这些步骤,可以将石灰石转化为活性钙,从而满足各个行业的需求。
生产过程中需要严格控制参数和产品质量,以确保最终产品的品质。
活性石灰回转窑工艺操作规程
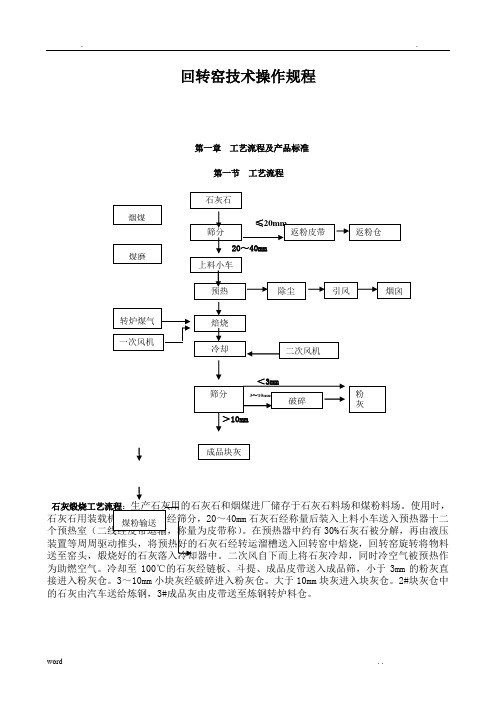
回转窑技术操作规程第一章工艺流程及产品标准第一节工艺流程生产石灰用的石灰石和烟煤进厂储存于石灰石料场和煤粉料场。
使用时,20~40mm石灰石经称量后装入上料小车送入预热器十二。
在预热器中约有30%石灰石被分解,再由液压为助燃空气。
冷却至100℃的石灰经链板、斗提、成品皮带送入成品筛,小于3mm的粉灰直接进入粉灰仓。
3~10mm小块灰经破碎进入粉灰仓。
大于10mm块灰进入块灰仓。
2#块灰仓中的石灰由汽车送给炼钢,3#成品灰由皮带送至炼钢转炉料仓。
第二节原料(石灰石)第三节燃料(烟煤)第四节主要经济指标第二章技术操作规程第一节开机操作接开机指令后,通知各岗位检查所属设备,检查本岗位所属设备,确认无误后,汇报工长,得到工长允许后,按下列顺序进行操作1挂上操作牌并记录2引入煤气,做爆发试验,准备点火3点火前通知其它各相关岗位4点火(执行点火操作标准)5按顺序开机待提升开机运转正常后,启动链板出灰机点火后:启动助燃风机—启动冷风套风机辅机转窑:挂上慢传联轴器—启动慢传电机()主机转窑:脱开慢传联轴器—启动主电机—调整窑速6向调度、工长汇报开机时间,向调度汇报煤气点火时间第二节停机操作正常停机分为熄火停窑和不熄火停窑,接停机指令后,按下列程序停机熄火停窑1、接停窑指令后,进行减料操作,做好停窑准备2、减料操作过程中,逐步降低风量、煤粉量和煤气量3、冷却器上部溜管插入钢钎,排空预热器推头上部物料。
4、停料后,停止喷煤粉,在窑内物料逐渐减少的过程中逐渐减少煤气量以及一次风、二次风量5、待窑内物料全部进入煅烧带后,停煤气及一次风,预热器及窑内料排空后停窑6、窑内料排空后,根据冬、夏季节生产情况,采取停引风机自然降温或降低引风量进行匀速降温7、停窑后,每隔30分钟转窑1/3~1/4圈,预热器进口温度降至500℃以下后,每隔60分钟砖窑1/3~1/4圈,直到窑冷却为止,以防窑变形8、停窑后,将冷却器内物料排空,同时处理预热器横梁上部结块。
活性石灰回转窑工艺操作规程

回转窑技术操纵规程之阿布丰王创作第一章工艺流程及产品尺度20~40mm<3mm石灰煅烧工艺流程:生产石灰用的石灰石和烟煤进厂储存于石灰石料场和煤粉料场。
使用时,石灰石用装载机装入料仓,经筛分,20~40mm 石灰石经称量后装入上料小车送入预热器十二个预热室(二线经皮带运输,称量为皮带称)。
在预热器中约有30%石灰石被分解,再由液压装置等周周驱动推头,将预热好的石灰石经转运溜槽送入回转窑中焙烧,回转窑旋转将物料送至窑头,煅烧好的石灰落入冷却器中。
二次风自下而上将石灰冷却,同时冷空气被预热作为助燃空气。
冷却至100℃的石灰经链板、斗提、成品皮带送入成品筛,小于3mm 的粉灰直接进入粉灰仓。
3~10mm 小块灰经破碎进入粉灰仓。
大于10mm 块灰进入块灰仓。
2#块灰仓中的石灰由汽车送给炼钢,3#成品灰由皮带送至炼钢转炉料仓。
第二节 原料(石灰石)第四节 主要经济指标序号 项 目 单位 指标 备注1 石灰产量104t ∕a20 三条线共60万吨 2 预热器 直径 mm 10400 三台 高度mm 8586 3 回转窑 直径 m 4 三台 长度 m 60 4 冷却器宽度 mm 4060 三台 长度mm 4060 年作业率% 90 石灰质量 CaO % ≥90 MgO % ≤5 SiO2 % ≤1.5 活性度 ml ≥300灼减%≤5成品块灰 粉 灰动力消耗电耗kw/吨灰40水耗吨/吨灰0.1 新水转炉煤气m3/吨灰280 热值84000kj∕m3煤粉Kg/吨灰80 无水工序能耗kg(标煤)/t95第五节主要技术参数序号名称单位技术指标1 日产量t/d 5502 预热器顶部温度℃1050±203 双色温度℃1300±504 窑头罩顶部温度℃650±505 窑头罩压力Pa -15±156 窑尾压力Pa -40±157 CO浓度%<18 电除尘进口压力kpa -3000±2009 预热器料仓料位m 5.0~8.010 冷却器料位m 篦下0.511 电除尘入口温度℃260±2012 预热器侧壁温度℃40013 排灰温度℃10014 磨机转速转/min 5015 最大入磨粒度mm 4016 入磨水份%≤1217 煤粉粒度-200目6518 磨机装机总功率kw 150第二章技术操纵规程第一节开机操纵接开机指令后,通知各岗位检查所属设备,检查本岗位所属设备,确认无误后,汇报工长,得到工长允许后,按下列顺序进行操纵1挂上操纵牌并记录2引入煤气,做迸发试验,准备点火3点火前通知其它各相关岗位4点火(执行点火操纵尺度)5按顺序开机待提升开机运转正常后,启动链板出灰机点火后:启动助燃风机—启动冷风套风机辅机转窑:挂上慢传联轴器—启动慢传电机()主机转窑:脱开慢传联轴器—启动主电机—调整窑速6向调度、工长汇报开机时间,向调度汇报煤气点火时间第二节停机操纵正常停机分为熄火停窑和不熄火停窑,接停机指令后,按下列程序停机熄火停窑1、接停窑指令后,进行减料操纵,做好停窑准备2、减料操纵过程中,逐步降低风量、煤粉量和煤气量3、冷却器上部溜管拔出钢钎,排空预热器推头上部物料。
石灰的煅烧工艺及其结构对活性度的影响

石灰的煅烧工艺及其结构对活性度的影响摘要:用扫描电镜研究了活性石灰的煅烧工艺、显微结构与活性的关系,研究了活性石灰的产生机理及影响活性的因素,并对活性石灰的杂质含量进行了测定,煅烧工艺及其它高温或保温时间使钙晶体完整,提高了石灰的活性关键词:石灰石;煅烧处理工艺石灰石是钢铁炼钢的主要使用渣土原料,其主要成分是氧化钙。
石灰钢液是各种脱硫、脱磷、脱氧溶剂不可或或缺少的重要原料,为了有效提高石灰钢液的化学纯度,减少热量的损失,石灰必须具有较高的化学反应活性,快速受热熔化,迅速分解成渣的特性。
石灰石在转炉内分解吸收热量,炼钢石灰一般采用轻烧后使用。
活性是判断炉渣形成的重要指标,轻灰的活性与石灰的化学成分、石灰的岩性结构和煅烧工艺条件有关,其中岩石的化学成分和结构是影响煅烧石灰活性的内在条件,而焙烧条件是外部条件,不同的来源和开采条件影响了石灰的活性,导致石灰的化学成分不同,特别是矿物原料的组成和含量不同,对石灰的活性和后续使用有一定的影响,而矿化条件影响石灰的组成,石灰石颗粒的分布和大小影响石灰的活性。
煅烧条件是石灰煅烧过程中应用的工艺条件,主要是煅烧温度,煅烧时间,升温速度,粒度,保温时间等。
[1]通过研究煅烧时间、升温速率和粒度对这些条件的影响,根据需要调整煅烧工艺条件,以得到我们需要的产品,本文主要研究了外界条件对煅烧石灰活性的影响,为了解释相同条件下不同因素对煅烧石灰活性的影响,利用石灰石产品的结构研究了不同沉积物中煅烧石灰石的活性。
[2]一.实验选材选取具有a、b、c三种不同煅烧来源的保温石灰,在加热电阻煅烧室中以5℃/min的煅烧速率进行加热,然后继续加热至达到合适的煅烧温度,在90min的保温煅料燃烧时间温度下,研究了950℃、1000℃、1050℃下对石灰石活性的直接影响,在1100℃、1150℃和1200℃煅烧条件下,研究了保温煅烧时间对轻灰和石灰活性的直接影响。
保温时间分别为30分钟、60分钟、90分钟和120分钟。
活性石灰焙烧工艺
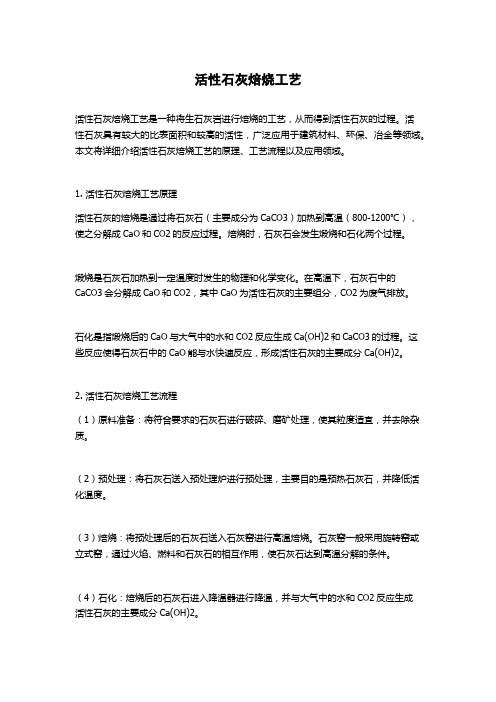
活性石灰焙烧工艺活性石灰焙烧工艺是一种将生石灰岩进行焙烧的工艺,从而得到活性石灰的过程。
活性石灰具有较大的比表面积和较高的活性,广泛应用于建筑材料、环保、冶金等领域。
本文将详细介绍活性石灰焙烧工艺的原理、工艺流程以及应用领域。
1. 活性石灰焙烧工艺原理活性石灰的焙烧是通过将石灰石(主要成分为CaCO3)加热到高温(800-1200℃),使之分解成CaO和CO2的反应过程。
焙烧时,石灰石会发生煅烧和石化两个过程。
煅烧是石灰石加热到一定温度时发生的物理和化学变化。
在高温下,石灰石中的CaCO3会分解成CaO和CO2,其中CaO为活性石灰的主要组分,CO2为废气排放。
石化是指煅烧后的CaO与大气中的水和CO2反应生成Ca(OH)2和CaCO3的过程。
这些反应使得石灰石中的CaO能与水快速反应,形成活性石灰的主要成分Ca(OH)2。
2. 活性石灰焙烧工艺流程(1)原料准备:将符合要求的石灰石进行破碎、磨矿处理,使其粒度适宜,并去除杂质。
(2)预处理:将石灰石送入预处理炉进行预处理,主要目的是预热石灰石,并降低活化温度。
(3)焙烧:将预处理后的石灰石送入石灰窑进行高温焙烧。
石灰窑一般采用旋转窑或立式窑,通过火焰、燃料和石灰石的相互作用,使石灰石达到高温分解的条件。
(4)石化:焙烧后的石灰石进入降温器进行降温,并与大气中的水和CO2反应生成活性石灰的主要成分Ca(OH)2。
(5)成品处理:将石化后的石灰进行破碎、筛分,得到符合要求的活性石灰产品。
3. 活性石灰焙烧工艺应用领域(1)建筑材料:活性石灰广泛应用于建筑材料中,例如砌筑砌块、粉刷石灰浆、砂浆等。
活性石灰具有良好的水化硬化性能,能够提高建筑材料的强度和耐久性。
(2)环保:活性石灰可以用作气体净化剂,能够吸收和去除废气中的SO2、NOx等有害物质。
此外,活性石灰还可以用于水处理领域,去除水中的重金属、硫化物等污染物。
(3)冶金:活性石灰可用作冶金炉料添加剂,能够提高炉渣的脱硫性能,并调节炉渣的成分和性质,提高冶金过程的效率和产品质量。
石灰煅烧工艺流程
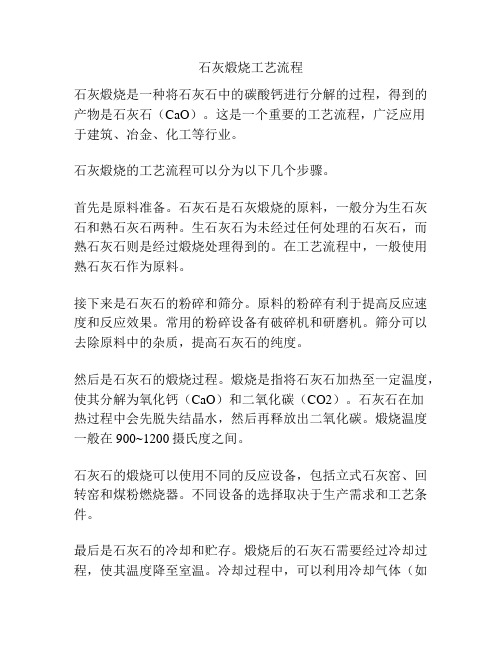
石灰煅烧工艺流程石灰煅烧是一种将石灰石中的碳酸钙进行分解的过程,得到的产物是石灰石(CaO)。
这是一个重要的工艺流程,广泛应用于建筑、冶金、化工等行业。
石灰煅烧的工艺流程可以分为以下几个步骤。
首先是原料准备。
石灰石是石灰煅烧的原料,一般分为生石灰石和熟石灰石两种。
生石灰石为未经过任何处理的石灰石,而熟石灰石则是经过煅烧处理得到的。
在工艺流程中,一般使用熟石灰石作为原料。
接下来是石灰石的粉碎和筛分。
原料的粉碎有利于提高反应速度和反应效果。
常用的粉碎设备有破碎机和研磨机。
筛分可以去除原料中的杂质,提高石灰石的纯度。
然后是石灰石的煅烧过程。
煅烧是指将石灰石加热至一定温度,使其分解为氧化钙(CaO)和二氧化碳(CO2)。
石灰石在加热过程中会先脱失结晶水,然后再释放出二氧化碳。
煅烧温度一般在900~1200摄氏度之间。
石灰石的煅烧可以使用不同的反应设备,包括立式石灰窑、回转窑和煤粉燃烧器。
不同设备的选择取决于生产需求和工艺条件。
最后是石灰石的冷却和贮存。
煅烧后的石灰石需要经过冷却过程,使其温度降至室温。
冷却过程中,可以利用冷却气体(如空气或冷水)对石灰石进行冷却。
冷却后的石灰石可以将其贮存在密封容器中,以避免吸湿和氧化。
石灰煅烧的工艺流程还可以根据实际情况进行调整和优化。
例如,在煅烧过程中可以使用适当的添加剂,以提高产品的质量和性能。
在冷却过程中,还可以对冷却气体进行处理,以达到节能和环保的目的。
总的来说,石灰煅烧是一个复杂的工艺流程,需要合理的控制参数和装置设计。
通过煅烧,石灰石中的碳酸钙被分解为氧化钙和二氧化碳,可以得到高纯度和高活性的石灰石产品,广泛应用于各个行业。
活性灰生产工艺流程
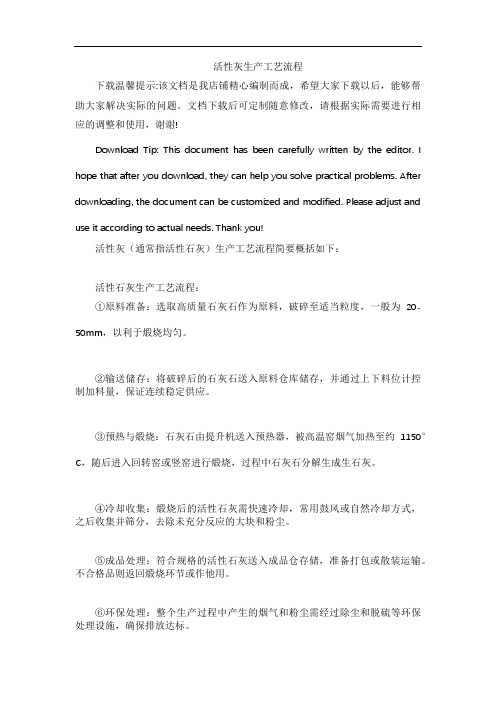
活性灰生产工艺流程下载温馨提示:该文档是我店铺精心编制而成,希望大家下载以后,能够帮助大家解决实际的问题。
文档下载后可定制随意修改,请根据实际需要进行相应的调整和使用,谢谢!Download Tip: This document has been carefully written by the editor. I hope that after you download, they can help you solve practical problems. After downloading, the document can be customized and modified. Please adjust and use it according to actual needs. Thank you!活性灰(通常指活性石灰)生产工艺流程简要概括如下:活性石灰生产工艺流程:①原料准备:选取高质量石灰石作为原料,破碎至适当粒度,一般为20-50mm,以利于煅烧均匀。
②输送储存:将破碎后的石灰石送入原料仓库储存,并通过上下料位计控制加料量,保证连续稳定供应。
③预热与煅烧:石灰石由提升机送入预热器,被高温窑烟气加热至约1150°C,随后进入回转窑或竖窑进行煅烧,过程中石灰石分解生成生石灰。
④冷却收集:煅烧后的活性石灰需快速冷却,常用鼓风或自然冷却方式,之后收集并筛分,去除未充分反应的大块和粉尘。
⑤成品处理:符合规格的活性石灰送入成品仓存储,准备打包或散装运输。
不合格品则返回煅烧环节或作他用。
⑥环保处理:整个生产过程中产生的烟气和粉尘需经过除尘和脱硫等环保处理设施,确保排放达标。
⑦质量检测:定期对成品活性石灰进行化学成分分析和活性度检测,以确保产品质量满足下游行业需求。
此流程旨在高效、环保地生产出高活性度的石灰产品,广泛应用于钢铁、化工、建材等多个领域。
3.2-16石灰焙烧
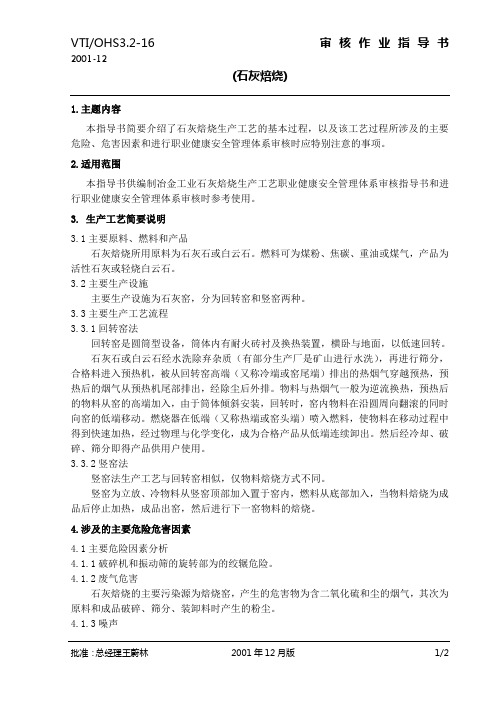
1.主题内容本指导书简要介绍了石灰焙烧生产工艺的基本过程,以及该工艺过程所涉及的主要危险、危害因素和进行职业健康安全管理体系审核时应特别注意的事项。
2.适用范围本指导书供编制冶金工业石灰焙烧生产工艺职业健康安全管理体系审核指导书和进行职业健康安全管理体系审核时参考使用。
3. 生产工艺简要说明3.1主要原料、燃料和产品石灰焙烧所用原料为石灰石或白云石。
燃料可为煤粉、焦碳、重油或煤气,产品为活性石灰或轻烧白云石。
3.2主要生产设施主要生产设施为石灰窑,分为回转窑和竖窑两种。
3.3主要生产工艺流程3.3.1回转窑法回转窑是圆筒型设备,筒体内有耐火砖衬及换热装置,横卧与地面,以低速回转。
石灰石或白云石经水洗除弃杂质(有部分生产厂是矿山进行水洗),再进行筛分,合格料进入预热机,被从回转窑高端(又称冷端或窑尾端)排出的热烟气穿越预热,预热后的烟气从预热机尾部排出,经除尘后外排。
物料与热烟气一般为逆流换热,预热后的物料从窑的高端加入,由于筒体倾斜安装,回转时,窑内物料在沿圆周向翻滚的同时向窑的低端移动。
燃烧器在低端(又称热端或窑头端)喷入燃料,使物料在移动过程中得到快速加热,经过物理与化学变化,成为合格产品从低端连续卸出。
然后经冷却、破碎、筛分即得产品供用户使用。
3.3.2竖窑法竖窑法生产工艺与回转窑相似,仅物料焙烧方式不同。
竖窑为立放、冷物料从竖窑顶部加入置于窑内,燃料从底部加入,当物料焙烧为成品后停止加热,成品出窑,然后进行下一窑物料的焙烧。
4.涉及的主要危险危害因素4.1主要危险因素分析4.1.1破碎机和振动筛的旋转部为的绞辗危险。
4.1.2废气危害石灰焙烧的主要污染源为焙烧窑,产生的危害物为含二氧化硫和尘的烟气,其次为原料和成品破碎、筛分、装卸料时产生的粉尘。
4.1.3噪声主要噪声源有排烟风机、冷却风机、破碎机和振动筛等。
4.1.4热辐射石灰窑、预热机对其岗位操作工人产生热辐射。
5.审核注意事项5.1由于焙烧的燃料是煤粉、重油或煤气审核时应注意其保管、存放、领用、使用等环节的防火、防爆。
石灰石在竖式石灰窑内的煅烧工艺(精选5篇)

石灰石在竖式石灰窑内的煅烧工艺(精选5篇)第一篇:石灰石在竖式石灰窑内的煅烧工艺石灰石在竖式石灰窑内的煅烧工艺灰钙粉吧张志强关键词:石灰窑;氧化钙;灰钙粉;氢氧化钙1 竖式石灰窑结构简介竖式石灰窑内部分为3个区域,即预热区、煅烧区、冷却区预热区在窑的上部,其作用是使由煅烧区升上来的废气与新投入的石灰石和炭材相遇,进行热交换,对将进入煅烧区的石灰石和炭材进行预热,因为石灰石的分解温度为812℃,所以大家把预热区与煅烧区的温度分界点定为850℃。
煅烧区是在窑的中部,是窑内进行化学反应的主要区域,也是全窑温度集中的地方,中心温度可达1200℃,边缘区域的最低温度为815℃,由冷却区升上来的空气在此处起助燃作用。
煅烧区的温度和位置,决定于物料下降速度、混合料的粒度、风量大小、风压高低、窑料配比等因素。
煅烧区主要反应有:(a)燃料燃烧C + O2 = CO2+33 777 KJ/kg炭 C + O2 =CO+10216.5KJ/kg 炭(b)石灰石CaCO3分解CaCO3 =Ca0 + CO2-1788.9kJ/kg 冷却区是在窑下部,当煅烧好的生石灰下降到这个区域时,与鼓风机送入的冷空气相遇产生热交换,生石灰被冷空气冷却到1OO℃以下自窑下卸出。
进人窑内的空气则被生石灰预加热后,上升到煅烧区,参加燃烧反应。
2 影响石灰石煅烧的主要因素影响石灰石煅烧因素主要有煅烧温度、石灰粒度、石灰石与燃料(焦炭)的混合均匀程度。
2.1 温度对石灰石煅烧的影响石灰石煅烧速度与温度有极大关系。
煅烧温度在900℃时,每小时只能煅烧0.33 cm;若在1000℃时,则每小时可烧透石灰0.66 cm,加快1倍;若在1 1O0℃,则每小时烧透1.4 cm,加快了3倍。
通常实际生产中石灰窑的煅烧温度应控制在1050℃左右,故要求窑内温度稳定且均匀分布,要求三个区域的位置适宜,同一截面的温度最好一致,这样石灰石分解就得到保证。
如果煅烧区下移,将使生成的石灰得不到充分冷却,空气得不到充分预热,冷却区缩短;如果煅烧区上移,石灰石预热不好(预热区缩短),热气得不到冷却,窑气带出热量增加。
活性石灰焙烧工艺

石灰石焙烧工艺碳酸钙的分解即剔除二氧化碳气体,留下固体氧化钙,这就是时间和温度起的作用。
CaCO3在890℃的温度下被分解成CaO 和CO2。
由Metso Minerals提供用于此目的的焙烧系统已设计完成。
石灰石表面的焙烧实际上在850℃开始,随着CO2气体与其他气体的混合,CO2气体部分压降低而发生焙烧。
这种较低的焙烧温度只适合于在正常大气压下每一颗粒物料较薄的外层。
当焙烧石灰石时,焙烧温度必须从每一物料颗粒的表面通过CaO厚层的稳定增高渗透到其内部,这使得热传导性比原矿石更低。
这就意味着大块石灰石的焙烧要比相同重量较小石灰石的焙烧需要更多的时间和更高的表面温度。
当给焙烧系统喂入不同粒度的物料且粒度比例大于2:1时,若料石能从给料仓内锥形料堆顶滑落下来,就易于发生不同粒度料石的分离。
这种分离就意味着系统的给料率发生了变化,也改变了预热器和回转窑中的热传递量。
为了阻止这种分离,建议供料时间间隔较短为好。
在多数情况下,每隔四个小时给料仓加一次料。
当大小不一的混合物料通过回转窑时,粒度较大的物料先落下并滚过物料滑床表面。
这样,较大颗粒物料比较小的物料得到更多的焙烧热量,并滑到料层下面回转窑的耐火砖衬上。
较大颗粒物料在回转窑中的连续翻滚使得所有物料在焙烧期间反复暴露于火焰或热气的时间很短。
在这种情况下,高温火焰不会过度焙烧物料颗粒表面。
这种焙烧热温下的全暴露只需要物料厚度的1/2热渗透。
完全焙烧的石灰块温度从中心895℃到表面1230℃。
对于任何延长时间而产生的表面较高温度都意味着过度焙烧。
较细的物料(当它们通过回转窑时滞留在料层底部)更多的则是靠与作为主热源的高温耐火砖衬的接触。
因此,回转窑的内衬应保持耐火材料所允许的热能特性。
正确地调整燃烧器可使回转窑的燃烧区或在更大范围上形成一层耐火层,这种耐火层的形成意味着对较细的物料颗粒具有较好的热传递效果。
另外,回转窑筒体内衬的这种耐火层可提高隔热能力,进而防止热量损耗,提高燃烧系统的燃料效率。
- 1、下载文档前请自行甄别文档内容的完整性,平台不提供额外的编辑、内容补充、找答案等附加服务。
- 2、"仅部分预览"的文档,不可在线预览部分如存在完整性等问题,可反馈申请退款(可完整预览的文档不适用该条件!)。
- 3、如文档侵犯您的权益,请联系客服反馈,我们会尽快为您处理(人工客服工作时间:9:00-18:30)。
石灰石焙烧工艺碳酸钙的分解即剔除二氧化碳气体,留下固体氧化钙,这就是时间和温度起的作用。
CaCO3在890℃的温度下被分解成CaO 和CO2。
由Metso Minerals提供用于此目的的焙烧系统已设计完成。
石灰石表面的焙烧实际上在850℃开始,随着CO2气体与其他气体的混合,CO2气体部分压降低而发生焙烧。
这种较低的焙烧温度只适合于在正常大气压下每一颗粒物料较薄的外层。
当焙烧石灰石时,焙烧温度必须从每一物料颗粒的表面通过CaO厚层的稳定增高渗透到其内部,这使得热传导性比原矿石更低。
这就意味着大块石灰石的焙烧要比相同重量较小石灰石的焙烧需要更多的时间和更高的表面温度。
当给焙烧系统喂入不同粒度的物料且粒度比例大于2:1时,若料石能从给料仓内锥形料堆顶滑落下来,就易于发生不同粒度料石的分离。
这种分离就意味着系统的给料率发生了变化,也改变了预热器和回转窑中的热传递量。
为了阻止这种分离,建议供料时间间隔较短为好。
在多数情况下,每隔四个小时给料仓加一次料。
当大小不一的混合物料通过回转窑时,粒度较大的物料先落下并滚过物料滑床表面。
这样,较大颗粒物料比较小的物料得到更多的焙烧热量,并滑到料层下面回转窑的耐火砖衬上。
较大颗粒物料在回转窑中的连续翻滚使得所有物料在焙烧期间反复暴露于火焰或热气的时间很短。
在这种情况下,高温火焰不会过度焙烧物料颗粒表面。
这种焙烧热温下的全暴露只需要物料厚度的1/2热渗透。
完全焙烧的石灰块温度从中心895℃到表面1230℃。
对于任何延长时间而产生的表面较高温度都意味着过度焙烧。
较细的物料(当它们通过回转窑时滞留在料层底部)更多的则是靠与作为主热源的高温耐火砖衬的接触。
因此,回转窑的内衬应保持耐火材料所允许的热能特性。
正确地调整燃烧器可使回转窑的燃烧区或在更大范围上形成一层耐火层,这种耐火层的形成意味着对较细的物料颗粒具有较好的热传递效果。
另外,回转窑筒体内衬的这种耐火层可提高隔热能力,进而防止热量损耗,提高燃烧系统的燃料效率。
对O2气体进行连续分析(从回转窑所排的气体中进行采样并记录O2气体量)可以不断显示石灰的生产效率。
最佳的燃烧效率应符合超标气体排放小的要求,即回转窑气体排放中O2的含量约为1/2-1%。
燃烧率(燃烧系统所耗燃料)必须定期调节以保持石灰的产量。
若燃烧率变化,必须通过系统同时改变风流量。
必须调节风流量以便使燃烧区有足够的空气使燃料得以充分燃烧。
风量不够会在回转窑进料端产生一氧化碳(CO),这种CO可能与给料盖处泄露的气体相混合,导致燃烧延缓,并升高回转窑排气温度。
一旦CO发生了提高温度的作用,就有可能对耐火材料和不锈钢部件的使用寿命带来不利影响,小量的超标气体(燃烧区)可使回转窑排气量和温度保持在一个较低的水平上。
过量的超标气体减少了回转窑燃烧端的气体,从而降低了燃烧区的温度,由于这种温降物料的热传递也会降低,从而造成石灰欠烧,还会使含硫量增高。
通过系统的风量可通过调节通风或通过燃烧护罩调节风压来改变,理想的燃烧盖通风应稍有负压。
燃烧器火焰形状以及物料的热传递量取决于燃料引入的燃气量。
由于燃料的流量是恒定的,通过燃烧器的气体的增加减小了火焰但增加了强度。
一次风的增加还会降低燃烧区的温度,减少一次风会使火焰变长和更柔和,同时提高了燃烧区的温度。
如高温计测得的燃烧区温度是比较相对的,还是应观察燃烧器火焰反映的一些热温。
经验表明当生产特级石灰时,在恒定的通风条件下使用稳定的回转窑负荷,热电偶的读数会较恒定。
通常可说明的是焙烧系统的有效运行,石灰的产量取决于下列工作变量。
1、焙烧系统的入料必须是有品质的干净石料,如“性能声明”中所规定的。
2、回转窑的排气和预热器进口温度在整个运行中应保持恒定。
3、如回转窑RPM所确定的滞留时间在正常运行时应保持恒定。
4、给料率的波动对产量有直接影响,除非焙烧控制变量及时调整。
给料率的变更只是用于提高或降低生产率抑或适应停机时间。
5、保持恒定的燃烧条件是非常重要的。
这是由控制系统自动完成的。
该控制系统可控制进入燃烧系统的风量和燃烧量,通过控制ID风机的转速保持正确的护罩通风。
燃烧条件的变更应保持在一个最低的水平。
在作变更前应给系统充足的时间来调定一变更。
短时间内这种变更过于频繁会导致系统定期(周期)运行,如再回复到平衡状态极为困难。
一般来说,应记住均匀给料,恒定通风,保持回转窑恒速都是高品质石灰生产中的最为重要的因素。
第二部分石灰石焙烧系统石灰石料仓石灰石由买方所提供的带式运输机被送往料仓,石灰石通过仓顶开口进入料仓并分配给预热器给料溜槽。
料仓装有声控料位指示器,并通过工艺控制计算机发出高料位和低料位报警,PLC 的高料位报警用于自动关闭给料系统。
当料仓出现低料位时,PLC低料位报警用来自动起动给料系统。
料仓的容量很大足以为回转窑提供4-6小时的给料量。
带式运输机的能力被选择用于给料仓供料1至2小时。
预热器每个预热器仓通过方形溜槽收到来自料仓的石料。
溜槽在料仓和预热器之间建有气密封,因而无需在料仓顶部的复杂的机械密封。
石灰石滞留在预热器仓斜底面上,形成了一个从底面到石料分配器的环状石柱。
回转窑的处理和燃烧气体被送入石料床层,其平面顶部与内垂直壁板相接,在每一预热器间的隔墙下面。
参看Metso Merals图,7-81978,可在该图看到这一部分。
气体的热量为:原料中15-35%的CO2在预热器中被释放。
没有完全焙烧的石灰石由推捣装置从每一个预热器仓被推入预热器中间料仓,这些装置包括由棒杆推动的合金钢铸件,它是由液压缸控制的。
这种铸件是预热器中唯一的非耐火部件。
当推捣装置运动时,石料中的压力增大。
推捣装置的端面与内顶间的角度在Metso Mineral的设计中是较大的,这就降低了石块与bull nose间的压力,因而减少了在bull nose处石料的破碎和耐火材料的磨蚀。
每一预热器仓间均有隔墙,其底部设有进入料床的气流通道,进一步提高了从气体到石灰石的热传递并降低了预热器排气温度和温降。
预热器液压动力装置通过预热器的石灰石流量由液压千斤顶控制。
液压动力装置提供推动千斤顶的油缸所需的液压。
操作员可设定每天所需的产量,PLC可确定每小时所需的“冲程”次数并控制“冲程”顺序。
传送溜槽没有完全焙烧的石灰石从预热器被推入料仓,从石料料仓进入传送溜槽。
石料滑过传送溜槽的斜面进入回转窑,取消传送溜槽中的垂直壁板减少了石料的破碎。
溜槽底部采用碳化硅砖铺设以防止冲击和磨蚀。
回转窑的气体经传送溜槽进入预热器。
在回转窑和传送溜槽之间有一弹簧片密封以最大限度地减少进入处理中的漏气量。
回转窑物料从回转窑的高端流向低端,而同时火焰和燃烧气体是逆向流动。
回转窑装有变速驱动,这样可优化物料的装载,AC变频控制器控制变速。
驱动的减速比是为回转窑在50Hz并在常速条件下运行以达到设计能力而选用的。
该回转窑设计有两个支撑,以降低支点沉降差,简化对托轮的调节。
在回转窑两端装有锥形段,进料端锥段是防止给料溅出,而排料端锥段可提高物料的装载量并延长物料在火焰下的滞留时间。
多数石灰窑在排料端装有耐火挡墙,但Metso所提供的锥段可达到同样的目的而又不会增加排料端突出部分的重量。
锥段的另一个好处就是减小了防火罩的尺寸。
防火罩焙烧过的石灰通过闸门从排料锥段落下并进入冷却机。
闸门为合金铸件,有一个75mm的方形开口并设置在一斜面上,较小粒度的物料进入冷却机而过大的物料留在篦板上。
过大的物料通过开启一个门并将物料送入熟料溜槽的方法排出。
Metso公司的Niems冷却机物料经防火罩闸门后进入冷却机,冷却机的中心线相对于回转窑有些偏移以便使冷却机中心物料载荷居中。
从顶部看,冷却机为方形并被分成4个小方块体,每一方块体都有空气分配器,在排料仓底部还有一个振动给料机。
每一方形体的排料速度都可在控制室进行单独调节。
空气由冷却风机强制吹入冷却机,空气冷却逆流的石灰,然后向上移动经防火护罩闸门进入回转窑为燃烧提供氧气。
这4个方形体之间气流分配可通过人工调节器调节,参见1-67378图。
该冷却机原设计是由Lee Niems先生完成的(Lee Niems公司的资产由Metso Minerals买下)。
Lee Niems先生仍继续冷却机的研发工作以改进物料和气流,这些研发成果都为若干个有效的美国专利并由Metso Minerals公司提供。
冷却机的排料给料机。
有4台振动给料机装在冷却机底部以控制排料,冷却机中的物料厚度由控制系统保持。
这4台给料机运送来自每一个方形体的冷却过的石灰,每一台振动给料机的振动率是由操作员通过计算机控制系统进行调节。
振动率的调节要求使冷却机功能发挥至最大限度并将来自所有4个方形冷却体的石灰温度降至最低。
冷却(机)风机冷却(机)风机用于强制空气经过冷却机中的石灰床。
由于石灰床气孔和高度的变化,气流压降也随之变化。
为保持有一恒定的气流可测量风机进口风,进口气流调节阀由控制系统中的控制回路自动调节。
袋式除尘器预热器逸出的废气可通过环境空气来冷却(如有必要),闭路控制装置可调节气流调节器的位置以保持在除尘器进口处所允许的最高温度。
废气在脉动式除尘袋中被净化,除尘袋中有内接组件。
气体从除尘袋外部进入内部,然后进入净气室,除尘袋设置在钢制网笼上。
当整个除尘袋的压降超过预先设定值或净化周期间隔时间超过限值,其中心组件就会被脉动清理,可对除尘袋外侧喷射高压压缩空气以破碎尘块,这些尘块就会落入料仓底部,所收集的粉尘经一可旋转的气密出口由重力排出。
所有除尘袋组件中经净化的气体被收集到一导管中并送至ID风机。
吸风机吸风机(ID)吸引燃烧产品——石灰石中的CO2,和通过系统的泄漏气体,而同时要保持回转窑在一定的负压条件下运行。
该风机装有一个进口气流调节器,它是由自动回路控制以保持在防火罩内有一恒定的负压。
排气烟囱从ID风机出来的气体将直接进入排气烟囱,装有梯子的检测口平台也可提供。
操作原理概述焙烧的生产率取决于从预热器中喂料次数,推捣器是容量给料机,因此,在喂料次数和石灰产量之间有一固定比率,大多数石灰厂的操作员喜欢在窑速和预热器喂料速率之间保持一个恒定比率,以使窑中的填料保持恒定。
每小时的喂料次数和窑的转速由PLC操作员设定。
重要的温度是回转窑排气、预热器进口、燃烧区、二次风和预热器排气温度。
回转窑的排气温度由PLC操作员设定并决定着产品质量。
回转窑的燃烧率可由人工调节或由自动控制回路调节以保持窑的排气温度。
若窑的排气温度过高,产品就会很硬(低LOI)且活性低,若排气温度过低,产品就很软(高LOI)活性高。
在正常运行期间,窑的排气温度和预热器进口气体温度之间的温度应略有降低。
这种降低是由窑的给料端密封漏气所致。
若窑排气温度与预热器进口气体温度之间所确定的差值减小或有所增大,这就有可能是窑排气中有易烧物质,密封泄漏气中的氧气在燃烧这些物质,进而提高了预热器进口气体的温度。